Ystral Batt-TDS offers faster electrode slurry mixing
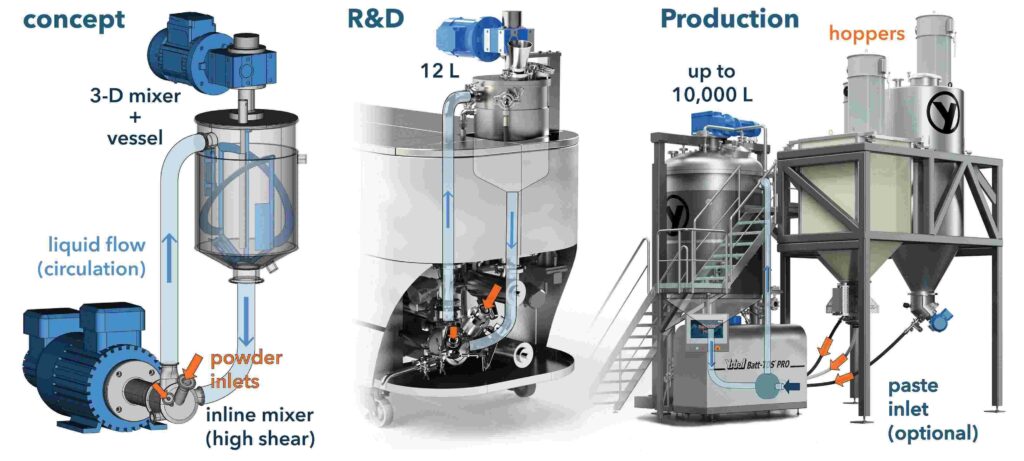
(Image courtesy of Ystral)
Surging EV adoption has placed unprecedented demand on lithium-ion battery production, so advances in manufacturing processes such as electrode slurry production are critical. Ystral’s Batt-TDS mixing platform is designed to reduce process times significantly while maintaining precision and efficiency, writes Peter Donaldson.
Electrode slurry preparation typically involves the dispersion of powders into a liquid medium. Conventional methods rely on planetary mixers that need long processing times due to high viscosity thresholds (several million centipoise) and limited shear rates. The Batt-TDS system achieves high shear rates independent of viscosity constraints with advanced rotor-stator technology.
Dr. Holger Becker, process and application engineer at Ystral, notes that the speed of Batt-TDS helps to make it more efficient overall than planetary mixers. “The motors may be the same size, but the overall energy requirement is significantly reduced due to the shorter process times,” he says.
Rapid mixing
Batt-TDS operates on a circulation process featuring an inline mixer for dust-free powder induction and dispersion, combined with a 3D mixer for rapid batch homogenization.
Unlike traditional mixers, which depend on prolonged exposure to shear stress, the Batt-TDS inline mixer concentrates this stress within milliseconds. The result is a 10,000-fold increase in specific capacity and a drastic reduction in mixing time, transforming hours-long processes into near-instantaneous operations.
“This means more can be produced with a smaller footprint,” Becker says. “If you look at the overall cycle, you can expect a time saving of approximately three hours.”
The powder is introduced and dispersed into the liquid stream under vacuum so that no dust can leak out, allowing the operator to work safely with less personal protective equipment. Eliminating dust release also reduces product waste and associated costs, he notes.
Tailored for high viscosity
One of the most significant challenges in battery slurry production is managing high-viscosity materials while ensuring effective dispersion. The Batt-TDS inline mixer addresses this with a large stator diameter and a finely tuned rotor-stator gap, enabling controlled exposure to high shear forces. This configuration allows for precise dispersion of powders across a wide viscosity range, from low to high, without compromising process efficiency.
The flexibility of the system lies in its ability to decouple shear rate from material viscosity, enabling gentle yet efficient separation of agglomerates without any centrifugal effects. This approach not only enhances the homogeneity of the slurry, but also minimises energy consumption and mechanical wear.
Furthermore, the adjustable shear rate allows the Batt-TDS to adapt to various powders and cell chemistries, optimising the dispersion process for diverse formulations. Different recipes can be stored in the control system.
To maintain process consistency and avoid contamination when switching between cell chemistries or slurry compositions, it is essential to stick to the validated cleaning procedure, Becker says.
The ability to handle a variety of materials, including carbon nanotubes and novel binders, is also helpful when developing new formulations, he emphasises. “If the powder will flow, we can handle it. However, new materials always need to be tested and the equipment can be adjusted.”
Ystral’s Batt-TDS platform caters for a range of operational scales, from research and development to full-scale production. Batt-TDS Navi, for example, is a compact, 12-litre unit for formulation development and process trials, while Batt-TDS Pro Supra is a large-scale production system, capable of processing 10,000-litre batches for cathode or anode slurry preparation.
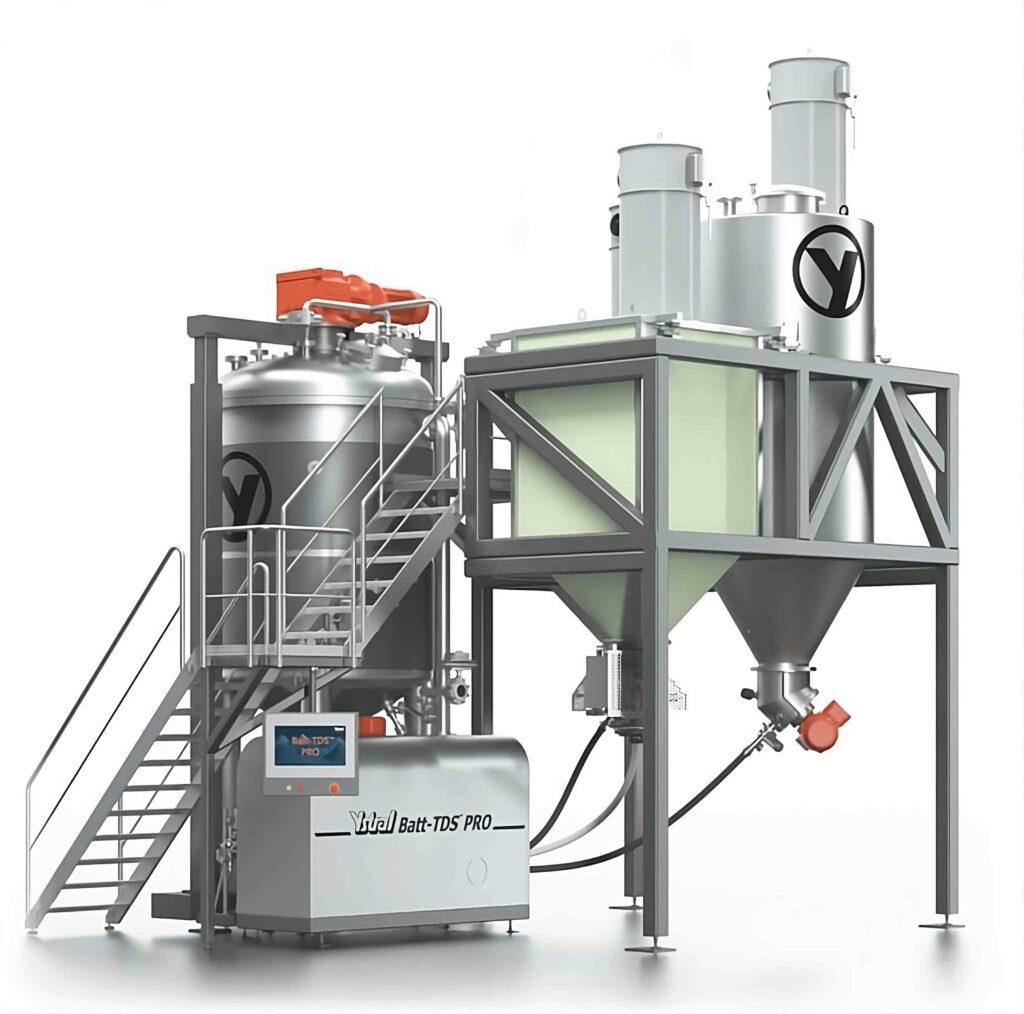
(Image courtesy of Ystral)
Scaling up
Crucially, the system ensures seamless scalability, allowing r&d results to be translated directly to production environments. This eliminates the need for costly and time-intensive revalidation when scaling up processes.
“For the Batt-TDS the size of the process tank doesn’t matter. It is only circulation time that is important for the overall process.”
Click here to read the latest issue of E-Mobility Engineering.
ONLINE PARTNERS
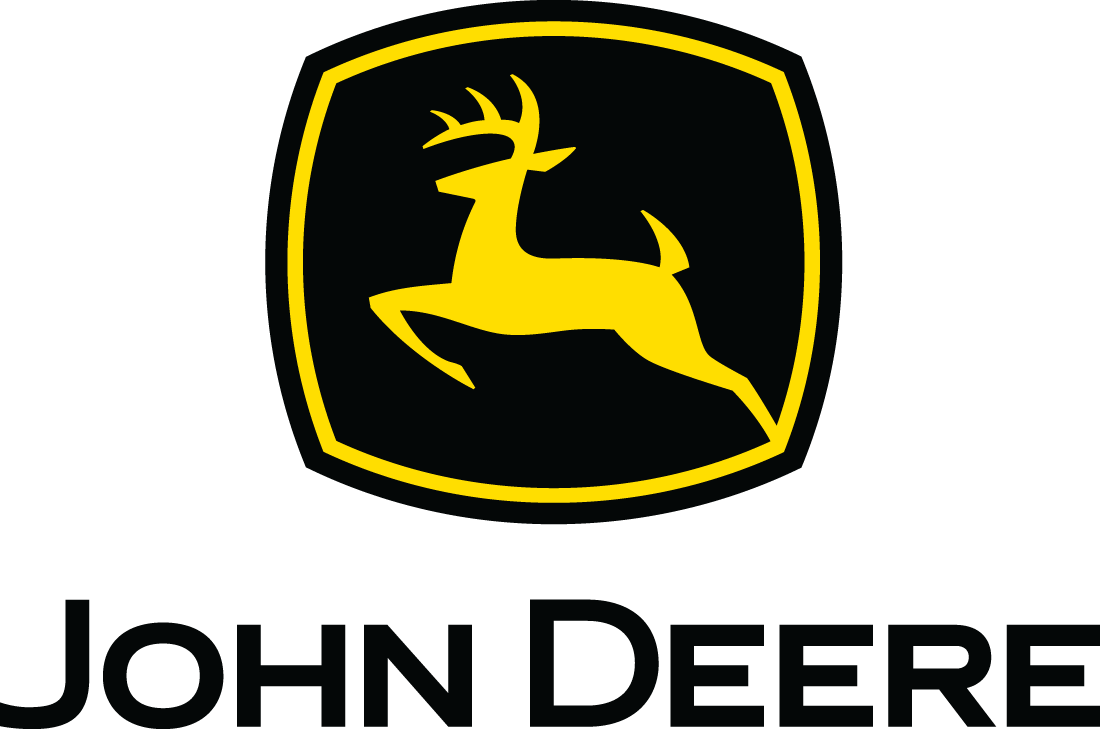
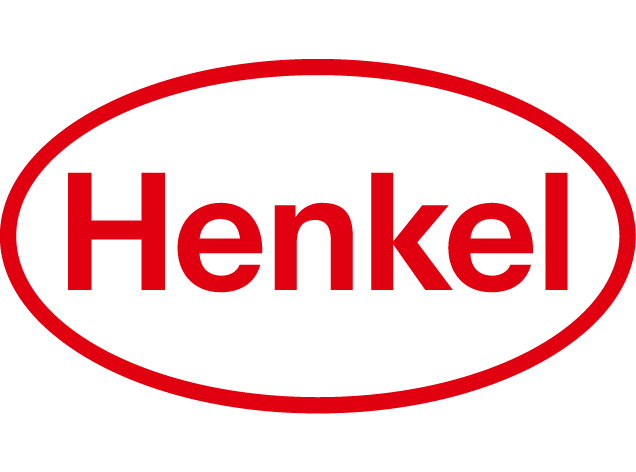
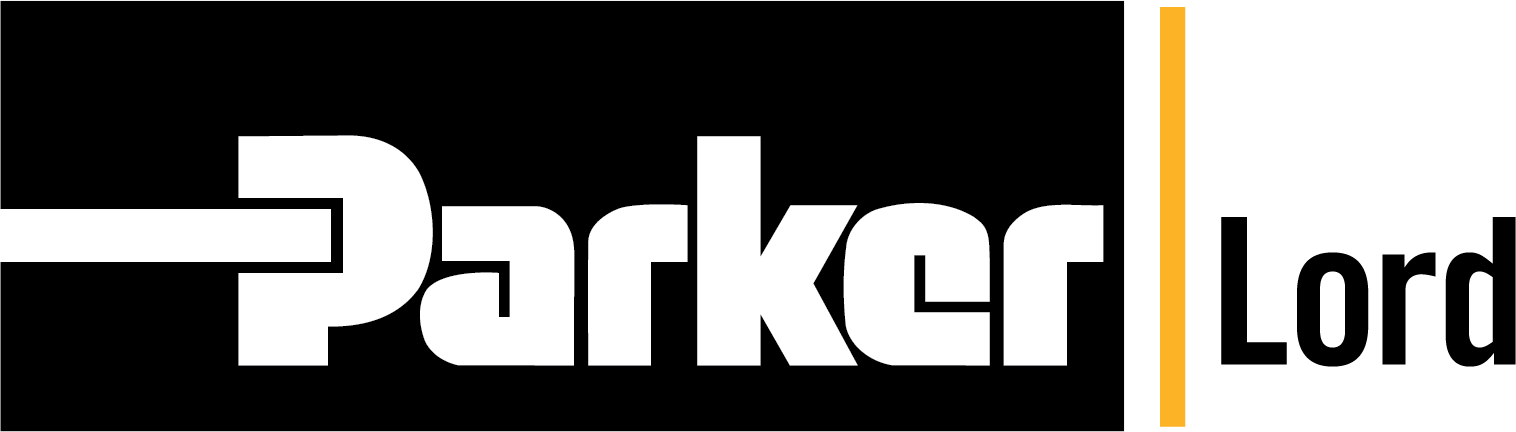
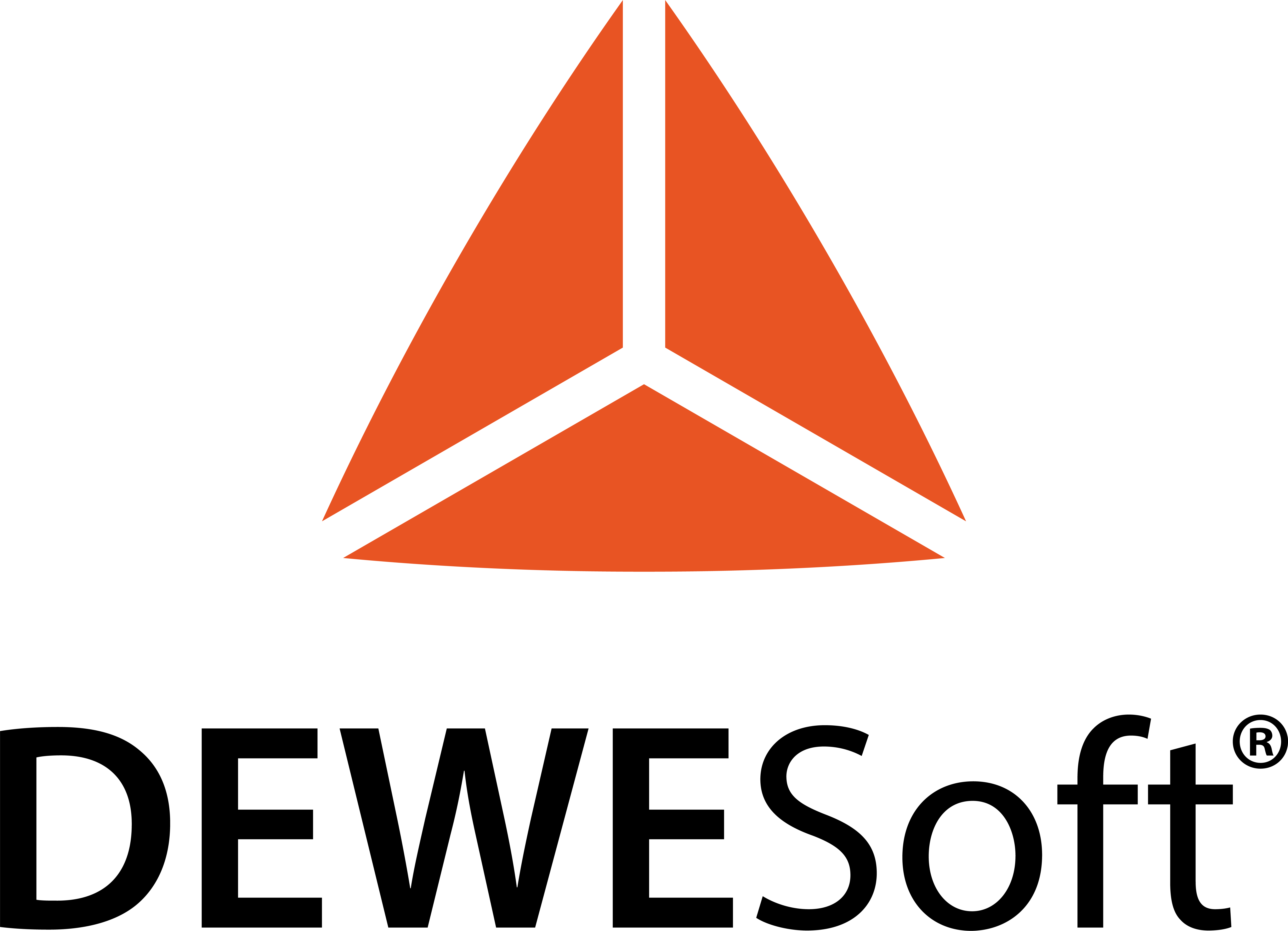
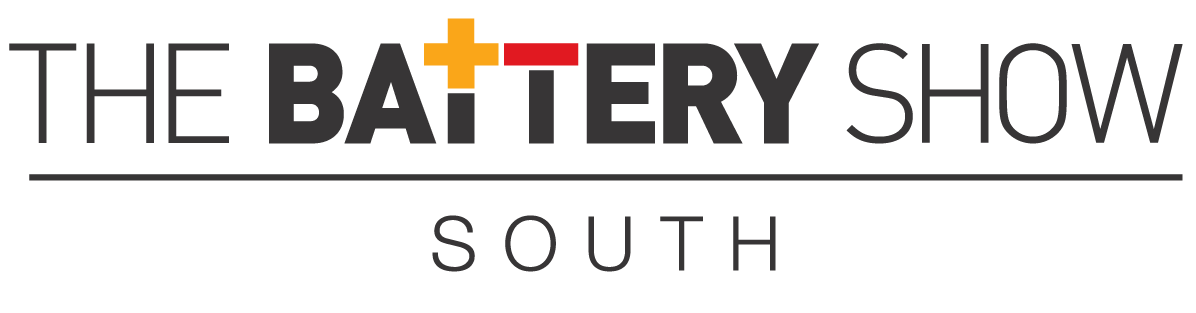
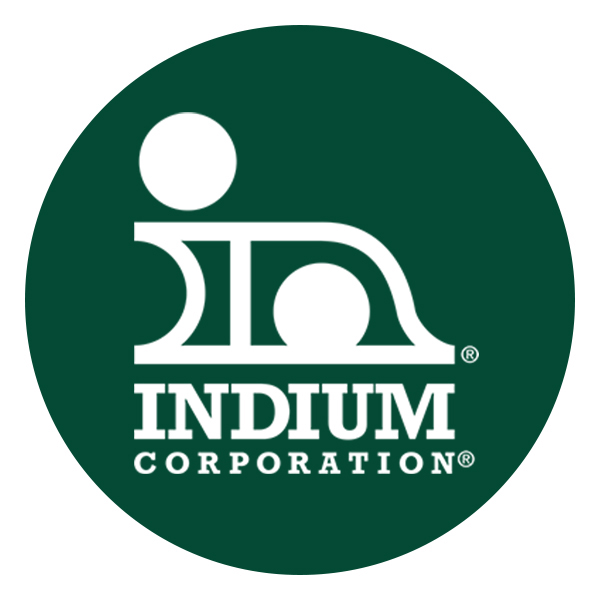

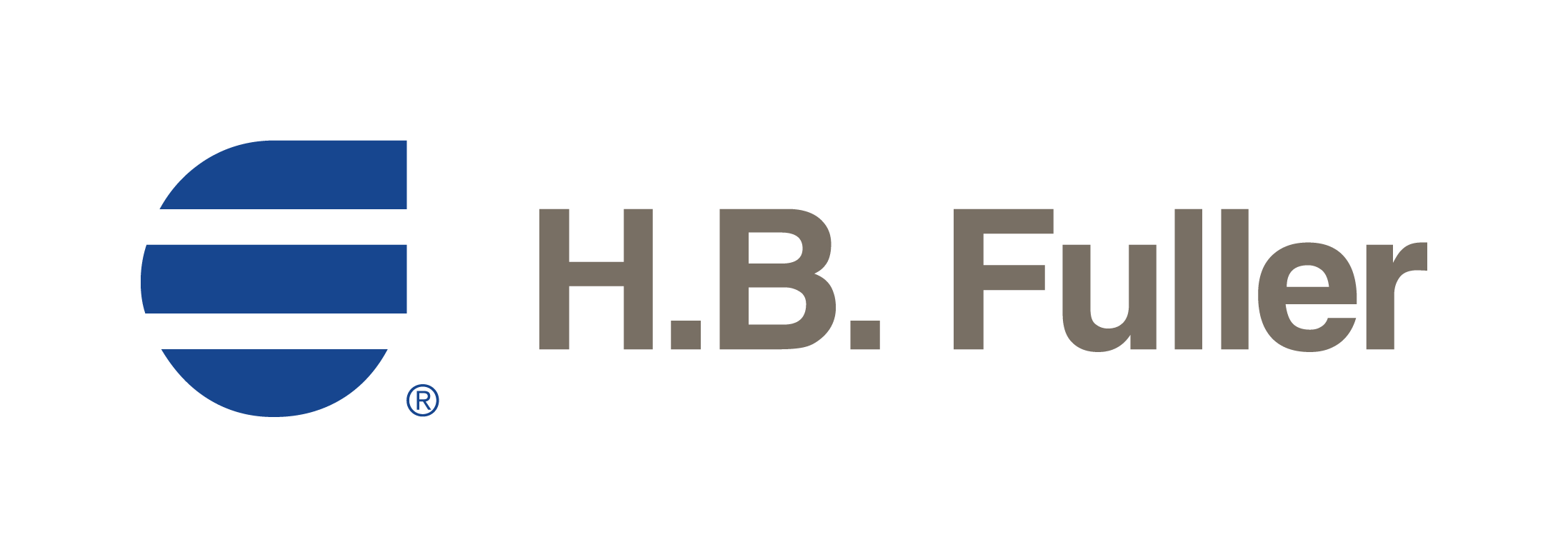
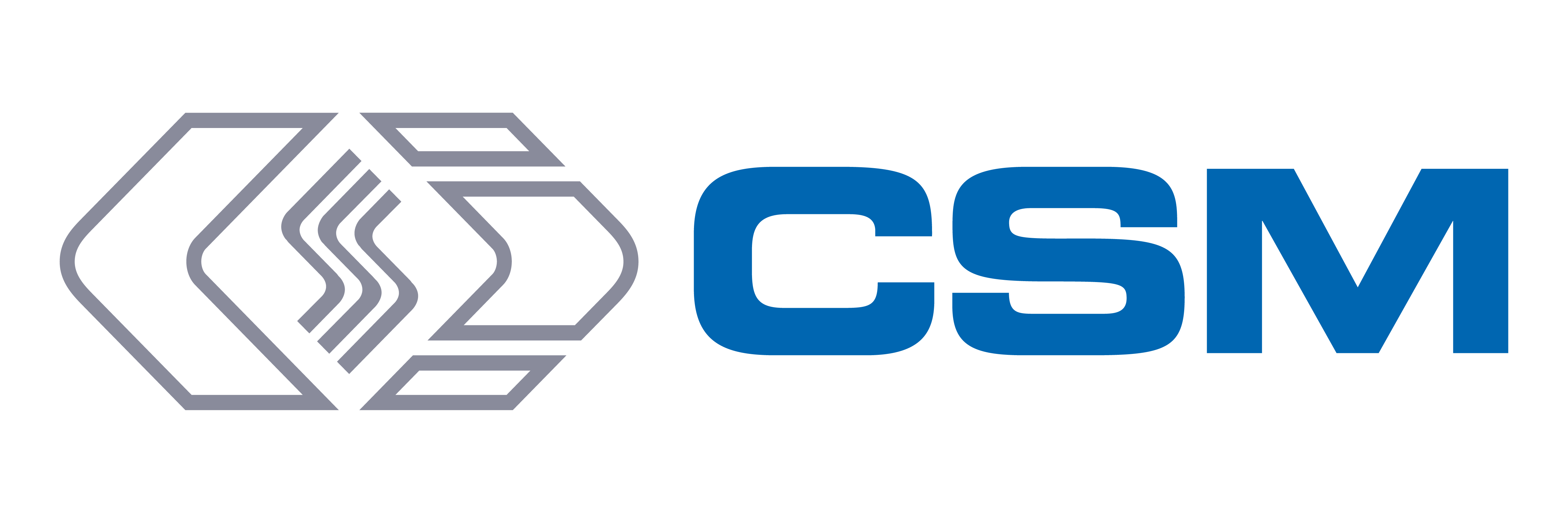
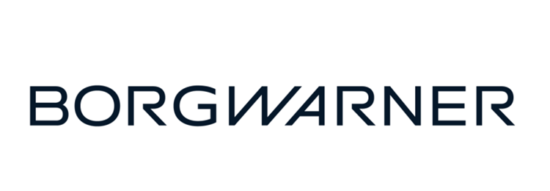