Workhorse Group C-Series
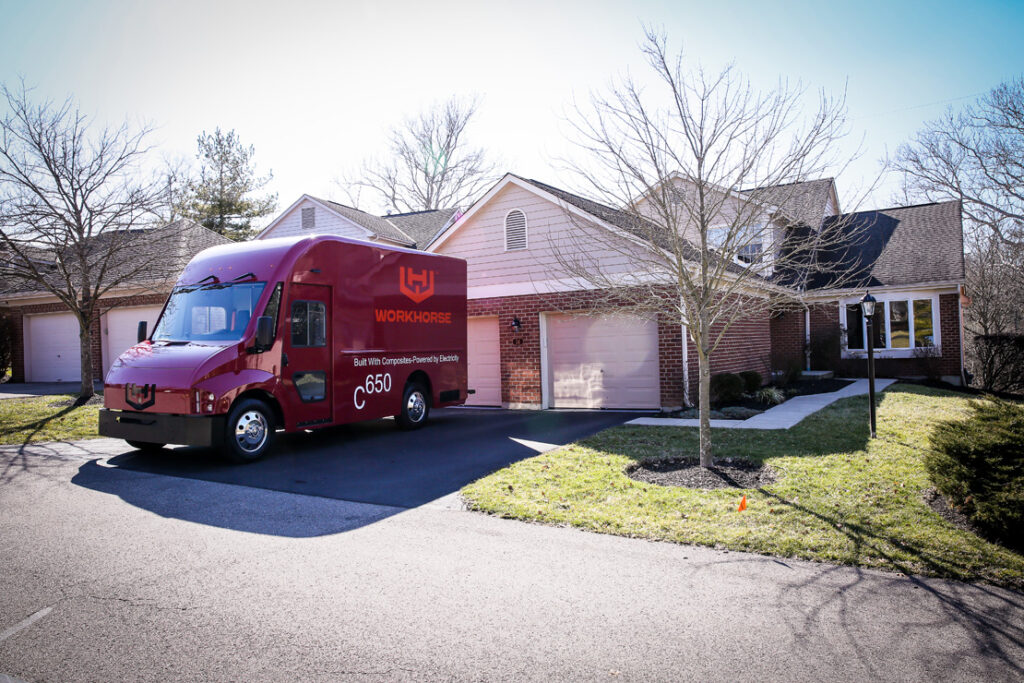
(Images courtesy of Workhorse Group)
Rory Jackson details the development of these electric delivery vans, which have been designed and built from the ground up…
Delivering the goods
The Workhorse Group designs and builds battery-electric medium-duty trucks, and earlier this year it started production of its C-Series vans – a family of eventually four commercial EVs intended for use in large courier fleets. The company, headquartered in Loveland, Ohio, was originally launched as AMP Electric Vehicles in 2007 with an eye on hybridising trucks run by UPS and electrifying finished passenger cars.
In both regards, it achieved notable successes, including productionised electric conversion kits for the Chevrolet Equinox SUV, the Mercedes- Benz ML350 and the Jeep Grand Cherokee. Also, its hybrid-electric Class 6 UPS van was capable of 35 MPGe (miles per gallon gasoline equivalent, or 1.04 miles per kWh), compared with the 8 MPGe of UPS’ conventional ICE-powered van. However, the company acquired a manufacturing plant in Indiana in 2015, having seen that becoming an OEM was more cost-efficient than refitting existing vehicles.
The first two vans in the series are the C1000, after its 1000 cu ft of interior cargo space, and the C650, with 650 cu ft of storage. Workhorse is also developing a refrigerated version of the C650 and a C1200 that will have 1200 cu ft of space, as well as a UAV based system called Horsefly, to be launched and recovered from C1000 for autonomous tethered drop-off of packages over the last mile.
The C650 has been designed as a sprinter-type light commercial van, with a 401.3 cm wheelbase and a 627.4 cm vehicle length, while the C1000 replaces traditional ICE box trucks for longer postal routes in major cities, being 823 cm long and having a wheelbase of 482.6 cm. The C650 also typically integrates a 72 kWh battery pack, while the C1000 usually comes with 102 kWh of capacity.
Otherwise, the two have largely identical dimensions – 309.9 cm tall, 218.4 cm wide, and with ground clearances of 18.4 cm. They also have essentially identical powertrains and drivetrains, with the same architecture, components and technology choices underpinning them.
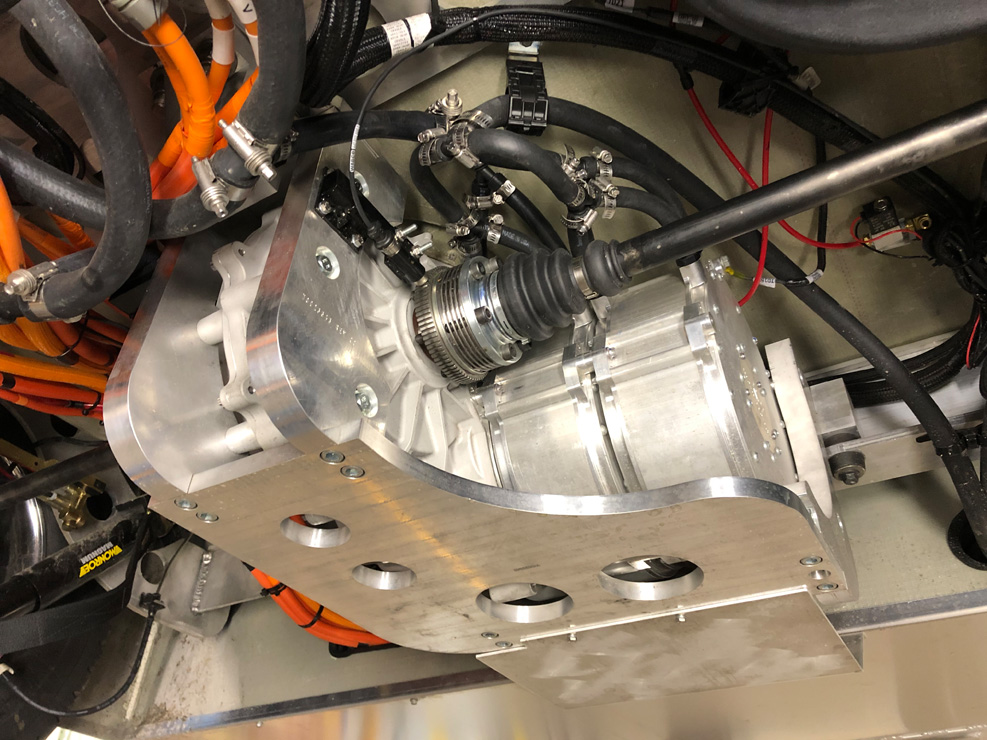
Onboard energy is stored in packs constructed around pouch-type lithium nickel manganese cobalt oxide (NMC) cells. Traction is supplied by two axial flux motors that provide rear-wheel drive, and automatic regenerative braking is integrated for enhancing range and drive comfort.
As well as a top speed of 75 mph (120.7 kph), the vans have recently achieved a specific energy consumption of 49 MPGe, as validated in tests by the California Air Resources Board and the USA’s Environmental Protection Agency, which paved the way for their sale and operation in California.
Key design factors
Through discussions with drivers and technicians at UPS, DHL, FedEx and other courier services, Workhorse has sought to improve every facet of traditional delivery vans, most of which continue to use designs from the 1950s, with heavy construction materials, beams and axles.
The company’s electric powertrains and lightweight materials still had to work within certain constraints, however. For example, the cabin floor is still typically about 30 cm from the ground, but Workhorse could also exploit battery energy regeneration during the frequent stops, starts and creeps that postal drivers perform on their rounds.
In addition to positioning the floor at about 18 cm above the road to reduce the step count by one, Workhorse has replaced most of the traditional cabin’s metallic structure and chassis with composites. That, and replacing the original fuel engine with an e-motor, makes the courier’s driving experience much quieter.
“The first time drivers tested our C-Series prototype, they were complaining about a clanging sound,” recounts Rob Willison, COO of Workhorse Group. “The culprit was the roll-up door on the rear, which hadn’t changed at all – they’d just never heard it over the clamour of the ICE and the metal chassis before.
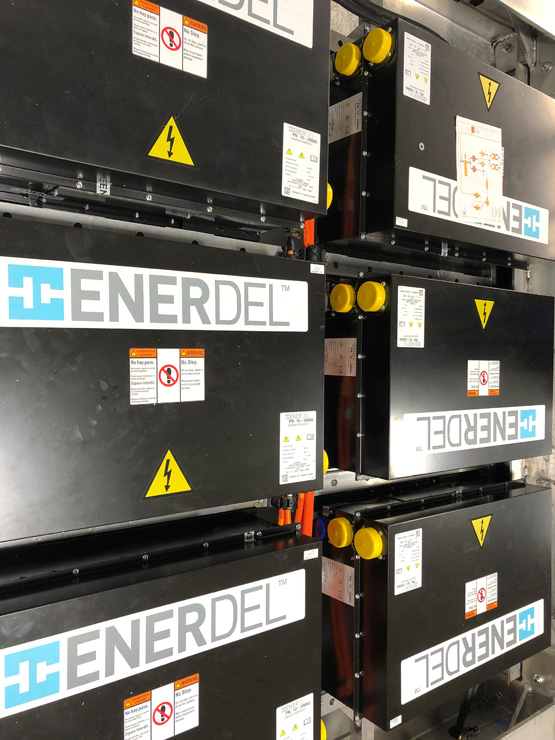
“They could also hear the condenser fan we put under the hood. We’d set that as a constant-speed, on/off system, but then changed it to use PWM, to keep the driver’s environment as annoyance-free and relaxing as possible.”
Also, based on Workhorse’s interviews with maintenance technicians, the rear drive is packaged in a ‘cradle’ that integrates the traction motors, gearbox, half-shafts, brakes and some cooling lines.
The cradle can be unfastened and dropped as a single unit when inspections are needed, and replaced with a spare one within an hour. Meanwhile, the dropped cradle can be bench-serviced.
Many ICE-powered postal vans incorporate similar packaging concepts in their drivetrain, but Workhorse is one of the first companies to design such a system for a commercial EV. “The C-Series is also unique in that it has an independent rear suspension with two trailing arms – all the other vehicles in this size class have a single differential axle with leaf springs,” Willison says. “So by comparison, our system gives a much more comfortable ride.
“And on the front, instead of a solid axle we have a short-long arm [SLA] suspension with coil springs, again to ensure a much nicer ride than is typical. We’ve tested our chassis over highspeed road bumps at the Transportation Research Centre in Marysville, Ohio, and we’ve seen the body keep perfectly solid as the wheels oscillated over the bumps.”
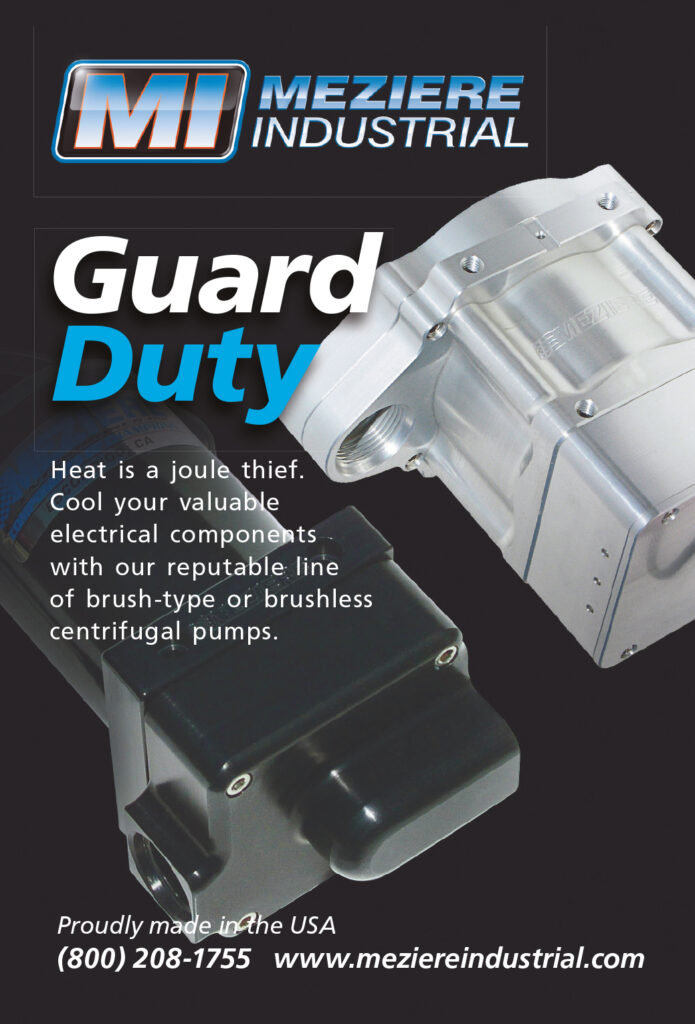
As a final point for ease of maintenance, QR codes have been placed on every component. If there’s a technical problem with a part, a technician can simply scan its code rather than having to scroll through inventory lists and catalogues for the serial number. The scan will output the part number, streamlining mechanics’ assessment work significantly.
“The result is that the C-Series has lower operating costs, less noise, zero emissions and more carrying capacity than conventional ICE postal vans,” Willison says. ”EVs in general offer great opportunities to achieve all these important commercial targets, although for us, our lightweight composite chassis has been the real enabler for getting the most out of our powertrain.”
Composite materials
Workhorse studied a range of materials to gauge how best to minimise the weight of the chassis, observing that cost rose exponentially with strength among composites, metals and essentially all the other materials.
“As you go from economy fibreglass to structural/unidirectional fibreglass, up to Kevlar and carbon composite, you’re getting incrementally stronger and lighter, but the cost is going up much faster,” Willison explains.
“However, there’s a sweet spot between economy glass and structural glass, so we’ve used a lot of structural type unidirectional weave fibreglass, running through the walls, floors, doors and so on, all as a largely monocoque structure.”
Most of the chassis is therefore a sandwich of two fibreglass layers around a core material selected for further lightness. Most of the structure uses balsa wood as the core, although polypropylene is used in some places as well. Also, in areas of high mechanical stress – such as the A-pillar, the chassis and shelving areas, where high bending stresses can occur – aluminium structures are used.
Metals have also been retained where composites lack the necessary strength, flexibility or for cost reasons. For example, all the suspension parts are aluminium, and aluminium pieces are installed as brackets to support electrical components.
“In the future, we may switch to using sheet-moulded or injection-moulded plastic compounds in place of some composites, to save further weight and costs, but for now, open-moulded, hand lay-up fibreglass is serving us and our end-users very well,” Willison says. “Ideally we’d even like to design out areas of thicker core materials, to optimise the weight to the strength needed.
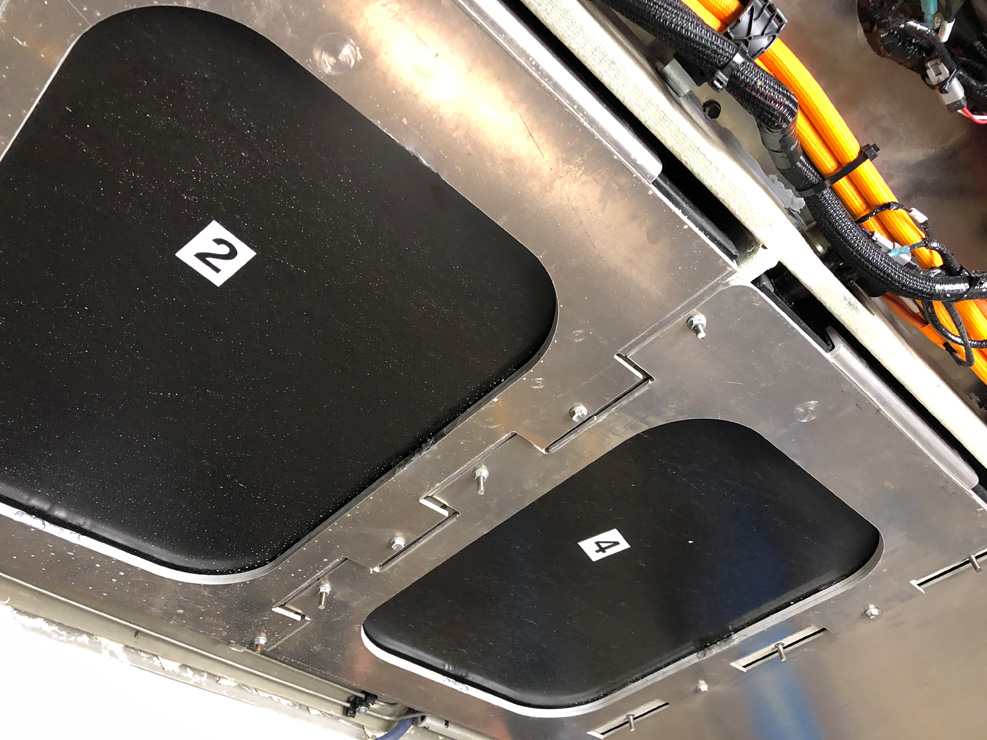
“At the moment, our empty curb weight is about 2500 lb less than the closest comparable ICE delivery van. To have achieved that with a 70 kWh battery pack was not easy – after all, most passenger EVs come off heavier than their ICE counterparts.”
The chassis has also been designed in Autodesk CFD to be much more aerodynamic than conventional step vans, as typically such vans feature a flat front and windshield, which greatly increases drag. As such, the C-Series features a curved front end, with the curve gradients and corners shaped to maximise energy efficiency when operating at speed on highways.
Control software
The vehicle has five different CAN buses, ranging from 500 kbit/s to 1 Mbit/s, with US multinational engineering firm Parker Hannafin having been chosen to construct the control modules. That company’s IQAN protocol was seen as ideal by Workhorse for object-oriented programming, which was useful for the rapid development of state diagrams as well as graphical tools for the control architecture.
A Parker MC43 forms the main ECU, and enables separation between the vehicle’s controls, telematics and BMS. Firewalls can be set up to prevent corruption of data transmitted between them if end-users have any concerns about their data.
The MC43 is also responsible for taking key inputs from the steering angle sensor, accelerator, brake position sensor, onboard two-axis accelerometers, and outside air temperature sensors for example, to determine the control outputs and limits for the vehicle’s handling, energy regeneration, thermal management, acceleration, battery safety and so on.
Drivetrain
As mentioned, the core of the drivetrain is a pair of axial-flux motors mounted on a common shaft. Which model they are is undisclosed but they were selected for their high power efficiency.
Each has an internal permanent magnet rotor and an external dual stator – one stator plate over each rotor face. This is mainly for increased magnetic efficiency and lower magnetic losses compared with single-stator systems.
“Going with a dual axial drive also allows us to shut down one motor at cruise whenever possible, which makes for greater energy efficiency – and of course there’s also redundancy in case one drive has an issue,” Willison says. “There are also the NVH benefits of having two smaller motors rather than one bigger one.”
He adds that when looking at the range of commercially available automotive electric drives, while there are many small electric trans-axles and very large e-axles and motors for Class 8 trucks, there are comparably very few for the C-series’ weight class: between 12,000 and 14,000 lb. Most companies therefore opt to take an overly large drive and derate it, or take two smaller motors and integrate them in an all wheel drive system.
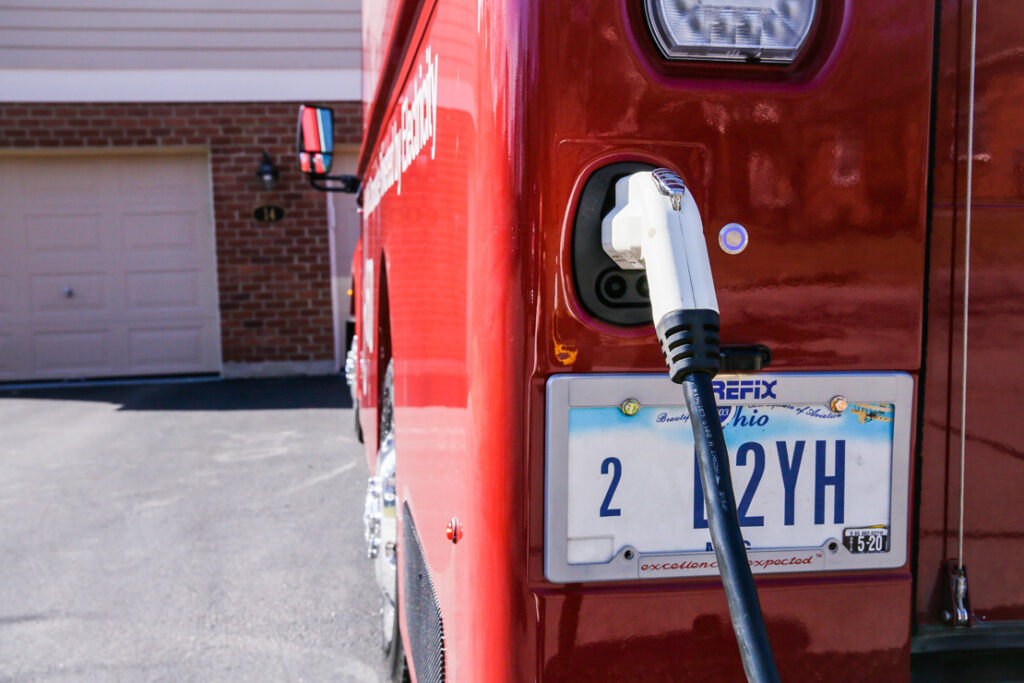
In Workhorse’s case, the e-axle has proven effective in giving 75 mph at 9000 rpm, as well as a collective 425 bhp of power and 7500 Nm of torque, while generating as little noise and vibration as the company’s engineers had hoped for. Willison adds that 65-68 mph tends to be the most energy-efficient cruising speed.
The gearbox provides a 10.5:1 reduction from the motors to the wheels, with two half-shafts to the trailing arm suspension. CV joints are used on the rear drive axles, having been found to provide a smoother ride than U joints.
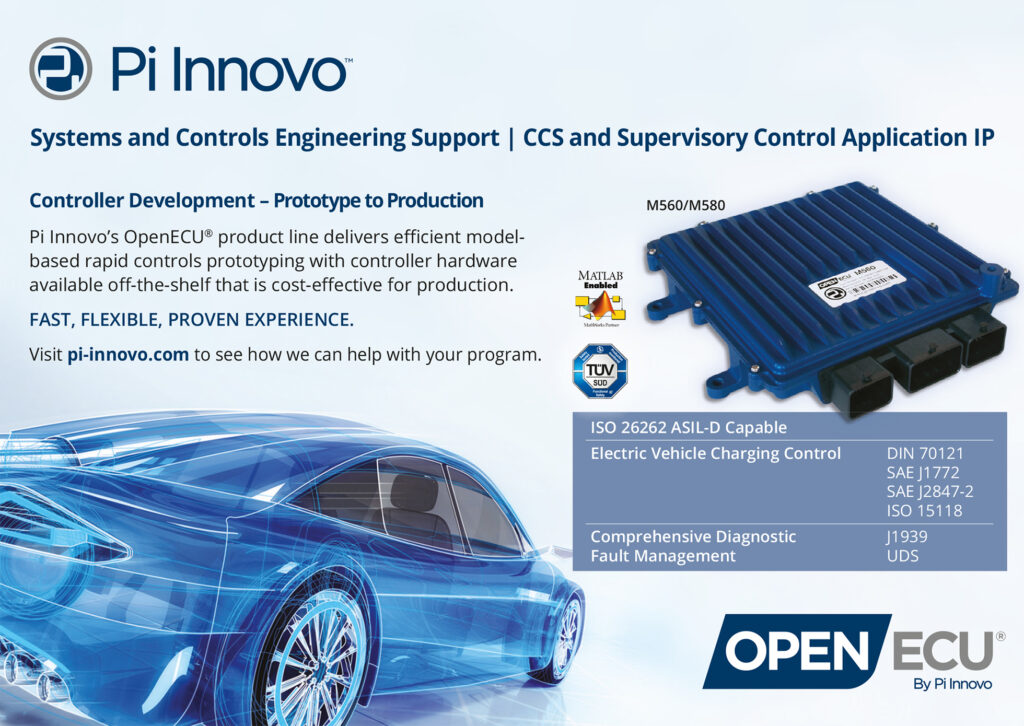
Also, while most postal trucks have dual rear tyres, the relatively light weight of the C-Series allows the use of single wheels at the back while handling the same cargo payloads, reducing part count and costs.
“Our steering axles at the front take most of the lateral and braking loads, although our rear drive takes the regenerative braking loads, which helps balance the distribution of loads and wear to a large extent,” Willison says. “Another benefit of mixing standard and regenerative braking is that we don’t go through brake pads anywhere near as quickly as most postal vans.
“We also write our own control software for the drive system – managing the vehicle efficiently during acceleration, deceleration, regeneration and cruise is a core competency of ours, even to the point where we’ll allow a fleet to set maximum power and regen.
“That’s something we can do geographically too. If you’re in Colorado for example, and you need to go up and down hills, we can unlock more power than in, say, Iowa or other states with flat terrain.”
A key technology in this efficiency driven approach to Workhorse’s control software is its proprietary Metron analytics and telematics application. It tracks up to 900 parameters in the vehicle and its components to help fleet managers determine how drivers are using the vehicle, and whether modifications to the control software parameters – or the powertrain hardware – could be helpful.
Regenerative braking
As mentioned, the frequent stop-and start operation of delivery vans working in busy streets allowed Workhorse to apply regenerative braking to great effect, The onboard motors serve as generators for delivering power back to the battery packs, with the company choosing cells that would provide a more cost-effective option in the long run than a more expensive supercapacitor or range extender.
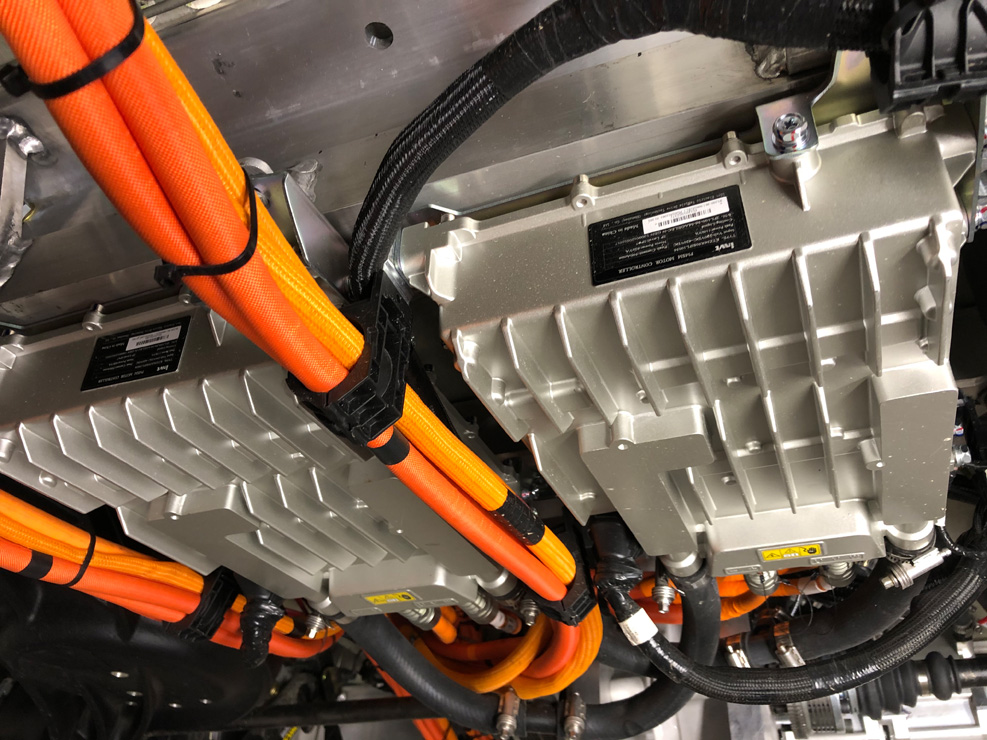
It is also worth noting that the constant movement of the driver’s foot between the throttle and brake pedals is a known cause of repetitive strain injuries among couriers. Workhorse’s proposals for regeneration were therefore received very positively by delivery companies and fleet managers, for the automation of braking and consequent reduction of health insurance costs as much as for energy efficiency.
The degree of regeneration is directly proportional to speed, and is capped at a maximum level of g-forces during deceleration. Rear-wheel speed is measured, as is wheel slip caused by skidding on icy roads during regeneration-induced deceleration, so at the first sign of slippage the regeneration is automatically deactivated.
“Generally though, the regen is much more aggressive than in most cars, the rationale being that these are professional drivers who will be trained extensively in how to handle the vehicles before operating them,” Willison says. “We dial it back at lower speeds to prevent repeated whiplash for the drivers making rounds in the suburbs, and at higher speeds we limit the current going back to the battery to keep the maximum power between 150 and 200 kW.
“We often find our end-users recouping 40-50 kWh a day from regeneration, so it’s a huge enabler for the kind of ranges they need. It also means we can have a smaller overall battery on board.”
Battery
The battery is designed to scale up modularly, with each pack storing up to 17.5 kWh of usable energy. Up to eight packs can be installed under each vehicle, with Workhorse typically recommending enough energy to power 95% of a route’s distance.
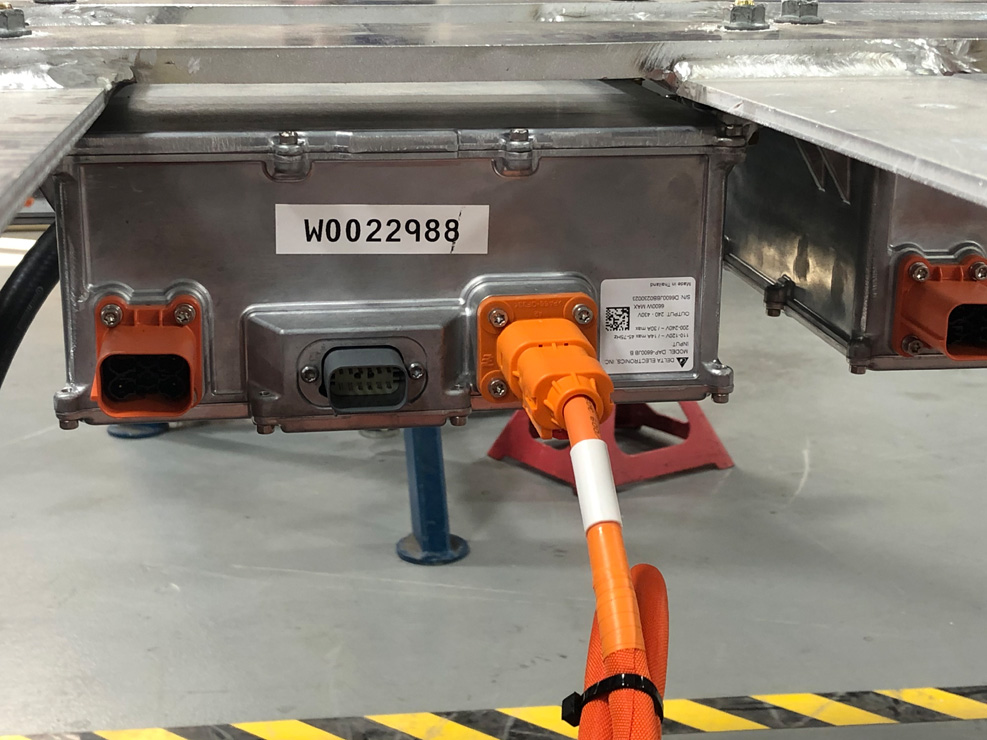
Packs can also be added or removed throughout the year, for example to account for months such as November and December, when more deliveries tend to be carried out and extra power is needed for heating the electric systems.
“There are some limitations there though – more packs and more power drawn can mean more strain on cell balancing, for example. Generally though, this system allows end-users to just buy the number of batteries they need and manage their usage seasonally,” Willison says.
Each is designed around pouch type cells, primarily for the format’s ability to take repeated recharges from regenerative braking without suffering lithium dendrite build-ups to the same extent as prismatic and cylindrical cells.
Willison explains, “We previously used 18650 cylindrical cells, which are robust and can be used for repeated discharging and recharging, but you need to connect quite a few of them in parallel to be able to push all that regeneration. From our studies we’ve found pouch cells to be more adept at accepting large power fluctuations safely without losing significant storage capacity or lifespan.”
He adds that the NMC cells provide the best mix of life, cost, weight, charging speed and availability. The company emphasises that the ratio of manganese to cobalt is a critical part of its proprietary technology, and says many companies are tailoring this ratio to optimise the battery to the vehicle and duty cycle.
“We anticipate the pouch cell becoming an increasingly popular way for EV developers and fleet managers to get to a lower cost-per kWh figure,” Willison says. “Much of that comes from the packaging, simply because the pouch cell’s footprint gives it a greater quantity of active internal battery parts versus its casing, which means reduced casing costs in producing them. Also though, with pouch cells you don’t have to wire-bond each cell, which is a fairly intensive and costly part of battery manufacturing.”
Early versions of the trucks used a rail-based architecture for mounting packs to the underside, which also made it easier to have spaces around each pack to allow more air to flow around the cells and encourage greater heat dissipation. The company’s current pouch-cell packs, however, are designed with common cooling rails on their undersides for easier heat dissipation, making the central rail down the chassis unnecessary.
As a result, the present C-Series vans are now built with skateboard type perimeter frames, with enough open space between the wheels and transmission for installing up to six battery packs.
“From a manufacturing standpoint, the skateboard approach allows us to be somewhat agnostic towards the suppliers and configurations of batteries we might want to use,” Willison notes. “That’s really important if an end-user or a sudden surge in demand is pushing us towards a higher volume or a different form factor of battery pack.”
The arrangement of packs around the C-Series’ undercarriage is dictated largely by cooling needs, as well as by Workhorse’s increasing emphasis on modularity. “Our physical battery cavity allows us to adopt new packs and technologies very rapidly,” Willison says. “Because the vehicle can last twice as long as ‘traditional’ step vans with steel frames and ICEs, the battery cavity can adopt new technology when it becomes available.
“It’s like dropping a new engine into an old car, but this engine has twice the capacity, twice the range and half the cost.”
Battery management
“When we started out as a small EV OEM it wasn’t always easy to get the attention of a Tier 1 supplier, so we worked on our own BMSs and DC-DC converters from effectively blank sheets to build up our competencies and supply chains internally,” Willison says.
The company has continued to develop its own BMS software (although COTS microcontrollers and other hardware are used for running the software), focusing on functions such as battery cell balancing across different charging speeds.
The present system can process charging rates up to 200 kW, although the company notes that no commercial fleet to date has genuinely needed such fast recharging.
With most fleets performing daytime postal services and parking their vehicles overnight, a 70 kWh pack can subsist on a regular Level 2 charge, as Workhorse recommends.
“A lot of customers want to fast-DC charge at 50 kW, which is a good mix between an expensive fast-charge and a slow Level 2. One of the benefits of our lightweight chassis is that you can get 110 miles out of a 70 kWh pack,” Willison says. “If the vehicle was much heavier, we might need a 120-150 kWh pack, which would then make a Level 2 overnight charge unfeasible.
“You would then have to do regular DC fast-charging, which is bad for long-term battery health and costs – and some fast-chargers can cost $15,000-30,000 – so the cost effectiveness of owning our system would be diminished a lot. That’s another reason why we discourage fleets from integrating a bigger battery than they need: it keeps charger hardware costs low.”
In addition to charging and balancing, the Metron system makes use of the stats tracked by the BMS, with metrics such as SoC, cell temperatures, voltages and so on for each of the 5 million miles collectively accumulated by the vans.
“We’ve shared some of that with companies such as Panasonic and some research institutes, to look at things like the effects of different battery cycling and temperatures,” Willison says. “It’s a huge database, which our software has amassed through the CAN network and analysed in order to optimise battery performance and lifetime.
“We also analyse and optimise for different delivery routes, by comparing battery data with GPS and weather data. Broadly speaking we see the same results as everyone else: the less you discharge and recharge a battery, the longer it lasts. But if you can figure out how to cushion the top end voltages and what the extremes are that drivers are limiting themselves to, you can figure out how to get them a significant bit of extra lifespan and value.”
Power electronics
A 7 kW Delta onboard charger is typically installed, although the company can double-stack them to enable 14 kW AC charging, for end users wanting to push the limits of AC recharging.
“The batteries can actually physically handle 300 kW, but as we’ve said, no one really needs that. We offer onboard charging settings at 7, 14, and 22 kW depending on requests,” Willison says.
Previous chargers have had challenges, Willison notes. Other brands evaluated by the company were found to pose particular challenges with thermal management in terms of sufficient heat dissipation, as well as inconsistent application of thermal transfer paste.
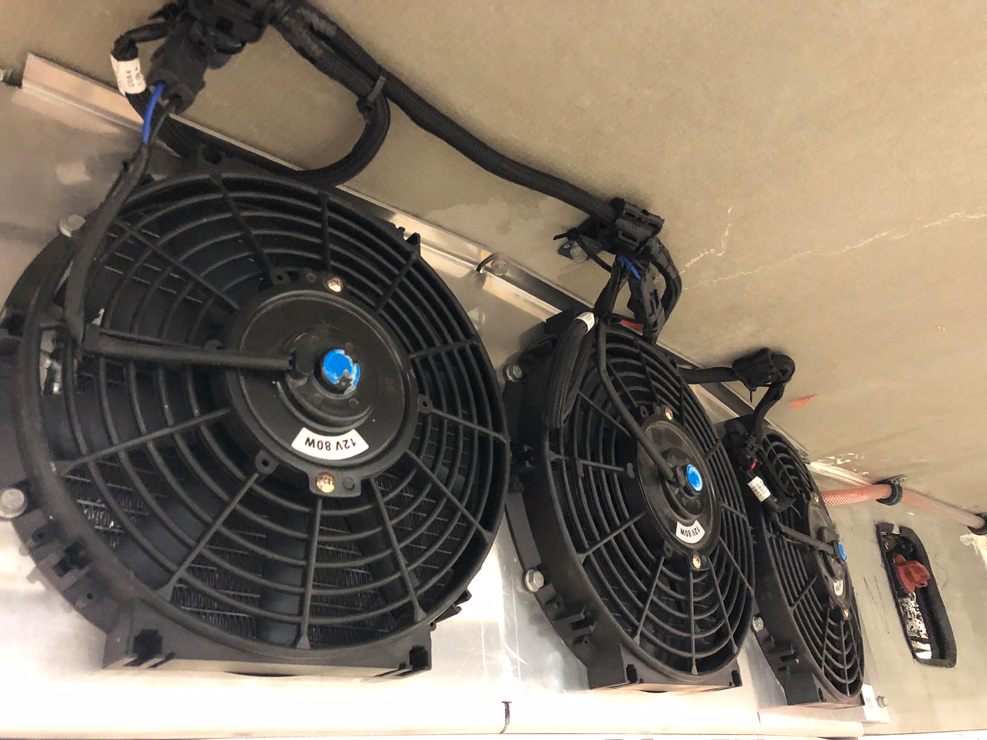
“We do post-mortems with failed components, internally, with the suppliers and with independent testing labs.” Willison adds. “We’ve also tested a lot of COTS power converter systems, which led us to opt for a highly customised, proprietary motor-inverter.
“Although we can’t share any details about that, I can say we’ve never had any failures with the unit. We have put in a lot of work to get the inverters right.”
The main DC-DC converter is a Delta 2.5 kW module, which regulates voltages from the battery’s 420 V down to the 14 V needed for the ancillary systems. The air compressor and some other HV components operate in the 400 V range.
“We would like to step up to 800 V on the main battery, but many peripheral systems made for the automotive sector are in the 400 V range, so until the higher voltage units are available at a reasonable price, we will stick with the 400 V,” Willison says.
Also, a Bell Power DC-DC converter steps down to the 24 V for the Horsefly drone-launching system, as well as the 12 V needed for the cabin systems.
Active cooling loops
Thermal management has long been a major focus of the company, with UPS and similar customers having asked since 2015 about improving their battery cooling systems, particularly as drivers operating on tarmac roads in southern US cities during summer were experiencing discomfort owing to the heat in their cabins.
Aluminium pumps from Meziere are used to push water-glycol coolant around the various cooling circuits on the C-Series, and were chosen mainly for their mechanical ruggedness.
“They have been outstanding – great quality and we have never had a failure,” Willison says. “We even [inadvertently] ran a pump dry for several hours on a test mule, and it operated as per spec as soon as we refilled the glycol loop.”
One circuit runs from the onboard charger to the DC-DC converters, then around the motors’ stator plates before running to a radiator that is fitted with three fans.
The battery is cooled separately, using a combination of Freon and an evaporator (similar to those found on refrigerators) to enable faster thermal balancing and heat extraction than the water-glycol circuit, given that batteries are more prone to sudden or intermittent spikes of heat than the other components.
“The exception is the IGBTs, which can spike quickly, so the coolant is designed for spot-cooling on the power electronics units,” Willison says. “The Meziere pumps are ideal for suddenly raising the volume flow of water-glycol, to rapidly flood and cool the transistors.
“The compressor, which we use for battery cooling as well as air conditioning, is made by Mitsubishi,” he adds. “We’ve used that system in a number of different vehicles, and we have never had a single failure from it in any way.”
Aside from the air and liquid cooling, the BMS monitors cell temperatures and adjusts the current drawn from each pouch as a primary means of maintaining safe levels of heat.
The future
Workhorse is now planning an all-wheel drive C-Series van, which will feature in wheel motors within the front tyres. The company has narrowed down the choice of front motors to three potential suppliers.
“Adding in-wheel motors is a pretty easy integration to perform when you’ve got SLA front suspension, and we have a lot of customers in the north-eastern United States who often have to contend with harsh weather conditions, so an all-wheel drive is highly desirable for them,” Willison explains.
Some key suppliers
ECU: Parker HannafinOnboard chargers: Delta
DC-DC converters: Delta
DC-DC converters: Bell Power
HVAC compressor: Mitsubishi
Condenser and evaporator controls: Denso
Coolant pumps: MeziereTyres: Goodyear
Brakes: ADVICS
HV connectors: Amphenol
Cable harnesses: in-house
Motors: undisclosed
Batteries: undisclosed
ONLINE PARTNERS
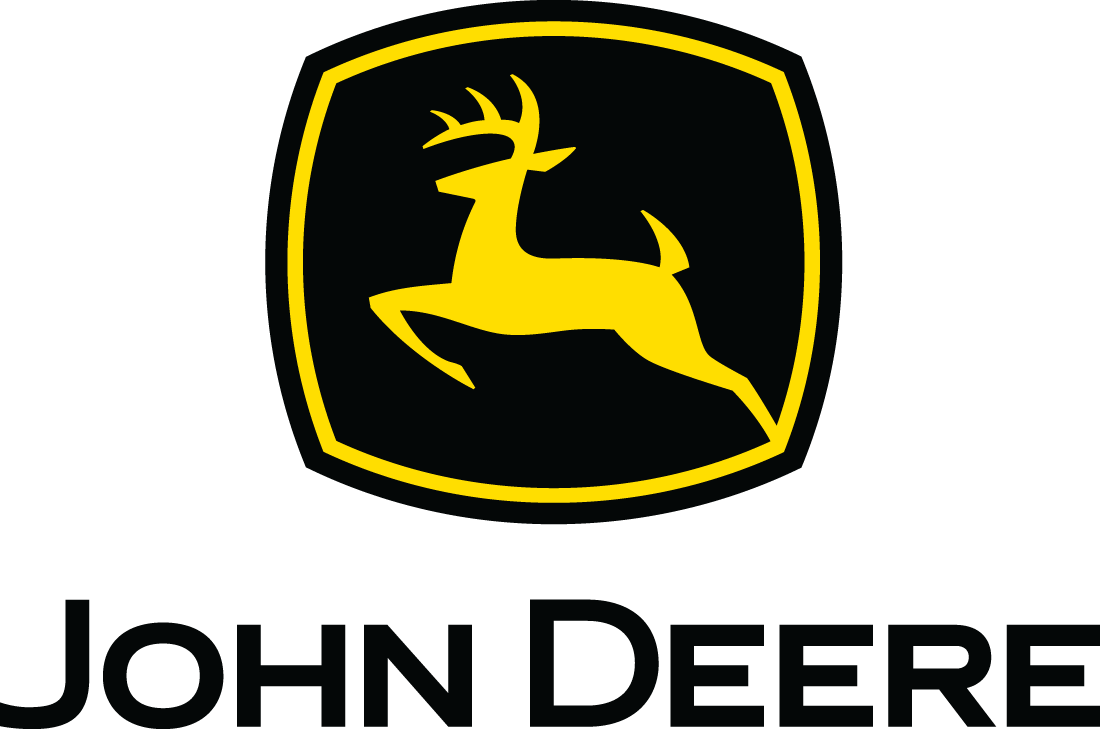
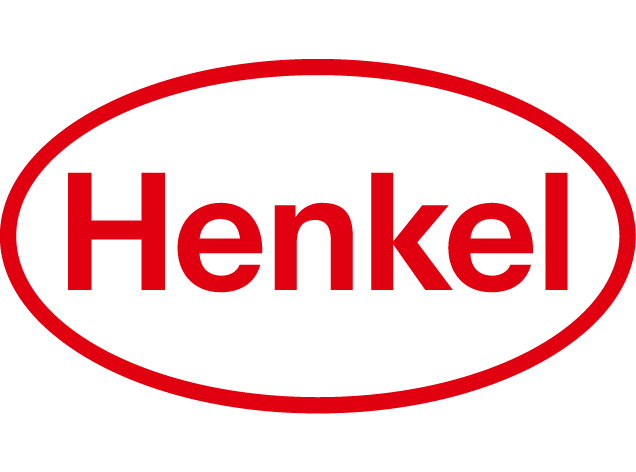
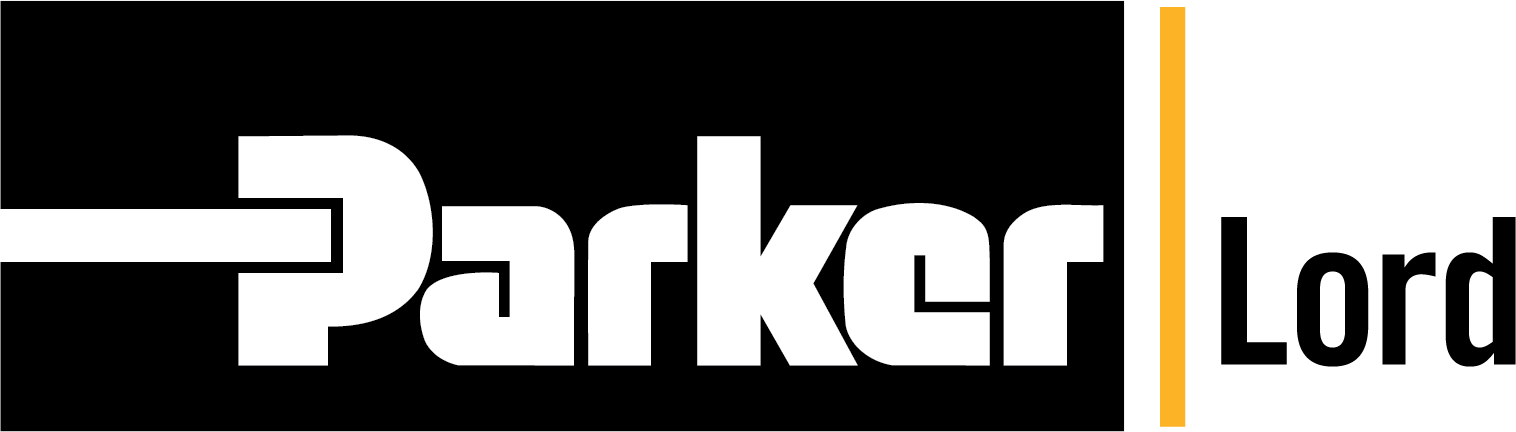
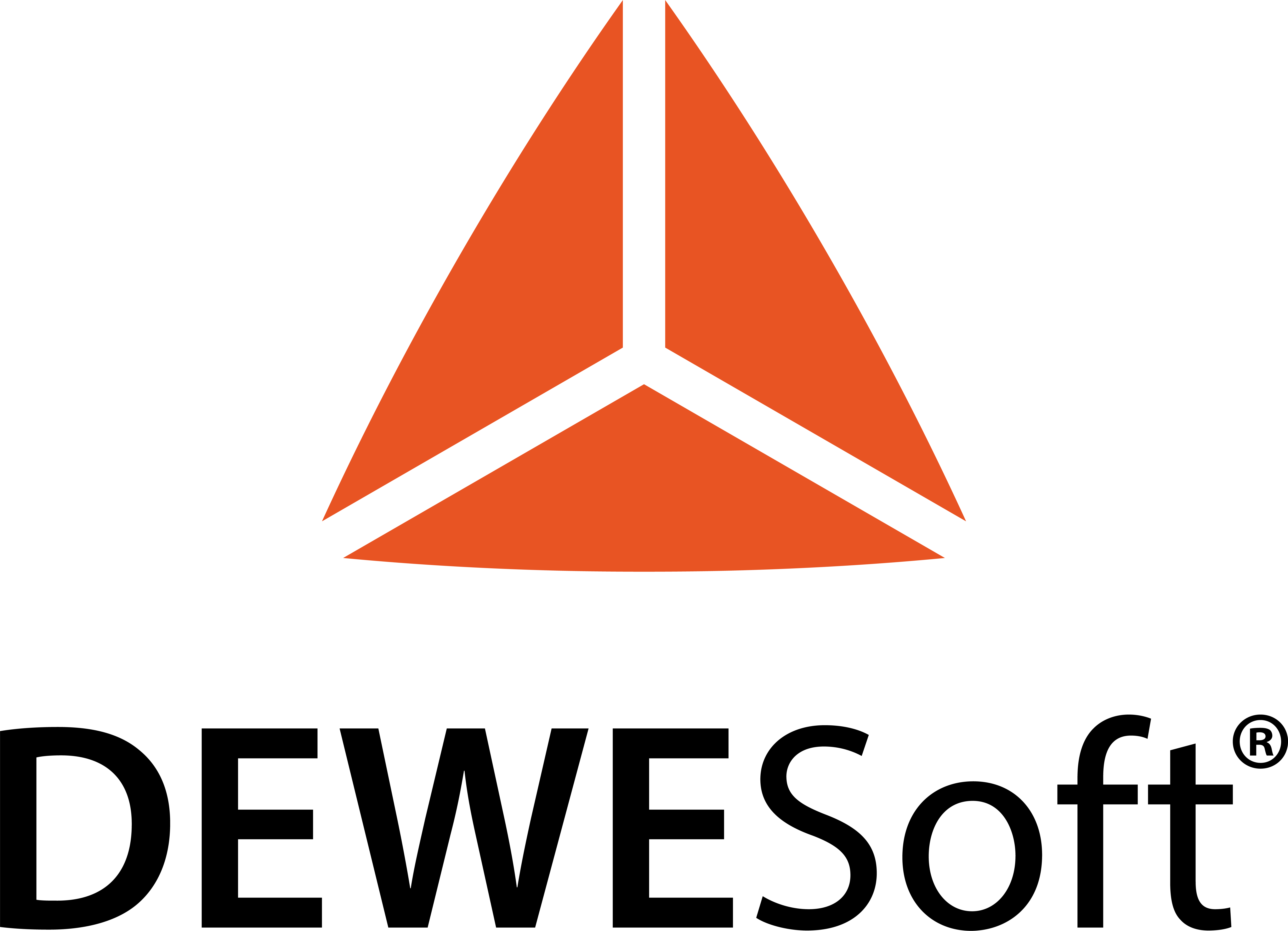
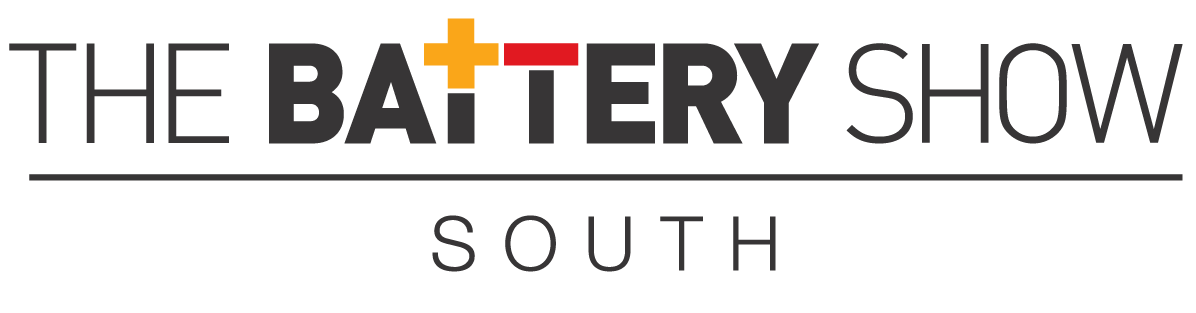
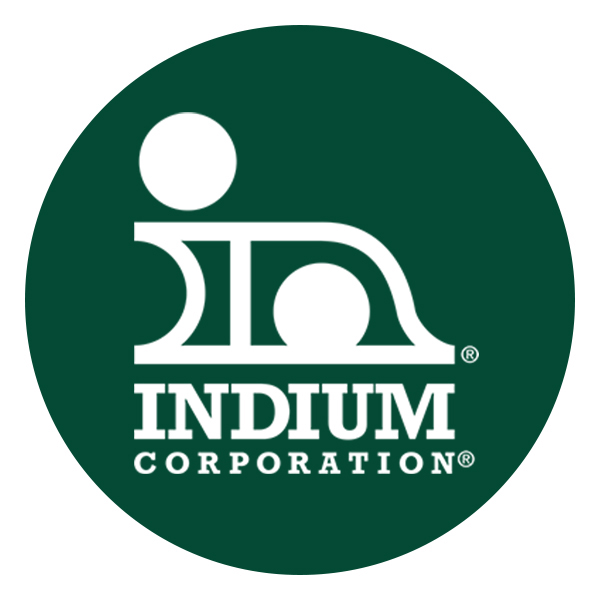

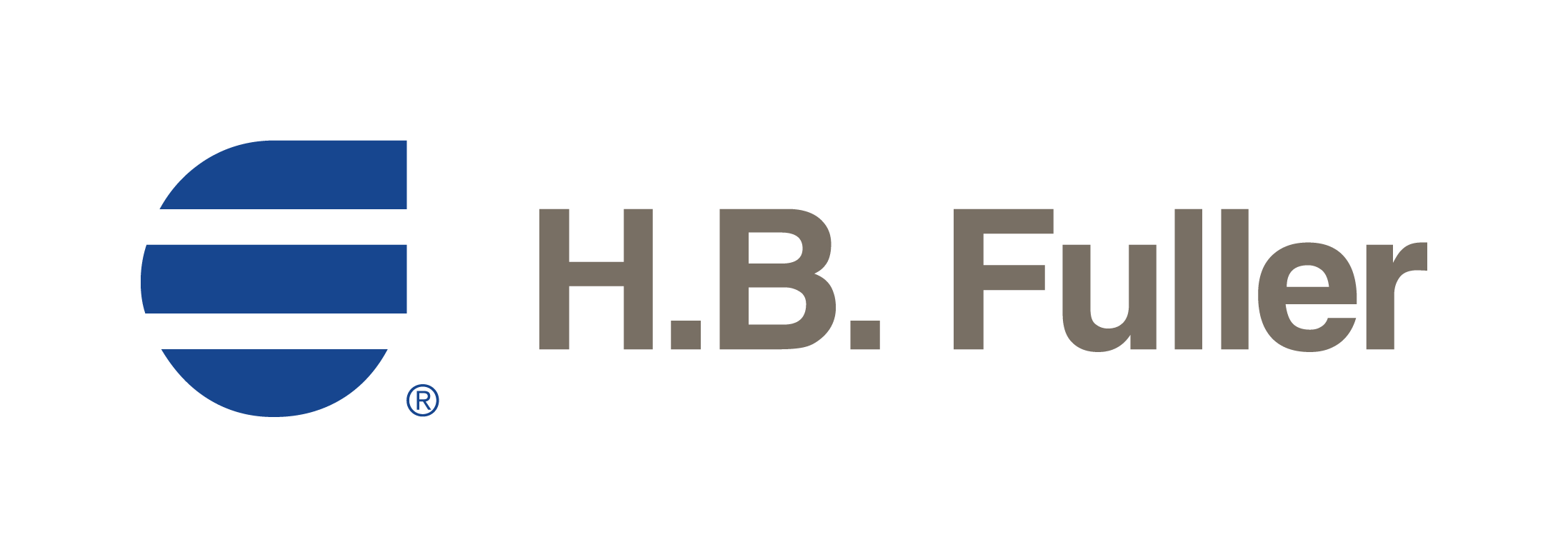
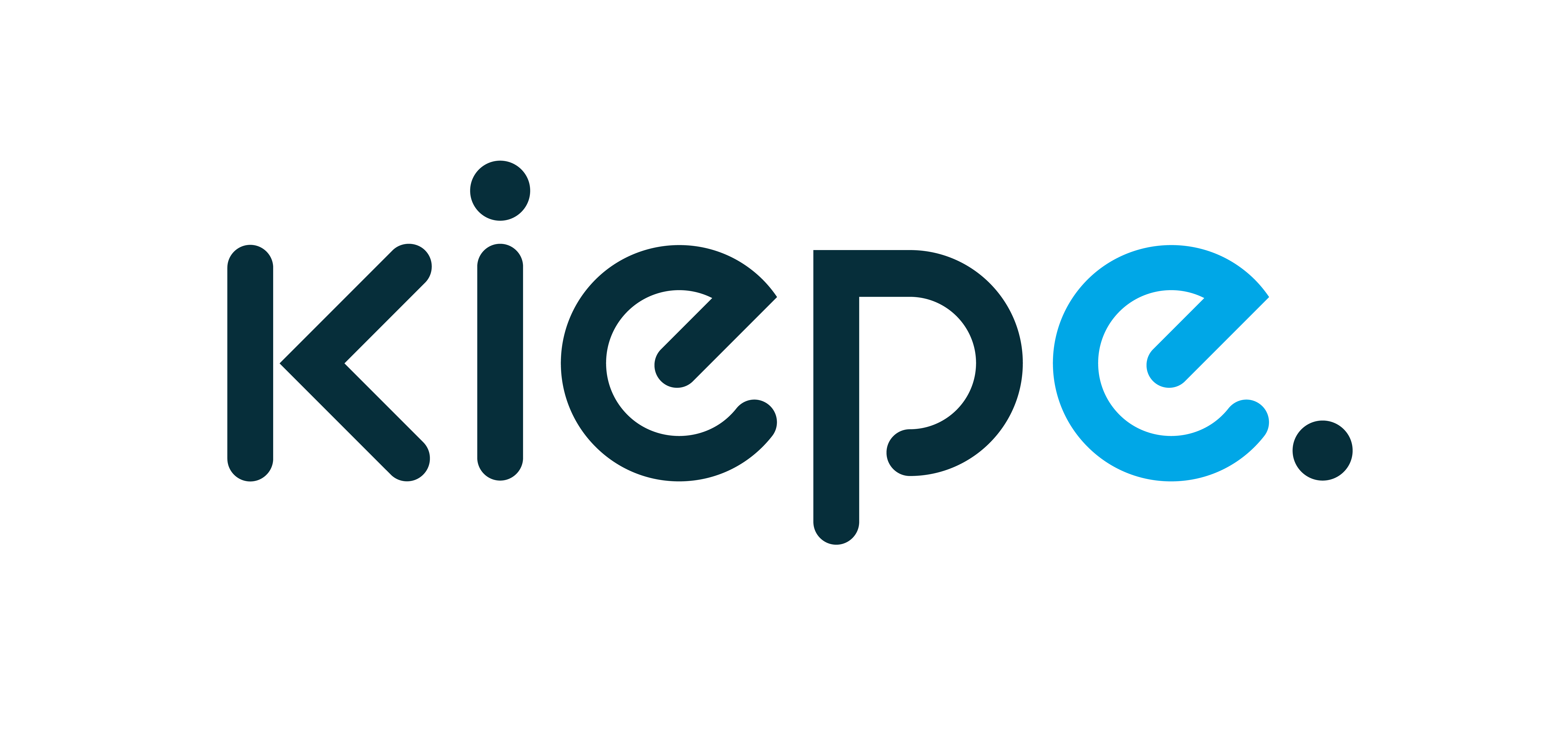
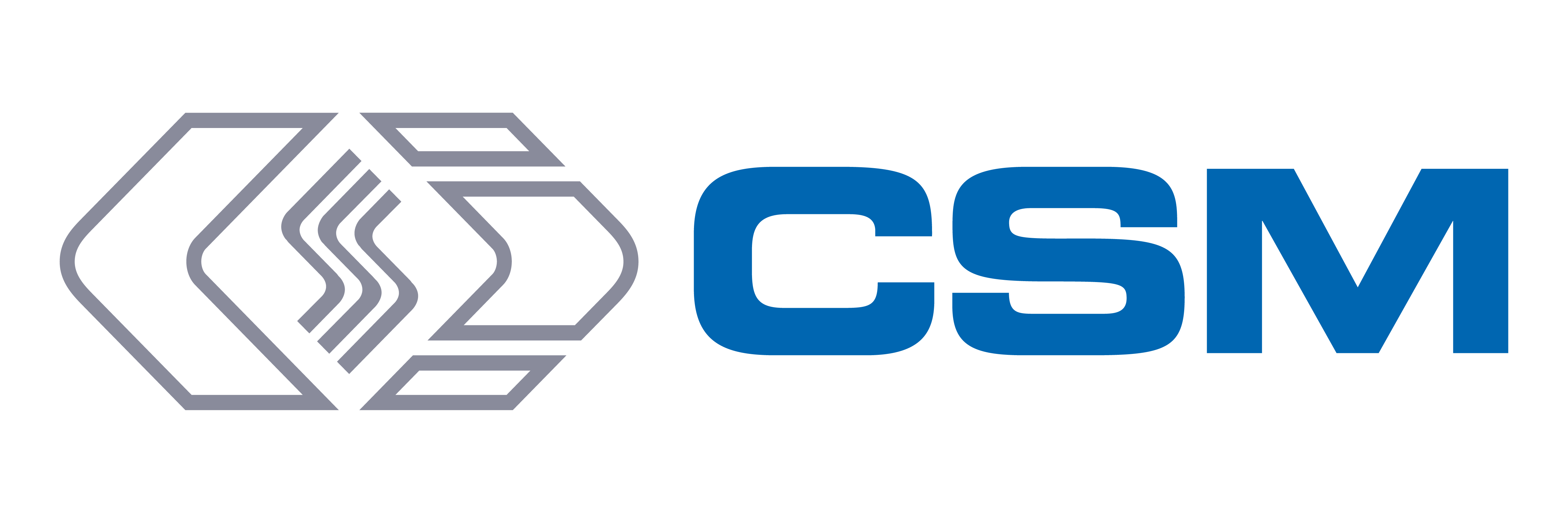