Weight-saving composites for electric buses
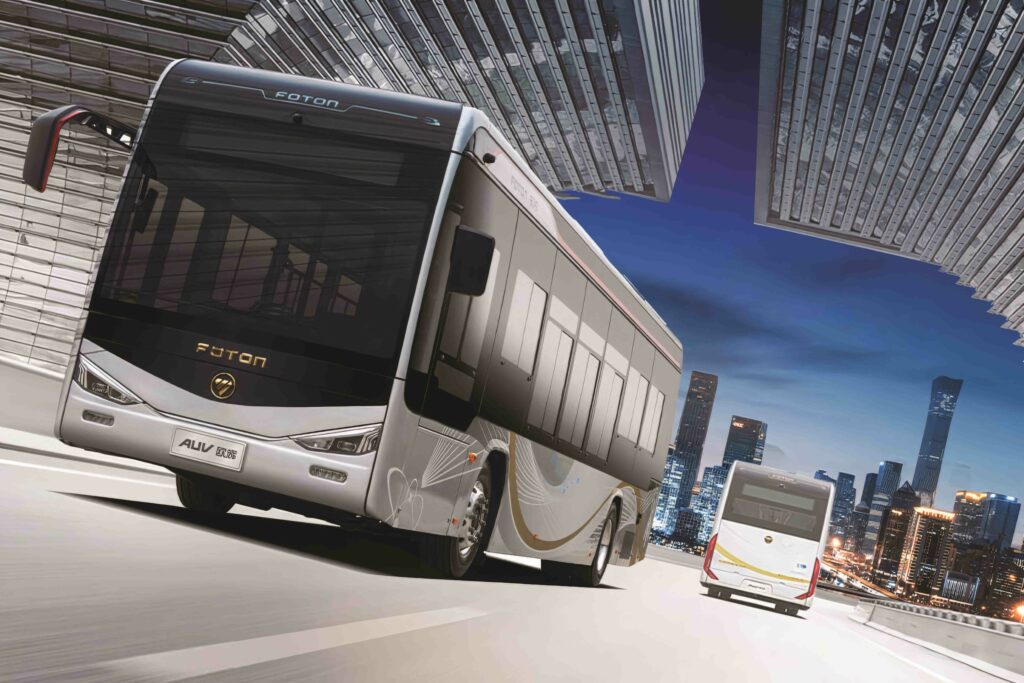
(Image courtesy of Exel Composites)
Exel Composites in Finland has developed a large-scale composite process for electric buses, writes Nick Flaherty.
It has secured a project with Foton Bus and Coach in China to supply glass-fibre composites, which will reduce the maintenance requirements and weight of the vehicles due to their corrosion-resistant and lightweight properties.
The geometric design flexibility of composites enables wider structural engineering possibilities than traditional metals, such as steel and aluminium.
Exel Composites will produce a series of structural, composite profiles for many different bus models, including fibre-reinforced plastic (FRP) side panels, skirt panels and fake roofs.
Pultrusion technology allows the continuous production of FRP structural shapes in an automated process by pulling fibre glass through a resin bath or resin impregnator. The resin hardens from the heated steel pultrusion die, resulting in a strong, lightweight product that follows the shape of the die. This process offers greater tensile strength and durability, while reducing density by 30% compared with traditional aluminium profiles.
The weight savings provided by fibre glass, compared with aluminium, reduces the strain on the chassis and the battery. The composite panels do not rust and can last for decades.
ONLINE PARTNERS
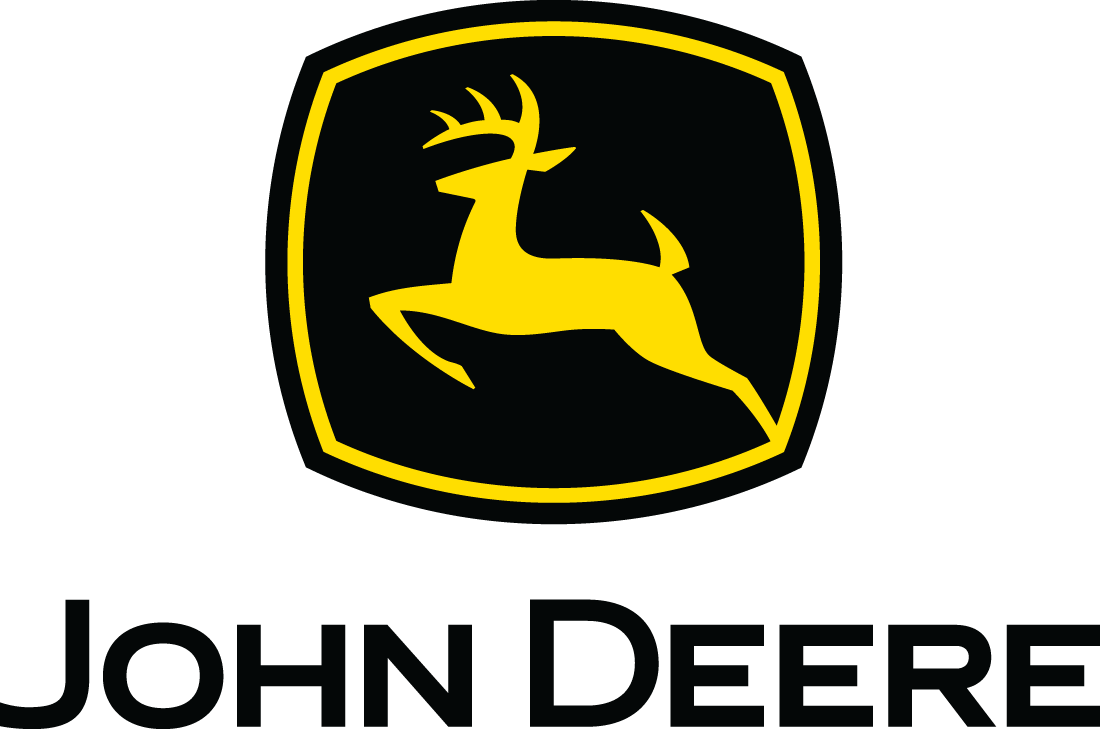
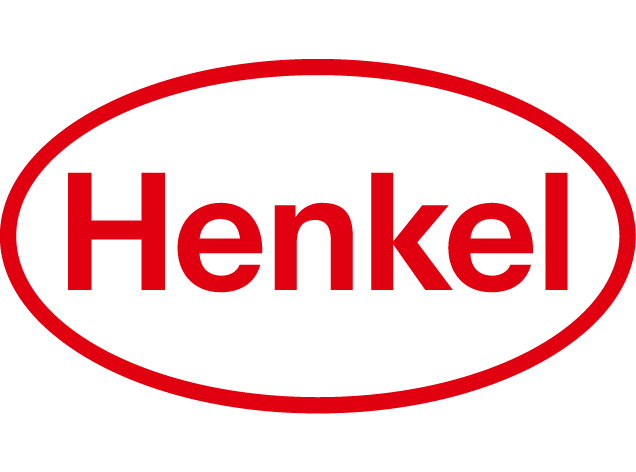
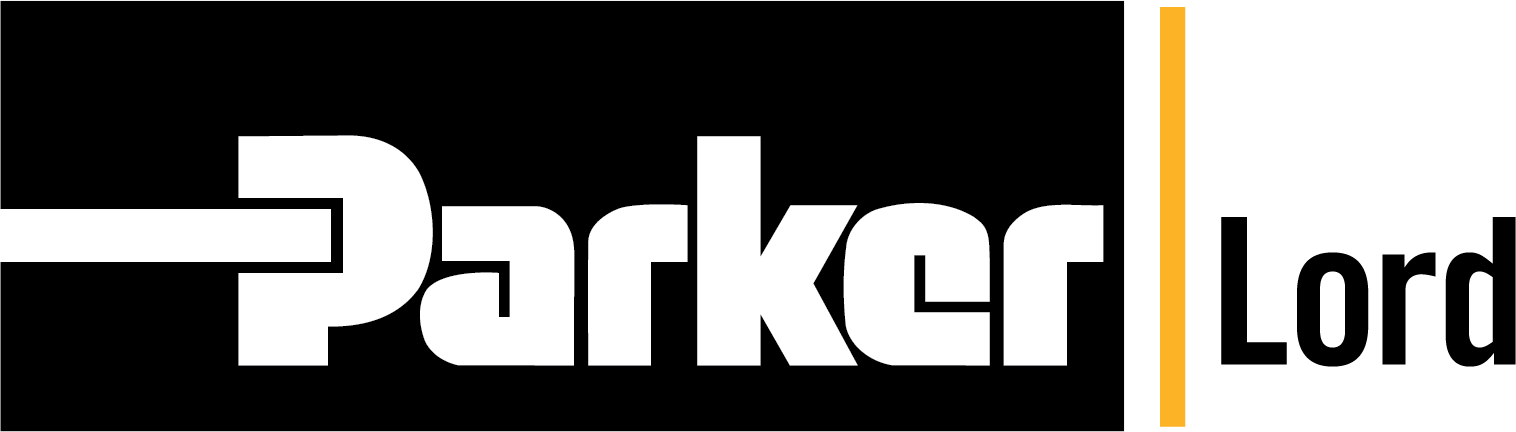
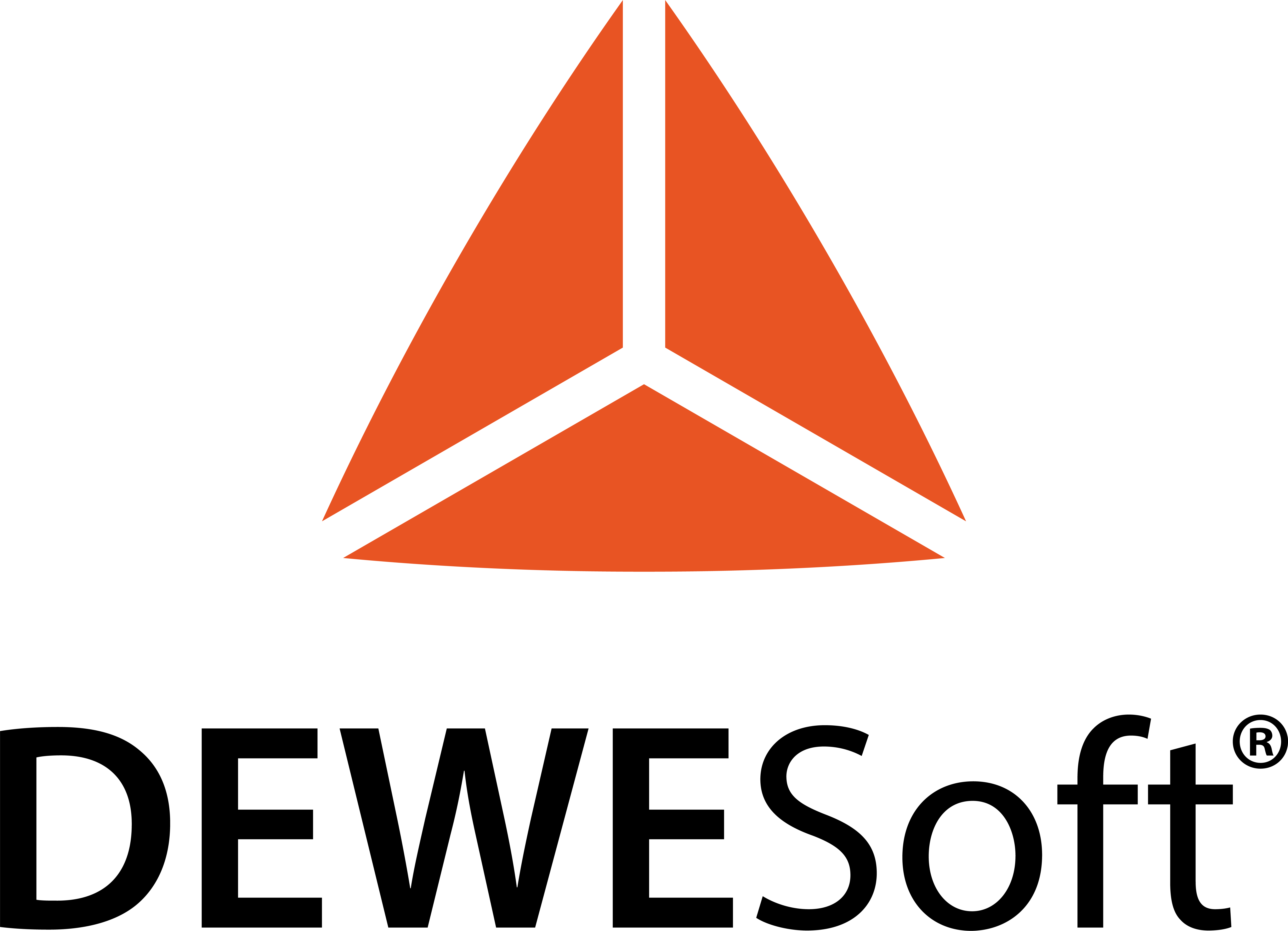
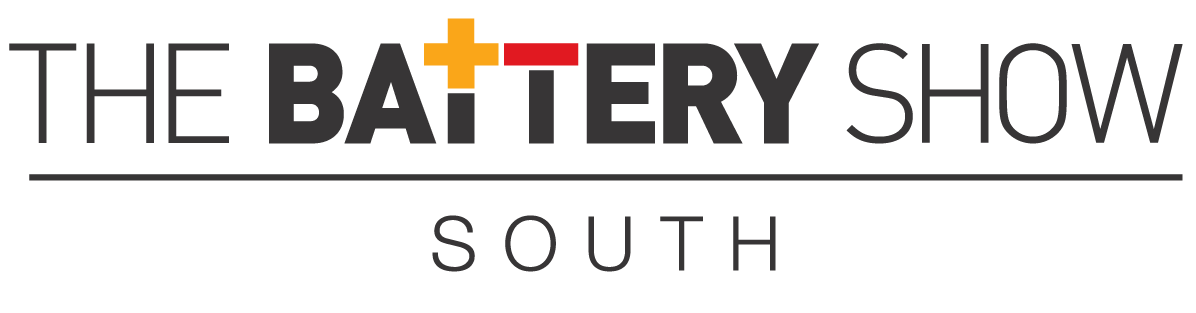
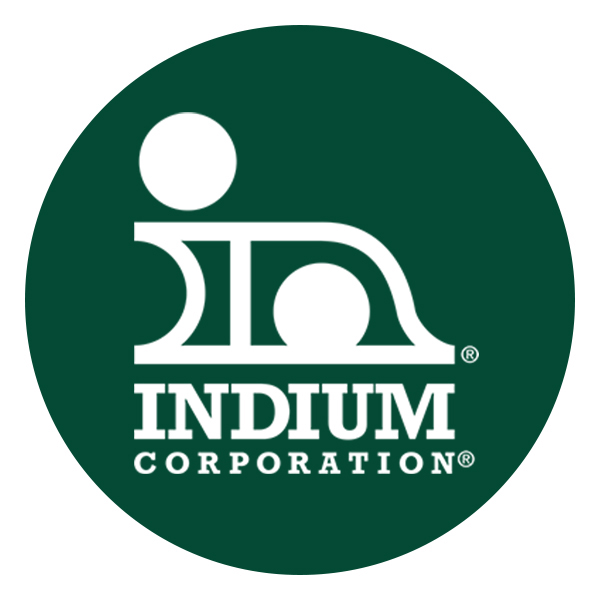

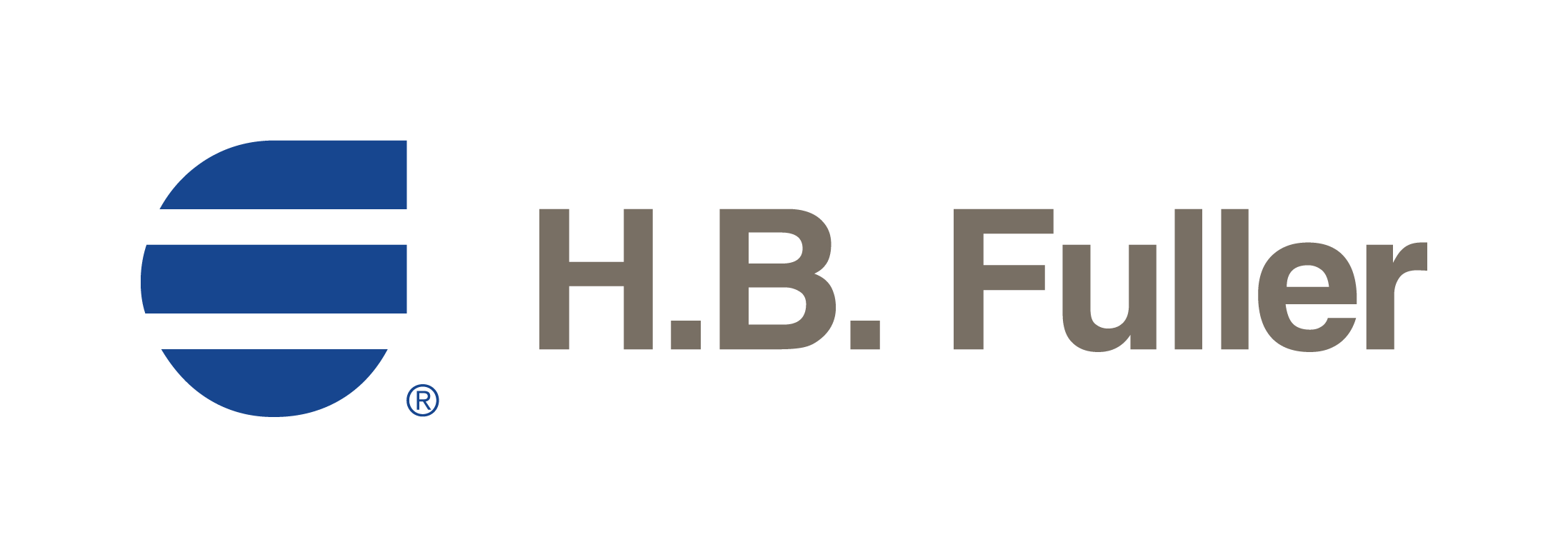
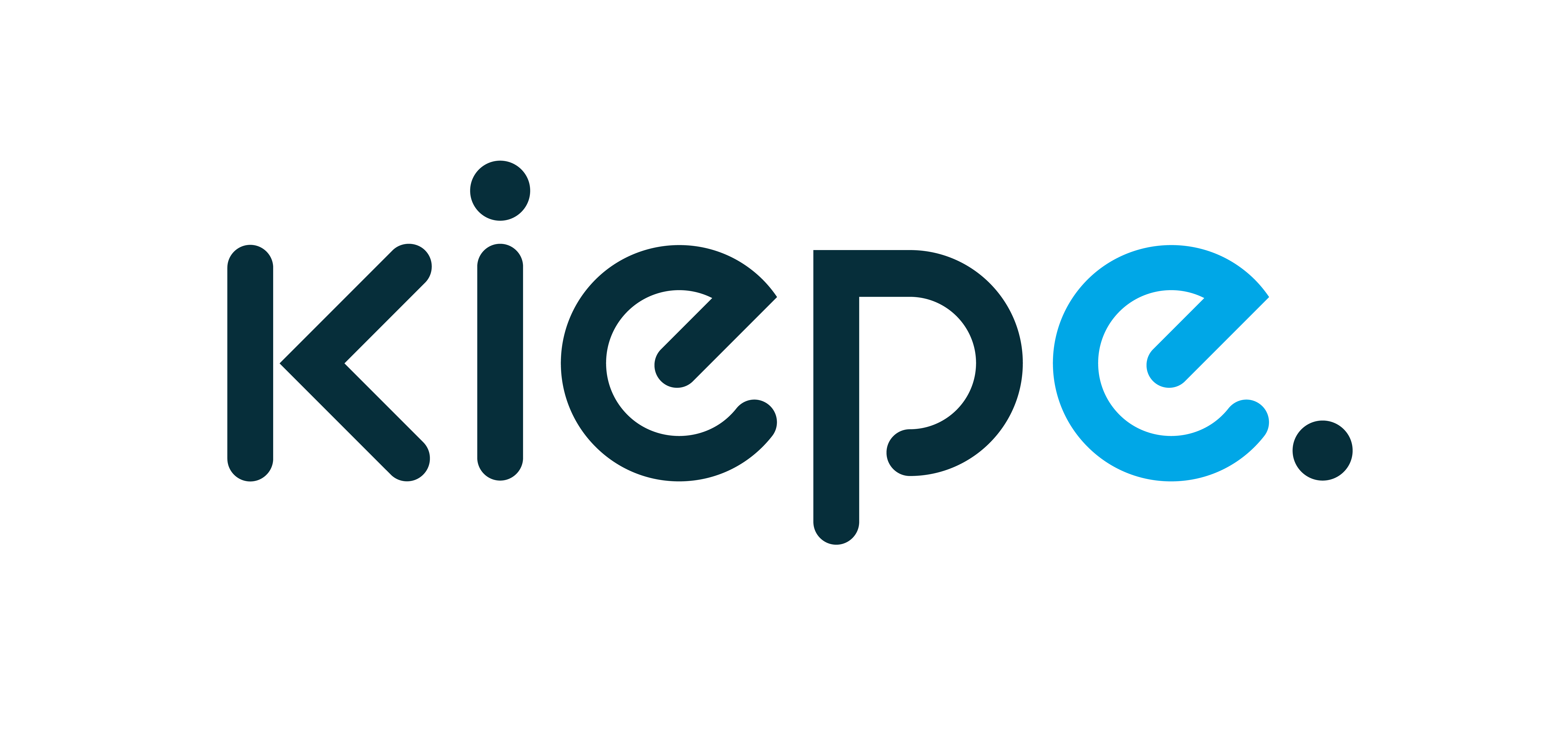
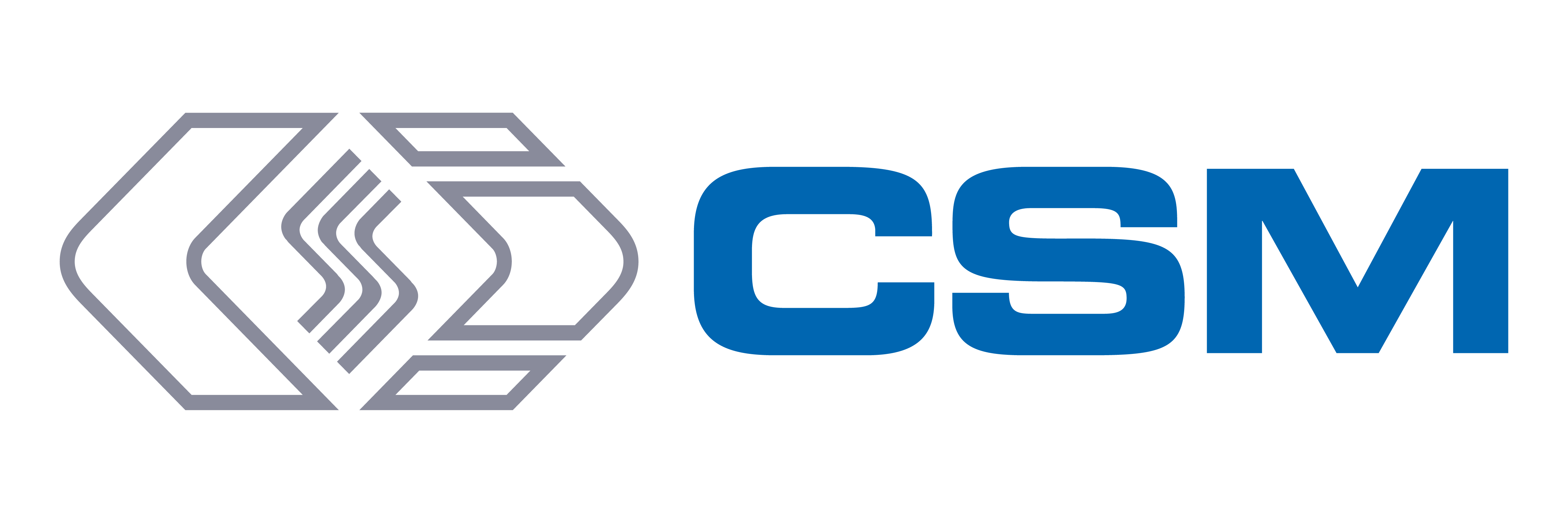