WAVE hello to wireless charging for commercial EVs
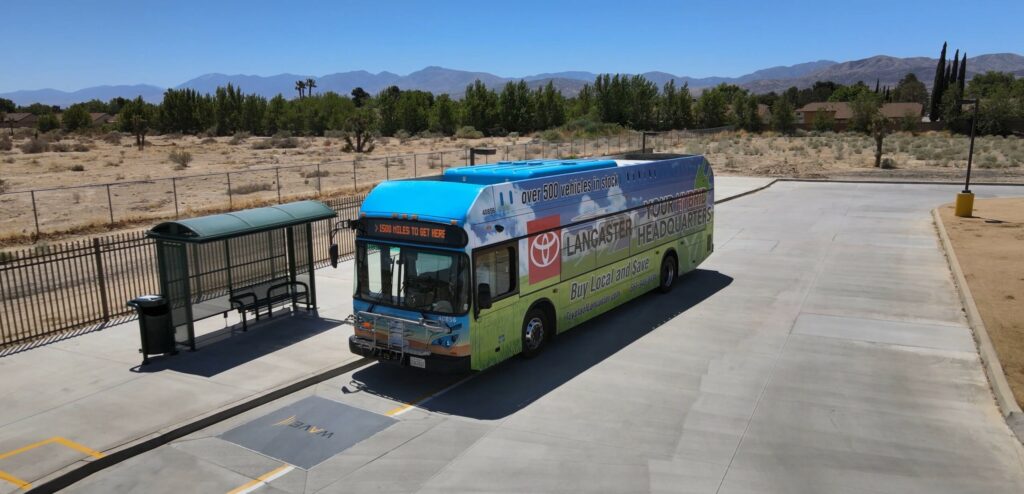
(Images courtesy of WAVE)
Aaron Gillmore, the CEO at wireless inductive charging system developer WAVE, believes that the market has reached a take-off point in commercial medium- and heavy-duty commercial EV fleets (writes Peter Donaldson).
“The technology is here now,” he says. “Over the last 10 years the WAVE team has put in a lot of work to design high-power, wireless inductive charging that is highly efficient and reliable.
“Circumstances are finally converging for the market to take off, including incentives, regulatory pressure and vehicle availability.
“Most WAVE charger deployments have been in the EV bus market, because circumstances converged there first, but now the truck market, which is orders of magnitude larger, is starting to come together. There are also other medium- and heavy-duty EVs where we see interest, such as top handlers in ports, amusement park trams and electric trains.”
WAVE currently offers wireless charging systems with 125, 250, and 500 kW power ratings, enabling rapid charging of high-capacity batteries. The main engineering challenges have centred on developing a product that was at least as efficient as conductive (plug-in) charging.
“The larger the system is dimensionally, the more room you have to control the field and the more tolerance there is for coil alignment,” Gillmore explains.
“The added weight of the wireless equipment is more than offset by the smaller battery pack size that results when fast, automated, high-power charging is strategically placed along vehicle routes, maintaining a high state of charge throughout the day. Wireless provides an iterative route and operational design optimisation opportunity to really save time and costs to EV fleet customers.”
The main development challenge now is to make the systems smaller, lighter and easier to manufacture at scale so that the technology can expand into more markets, he adds.
In terms of componentry, the vehicle-side hardware consists of a secondary receiving pad, a rectifier to covert high-frequency AC to DC, and the user interface. The components on the infrastructure side include the primary power supply cabinet with its cooling unit, the primary power electronics cabinet and the primary charging pad.
The secondary charging pad is mounted underneath the vehicle, and the current induced in it by the magnetic field from the primary pad is run through a rectifier to produce DC within a BMS-controlled acceptable range for the batteries, Gillmore explains. The vehicle and infrastructure sides of the system communicate over wi-fi to coordinate the charging process.
WAVE currently has more than 100 charger systems deployed, Gillmore says, most of which are 250 kW installations in transit applications, with truck installations now being rolled out. The first of these are 125 kW systems in Class 8 yard trucks at the West Basin Container Terminal in the Port of Los Angeles (POLA), while a 500 kW system has been demonstrated on a Cummins Class 8 day cab tractor with a Kenworth chassis.
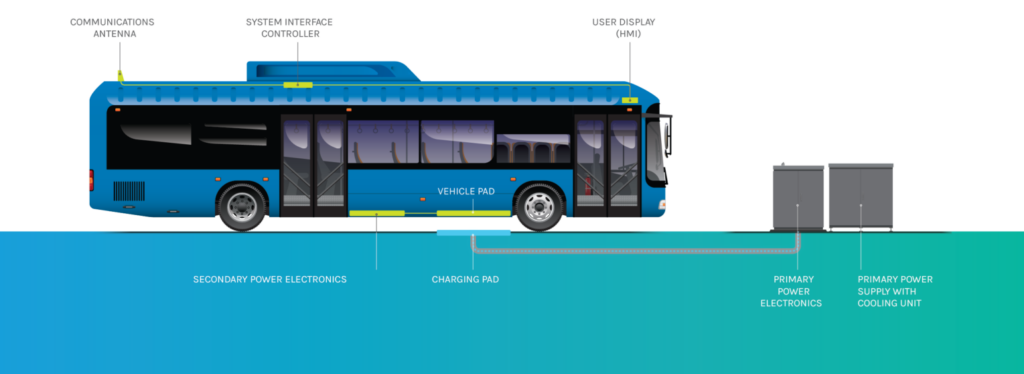
The latter is to go into drayage service (regional cargo transport around a port) with Total Transportation Services in the POLA soon, where it will run on a duty cycle of more than 20 hours a day. The 250 and a 380 kW systems for electric top handlers are also due to begin operations at the port in the coming months.
“We will continue to progress the r&d with our partners for a 1 MW system that is expected to go into regional service between Seattle and Portland for UPS near the end of this year,” Gillmore adds.
Buses deployed with WAVE systems currently have plug-in charging ports in addition to their wireless chargers so that they can be plugged in overnight, which is a mentality that Gillmore would like to change.
“You can use wireless for depot charging too, while deploying far fewer chargers,” he says. “There are opportunities when buses come back to the depot for washing, inspection or service to have a wireless charging ‘fast lane’, and they could get enough charge in 30-40 minutes to go into their duty cycle the next day.
“They could run a more perpetual duty cycle if chargers were placed where vehicles typically stop in numbers throughout a day. This could result in fewer chargers used at a higher rate than 1:1 in a depot, while spreading the load on the grid in space and time.
“That will lower the time to build the infrastructure, lower the capital expense, and lower the operating expense compared to 1:1 plug-in depot charging alternatives.”
ONLINE PARTNERS
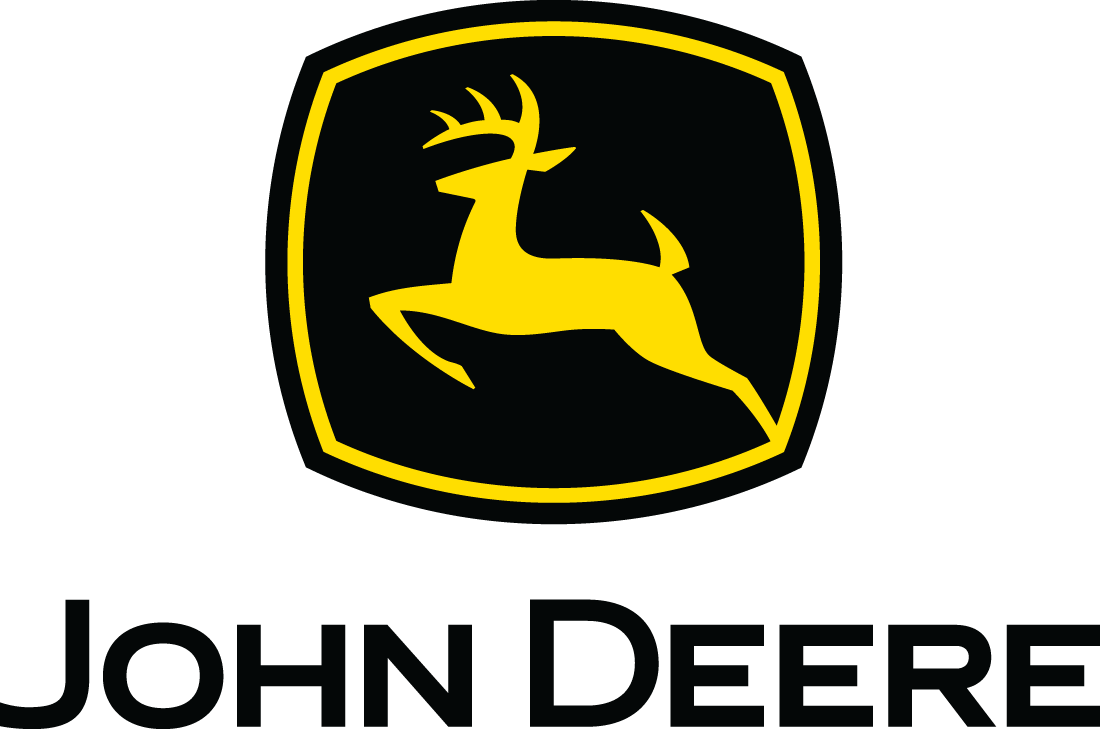
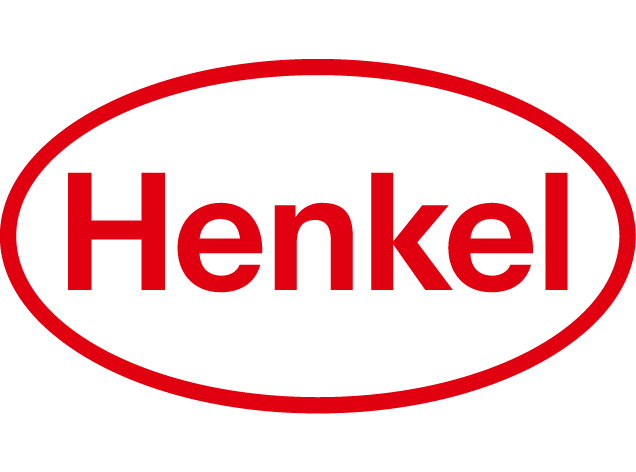
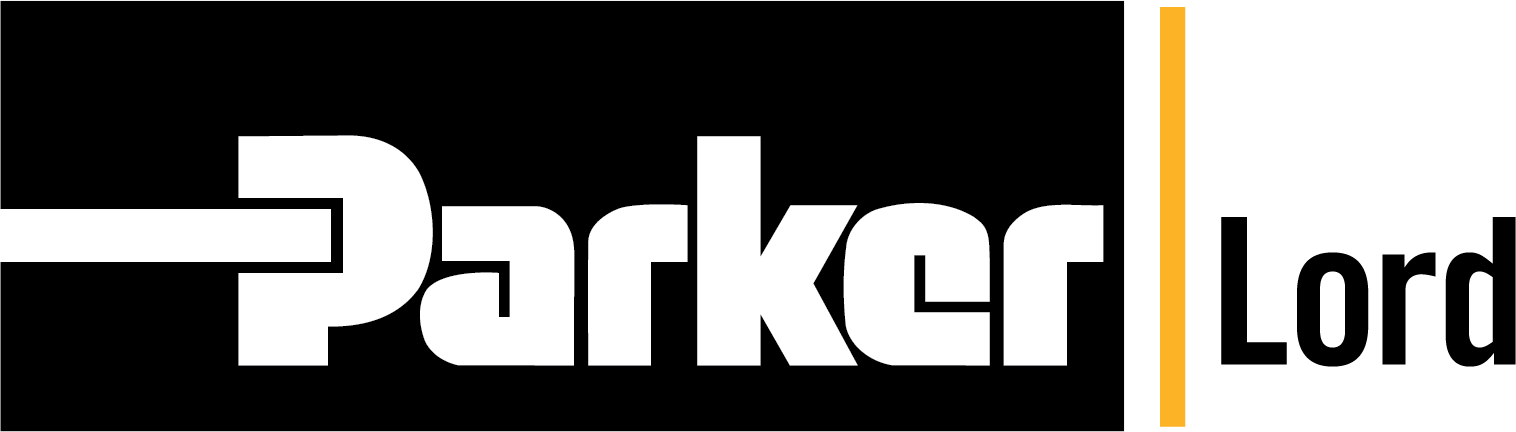
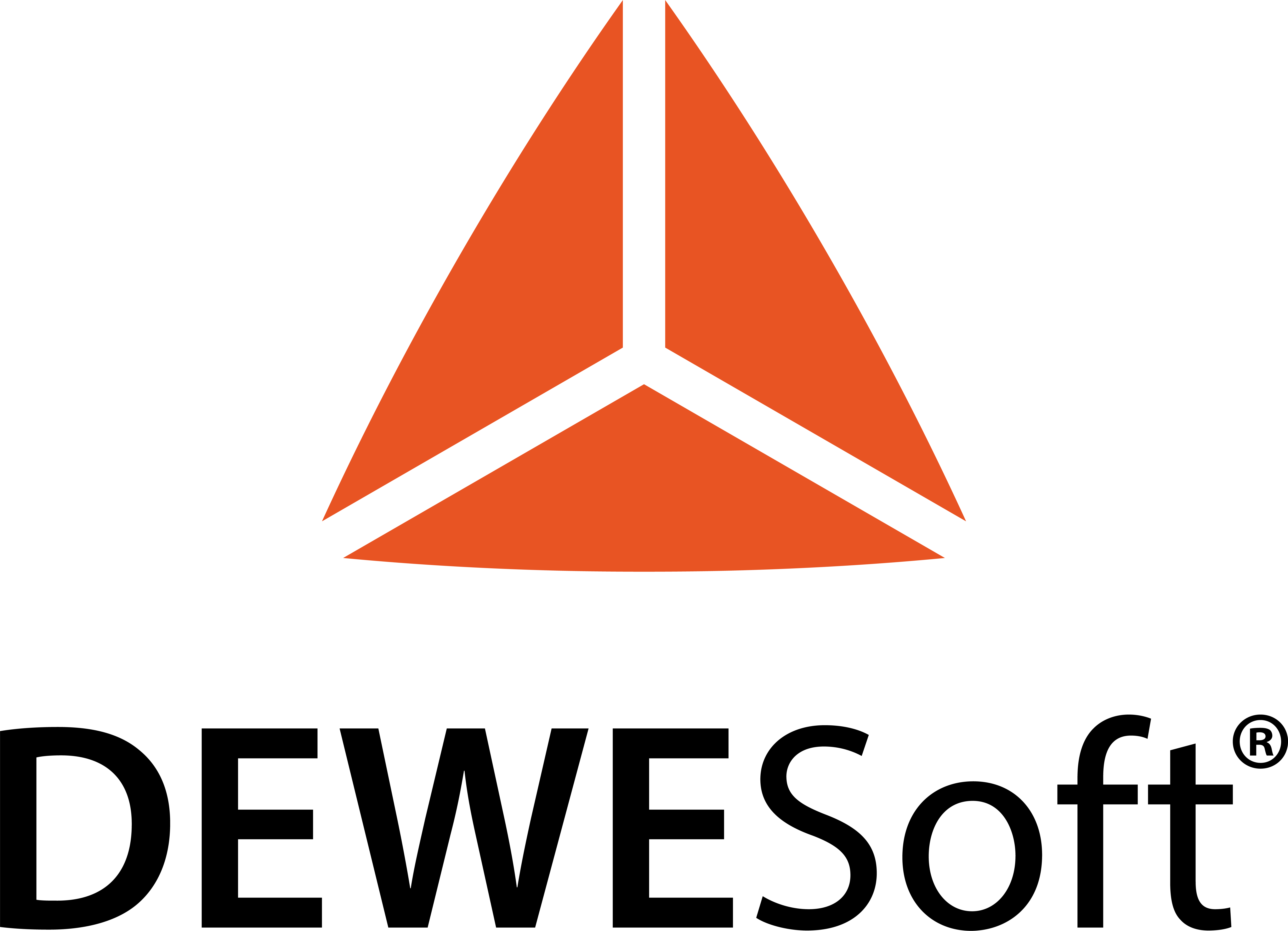
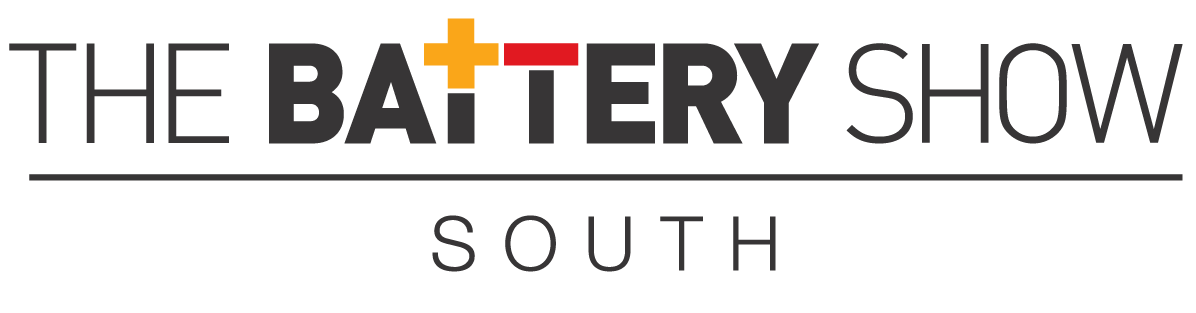
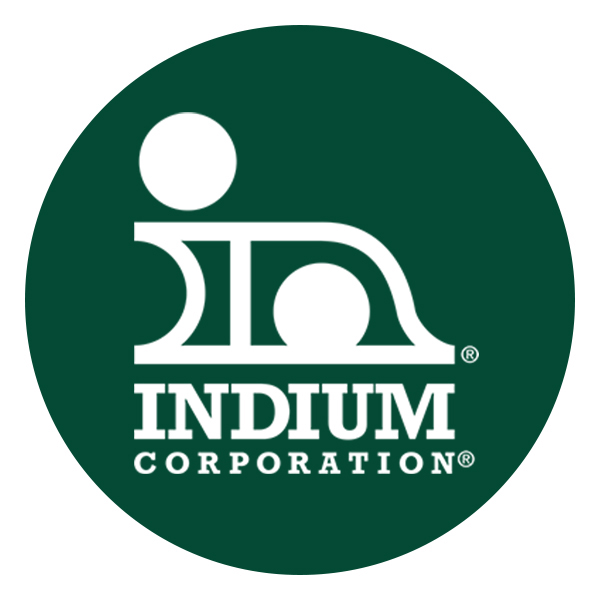

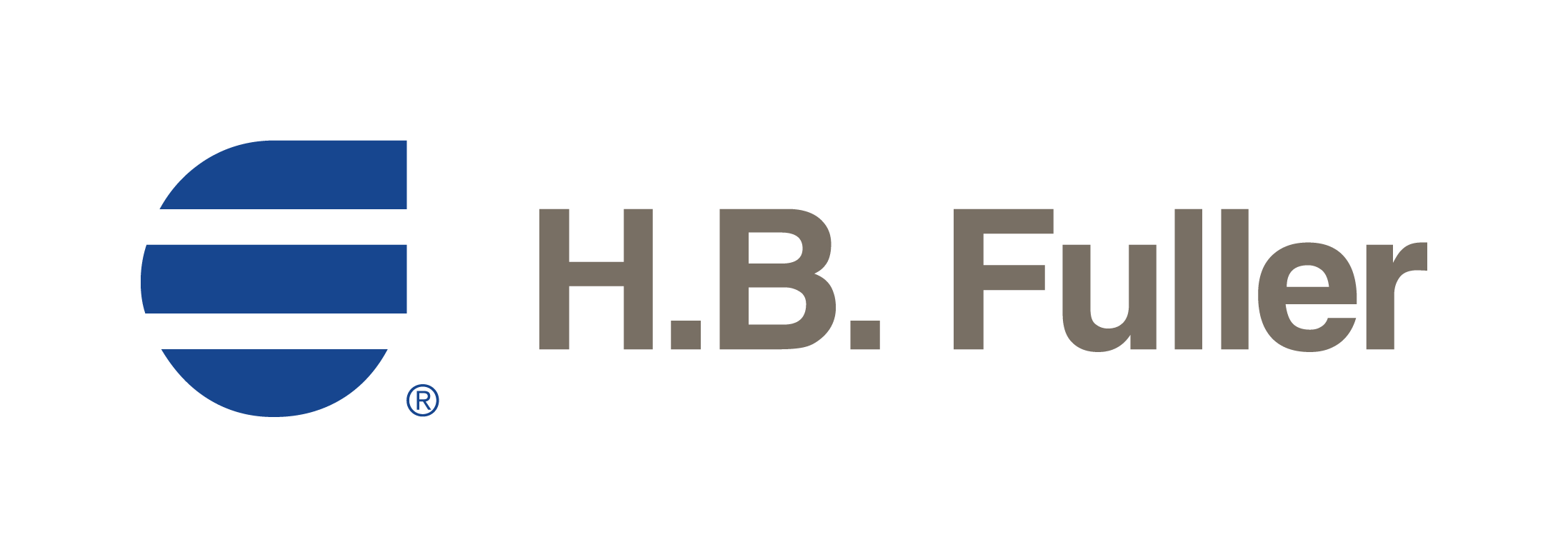
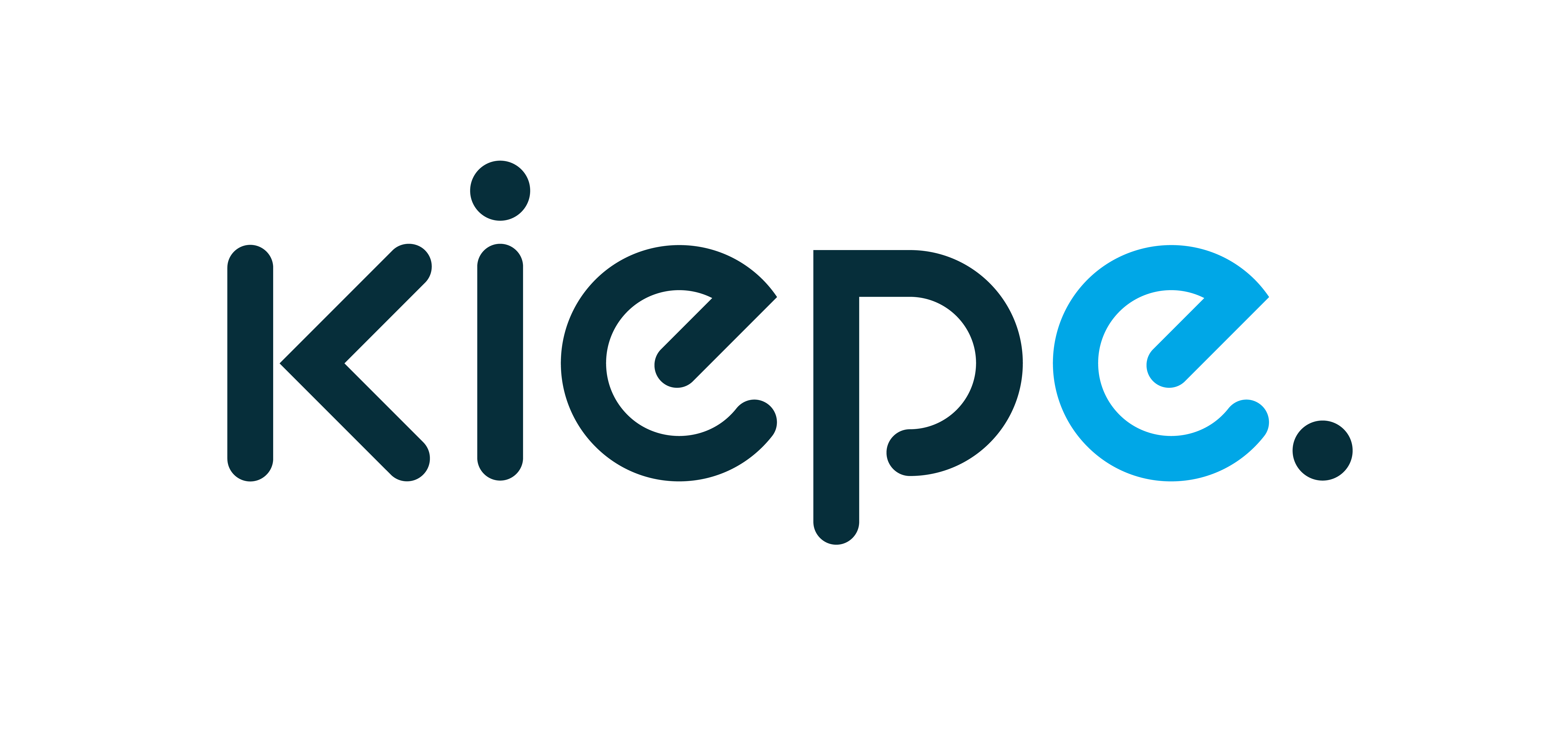
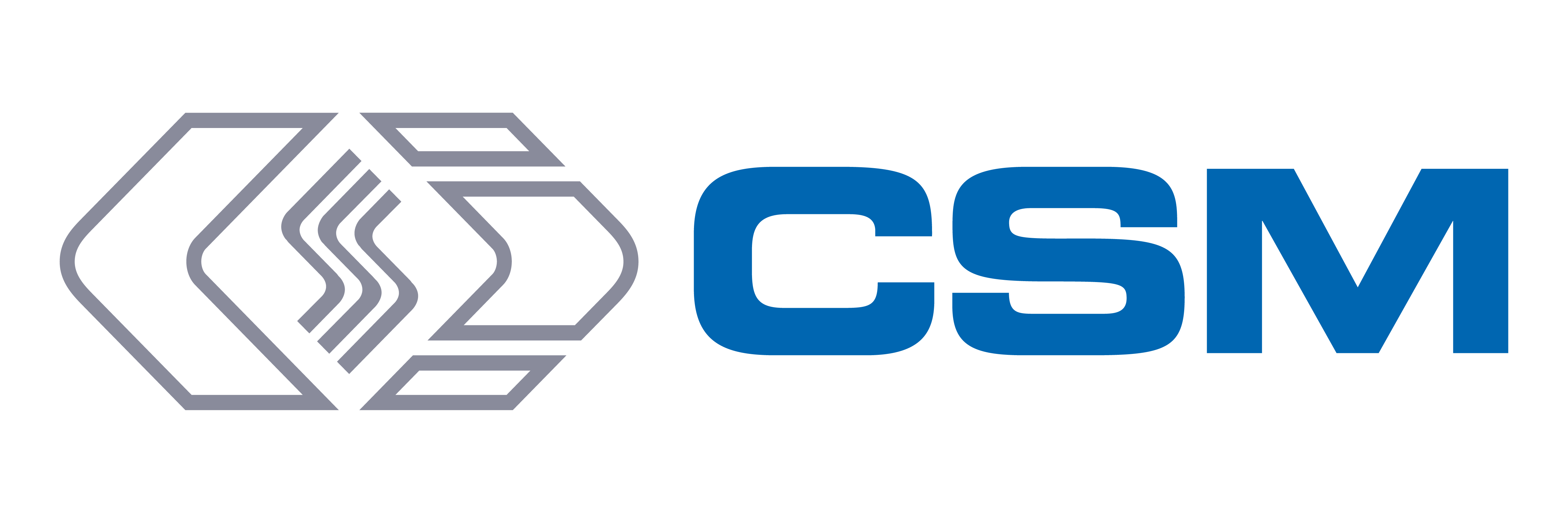