Rising demand for mechanical insulation stripping of busbars
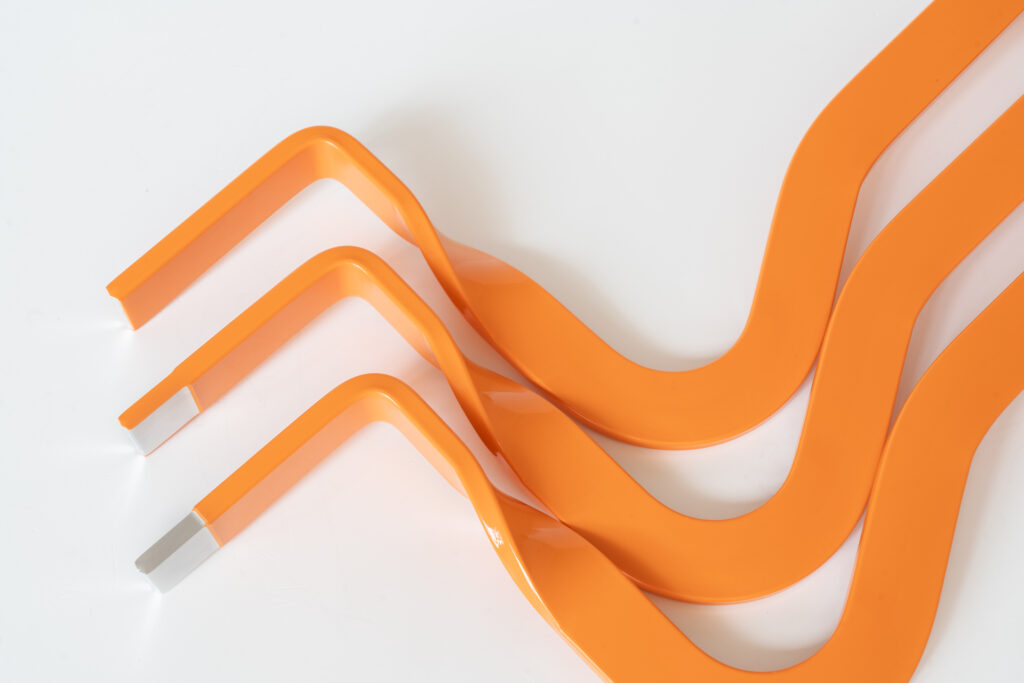
(Image courtesy of WAFIOS)
Busbars can be found in a wide range of electric vehicles, from small passenger cars to large trucks. Different requirements, dimensions and geometries have to be considered in the manufacturing process of these vehicles. Busbar machines from WAFIOS cover a broad product range. One process step is insulation stripping which can be completed mechanically or with lasers. Mechanical insulation stripping is the right choice for manufacturers seeking rapid cycle times and cost-effective production.
WAFIOS busbar machines can be adapted to the individual requirements of a production process, whether short or long busbars, complex busbars and busbars with or without twisting shall be produced. The BMF series is particularly suited for the production of more compact busbars, such as those installed in vehicles that offer little space. Just like conventional bent parts, the busbars are manufactured in a 3D bending process. The patented WAFIOS tool technology makes very tight radii with a thin profile possible. In addition, the alignment of the busbar ends can be modified in a flexible way by twisting. At the same time, the patented rotary roller infeed unit, which is used in virtually all WAFIOS wire bending machines, offers maximum production speed. During production, only the lighter component is rotated, and not the bending head itself.
Are you looking for a busbar machine that can handle extra-long busbars with a large conductor cross-section? The TWISTER² 25 and TWISTER² 35 are the answer. Originally intended for the tube-bending sector, the TWISTER² has been adapted for e-mobility. The result is a machine that can process busbar cross- sections of 300 mm² and lengths of up to 3,000 mm. The tools use the rotary-draw bending method from the tube-bending sector. They are very gentle on the material and prevent surface deformation, for example. At the same time, there is a sufficient bending moment available to bend busbars of up to 300 mm² over the long as well as the short profile side.
Automation solutions for individual busbars and optimal production processes
For the busbar bending machines, WAFIOS offers end-to-end automation solutions for additional or subsequent operations. These include punching various geometries, ultrasonic welding, feeding in and mounting stator connector parts, labelling the busbars and discharging onto workpiece carriers or transport belts in the correct position. This enables manufacturers to increase their productivity, improve quality and reduce the cost per piece.
“With automation solutions like EasyRobot, handling busbars is no problem. The operation of the robot is fully integrated into the bending machine,” says Jörg Eisele of the WAFIOS Executive Board.
Mechanical vs. laser insulation stripping
Insulation stripping is an important step when processing busbars. Following insulation stripping, the surface must be free from any residue of the PA 12 material.
Mechanical insulation stripping ensures that any trace of the insulating material is removed without leaving any residue behind. For this purpose, a small amount of the core material is also removed. By contrast, physical reasons mean that the CO2 laser always leaves behind a layer in the micrometer range. This layer then needs to be removed with brushes to minimize the volume resistance.
Due to the high level of price pressure in the market, demand for mechanical insulation stripping has continued to rise.
“Mechanical insulation stripping is a cost-effective alternative to the CO2 laser. It helps to reduce the cycle times involved in insulation stripping by 40 percent or more, which means a higher output rate from the entire machine system,” says Eisele.
Fully integrated and highly flexible
The insulation stripping system in the BMF 60 and BMF 90 busbar machines offers maximum flexibility, with seven axes and two milling units. The material is first stripped on the top and bottom, then it is rotated by 90 degrees and the side surfaces are machined. The CNC insulation stripping device allows any kind of combination to be produced at the busbar end, depending on the connection situation of the busbar. These include having just one side stripped, the top and bottom stripped or all four sides stripped.
The insulation stripping device is integrated into the machine between the infeed and cutting unit. It is fully adjusted using the simple and intuitive WAFIOS Programming System WPS 3.2 EasyWay.
Click here to read the latest issue of E-Mobility Engineering.
ONLINE PARTNERS
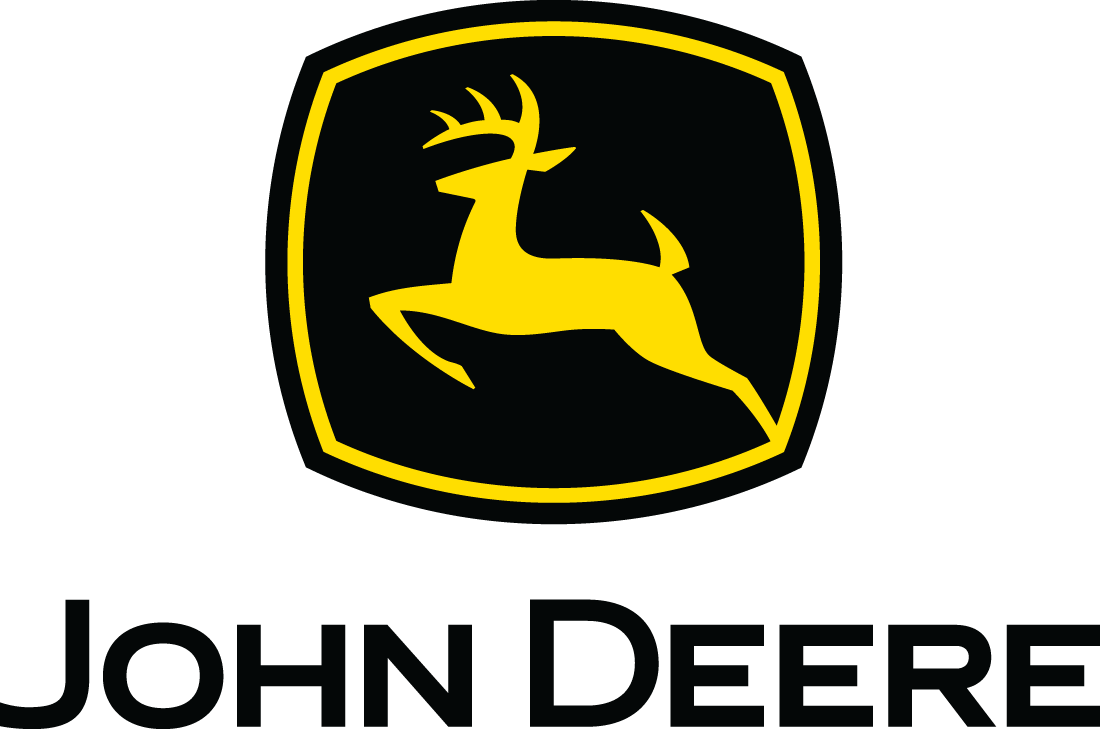
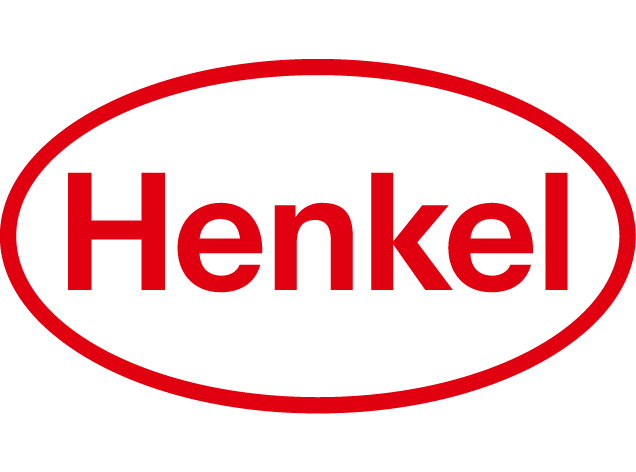
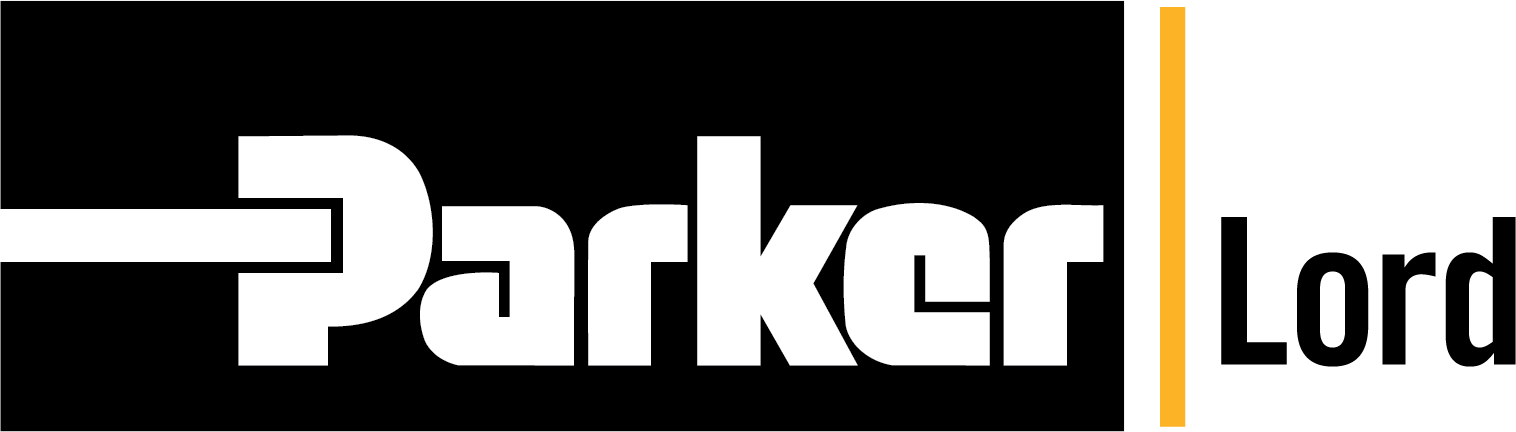
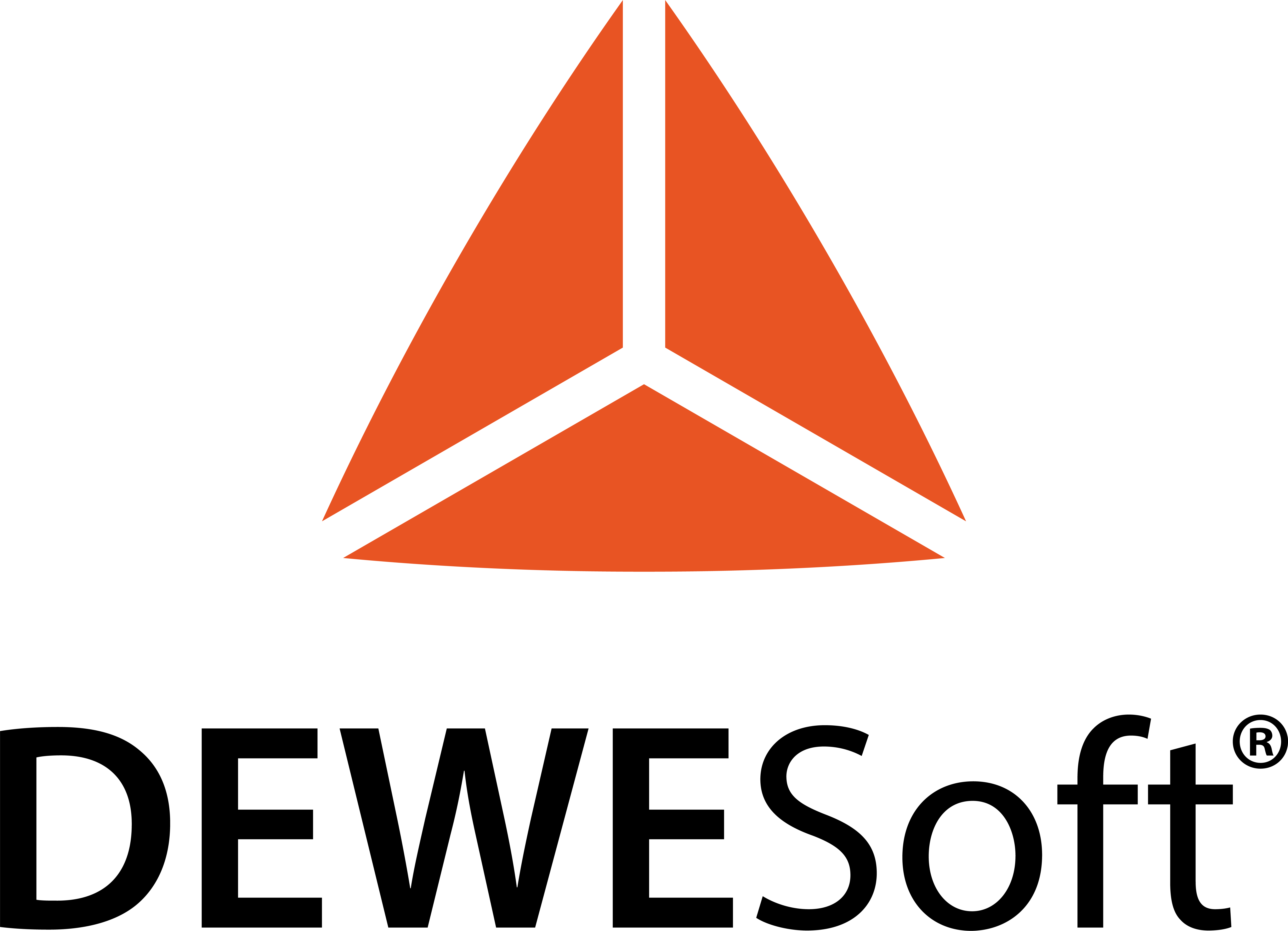
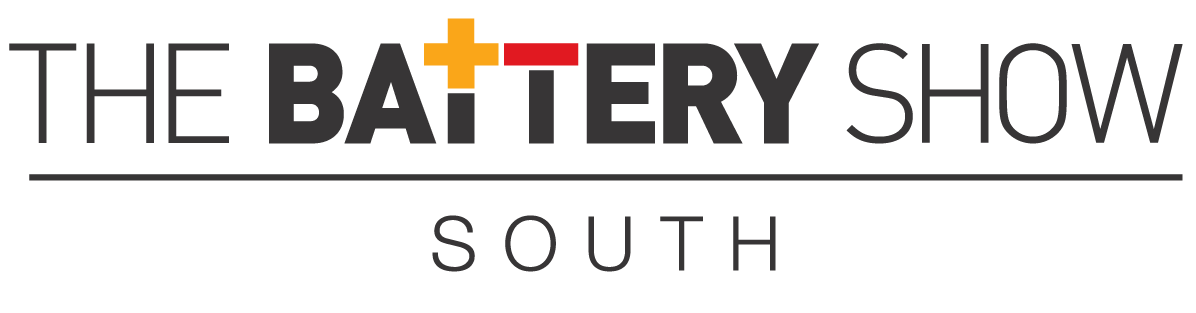
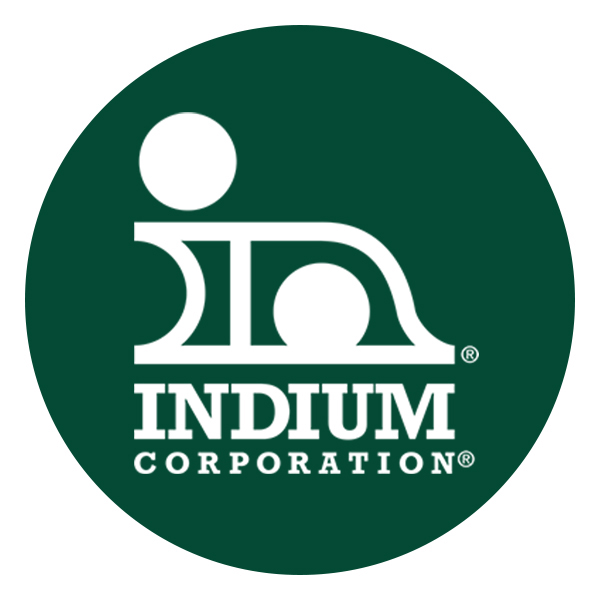

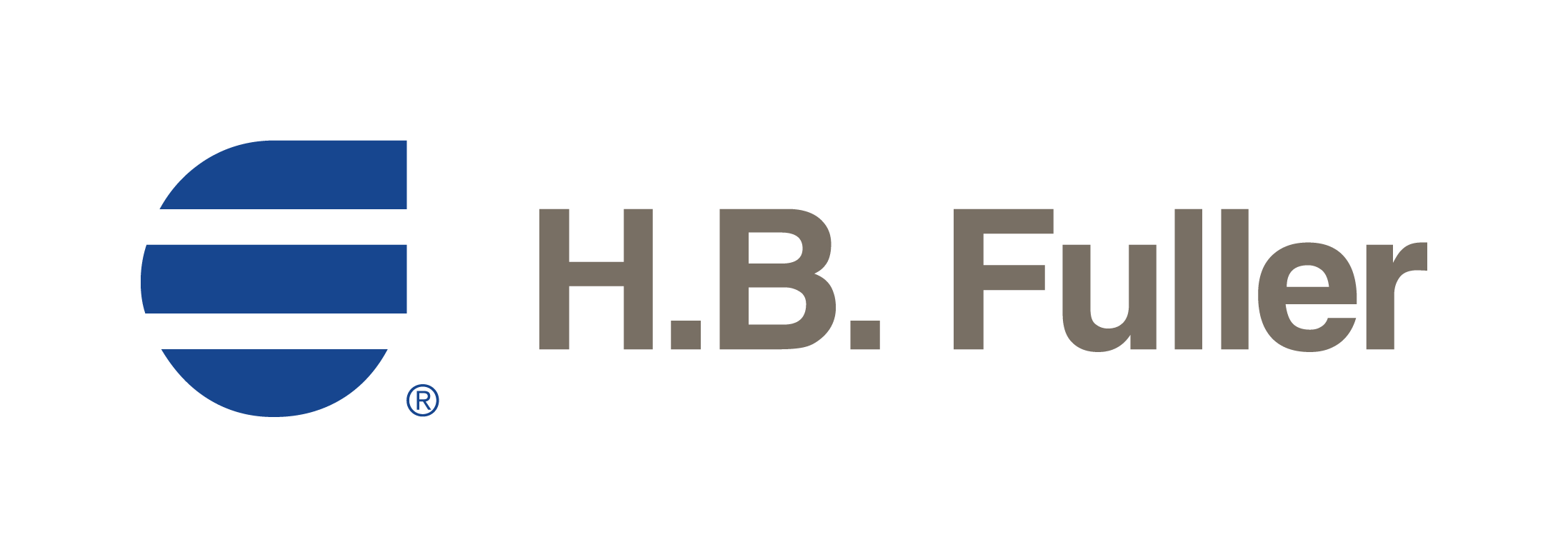
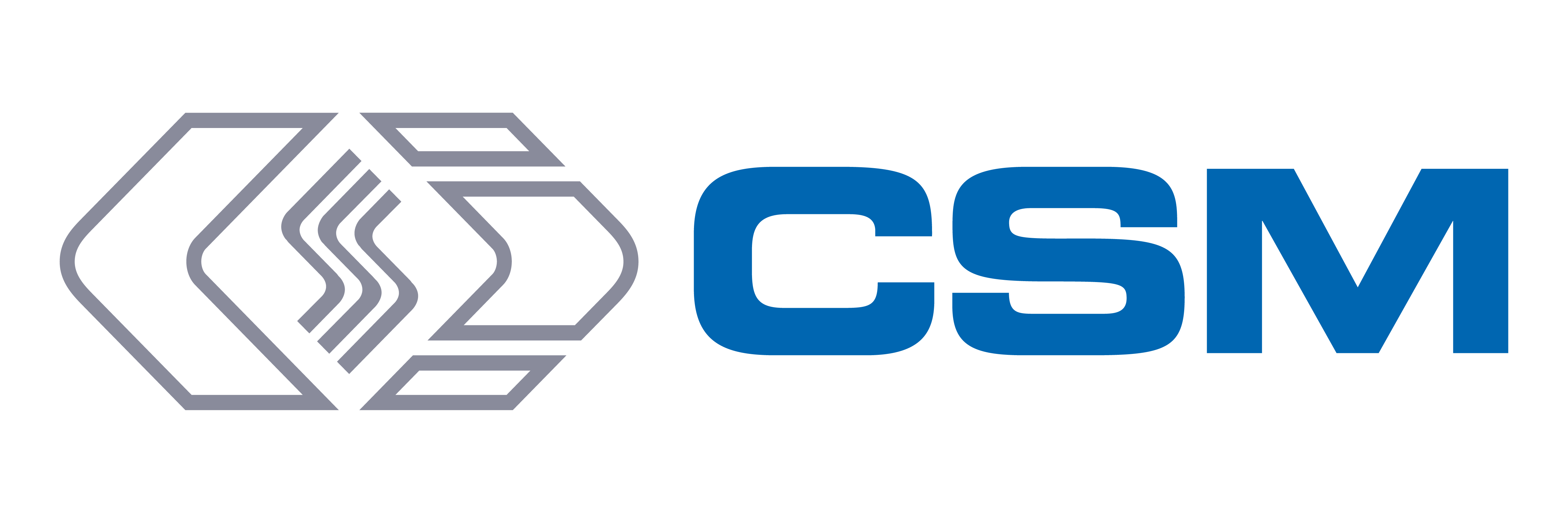
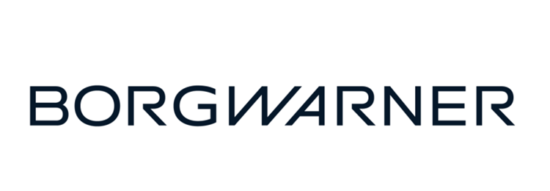