Vitesco Technologies develops innovative power module
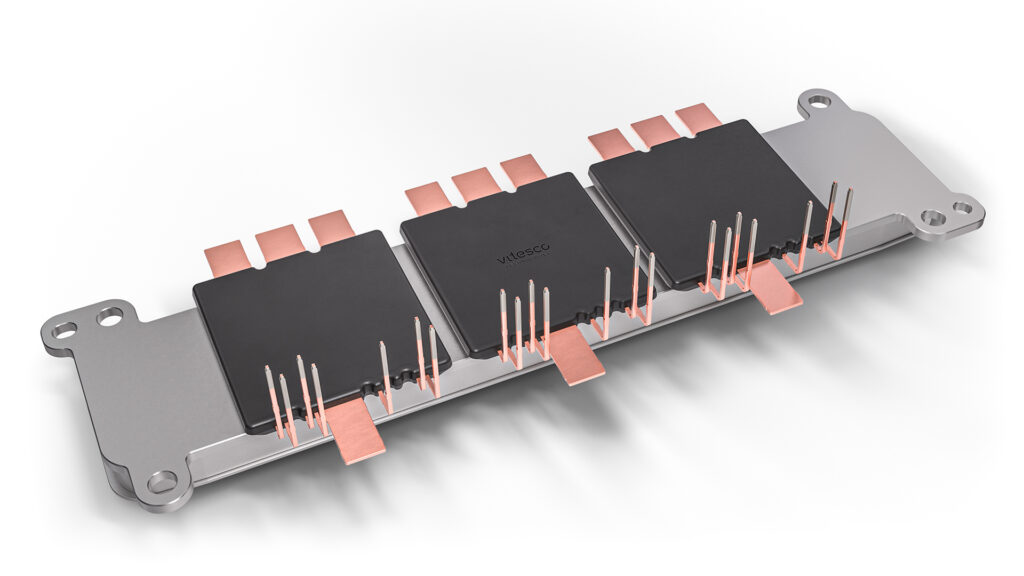
Vitesco Technologies, a leading international supplier of modern drive technologies and electrification solutions, is developing a power module which will be manufactured using transfer molding process.
During this process the power electronics are sealed under a dielectric material that protects the components extremely well. The result is a very robust, cost effective and reliable electronic. The power module consists of three overmolded half-bridges and forms the core of an inverter system, which controls both the drive energy and the energy recovery (recuperation) in high-voltage electric vehicles.
Manufactured at the Nuremberg electronics plant, the power modules will be delivered to a large global car maker from mid-2025 onwards.
Vitesco Technologies has been adapting and utilizing transfer molding technology since 2020, first applying it to compact Transmission Control Units designed for full integration inside a gear box. The overmold power modules now combine highly efficient state-of the art silicon carbide (SiC) chip technology with overmolding to facilitate a particularly robust product with increased power density, lower cost and reduced weight.
“These power modules are a good example of our strategic approach of using the scalability and modularity of our power electronics to develop and manufacture submodules in addition to the complete electronics. Combined with our extensive overmolding expertise, we can deliver an extremely robust product to our customers. This is yet another example of how we successfully transfer proven technology to an electrification product,” said Thomas Stierle, member of the board and head of Vitesco Technologies’ Electrification Solutions division. Vitesco Technologies has extensive expertise in power electronics and is already on the market with its fourth generation. The newly developed overmold power module expands the company’s strategic portfolio. “A very deep system competence is necessary to ensure that a submodule of this kind, which forms the core of the inverter, can be successfully integrated into the full system,” Michael Horbel, head of product and platform management high voltage inverter at Vitesco Technologies, explained. “Our degree of electronics modularity and scalability enables us to offer more flexibility in terms of customerspecific interfaces,” Horbel added.
Vitesco Technologies will continue to use this strength to bring further electronic sub-modules to the market. The lead plant for these modules is Vitesco Technologies’ Nuremberg site. With its existing competencies and experience, the plant offers a high degree of automation as well as the focus on electronics and e-mobility required for the power modules. This is a further step forward into the “Plant of the Future” concept, defined for the Nuremberg plant to maintain its international competitiveness.
ONLINE PARTNERS
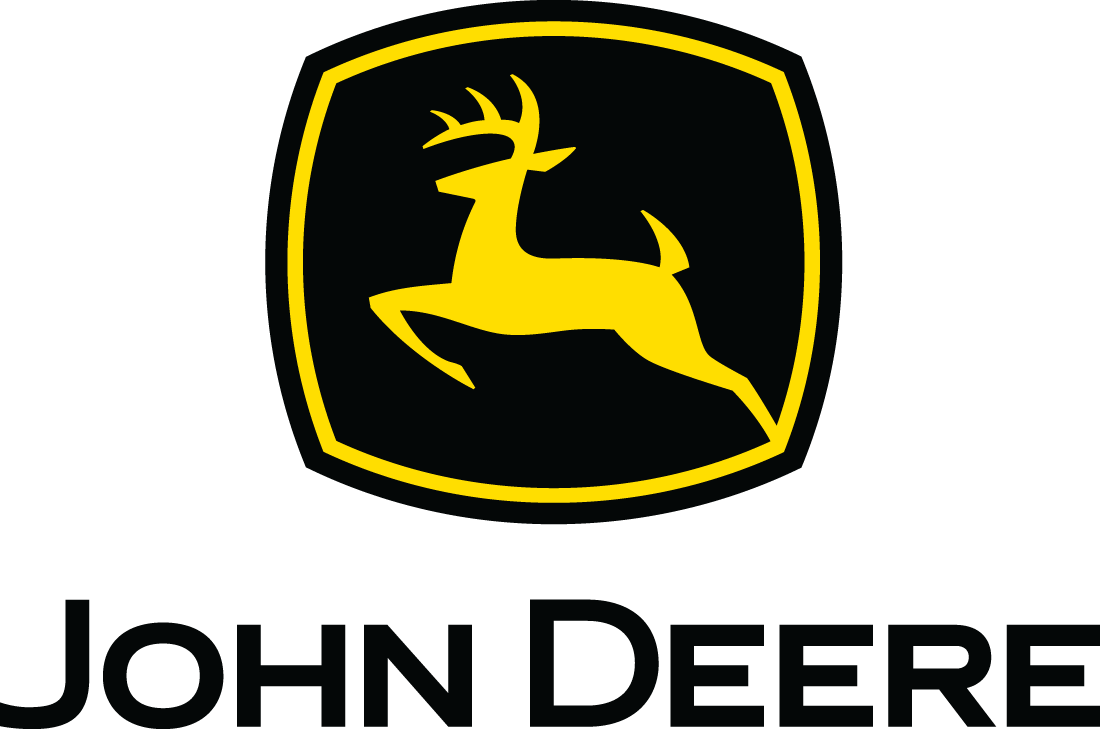
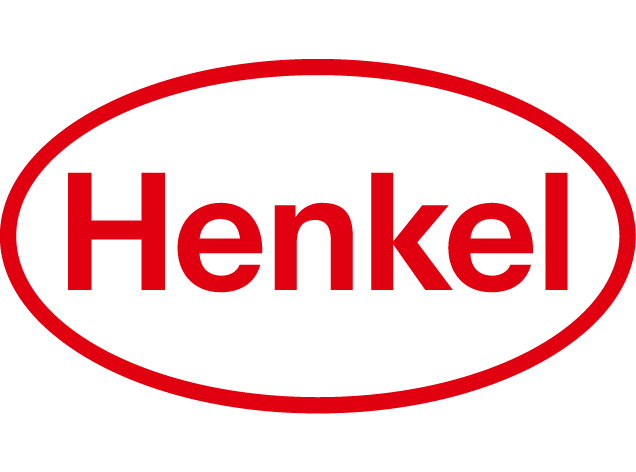
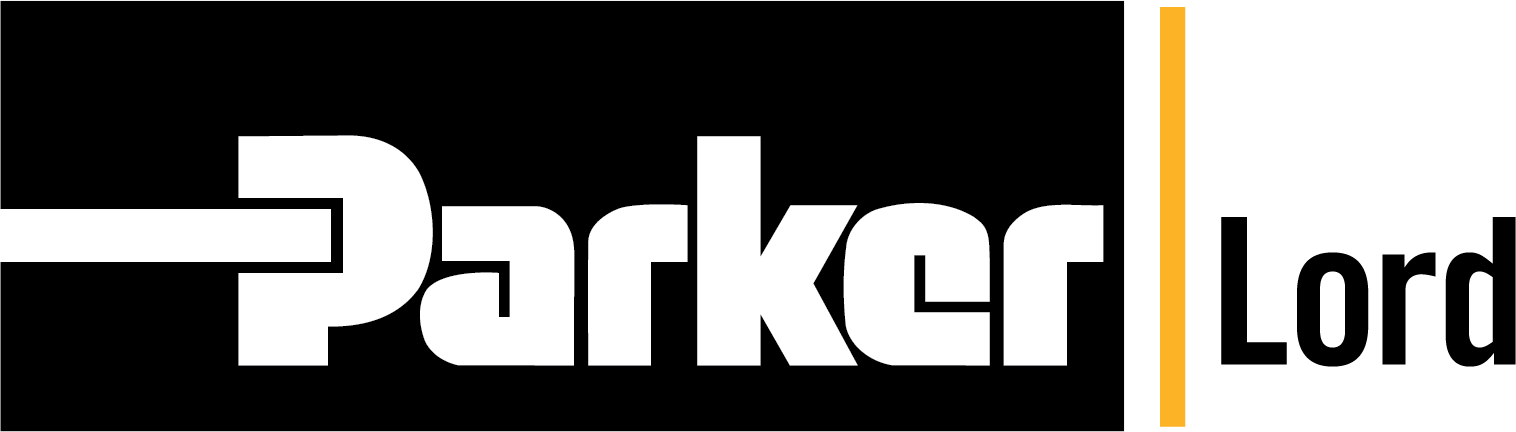
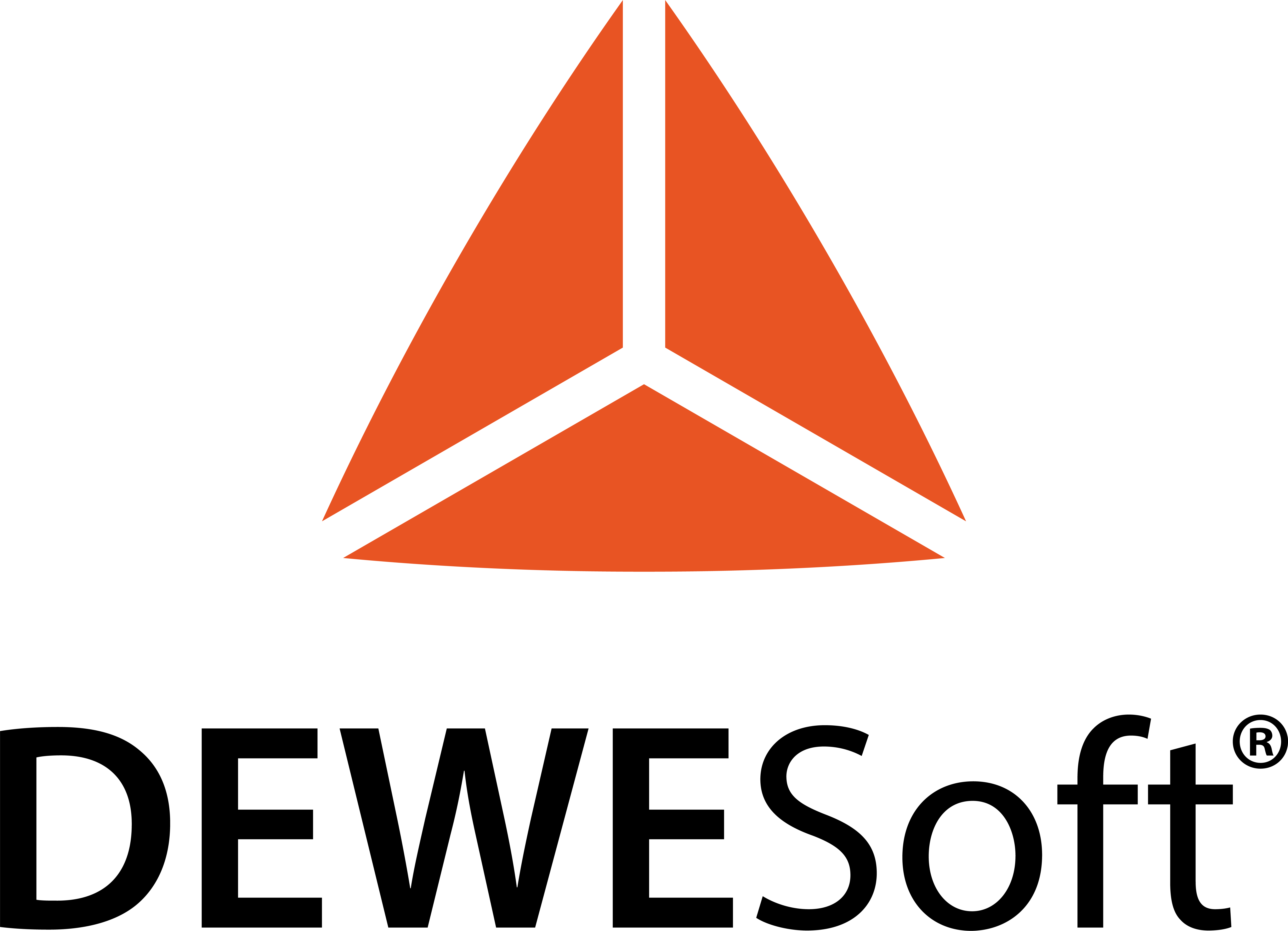
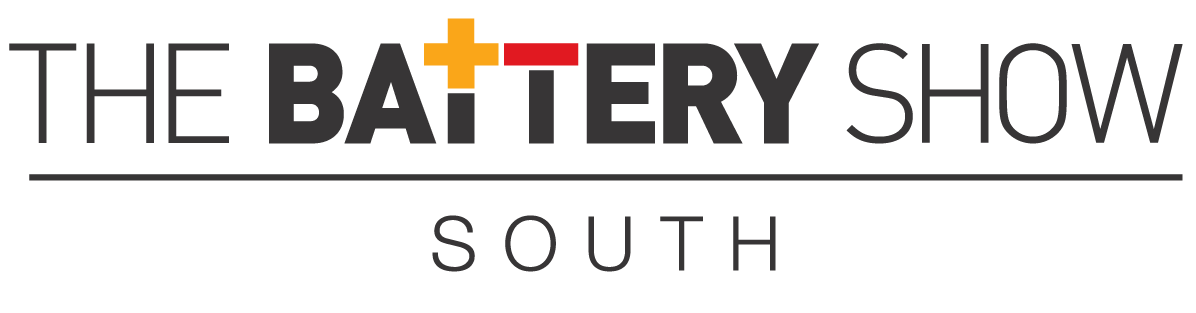
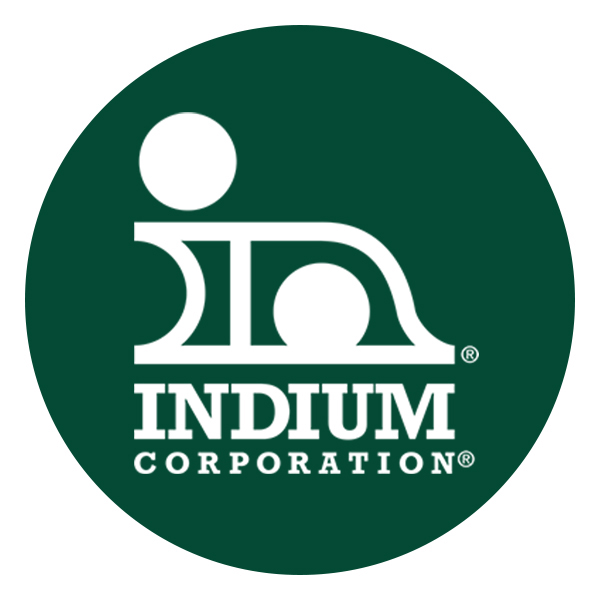

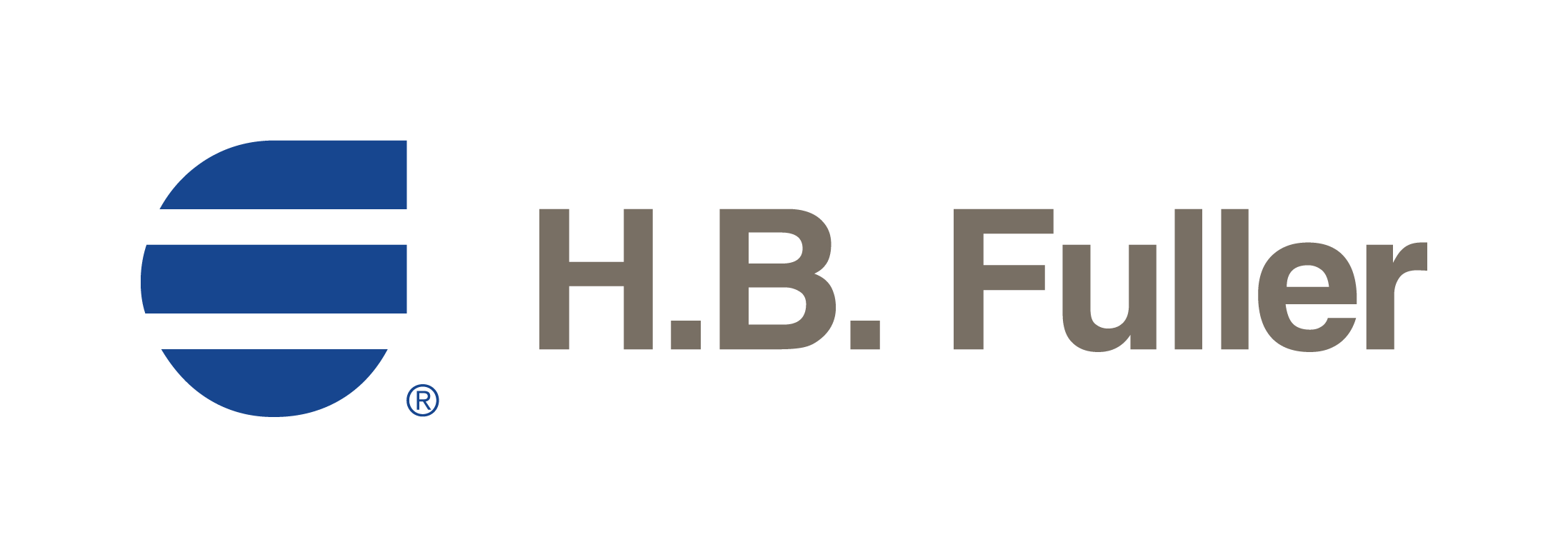
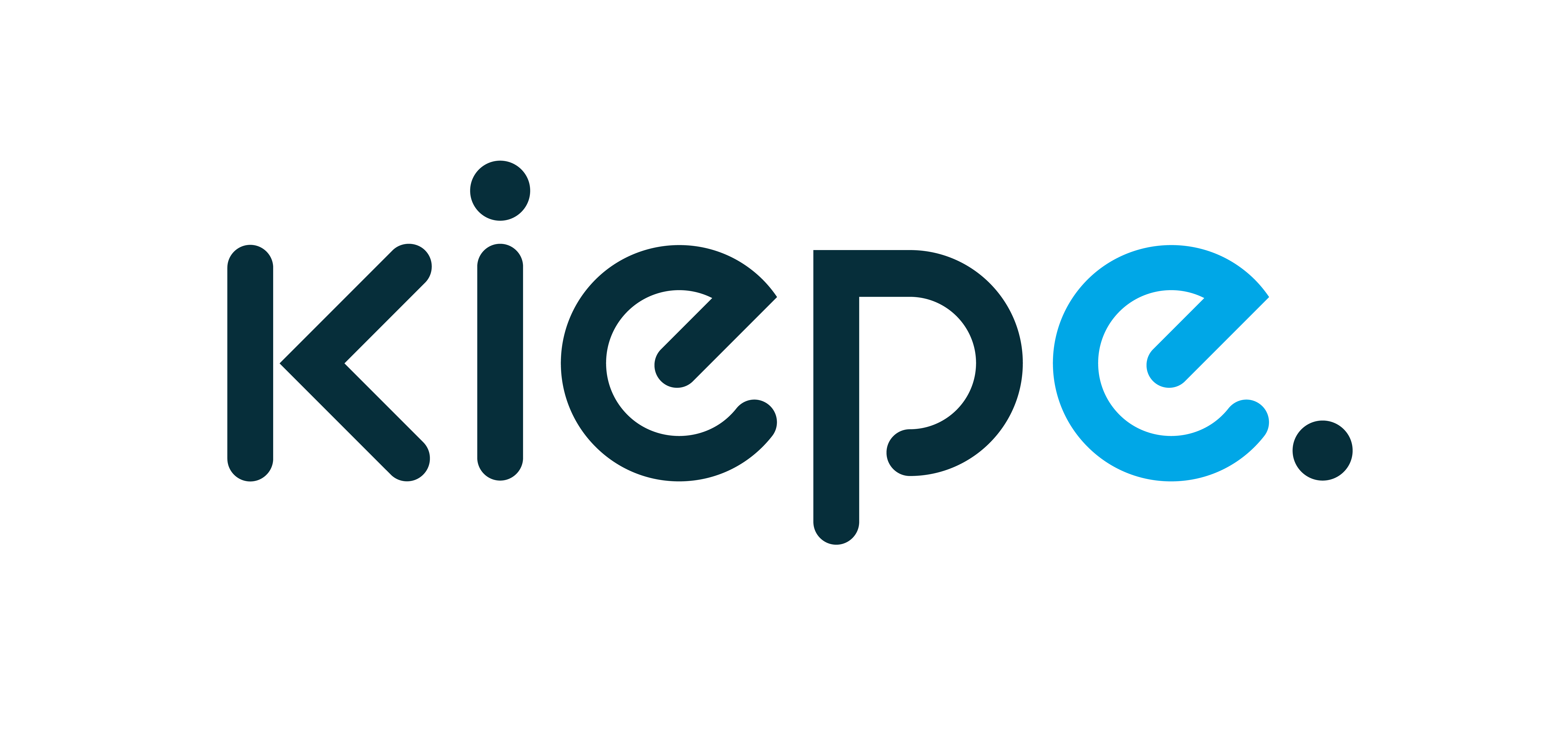
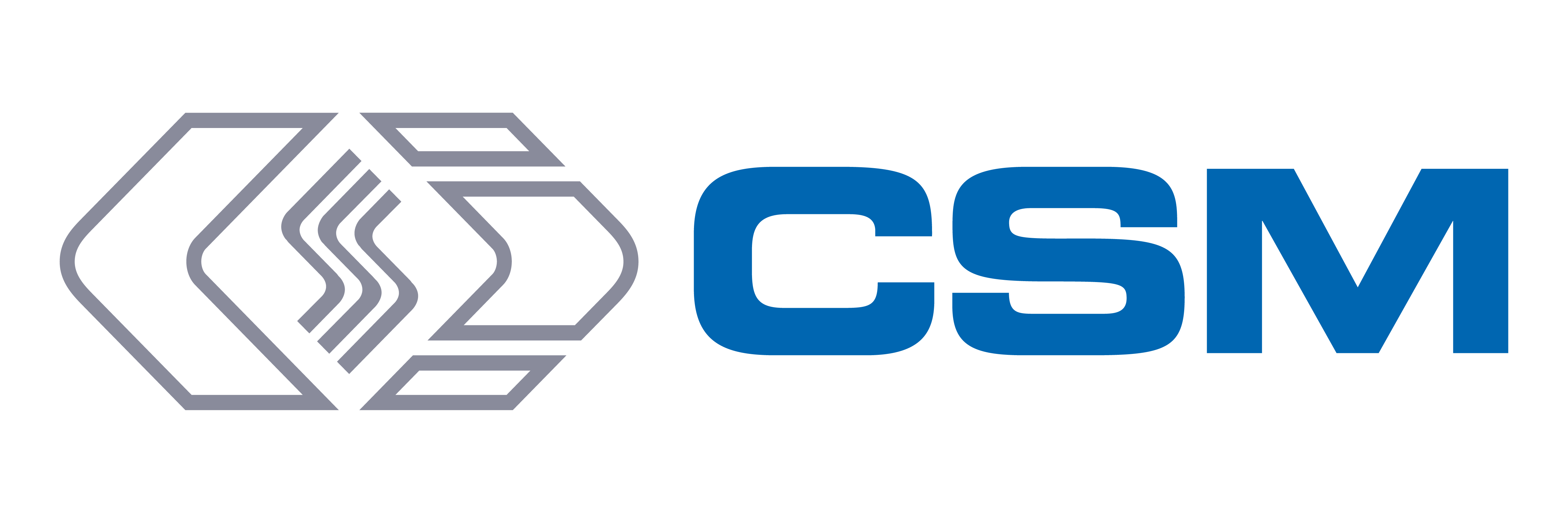