Vehicle-to-grid charging
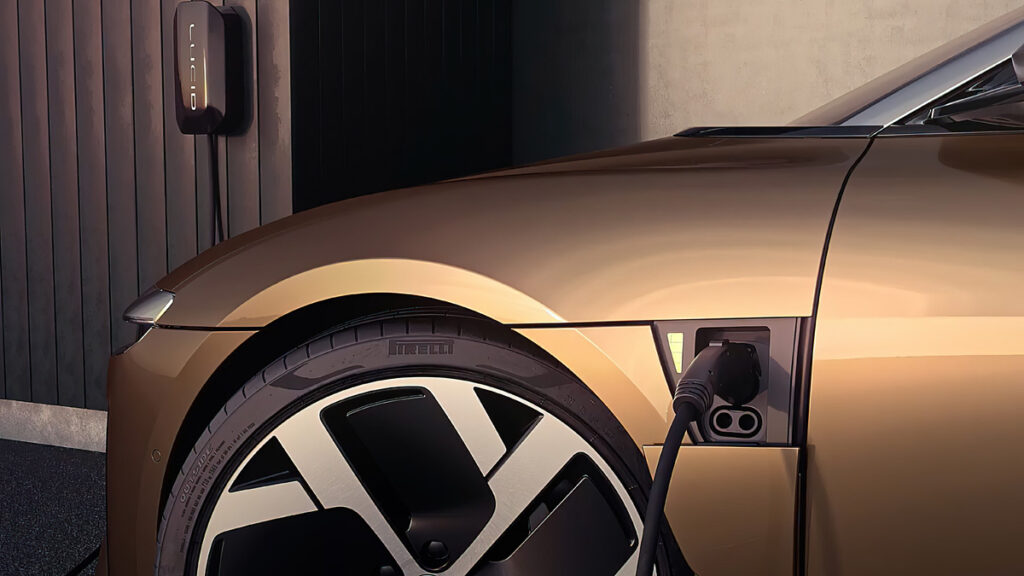
(Courtesy of Lucid Motors)
Although bidirectional charging for EVs remains a niche technology, writes Nick Flaherty, progress on its uptake is being made.
Vehicle-to-grid (V2G) charging is an appealing technology, as it enables EV batteries to be used as part of the electricity grid to even out demand. For example, electric car owners could charge their vehicle at off-peak rates overnight and sell energy back to the grid during the day while not in use.
Despite it having been around for decades though, the technology has yet to be widely adopted. It has been hobbled by a lack of standards across connectors, chargers and comms, as well as a lack of vehicles and the issue of range anxiety.
When users worry about the range they have with a vehicle, they are unwilling to offer up that battery capacity for other uses. As a result, car makers have focused on charging speed rather than installing the bidirectional chargers needed to share the energy in the battery pack.
One notable difference is the Nissan Leaf, which does have a bidirectional charger and which has been the mainstay of V2G projects around the world over the years. However, it uses the ChAdeMo connector system, which has had limited uptake in Europe and North America, where the combined charging system (CCS) is preferred. Bidirectional charging for this is only just being standardised.
Electric car maker Lucid Motors, in the US, wants to change this. Its Lucid Air features the company’s Wunderbox bidirectional charger, which includes CCS charging and a 900 V battery pack with a range of more than 517 miles (800 km). The 350 kW onboard charger (OBC) has been designed to connect to high-speed DC charging but also to feed AC back into buildings or even other vehicles.
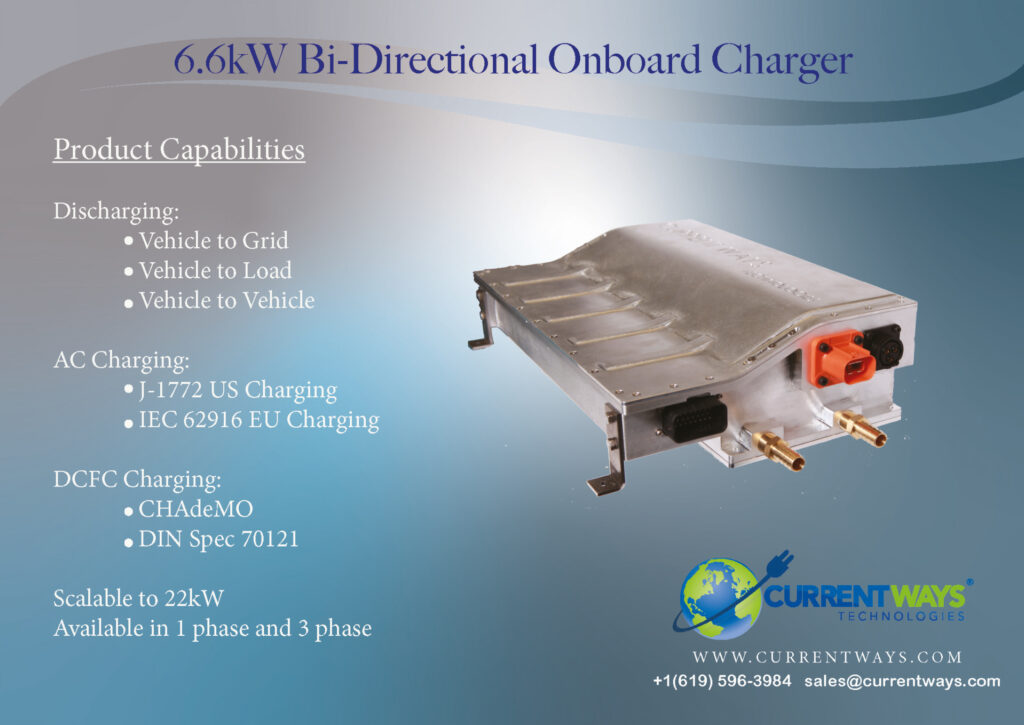
Lucid has also designed a bidirectional charger, the Connected Home Charging Station, for the home, as well as what it calls static Energy Storage Systems (ESSs) using its batteries to provide a second life for older batteries that can no longer be used in cars. The first ESS prototype has now been installed at Lucid’s Silicon Valley HQ.
This highlights the change in thinking for V2G. Connecting vehicles directly to the grid comes with major challenges for the coordination and control, so there is more of a focus on connecting to the home or office.
That still requires much more sophisticated control than first envisaged though. In early projects the cars were plugged in and shared power directly with a home or office, then unplugged when the power was no longer needed.
Now users want to make sure the vehicle is ready to use with an acceptable level of battery power.
That means the control systems are having to learn the usage patterns of the drivers to ensure there is enough power.
This involves many more comms and control between the vehicle and the local grid in the house or the building management system in the office, which until recently have not existed. These signals then need to be standardised across multiple car makers and charger providers. That of course has taken much longer than anticipated.
What the early projects did show though was a key, unexpected point. There is still the perception that V2G will damage a battery pack by constantly charging and discharging the cells. While that is true for deep-discharge below 20% of the cell capacity and overcharging past 100%, early V2G projects – including the VIGIL project at the University of Aston in the UK – showed that keeping the charge between 20% and 80% can actually extend the life of the battery pack.
“The VIGIL concept was to use a building as a net energy sink that will always need energy,” says Dunstan Power, whose consultancy Bytesnap was part of the project. “What we wanted to do was offset the energy load from a Nissan Leaf with Nortec monitoring equipment on the grid side. However, getting reliable bidirectional chargers was a problem.”
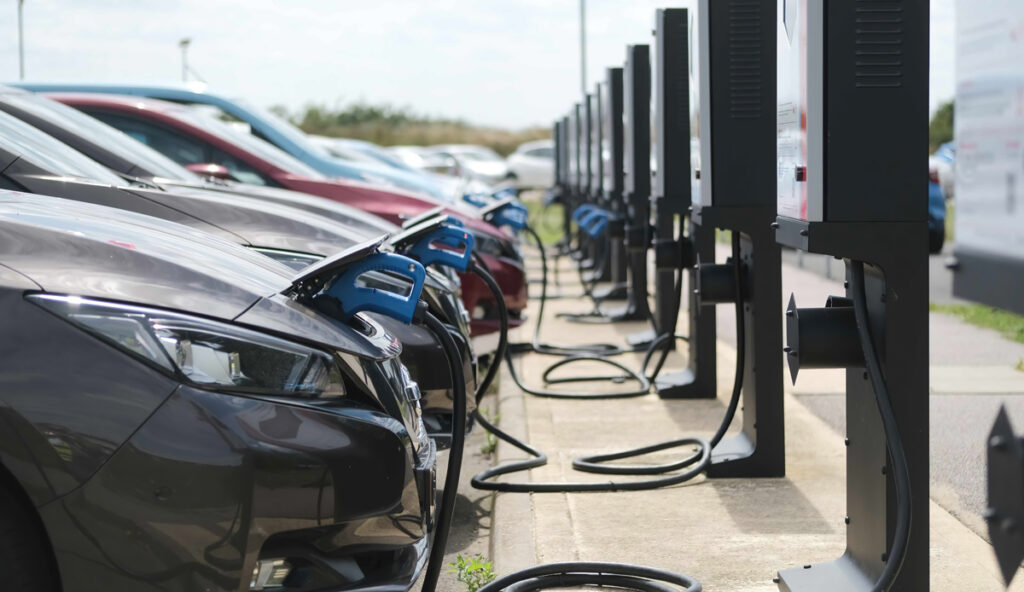
(Courtesy of E.ON)
Standards
Part of the challenge for V2G is standards for CCS. ISO 15118 is the key document for the comms, without which OBC makers are unwilling to commit to bidirectional designs. However, there are many different parts to the standard, from the original one in 2014, revised as part one (ISO 15118:1) in 2019 to part 8 in 2020 and part 20 (ISO 15118:20), which is set to be approved by the end of this year.
This standard specifies the terms and definitions, general requirements and use-cases for conductive and wireless two-way charging, which raises another issue. All the projects are based around bidirectional cable connections, although the standards are now approved for commercial vehicles such as buses that can be powered by an overhead pantograph. Then there is wireless charging, which is just coming onto the market, so the standards have also had to support bidirectional wireless charging.
ISO 15118:8 2020 specifies the requirements for the physical and data link layers of high-level wireless communication between the vehicle and the supply equipment, which is used as an alternative to wired communication technology.
After five years of development, Part 20 defines the V2G comms interface. It covers the full range of EVs, from cars, motorbikes and trucks to buses, ships and even aircraft. It is an extension of ISO 15118:2 that includes AC and DC bidirectional charging, and smart functions for payments both to and from the energy supplier.
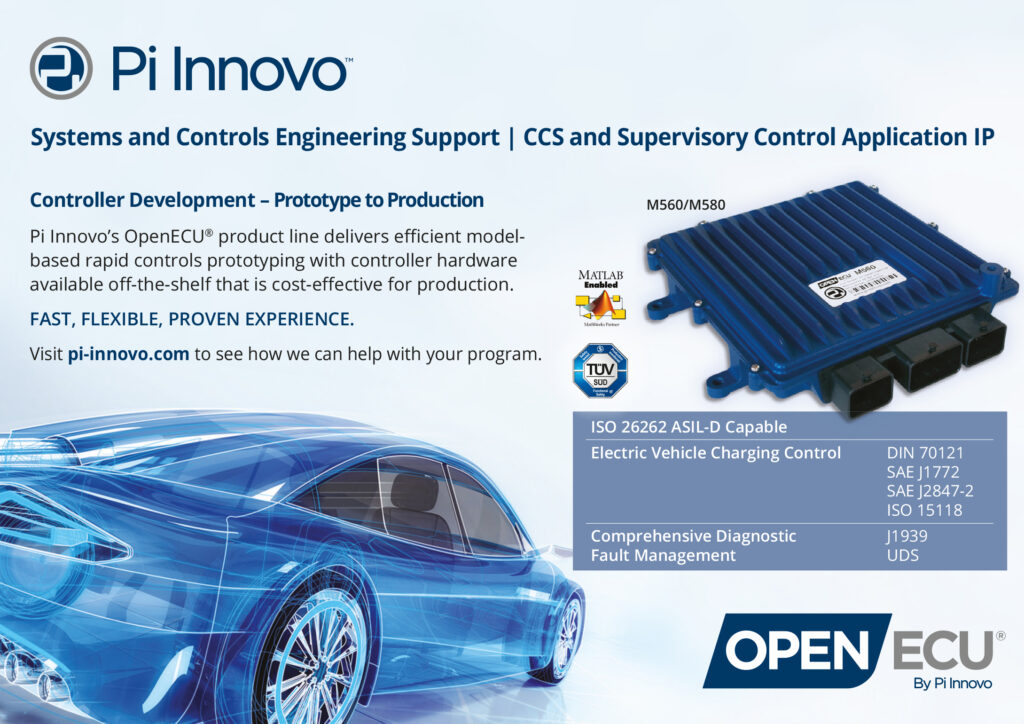
It also introduces two key parameters: the bidirectional BPTChannel and GeneratorMode. BPTChannel is used to distinguish between single- and dual-channel architectures in the charger, with two separate meters used for the opposing energy flows. Consequently, two switches are used and turned on/off depending on the direction of current flow.
The GeneratorMode parameter indicates if the system (the EV and the EV supply equipment) operates as a grid-following generator (only injecting active and reactive power) or as a gridforming generator that can control the voltage and frequency of the network.
Then there is the OCPP standard for linking to the home or office building. Unlike connections to the grid, this requires a standard for the link, which is implemented in the controller board rather than the charger.
Like ISO 15118, OCPP has evolved slowly. The current version used in most controllers is OCPP 1.6, although a version 2.0 has been defined, and there is a 1.6+ version that includes some of the more popular functions from 2.0.
“We wanted to have a common language from the building management system to the charger, to convert the OCPP v2 – which has V2G functions – to 1.6,” says Power at Bytesnap, which has spun off a controller board subsidiary called Versinetic.
“OCPP 2.0 has plenty of ability to talk to different parts of a smart grid with lots of extensions,” he said. “We have software libraries for both 2.0 and 1.6 that are for sale, and there is potential to link to smart grids in the future.
“Judging by requests from customers though, the industry seems fairly stuck on 1.6, which is standard smart charging with load balancing, and there are extensions with V2G tacked on with 1.6+.”
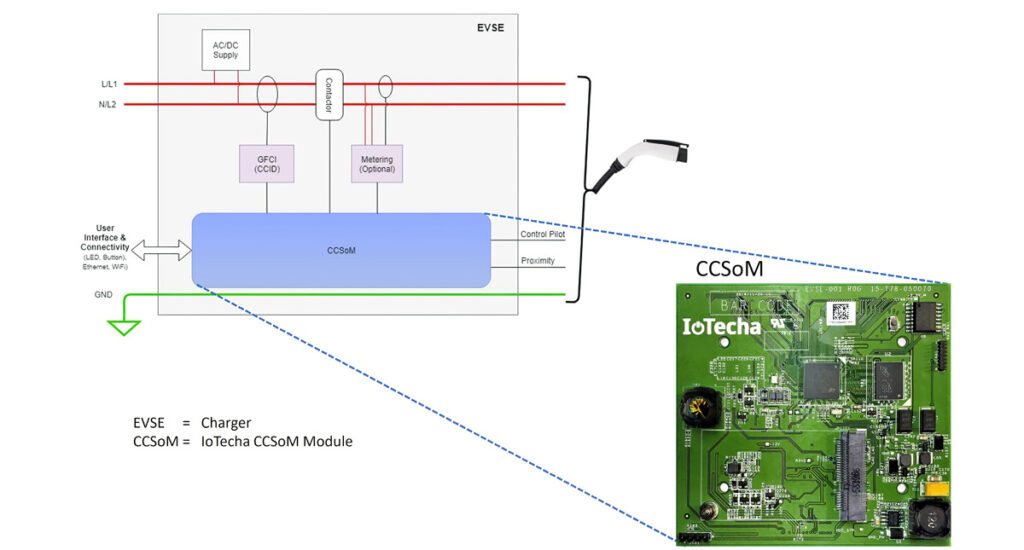
(Courtesy of IoTecha)
Comms and control
This is key to linking to the home, and is known as V2H. “The 15118 protocol is in the phase of developing enabling V2H, and everyone is working on that,” says Oleg Logvinov, CEO and founder of EV charging company IoTecha. “With Lucid and Audi we are starting to see auto makers becoming less reluctant to allow the battery to be used for other purposes.
“In one interesting demonstration with Lucid and using AC V2G charging of a vehicle parked near an office, the car absorbed solar power and supplied it to the office. That could save the owner $5000 a year, changing the economics of owning an EV,” he says.
With V2H connections to the home, he sees 20 kW as probably the maximum discharge rate, for the home to use the vehicle’s battery for as long as possible, for example for lights and air conditioning.
In a commercial setting with a school bus, say, that is charged up overnight but parked during the day, probably up to 100 kW is a reasonable level of discharge for grid stabilisation.
“It’s a balance between the cost of inverters and the cabling,” Logvinov says. “But this use-case is well-defined. It’s actually an asset management and big data problem. The bus may not need a 100% charge in the afternoon if the route is 10 miles for example, but it’s actually capable of 120 miles, so even 30- 40% is usable.
“It’s the same for the office charging – there’s the daily run to the office but at the weekend you need the car to go away somewhere. That is where we will have an opportunity to combine AI and modelling, and allow the technology to maximise the value.”
This is key to defining the functionality of the controller boards. “We realised early on that we would need cloud computing, and we use embedded Linux, which is good enough,” says Logvinov.
IoTecha has also developed a monitoring tool, called PilotShark, that provides non-intrusive monitoring of the comms between the vehicle and the grid. This tackles a problem where the signals carried over the power cables require an acknowledge (ACK) signal for each data packet. When you add another node to the network (as in the protocol monitor) the ACK signals can cause interference.
The PilotShark uses the ST2100 from STMicroelectronics with a 333 MHz ARM926 processor, but reprograms the chip to suppress the ACK signals and collect packets from both directions and reassemble the data streams to help debug the system.
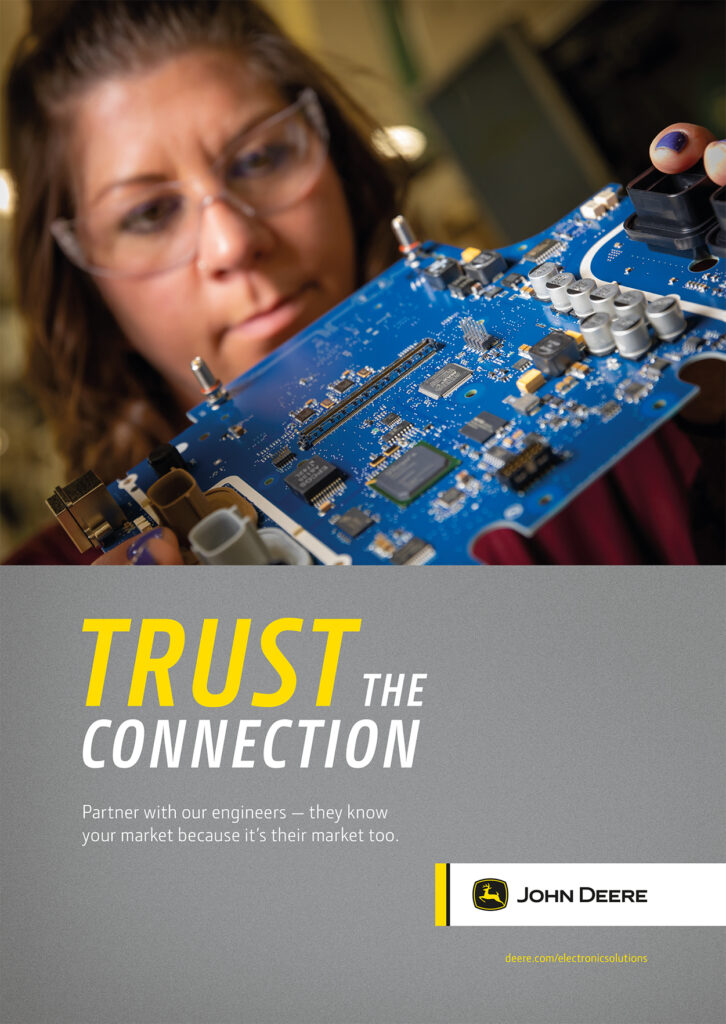
Connecting to the home or office with V2G is far easier than connecting to the grid. “If you look at the current state of the industry it’s easier to find valuable use-cases for the meter before you go to grid-scale solutions,” Logvinov says. “Virtual power stations are more complex from a regulatory perspective, rather than getting it done ‘behind the meter’ into the home.
“On the grid scale you can connect through the telematics, but topologically you need to know where you are,” he says. “You have to know about the other loads and sources of power, so you have to look at the building load and stationary storage, and associate a specific charger with a specific location. Then there are the standards for the connectivity, which is based around OCPP.
“OCPP has proven itself to work reliably in the field, and most of the charging operators use it with 1.6 at the moment, with JSON [JavaScript Object Notation, a lightweight format for storing and transporting data], but that will transition to 2.0 within the next year or so.
Now that the standards are starting to settle down, industrial multinational ABB for example is rolling out a network of 11 kW bidirectional chargers in France, to be followed by networks in Italy, Germany and the UK.
“There are some major differences between 1.6 and 2.0 though. Some of the elements of 2.0 were in 1.6+ – plug-in chargers for example.”
This will use software from DREEV, a joint venture between energy supplier EDF and charger maker Nuvve, in a kiosk form factor to allow drivers to export surplus power to the grid and with the potential to generate up to €20 per EV per month.
“Our cooperation with DREEV is one of the leading efforts worldwide to deploy real V2G technology in the field,” says Frank Muehlon, head of ABB’s global business for e-mobility infrastructure solutions, which also supplies chargers to many roll-outs across Europe and Japan. The 11 kW chargers are quicker to roll out than larger versions, he says.
There are still major differences between different countries for linking to homes and offices though, says Power, and that requires flexible technology. “We use Linux so that we can add drivers for cellular links or wi-fi , for example, to allow for future specification changes. Every country is doing its own thing with different standards,” he says.
Embedded Linux provides a flexible software infrastructure, he adds. “We are not trying to do hard real-time processing, we use JSON over web sockets with messages in the OCPP 1.6 format. Originally we used a different message format that was defined in OCPP 1.2 to 1.5. The main problem is memory and resources – we are essentially hosting a web server in the controller so that you log into and configure the charger.”
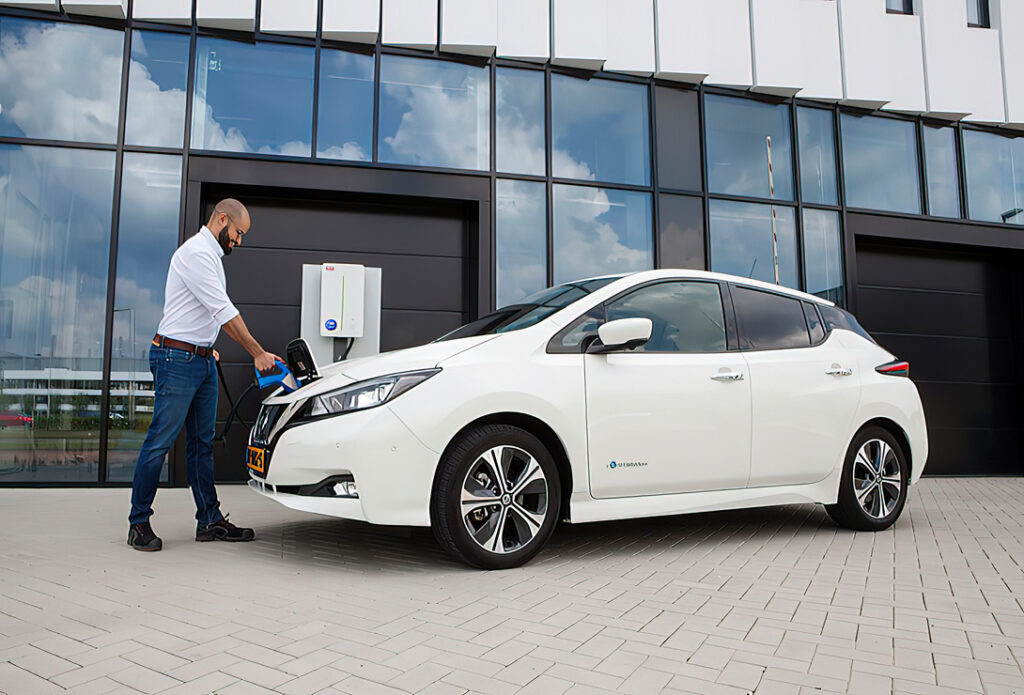
(Courtesy of ABB)
Commercial vehicles
Commercial vehicles such as buses present a different set of challenges for V2G. Their battery packs are larger, providing a greater reservoir of energy, but the buses need the energy for their routes, and adding V2G cannot be allowed to have an impact on their reliability by stressing the components.
The world’s largest Bus2Grid project is being installed at a bus station in London called Go-Ahead London. BYD Auto is supplying the OBCs – two sets for each bus – and the charging station equipment for a fully integrated system using CCS Type 2 Mode 3 connectors.
The site charger has a nominal power rate of 80 kW, and each OBC has a nominal charging power rate of 40 kW with 20 kW for discharging.
“At an early stage we determined that the impact of V2G on battery life would be too small to measure in the duration of the project,” says Frank Thorpe, the UK managing director at BYD Auto.
“We have therefore used a modelling approach which indicates that, with control measures such as state of charge and power delivery limits, the effects of V2G are minimal when seen in the landscape of a front-line city bus operation.
“This gives us confidence that the overall impact on battery life will be very small and that our battery warranty will be unaffected.”
By limiting discharge power to half the charging power, the stress on components such as the silicon IGBTs in the OBCs is minimised, says the company. “There are stringent requirements that need to be satisfied in order to authorise the connection of power-generating equipment to the UK grid, so we carried out extensive testing to satisfy them,” says Thorpe.
The project uses a dedicated cloud platform that calculates the demand across the bus depot and the estimated vehicle dischargeable capacity in real time, and sends that data to the local power grid platform. This control software takes into account the time a bus is required for service, and prevents any V2G activity if that would affect the availability for its scheduled duty.
The primary control path uses BYD’s telematics platform to communicate wirelessly using the Modbus and TCP/IP protocols between each vehicle and a cloud platform that manages V2G activity.
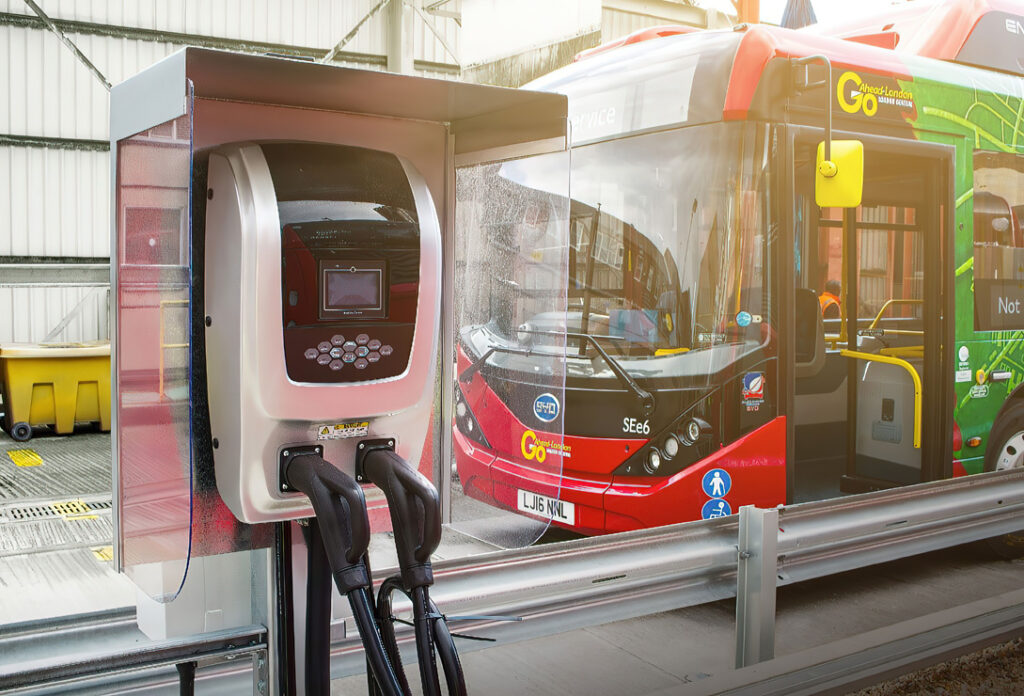
(Courtesy of BYD Auto)
Pantographs
Bidirectional pantograph systems, or “automated connection devices” as defined in 15118:20, are being tested in real-life conditions at the VDL Enabling Transport Solutions’ charging test centre in The Netherlands. This test system is using chargers from Siemens with a switching matrix and stationary battery system to manage the power capacity requirements.
The set-up is managed via an energy management application running on MindSphere, the cloudbased, open IoT operating system from Siemens. VDL will use it to conduct interoperability and function tests on electric buses and trucks from different manufacturers.
“The Siemens technology allows us to test different e-bus and e-truck technologies in combination with charging stations and an energy storage system,” says Menno Kleingeld, managing director at VDL.
“With the energy management application we can control the flow of energy as needed. We also use secondlife batteries in the storage system, which means we can re-use our earlier e-bus batteries.”
This V2G capability will be used to cover peaks in power demand across the test centre.
“Three of our latest 150 kW fast-charging stations are being used at the centre,” says Monique Mertins, head of charging infrastructure for e-bus and e-utility vehicles at Siemens Smart Infrastructure.
“The charging electronics can be temporarily interconnected, making it possible to charge three vehicles in parallel with a capacity of 150 kW each, or one vehicle particularly rapidly up to 450 kW using high-power charging.
“That means power can be adjusted flexibly and the charging infrastructure optimised for depots with different requirements.”
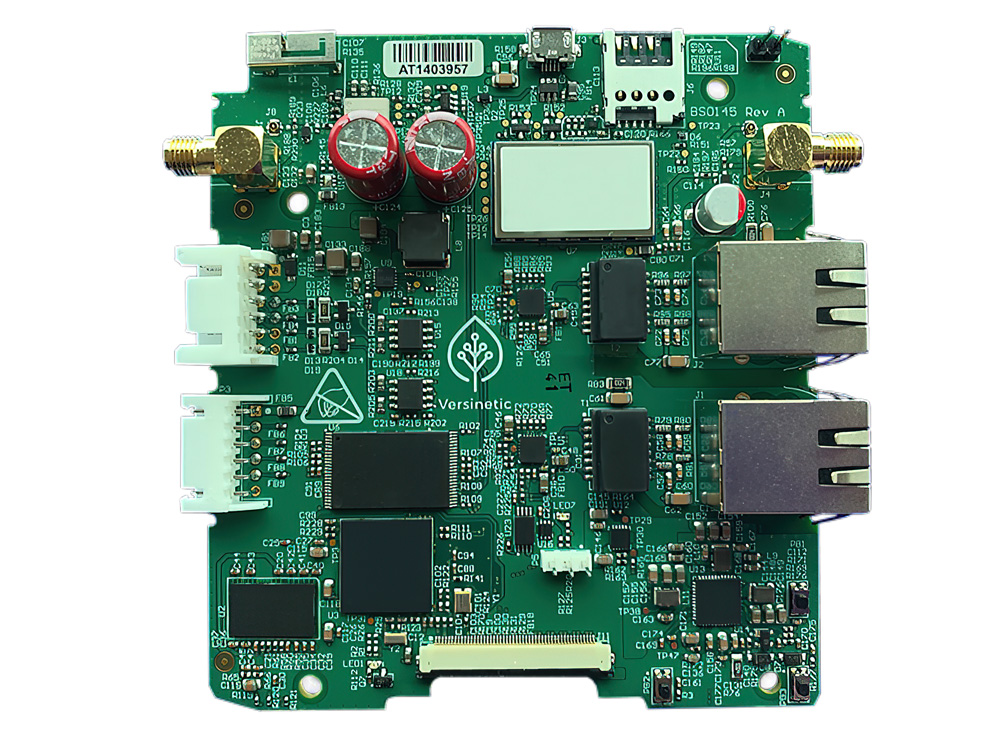
(Courtesy of Versinetic)
Grid connections
A new dynamic mode in the ISO 15118:20 standard allows for more flexible links to the grid. It creates a distinction between the scheduled control mode, where the car or driver is in charge of the process, and the cloud platform taking control.
With the scheduled mode, the EV and the charging station negotiate a power profile based on the information exchanged with the ‘Charge Parameter Discovery’ request and response messages.
In this mode, the EV is responsible for computing a charging profile that is compliant with the user’s mobility needs – for example how much energy is needed to fully comply with the EV’s battery and when the driver needs to leave the charging station – as well as the charging station’s power limits.
With the dynamic mode, control is fully delegated to an off-board system and requires no negotiations. The EV sends across the same charging-related parameters to the charging station as in scheduled mode, but the charging station responds with only single power set points to the EV without any pricing information or power forecast in the form of a proposed charging schedule, and the EV has to abide by those set points.
The off-board system in charge of the control is responsible for ensuring that the user’s mobility needs will be satisfied. The dynamic mode is particularly useful if a fast response mechanism is needed to provide grid services, such as frequency control.
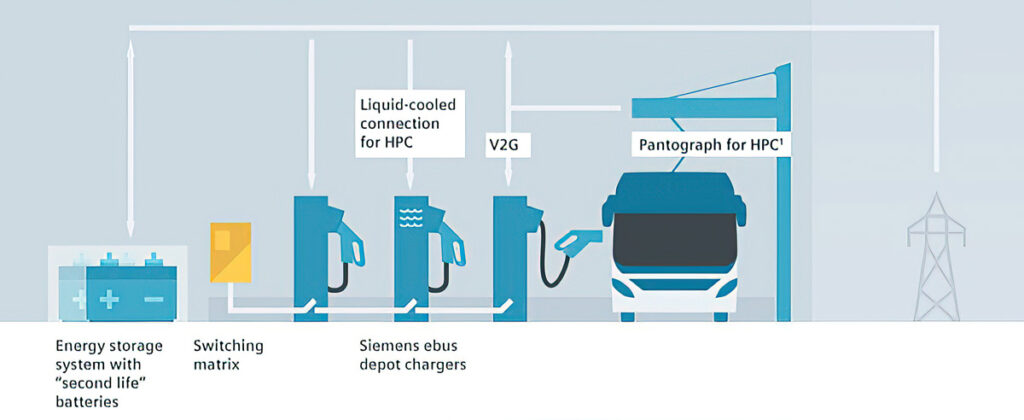
(Courtesy of Siemens)
Certificates and security
However, the path to V2G is not a smooth one. In 2019, charging network operator ChargePoint highlighted problems with the implementation and scaling of ISO 15118 for a secure EV charging ecosystem. The problems were around the security certificates that allow energy sources to connect to the grid.
“The way 15118 was written is very biased toward a small group of organisations that hand out and control those certificates,” says Eric Sidle, senior vice-president of engineering at ChargePoint. “With 15118, a higher level mobility operator is injected into the system.”
One of the key security technology providers is Hubject, which is a joint venture between the BMW Group, Bosch, Daimler, EnBW, innogy, Siemens and the Volkswagen Group, and is therefore a key part of the V2G EV ecosystem. There is a potential issue though with other car makers such as Ford using the Hubject technology, which could slow down the adoption of grid connections for V2G. While Ford is using the 15118 standard for the comms protocols, it has other techniques that use its own encryption technologies outside of the standard.
Conclusion
“We need to accelerate the development of the regulatory framework that encourages V2G,” says Logvinov. “The technology is here, and there are ‘behind the meter’ applications where the technology can showcase itself, so there is no need to wait for a specific use-case.
“We have two massive ecosystems with power grid and transportation. They are now becoming fused together as electrification becomes a very substantial load on the grid but also a tremendous source of energy, and that creates a wave of innovation.”
As the standards settle down, with 15118:20 emerging in 2021 to provide bidirectional charging for CCS systems and OCPP 2.0 providing more options for flexible V2G controls, the underlying technology is maturing and finding new opportunities. At the same time, car makers are including bidirectional onboard chargers.
But despite the proposal that V2G can reduce the cost of a vehicle, it will still take some time for the technology to reach the kinds of volume applications that will see more sophisticated chargers come down in price for mass roll-out.
ONLINE PARTNERS
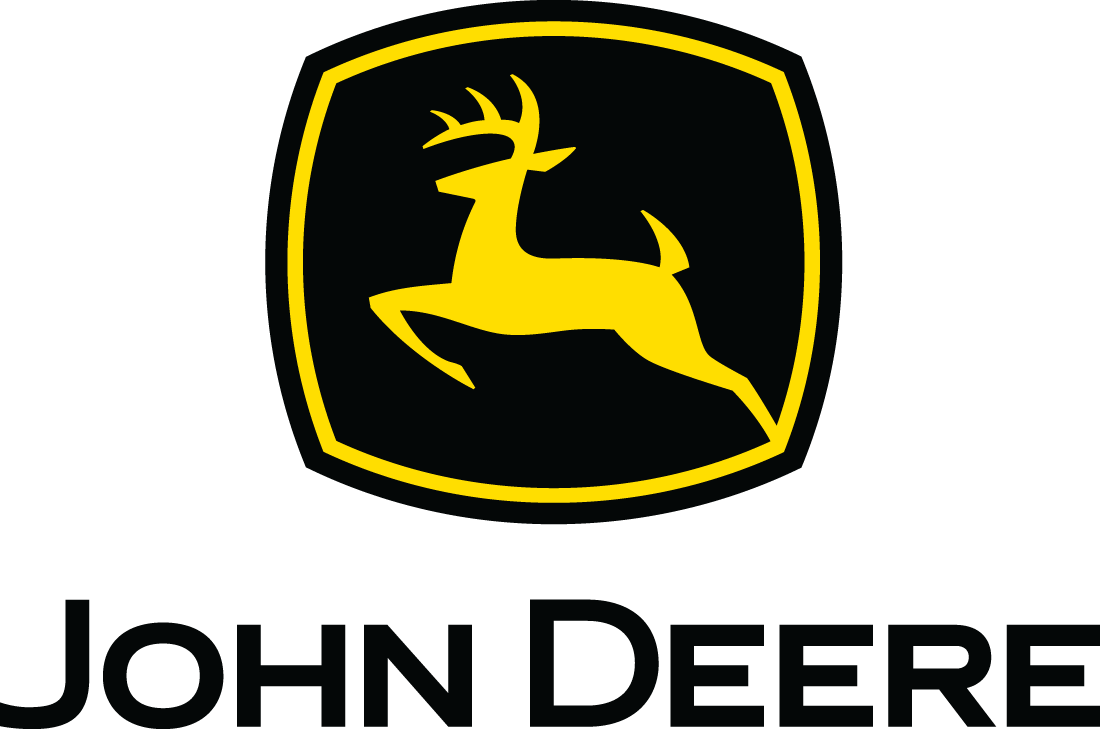
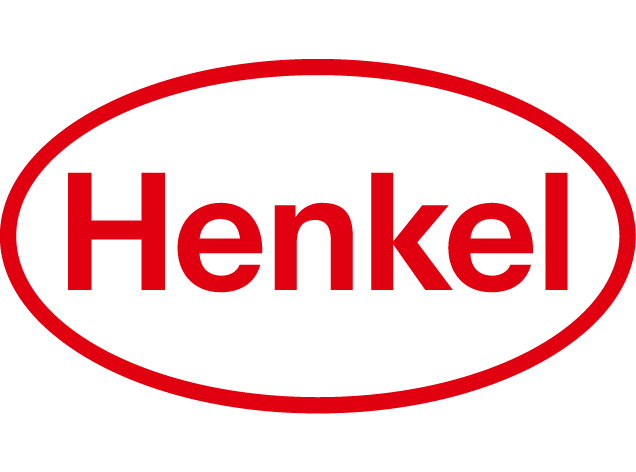
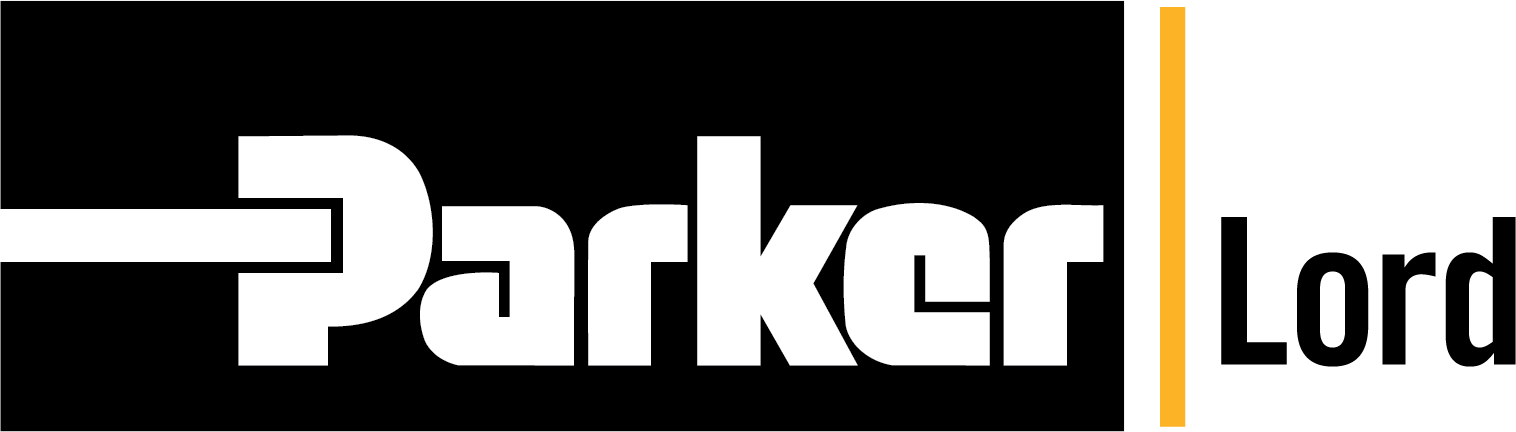
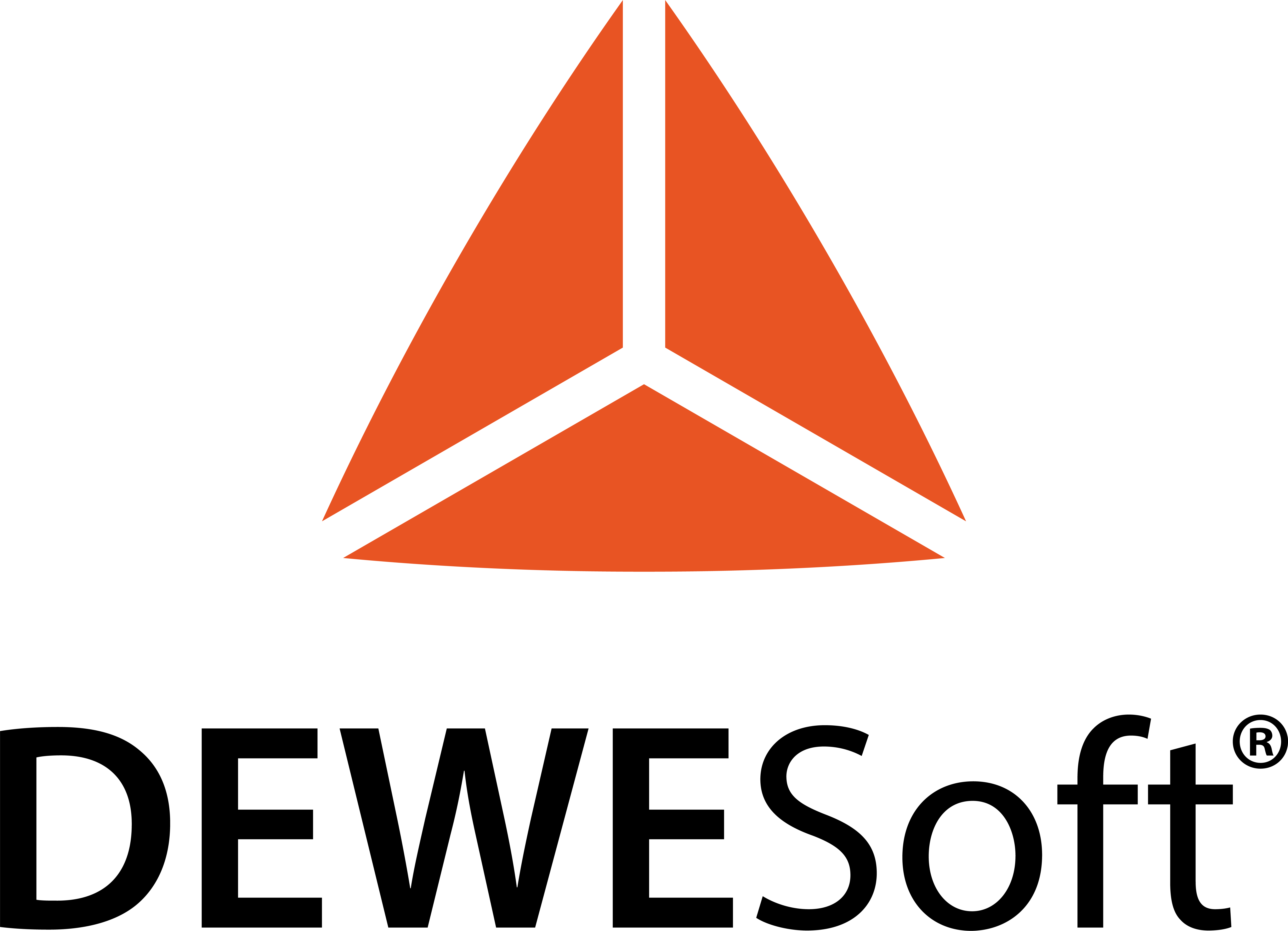
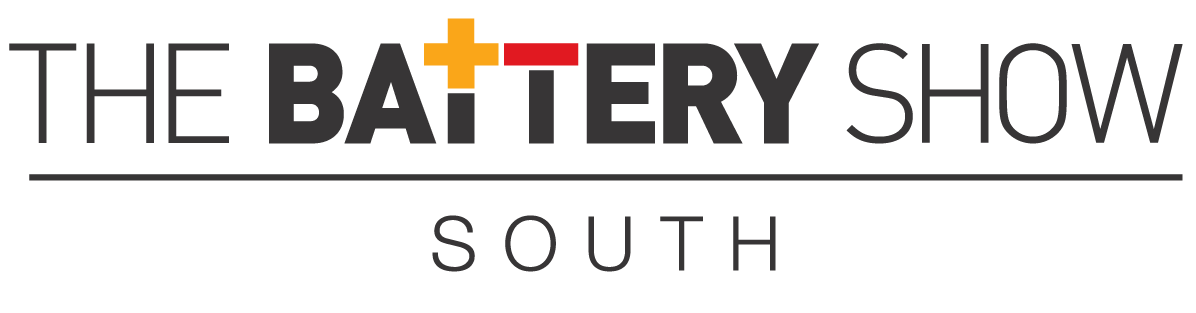
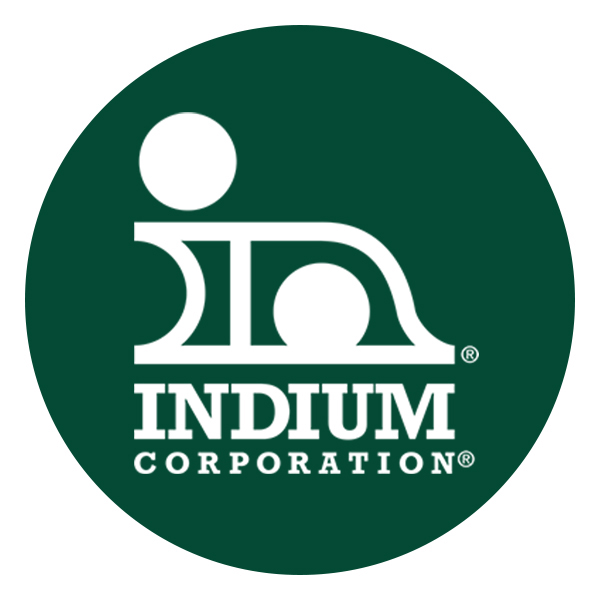
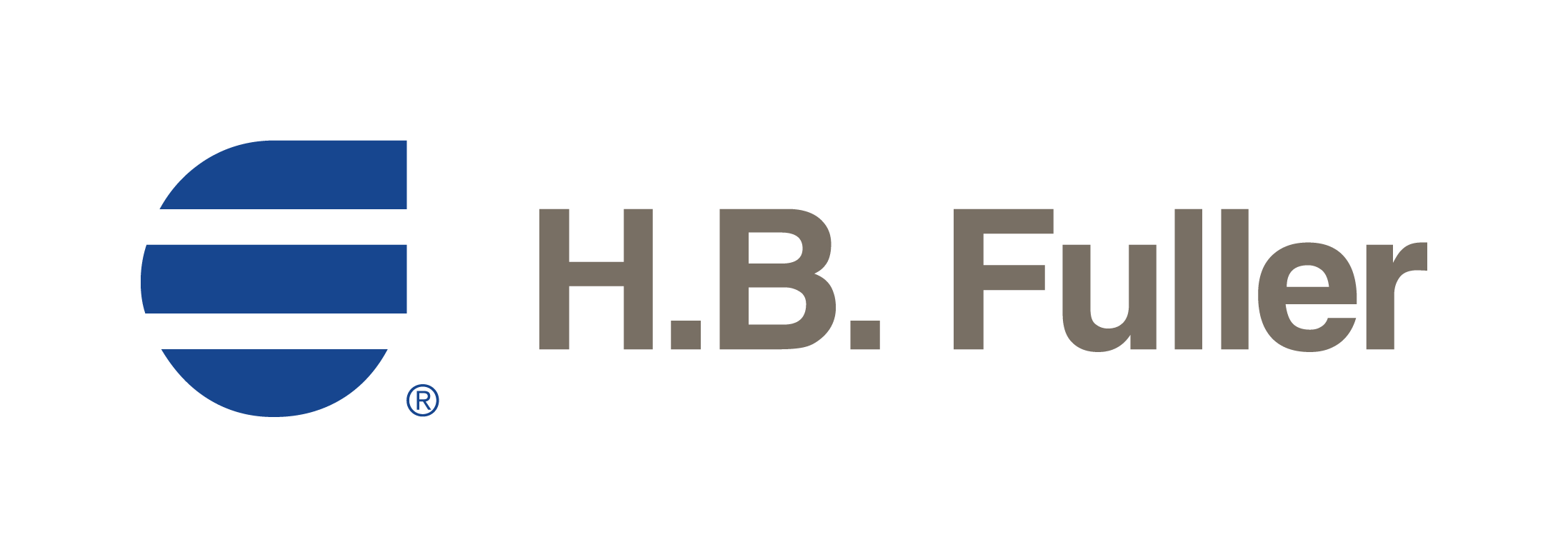