In conversation: Tim Woolmer
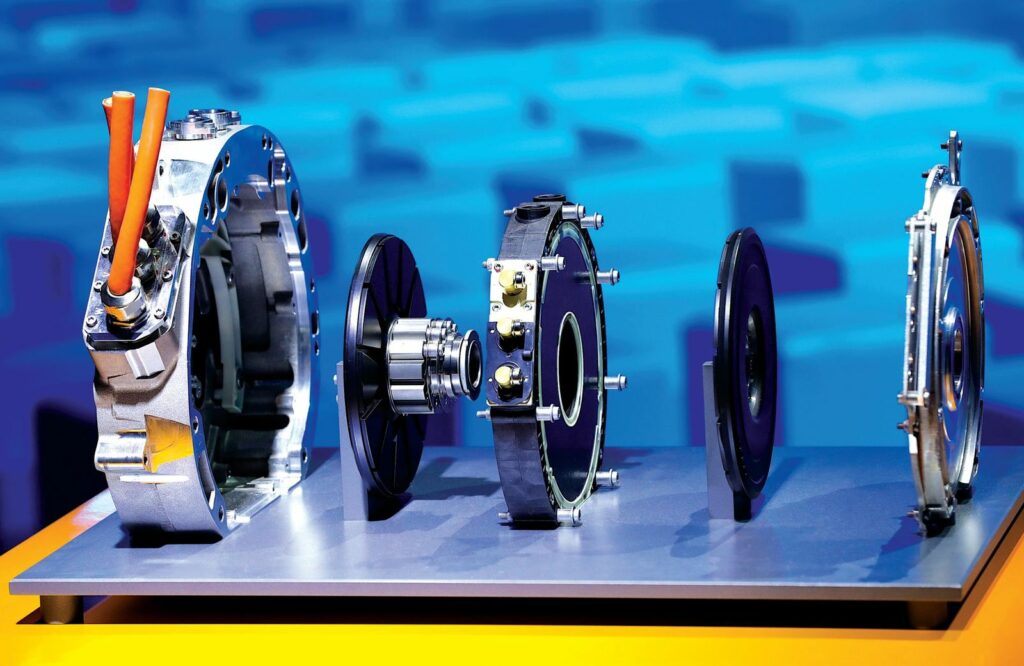
(Image courtesy of YASA)
Going flat out
The CTO of YASA Motors tells Rory Jackson how his axial-flux ‘pancake’ motors originated from a complex algorithm and a simple question
Today, Tim Woolmer is the CTO of axial-flux electric-machine manufacturer (and wholly owned Mercedes-Benz subsidiary) YASA Motors, but his initial entry into the world of e-mobility was something of a happy accident.
“When I was in my undergraduate years, Oxford University had this extraordinary algorithm for assigning challenging projects to fourth-year engineering students, but when it had to choose one for me, the algorithm broke; so, very unusually, I was told that I had to decide and write my own project brief,” Woolmer recounts.
“I took some time to think about what I was really interested in. This was 2003, and I soon found myself asking why there weren’t any electric cars. This was after the General Motors EV-1 had been killed, and still pre-Tesla. Really, there was nothing other than small, electric city cars. But what we did have were the first mass-produced, small mobile phones, MP3 players and other consumer electronics running on Li-ion batteries.”
Compared with the poor energy density of lead-acid batteries, and the minor improvements of nickel-metal-hydride, Li-ion represented a breakthrough, which indicated to Woolmer that EVs were on their way. While he was not yet focused on electric motors, he took stock of the sheer size and money potential of the automotive industry, and determined there had to be some fundamental reason why EVs had not worked yet, despite several competent companies having tried their hand at them.
“I found a supervisor who was similarly interested and started a project investigating that reason. I concluded it was all about range, which it was at the time, and developed a small, wireless induction charger that worked over an air gap,” Woolmer explains.
“My big dream back then was that we’d dig up all the roads in Britain, or maybe the whole world, and you’d bury these induction chargers so everyone could drive over them, and be recharging their electric cars all the time. It was a great and borderline utopian idea, if you ignore that no-one digs up critical infrastructure unless it’s an emergency – such is the idealism one has at university – but it led to my supervisor bringing me into another project.”
That project was a hydrogen sportscar being developed by the Morgan Motor Company (the company is featured in our Dossier on p20), as part of a wider consortium that included other rising names in the EV world, such as Riversimple (see Issue 10, summer 2021), whose technical director, Hugo Spowers, had a significant influence on Woolmer.
“I have huge respect for Hugo, because he comes from motorsport, and so understands holistic system design, weight distribution and other engineering disciplines vital for EVs,” Woolmer says.
“I was less enthused about hydrogen than he was, but I absolutely embraced his thinking around lightweighting and whole system design, centred around his ‘Mass Decompounding’ principle. If you can make one subcomponent lighter, say, dial back 100 kg on the motor, you make a lighter EV, which means you can use a lighter brake, suspension, chassis and battery pack. And, taking weight out of all those means you can switch to a lighter-still motor again, because you don’t need as much torque to propel the vehicle.”
With that principle in mind, Woolmer soon found himself undertaking his PhD project, focusing on traction systems for upcoming EVs and HEVs. Qualities he was particularly interested in were how they had been designed to reduce weight, and to increase both efficiency and manufacturability.
Softly, softly
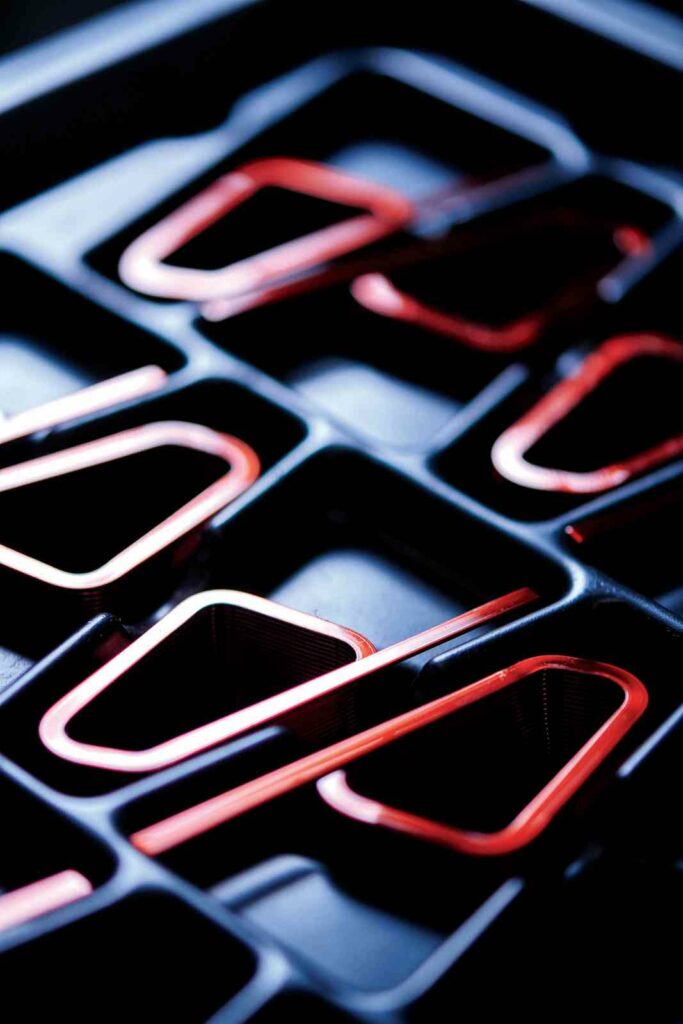
“That got me looking into electric motor structures, topologies, and components that could reduce their weight and size for automotive applications. I was especially interested in a material called SMC [soft magnetic composite], made by Hoganas in Sweden,” Woolmer says.
“Making e-machines with stacked, electric steel laminations limits you to 2D shapes, but SMC powder is effectively electric steel – just steel with a lamination-type coating around each piece of powder – and you can press it in complex ways to make 3D shapes. Early SMCs weren’t great, and in the 90s they were quite loss-prone, but they improved so much that by the end of my PhD, the best powders could work about as well as standard electric steel.”
One constraint on SMCs’ critical manufacturability advantage over laminations was the force it took to press them, and finding a press capable of making parts wider than 10 cm was difficult. So, Woolmer had to design his own topology of motor segments, by which a stator and rotor could be assembled from pressed SMC parts.
His supervisor pointed him towards axial-flux motors, suspecting that their shape and dynamics would work better with a segmented topology than radial-flux machines. Subsequent r&d led to Woolmer’s concept for what today remains the fundamental design philosophy of YASA’s motors, which can only be made with SMCs, but met all the criteria he felt were critical to future success in EVs, including light weight, power efficiency and cost-effective mass producibility.
“I stumbled upon this concept early in my PhD, so I got three years to build motors and inverters, and try them in cars. They were far from perfect, because I was, after all, just a PhD student without the massive resources of a real manufacturer, but, as stated in the final report, we achieved around 40-50 kW of continuous power from a 12 kg motor.
“That meant around 3-4 kW/kg in an e-motor in 2009, compared with around 0.6 kW/kg in a Toyota Prius’ motor, so we saw there was a huge difference this technology could make in the market, and we gained some seed money from the university to optimise our prototype into something more akin to a proper product. We ended up calling that product the YASA 750, and we still sell it today, 15 years later.”
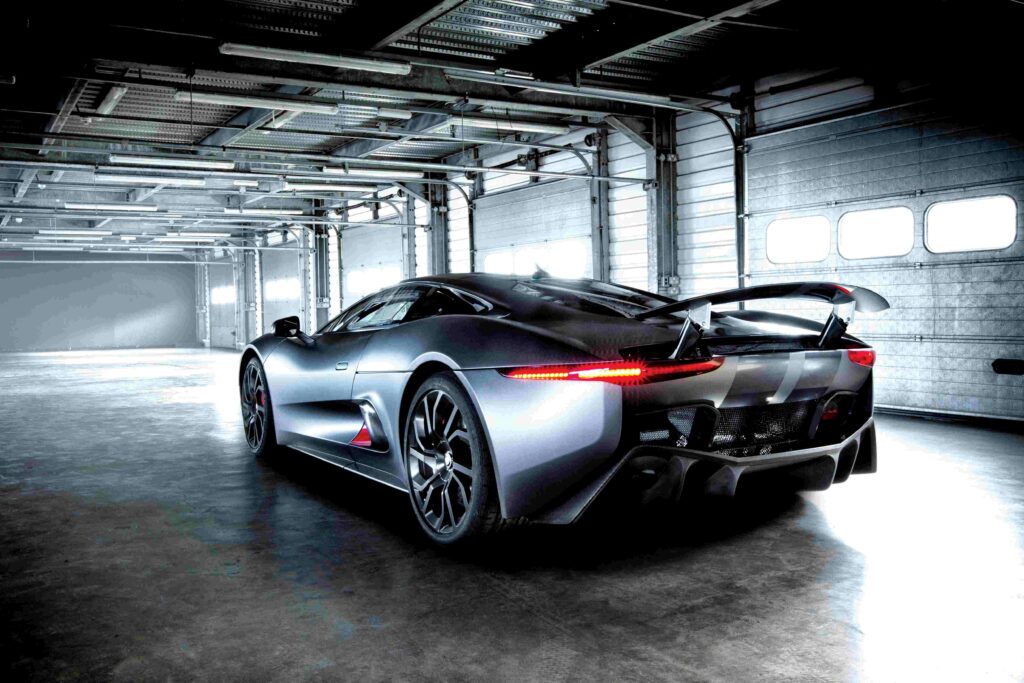
(Image courtesy of Jaguar)
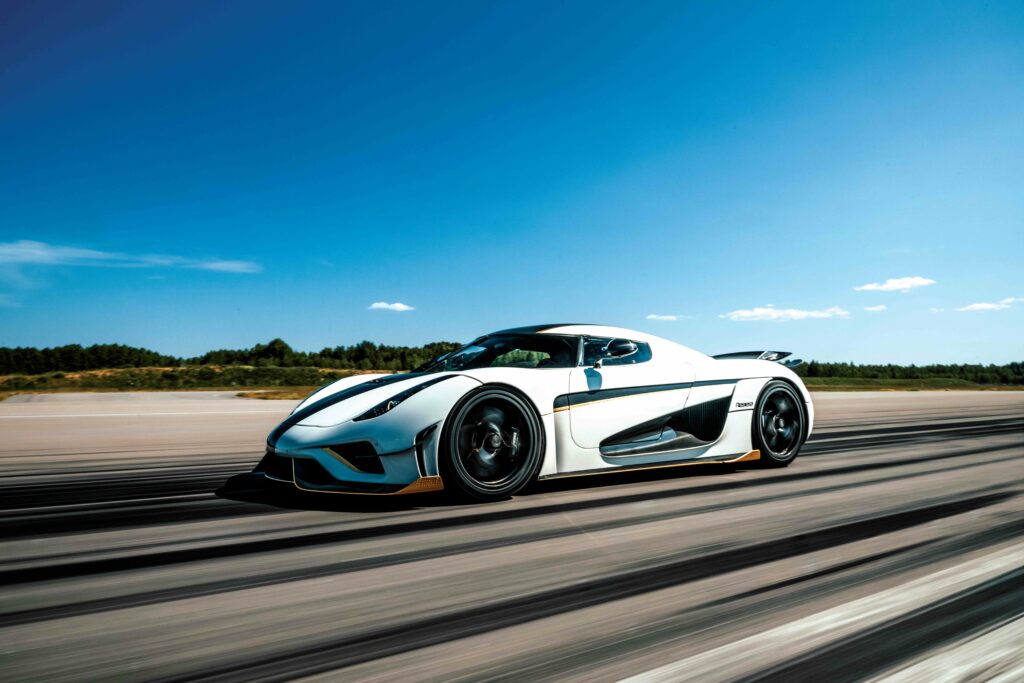
(Image courtesy of Koenigsegg)
Power in motion
Following these early designs, YASA went on to numerous successful collaborations across motorsport and commercial automotive. One was the CX75 Concept hybrid-electric sportscar, developed by Jaguar in partnership with Williams Advanced Engineering (now WAE). This concept HEV combined a relatively small, four-cylinder Cosworth engine with two electric motors: one rearward-mounted on the engine shaft for boost power and the other on the front axle.
“Their motor was the best in production at the time – a 50 kg, 400 Nm, American-made machine, which worked at 7500 rpm,” says Woolmer. “That was the spec they wanted, and we came back telling them we could do something similar, but weighing 20 kg.
“There were big challenges along the way, because the YASA 750 had been relatively high speed, low torque – about 2000 rpm nominal – and stresses increase with the square of speed in e-machines, but we soon demonstrated that the magnetics worked, and we could deliver the torque Jaguar wanted.”
Most critically, YASA went on to iterate six versions of the Jaguar project motor over the subsequent seven to eight months, solving problems and hitting new benchmarks along the way, thereby proving its capacity for rapid r&d and innovating crucial new forms of pole combinations, resonance workarounds, and cooling to reach the customer’s torque, power and packaging constraints.
For instance, when getting heat out of the stator proved impossible for the three-layer winding that YASA had initially opted for (specifically due to how hard Jaguar pushed them in testing), Woolmer and his team switched to an edge winding in which cooling fluid runs in contact with a single winding layer. A subsequent series of tip tests (consisting of about 10 rapid, 0-60 mph acceleration and braking cycles) by Jaguar found the new cooling design could withstand around 17 cycles without derating.
This has led to a cooling approach unique to YASA’s modern motors in which cooling oil flows directly past the copper, bypassing the many layers of epoxy, slot linings and jackets typically seen in radial machines, and taking advantage of the thinner componentry of the axial-flux topology.
“Jaguar were happy, henceforth putting our motors into five or six C-X75s to take to the press, with those cars performing fantastically, and then the project got cancelled,” Woolmer says. “It was meant to go into a limited,
250-unit production run and, for us, 500 motors would have been a big deal, but we’d still learned how to massively step up our capabilities and that of our technology, and it led a year or two later to our Koenigsegg project.”
By that time, Woolmer and his team had distilled these new capabilities into the higher-speed YASA 400, and Koenigsegg sought to install two YASA 750s on the rear axle of its Regera PHEV touring sportscar, with a YASA 400 on its engine. As both motors were now largely COTS products, this collaboration saw only minor modifications and custom work compared with the Jaguar and other projects. With around 200 Regeras meriting 600 YASA motors, this provided a vital runway for YASA to go on to work on numerous series-hybrid powertrains with McLaren, Ferrari, Lamborghini, and more.
“That took a new generation of technology and re-engineering, going from lab-built parts to something that could go down a production line – from bonding techniques to laser-welding, from machined glass fibres to moulded polymers, and so forth,” Woolmer says.
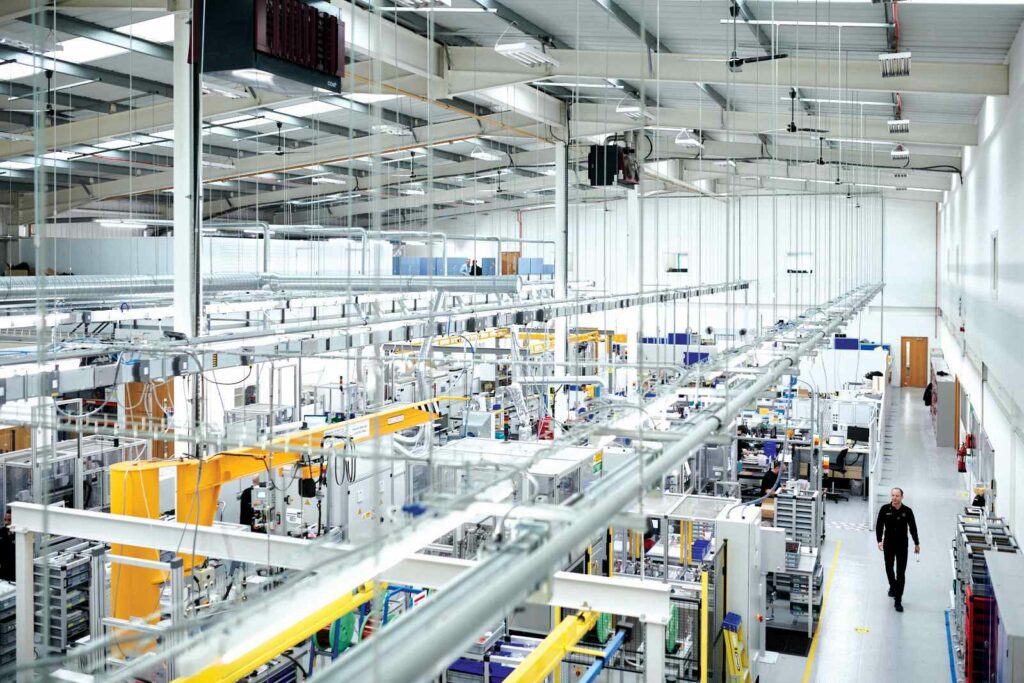
(Image courtesy of YASA)
Machines making machines
This new generation is enshrined in YASA’s facility at the Oxford Pioneer Park in Yarnton, Oxfordshire, which is the first model factory for producing its e-motors at scale.
“To get to where we are with this facility, it has taken a lot of inventing machines that could make our machines. People take for granted that there’s a pre-existing supply chain for everything we want to do, and there just wasn’t,” Woolmer says.
“Probably 70% of the machines in the factory have been designed by YASA’s automation team; the other 30% includes some COTS machines they’ve modified too. For example, we can use a balancing machine to balance the rotors – that’s a COTS machine and process – but the single-layer, edge-winding process for our stator coils was developed in-house, as was the way we impregnate them. We absolutely could not have afforded to go to a big automation consulting company to get a process developed for us, so making one in-house was the way to go.”
Further examples exist. For instance, approaches for laser-welding polymer components are widespread in automotive, but extremely rare in electric motor manufacturing, so YASA’s technique was also developed in-house.
Beyond this, the assembly of each motor design is an entirely YASA-patented series of processes, including the pressing of the aforementioned SMC blocks, copper winding, joint welding, enclosure moulding and welding, and various other bonding and coating techniques.
From Yarnton to Berlin
Naturally, a production run of Mercedes cars (and those of other OEMs interested in using YASA’s motors for their next-generation EVs) will consist of much higher numbers than the few hundred previously sought by Jaguar and Koenigsegg.
“Automotive does tend to be conservative when scaling up, and so you don’t really see new technologies going from zero to very high volume overnight,” Woolmer observes. “In my experience, one can go up by one order of magnitude at a time, but not two, so as the Yarnton facility can produce tens of thousands of motors per year, our next act could see us ramping up to something in the hundreds of thousands, but not the millions just yet.”
He says part of YASA’s remit from Mercedes is to remain reasonably agile and innovative in e-motor development in order to maintain a technological edge in electric propulsion, while the German parent company provides an easily adjustable lever of industrial capital and know-how to scale up when it is deemed optimal.
“Mercedes really knows how to build factories, how to write 500-page specifications, how to optimise the perfect mass-manufacturing machine – none of that is YASA’s heritage. So, we’ve worked extremely closely with Mercedes over the last three years, and now they’re converting one of their factories in Berlin from making ICEs to making YASA products in the hundreds of thousands,” Woolmer notes.
“Most of the processes you’d find in Yarnton, you’ll find in Berlin soon, but they’ve all been polished, optimised and scaled. A lot of what is performed manually in Yarnton has been automated in Berlin, meaning less manual handling, less pushing of goods on trolleys, more conveyors and robotic arms. Doing that takes a lot of money, because automation is expensive, but that was always the vision for working with Mercedes: to scale the technology.”
While not an official plan, Woolmer acknowledges that after producing hundreds of thousands of YASA motors, the next stage will be to output millions. The fundamental question prior to making that great leap will revolve around whether the best place for its axial-flux machines is in high-performance sports EVs – Mercedes’ main motivation in acquiring YASA – or whether new roots will be found to justify scaling this up to millions for mainstream automotive.
“It’s too early to tell just yet, but as we watch our technology getting scaled up, and how Mercedes is pulling that off, you really start to get a sense of Mercedes’ strengths, and that even though developments in Yarnton and Berlin are both going great, we’ve not hit our sweet spot just yet,” concludes Woolmer.
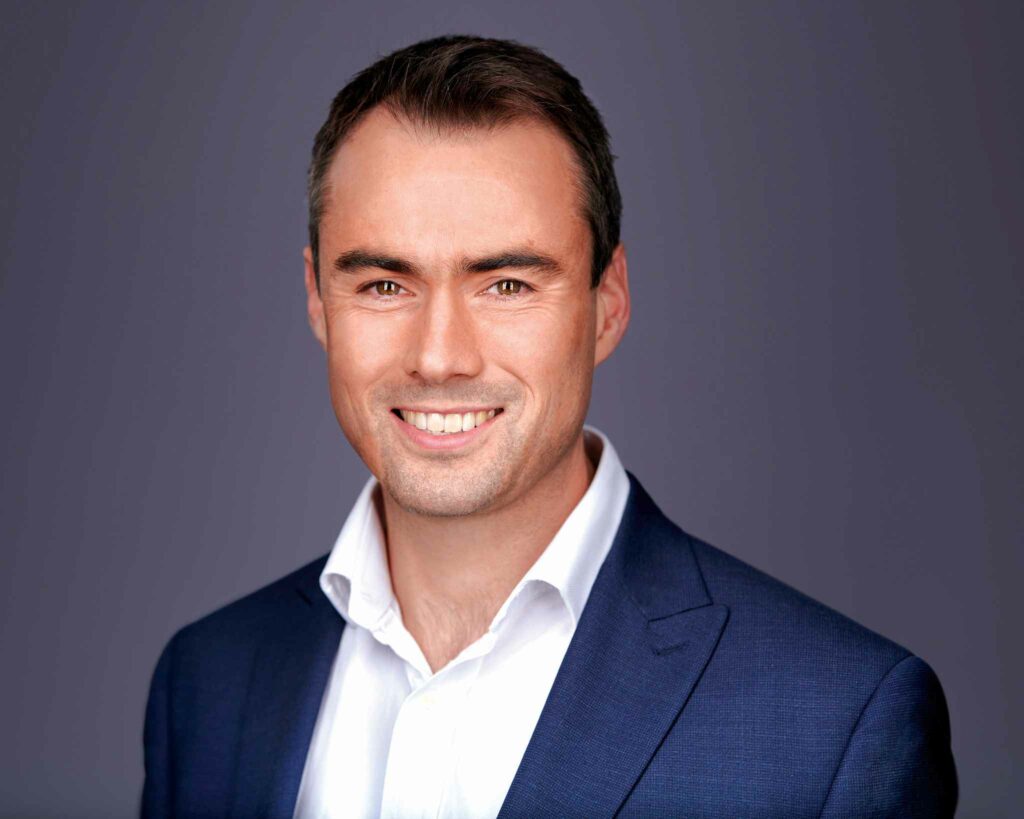
Tim Woolmer
Tim Woolmer was born in Oxford, UK, and he grew up in Somerset in the southwest of England.
After attending various local schools in that portion of the country, he returned to Oxford at the age of 20 to begin his undergraduate (Bachelor’s) degree in Engineering with Science.
Woolmer continued his studies at Oxford University for some time, going on to do his PhD there from 2005-09. He founded YASA in the same year that his course finished.
With his colleagues, he went on to develop axial-flux e-motors for numerous partners across the motorsport and automotive worlds, as well as acquiring more than 150 patents for the yokeless and segmented armature that YASA’s name is derived from, and with which its motors are engineered.
In 2018, the company opened its first series production facility in Oxfordshire, capable of outputting up to 100,000 units per year, and it officially became a wholly-owned subsidiary of Mercedes in 2021. That same year saw the spin-off from YASA of Evolito, for the latter to develop the former’s technology in an aerospace capacity, which Woolmer also works with and supports.
Click here to read the latest issue of E-Mobility Engineering.
ONLINE PARTNERS
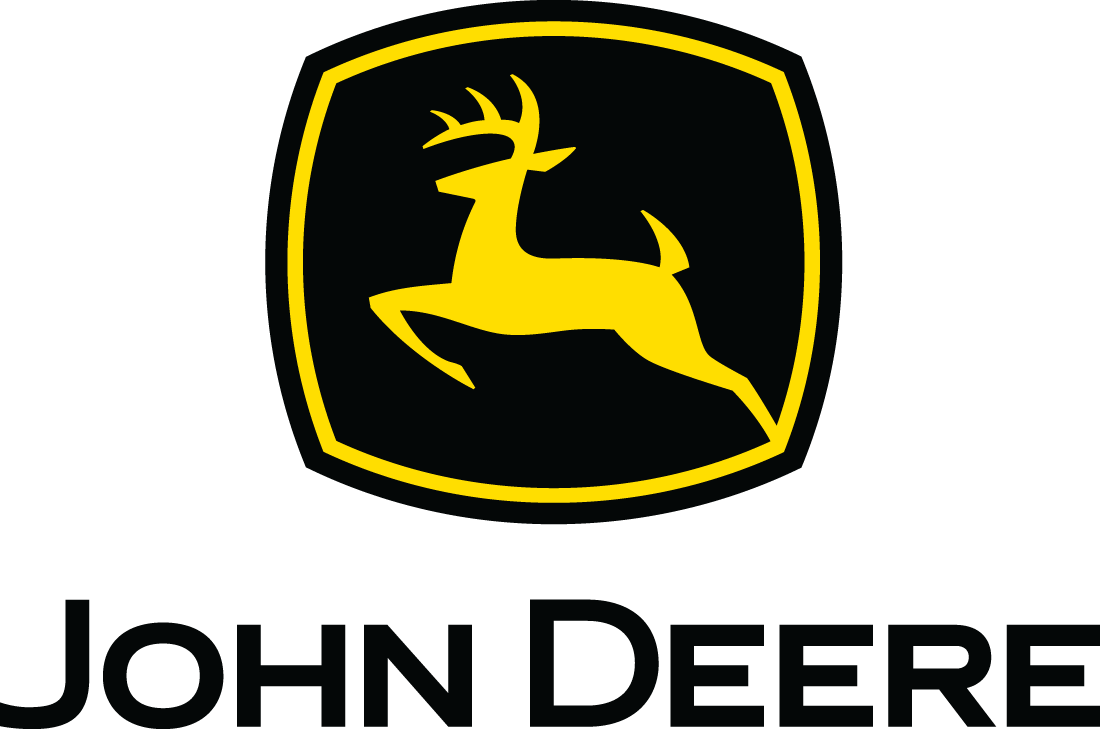
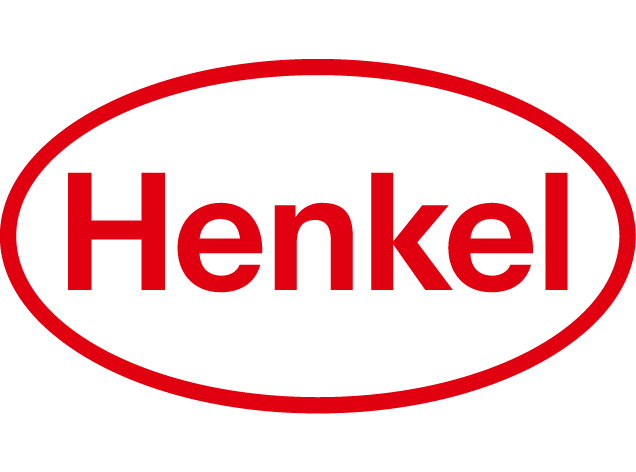
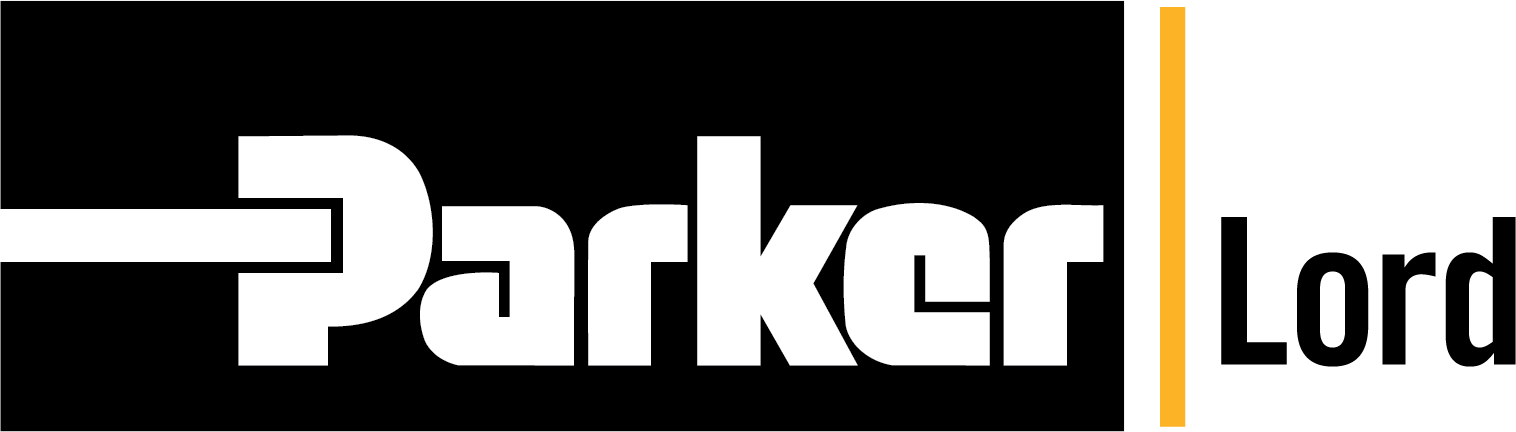
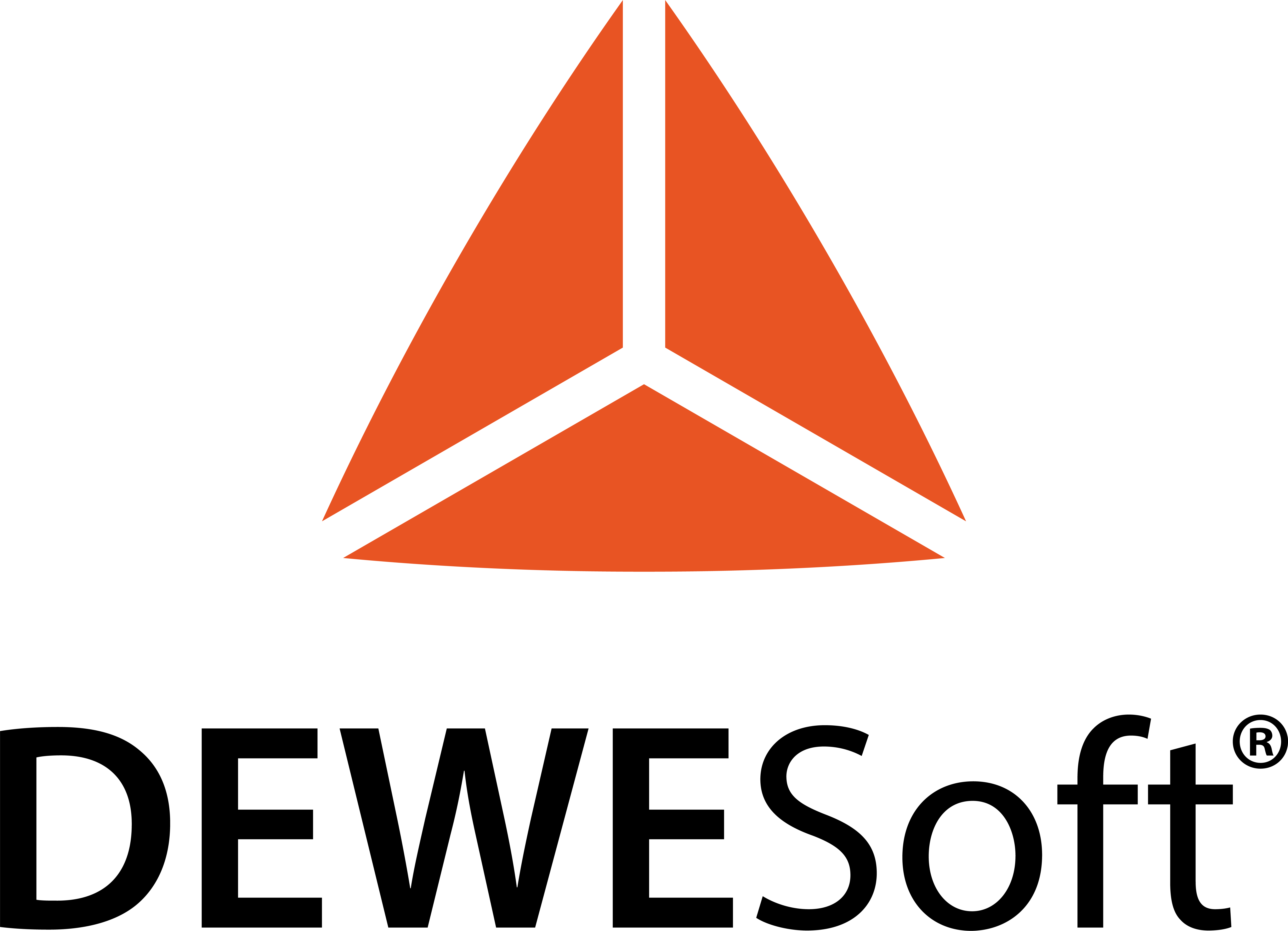
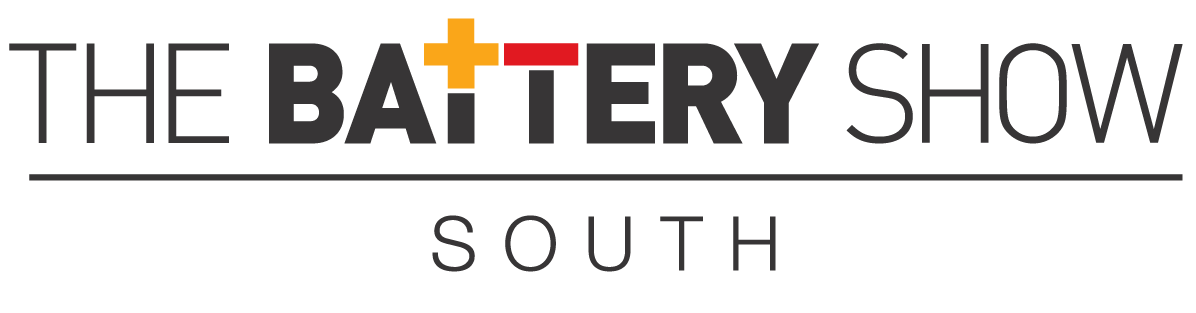
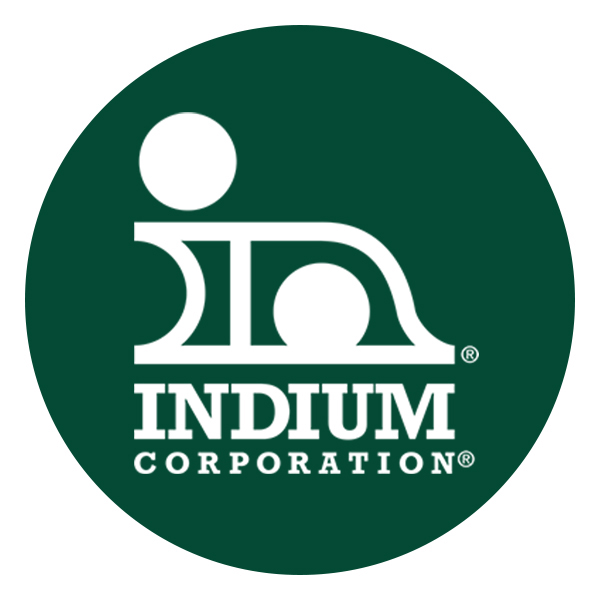
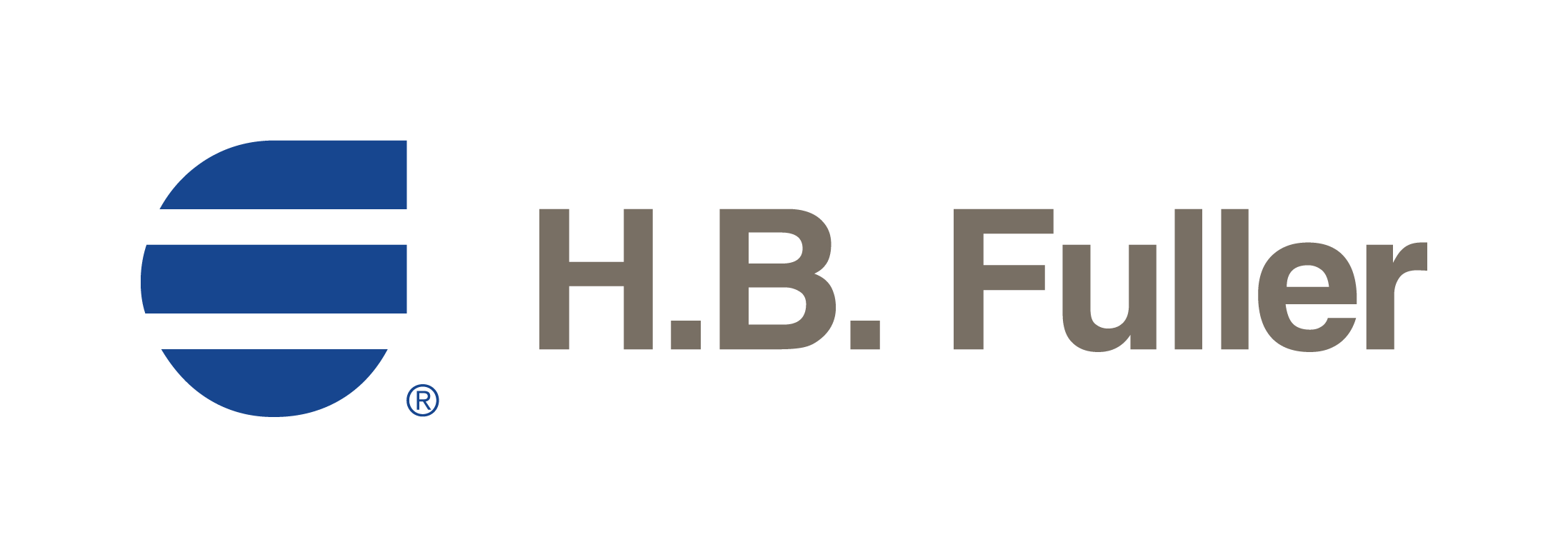