Thyristors save space in charger
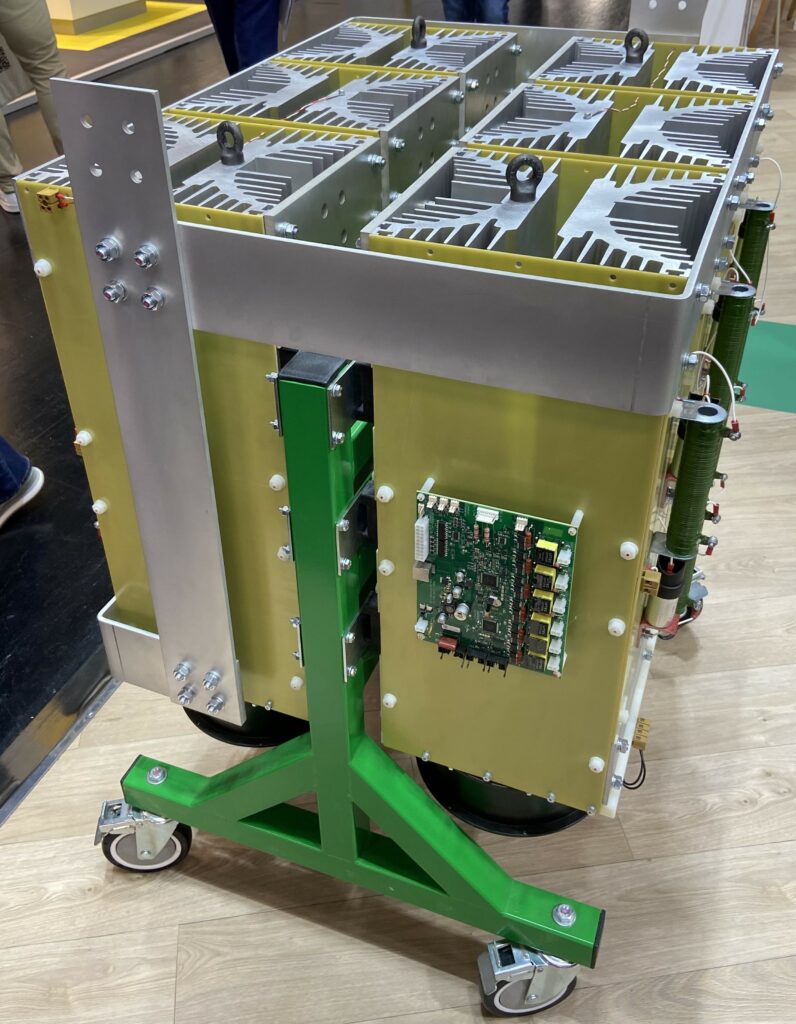
Littelfuse has developed a reference design for a 2 MW bidirectional fast charger for commercial vehicles (writes Nick Flaherty).
Rather than using MOSFETs, the 12-pulse thyristor stack can support a 2 MW output in a smaller volume with just forced-air cooling.
Five 70 kW modules using thyristors that are stacked to provide 350 kW occupy 0.175m³, excluding any pumps and radiators needed for cooling the circuit. For a dual 350 kW charger, the minimum space consumed is a cube with 1.5 m sides and a volume of 3.4m³. This volume includes the power electronics, the cooling system and auxiliary systems.
In comparison, the space required for a MOSFET-based AC-DC converter design is 35 litres for a 70 kW module that can fit into a 483 mm-wide rack with an 800 mm depth and two height units, said Dr Martin Schulz, global principal, application engineering, at Littelfuse.
The thyristor approach uses design techniques from high-power electrolysis systems using a circuit topology based on thyristors. Here, a 12-pulse bridge rectifier configuration implements a single stage with the same size transformer as a MOSFET-based design of equivalent power. The space savings come from the thyristor topology, which can be as small as 10% of the size of a scaled-up MOSFET design.
Dr Schulz expects battery voltage packs for commercial vehicles to reach 1.5 kV, which would put more pressure on the charger design.
With the thyristor-based, battery-equipped circuit topology, the charger can either relieve the grid of peak demand or supply stored energy to the grid. Unlike the thyristor designs, the rectifier design of the MOSFET-based chargers is not capable of returning power to the grid.
In contrast, the firing angle of the thyristors determines whether the circuit dispenses DC power to a battery or AC power back to the grid. If the firing angle is less than 90º, the thyristors are in the rectifier mode; when it is between 90 and 180º they are in inverter mode.
Using an appropriate power thyristor that can deliver over 1000 A with a conducting state resistance of around 1 mΩ, a B6-configuration bridge circuit can output 1.1 MW with only 2200 W of internal losses. The resulting efficiency exceeds 99.7%.
The thyristor-based design also needs much less space. A 2000 V B12C stack capable of outputting 1700 A has the dimensions as shown above. Two of the air-cooled units require 0.4 m3. By eliminating liquid cooling and the corresponding pumps, tubes and chillers, the thyristor-based design reduces the installation space from about 6 m3 to less than 1 m3, saving 83% of the space needed for installation.
A 2.4 MW thyristor-based charger can transfer 400 kWh into the battery pack of a long-haul EV within 10 minutes. Assuming the charger provides a 10 minute charge for three vehicles in an hour, over 24 hours, the charger could supply 72 vehicles a day.
It can also reduce the losses incurred by a MOSFET-based charger by 90%. The lower cooling demands on the charger power electronics further reduce energy consumption.
ONLINE PARTNERS
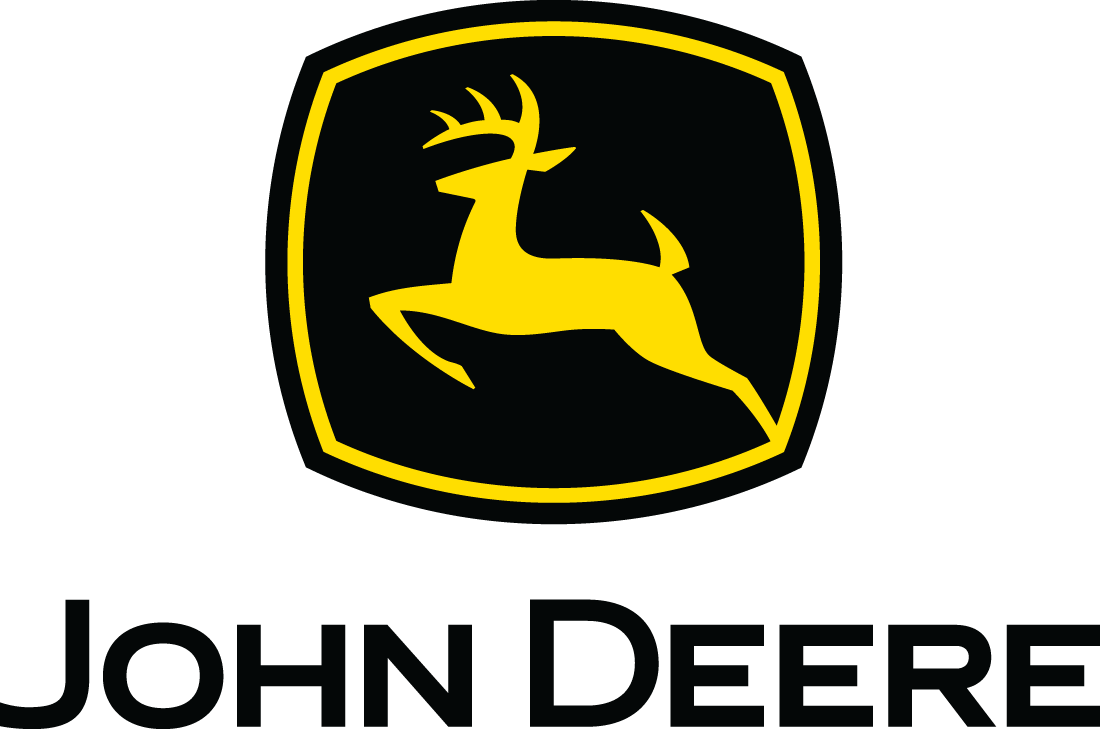
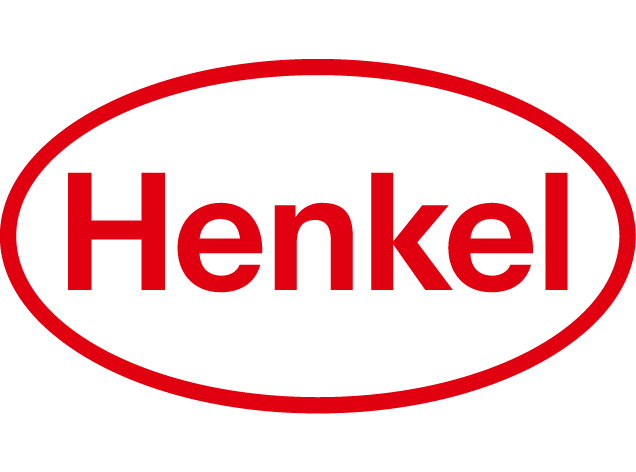
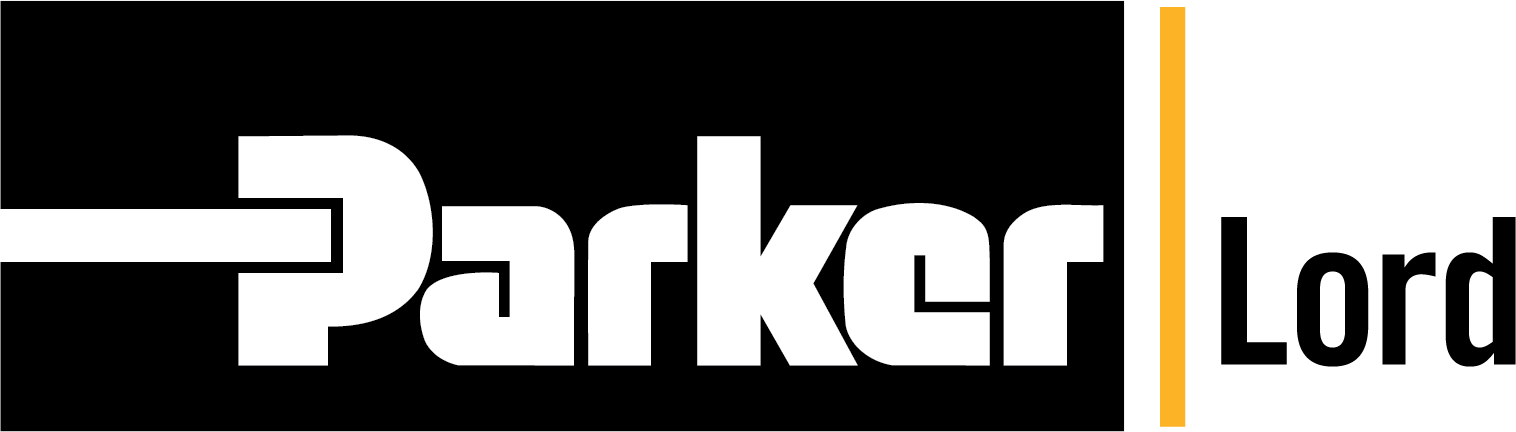
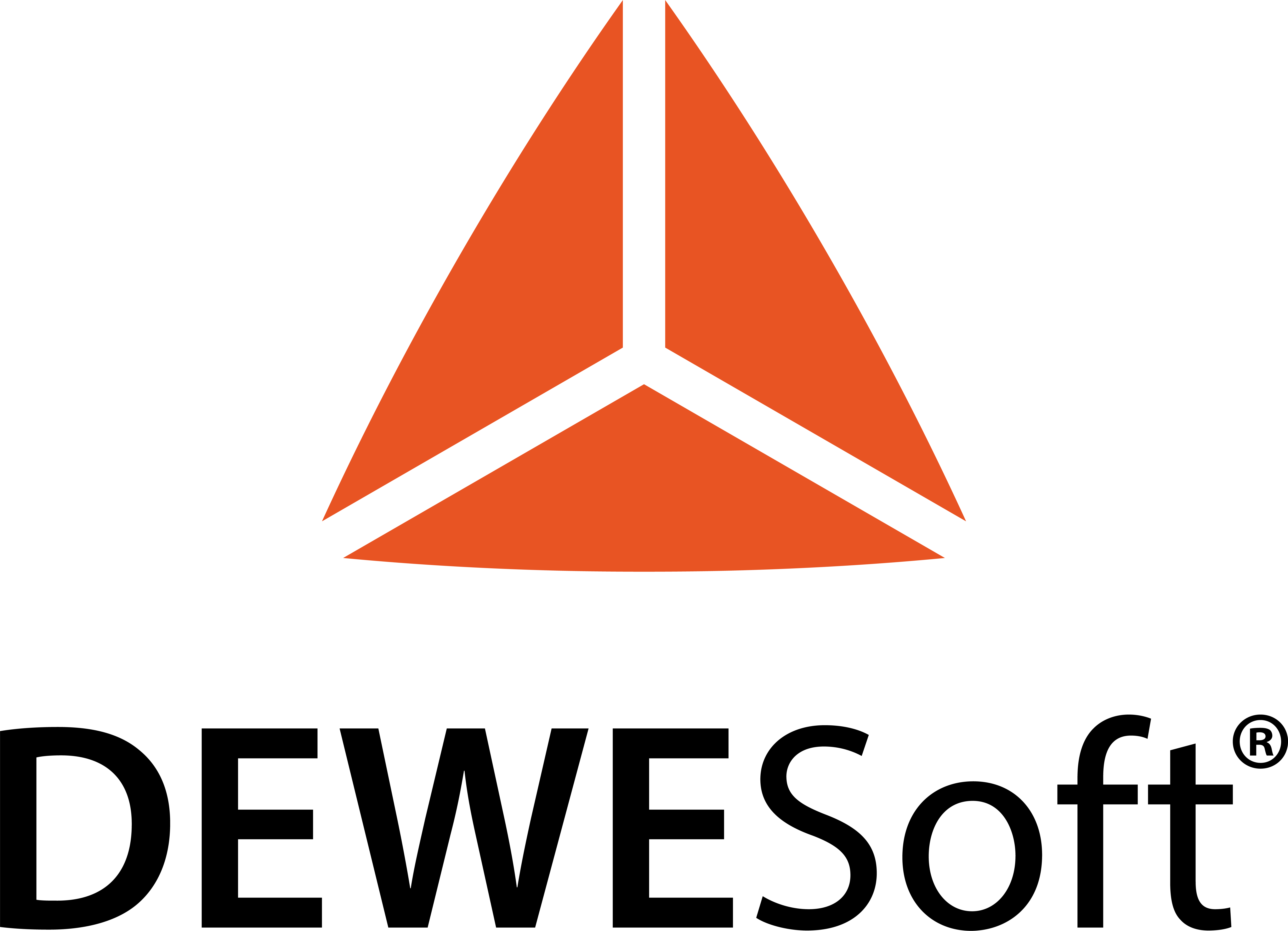
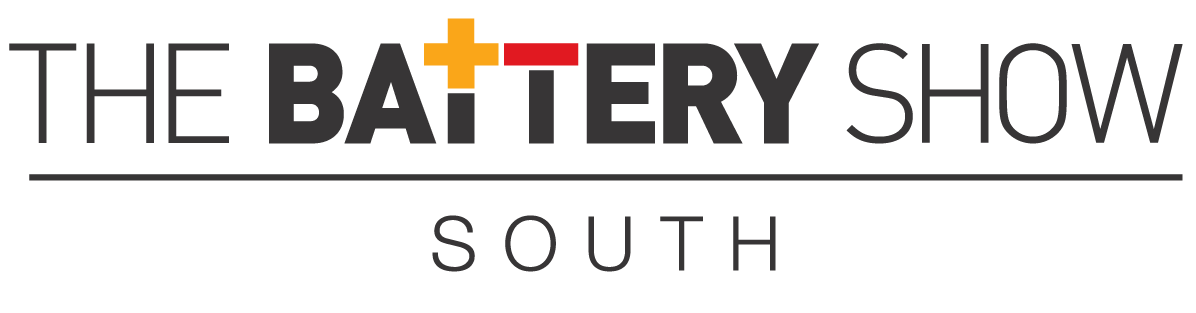
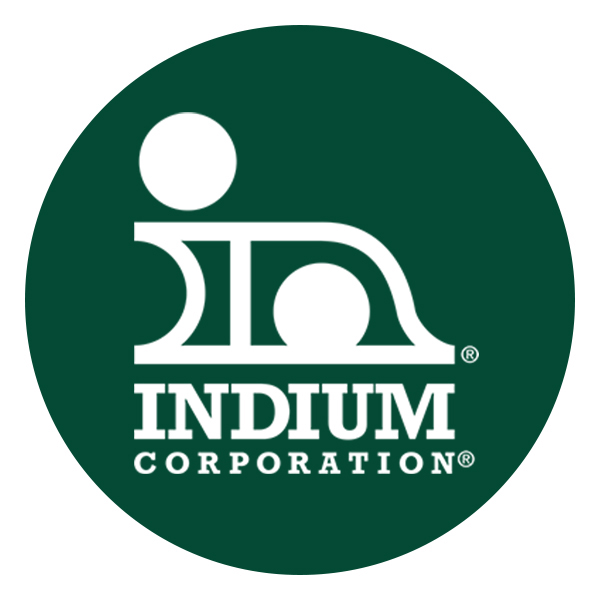
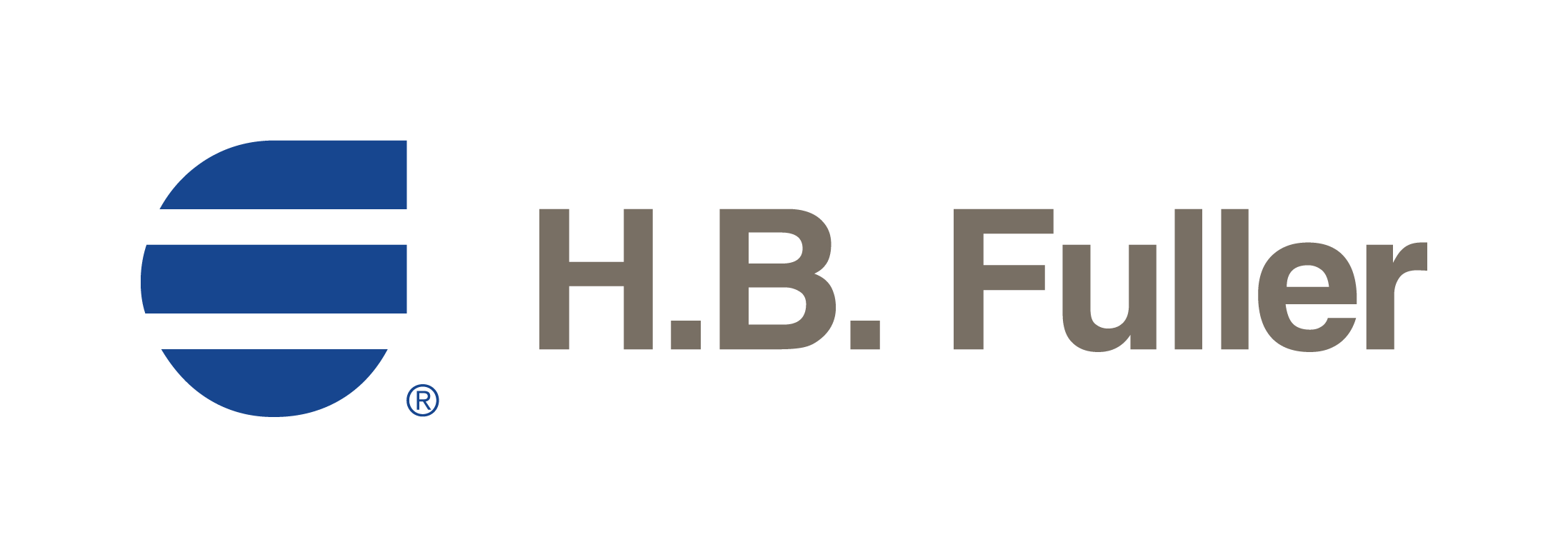