Thermal runaway prevention
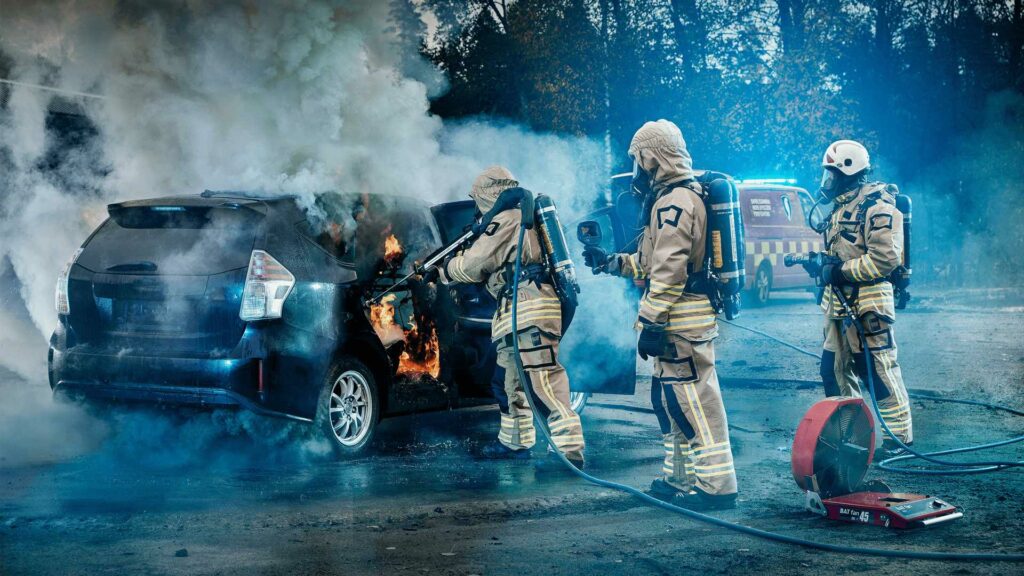
(Image courtesy of Coldcut Systems)
First line of defence
Peter Donaldson speaks to experts who are working on cell design and chemistry to avoid thermal runaway
Protection from thermal runaway in an electric vehicle (EV) battery requires a holistic solution that affects every aspect of the pack’s design and operation. The consensus seems to be that protection options are limited to prevention and mitigation rather than stopping a runaway once it has started.
Prevention begins with cell design and chemistry, while stopping propagation from the initiating cell to its neighbours involves pack and module design. Many aspects of design, including chemical, structural and electrical/electronic have an impact, and measures external and internal to the cell can be applied, including rapid cooling, fuses, built-in shutdown mechanisms and venting. We quizzed leading experts in these areas.
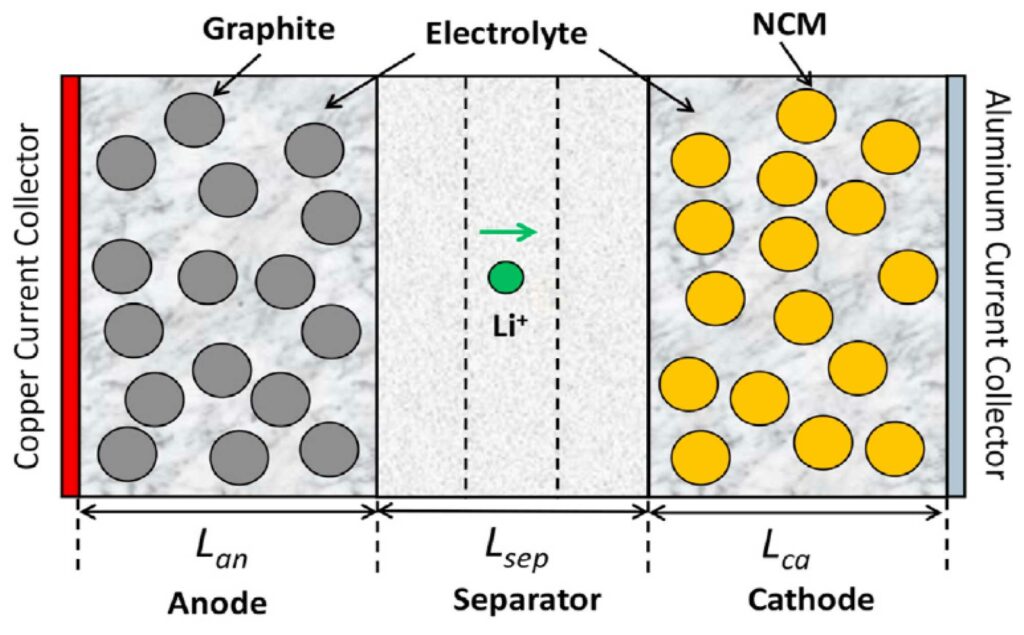
Starting with the cell
Cell engineering and electrochemical development are vital to reducing the probability of thermal events. Any measure that reduces the likelihood of dendrite formation would be a good starting point; for example, special coatings on electrodes, electrolyte formulation, etc. Stringent quality control on assembled cells is also critical to minimise any latent manufacturing defects that could lead to internal shorts and eventually a runaway.
Cell chemistries behave differently in thermal runaway. Lithium iron phosphate (LFP), for example, has maximum temperatures of about 600 C, significantly lower than nickel manganese cobalt oxide (NMC) with over 1000 C, an expert says. “The particle ejection of an LFP cell is also not as strong as with an NMC cell. This leads to different impacts on the environment in the battery (in terms of propagation), but also in terms of the risk to the occupants.”
Normally, the lower energy density chemistries, such as LFP and low nickel content NMC cells, present significantly lower risk, even if one of the cells catches fire, as the adjacent cells are less likely to fail.
The fundamental properties of different cell formats and sizes also have to be considered, another expert says. For example, cylindrical and prismatic cells have a vent due to their design, which means a runaway can be better prevented with the support of a current interruption device. Smaller cells have a lower capacity and therefore store less energy. In this respect, the influence of a thermal runaway of a smaller cell is less than that of a larger one.
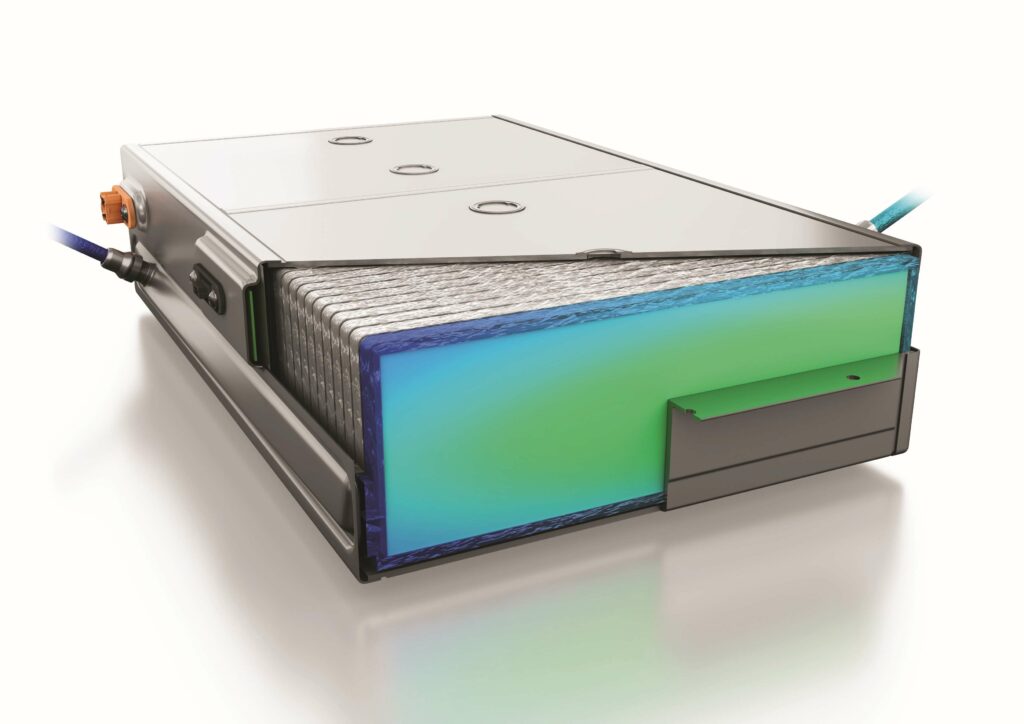
(Image courtesy of Mahle)
Pack factors
It is critical that good assumptions are made in the initial pack design for the volume and performance requirements of components, from cell to pack level.
“Far too often, we work on projects where ambition has met reality and it is necessary to ‘fire fight’ to address unforeseen issues,” another expert says. “There is still a skills gap in the industry for how to properly design and integrate batteries into a vehicle, and certainly, this will improve with time as OEMs and engineers gain experience.”
There must be a plan for what occurs during thermal runaway and the pack design must reflect that, a further expert says. The primary enemy is heat – heat generated within the cell, as well as that carried by the gases produced by the failing cell.
“The thermal management system is solely responsible for dissipating the heat conducted/convected from the cell. Dissipation of the heat will mitigate the temperature rise in neighbouring cells and reduce the chance that they enter thermal runaway.
“The gas is more difficult to deal with, as it is hard to limit the interaction of the gas with the rest of the battery pack. This is where battery pack engineering comes into play. The solutions vary substantially due to the shapes, sizes and chemistries of the various types of battery cells used,” he says.
“Compared to cell-to-pack (C2P) architecture, a module-based pack design means there are additional components in the battery pack that intercept particle ejection in particular, so the pack lid is not directly affected. This ensures the influence of the thermal runaway on the pack housing is reduced,” notes another expert.
Proper battery management, and vehicle energy and thermal management are critical to ensuring each cell in a pack is operated within safe limits. It is also critical to avoid high thermal stresses that could lead to excessive heat that cannot be removed if the thermal management system is not operating properly immediately after the vehicle has been driven hard or charged rapidly, another expert cautions.
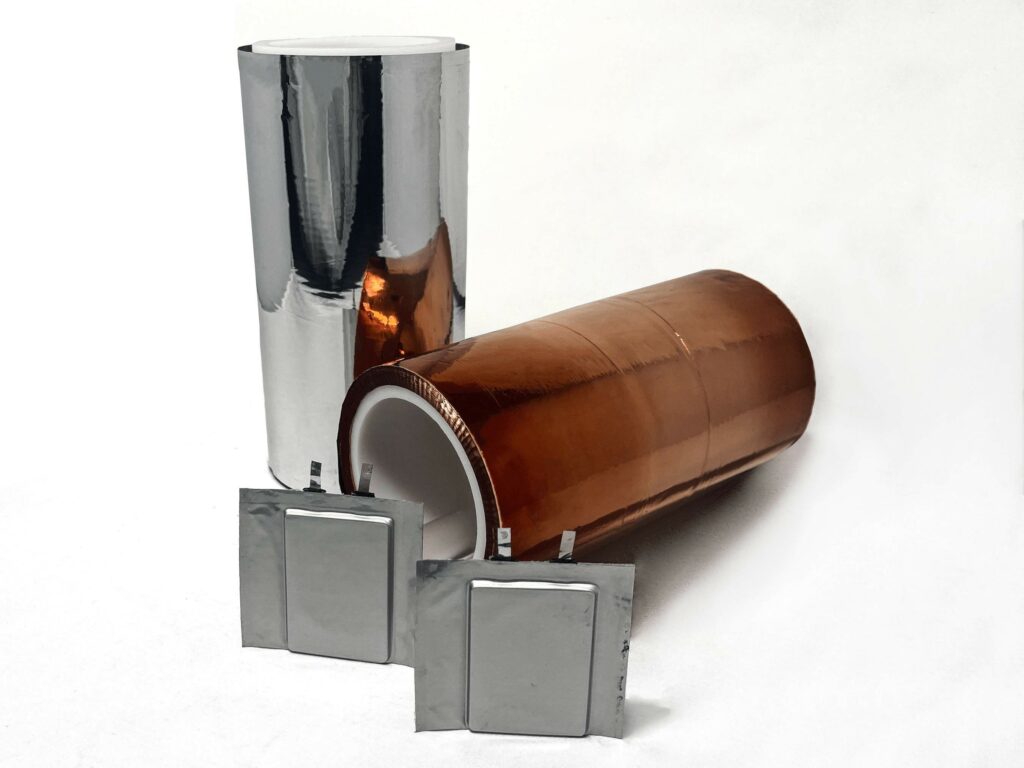
(Image courtesy of Soteria)
Immersion cooling
Immersion cooling, a technology borrowed from the IT domain and used in data centres, provides excellent thermal management and mitigation of thermal runaway propagation.
“The increased surface area for heat transfer, and the direct contact between the cells and coolant ensures maximum heat transfer,” an expert says. “The drawbacks are the lack of familiarity with immersion cooling and the weight of the fluid. Water-glycol indirect cooling has been used for decades and OEMs are very familiar with the technology, but immersion is new.
“Additionally, the expectation is that the mass of fluid added will outweigh the water-glycol currently used, as well as the weight of the aluminium cold plate and thermal interface material. A comprehensive study and demonstration have yet to be done, but the sentiment still exists in the industry.”
The main drawbacks to conventional, indirect cold-plate cooling are the limited surface area for heat transfer, and the amount of material between the hot battery cell and the water-glycol coolant, another expert says. One approach to increasing the amount of surface area is a ‘3D’ cold plate or multiple cold plates.
“Rather than cool the batteries just on one side, there could be cold plates on the top and bottom of the cells, or cooling ribbons and cold plates could be used in conjunction. The drawback to this is the complexity, weight and cost of implementation. Adding a second cold plate will double the weight and cost of the thermal management system, as well as increase the manufacturing complexity,” he says.
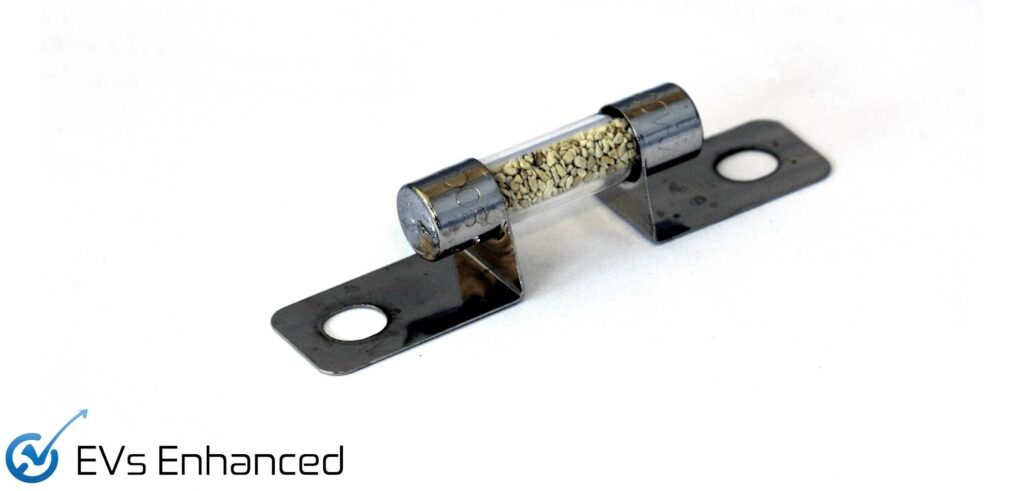
(Image courtesy of EVs Enhanced)
Thermal insulation
Radical use of thermal insulation is another mitigation approach, the expert adds, elaborating that cells could be thermally isolated from one another by using insulating foams, sheets or resins.
“If the cells are thermally isolated from one another, the risk of propagation disappears. The consequence, of course, is that a thermally isolated cell is equally difficult to cool since it is isolated from the coolant system as well. This will minimise the amount of heat that can be removed from the cells, which will ultimately limit the rate at which the cells can be charged.
“This type of system will certainly not be implemented in any sort of fast charge or discharge system.”
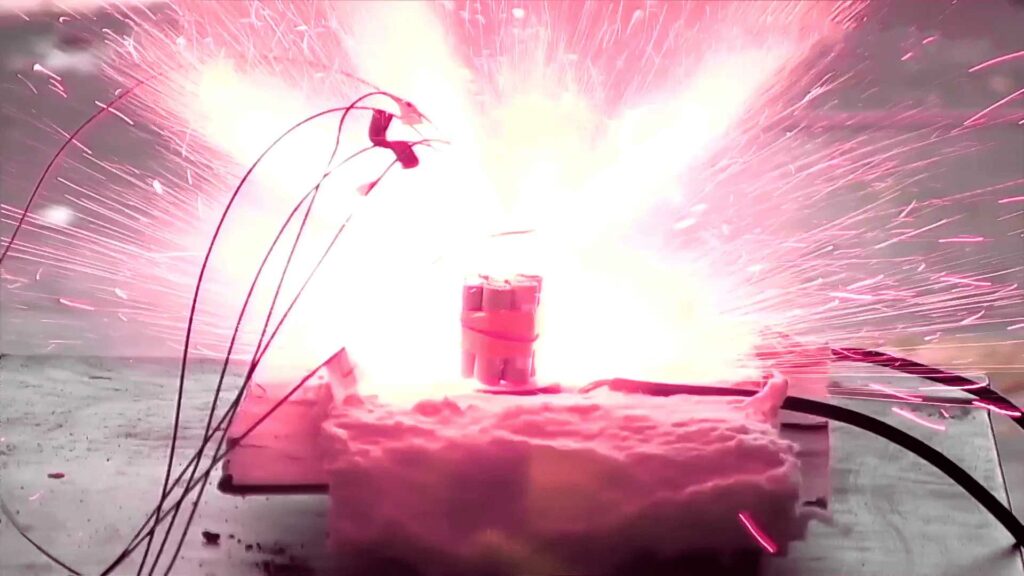
(Image courtesy of US CDC)
Mitigation options
While it might not be possible, for the moment, to stop a thermal runaway in a cell, it is practical to isolate the problem to the cell in which it started, or at least to a small group of cells immediately around it.
In the earliest stage of a developing thermal runaway, the electrical aspects of the cell are most important, another expert says. An immediate stop to charging or discharging can reduce the risk of an uncontrolled release of heat inside the cell. Commonly used technologies include thermal fuses, positive temperature coefficient (PTC) current-limiting devices and fail-safe separator membranes.
A thermal fuse, as the name suggests, is a fuse that melts and stops the flow of current to and from the cell permanently when the temperature reaches a set limit. For redundancy, these can be used in conjunction with metallised film current collectors, which essentially work in the same way.
PTC devices are made from materials that exhibit a sharp increase in resistance when the temperature rises above an engineered-in threshold, limiting the current flow and helping to prevent a further rise in temperature. In a cylindrical cell, such as an 18650, the PTC device is built into the top cap and positioned in the cell’s main current path.
It consists of a non-conducting, crystalline polymer material with a granular, conductive material such as carbon black embedded in it. Current passes through the device in normal cell operation, but if it gets too high the polymer expands in response to ohmic heating, progressively moving the conductive particles apart, which increases resistance and eventually disconnects the conductive path. Unlike a thermal fuse, the action of a PTC device reverses as the material cools down.
Typically made from polymers such as polyethylene or polypropylene from composites that combine polymers with ceramic and other additives, and even from structured nanomaterials, the separator membrane prevents electrons from flowing directly between the anode and the cathode, thereby forcing the current to pass through the external electric circuit and the load, while allowing the ions to pass through. Increasingly, separators are designed with in-built thermal, mechanical or chemical shutdown mechanisms for safety.
For example, some separator membranes are designed to undergo a phase change at high temperatures, physically blocking the flow of ions through the cell, and consequently stopping the flow of current through the external electric circuit. This prevents further heat generation within the cell. Mechanical shutdown mechanisms respond to excessive pressure within a cell arising from gas generation during an incipient thermal runaway by deforming to block ion flow.
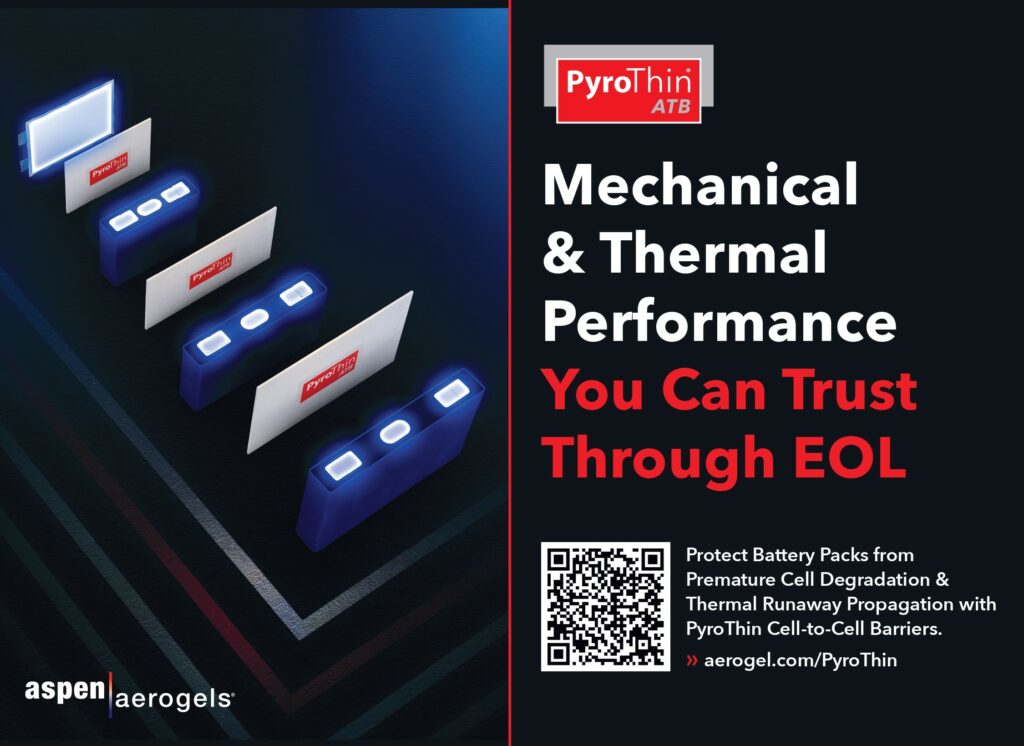
Essentially, the same job can be done chemically through the inclusion of additives within the separator that respond to abnormal conditions, such as excessive temperatures or charge states, by undergoing chemical reactions that lead to increased resistance or ion-flow blockage.
It is important for the cell that has entered thermal runaway to be vented in a controlled manner to relieve pressure. Bottom-venting cells are a useful advance in design. They can discharge their exhaust gases down through a perforated cooling plate, making the gas management problem much easier to solve.
Venting is just as critical in other areas of the pack. Pressure relief valves protect housings against mechanical damage that may occur in the event of pressure differences between the interior of the housing and the environment. They also seal against external liquids and dirt.
One company we consulted has developed a new pressure relief valve for venting battery housings in case of sudden overpressure due to thermal runaway, which helps to prevent thermal propagation.
Protection of surrounding cells from the effects of heat and particle bombardment from a failing cell requires heat-resistant materials with low thermal conductivity and high mechanical strength.

(Image courtesy of Eatron)
Propagation barrier materials
Typically, there are five main challenges involved in preventing propagation during thermal runaway, an expert says, and the selection of materials has an impact on all of them.
The first is conductive heat transfer from cell to cell, while heat transfer through secondary components such as module housings is the second. The third is the ejection of hot gas and/or flame from the failing cell, which heats adjacent cells. Particles ejected from the cell, causing failures in adjacent cells or modules through short-circuiting, for example, pose the fourth.
Finally, electrical arcing can damage nearby cells and other components, and ignite flammable gasses, an expert says.
“Typical solutions for cell-to-cell heat transfer include aerogels and silicone foams, with aerogels significantly increasing in market share due to their strong performance. Other solutions are being developed, depending on cell format, such as potting resins and silicones.
“The other issues are best addressed using robust thermal and electrical insulation, varying depending on the position of use and the properties required, such as processability and dielectric properties,” the previous expert says. “A large suite of solutions is available, such as mica composites, carbon-fibre composites, meta-aramids, polyimides or moulded plastics, all of which depend on the requirements at part level as to which is most suited.”
The two most commonly used containment and mitigation measures are thermal propagation protection between modules and cells, and the other is fire containment within the pack, notes another expert. In the first solution, aerogel, mica or fire-resistant foams are used between cells or modules to minimise heat transfer. For the second measure, fire-protection pads or coatings are applied on the casing area, such as the battery lid, to minimise the heating of the substrate and prevent burn-through.
In pouch or prismatic packs, ensuring a thermal runaway is contained to a single cell or a group of cells requires a high-temperature thermal insulation, such as an aerogel, to act as a firewall. A cell-to-cell barrier acts as the first line of defence.
Any measure that could immediately change the temperature, cut access to oxygen within the cell, and immediately drain or dry the flammable electrolyte could help in theory,” another expert says. “But in practice these measures are not really widely available; hence the focus should be on containment.”
Another option is rapid cooling, which prevents further propagation and can sometimes even stop the runaway. Rapid cooling can be practical in certain applications, such as stationary storage or commercial vehicles with segmented energy storage, according to an expert.
“The main barrier is ensuring the cooling system is sufficiently isolated from the thermal runaway event to remain active, and ensuring there is enough cooling power from the system available to arrest the event and extract heat driving the process,” he adds. “This is often only practicable in an automotive application using immersion cooling, which remains an engineering challenge to produce efficiently at large scale with an acceptable cost and weight for mainstream applications.”
In addition to the density of the cells and modules in the pack, and the insulation between them and on the lid, the material of the lid itself is important to containment, the expert says. One common choice is electro-coated steel with a melting point above 1,500 C, while other substrates such as aluminium and some polymer composites have much lower melting temperatures.
Also important are interface materials, including adhesives, with high thermal conductivity to ensure good heat transfer from the cells to heat sinks or cooling plates. Preventing unwanted heat transfer with materials, such as thermally insulating materials and flame-retardant barriers placed between the cells, is also critical.
Such materials include silicone potting, and foam sheets placed between the battery cover and the cells. Silicones do not generate toxic smoke, so they help provide extra time for passengers to exit the vehicle once a runaway has started, notes an expert in these materials.
Further, electrical insulation between cells using coating or other barriers is vital to prevent electrical short circuits or arcing between cells and other electrical components.
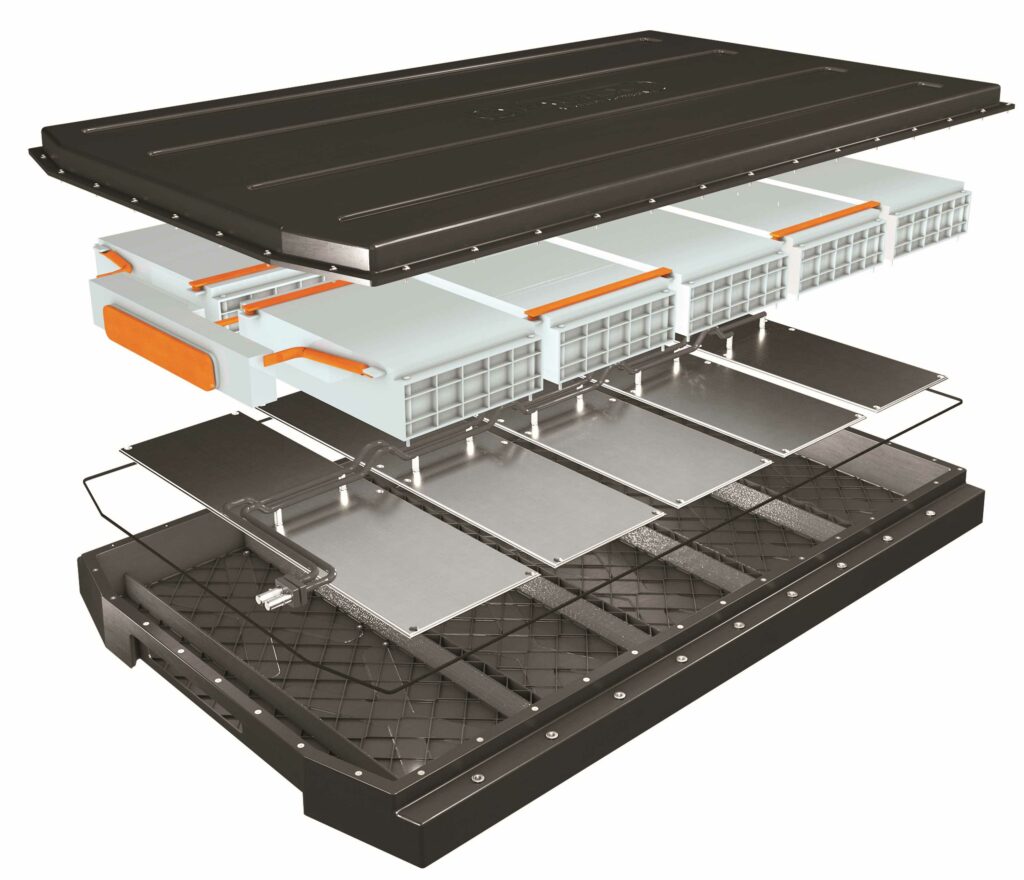
(Image courtesy of LANXESS)
Material advances
Progress in the materials used in cells and packs has been substantial in recent years, but there is more to come. As the industry develops new and better materials to include in battery packs, they must be thin enough to fit into the tight gaps between cells, or between the cell and cover, to maximise pack-level energy density without compromising their runaway mitigation performance. Because thermal runaway presents both fire and electrical hazards, multifunction materials that can withstand high temperatures and achieve strong dielectric performance are becoming increasingly important. Furthermore, the material should be easily applicable at industrial scale through automation.
Our expert’s company is active in passive fire-protection coatings that are only activated during a thermal runaway event, so they can maintain a low thickness at ambient conditions. The material is mostly applied in areas where the substrate needs to be insulated, such as the battery cover/lid or frames, or the module cover, he explains.
One such coating can be triggered by heat exposure. It absorbs heat for phase-changing and forms a foam-like structure with air pockets to insulate the substrate from fire. The expert says it contains thermal insulation/heat-refractive pigments to minimise thermal conductivity, which minimises heat transfer from the cell fire to the substrate.
He says the material can be sprayed via airless application or flat stream/dispensing, and it has already been industrialised for years on customers’ automated lines.
More recently, the company has developed a new coating with similar insulating and protective capabilities, but it expands much less during a thermal runaway so that it fits into compact battery designs better. It also offers much better dielectric insulation performance and durability against ageing, the expert adds.
Besides aerogels, a wide range of materials – from mica, CFRP and metals as barriers to foams as cell-level insulation and propagation mitigation – are either proposed or in active use today, an expert says, adding: “Foam has been one of the most promising approaches and, although the idea originated in the 2010s, it has just recently been put to use by Tesla.”
Silicone is well positioned for the compromise between density, fire protection, thermal resistance and mechanical properties. Foams formed from silicone are also very light, contributing to weight savings in the battery pack.
Further, their application is easily automated, our expert says, as their two liquid components are mixed and injected into the pack, flowing and expanding to fill the gaps between the cells, and curing at room temperature if required by the manufacturing process.
“Aerogel is the answer for stopping thermal propagation or mitigating longer than the current five-minute recommendations. Aerogel is the world’s lightest solid and best insulator, making it an ideal material for cell-to-cell barriers,” claims an expert in the materials.
Most aerogels are made from silica in a ‘solgel’ reaction in which the liquid inside pores has been replaced with gas, resulting in a solid with extremely low density.
The solid component consists of tiny, 3D, intertwined clusters that make up just 3% of the material’s volume and are very poor thermal conductors. The rest of the volume is air with very little room to move, which inhibits the other heat-transfer mechanisms of convection and gas-phase conduction.
In thermal-barrier applications, aerogel is typically used as a firewall between cells. It has exceptional mechanical properties, our expert says, enabling it to act as a compression pad, allowing for cell expansion and contraction during charge/discharge cycles.
“Cell-to-cell barriers do not operate in isolation, so our materials are designed with a system-level approach. Our team takes into consideration how cells expand over time as they age and compress the barriers between them. By a pack’s end-of-life (EOL), the aerogel is compressed to a fraction of its original thickness. The material has a thermal conductivity lower than still air, so when it is under strain the thermal conductivity actually improves.”
“The increase in presence of aerogels globally as a solution, and their reduction in cost, present a significant advance,” another expert concurs. “It seems as though aerogels have finally hit their stride in commercial adoption at scale.”
“Much attention is given to the promise of solid-state electrolytes. However, there have been many promising advances in alternative liquid electrolyte chemistries,” he adds. “These hold a lot of promise in that they can perhaps be integrated into existing cell designs much more readily. It is important that we do not miss opportunities to further these developments.”
Some of the most promising ongoing developments in terms of prevention or significant reduction of impact include ionic liquids and solid-state electrolytes, he says, and he expects many safety benefits to come from advancements in electrode designs and additives.
But, he cautions: “We can expect emerging technologies to perhaps fall short of expectations of absolute safety against thermal runaway until they are verified through extensive testing and in full-scale production.”
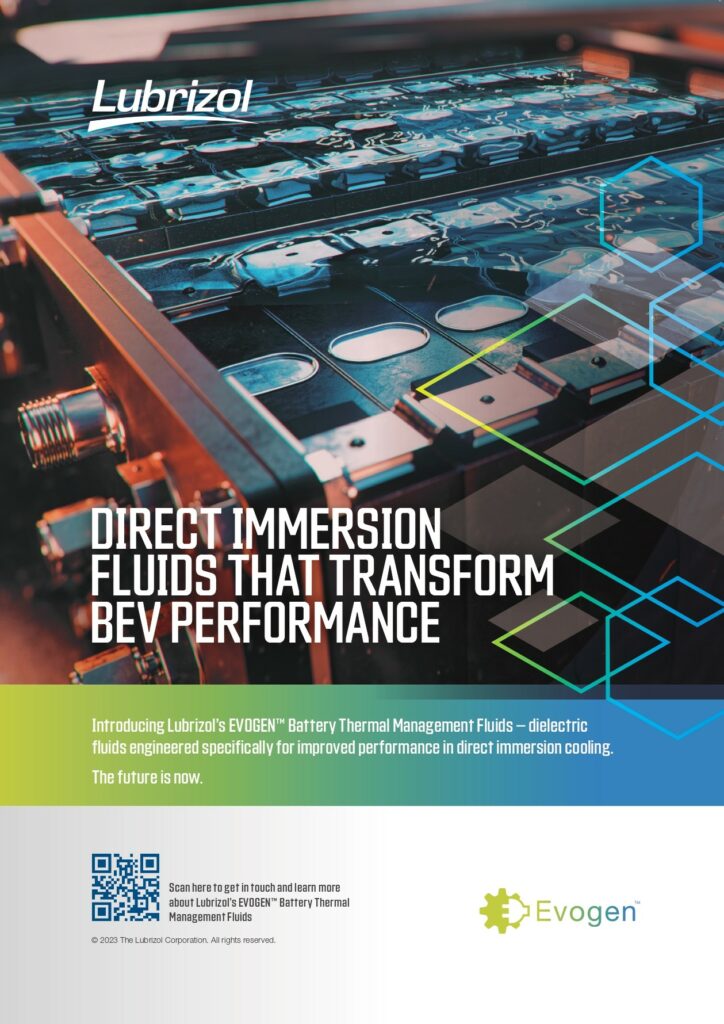
AI in BMS and design
The battery management system (BMS) plays a central role in maintaining the health of the battery and ensuring it is operated within safe charging, discharging and temperature limits. It gauges the battery’s state of charge and state of health though suites of sensors that monitor parameters such as voltage, current, temperature and pressure.
Development of these systems is beginning to incorporate aspects of artificial intelligence (AI), according to an expert from a company that creates machine-learning models and software functions that can be embedded in a BMS.
“Our software operates on typical measurements available in an onboard BMS, and it is trained on live data from EV fleets we have access to, as well as offline data captured from battery packs during cell teardown analysis,” he says.
“The algorithms consist of a combination of signal processing to extract insights from measurement data, and later machine-learning models to infer diagnostic and thermal runaway-related risk information from the extracted insights. This setup is a powerful tool to combine battery expertise with modern machine-learning pipelines to arrive at solutions that are real-world capable and have a shot at significant reduction of thermal event risks.”
The company’s engineering team has made significant advances in recent months; for example, reducing the processing and memory requirements of the software’s lithium-plating detector to ease its deployment in common automotive-grade BMSs, the expert explains. The company has also announced a partnership that allows it to offer the software on microcontrollers from a major manufacturer.
“We have successfully concluded the deployment of our thermal runaway detector in a pilot EV fleet and have validated our thermal runaway risk-prediction algorithms on customer vehicles. As a result, we’ve started to generate warnings for them to manage their fleet in a much safer manner. Additionally, the engineering team has developed a transfer learning methodology to enable deployment of its products to new batteries and fleets much faster by requiring much less, and sometimes no, data from customer’s cells and batteries for characterisation and fine-tuning.
“Finally, as a more general and higher-level safety measure that also contains the ability to detect issues that could lead to thermal runaway, we’ve developed a completely unsupervised learning-based approach to anomaly detection to ease deployment into fleets where we have not had the chance to characterise the batteries extensively.”
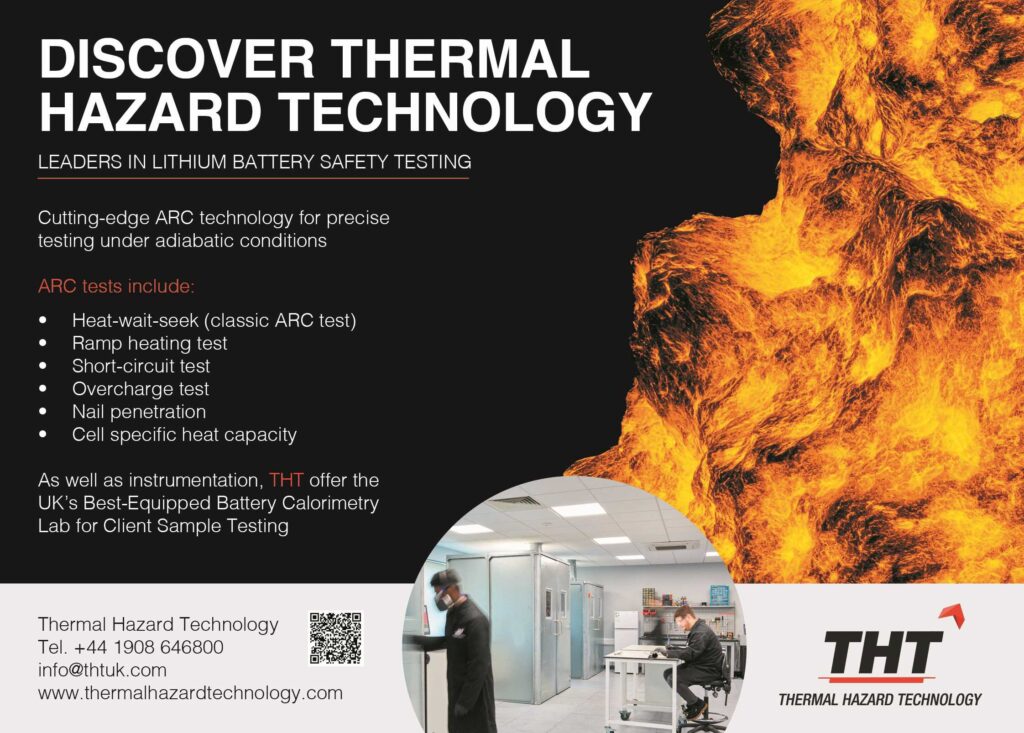
AI in battery testing
AI is becoming increasingly important in battery design and testing, particularly in relation to safety in general and to thermal runaway specifically. For example, machine learning is helping engineers create better test plans. Batteries are difficult to simulate using traditional tools, so engineers rely heavily on physical testing to ensure different cell chemistries meet performance requirements and respond safely under varying conditions.
Such tools can be used to create models that help focus testing on the most important parameters, ranges and operating conditions to ensure the coverage of critical safety areas. This can help with cell selection and validation testing, and the detection of signals that might lead to a runaway, says an expert from a company that creates such tools.
The company’s AI platform enables engineers to create models from lab and field data to look for potentially dangerous anomalies. With deep-learning anomaly detection tools, they can monitor thousands of channels for a wide variety of subtle abnormalities in voltage and thermal measurements.
A recent enhancement to the anomaly detection capability allows the parsing of hundreds of test data channels within minutes, along with the inspection of raw test data to ensure it does not contain anything erroneous from faulty sensors, poor measurement logic or sensor placement, or system malfunctions.
Using this approach, engineers can quickly identify when batteries undergoing long-running ageing tests are showing early signs of failure and quickly shut them down for repair or retesting. Similarly, measurements from fielded batteries can reveal voltage drifts that may indicate an impending thermal event in time for the battery to be shut down to avoid damage or injury, the expert says.
While machine learning-based AI models can only reconstruct battery behaviour from within the design space of values on which the models were trained, as more battery chemistries are tested and tracked with field data, the reach and capability of trained models will grow.
“As more thermal runaway events are captured in telemetry data, engineers can create more accurate models to predict and prevent similar events,” the expert concludes.
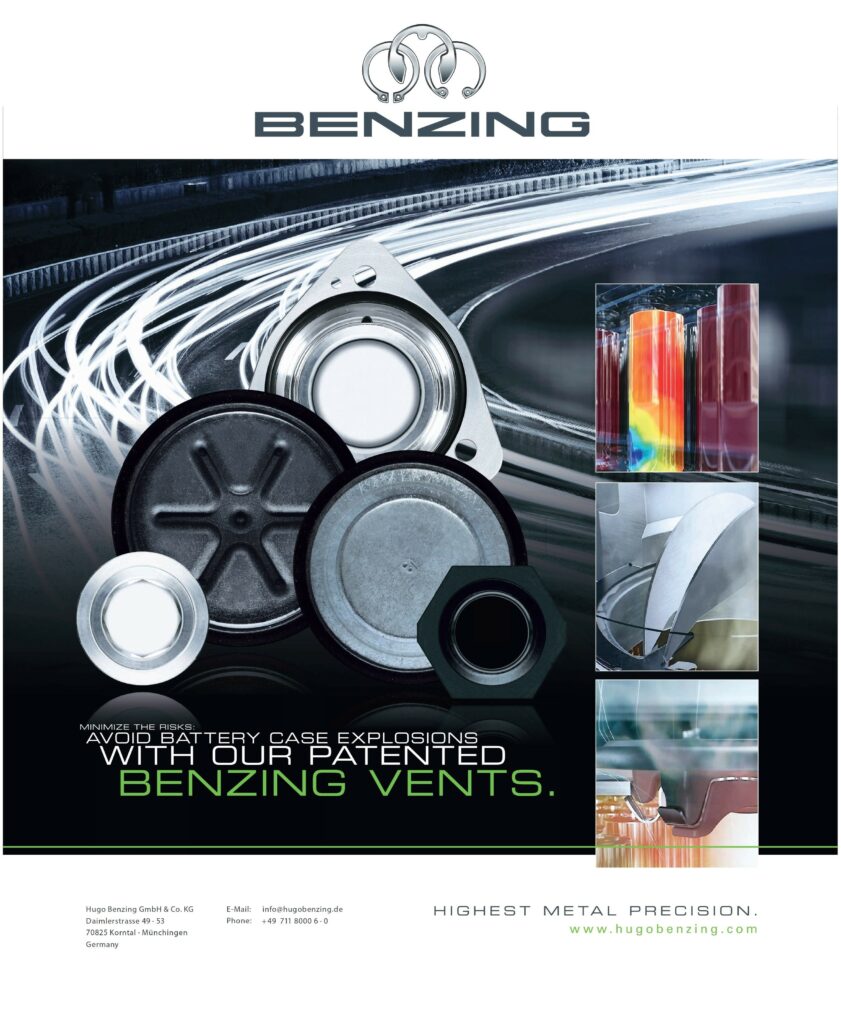
Acknowledgements
The author wishes to thank the following for their help with this article: John Williams, vice-president of technical services at Aspen Aerogels; Conor Sheehan, automotive application development engineer at DuPont; Can Kurtulus, CTO of Eatron Technologies; Laila Bonilla, business development manager, and Laure Bertrand, tech service manager, at Elkem; Dr Kim Dana Kreiskoether, specialist battery cell/system at Henkel; Dr Richard Ahlfeld, founder and CEO of Monolith; Dr Stefan Reichle, EMG advanced manufacturing & market unit manager, alternative mobility at Parker Hannifin; Dr Andy Richenderfer, senior research engineer and Dr Chris Rasik, technology development manager, at Lubrizol; and Shuang Ma, global battery safety platform leader at PPG.
Click here to read the latest issue of E-Mobility Engineering.
Some suppliers of thermal runaway prevention
Aspen Aerogels
Avery Dennison
DuPont
Eaton
Eatron Technologies
Elkem
Graco
Henkel
Hugo Benzing
JBC Technologies
KULR Technology
Lubrizol
Monolith
Parker Lord
PPG Industries
Schaeffler
Thermal Hazard Technology
TLX Technologies
Webasto
+1 508 691 1111
+1 440 534 6000
+1 302 774 3034
+1 269 342 3000
+44 1926 623039
+44 121 601 6397
+32 89 770 847
+49 211 797 0
+49 711 8000 6 0
+1 440 327 4522
+1 408 663 5247
+32 2 78 1911
–
+1 937 278 9431
+44 1449 771775
+44 121 313 5830
+44 1908 646800
+1 262 372 2165
+49 89 85794 52803
ONLINE PARTNERS
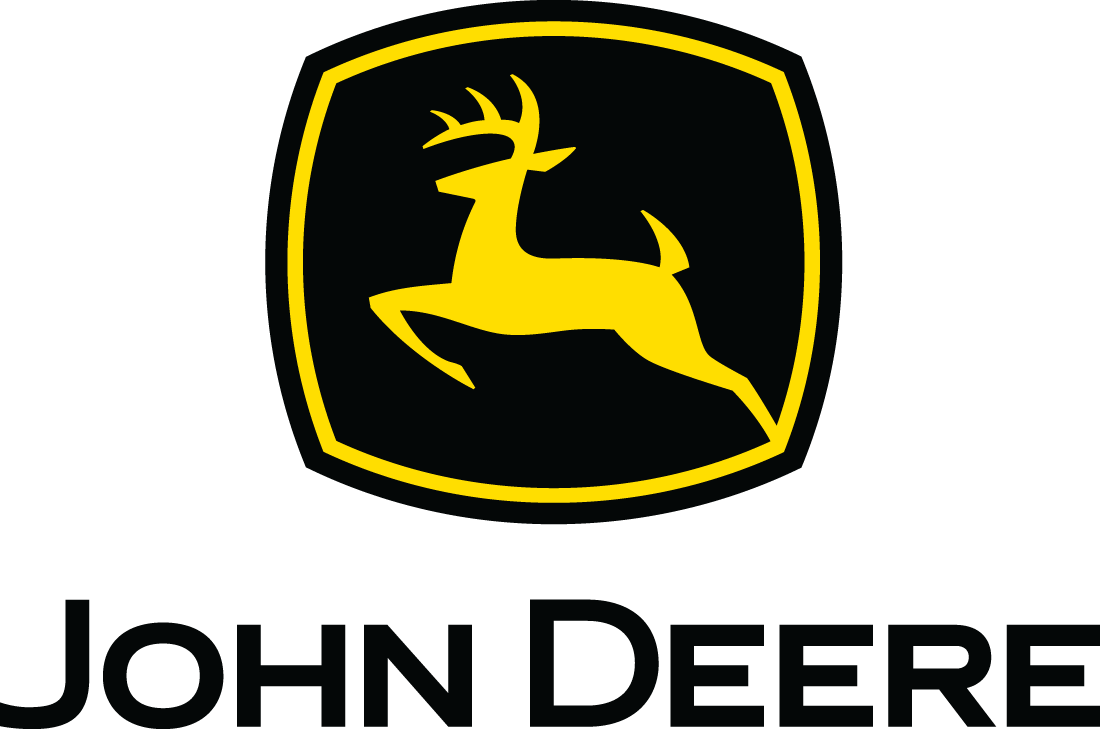
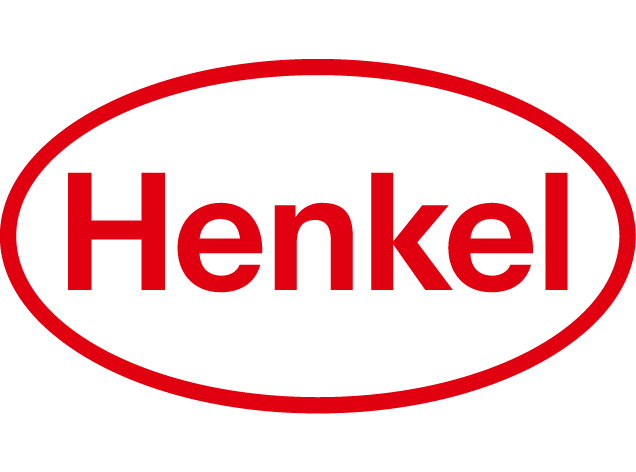
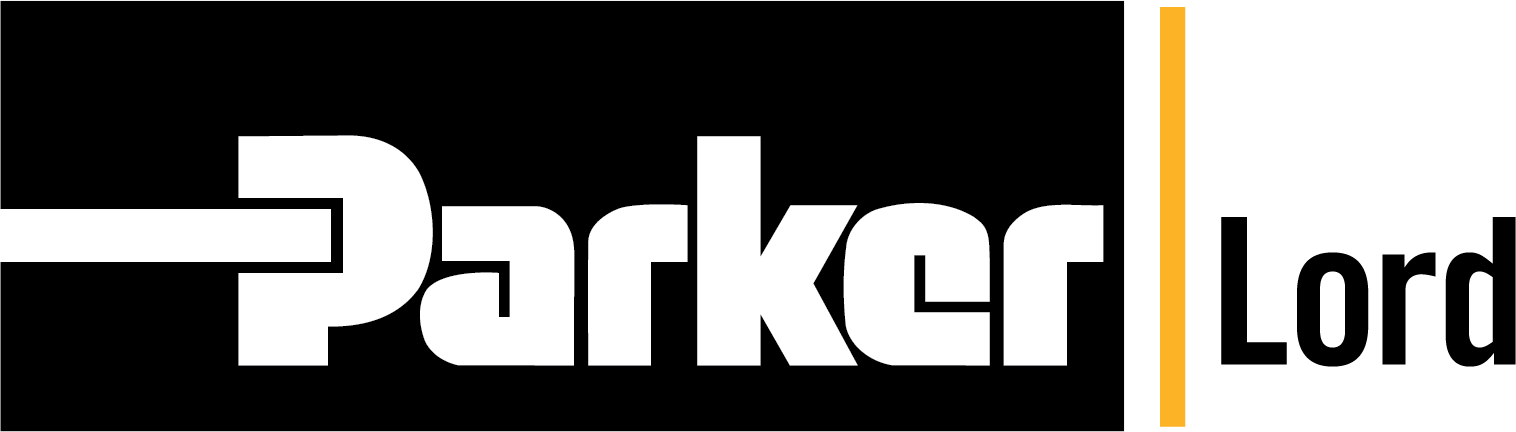
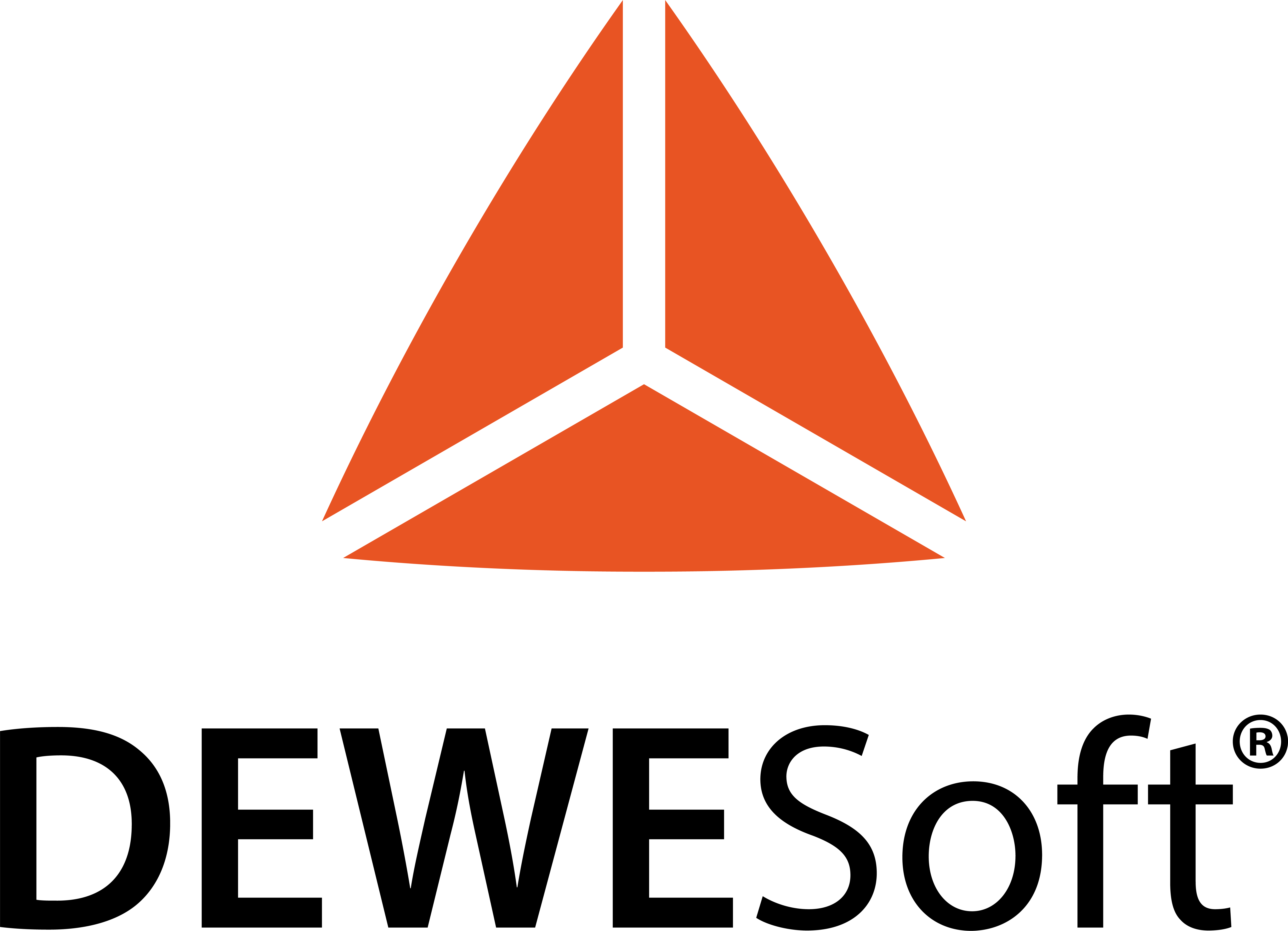
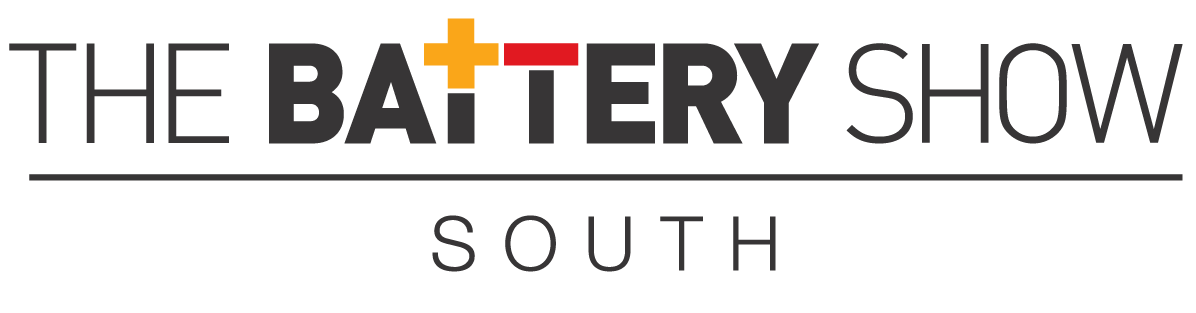
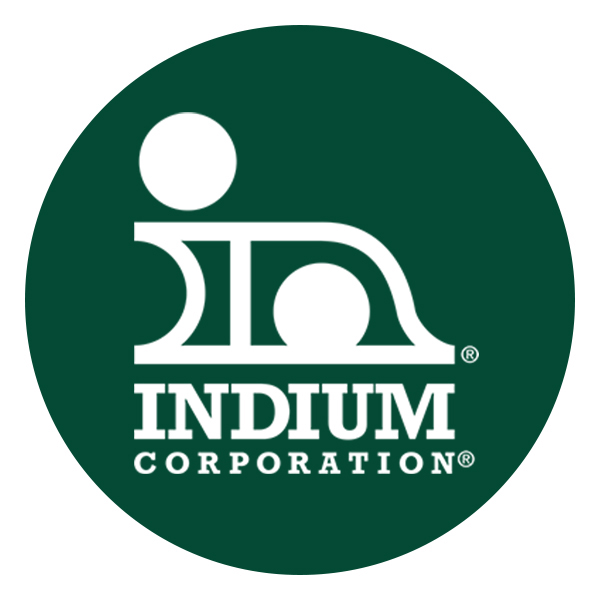
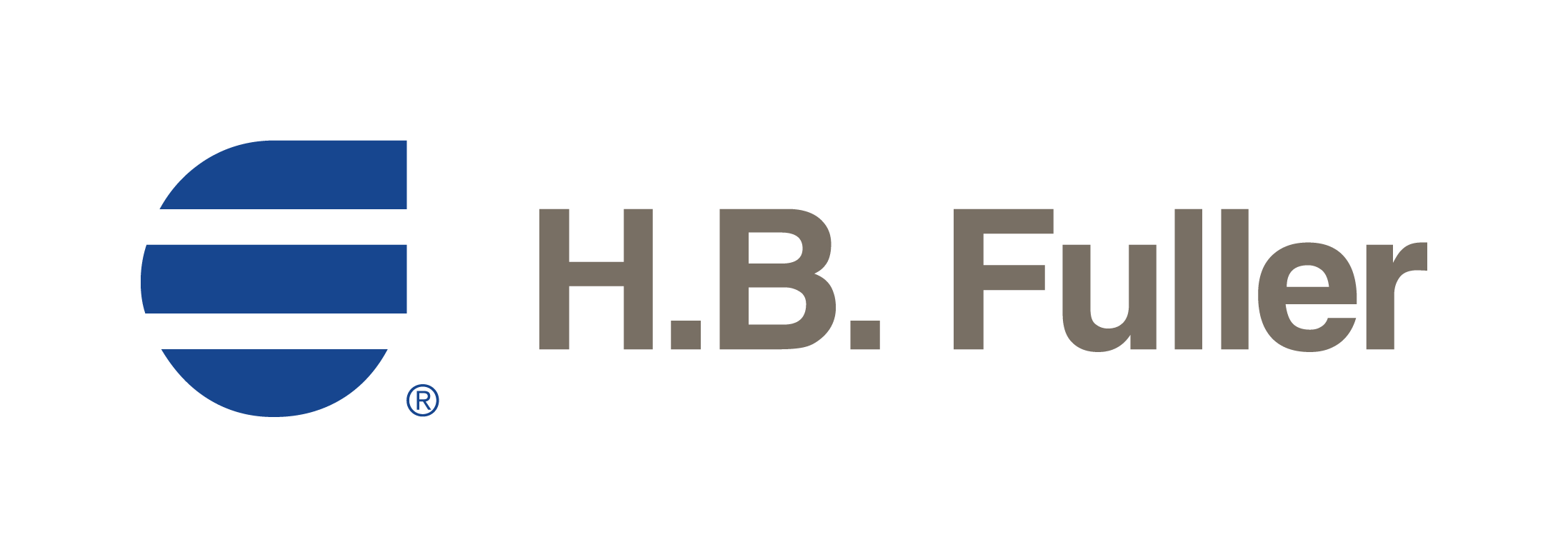