The Battery Show USA show report
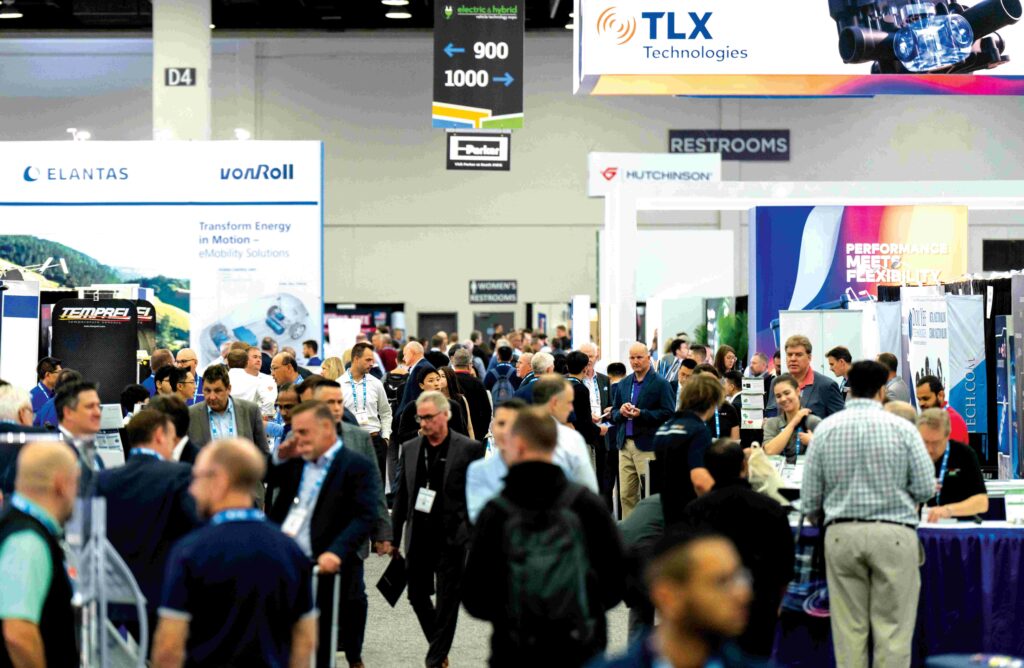
(Image courtesy of Accesswire)
Designs on the future
A wealth of advanced battery tech for EVs was on show in Detroit, as Peter Donaldson reports
Staged for the first time at Huntington Place, Detroit, The Battery Show and Electric & Hybrid Vehicle Technology Expo, North America showcased a myriad advanced battery technologies. Organiser Informa Markets reports that more than 21,000 professionals from around the world attended and 1250 organisations exhibited, making the 2024 event the largest in its history, which dates back to 2010.
However, this comes at a time of growing economic and geopolitical uncertainty, occasioned by the wars in Ukraine and the Middle East, and the threat of sanctions against China (to which the latter will most likely respond in kind), with supply-chain implications for most EV manufacturers in the West and elsewhere.
Recent sales statistics probably don’t reflect this yet. ABI Research’s 2024 third-quarter report shows passenger vehicle sales returning to pre-pandemic levels, reaching 91.7 million shipments in 2023 and 94.7 million shipments in 2024, although the sales growth this year of 3.3% is down from 11.7% in 2023.
While the organisation reports that the EV market is experiencing what it calls a mild slowdown, it points out that overall sales growth remains stronger than that for ICE vehicles.
However, battery EVs (BEVs) in the passenger vehicle sector face their own problems related to factors such as high purchase prices, running costs and widely publicised fires, compounded by high depreciation due to businesses putting large numbers of relatively young, used EVs (bought in response to the carrot-and-stick of government subsidies and zero emission laws) onto markets where demand is already weakening, such as the UK.
“We’re just getting a taste for what happens when you try to legislate technology instead of allowing technological performance and customers to drive demand,” commented one seasoned industry insider.
The industry needs to apply some “non-conventional wisdom” by avoiding typical, large company responses to expected slowdowns, such as laying people off, cutting their marketing and ripping apart their r&d.
“We’ve seen it so many times in the past,” said the insider. “A lull in the automotive sector is like a lull in the chip sector or any other market. The big question is who wants to be the winner coming out the other side?”
However, he still sees plenty of opportunity for alternative powertrains. He stresses the importance of developing safe, reliable and accessible rapid charging, and deploying the infrastructure, as well as developing better, safer batteries whose health is easier to monitor and predict, and more refined and responsive thermal-management systems.
He also sees more potential for developing fuel-cell vehicles that match the performance of BEVs, and further developing hybrids, which are increasing in popularity once more. “I’m seeing now that, locally, many car dealers are having trouble keeping hybrids on the lot.”
Continuing development of EV technology through difficult times is particularly important if US and European manufacturers are to remain competitive with the Chinese, he says. “If we just sit back, and wait and see, we’re going to find that the Chinese are going to be leading in so many categories that it’s going to take a tonne of tariffs to stop them.”
Meanwhile, companies that exhibited in Detroit continue to develop innovations to address these issues, at least from a technological standpoint. What follows is a sampling of products designed to speed up manufacture, enable higher charge rates, refine thermal management, improve safety and reliability through more secure connectivity, and provide better protection from shorts and electromagnetic interference.
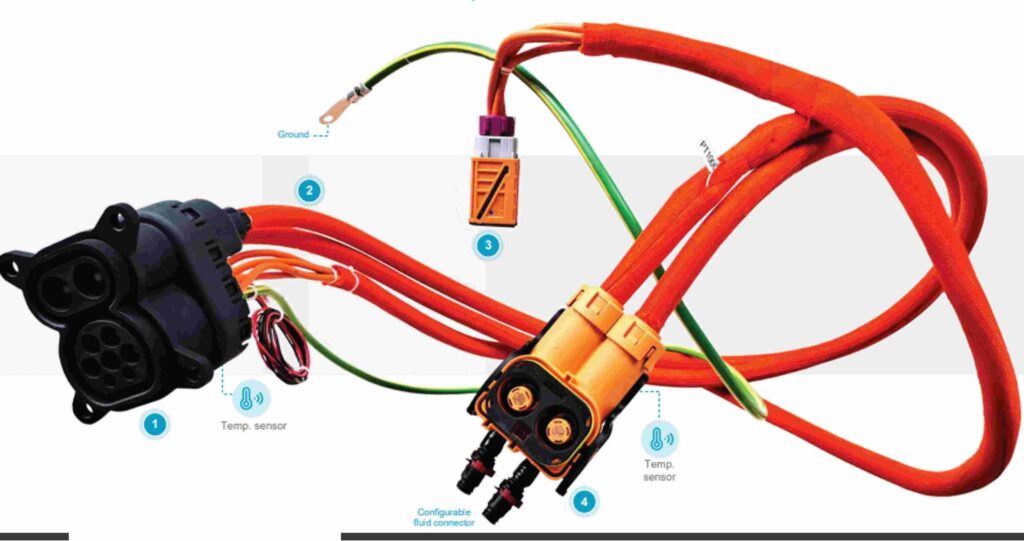
(Image courtesy of Amphenol)
Amphenol Tuchel Electronics presented its innovative, liquid-cooled power inlet for EVs that accept combined charging system (CCS2) connectors, with the purpose of enhancing high-rate charging capabilities, reducing charging times, and improving system efficiency while ensuring safety and reliability.
“We’ve designed a water-cooled loop within the CCS2 inlet to aid heat dissipation from the inlet, enabling higher current transfer,” says Amphenol’s Greg Dziubek. “This allows EVs to charge faster, reducing the time to charge significantly and moving closer to the convenience of refuelling gasoline vehicles in minutes.”
The system integrates with existing EV cooling systems, using the same fluids and thermal-management loop as the battery. Amphenol has also partnered Gebauer & Griller to integrate their water-cooled cables with its CCS2 solution. The cable design includes a tube that has been modified for this application to insulate coolant from high-voltage components, preventing galvanic corrosion.
Dziubek explains: “Heat transfer occurs through this material, maintaining electrical isolation while ensuring effective cooling of the cable.”
The use of liquid cooling allows the cable cross-section to be made smaller without compromising performance. A 50 mm2, water-cooled cable can rival the functionality of a much thicker, 250 mm2, uncooled cable. “This can lead to potential weight savings for vehicles, as thinner cables can replace larger, heavier ones,” he notes.
In terms of additional features, the CCS2 inlet retains standard functionalities, such as AC/DC charging and robust communication systems. It includes safety mechanisms, such as a locking pin to secure the connector during charging and optional indicator lights to show the charging status.
“We can also integrate heating units to prevent freezing in cold climates or de-icing through the vehicle’s existing thermal-management system,” Dziubek says. This indicates a change in direction by Amphenol Tuchel towards supplying solutions such as this, rather than just components, with a focus on being a problem-solver for OEMs.
Amphenol’s design is still in early development. Preliminary prototypes are undergoing testing, with timelines for production tools estimated at six to nine months after the design is finalised. Full-scale production is anticipated within a year, depending on customer interest.
Avery Dennison discussed its new high-voltage-resistant FT-0031 dielectric tape, launched as part of the Volt Tough EV battery portfolio. Avery Dennison’s Scott Krusinski describes the FT-0031 as a “second-generation” product that builds on the initial Volt Tough designs to address specific challenges in modern EV applications. He says the new iteration achieves significant improvements in dielectric strength, conformability and tear resistance.
One of the tape’s standout properties is its dielectric strength of over 11 kV, supported by a durable acrylic adhesive, which “provides high shear strength and heat resistance”, ensuring it can endure for the lifespan of a battery pack. This high-performance adhesive bonds to metal components; an essential feature given the tape’s primary role in insulating areas of high electrical potential across complex metal surfaces.
The FT-0031’s conformability is another defining attribute. Krusinski says the tape incorporates a proprietary, elastic film that is capable of “stretching over 600% before it rips”, making it ideal for applications such as cooling plates and ribbons.
“It is conformable to metal-forming processes and tear-resistant against burrs,” so it can be applied flat and then shaped or stretched without compromising its insulation integrity, he explains.
In cooling-plate setups, the tape can be applied before the metal undergoes air-pressure moulding, which creates coolant channels. Despite significant deformation of the metal, the FT-0031 remains securely in place, stretching to accommodate the new shape without tearing – a feature Krusinski regards as a key differentiator from products that use less flexible polyester film.
FT-0031 is designed to be easy to apply. Krusinski notes that it only requires about five PSI to stick and develops satisfactory initial adhesion, with maximum adhesion over 72 hours. Moreover, the tape can be removed and reapplied if rework is needed, making it ideal for iterative manufacturing environments. This reusability could also ease the recycling process at the battery’s end of life, he adds.
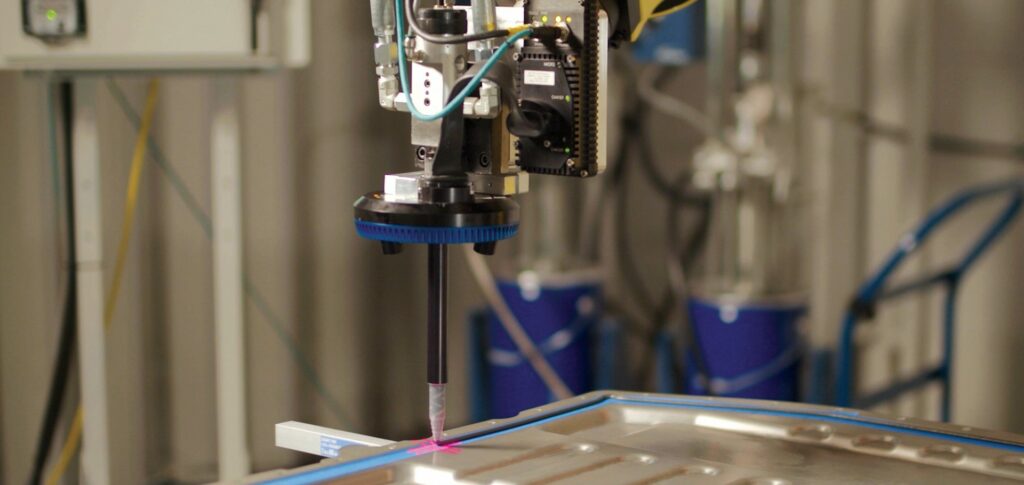
(Image courtesy of Nordson)
Nordson unveiled its ProMeter S, an advanced adhesive and sealant dispensing system, designed to meet diverse industrial needs, including those of EV battery production. The system employs a “first-in, first-out” approach, ensuring efficient material flow, and preventing the build-up of old material in the nozzles and elsewhere.
According to Nordson’s Jennifer Shupp the ProMeter S is a modular and low-maintenance solution designed for long-term reliability.
“It can be used in the production of battery modules, casings, busbar connections and even thermal management of battery trays,” Shupp says. Nordson has conducted extensive trials to confirm its ability to handle various thermal interface materials.
One of the system’s defining features is its positive rod-displacement technology, which uses a rod in a cylinder to precisely control the flow of material.
“The length of the rod’s travel determines the dispensing volume, and the speed of travel correlates to flow rate,” Shupp explains, adding that this flexibility supports a range of dispensing patterns, including beads, patches and swirls. This capability reduces material waste and enhances adhesion.
Durability is enhanced by Nordson’s proprietary Scoreguard coating on the rod, which resists scratching and pitting caused by abrasive additives, such as thermally conductive ceramics, says Shupp. This reduces wear and tear, prolonging the seal packing’s lifespan and lowering maintenance costs.
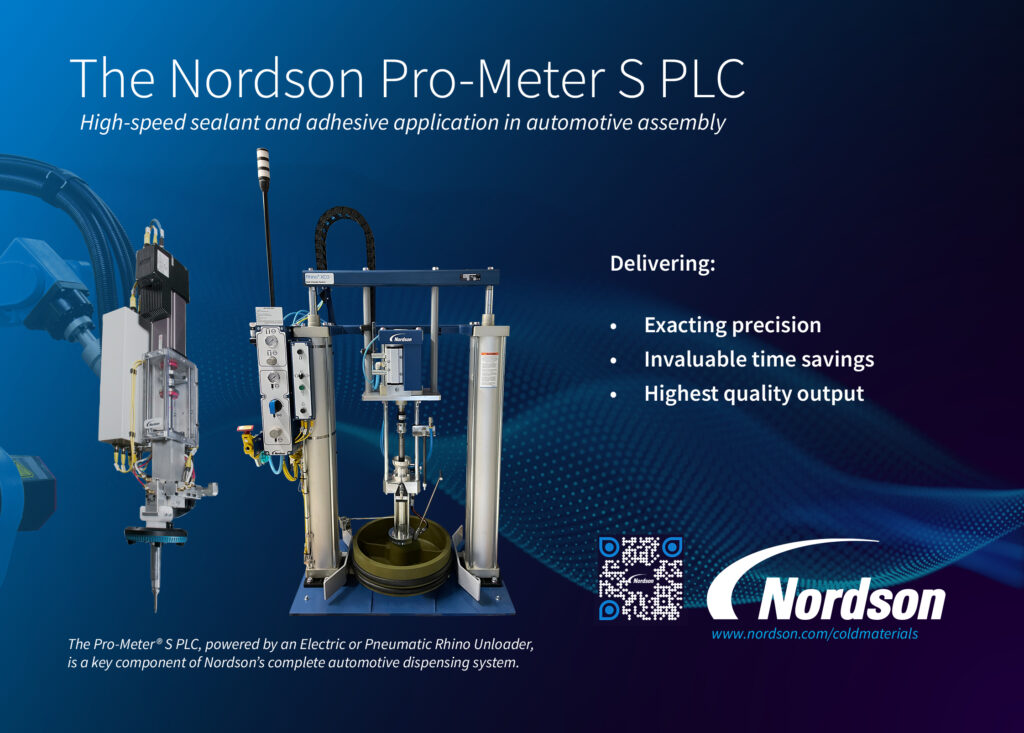
The integrated servo actuator enables mid-stroke speed adjustments for the precise application of complex patterns, such as corners.
The system also offers flexibility in mounting, either as a stationary pedestal unit or mobile robot-mounted, depending on whether the work moves under the dispenser or the dispenser moves over the work to form the bead.
Nordson provides a wide range of interchangeable nozzles to cater to specific customer needs. “We can create triangular patterns, flat dispenses or other variations based on the application,” Shupp says.
With chamber capacities from 35 cc to 300 cc, ProMeter S covers a wide range of applications. To pair with this metering system, the company offers Rhino pumps to extract material from the industry-standard 5 G pails and 55 G drums. All of this is managed via a PLC-based logic controller. All of Nordson’s solutions require standard industrial electricity and compressed air.
HB Fuller showed EVBond 775, a reactive hot-melt adhesive (RHM), designed to enhance the assembly of battery packs in EVs. HB Fuller’s Marlen Valverde, highlighted its advanced capabilities in bonding mica shields to metal enclosures.
EVBond 775 is a single-component, hot-applied polyurethane adhesive, formulated to meet stringent requirements for bonding mica shields, which is critical for fire protection and thermal insulation in battery systems.
“It grips the mica to the metal enclosure very fast, with cycle times under 20 s,” while significantly exceeding the strength of traditional, pressure-sensitive adhesives (PSAs), Valverde notes.
Historically, PSAs have been the industry standard, but their limitations – such as weaker bond strength and vulnerability to environmental factors – have led to cumbersome manufacturing processes.
“PSAs often required additional design steps to compensate for their lower grip, like flipping covers or protecting assemblies from cold,” Valverde explains, adding that EVBond 775 eliminates such inefficiencies, offering an “aggressive, universal tack” that is suitable for various substrates, including mica, metals, plastics and ceramics.
The adhesive supports cost-efficiency by enabling manufacturers to use less material.
Its robust bond strength allows for transport under extreme conditions without performance degradation. EVBond 775’s moisture-curing property ensures complete cross-linking, even in low-humidity environments, without requiring special climate control.
The adhesive has also been used successfully in thermally conductive applications, such as attaching cylindrical cells to cooling ribbons. Its thin, highly wettable application layer enhances thermal dissipation.
As a one-component system, the company says EVBond 775 simplifies equipment needs, reducing maintenance and setup complexity, promising faster production cycles and significant cost savings.
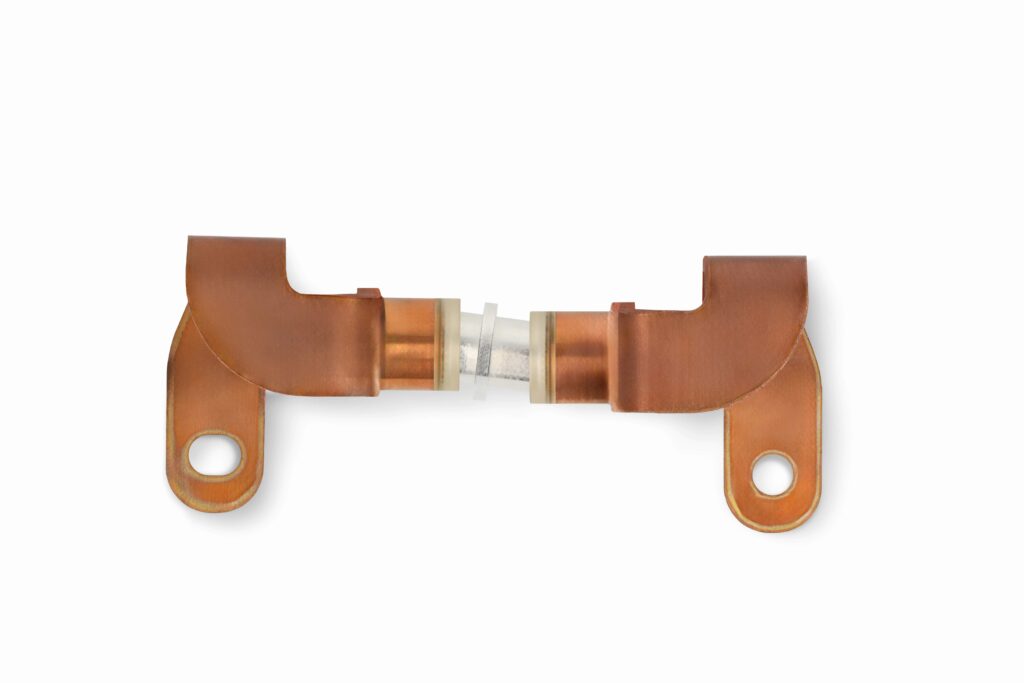
(Image courtesy of ODU Automotive)
ODU highlighted its range of tolerance-compensating, high-voltage connectors for EV powertrain components. Tolerance compensation is increasingly important in many areas of the powertrain, particularly between e-motors and inverters, as integrators and OEMs seek to produce safer, more reliable connections more quickly.
ODU Automotive’s James Kruzich says: “Busbars from the e-motor to inverter always have slight misalignments because of their rigid construction and tolerances in assembly”. The inherent stiffness of busbars prevents them from compensating for any misalignments, making innovative connector solutions essential.
ODU addresses this problem with its LAMTAC Flex connector, which offers up to ±1 mm tolerance compensation in any direction. This design eliminates the need for traditional, bolted connections, reducing labour and assembly complexity. By avoiding bolted joints, manufacturers can save space and minimise risks such as dropped bolt nuts, which can disrupt assembly or maintenance. Furthermore, ODU highlights that “there are no additional covers or labour associated with bolting these down”, Kruzich says.
Tolerance compensation is achieved through multiple innovative methods. ODU’s solutions include flexible pins, as used in the LAMTAC Flex connector and LAMTAC Float socket, which accommodate small misalignments. Both systems are capable of compensating for up to ±1 mm in any direction and they are available in contact sizes ranging from 5-20 mm. Another method uses flexible busbars to manage alignment discrepancies.
The time and cost savings provided by these solutions are significant. By eliminating the need for bolting and reducing assembly complexity, they can be put together “much faster”. Additionally, the lack of bolts ensures high-voltage connections are secure against loosening as a result of vibration.
ODU’s tolerance-compensating connectors are often used in battery management system (BMS) connections, as well as the motor-to-inverter interface.
Lubrizol told us about its efforts to revolutionise battery cooling with its Evogen dielectric thermal-management fluids, which can be used in cooling applications such as immersion cooling.
Unlike traditional, indirect cooling methods, which rely on cold plates, ribbons and water-glycol solutions, immersion cooling submerges batteries directly into a non-conductive fluid, dramatically improving heat dissipation and safety, according to Lubrizol’s Binbin Guo.
“Immersion cooling allows more surface contact between the source of heat and the cooling fluid, ensuring better heat-transfer performance compared with indirect cooling systems,” she says.
This method can simplify system architecture by eliminating the thermal interface materials commonly used for indirect cooling, offering efficiency and design simplicity, Guo says.
The key is the dielectric fluid; a non-conductive and insulating medium that interacts safely with battery components. Guo says this design enhances cooling performance and also helps prevent potentially catastrophic events such as thermal runaway.
“Thermal runaway can occur due to various factors, including degradation, manufacturing defects or abuse,” she says. “Our fluids minimise the impact, as demonstrated in third-party nail-penetration and thermal abuse tests.”
Beyond cooling, the fluid plays a critical role in system safety and compatibility. Lubrizol evaluates multiple parameters to tailor formulations for specific customer needs: “We consider viscosity, thermal conductivity, density and specific heat capacity to optimise heat transfer. Compatibility with materials like hoses and gaskets, anti-corrosion properties and resistance to water ingress are essential.”
Evogen thermal-management fluids also soften the impact of thermal events. In experiments comparing air-cooled batteries to immersion-cooled ones, “we observed a dramatic reduction in flaming particles and heat dispersion with our fluids”, says Guo. This reinforces the fluid’s ability to control overheating and limit thermal damage to adjacent cells.
Adopting immersion cooling requires a significant shift in EV battery pack manufacturing, including capital investments and process changes. However, Guo explains that Lubrizol is collaborating with OEMs, demonstrating the benefits of immersion cooling and helping them to improve reliability and safety.
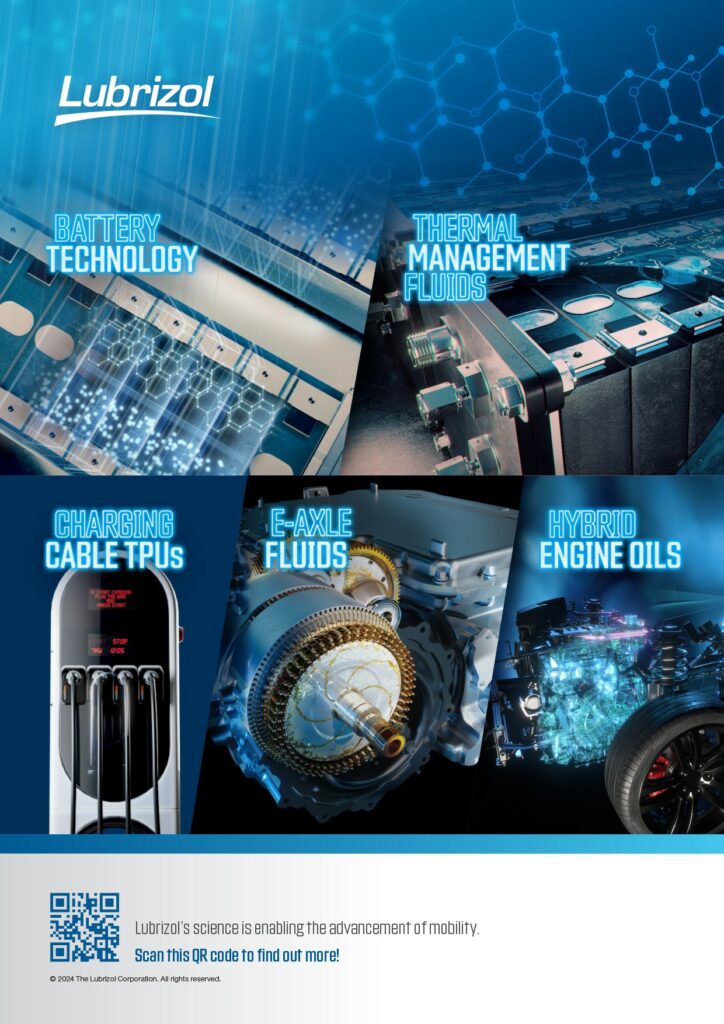
Stafl Systems showcased its next-generation BMS, designed to elevate safety, accuracy and efficiency in diverse e-mobility applications. Building on its extensive experience across electric aviation, marine and heavy equipment sectors, BMS2000 is a complete overhaul of its predecessor, the BMS1000.
“The BMS2000 represents a full refresh of both hardware and software,” says Stafl Systems’ Erik Stafl.
He says Stafl Systems has integrated the latest analogue sensing and microcontroller technology, using a new safety-critical software architecture and several new battery pack sensors.
At its core, the BMS2000 uses Analog Devices’ sixth-generation ADBMS6830 front-end circuitry, providing highly accurate and redundant voltage and temperature measurements. This supports functional safety certifications up to ASIL-D, the highest automotive safety standard.
“Redundancy and accuracy are crucial for high-reliability systems, allowing time-correlated cell voltage and current measurements within one microsecond,” Stafl explains.
This precision enhances algorithms such as Kalman filters to assess state-of-charge (SoC) and state-of-health (SoH) with exceptional fidelity.
The system incorporates the latest NXP dual-core lockstep microcontroller, enabling real-time error detection through cross-checking processors. “With more compute power and memory, we can run sophisticated algorithms and even handle auxiliary vehicle-control functions,” Stafl notes.
The hardware stack features advanced, smart contactor drivers from Texas Instruments, ensuring robust feedback and diagnostics for electrical disconnect relays. An integrated isolation fault-monitoring system pinpoints problems within the battery stack by measuring resistance and parasitic capacitance.
On the software side, Stafl introduced a partitioned architecture, separating safety-critical functions from the application layer. He says this design allows customisation without jeopardising core safety features, streamlining safety certifications and enabling flexibility for diverse applications.
Additional sensors for humidity, pressure and VOC emissions enable the early detection of thermal runaway precursors, while a built-in accelerometer adds further monitoring capabilities.
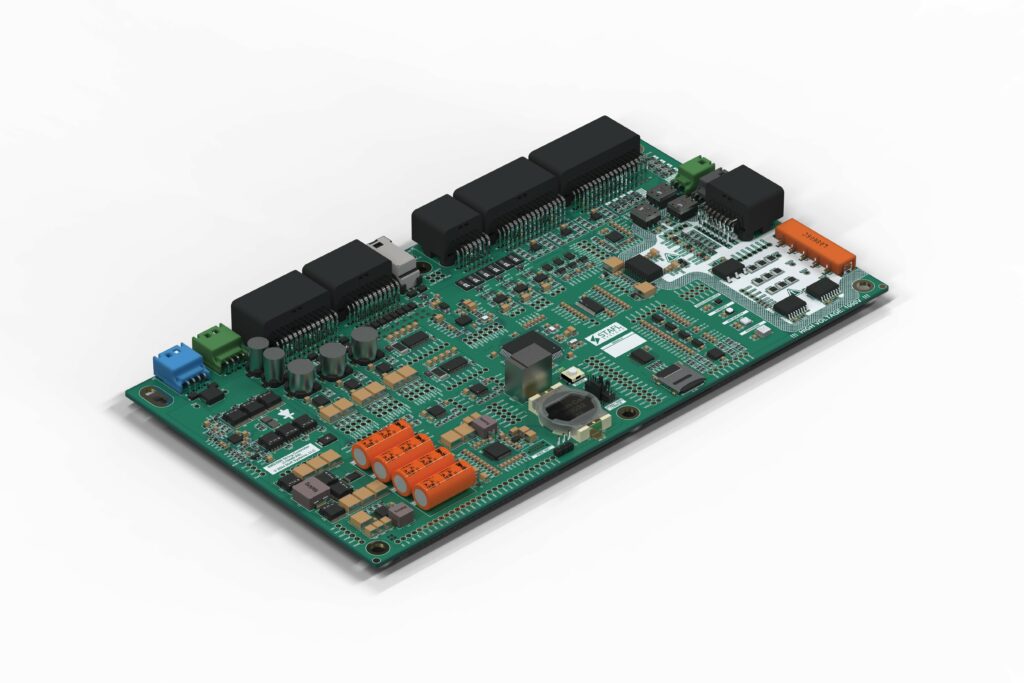
(Image courtesy of Stafl Systems)
Stafl is now shipping BMS2000 samples, with production support slated for the second quarter of 2025.
TDK introduced its IPM01, a permalloy, electromagnetic interference (EMI) shielding sheet, designed to address noise-suppression challenges in EV powertrains. The ultra-thin material, measuring just 6 µm, promises high performance while cutting weight and thickness by up to 90%, compared with conventional shielding solutions.
Developed using a proprietary process in Japan, the IPM01 leverages TDK’s decades-long expertise in advanced materials. “The process is key to achieving this level of thinness and performance,” says TDK’s Bryan Burton.
The material is primarily aimed at mitigating switching noise from DC-to-DC converters; a common issue in EV powertrains that can interfere with critical electronics, RF systems and cabling.
IPM01’s high-permeability alloy attenuates electromagnetic noise effectively. Unlike aluminium or traditional, ferrite-based materials, its performance is superior, even at reduced thickness. The material absorbs electromagnetic energy and converts it into heat, aided by a conductive copper layer that reflects noise back into the absorptive medium.
“It takes a much thicker piece of aluminium to absorb the same signal,” Burton notes.
The material’s flexibility makes it suitable for a variety of shielding applications within EV powertrains and other electronic systems. Supplied in 300 mm x 200 mm sheets, it can be cut to precise shapes using scissors or dies, allowing designers to shield individual components or entire cases.
The material sticks using double-sided tape and is robust enough for industrial handling, although sharp bends should be avoided. Burton emphasises: “It’s not delicate, like gold leaf. It’s robust, yet adaptable for flat or gently curved surfaces.”
IPM01 can eliminate the use of heavy, bulky metal housings for inverters and DC-DC converters. And its ability to isolate or contain EMI on specific circuits enhances system performance.
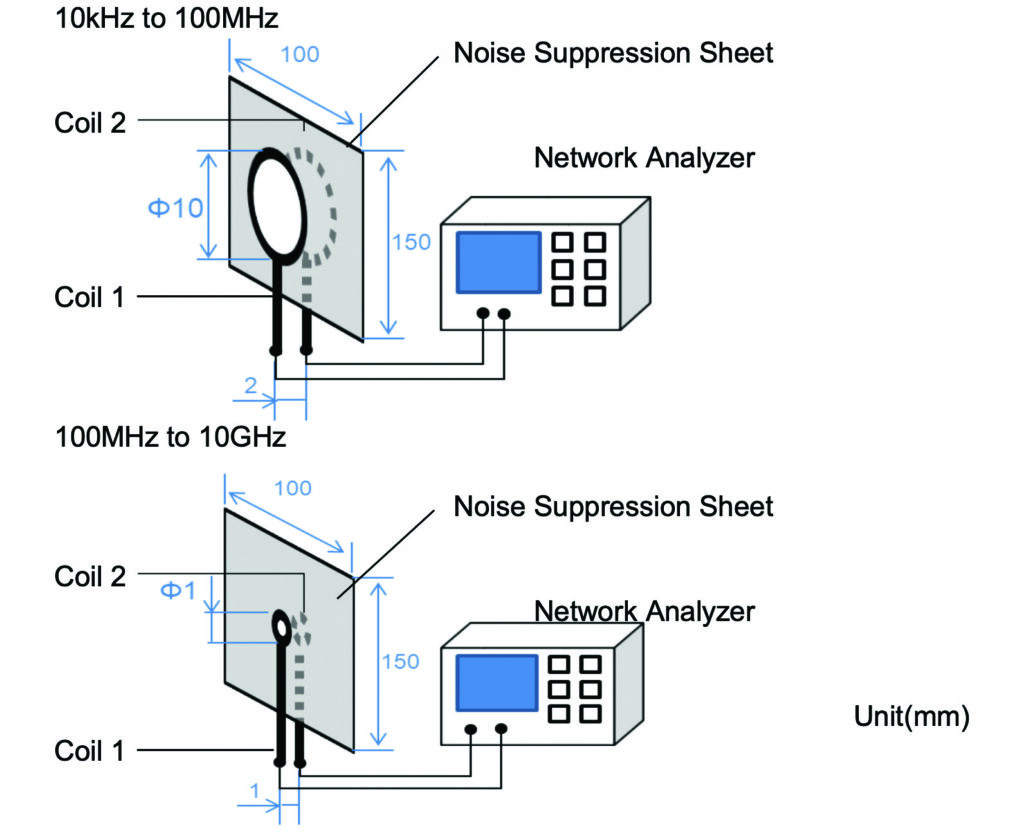
(Image courtesy of TDK)
TDK plans to release a (thicker) high-temperature variant, capable of operating at up to 150 C, with tripled shielding effectiveness.
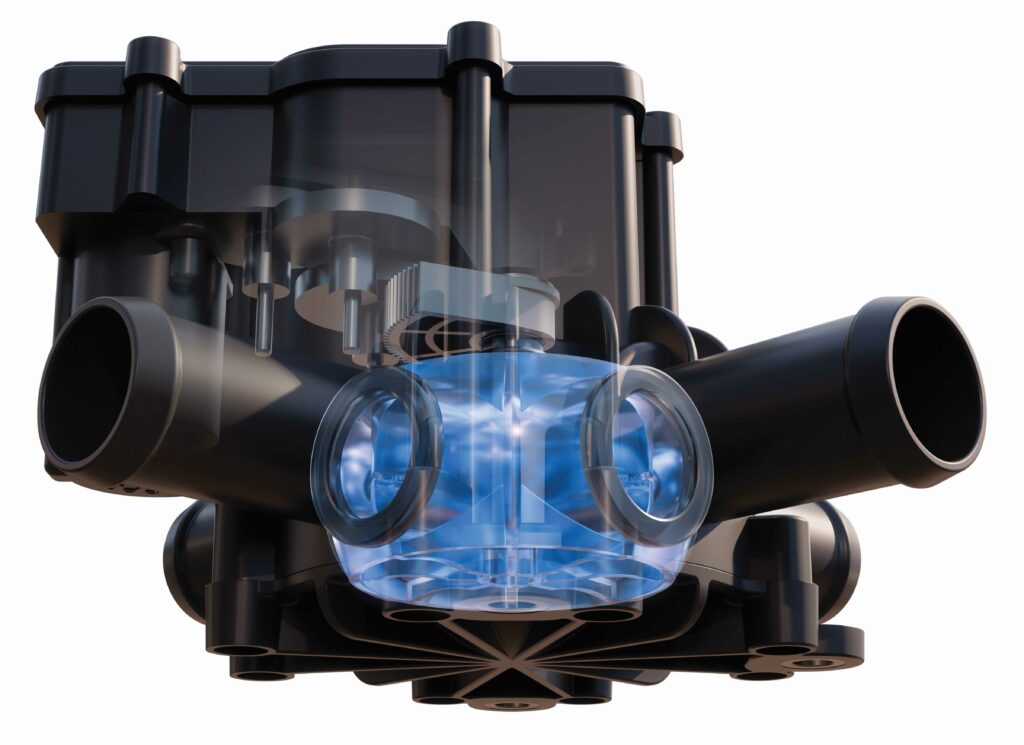
(Image courtesy of TLX Technologies)
TLX Technologies discussed its modular-valve technology, developed to address the growing complexity and performance demands of EV thermal-management systems. The valves are designed to offer flexibility, efficiency and compatibility with various voltage and communication protocols.
TLX Technologies’ Dennis Jensen, says the rationale behind the innovation: “There just weren’t a lot of options for valves that were e-mobility ready, able to withstand harsh environments and demanding performance requirements, at a cost-effective price point.”
The valve’s design includes both 12 V and 24 V DC support within the same package, enabling global compatibility. And the integrated control board accommodates LIN and PWM communication protocols, providing manufacturers with the ability to adapt mid-project without major redesigns.
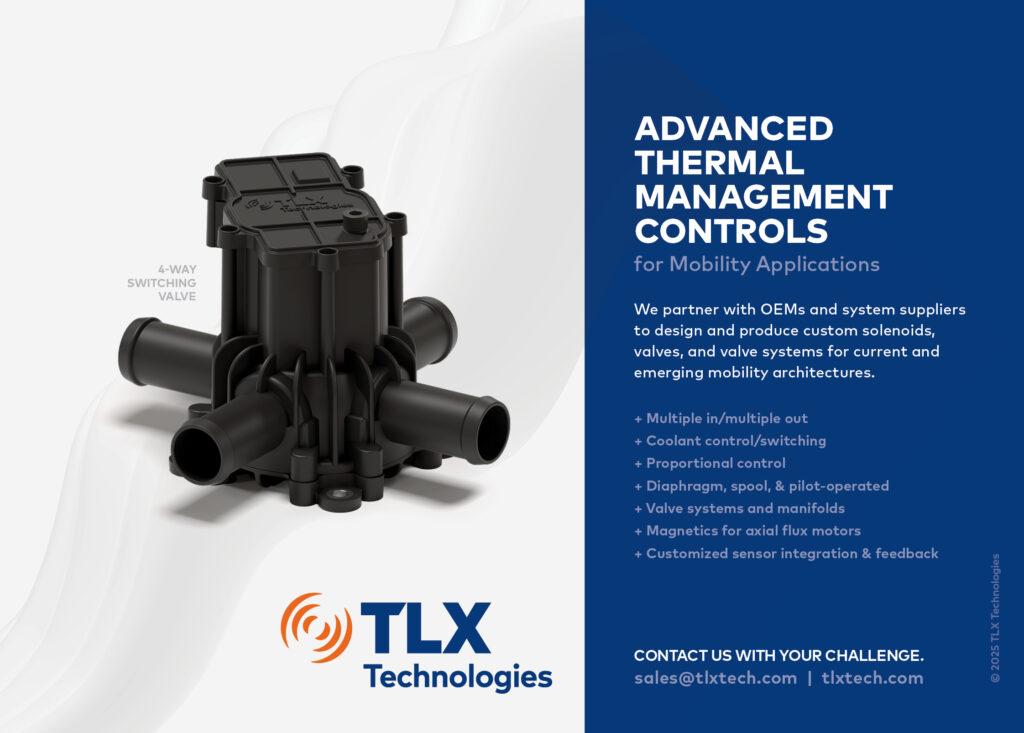
“If specs change during development, you don’t have to dump your work. This valve can handle both,” Jensen says.
Port sizes are capped at 25.4 mm to balance cost and applicability across vehicle types, from light-duty trucks to commercial semis. Although the initial modular valve products exclude CAN bus connectivity to reduce cost, TLX can adjust the board to support CAN if it is critical for a customer’s project.
The valve is engineered for minimal energy consumption. Unlike traditional valves that require constant power to maintain position, TLX’s modular valve uses a pulse to switch position and it remains locked without ongoing energy draw. Internal leakage has been minimised, with rates measured in cubic centimetres per minute at a flow of 100 litres per minute.
TLX plans to expand its modular-valve offerings, including a three-way, proportional set for testing in 2025. It envisions broader applications in thermal-management systems, especially as EVs increasingly integrate AI for predictive maintenance.
Dynamic thermal management is the future, Jensen asserts, stressing that the new modular valves provide the physical means to act on advanced data and keep EVs running efficiently.
Click here to read the latest issue of E-Mobility Engineering.
ONLINE PARTNERS
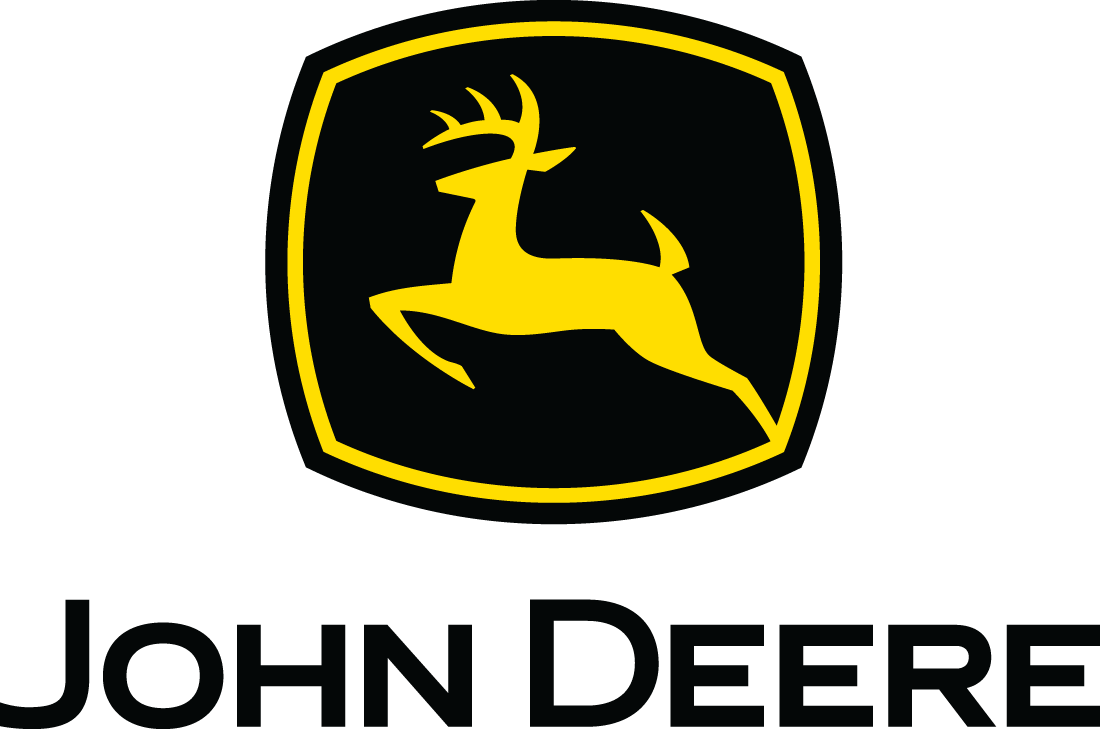
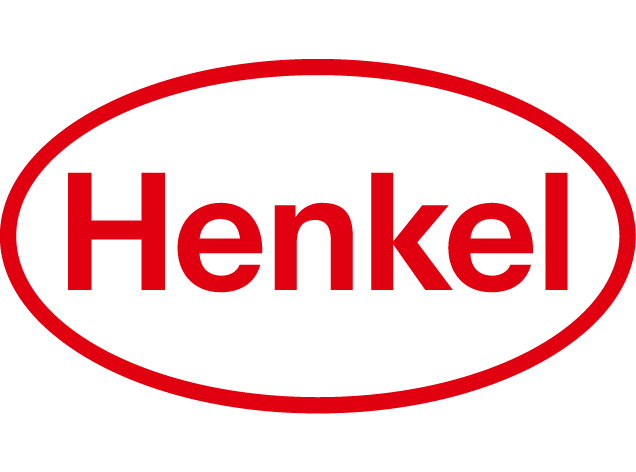
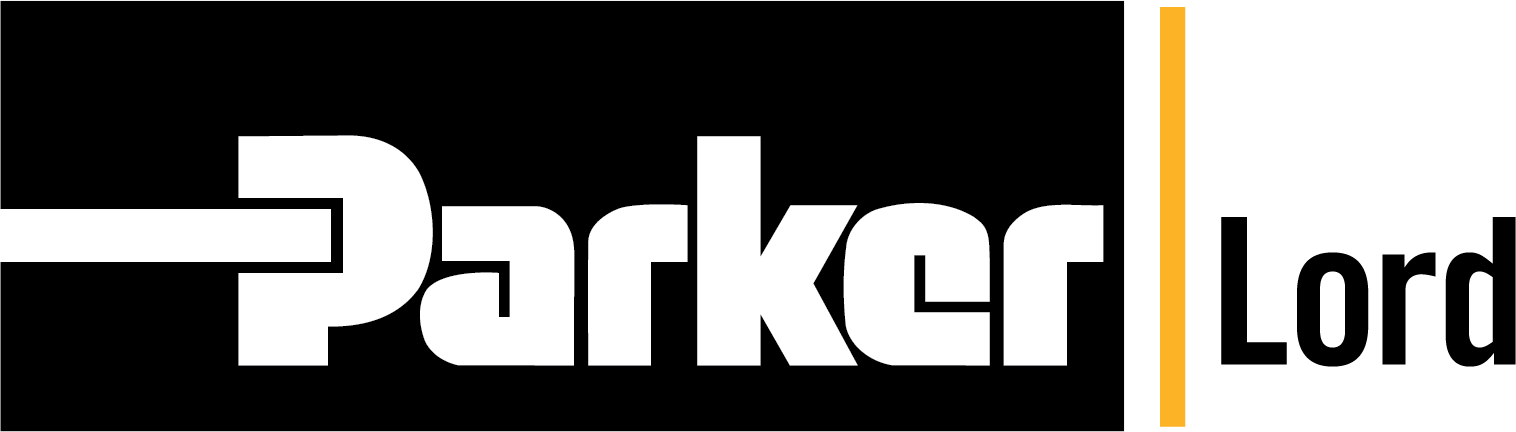
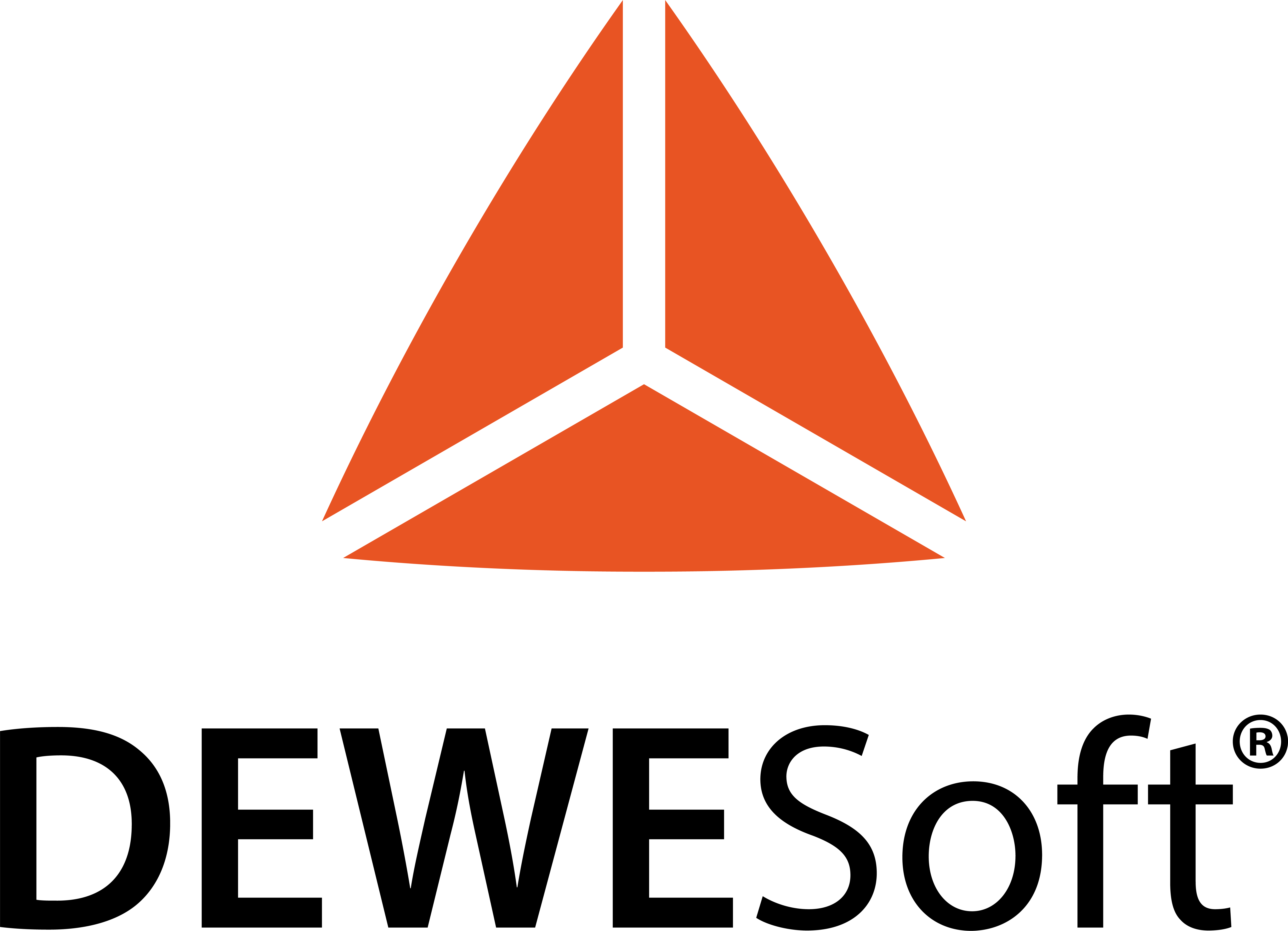
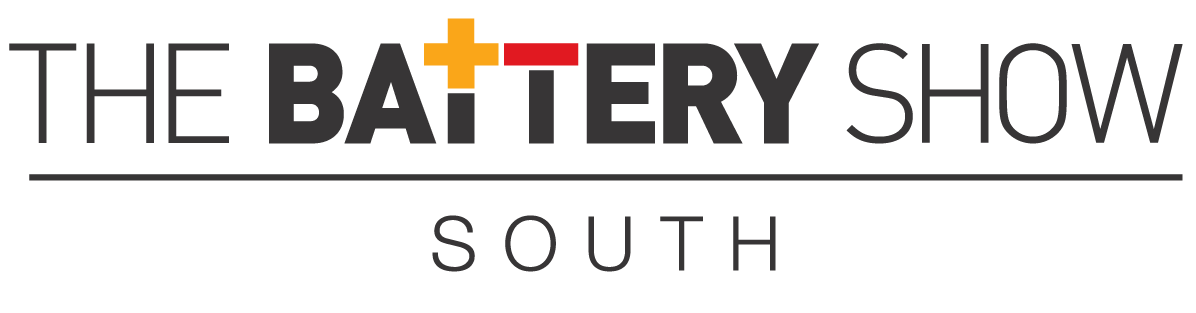
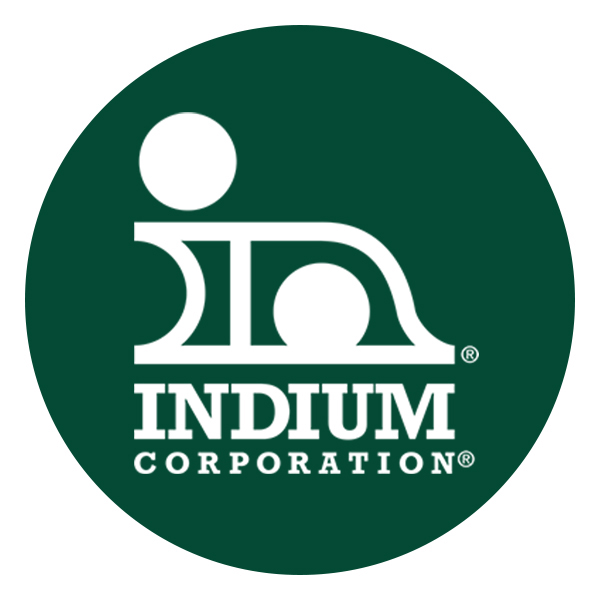
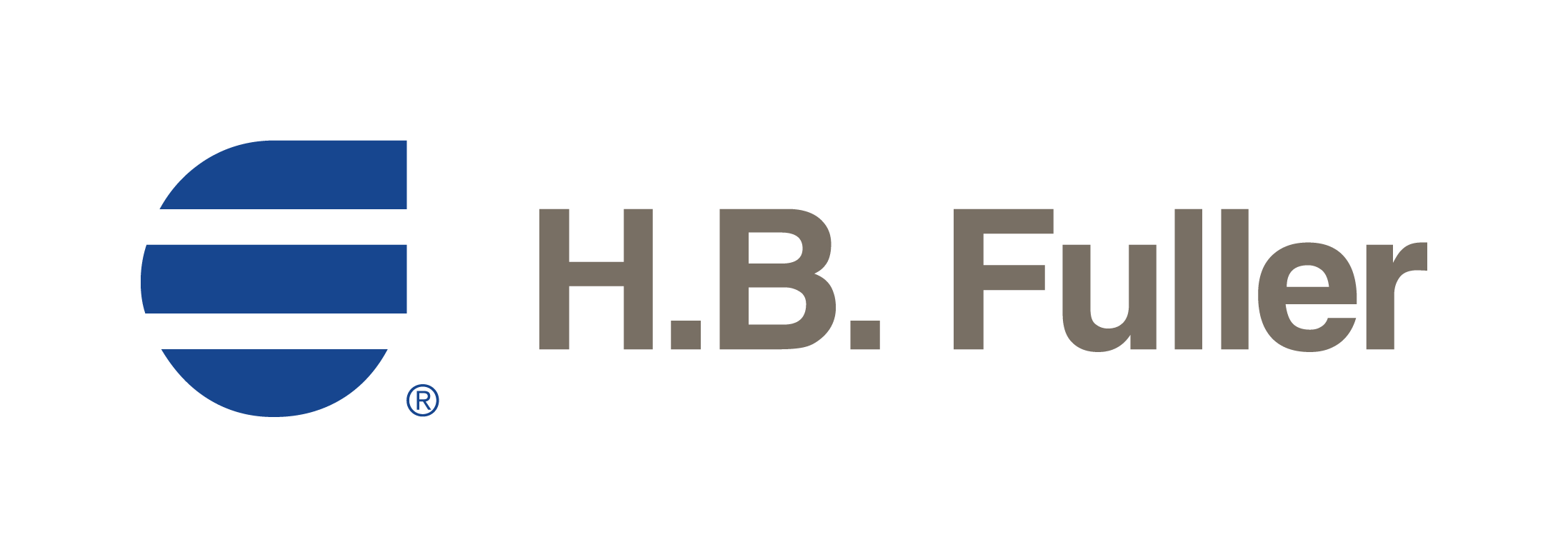