New manufacturing innovations offer EV weight loss
The quest for greater efficiency and range in EVs is often focused on battery technology and drivetrain efficiency, but fundamental physics point to another key factor in the equation: weight. The increasingly popular move from 400V to 800V systems saves weight through lighter cables, but even reductions of a few kilogrammes can make a tangible difference and one company is exploring innovations in sheet metal that could change the game.
The challenge here is in reducing weight without sacrificing strength and durability. Lighter metals can make welding and joining more difficult if they’re prone to warping or may not handle the heat as well as heavier ones – so simply changing the materials is not the way to manufacture lighter vehicles.
Aluminium is increasingly used in car bodies as it is more affordable and more lightweight than other metals. However, it can sometimes be difficult to form and join with other metals and tougher grades of aluminium – or parts that have complex shapes – can introduce a huge range of variables into the lightweight vehicle manufacturing equation.
Casting thicknesses can often vary across cross-sections, making high-quality joining difficult, and with clean surfaces vital for proper welding, gluing and soldering, inconsistent surface conditions necessitate additional treatments, including washing and passivation, extending production time, adding complexity and reducing the anticipated cost savings.
Working with high-strength and press-hardened steels is also challenging as their beneficial durability and strength make them more resistant to cutting or stamping in manufacturing, which makes joining more challenging. A good watertight and gastight seal is vital, particularly in electrical compartments, as without it there can be leaks and corrosion.
Evolving materials
Vehicle materials are evolving all the time, with new joining techniques and new advanced materials such as lighter-weight alloys and composites, but in an automotive environment, the dynamic forces put a premium on good part-to-part connections. Understanding the force that a connection can carry is hugely important in materials consideration.
This is not just a matter of maximum force, but of durability under stress and with dissimilar materials like steel, aluminium and carbon composites all having different thermal, mechanical and physical properties, it is not a simple matter to achieve a reliable joint that takes these different properties into account.
To address and resolve these challenges, Stanley Engineered Fastening has been exploring how thermal innovation can safely and effectively bond lightweight materials, making it possible to build a reliable and durable product without heavier construction. Some of their new techniques in joining could help pave the way to new methods of manufacturing.
Tucker Plasma Riveting (TPR), for example, integrates plasma technology with traditional self-pierce riveting (SPR), expanding the capabilities of SPR beyond its current limits. This innovation enables the joining of even stronger ultra-high-strength steel (UHSS) top-layer stacks with reduced force and makes it possible to assemble previously unachievable material combinations using SPR.
As a result, lightweight sheet metals, including aluminium and mixed materials, can continue being joined without pre-drilling holes, now at tensile strengths up to 2,000MPa and thicknesses of 2mm. This not only reduces the setting force with no punch stroke but results in lower noise emissions and ultimately enhances durability and longevity.
Tucker Plasma Joining (TPJ) is another technique that offers a single-sided access solution that delivers superior structural performance, enabling the joining of steels with tensile strengths of up to 2,000 MPa without the need for a pre-drilled hole. It employs ‘plasma pins’ to penetrate the sheet metal, locally softening the top sheet, and creates strong and reliable bonds, even when joining dissimilar materials.
This adds new application capabilities throughout the vehicle, pushing beyond the standard limitations that would typically require specialised rivets and dies. TPR and TPJ, for example, offer significant advantages when joining aluminium castings as the heat transfer involved in facilitates the deformation of aluminium without causing cracks, making them particularly effective for F-state castings, which are increasingly prevalent in Body-in-White (BIW) design.
There are also innovations in cleaning techniques, with Tucker CleanJet for Stud Welding used to prepare metal surfaces. This plasma-powered solution is attached to the stud weld head and run just prior to the stud welding process to ensure an ideally clean surface every time, guaranteeing a stable stud weld process and shoring up the joint quality.
Tucker Automated Cleaning (TAC) is a cleaning system that uses a robot-mounted torch for linear cleaning of sheet metals, preparing surfaces for soldering, TIG welding or adhesive bonding. This standalone solution offers reduced spatter – due to no oil or other contaminants on the surface – and leads to less post-weld cleaning
Thermal innovations such as can change the game, as they create strong, durable bonds and joints that make it possible to join materials that were previously incompatible. This can expand design possibilities for next-generation vehicles, but their benefits have the potential to extend beyond improved material compatibility, with efficiency improvements that make all lightweight vehicle production more economically viable.
Ultimately, put simply, these new thermal innovations improve cleanliness and joining to make it easier to hold two lightweight metal sheets together. That gives more options for manufacturing at a lighter weight without additional costs, enabling the production of safe, reliable and quality vehicle parts that stop that range dial dropping so quickly.
Click here to read the latest issue of E-Mobility Engineering.
ONLINE PARTNERS
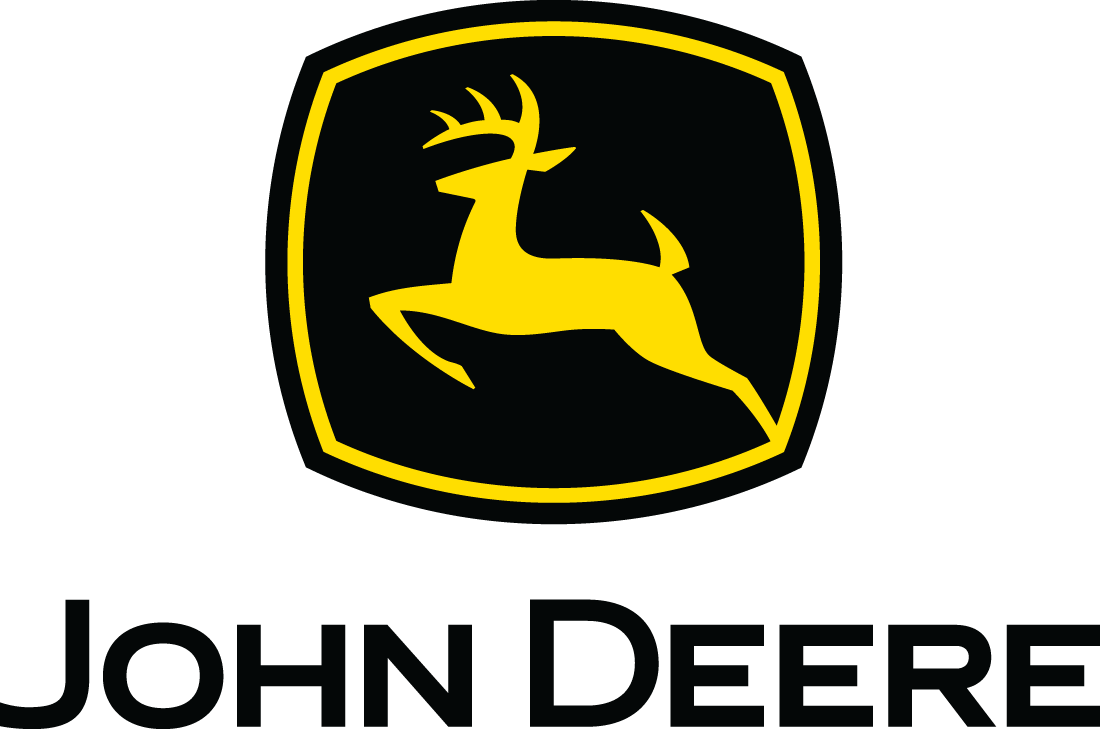
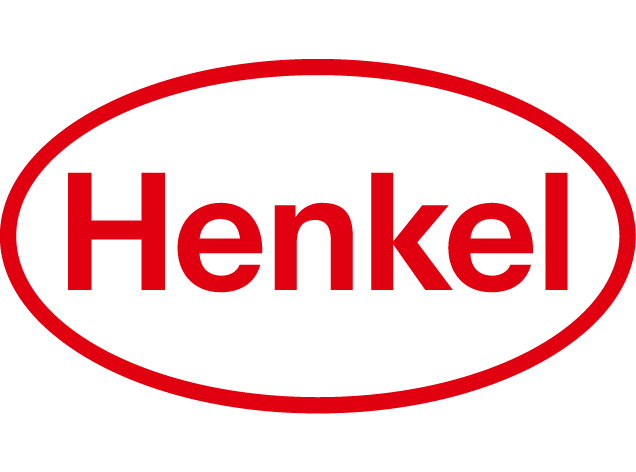
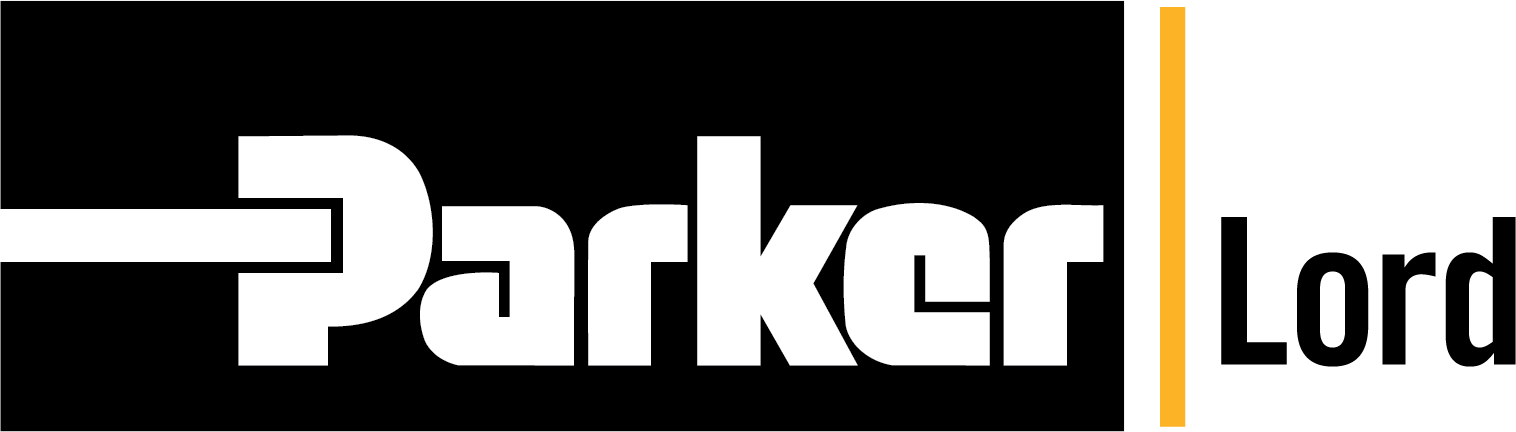
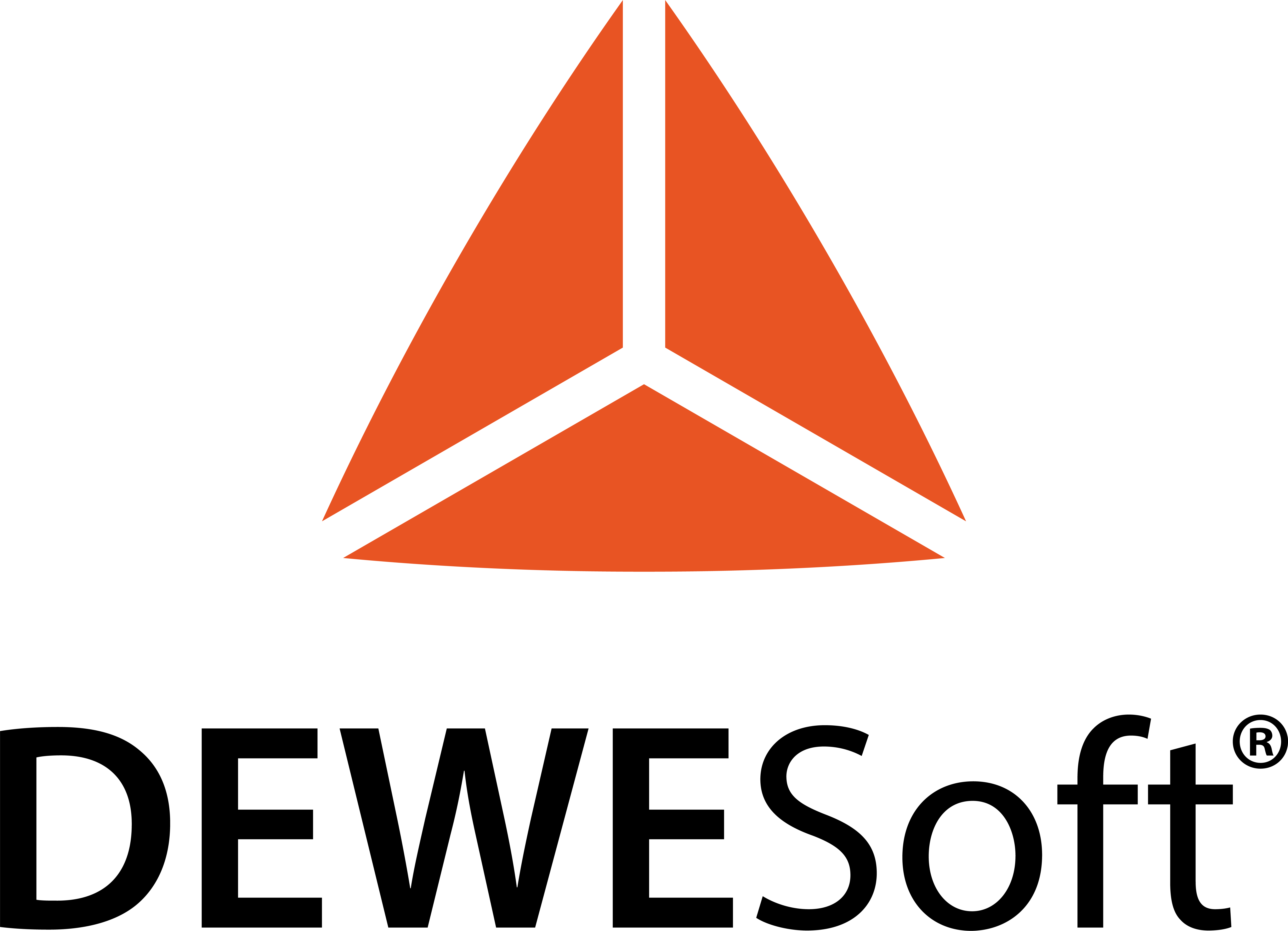
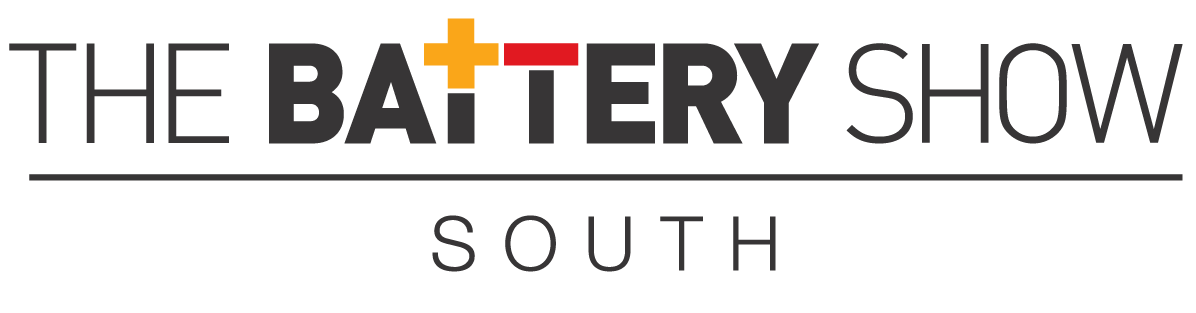
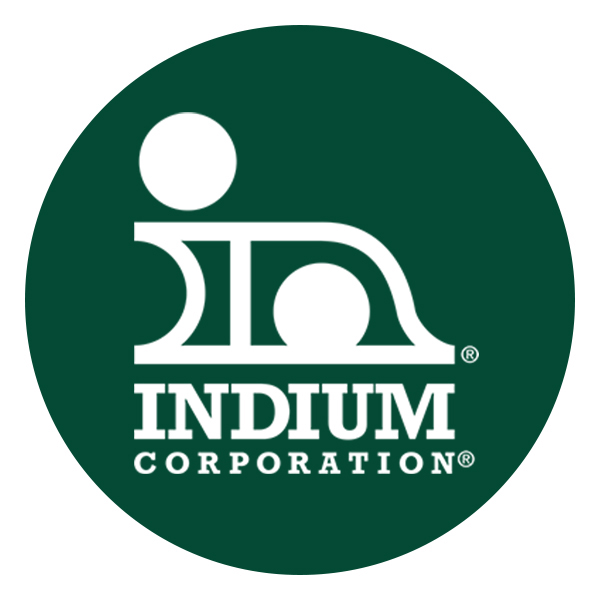

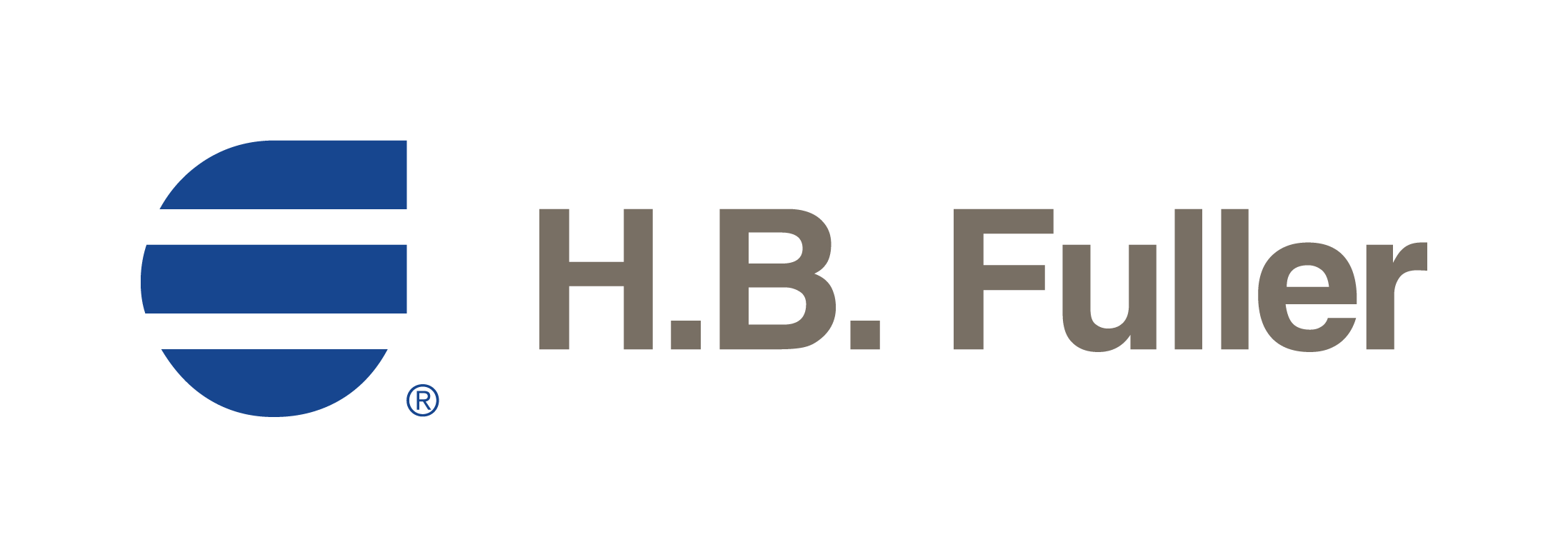
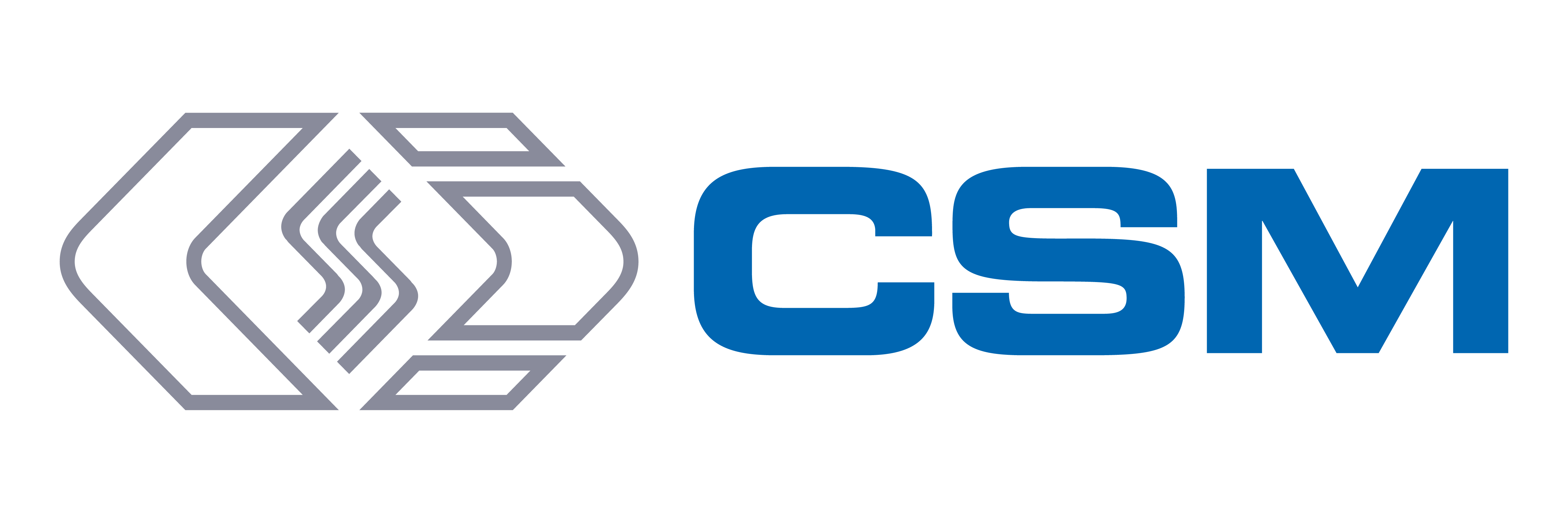
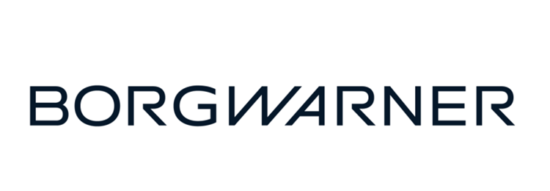