Soteria e-bike project
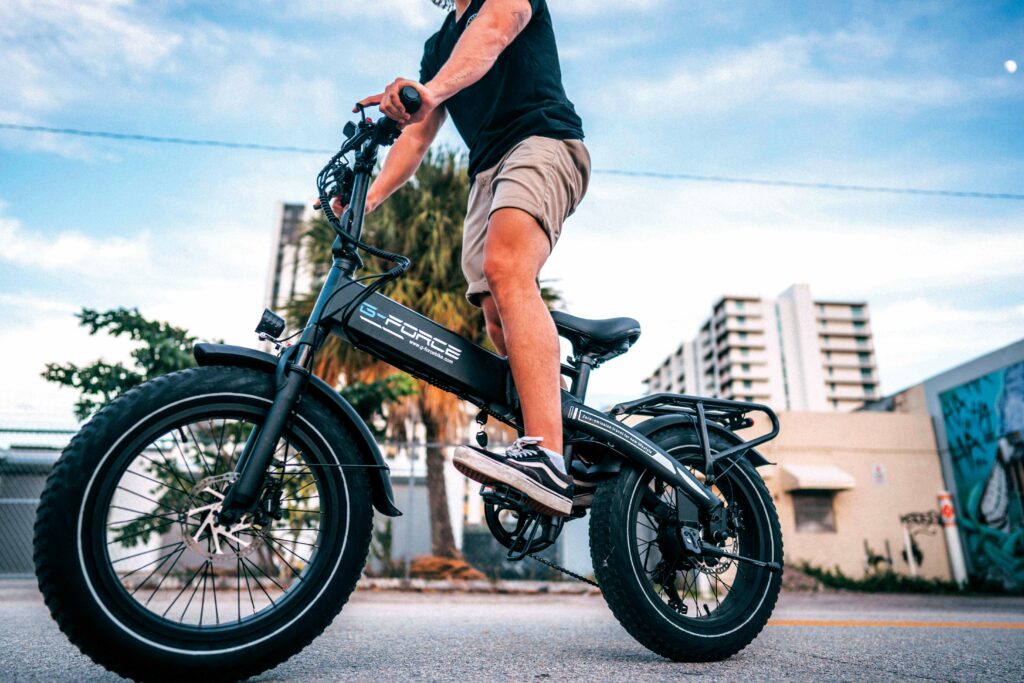
(Image courtesy of Pexels)
Fired up over safety
With lithium-ion batteries among the top causes of fatal fires in New York, Peter Donaldson talks to a company set on making e-bikes less risky
It only takes a few minutes on the internet to realise there is a big safety problem with e-bike batteries. Even a basic search for ‘e-bike battery fire statistics’ yields alarming numbers, press reports, government recommendations and official statements, such as the London Fire Brigade’s (LFB) recent declaration that e-bikes and e-scooters are now the city’s fastest growing fire risk.
In February, the LFB reported a 78% increase in such fires in 2023, compared with 2022, with 155 cases attributed to e-bikes and 28 to e-scooters. Three people died and about 60 were injured. It’s a similar story around the world, with the US House of Representatives passing the Setting Consumer Standards for Lithium-Ion Batteries Act in May in response to pressure from the New York City Fire Department, among others.
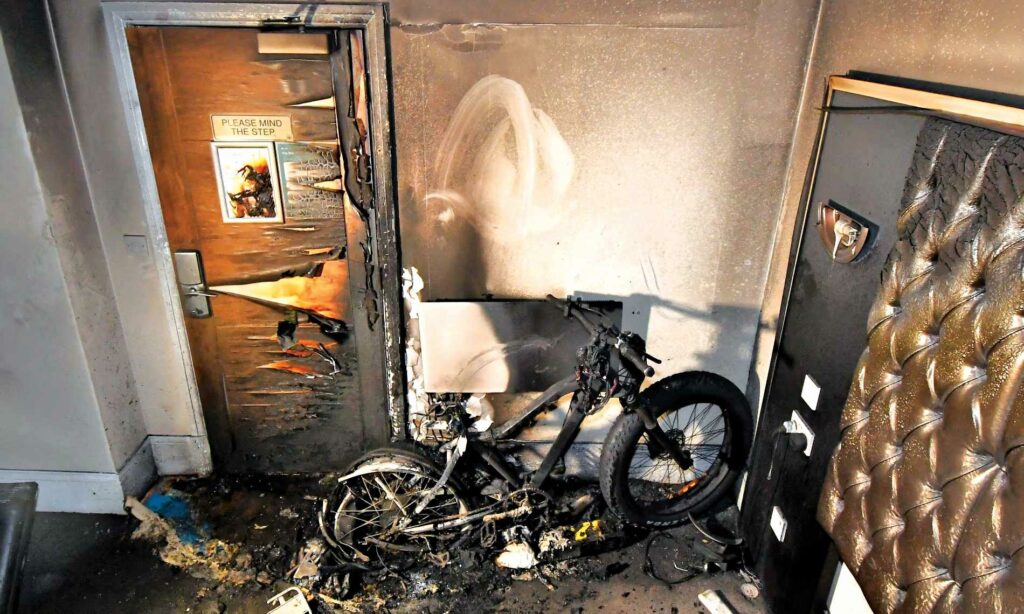
(Image courtesy of Merseyside Fire & Rescue Service)
Point of crisis
“We reached a point of crisis in New York City. Lithium-ion batteries have caused approximately 500 fires and killed 24 people in the last two years, and continue to be among the top causes of fatal fires in New York City,” said fire commissioner Laura Kavanagh when she testified before the US consumer product safety commissioner in July 2023.
It is against this background that Soteria Battery Innovation Group – alongside 13 collaborators, including NASA, Dow, the FDNY and Clemson University – has been carrying out research to come up with a standard set of design features that improve safety, which the industry can apply to the manufacture of e-bikes, either voluntarily or by force of law.
This global consortium boasts more than 110 member organisations, drawn from government, academia and industry, including Mercedes Benz, DuPont and General Motors.
Soteria’s initial research included the dismantling of more than 20 battery packs from OEMs and third-party producers, and a poll that questioned more than 1,018 e-bike riders, of whom 157 had experienced a battery fire.
Riders were profiled to build a picture of typical use patterns, their experience with fires, and demographics that could have an impact on the probability of a fire, while OEMs were interviewed to gain an understanding of how they approach pack design with safety in mind.
Soteria found third-party battery packs, which cost about 40% of the price of an equivalent OEM pack, unsurprisingly used lower-quality components and had fewer safety features. However, some encouraging results also emerged, with many e-bike riders putting fire-protection measures in place while charging, and a significant majority (67%) exclusively using OEM packs.
Among these packs, most included some form of temperature sensor, and one pack stood out for having the safest design, more of which later.
Commenting on the early results in late June 2023, the group’s CEO, Brian Morin, noted that two of the packs dismantled by the team appeared to contain counterfeit Samsung cells, adding another layer of risk.
In terms of design, most packs showed inadequate or zero spacing between the cells, increasing the risk of cell-to-cell propagation of a thermal runaway. They also lacked any type of insulating material between them that could stop or slow such propagation.
What’s more, he said several had a battery management system (BMS) that was either explicitly not designed to balance the charges between cells or no mention was made of cell balancing in the documentation.
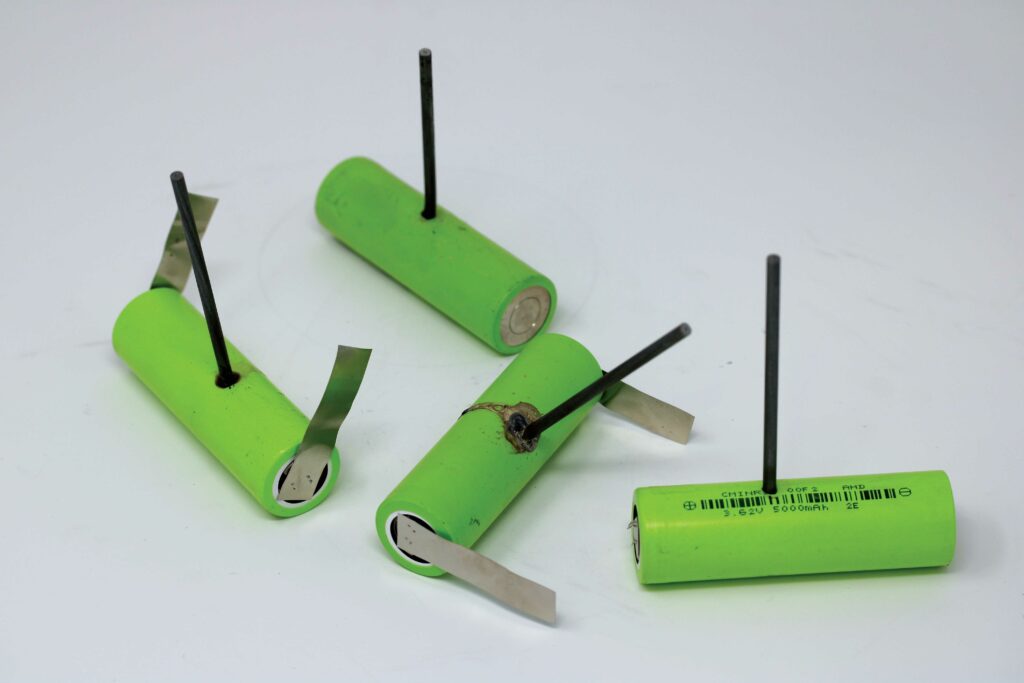
(Image courtesy of Soteria)
Low probability, high consequence
We caught up with Morin in May to bring us up to date with Soteria’s work and to gain his perspective. The vast majority of batteries that fail do so without catching fire, he points out.
“The fail-safe rate is about 99.9%, which at first glance looks like a good number. However, when you have 300,000 e-bikes in New York City, it means six new fires a week, and each is a building fire because of the ferocity and immediacy of the fires,” he says. “There is no chance to put it out before it ignites the building.”
Morin believes the overarching cause of a battery failure resulting in thermal runaway and a fire is a weakness somewhere inside the battery that generates heat, usually within a single cell. What happens next depends on how well the cells are thermally isolated from each other.
With good protection around the cells, an individual cell failure will lead to a battery fire about once in five million cases, which, with 50 cells per pack, would lead to a fail-safe rate of about 99.999%. This, he says, would make battery fires 100 times rarer than they are today.
Morin cites four main causes of e-bike battery failure. The first is cell ageing, where a cell that is weaker than the others is overworked, and eventually overheats and consequently enters thermal runaway.
The second is mechanical damage to the pack through, for example, rough usage, resulting in damage to internal connections, which, over time, cause the cell to be overworked or lead to heat build-up outside it. In either case, the cell overheats and ignites.
Thirdly, some packs provide the cells with little or no protection from shock and vibration, so an individual cell can be damaged, again leading to overheating and eventual thermal runaway.
Electrical damage is the fourth major cause. “Charging cold or bad chargers, or a weak cell, can cause the cells when charging to not be able to accept the lithium into the anode, which will cause it to plate on the surface. This can cause internal short circuits, which, again, will lead to overheating and thermal runaway,” Morin explains.
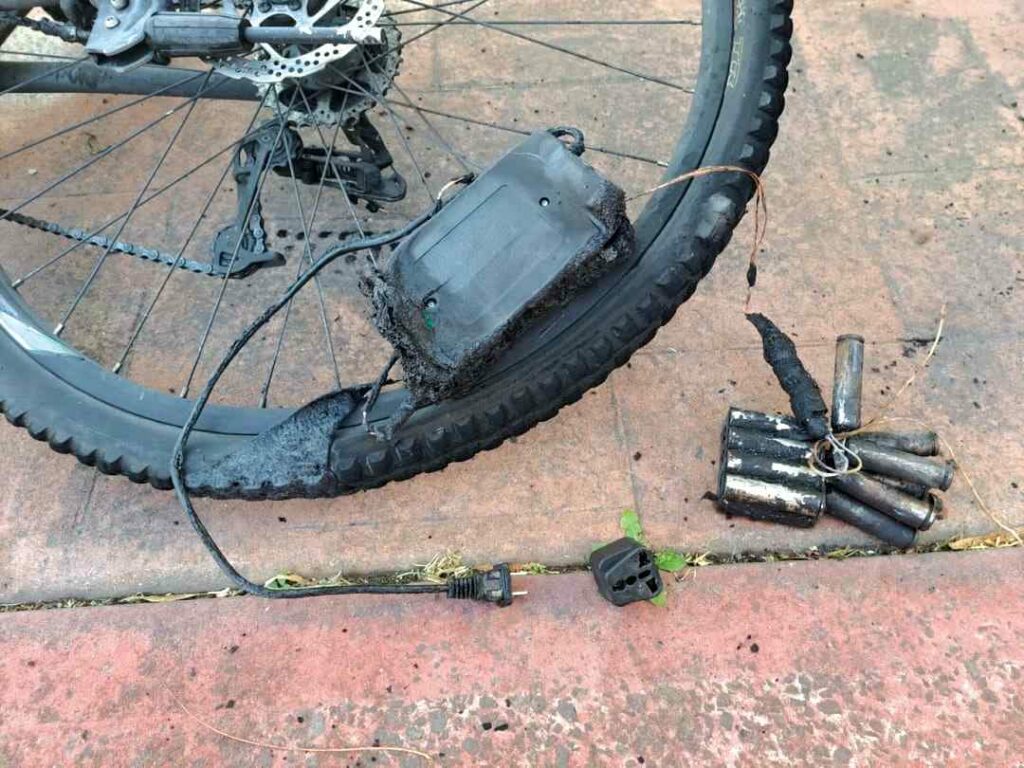
(Image courtesy of New South Wales Fire & Rescue Service)
Counterfeit cells and packs
Another serious problem upon which Soteria’s investigative work shed light is the proliferation of counterfeit batteries and cells.
“The biggest thing is that the cells potentially do not match the performance of the copied cells, so they are going into packs that are designed for a different cell, “Morin says. “Temperature ranges, voltage ranges and other features can be different from one cell design to another.”
Counterfeit batteries will almost certainly be made of cheap materials and lack the safety mechanisms engineered into high-quality ones, and quality is likely to be of the minimum necessary to prevent immediate failure.
What’s more, they are extremely unlikely to be assembled in tightly controlled environments, such as the expensive clean rooms in which reputable manufacturers put cells together, with the risk that dust, moisture and other contaminants will get in and cause early failures.
As considerable effort goes into making fake cells resemble high-quality ones from reputable manufacturers, they are not easy to spot.
“Counterfeiters are really, really good, so it’s only possible to tell by taking a cell of known manufacture and comparing it to the potentially counterfeit cell, and then looking at specific features such as the size and shape of the button, the type of casing materials and marking, the size and features on the can, and other features,” he says.
To avoid the fakes, Morin advises battery builders buy cells either directly from a manufacturer or from a trusted company with a good reputation as a distributor of that manufacturer’s cells.
Unfortunately, it is almost impossible for consumers to distinguish counterfeits from the genuine article. “The cells are on the inside of the battery and impossible to identify from the outside,” Morin says. “For now, the likelihood of counterfeit cells is highest from the very lowest-price packs, but there are high-quality replacement packs out there from reputable companies.”
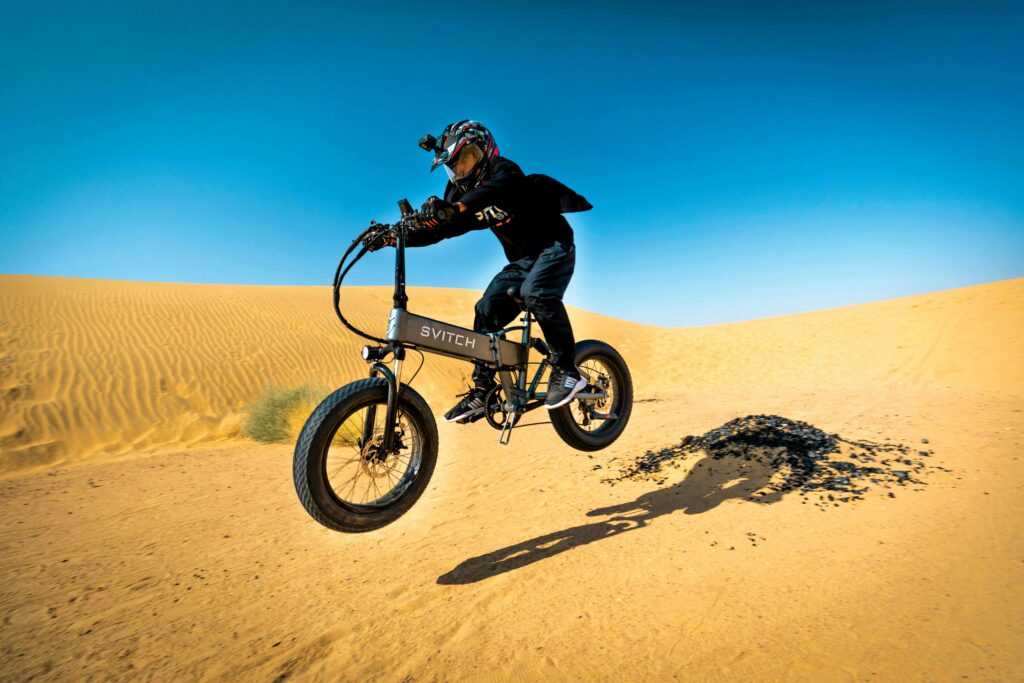
Safety, present and absent
Modern e-bike battery packs usually have a range of safety features, including protection against overcharging, overdischarging and excessive currents. They are also structurally stable, and usually sealed against the ingress of moisture and contaminants.
“There are also several safety features that we’ve identified that were not present in any of the e-bike batteries we examined,” Morin says. “We sat our committee down and asked them, ‘what is the minimum, clearly defined feature set that will give a very safe battery?’.”
They came up with five features that happen to be standard in batteries for larger EVs. The list begins with cells that are certified to an international safety standard and manufactured under a well-established quality assurance programme, such as UN 38.3.
Next, each battery pack should be fitted with a vent that keeps moisture out, but allows the hot gases from a failing cell to escape without creating excess pressure inside the pack or heating up the rest of the cells.
Although fuses are relatively common, Soteria recommends there being a fuse between each cell and its neighbours in a module, and between each module and its neighbours in the pack; the idea being to prevent a damaged cell from drawing excess current that could damage the surrounding cells or battery system components, and generate heat inside the pack.
The fourth and fifth features concern thermal management. Each cell should be connected to a thermal conductor that will transfer heat away from it and to the outside of the pack. “This, by itself, will prevent many battery pack fires,” Morin says.
Also, each cell should be thermally insulated from its neighbours.
And, lastly, the BMS should – in addition to providing the standard overcharge, over-discharge and over-current protections – receive data from a set of temperature sensors and be able to shut the pack down if a high temperature is detected.
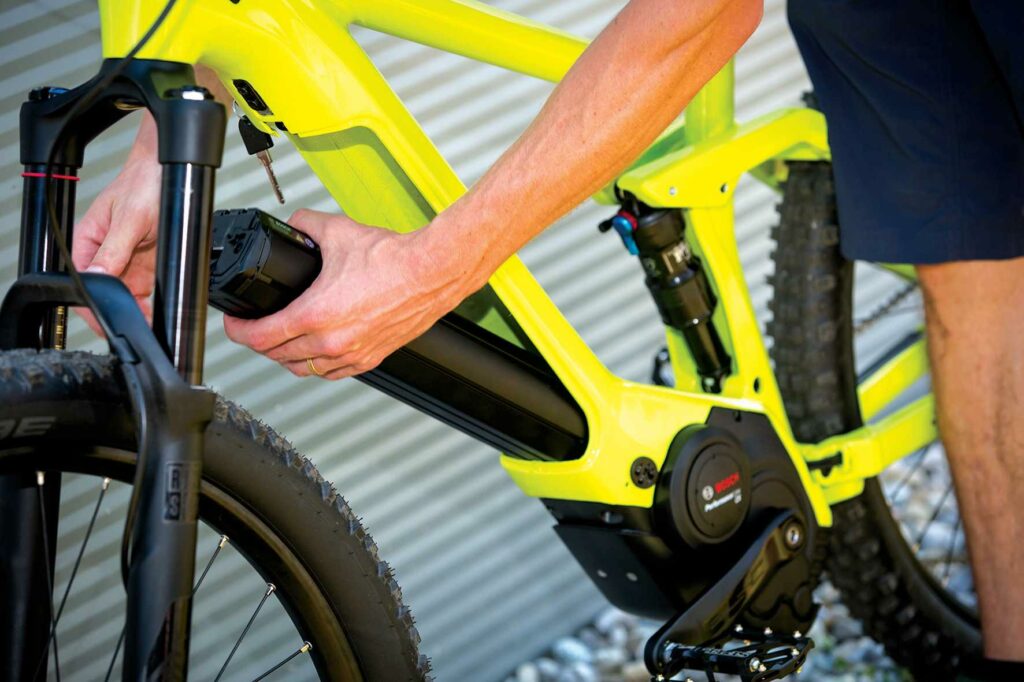
(Image courtesy of Bosch)
Rider input
Soteria’s study identified a number of operational factors associated with battery failure in e-bikes, such as riders using them for deliveries. Morin stresses there is nothing special about any individual trip for deliveries that is different from, for example, commuting, but delivery riders do experience higher failure rates for several possible reasons.
“If I had to guess, I would say they just use their batteries to a much higher and longer degree, not throwing them away when they get worn, and it is the old batteries that have weak cells in them or have had some level of mechanical damage.”
Riders carrying out their own maintenance also seems problematic. While working on mechanical systems such as chains, sprockets and tyres is fine, Morin points out that anything related to the electrical components should only be handled by a trained technician.
“Under no circumstances should someone replace the cells on the inside of a battery,” he stresses. “There is just too much that can be different about the new cells, and some of the things that need to be done to take the old cells out are irreversible and will leave the battery in a vulnerable state.”
Morin also recommends that refurbished batteries should not be used, given the standard of many on the market. He explains that taking a battery apart and replacing the cells, even with identical ones, will leave it in a vulnerable state. Any connections and welds done by hand will tend to be of variable quality and greatly increase the failure rate.
The final operational factor identified by Soteria was riding mountain bikes in the way they are designed to be ridden.
“Here, the use patterns are more aggressive, with far more vibrations from general use, and more shocks from wipe-outs that are a normal part of mountain biking,” Morin notes.
“That’s not to say don’t ride electric mountain bikes, but plan to replace the batteries more frequently just to be safe, and check them for any mechanical damage before every ride. Never use a pack that has more than cosmetic damage to the surface of the case.”
The safest pack that Soteria examined had several key features that were missing from the others. It was of very high quality in its materials and construction, revealing particularly good welds, for example. It also had a custom BMS; an approach that typically provides more sensors and software to monitor cell quality and ageing through a battery’s service life.
In this case, it had several well-placed temperature sensors within the pack. The cells in this pack were also of a very high quality from a reputable manufacturer and they were manufactured to UN 38.3 or an ISO quality standard. It still left something to be desired, however.
“Even the best packs were missing some of the five requirements we plan on having,” adds Morin.
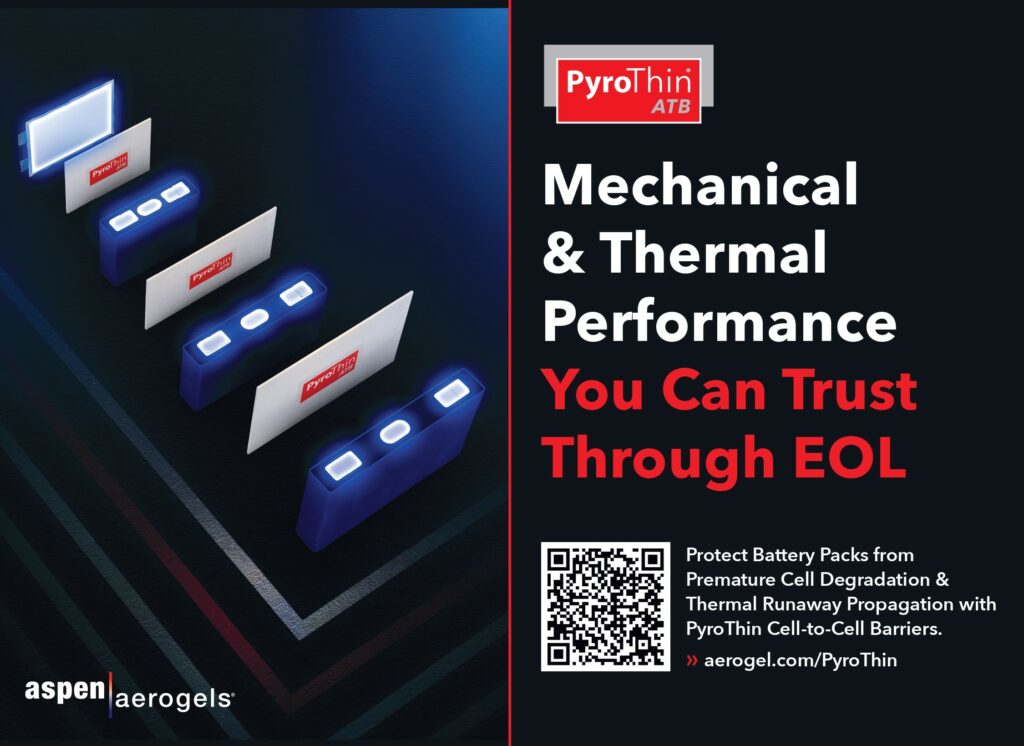
Technological progress
Several emerging technologies could improve the safety of e-bike batteries, according to Morin, and are likely to be used in combination with the abovementioned fuses, vents, thermal conductors and thermal insulation. These include composite current collectors made from combinations of polymer and metal, which are designed to be fail-safe to give cells localised protection from excessive currents.
Thermally stable separators are another emerging technology for use inside cells. They are under development to replace conventional, plastic separator membranes with alternatives that remain stable at temperatures that are hundreds of degrees higher, preserving the barrier that prevents short circuits between the anode and the cathode.
Morin points out that several companies now offer non-flammable electrolytes, which significantly reduce the risk of a battery catching fire.
In larger EV battery packs, sensors are increasingly being used to detect overheating and alert the BMS to the presence of the gasses produced when a cell starts to emit them in the early stages of a thermal runaway, enabling the BMS to cut the battery off from further loads or currents. The application of such devices to much smaller e-bike batteries requires miniaturisation and a reduction in cost.
As they get bigger, e-bike batteries of the future could benefit from well-designed cooling systems, with both passive and active options under development, Morin says.
He is critical of both industry and regulators for not agreeing on standards and testing procedures that are good enough to ensure the safety of batteries. “While each existing standard is a step in the right direction, compromise between the component manufacturers who make up the committee can lead to missing features representative of higher safety,” he says.
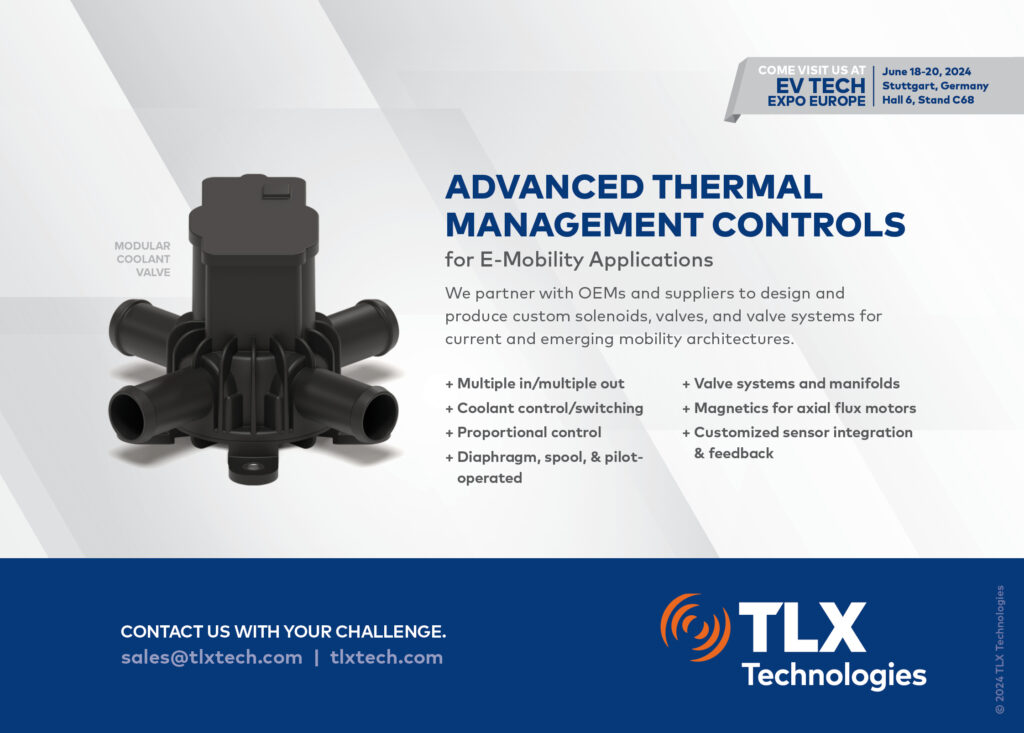
New standard, political action
Soteria is planning to publish its own standard this summer with what Morin calls a comprehensive list of necessary design features enabled by the above technologies.
“We have to recommend using this, or a standard that includes at least all the features included in our own standard,” he says. “If nothing else, put in abundant active temperature monitoring and passive cooling for every cell in the pack. This isn’t enough, but it is a big step in the right direction.”
The industry is also collaborating on political action to establish and uphold safety standards with, for example, bills presented to both parts of the US Congress (the Senate and the House of Representatives), which, if passed, will require a nationwide battery safety standard to be put in place. Further, the Society of Automotive Engineers (SAE) has formed a micromobility standards committee to address the issue.
“Active participation is needed to make sure the bills pass, and that the committees put in place standards with all of the necessary features that will produce a very safe battery pack,” Morin says.
While getting these bills through Congress is important, he argues that the fastest way to achieve the industry’s safety goals is through voluntary adoption of the Soteria standard, and using markings to identify to consumers that enhanced safety features are in place.
Interim precautions
Until such a standard governs the production and testing of e-bike batteries, the owners, riders and operators will remain obliged to handle and maintain them in a manner that minimises risk. This, Morin argues, involves taking a conservative (and somewhat expensive) attitude towards service life, particularly of cheaper batteries.
“I wouldn’t use an e-bike battery pack beyond about 250 charges. After this, the cells can start to age, and not knowing the quality of the battery pack manufacturer, it is safer to replace it with another high-quality pack.”
(It is possible to have a service centre check the battery’s state of health, even if its BMS doesn’t report it to the user.)
Morin also advises against further use of any battery with more than cosmetic surface damage to the pack casing, and only ever to use a charger recommended by the battery’s manufacturer, and always to charge it in a cool, dry place, well away from flammable materials.
Another non-obvious risk is that conventional alarms are not good at detecting the smoke and gases from lithium-ion battery fires. Such alarms are designed to detect the smoke from burning wood, plastic, paper and other common domestic materials, which range in size from a few microns to tens of microns, and their effectiveness drops significantly for particles smaller than 1 micron. Unfortunately, the smoke from a lithium-ion battery is mostly composed of particles smaller than 0.1 microns.
To solve this problem, Soteria is developing a dedicated detector that is sensitive to the emissions given off by lithium-ion battery fires, including hydrogen, carbon dioxide and volatile organic compounds (VOCs). As many batteries are designed to vent gases before the cells reach a temperature at which they will ignite, Soteria’s alarm can sound an alert up to 15 minutes before a fire starts.
In one set of tests, the organisation says, a single cell going into thermal runaway brought the hydrogen level from below 1 ppm (ambient) to over 500 ppm. Morin says the system is expected to be available in the autumn.
Progress and future plans
Since Soteria reported its interim results last summer, it has continued to push its work forward. This has included the disassembly of more battery packs, including used ones to build an understanding of how usage affects their condition, and interviews with e-bike manufacturers.
The consortium has run a workshop with more than 20 participating organisations, and it was this event that defined the minimum feature set required to make a very safe battery.
The results of this workshop also informed the draft of the Soteria E-bike Battery Safety Standard, which has been refined and is now supported by an audit checklist that battery developers can use to ensure their products conform to the standard.
Going forward, the consortium’s efforts are focused on getting the safety standard published and working with industry to help them implement it.
“We will work with the supply chain to ensure companies can produce components of the quality required, and with battery pack manufacturers to help them design packs and get them certified to the standard,” Morin emphasises.
“We also plan to run a communication campaign to help e-bike riders understand the difference in battery pack design and how it affects their safety.”
Soteria has issued an open invitation for anyone interested in advancing e-bike battery safety to get in touch.
Click here to read the latest issue of E-Mobility Engineering.
ONLINE PARTNERS
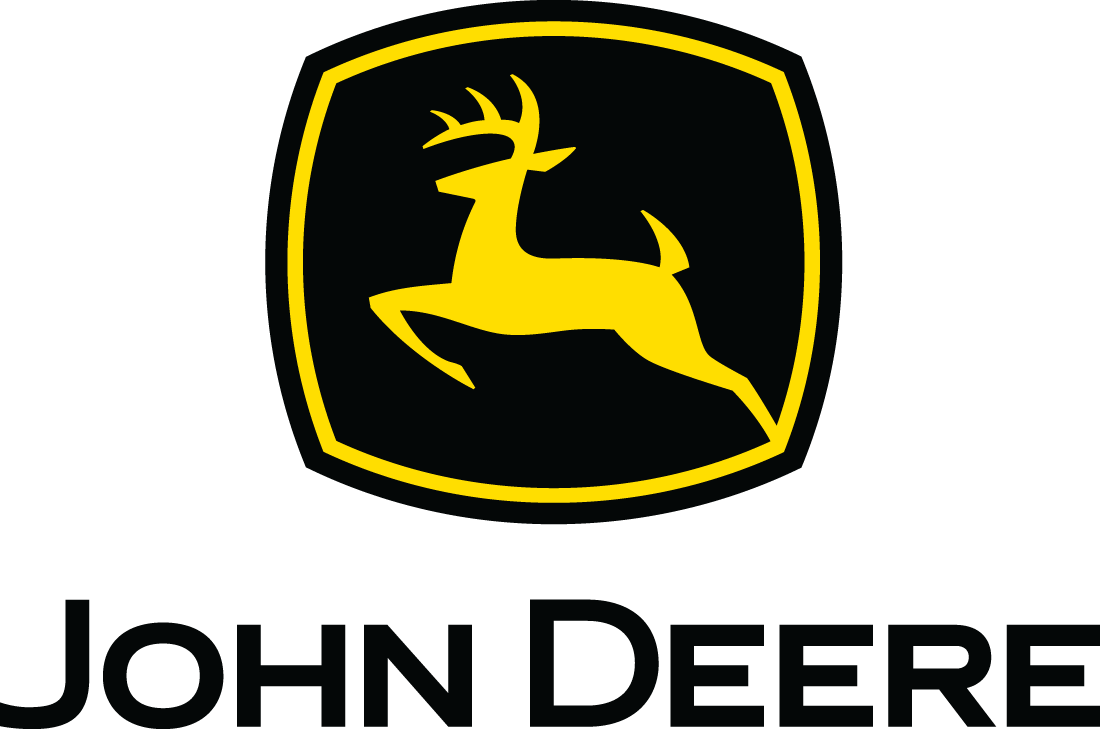
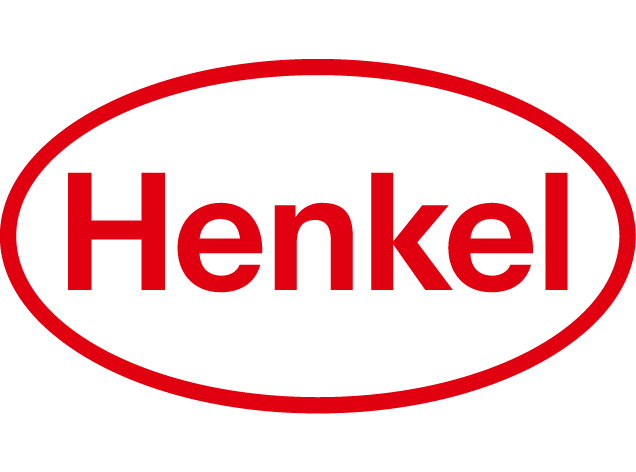
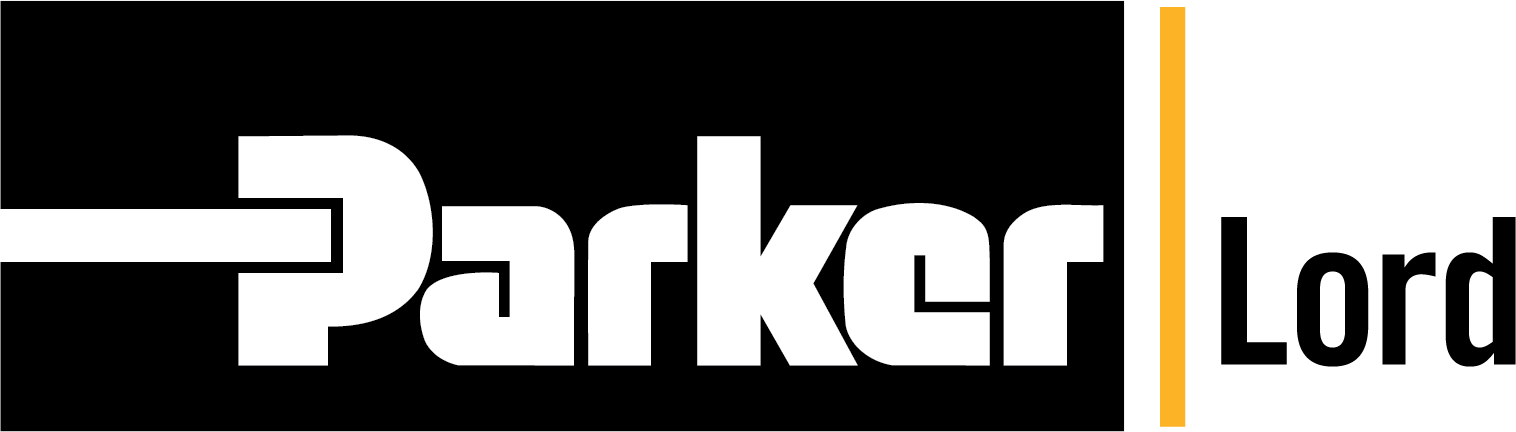
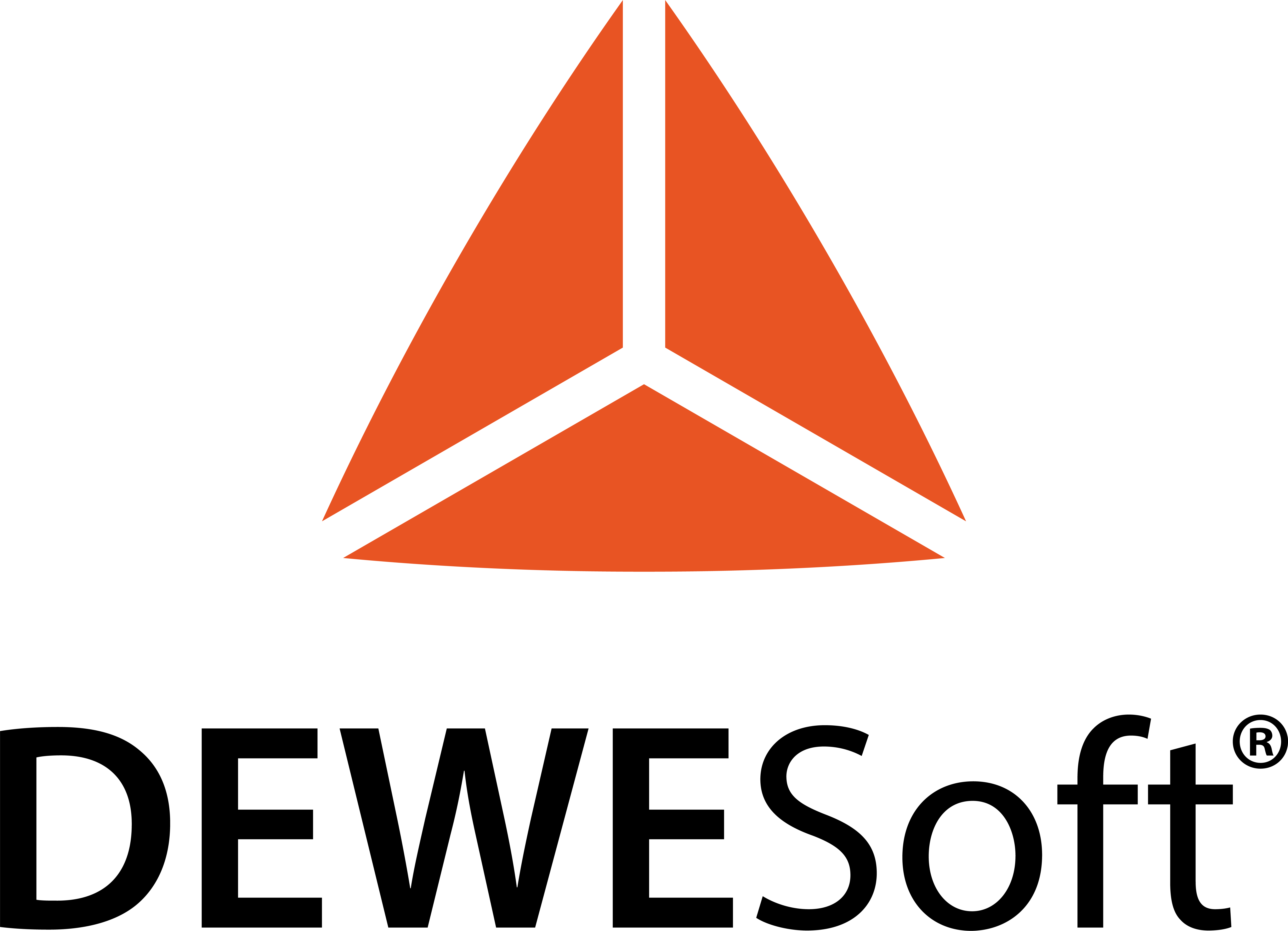
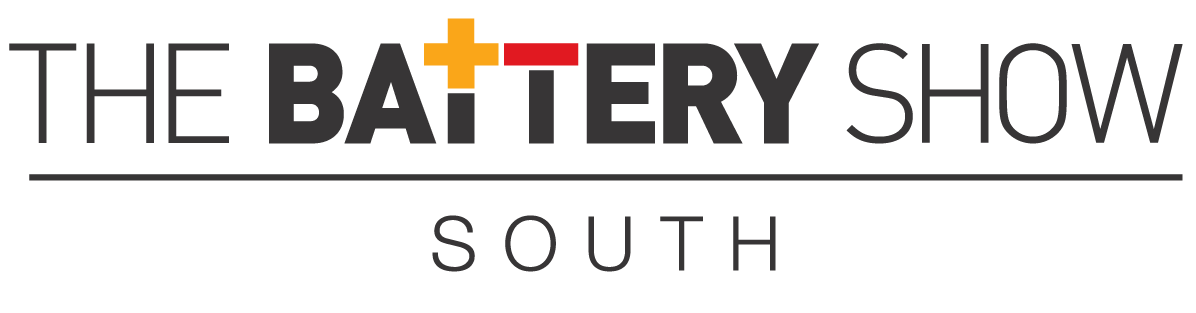
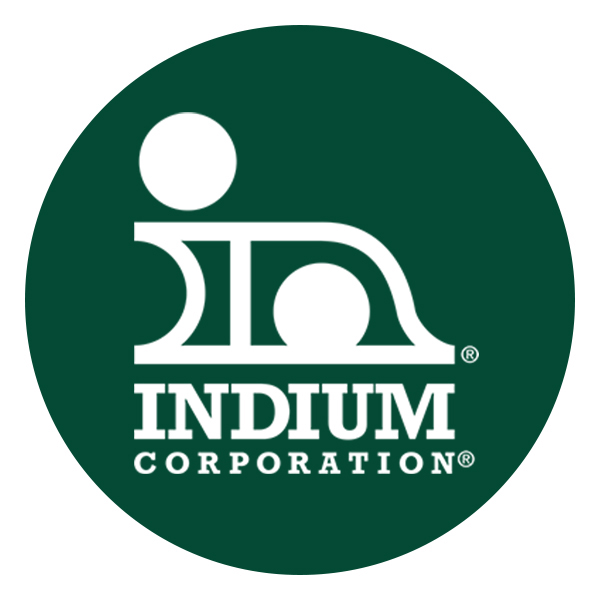
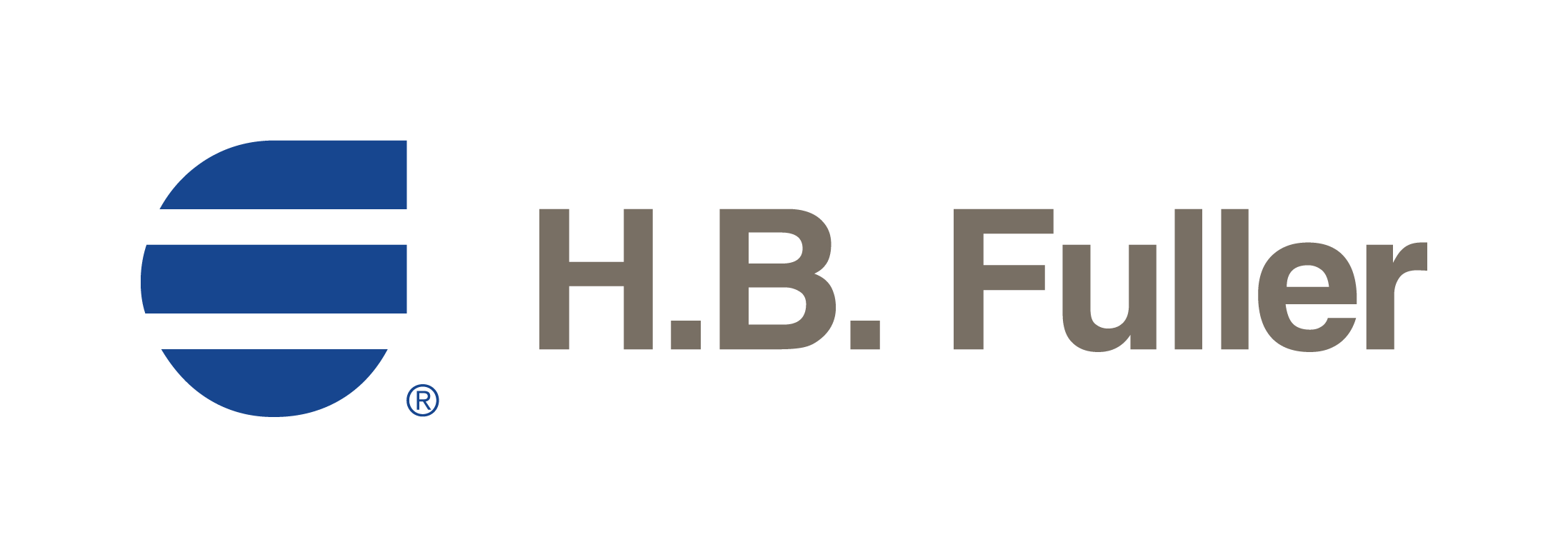