Sion powers ahead with its Licerion battery tech
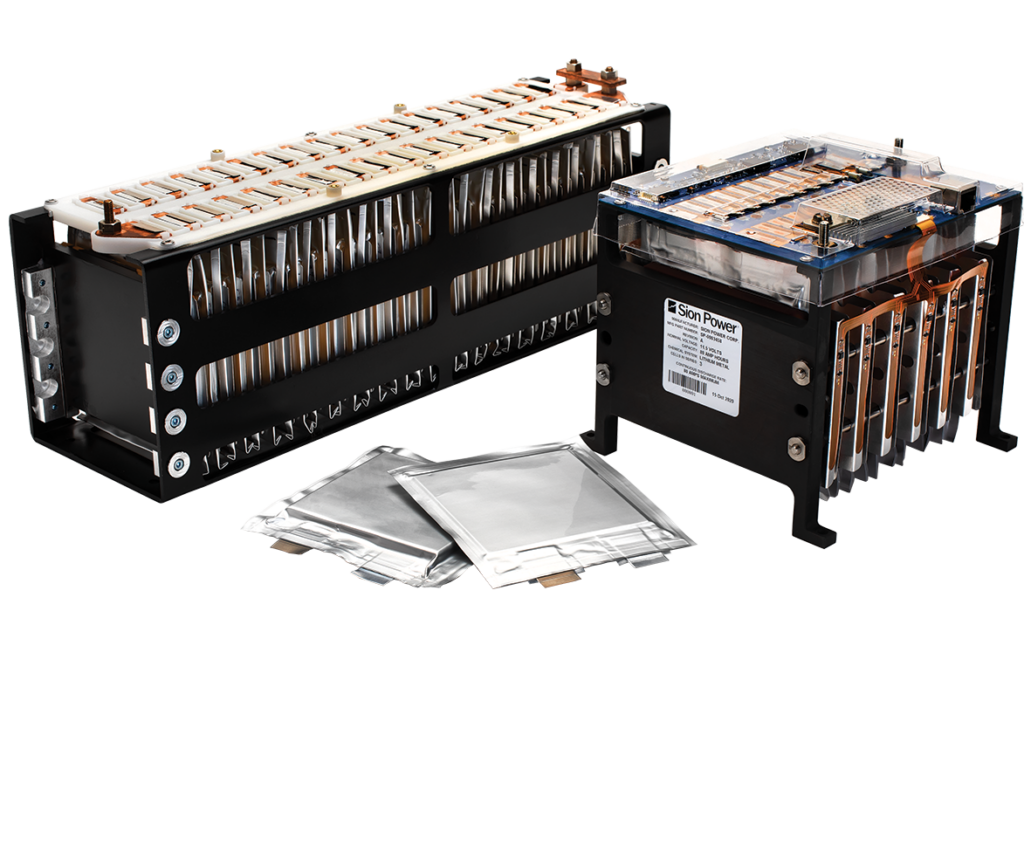
(Image courtesy of Sion Power)
In the seemingly eternal quest for greater energy density in batteries, one of the most promising lines of development is the lithium metal battery, in which the conventional graphite anode is replaced by a pure lithium metal foil. This is the approach that Sion Power is taking with its Licerion battery technology, as CEO Tracy Kelley explains to Peter Donaldson, bringing us up to speed with the company’s progress.
“Lithium metal is very energy dense,” he says. “The normalised energy of the graphite used today is 360 milliamp hours per gram (mAh/g); that’s its theoretical capacity. For lithium metal, it’s around 3,862 mAh/g, so it’s an order of magnitude more energy dense. What that allows us to do is essentially take the vast majority of the volume out of the anode, and because it is a more volumetrically efficient battery, you get a huge bump in the weight reduction by making that change.”
In terms of specific energy and energy density at cell level for car battery applications, the engineering team is targeting figures in the range of 400-450 watt-hours per kilogram (Wh/kg) and 1,000 watt-hours per litre (Wh/l). What those figures will be at pack level depends heavily on the design, architecture and materials of the pack.
Advantages
However, Kelley says a pack based on Licerion technology would have a 30-40% advantage over a conventional lithium-ion battery pack.
Licerion technology is also compatible with a wide range of cathode materials, including high-energy, nickel-rich materials such as lithium nickel manganese cobalt oxide (NMC), as well as lower energy options such as lithium iron phosphate (LFP). LFP is widely used because it doesn’t contain any of the rare metals such as cobalt. It’s also very stable and much cheaper, he says.
“We like to call our system cathode-agnostic, as we are able to take commercially available cathode materials and incorporate them, and we project a substantial energy bump from the chosen material,” says Kelley.
Licerion cells retain a liquid electrolyte, although the technology provides a path to a solid electrolyte in future developments, he confirms. Today, however, Sion Power is working on maximising the service life of its lithium anode.
“As we produce that anode, we are able to put certain conductive structures on the surface that shield it from the liquid, in theory, cutting down on potential parasitic reactions,” he says.
Cathode and electrolyte materials are among the key cell components that Sion power can change to tune the cDefault Paragraph Styleell chemistry for specific applications. The company formulates its own electrolytes, as the standard compositions are designed to work well with graphite anodes.
“We tune the electrolyte, optimising it so that it is lithium-metal-friendly,” Kelley says. “That could entail changes in the conductive elements of standard solvents used in lithium-ion cells, or it could be an additive to enhance stability. There are a number of things we can do, but we always keep an eye on the commeDefault Paragraph Stylercial availability of the materials we are testing.”
Safety features
Licerion technology also incorporates several redundant safety mechanisms. One of these is the use of an externally applied compressive force to suppress the growth of dendrites and the development of side reactions. Dendrites are sharp, branch-like projections that can penetrate the cell separator and create a short circuit between anode and cathode, and the company has several patents in the area of suppressing dendrite growth.
“It is our belief – and we are not alone – that any cell that is commercially viable will need to apply some type of pressure to mitigate some of these side reactions, as well as dendritic growth,” says Kelley.
Sion Power also carefully tunes the anode foil thickness for each application to minimise the amount of lithium metal in the cell without compromising performance. “Typical thicknesses of available lithium foils are from 30-50 microns. We routinely produce foils that are 5-15 microns thick,” he says.Default Paragraph Style
“We believe the overall reduction of lithium in the system is key to mitigating some of the safety problems of the lithium-ion cell. Lithium is highly reactive, so having less of such an energetic material in there helps mitigate the total output of energy from any thermal event.”
Thorough testing
The company’s prototype cells have been through sets of government-mandated safety tests, including the UN38.3 tests that determine whether batteries are safe to transport and in-house customised tests.
“We have custom-designed equipment inDefault Paragraph Style-house to consistently bring cells to failure and to understand multiple aspects of failures, including the initiation temperature, thermal release, the types of gas being released during these behaviours and the potential for a failed cell to ignite the cell next to it,” Kelley says.
In terms of progress towards commercialisation, Sion Power recently partnered LG Energy Solution and is pursuing other partners. It is currently procuring equipment to build a “scale prototype”, which is intended to be the first commercially viable cell.
“That equipment will be installed by year-end, and in the 2027 timeframe, we expect to be delivering the first commercial cells to customers,” Kelley adds.
Click here to read the latest issue of E-Mobility Engineering.
ONLINE PARTNERS
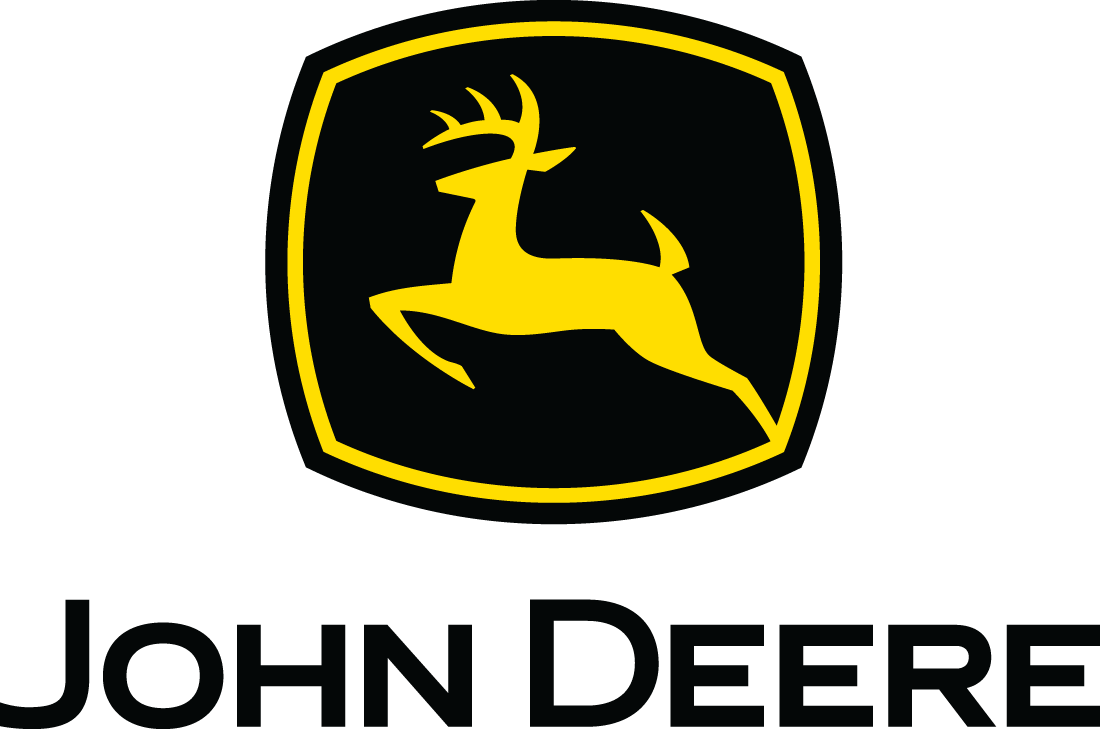
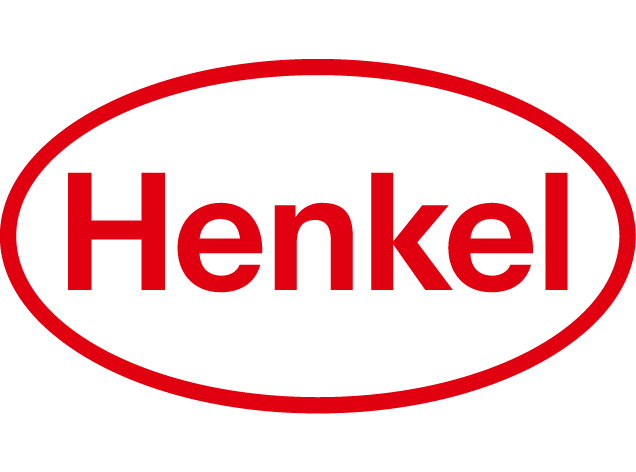
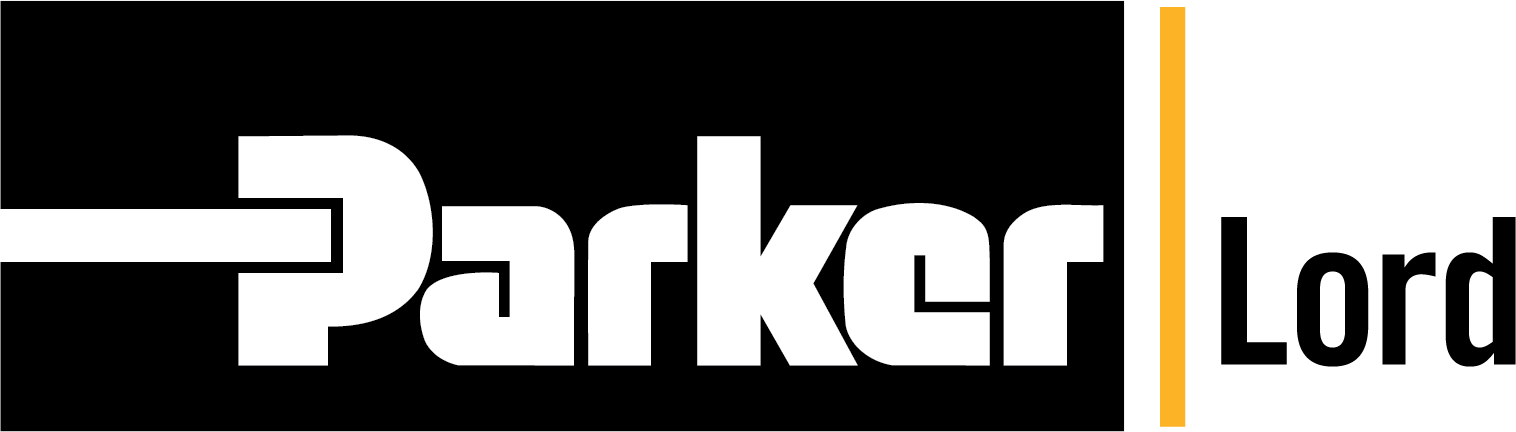
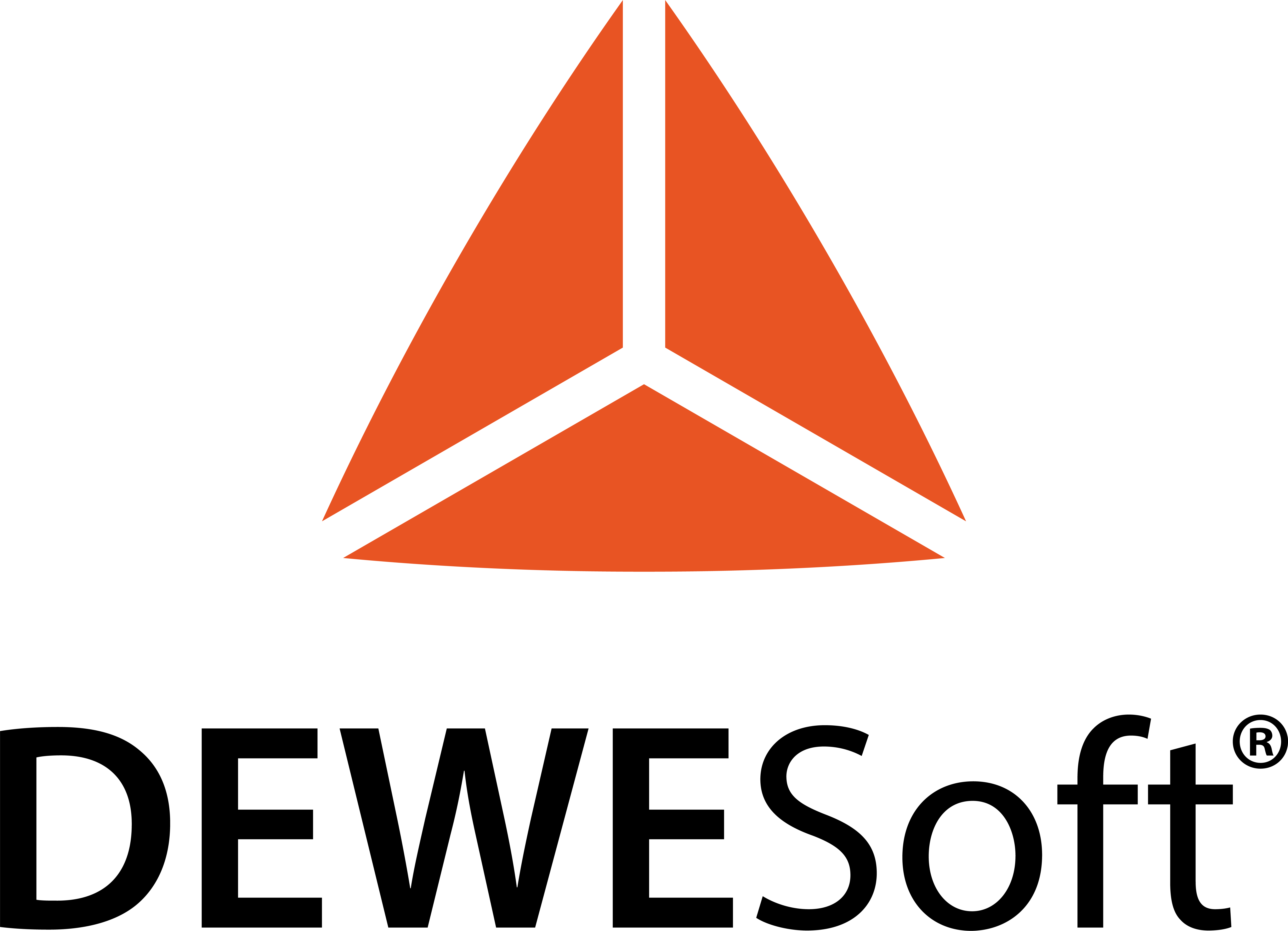
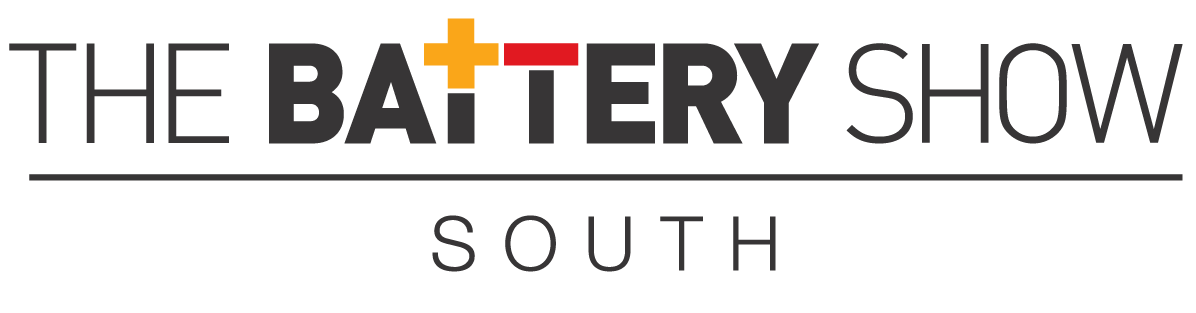
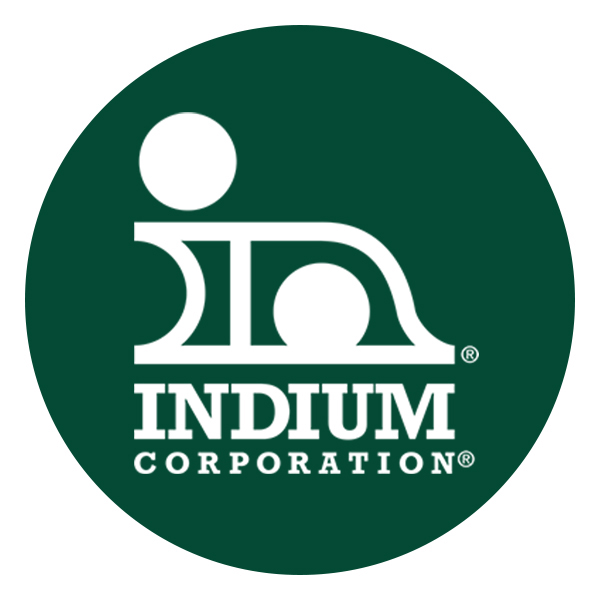
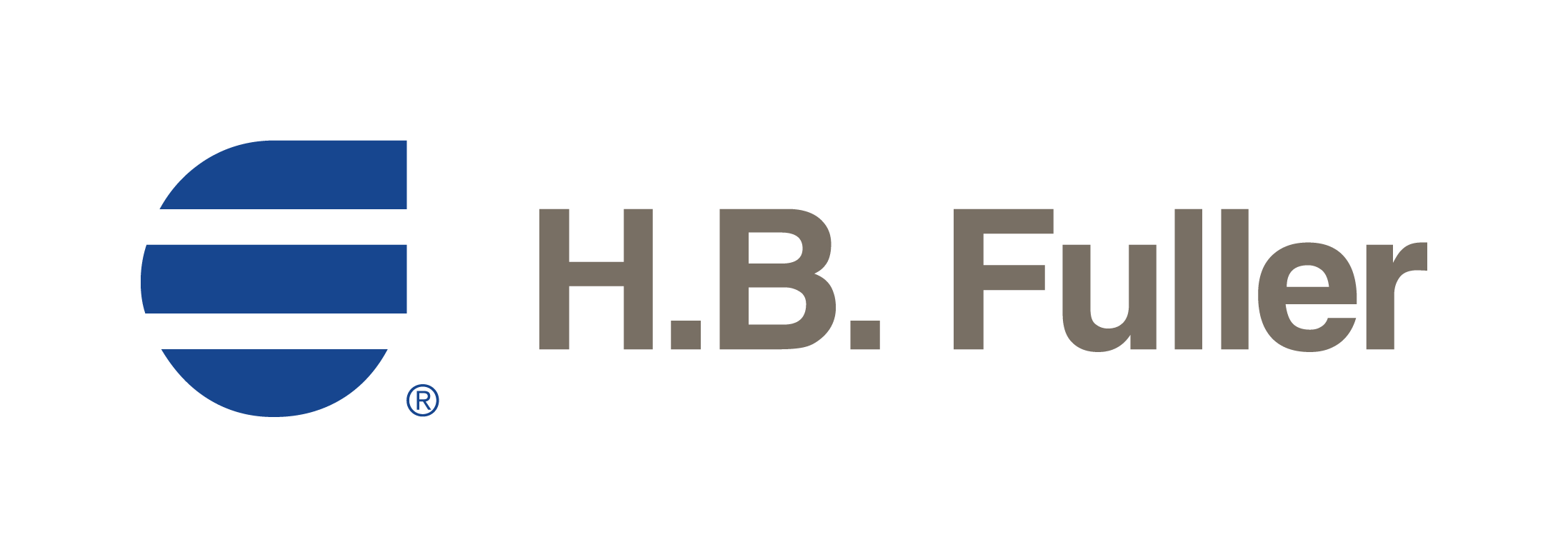