Schuler automates high-speed blanking with Backlack
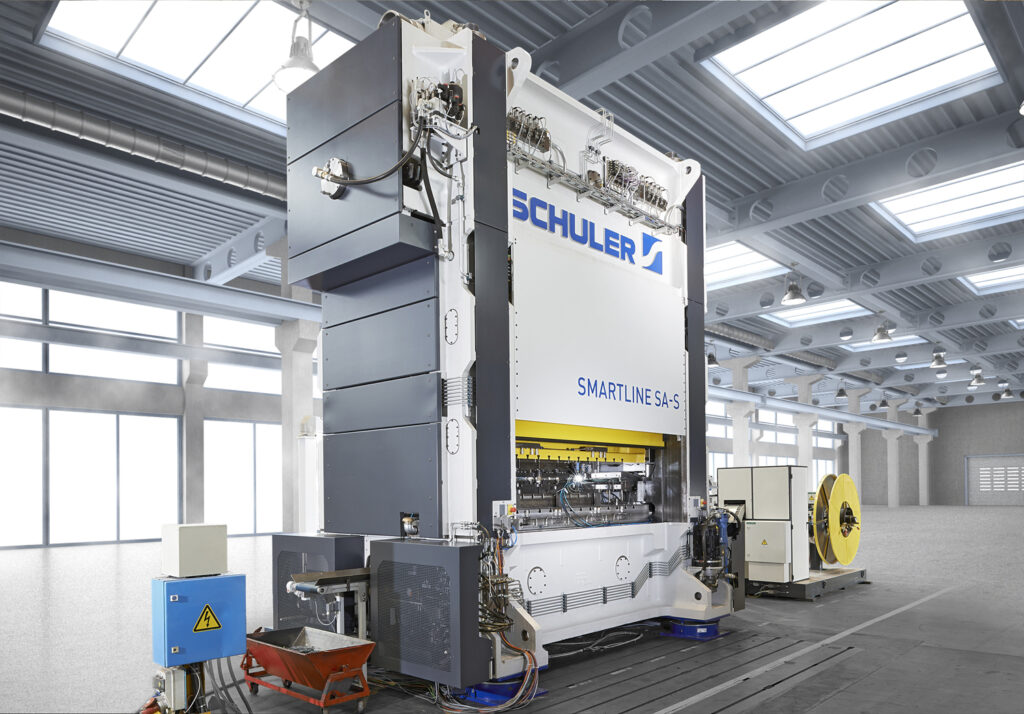
Various methods are used to produce stacks of laminations for electric motors from electrical sheets. Schuler has integrated its Backlack technology into a complete, fully automated turnkey system with a high-speed press, as well as stacking and baking stations. This includes all processes from unwinding the raw material to the finished rotor and stator stack, which feature improved magnetic properties.
In the Backlack process, the electrical sheets are joined together to form a stack under pressure and high temperatures in a baking station by Swiss company SWD AG. This creates a full-surface bond, which will reduce vibration and noise in the motor.
Due to the denser layering of the sheets, cooling liquids can neither escape nor penetrate. The higher thermal conductivity of bonding varnish compared with air is an advantage for cooling, and the sheets are perfectly insulated from each other.
A fully automated system collects the electrical sheets underneath the progressive die, brings them into the form of individual sheet stacks of the desired height and then transports them to the separate bonding varnish stations. Up to 80,000 rotor and stator stacks can be produced per year.
Schuler will be exhibiting at the EuroBLECH trade fair in Hanover, Germany, at Stand G82 in Hall 27, from October 21-25.
ONLINE PARTNERS
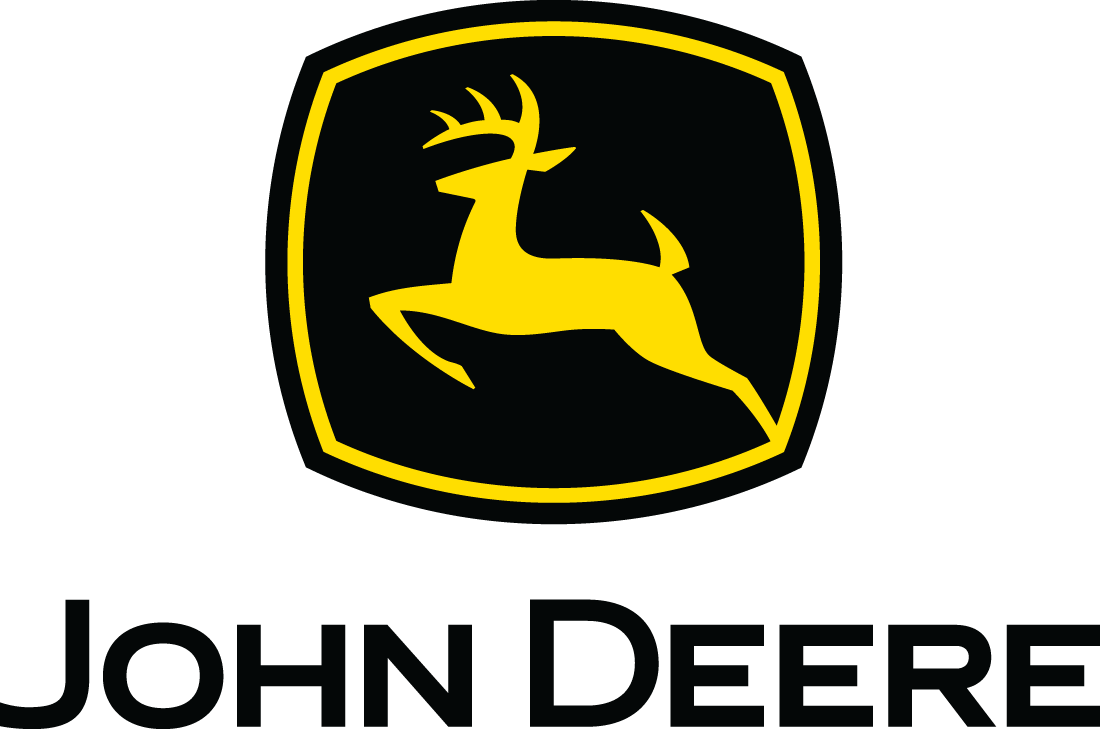
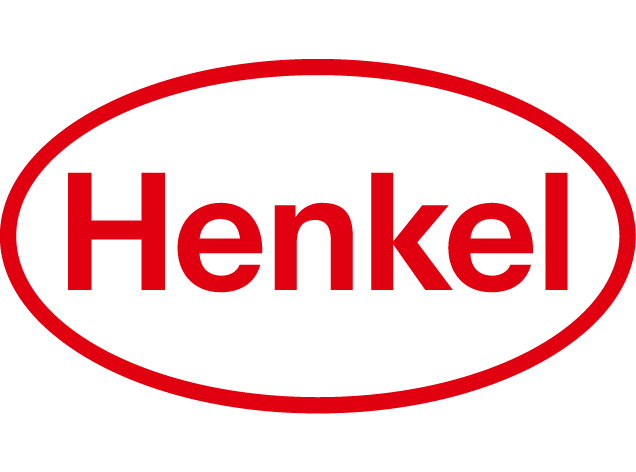
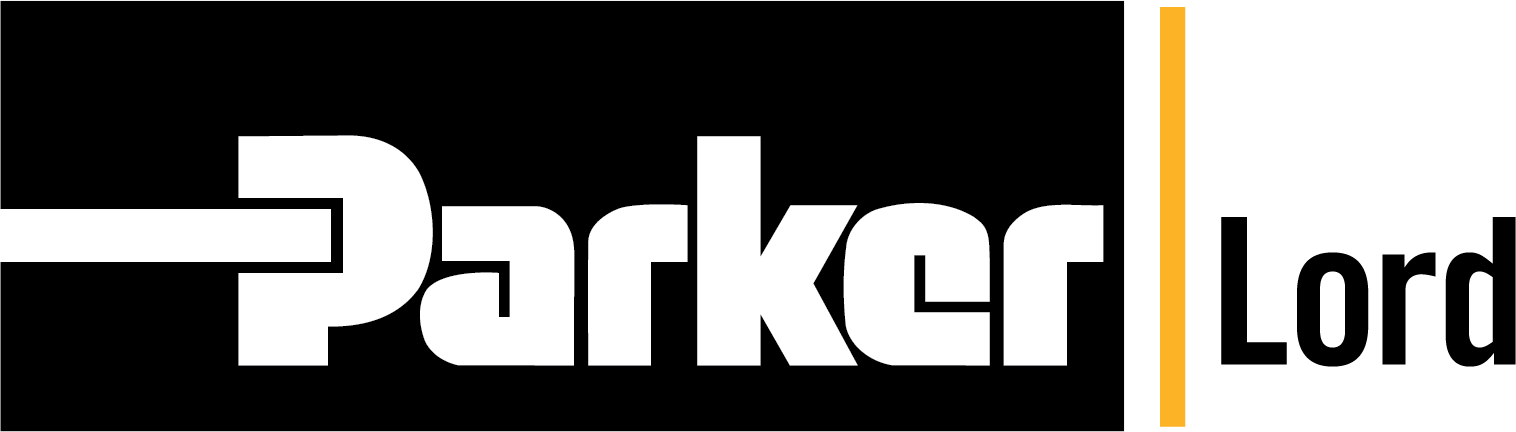
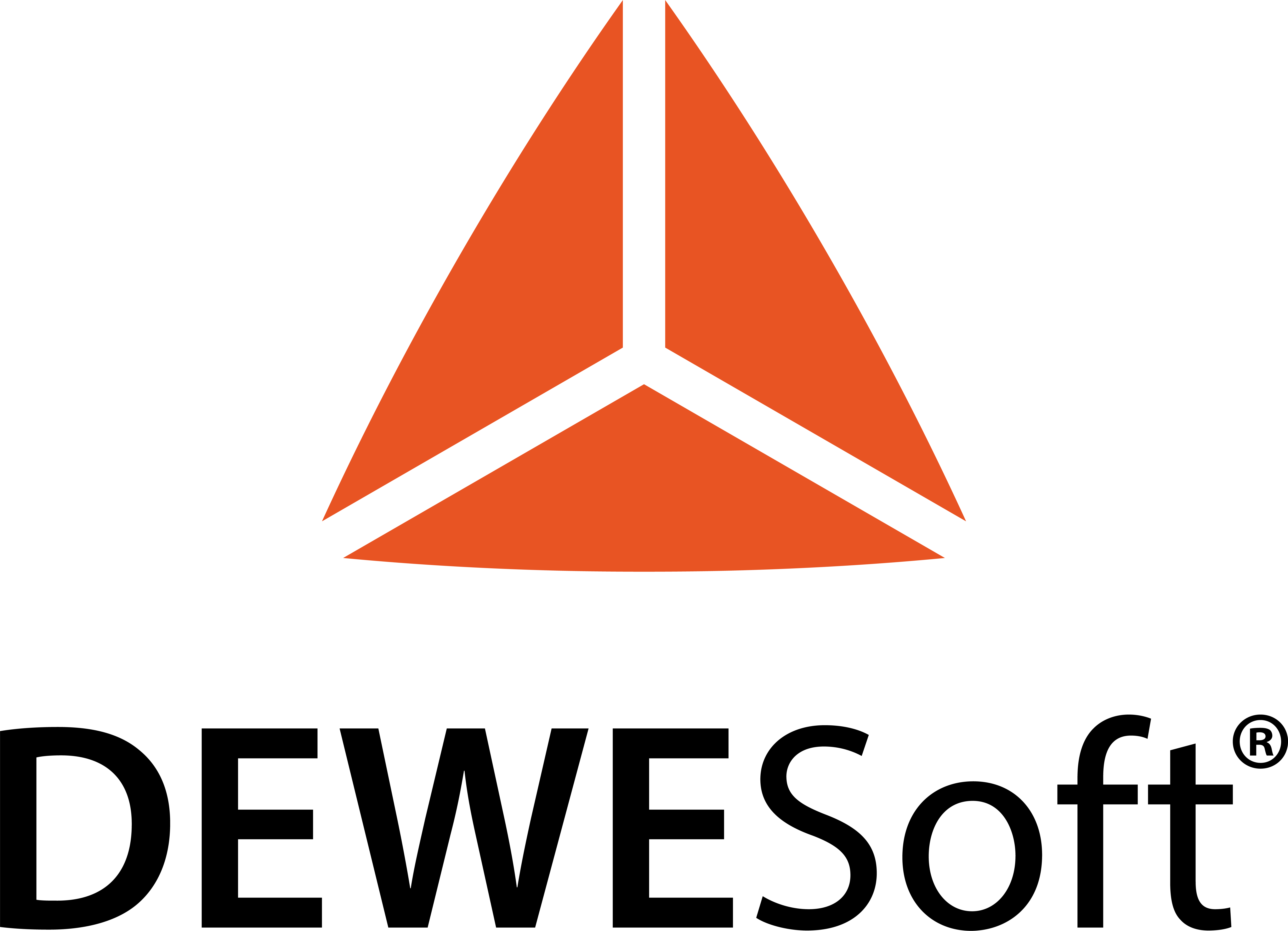
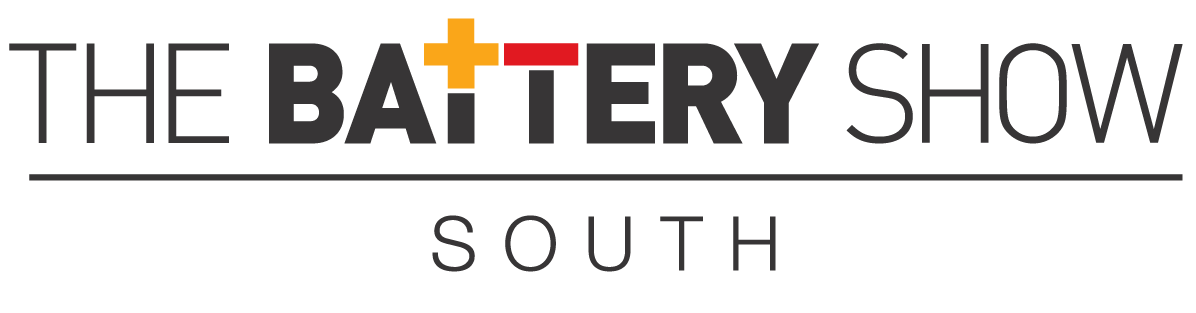
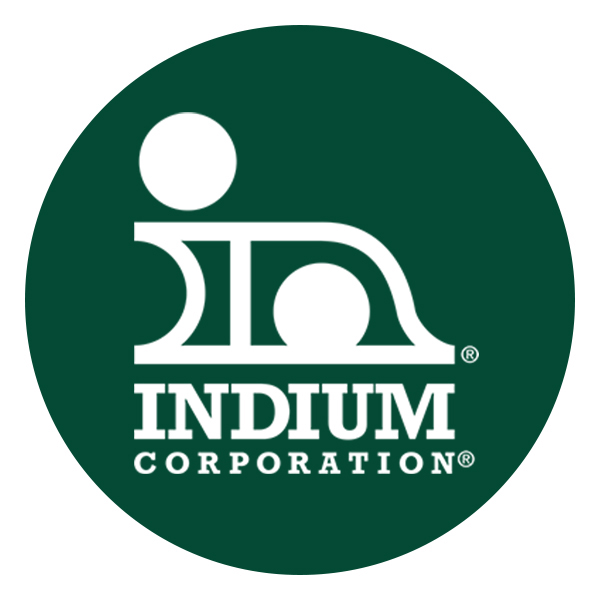

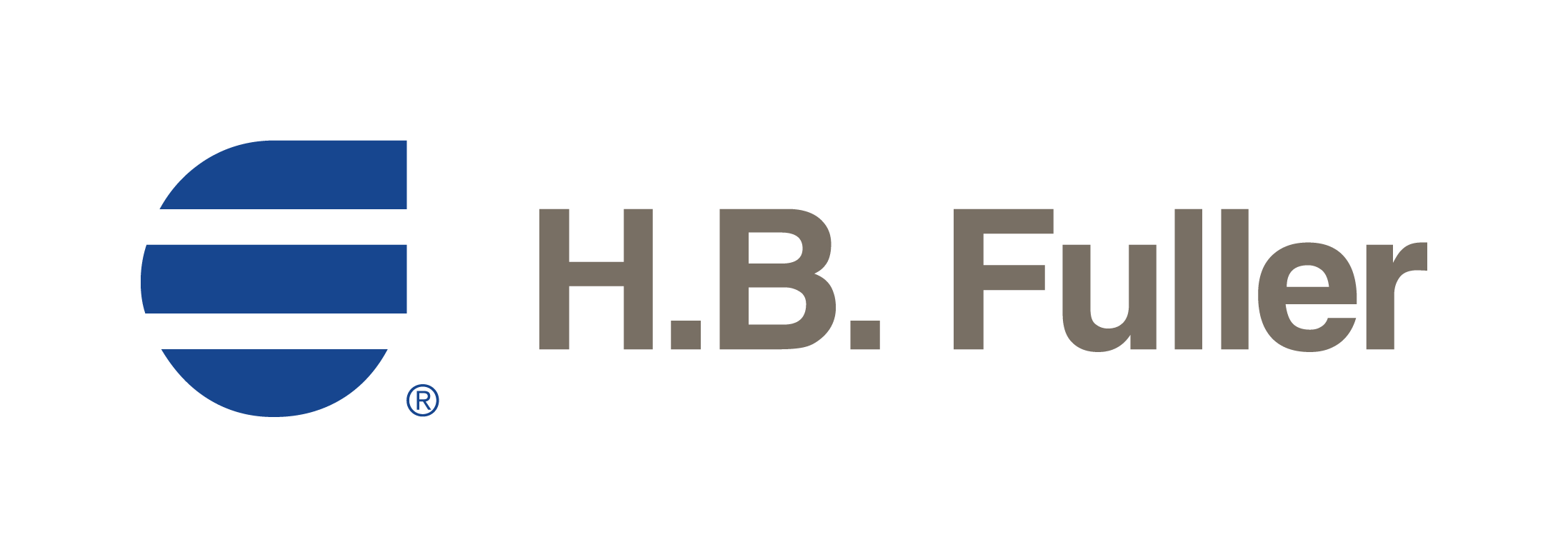
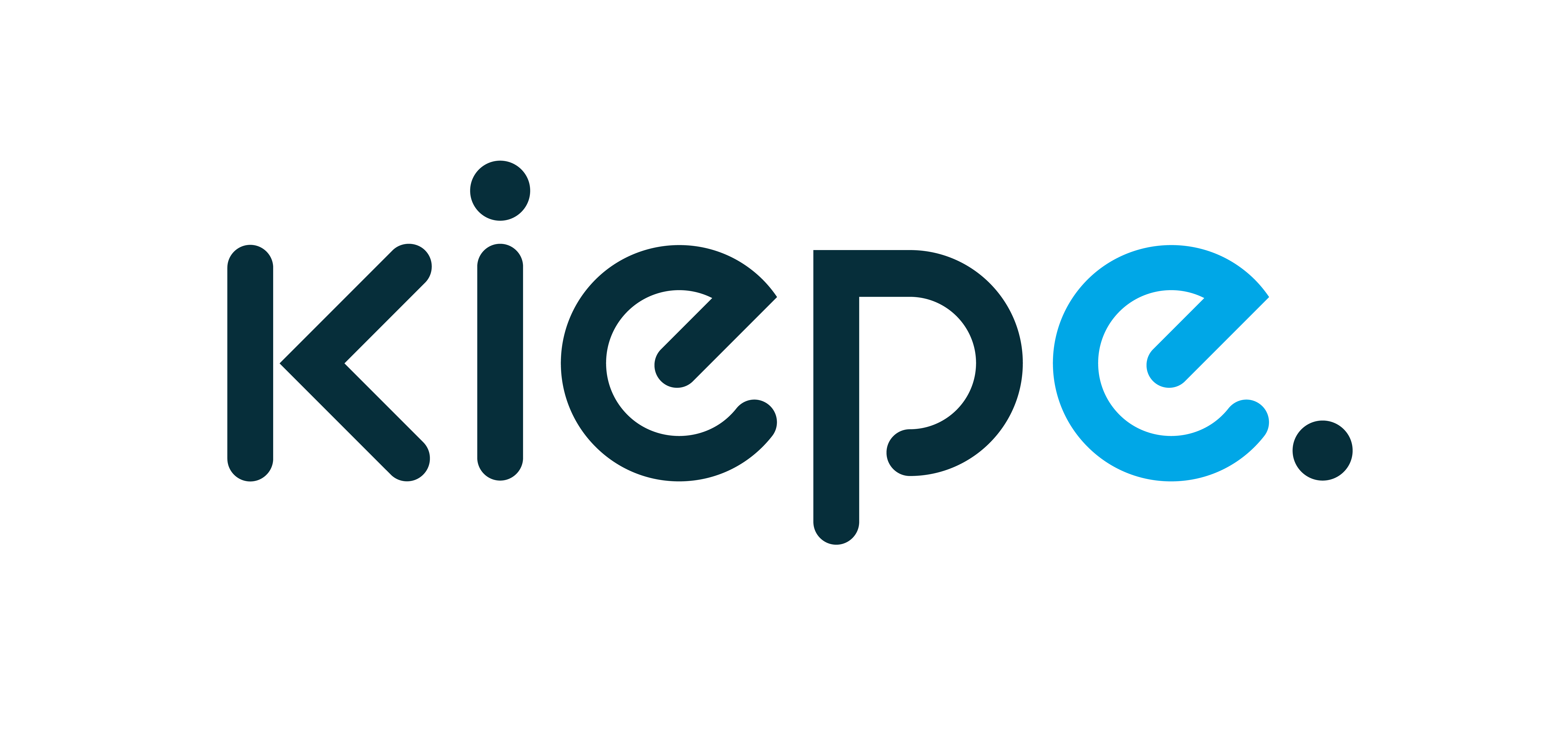
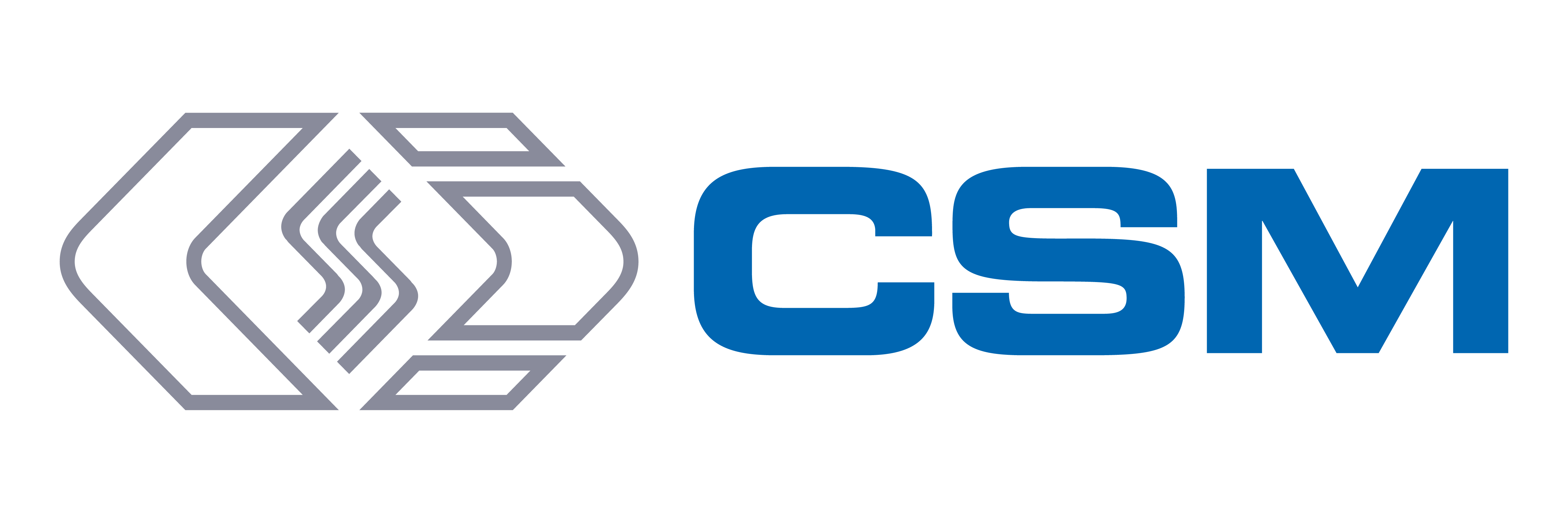