Riversimple Rasa
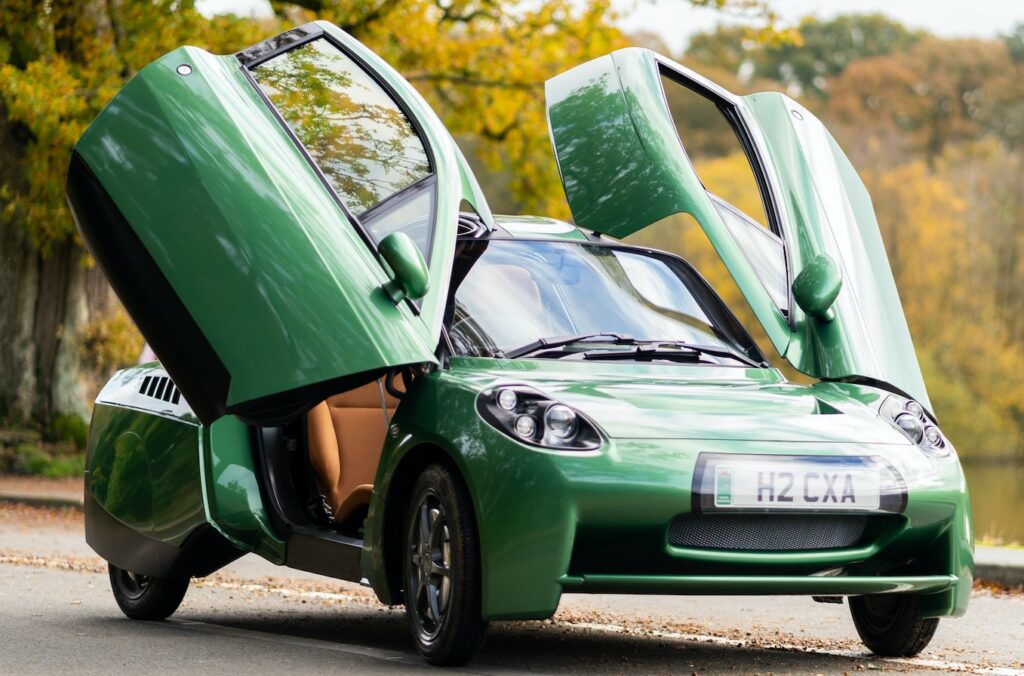
(Courtesy of Riversimple)
Ever increasing circles
Rather than go all-out on the technology, this EV has been conceived with reusable components – and the circular economy – in mind. Rory Jackson reports.
End-to-end sustainability is a troublesome target for EV engineers to track. Reducing vehicle emissions at the point of use is easy enough, but reducing the emissions they cause at the power generation end is harder, and hardest of all is achieving sustainability in the actual supply chains and construction of EVs.
Eliminating the waste, emissions and pollution from mineral extraction, manufacturing and shipping would be a vast undertaking if it was attempted all at once, and would require global systemic changes that are unimaginable to many.
In creating the Rasa car, however, UK-based Riversimple has focused on well-established practices in systems integration, tried-and-tested componentry, localised supply chains and standardised guidelines in design and testing.
The ethos behind this hydrogen powered two-seater roadcar, as well as Riversimple’s overall business model, is the principle of ‘circular economics’, in which mineral and hydrocarbon extraction – and their associated waste and pollution – are minimised in favour of a closed-loop economy based on recycling products at the end of their life to 100% of their original quality.
As Riversimple’s technical director and co-founder Hugo Spowers explains, “The ecosystem works on cyclical principles, but traditional manufacturing – not just in automotive – is a linear process. Mined substances and globalised supply chains are used to construct and sell units of cars and engines, which last for maybe 15 to 20 years before ending up as landfill, without any strategy for closing the loop of material flows.
“Mobility-as-a-service is widely discussed now, and higher per-unit profits can be achieved all the way up the supply chain by focusing on selling a service rather than things. We provide our cars under service contracts, including all costs, especially fuel, or ‘sell their mileage’ over many years and many different users. We then take them back at end of life and remanufacture them, rather than letting them end up on a scrap heap as cars conventionally are.
“It changes the vehicles we make because our profits depend on longevity and low running costs rather than obsolescence and spare parts. Investing in efficiency is profitable if you are paying for the fuel for the life of the car.”
The Rasa therefore forgoes batteries, as much for their recyclability limits as their poor specific energy relative to hydrogen gas (the latter storing around 200 times the kWh/kg of the former). Riversimple’s discussions with suppliers have indicated comparably higher technological capability and profitability of material recycling in the near future, from composites for the structure to the finely divided platinum catalyst used in the fuel cells.
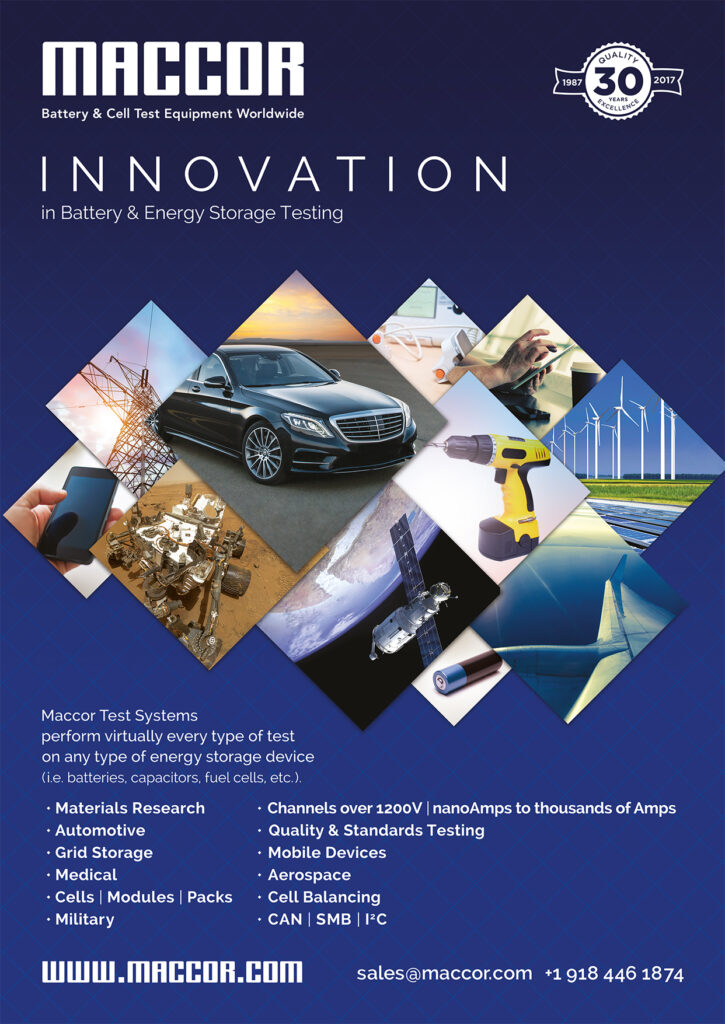
“A 100% recyclable car is a long way off, but by ‘back-casting’ from this goal we can develop a roadmap for how to get there that avoids investing in interim solutions,” Spowers says. “It is all too easy to develop solutions that are ‘less bad’ but that are not on the path to sustainability, and that investment soon has to be written off because being less unsustainable is still not sustainable.
“We can also stay flexible in adopting new materials and components – to ensure that reusability, energy efficiency, safety and cost can all be continuously re-optimised – without designing ourselves into a corner.
Also, while automotive OEMs traditionally build cars in plants with a capacity of over 300,000, and with lead times of 8-10 years for a new plant, Riversimple plans to build far smaller plants, with 2-3 year lead times, that will manufacture 5000 cars per annum.
This approach is intended to greatly lower the company’s investment risk, and enable the flexibility it wants by allowing it to adopt new components, machinery and tooling between plants and mass-customise to meet changing market needs.
The Rasa hydrogen powertrain
With that approach in mind, Riversimple has designed its powertrain not for best-in-class componentry but for holistic system-level goals. These include energy efficiency over the car’s lifetime, cost over mileage and long term sustainability measured through the reusability of parts, with 100% recyclability being the ultimate goal of Spowers and his team.
The Rasa’s hydrogen tank provides the powertrain’s energy storage. The tank’s pressure regulator and an intake fan feed hydrogen and air respectively into a proton exchange membrane (PEM) fuel cell to produce current.
The fuel cell’s power output then connects to a Brandner DC-DC converter to transform the voltage from the fuel cell to the desired values for the car’s main power bus.
“That DC-DC is about 98% efficient,” says Andy David, head of software. “We use a second Brandner DC-DC for the 12 V cabin systems too. They’re extremely well-engineered analogue systems, and operate over inputs of 30-60 V and 0-400 A, and can output up to 120 V, although we don’t need to go that high.”
The traction systems connected beyond the DC-DC converter consist of four pairs of motor-inverters and in-wheel motors, as well as a bank of supercapacitors.
The motors are powered by having the fuel cell produce the constant energy consistent with the cruising speed being demanded at the pedal, while the supercapacitors provide the extra energy needed for acceleration, as well as providing a bank for the energy recouped during deceleration (the DC-DC connects to the supercapacitors, which are in effect the main power bus, the bus voltage floating according to the supercapacitors’ voltage).
“The supercapacitors can store up to 1.9 MJ or 0.5 kWh of usable energy; they’re not the primary energy source, just a secondary source for transient demands such as changes in speed, incline or wind resistance,” David explains.
“At peak braking, the motors deliver around 60 kW to the supercapacitors, which lasts for maybe 5-6 seconds from our top speed.”
Throughout the powertrain and the rest of the Rasa, Riversimple has sought to resolve many of the issues being experienced by large OEMs in hydrogen automotive engineering by keeping weight and hence power consumption as low as possible.
“Our fuel cell has a peak output of 10 kW and a continuous output of 8.5 kW, so we never need more than 13 bhp,” David notes. “Our 650 kg car can go from 0 to 60 mph in just over 9 seconds, and has a 300-mile range before it needs refuelling – and it’s using as much power as three electric kettles throughout all this.”
The engineering philosophy adopted to achieve these is referred to by Riversimple as ‘mass decompounding’, where using a lighter body enables a lighter chassis, which in turn allows for a less powerful and therefore lighter powertrain. That then allows for a lighter body, resulting in a continuous reduction of weight and power requirements across the vehicle.
Lightweight materials
The Rasa’s powertrain is built into a monocoque chassis weighing around 75 kg. The composites of the chassis and body have been optimised for qualities including weight, aerodynamic efficiency and crash safety.
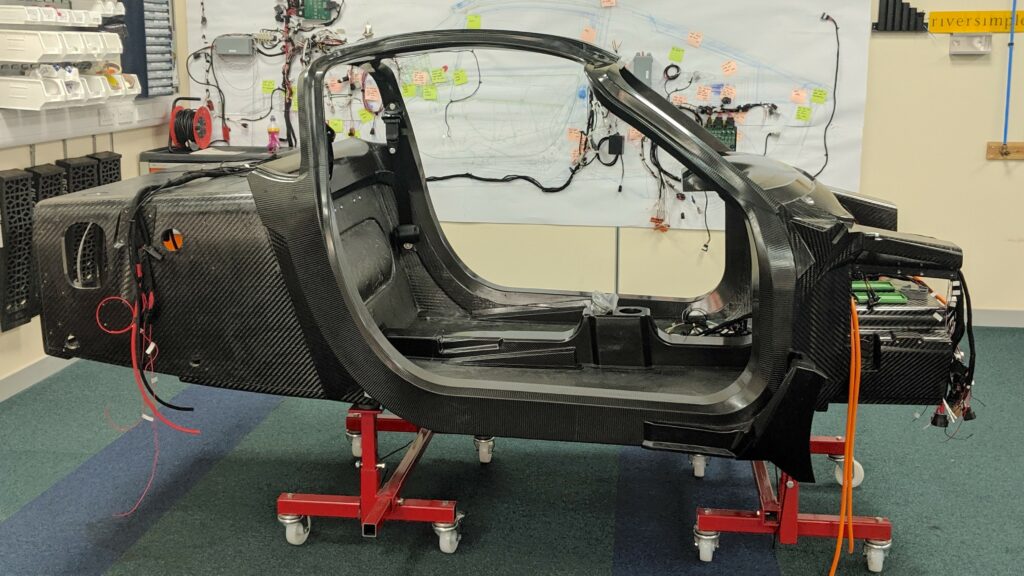
“Careful engineering of composites can increase impact energy absorption while reducing the mass required to protect drivers and passengers,” Spowers says. “With a lower mass of structure, you can use a smaller powertrain, and a lighter car has less kinetic energy to manage in crashes.”
For further safety, the Rasa has a 200 mm layer of impact-absorbing material outboard of the main chassis in case of a side impact. The car’s aerodynamics and pitch stability have been tested in wind tunnels, and currently it has a drag coefficient measuring 0.248.
“We’ve also simulated our crashes in partnership with Vectayn, which specialises in highly accurate composite impact modelling, so we’re confident the Rasa will pass all frontal impact tests without needing frontal airbags, which we’ll use as a last resort if we can’t manage impacts at a structural level,” Spowers adds.
Despite their many advantages, composites are generally not recyclable. The chassis is therefore made from standard non-recyclable carbon composite, currently by hand lay-up but with plans to switch to braiding machines and other automated methods for volume production. Both honeycomb and foam are used as core materials for added strength in the chassis, doors and other outer surfaces.
In the long term, Riversimple anticipates being able to recover composite materials to 100% of their original quality, and it is considering different options for achieving that.
In this respect, Spowers points to a roadmap study it commissioned from EPEA. This Swiss company is focused on closed-loop chemistry research with the aim of achieving 100% reuse of materials – including reinforcement materials made from hydrocarbons – without creating emissions.
“EPEA only agreed to work with us because we’re committed to 100% reusability in the long run,” Spowers notes. “If you only ever aim to recover 80-90% of your materials, there isn’t really a conversation.
“Suppliers will in effect lease their epoxy resins to us, and take responsibility for recovering them chemically after we recover our cars,” he adds.
“That allows them to gradually decouple revenue from virgin resource consumption – a smart move in an oil based business – and it is an essential change in their business model in order to justify the initial investment in the r&d.”
System architecture and control
For simplicity, the Rasa’s powertrain is controlled using just three COTS automotive ECUs, with the r&d focus having been on how to integrate and manage the components rather than advancing the components’ technology.
The three ECUs are 12 V Power PC based MotoHawk units from Woodward, powered by MPC5554 Freescale microprocessors. They have three CAN channels, 2 Mbytes of flash memory, 64 kbytes of RAM, and 32 k of PROM.
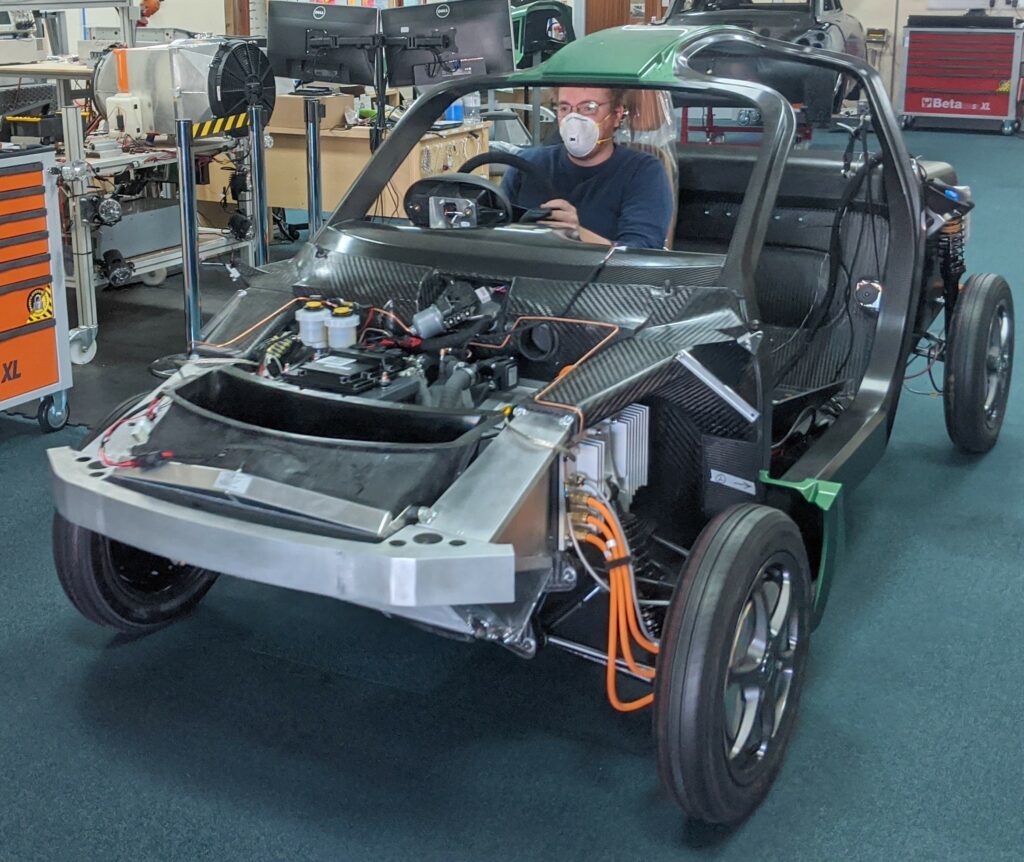
They communicate with each other over a single network, and each connects to two further networks for key subsystems. For instance, a high voltage controller (HVC) connects to the fuel cell as well as a rear I/O box installed for easy digital or analogue integration of other HV systems in the future.
The HVC controls the Rasa’s start-up and shut-down sequences: turning the ‘ignition’ key triggers this ECU to run pre-drive safety checks before switching on the fuel cell and other power components, and starting the delivery of hydrogen and oxygen to the stack. “It instructs the fuel cell on what state we want it in, from power-producing to non-power-producing, sequencing through the necessary transitory states in between,” David explains.
“It also manages the cooling of the fuel cell and our DC-DC converters. To maximise energy efficiency, we generally avoid creating heat in the first place, but excess heat produced by the fuel cell is piped off through a liquid circuit to heat the cabin preferentially, and only piped to the radiator as a last resort. If the DC-DC heats up too much, the HVC can ultimately reduce the current draw.”
Meanwhile, a body controller manages cabin functions including the lights, indicators, wipers and dashboard (including speed and operating data). It also acts as the gateway to Riversimple’s telemetry system, which is kept separate from the other networks as a cybersecurity measure.
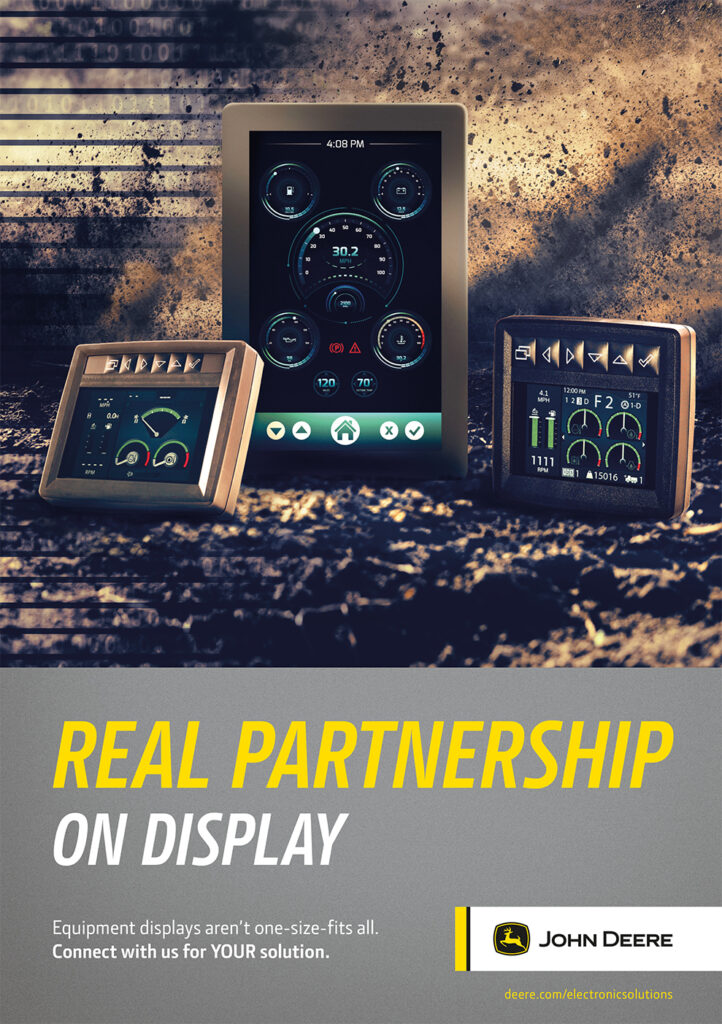
The third ECU is a vehicle system controller, which converts pedal positions into traction or braking commands, and coordinates the speed and quantity of charges and discharges at the supercapacitors.
This includes determining how much charge to reserve in the supercapacitors, based on vehicle speed, elevation and downward or upward slopes in the road, as well as some thermal management for extreme driving conditions.
“Not having a battery removes a great deal of the thermal management concerns typical of EVs, and supercapacitors have nowhere near the same heat issues or thermal runaway risks that can arise from insufficient cooling,” David notes. “There are also far fewer things to control in the Rasa compared with an IC-engined car, and our control loop works on the order of milliseconds, not microseconds, so fundamentally our software has fewer problems to solve.”
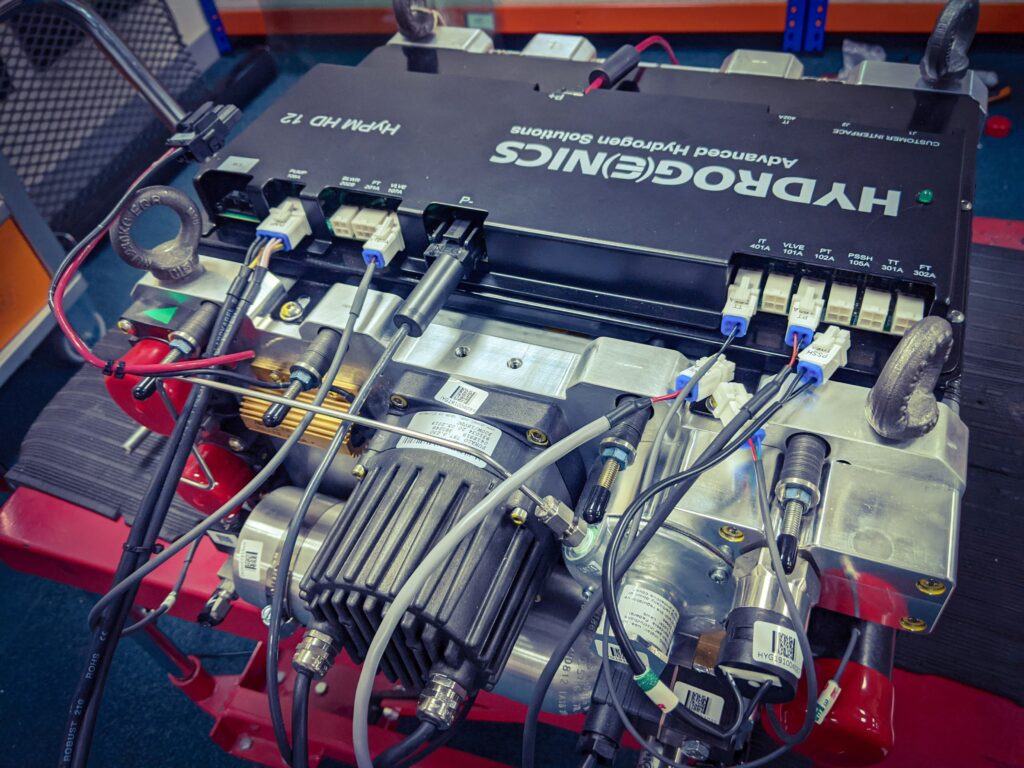
Integration before innovation
The Rasa’s suite of sensors has been selected and configured to maximise the safety of its passengers. It includes two sensors for acceleration pedal deflection, two for brake pedal pressure (front and rear), and one for any hydrogen leaks.
“We’ve integrated COTS products as much as we can, rather than trying to innovate our own solutions, which allows us to demonstrate how much of what we’re doing is already proven commercial technology.” David explains.
“Much of what we’ve done is come up with ways to combine various COTS items so that the result is useful,” he adds. “For example, the fuel cell already tells us via CAN its operating temperature, coolant temperature, output voltage, output current, and other bits, so we don’t need thermistors or any other sensors there. Likewise, the inverters monitor current draw, regenerated current, operating voltages, temperatures in the motors and in themselves, and a few other parameters.”
Specifications
Rasa hydrogen-electric two-seater roadcar
PEM fuel cell
Four in-wheel motors
Weight: 650 kg
Top speed: 60 mph (96.56 kph)
Acceleration: 0-60 mph in 9.7 seconds
Maximum continuous power: 10 kW
Operating energy consumption: 250 MPGe (equal to 1.13 litres/100 km)
Range: 300 miles (483 km)
Safety considerations
The company is aligning its development processes with ISO 26262, conforming to its guidelines on how to test and measure risk – that is, the unintended consequences stemming from any component’s failure to operate as intended.
Also, exhaustive tests were run on the motors, supercapacitors and other components to build up data on pre-failure conditions to ensure that mitigating behaviour functions such as thermal and power management were programmed across the Rasa’s ECUs.
Hydrogen management
A standard Type 3 hydrogen tank (made from carbon fibre with an aluminium liner) is currently used in the Rasa for storing the gas at 350 bar.
To ensure stable delivery of hydrogen, Riversimple is working with UK company PresReg on a customised pressure regulator, as the latter focuses much of its r&d on making lightweight, compact pressure regulators (relative to most currently available COTS systems).
The PresReg unit is a 650 g slimline cylinder measuring 135 mm long, preset by the supplier to the Rasa’s outlet pressure requirement, and Spowersnotes that it exhibits higher stability of outlet pressure than the other regulators they have tested. Also, its shape lends itself eventually to being integrated inside the hydrogen tank, which will make for neater and safer packaging.
While there is growing talk throughout the industry of 700 bar being a superior storage pressure for automotive hydrogen, in terms of the improved energy storage and hence range it grants, Riversimple plans to stay at 350 bar for the foreseeable future, for several reasons.
“There’s an enormous range of certified componentry available for working at 350 bar, and trains, buses and so on are operating on 350 bar tanks,” Spowers notes. “Some car models will need 700 bar to meet their range targets, but with us having focused on first reducing the hydrogen consumption, we don’t particularly need more hydrogen in a smaller volume.”
Energy is also required for pre-cooling hydrogen in 700 bar tanks, which is not necessary with 350 bar ones. As Spowers explains, “Hydrogen heats as its pressure drops, so the greater the quantity of hydrogen, the greater the pressure change and the greater the mass flow rate, so more heat is generated.
“So, if you have a 5 kg tank at 700 bar, refilling at 1 kg/minute requires pre-cooling to around -40 C. Our 1.5 kg, 350 bar tank can be refilled at a third of the speed for a still shorter duration, and unless you’re in a very hot climate, there’s no need for pre-cooling.
“Pre-cooling is very energy-intensive, but it’s not included in the energy consumption figures of cars that require it, despite being a big sunk cost.
“But of course, we’d certainly be able to switch to 700 bar if it becomes the only standard and if the availability of certified parts improved to match those working at 350 bar.”
Riversimple is also currently in talks to develop a Type 5 (all-composite and linerless) tank in the UK. The company is working to bring its supply chain back into the UK and develop circular contracts with suppliers, paying for the use of components rather than buying them outright.
The fuel cell
“Choosing a fuel cell has implications for the voltage you choose for the main bus, along with other similar considerations for the electrical architecture,” Spowers notes.
“Power density isn’t critical for us as we don’t need as much power as a conventional fuel cell EV architecture, and that’s important because power density relates linearly to cost. If you want to halve the volume of your fuel cell while keeping the power the same, the resulting fuel cell will probably cost around twice as much.”
Spowers adds that there are three technical challenges to automotive adoption of hydrogen technology, assuming OEMs continue trying to minimise investment costs by making hydrogen powertrains with their existing equipment: fuel cell power density, cost and hydrogen storage density.
“That creates a three-way tug-of-war,” he says. “For instance, you improve power density by increasing the pressure – as with combustion engines – and hence the reaction rate inside the fuel cell stack. That means you increase the fatigue stresses on the proton exchange membranes, along with the difficulty of maintaining a consistent distribution of gases and humidity throughout the stack.
“Not only must your material costs go up to maintain structural integrity, you also need a compressor to maintain oxygen pressure, running off electricity from the stack, so you also lose efficiency, exacerbating the hydrogen storage challenge.
“Alternatively, if you try to increase power by running the fuel cell at a higher current density, your cell voltage drops. 0.6 V per cell is where most fuel cells operate; any lower and you dramatically lose efficiency.
“But if you run your cells at 0.7 V for about half the power, you gain almost 17% efficiency. Although the stack is more expensive, we can profit from this approach, maintaining the price for the customer through high efficiency and low hydrogen consumption.”
With these parameters in mind, Riversimple currently uses a 12 kW fuel cell from Hydrogenics. In the Rasa’s powertrain, it is always run at less than full power to enable the car’s top continuous speed of 60 mph at higher power efficiency than at continuous peak.
“It’s designed with very careful design trade-offs between efficiency, temperature, humidity and other factors,” Spowers says, adding that Riversimple’s design philosophy and the speed with which new fuel cells are being unveiled mean they are constantly evaluating fuel cell options, for goals such as energy efficiency, weight reduction, lifespan and recyclability.
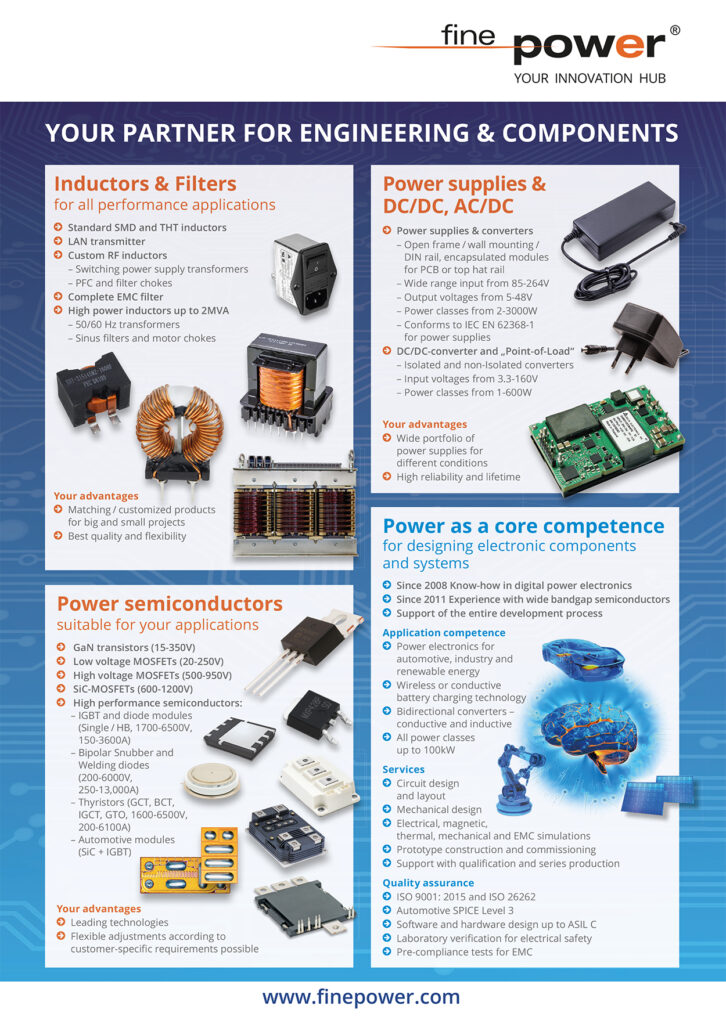
In-wheel motor drive
Four radial-flux permanent magnet in-wheel motors provide the Rasa’s traction, with control performed via four vehicle-side Sevcon inverters.
Distributing power this way reduces both the fuel cell size and thermal losses compared with an e-axle concentrated on one or two motors, preventing the need for liquid cooling.
Riversimple performed the mechanical design of the motor in-house, with the electromagnetic modelling and optimisation by Motor Design and input from Inetic on manufacturing considerations and designing the windings and busbars.
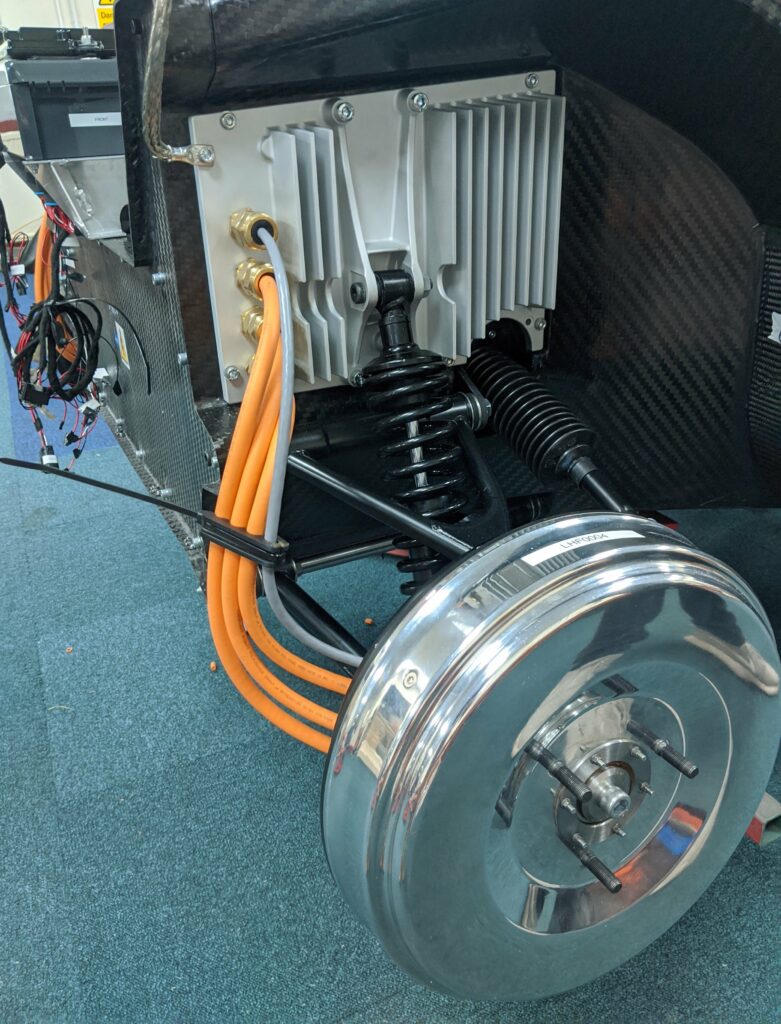
Each motor is air-cooled, and is capable of 15 kW peak power, with 27 stamp-laminated poles and 24 single-piece magnets. Inetic has manufactured the motors and is a close partner in the project, committed to working with Riversimple towards volume production.
“We’ve designed the motor, brakes and suspension pick-ups in one integrated structure,” Spowers explains. “Our older motor in our first prototype was bolted onto the wheel via its outer diameter, which meant it couldn’t be balanced in a tyre balancer – it just wasn’t practical for a roadcar, so we’ve also designed our own wheel.
“It’s a six-spoke wheel, very lightweight, with a 3.5 in [8.9 cm] rim. Within this profile are the spokes, the entire electric motor, the brakes, the upright and the suspension pick-ups. That enables a kingpin angle of 7º with a scrub radius of 1 cm – exactly what we wanted.”
The Rasa’s wheels also integrate 12 in-diameter drum brakes designed in-house, with the suspension pick-ups fitting into the space between the shoes. The drum is shaped as an annular ring that bolts onto the motor’s outer diameter, with 20 mm shoes.
“It’s an unusually narrow and large diameter drum, more than capable of stopping such a light car, but it’s primarily for use in emergency stopping or braking below 10 mph, as most of the braking is electrical,” Spowers adds.
“Our motors also have bespoke encoders, from Zettlex. We’ve used other position sensors, including inductive resolvers and less expensive solutions than Zettlex’s, but never had such a clean signal until we used theirs. There are a lot of electrical flows in the motor, so noise is a real issue that can hamper measurement precision.”
The supercapacitors
Acceleration and deceleration involve high energy flows of up to 60 kW, which made supercapacitors a clear choice for the Rasa’s load-levelling system: 55% of the kinetic energy is captured at its maximum electrical braking of 0.3 g in test cells.
“We couldn’t absorb 60 kW with a battery, not without increasing the weight of the car by 50%,” Spowers says. “Our supercaps weigh around 45 kg collectively, and we never get anywhere close to the peak current they can handle.”
He adds that their round-trip efficiency (the ratio of energy required to charge a battery to the energy available during discharge) is also far better than with batteries, especially at high currents, and while energy density is the limiting factor for supercapacitors in this case, the solution chosen for the current Rasa meets all of Riversimple’s requirements.
Spowers notes that the reduced energy storage requirement is another instance of mass decompounding. Furthermore, there will always be a percentage of the kinetic energy that can never be recovered, but the lighter the car the smaller that absolute figure is with every deceleration, yielding compounding efficiency gains.
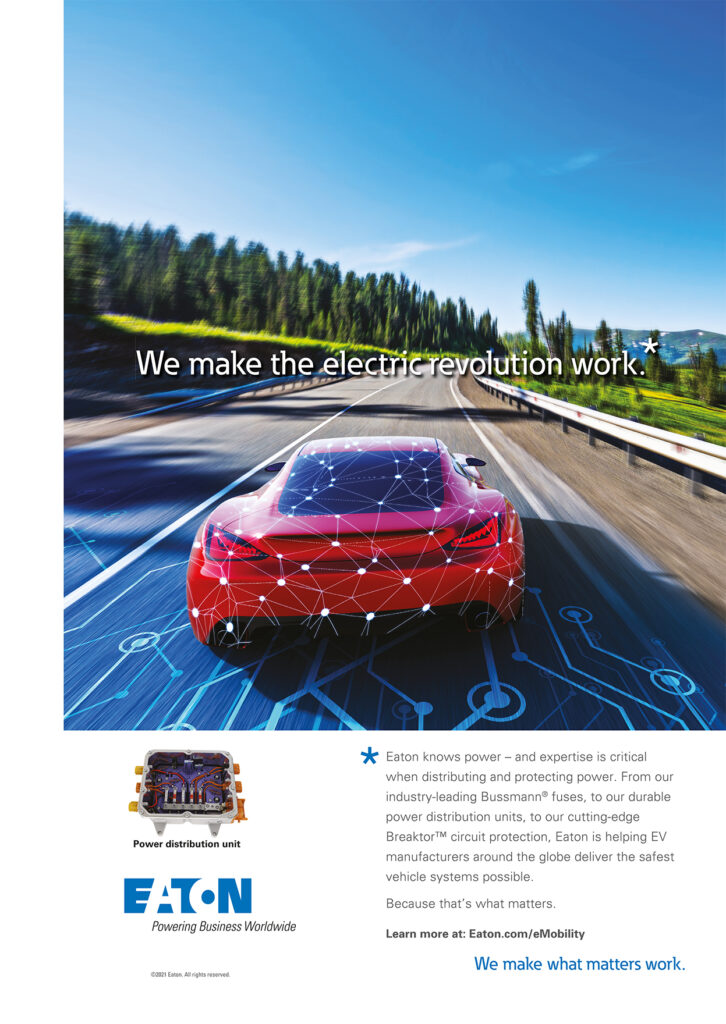
“The hybrid supercaps we’ve received from JSR Micro have a bit of lithium enrichment, and have more than three times the energy density of the conventional supercaps we’ve used previously,” Spowers explains. “But it’s such a fast-moving field – we’ll be trialling some very promising supercaps from Allotrope later this year, which could again treble the energy density in the car.”
While the supercapacitors are used only for transient energy demands, increasing their energy density is key to ensuring the Rasa can operate on mountainous roads, where downhill and climbing routes will require increases in storage and load-levelling of potential energy.
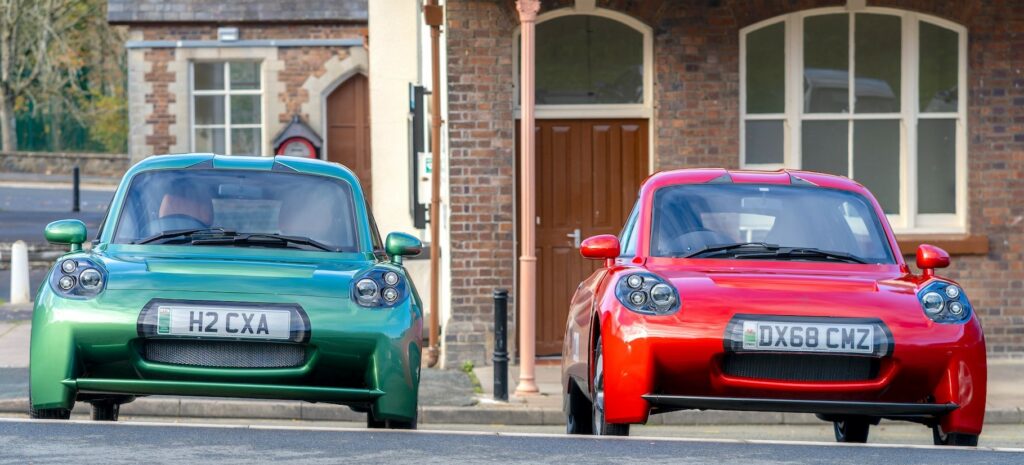
Future plans
With its engineering and low-volume production plans becoming more definite, Riversimple is continuing to form industry partnerships and discussions around building a circular e-mobility economy.
In addition to its existing network of suppliers, consultants and cross industry contacts, the company has recently secured funding from the European Regional Development Fund to launch a circular economy innovation centre in Wales, named Circular Revolution, in partnership with Swansea University and the University of Exeter.
The centre will be aimed at reaching out to organisations seeking to engage with more sustainable products, services and business models – first in Wales and then further afield – as well as researching how to implement circular models, particularly in supply chains.
Some key suppliers
PEM fuel cell: Hydrogenics
Hydrogen fuel tank: COTS
In-wheel motors: Inetic
Motor design consultation: Motor Design
Supercapacitors: JSR Micro
Motor position encoders: Zettlex
Inverters: Sevcon
DC-DC converters: Brandner
I/O units: Wurth Elektronik
ECUs: Woodward
Dashboard: Continental
ONLINE PARTNERS
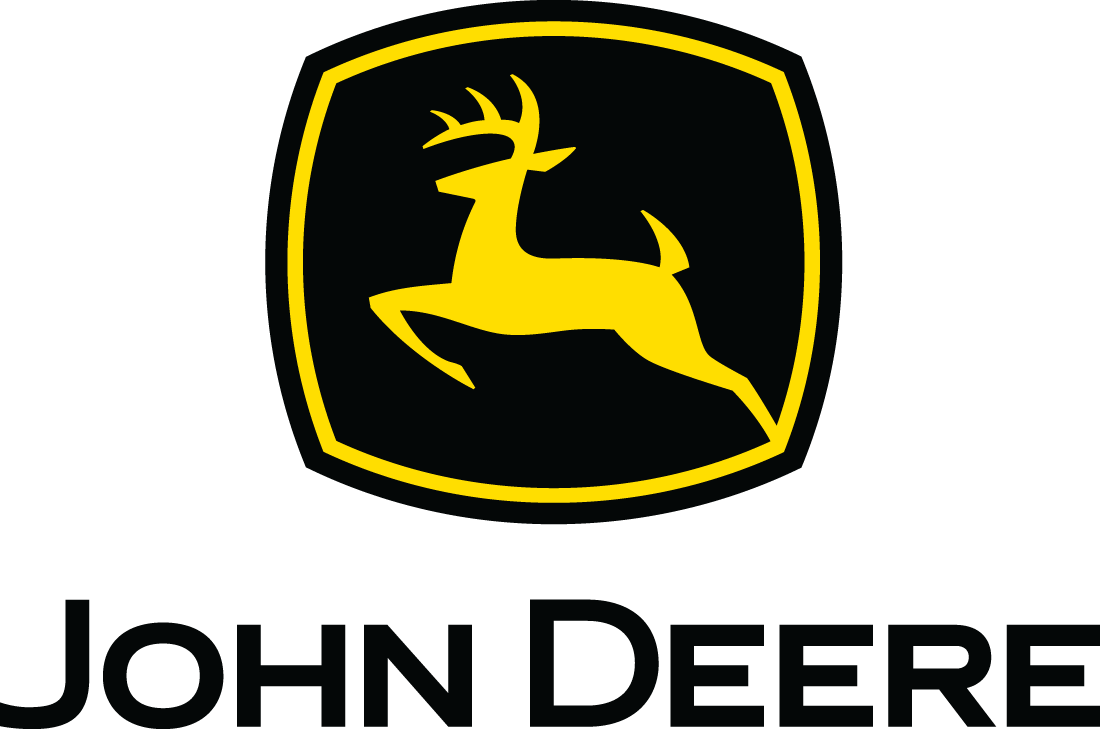
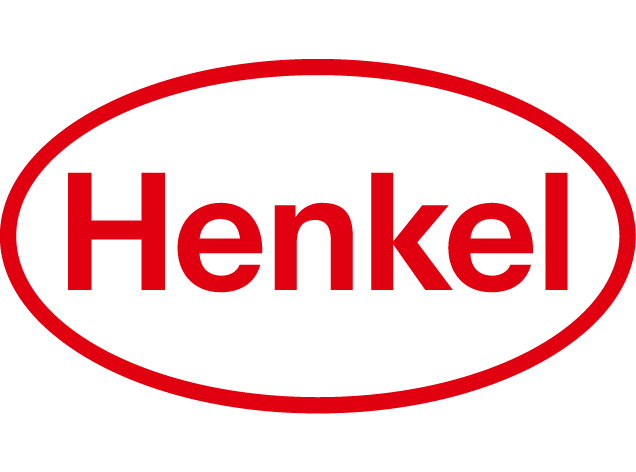
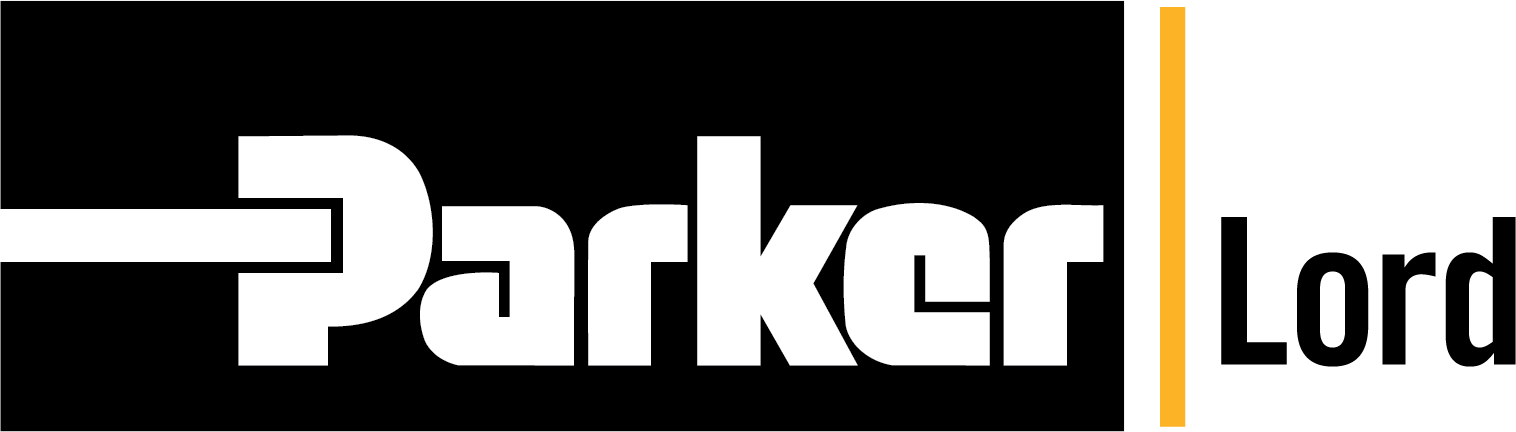
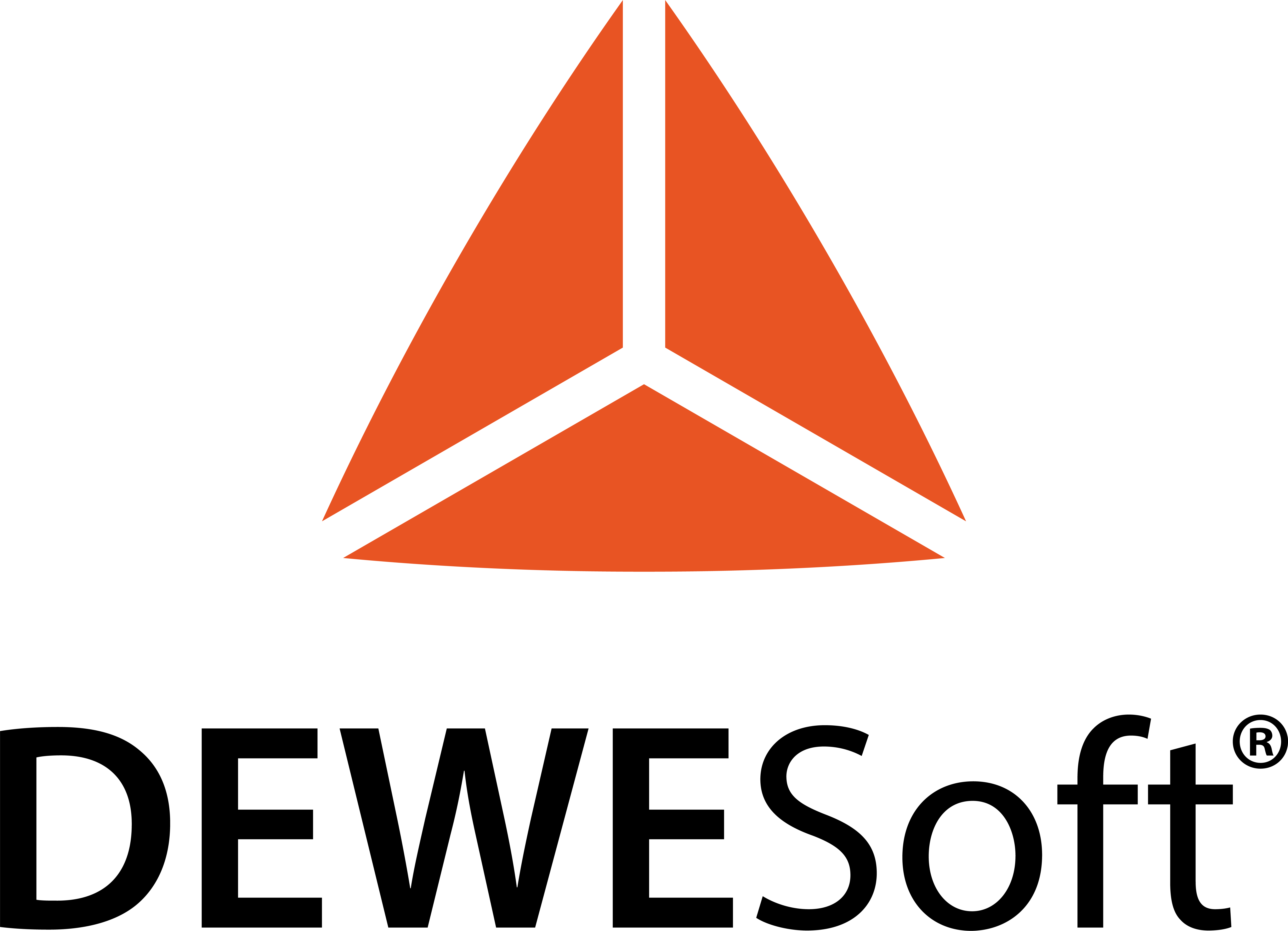
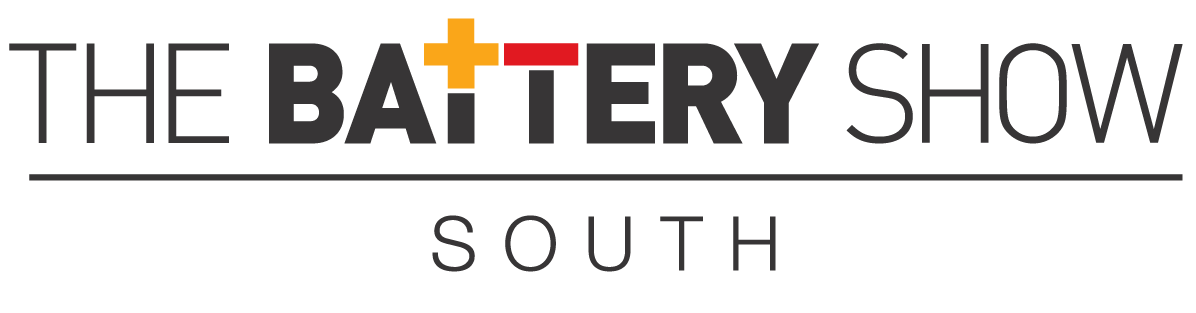
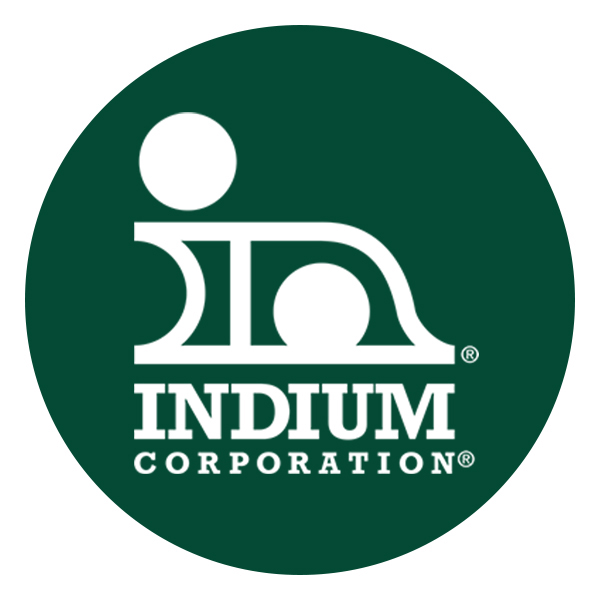
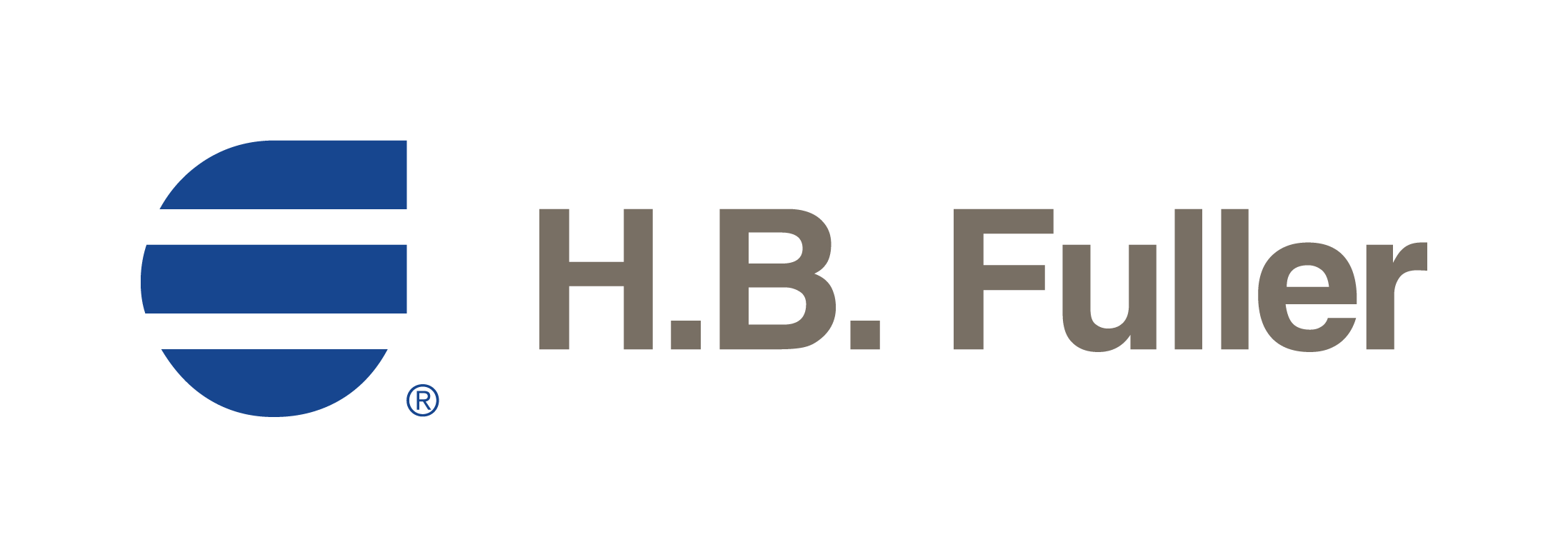