Building lighter components with 3D printing
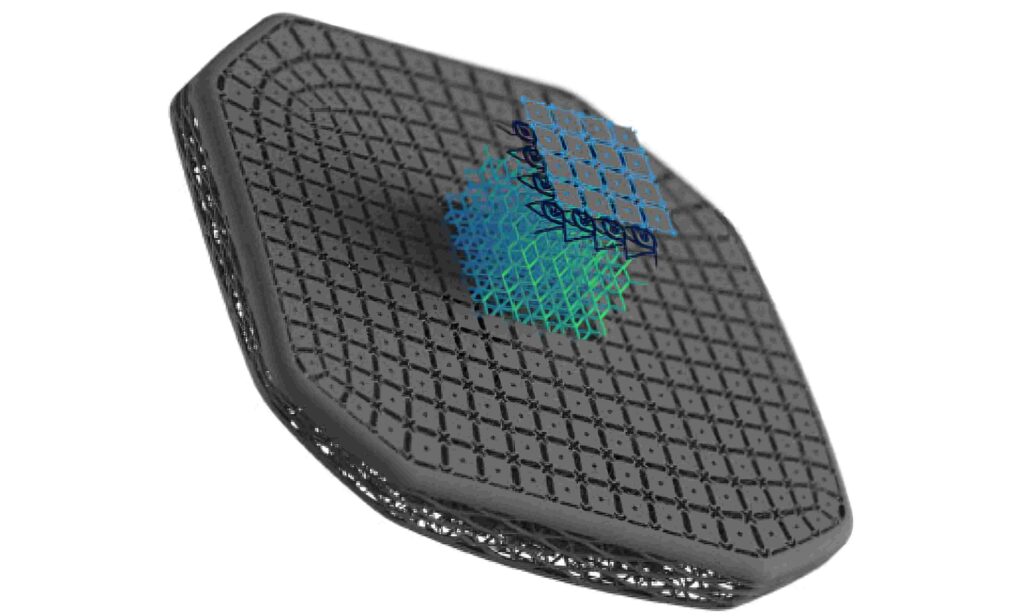
(Image courtesy of CEA)
Researchers in France are developing a new way to use additive manufacturing (AM) for EVs, writes Nick Flaherty.
Renault Group is working with French research group CEA-Liten on a complex mesh structure that can be produced in a single, 3D-printing AM stage to produce components with adaptive mechanical behaviour.
CEA-Liten has filed 10 patents on the technology, which can be used to reduce the weight of the materials in an EV.
Each of the Thermoplastic Polyurethane (TPU) strands making up the mesh of the lattice structure can be parameterised three-dimensionally to form multi-layer networks of cells in which each layer has a unique function and characteristics. The resulting monolithic and monomaterial parts are simpler to produce in a single 3D-printing operation, without any assembly, eliminating scrap.
The technique can be used for seats, using a single material to achieve levels of comfort, cushioning and support that cannot be achieved with the usual fabrics, foams and reinforcements. It is also 30% lighter. A seat can even be modelled to the shape of the driver.
Renault has used AM to make tooling, as well as prototype parts. The structure developed by Renault and the CEA opens the way to new applications, including areas the vehicle occupants come into contact with, such as front seats.
“The almost total freedom of design, savings in materials and weight, integration of functions and reduction in manufacturing times mean that AM is a sector strongly supported by the CEA,” said CEA-Liten CEO François Legalland.
ONLINE PARTNERS
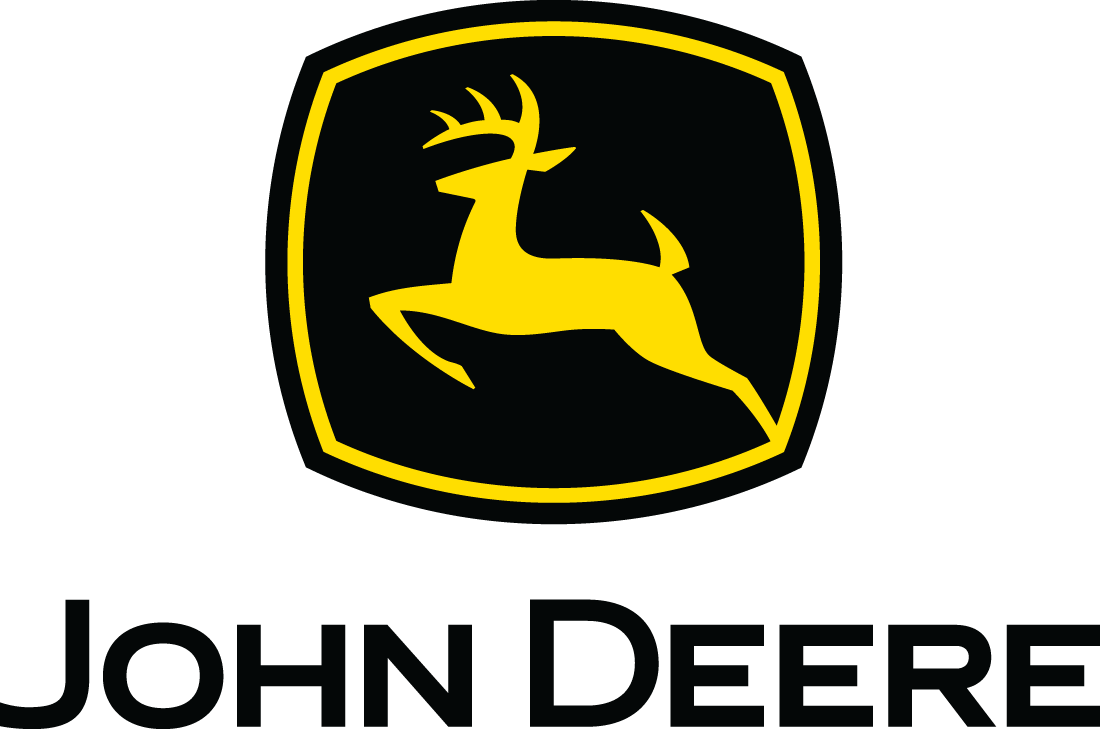
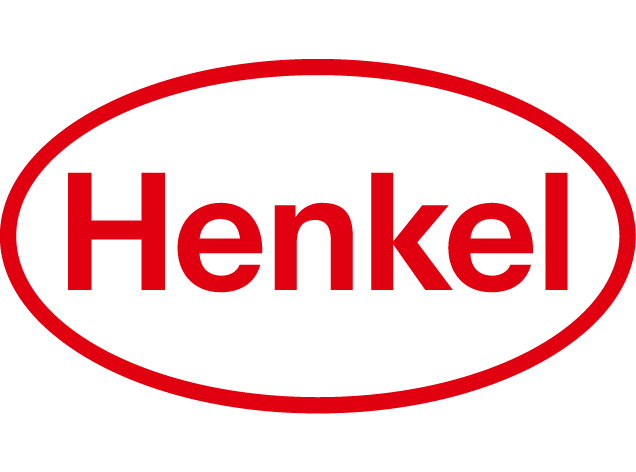
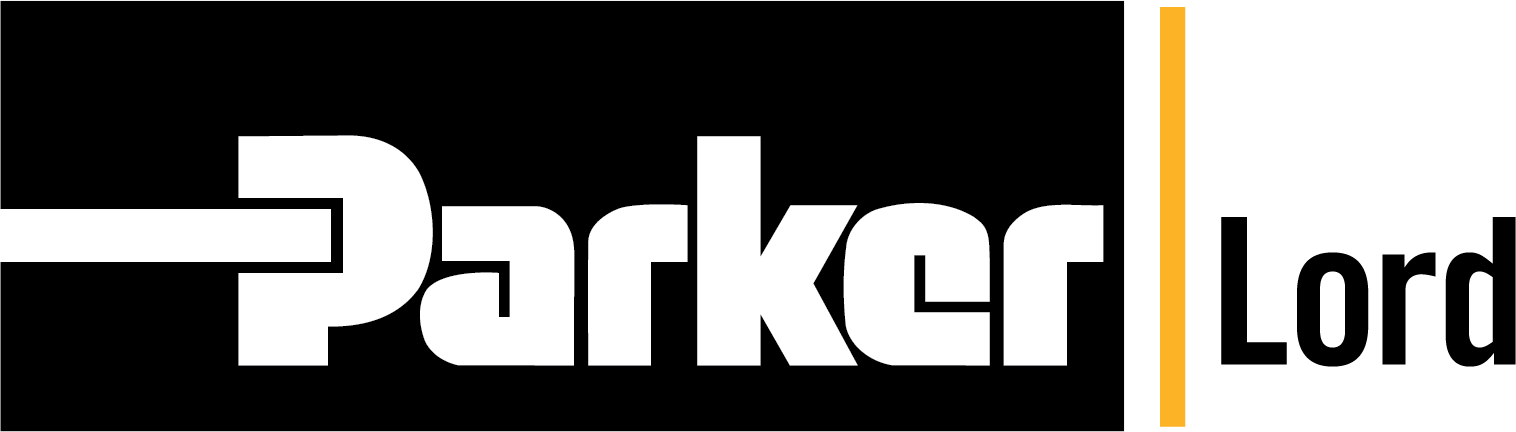
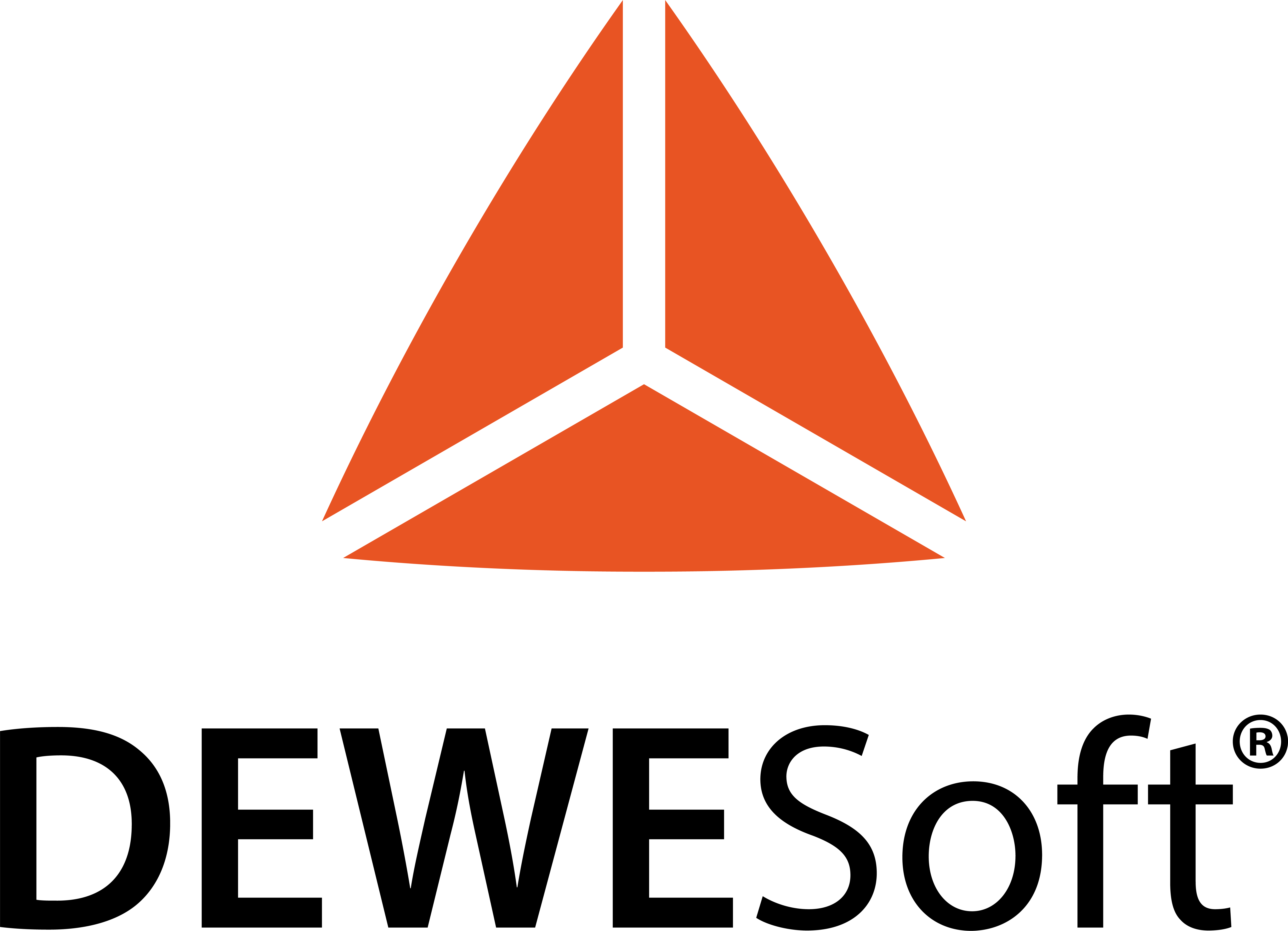
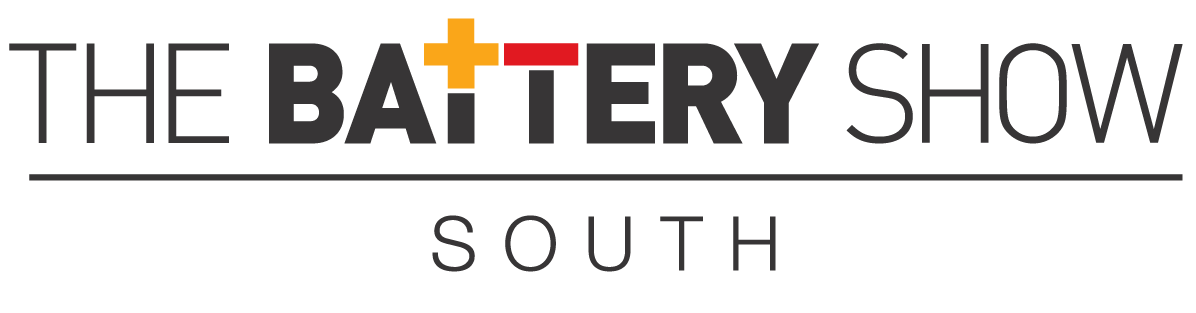
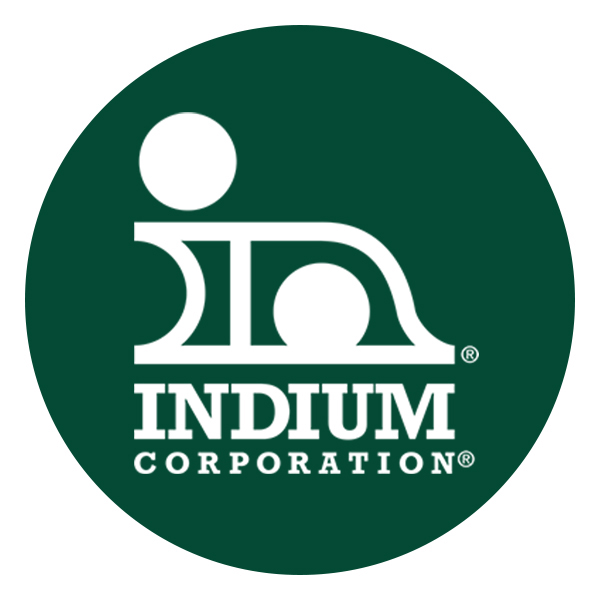

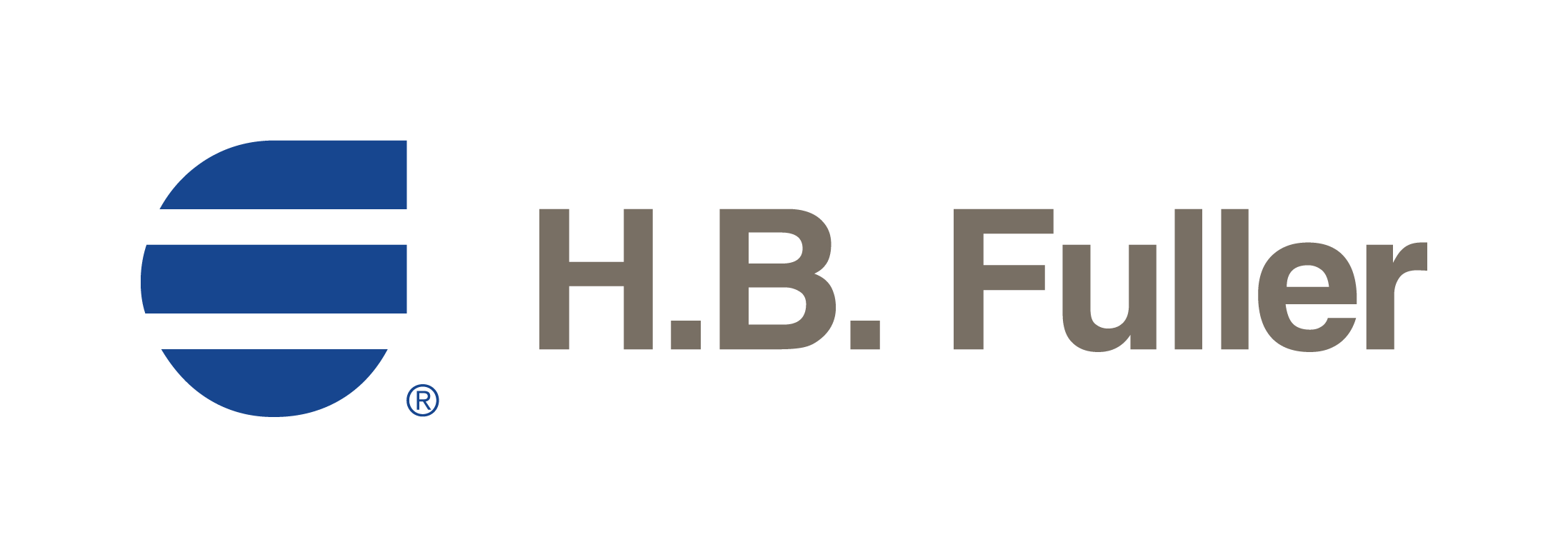
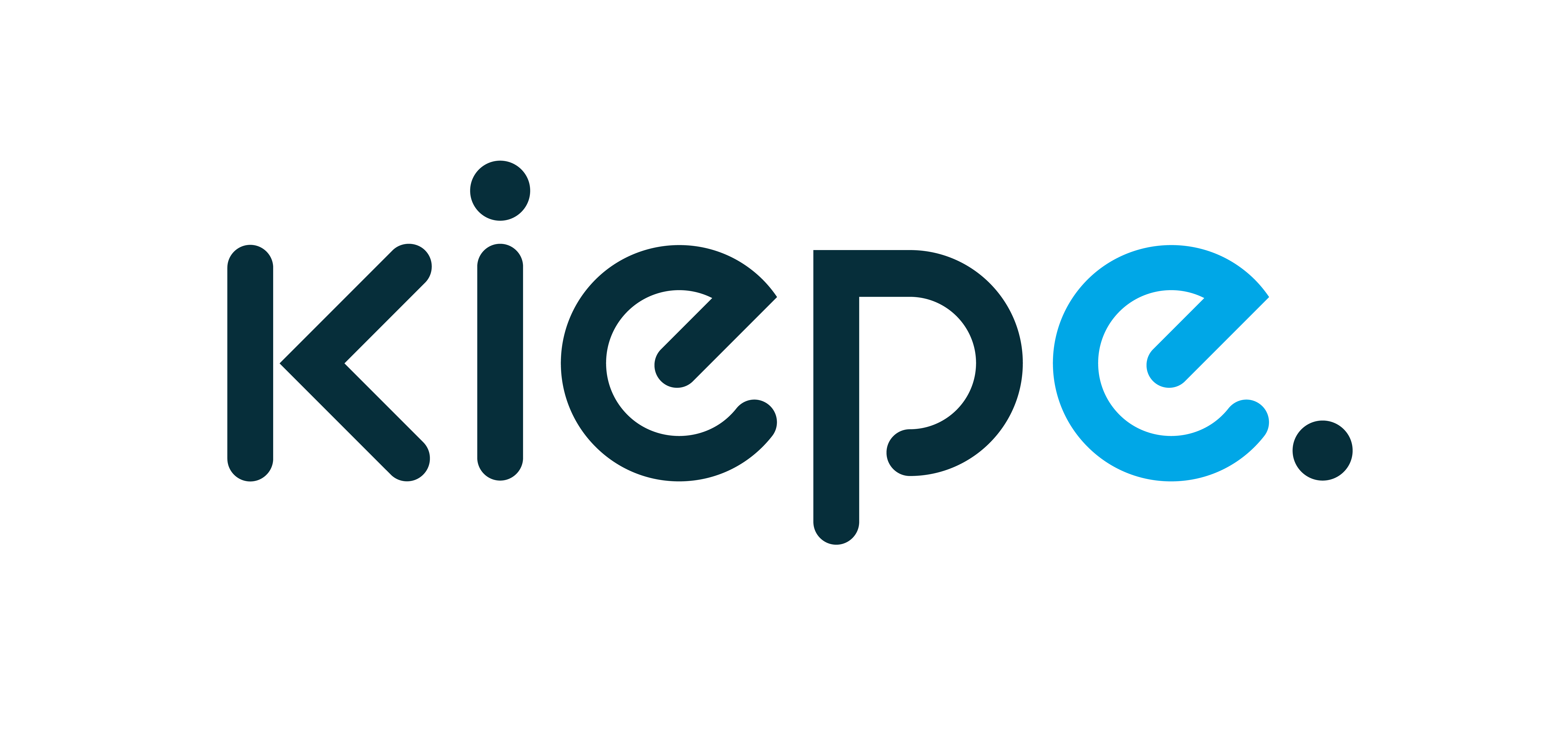
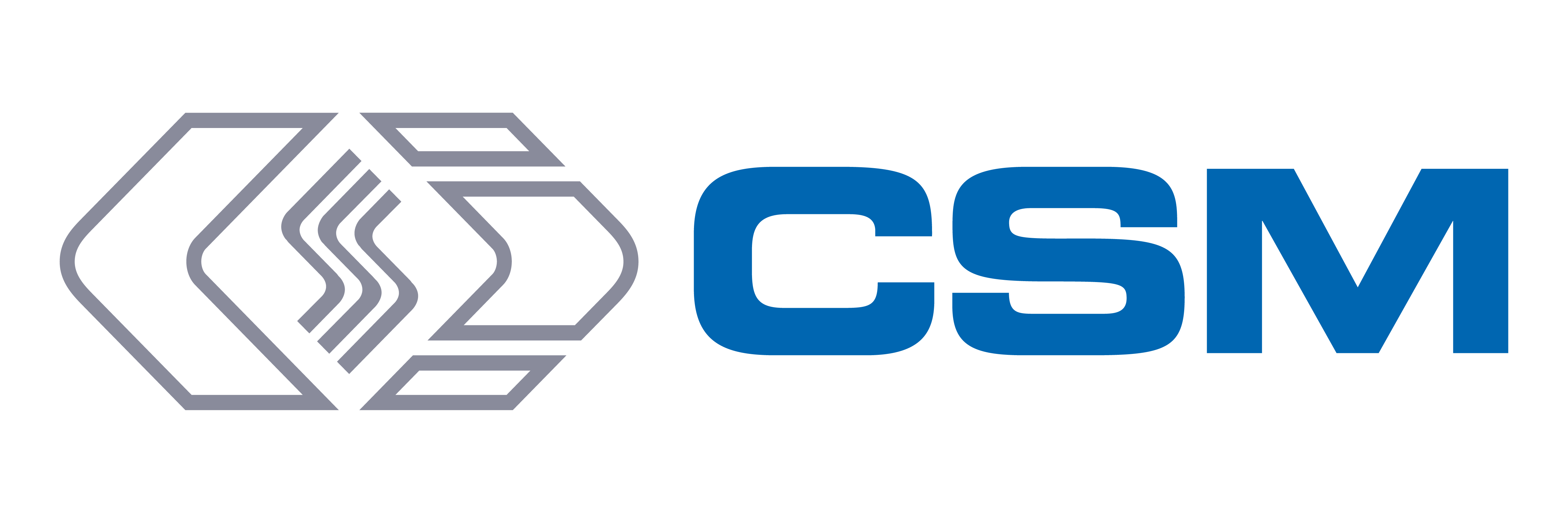