Robot makes light work of wiring harnesses
The first version of Q5D’s robot for automating the assembly of wiring harnesses for electric vehicles (EVs) is being shipped, writes Nick Flaherty.
Q5D is using its CY1000 system to assemble the wiring harness in the roof lining of a prototype SUV being tested in the UK.
“We have proven we can do it more cheaply, and we are doing a small production run for them with all the terminations proof of concept. Then we go to a contract manufacturer and provide the machine to them,” says Steve Bennington, CEO of Q5D.
“Now they are looking at other parts of the vehicles, such as doors, bumpers and seats. No two wiring looms are exactly the same and this causes problems in every aspect of the car. This is an opportunity to have wiring looms that are identical, and can be easily changed and introduced.”
The company is negotiating pilot lines for automotive manufacturers. The pilot machines have shown a 30-50% reduction in the cost of the wiring for a vehicle. For a large EV, this can be a saving of hundreds of dollars per car.
This comes from reducing the labour expense by 80-90% and cutting shipping costs. It costs more to ship a wiring harness from Egypt, where it is made, to Spain, where it is installed in the vehicle, than it does to make it, says Bennington. With the Q5D robot, the assembly can be co-located with the installation line.
There is another less obvious saving on inventory for the assembly of aftermarket spare parts. “With our system, you can make to order with lean manufacturing. This can change the design process; for example, designing for fewer connectors and different designs for battery packs,” he says.
“With our machines integrating wiring into the component parts and assemblies, the final product can be assembled by machine as well.”
One area of development is the battery management system, where Q5D has used its robot to wire up a case, so the battery cells become functional once they are installed in it by a conventional, industrial robot. The whole case can then be installed in the vehicle robotically and become functional.
Q5D developed a bill-of-materials and takt time calculations for product assembly, showing this approach can make the battery management system for a total cost equivalent to that of the cheapest imported solution without compromising on quality. Manufacturers can gain cost savings and productivity gains because assembly onto the chassis can be automated.
The system uses a custom control system, based on a field-programmable gate array (FPGA) and a Raspberry Pi single-board computer.
“First, we looked at off-the-shelf, single-board computers designed for industrial applications,” says Chris Elsworthy, chief technology officer at Q5D. “Many were very mature, but we wanted to connect things that were outside their ecosystem. We found we would only use 10% of the functionality of these computers and that 10% wasn’t a perfect fit for what we wanted.
“This led us to design our board in its entirety. We are using an FPGA for fast processing, and originally put a microcontroller next to it, but it turned out to be difficult from an architecture perspective. In the end, we broke the electronics into two parts.
“We have a high-speed FPGA board, which is entirely our design and construction, and we added a Raspberry Pi to do all the upfront processing. The Raspberry Pi does some maths, chucks the work together and inserts that into the FPGA. The FPGA then does all the real-time maths,” he said.
Click here to read the latest issue of E-Mobility Engineering.
ONLINE PARTNERS
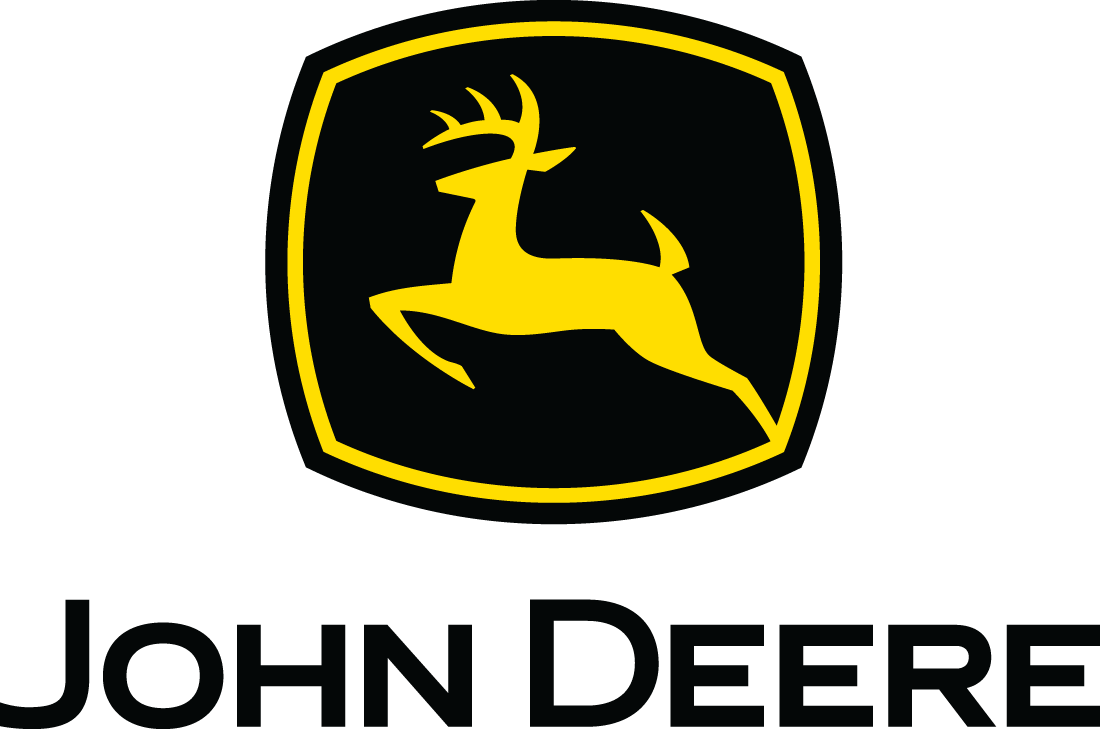
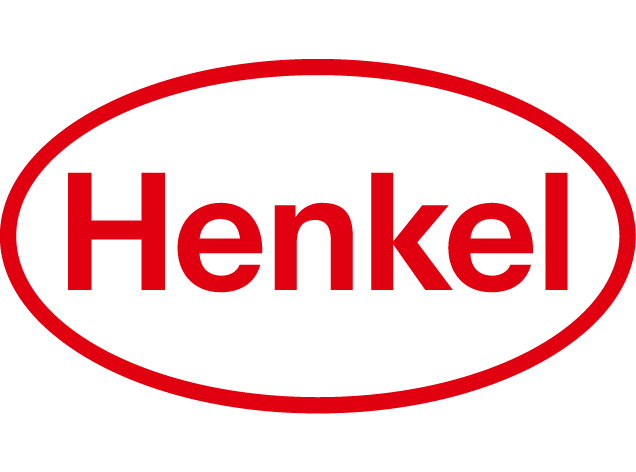
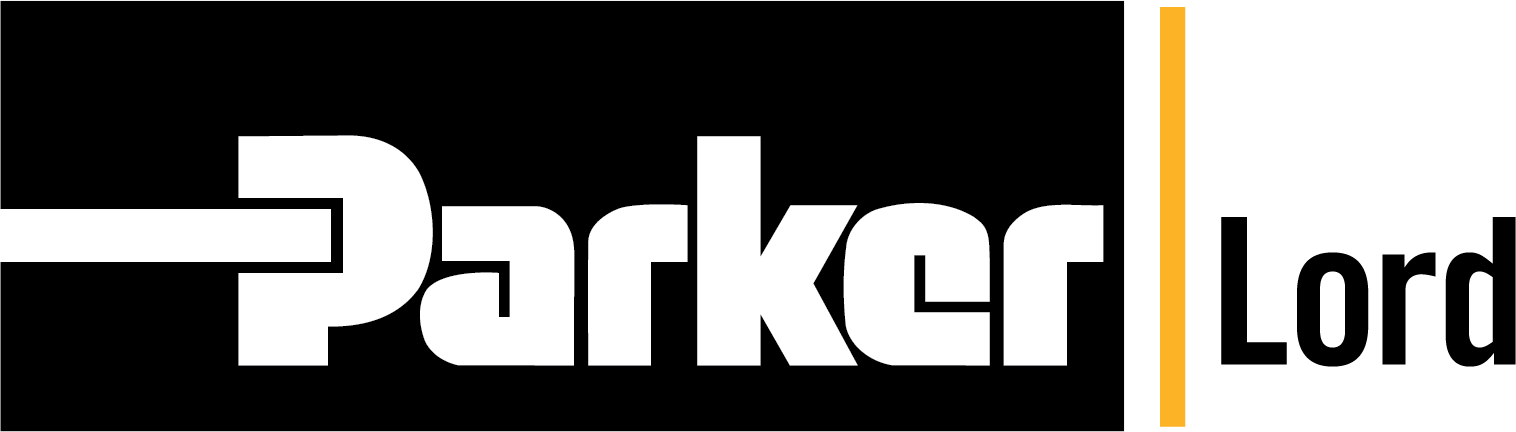
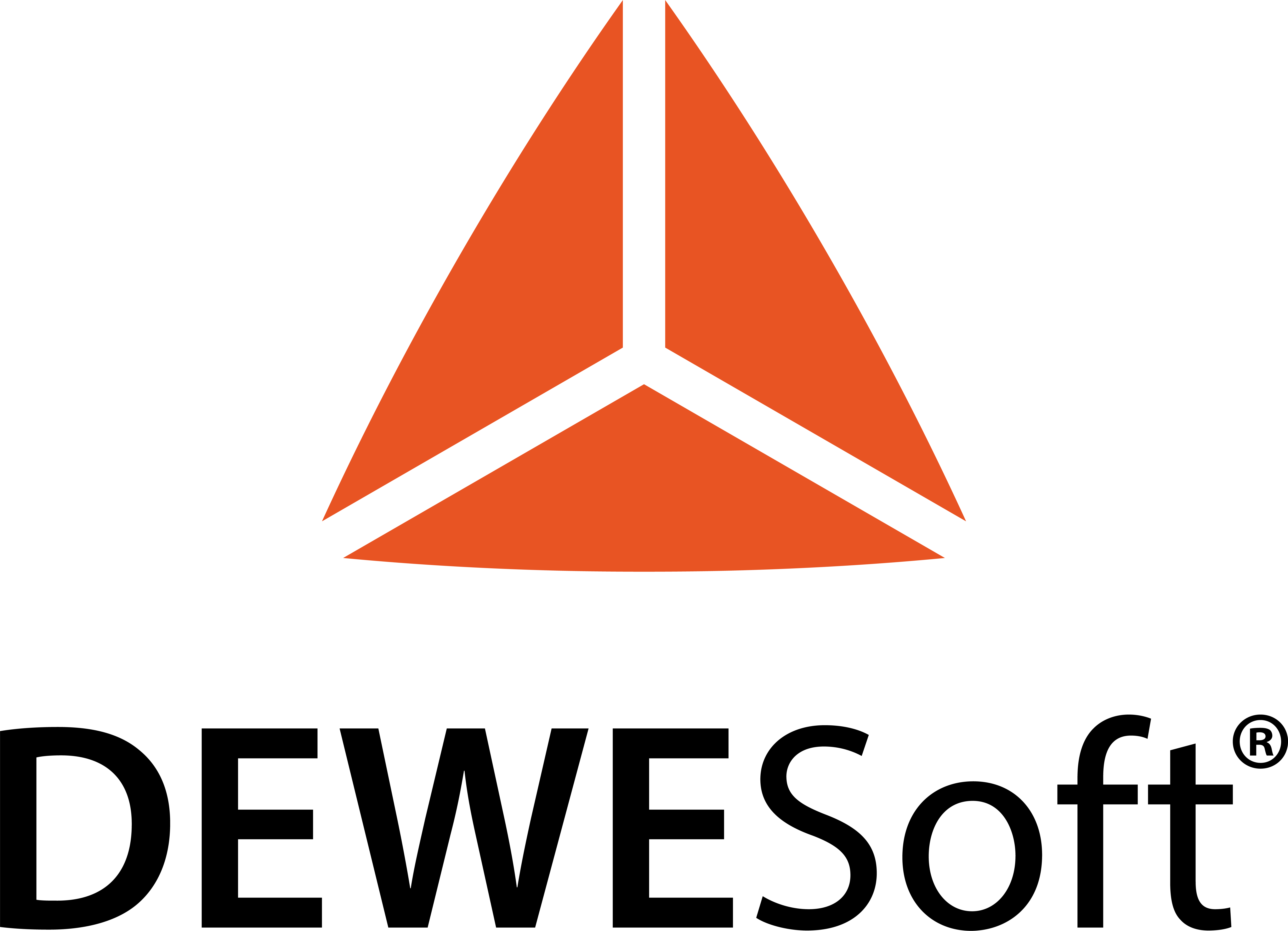
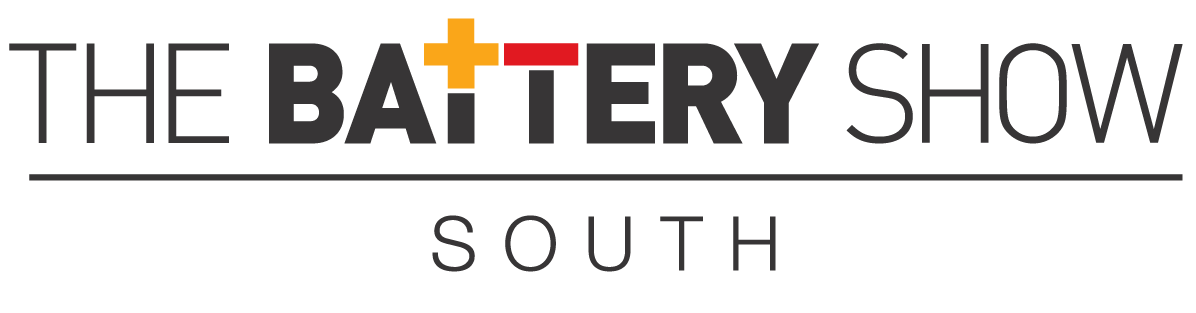
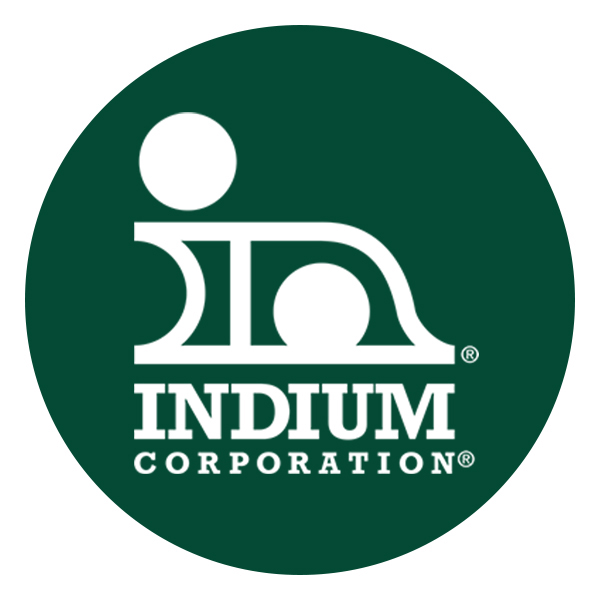
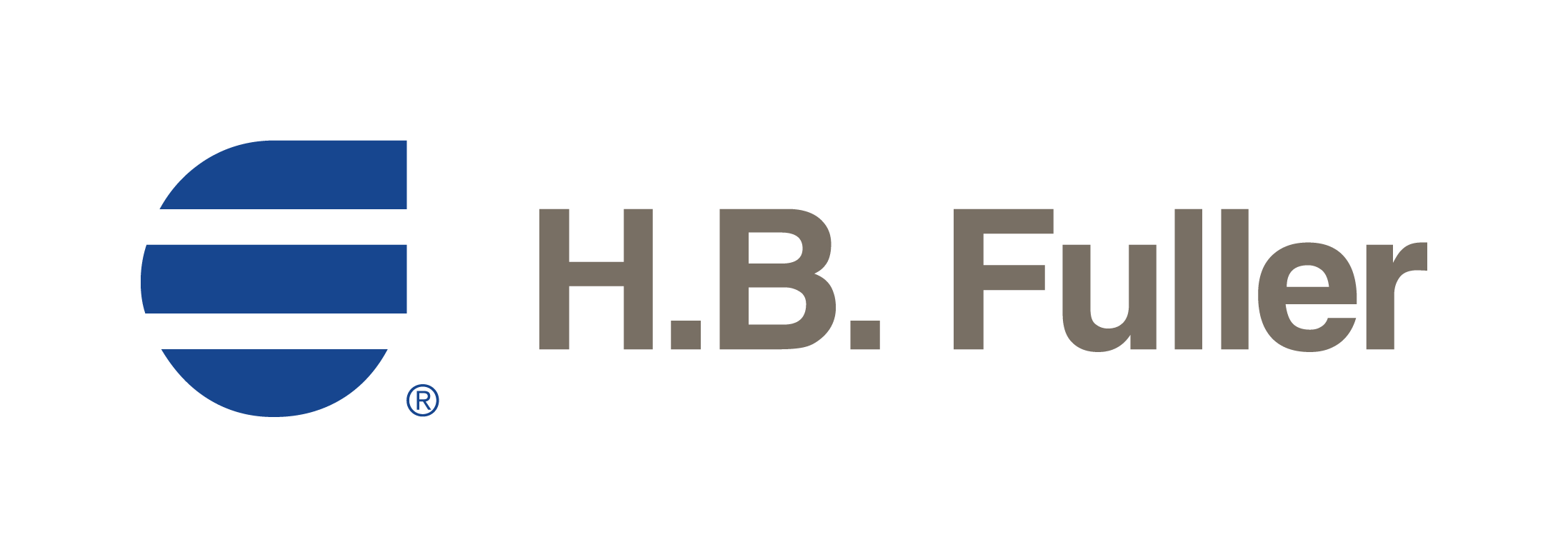