Adhesives: essential EV enablers
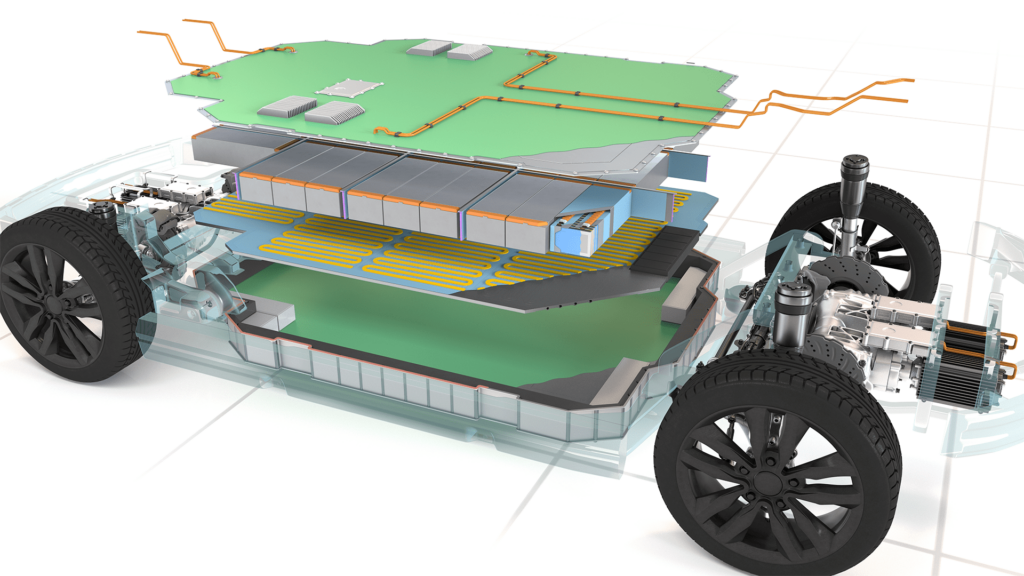
Adhesives are used in vehicles of all kinds, but they are particularly essential in electric vehicles (EVs) because they perform key functions within battery packs and help save weight in body structure, translating into performance and energy efficiency, as David Fetterman, PPG Industries’ global segment director for adhesives and sealants, explains to Peter Donaldson.
PPG is focused on what Fetterman calls enabling solutions for electrification, including thermal interface materials (thermal gap filler and thermally conductive adhesives), sealers and structural adhesives in batteries.
Additionally, the company delivers solutions to bond multiple dissimilar materials while improving structural strength and rigidity, along with potential weight savings. These range from trim/assembly with two-pack (2K) polyurethane technologies for lightweight lift gates to epoxy-based structural adhesives and rubber-based materials, which make vehicle bodies quieter by reducing or eliminating aerodynamic flutter, for example.
PPG is introducing new products through customer collaboration, identifying improved technologies that use epoxies, silicone and modified silyl (MS) polymers and newly designed water-based binders, Fetterman says. These include liquid-applied sound-dampening products that enable a quiet and comfortable ride, thanks to the absorption of low-frequency vibration.
Anticipating needs
“The greatest short-term challenge facing the automotive adhesives and sealants market is anticipating needs for speciality products around battery EVs, where they must perform thermal management functions,” Fetterman says. “As the shift to battery EVs accelerates, PPG is also focused on developing new battery adhesives with multifunctional properties, including thermal conductivity, electrical insulation, and higher thermal and fire resistance, with better processability.”
Customer collaboration is essential to the successful development of such multifunction materials. “Suppliers are becoming more integrated with OEM design teams to accelerate the use and adoption of adhesives and sealants earlier in the design process,” Fetterman says.
He emphasises that with the need to facilitate mass production at the OEM and Tier 1, processability must be managed carefully via the use of specific formulation tools. The processability of an adhesive or sealant, he explains, is a combination of open time, handling time, compressibility and compatibility with the application system at high application rates.
Strong and adaptable
In volume production, adhesives have to be applied efficiently to meet the demands of fast-moving assembly lines, and they must be adaptable to a variety of application systems. Further, the presence of a large, heavy battery brings the need for a reinforced structure, particularly in the sill area – resulting in higher thermal mass in the sill, and a nested structure with thermal insulation characteristics that effectively reduce the temperatures to which the materials are subjected in cure ovens.
This has created a need for ‘broad bake’ adhesives that can achieve high strengths over a wide range of cure times and temperatures, Fetterman adds.
Adhesives that cure to the strengths required at low temperatures reduce energy consumption in manufacturing, which helps to shrink the carbon footprint of EVs. Other moves in this direction, he notes, include the adoption of technologies such as 4-wet sealers, water-based materials, technologies that minimise the release of volatile organic compounds (VOCs) and multifunctional materials. (The 4-wet process involves the application of four layers of sealers in a wet, liquid state without allowing intermediate drying or curing steps between the layers.)
“PPG products are nearly 100% solids, providing additional sustainability benefits,” he adds.
Safety and performance
In terms of new products, Fetterman says PPG is focusing on materials intended to increase EV safety, comfort and performance. Besides thermal interface materials and battery pack assembly sealers and adhesives, these include low-density sound deadeners applied as liquids, wet-application coatings, low-temperature-cure materials, and adhesives for alternative substrates such as magnesium.
“Each of these solutions is driving the development of stronger and safer vehicles,” Fetterman says.
ONLINE PARTNERS
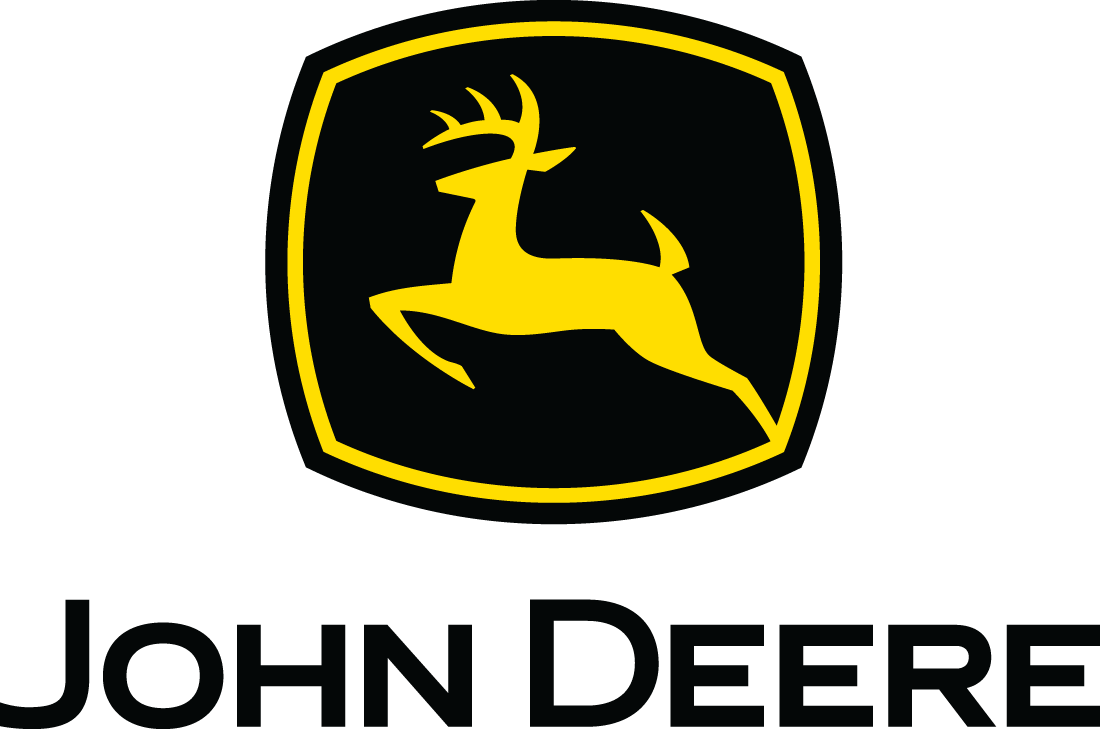
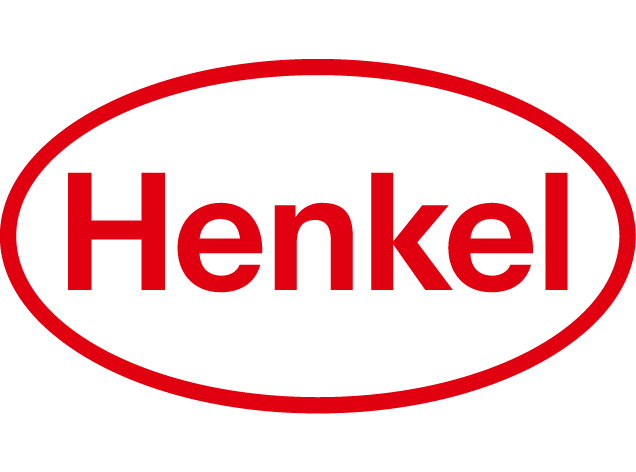
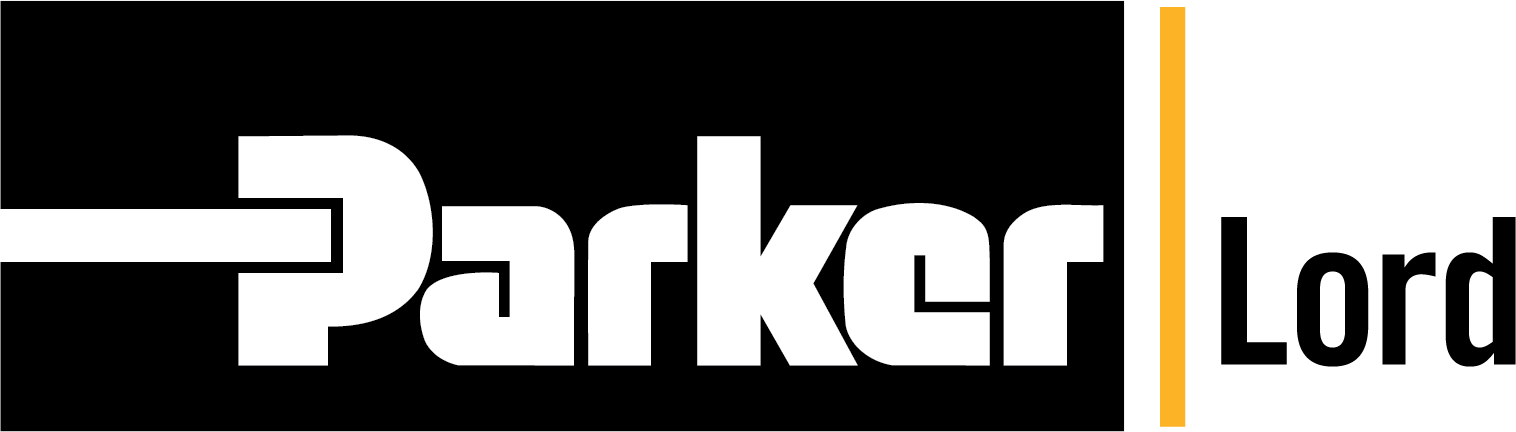
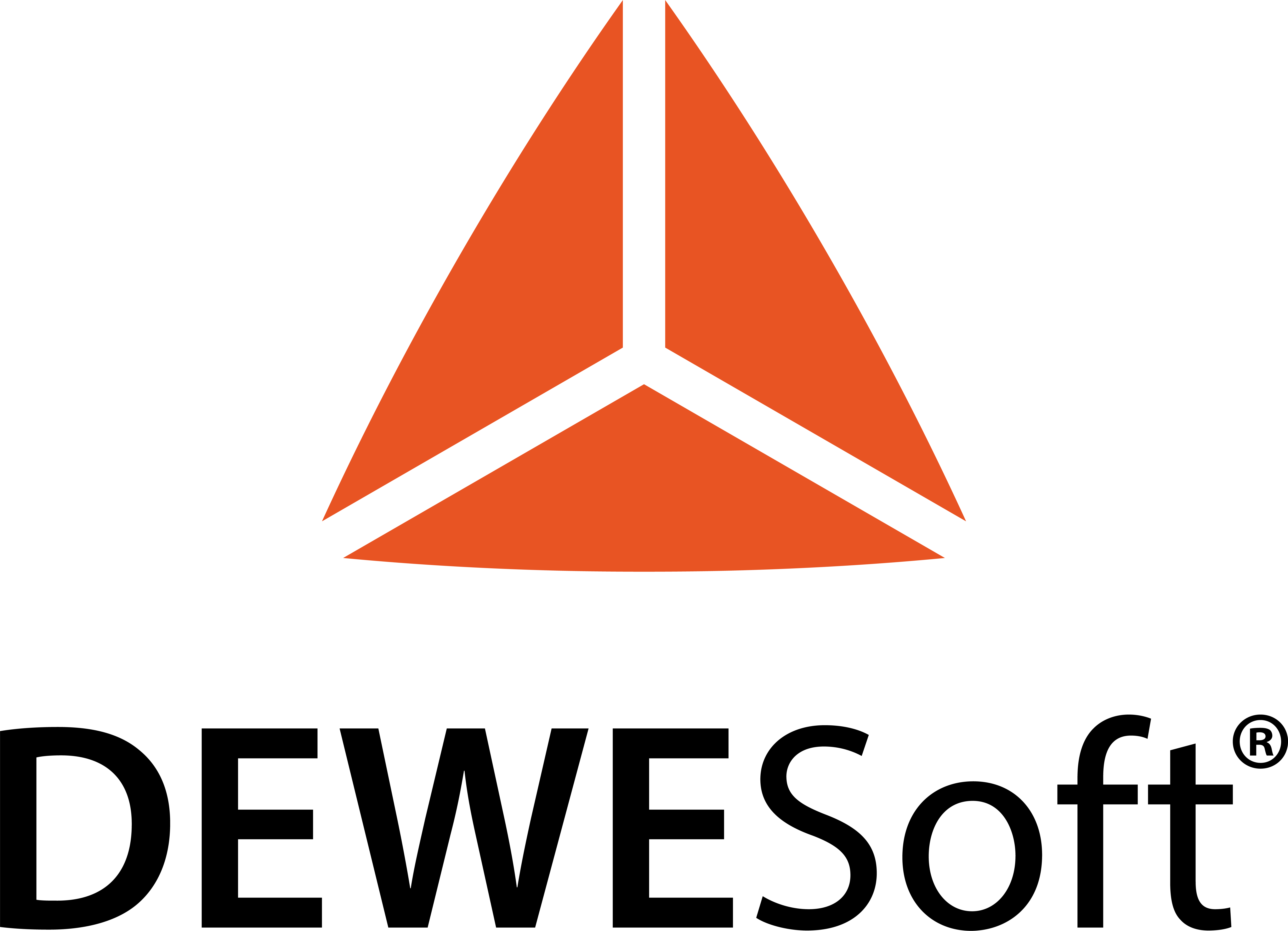
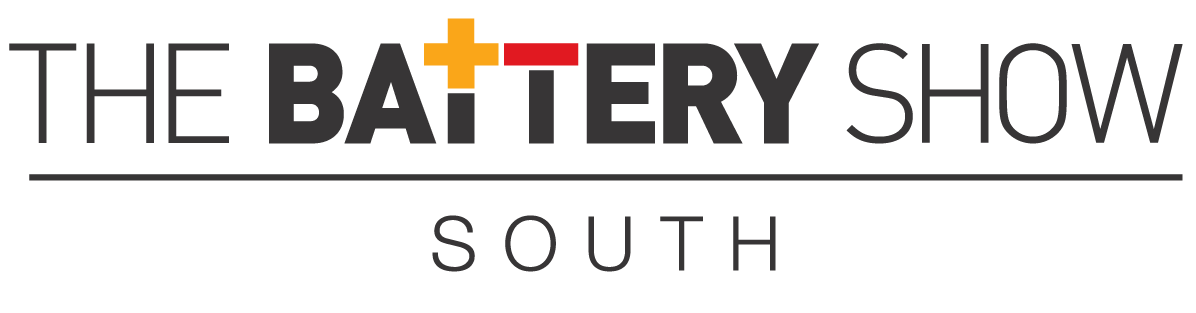
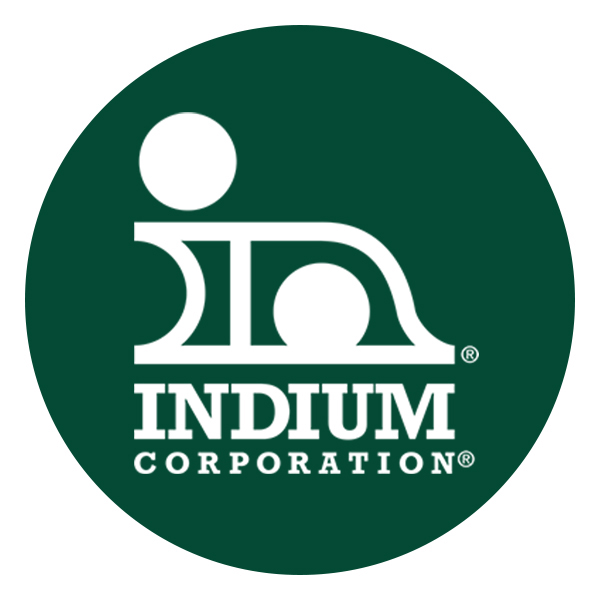

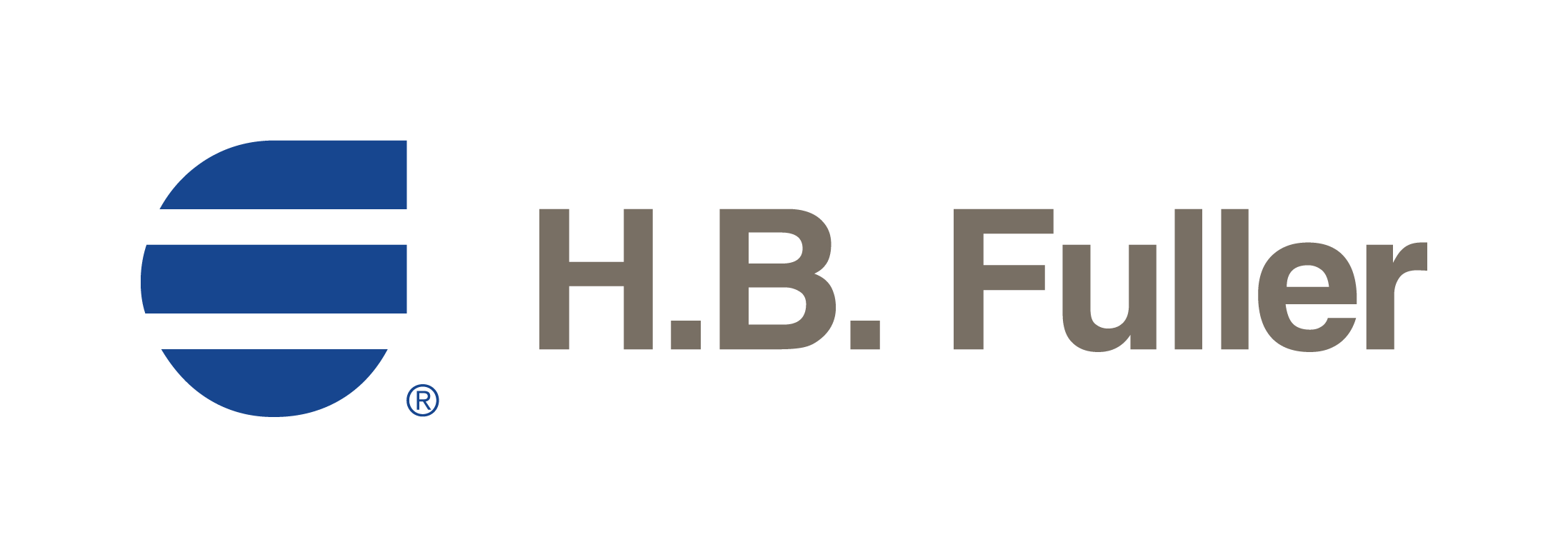
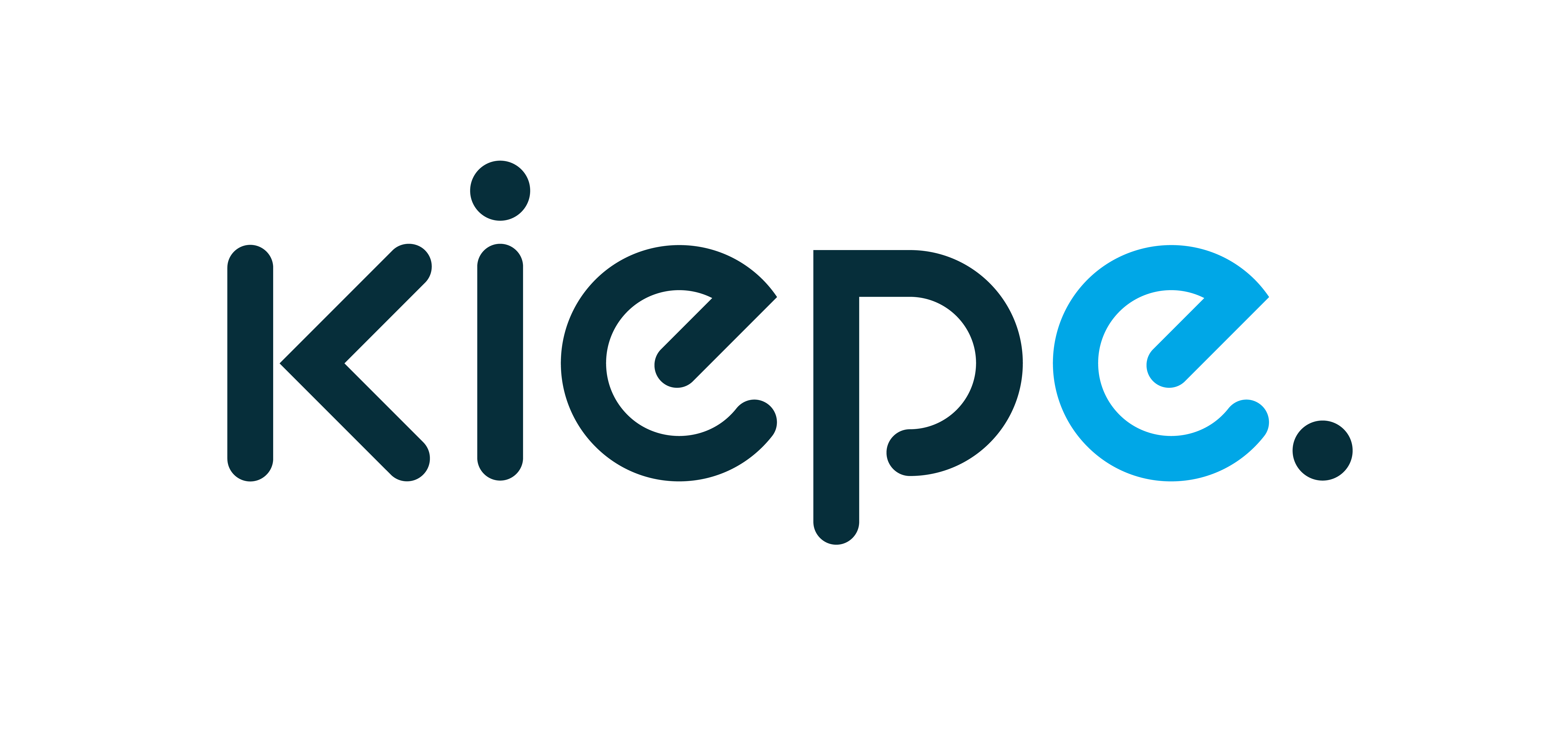
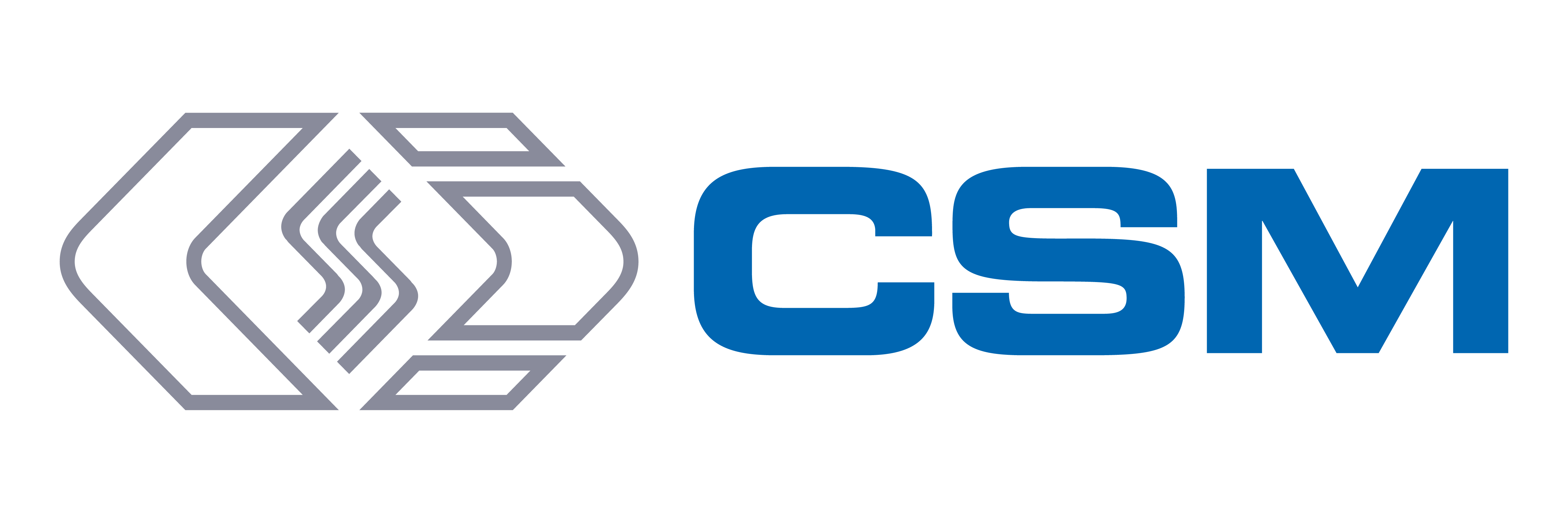