Potting & encapsulation
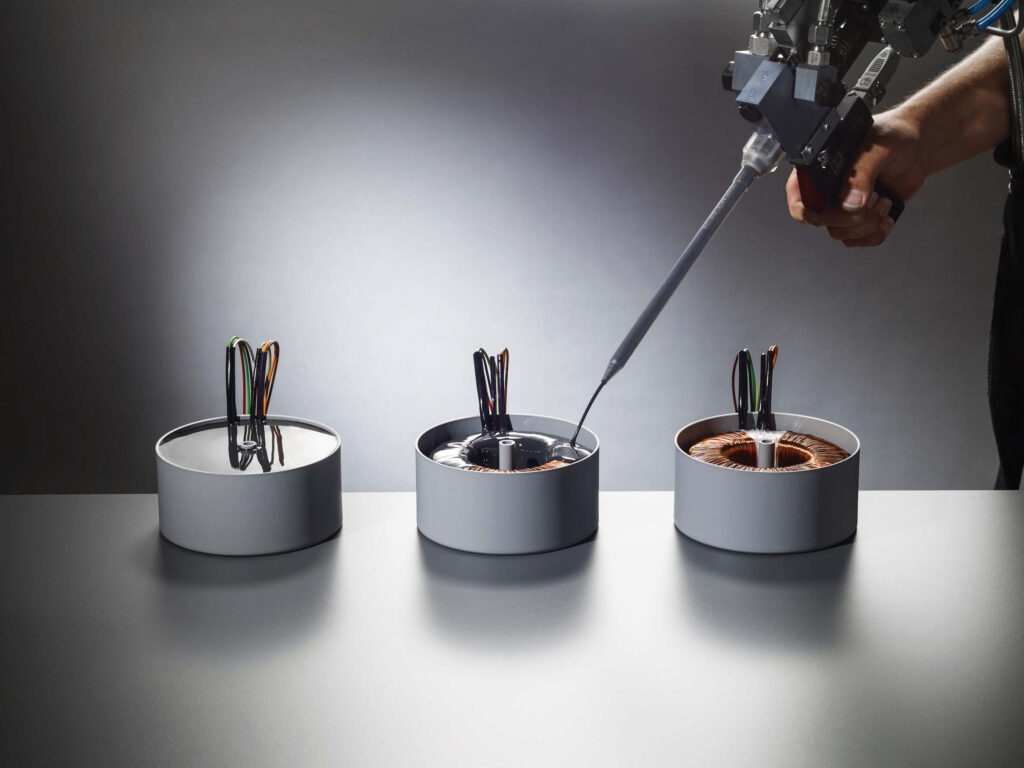
(Image courtesy of Axalta)
Potted parts
Peter Donaldson examines the finer points of potting and encapsulation
Many electrical and electronic components last longer, perform better and stand up to the stresses and strains of hard use with fewer complaints if they are potted or encapsulated in a polymer. While the two terms are often used interchangeably, they don’t quite mean the same thing.
Potting is a process by which a form or ‘pot’ containing the parts to be protected is filled with a polymer resin and becomes part of the finished component.
Encapsulation differs in that the parts and the hardened resin around them are removed from the pot to be placed in an assembly. Which method is chosen depends on various factors, such as the design of the component, the manufacturing and assembly process, and the demands of the application.
The resin can be formulated to provide the components with benefits such as protection from moisture, tailored thermal conductivity, electrical insulation, and isolation from shock and vibration. It can also help to make the components more resistant to tampering and conceal them from prying eyes if there is sensitive intellectual property.
While the same polymer type may serve in either role in different applications, this is not always the case. Defining a specific polymer as a potting compound or an encapsulant is generally a marketing technique, and is based on a component used in a specific industry, says Joe Staller at Epic Resins.
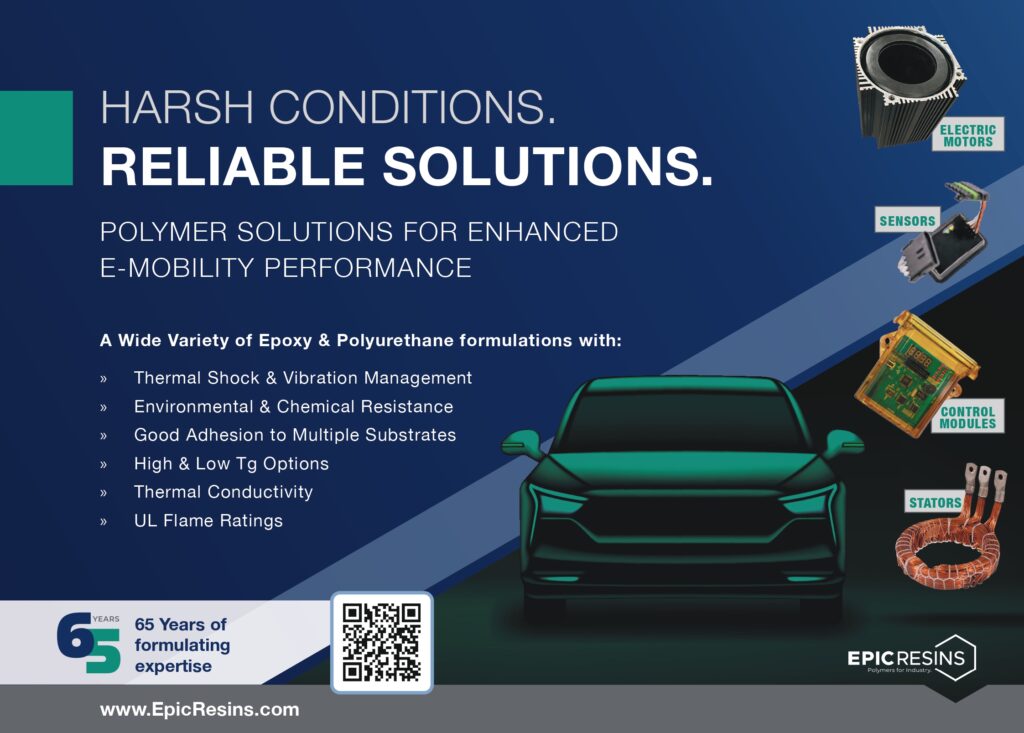
A polymer used as a potting compound could act as an encapsulant, and vice versa. Equally, a material that makes a good encapsulant in one application may not work at all in another, he says. As one application may be more demanding than another in a variety of ways, the polymers may need different properties.
“We feel it is important to have this conversation with customers so that we have a thorough understanding of their application. This allows us to provide recommendations and support beyond the generalised use of a polymer.”
The two processes can place different demands on the material. For example, encapsulation may involve applying the polymer directly to a component within a housing, effectively forming a shell around it. This requires high form stability, unlike a potting compound, which must sufficiently self-level to fill the entire housing without residual voids, notes Dr Kevin White at Henkel.
Potting and encapsulation are referred to as embedding processes, alongside a third major process of this kind, called impregnation. Here, the part to be protected is immersed in a liquid and then pressure or a vacuum is applied to ensure complete wet-out of the component. This causes all air to be eliminated and all of the component’s surfaces are covered by the polymer.
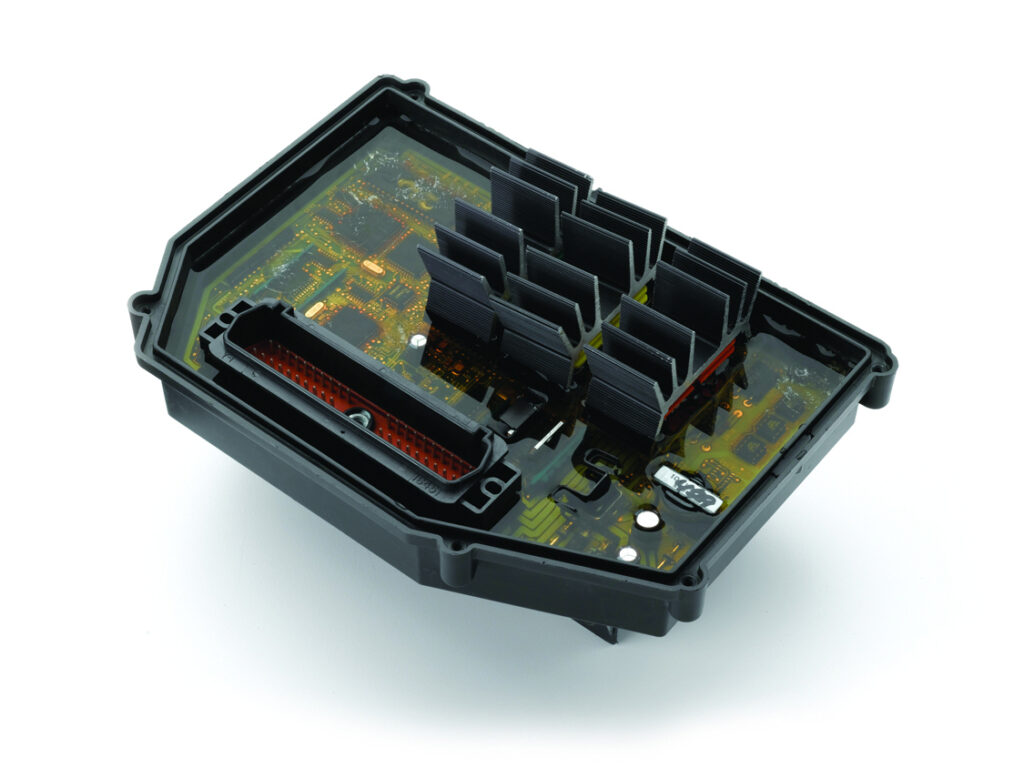
(Image courtesy of Epic Resins)
Varied applications
The list of components protected by these methods is long and includes onboard chargers, battery packs, power electronics, electric motor stators and rotors, electronic control units (ECUs), battery management systems (BMS) and sensors.
In EVs, thermal-potting compounds are important for any heat-generating element, and they find widespread use in power electronics and e-drive components; a key example is power conversion devices such as inverters. Low-density, thermally insulating potting compounds can also be used in battery modules or packs to encapsulate the cells to help prevent a thermal runaway event from one cell to another.
“Another possible application would be the encapsulation and protection of the current collector/busbar assembly, says White at Henkel. “The potting product can assist in the protection of the electrical connections, and act as a vibration dampener to protect the delicate wire bonds or other types of connection between the cells and the busbar assembly.”
Today, additional functionalities are added to encapsulating and potting materials, but mainly the latter. These include thermal conductivity, flame retardance, and even thermal insulation to combine the mechanical protection with safety management and protection of parts from fire, especially in batteries.
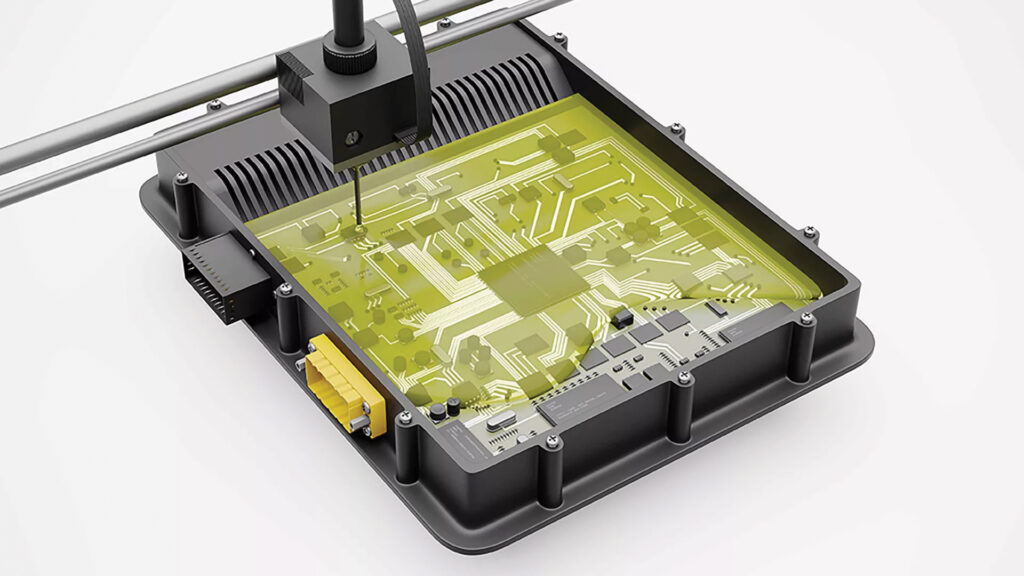
(Image courtesy of Sika)
To pot or encapsulate?
The choice of which type of protection to apply to a component or assembly is affected by many factors. These can include the operating and environmental conditions, the properties and processing requirements of the resins, the shape and size of the components, how serviceable they are intended to be, and the cost and production volume.
Potting is generally better for more extreme conditions, but it makes assemblies more difficult to repair, notes Brandon Brown, vice-president of engineering at C-Therm.
Besides shock and vibration, operating and environmental conditions that must be considered include heat-related factors such as the anticipated maximum temperature, total thermal load and the chemical stresses to which the resins are likely to be exposed.
In electric-motor windings, this might include exposure to oils such as automatic transmission fluid (ATF) used as a coolant, notes Ulf Koschmieder at Axalta, a company with a background in coatings for transport applications has a range of high-performance epoxies.
Often, these factors are affected by the location of the components to be protected, Epic Resins’ Staller notes. A sensor in a vehicle cabin will face very different conditions from one under the bonnet, requiring greater protection from thermal cycling, while a sensor immersed in a fluid would need protection with specific chemical resistance properties. “Each application is unique and requires unique polymer property considerations.”
“Potting is the process best suited to fully cover a large number of electronic components with small features, particularly inductors,” says White at Henkel. “For components not contained in a housing, such as an isolated chip on a PCB, encapsulation or a coating may be more appropriate and would consume less volume of material.”
“It is up to our customer to evaluate how much stress is placed on their component and to decide how they want to protect it, particularly when they are concerned about its geometry and power density, which demand different handling of thermal and safety management,” says Manuel Paintmayer at ViscoTec.
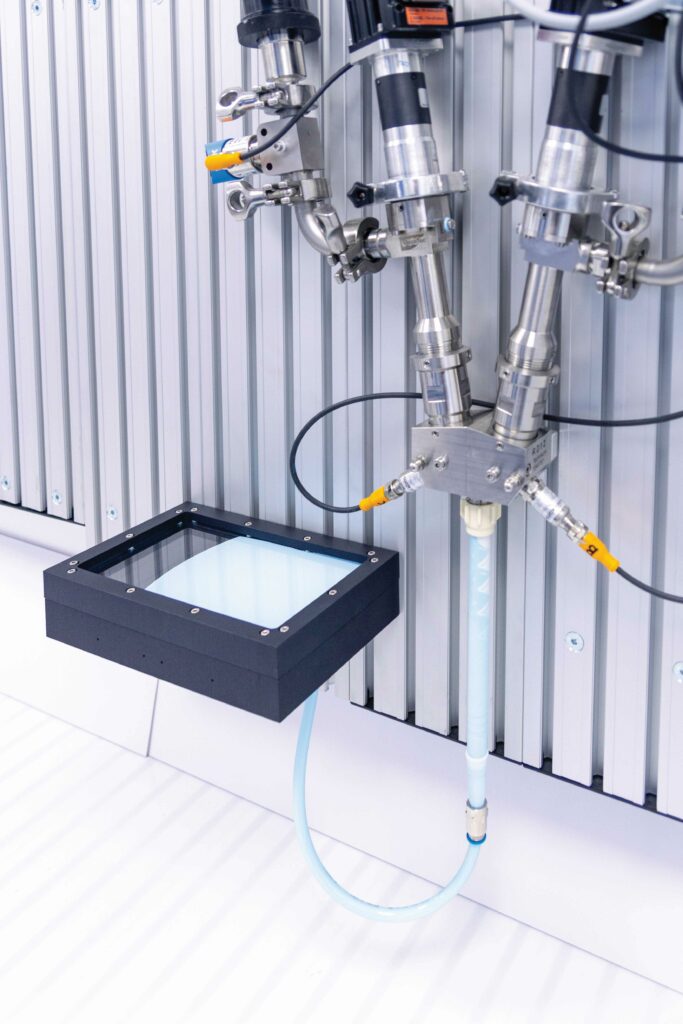
(Image courtesy of ViscoTec)
Materials and dispensing
Potting and encapsulation materials are typically epoxy, polyurethane or silicone resins. Epoxy provides excellent adhesion, mechanical strength and chemical resistance. Polyurethane exhibits good electrical insulation and mechanical protection, and can be flexible. Silicone is best for flexibility, thermal stability and resistance to extreme temperatures.
The higher the application temperature, the more likely that epoxy and silicone will be chosen, says Paintmayer. Silicones are favoured if higher flexibility is needed to minimise stress transfer to electronics.
Low glass transition temperature (Tg) is a critical temperature at which an amorphous material will transition from a rigid, glassy state to a softer, more flexible one. Epic Resins reports rising demand for two principal properties in potting and encapsulation materials for EV applications: soft elastomers with a low glass transition temperature (Tg) and rigid polymers with a very high Tg.
Low Tg materials put significantly less stress on sensitive components and offer vibrational dampening, while hard, high Tg materials tend to have lower coefficients of thermal expansion (CTE) and better chemical resistance, he adds.
Epic Resins can provide products with high or low Tg to satisfy a wide range of EV applications with temperature ranges from -50 C to over 150 C. They can also modify these parameters, and tweak related properties such as tensile strength, elongation, thermal conductivity, viscosity and density.
Offering characteristics intermediate between silicones and epoxies, polyurethanes and acrylates are generally less resistant to moisture penetration, chemical attack and high temperatures, says White at Henkel.
“Silicones are particularly useful in potting applications because of their extremely low Tg and high degradation temperatures, which provide consistent mechanical performance over their operating temperature range of roughly -40 C to 175 C,” they add.
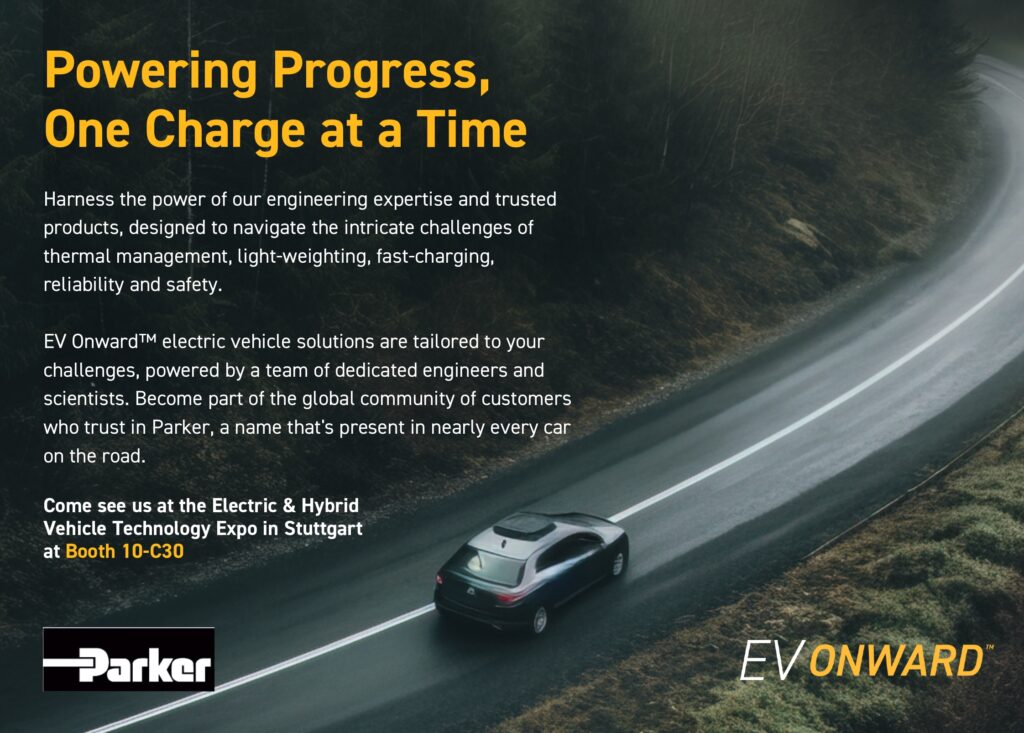
Silicones also have a very low surface energy and therefore wet-out surfaces extremely well, which is ideal for potting applications. The wet-out is particularly important to avoid moisture ingress and ensure excellent resistance to corrosion.
White say silicones have a very low modulus (stretch a lot) relative to other polymers, which is crucial for giving stress relief during thermal cycles.
“The low modulus is important for thin sections with a large CTE mismatch between components. Silicones have an immense range of molecular weights and architectures, which makes them very flexible as starting materials. Silicones are soft materials with high-temperature stability. Their high-temperature resistance compared to urethane is the main advantage, but silicones are much more expensive and adhere less well to substrates than do urethanes.
“Epoxies are also widely used for high-voltage applications in EVs, but they have a much higher glass transition temperature and higher modulus, which makes the CTE mismatch much more important to manage to avoid component damage,” he adds.
Over the last five years, Axalta has been developing new epoxy-based materials for the encapsulation of electric machines in industrial applications, such as servo drives, and it is looking to apply them to EV motors, Koschmieder says. The idea is to improve thermal conductivity by encapsulating the stator so that the motor can produce more power without overheating.
“With regard to possible EV use, we did tests with a couple of ATF oils and got brilliant results,” he emphasises. “Some of these oils are very aggressive due to the additives included.”
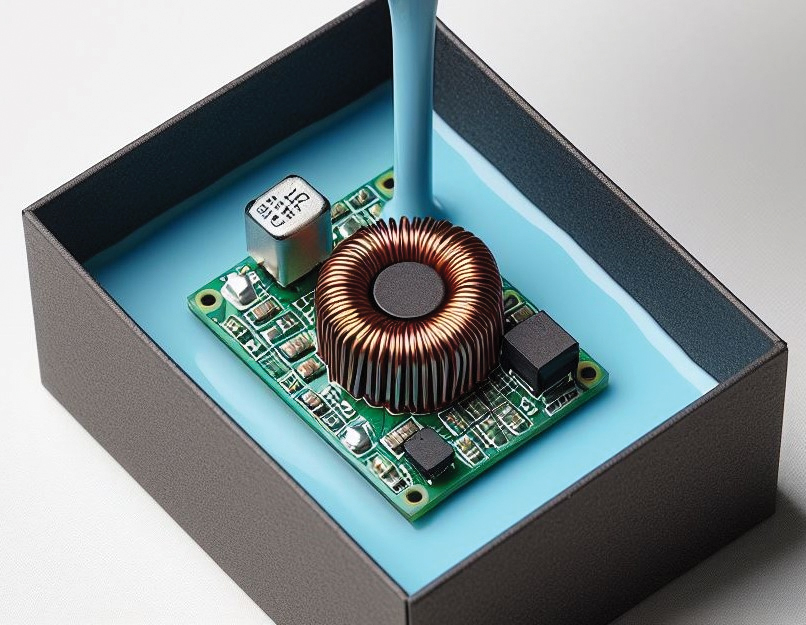
Essential fillers
All of the polymers used in potting and encapsulation have relatively low thermal conductivity, and therefore typically have fillers such as alumina mixed into them to increase their ability to dissipate heat, improve their electrical conductivity or, in some cases, reduce cost.
“A common challenge in the industry is formulating the products in a way that the filler distribution remains uniform,” says Brown of C-Therm. “Agglomeration and sedimentation are issues often faced in manufacturing, depending on the shelf-life stability of the composite.
“Typically, the lower the viscosity, the more quickly they tend to sediment. Several sophisticated systems are available from groups like bdtronic that provide automated dispensing of precise amounts of material. It is crucial to do so at speed and place the material precisely in scaling manufacturing.”
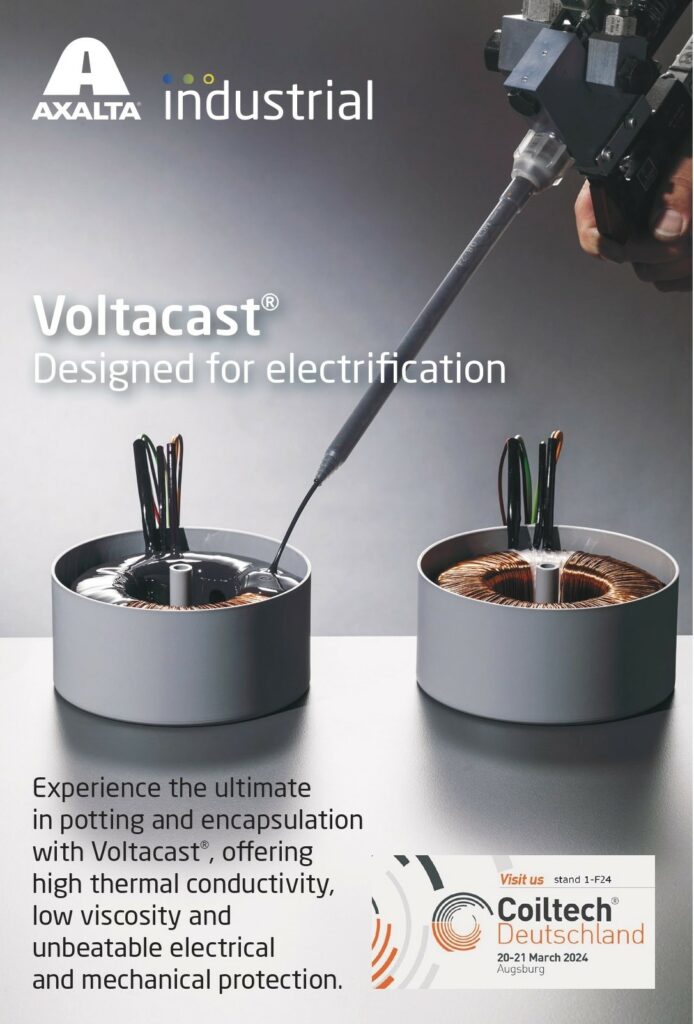
Henkel’s Bill Brown says dispensing is vital in any thermal potting application because of the high volumes and potential abrasion of components by the hard particles of the thermal filler.
“The dispensing system needs to be matched with the dosing accuracy required and must be well integrated with the overall process flow. For thermal potting, remixing is often required prior to dispensing to ensure good homogeneity of the high-density thermal filler, while thawing may be needed for one-component systems,” he says.
The dispensing process can be manual through a pressure-driven gun or with meter-mix equipment for large-volume production. For two-component systems, dynamic and static mixing heads may be used, with static mixing the most common for thermal potting due to the abrasive qualities of the filler.
The most common dispensing methods for potting of batteries include static, static-dynamic or fully dynamic mixing in preparation for low-pressure injection or filling. The latter are typically accomplished with gear pump, progressive cavity pump or piston-pump systems, says ViscoTec’s Paintmayer.
In contrast, high-pressure mixing and injection systems are used with foaming materials. For potting high-power electronics, mixing units based on progressive cavity or piston-pump technology are mainly used.
ViscoTec makes dosing and filling systems, along with dosing components based on the progressive cavity pump technology for semi-automatic and fully automatic production plants and assembly processes.
“We have been able to dispense a wide variety of materials, but in the area of potting and encapsulation we have gained most experience with silicones and polyurethane,” says Paintmayer. “For thermally conductive and thus typically abrasive fluid types, we have optimised our pump technology to combine high precision with long equipment life.”
After dispensing, the material needs to be cured, which can often be done at room temperature, but may be accelerated at an elevated temperature, Brown at Henkel adds.
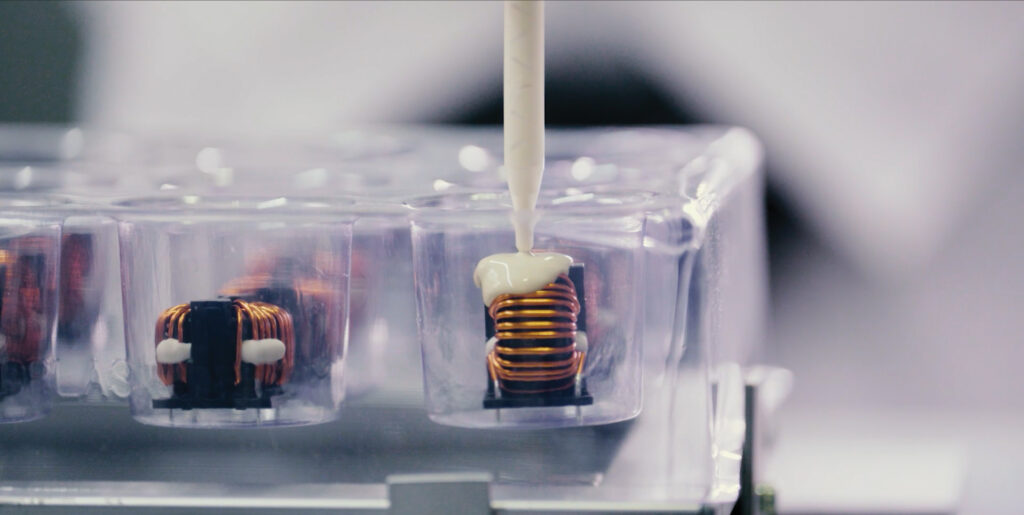
(Image courtesy of Henkel)
New materials and methods
Axalta is working on a new epoxy material that meets the Class H temperature specification of 180 C and offers thermal conductivity in the range of 1.5-1.6 watts per metre kelvin (W/mK). This, says Koschmieder, enables good heat transfer from encapsulated motor windings.
“It’s the same resin base that showed excellent resistance to some ATF oils. Of course, we can’t test every ATF oil in advance, so we would recommend that customers do some of their own tests with particular ATF oils.”
C-Therm tests all kinds of potting and encapsulation materials, says Brown, including cured and uncured products used in r&d and manufacturing. It has introduced sensing technology that can thermally map the composite material formed by the resin and filler, assessing the distribution of the filler as it relates to thermal conductivity.
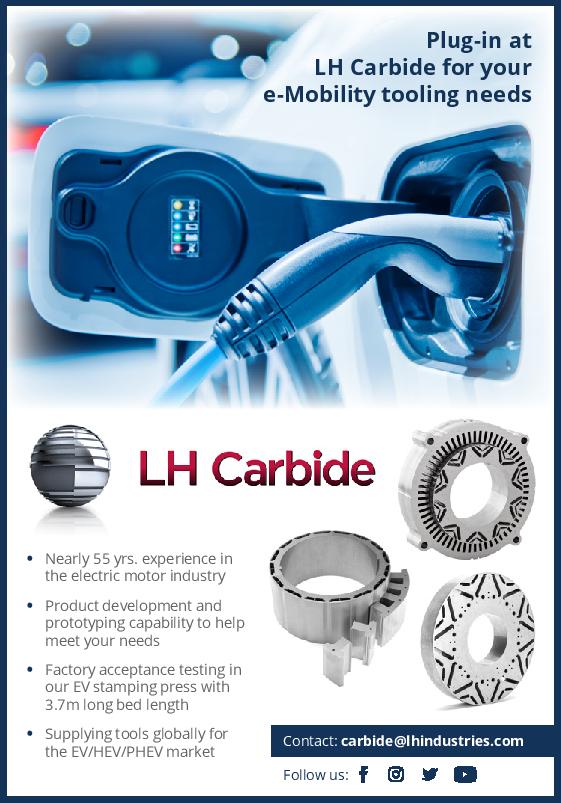
“We are starting to deploy the sensors in manufacturing, monitoring in real time the process of dispensing potting compounds and two-part adhesives to check for sedimentation,” he adds.
In terms of process, incorporating thermal property sensors in the dispensing equipment will significantly improve manufacturing confidence in the application of these materials, says Brown. For the automotive industry, this will give assurance of greater consistency in the performance of potting materials and two-part adhesives.
“The immediate benefit will be less downtime on dispensing equipment, less scrap or rework, and much improved traceability at a critical step of the manufacturing process,” he adds.
Henkel notes the surge in demand for EVs has brought a significant increase in volume, plus a drive to lower cost while maintaining performance in critical applications. This pushes the development of new and improved materials, and addresses unmet needs, which the company seeks to pursue though collaboration with customers and partners.
For potting compounds, White says the goals are to expand their operating temperature range, reduce density, and improve their overall mechanical and electrical protection characteristics. At the same time, the company’s engineers work to maintain thermal conductivity and a cost structure suitable for large volumes.
“From a process perspective, the goal is always to have a product that can integrate seamlessly into customer process flows, which means ensuring excellent coverage and wet-out without requiring vacuum or other post-dispensing treatment, and carefully balancing working time with cure time to enable high throughput,” White says.
“By removing the need for vacuum assistance for penetration into a component or removing the need for heat curing, Henkel is developing solutions that reduce overall process costs and complexity.”
Challenging systems
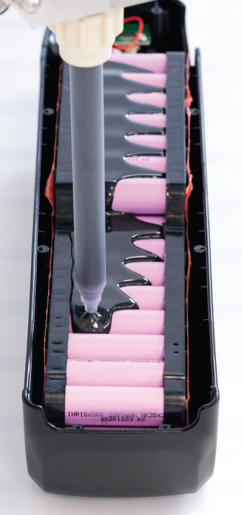
(Image courtesy of ViscoTec)
According to ViscoTec, r&d is leading to materials with improved thermal conductivity, higher temperature resistance, improved fire protection, shorter curing times, and greater flexibility and environmental sustainability. “Faster-curing potting materials may challenge automated dispensing systems to provide the highest process reliability while also reducing waste and lowering the CO2 footprint,” says Paintmayer.
The ability to dissipate heat is one of the main drivers in the development of new potting and encapsulation materials, to which thermal conductivity is critical, says Brown at C-Therm.
“This is why fillers are used, but they are heavy and expensive. In formulating these materials, it is better not to just load up the filler ratio, as the material still has to be pumped, so viscosity and abrasiveness are important considerations. Ideally, as little filler as possible should be used to achieve the desired thermal conductivity within the polymer matrix. To do this well, it is essential to pay careful attention to filler distribution.”
Thermal properties also have an impact on electrical properties and, together, they affect overall efficiency.
Epic Resins’ Staller says tailored thermal conductivity is required to maintain optimum electrical conduction efficacy in both conductors and power electronics. He also points to the critical role played by sensors in EV safety and efficiency, arguing that protecting them from the effects of thermal and electrical stresses is vital to their sensitivity and longevity.
In providing protection from electrical stresses, the move towards higher voltages requires materials with greater dielectric strength to provide adequate insulation for all components.
White at Henkel says there are relatively few electrically insulating materials with good thermal conductivity, reasonable cost and availability, and suitable rheology for low-viscosity applications.
“In a composite, thermal conductivity is essentially a function of the total volume occupied by the filler. And, in general, thermal conductivity builds up much more slowly than viscosity, leading to a number of challenging design trade-offs,” they add.
“Silicones have a remarkable suite of mechanical properties owing to the silicon-oxygen backbone structure at the molecular level, but there are trade-offs in the adhesion strength and resistance to hydrocarbon fuels that are difficult to overcome, particularly with the extreme filler loadings required for thermal applications.
“Epoxies are far superior to silicones with regard to adhesion, but it is difficult to control the modulus and glass transition temperature without loss in other critical properties, such as chemical resistance or upper operating temperatures.”
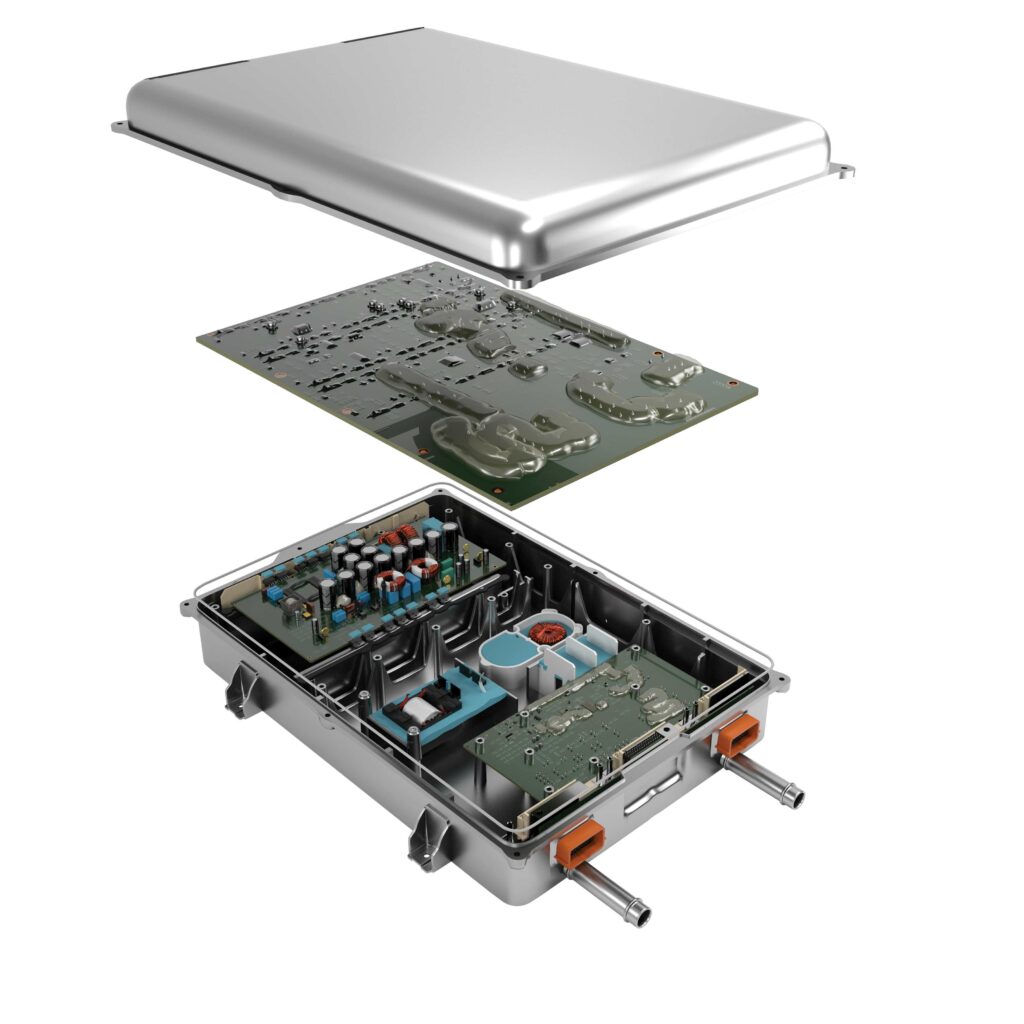
(Image courtesy of Henkel)
Changing battery architectures
New battery architectures, including cell-to-pack and cell-to-chassis configurations, are influencing the formulation and dispensing of materials, ViscoTec’s Paintmayer says, adding that they necessitate adaptations to cater to diverse form factors and methods of integration.
“The focus is on customising potting and encapsulation solutions to meet specific design and performance requirements. Enhanced thermal conductivity and improved mechanical properties are crucial to ensuring efficient heat dissipation and structural integrity for various cell arrangements.
“With cell-to-chassis concepts especially, potting materials also take on the tasks of mechanical fixation and structural bonding, combined with thermal management, including the prevention of thermal runaway.
“Combined with the growing demand for repairability, which so far seems not to be under consideration for the next generations of EVs, this challenges material developers to provide strong structural bonding along with debonding capabilities.”
These battery architectures also have an impact on automated dispensing systems, presenting a variety of requirements, ranging from many small, individual injections to a smaller number of larger shots at fewer points.
Power electronics issues
Increases in both power density and voltage in power electronics, along with trends in packaging, also present challenges to potting and encapsulation. Power electronic systems include unidirectional and bi-directional inverters, DC-DC converters, BMS and battery chargers (both on-board and external), and they are also used in advanced driver-assistance systems.
Epic Resins’ Staller notes that EV manufacturers are increasingly combining two or more of these systems, often housing multiple components in one enclosure to reduce the total length of cabling and coolant lines in the vehicle.
“Individually or combined, these power electronics process an extraordinary amount of electrical energy while orchestrating precise control over a multitude of components,” he says. “Managing this energy requires a delicate balance of properties to ensure safety, efficiency and longevity.”
Staller adds that choosing the appropriate advanced polymer that can simultaneously dissipate heat, mitigate thermal cycling and insulate high voltages while inhibiting flame propagation is critical.
With high-voltage inverters, for example, the challenges are to prevent insulation breakdown and short circuits, says Axalta’s Koschmieder. Whether they are based on insulated gate bipolar transistors (IGBTs) or silicon-carbide metal-oxide semiconductor field-effect transistors (MOSFETs), the solid-state switches inside inverters produce stepped sine waves.
“The voltage increase when the semiconductor switch turns on affects inductive components, creating a voltage spike of opposite polarity for a short time. That will lead to a voltage peak twice as high as that of the intermediate circuit in the inverter. With these very high voltages, there can be discharges into the surrounding materials, especially if there is any air remaining inside the enclosure, and these discharges can cause very quick destruction of the insulation,” he explains.
This, he adds, will reduce the lifetime of the motor drastically. The need to prevent such damage is driving demand for materials with high dielectric strength and good penetrating properties.
Henkel stresses that the increasing density of electrical components, and the need for rapid charging and discharging of batteries via the power electronics are, as elsewhere in the powertrain, driving demand for higher thermal conductivity.
“This inherently boosts the loading of thermal filler required, and significantly impacts viscosity and flowability. The impact on viscosity is manageable for encapsulating systems, but for potting applications the flow properties throughout the shelf life must be carefully managed to ensure complete filling of the component and integration with customer production lines,” White explains.
Novel motor topologies and locations also affect requirements for protective materials, and they are making custom solutions vital to success and longevity, says Staller at Epic Resins. There are multiple topologies where motor encapsulation is essential, he adds, citing axial flux motors as an example, particularly in-wheel applications. “This location exposes the motor to greater environmental stresses, including water and vibration. Completely encapsulating the conductors gives them excellent protection.”
In radial flux machines, particularly in interior permanent magnet (IPM) synchronous reluctance motor
(syn-RM) applications, the magnets must be secured to the motor. “These compounds fasten the magnets in the correct position, creating a precise magnetic-flux location for optimised electric and magnetic field coupling, yielding maximum torque and efficiency,” Staller explains.
Alongside thermal conductivity, thermal stability is a vital property when choosing a motor encapsulation compound, because it maintains the polymer’s properties over extended periods of thermal exposure, and it is important to assess this. “Monitoring weight change and hardness change of a polymer at elevated temperatures gives a great comparison to determine the stability of a motor compound,” he says.
Repair and recycling
The need for repair and recycling is a significant challenge for potting and encapsulation materials, and Henkel reports significant interest in effective strategies for controlling the release force without affecting in-service performance.
“Silicone-based materials are inherently well suited for repair due to their lower strength, as they can be readily removed from components manually and subsequently washed off with appropriate cleaners, allowing a component to be reused or recycled without contamination,” according to Brown at Henkel.
“Henkel has an advanced research team, focused on de-bonding technologies. The team is continuing to test and develop solutions that support in-plant repair, vehicle service and end-of-life recycling.”
On-board charger, with potting and encapsulation applied to electronic and electromagnetic components (Image courtesy of Henkel)
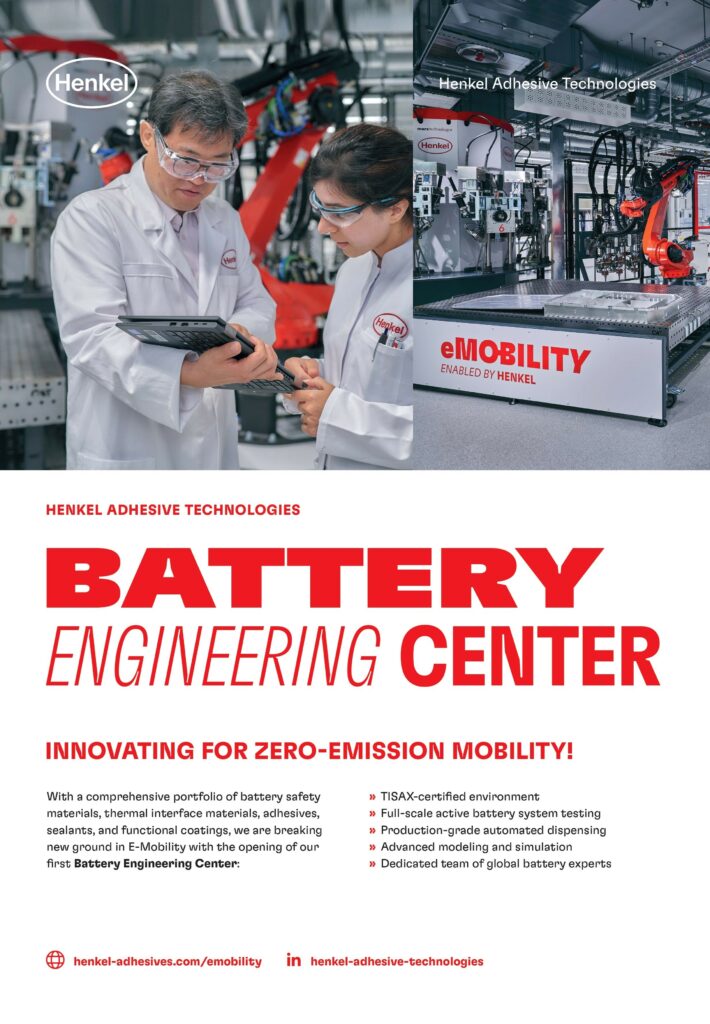
ONLINE PARTNERS
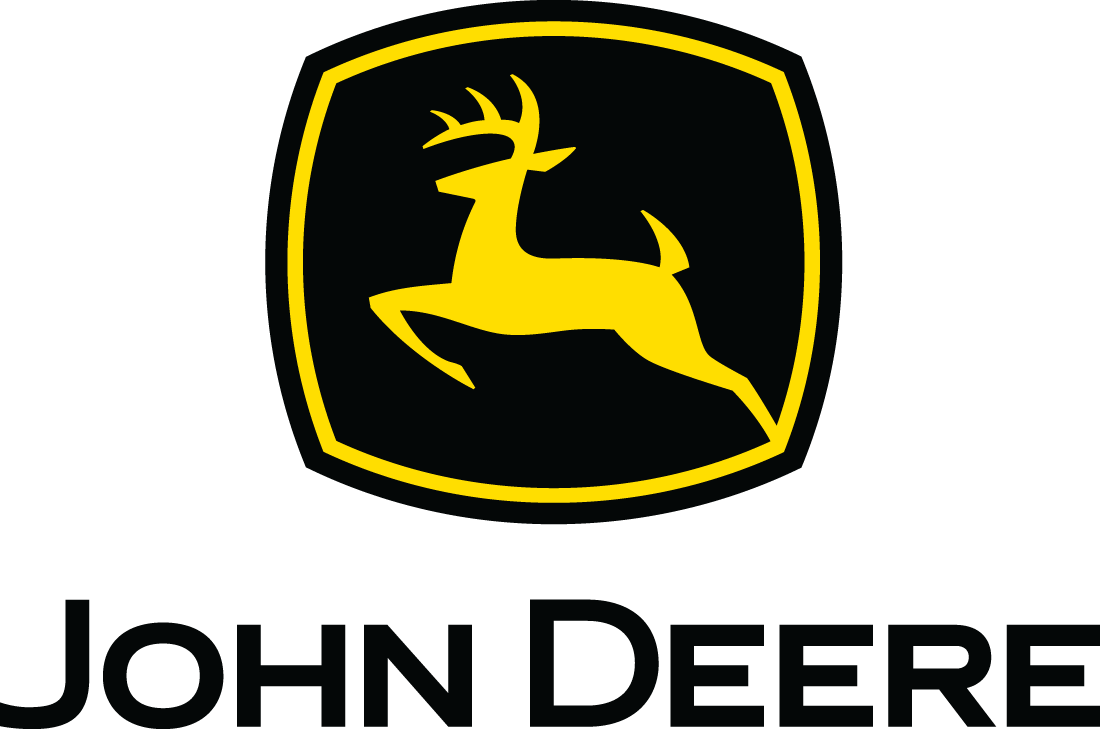
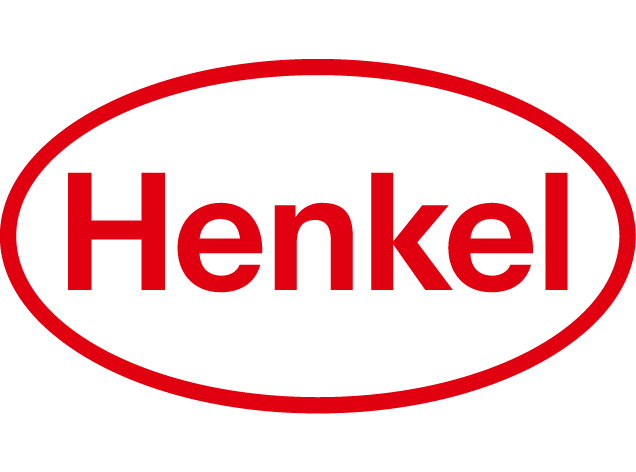
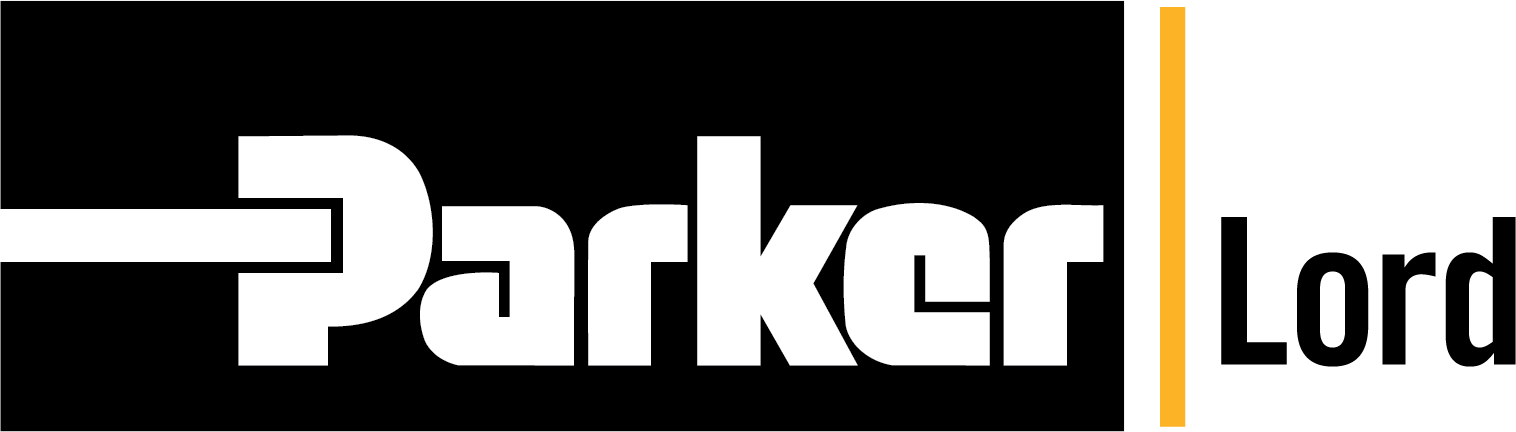
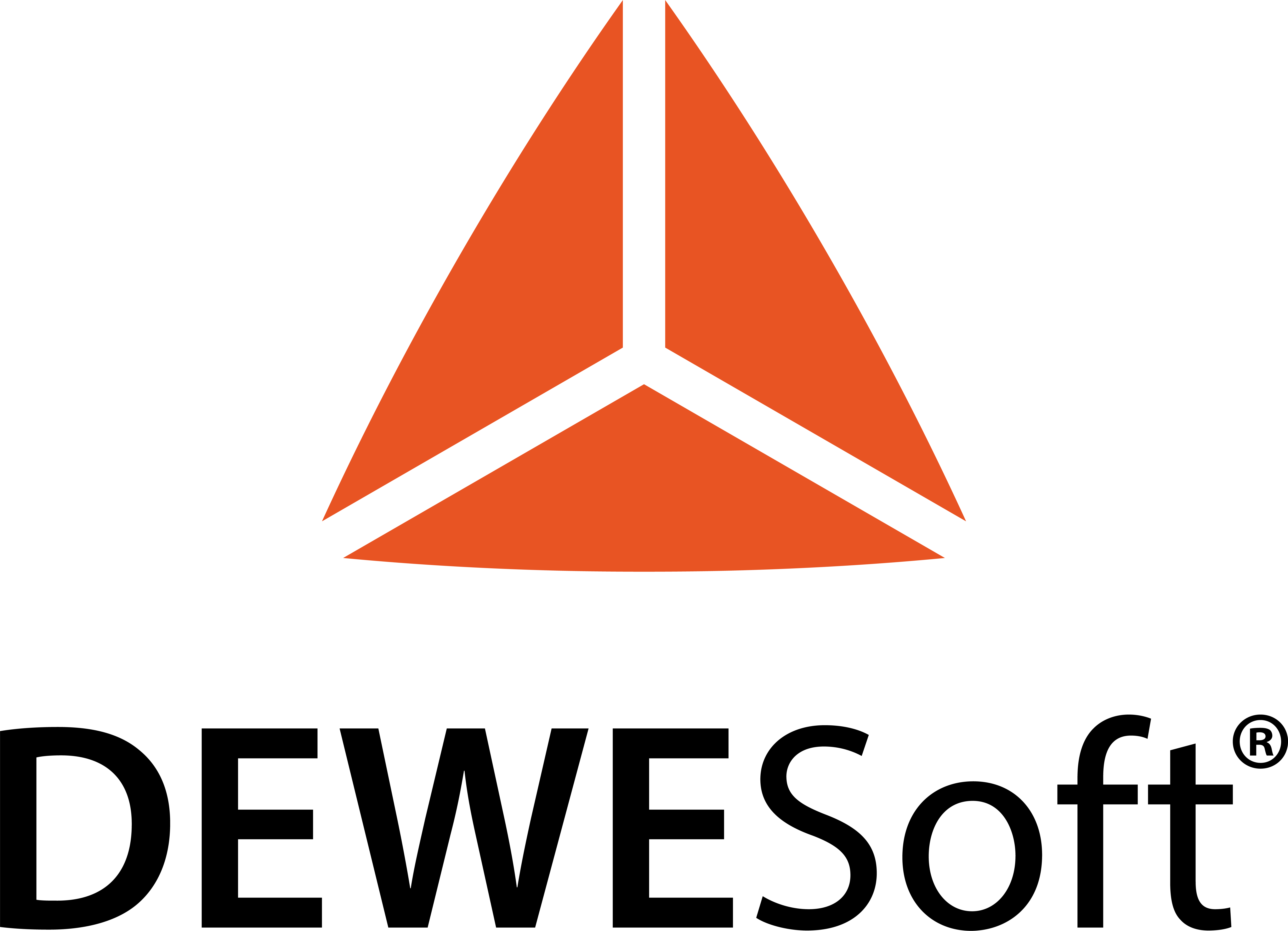
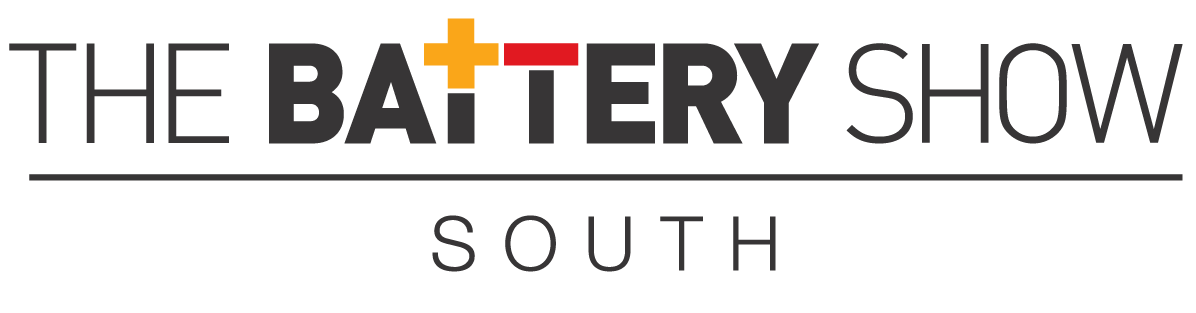
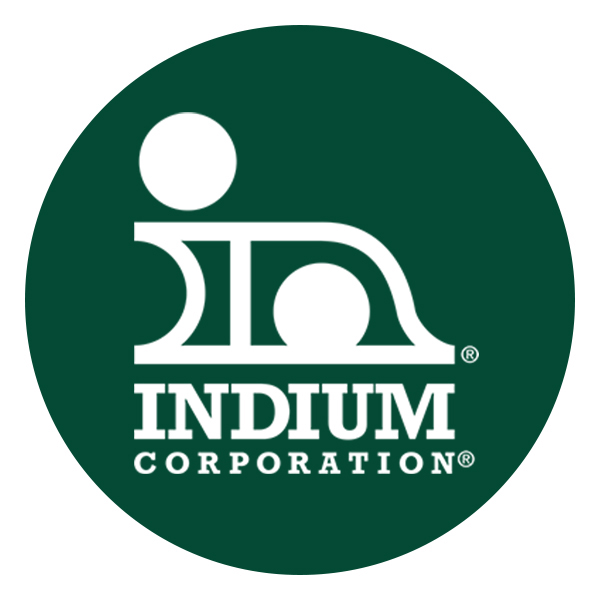

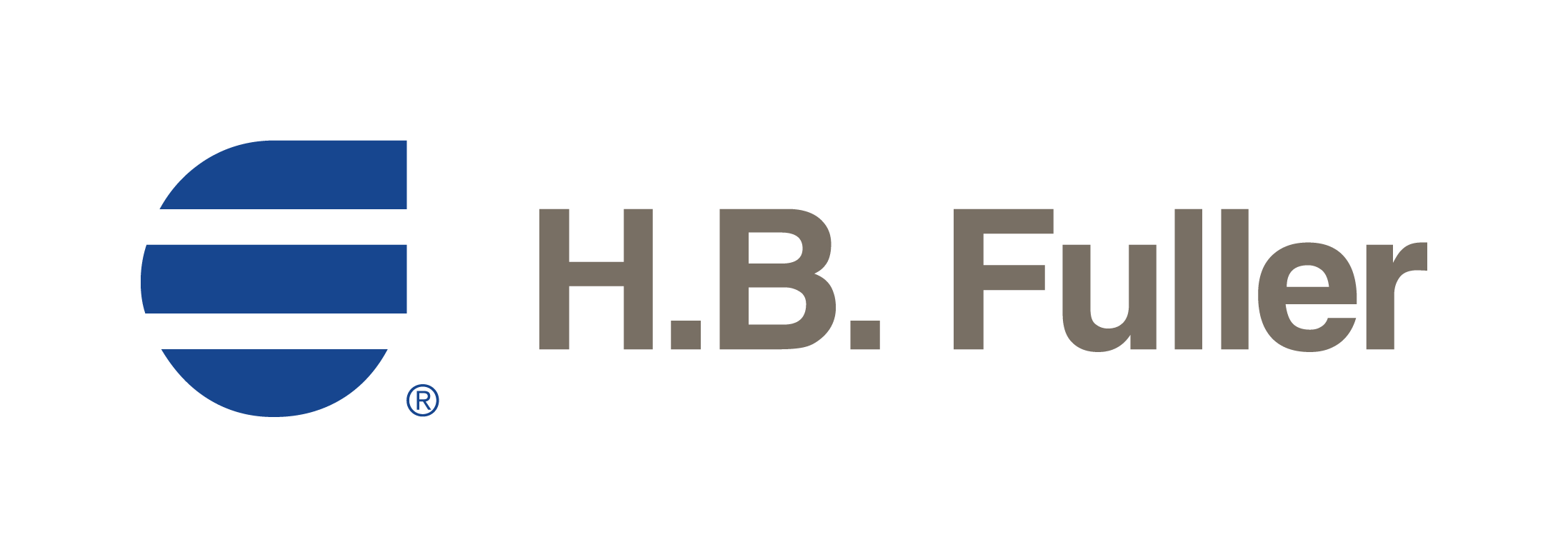
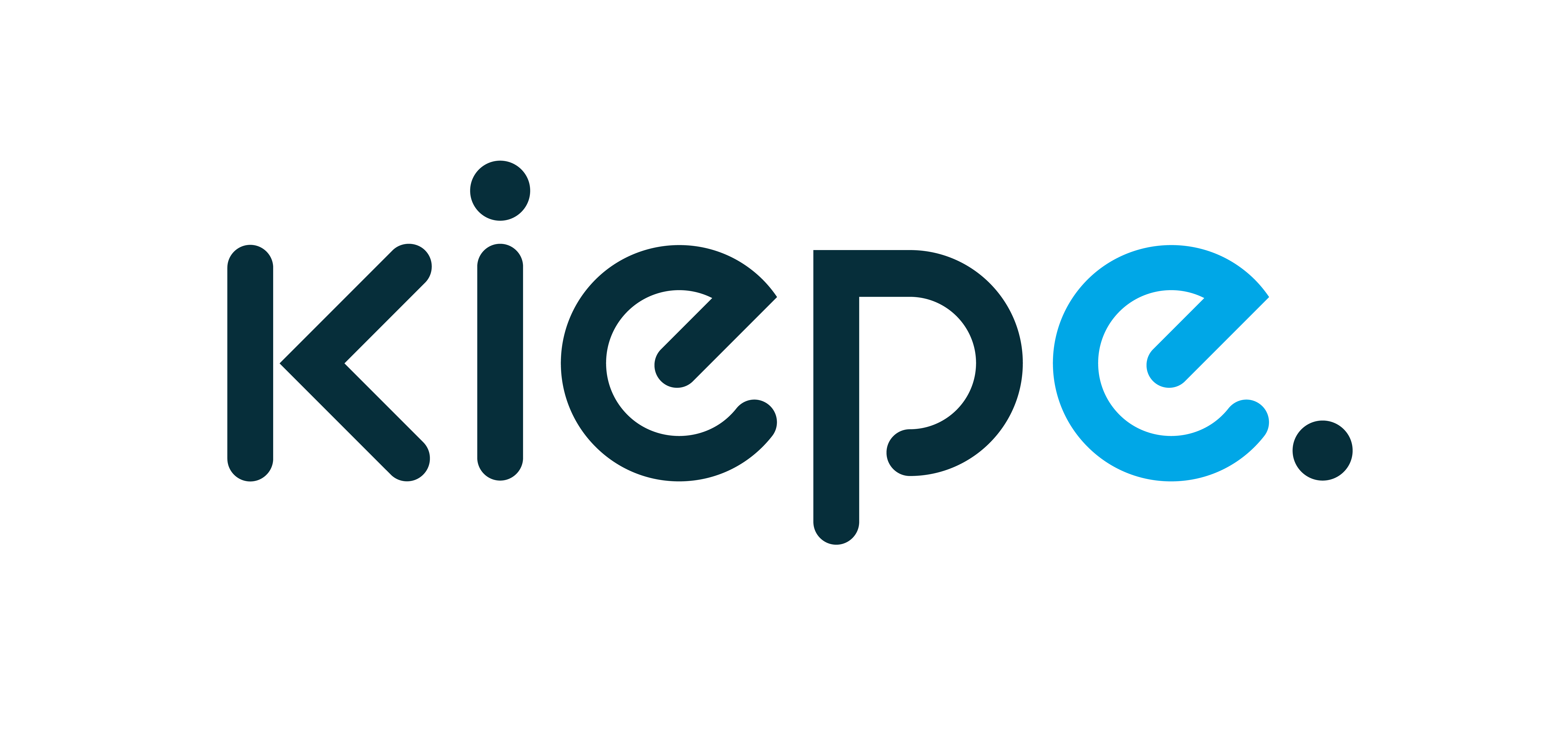
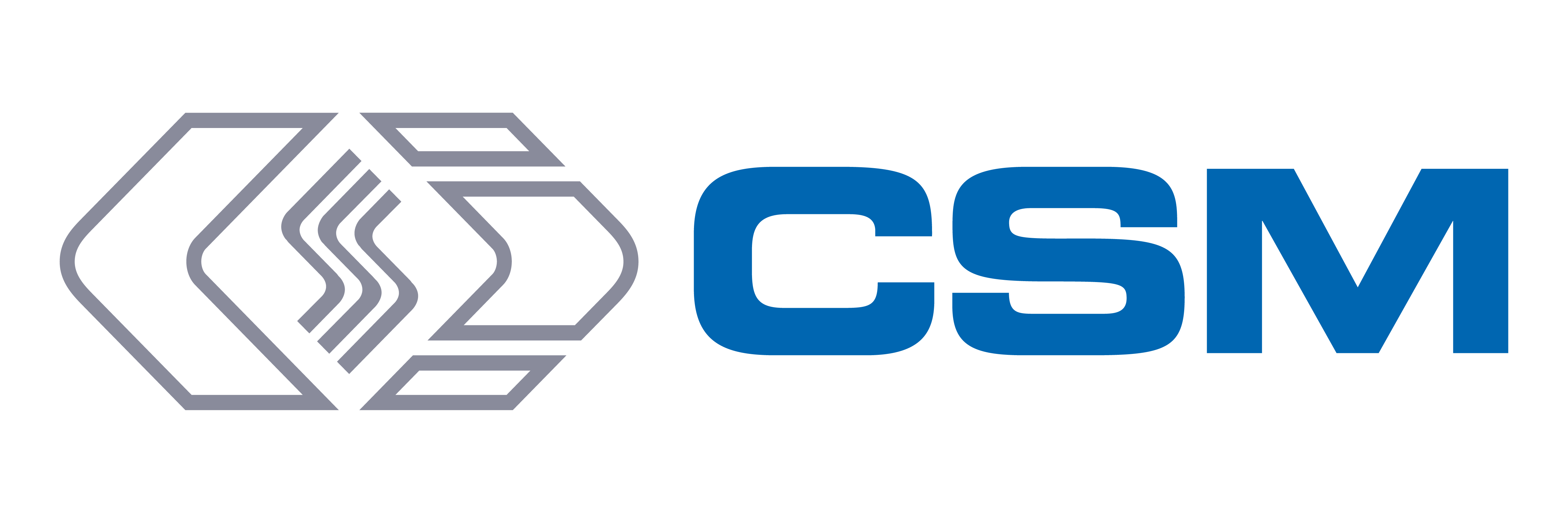