Polymer safety boost for lithium battery cells
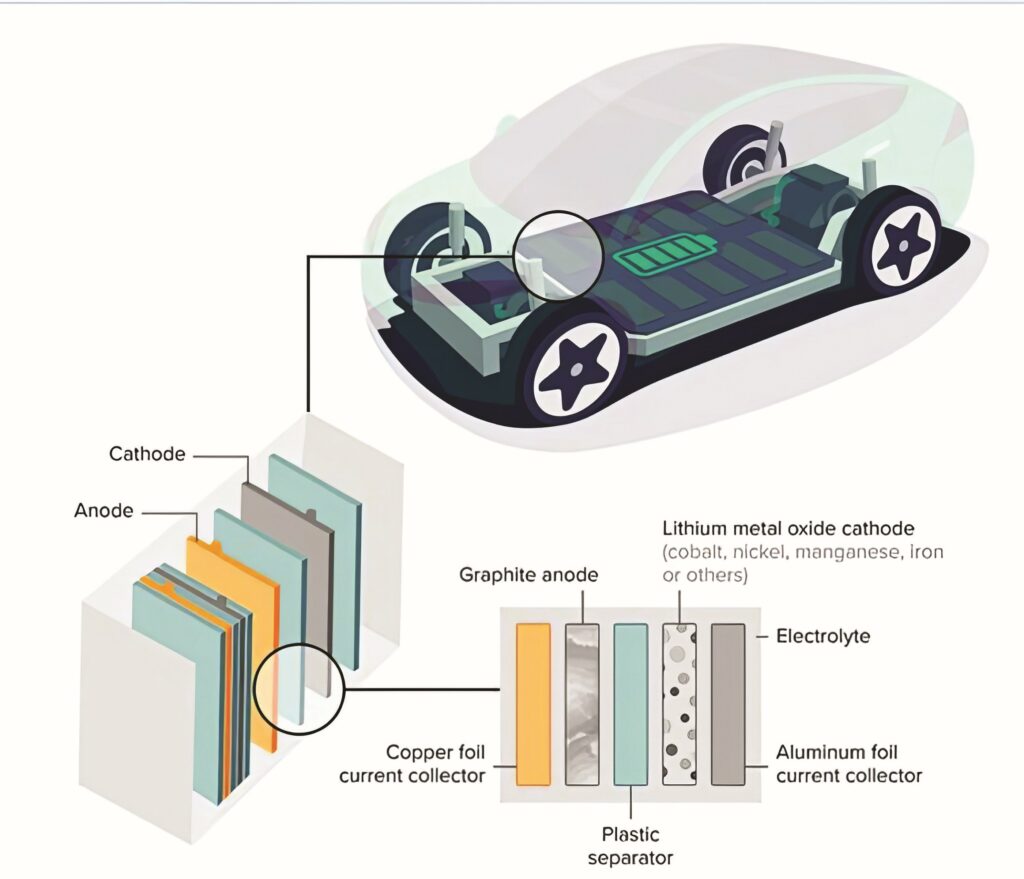
(Image courtesy of Incheon University)
Researchers in Korea have developed a polymer separator to boost the safety of lithium-ion battery cells, writes Nick Flaherty.
Separators composed of polyolefins, a type of polymer, can be employed to keep the anode and cathode apart to prevent an internal short circuit. However, these separators can melt at higher temperatures, and the inadequate absorption of electrolytes can result in short circuits and diminished efficiency.
To tackle these issues, several methods have been proposed. One is to apply ceramic coatings on the separators to improve the way they handle pressure and heat. However, this can increase the thickness of the separators, reduce their adhesion and harm battery performance.
Another technique is to use polymer coatings in graft polymerization, which involves the attachment of individual units (monomers) to the separators to give them the desired qualities.
Research at Incheon National University (INU) in Korea has shown successful graft polymerization on a polypropylene separator (PPS), incorporating a uniform layer of silicon dioxide (SiO2). The study was motivated by the need for high-performance battery materials in EVs to achieve a longer driving range and ease consumer concerns about battery explosions.
“Battery explosions are frequently initiated from the melting of a separator. The commercial battery separator is made of polyolefins, a class of polymers that are vulnerable to heat. We aimed to improve the thermal stability of the commercial separators by coating them with thermally robust materials such as SiO2 particles,” said assistant professor Jeongsik Yun at INU.
In the research, a PP separator was modified. Initially, it was coated with a layer of polyvinylidene fluoride – a chemical chosen to enhance electrolyte affinity and thermal stability – while introducing grafting reaction sites. Then, the separator underwent grafting with methacrylate molecules, followed by a final coating with SiO2 particles.
These modifications made the separator stronger and more resistant to heat, suppressed the growth of lithium dendrites and helped to improve cycling performance.
After completing modification, the Li-ion transference rose from 0.36 (PPS) to 0.66 (GDPS-SNPC) as the SiO2 thin coating at the grafted separators exhibits different cell impedances and electrochemical performances.
The casting process resulted in better cell performance than the immersion method. LiFePO4 (LFP) half-cell tests with different separators delivered a specific capacity of 160.5 ± 1 mAh g−1 at 0.2 C with excellent reproducibility, but cycling tests at 1.0 C had diverse results. No capacity degradation was seen for separators built with nanoparticles using immersion or casting, while the PPS cell exhibited 88.32% capacity retention.
Long-term stability tests showed stable cycling over 1,000 hours at a current density of 1 mA cm−2, while the other cells died before 500 hours. The extremely long lifecycle of the cast cells is attributed to a very smooth Li-plating/stripping process with just 200 nm of SiO2 coating, which does not deteriorate the volumetric energy density of Li-ion batteries.
The modifications preserved the energy storage of Li-ion batteries per unit volume and outperformed other coating methods in cell performance. This technique thus shows promise.
ONLINE PARTNERS
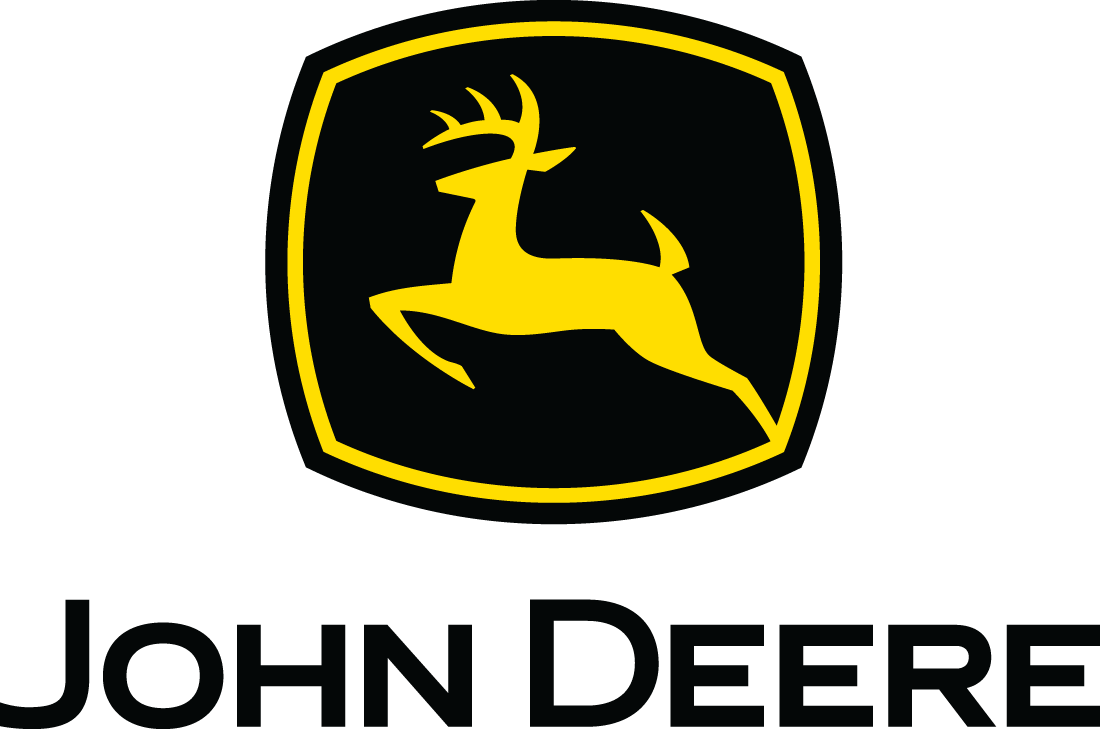
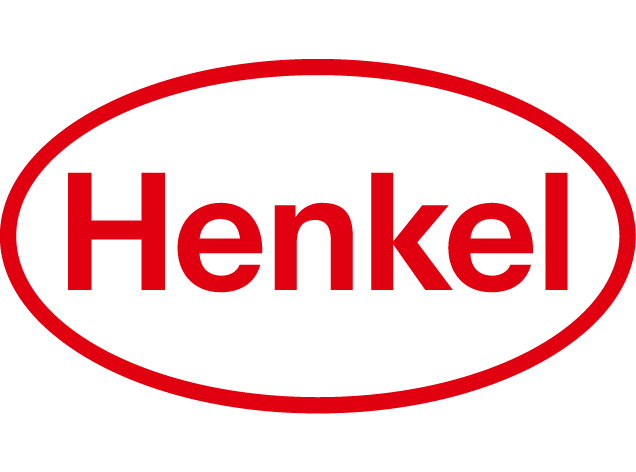
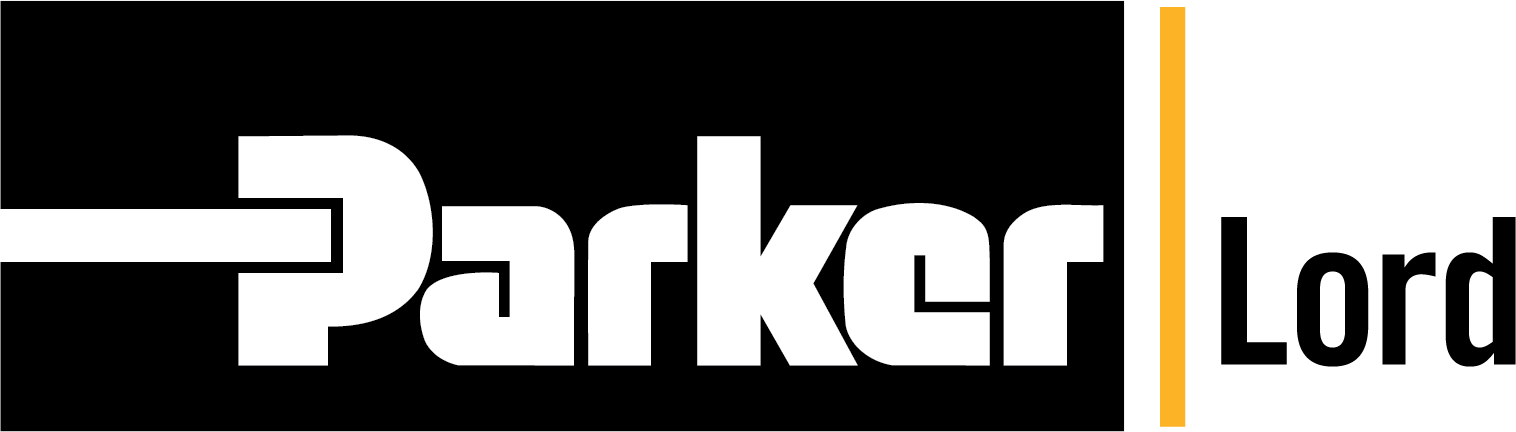
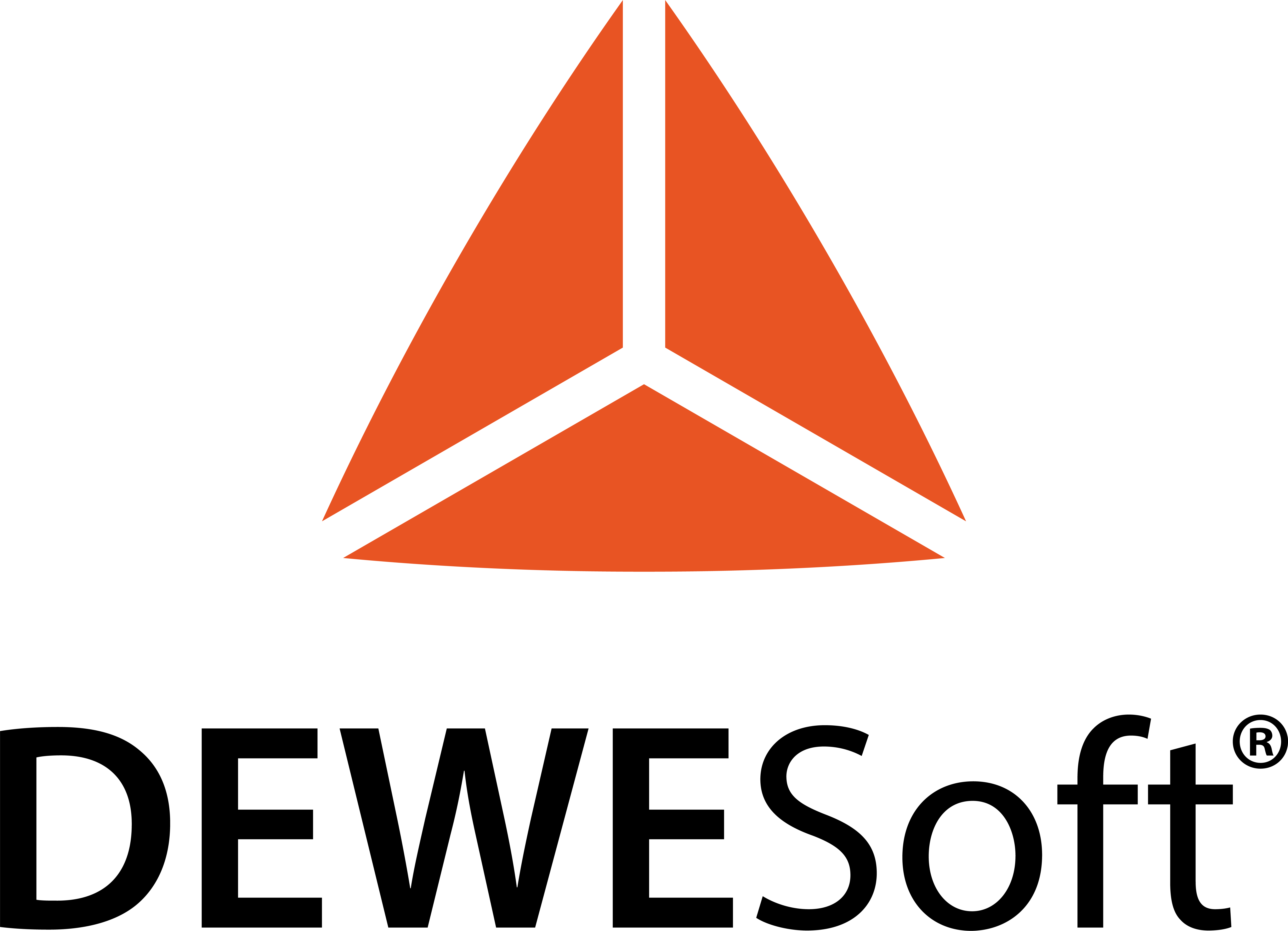
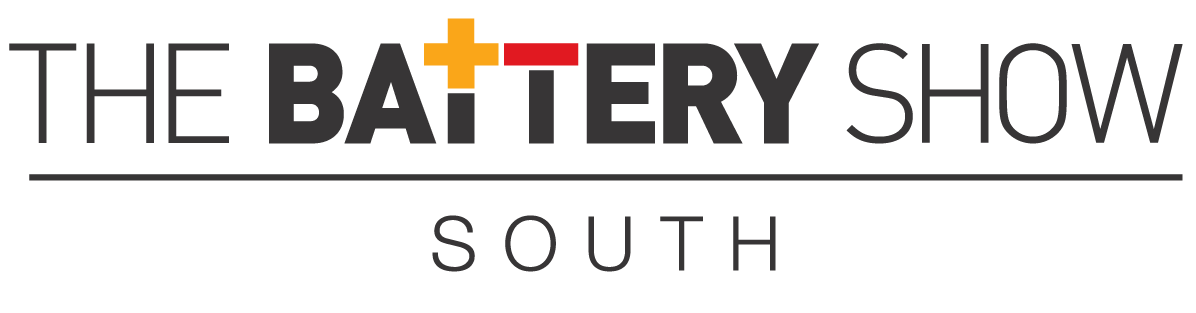
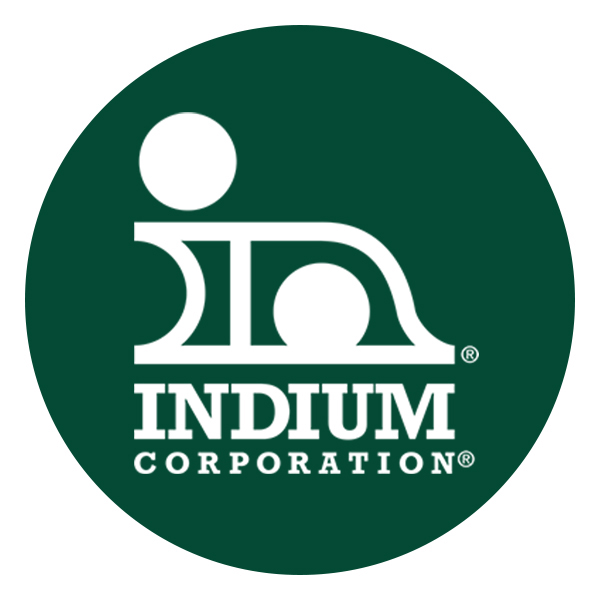

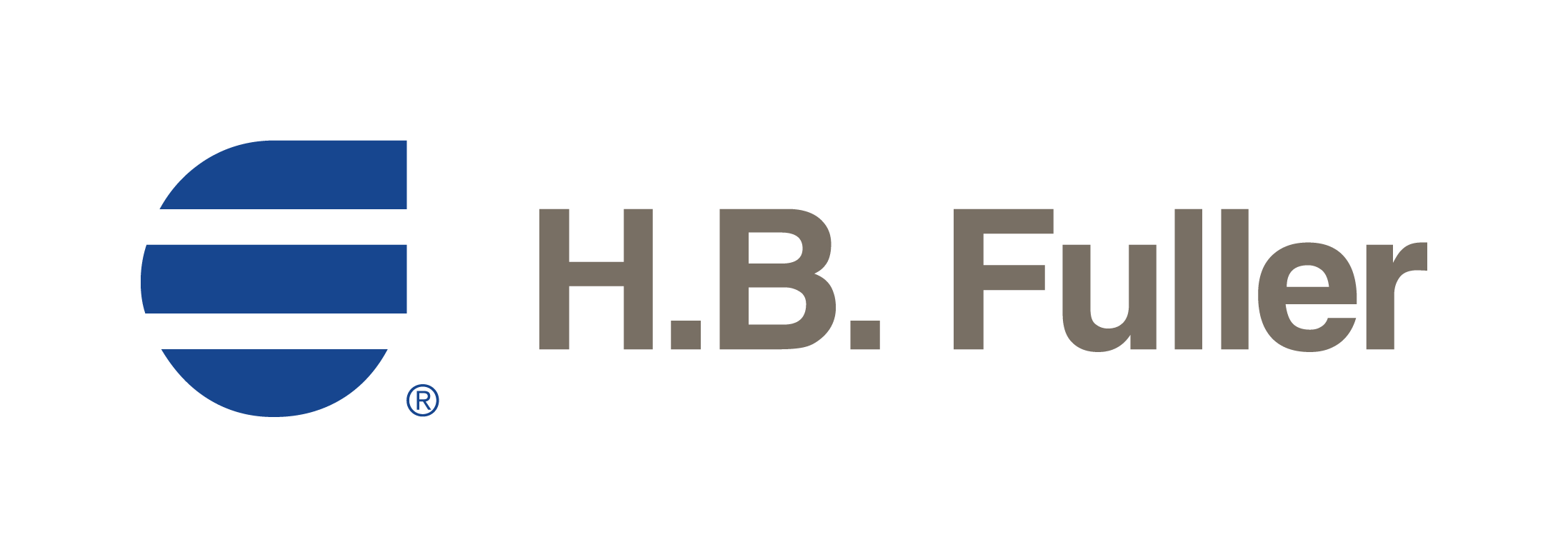
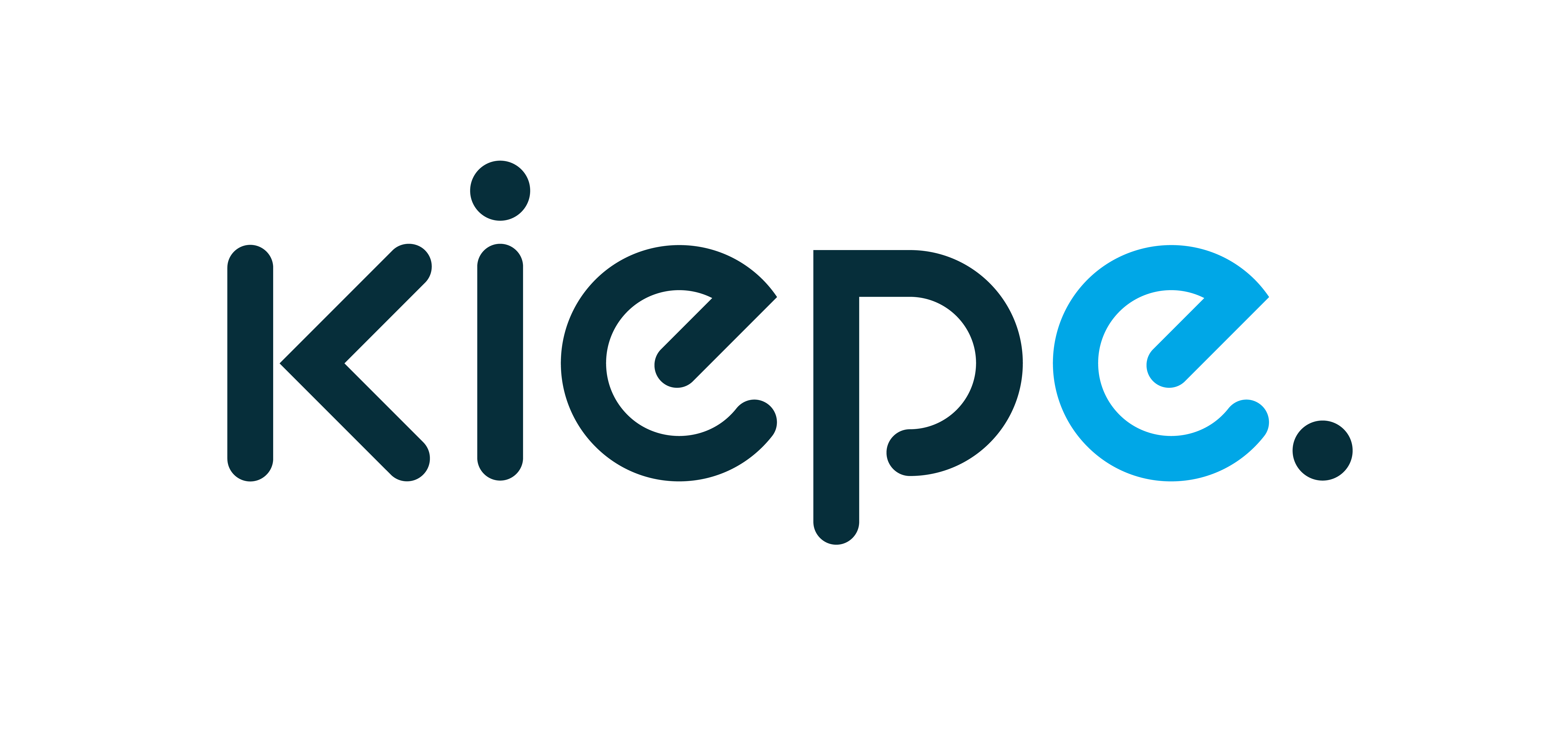
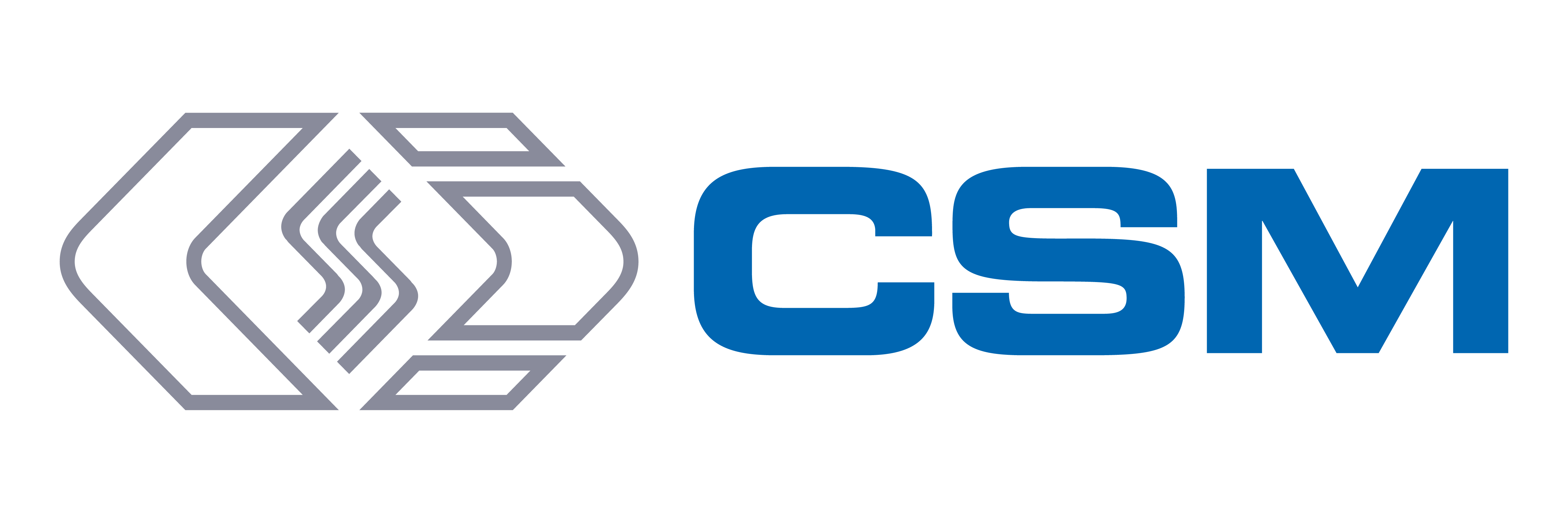