Polymer considerations for EV
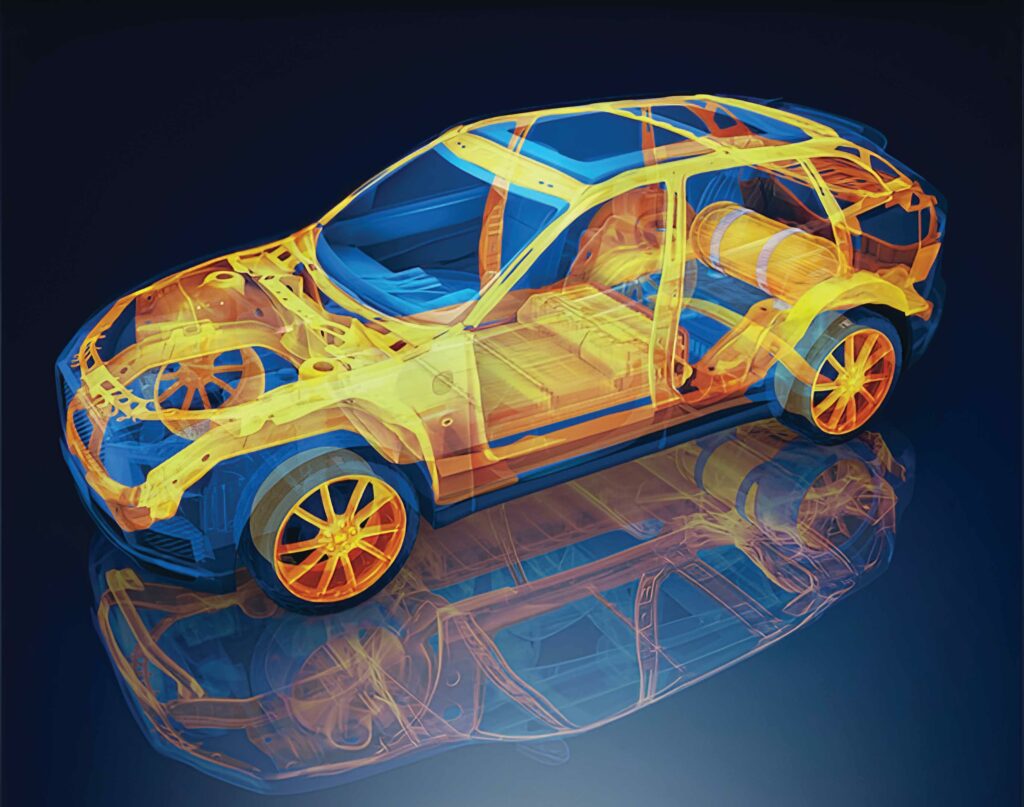
(Image courtesy of Modalt)
Plastic fantastic
Lightweight with higher temperature resistance, thermoplastics are ideal for e-mobility powertrains, Nick Flaherty reports
The push to make e-mobility designs lighter to boost range is driving significant innovation in materials. Thermoplastics are being redesigned to provide various combinations of temperature and flowability for manufacturing and plating capabilities.
The latest thermoplastic material can even be used in the hostile environments of the electric motor, replacing aramid papers and enamel coatings of the wires used in rotors. This is reducing the cost of building motors while increasing power density and performance. Alternatively, thermoplastics can be used to create smaller, lighter motors in lower-cost designs, which can even result in 3D-printed vehicles.
As voltages increase, thermoplastics are also being used more widely in charging systems, reducing their weight and cost. This is improving the durability and reliability of charging stations, which is a key challenge for the industry. The lighter materials also make it easier to ship and install charging stations, both for public use and at home.
Thermoplastics are one of the two main types of plastic, the other being thermosets. When heat is applied, thermoplastic materials become soft and malleable, and become hard again once cooled, making them suitable for injection moulding.
In general, the viscosity of thermoplastic melts is higher than for thermosets, but not necessarily for highly filled materials. This is key for e-mobility powertrain applications where the temperature issue is more important, particularly with higher-voltage 800 V and 1000 V designs.
However, there are limitations to using conventional thermosetting resins reinforced with carbon fibre (CFRP) because of the slow manufacturing speed, high price and low recyclability.
As a result, thermoplastics such as polypropylene (PP) and polyethylene terephthalate (PET) have been used as a matrix, considering their cost-effectiveness, formability and recyclability. Among the thermoplastic polymers for the CFRP composite, PP is one of the most widely used thermoplastics in the industrial field, and it has the advantage of being particularly excellent in terms of shock absorption for e-mobility designs.
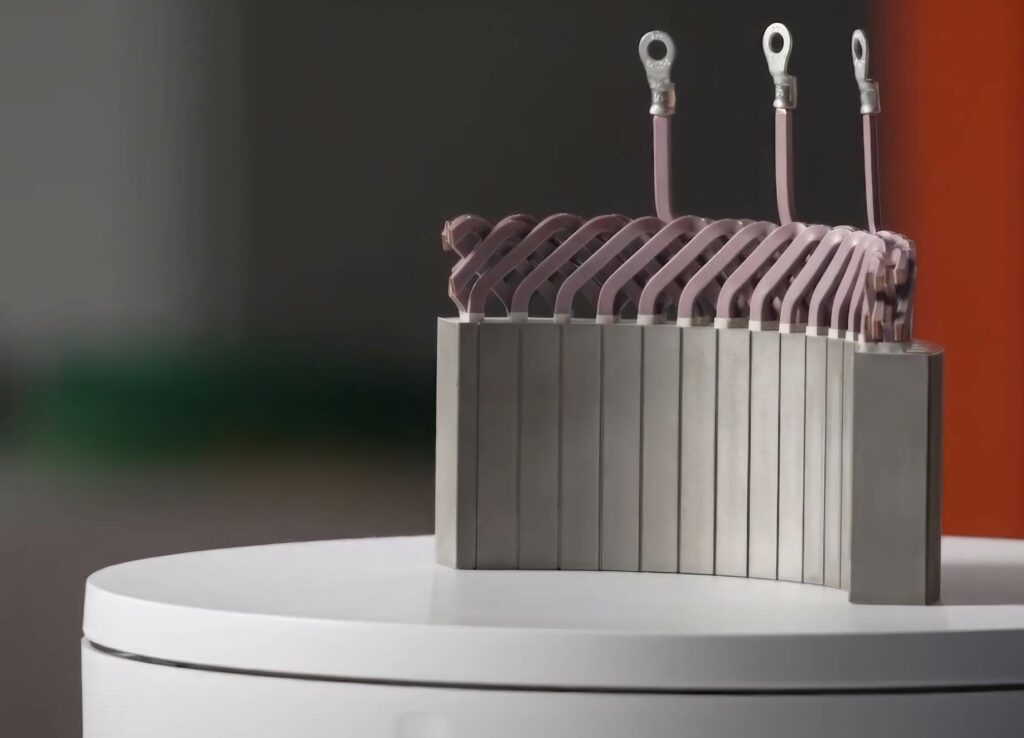
(Image courtesy of Syensqo)
Motor designs
Thermoplastic materials are also being repurposed from internal combustion engines (ICE). One material was found to have very good insulation properties, especially on magnet wire; a characteristic that turns out to be key for e-motor designs. The material developer worked with a magnet wire supplier to start producing thermoplastics that could be extruded onto magnet wire, rather than using enamels.
The material was designed to be extruded directly onto the copper wire in one pass on a pre-formed winding without the need for additional materials or processing to improve adhesion. Removing these steps will help reduce process complexity, and therefore manufacturing costs.
The pre-formed windings for a 400 V motor typically have a coating of
40-70 microns (μm), but they require 100-170 μm for 800 V, and this is very difficult with enamel as it requires several passes with more curing cycles, which can create problems for the inner layers.
This requires a careful balance of electrical and thermal performance, and the thickness of the thermoplastic can be tuned from a few microns to several hundred microns. A 125 μm coating has a 13.4 kV breakdown voltage, so it can be used up to 1200 V.
This is especially valuable for motors that run at 800 V. Cutting the thickness of the covering from 125 μm to 50 μm increases the power density by 10%, boosting efficiency by 2% at the same temperature. The thinner coating gives a higher bending radius to fit more coils into the motor for greater power. This, however, has higher thermal requirements as the higher-power motor generates more heat, so the material can operate safely up to 250 C.
Thermoplastics are also used for slot-liner insulation in rotors to replace aramid papers, which have to be inserted into the motor.
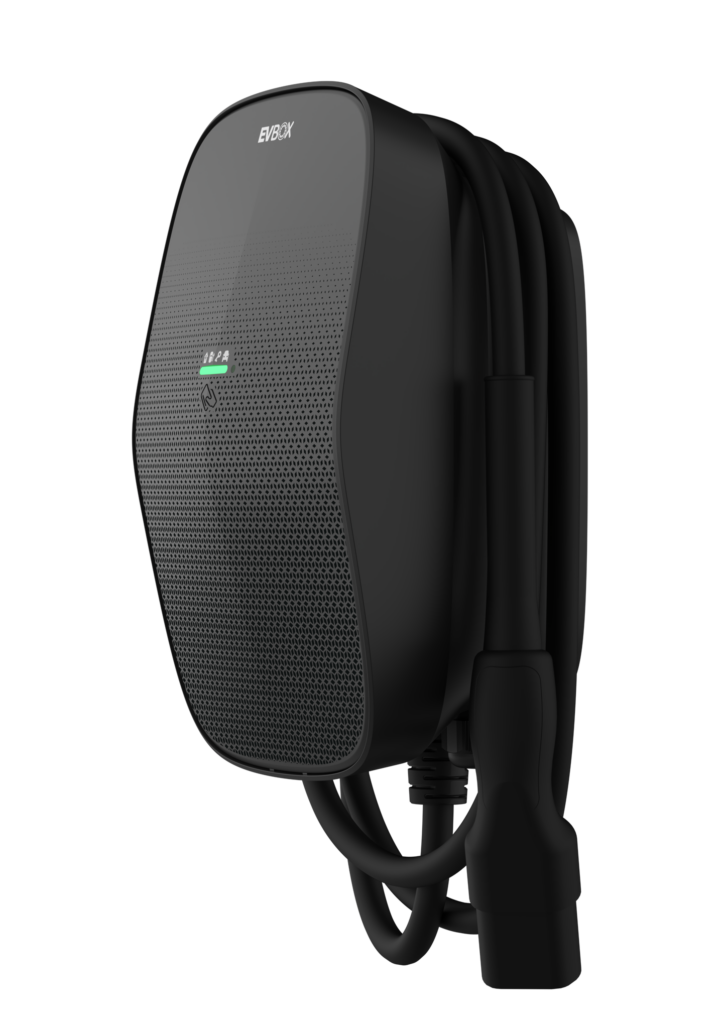
(Image courtesy of Livo)
Rotor sleeve
Premium e-motors want higher rotation speeds for higher torque, and these traditionally use carbon fibre in epoxy as the rotor sleeve. Thermoplastic carbon-fibre tapes avoid a wet manufacturing process and can be directly wound onto the stator for high-volume production processes.
Thermoplastic materials boost the range and safety of EVs, especially where high-performance polycarbonate comes into play. Components made of polycarbonate are particularly lightweight and weigh up to 50% less than those made of glass. The lighter an EV is, the better it can compensate for the usually heavy weight of the batteries.
Polycarbonate also allows for seamless surfaces. This enhances aerodynamics, which then reduces energy consumption due to lower drag. This results in the battery being preserved and the range increased. Various concept vehicles have taken advantage of this material to change the way components are designed and manufactured.
Charging stations
Using thermoplastics rather than metal in charging stations brings several advantages. At any given time, 20-25% of the world’s charging stations are not operational, partly as a result of wear and tear, and inclement weather putting a severe strain on plastic parts, such as plugs and sockets.
As well as thermal resistance, insulation and mechanical-performance retention across a range of weather conditions, the plastics used for
EV-charging infrastructure need multiple qualities to withstand the test of countless use cycles (plug-unplug), plus humidity, cold and sunlight due to being outdoors all year round, and even accidental car runovers on the plugs.
In many cases, standard-grade polyamides and polycarbonates are starting to show their limits. There is demand for higher-performance thermoplastics to meet requirements while making the charging stations lighter, stronger and easier to repair.
Plastic structures must be shielded, particularly with higher-power, fast chargers. With large currents flowing for charging up to 450 kW, the chargers must meet electromagnetic interference regulations (EMI), meaning the units must be shielded so they do not interfere with other nearby electrical equipment.
All of this must be achieved while also ensuring the thermoplastics can be recycled to meet tightening regulations, particularly in Europe, which will eventually make it mandatory to include a proportion of recycled content in all types of infrastructure.
The latest high-performance polyamide materials have recycled grades, while offering optimal resistance to humidity and long-lasting mechanical resistance, particularly for fast-charging plug connectors. This could increase the number of charging cycles they are capable of withstanding, so wear resistance is definitely a valuable property of the material.
The thermoplastic materials for charging units are being tested with equipment makers, starting with plug connectors, but this is in the early stages.
This protective function is also important for home charging units. This is another case for polycarbonates with robustness, corrosion resistance, electrical insulation and fire resistance. Importantly, the plastic can be produced in a highly environmentally-compatible manner for lower carbon emissions. It has been used for the first wall box made of the material that is climate-neutral from cradle to factory gate.
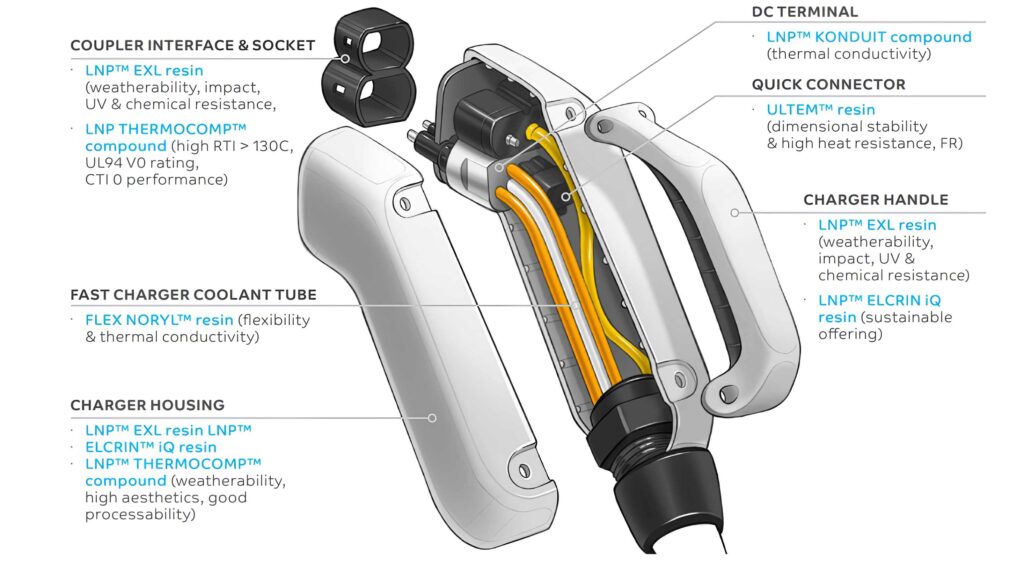
(Image courtesy of SABIC)
Materials research
A European project is developing a high-temperature thermoplastic for electric aircraft. The aerospace sector typically uses lightweight, high-performance, thermosetting plastic composites, also known as epoxy resin-based composites, in many applications, but these materials are not as heat-resistant as other metal aircraft components.
Components made from a thermoplastic base have been shown to be more efficient, from the perspective of their thermal properties, than thermosetting composites. A known property that makes them very useful is that they can be recast, reshaped, processed and recycled without the need for any additional curing process in order to harden and set.
They are more versatile, cheaper and eco-friendly than conventional thermosetting composites, and they have a longer service life, thanks to their higher resilience and fatigue resistance, and greater resistance to corrosion.
A test laboratory uses new infrared (IR) thermography techniques to obtain accurate and non-intrusive measurements of the actual temperature of materials during fire tests. The ultimate aim is to conduct virtual tests on thermoplastics and compare their performance in real applications with those of conventional thermosetting composites.
The project aims to establish a methodology that allows the characterisation of thermoplastics to improve the prediction of their behaviour and resistance when subjected to mechanical loads or fire and high temperatures.
The measurements obtained by infrared thermography allow computer simulations to be carried out, which virtualise testing to select this type of material in the aeronautical industry. This can significantly reduce the number of validation tests.
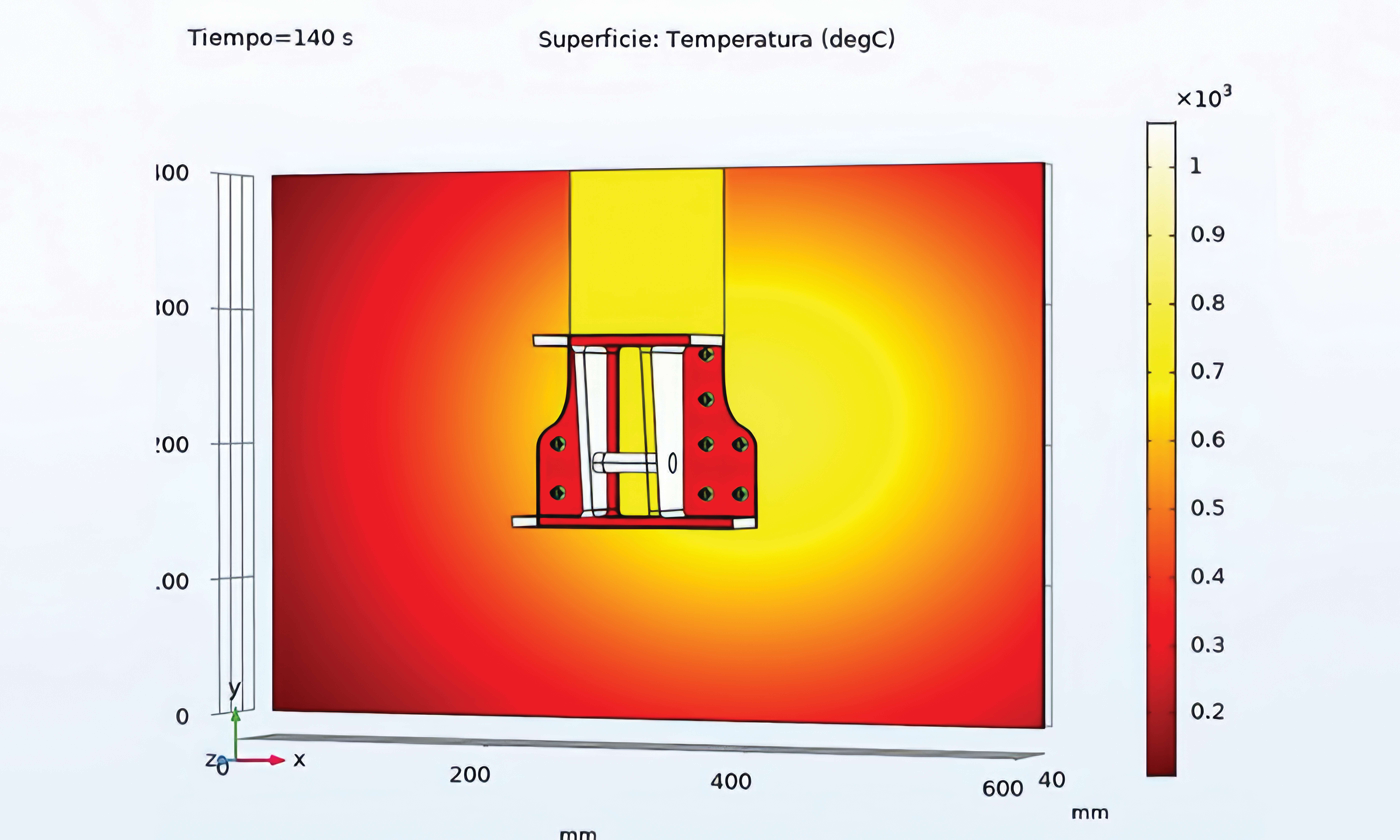
(Image courtesy of Carlos III University)
Biodegradability
A team of researchers has developed a plastic that has similar thermoplastic properties to polyethylene but is also biodegradable. The material is a semicrystalline polyester, which breaks down fully to its starting materials using mild chemical or biological processes.
High-density polyethylene (HDPE) is particularly strong and durable. It owes its thermoplastic properties to the internal structure of its molecular chains, which are arranged in a crystalline manner with added attraction due to van der Waals forces.
The molecular chains are also pure hydrocarbons. The combination of crystallinity and hydrocarbon content means that microorganisms, which might be able to degrade the plastic, cannot access the chains to break them up.
The polyester has similar crystallinity to HDPE and retains its mechanical properties, but unlike polyethylene it also contains functional groups that could theoretically be degraded chemically or enzymatically. However, under normal circumstances, the more crystalline a polyester is (i.e. the more similar to HDPE), the less readily it can be biodegraded.
Adding ethylene glycol, one of the building blocks of polyester, gives a high melting point, but it also increases degradability in these polyethylene-like materials.
The end goal is closed-loop chemical recycling in a process that breaks the plastic down into its raw materials and produces new plastics. The added benefit of this approach is that, if any materials do get into the environment despite this closed loop, they can biodegrade without any lasting impact.
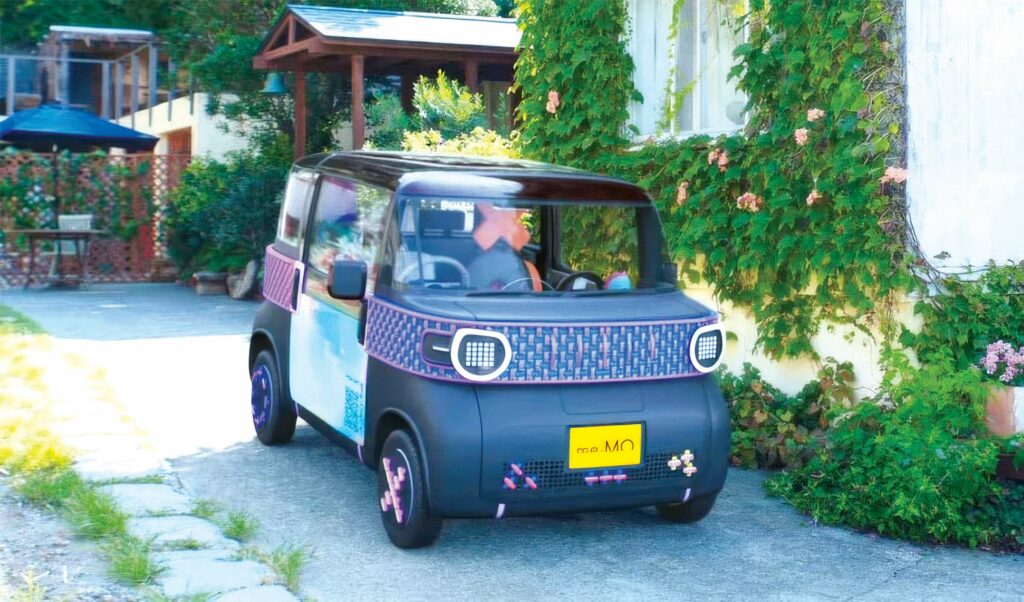
(Image courtesy of Daihatsu)
3D printing
Thermoplastics are changing the options with additive manufacturing, or 3D printing. The latest high-performance, polyamide-based composite reinforced with carbon fibre has a density of 0.87 g/cc (grams per cubic centimetre), particularly for lightweight electric aircraft designs.
This is used with powder-bed fusion or selective laser sintering (SLS), where a high-power laser heats the granules to create functional prototypes and components with a balance of lightness, stiffness and thermal resistance.
The heat deflection temperature (HDT) is a critical property for 3D-printing materials, especially when using fused deposition modelling (FDM). It is an important consideration because the material is heated and melted to create a 3D object, and the HDT of 1.82 megapascals (MPa) of 182.5 C for the polyamide material provides high values of specific tensile and impact strength.
The post-process surface finish is key for smoothness for aerodynamics. The surface roughness (Ra value) is 5.44 µm after the SLS process, 1.56 µm after manual finishing, and 0.83 µm after CNC processing, ensuring smooth and precise surfaces.
3D-printing thermoplastics are also being used for the load-bearing frame of an electric cargo scooter with a new technique.
SEAM (screw extrusion additive manufacturing) technology was used to produce the shelf and frame. A custom 3D-printing process is eight times faster than conventional methods, but it also processes cost-effective, standard plastic granules. Compared with conventional fused-layer modelling (FLM) processes, which use expensive filaments, production costs are up to 200 times lower.
SEAM technology was used to manufacture the shelf and frame construction of the scooter. The printing process is carried out by drawing plastic granules into the extruder using a modified extrusion screw and plasticising them. A material output of up to 10 kg per hour can be achieved, and the resulting plastic melt is deposited in layers on the construction platform. The continuous storage process makes it possible to produce large-volume, resilient components. The granules can be obtained from recycled thermoplastics.
A concept e-vehicle has also been developed with 3D-printed thermoplastics to explore new designs and construction techniques. The materials and 3D printing changed the way the cars were manufactured, and made it possible to change not only the design but also the form of the vehicle by constructing a modular structure of interior and exterior parts.
The design has an external battery pack, which expands the range of platform options to include a mobile shop, a truck, a flat cabin/luggage space that is easy to use and clean, and removable interior and exterior parts.
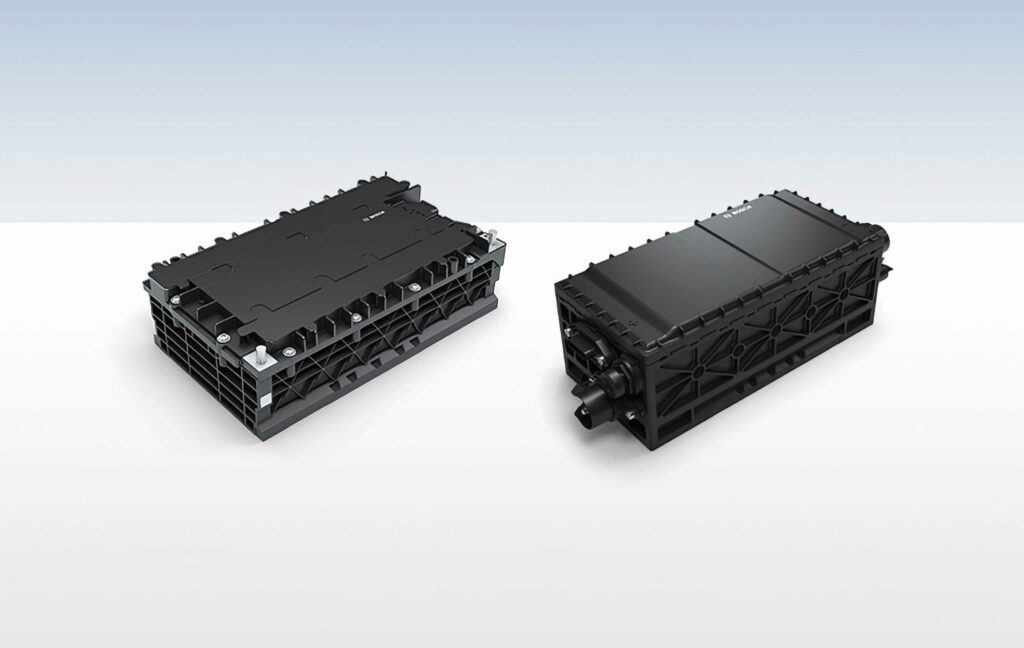
(Image courtesy of Bosch)
Coatings and acoustics
As well as the structural and light weight requirements, the ability to apply various coatings to the thermoplastic is vital for several reasons. While the EMI shielding is, of course, a major requirement, so are the vehicle acoustics.
For a vehicle’s occupants, the focus is on noise reduction. While outside the vehicle, the focus is on safety, because e-vehicles do not produce the same noise as a combustion engine, but inside, the focus switches to the acoustics of the electric drivetrain and operating noise.
To cut vibration noise, there are several dry-lubricating, bonded coatings in the form of polymer systems based on PTFE, PFA or FEP fluoropolymers, as well as MoS2 or graphite.
This helps reduce the contact noises caused by vibration by using flock coating, with cathodic dip coating (KTL) as the base layer. Further advantages of the pure flock coating are the compensation of manufacturing tolerances, and noise insulation on metal and plastic surfaces.
However, when using 48 V, the operating temperature of fasteners rises to over 160 C, meaning that for safe operation, silver coatings in thicker layers must be deposited on the components.
A professional coating is also crucial for the safe operation of large vehicle batteries, because efficient protective devices, such as corrosion-protected housings, can only be created with high-quality surface technology.
The transmission of high-frequency signals in the vehicle is often overlooked and the coatings of various components can reduce the impact of interference sources. A multi-layer structure allows static charges to be selectively dissipated and signal transmission interference to be reduced, while also providing electrical insulation.
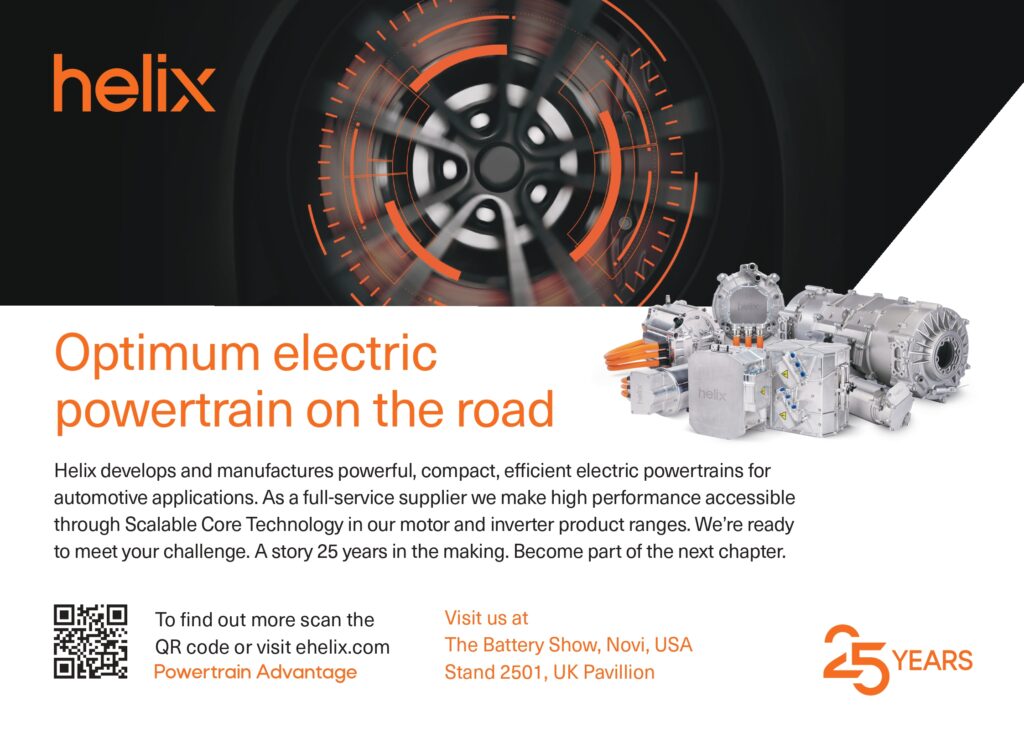
Fire protection
Most engineering plastics meet fire requirements at thicknesses of 1 mm. However, the rising number of electrical components with a high-power output is increasing demand for flame-retardant thermoplastics.
With the popularity of electric cars and the potential danger of thermal runaways, the automotive industry headed towards different standards that were mainly designed for stationary applications. Those standards are mainly described in the Underwriters Laboratories Standards UL 94 and UL 746 (see Standardisation and ratings).
The intention of applying these standards is to prevent an electric malfunction causing a fire from parts in the vicinity of the battery cells. With appropriate materials in place that are resistant to short-time ignition sources, the outbreak of a battery cell fire triggered by external malfunctions is less likely. The sources of ignition are typically high current arcs, hot wires and fusing transistors or capacitors.
Flame-retardant plastics are useful in the following e-mobility applications: in the vicinity of sensitive materials, such as battery cells, to prevent thermal runaways; components with a high potential for ignition due to nearby electric currents, such as breakers and switches; and in EV charging cables (cable sheathings) for increased safety and the prevention of fire propagation.
Overload, improper use, and manufacturing and assembly errors, such as defective soldered points or loose connections, all constitute real fire hazards. The aim of technical fire safety in the eventuality of a malfunction is to prevent the ignition of the component and stop flames spreading to the immediate surroundings.
In certain cases, an additional requirement exists that the housing must not catch fire if exposed to an external source of ignition. The technical fire-safety requirements are described in special safety regulations for electrically operated devices and installations. The measures required are meant to ensure the safety objective is achieved. This includes measures of a structural nature, such as the limitation of temperature in case of malfunction or the use of materials with a low level of ignitability and flame spread.
48 V hybrid
The design of the battery pack for 48 V hybrids is key, and thermoplastics are vital here. The battery is small and cost-effective due to passive cooling. The challenge of a plastic-encased battery is to handle the load while cells expand over the life of the battery. This is achieved through a unique arrangement of the cells within the housing that incorporates passive cooling.
For example, a 14 kW hybrid 48 V battery with a nominal energy of 360 Wh weighs under 6 kg and measures 300 x 175 x 90 mm. The coming generation of vehicles will rely heavily on 48 V systems. This is because a higher voltage is required to generate the power necessary to supply the processors that control highly automated systems. The 90 mm height means the pack can be stowed away in the trunk or under the passenger seat.
The cells operate at up to 75 C, and so require a less complex cooling method and can use passive heat sinks. However, this needs a class of plastic with a higher temperature performance.
The thermoplastic not only cuts costs and size compared with aluminium, but it can also be moulded into smooth, complex forms through injection moulding. The smooth surface finish helps with air flow throughout the platform, and it is simpler and more cost-effective to assemble than aluminium units.
The use of plastics for battery pack casing is addressed in detail in EME 19 (May/June 2023), but several research projects are looking at how to achieve important properties such as electromagnetic shielding and fire resistance in thermoplastics. Reinforcing the material with long fibres enables the production of high-stiffness materials without compromising impact resistance.
This is being used for a battery module that will be designed and validated in the laboratory through experimental electrical, mechanical and thermal tests, simulating various driving cycles. It is aimed at electric ground and air vehicles with high-temperature requirements.
Thermoplastic composites with carbon fibres and PET have also been used for an underbody shield to protect the lithium-ion batteries from ground impacts.
The underbody shield (UBS) is composed of two parts: the main shield plate and the collision protection bar (CPB). Mechanical behaviour against impact was assessed using finite element analysis, considering the position of the CPB and the shape of the underbody shield plate, and where an impact is likely to occur as a vehicle travels along a road.
For the UBS, the hybrid composite of carbon fibre (CF)/PET and
self-reinforced polypropylene (SRPP) were used, and the ratio between the CF/PET and SRPP was optimised. Through finite element analysis, the optimal underbody shield was designed with a thickness of 2.4 mm and a hybrid ratio of CF/PET:SRPP as 1:2.
Finally, the UBS was manufactured using a thermo-forming process and mounted to an electric vehicle, and then a crash test was performed against a concrete obstacle. The developed underbody shield was able to successfully protect the battery against impact damage, showing the deformation of a rear part was within 5 mm and no battery leakage occurred.
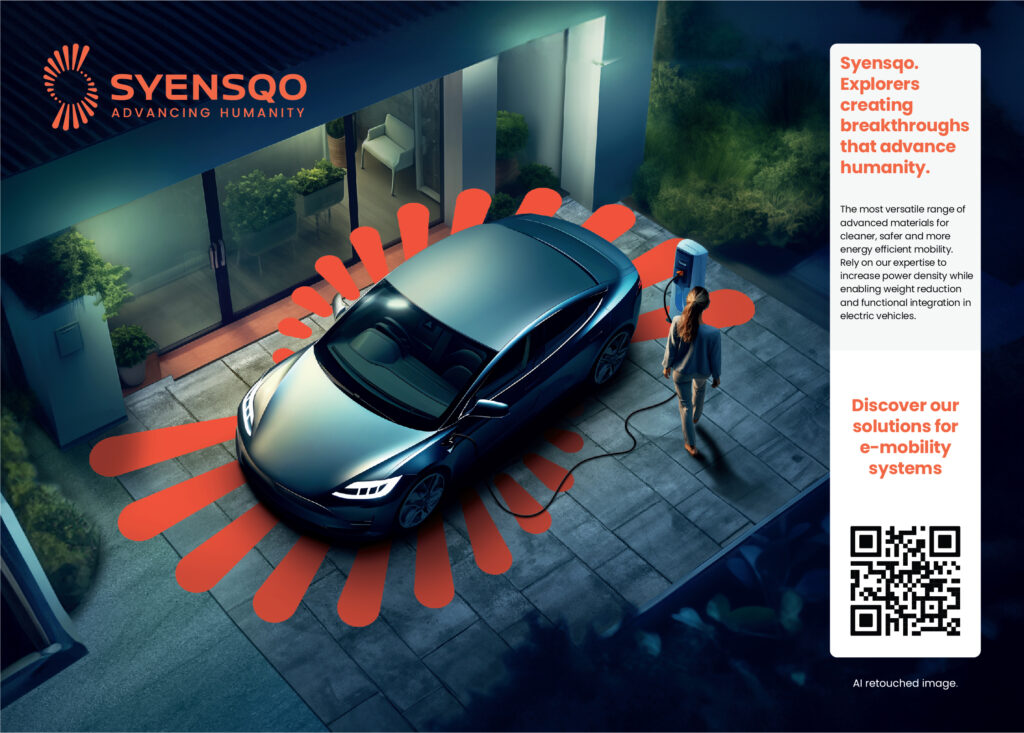
A world of opportunity
The move from thermoset to thermoplastic materials is opening up new design opportunities across e-mobility with a huge range of materials. Selection is dependent on the exact requirements of the component, from tensile strength to temperature stability and coating capabilities.
While thermoplastics can be reinforced with long and short carbon fibres to boost the tensile strength for applications such as battery packs and body protection panels, the materials are also being used in the powertrain of electric platforms.
The ductility of the material means that certain thermoplastics can be used to replace the enamel around stator wires in a motor, improving power density and lowering overall weight, while also reducing the number of assembly steps.
Thermoplastics are also being used for 3D printing in additive manufacturing. Prototype components can be developed quickly that have similar properties to the final design, which is particularly vital for light testing of electric aircraft.
Acknowledgements
With thanks to Simone Bottegal at Syensqo, Constantin Schwecke at Covestro and Fernando López at the Carlos III University of Madrid for their help in the preparation of this article.
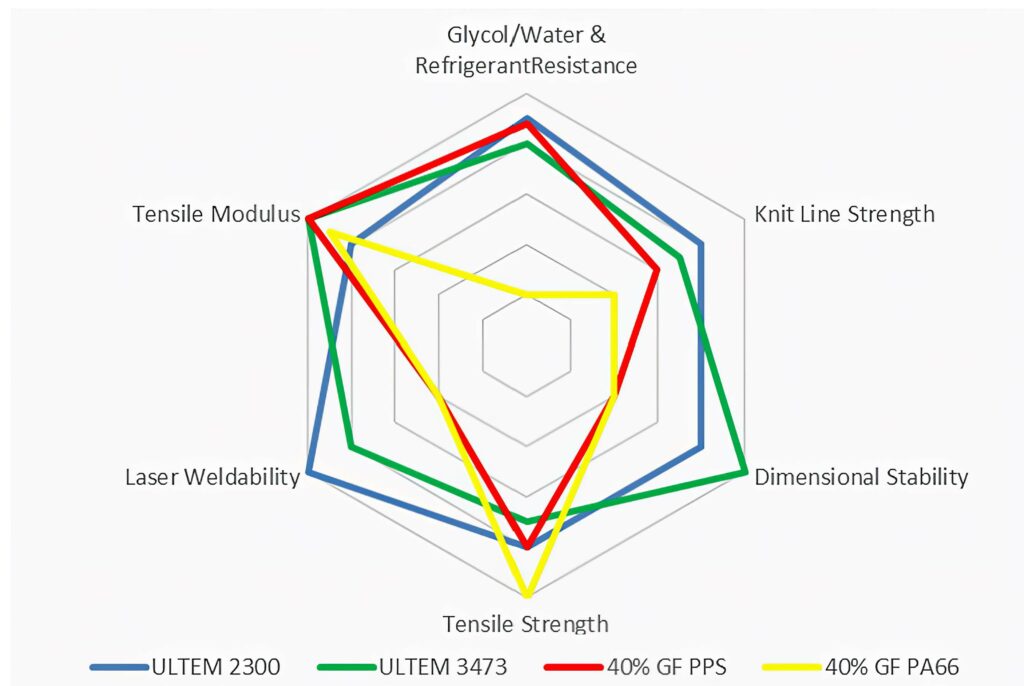
Thermoplastic types
Thermoplastics are the most commonly used type of plastic, with the top three being polyethylene (including high-density HDPE and low-density LLDPE/LDPE), polypropylene (PP), polyvinyl chloride (PVC) and polyethylene terephthalate (PET). Within each group are many different types of material, from solids to films, and many variants with differing properties.
Acrylonitrile butadiene styrene (ABS), among other specialist styrenic materials, is rigid, opaque, glossy and tough, with good low-temperature properties, good dimensional stability and low creep. ABS is easily electroplated, and sometimes parts require this for shielding purposes, for example.
Aramids PI aromatic polyamide is becoming an increasingly popular choice for e-mobility, particularly electric aircraft, due to its high strength, exceptional thermal and electrical properties up to 480 C, and resistance to ionising radiation.
PEEK (Polyether ether ketone) is a rigid, opaque (grey) material with a unique combination of properties, which include exceptional chemical, wear, electrical and temperature resistance, as well as dimensional stability and numerous processing capabilities. It is increasingly being used as a replacement for machined metals in a wide variety of high-performance end-use applications, ranging from components for cars and aircraft to the pumps, valves and seals in a powertrain.
Polycarbonates are strong, stiff, hard, tough and transparent engineering thermoplastics that can maintain rigidity up to 140 C and toughness down to -20 C, and special grades even lower.
Polyesters (thermoplastic) PETP, PBT and PET are engineered polymers that are used in the manufacture of a wide range of components, including under-bonnet parts and exterior parts such as window-wiper holders and exterior-mirror housings.
Polyetherimide (PEI) resins have long-term, high heat capability with dimensional stability from -40 C to 130 C for onboard chargers and DC-to-DC converters, as well as fast charger handles and connectors with inherent low flame, smoke and toxicity (FST).
Other amorphous, thermoplastic polyimides (TPI) have extreme high-temperature performance for aerospace applications, and they can withstand the higher temperatures required for lead-free, solder-reflow manufacturing processes for connectors.
Some suppliers of thermoplastic resins
Belgium
Germany
Japan
Saudi Arabia
The Netherlands
USA
Asahi Kaseo (USA office)
Ascend Performance Materials
Celanese
Nexeo Plastics
LyondellBasell
+1 713-315-5700
+1 713 315 5700
+1 972 443 4000
+1.833.303.0922
+1 713 309 7200
Click here to read the latest issue of E-Mobility Engineering.
ONLINE PARTNERS
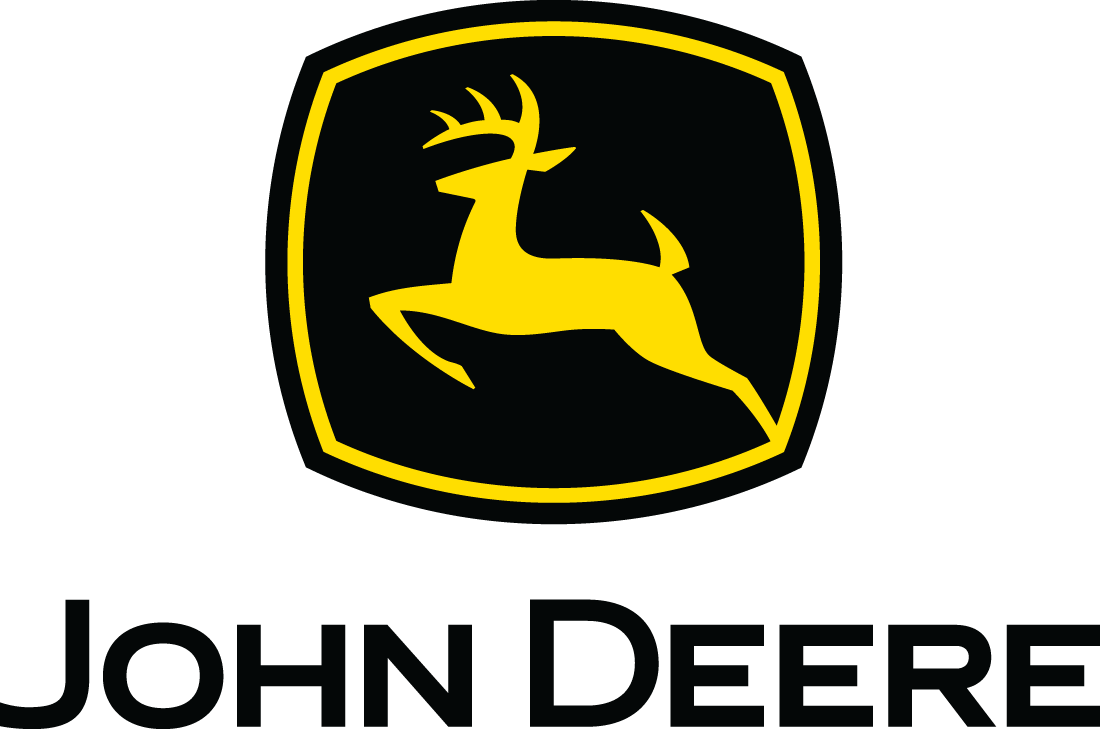
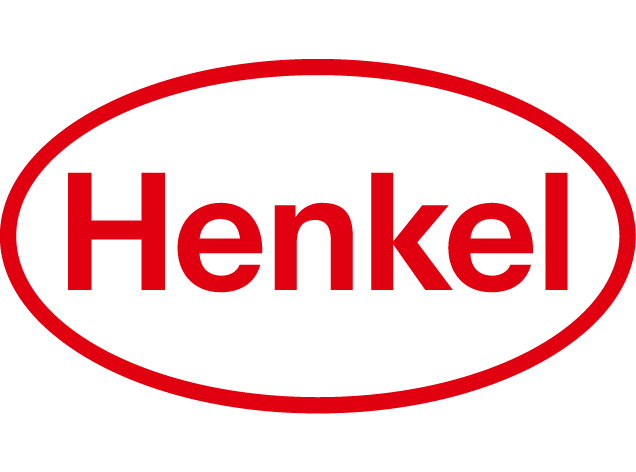
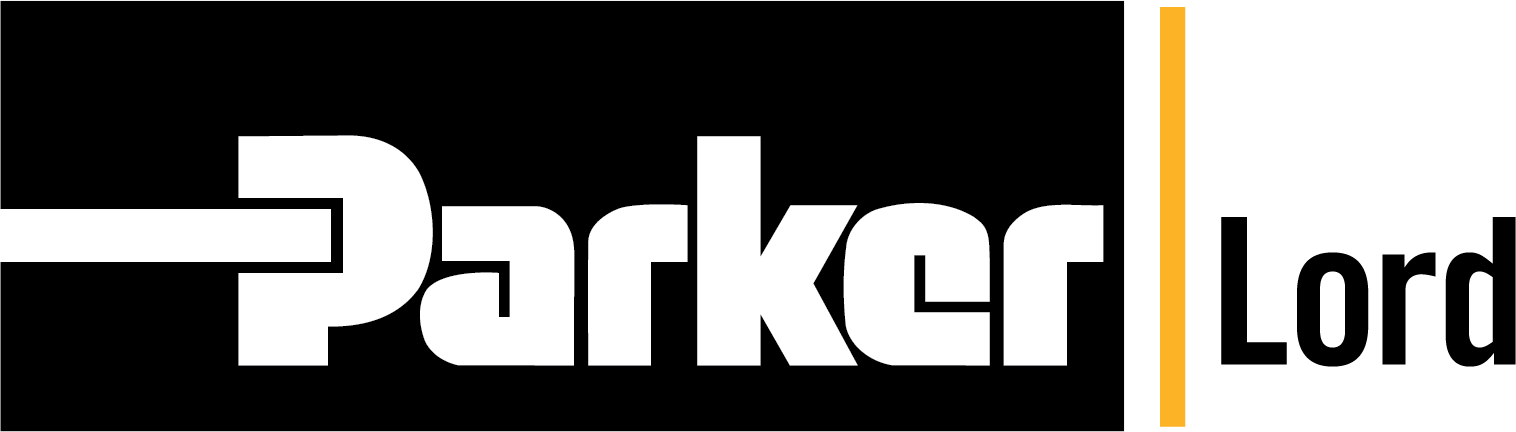
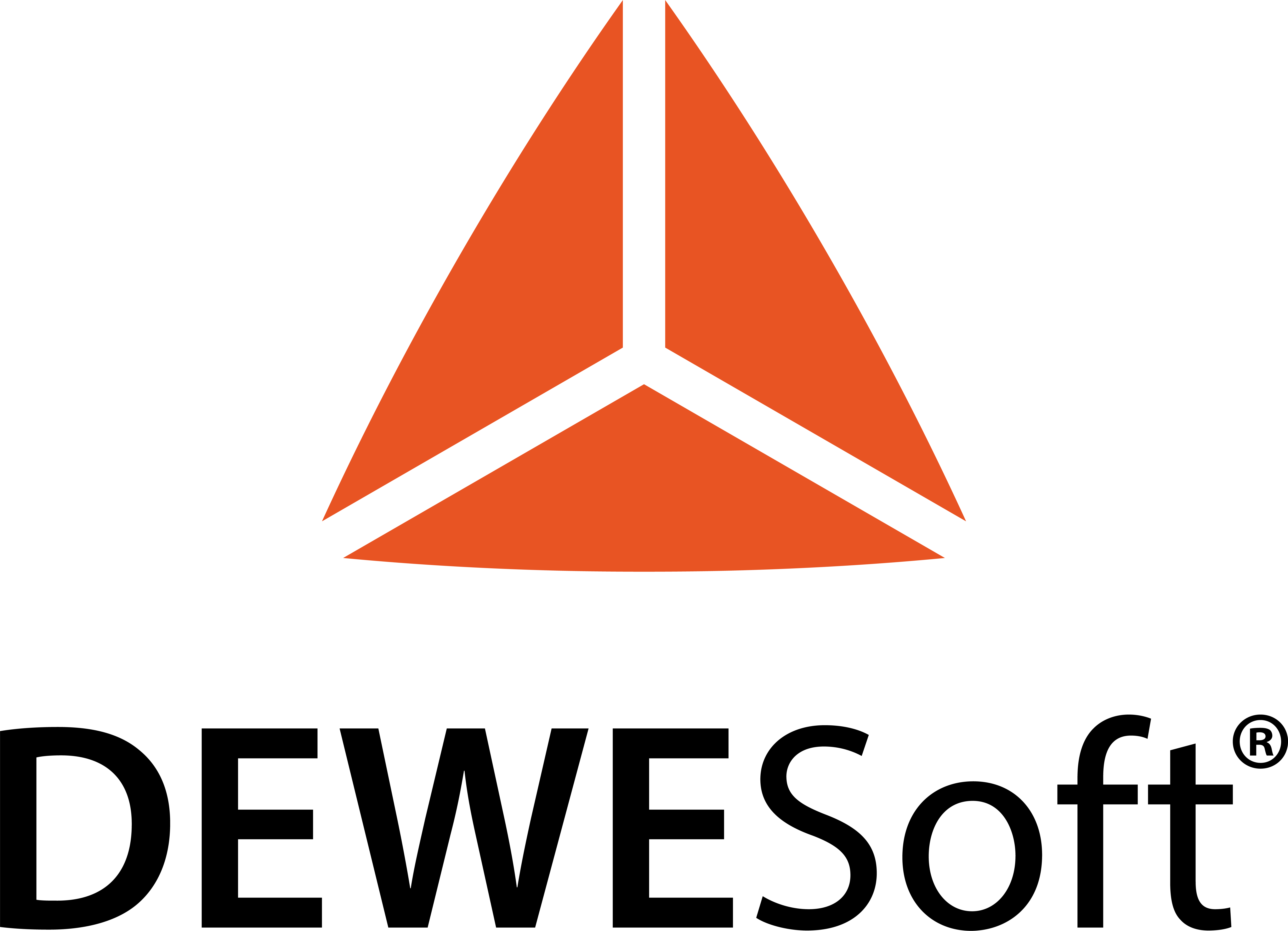
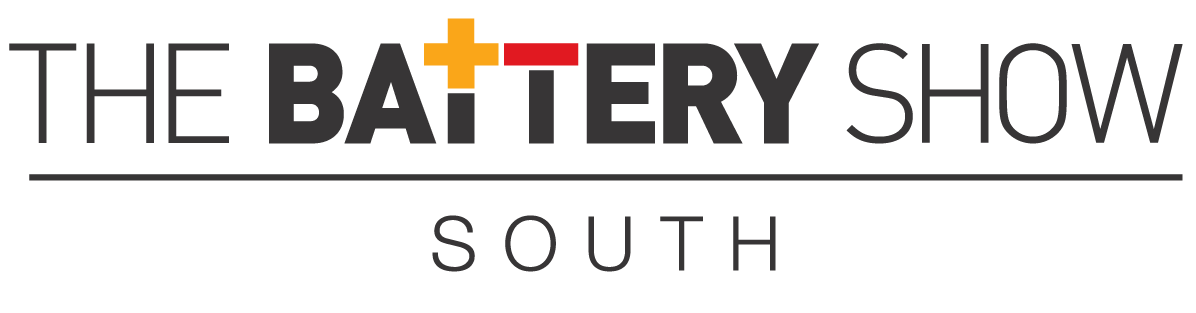
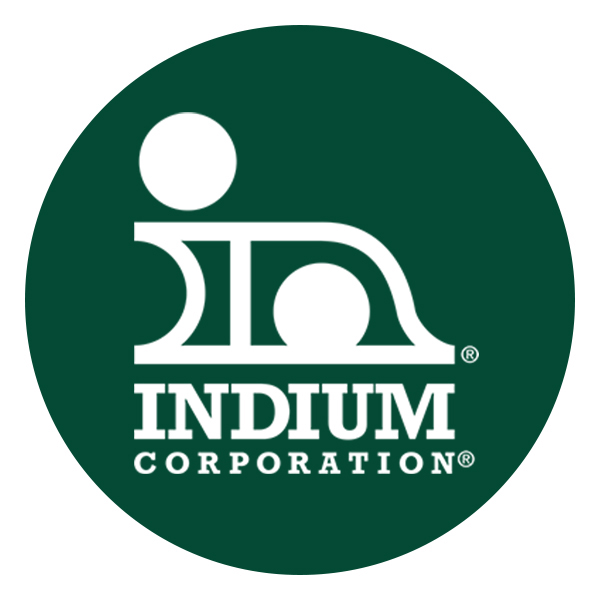
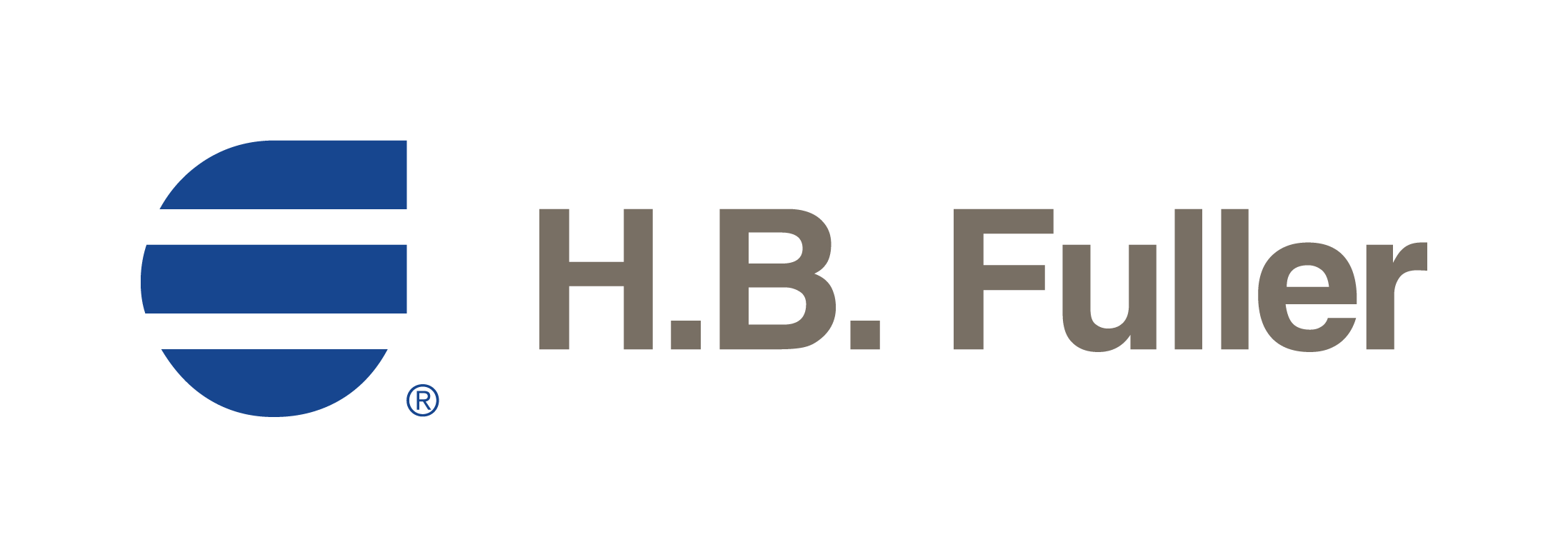