No contact with CAN monitor
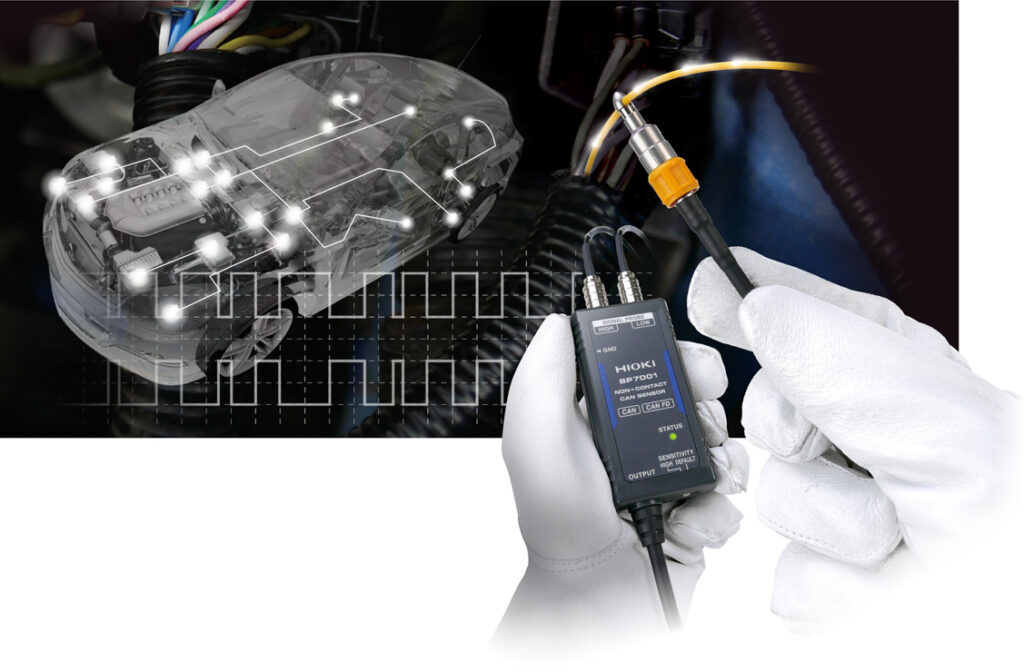
Hioki has extended its non-contact voltage test technology to allow developers to monitor CAN bus networks (writes Nick Flaherty).
The SP7001/7002 CAN sensors can detect the CAN fl exible data (CAN FD) rate that supports higher rates than the earlier CAN standard, as well as CAN frame signals from above the wiring insulation in EVs without any metallic contact.
That avoids engineers having to peel off part of the wiring insulation to directly probe or clip to the wiring, or attach a sub-harness to the cables to capture the signals on the CAN bus. These cables would need to be replaced.
The CAN sensors are based on a capacitive-coupled current cancellation technique used in the SP3001 voltage sensor, which relies on the cables being insulated rather than using bare metal wires. That makes it suitable for the CAN bus cables
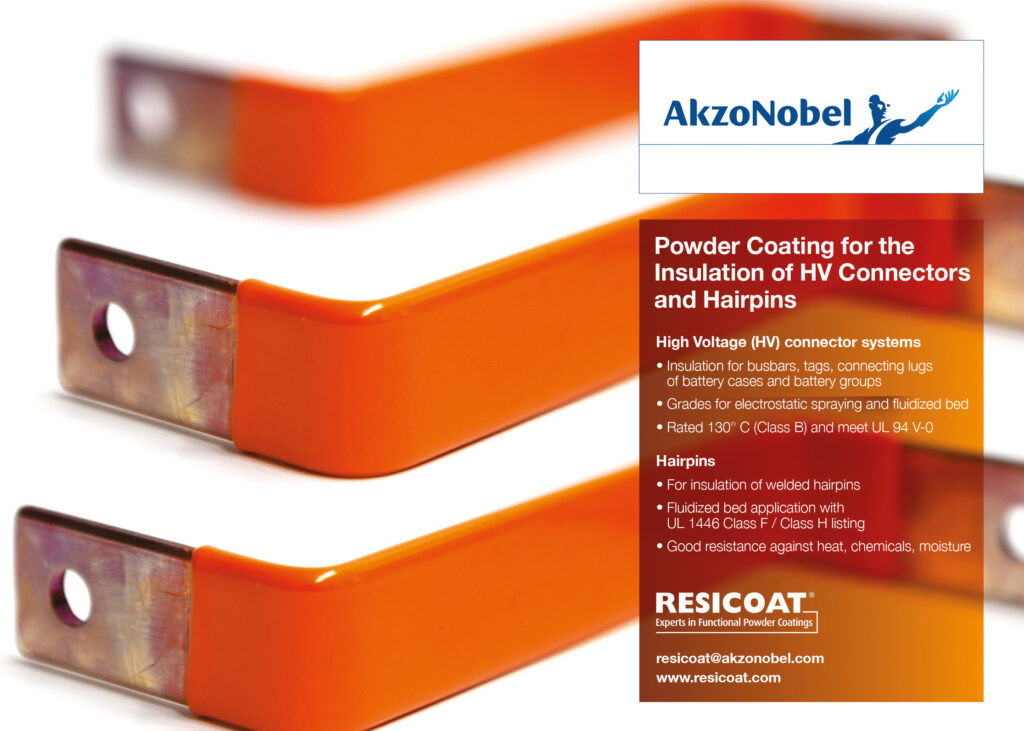
The SP7001 supports the CAN FD protocol, while the SP7002 works with the earlier CAN protocol. The non-invasive approach provides higher levels of accuracy, as the electrical characteristics of the CAN bus can be affected by direct probing, which can in turn affect the ECU’s operation. Some ECUs might shut down by design because of unexpected signals.
The CAN sensors can be connected to the industry-standard D-sub ninepin interface so that engineers can use the sensors with existing CAN FD/CAN analysis systems.
Both sensors are scheduled for release shortly.
ONLINE PARTNERS
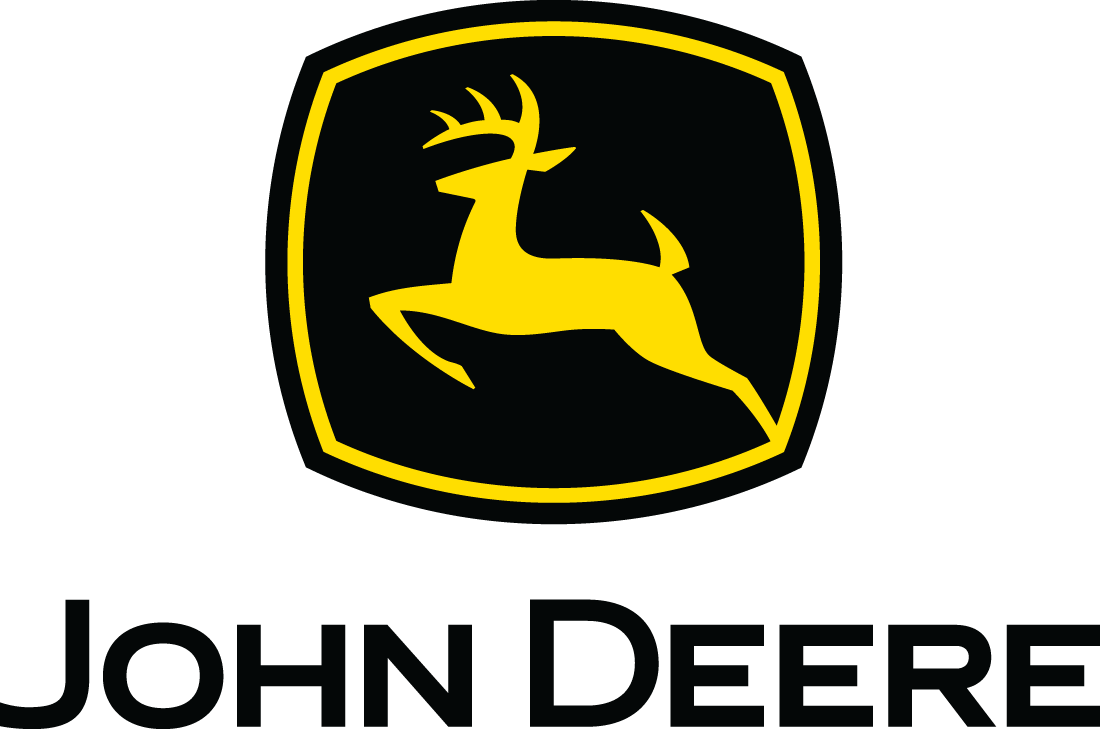
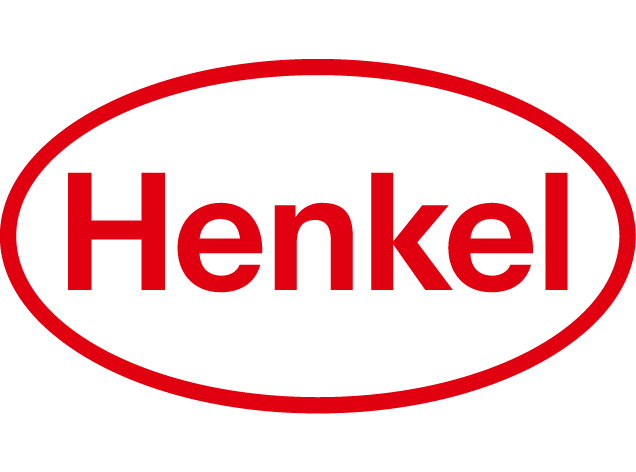
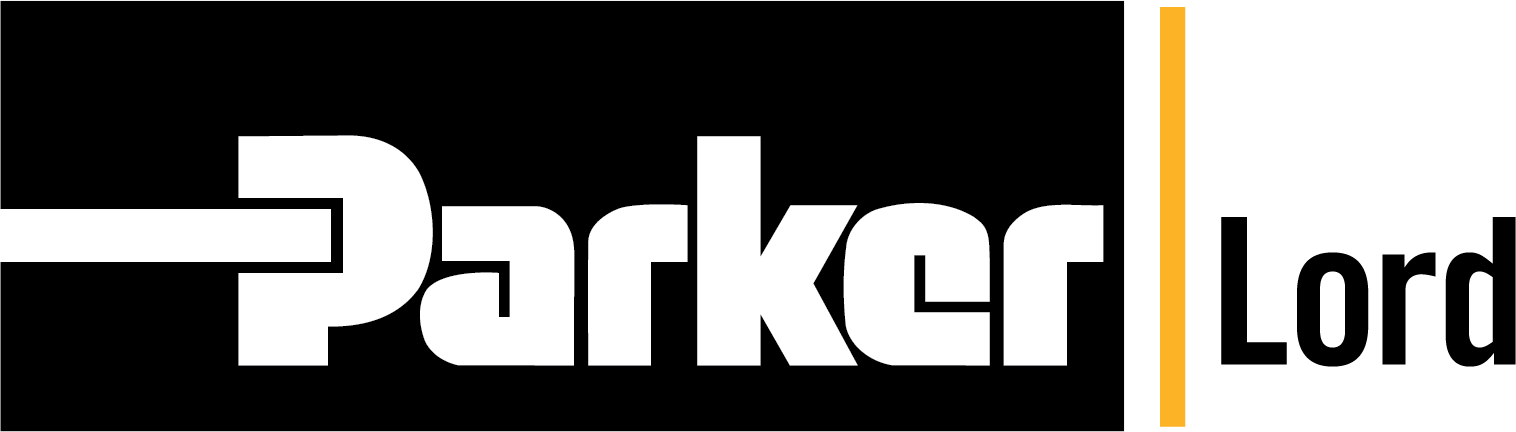
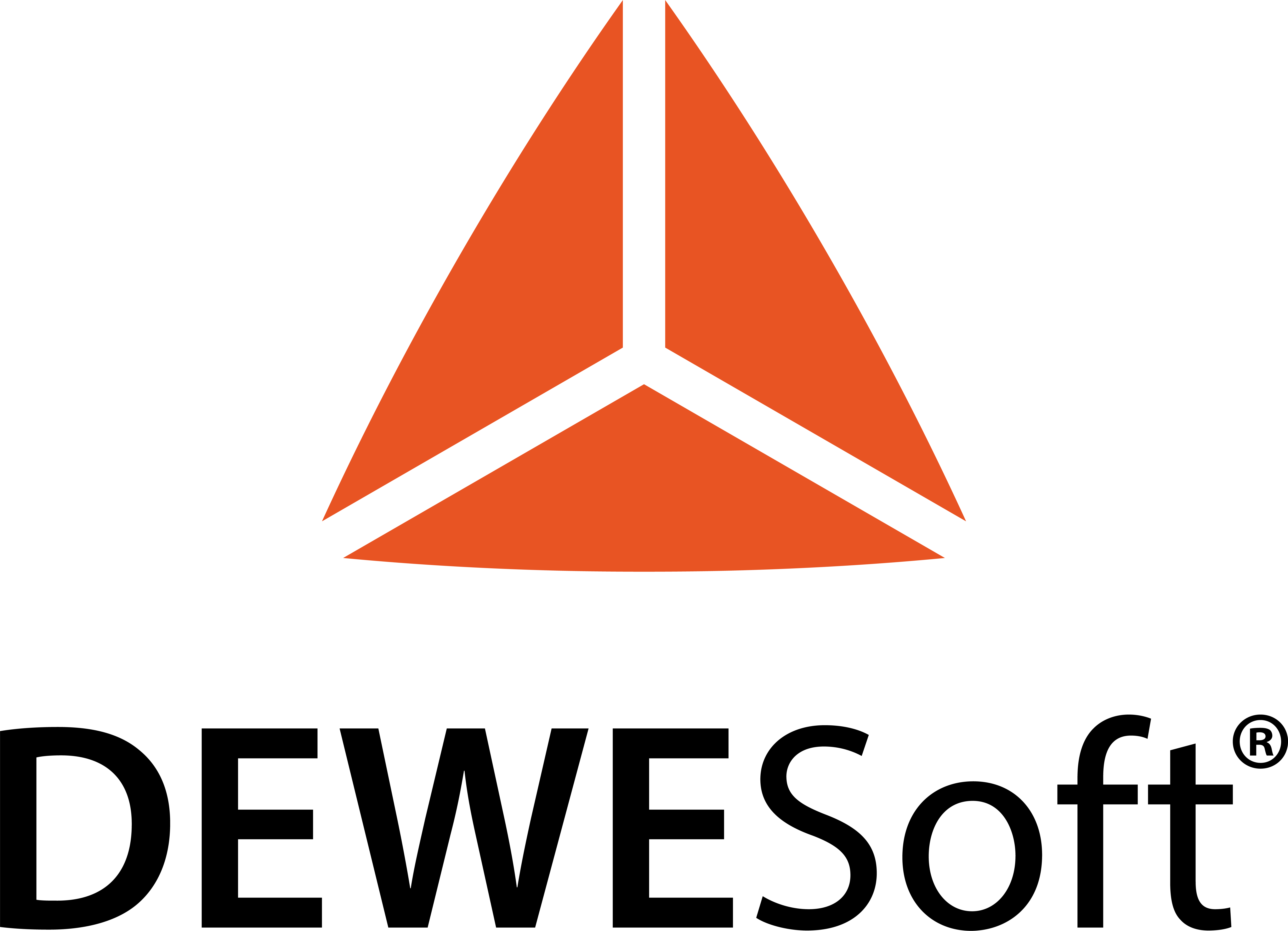
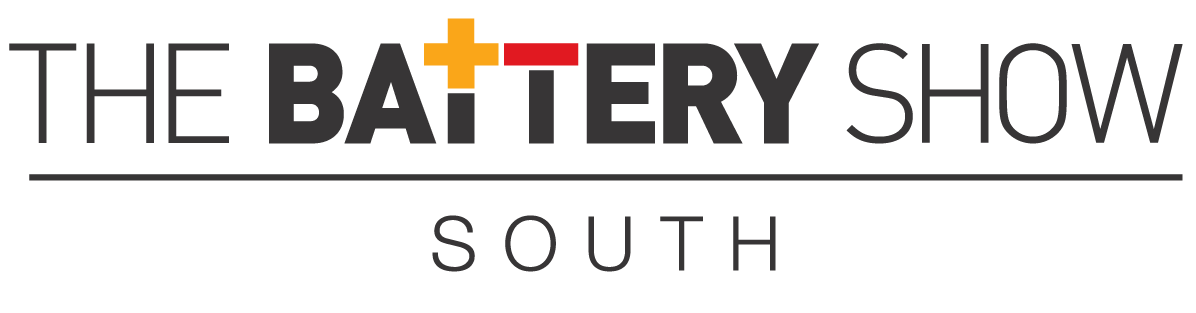
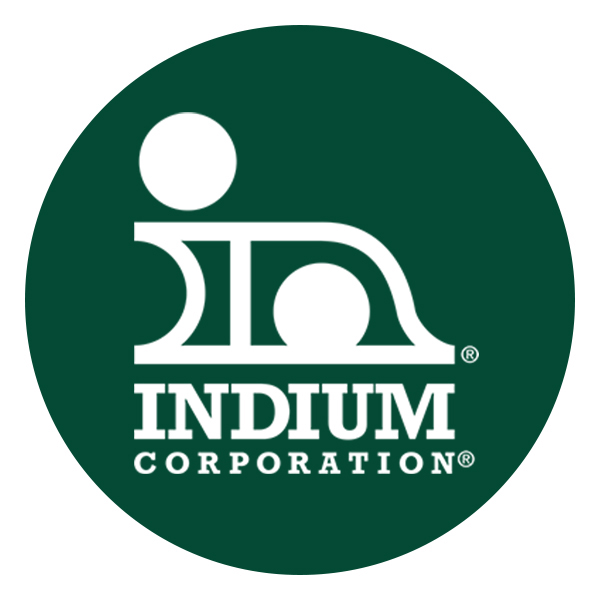

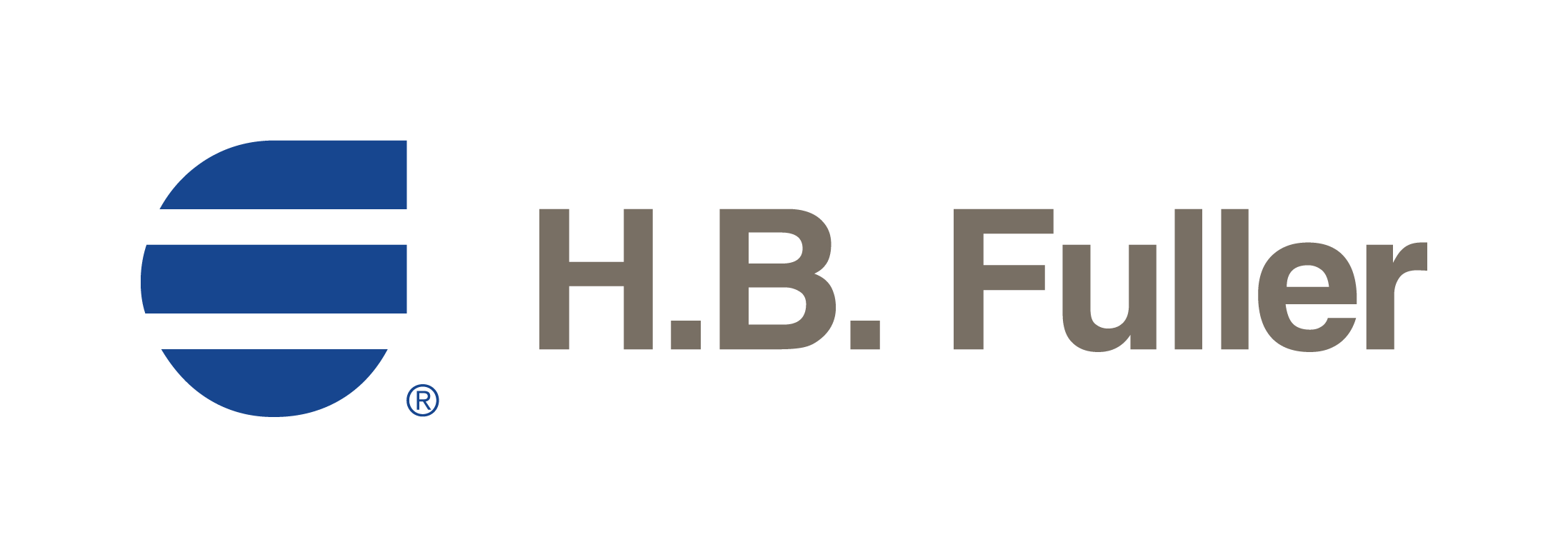
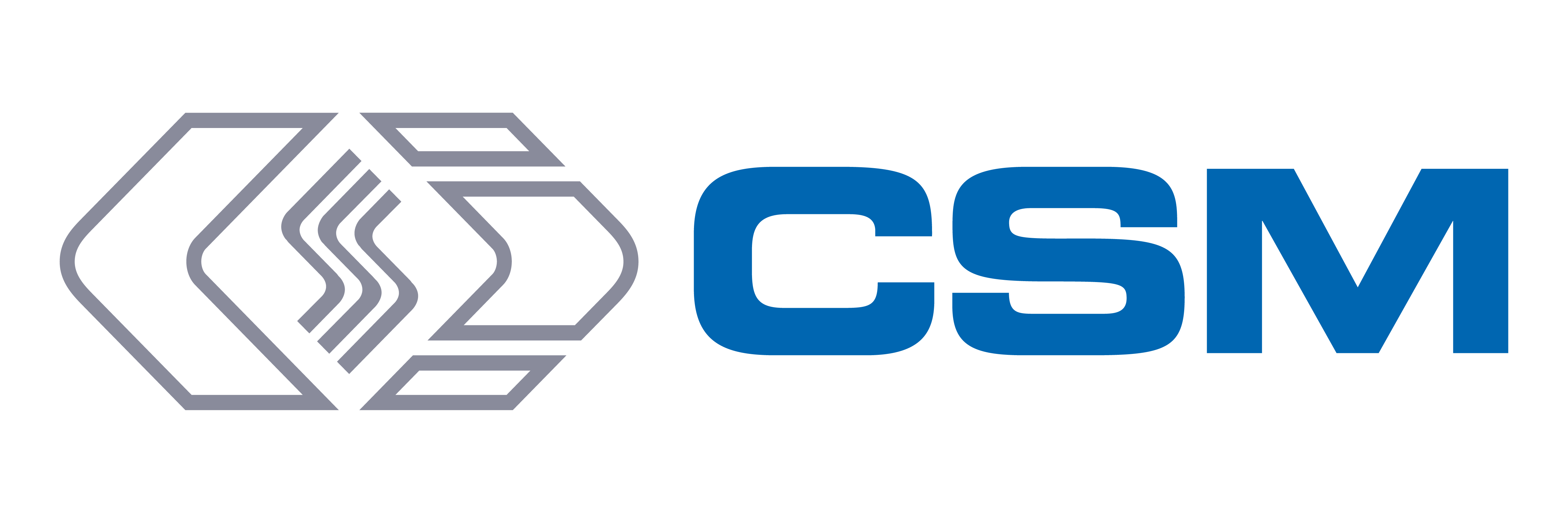
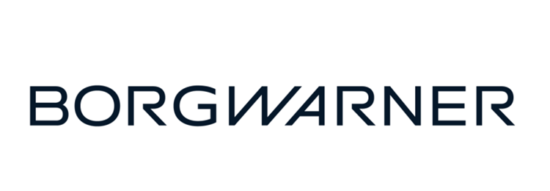