Motor testing
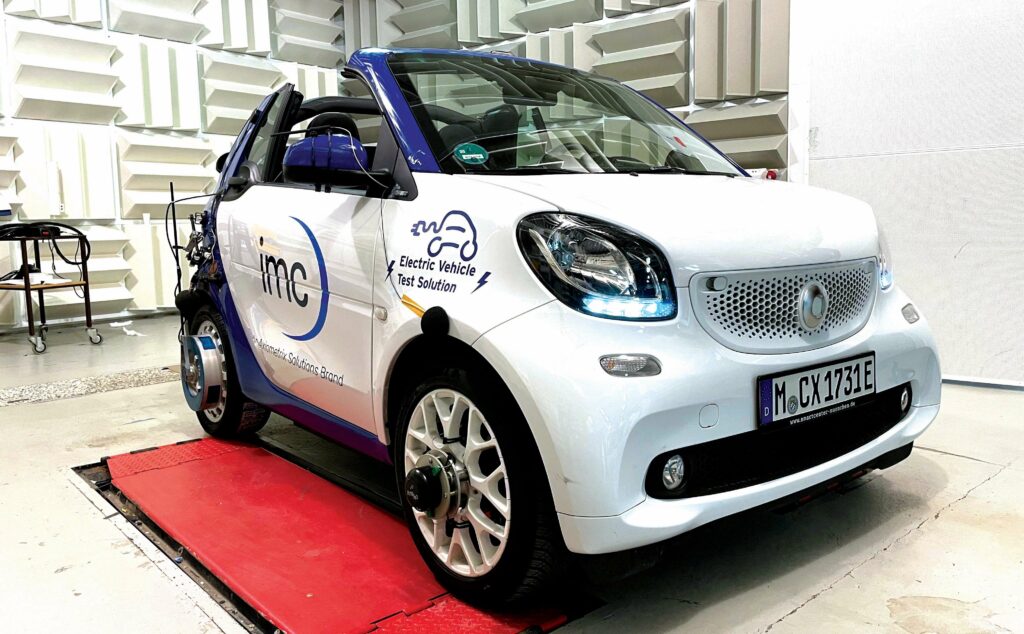
(Image courtesy of IMC)
The mechanical heart
Peter Donaldson examines various means of testing electric motors
Although mechanically simple, compared with internal combustion engines, the electric motors forming the heart of the propulsion system of EVs of all kinds must go through intensive testing. This involves the use of many technologies and procedures to probe performance, efficiency, reliability and safety at every stage of manufacture and integration.
During manufacture, electrical testing starts fairly early on in the process: verifying the integrity of insulation under high voltage, measuring the resistance of windings to ensure they are uniform and falling within the specified tolerances. Then both surge testing and partial discharge testing that, can detect short circuits, weaknesses and early-stage faults with the insulation of windings.
Mechanical testing at this stage focuses on key areas such as dimensional measurement as a quality control check on casting and machining rotors and stator housings, along with balancing rotors to ensure smooth operation. This is essential to reduce the risk of damage to bearings, insulation and connections from vibration, and knock-on effects to systems coupled to the motor. This is complemented by thermal testing, using infrared cameras to check for hotspots in operation.
End-of-line (EoL) testing includes functional runs that replicate the operational conditions that the motor is intended to face, validating torque output and rotational speed (from which power is calculated) along with efficiency. Manufacturers also analyse noise, vibration and harshness during EoL testing as a quality assurance check.
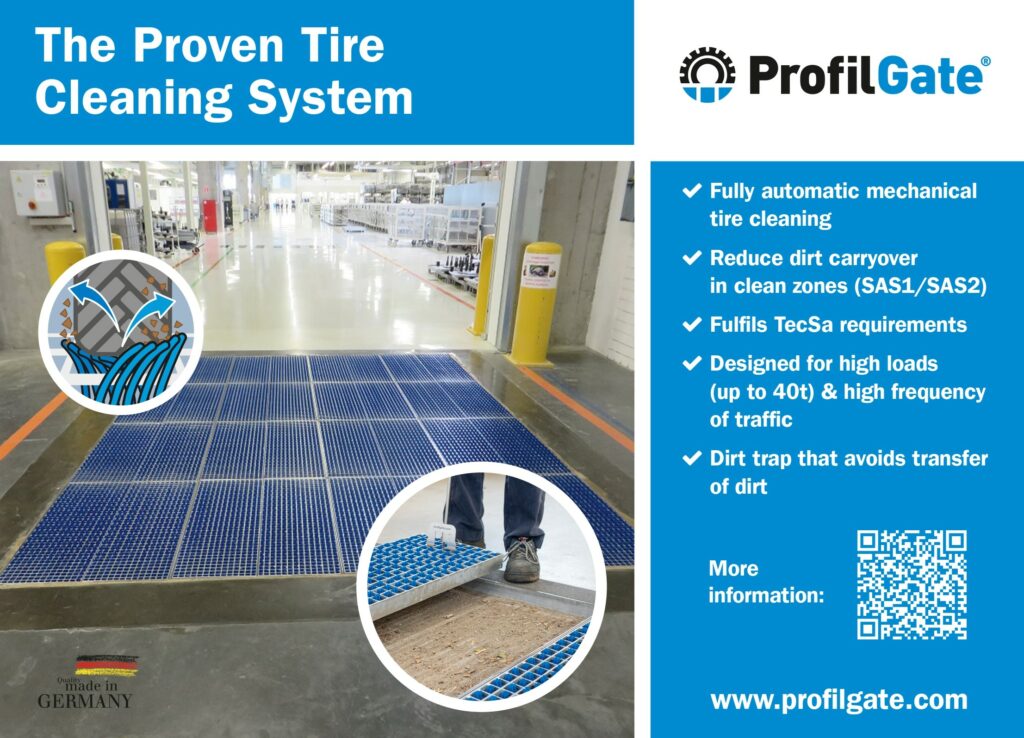
System-level tests
When the motor is integrated into its intended powertrain, the combined system must face a new set of tests, which involve additional components, and emphasise system-level performance plus different parameters and stressors.
Powertrain dynamometers are used to measure torque, speed and power across the full operational range, and the duty cycles they are designed to face, while inverter-motor testing systems are used to evaluate interaction between the motor and its power electronics.
Thermal and cooling system testing is also carried out at the powertrain level to assess responses to the temperature and humidity ranges in which the motor is intended to operate, as well as probing the performance of the thermal management system, particularly cooling of the motor and inverter.
Further, efficiency analysis involves measuring electrical input and mechanical output to gauge how much energy is lost in the conversion, and the impact of harmonics on motor performance and energy use is also examined.
It is particularly important to look closely at harmonics in motors controlled using non-sinusoidal waveforms, such as those produced by variable-frequency drives (VFDs) or other switching power supplies, as these can cause harmonic distortion.
In turn, that can lead to additional heating in the motor windings and power supply, mechanical vibration and electromagnetic interference. Harmonic distortion can cause irregularities in the motor’s torque output, leading to undesirable fluctuations, known as torque ripple.
It can also contribute to additional losses, which is a particular problem in systems designed for high-efficiency, where even small inefficiencies can be significant.
At vehicle level, the motors are stressed along with the rest of the vehicle on chassis dynamometers that test performance under simulated road conditions, while acceleration and braking tests measure responsiveness in various scenarios. More specific tests are carried out on high-voltage test benches to validate the interaction between the battery, inverter and motor, while regenerative braking analysis examines how well these components operate together in energy recovery mode.
Environmental and durability assessment includes vibration and shock testing to simulate real-world stresses that could affect all the vehicle’s systems, including its drive motors, while corrosion testing assesses the effects of environmental factors such as moisture and road salt.
Electrical machines such as motors, generators and power electronics, including inverters and DC-DC converters, are all sources of radio-frequency emissions, so further specialised testing is carried out to ensure the levels of electromagnetic interference (EMI) are low enough to comply with the standards for electromagnetic compatibility (EMC).
Increasingly, both virtual and hardware-in-the-loop (HIL) simulation are used to replicate real-world conditions, stressing motor and control systems before full physical systems are put together.
EME spoke with several companies that address motor testing to gauge their different approaches, from comprehensive coverage to highly specialised products and services.

(Image courtesy of Autforce)
Tailored solutions
Autforce, for example, offers test benches and software, and it provides motor testing with a focus on customisation and measurement precision, combining automation, external measurement integration and simulation tools.
The company’s tailored solutions accommodate a wide range of electrical machine sizes and power ratings. Past projects include test-bench systems for motors producing just 7.5 kW with a maximum speed of 15,000 rpm, ranging up to motors rated at 650 kW with 11,000 Nm of torque, 800 A peak current and speeds reaching 17,000 rpm, according to test-bench engineer Rainer Jung.
Motor types supported include permanent magnet synchronous motors (PMSM), induction motors (IM) and switched reluctance motors (SRM).
Autforce conducts end-to-end testing, including both component-level (motors and inverters) and system-level (powertrains and vehicles). Performance and efficiency assessments involve the use of customer-specified measuring equipment and external test devices. If real-time capability is required, the appropriate hardware is integrated to ensure accuracy, according to Jung.
For example, Autforce employs the Yokogawa WT 5000 power analyser when necessary, providing a basic power accuracy of +/-0.03% across a broad voltage and current range. Dynamometers are used for simulating real-world load conditions, with test data based on customer-supplied driving tests rather than pre-existing datasets.
Thermal and environmental testing capabilities include temperature and climate chambers for extreme conditions. The company also uses image processing with AI capabilities to analyse thermal images. Cooling scenarios for liquid-cooled motor setups are tested using flow temperature, return temperature and volume-flow measurements. For air-cooled systems, Autforce collaborates with partner companies to improve measurement accuracy, Jung adds.
Thermal runaway testing and thermal-management system evaluations are available, with feasibility studies conducted for each project. Durability, NVH and EMI/EMC testing solutions vary, based on project requirements. Equipment is sourced based on accuracy needs, and hydraulic cylinders or shakers are used for simulated road-condition durability tests. EMI/EMC testing follows regulatory standards, with grounding concepts, EMC shielding and specialised coatings incorporated into test equipment design.
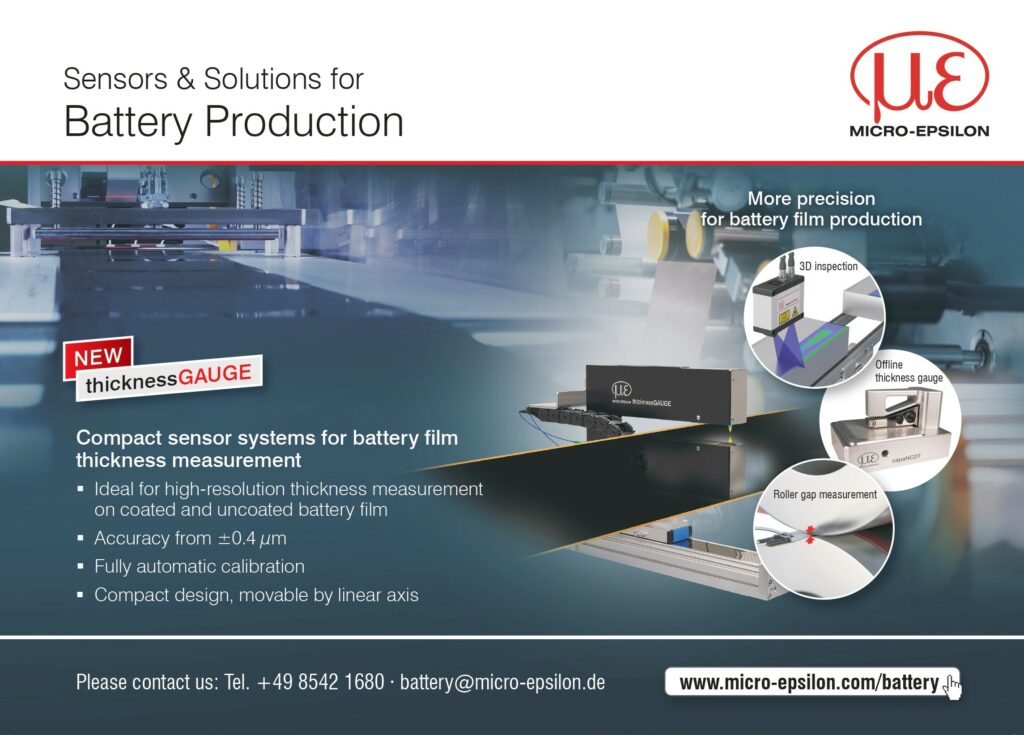
Autforce integrates its testing systems with hardware-in-the-loop (HIL) simulation tools for pre-physical testing validation. The company’s data acquisition and analytics capabilities allow for real-time data collection and storage, supporting predictive maintenance and design optimisation.
Jung adds that its software has been implemented in multiple industrial applications, building a database that is useful for wear assessment and maintenance planning.
The company also integrates automation into its test solutions through its proprietary automation software, Autfactory, which can be configured to meet specific customer needs. It is also parameterisable, meaning the user can change parameters such as measurement values and thresholds during setup.
Jung explains Autfactory’s role through its position in a conceptual automation pyramid. At the base of the pyramid is the process level concerned with the machinery, people and processes directly involved in manufacturing. Next comes the field level on which input and output signals are exchanged. Together, these can be thought of as the shop floor.
Autfactory is designed to operate on the next three levels up: the control level, where control of machinery through interfaces with programmable logic controllers (PLCs) takes place; the level inhabited by supervisory control and data acquisition (SCADA) systems, and associated human machine interfaces that allow operators to monitor, evaluate and intervene in ongoing processes; and the level where the manufacturing execution system (MES) helps with production planning, production data acquisition, determination of key performance indicators (KPIs), material and quality management. The management level sits at the top, where functions such as enterprise resource planning (ERP) take place.
Autfactory’s ‘control’ package is well suited to test benches of all kinds, says the company. Its ability to create and modify test sequences graphically makes it accessible to users without deep knowledge of code, enabling them to configure the system through an intuitive interface rather than programming it.
The company quotes a communication speed of under 10 ms, meaning the system can send and receive data (read/write operations) in less than 10 ms per cycle. This is crucial in real-time industrial applications, ensuring commands, data acquisition and system responses happen quickly and predictably. On a test bench, for example, a measurement would be taken, the result analysed for pass/fail criteria and logged, and the system would move to the next step in the sequence, all within 10 ms.
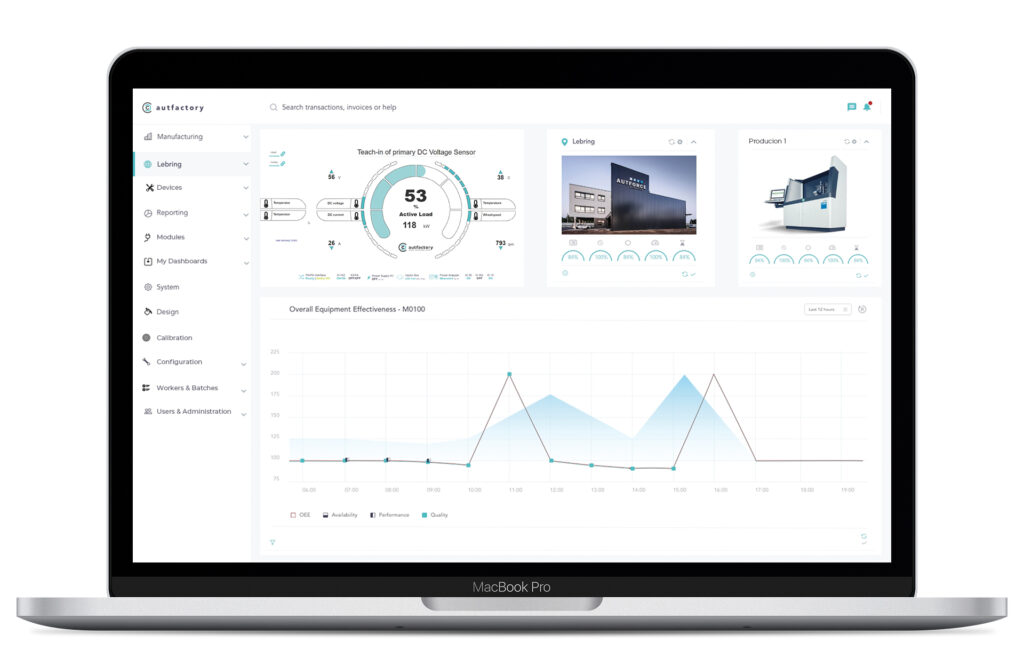
(Image courtesy of Autforce)
Broad spectrum testing
IMC Test & Measurement provides solutions based around test stands, data acquisition systems and measurement software for validating prototypes, optimising products and monitoring processes in both mobile and stationary applications. Part of Axiometrix Solutions, the company makes equipment used in motor testing across industries, including the e-bike, automotive, aerospace and rail sectors.
Its data acquisition systems, such as CRONOSflex, control test benches in real-time, and facilitate automated test sequences. These systems measure voltages up to 1000 V and verify currents up to 1600 A using fluxgate converters. CAN bus-based measurement modules allow monitoring of slower signals, such as temperature. Additionally, IMC provides telemetry solutions for data acquisition on rotating components. Typical applications are prototype testing and – for lower performance motors – EOL testing also.
The integration of CAN bus and other interfaces enables direct communication with control units and inverters, allowing for targeted control of the devices under testing.
“Collaboration with partners serves to provide comprehensive test-bed solutions for different motor types, including those with PMSM, IM and SRM architectures,” says technical product manager Martin Riedel.
Automation and data analysis software supports fully automated test sequences, including cascading and looped endurance testing. Third-party devices, such as temperature and climate chambers, can be integrated into test setups, enabling automated, cyclical temperature variations while data analysis is performed in the background. Test-cycle results can be automatically compiled in reports in PDF or PPT format.
The company offers data acquisition solutions for both component- and system-level testing. Applications include powertrain measurements using telemetry data from rotating components, such as strain gauges (the outputs relate to torque) and speed sensors, to calculate mechanical power.
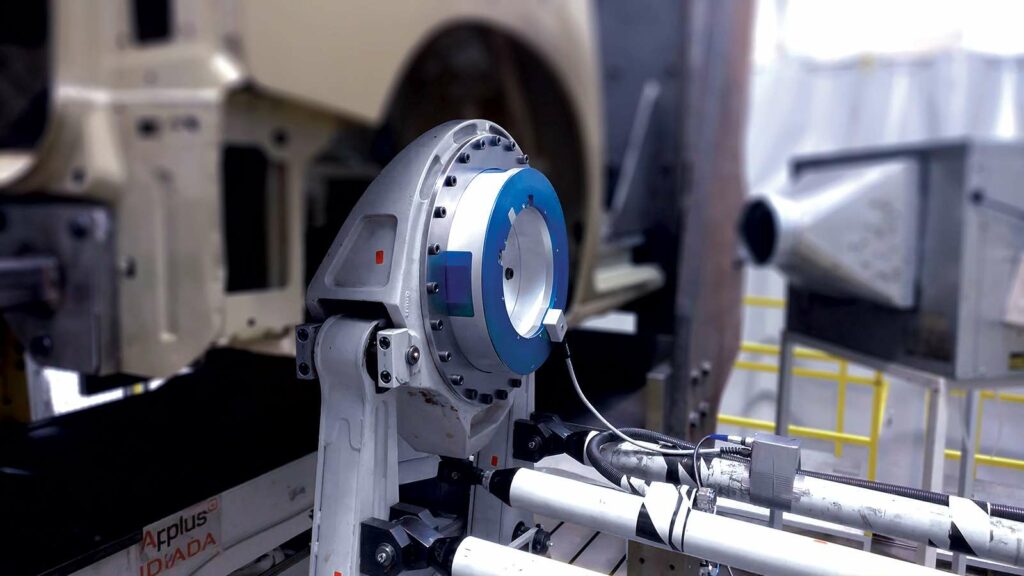
(Image courtesy of IMC)
Multi-channel acquisition
For stationary test benches, IMC’s systems use high-precision sensors, such as torque-measuring shafts and incremental encoders, to ensure accurate torque and speed measurements to support efficiency calculations. Synchronised data acquisition through multiple channels enables real-time calculations of efficiency, among other benefits.
“The availability of accurate, highly sampled, and synchronised measurement data is essential for the complete acquisition and evaluation of a DUT (device under test), and guarantees valuable insights, but also prevents data loss or offset of measurement data,” Riedel says.
For mobile applications, the company employs strain gauges on drive axles and uses telemetry to transmit signals from rotating shafts to stationary measurement systems. The company’s data acquisition hardware provides sampling rates up to 100 kS/s and bandwidth up to 48 kHz, facilitating harmonic analysis and capture of transient behaviour within integrated test environments.
Dynamometers can simulate real-world load conditions by recording road-load data with the IMC WFT-Cx wheel force transducer, which is processed and used to control load machines within a test bench setup.
Thermal and environmental testing capabilities include analogue and digital interfaces for integrating third-party test-bench components, such as environmental chambers and thermal imaging systems. IMC’s solutions can support thermal runaway testing and thermal-management system evaluations, particularly in battery testing applications.
For durability testing, the company’s data acquisition systems enable long-term vibration and shock testing under simulated road conditions. This equipment supports integration with hydraulic shakers and other environmental testing setups.
IMC also provides data acquisition solutions that integrate with HIL simulation tools. The data analysis software facilitates technical data processing, automating unit and sampling rate conversions, and supporting complex calculations across multiple channels and large datasets.
The company emphasises that integration with external databases, Python and Microsoft Office software enhances analysis capabilities, and custom algorithms can be incorporated to meet specific user needs.
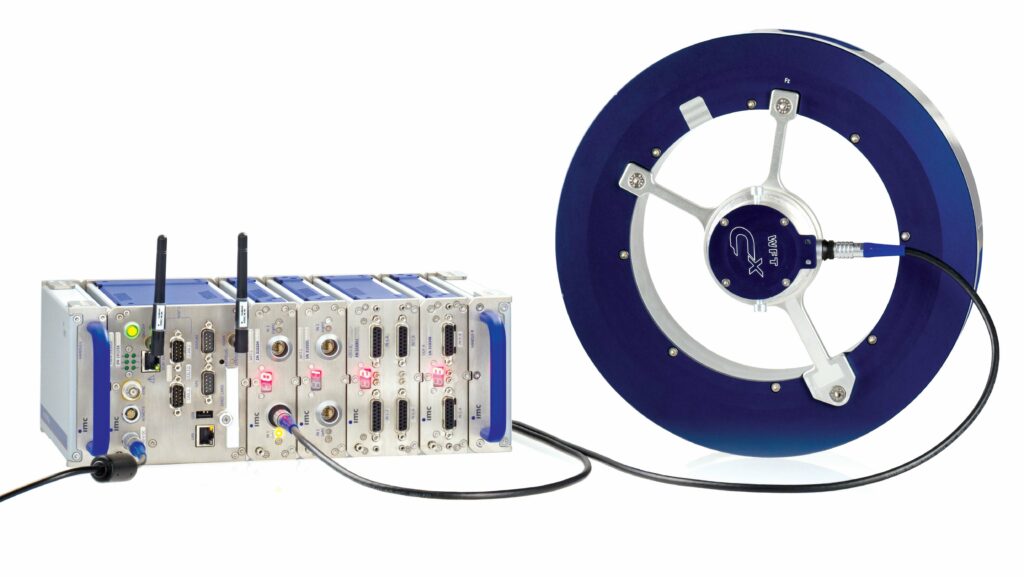
(Image courtesy of IMC)
Sound measurement
GRAS Sound & Vibration, also part of Axiometrix, focuses on precision acoustic data capture, offering microphones that support testing of small, electric motors to large powertrain systems. These solutions integrate GRAS’s EQset microphones, which support automated calibration, into customised test setups, ensuring reliable and repeatable measurements.
For performance and efficiency testing, the company’s Ultra Thin Precision (UTP) microphones are used to capture high-frequency noise and vibration data, crucial for analysing motor efficiency across varying operating ranges.
UTP microphones also facilitate harmonic analysis and transient behaviour capture, both of which are essential for motor optimisation, when integrated with advanced analysers. When used alongside dynamometers, GRAS microphones contribute to simulation of real-world conditions such as varying road gradients and regenerative braking.
These microphones are designed to operate under extreme environmental conditions, maintaining performance in high-temperature and high-humidity environments, supporting detailed acoustic analysis during cooling simulations for both liquid- and air-cooled motor setups. Additionally, GRAS microphones detect noise and vibration anomalies during thermal runaway testing, aiding thermal management evaluation.
For NVH testing, GRAS high-sensitivity microphones, such as the 146AE, capture intricate acoustic data necessary for refining motor and powertrain designs, and they are engineered for long-term durability testing under simulated road conditions. They are also built to meet stringent standards for EMI and EMC testing.
The equipment integrates with simulation tools such as HIL systems to help reduce development time. The company’s real-time data acquisition and advanced analytics capabilities provide insights for predictive maintenance and design optimisation.
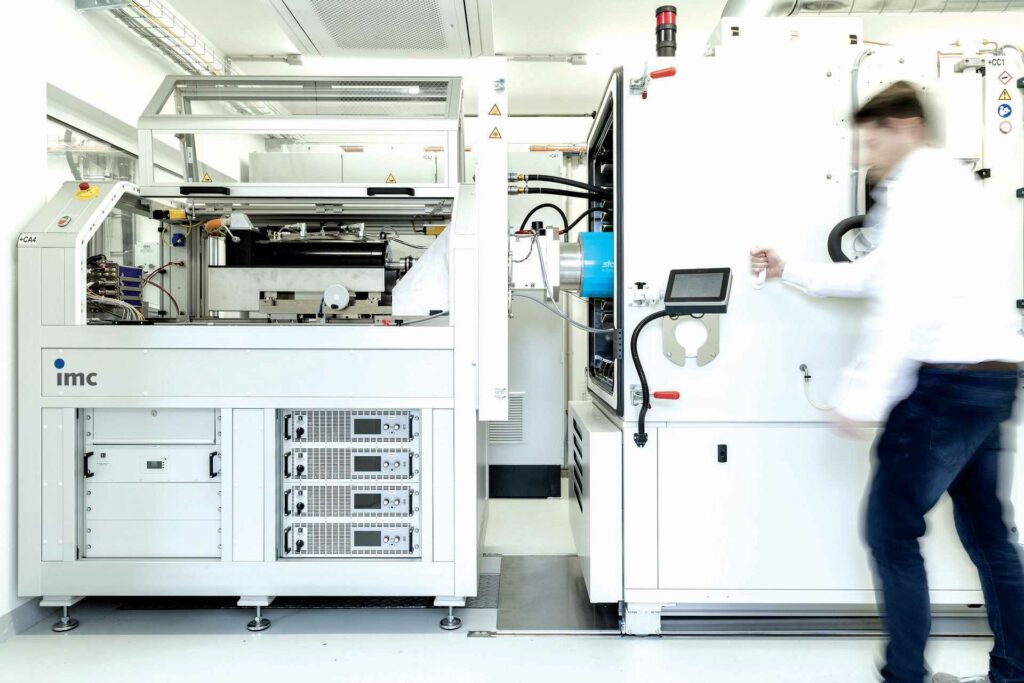
(Image courtesy of IMC)
Advanced power analysis
Power analysers are an important category of test equipment used to gauge the performance of inverter-driven electrical machines. For example, Hottinger Bruel & Kjaer (HBK) produces the eDrive series, offered as a comprehensive power analysis and data acquisition system that is designed to support testing across various motor types and applications.
Based on digital cycle detection, these systems are designed to connect to a PC that can display power readings in real-time, store results and raw data, and analyse stored data in post-processing. The company says eDrive analysers deliver reliable results, even through dynamic load changes; conditions that reveal weaknesses in more conventional power meters.
The eDrive family accommodates a wide range of motor sizes and power ratings, and it is compatible with the broad range of sensors needed to gather data from motors ranging from small household appliances and pumps (measured in watts) to larger industrial motors, EV powertrains and elevators (in kW), and even large-scale applications such as trains, ships and wind energy systems (in MW).
Furthermore, the system is compatible with various motor types, including PMSM, induction motors, switched reluctance motors, machines with large numbers of phases (six, 12 or even up to 21) and linear motors.
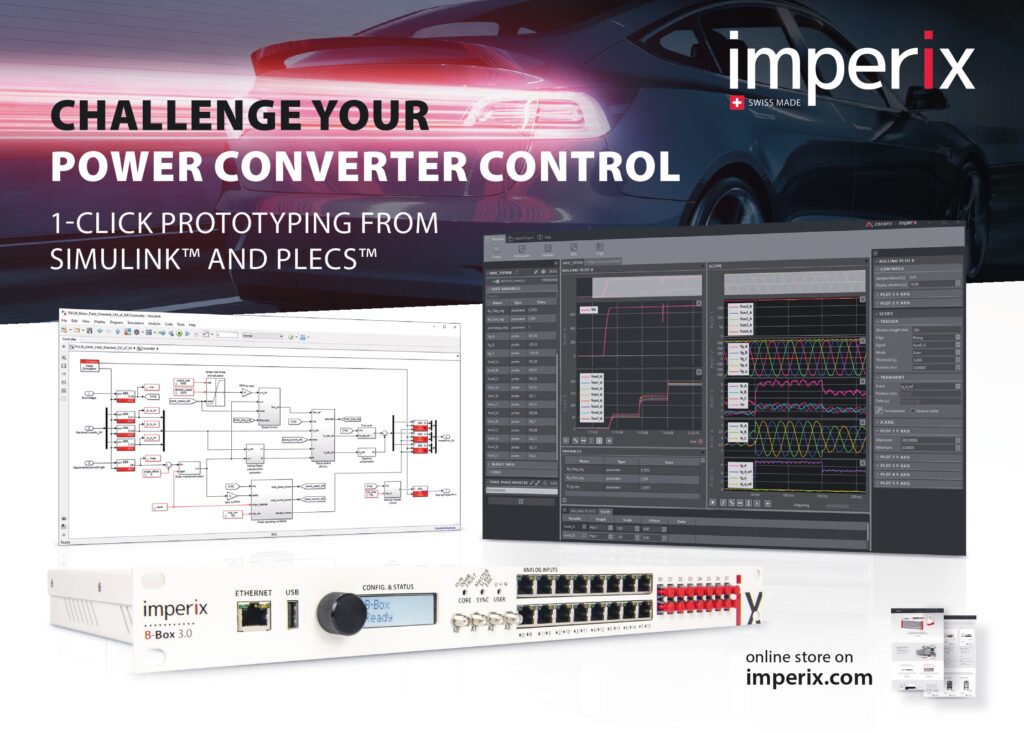
Automation is available on the data storage and analysis side, including automated file transfer, file conversion and batch processing of multiple tests. Additionally, the system supports all levels of the development ‘V’ model, from basic research and component development to subsystem and full-system integration testing, the company says.
Cycle detection is a digital process used to identify and track the fundamental frequency of an electrical signal in real-time, enabling the analyser to make accurate power calculations on a per-cycle basis. By detecting individual cycles, the eDrive system ensures power, torque and efficiency measurements are computed with the correct averaging intervals. This level of granularity is essential in applications where dynamic performance evaluation is required.
Digital real-time cycle detection uses a built-in crosscheck function to detect any failed cycles, preventing inaccurate power calculations from being recorded. This ensures accuracy, even when the motor’s rotational speed fluctuates rapidly, typically under transient load conditions or in standardised driving cycles, such as the Worldwide Harmonised Light Vehicles Test Procedure (WLTP).
This is particularly beneficial in scenarios with variable-speed drives, where traditional analysers that rely on analogue phase-locked loop (PLL) techniques may struggle to maintain accurate frequency tracking.
The eDrive systems minimise measurement inaccuracies by dynamically adjusting the input range of loads. A real-time measurement uncertainty calculation, which HBK calls unique, provides users with uncertainty values for every setpoint, even under varying loads.
Harmonic analysis capabilities include grid harmonics (meeting the IEC 61000-4-7 standard) at the inverter input and wideband harmonics at the inverter output. These measurements are performed with 18-bit resolution, ensuring high precision and the ability to detect low amplitude harmonics. The system provides detailed harmonic insights that are critical for evaluating power quality and motor performance.
For noise, vibration and harshness (NVH) testing, the system supports optional, 24-bit IEPE inputs for accelerometers and microphones with bandwidth up to 200 kHz and a sample rate of 500 kS/s. It can perform Fast Fourier Transform (FFT) analysis, spectrograms and order tracking, allowing users to correlate motor-control parameters with NVH characteristics. A practical application is the evaluation of the relationship between inverter modulation methods and torque ripple.
Durability testing presents the challenge of managing vast amounts of data over extended periods of time. The system can record all data continuously at full sample rates to an SSD, although this would result in terabytes of data. Instead, it offers intelligent data management.
One of these is fixed-time grid sampling, which involves capturing high-resolution data at intervals; for example, one-second snapshots every hour. Another is the use of condition-based triggers, capturing high-resolution data only when predefined thresholds are met, such as torque ripple exceeding 10%.
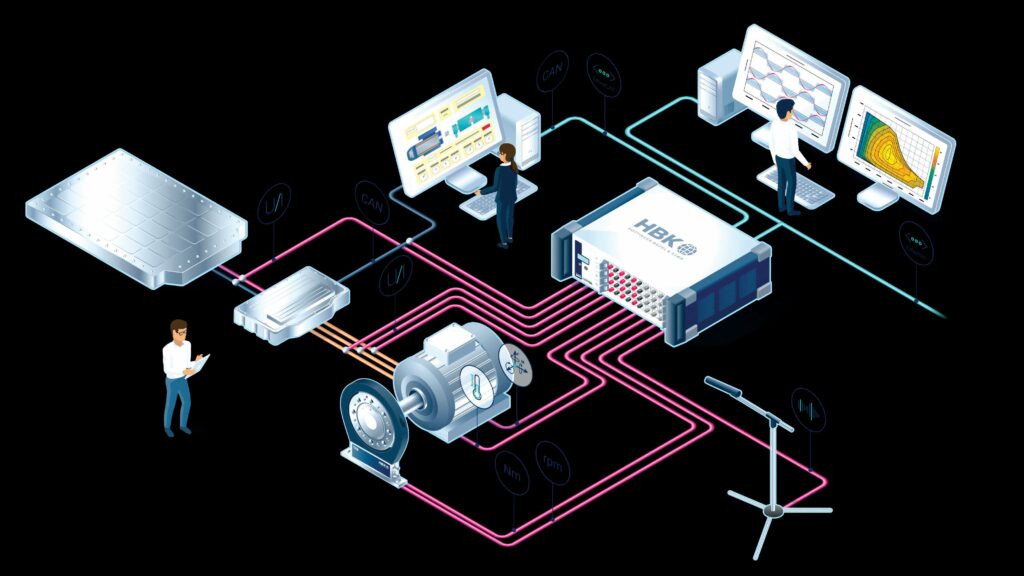
(Image courtesy of HBK)
eNVH and acoustic coupling
tectos provides advanced testing solutions for electric motors, powertrains, and related components, offering systems that accommodate a broad spectrum of power levels and motor types. According to managing director and CEO Dr. Dieter Höfler, tectos’ equipment can handle “the full range of potential mobility applications,” from small motors to those used in high-power applications such as EVs and even industrial machinery producing power levels of several megawatts.
A standout feature of tectos’ systems is the capability to analyse electric noise, vibration, and harshness (eNVH), identifying root causes of motor noise, and helping engineers optimise their noise reduction strategies through analysis of eNVH and acoustic coupling.
“Sometimes the most efficient operation point is noisy,” Höfler points out. “So using the eNVH approach helps to optimise the noise by tuning the inverter to reduce the structure borne noise of the motor itself. “We generate a 4D map where you can see the correlation between efficiency and noise over speed and load. In developing driving strategies for a car, for example, you can mask e-motor noise with other driving sounds. This means the higher the speed of the car the more noise the motor could be allowed to make because it is covered by tyre and wind noise.”
Motor architectures supported include PMSM, IM and SRM, a flexibility enabled by the use of a “universal” inverter, which replicates the behaviour of the original test specimen inverter. This allows for the electric motor to be analysed in advance, leading to an optimised inverter design. The universal inverter is designed for outputs up to 900 A, 520 V and 400 kW under normal operating conditions. It can also handle overloads (defined under constant motor rating (CMR) conditions) for up to 60 seconds at a time before protective measures are activated, withstanding repeated overloads over a 600-second period.
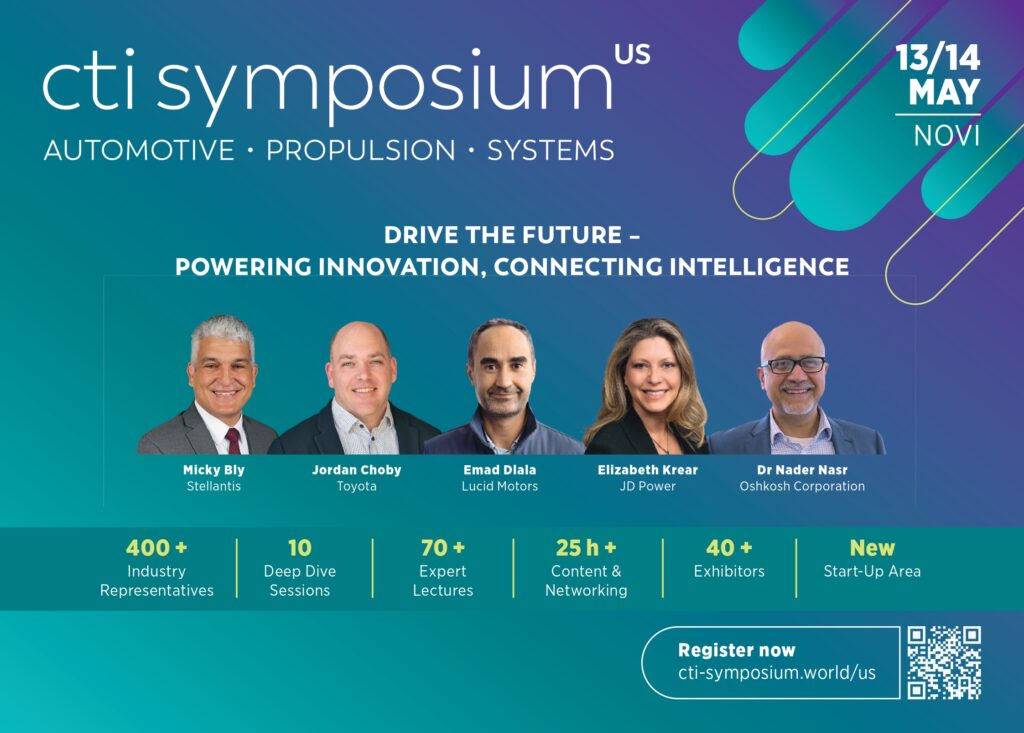
The company emphasises a high level of customisation in its solutions, particularly when it comes to automation. Many of its customers have automation systems in place, and tectos integrates its test equipment with them.
“We learned that the automation needs to be separated from the test system. Customers usually do not want to change their existing setups,” Höfler explains. In cases where a customer is starting a greenfield project, tectos offers a selection of automation solutions, ranging from well-established, sophisticated setups to open solutions based on tools such as MATLAB with communications interfacing from National Instruments (NI), for example.
In addition to testing individual components, tectos’ systems also support end-to-end testing, encompassing motor and inverter components as well as larger powertrain or vehicle systems. “You need to focus on the whole product, which in fact consists of different systems,” Höfler notes.
The company utilizes a patented solution to measure output power precisely at the output of the unit under test (UUT), minimising interference from friction, while precise electric power analysers from external suppliers such as DEWETRON are used to generate highly accurate efficiency maps.
While tectos relies on external partners for certain aspects of environmental simulation, it can test motors and systems across a temperature range from -80°C to +150°C under varying humidity conditions. The company also provides advanced solutions for testing liquid-cooled and air-cooled systems, modelling factors such as convection and heat dissipation to simulate cooling performance accurately.
For EMI and EMC testing, the company works with specialist partner Emitech, enabling tectos to test its own products and deliver EMI/EMC benches to customers. Some of its own products, such as glass fibre drive shafts, are specially designed for EMC.
tectos’ systems are also equipped with robust data acquisition and analysis capabilities to provide real-time insights in support of predictive maintenance and optimisation for example. Höfler highlights the importance of root cause analysis, a method that helps engineers understand and troubleshoot complex systems. tectos also integrates its equipment with simulation tools, including hardware-in-the-loop systems, for system design validation.
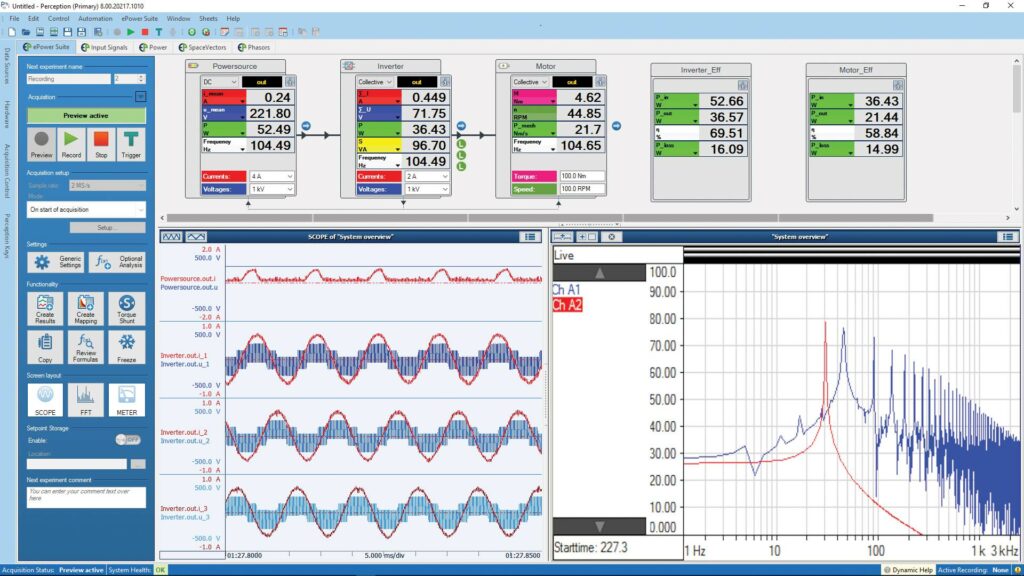
(Image courtesy of HBK)
Future directions
Inevitably, AI and machine learning (ML) figure heavily in prospects for further advances in test systems generally, and they are already beginning to transform e-motor testing. For example, AI-driven systems are likely to automate more test procedures, reducing manual effort and minimising human error, while ML will get better at adapting testing sequences based on real-time data, optimising conditions for different motor types and use cases.
AI-powered digital twins will become increasingly powerful, enabling higher-fidelity, real-time simulation and what-if analysis, while HIL testing combined with AI will create more accurate and adaptive test environments. ML algorithms can find correlations between test parameters and failure modes, helping engineers to improve designs. Finally, the integration of cloud computing with edge AI will enable real-time remote monitoring and testing.
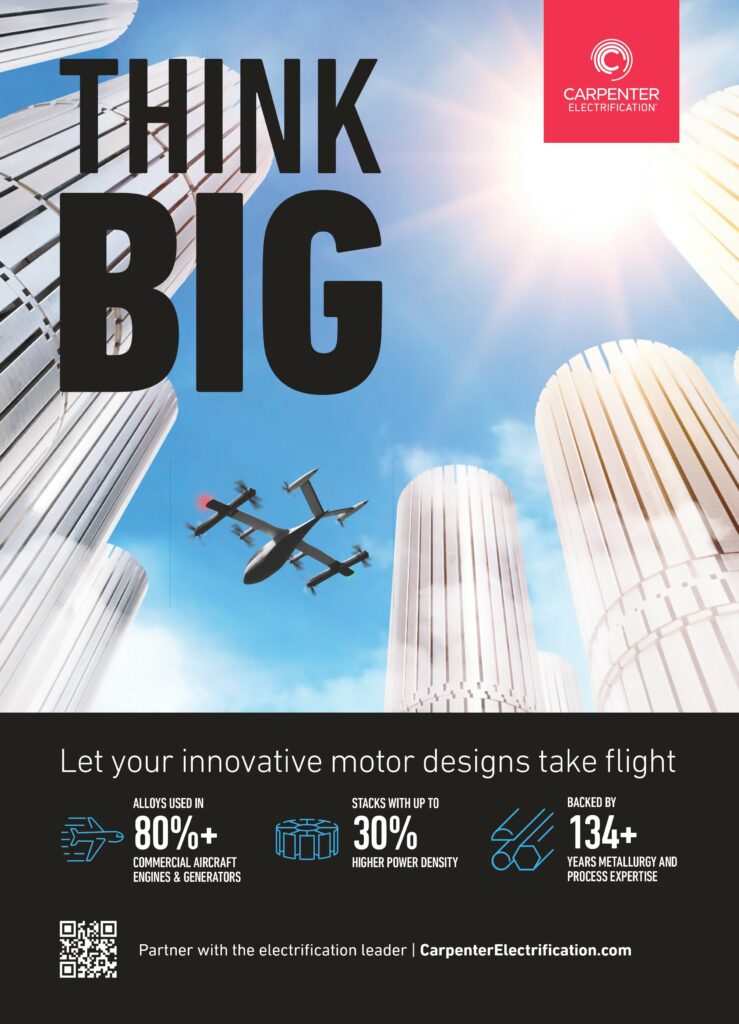
ONLINE PARTNERS
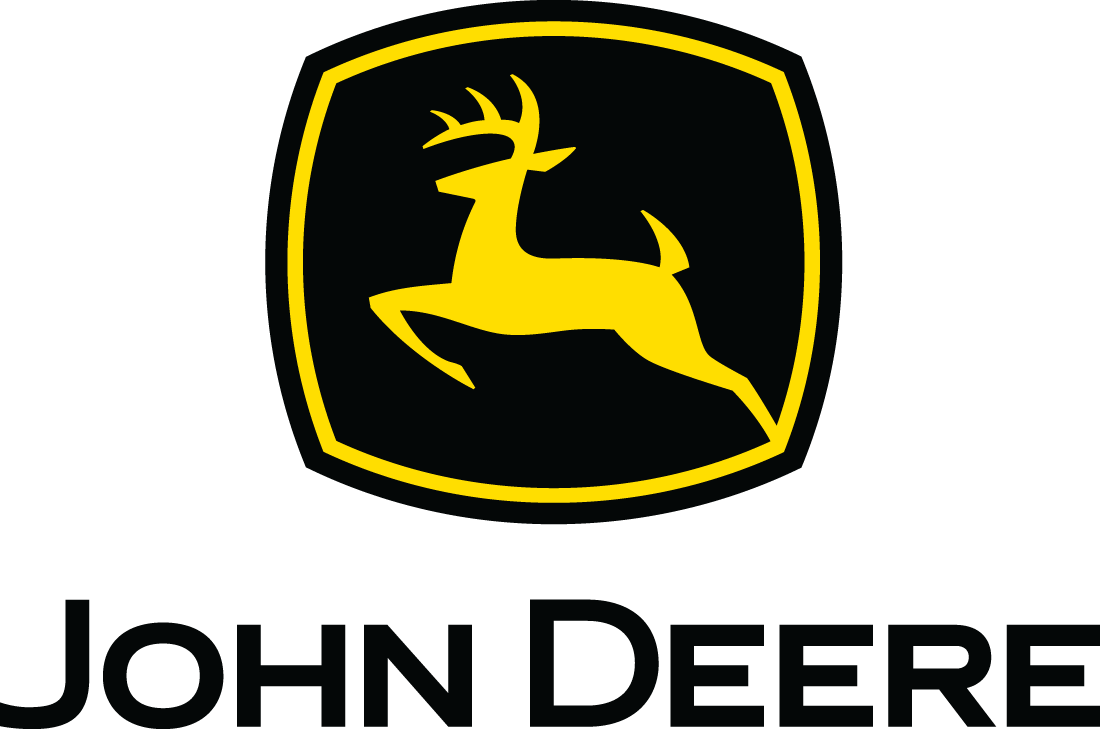
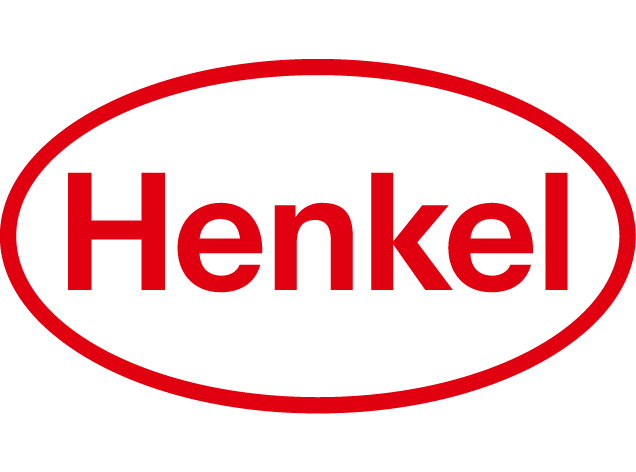
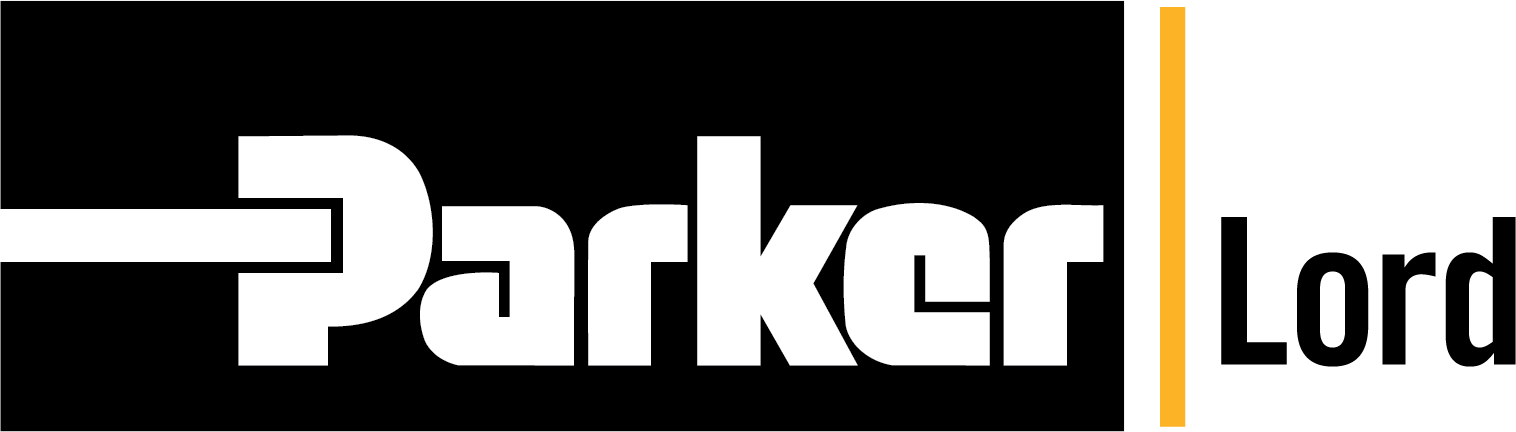
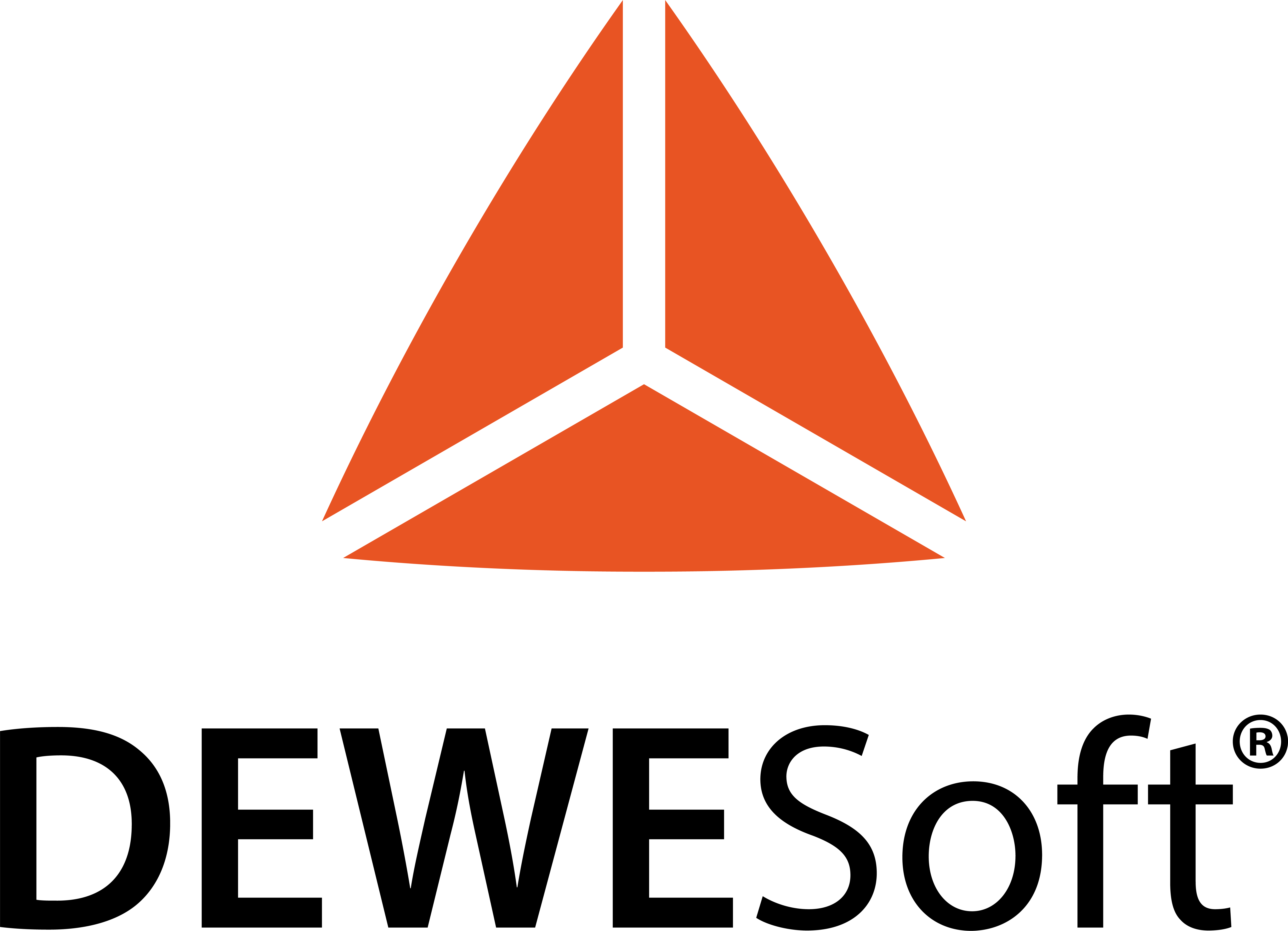
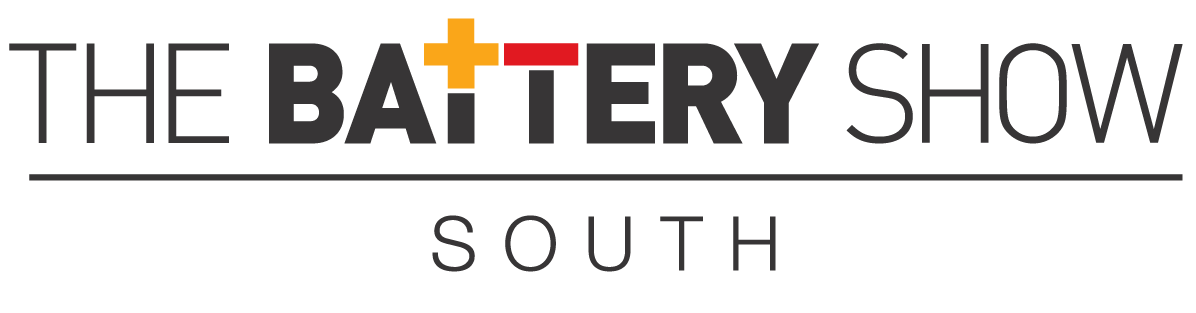
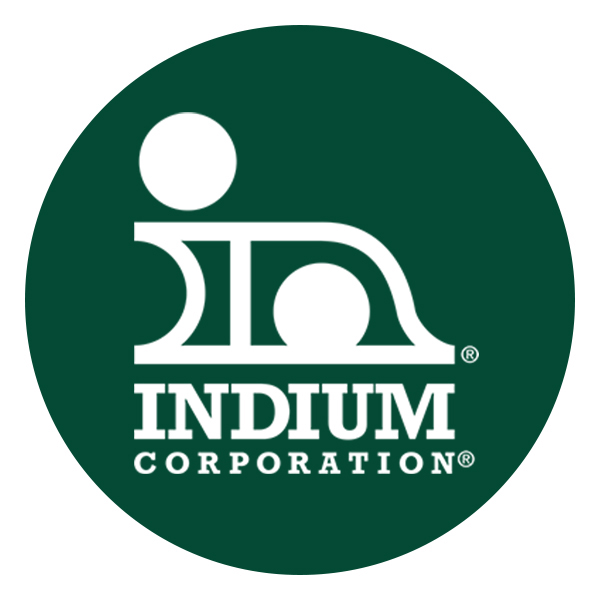

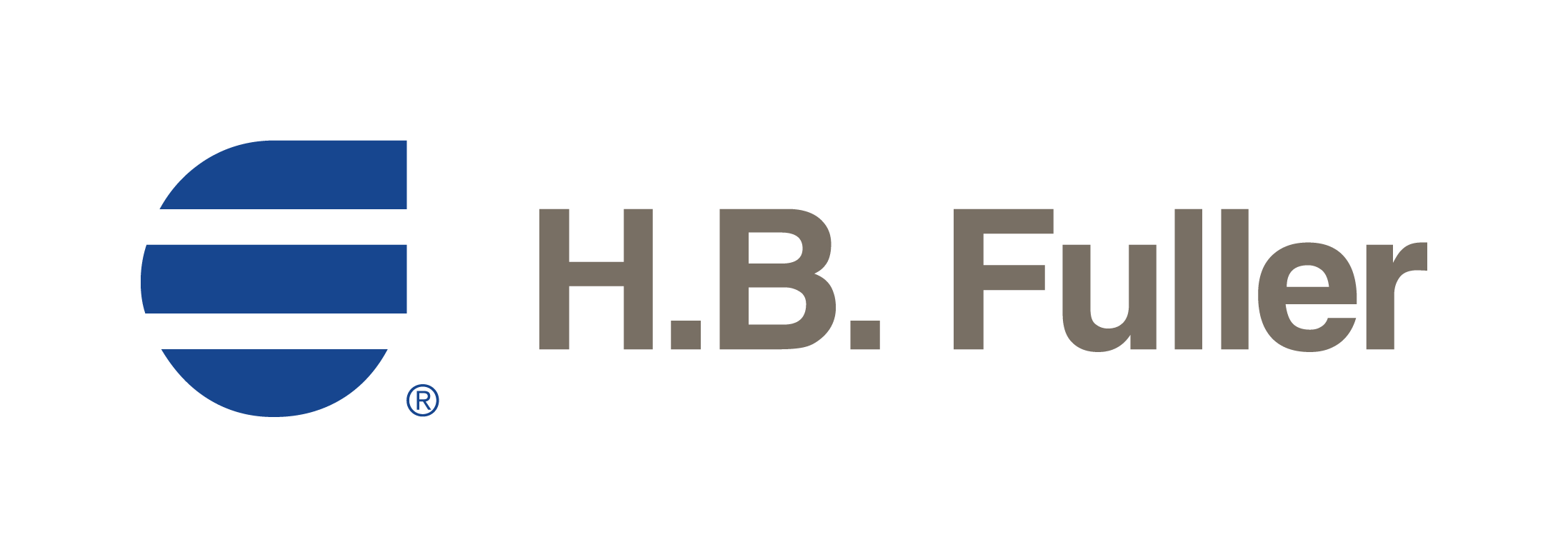
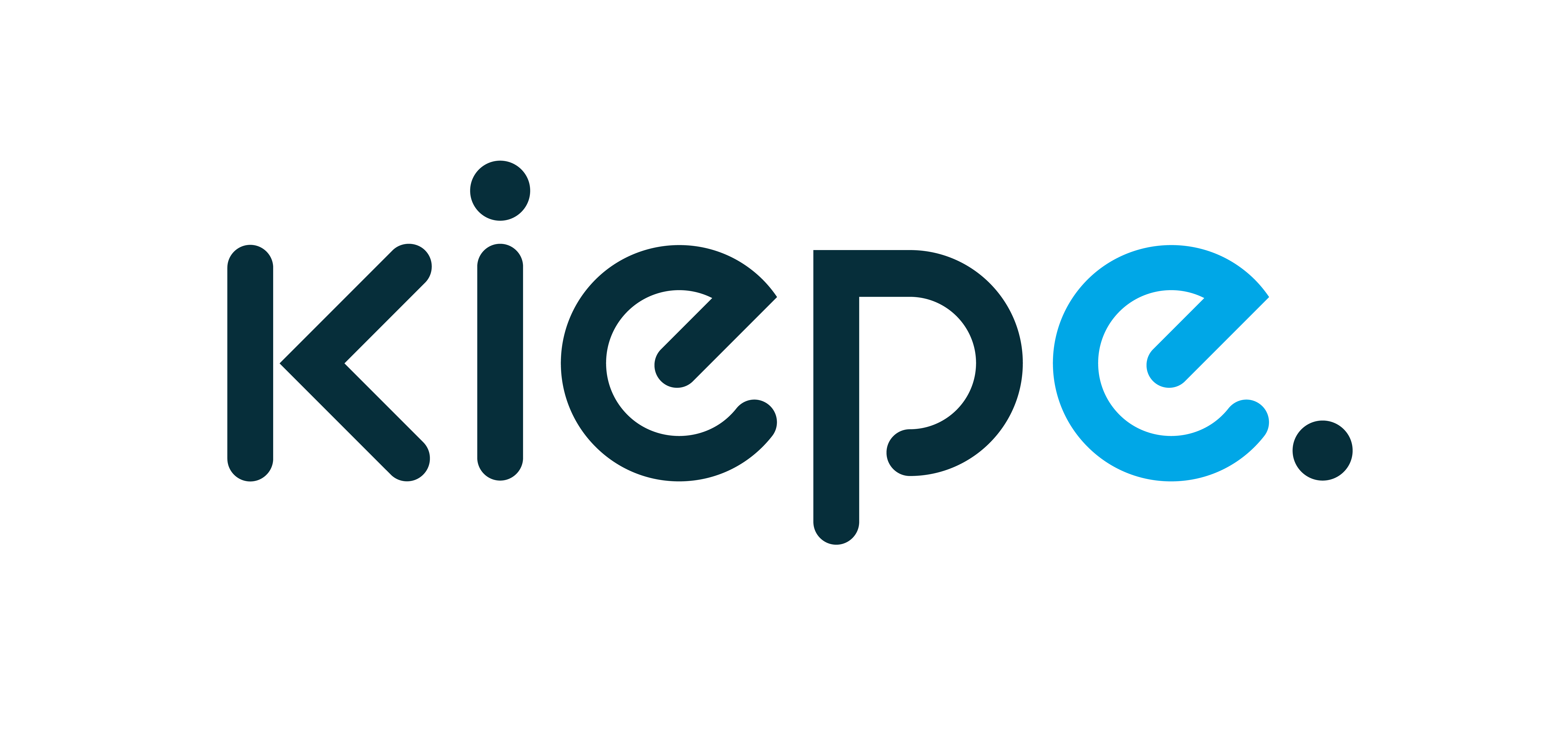
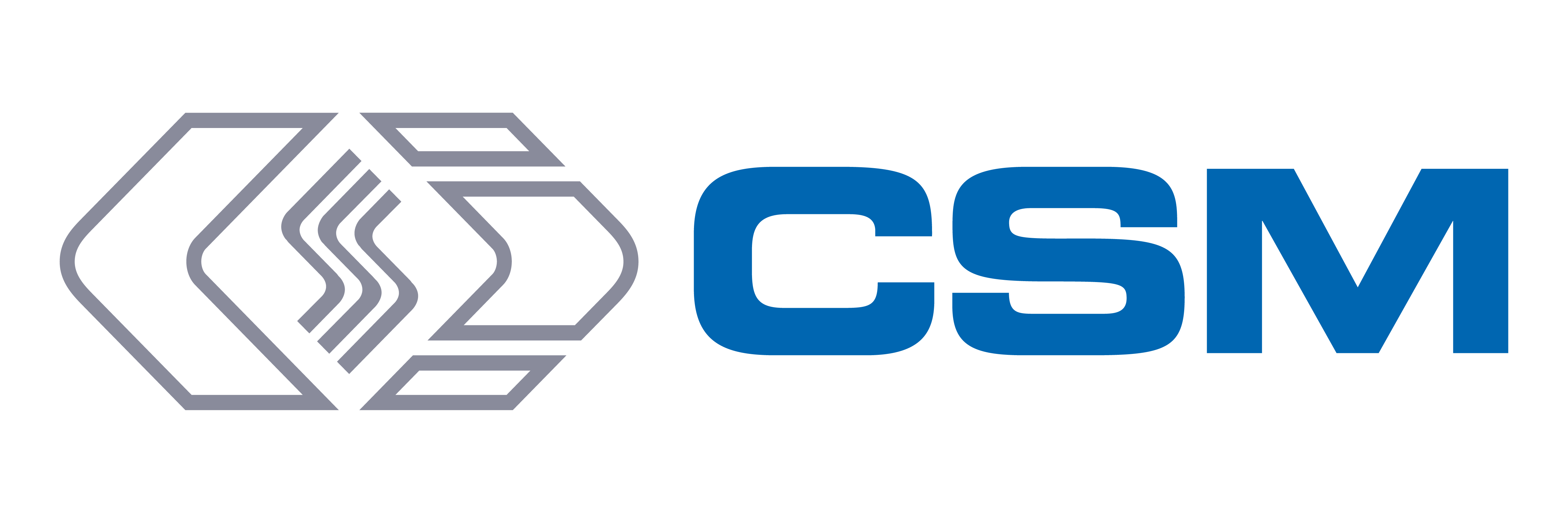