Ian Foley
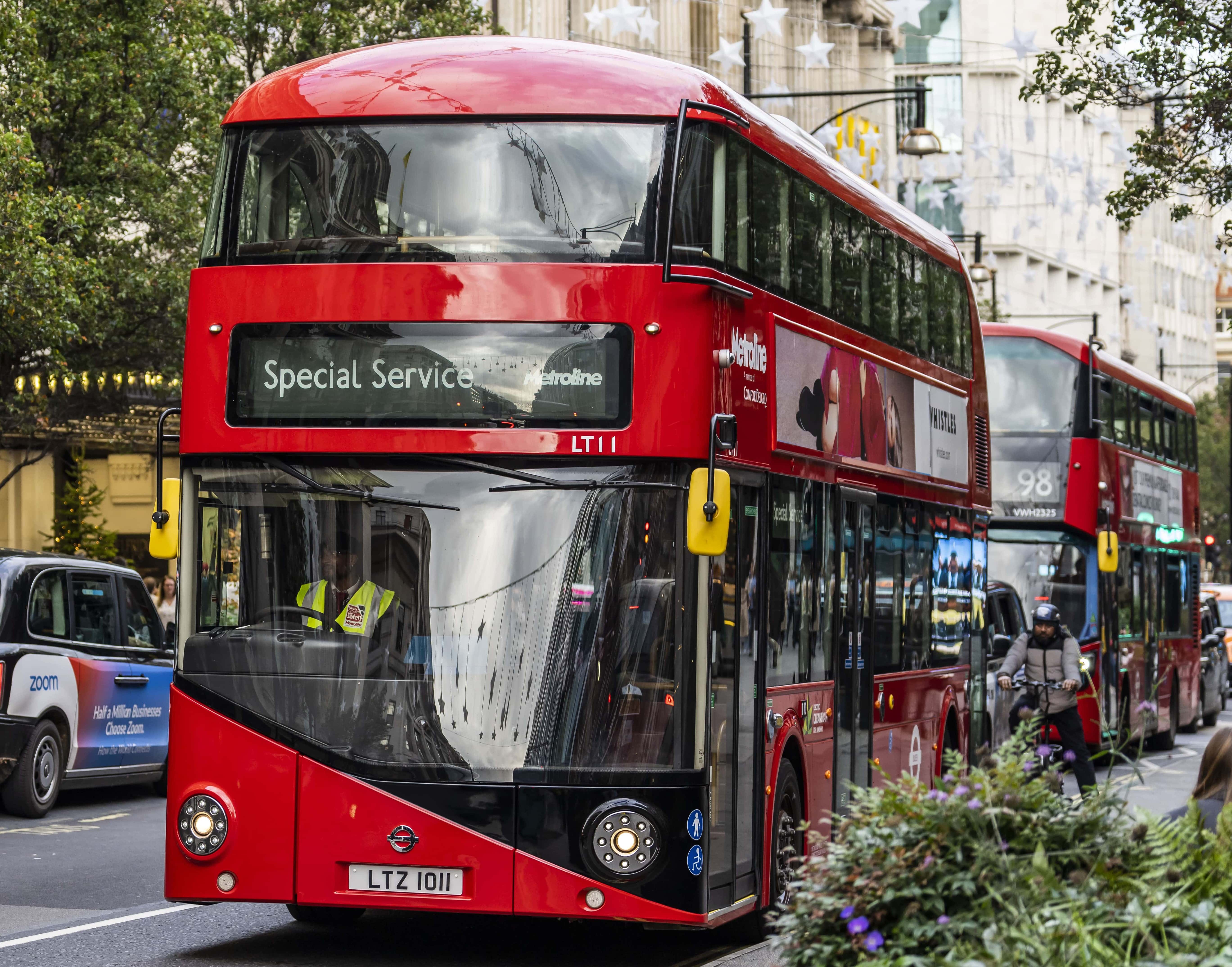
(Images courtesy of Equipmake)
Equipmake’s CEO explains the technologies that underpin the company’s evolution into scale production of e-mobility motors. Rory Jackson reports
While specialising in a market niche is useful for some e-mobility component manufacturers, others can find that it pays to diversify. Equipmake falls squarely into the latter category, having supplied electric motors for industries ranging from public transport to space.
Its progress has been spearheaded by Ian Foley, who founded Equipmake and is its CEO. He has been with the company for more than 25 years, but his first experience in e-mobility was at Williams Hybrid Power, which he also founded (after founding Equipmake), and served as managing director for a time simultaneously with ongoing work at Equipmake. That company had a particular focus on electrically driven flywheel energy storage systems, in which energy is stored via the high-speed rotation of a flywheel.
Flywheel hybrids
“I’d been involved in power electronics before then, when Equipmake was tasked with projects like developing power management systems for railway signalling power supplies,” he says.
“Those were 600 V systems with electronic power fuses. There was a lot of detailed r&d for them into how to drive power electronics effectively and reliably, which would later feed into how we would design inverters for EV applications. My first step into e-mobility though was developing hybrid powertrains with flywheel energy storage.”
The r&d was motivated primarily by motorsport requirements. When Formula One announced plans to go hybrid in 2006, Foley took inspiration from the centrifuges developed by the British-German-Dutch nuclear enrichment consortium Urenco Group. Urenco had used its experience of nuclear enrichment centrifuges to develop an electrically driven flywheel energy storage system, which Foley had worked with previously.
“It was effectively a carbon fibre composite electric motor, spinning at about 40,000 rpm, and we recognised there was good potential if you could scale that down and continuously power-cycle it,” he says. “So we acquired the technology, spoke to the Formula One teams about it, and Williams became initially a customer, then an investor. The flywheel system was tested, but didn’t end up on a Formula One car, and instead found itself on the Audi Le Mans car, which then won at Le Mans three times.
“That was a very challenging project, because a flywheel has to run at 40,000 rpm in a vacuum, and it has to be reliable in a racing environment, where the car is bouncing over kerbs and vibrating heavily, so we built up a lot of experience of how to ruggedise electric powertrain systems.
“Ultimately, flywheels were superseded, because their main benefit was heavy power cycling for long periods with no loss of performance. That works best when you need high power relative to energy, and modern EV engineering philosophy is all about maximising energy relative to power consumption. But the lessons learned about developing high-performance electric motors, and controlling and ruggedising them for vehicles, was all directly applicable to what we do at Equipmake now.”
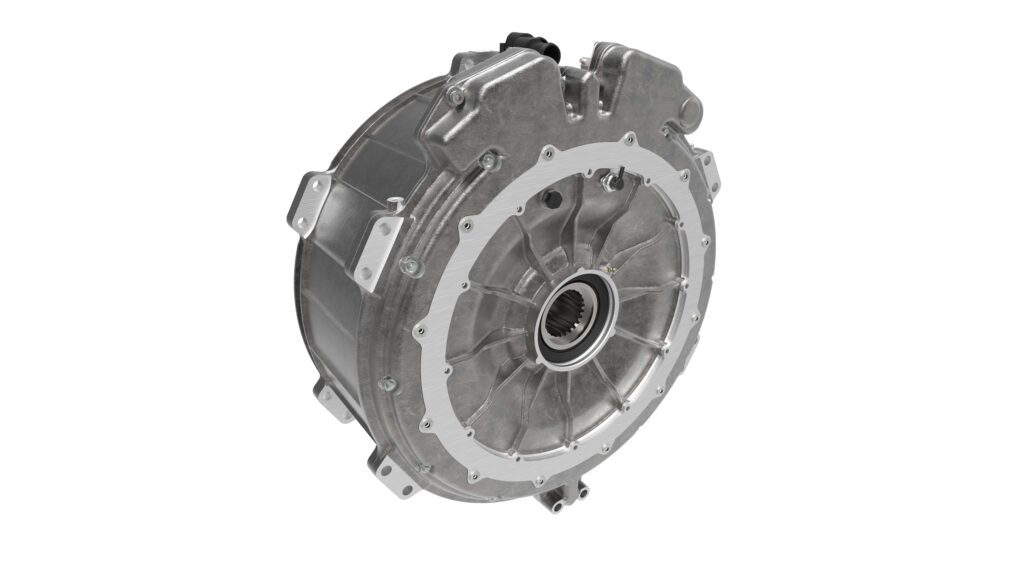
Spoke motors
Although Equipmake was originally an engineering consultancy, for the past 10 years it has shifted strongly into r&d of electric motors and inverters, and has recently become known as a scale production company.
Its flagship product, the 220 kW, 450 Nm APM-200, is often referred to by its unique ‘spoke motor’ architecture. Most EV motors are permanent magnet machines with external stators and internal rotors, with the magnets integrated inside the rotor rather than being surface-mounted, and most often this IPM configuration entails vee-shaped permanent magnets inside a laminated rotor.
“With a spoke motor, you still have a laminated rotor but the magnets stand upwards, like the spokes on a wheel,” Foley says. “The end effect is that it has very high torque and power density.
“Before we developed one, GE wrote a paper exploring the potential of spoke motors, and ZF and Infineon did a large EU project on developing one, but all of them saw major challenges in terms of how to manufacture the rotor cost-effectively, and how to thermally manage it in operations so the magnets were kept cool.
“The solution for both challenges lay in the structure of the rotor. We came up with a novel design – and we’ve used something similar in our larger HTM-3500 motor – where we interlock the rotor with the laminations, making it cost-effective to assemble. We also directly cool the rotor, which allows us to make it out of aluminium, making it much easier to forge and machine than steels or iron.
“Aluminium wouldn’t be suitable if the rotor got hot, because of stresses, but because we incorporate a water-glycol cooling system with a rotating water seal to cool the magnets, it keeps it within a temperature range where the cycle life and fatigue life are okay.”
Silicon carbide
The HTM-3500 is a 400 kW motor that measures 540 mm in diameter and weighs 195 kg. In addition to incorporating some similar technologies to the APM-200, it can be supplied with an 800 V SiC inverter which Equipmake produces.
“Our first SiC inverter was actually for powering electric fuel pumps in a space rocket application, for Gilmour Space in Australia,” Foley recounts. “In e-mobility, SiC is more expensive but much more efficient at power switching, and that greater efficiency means you can get a little more range with a slightly smaller battery pack, offsetting the purchase cost somewhat.”
Also, where SiC is not used for the HTM-3500, twin inverters running on silicon IGBTs power the motor instead. Essentially that means SiC halves the physical footprint of the inverter in the powertrain.
“That can be reduced even further if you integrate the motor and inverter together of course, but I don’t think integration works in every application,” Foley says. “If you think about two-in-one packages from a maintenance point of view for instance, a change or repair of one component requires taking the whole system apart, and even designing them for integration often requires major changes to both.
“But of course, cabling and connector costs can be reduced via integration, as can weight. Most people buy inverters as modules, and a lot of each module is just connection or interfacing parts, so it’ll be interesting to see how people come up with integrated SiC solutions more and more going forwards.”
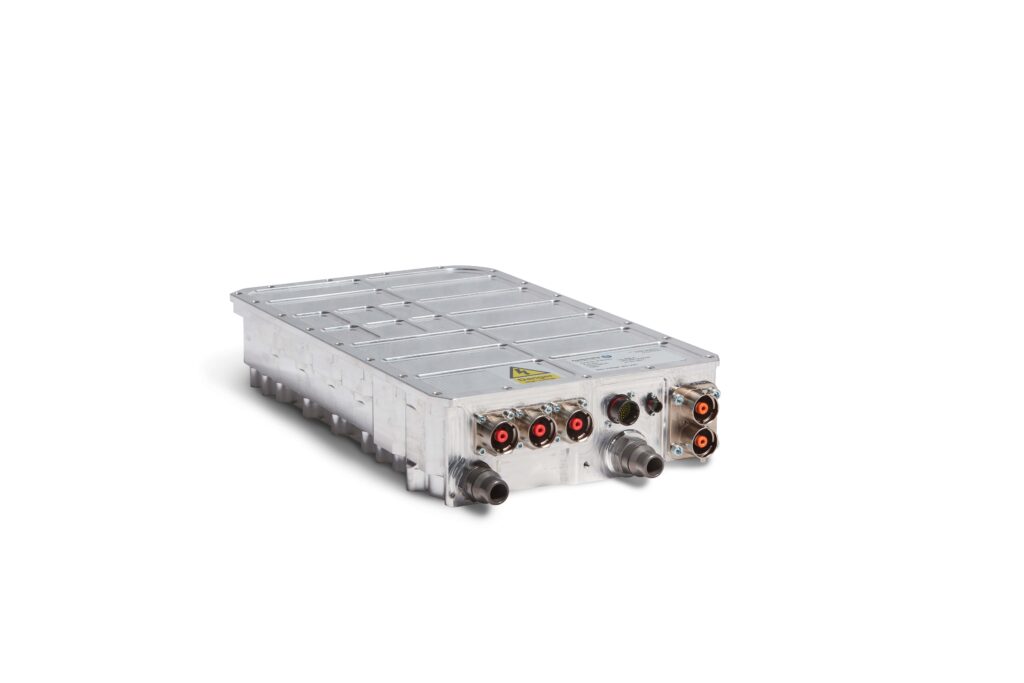
Metal additive manufacturing
A lot of additive manufacturing (AM) has been used in the design and production of another of Equipmake’s motors, the Ampere-220, specifically for parts that cannot be manufactured using conventional forging, stamping or cutting.
“It all came down to cooling, which again is key to ensuring a motor can run near the top of its power output for long periods without losing current to heat or suffering fatigue from thermal expansions and contractions, but as the Ampere-220 runs at 30,000 rpm to the APM-200’s 10,000 rpm, running water through it via a rotating seal was unfeasible, the seal just wouldn’t work,” Foley explains.
“Instead, an internal heat exchanger is printed using aluminium on the face of the Ampere-220’s high-strength steel rotor, which essentially means it works as a fan, rapidly recirculating air inside the housing and against a water-glycol radiator. It is so fast that it’s actually very effective at keeping everything inside the motor quite cool, and getting that air scooping and flow right was only really possible through AM of that heat exchanger and its blades.”
In the future, Equipmake plans to explore and exploit other uses for additive printing. In one project, it is working with an unnamed AM machine producer that has been able to print copper in a controlled and repeatable way.
“Doing that using any material with high thermal conductivity is challenging, particularly if the laser used for sintering causes a dissipation of heat through the powder,” Foley says. “But the machine producer’s capability means it could be possible to print stator windings in really bespoke ways.
“Often, copper losses get worse as you get closer to the rotor magnets, so if you can tailor winding shapes to deviate from how the windings tend to be formed, there’s potential for great gains in power density and efficiency. It’s just a matter of finding out whether it’s cost-effective through AM.”
The company also sees great potential in motor control and architecture techniques that could enable faster speeds and hence higher power. That though will bring greater imperatives for cooling advancements, for which Foley views AM and SiC as being key to unlocking greater thermal efficiency across electric powertrains.
Rare earths
Equipmake uses neodymium and samarium-cobalt grades across its PMAC motor portfolio. The former includes additives such as terbium and dysprosium for enhanced performance at high temperatures, while the latter also retains good performance qualities across some elevated temperatures.
“We have also developed a motor using ferrite magnets, where size wasn’t an issue,” Foley says. “That’s interesting to think about, because there’s a perennial challenge around neodymium supply chains and costs.
“There are ongoing developments to try to reduce the amount of particularly expensive additives in rare earth magnets, but to be honest I think the problems will be solved through the supply chain before any breakthrough in ferrite or other non-rare earth elements.
“When demand gets urgent, people tend to go out and find resources. It used to be said in the 1980s that by the 2000s we’d have run out of oil, but in an analogy even the head of OPEC back then commented, ‘The Stone Age didn’t end because a lack of stone’. People found better materials, and that’s what’s going to happen to oil as EVs supersede IC-engined vehicles.
“Also, rare earths just aren’t as rare as people sometimes think. If you think of lithium mines for making battery packs, they used to be few and far between, but now there are two in the UK, Australia’s found a load and India has too.
“The massive global demand for lithium now means people have tried that bit harder to find sources of it. Even though mineral resources are finite, new resources always tend to be found when the demand is high enough.”
Beyond this, Equipmake also sees great potential for accumulating magnets through the circular economy, with technologies for recycling and remagnetisation of permanent magnets already on the horizon.
Equipmake’s partnerships and projects
To date, the company’s electric propulsion solutions have been used in various EV projects, with the best known being their integration into buses such as those belonging to First Group (the largest bus operator in the UK), as well as an iconic red double-decker Routemaster bus belonging to Transport For London, which at the time of writing was undergoing trials.
“There’s a general acceptance that replacing buses outright with new electrified OEM models isn’t feasible in terms of time or funding. There are something like 30,000 large buses in the UK, maybe 3 million in the world, and most of them last at least 15 years,” Foley says.
“So there’s a wave of encouragement for converting buses that are around halfway through their life, and our ZED [Zero Emission Drivetrain] solution has been optimised for installing into existing or new buses alike. That includes one bus manufacturer in South America, and some customers building electric fire trucks.
Notably, the 750 V ZED bus powertrain uses the HTM-3500, rather than the APM-200. Foley says the APM-200 is ideal for high-torque, high-power applications, but buses generally have a high-torque, low-power duty cycle.
“IPM rotors also exhibit more reluctance torque, which is better for bus applications, but mainstream automotive needs a better balance between torque and power, and that’s where the APM-200 comes into its own,” he says.
“The HTM-3500 is however much smaller and lighter than many other electric motors of its power output, primarily because we optimised it for our bus integration projects. That shrinkage though means we can use it to repower vehicles in a way that we couldn’t if we’d bought competitors’ motors.”
The HTM-3500 is designed and manufactured using a segmented approach, which avoids the exorbitant cost of stamping such a large-diameter rotor. That helps with bulk orders and integration costs for bus fleet managers.
In addition to Equipmake supplying to integrators across the UK and the Americas, a licensing agreement has recently been signed with Sona Comstar in India for the latter to manufacture some of Equipmake’s motors and inverters for the growing Indian EV industry. Also, in late June this year, Equipmake announced it will be working with Switzerland-based H55 to produce a motor for its electric aircraft.
“H55’s EV will be a single-engined propeller aircraft, to be aimed primarily at the pilot training market, but we anticipate it’ll be the first aircraft of that class to be fully electrified,” Foley says. “It’s not the first aircraft we’ve delivered motors to, we’re also the supplier for a leading EVTOL manufacturer, with their prototype using our motors and inverters.
“The eVTOL market is an interesting one. For those, our motors tend to use a particular design of SPM [surface permanent magnet] rotor, because in that use case the torque density – specifically, torque versus weight – is more important than cost.
“That approach wouldn’t be viable in other applications due to cost, but in aerospace the weight is so important that SPM designs often wind up being worth it. That’s important for eSTOL, single-propeller designs like H55’s as well, so we tend to go with a similar design for those kinds of integrations.”
Future plans
Having recently started scale production, Equipmake plans to refine its manufacturing capabilities. Initially that will not be for the hundreds of thousands of units that large companies such as Bosch produce, but more for orders of hundreds of units at a time, which is more typical of the EV industry at the moment.
“As the industry grows and EVs get built in greater batches and with lower costs, we’ll ramp up in similar way, so in a couple of years we’ll be producing orders in the thousands per year, and maybe tens of thousands per year in 10 years’ time,” Foley says.
“We tend to develop motors for specific markets, rather than having a ‘standard range’; our HTM motor for instance was made specifically with buses and trucks in mind. But there are plenty of applications ripe for exploring in e-mobility, and to that end we’ve obtained a 50,000 sq ft facility to double our capacity and workforce within the next couple of years.
“We’ll definitely carry on with our r&d though. Staying at the cutting edge of power density will depend on keeping abreast of the latest advances in supply chains, power switching and thermal management.”
Ian Foley
Ian Foley was born in Liverpool, England, and after his primary and secondary education in the Liverpool area he went on to study at Coventry Polytechnic (renamed as Coventry University in 1992) for his Bachelor’s Degree in Electrical and Electronic Engineering. Soon after, he studied for a Master’s at Cranfield University, also in England, in Control Systems Engineering, which he achieved in 1988.
Later that year he began working as a development engineer in Lotus Engineering, on active steering and suspension systems. He soon moved into racing, first as head of r&d for Team Lotus F1, then as director at GTI Lotus Racing, before founding Equipmake as managing director in October 1997; he has been at the company since then.
During that period, he also founded and served as managing director at Williams Hybrid Power from 2007 until 2014, when it was acquired by GKN. He continued to work for the company (rebranded as GKN Hybrid Power) for 2 years as business development director.
ONLINE PARTNERS
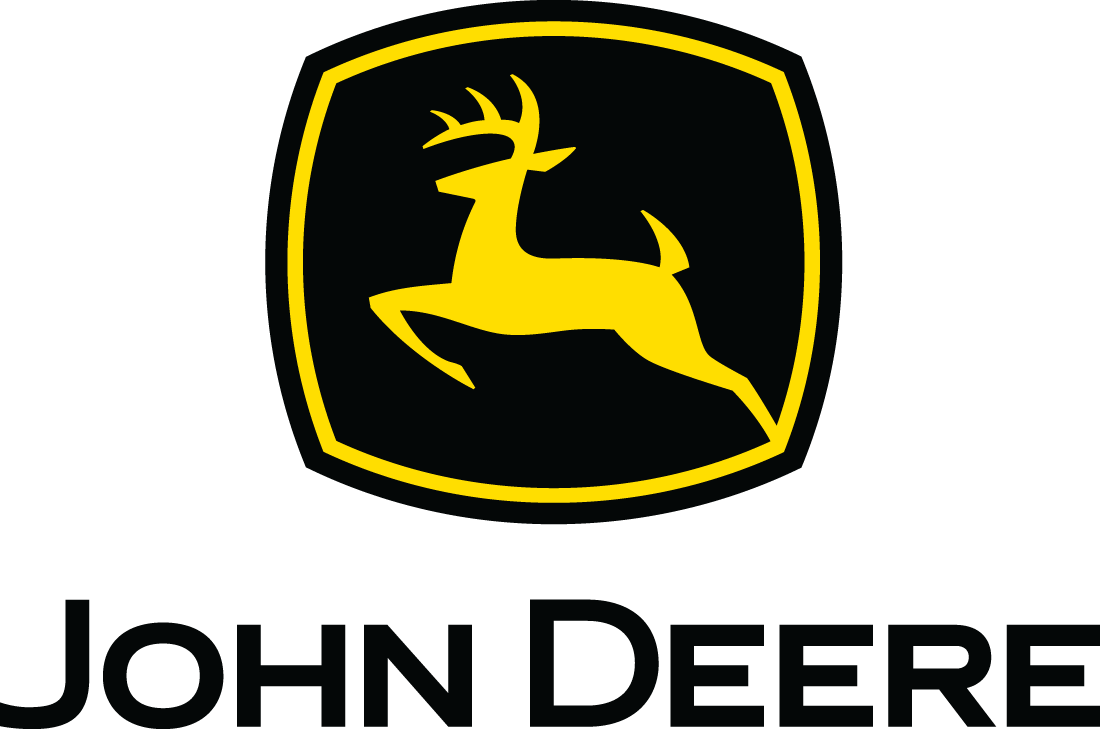
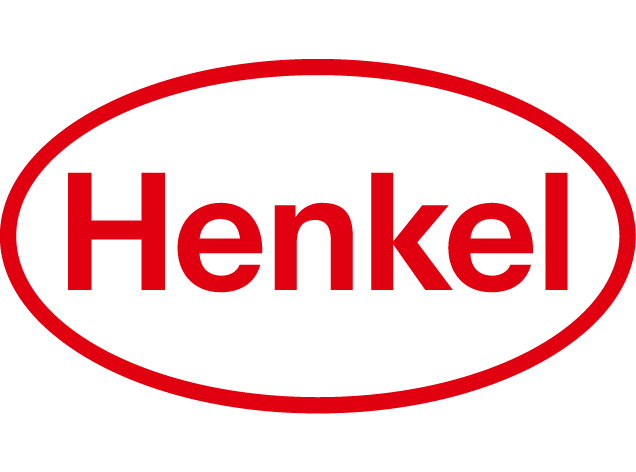
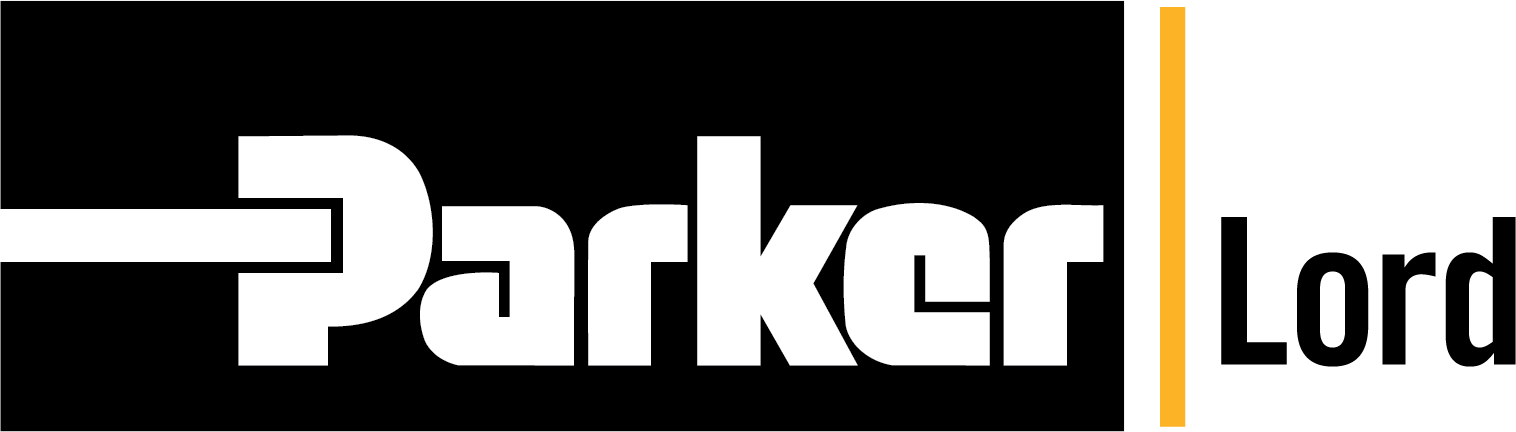
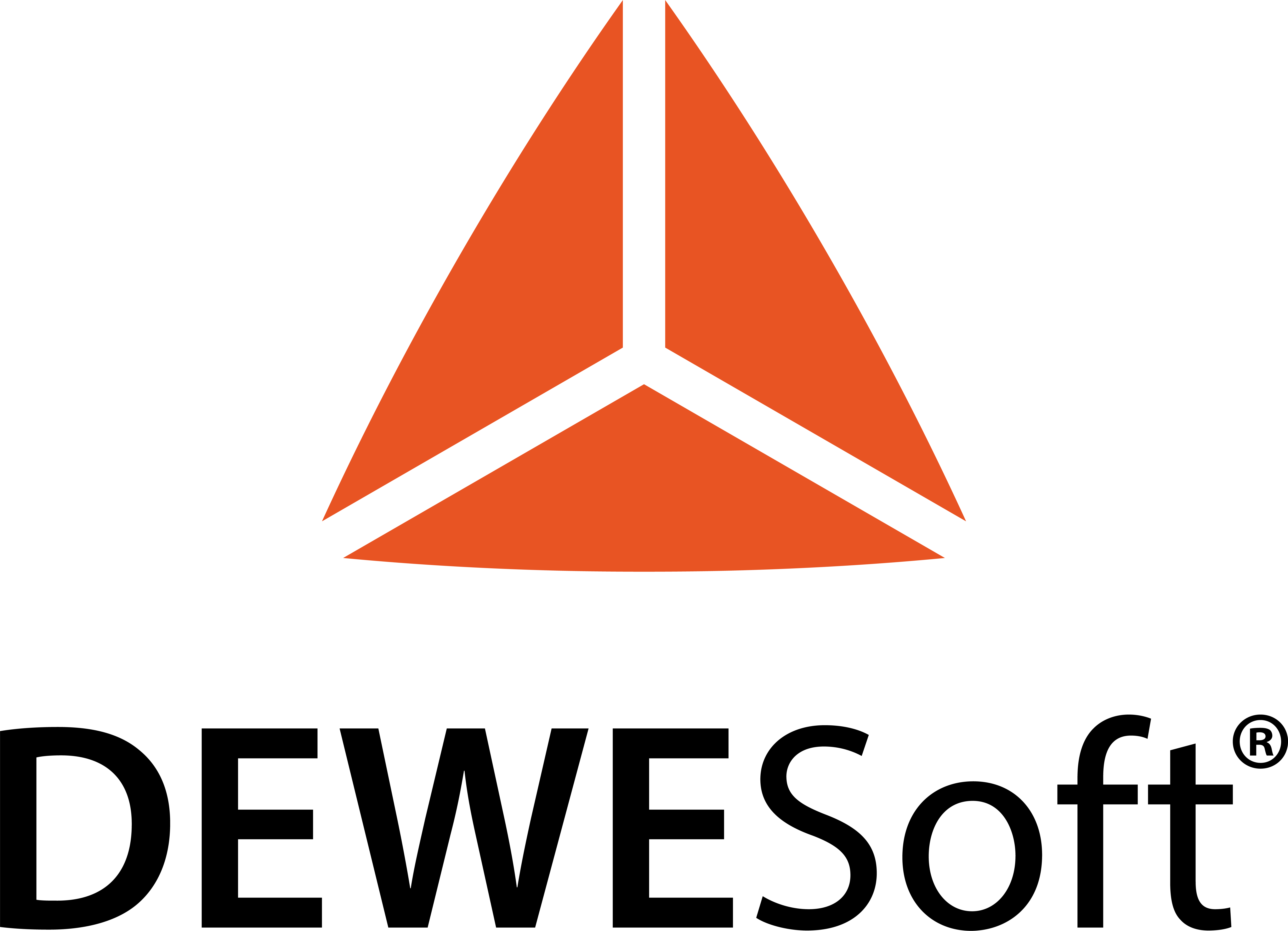
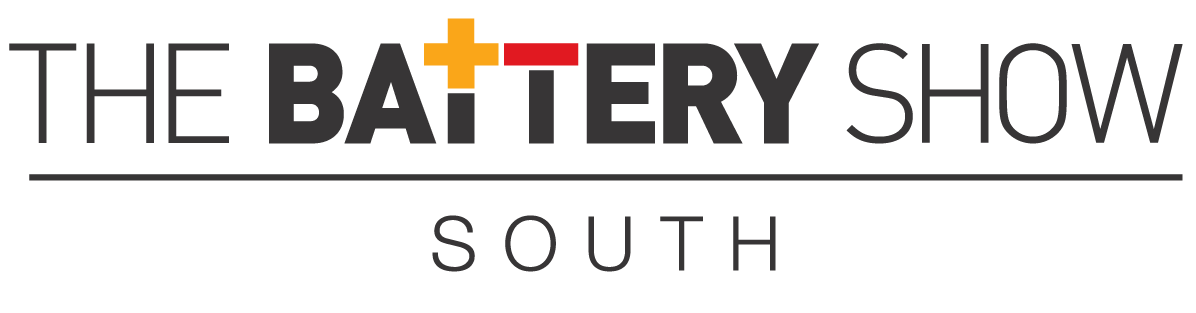
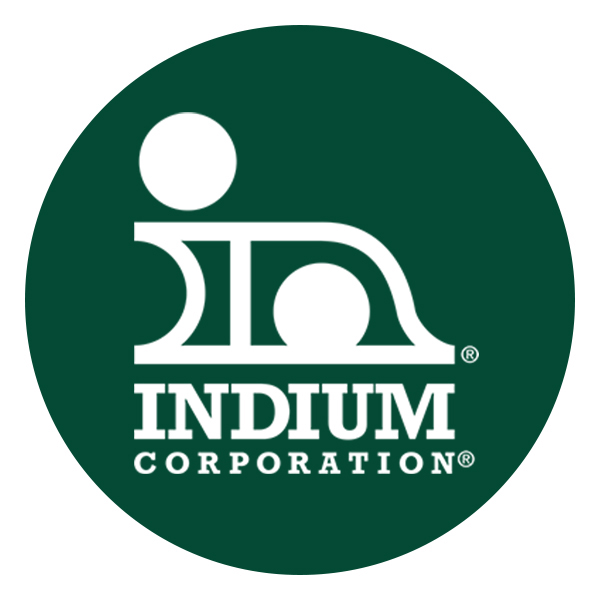

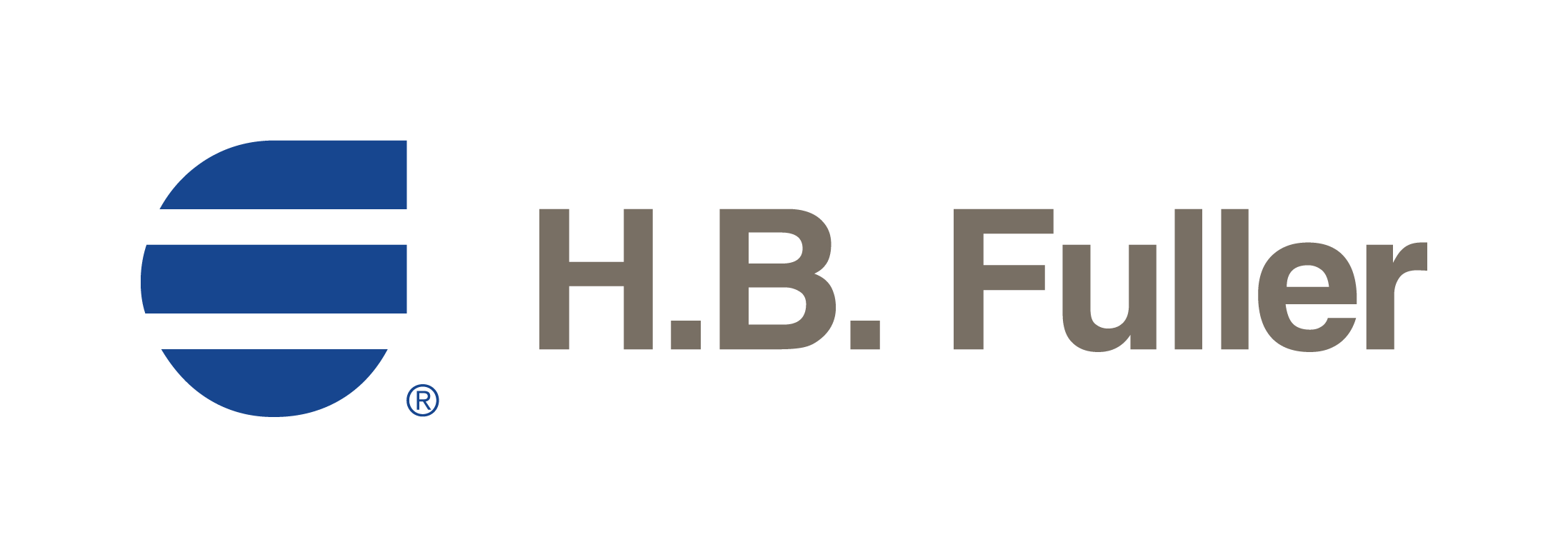
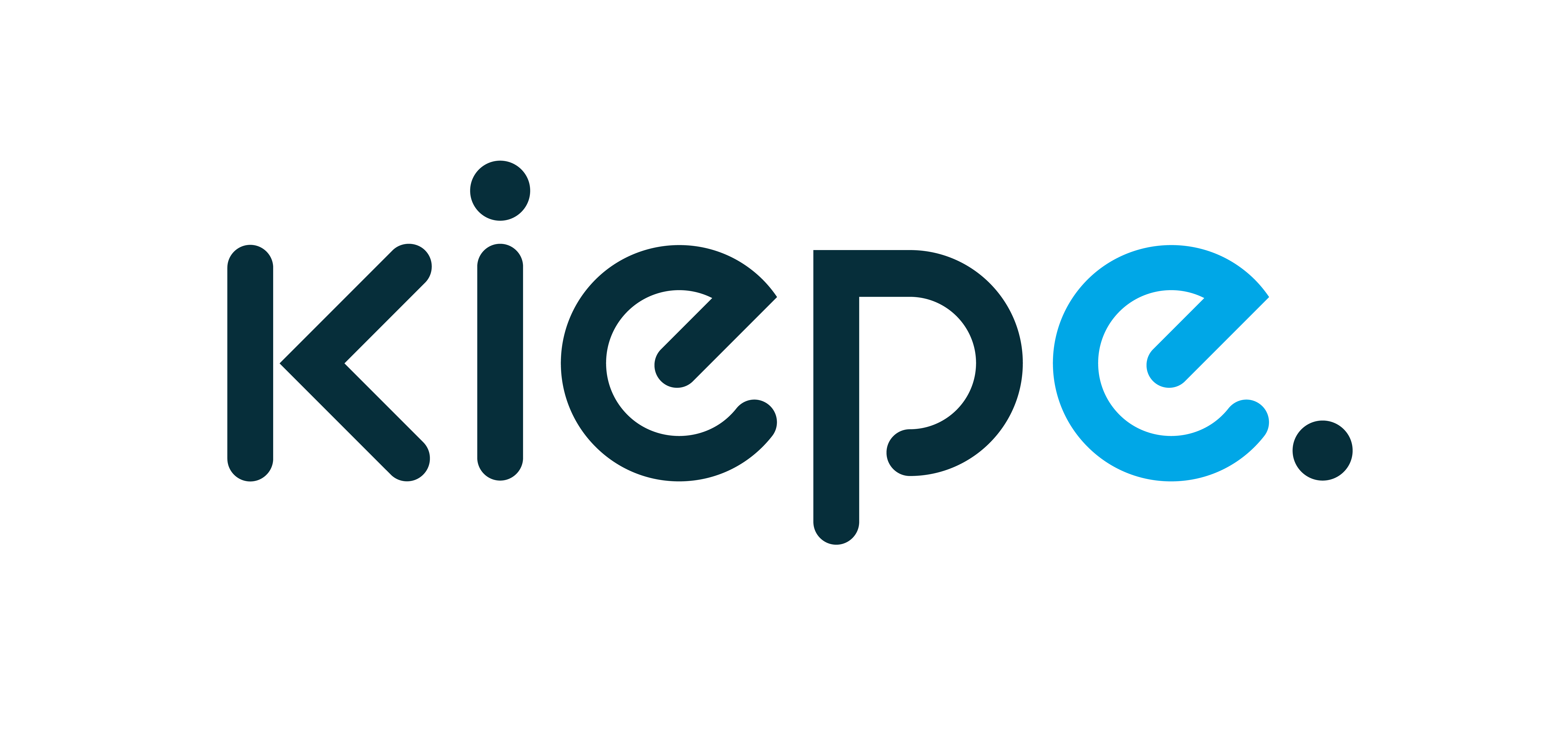
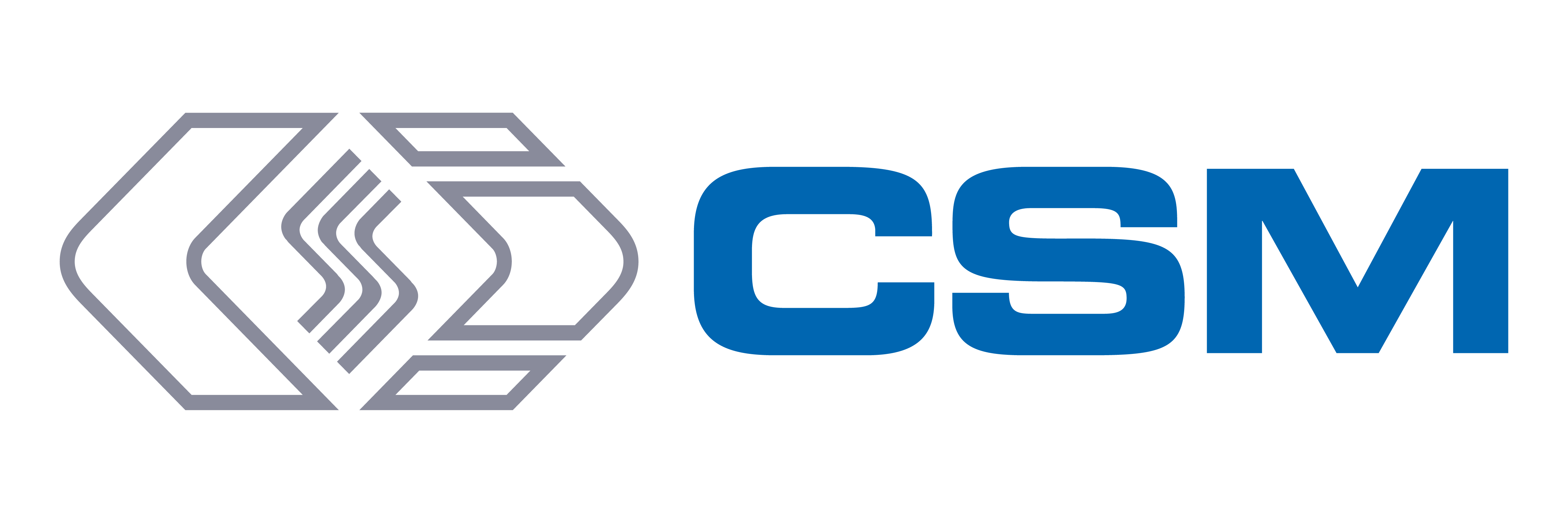