Modular batteries
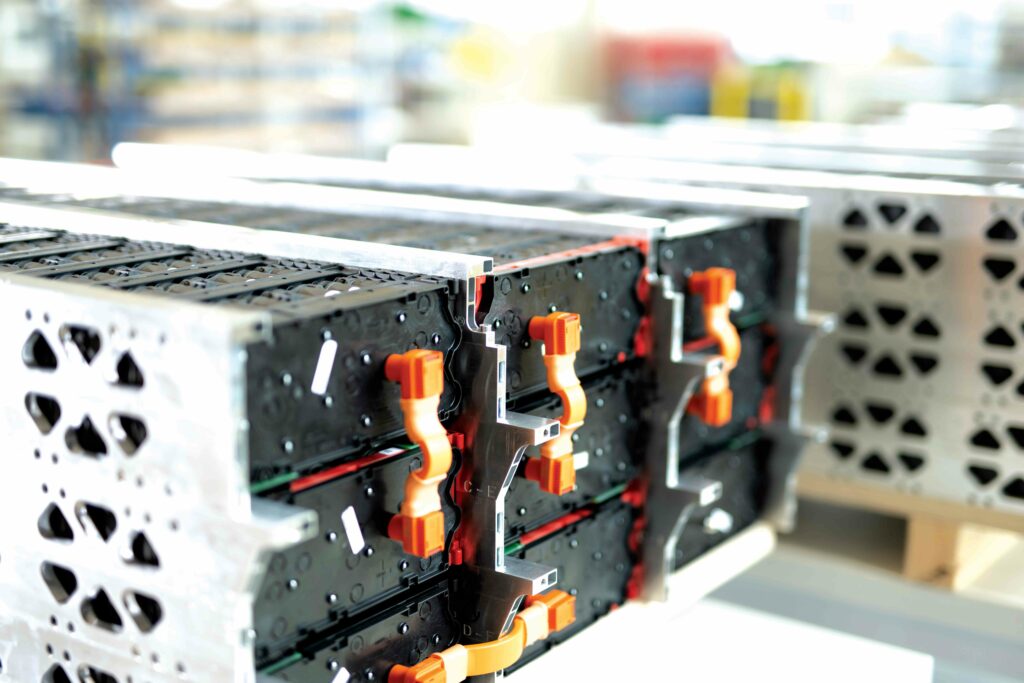
(Image courtesy of Kreisel Electric)
Modular magic
In optimising modular battery technologies, it’s important to harmonise design and control. By Peter Donaldson
Modular battery systems remain an essential component of e-mobility, offering unique advantages that complement recent advancements in cell-to-pack (C-t-P) technologies. While C-t-P designs optimise energy density by eliminating modules, modular batteries provide critical flexibility, scalability and serviceability. Engineers navigate complex trade-offs to integrate these features while addressing challenges in cost, weight, thermal management and recyclability.
One of the most prominent benefits of modular batteries is their inherent flexibility. Modular systems use pre-configured units as building blocks, enabling manufacturers to adapt battery packs to various sizes, shapes and applications. This adaptability is particularly relevant for lower-volume production or specialised EV sectors, such as off-highway vehicles, marine applications or industrial machinery. By standardising modules, manufacturers can cater to diverse needs efficiently without extensive re-engineering.
For example, a modular approach enables rapid scalability of battery packs to meet varying energy and power requirements, often by adding or rearranging modules. This modularity supports design iteration with minimal disruption to manufacturing lines, making it easier to accommodate changing customer specifications and emerging applications.
Additionally, these systems simplify the validation and certification process, because once a module has been certified, it can be reused across various configurations, reducing the overall time and expense of bringing products to market.
Modularity also has benefits for battery manufacturers if they have sufficiently flexible production systems. Traditional battery pack production lines are often expensive and inflexible, as they are built to cater only for one specific design, while C-t-P architectures tend to drive costs even higher due to their specialised tooling and machinery. However, with a module-based system, a single production facility can cater for several different customers, significantly reducing both time and cost to market.
From a sustainability perspective, modular batteries contribute to more efficient end-of-life management. Modules can be removed, refurbished or repurposed with relative ease, supporting re-manufacturing and recycling efforts. This reversibility reduces waste and enhances the environmental benefits of EV adoption.
Modular systems also provide a serviceability advantage. In the event of a failure, specific modules can be replaced without discarding the entire battery pack. This reduces downtime for fleet operators and individual users alike, particularly in commercial applications where reliability is paramount. Furthermore, modular designs allow for the integration of diverse cell chemistries to suit different performance and cost priorities.
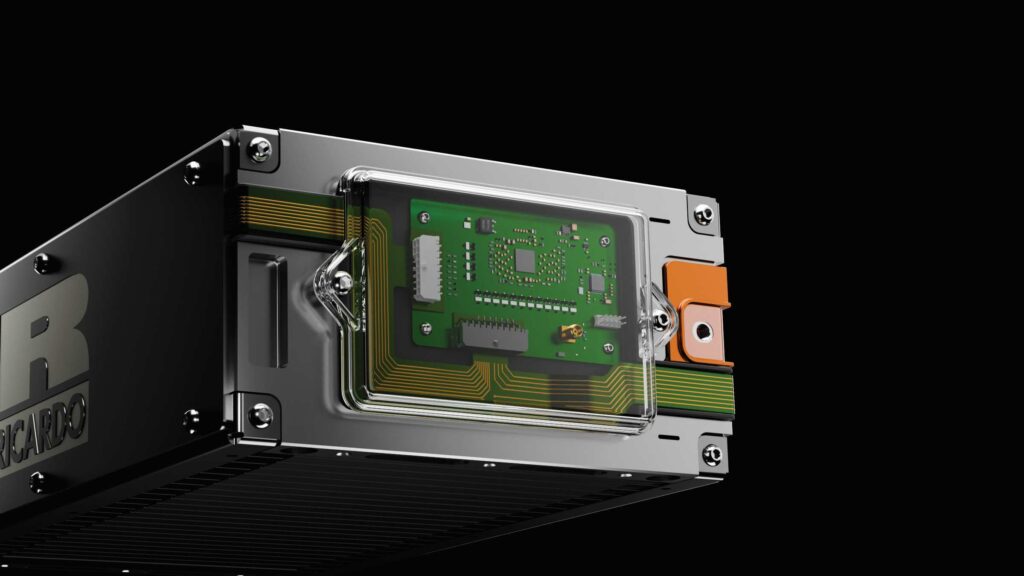
(Image courtesy of Ricardo)
Evolving role
Design philosophy is evolving in response to industry demands for higher energy densities, reduced costs and improved manufacturability. Innovations in modularity aim to narrow the gap between the performance of modular systems and C-t-P designs.
For instance, smarter module designs now achieve energy densities comparable to C-t-P systems by optimising the structural integration of cells and modules. Advanced manufacturing techniques simplify assembly, reduce the parts count and enhance structural efficiency.
The industry is also exploring hybrid approaches that combine modular principles with C-t-P elements. For instance, large-format cells can be grouped into stackable units that function like modules but offer the packing efficiency of C-t-P designs. This hybrid approach delivers the flexibility of modular systems while maximising energy density and minimising material costs.
Applications beyond the automotive sector are increasingly driving innovation. Off-highway, heavy-duty and marine vehicles often require highly adaptable battery systems that are capable of enduring long operational lifetimes. In these sectors, repairability, scalability and future-proof design take precedence, making modular solutions an attractive choice.
Smaller manufacturers or those without extensive in-house battery expertise are also benefitting from modular solutions in the form of ready-made systems that enable rapid electrification of existing platforms, bypassing the investment and time required to develop bespoke battery designs. As the market diversifies, modular systems continue to play a critical role in accelerating the adoption of e-mobility across various industries.
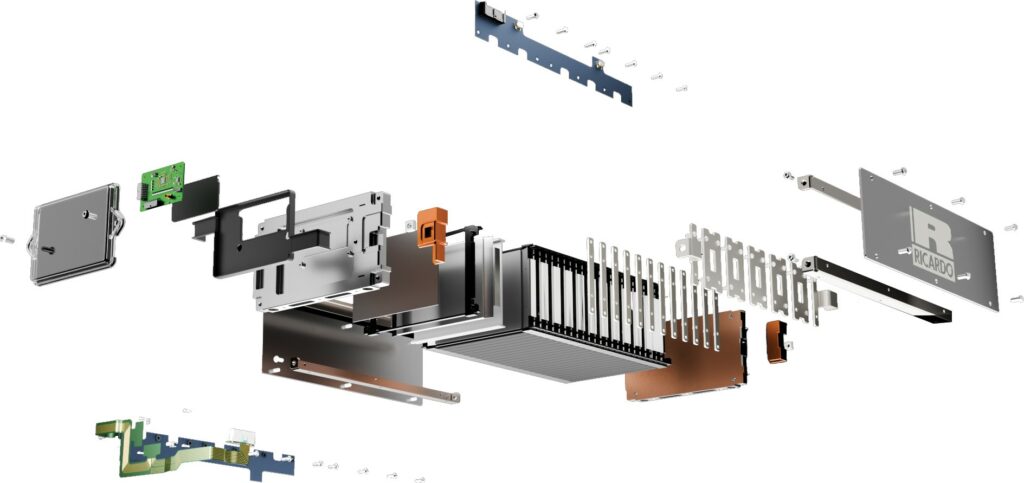
(Image courtesy of Ricardo)
Complex trade-offs
Designing modular batteries involves navigating a complex matrix of engineering trade-offs. The key challenges revolve around balancing energy density, thermal management, cost and system complexity while maintaining safety and performance.
The inclusion of modules inherently reduces the overall energy density of the battery pack. Modules add inactive material – such as enclosures, connectors and cooling infrastructure – that does not contribute to energy storage. This is a significant trade-off compared with C-t-P systems, where cells are packed more densely, maximising volumetric and gravimetric efficiency.
Effective thermal management is critical for both safety and performance. Modular systems allow for the segregation of cells, which can help to contain thermal runaway events, but this segregation can increase weight and complexity, so cooling systems must be designed to dissipate heat efficiently without compromising energy density or structural integrity. Some systems are exploring immersion cooling or integrating liquid cooling channels within modules to improve thermal performance.
Cost is a pervasive consideration in all battery designs. Modular systems typically involve more components and assembly steps than C-t-P designs, which can increase manufacturing costs. However, these costs can be offset by the economies of scale achievable with a standardised design system that allows for rapid adjustment of the module’s final design and cell configuration before committing to manufacture. Advanced automated design tools further reduce costs by accelerating the design process and minimising manual iteration.
The serviceability of modular systems is a major advantage, but introduces its own challenges. Engineers must ensure modules can be removed and replaced easily without compromising the structural integrity of the pack. This often requires additional design elements, such as reinforced housings or accessible interfaces, which add weight and complexity. Balancing these requirements with the demand for lightweight, compact designs is a constant challenge.
Safety remains paramount in all battery designs, and modular systems are no exception. Engineers must carefully consider how to isolate and protect cells within a module to prevent cascading failures in the event of a thermal incident. The structural design of the module plays a crucial role in this regard, providing containment while ensuring heat and gases can be vented safely.
While modular systems excel in scalability, achieving optimal performance often requires customisation. Applications with specific power or energy requirements may demand tailored configurations, which can increase development time and cost. Engineers must weigh the benefits of a standardised, modular approach against the potential gains of bespoke designs.
The evolution of modular battery technology for EVs is marked by diverse innovations in packaging, thermal management and electronics integration. As energy density approaches the theoretical limits for current chemistries, efforts are increasingly being focused on refining the way battery cells are organised into modules, offering flexibility, safety and cost-effectiveness. Engineers in the EV industry are navigating a rapidly maturing landscape where technology and economic pressures are shaping module design.
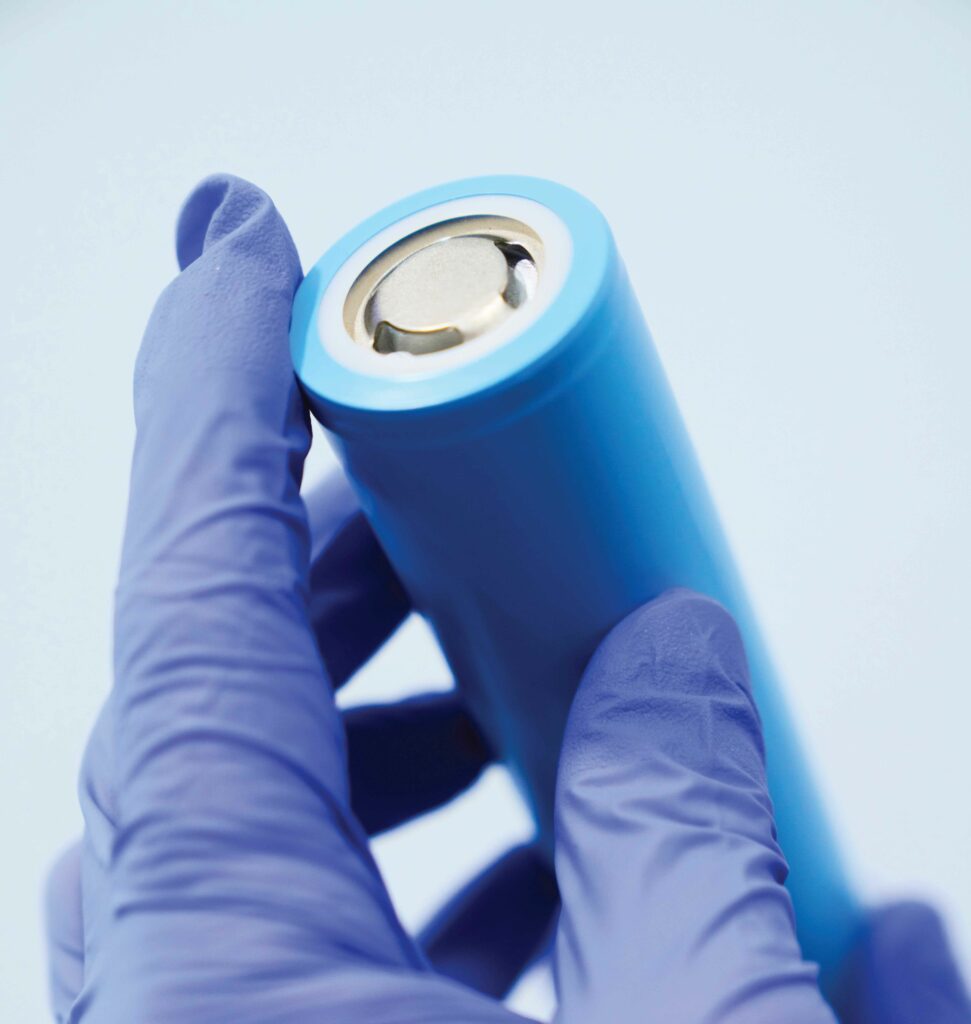
(Image courtesy of About:Energy)
Designs on flexibility
The integration of modularity within battery systems plays a crucial role in balancing the demands of diverse vehicle applications, from buses and trucks to offroad vehicles. Modular designs enable manufacturers to use a combination of different cell chemistries and form factors within the same platform, although this has not yet become common practice.
For instance, prismatic lithium-ion phosphate (LFP) cells, known for their safety and stability, can be integrated alongside cylindrical cells, which may use higher energy-density nickel manganese cobalt oxide (NMC) chemistries, potentially offering a range of options tailored to energy content, lifespan and total cost of ownership.
The adoption of modular hardware and software architectures allows seamless integration across applications, supporting compliance with regulations and cybersecurity standards. This adaptability helps manufacturers address cost constraints while maintaining high quality and performance. They can achieve economies of scale, even in lower-volume applications, enabling the EV sector to compete with the cost structures of diesel vehicles.
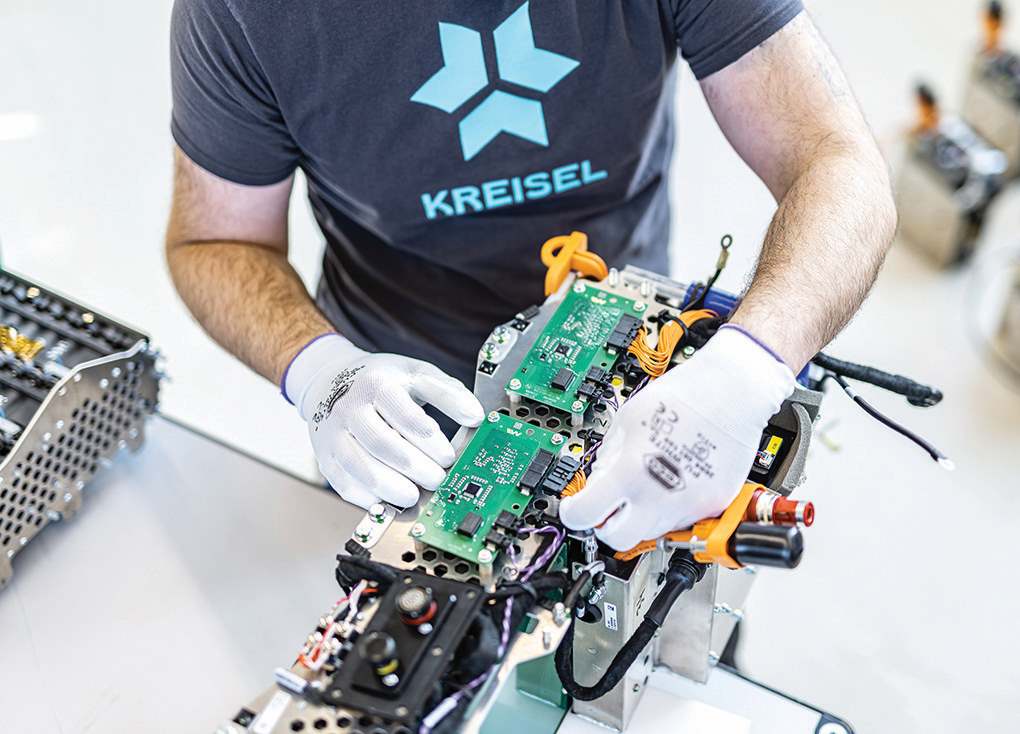
(Image courtesy of Kreisel Electric)
Thermal management
Thermal management remains a cornerstone of modular battery design and multiple factors affect it. One is cell form factor, with smaller, cylindrical cells potentially offering better cooling efficiency, while larger, prismatic and pouch cells sometimes complicate cooling and need structural allowances for swelling. However, the impact of cell form factor on thermal management must be considered alongside cell specifications, other specific applications and battery pack design.
Innovative materials and structural designs are being developed to address these challenges. Lightweight polymer composites are increasingly replacing metal casings to reduce weight while maintaining robustness. Simplified internal wiring and fewer welds also enhance thermal stability by minimising heat generation at electrical connections.
Also, C-t-P and cell-to-chassis architectures free up space for thermal management hardware.
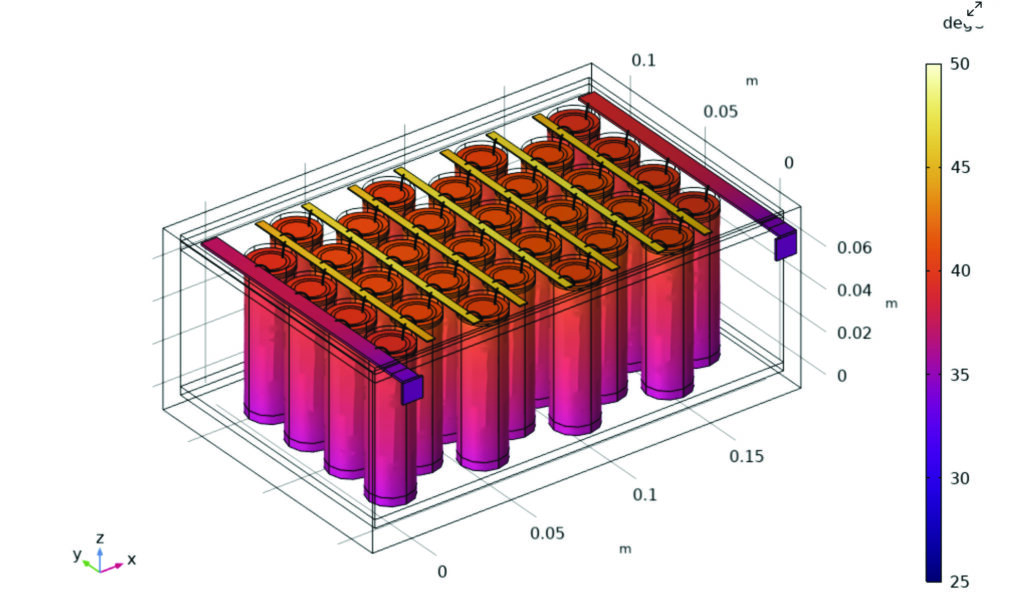
(Image courtesy of About:Energy)
Cell-to-pack limitations
The push towards C-t-P architectures brings a number of advantages over modular designs in some applications. By eliminating intermediate module structures, this approach enhances volumetric efficiency and reduces weight.
LFP cells are particularly conducive to C-t-P designs due to their inherent stability and tolerance for larger cell sizes, while high energy-density NMC cells are constrained by safety considerations. Intermediate-sized, cylindrical cells such as those made in the 46XX format are making strides in C-t-P applications.
Such designs enhance sustainability by reducing material usage and simplifying recycling processes. For example, integrating batteries directly into the chassis of vehicles, known as ‘cell-to-chassis’, represents the next frontier in modularity – reducing the number of components and streamlining the assembly process by focusing on direct electronic and thermal connections between the cells and the vehicle.
However, while C-t-P and possibly cell-to-chassis architectures can work well in the automotive sector because cars can be designed around the battery pack, this is impractical in other sectors such as ships, boats, agricultural machinery and off-highway vehicles. The latter two, in particular, have been developed over the last century to work as well as possible and there is little or no scope to redesign them around a battery, leading to them being fitted with modular, multi-pack systems (although these packs may use C-t-P architectures).
Another consideration is service life. Unlike cars, which may be built for service lives as short as seven to 10 years, marine, agricultural and off-highway vehicles may work for 30-50 years, so the serviceability and repairability that come with modular architecture are even more important.
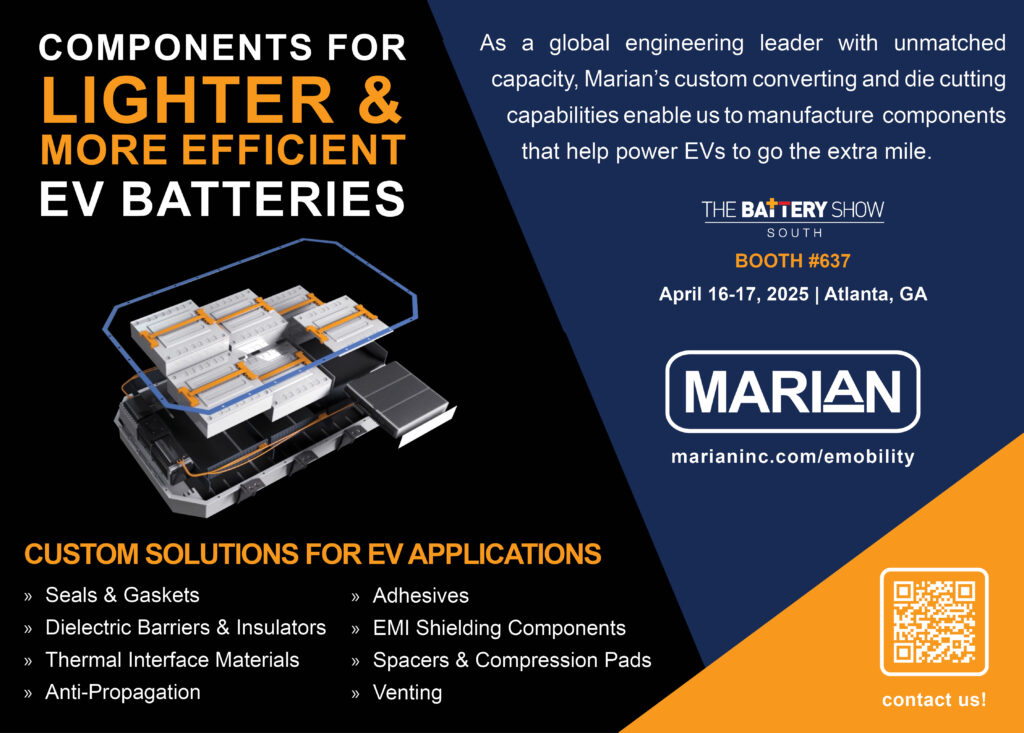
Cell chemistry
Cell chemistry affects module design in terms of energy density, safety and thermal management. High energy-density NMC cells require robust systems to control thermal propagation, whereas LFP cells offer design simplicity and higher safety margins. Silicon-based cells, despite their high energy potential, face challenges with volumetric expansion, necessitating structural adjustments within modules to accommodate swelling forces.
Cell-form factors are closely tied to chemistry, influencing design choices. For high-power applications, cylindrical cells often outperform prismatic formats due to their mechanical resilience and better cooling efficiency. Modular architectures of standardised design, which incorporate features such as adjustable cooling channels or flexible cell-expansion spaces that can be tweaked before production, can be optimised for specific chemistries and applications. While integrating such flexibility upfront requires more work, in the long term it saves time and money while reducing risk.
Safety remains a critical consideration, guiding design decisions at every level. Modules must be engineered to prevent thermal runaway and ensure safe operation, even in the event of cell failure. For example, designs that isolate failing cells and prevent propagation across the module can allow vehicles to remain operational and be transported safely for service.
Thermal propagation safety is critical, and advances in materials and layouts enable systems to withstand extreme conditions without resorting to controlled burn scenarios. Smaller cells with enhanced cooling capabilities, such as the 21700 cylindrical format, offer a practical balance between safety and energy density.
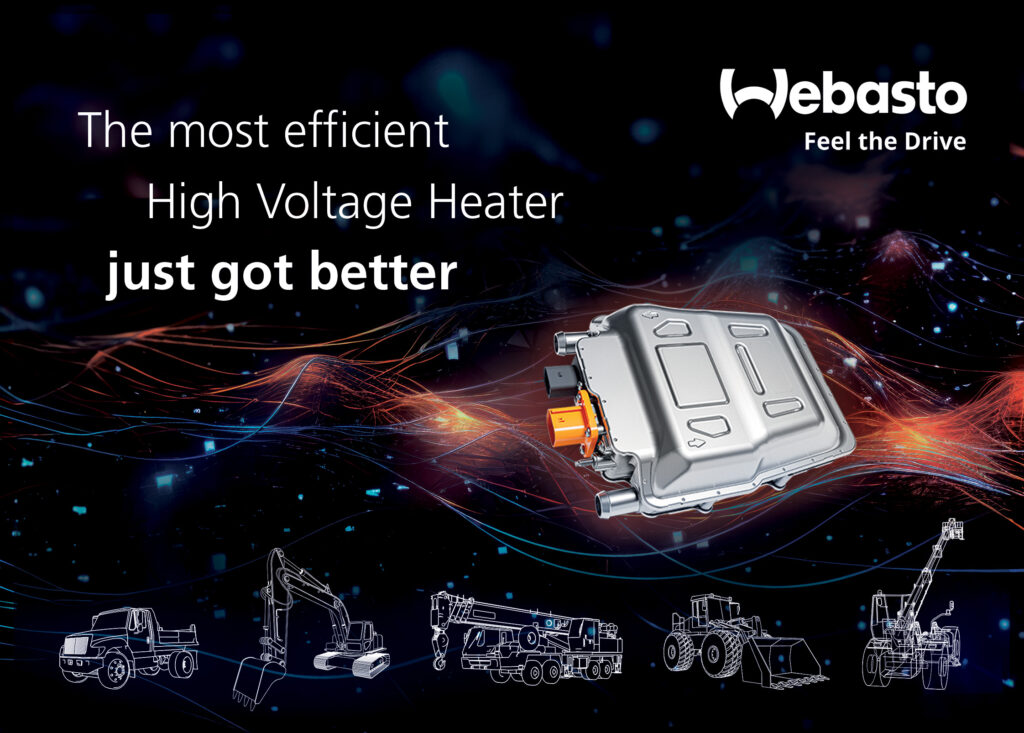
Advanced BMS integration
Battery management systems (BMS) are undergoing a significant evolution, particularly in modular designs. Wireless BMS technologies are emerging as a key innovation, offering remote monitoring capabilities and reducing the complexity of wiring within modules. These systems provide real-time data on cell health, temperature and state of charge, improving overall reliability and enabling predictive maintenance.
Modules increasingly include basic cell-monitoring units (CMUs) for internal measurements such as voltage and temperature. This modular, self-monitoring capability supports second-life applications and preventative maintenance by retaining operational histories and health metrics. However, higher-level functions, such as state-of-charge calculation and pack protection, are typically managed at the pack level for reasons of cost and efficiency.
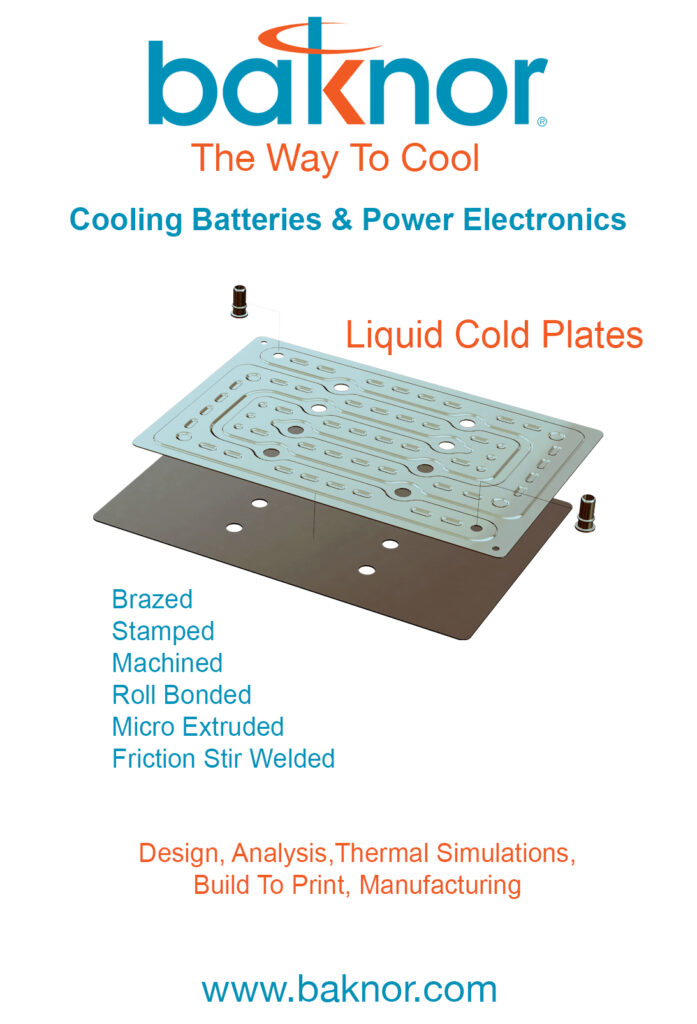
Pack-level functionality
The degree of self-sufficiency within modules varies, based on application requirements. While some designs prioritise fully independent modules with integrated BMS and safety features, others lean towards simpler modules that rely on centralised, pack-level management systems. This balance depends on factors such as cost, complexity and the specific needs of the vehicle platform.
For example, duplicating advanced electronics across multiple, small modules can drive up costs unnecessarily, making it more practical to centralise these functions. However, some level of modular autonomy, such as temperature and voltage monitoring, is essential for effective operation and maintenance.
Modular designs are increasingly geared towards sustainability and second-life applications. By embedding state-of-health monitoring and operational histories into modules, manufacturers can streamline the reuse and recycling of batteries. This data allows for accurate assessments of residual capacity and facilitates the repurposing of modules for less demanding applications, such as stationary energy storage.
Designs that prioritise easy disassembly and minimal material use enhance sustainability. Lightweight, recyclable materials and standardised components contribute to more efficient end-of-life processing, aligning with global efforts to reduce the environmental impact of EV batteries.
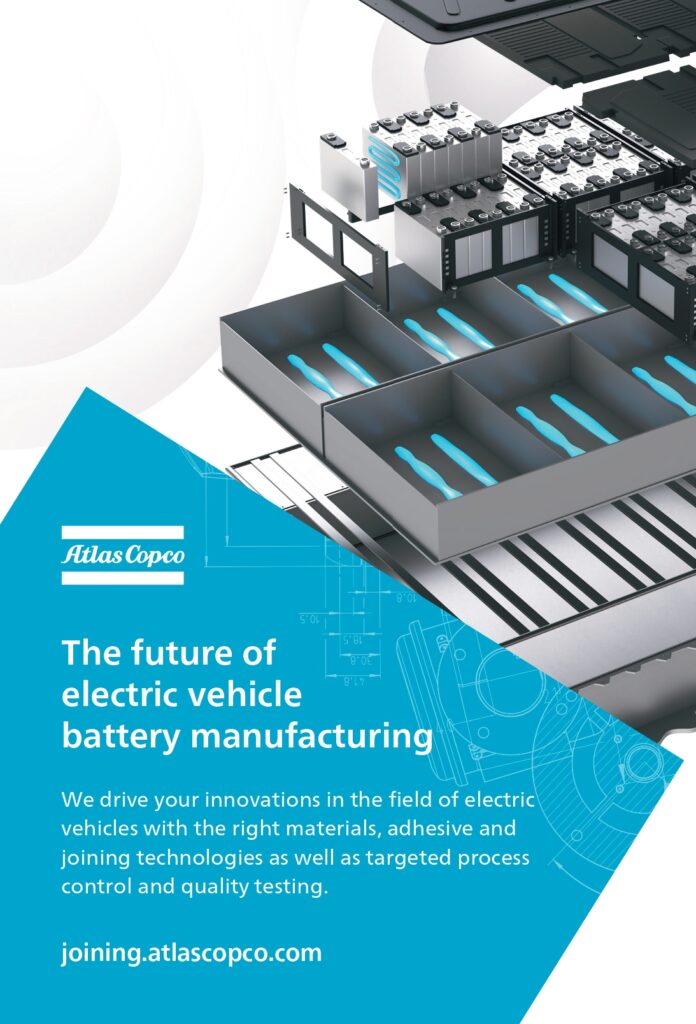
Safety mechanisms
The provision of safety mechanisms within modular battery packs has seen continuous development to meet increasingly rigorous requirements, driven by tightening regulations and the desire of vehicle OEMs to stay ahead of them. Safety measures, such as thermal fuses, venting systems and cut-off mechanisms, are increasingly integrated at the module level to enhance reliability and prevent catastrophic failure. While cell size remains a significant factor influencing these designs, advancements across the board emphasise the creation of safer and more efficient systems.
For smaller cells, safety features such as pressure and temperature-initiated current-interrupt devices (CIDs) and rupture valves are standard, offering robust protection against failure. Cylindrical cells particularly benefit from these integrated safety features, ensuring incidents such as thermal runaway can be mitigated early in the failure chain.
For larger LFP blade cells, safety is maintained through careful structural and thermal propagation inhibition, with some designs extending these protective measures to the pack level for added redundancy.
Engineers are also focusing on fusing cell connectors and incorporating design features that inhibit thermal propagation directly into the module design. This modular approach not only enhances safety, but also simplifies manufacturing and maintenance processes. Increasingly, the industry is moving towards the modular incorporation of features that historically resided at pack level, including thermal insulation and free-air volume limitation, to ensure better control over safety while maintaining flexibility in application.
Thermal management
Thermal management is critical in battery modules to maintain optimal operating temperatures and extend battery life. The industry has seen a shift towards designs that integrate mechanical stability and cooling functions. One approach involves using extruded profiles within the module structure that act as both cooling systems and structural backbones. This dual-purpose design minimises the complexity of thermal systems while supporting modularity by allowing straightforward adjustments to accommodate varying pack sizes.
Options for thermal management include passive and active systems. Modules equipped with passive thermal management rely on efficient material choices and structural configurations to dissipate heat naturally. Active systems, on the other hand, employ liquid glycol or refrigerated air cooling to regulate temperature more precisely, and they are often integrated autonomously within the modules, reducing dependency on the pack-level infrastructure.
For applications requiring high precision, individual cooling plates for each module are gaining traction. This modular thermal approach enables better customisation of cell arrangements within the module and supports designs that cater to unique chassis configurations. However, this flexibility often introduces complexity in interconnection and plumbing; a trade-off that engineers must address during the design phase. In configurations with multiple cooling plates, external connections are prioritised to streamline assembly and maintenance processes.
Energy density
The modular design of battery packs inherently affects energy density due to the additional packaging materials and components required. These include void spaces, compression plates and other structural elements, which, while critical, detract from the battery’s volumetric efficiency. Pouch cells, for instance, require compression foam or plates to counteract expansion forces, which reduces the overall energy density of the module. However, these components are necessary for maintaining structural integrity and operational safety.
While volumetric energy density may be compromised, gravimetric energy density can improve in some modular systems due to reduced weight in less dense configurations. This trade-off is particularly evident in applications where battery capacity needs to vary, such as in automotive platforms ranging from entry-level to premium.
The modular approach allows engineers to customise battery configurations without extensive re-engineering, providing flexibility across different use cases while ensuring a baseline level of performance and safety.
In standardising cell sizes, such as the 21700 format, manufacturers can strike a balance between energy and power density. This minimises development time and costs while allowing for the rapid adoption of new cell chemistries or technologies as they emerge. Such modular designs facilitate scalability and adaptability, ensuring systems remain competitive as requirements evolve.
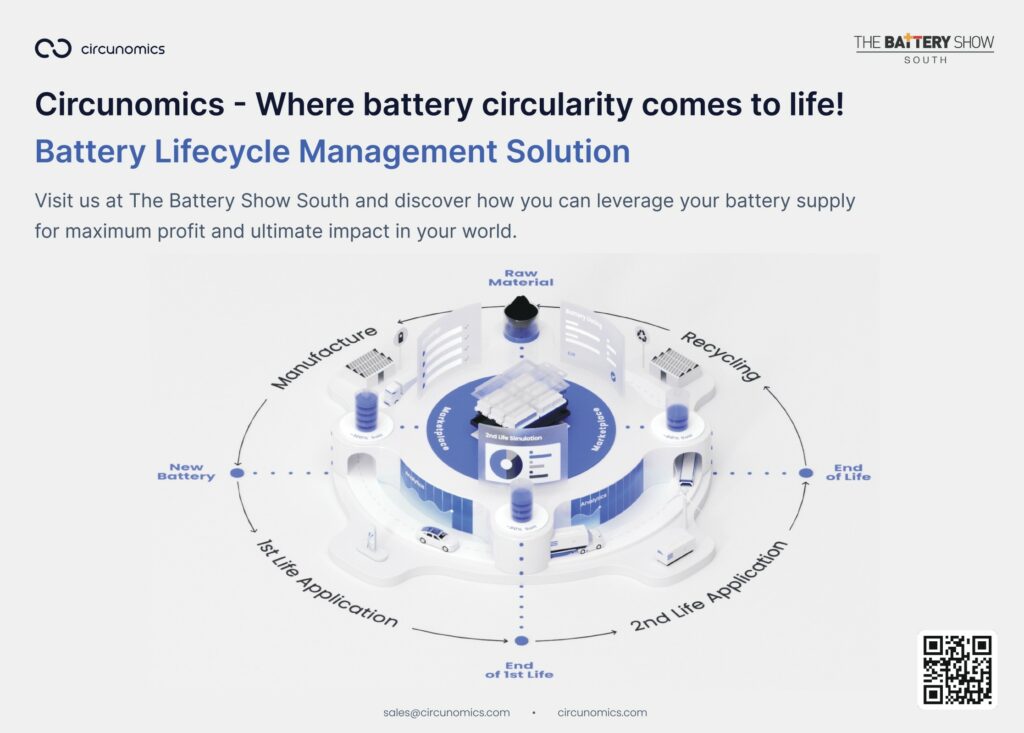
Monitoring and diagnostics
The move towards modularity has not only influenced thermal and structural considerations, but also driven advancements in BMSs. Modern ones incorporate cell-level balancing and diagnostics to predict potential failures and mitigate issues before they escalate. Sensors and control algorithms are critical components, providing real-time insights into the state of health and charge for individual cells and modules. This supports preventative maintenance strategies and extends the overall lifespan of the pack.
Incorporating these safety and monitoring mechanisms at module level simplifies diagnostics and enhances modular autonomy. However, a balance must be struck to avoid overengineering. Excessive duplication of monitoring systems within each module can lead to unnecessary cost increases and complexity. Instead, a tiered approach, where essential safety measures are implemented at module level and overarching controls are managed at pack level, has proven to be more cost-effective and practical.
Modular design also has an impact on fault isolation strategies. By integrating thermal fuses and cut-off mechanisms at module level, defective cells or modules can be isolated quickly, preventing failure propagation and improving the overall safety profile of the battery. Venting systems and pressure-relief mechanisms ensure any failure is contained and managed effectively, reducing the risk of damage to adjacent components.
Performance and efficiency
The inherent flexibility of modular battery packs is a significant advantage, allowing manufacturers to scale systems to meet the diverse requirements of a wide range of applications, from compact EVs to heavy-duty commercial trucks. However, this flexibility must not come at the expense of performance or efficiency. Modular designs must carefully consider the trade-offs involved in incorporating additional structural and thermal management components.
By focusing on common design elements and scalable architectures, manufacturers can reduce production complexities and accelerate time-to-market for new products. This approach supports future-proofing, as modular systems can accommodate emerging cell chemistries and technologies with minimal redesign.
Large-format LFP prismatic cells, while mechanically simple and cost-effective, pose challenges in terms of packaging and state estimation due to their size and unique characteristics. Advances in BMS algorithms are addressing these issues, enabling more accurate predictions of cell behaviour and enhancing the reliability of modular systems. These innovations highlight the importance of harmonising design and control advancements to deliver optimised solutions.
Getting specific
Designing modular battery packs for specific EV applications requires a careful balance of technological trade-offs and innovations. One critical consideration lies in creating modules versatile enough for integration into various vehicle architectures. Smaller modules offer greater flexibility, but compromise specific energy density, volumetric efficiency and cost-effectiveness.
Larger, standardised modules achieve better scale efficiencies and performance, but might not fit as seamlessly into specialised platforms. The decision-making process for module size and design benefits from extensive market studies and optimisation to maximise cross-platform utility, particularly in sectors with smaller production volumes, such as commercial vehicles.
The configuration of modules also has an impact on integration complexity. Adopting a universal cooling architecture is challenging as different vehicle types demand varying thermal management solutions, which highlights the need for early-stage design integration, where strategies can exploit shared heat sources, such as motors and inverters, to enhance efficiency.
Similarly, modular designs benefit from standardisation in cell sizes, which balances performance with cost and simplifies integration.
Another aspect of modular battery development is the trade-off between energy density and installation space. A universal approach introduces compromises. Standardised modules are inherently less space-efficient for niche applications, but their cost advantages, derived from economies of scale, make them an attractive option.
Modular designs tailored for scalability face challenges in maintaining optimal energy density, but despite that they often achieve better gravimetric efficiency due to reduced weight in downsized configurations.
Future directions
BMSs are evolving alongside modular technologies, reflecting a growing demand for smarter and more integrated control mechanisms. Two main architectures have emerged. The first uses a separate ‘master’ controller outside the modular pack, while the second gives every module ‘master’ capability. The first architecture offers greater flexibility and reduced system costs for multiple module applications.
While BMSs have typically always been modular, more robust communication strategies are evolving, along with functional redundancy for safety-critical applications. There is still room for better integration of BMSs into modules to minimise interfaces. Furthermore, a modern BMS should be capable of learning more about the state of the battery and cells in real time, enabling it to make predictions and derive immediate control measures to optimise the battery continuously.
Coupled with physics-based models, increasingly sophisticated algorithms enable real-time data processing, predictive analytics and proactive management of battery conditions. These advancements are crucial in enhancing battery longevity, safety and performance.
Integration of AI into BMS functions is particularly promising, allowing systems to predict failure modes, optimise charge cycles and adapt dynamically to changing operational demands. The inclusion of AI also supports functional redundancy; a critical safety requirement in automotive and high-performance applications.
Because wireless communication simplifies system integration and improves reliability, its wider use within modular batteries and further development of the technology can be expected. Thermal management will remain foundational to modular battery design, with approaches ranging from basic passive to advanced active cooling.
Direct immersion cooling is gaining traction for its ability to maintain consistent thermal conditions across cells, resulting in longer lifespans and improved energy density. By partially immersing cells in a thermally conductive fluid, these systems achieve efficient heat dissipation without significantly increasing weight or complexity. This is particularly beneficial in high duty-cycle applications, such as off-highway and industrial vehicles, where sustained thermal stability is paramount.
A well-designed immersion cooling system can guarantee that cells operate consistently within their optimal temperature range, resulting in a longer lifespan of up to 60% compared with cooling-plate technologies in equivalent applications and conditions.
Modular battery technologies are also leveraging advanced cooling-plate designs. Individual plates for each module allow greater flexibility in cell arrangement and enable better customisation for specific vehicle architectures. This modular approach minimises thermal gradients within the pack, improving overall safety and performance. Some designs integrate cooling systems directly into the structural components of the module, combining mechanical stability with thermal management to streamline assembly and reduce material usage.
Another advanced approach is the development of modules designed to support multiple cooling systems to allow more flexibility for customers, enabling the replacement or upgrade of subcomponents, such as cooling systems or control units, without requiring wholesale changes to the battery pack, supporting long-term cost-efficiency and sustainability.
The inherent scalability of the modular approach facilitates easier adaptation to evolving cell chemistries and emerging technologies. For instance, solid-state batteries, which may require higher compression and more flexible designs, could benefit from the modular framework’s adaptability. Similarly, the trend towards larger-format cells, such as prismatic LFP designs, aligns with modular architectures that accommodate various cell types without significant redesigns.
Engineers are exploring thinner and lighter materials for module construction, striving to improve volumetric energy density while maintaining structural integrity. Precision manufacturing techniques enhance production quality, reducing variability and optimising performance across modules. These incremental improvements collectively push the boundaries of what modular battery systems can achieve.
Modular battery-pack development is a dynamic interplay of innovation, standardisation and practical engineering challenges. By balancing trade-offs in flexibility, energy density and cost, engineers can create solutions that meet the diverse needs of the EV industry while paving the way for future advancements in energy storage technology.
Acknowledgements
The author would like to thank the following for their help with this article: Kieran O’Regan, co-founder and chief growth officer at About:Energy; Dr. Martin Busche, vice-president, battery r&d, product strategy and programme management at BorgWarner; James Eaton, CEO and founder of IONETIC; Anna Stadler, manager, battery technology development at Kreisel Electric; Stuart Morrison, CTO and managing director at MEP Technologies; Dr Bahareh Yazdani Damavandi, technical authority head for batteries at Ricardo; Seth Yates, head of product for battery systems at Turntide; and Jörg Hornung, vice-president, business line thermo-management at Webasto.
Some suppliers of modular batteries
About:Energy
BorgWarner
Hypercraft
IONETIC
Kreisel Electric
MEP Technologies
Ricardo
Turntide
Webasto
–
+1 248 754 9200
+1 801 317 8475
–
+43 7949 21400
+44 1382 492901
+44 1273 455611
+44 191 497 9007
+49 89 8 57 94 0
www.aboutenergy.io
www.borgwarner.com
www.hypercraftusa.com
www.ionetic.uk
www.kreiselelectric.com
www.meptec.co.uk
www.ricardo.com
www.turntide.com
www.webasto.com
ONLINE PARTNERS
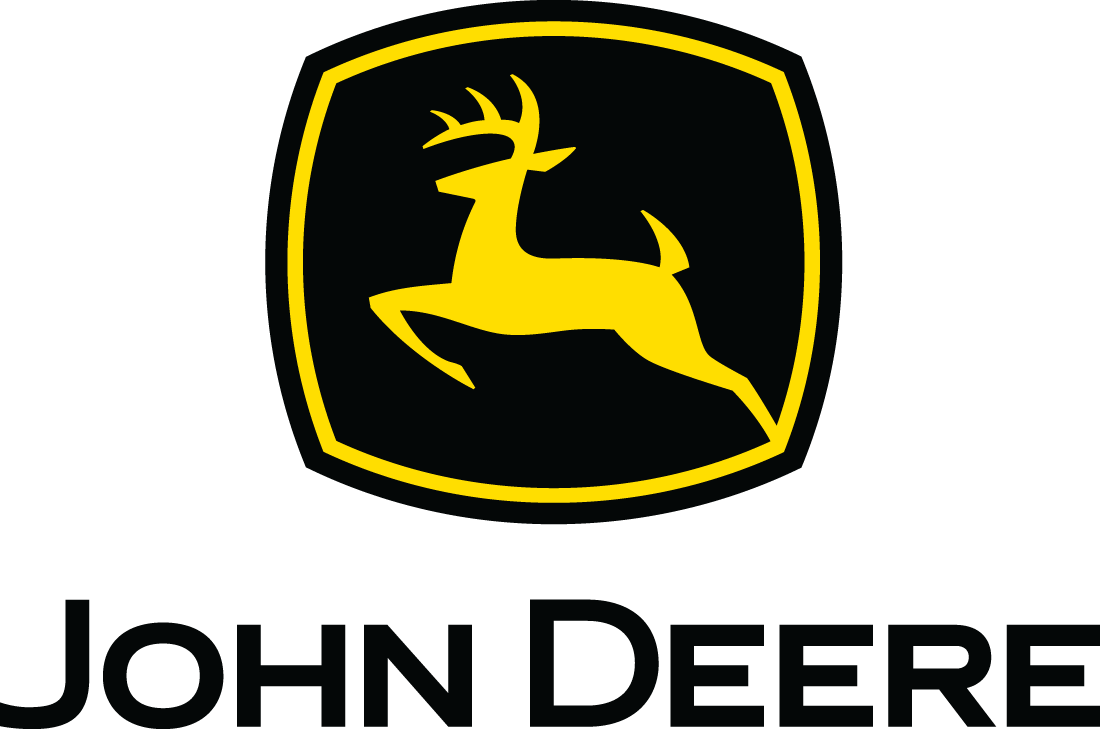
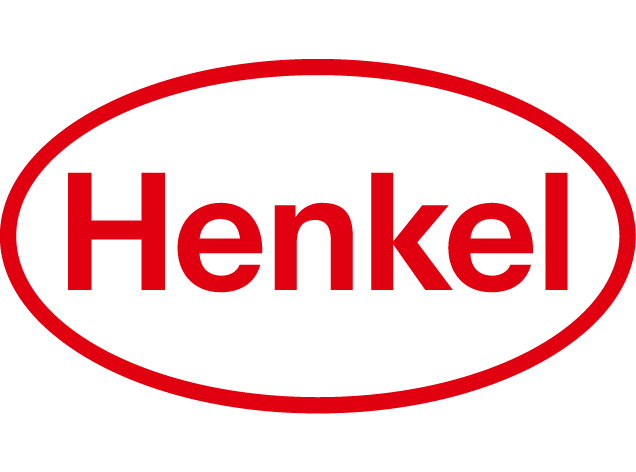
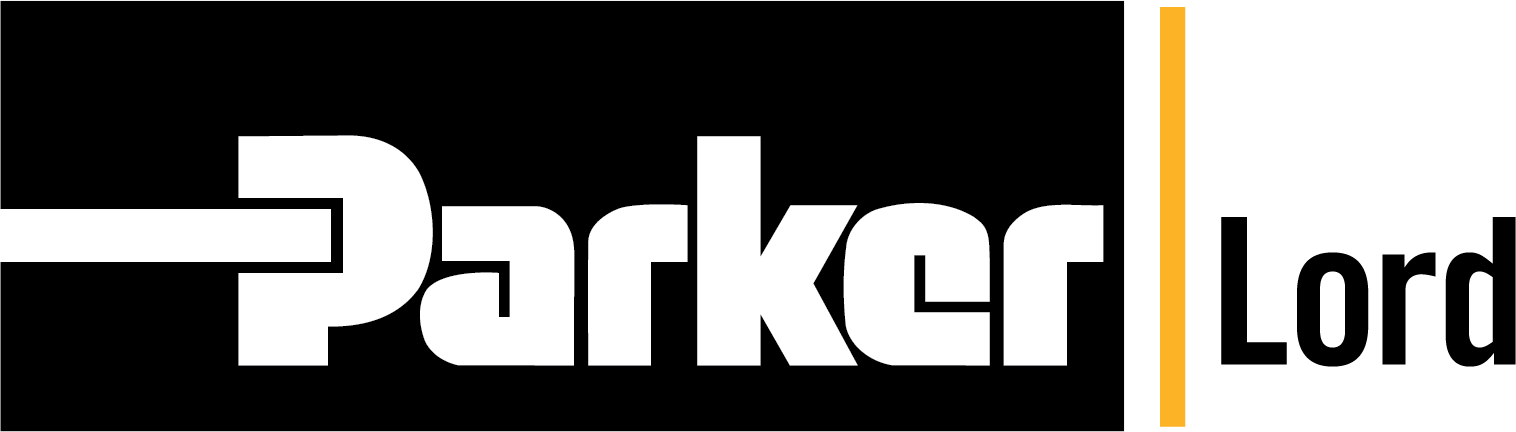
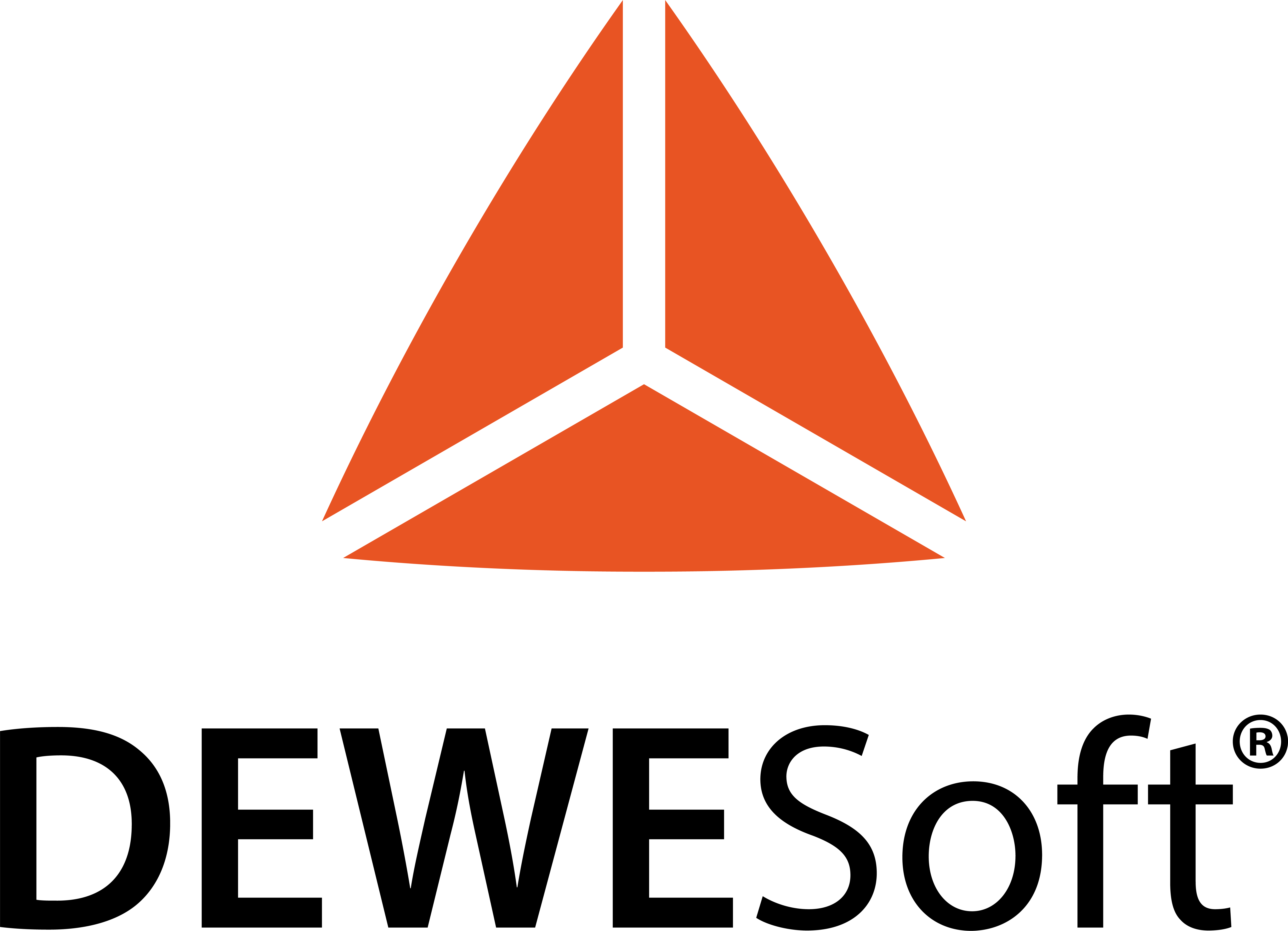
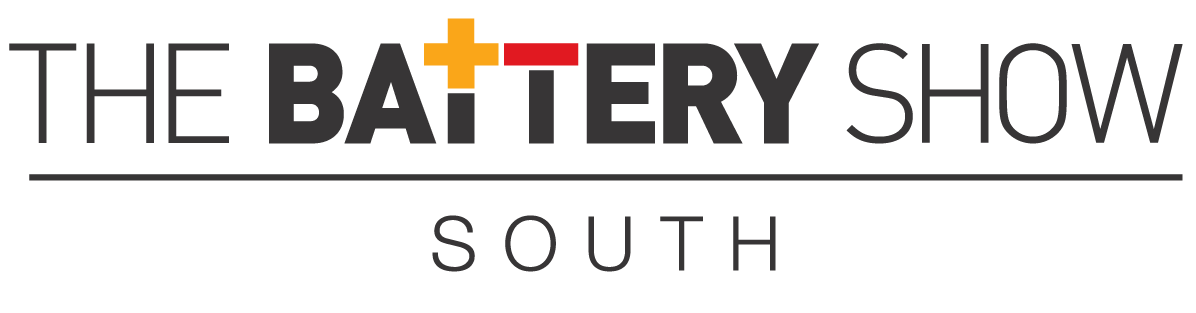
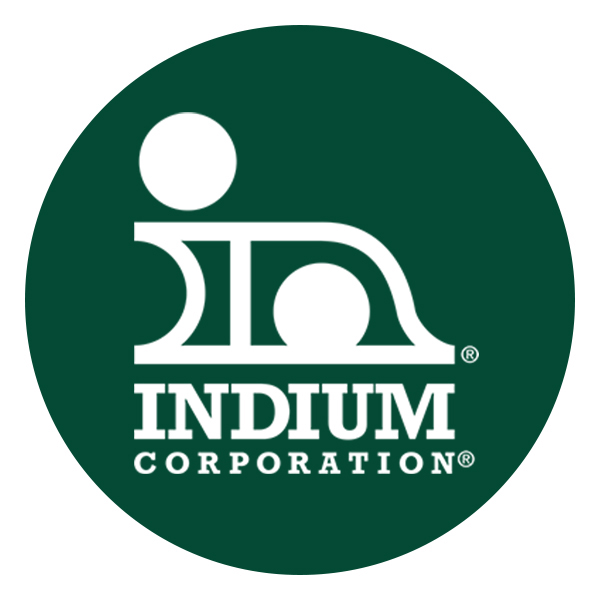

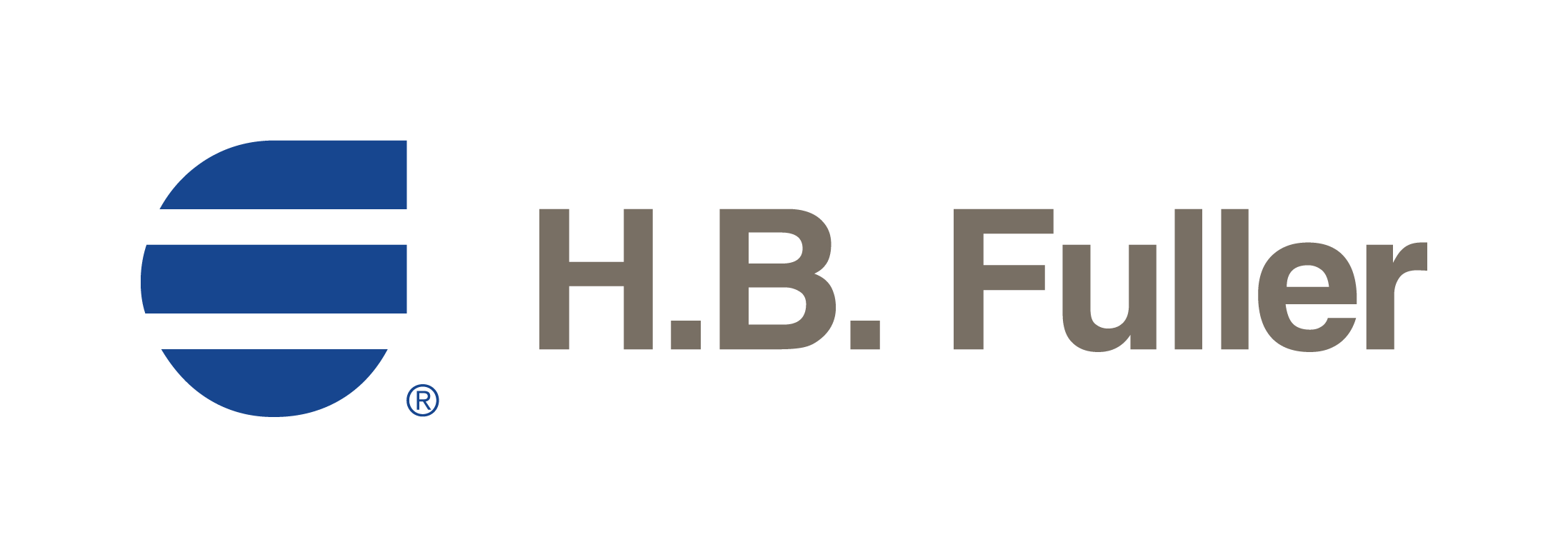
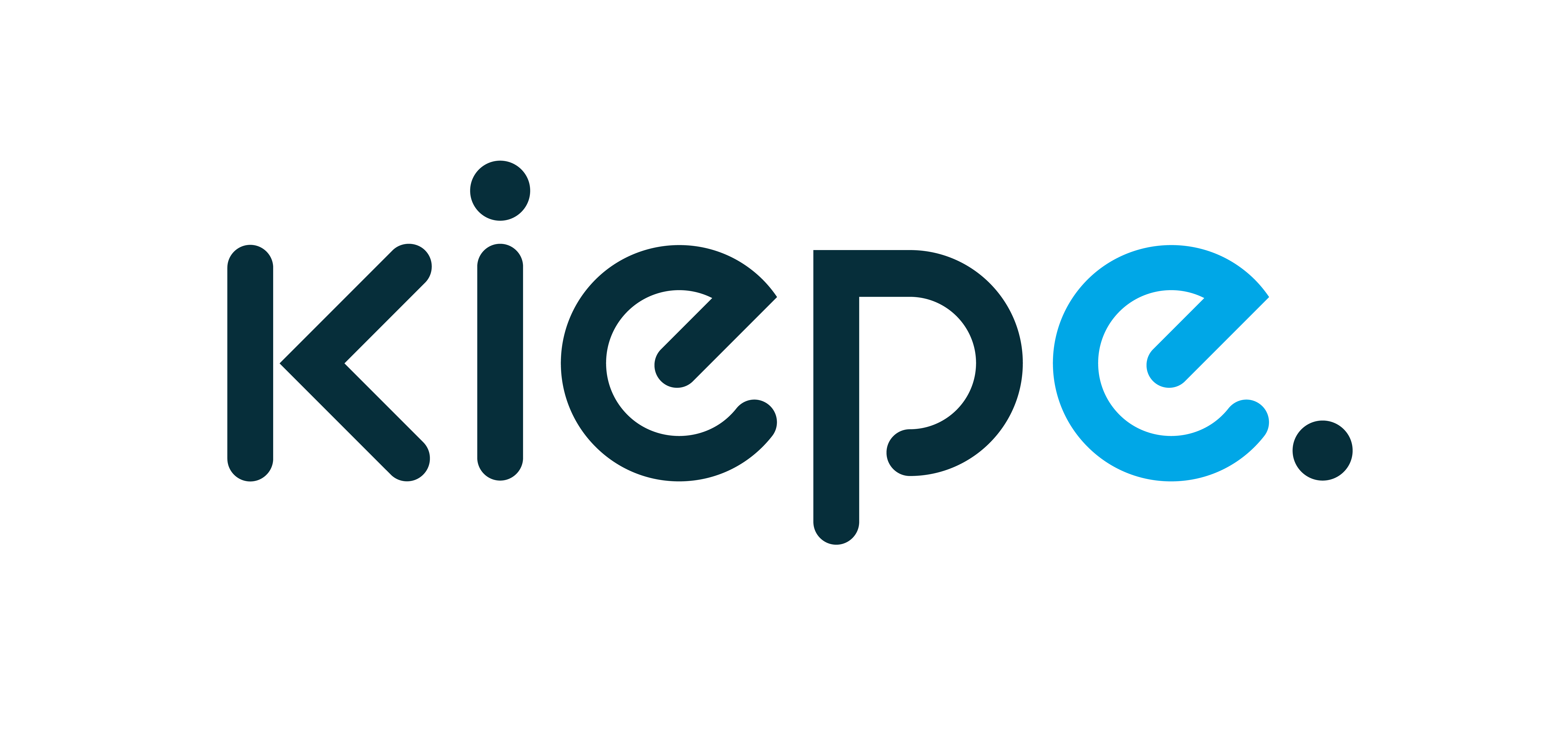
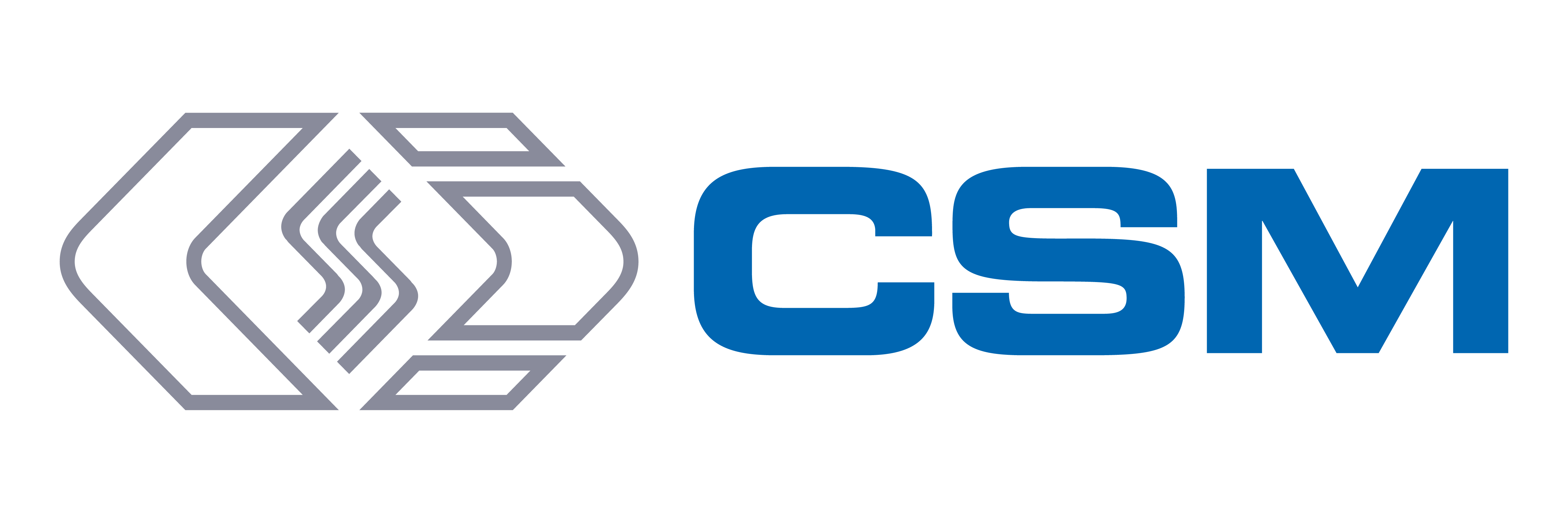