Lightning Systems LCF truck
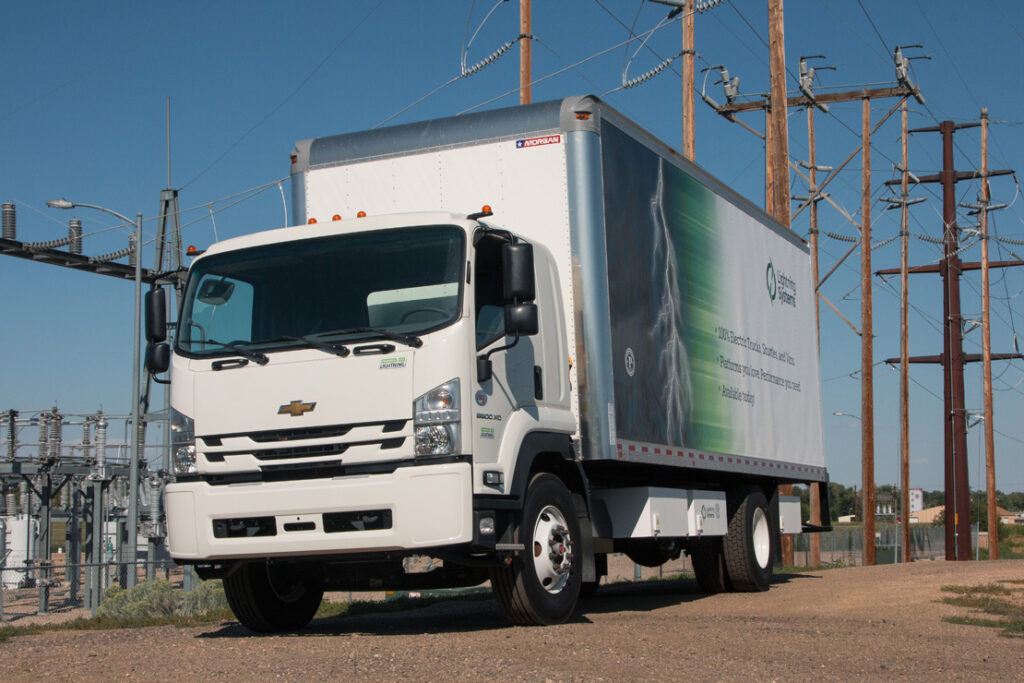
Rory Jackson reports on how this electrified version of a mainstream truck is operated and maintained.
Commercial appeal
Lightning Systems carries out full all-electric powertrain integrations on commercial road vehicles such as cargo trucks, buses and passenger shuttles. Founded in 2008 with a focus on hydraulic hybrid propulsion technology for trucks and buses, the Colorado-based company turned its attention to electric drivetrains in 2017.
It has a strong focus on electrifying widely used, mainstream vehicles, with the Ford Transit light commercial van being the first for which it has developed its Lightning Electric electrification kit.
With more and more US states planning emissions caps, and companies actively searching for ways to lower their fuel and maintenance costs, 2019 saw Lightning Systems approved for a California state purchasing contract on orders of its largest freight-running offering, the Lightning Electric Zero Emission Class 6 Low Cab Forward (LCF) truck, which uses General Motors’ Chevrolet 6500XD as its base chassis, and so can be referred to as the LSGM6500XD.
“There’s a diverse range of use cases for this vehicle, such as warehouse-towarehouse logistics, refrigeration and others,” says Keith Lehmeier, director of new product development and r&d at Lightning Systems. “We’ve even been approached by some customers who want to use it as a last-mile delivery platform, despite the fact that conventional wisdom would suggest that it’s far too big for that.
“The reason for that is because the convenience of online retailing has spread to encompass some huge, bulky items, such as furniture, large electrical appliances and more that can’t be delivered by small vans.”
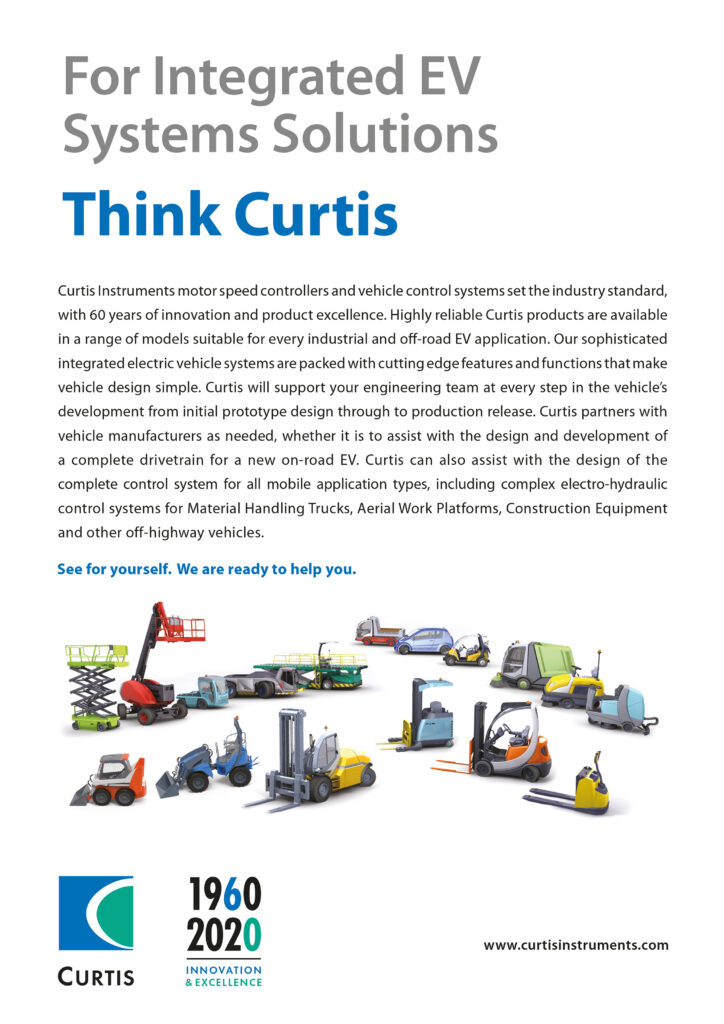
Development of the vehicle began in early 2018, when Lehmeier and his team saw a need across various markets for a medium-haul truck, for a broad range of applications in which an 18-wheeler would be too large but a Ford Transit would sometimes be too small and thus fail as a ‘one size fits all’ delivery platform.
The LCF is a 25,950 lb/11.6 t (maximum laden weight) medium-duty commercial truck with a minimum wheelbase of 538 cm. Its top speed is electronically limited to 65 mph/ 104.6 kph, with a peak power output of 295 hp (220 kW), and battery energy up to a maximum of 192 kWh (which provides an estimated top range of 130 miles/209.2 km).
As mentioned, the company develops electrification kits made up of all-electric components that can replace the conventional ICE and its associated components such as mufflers, fuel tanks, fuel lines, transmission and so on. These Lightning Repower kits are developed to fit the 6500XD chassis for weight, power, speed and other factors, resulting in a fully battery-electric vehicle.
Thus, each kit includes an electric motor, transmission system, electric inverter (which powers and controls the motor), battery modules, and accessories for power steering and HVAC. The electric motor and transmission are configured in a similar way to the conventional drivetrain, securing to a subframe that mimics the stock layout, and bolting directly onto the stock engine mounts in the front of the truck.
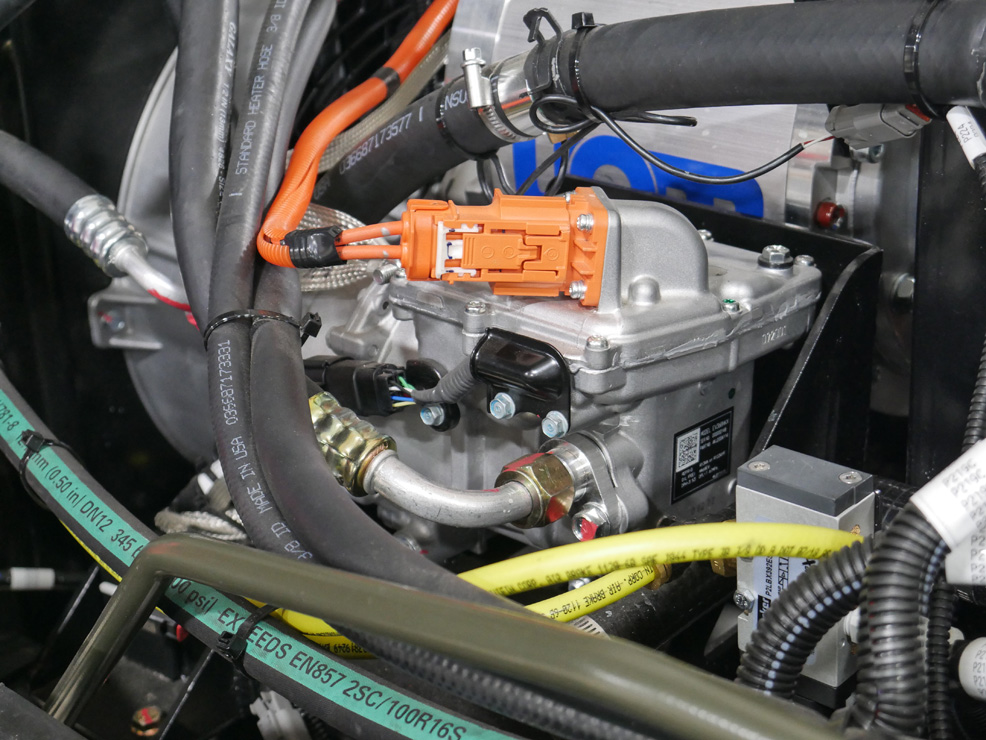
Also, the batteries are mounted inside the vehicle at predetermined locations with supplied and tested framework, and covered with shrouding for environmental protection from water and road dirt.
“Although it might seem like a fairly invasive procedure from a technician’s standpoint, we try to limit that invasiveness as far as we can. For example, the factory braking control module is left intact,” Lehmeier notes. “The factory restraint control module, seatbelt monitors, airbag controls, all of that is still General Motors componentry.”
Being a relatively heavy commercial vehicle, the LS-GM6500XD has additional specialist components such as air brakes and a heavy-duty power steering pump. This meant significant development had to go into Lightning’s direct-drive system, which still uses a somewhat conventional engine-driven air compressor and power steering pump, but in the absence of the old diesel engine, a second onboard electric motor (in addition to the traction motor) is integrated to drive them.
“That development hurdle was a notable departure from what we’d experienced with the Ford Transit, and took a lot of engineering effort. Transplanting individual ICE-related components with electrification subsystems is straightforward to us now, but bigger vehicles mean figuring out what to do with far more complex systems,” Lehmeier says.
“Whether it’s a 25,950 lb (gross) GM vehicle or a 10,600 lb (gross) Ford, everyone seems to be after the same minimum performance benchmark – a 100-mile range capability. So for the most part, our approach is the same for each platform, albeit with variations in the amount of application work required.
“We aim to exceed the fuel vehicle’s performance where possible. Some things are software-limited, like how a lot of our operators want a forced speed limit of 55 mph, but the torque of electric machines results in far better control over acceleration and deceleration than gasoline and diesel engines.”
An example of a key part of Lightning’s electrification strategy are what Lehmeier calls the modular energy “building blocks” – battery sub-packs of roughly 30-45 kWh, connected in parallel. These allow customised assemblies of however many sub-packs are needed for the size of the battery and the desired range of the user.
This approach enables the company to use near-identical battery technologies – not just chemistry and cell make-up, but cooling, BMSs and safety components – across all its vehicle lines.
The company’s extensive development and testing record databases have also fed back into its in-house numerical modelling software, which is used by its engineers to calculate and simulate battery requirements and other powertrain component recommendations based on the vehicle’s parameters and requested operating envelope.
Pre-delivery checks
Before starting a day’s deliveries, the driver is expected to carry out a series of checks, as laid out in an addendum to the GM6500XD user manual that, Lightning provides for testing the electrical systems.
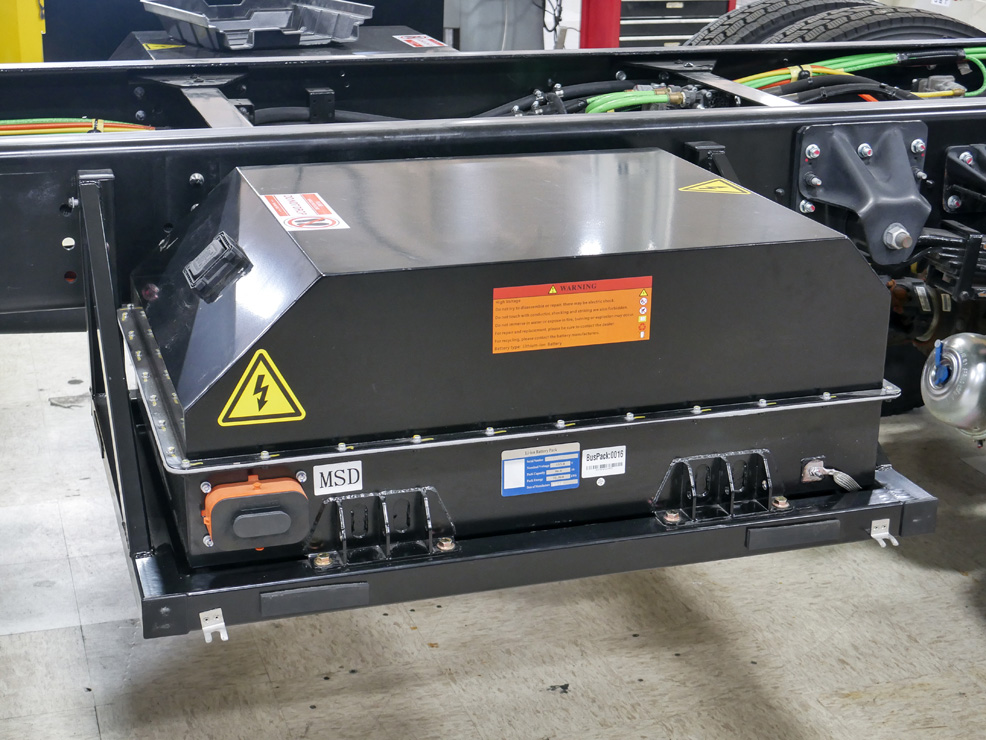
These include checking under the vehicle for fluid leaks – battery chemicals and coolant, rather than engine oil or fuel – and for loose wires and cables.
As the Lightning Repower kits are designed to work as a drop-in replacement for ICE powertrains, much of the other equipment is stored under the cab. The driver tilts this forward and checks that all cabling, wiring, connectors and coolant pipes show no signs of significant wear.
“We don’t touch a lot of components, such as the windshield wipers and the motors that move the windows up and down, so the General Motors operations manual is still valid for those,” Lehmeier says.
“Moreover, by regulation and convention, a lot of operators will have their own procedures for checking the floors, brakes and so on; we leave those up to them. Even this truck, with its two-speed transmission and accessory motor, has lower maintenance requirements overall than pretty much any ICE vehicle.”
Making rounds
As the operator is driving, key data is displayed on the instrument cluster panel. “We try to keep our processes and technologies, including our control interface, as vehicle-agnostic as possible,” Lehmeier notes. “In EVs, the tachometer for example doesn’t relay very useful information to the driver, so we replace that with a power flow indicator.”
Lightning Systems is acutely aware that its trucks will need to run in California’s most hilly and traffic-congested cities, such as San Francisco and San Diego, so its hardware and software have been designed with capabilities to help them deal with the problems such roads can present.
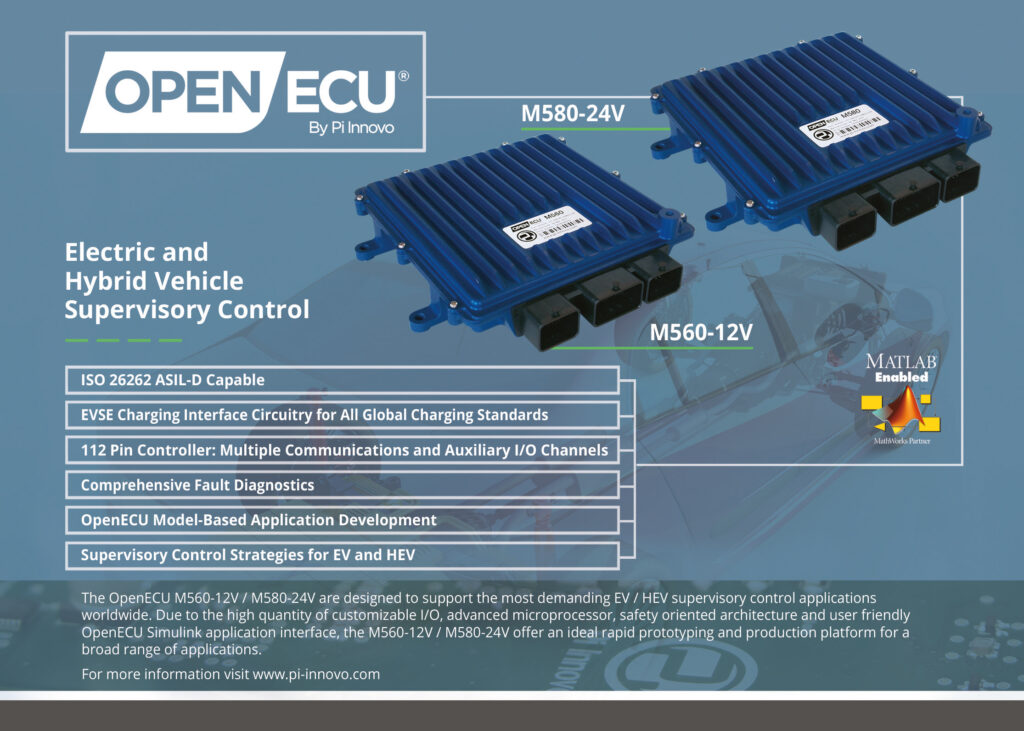
The first of these is the vehicle’s regenerative braking. The LSGM6500XD’s operator can activate this by taking their foot off of the accelerator pedal, which automatically causes the traction motor to function as a generator to start recharging the batteries, without activating the brake pedal.
As a result, the truck’s wheel brakes can be spared from overuse, which will help lower the inevitable maintenance costs that will come from the frequent stops and starts the truck will have to make. It is also worth noting that the high number of lengthy downhill streets presents many opportunities to conserve and replenish battery energy through this system integration.
Second, those streets can present a problem when the truck is going uphill and has to stop in traffic. The control system then implements ‘hill-hold’, which delivers just the right amount of power to the traction motor to prevent the vehicle rolling backwards when the driver takes their foot off the brake pedal.
And for parking spaces, the control system has been programmed with a ‘creep’ function, enabling the vehicle to autonomously maintain a slow forward or reverse motion when the driver takes their foot off the pedals, to ease the job of manoeuvring and parking at each stop.
This makes the truck behave just like any car with an automatic transmission, and adds to the sense of familiarity that the driver will feel when going from an ICE 6500XD to the LS-GM6500XD.
Enabling these precise control features requires a powertrain with comparable precision in terms of power conversion, efficiency and supply. To that end, the truck integrates the UQM PowerPhaseDT, an e-drive specifically designed for medium- and heavy-duty electric commercial vehicles.
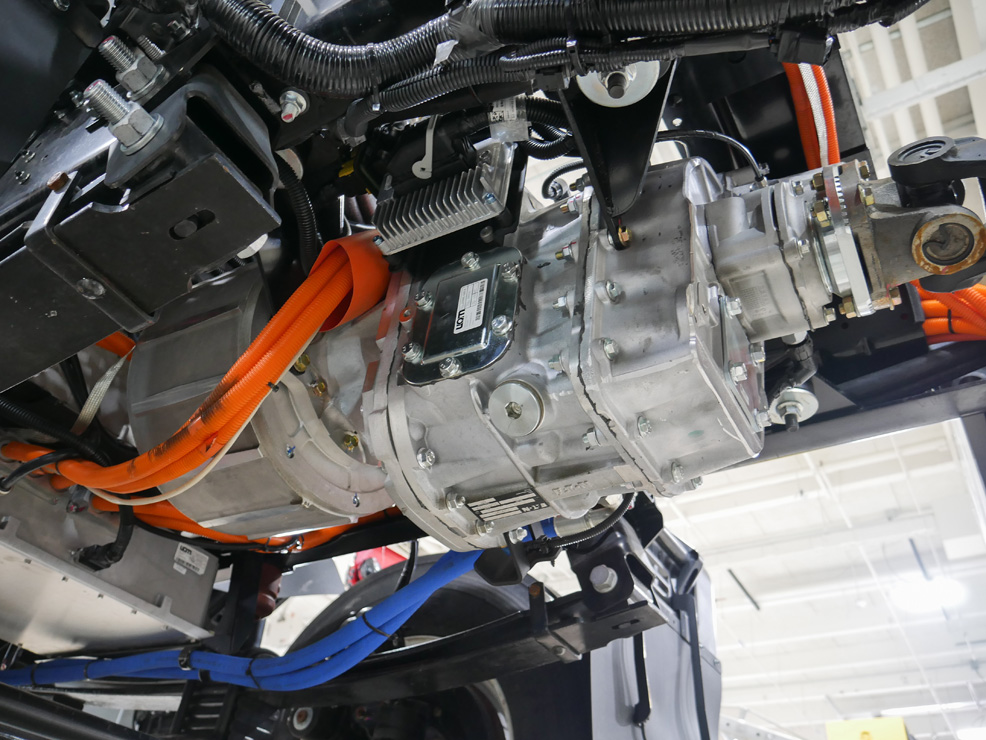
Its traction component is an HD220 from UQM (currently being integrated into Danfoss Editron). This three-phase permanent magnet AC motor and inverter system is the key to the LSGM6500XD’s 220 kW peak output, which is produced at its top speed of 6000 rpm (with 700 Nm as its maximum torque, when the truck is in second gear; in first gear, 2471 Nm of torque is generated).
It also provides a 150 kW continuous output, with 440 Nm of operating torque, from an input of 250-400 V DC. As well as the DC-AC power conversion from the battery to the motor, the bidirectional inverter takes the AC power regenerated during braking and converts it to a single DC voltage output in order to charge the battery.
The liquid-cooled inverter’s variablefrequency drive also slows the AC frequency of the motor to provide the creep capability, when activated through the driver interface and pedals. In addition to the UQM motor/inverter, the two-speed transmission for the e-drive was provided by Eaton, with Pi-Innovo developing the transmission control unit.
Between stops in cities, the truck is also likely to run for lengthy periods on US freeways, with long stretches between truck stops and charging stations, and significant potential for traffic collisions or pothole-related damage. To that end, the battery packs have been designed and integrated with security and failsafes in mind.
For one, the company has gone with NMC, 18650-type cells for the tried-and-tested reputation of the technology; these are encased in a steel enclosure to maximise protection and minimise impact or damage from piercing the cells.
The exact quantity of energy stored onboard (and thus the maximum operating range and charging time) can vary, with four options offered.
The smallest is 96 kWh capacity, consisting of three 32 kWh packs, which gives up to 106.2 km of driving distance and takes up to 1 hour and 45 minutes on a Level 3 (DC) charge. The largest capacity offered is 192 kWh, consisting of six packs, which provides a 209 km range and requires 3 hours and 30 minutes for a full charge from empty.
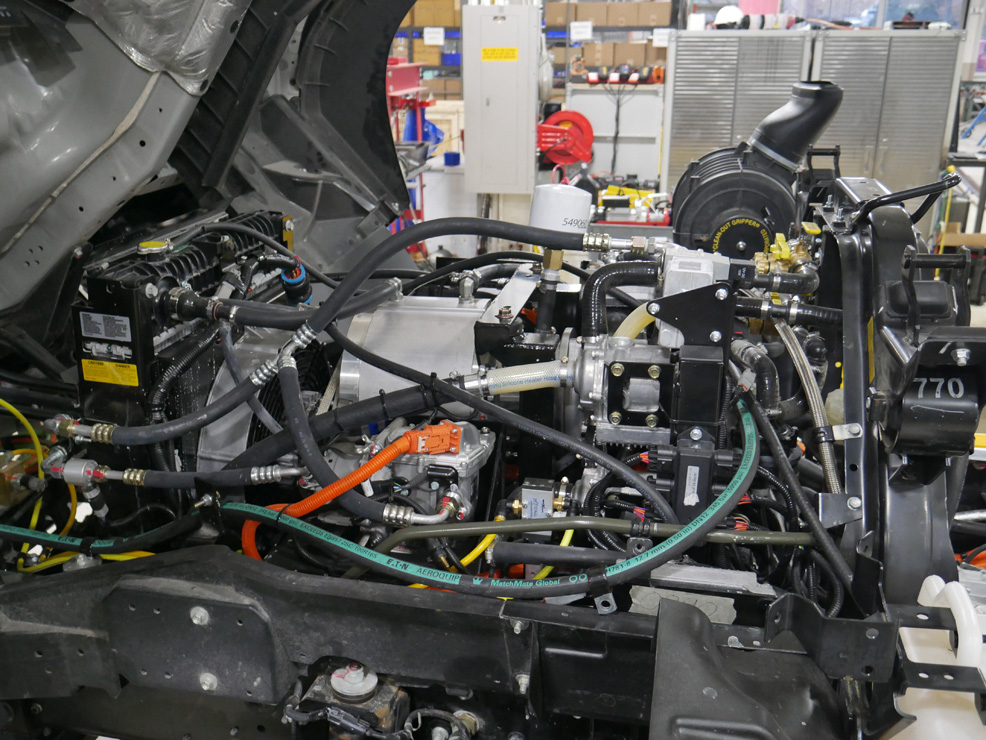
Notably however, the battery pack scales inversely with the maximum payload carrying capacity. Lightning Systems recommends a payload limit of 14,000 lb (6350 kg) with its 96 kWh configuration, and 12,200 lb/5533.8 kg at 192 kWh.
“Every time you add a battery pack, its weight eats into your payload capacity. The legal weight limit of Class 6 vehicles will not budge to accommodate you wanting more batteries, so range and package capacity have to be balanced in terms of what each customer wants,” says Lehmeier.
Each pack is also designed with waterproof vents to allow gas to escape and prevent pressure building up if cell damage should occur, as well as positive temperature coefficient-type resistors, which act as a fuse to prevent overcurrent.
Fuses are also built into the connections between each module to automatically disconnect one of them if its current gets too high, and ‘containment regions’ are built inside the modules to restrict thermal runaways from spreading.
Lightning Systems has also programmed its BMS to open the main battery contactors if overcurrent conditions should still be detected, shutting down the pack. Similarly, the battery system also integrates a highvoltage interlock loop to monitor the integrity of all HV connections, opening the contactors if a problem is detected. The BMS is also designed to monitor for (and react to) overcharging and over-depletion, among other hazardous conditions.
To keep the battery packs at their optimal temperature range during operation, regardless of environment and climate – which can vary considerably across the US – the thermal management is handled across a system of three key components.
A radiator serves to cool the packs to ambient temperatures, a chiller cools the pack below ambient temperatures in hot environments, and a heater warms it above the background temperature in colder climates – with a liquid-cooling system as the main temperature interchange medium.
Lastly, the mounting design has been modelled in CAD software, with particular focus on eliminating yielding and fatigue over an expected longterm usage on roads. That helps meet the five-year warranty the company provides on the battery and powertrain.
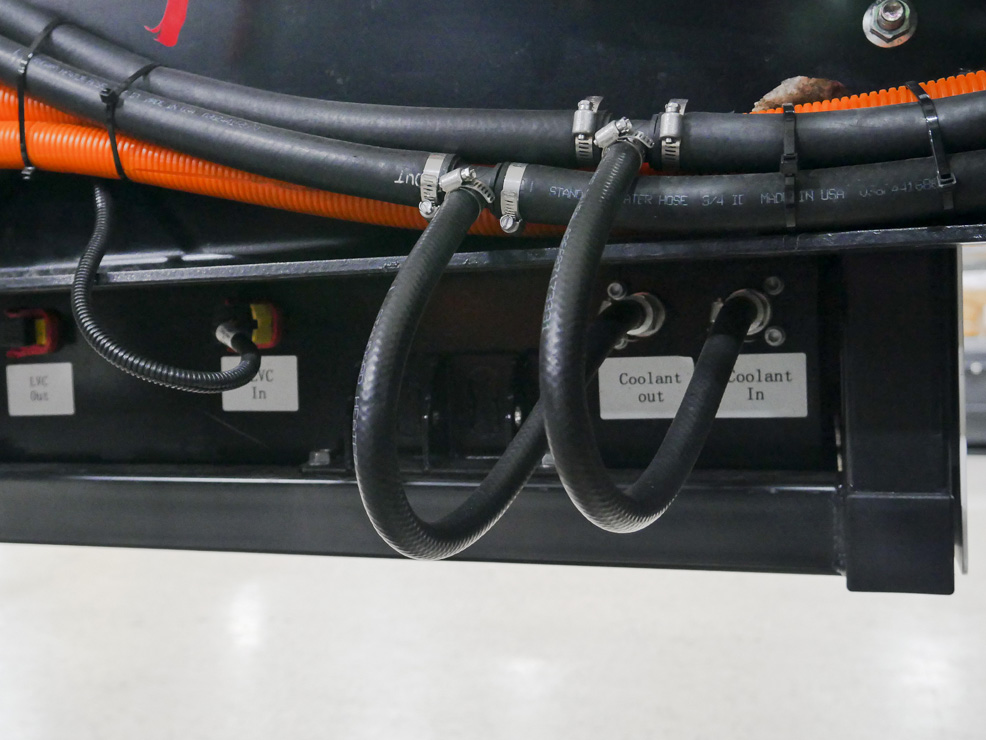
End-of-shift checks
Once deliveries are completed and the LS-GM6500XD is returned to its depot, the driver carries out a similar series of checks to those before the start of the journey.
After these, recharging should be carried out. A slow AC trickle charge is recommended for overnight replenishment to prolong cell lifetime. However, if the driver needs to recharge in mid-journey, a fast charge is available through the J1772 CCS1 Combo connector by the side of the cabin, enabling up to 50 kW of charging.
Lightning Systems also offers a range of charging stations, at different voltages and with different connector standards.
These include a 7.2 kW AC wall box charger at the low-power end, which provides a 240 V AC, 30 A feed (with a 25 ft cable and input plug), a 16.8 kW pedestal-type AC charger supplying 240 V with a 70 A current (which comes with an 18 ft cable and a 7 in colour display panel) and the aforementioned 50 kW, 480 V DC pedestal, which provides 72 A, two 18 ft cables, and either a CCS-1 or CHAdeMO.
If a problem is found with the battery, such as the BMS detecting potential signs of overvoltage or undercurrent, a manual service disconnect on the outside of each battery pack ensures that the battery is safely isolated and ready for inspection and servicing.
Pulling the disconnect out instantly trips the pack’s internal contactors (which makes the external connections safe), and interrupts the pack’s internal high-voltage circuit.
Analytics
It is essential that the LS-GM6500XD performs optimally in order to enable reduced servicing time and overheads for its users. To that end, Lightning Systems has developed Lightning Analytics, which as its name suggests is intended for tracking and analysing operational metrics for optimising vehicles’, drivers’ and technicians’ protocols.
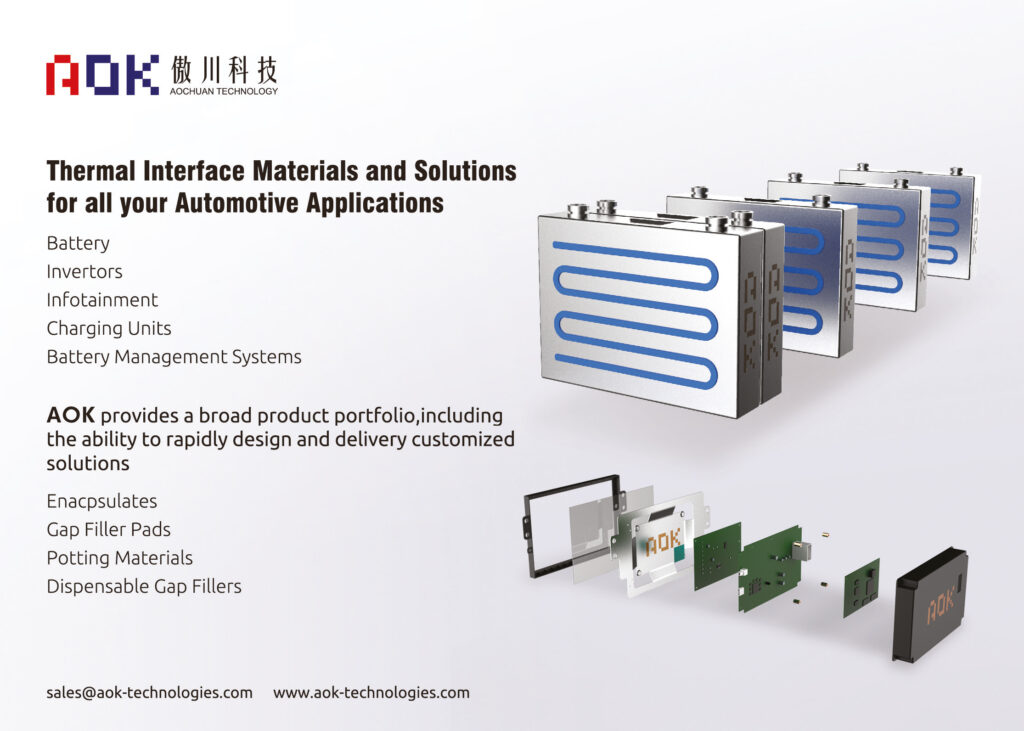
“It’s an advanced spin on telematics, with the controller for that connected via a CAN interface and communicating to our servers over an encrypted 4G data link,” Lehmeier explains. “On the one hand, we have the ability to predict how vehicles will perform – using our numerical modelling already mentioned – and the ability to measure how they’re actually doing at each stage of each operation.”
The company has aimed to provide a broader range and depth of analytics than is typical among smart vehicle manufacturers and integrators. As a result, Lightning Analytics provides GPS- and time-stamped records of more than 70 vehicle parameters each second, including speed, SoC and power consumption.
These are aggregated into a daily report, which at the end of operations provides graphs for tracking key variables such as miles per kWh, number of kWh consumed per hour, or speed and SoC used over distance (or time).
Pie charts for system optimisation are also generated, and illustrate factors such as the distribution and scale of power consumption by different onboard electrical components, as well as the different vehicle actions conducted over the day (showing how much time was spent parked versus time driving).
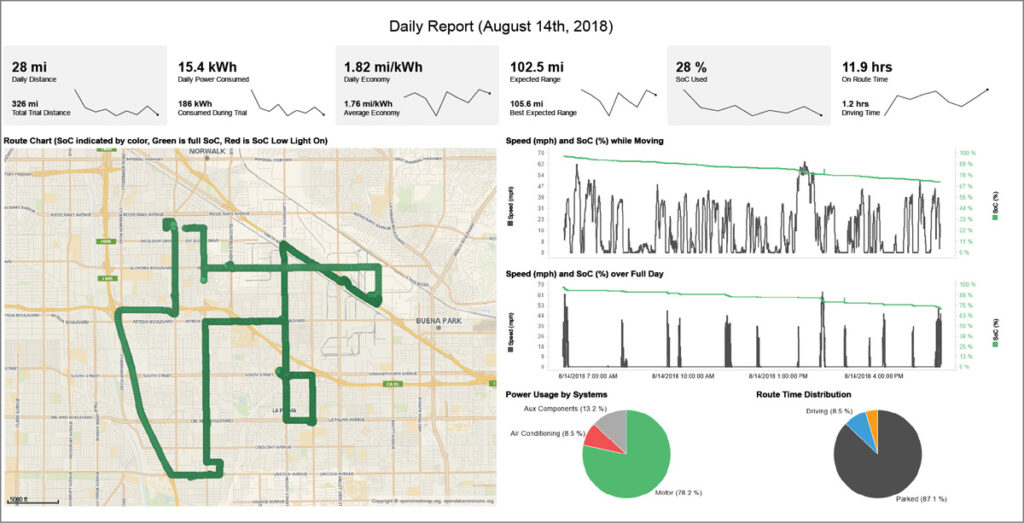
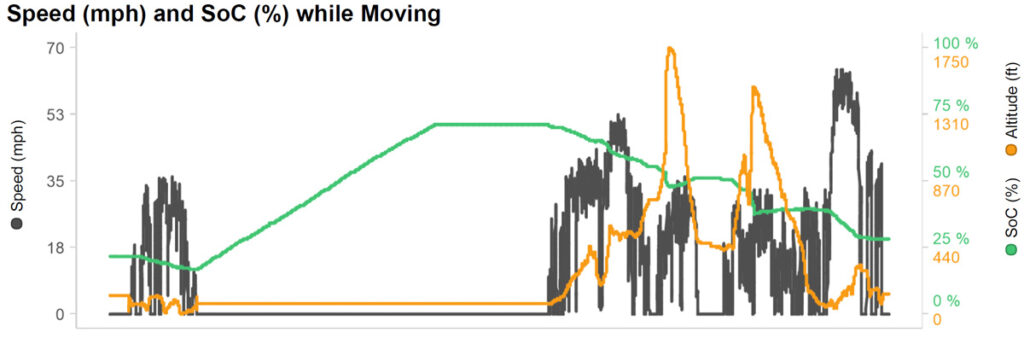
End-users can then check for specific aspects of performance. For example, SoC and altitude can be fixed to the y axis (versus time or distance on the x axis) and overlaid on a line graph to reveal where and how often the driver took advantage of the regenerative braking when going downhill – and how much the endurance or range were extended as a result.
Such data and lessons learned through Lightning Systems’ analytics could be used to train new as well as experienced LS-GM6500XD drivers in how to reduce the time and energy used during operations, further aiding a vast range of organisations to reach goals in efficiency and sustainability.
Specifications
Chassis: General Motors Chevrolet 6500XD
Maximum weight: 11.6 t Maximum range: 209.2 km Top speed: 104.6 kph Maximum power output: 220 kW Energy storage capacity: 192 kWh Maximum payload capacity: 6.35 t
Two-speed transmission
Three-phase, permanent magnet AC
NMC cell chemistry
Liquid cooling
DC and AC charging
Making rounds
Some key suppliers
Vehicle: General Motors
Inverter: UQM/Danfoss Editron
PM AC motor: UQM/Danfoss Editron
Transmission: Eaton
Transmission controller: Pi-Innovo
Battery cells: undisclosed
ONLINE PARTNERS
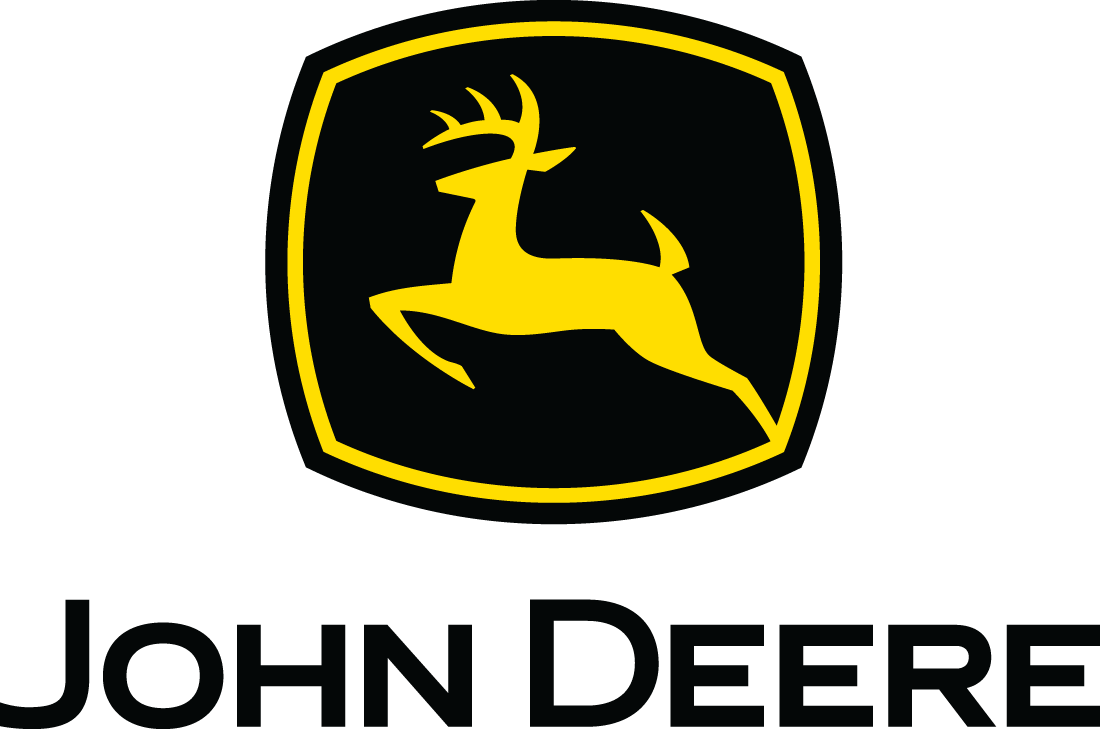
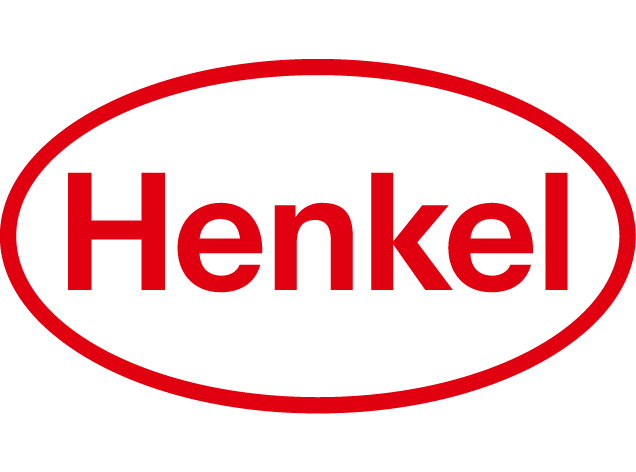
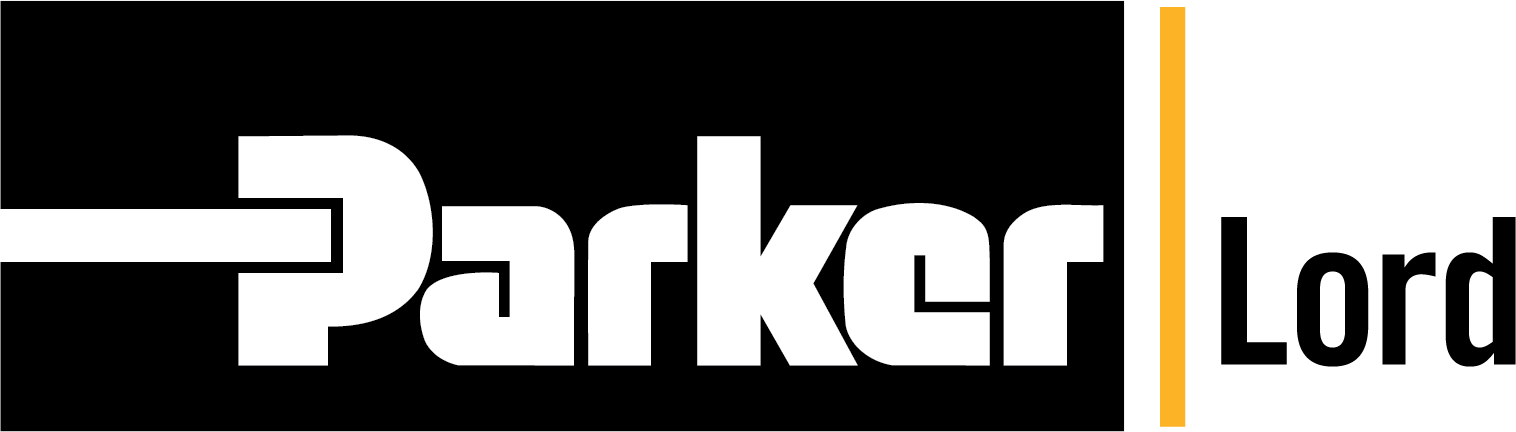
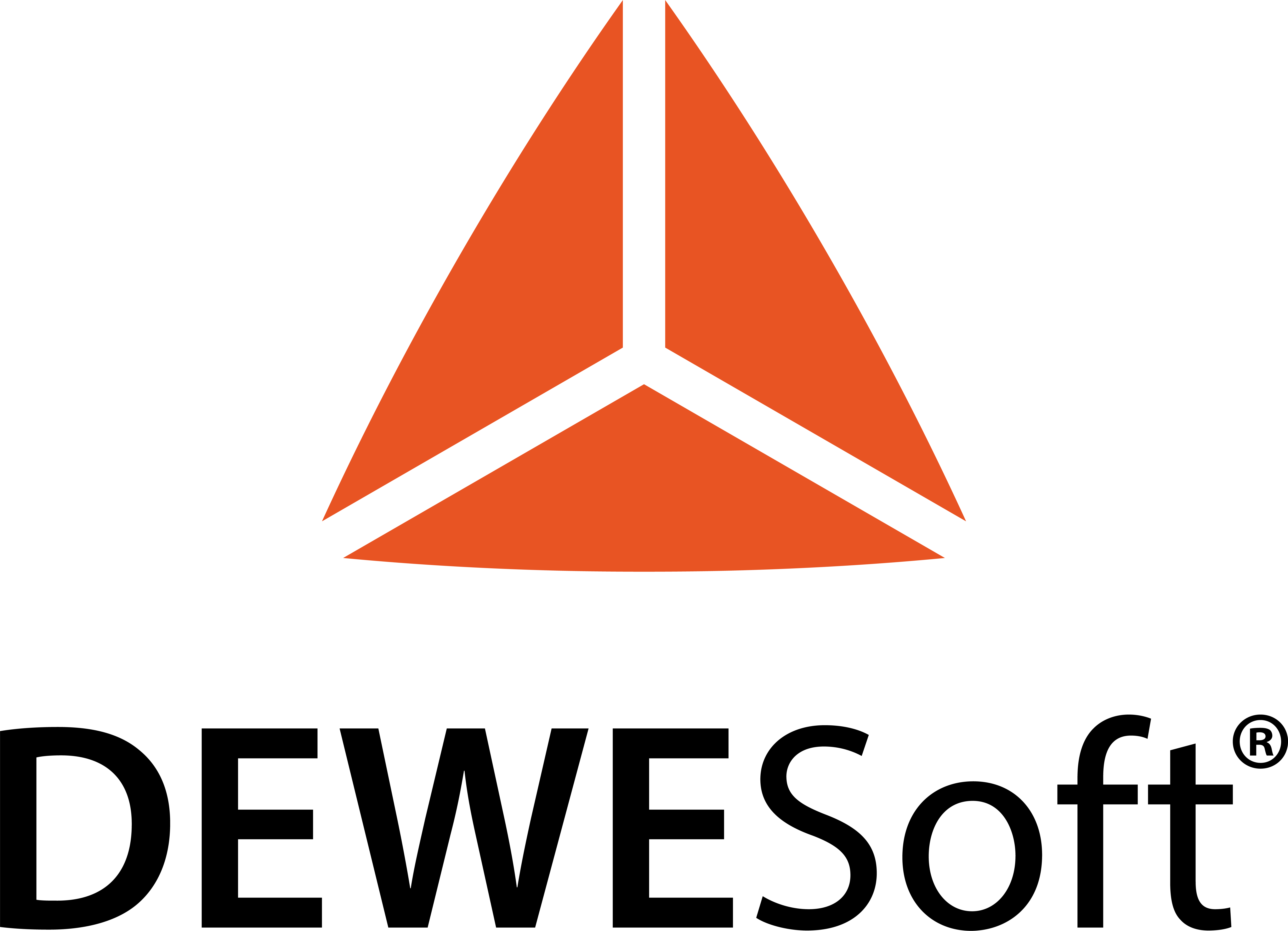
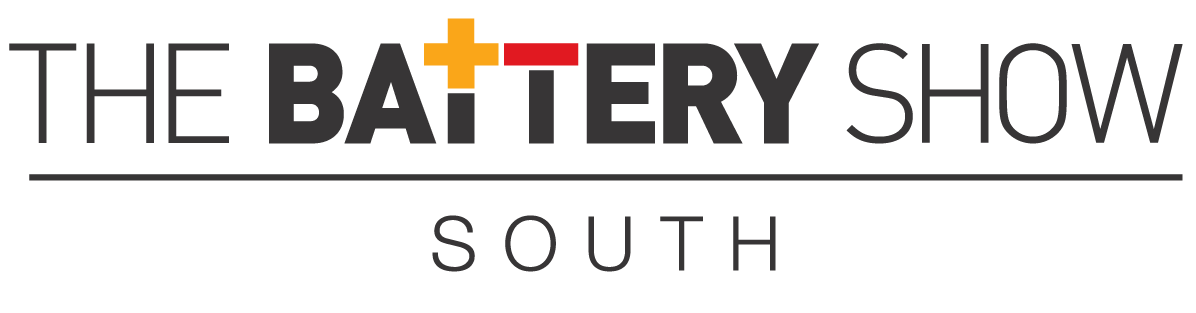
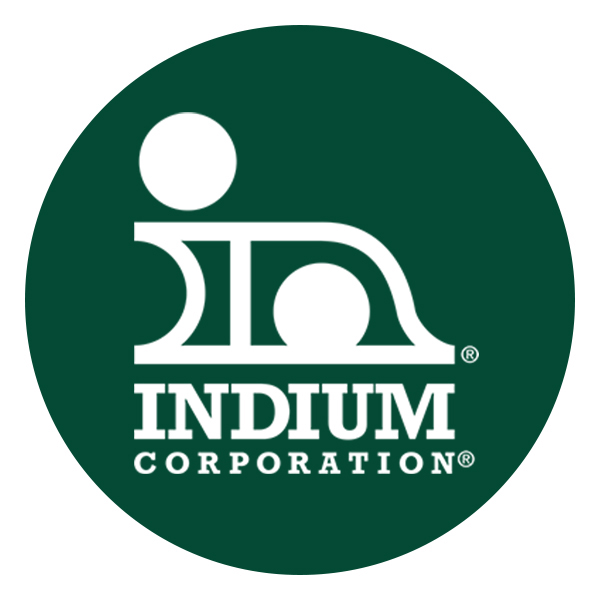

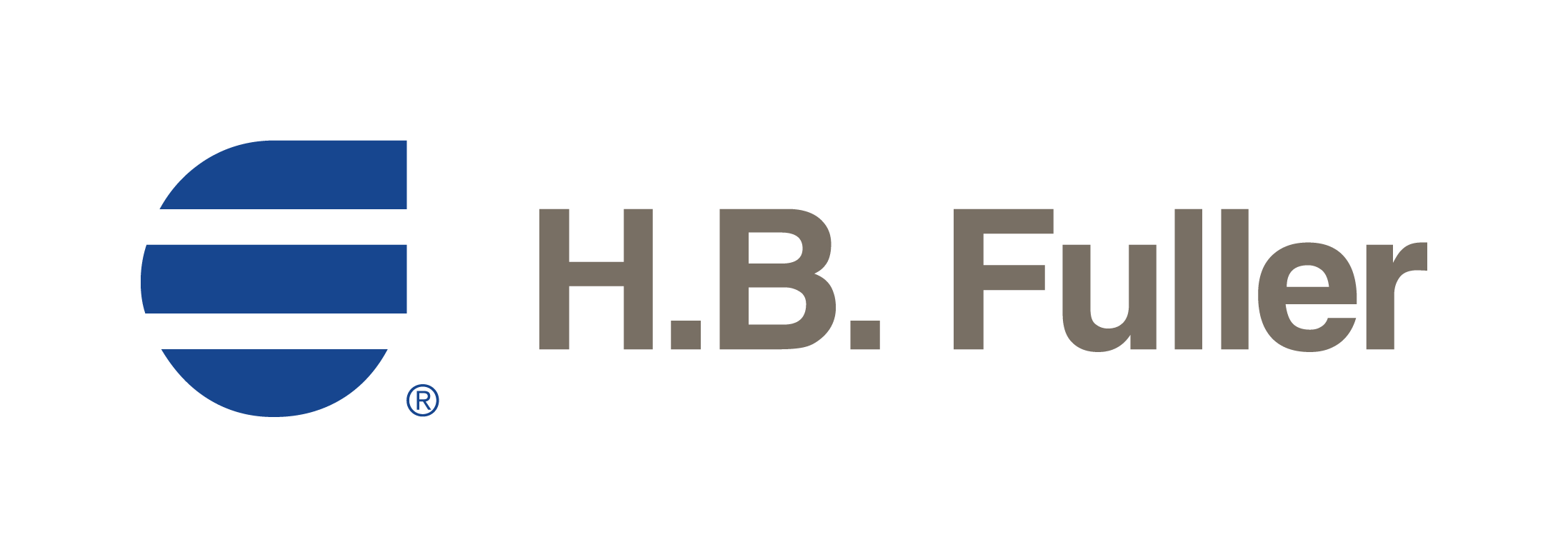
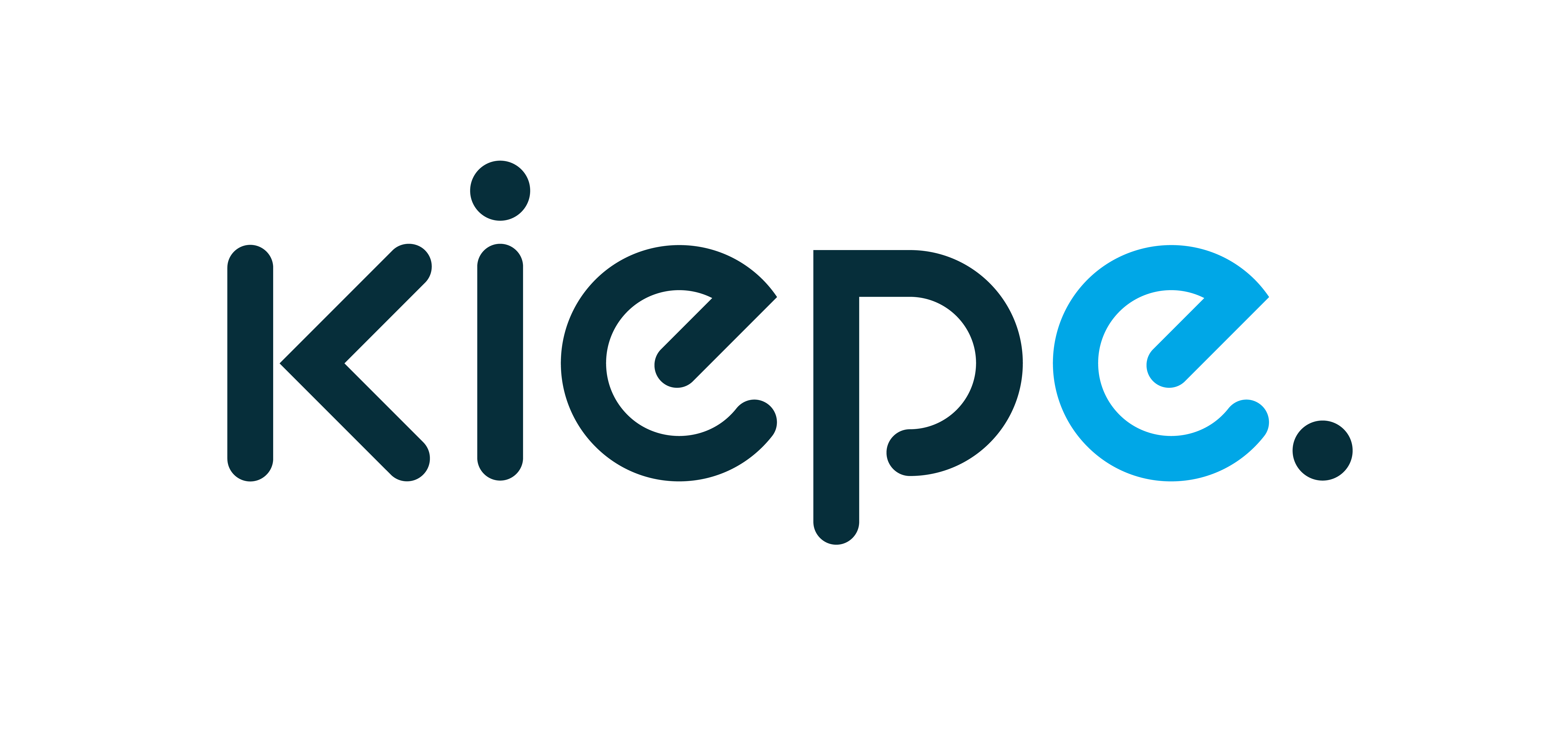
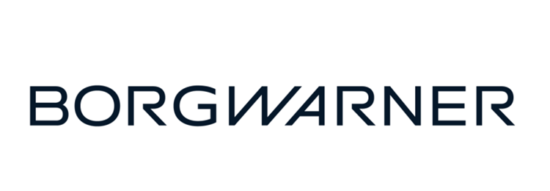