Inverter integration cuts size, weight
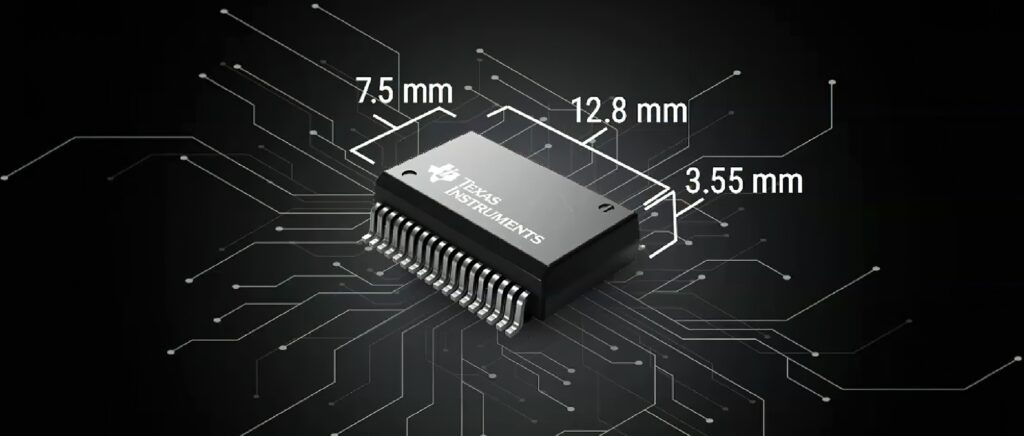
Texas Instruments has integrated a transformer into a gate driver to enable distributed switch architectures for inverters (writes Nick Flaherty).
The UCC14240-Q1 isolated DC-DC bias supply module integrates the transformer and components with 3.5 mm-high planar magnetics to reduce the size, height and weight of a distributed power system in an inverter. The integration of the transformer and isolation offers easy control and low primary-to-secondary capacitance, improving common-mode transient immunity.
“We are working on integrating the traction inverter with the C2000 and high-resolution PWMs for power supply control,” said Ryan Manack, TI’s director of automotive systems. “This improves the mechanicals and thermals, and reduces the weight and cost.”
However, a key challenge is the design of the gate drivers that control the switching transistors in the inverter, whether these are SiC, silicon IGBT or GaN. “The isolation barrier has to be crossed from a power perspective and signal perspective to move from the low voltage to the 400 or 800 V and at the heart of the traction inverter is six gate drivers,” Manack said.
“The question is how to bias the isolated gate drivers to drive the IGBT, SiC or GaN switches to increase frequency and reduce the size, and we need to power these. In the past, you could use one transformer but now we see customers moving to a distributed power architecture, so for the EV power system a smaller integrated transformer product is needed.”
A distributed power architecture meets the reliability standards of an EV’s environment by assigning each gate driver a dedicated, local, well-regulated bias power supply in close proximity. This architecture provides redundancy and improves how the system reacts to single-point failures.
For example, in an inverter design with six transistors, if one bias supply paired to a gate driver fails, the other five remain operational, as do their paired gate drivers. If five of the six drivers remain operational, the motor can slow and shut down in a well-controlled manner, or potentially continue operating indefinitely. Passengers in the vehicle might not even recognise a disturbance with such a power system design.
The large height, weight and area of external transformer bias supplies such as flybacks and push-pull controllers prevent the use of a distributed architecture in EV inverter designs.
“The increased power density means shrinking the size of the total solution but one component that sticks out – literally – is the transformer, so with a proprietary technology we have integrated the transformer inside the IC,” said Manack.
Fully integrating the primary- and secondary-side control with the isolation achieves a regulated ±1.3% isolated DC-DC bias supply with 1.5 W of output power to control the gate drivers of the power transistors in a distributed design, even up to 105 C. The high-accuracy output voltages provide better channel enhancement for higher system efficiency without overstressing the power device gate.
The module provides extra features such as input undervoltage lock-out, overvoltage lock-out, output voltage ‘power good’ comparators, overtemperature shutdown, soft-start timing, adjustable isolated positive and negative output voltages, an enable pin, and an open-drain output ‘power good’ pin. This requires 10 external components, down from 26 separate devices.
The integration brings benefits for EMI by enabling soft switching, which is not possible with a traditional flyback or push-pull architecture, but requires new control algorithms.
“To isolate that higher voltage from the system we can use a 3.5 pF capacitor rather than 10-35 pF capacitance for EMI and transient performance,” said Steve Lambouses, vice-president and general manager of the High Voltage Power business at TI. “However, that needs a completely different control algorithm with soft switching where we don’t need to mitigate EMI externally. There is a fully integrated closed-loop control without having to use an optocoupler isolator that can wear out.
“This also avoids transformer tuning, and we spend a lot of time with customers on transformer tuning,” he said.
ONLINE PARTNERS
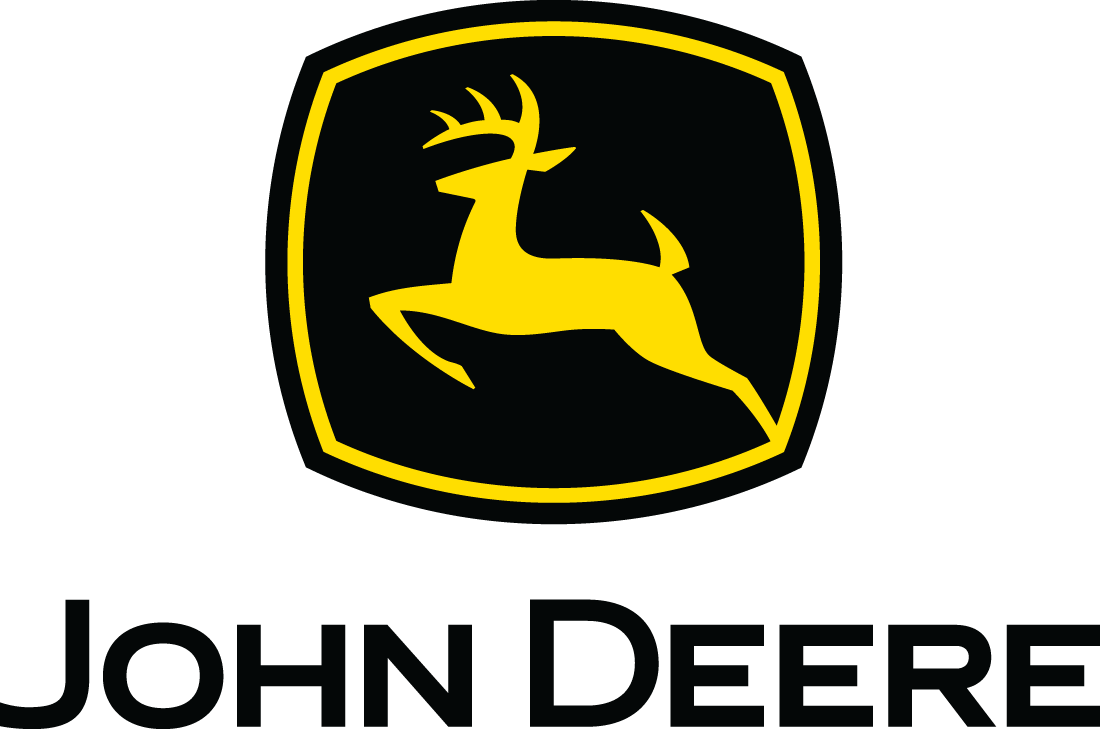
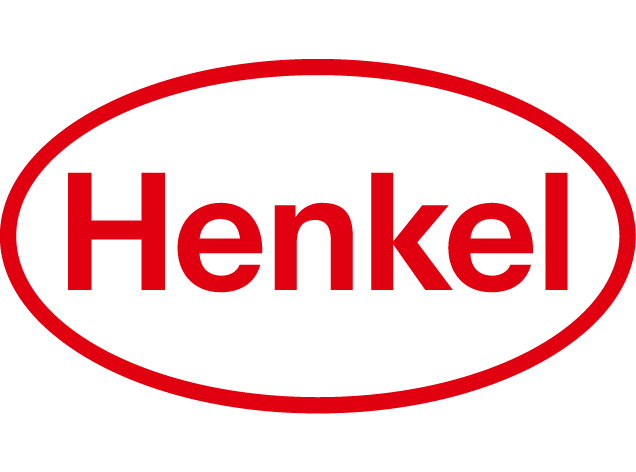
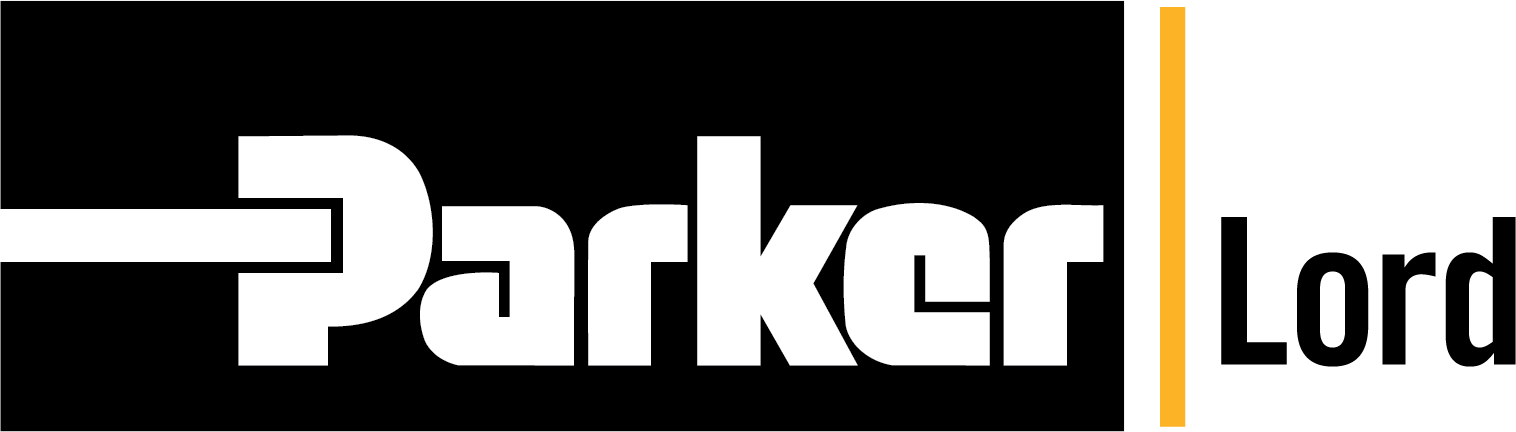
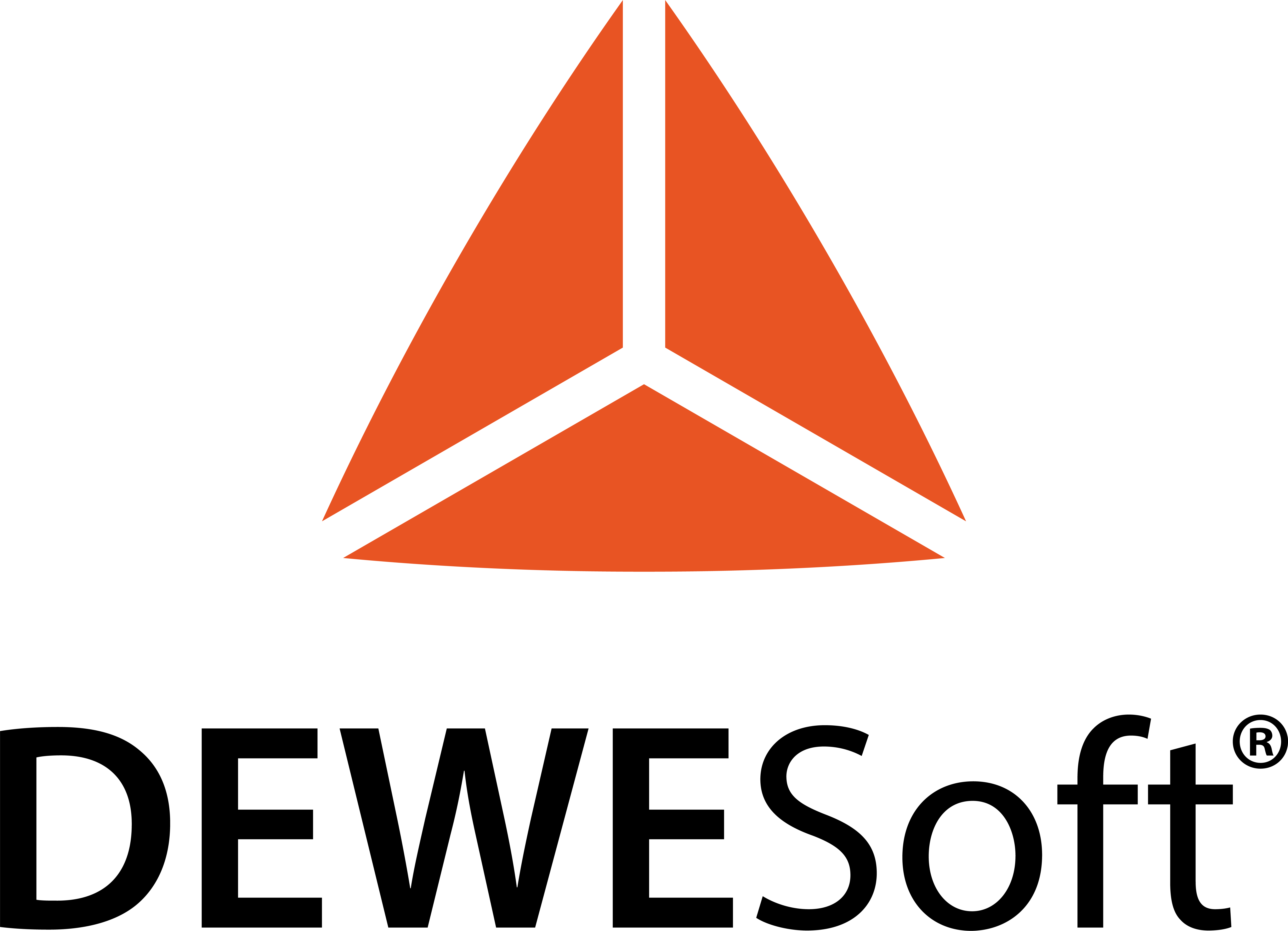
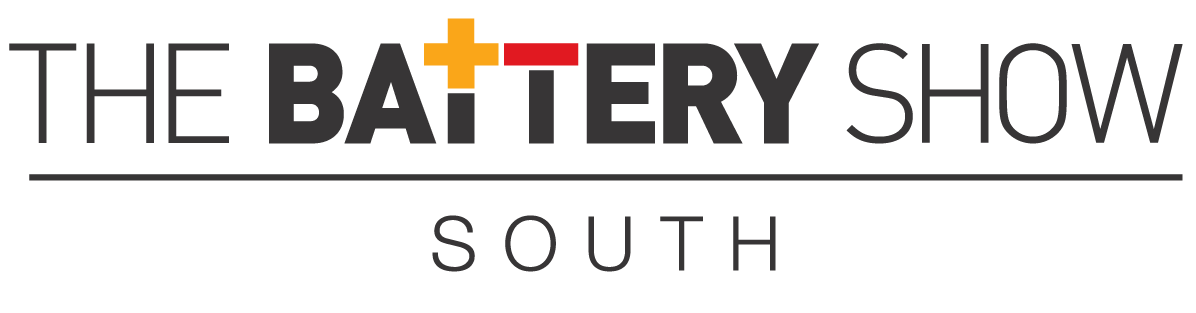
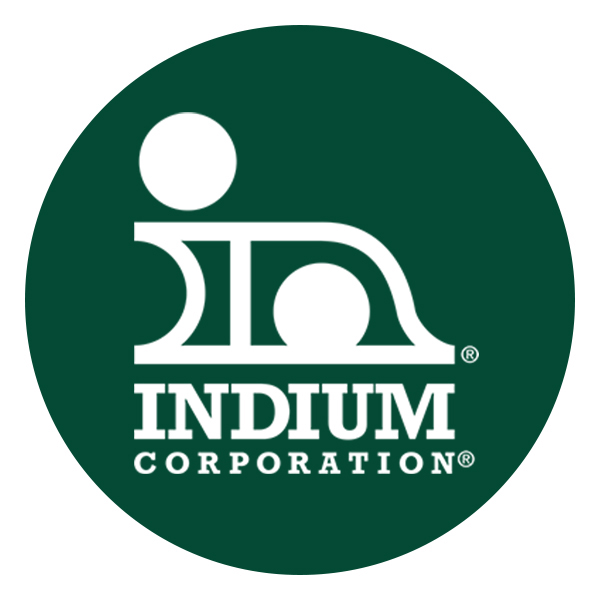
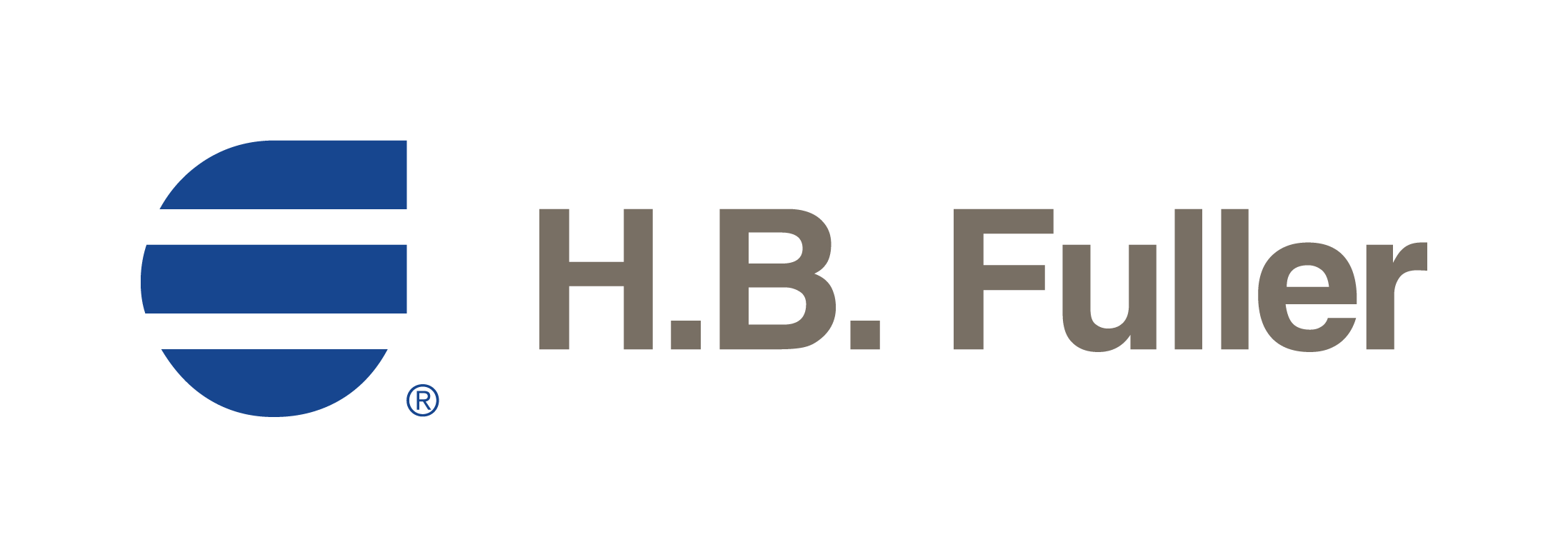