In conversation: John Stamford
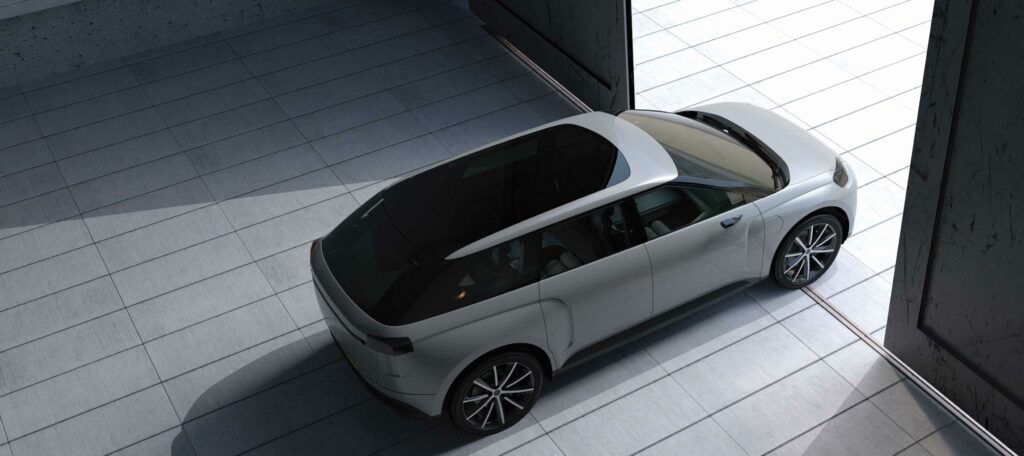
(Image courtesy of Dyson)
Green guru
The advanced powertrain chief engineer of Jaguar Land Rover got into EVs before EVs were even a thing. He tells Will Gray how far things have come
If you want to understand the evolution of electric vehicles (EVs), there are few better to speak to than Jaguar Land Rover’s advanced powertrain chief engineer, John Stamford. Having started his career developing ECUs for diesel engines, he got involved in EV development before EVs became a thing. The initial technologies he worked on achieved marginal gains, but they sowed the seeds for the future, and he has been involved in almost every generation of the EV evolution since.
“I’ve seen a lot of things come and go, and throughout that whole story, battery technology is what has paced development,” he says. “The electronics systems were there early on, although their integration and other ancillary systems have improved. The motor and inverter technology has been adapted, and applied more appropriately, but it’s the batteries that really underpin the whole journey and they are still not where they need to be just yet.”
Like many engineers, Stamford’s formative years were spent building with Lego and Meccano, but that gave way to a passion for electronics. Inspired by the early computers and electronic kits that his maths teacher father brought home for him to investigate, along with the Open University programmes he bookended his days with on BBC2, Stamford built a cathode ray oscilloscope in his early teens.
Later, he secured a place at Newcastle University to study electronics, and it was here that his research and development skills were honed, with him building a dyno and control system from scratch in the basement.
“We had been gifted an engine, but we had to set up all the systems around it,” he says. “We replaced the existing standard engine management system with our own improved sequential-injection version, and spent a lot of time getting that operational. I’ve always been very practical and my ability to visualise good solutions has been with me from the early days.”
Stamford’s first job, working on ways to replace mechanical fuel systems with electrical solutions on Perkins’ diesel engines, was a world away from the EV industry, but it opened his eyes to what could be possible and to the disadvantages of fossil fuels.
Having seen the opportunity, he moved to Wavedriver in 1997, where he was involved in developing an electric bus for the 2000 Olympics. It worked, to a point, but it demonstrated the shortcomings in the area at the time.
“The world wasn’t ready for electric vehicles back then,” he recalls. “They had lead acid batteries, induction motors and an advanced inverter/charger drive, but although they put their system into many different vehicles, all the ancillary systems that normally run off the engine weren’t electrified, so we ended up having additional motors driving belts, running compressors and pumps, and they just sat there, on most of the time, consuming energy and reducing range.”
Stamford soon returned to the diesel world, joining Motorola to lead the development of its ECUs for heavy duty vehicles, and shifting focus from specifying ECUs to designing and manufacturing them. He spent the next four years innovating in the ECU design space, mainly on control systems in high-temperature and high-vibration operating environments, but when the company chose to relocate to Germany, he stayed in the UK and joined an old boss at Ricardo.
It was there that Stamford set about establishing the Ricardo electronics group, most notably developing the Bugatti Veyron dual-clutch transmission-control unit. Following the project’s successful conclusion, he returned to the EV space, developing hybrid innovations for various OEMs.
In the short time since leaving Wavedriver, technology had moved on and minor fuel-efficiency gains were to be had, firstly with what Stamford calls “micro hybrids”, which use the alternator as a battery starter generator, and then with more powerful “mild and full hybrids”, which provided limited amounts of electric-only operation.
This work attracted the attention of Chinese OEMs, including Cherry, but Stamford recalls: “The electronics and drive systems were there, but people hadn’t really integrated them. The batteries were improving, and were adapted to be less about cold cranking amps and more about accepting and delivering energy, but in those early days it was all about the application and learning about the technology.
“There were no real voltage standards for the mild, hybrid systems – some were 48 V, some hundreds of volts – while the drive components, consisting of IGBTs [insulated-gate bipolar transistors], capacitors and transient suppressors, as well as battery management systems, and the control software and systems that go around those devices, needed progressing in terms of integration and diagnostics. There was a huge amount of learning about what was important at a system level.”
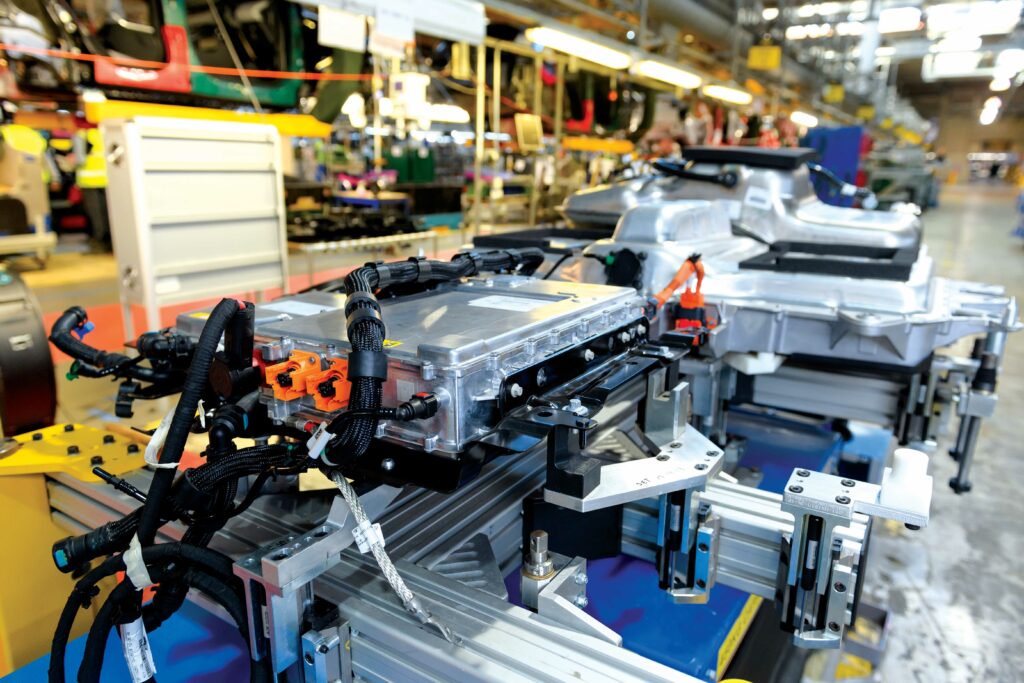
(Image courtesy of JLR)
Racing innovation
In 2007, when Formula One began discussing plans for hybrid technology, Mercedes AMG High Performance Powertrains hired Ricardo on a consultancy basis to help build its knowledge base. Soon after, it took on Stamford as head of electronics. In 2009, the optional use of the Kinetic Energy Recovery System (KERS) was introduced, with four teams – including McLaren Mercedes – putting it to use, but only at certain circuits where it offered enough benefit.
Having experimented with Flybrid’s flywheel approach and other tech, Mercedes opted for a more traditional system with a maximum permitted power of 60 kW. Its system was the first to win, in Hungary, but the marginal laptime benefits did not justify the investment for many and the system was dropped for a season, before returning in 2011.
Mercedes focused on reducing size and weight, and it used improved transistors and in-house power modules, working closely with battery suppliers to boost the power density of the cells by optimising the chemical, electrical and mechanical aspects of the cell. At the same time, the company wanted to quickly apply EV technology in a roadcar project and this led to the creation of the SLS AMG Electric Drive, for which Stamford was made chief engineer of the battery technology.
The car was designed with four 150 kW electric motors, one in each corner, and a 60 kWh battery using innovative pouch-cell technology. The system was packaged in the engine compartment and the transmission tunnel, and the car beat its ICE equivalent in a straight line, although it lost out on a lap of the legendary Nürburgring circuit due to its weight.
“Mainstream developments were taking five or six years, but the race team was able to do it much more quickly,” he recalls. “It was a really exciting project because we were pushing cell and battery technology hard, as well as developing advanced battery management features. It was a combined energy and power requirement, because it needed to have both the power and range, which we were aiming to get north of 250 km.”
Even at that point, the EV landscape was still fairly intermittent. Interest in early prototypes had waned, but companies were starting to believe EVs were on the cusp again and many were starting to conduct market testing. A number of different offerings started to appear on the market, but they were not seeing much take-up.
When Formula One doubled down on energy recovery systems – literally doubling the power to 120 kW and adding a turbocharger heat-recovery system, the MGU-H, to the kinetic system, which was renamed MGU-K – Stamford returned and developed a system he recalls as being “quite a work of art”.
The entire system was the size of two shoeboxes, sat beneath the driver. He explains: “The integration of all the electronics in a volume-efficient package was really ahead of its time. It was running at high voltages, and we started to introduce more efficient silicon-carbide switches and new battery management systems. I believe the Mercedes ERS system was the envy of the field, and contributed significantly to the powertrain and team’s success in winning Formula One world championships.”
So, did any of that technology truly transition from Formula One into roadcars? “Absolutely,” says Stamford. “The Formula One technology was expensive, but while they wouldn’t directly transition to the roadcar space, the concepts, the thinking and some of the integration did migrate, and now high-efficiency, high-speed electric machines and integrated high-voltage systems are seeing the light of day in many roadcars.
“We also did a lot of work on both the roadcar and Formula One projects on electric shock and fire hazards. We set fire to lots of batteries – deliberately, I might add – and had some issues we weren’t expecting. The philosophy in Formula One is to push it until it breaks, then back off a bit, so by doing that with batteries we learned an awful lot about failure mechanisms.”
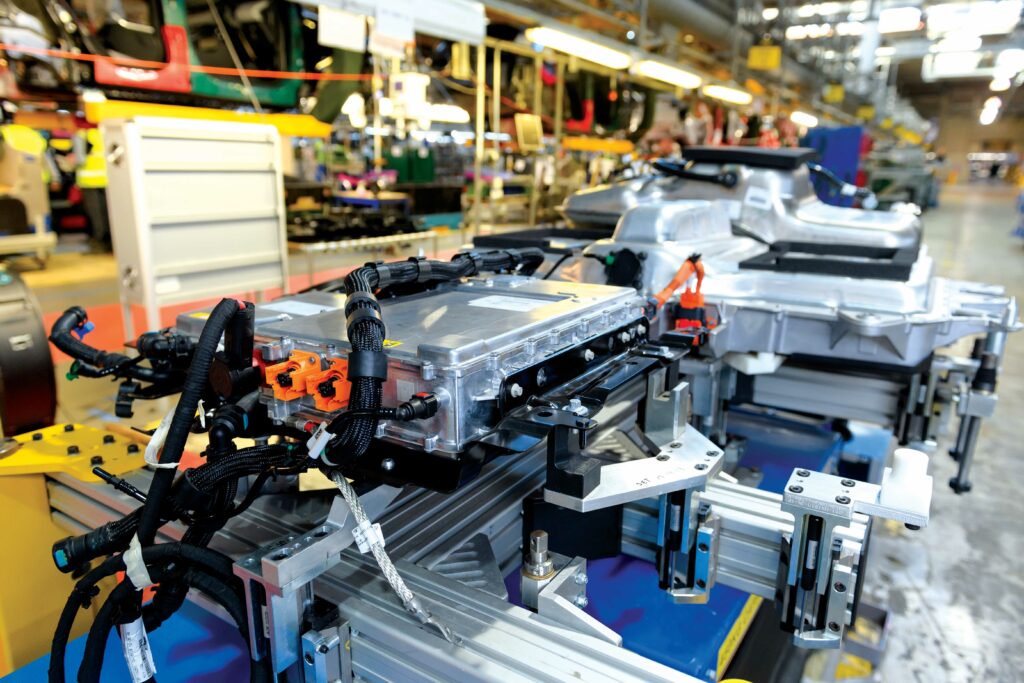
(Image courtesy of JLR)
Taking things forward
Stamford left Formula One in 2017, to join Dyson as head of engineering on a roadcar project. The aim was to adapt in-house motor and battery tech for the slowly establishing EV market, with innovations such as 800 V architecture, battery switching to allow access to all chargers and a 600 mile range. But, ultimately, the project was doomed.
“James Dyson had invested a lot in electric motors and batteries, and he wanted to benefit from the economies of scale in that space,” he recalls. “I brought in an understanding of what was necessary to meet legislative, safety and performance requirements, and deliver those in terms of an integrated battery, motor and power electronics solution.”
However, just as the first prototype systems became operational, Dyson decided EVs were not for him. “It came as quite a surprise to us all,” recalls Stamford. “He had his eye on Tesla, which hadn’t at that time made any money, and as the magnitude of the programme became clearer, some OEMs were announcing plans to electrify, so stealing a march early was not going to be so significant.”
Stamford was then snapped up by Jaguar Land Rover (JLR) to work on its electric and hybrid powertrains. There, he influenced work on 800 V architectures, silicon-carbide switches and in-housing key technologies, and he began to take on the task of improving component integration; latterly leading JLR’s advanced powertrain development team, based out of NAIC at Warwick University’s campus.
“In the most recent generation of EVs, there are still four electric domains,” Stamford says. “There is the battery, the electric drive units, the charging and DC-to-DC converters, and the heaters and air-conditioning systems that all run off high-voltage circuits, but they’re all quite disparate, and all those enclosures, harnesses, connectors, cooling and safety systems that surround those components cost a lot of money.
“Trying to integrate those components was the obvious next step. I think packaging and integration will see huge development. Ultimately, there will be two high-voltage domains going forward: the battery and EDU. If we can avoid lots of different high-voltage domains, it’s much easier to move electricity around internally inside an enclosure than it is between domains, where you’ve got to shield and protect it.
“As you don’t charge and drive at the same time, you’ve got high-value power electronics in the inverter and a lot of high-power inductors in the electric motors, so there are opportunities to reuse the electronics and avoid duplicating them. That’s where the advantage comes; not just in the physical integration of the different components, but also in technical integration and reusing components for multiple purposes.”
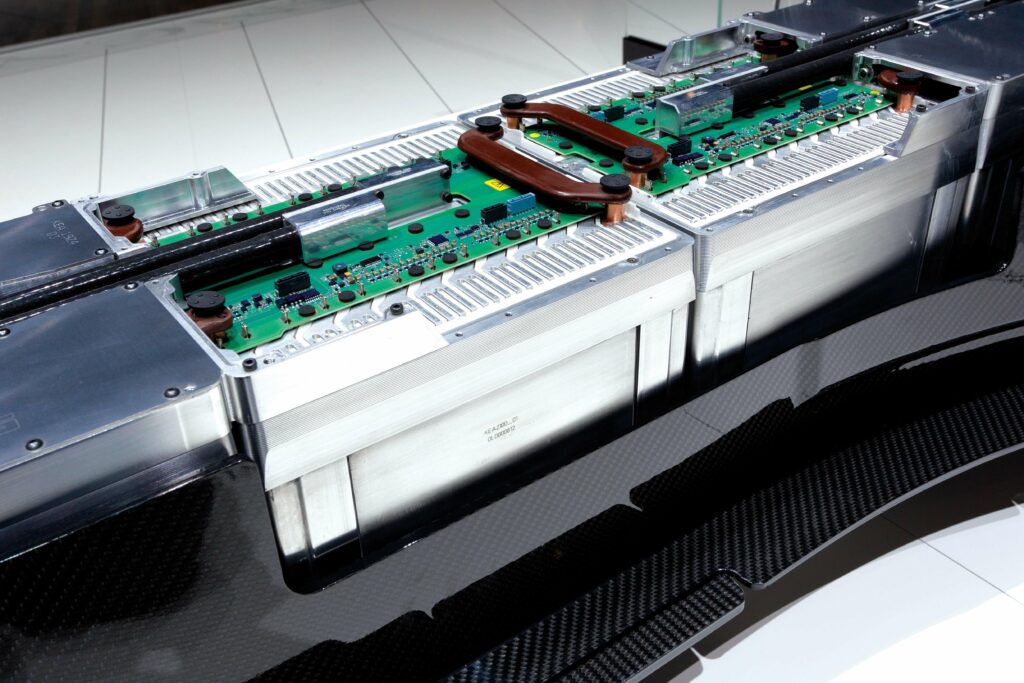
(Image courtesy of Mercedes-Benz)
Future technologies
Stamford explored some of those efficiency gains while at Jaguar, whose electric racing team recently became Formula E World Champions, and he says: “Some of the racing stuff is really interesting still, as the competition keeps driving progress – both in Formula E and Formula One. At Jaguar, I had a good review of their Formula E systems and made a few suggestions around the application of some of the technology in the racecars.
“The power electronics and motors are all open for development in Formula E, and it is really an energy formula, so it’s all about using the joules sensibly and efficiently. They have to be very careful how and when they apply the finite energy through the race, and that is a strategy discussion that encourages efficiency development, because if you’ve got the best technology and waste the least energy, you are in a better position to use the finite battery energy for performance.”
Achieving that, says Stamford, is not only the key to better efficiency, but also a great way to reduce the cost of EVs and accelerate their transition into the mainstream. However, that is not the only area of development he sees as being important in the coming years – with system redundancy, battery health transparency and range acceptance all taking high priority on his industry to-do list.
“Autonomous driving is on the way, so we need to avoid the potential for single-point failure modes that can take out all the systems on the car,” he explains. “That will be crucial, and to do that we need to think how the high-voltage systems are architected to give redundancy, ensure they are always available, and have a suitable backup system or fail-safe if a problem happens when you have your feet off, hands off and eyes off the controls.
“We are at the point now where EVs are just about reaching a cost parity with ICE, but the resale value is still hurting EVs, and I feel battery health needs to be more transparent. You could have a car that has done 10,000 miles, but has a battery that is at the end of its life, or a car that has done 100,000 miles and has a good battery that will last for a long time, and you just don’t really know by reading the odometer. Providing transparency of battery health will help, but I think that will scare quite a few companies.
“When it comes to range, adding battery to increase range costs weight, dollars and volume. So, I wonder, have we got to an acceptable range number now? And the key thing is about being able to charge quickly when necessary. Ultimately, that is more cost-effective than adding extra battery capacity, because driving around with an expensive battery that you don’t use the majority of the time is not sensible. That’s an interesting development area.
“Batteries will keep evolving too. They improve by about 3.5% every year and I think that will continue. My view is that solid state batteries will come in and follow a very similar evolutionary trend to the existing NCM cells. Solid state cells do have more packaging potential if you can reduce the safety zones, which will allow much tighter physical integration, lower weight and improve energy density, putting more energy into a fixed volume within the car.”
Ultimately, Stamford believes the benefits of EVs will truly start to be felt once the entire electrification of our day-to-day world takes shape, led by the passenger car market, followed by the high environmental-impact two- and three-wheeler applications, and then moving more into heavy-duty applications. Charging infrastructure is still an Achilles heel in the adoption of EV technologies and Stamford believes DC charging will dominate in the near future, even for home charging.
Eventually, with solar panels on rooftops and heat pumps powering indoor climates, the car will not just be a car; it will also take on the function of a power source. Developing the infrastructure to make this possible is, arguably, top of the priority list.
“You potentially have two sets of 100 kWh batteries on your drive, and the technology is now able to export that energy to support the home and grid,” he says.
“That will allow smart energy management in the house, and as we move to the green energies of wind and solar, which are not consistent in their availability, EVs will play a major part in balancing all those things in a more cost-effective way. And that’s going to be the real revolution.”
John Stamford
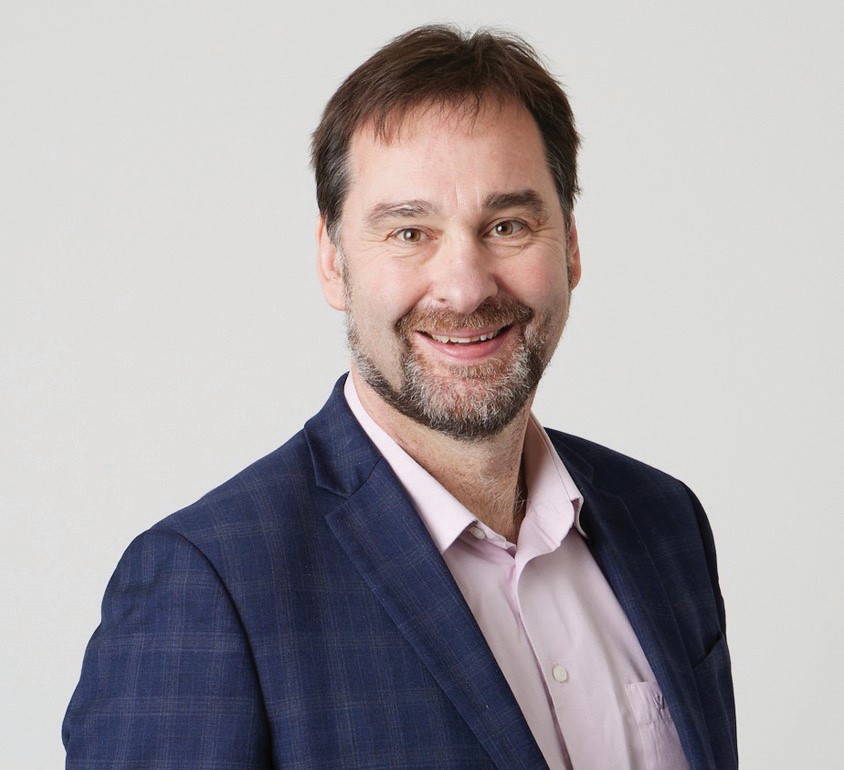
ONLINE PARTNERS
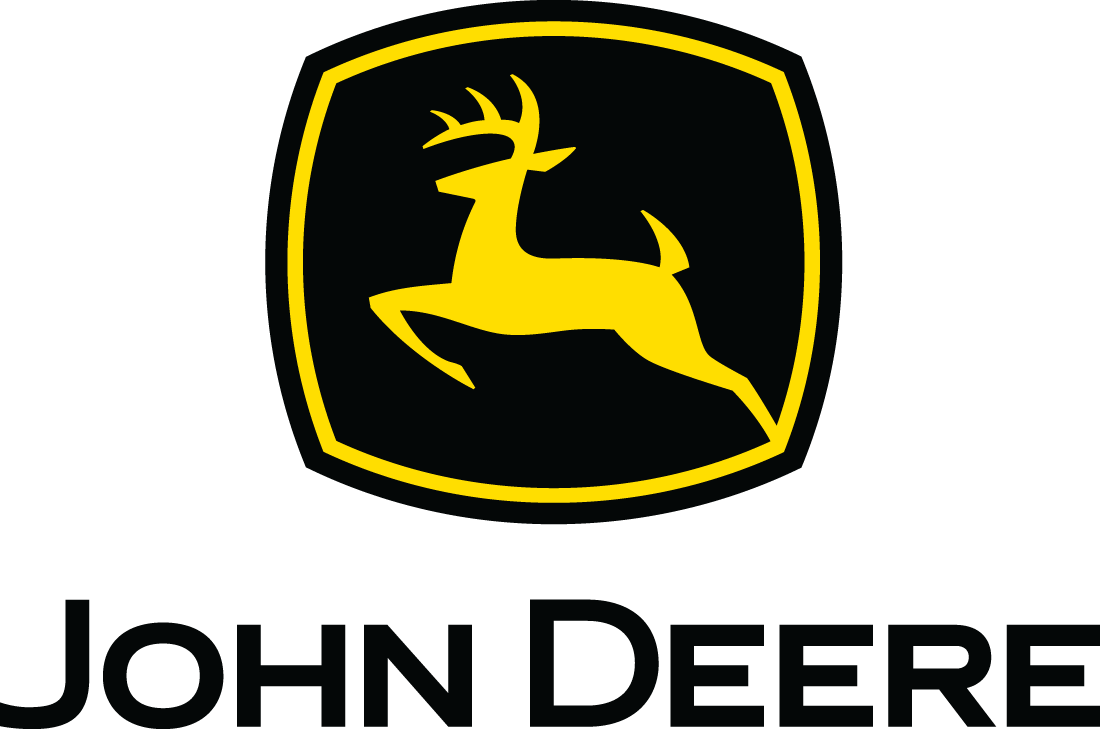
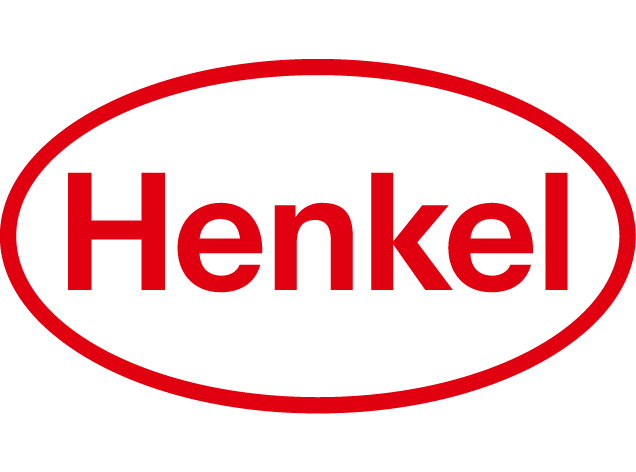
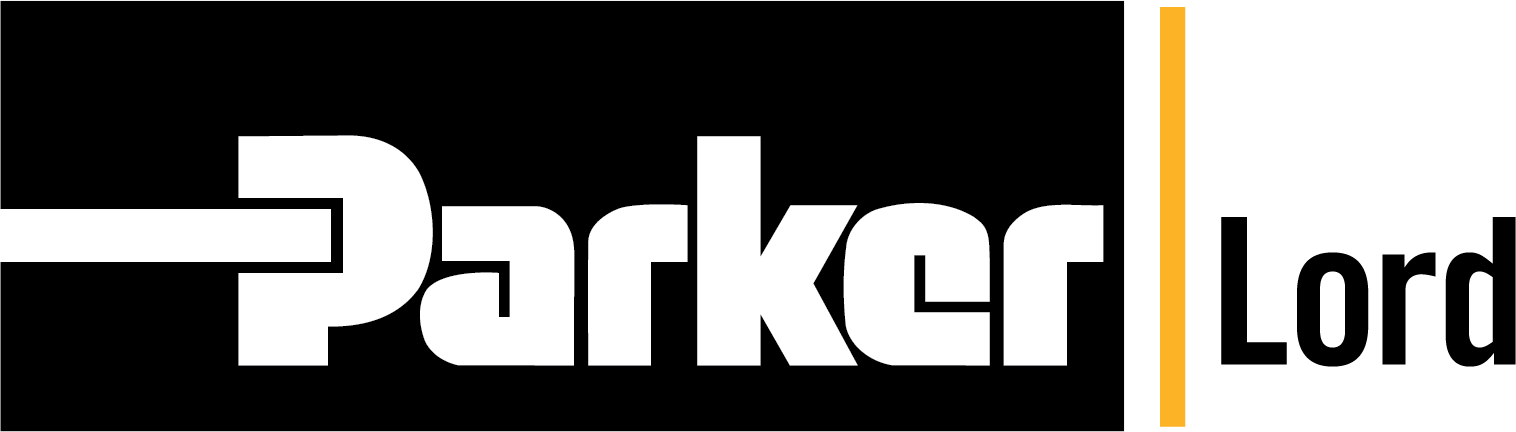
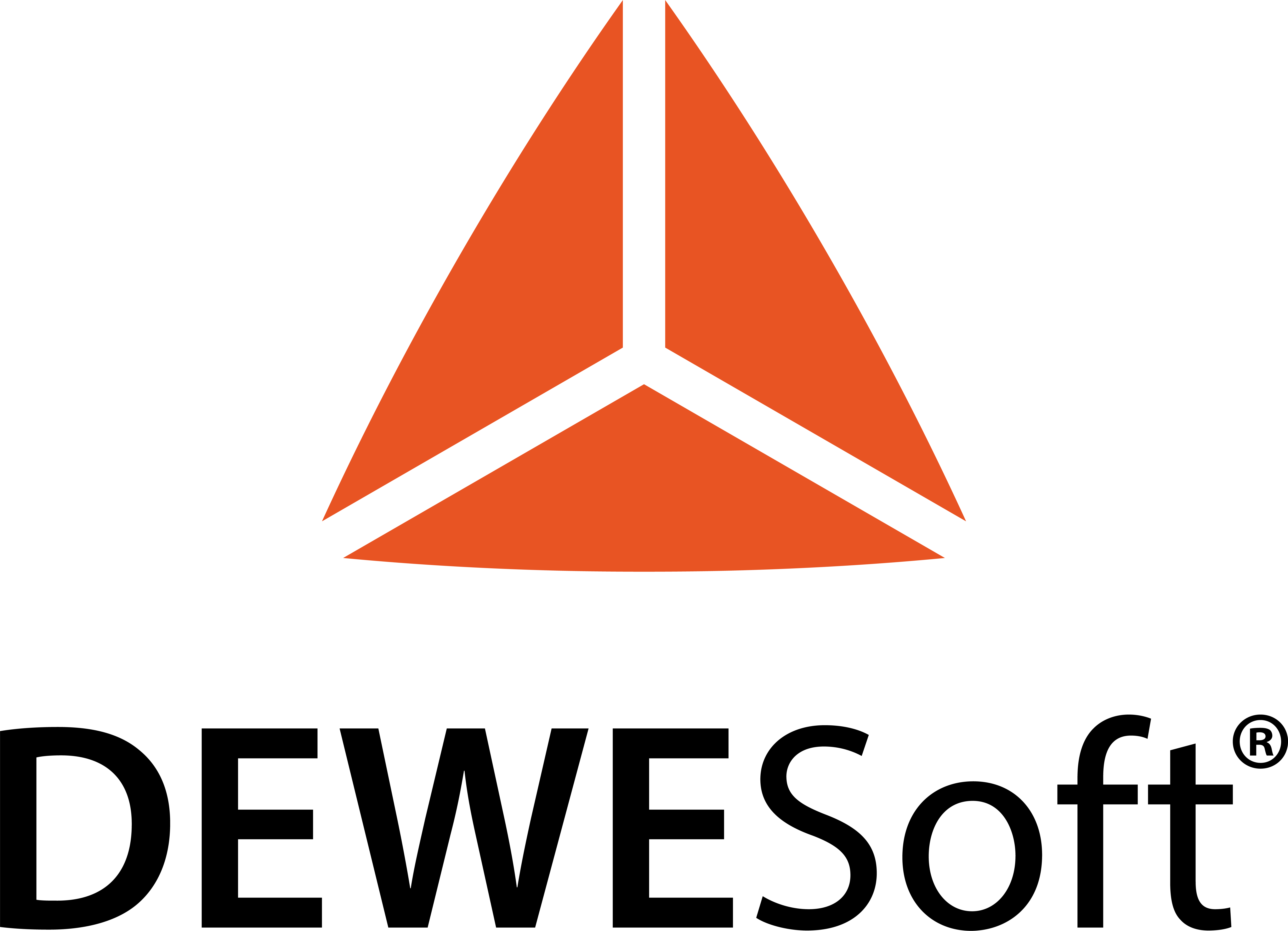
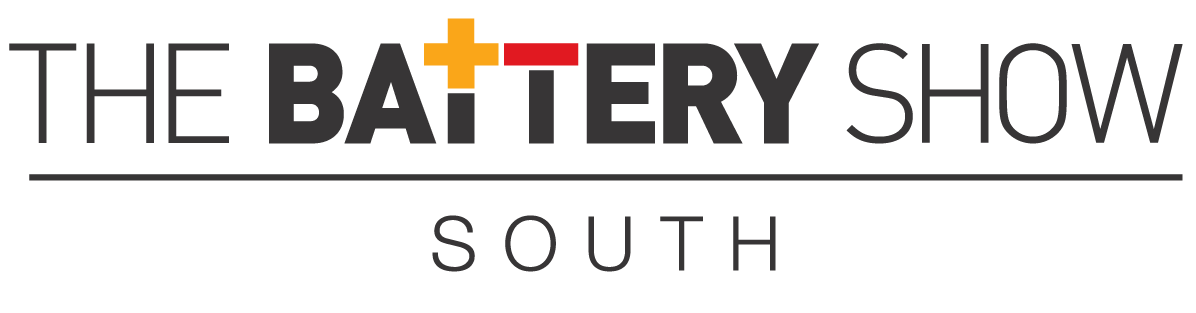
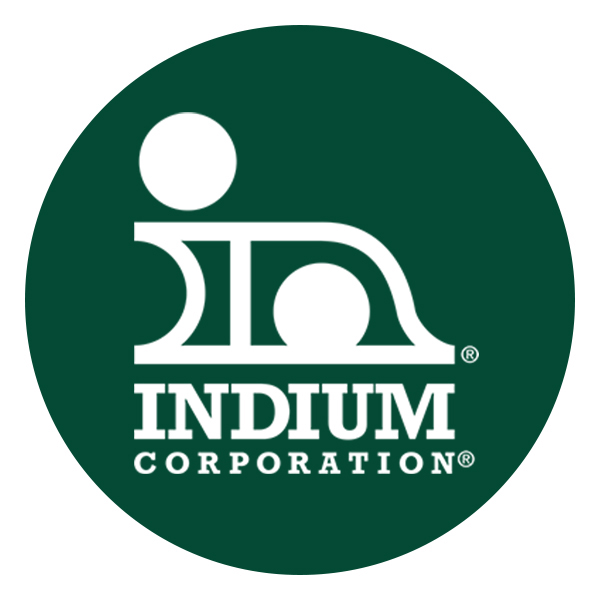

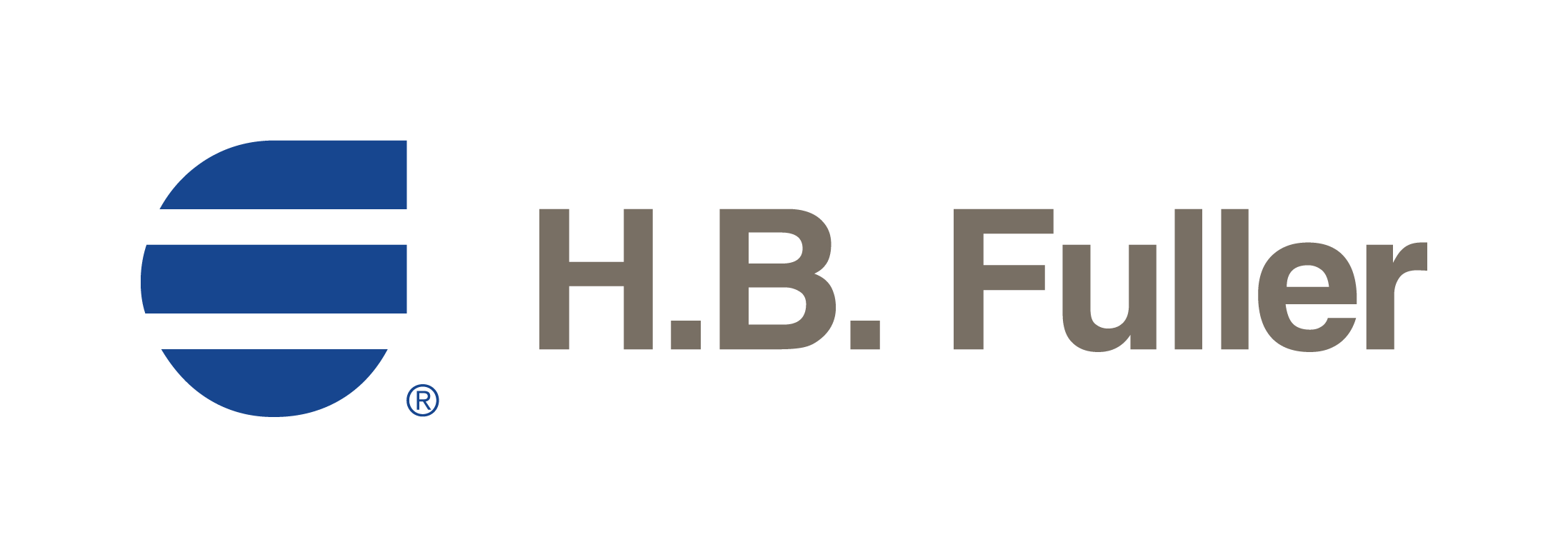
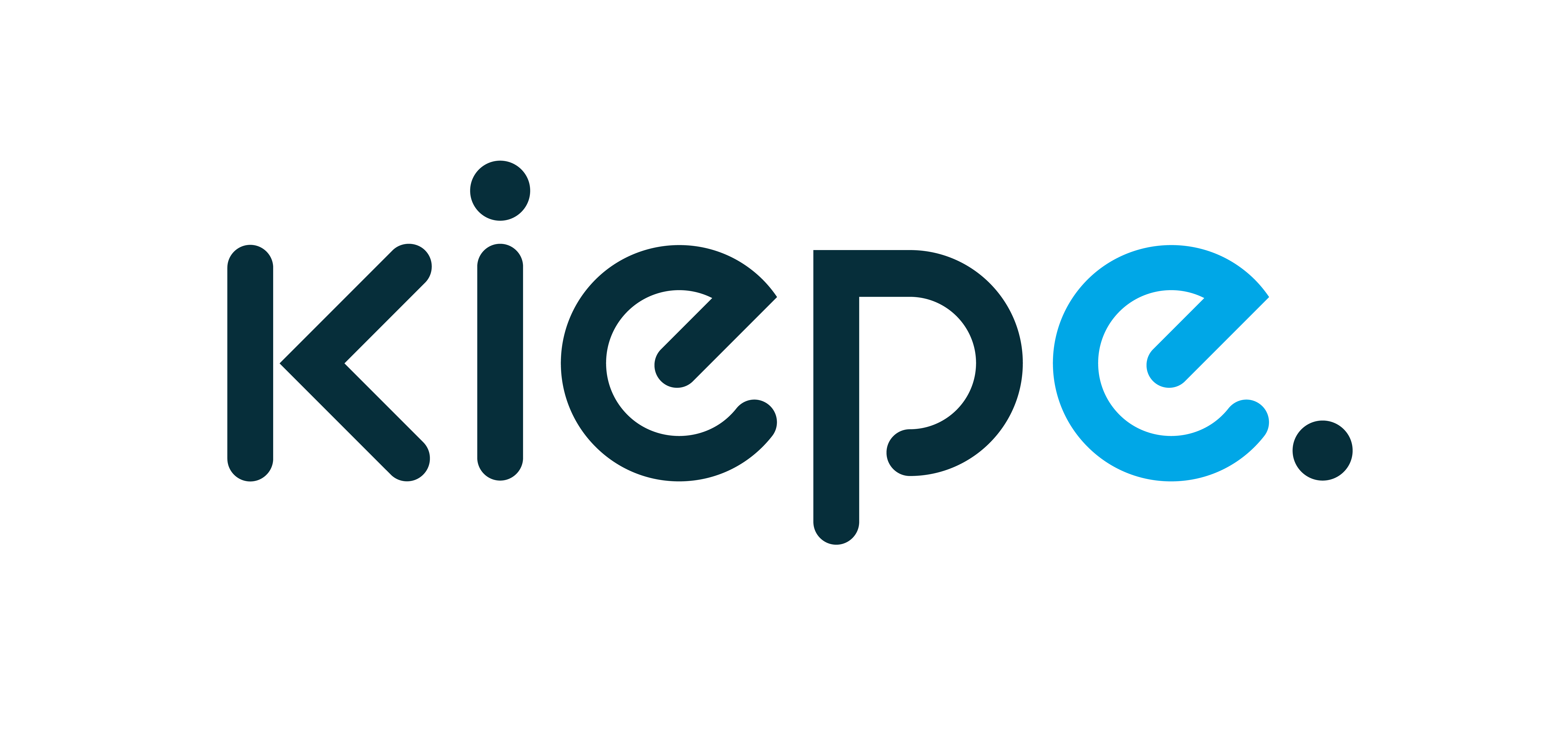
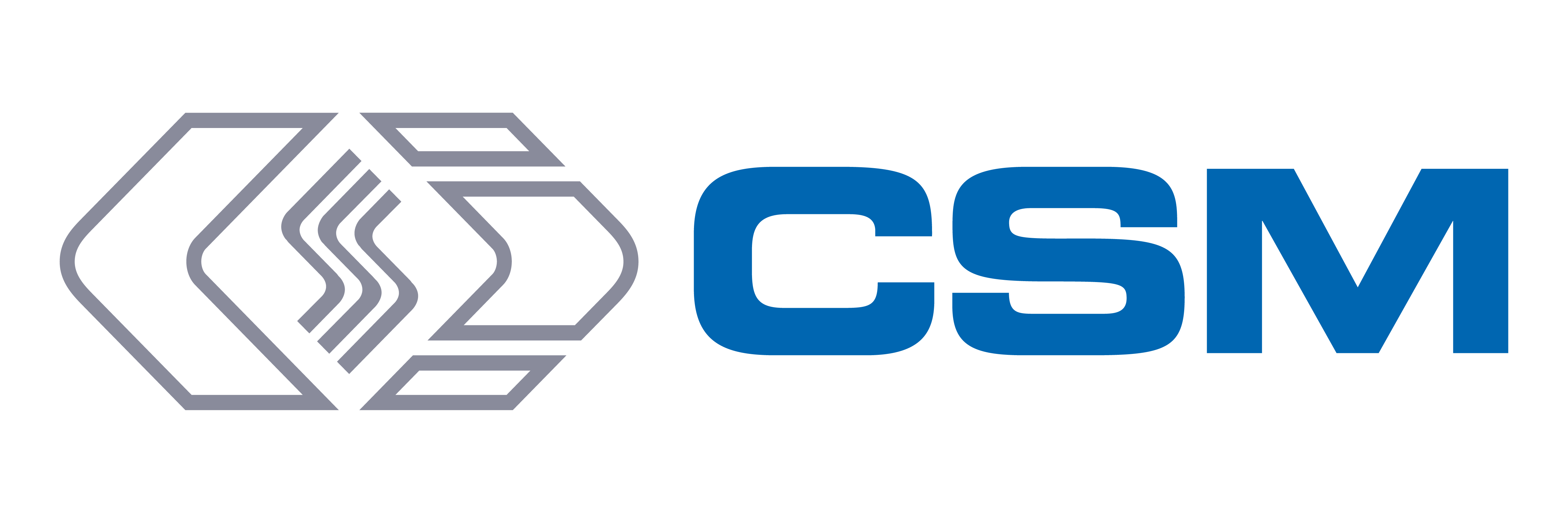