In conversation: Tony Fong
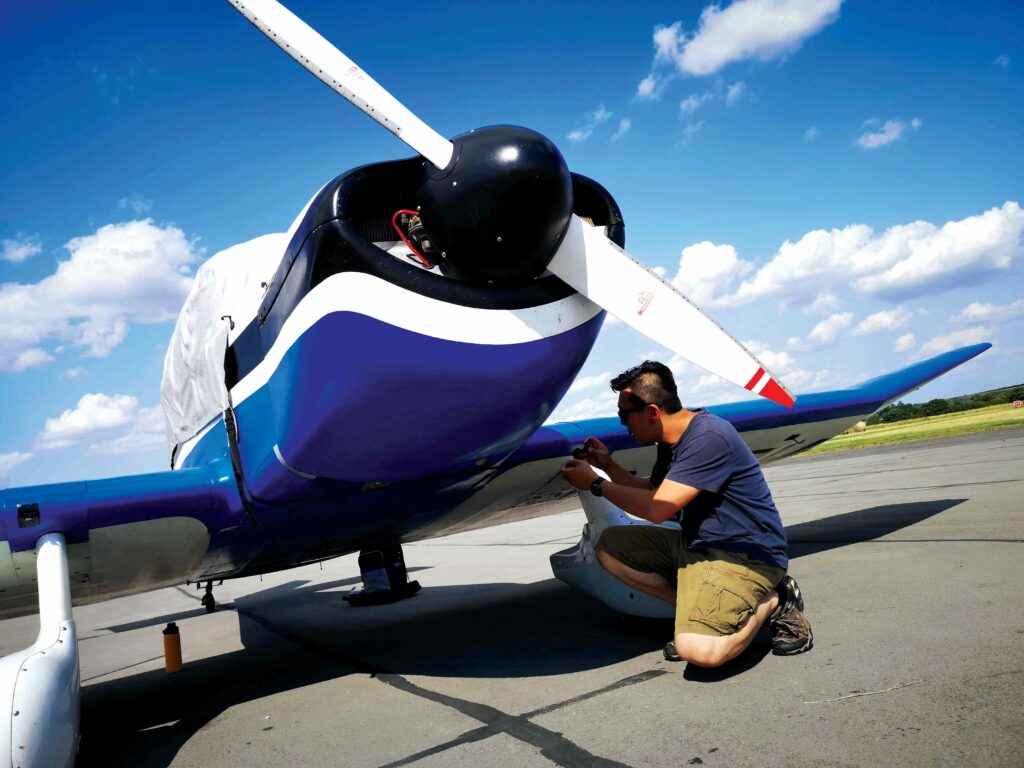
Tinker Tailor
Everrati’s head of engineering discusses novel ways of electrifying classic cars with Will Gray
Electric vehicle (EV) technology is moving at a rapid pace and much of that is thanks to people like Tony Fong. As head of engineering at luxury electric car company Everrati, he is pioneering cutting-edge innovation in the most unlikely of places – by implanting the latest powertrain components into old classics to create the systems of the future.
Fong is a self-declared “tinkerer” who loves nothing more than tweaking electrical systems in search for better performance. He has been doing exactly that ever since he was a child, when in his Malaysian birthplace he spent his youth flying radio-controlled helicopters and planes, and tuning the gyros and gaining control to optimise their flight.
Fast-forward to 2025, and Fong now spends his days working on far more complicated electric systems, hidden under the beautiful bodywork of Everrati’s range of luxury classic conversions, which includes the Land Rover Series IIA, Porsche 911, the distinctive Mercedes-Benz Pagoda roadster and the legendary Ford GT40.
The aim is not just to create a production line of magical electrified classics, but to use the system engineering processes involved in their development to push the boundaries of what is possible. Unleashed from the shackles of major brand OEMs, this is where Fong, who was originally trained in motorsport engineering, is in his element.
“It is kind of bridging the gap between Formula One, motorsport and automotive,” he offers. “Formula One is a scientific programme, albeit now with a level of cost cap, but this is about engineering in a practical sense, balancing the cost element whilst accelerating the integration of all these really good new components that are constantly being developed.
“We take a slight step back on the technology curve – so these components are validated and we know they work – and then we integrate them in a system and take it to market aggressively. It’s all about accelerating the process in a commercial sense, and demonstrating the vehicle and system can be registered, and it’s safe. That’s the magic formula.”
Fong’s career has followed the electrification evolution, moving from early-stage mild hybrids right through to the modern, full EV systems he is currently working on, and it all started with a realisation back in his remote-controlled flying days that electric power was not only key to eliminating emissions – it was actually the best powertrain system, full stop.
“There were lots of different power options you could use in radio-controlled vehicles – glow engines, petrol engines, electric and turbines – but even then the advantage of electric in terms of power delivery and refinement was quite apparent,” he recalls. “Now I can see that relating to the modern EV powertrains being developed.”
After graduating from Cranfield University with an MSc and following that with an MBA from Cardiff Metropolitan University, Fong secured a dream first job as a vehicle integration engineer at Ford, tuning cars and travelling all around the world to test cars in different environments.
At the time, even hybrid was still in its infancy, so much of Fong’s work at Ford and then Jaguar Land Rover focused on the Stage IV and V emissions-reduction standards and diesel particulate filters in ICE cars. However, these roles embedded in him an understanding of the entire vehicle development cycle, which he is now able to deploy in the EV world.
Hybrid innovation
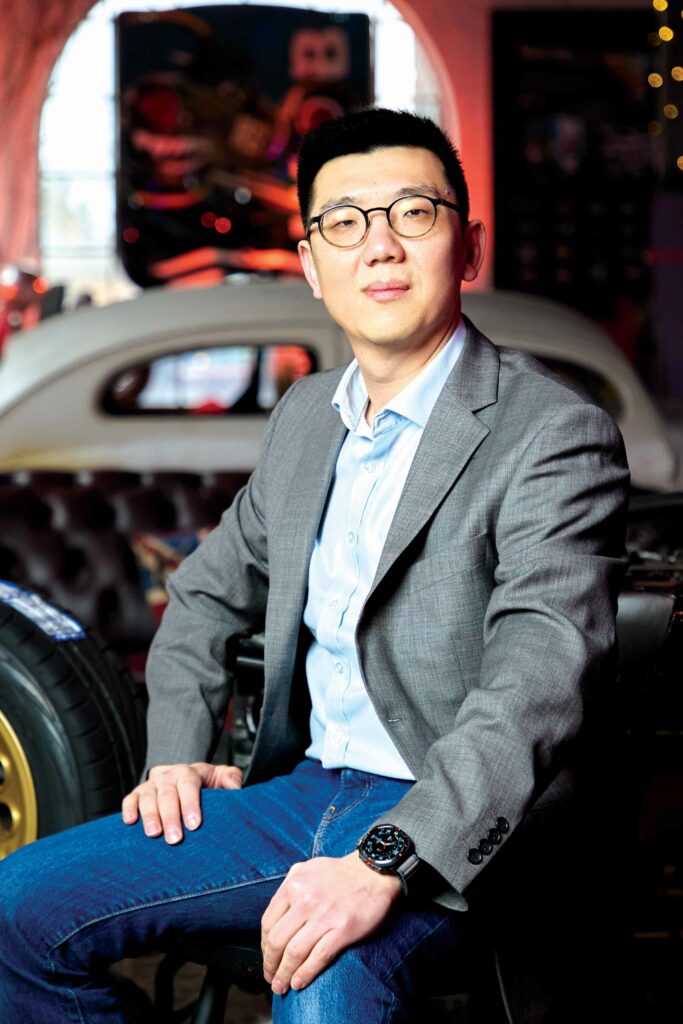
(Image courtesy of Tony Fong)
A move to Ricardo in 2014 fed Fong’s passion for innovation, and he began to specialise in electrics and systems. Many of his projects focused on mild hybrid technology and the innovations he worked on included an e-Supercharger, a belt integrated starter generator (BISG) and 48 V chassis control – a fascinating concept for a form of hybridised suspension.
“It used the battery to power the anti-roll bar,” explains Fong. “And because there was a lot of energy in the system going the other way too, if you could manage the surges that energy could be used to recharge the battery. It was very interesting and I think there’s still a lot of discussions around that, so it may advance in the future.”
Many of these hybrid programmes expanded on Fong’s past experience in vehicle integration as that is one of the biggest challenges of hybrid engineering. Indeed, he says the need to fit technology into an existing vehicle, rather than creating a ground-up design from scratch, makes its development far more challenging than full EVs.
After almost two years at Ricardo, he founded his own vehicle electrification engineering consultancy, AYF Solutions, and as hybrid technology matured and the development of EVs started to gather pace, he began to apply what he learned in the hybrid space to support OEMs with their efforts to steer their vehicles in a new direction.
“I’d built a good understanding of vehicle-level delivery and electrical design fundamentals, and I like problem solving, so most of my assignments involved parachuting in and trying to solve challenges faced by OEM component teams,” Fong recalls. “Often, when they had a big EMC problem, they did not necessarily know how to navigate around it, so I came in to help.
“The JLR battery team, for example, wanted to apply a common 48 V mild hybrid battery system across all platforms, but when you create common parts to reduce cost, there is always a compromise. On different platforms the battery could be installed under the vehicle, under the driver’s seat, in the boot, and they all had different unique challenges.”
Another project that Fong worked on was with MG, helping to develop its two-seat Cyberster GT Roadster at Longbridge prior to the factory’s closure. This briefly steered him away from electrical engineering back to chassis development, and at the time the vehicle – due to enter production this year – was a totally unproven concept.
Fong was tasked with working out how the car would perform on the road, but with no existing type comparisons available, it required a lengthy period of complex computer calculations and simulations – ultimately resulting in some interesting insights into the important impacts of an EV powertrain on the overall framework of a vehicle.
“When you measure roll-load data for the chassis and suspension design you normally start by using virtual data and simulations,” he says. “If you haven’t built the car, you have to find the closest type to it, and at that time there were a few two-seater hypercars around, but not many two-seater EV sports cars similar to the Cyberster.
“We had to use data from a number of two-seater ICE vehicles, and although the chassis on an ICE car and an EV are not massively different – the way it puts down in the suspension was quite similar – the extra weight adds more stress. Tesla, for example, has had wishbone failures, so it’s not just the powertrain that’s important in EV design; it’s also the chassis.”
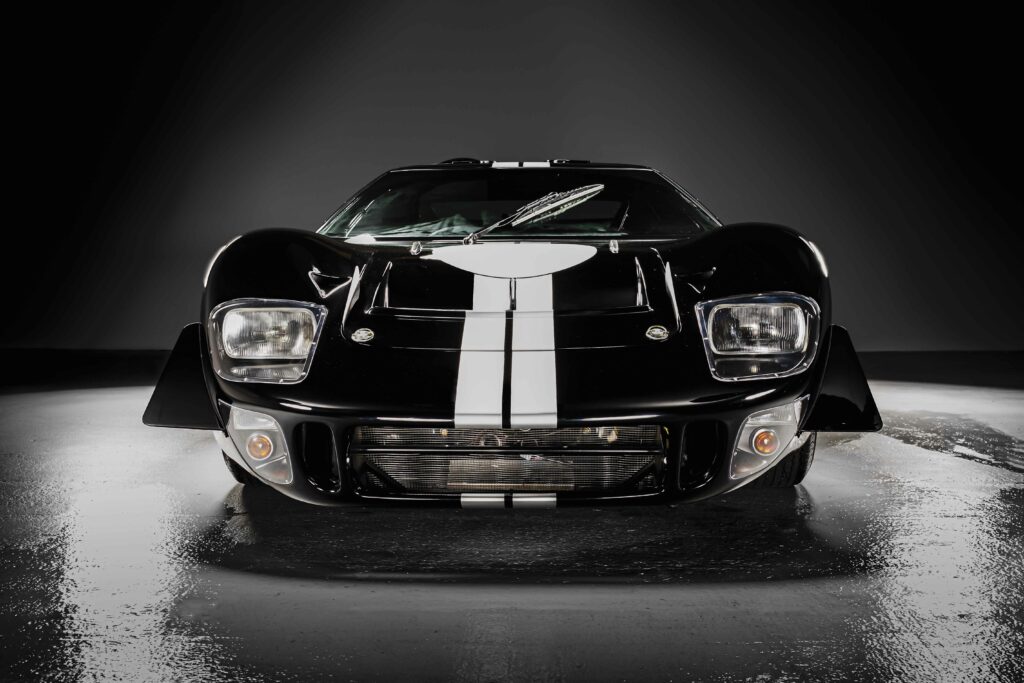
(Image courtesy of Everrati)
Electrified classics
In 2020, after around four years as a consultant and at the height of the global pandemic, Fong was approached by Everrati. The company was going through a funding round at the time and, pending its success, it was looking to hire an all-round EV expert to lead and accelerate the development of its electrified classics.
Fong’s ability to “wear many hats” was one of the qualities he believes got him the job, but so too were his hobbies outside of work.
“I am still involved in aeroplanes, but now I’ve got a pilot’s licence and I’m tinkering with full-size classic aeroplanes,” he explains. “I also competed in drifting, so I had done lots of vehicle tuning in my own time too.”
His unique and diverse skillset – spanning electrical and battery design, vehicle integration, compliance and commercial expertise – has been instrumental in Everrati’s evolution from a start-up to an established leader in the luxury automotive sector.
These are not vehicles for the masses. These are exclusive vehicles meticulously crafted for discerning owners with concours-standard restoration, state-of-the-art electric powertrains, and the finest materials and craftsmanship. To achieve this, the Oxfordshire firm works with leading UK and global partners, including Aria in California and W Motors in the UAE.
“We only build certain models and there’s a reason why we do that,” says Fong. “It takes between 4,000 to 15,000 engineering hours to develop a car properly from scratch, and while some people are willing to pay for that amount of development, in terms of building our company profile we settled on vehicles to develop then productionise.
“We’re trying to preserve the classic car as well as electrify it, and it’s a bit like a listed building – you can’t change much, but you want to use the latest materials and make them function well within that space. The models we selected have different powertrain layouts and different power requirements, so they cover as much variety as possible.”
Fong’s first task on arriving at the company was to lead the design and build of its first car, a Land Rover, in just eight months – with everyone working from home during lockdown. The company’s ethos, to optimise repeatability by not cutting the chassis and using clean bolt-on adaptations, added even more complexity to the challenge.
The development of that first-of-a-kind car, and others since, began by 3D-scanning and weighing the existing vehicle, with and without the powertrain, to identify the target weight and mounting reference points. This was followed by simulations to determine the power, weight and range that would be feasible, and what figures to target.
Fong explains: “Obviously, there’s a trade-off: if you want more range, the battery is going to be heavier, so we need to work out where the sweet spot is. We start with the art of the possible, and the absolute baseline is for it to perform with at least the same or greater performance as the original vehicle.
“If it’s a Porsche, for example, the benchmark will be the turbo variant. Then we work from there, and start to calculate if there is a possibility to have more power and how that knocks on to suspension upgrades, and so on. We do a cost-benefit analysis within the packaging space to work out if we take a different motor and gearing – what does that look like?
“One thing that isn’t often discussed in the EV world is that because an EV motor is a single gear, you have to determine whether you want top-end performance or low-end torque. If you halve the top speed, you have twice the torque in terms of acceleration, so a lot of early-stage simulations are done to work out the optimum performance.
“The whole powertrain and system integration is limited by the weakest link. For example, if the motor can do 800 bhp, you need the inverter and battery to match that. In the real world we also try to balance volume effects, where if we use the same types of motors in other vehicles that can have a positive benefit on the overall price points.
“The software side is then all about refinement, because power without control is nothing. The old turbo Porsches, for example, had shocking turbo lag, but electrification delivers all that performance with linear power delivery. That goes back to my good old days of flying my model airplanes – it’s the same, the refinement, and that’s the enjoyment of it all.”
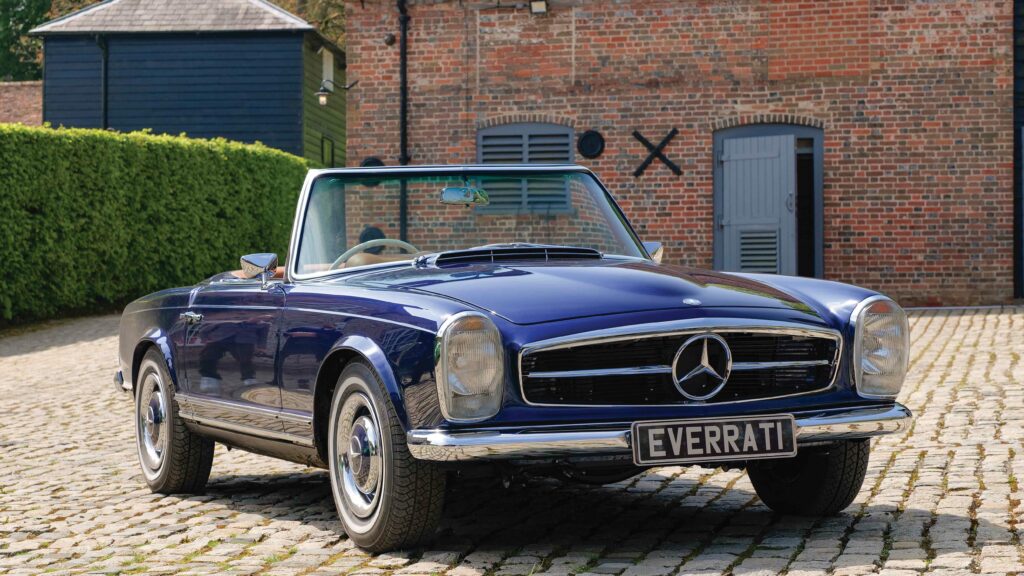
(Image courtesy of Everrati)
A repeatable process
The key to the company’s success is the repeatability of the process, but also the quality improvements and cost-efficiencies that can be achieved over time.
Fong explains: “We have a continuous improvement programme, so when we built car number one, as we went through the whole validation process we learned how things could be done better.
“When you are dealing with cars that are up to 60 years old, they’ve often been through a lot and the build process was also not as precise in the past. There’s quite a bit of variance, even between different periods of the same car, so we set very specific instructions to ensure donor cars are as close as possible to the one we used for the original design.
“As we do more cars, the core of the design – things like mounting points – does not massively change, so we do not need to revalidate it. But, naturally, the more you build the better it will get, so once we’ve done car number three or four, we go back to car number one and offer to upgrade it if there’s the opportunity to do so.”
Fong has taken personal satisfaction from each of the vehicles he has developed, but points to the GT40 as “the most exciting one” because of its status as a legendary, high-performance car. The electrified version uses a Helix motor, proven on the Lotus Evija, and the initial development process turned out to be very quick indeed.
“We started off by following the same architecture we had on our first vehicle, the Land Rover, even though it’s a very different requirement in the way it delivers the power,” he recalls. “We dropped in the battery and within two weeks we were doing 140 mph at the runway – that was one of my most satisfying moments.”
Fong’s pride in the Land Rover, meanwhile, is based on his team’s success in proving it possible to achieve multi-vehicle production repeatability. “We did a second-generation update, doing a cost-down exercise, refinement, simplifying the assembly, and we made it a lot safer, more user-friendly and so easy to drive.
“We wanted to preserve the original feel, the four-wheel-drive system, the clunk in the gear selector, so we reworked the mechanism into a drive selector and retained the transfer case, so you can still play with diff lock, and high and low gear. I was really proud to show that we can build cool cars, but to a viable business case and in a streamlined way.”
In contrast, the Pagoda is about pure refinement – and being able to achieve this by using modern technology whilst meeting the UK’s strict requirements for re-imagined classics. The axle, suspension and chassis must all remain the same, and being able to maintain the drive and feel of the original proved to be a very satisfying challenge for Fong.
“The Pagoda is a front engine, rear-wheel-drive car, so you have to keep the rear axle and the ring and pinion gear, and drive your motor into that,” he explains. “We had to work out how to refine that mechanically, by making the prop design work really well, and we also had to make the ramp-up strategy and the regen strategy work harmoniously.”
The company works with a range of suppliers, and Fong’s past experience has ensured it has an “escape path” if one supplier lets them down. It has also been crucial to understand the homologation framework – EMC guidelines, battery and electrical safety, mountings – to ensure these machines are brought to market.
In fact, those elements are key to Fong’s future plans, which revolve around Everrati’s growing business-to-business offering, Powered by Everrati. He explains: “We’re now looking to create a scalable, modular system with flexible packaging – a family of powertrain systems that can be used for other niche vehicle manufacturing.
“We’ve been through that development cycle, and I think we can address that pain point for a lot of people because we have a demonstrable vehicle. We’re also teaming up with Soda SDV, which uses a software-defined vehicle and a library of features to create fully validated control systems for other vehicles.
“We use a Helix motor, validated on the Lotus Evija, a McLaren inverter validated in our platform, and we are partnered with Raeon batteries, and all of that allows us to take our systems and apply them in any car that any other company wants to do, with fully flexible and validated solutions. That’s the next phase and it is something that really excites me.”
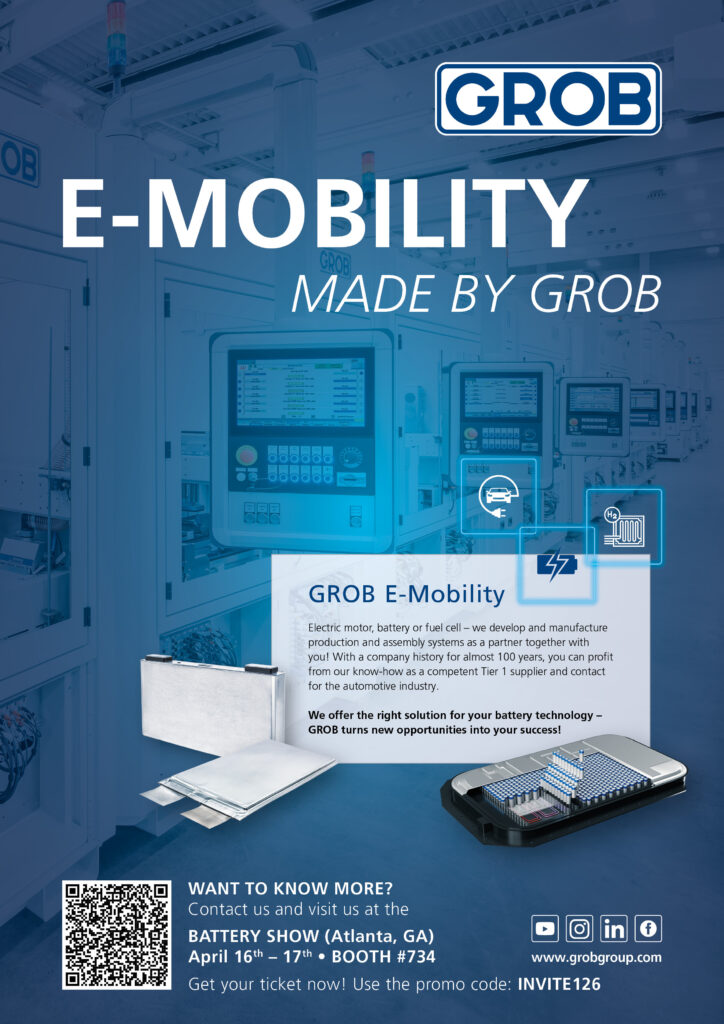
ONLINE PARTNERS
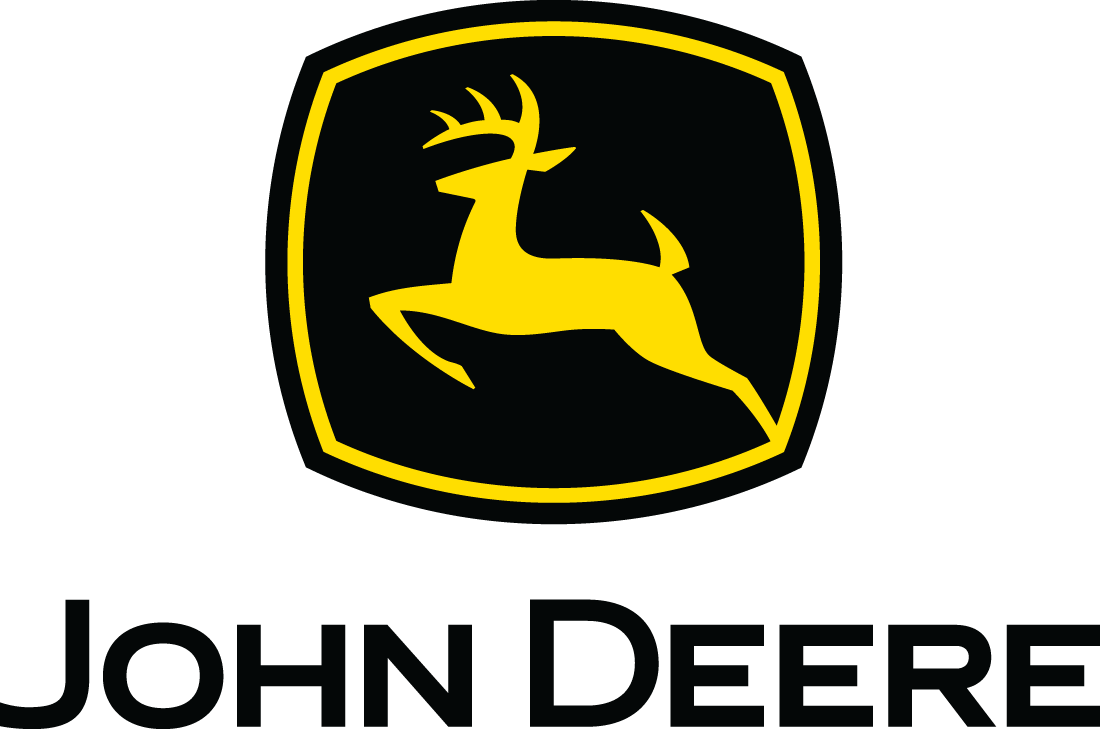
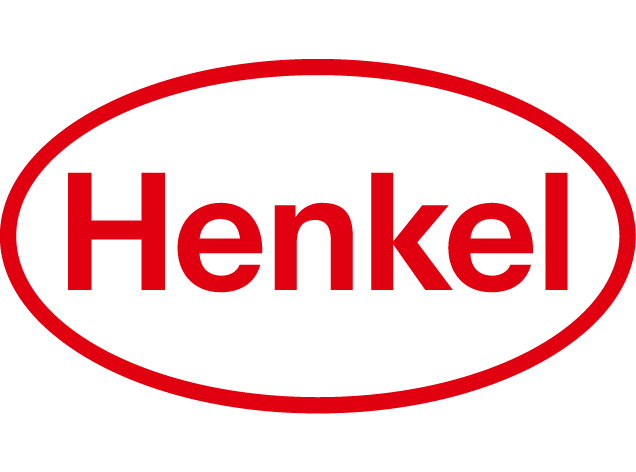
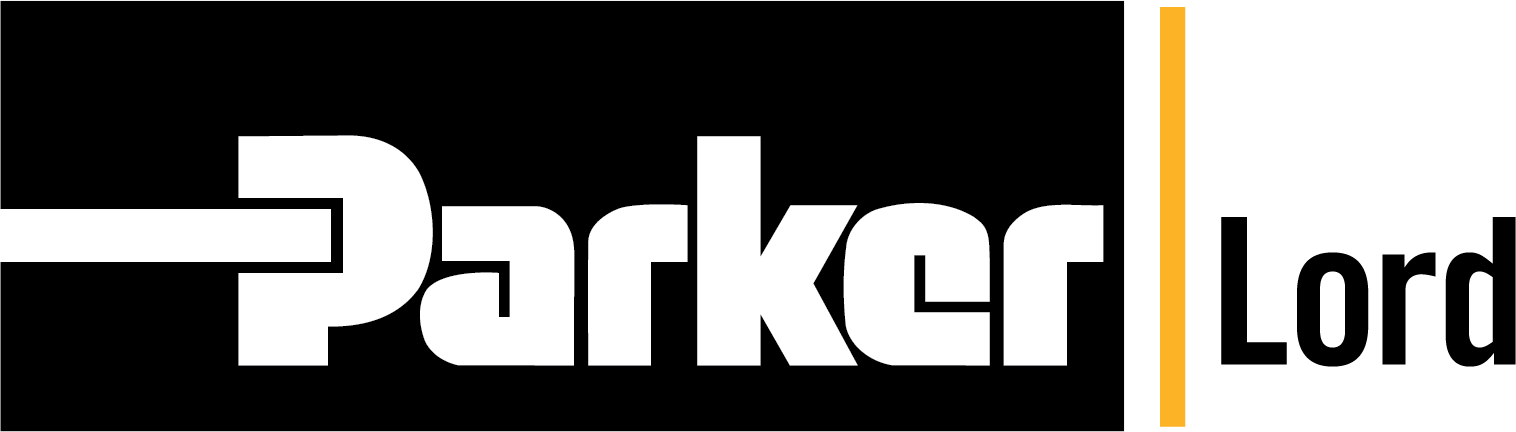
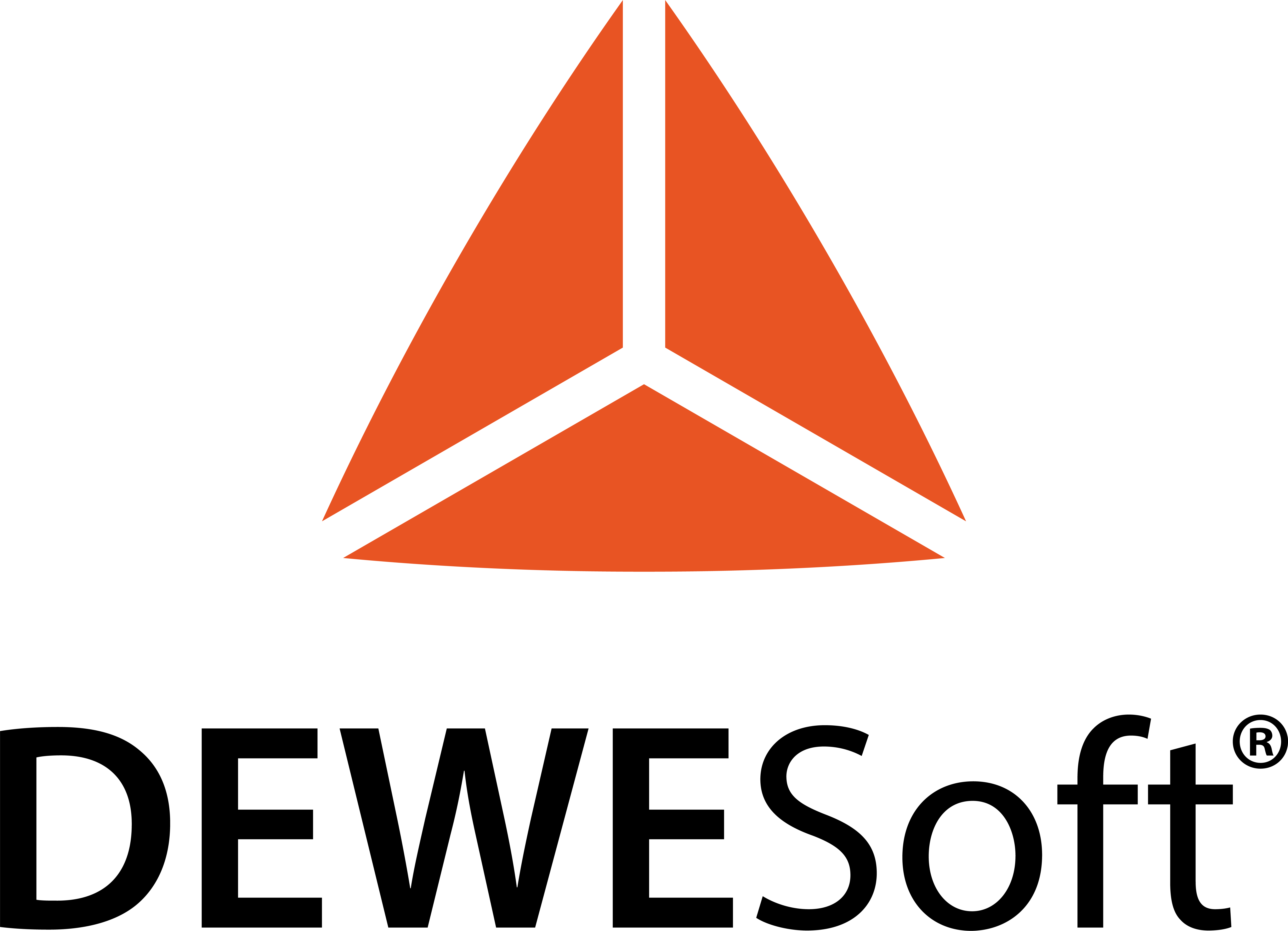
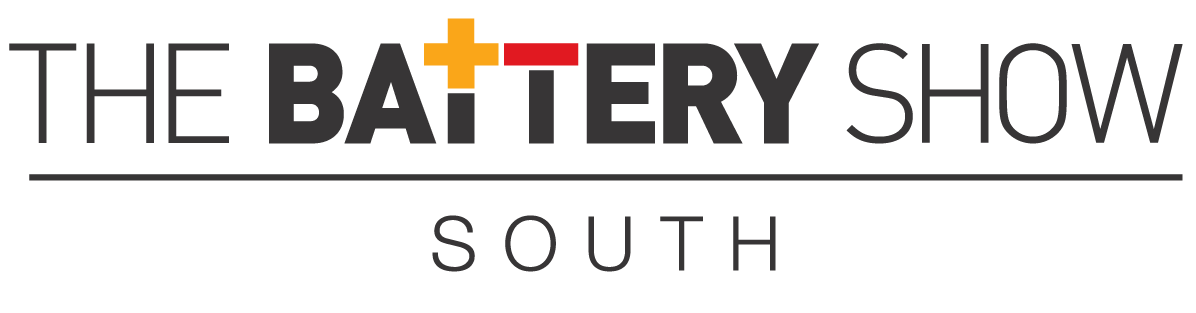
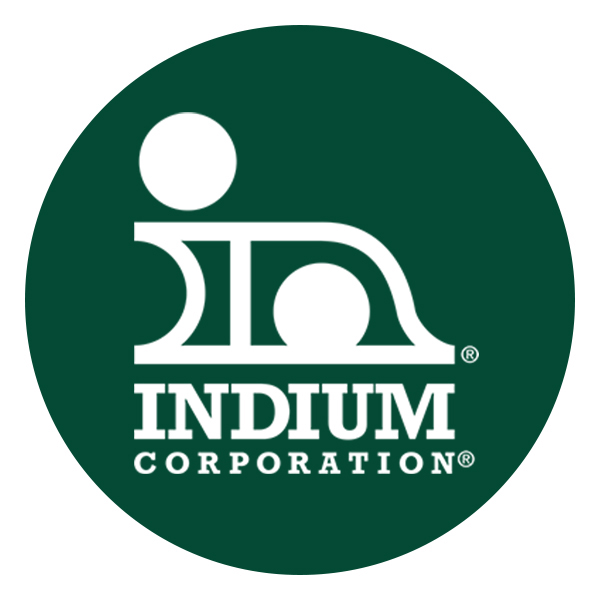

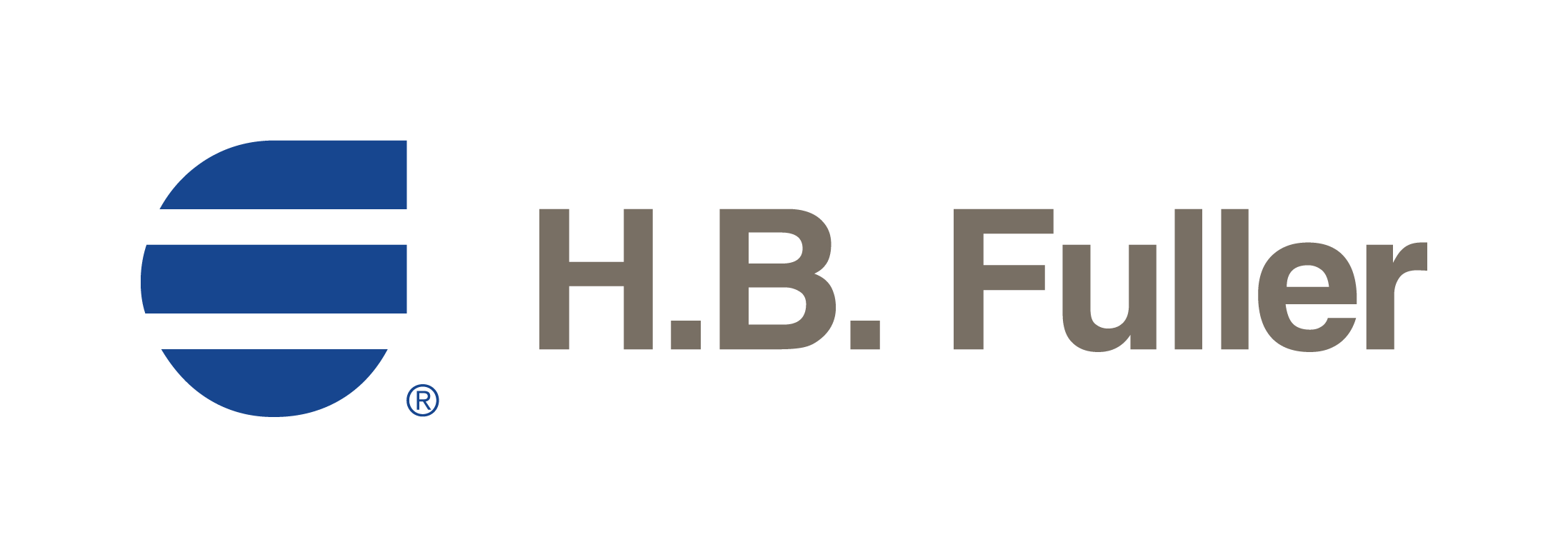
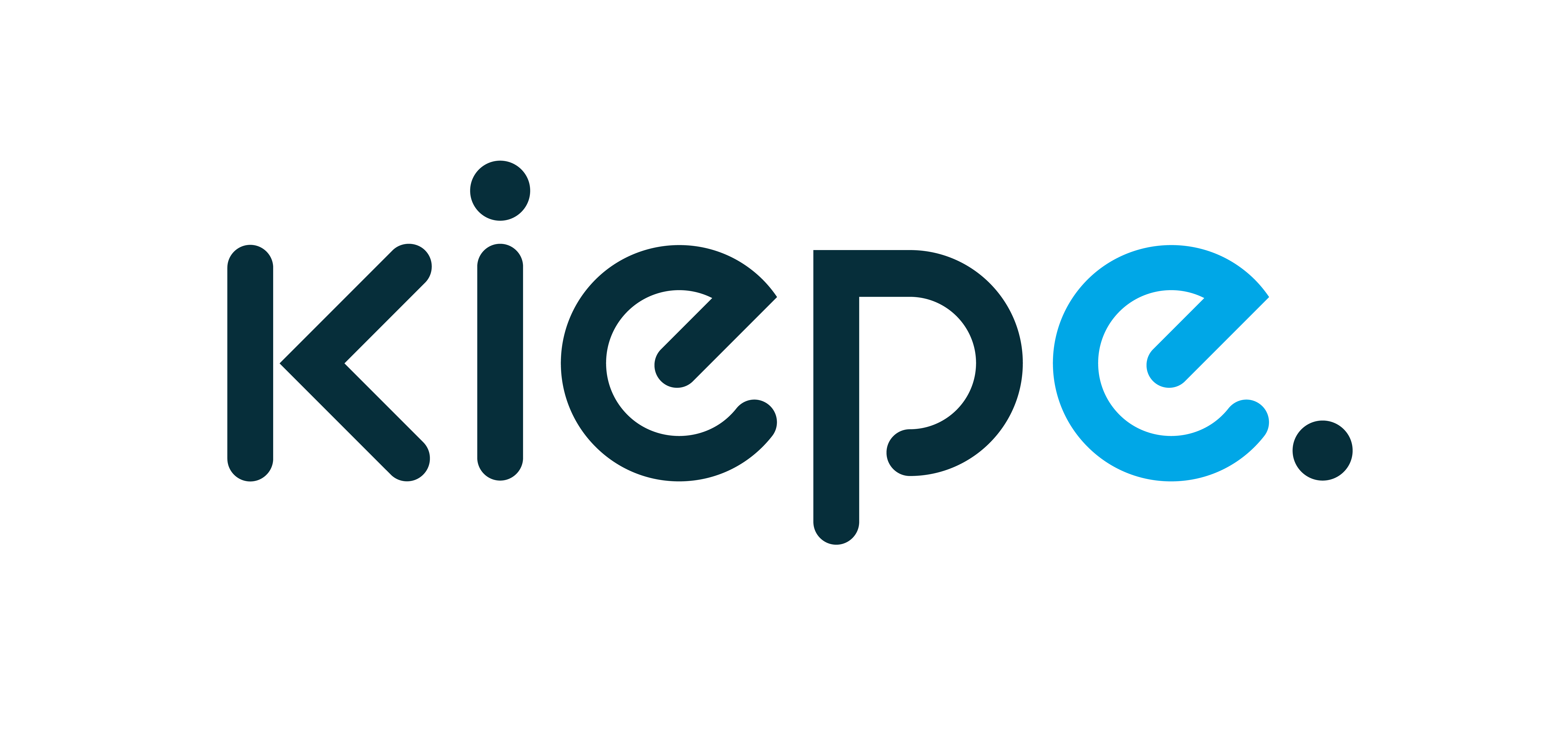
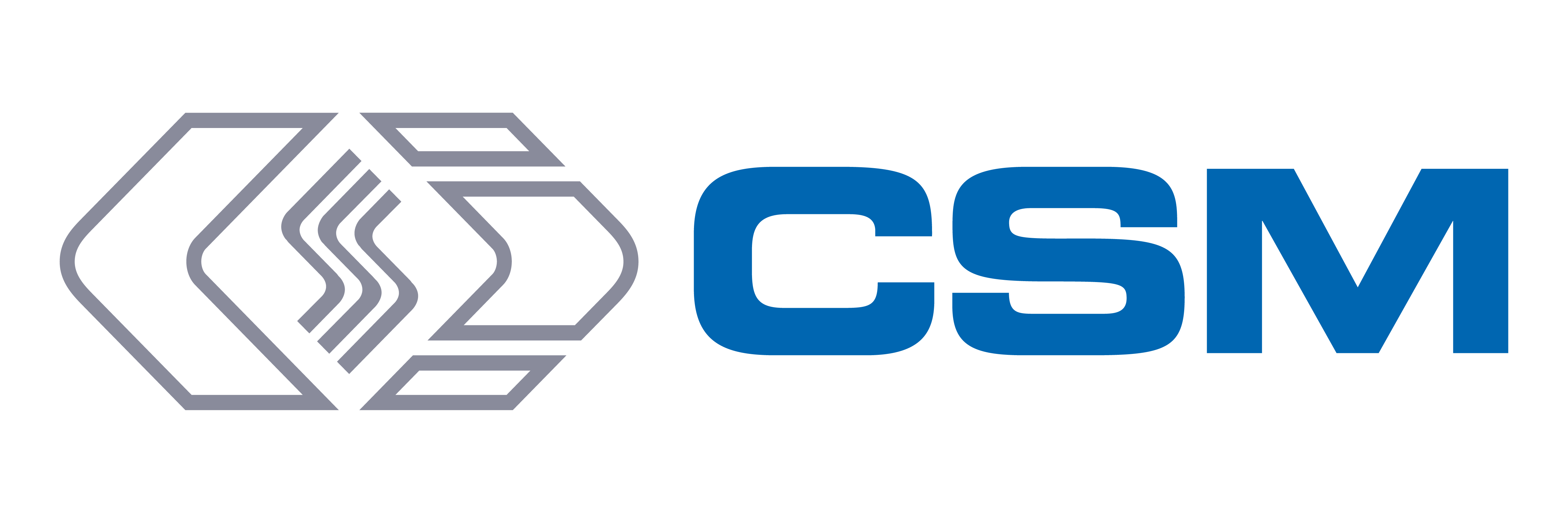