Hybrid energy storage systems
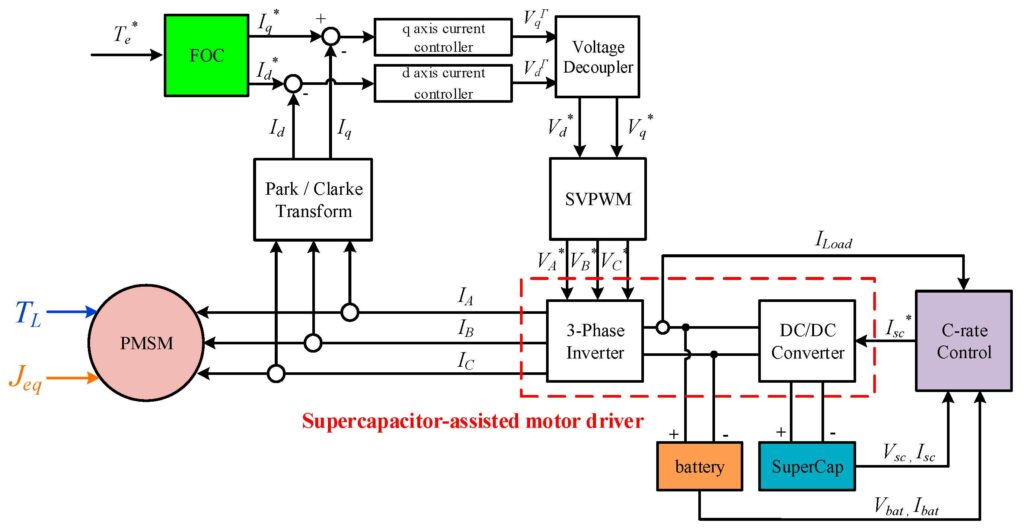
Hybrids of all kinds hold out the prospect of the best of both worlds, but the engineering challenge often entails a lot of effort to create something that is greater than the sum of its parts. Hybrid energy storage systems (HESS) that combine batteries and supercapacitor banks are a prime example, writes Peter Donaldson.
The attraction is a system that boasts the energy density of a battery with the power density, rapid response and long cycle life of supercapacitors. This combination gives the battery an easier time, extending its service life by having the supercaps handle peaks and transients in demand from the load.
The cost is the inevitable extra complexity of a hybrid system and the software to control it; for example, by making decisions on how to divide the load between the two energy storage devices in real time.
While supercapacitors excel in power density, they typically have lower specific energy and energy density compared with batteries, meaning they cannot store as much energy per unit mass or per unit volume respectively.
Consequently, the total energy storage capacity of a hybrid system may be less than that of a pure battery electric vehicle (BEV), potentially reducing range. This may be a showstopper for good reason in some applications, but if the rollout of charging infrastructure eases range anxiety, the battery safety and longevity benefits offered by HESS may become much more attractive.
A key early decision in designing a HESS for an application is the choice of topology, of which there are three types.
First there is the passive HESS, where the battery and the supercapacitor bank are connected in parallel and supply the load directly. This is simple and relatively low cost, but it doesn’t make the most of the benefits of the supercaps because its parallel connection limits the voltage variation at the terminals that they need to deliver energy.
The second topology is characterised as semi-active, encompassing systems in which either the supercap bank or battery is connected to the motor drive via a DC/DC converter, through which it is controlled, while the other is linked to it directly.
If the converter controls the supercaps it must be as responsive as they are to handle the spikes and transients well. With the battery connected directly to the drive of the motor, the latter benefits from the flat voltage profile of a lithium-ion battery as it is operated within the voltage range where it is most efficient, and sensitive components are protected from voltage fluctuations.
If the converter controls the battery and the supercaps are directly connected to the motor drive, their rapid reactions to power demands can make the HESS very responsive.
Also, the battery can keep the supercaps charged while discharging smoothly, as its discharge profile is independent of the load profile.
The principal drawback is that the HESS output voltage to the motor drive cannot be constant because supercap voltage is proportional to the size of the stored electric charge, and this changes as current is delivered to the load.
Fully active topologies in which both the battery and the supercap bank are connected to the motor drive through parallel or multi-port DC/DC converters address the problems of both passive and semi-active types of HESS, at the cost of even greater complexity in control (yet another area in which machine learning is being applied) and a drop in efficiency, thanks to the extra power-conversion stage.
However, the promise of better performance overall in terms of power delivery, efficiency and energy recuperation, along with extended battery life, makes the technology very attractive and the focus of major r&d efforts worldwide.
A key early decision in designing a HESS for an application is the choice of topology, of which there are three types.
Click here to read the latest issue of E-Mobility Engineering.
ONLINE PARTNERS
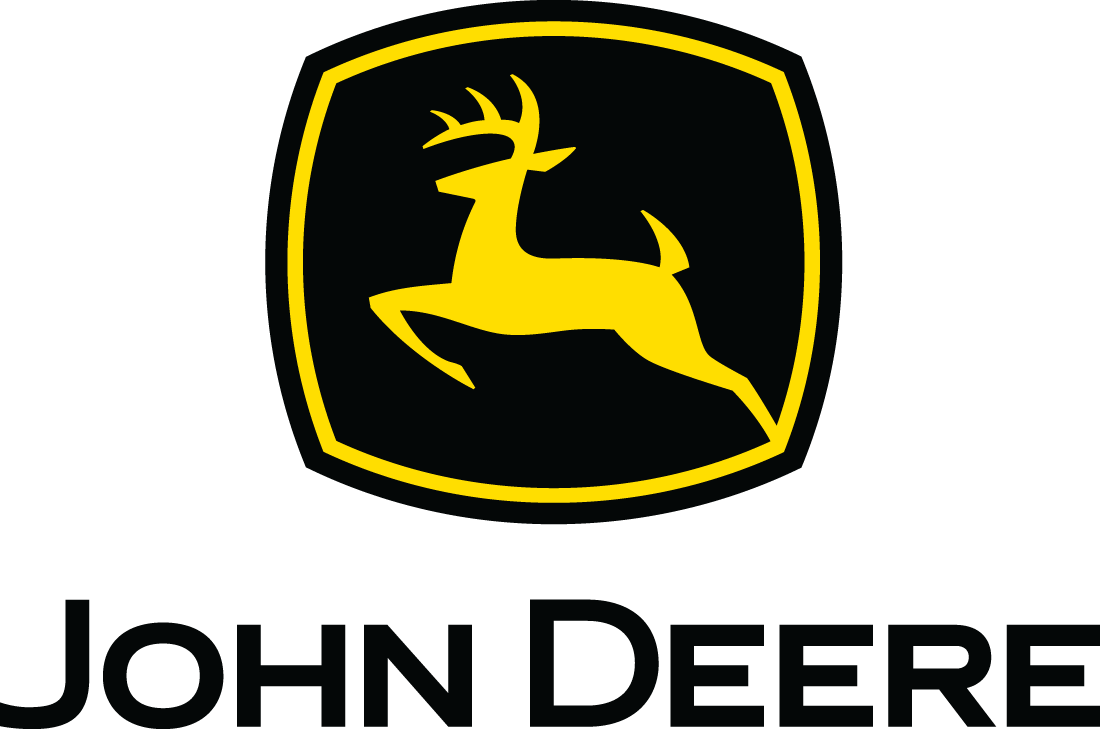
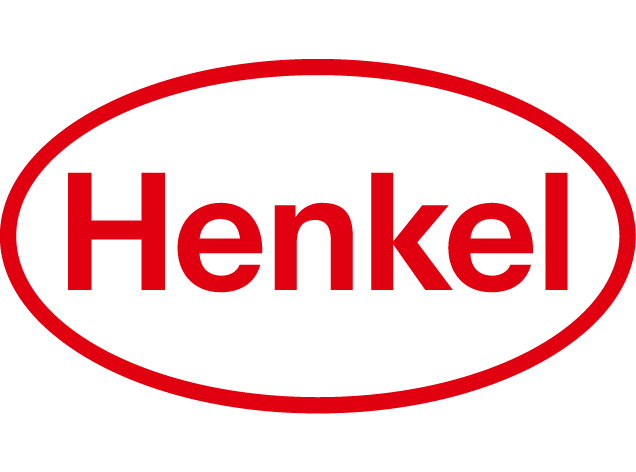
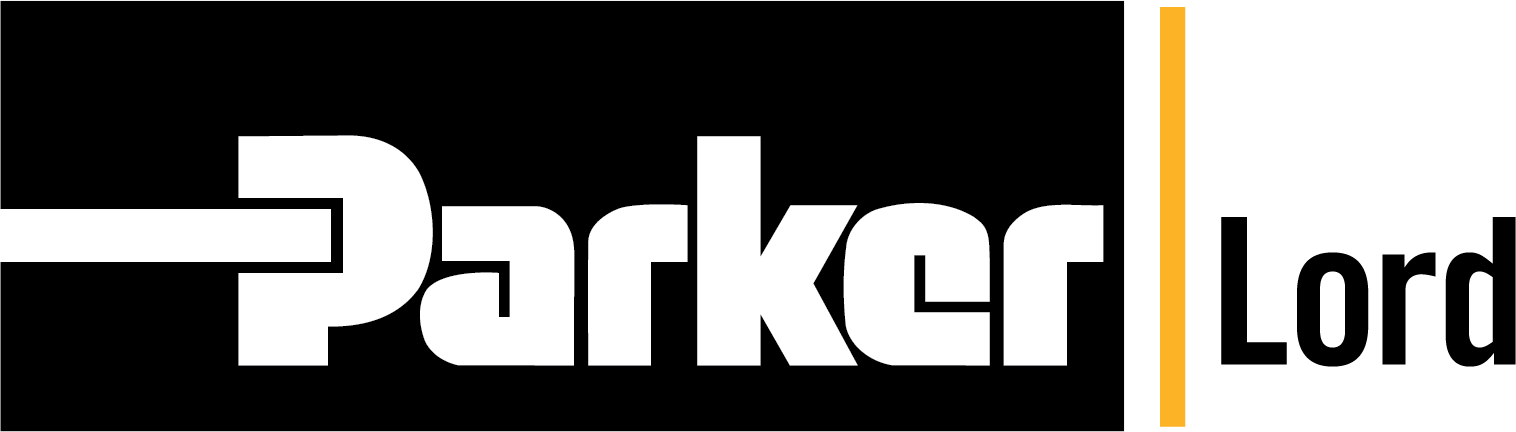
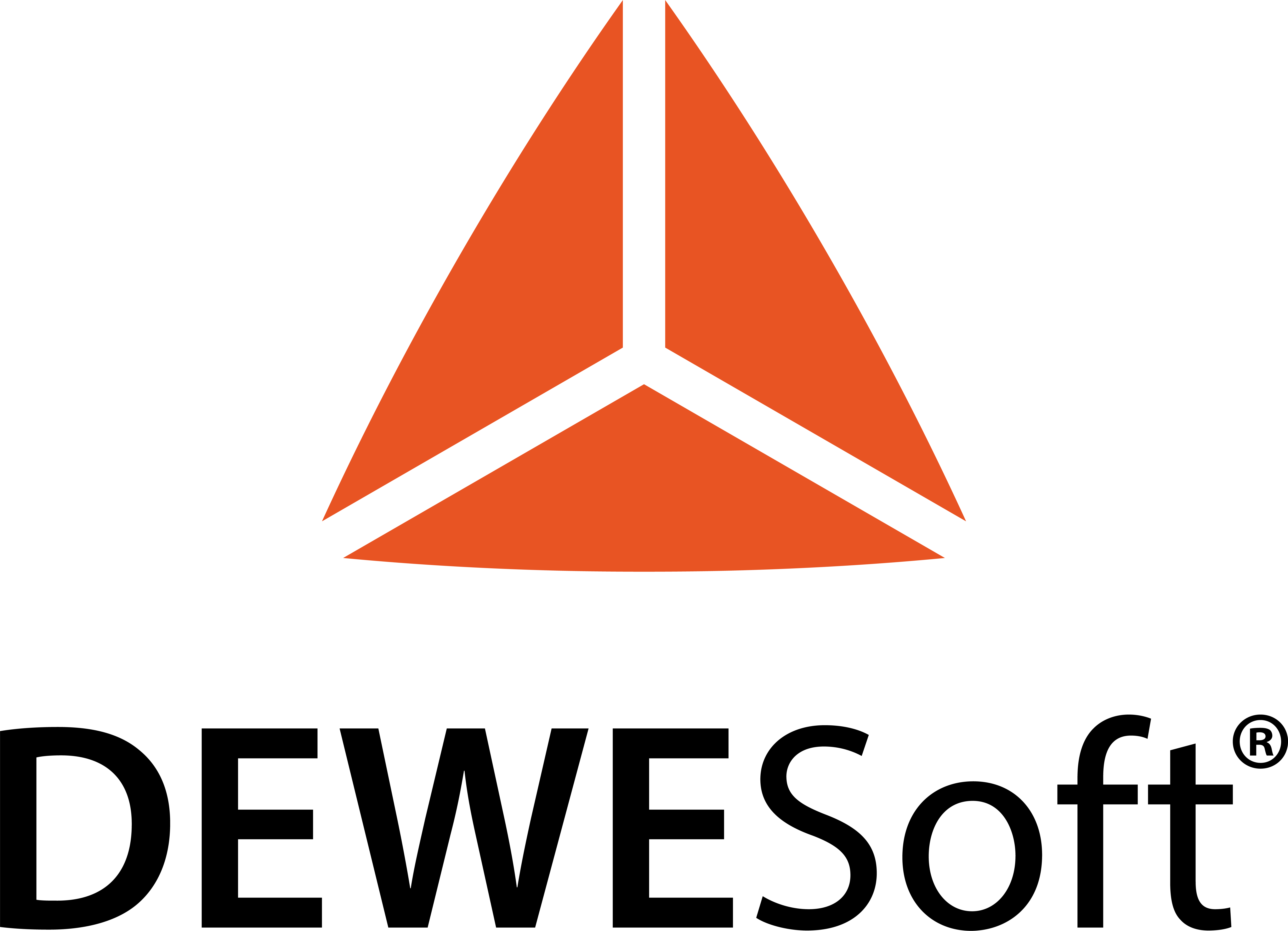
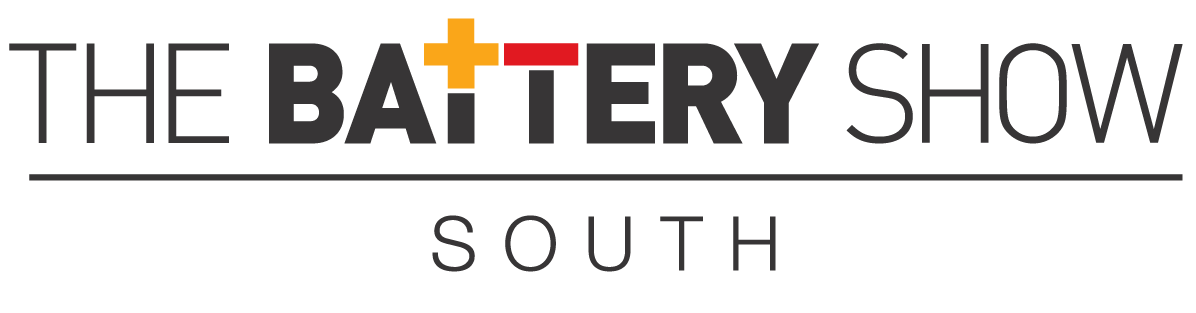
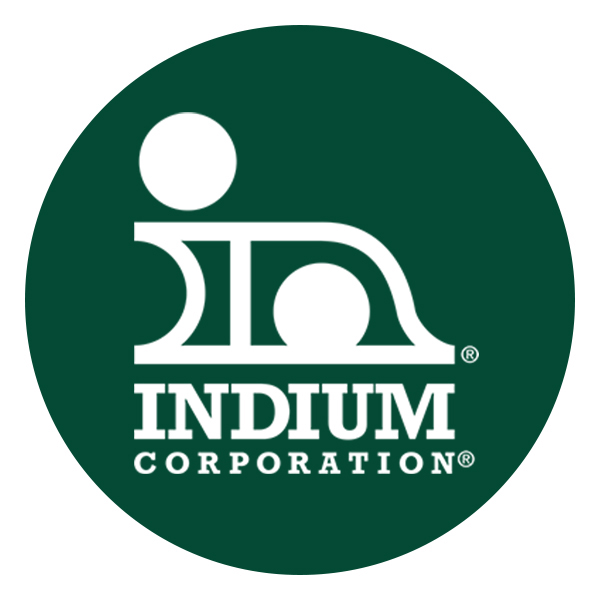
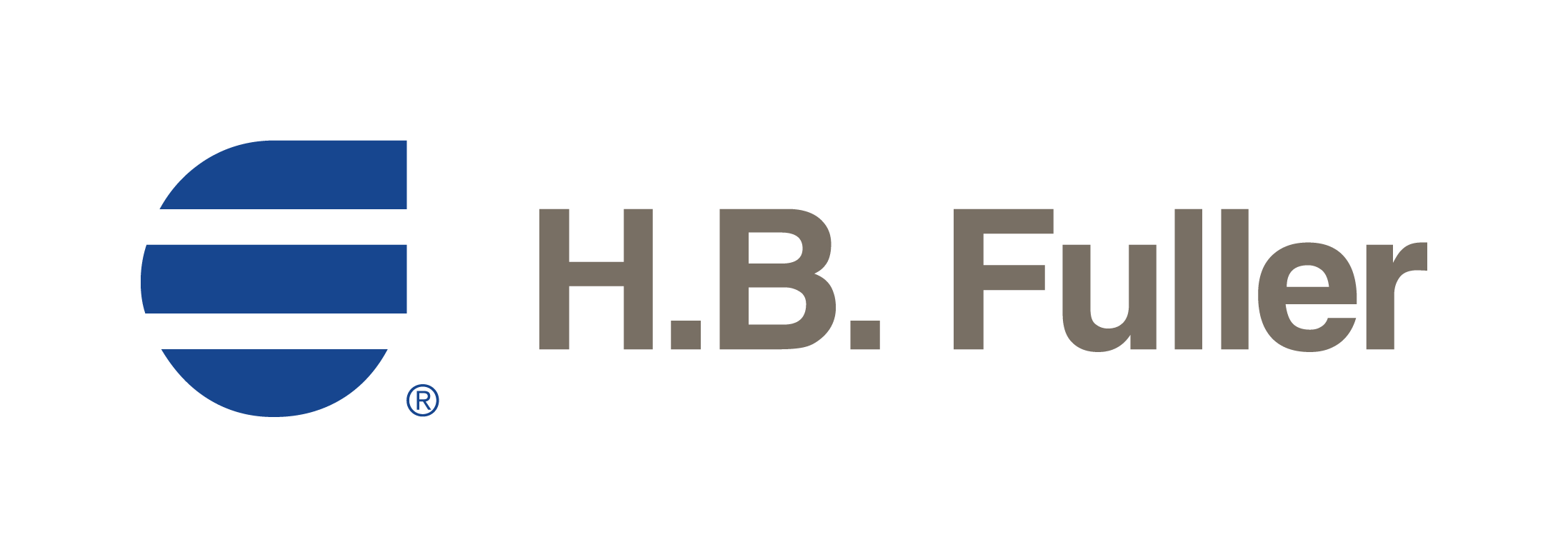