Hybrid electric propulsion passenger aircraft
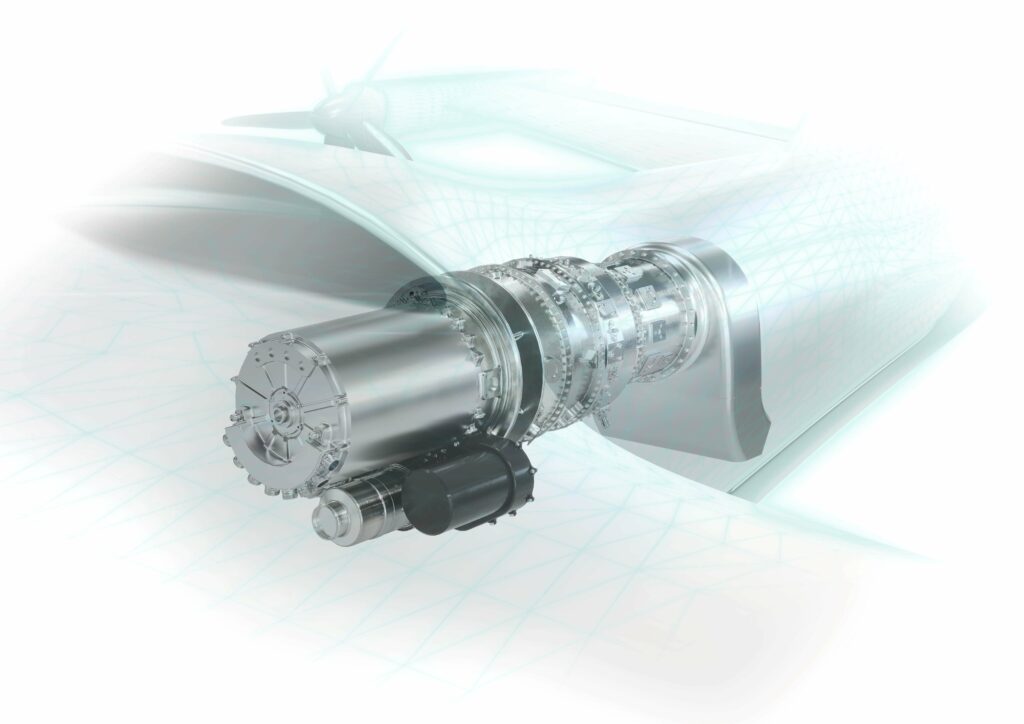
(Image courtesy of Rolls-Royce)
A European project is developing a new propulsion system for medium-range aircraft with up to 35 passengers, writes Nick Flaherty.
Several Fraunhofer Institutes and Brandenburg University of Technology Cottbus-Senftenberg, under the leadership of Rolls-Royce Germany and other partners such as research institution ACCESS, are collaborating on the hybrid electric-propulsion system.
The Clean Sky programme aims to use a gas turbine that generates electrical energy, which charges intermediate battery storage; the aircraft draws its electrical energy from this storage for propulsion.
This technology uses larger, slower-rotating rotors that produce less noise on the ground, creating a significantly smaller noise footprint than conventional propulsion aircraft. The modular structure of the proposed concept also allows for the future use of alternative fuels or entirely new power sources.
By mid-2026, the partners aim to develop manufacturing technologies for hybrid electric-propulsion components, qualify existing technologies for use in the air and produce prototype components.
One ambitious goal is to significantly shorten the lead times from the finished design of a functional prototype from several months to a few weeks. Other projects involve creating highly flexible production concepts that are essential for efficient mass production.
Production technologies include additive manufacturing (3D printing) and forming, which have not been applied to passenger aircraft construction before.
Qualifying them for this industry with its stringent requirements for quality, reliability and durability is a challenge that the institutes are addressing.
The Fraunhofer Institute for Machine Tools and Forming Technology IWU is coordinating the project, with a focus on the geometry of the wire windings (coils) in electric drives that enable more efficient operation or higher torque. It is also working on production processes for the combustion chamber housing via bulk-forming and flexible component machining.
The Fraunhofer Institute for Material and Beam Technology IWS focuses on laser-based additive manufacturing. In Directed Energy Deposition (DED), metal is melted and subsequently welded where needed. This technology allows the printing of components up to 10 m long.
Fraunhofer IWS uses laser powder bed fusion (PBF-LB) as the best method for manufacturing the combustion chamber. In this process, a laser melts metal powder layer by layer onto a component. Cooling holes are inherently spared during printing, saving material.
The Fraunhofer Institute for Manufacturing Technology and Advanced Materials IFAM develops an innovative, metallic 3D-printing process established by Israeli company Tritone Technologies. The MoldJet system combines two manufacturing processes that work alternately for layer-wise component manufacturing.
In the first layer, the form is produced as a negative to the component geometry from a wax-like polymer using inkjet print heads. This printed layer of form material is then filled with metal powder paste through a slot nozzle and a squeegee. The layer construction creates complex components with undercuts or internal channels without support structures.
The Center for Hybrid Electric Systems at Brandenburg University of Technology Cottbus-Senftenberg is taking on development tasks.
“There’s a shift towards electrical systems,” says Ruud Den Boer, project officer at Clean Sky.
“If you look at wing ice protection, many aircraft currently use a pneumatic system with a sealed rubber boot that mechanically breaks up the ice, but when you make this wing ice-protection function electrical, the big advantage is that during the flight you can manage your use of the electricity more efficiently and prioritise the energy use between the aircraft’s different on-board systems.”
Click here to read the latest issue of E-Mobility Engineering.
ONLINE PARTNERS
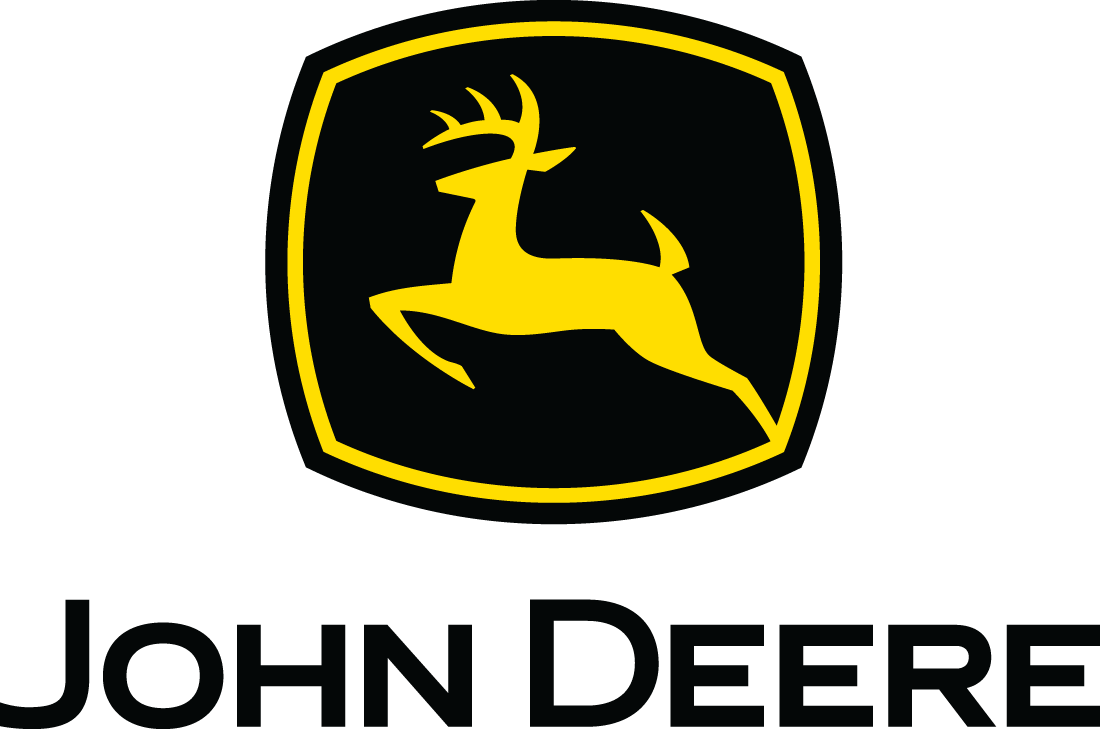
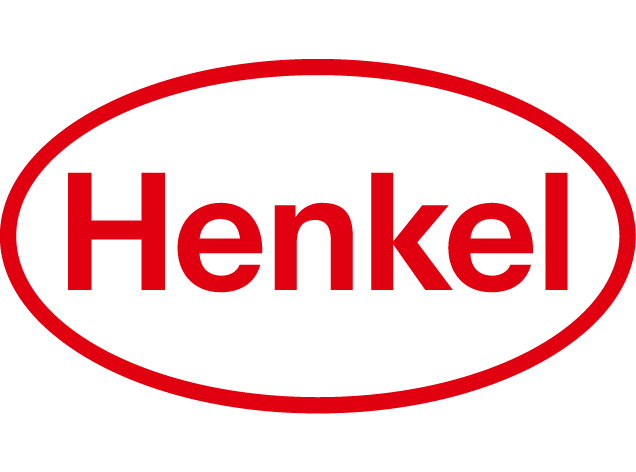
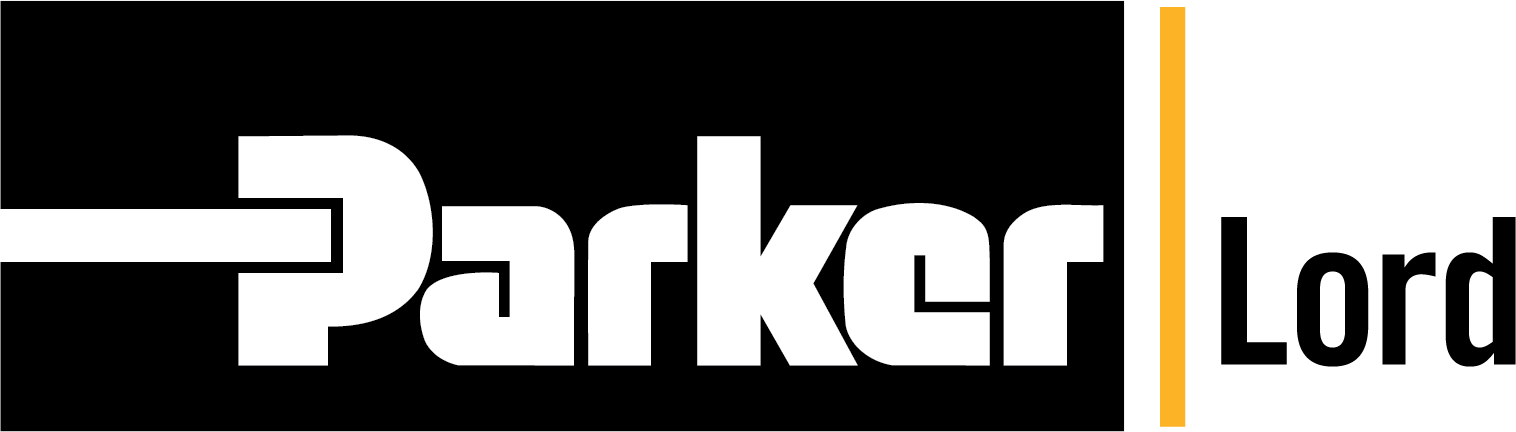
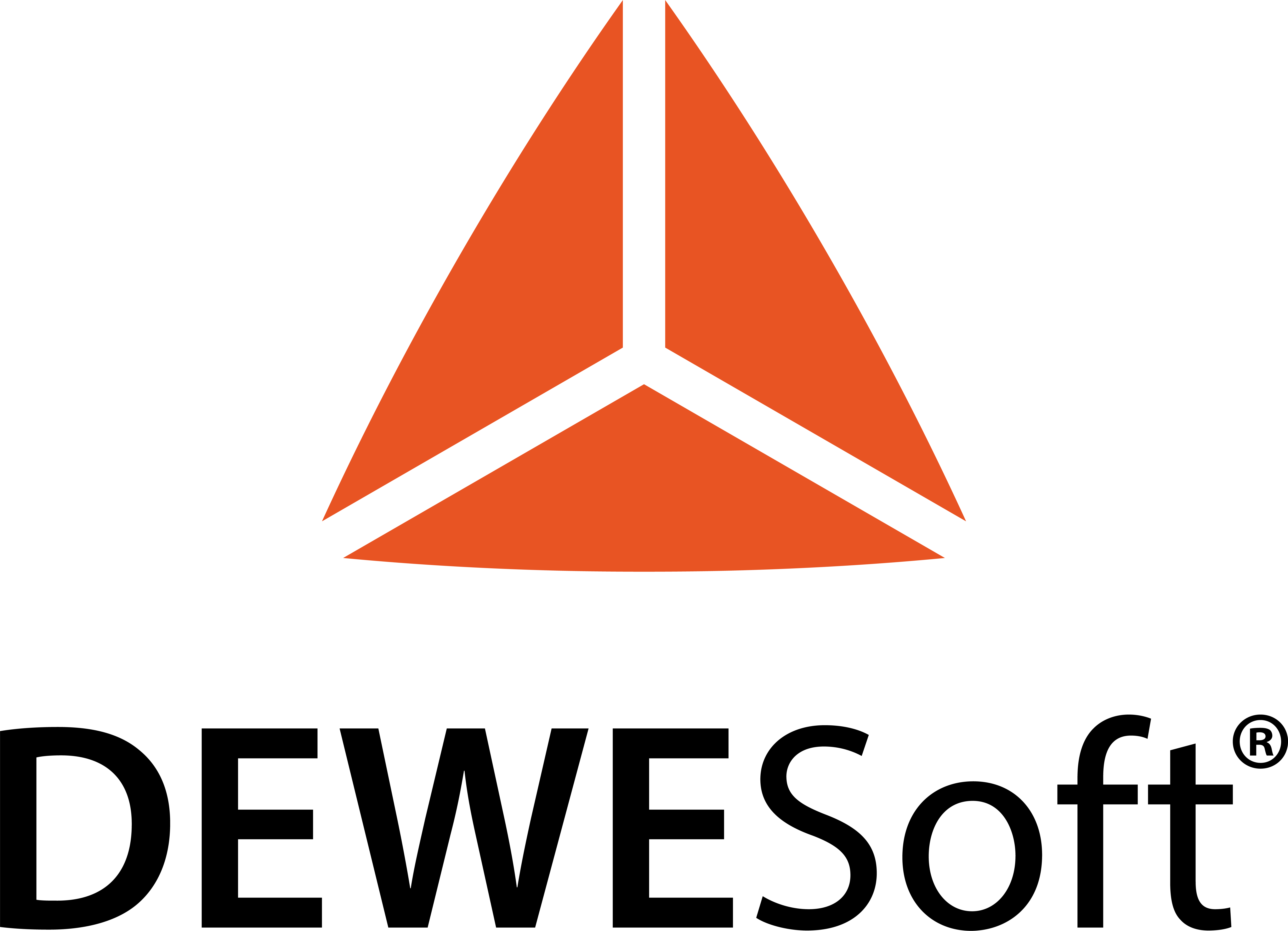
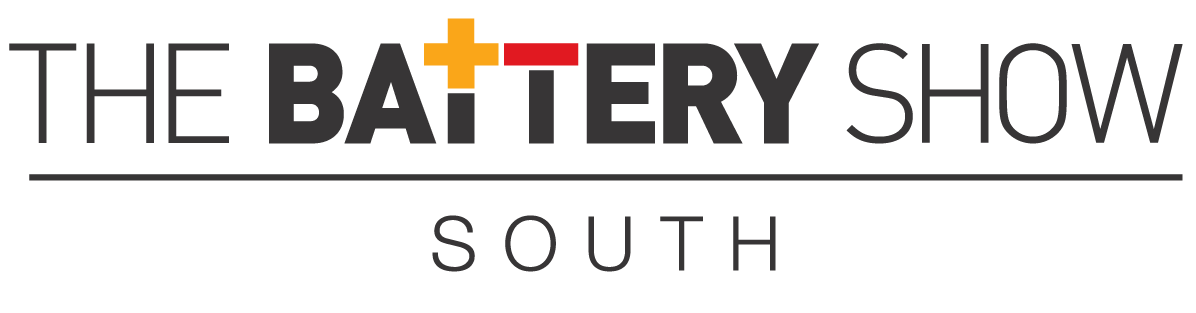
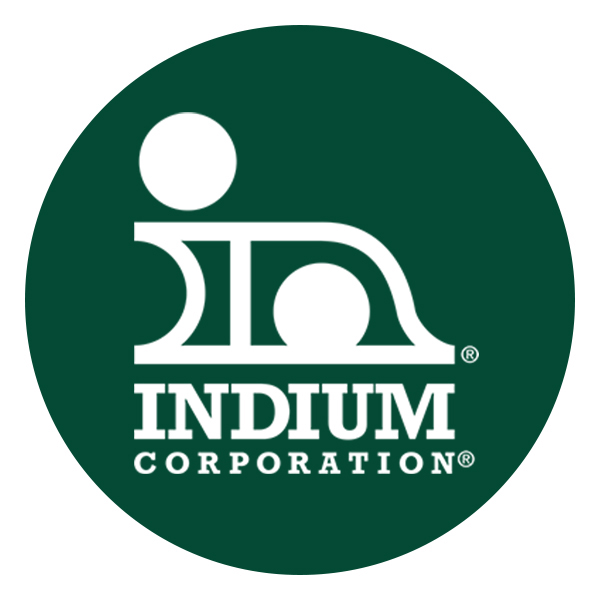
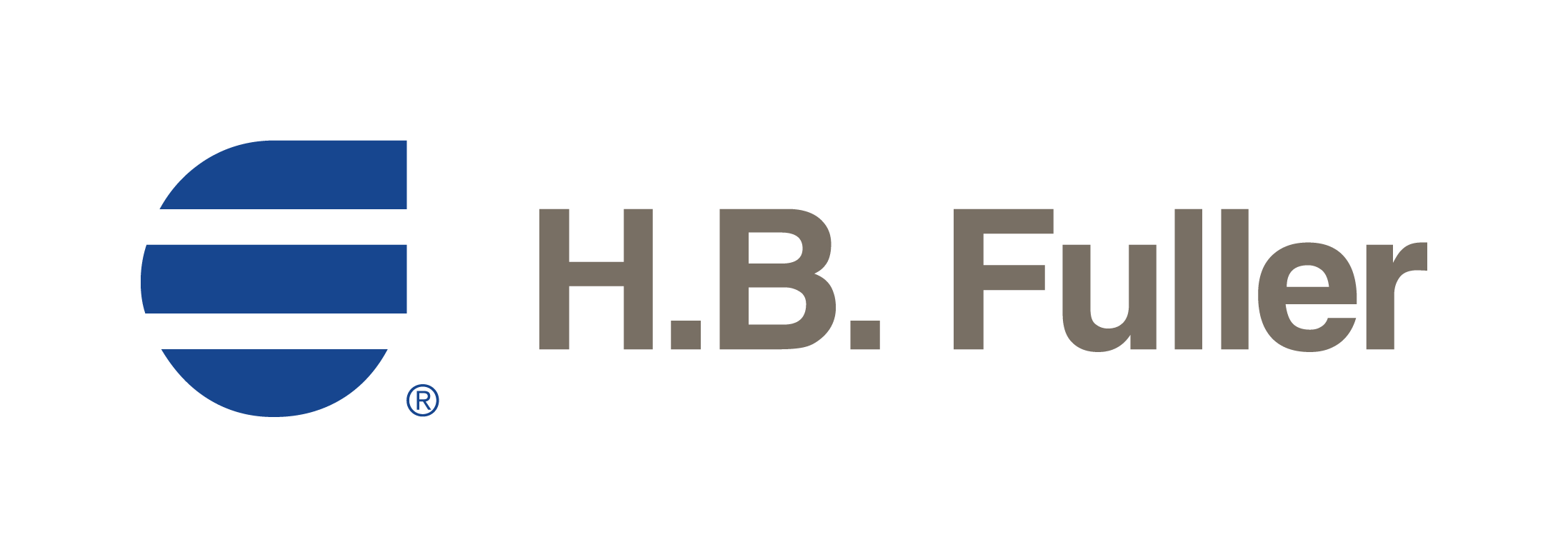