Henkel’s Battery Engineering Center
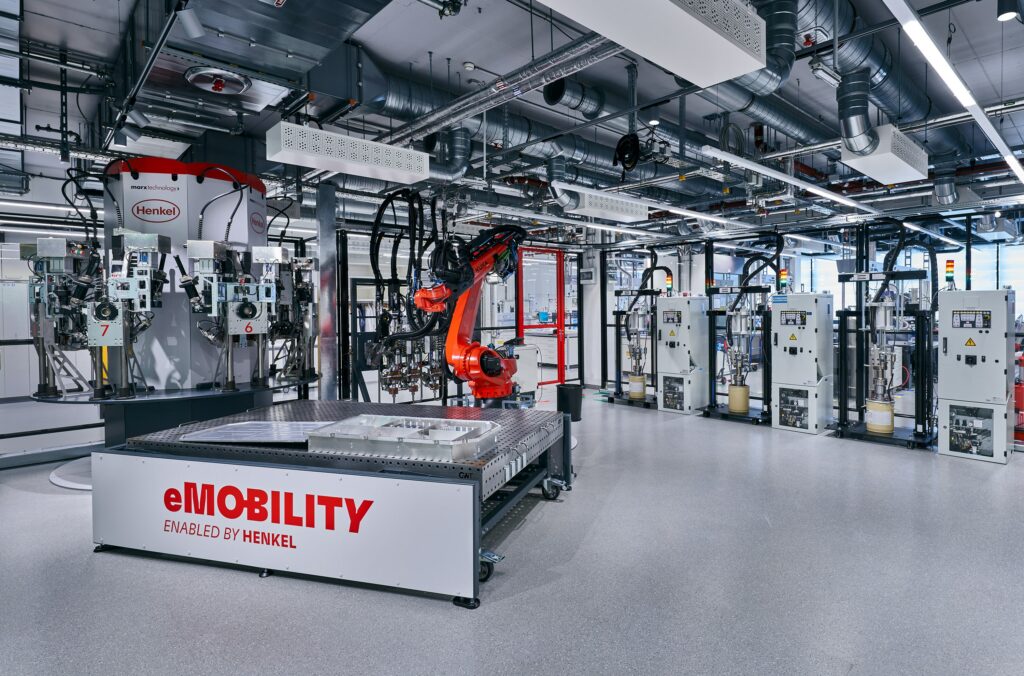
Primarily known as a producer of chemical solutions across a number of different industries, German multinational group Henkel has launched a Battery Engineering Center (BEC) within its Inspiration Center Duesseldorf, aimed at providing strategic partnerships to OEMs and battery manufacturers (and others in the e-mobility space) through the BEC and its services and products there.
Dr. Olaf Lammerschop, global technology lead for e-mobility at Henkel, explains to us how the BEC came about. “In a growing and fast-moving industry like e-mobility, frequent innovations are required to meet new design needs of OEMs and battery manufactures. Henkel is investing heavily into new technologies & product development to enable our customers to realize higher battery capacity, faster charging, and increased battery safety.”
“With an increased complexity of battery components and interdependencies of materials towards the overall battery pack performance, it is essential for Henkel to fully understand all the influencing factors and be able to test automotive battery packs.”
Understanding these changing dynamics in the market and translating the customer requirement of material validation on system level into action, Henkel decided to take its expertise – gathered over 100 years of supplying adhesives to the automotive space – in a major new direction.
In line with its commitment to being a thought leader and innovation driver in the e-mobility market place, Henkel invested in the creation of a fully-equipped Battery Engineering Center: a facility capable of applying Henkel products from its portfolio, e.g. thermal interface materials (TIMs), adhesives, sealants, and battery safety materials, to a real-life, full-size battery pack, and then testing the overall performance of the resulting system to the same level its customers would.
The customer’s journey
The first Battery Engineering Center is now operational onsite at Henkel’s headquarters in Duesseldorf, having been architected according to the needs of OEMs and battery manufacturers in the development phase of a new battery design.
When taking their battery concept or prototype through the BEC, customers will find their journey divided into three broad stages: first, a simulation and modelling stage, second an application and assembly stage, and third a testing and validation stage.
Modelling and simulation
Initially, Henkel’s engineers will examine the design of a customer’s battery pack, and gauge its mechanical and thermal properties against its ideal or targeted performance specifications.
“As cell-to-pack or cell-to-car battery designs become more prevalent, the structural integrity of the cells in the pack is key. This is achieved through adhesive bonding of the cells into the pack by structural or thermally conductive adhesives. Hence, the adhesive properties are designed according to component simulations, attaining best performance results. ,” Dr. Lammerschop notes.
“Developing those application-specific products is typically a time-consuming process including multiple iteration steps with the customer. Having the short customer timelines in mind, we have shortened our development process at Henkel by linking simulation with our global formulation database.”
To create this optimal material, Henkel typically begins by building a digital twin of the customer’s pack, to simulate how it will perform inherently under varying conditions, and also when combined with different materials created via different chemical formulations.
By focusing on the battery’s performance optimization, the BEC team can simulate, for instance, how the customer’s pack – imbued with Henkel’s – performs in a crash, to visualise if a new kind of adhesive will maintain structural integrity or lose some cohesion. Countless other scenarios can also be simulated, such as an overheating event, a thermal runaway, or a fire, which can gauge critical safety functions for a pack, such as how well its materials slow a thermal runaway event, or slow the rate at which a fire propagates in the pack.
Based on the results of such simulations, Henkel can then re-iterate the simulation with a slightly different material in the pack’s digital twin, over and over, until a Henkel product is found to achieve optimal performance for the simulated pack, whether it be an adhesive, a TIM, or some other material.
Application
The Battery Application Center exists for the practical aspects of battery engineering, particularly the automated application of chemical products, and the disassembly or assembly of packs. Key to Henkel’s design of the Battery Application Center was a wish to imitate customers’ production environments as closely as possible, to maximise its value in creating packs that are fit for large-scale manufacturing.
“Our Battery Application Center is equipped with a state-of-the-art automated dispensing system through which we can apply our broad range of solutions on any type of battery pack at a series production scale.”
“As we continue to innovate and grow our portfolio of battery solutions, we have built the Battery Application Center with the future in mind, so whenever we create a new material or technology, we have the flexibility to set it up for fully automated dispensing there.”
Having applied the battery adhesives, lid sealants, TIMs or other materials sought after by the customer, the pack can be taken through the BEC’s Battery Test Center. Here, each pack can be electrically-cycled, either in typical operational conditions, or in extreme conditions; these can include fast-charging and -discharging, or extreme environmental temperatures and moisture levels, ranging from -40 to +90 C and 10-90% humidity.
“Our Battery Test Center is equipped with cutting-edge tools and software for full-scale battery system testing. Our capabilities encompass a range of rigorous stress tests for batteries, such as temperature and humidity cycling, fast charging and discharging, as well as leakage tests” Dr. Lammerschop says.
For electrical cycling, the Battery Test Center is geared for fast charging and discharging of 800 V systems with up to 330 kWh, measuring how the Henkel products improve and influence the overall car performance. Beyond this, the company has additional partners through whom it can perform thermal runaways and other destructive testing, to gain a clear picture of our products on the battery safety performance.
Through the Battery Test Center’s climatic chamber and various other testing equipment, customers’ packs and the Henkel material integrated into it (or the combination of multiple materials integrated, as the case is more likely to be) can be repeatedly cycled until fully validated for mass production.
Sustainable, digital future
Further BECs are in development, modelled upon the successful pilot BEC in Dusseldorf, with data and formulations collected in one BEC to be shared instantaneously via Henkel’s internal servers with the others across America, Europe and Asia, to keep simulation, modelling and engineering capabilities optimised across all Centers.
“Going forwards, we are investing R&D resources into key areas,” Dr. Lammerschop comments. “One is enabling new debonding technologies to make battery pack MROs less challenging, including a range of different ‘trigger mechanisms’ for quickly and efficiently disassembling bonded structures, such as applying a thermal trigger, liquid solutions, or electrical debonding trigger.”
Debondable adhesives stand to hugely enhance the sustainability of battery packs by enabling all of their internal components to be cleanly detached from one another and the pack housing at end-of-life, such that any parts that could be reused or remanufactured, will be (thus contributing to the growth of circular economies in e-mobility). This includes re-use of components from prototype packs that may have been damaged during testing.
On top of all of this, Henkel is also researching further avenues of sustainability in e-mobility, such as reducing the CO2 emissions from production towards increasing battery cell capacity by reducing cell resistance with conductive coatings.
The resulting sustainability will then be passed onto its customers’ products via the BECs in future, from modelling and simulating how more sustainable materials may behave in digital twins of new pack concepts, to how such materials may be applied in a low-cost, high- throughput manufacturing context, to testing and validation of complete packs to guarantee a safer, greener future for all of Henkel’s customers.
ONLINE PARTNERS
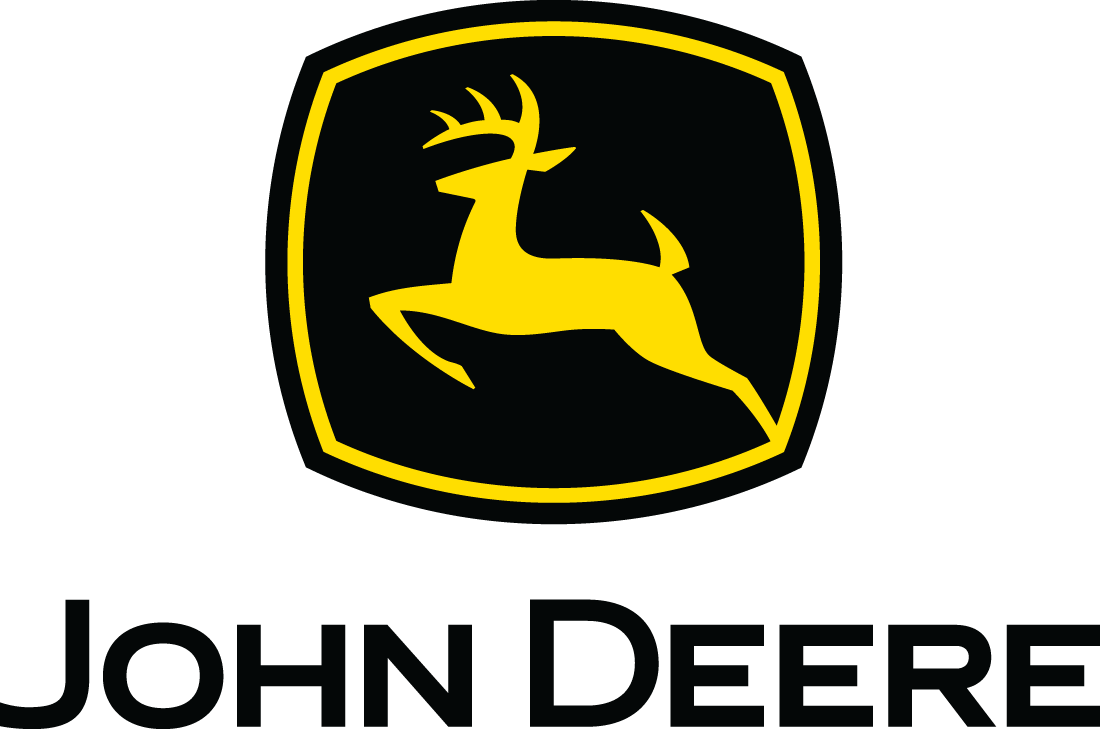
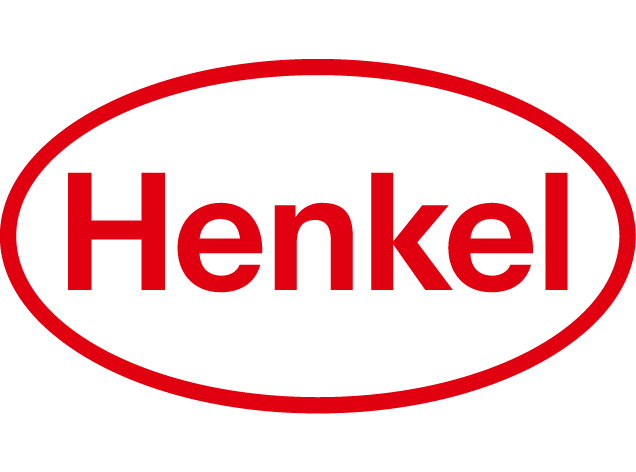
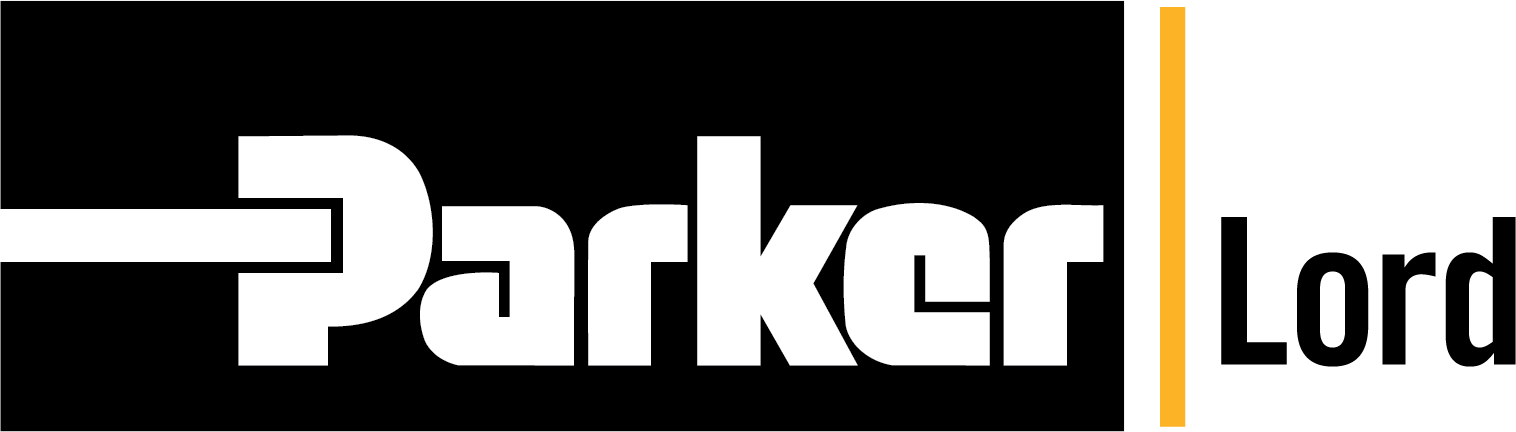
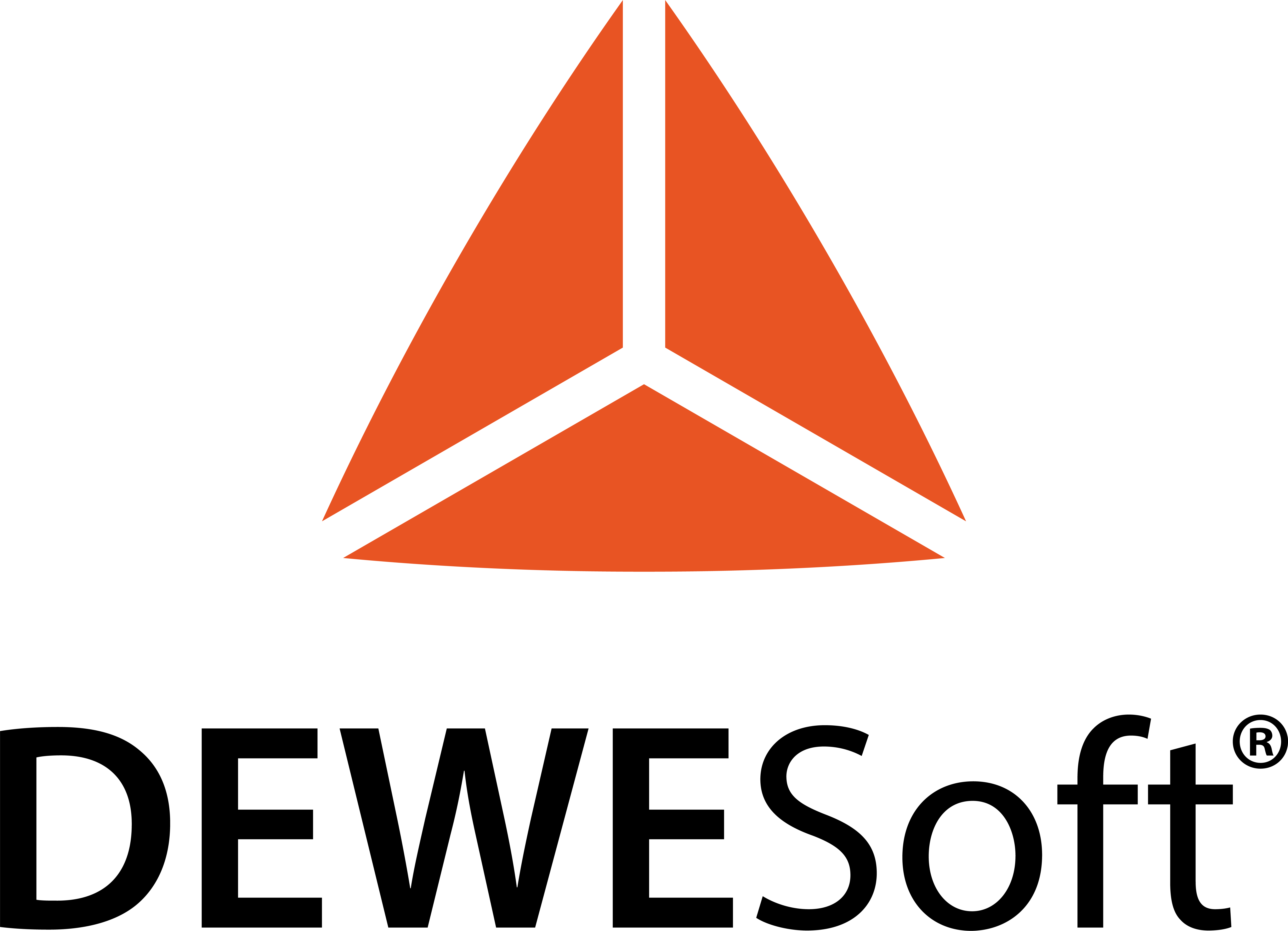
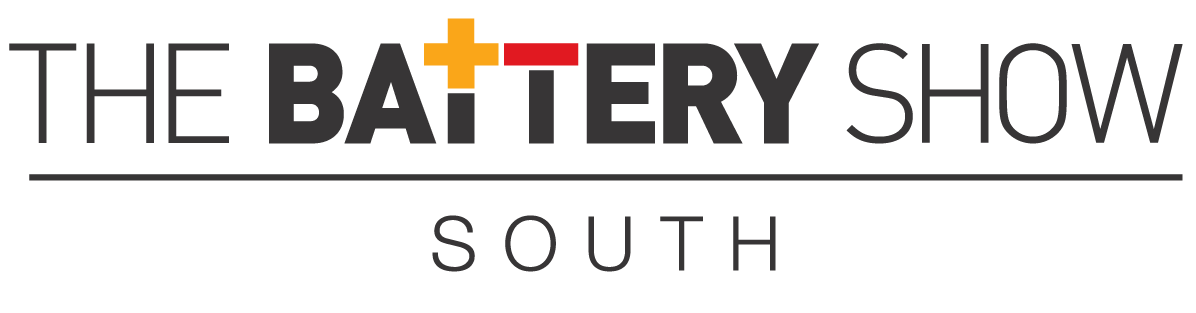
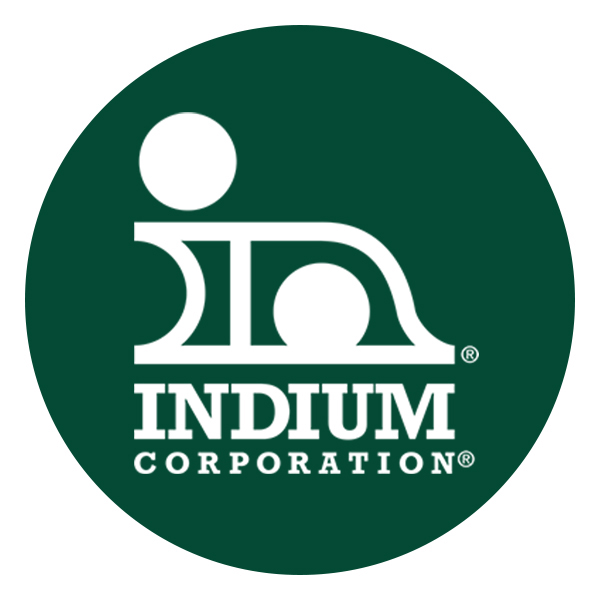

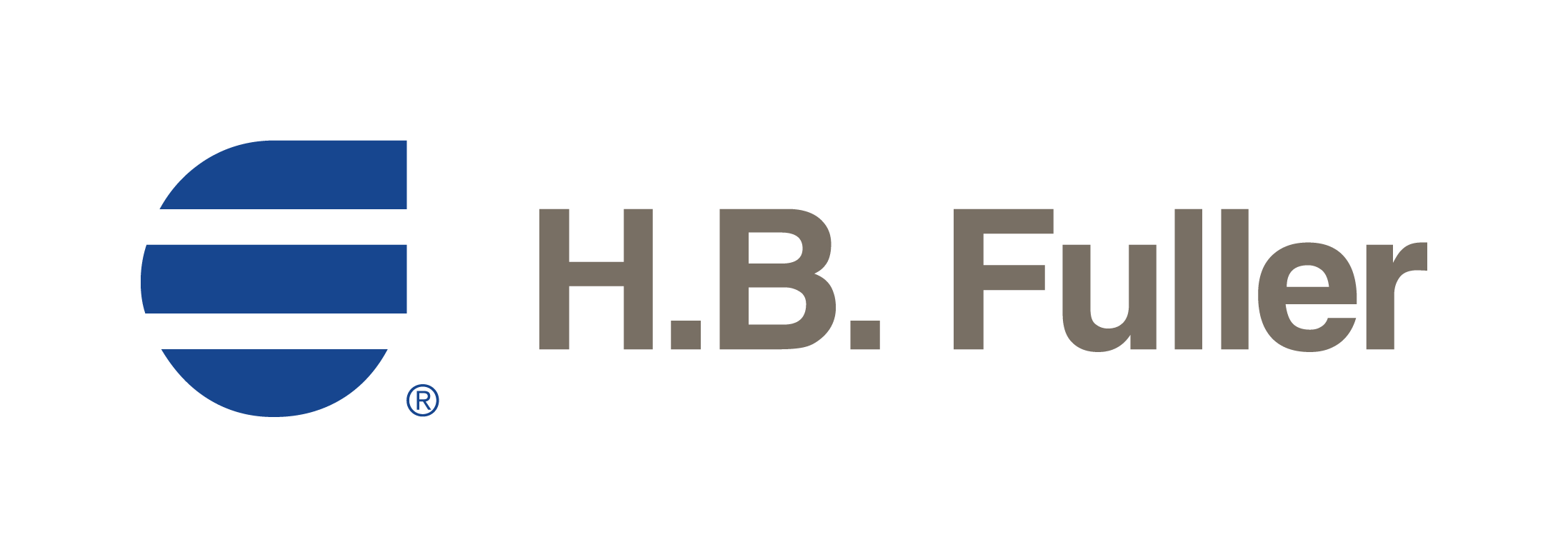
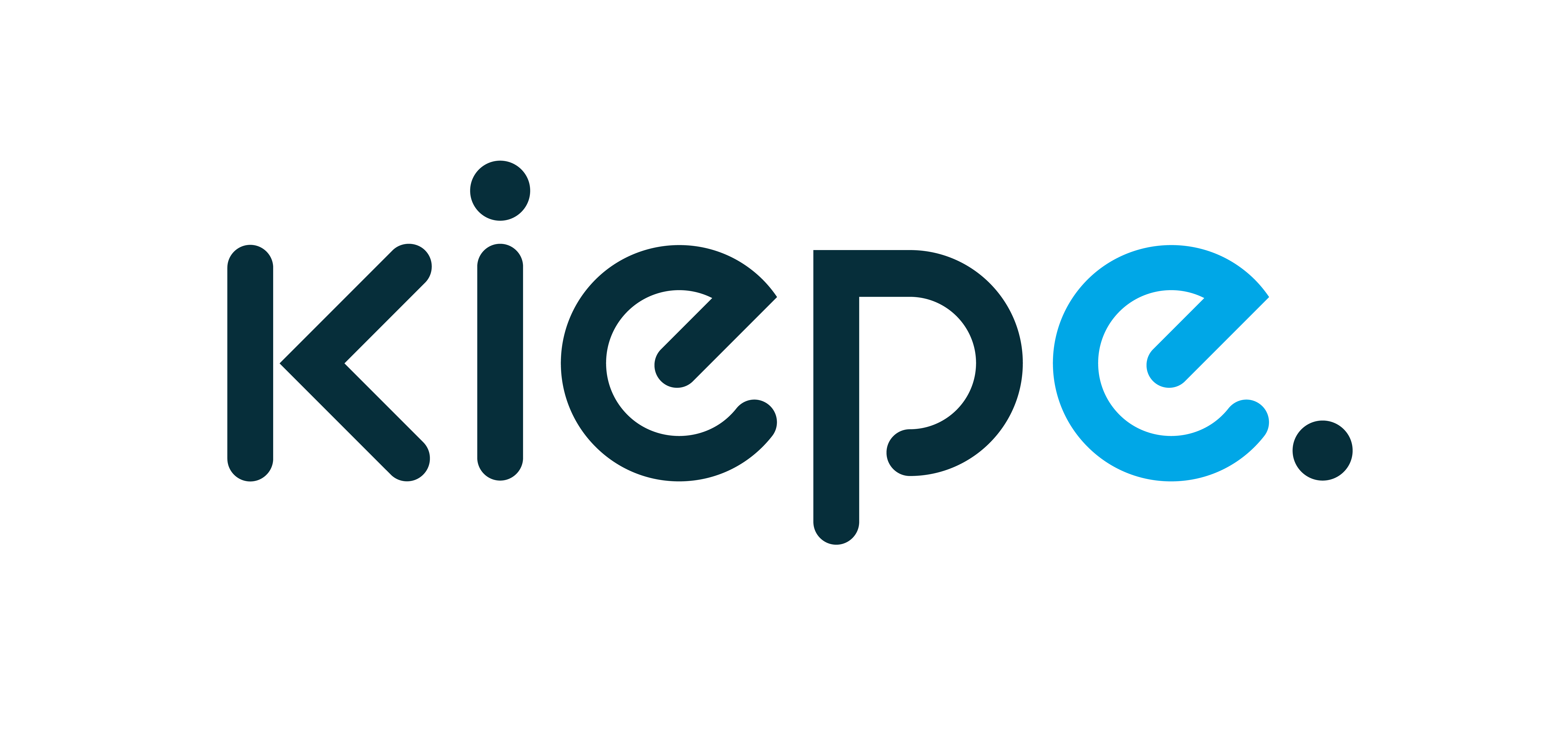
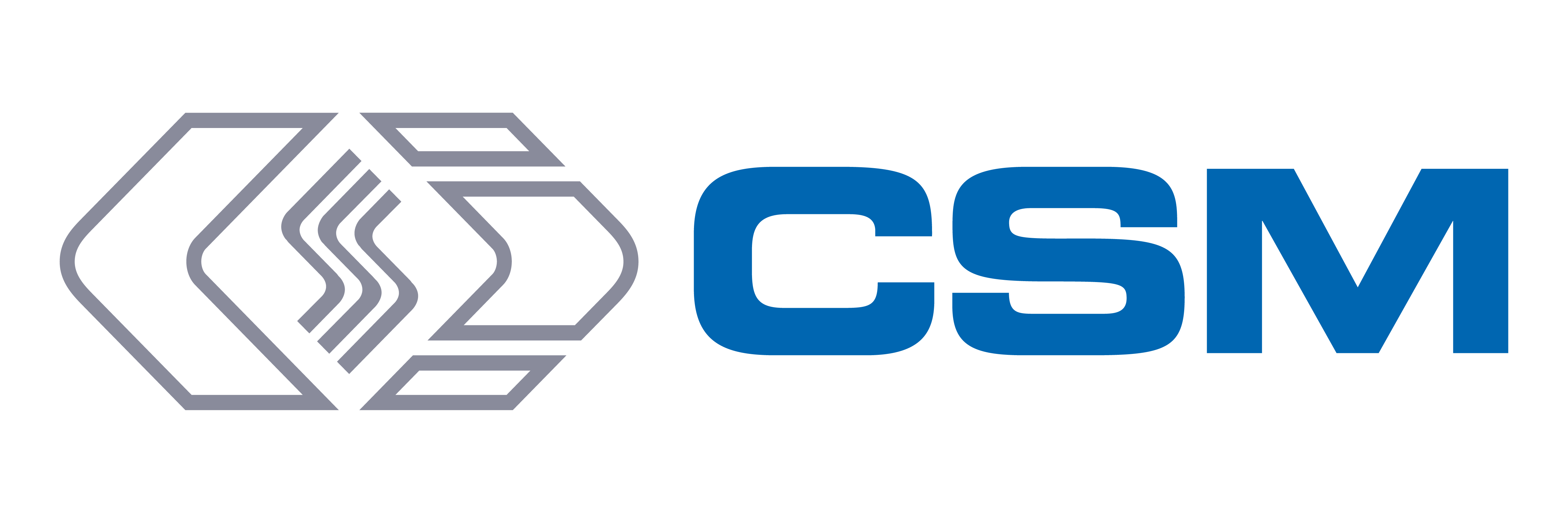