Henkel discusses developments in battery materials
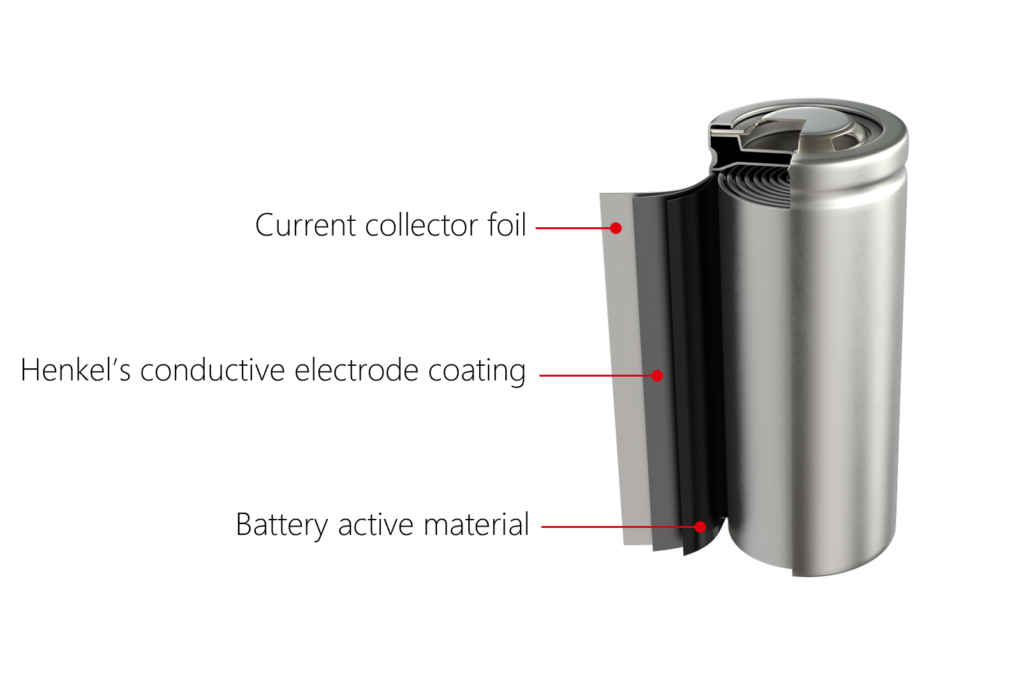
(Images courtesy of Henkel)
As with most areas of engineering, advanced materials are essential to achieving the energy density, power density, safety and reliability goals for EV battery systems, as well as sustainability-related targets in repair, reuse, repurposing and recycling – collectively known as re-X (writes Peter Donaldson).
Dr Keon Lee, head of product development and innovation for battery systems at Henkel, argues that adapting globally to e-mobility represents an unprecedented technological transition that is overwhelming many long-established mobility industries, from light vehicle and heavy truck manufacture to aerospace.
Enormous interest and demand is inspiring a variety of innovative ideas, he says, while start-ups claiming to offer disruptive solutions for batteries as well as EVs proliferate. This, he adds, is generating debate about which form factors are likely to dominate, whether solid-state batteries will be mass-produced for popular EV models, how much impact will be achieved and by when. “In this complex world, only companies that are agile enough can survive,” he says.
Henkel’s efforts to accelerate innovation in battery materials are focused by its Fuel the Future (FtF) effort, launched in 2021, to address the four high-level drivers of passenger safety, longer range, rapid charging and the circular economy. To analyse emerging technology trends in these areas, and interpret them in the form of materials requirements, the company has organised them into the ‘safe battery system’, ‘battery cell technology’, ‘integrated battery design’ and ‘sustainable battery’ work streams.
“Henkel invited experts from different sectors to join the FtF team,” Dr Lee explains. “They all have battery-related knowledge in common, but they also have different experiences and specialities, from chemistry to simulation.”
All the work streams can draw on expertise in thermal management and application technology for support. “It is about offering very practical, ready-to-use solutions to customers such as OEMs and battery manufacturers,” he says.
Safe battery systems
With increases in energy density to improve range come increases in the heat released during thermal runaway events, making it very challenging to build safe battery systems without sacrificing specific energy and energy density, and remaining competitive in cost terms, according to Dr Lee.
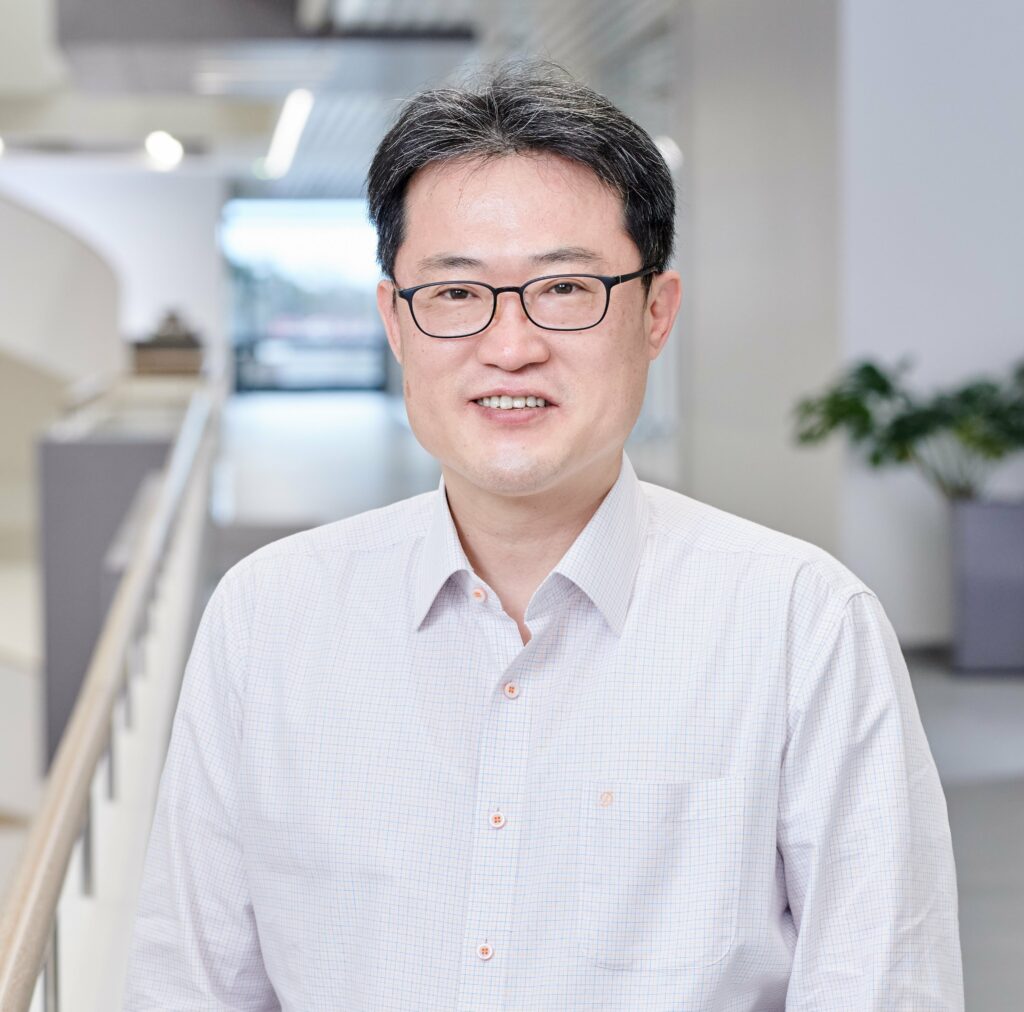
“To tackle this challenge, comprehensive knowledge is required to ‘connect the dots’,” he says. “For instance, during a thermal runaway event, we need to understand how much heat is generated and transferred inside the pack, how the flammable gas flows out of the pack, how this phenomenon can be reproducibly and reliably tested, and how much volume and weight can be allocated to precautions. The best solutions with optimised materials design flow from understanding all these factors.”
Cell technology
Cell chemistry and form factors influence the design, manufacture and thermal management of a system, Dr Lee argues, and because they contribute most to the cost of the pack – and, by extension, the entire vehicle – any breakthrough at cell level will have a large impact.
The dry electrode process, for example, can potentially enable lean manufacturing in terms of capital and operational expenses, he says, and removes the need for hazardous and difficult-to-dry solvents. It is also considered the best process for manufacturing solid-state batteries. However, ensuring proper transfer of the dry film to the current collector is not easy.
“Henkel’s solution is a conductive coating technology that guarantees adhesion, fast coating, low interfacial resistivity, and milder electrode process conditions without sacrificing battery performance,” Dr Lee says. “This has been achieved through a knowledge of coatings and a deep understanding of the process as well as battery structure and performance.”
Other future technologies for which the company is working on enablers include solid-state batteries, lithium sulphur batteries and fuel cells.
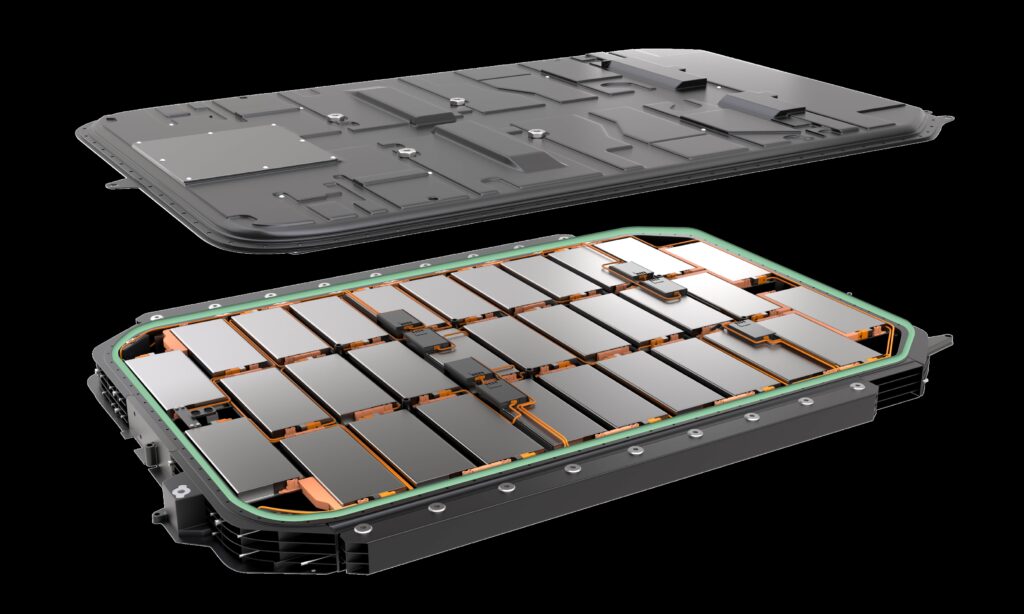
Design considerations
Materials selection is a major challenge in battery design, as different ones are required for different applications in the pack, and they have to be compatible. “Because a battery pack is a big, integrated system with hundreds of parts, how one material behaves cannot be estimated solely from the numbers on a technical data sheet,” Dr Lee says.
While building and repeatedly testing real packs or mock-ups is possible, it is time-consuming and expensive. Henkel has chosen instead to use simulation and digital twins to explore the behaviour of materials in thermal management, structural integrity, application and formulation.
Thermally conductive adhesive, for example, is getting more attention with regard to cell-to-pack configurations thanks to its heat-dissipating performance and strong adhesion, Dr Lee notes. Using these digital technologies, he says, the company will address issues and trade-offs that would be too complex with traditional approaches.
These include how to identify an adhesive with a thermal conductivity that works best with the thermal management system, to what extent cells can contribute to structural integrity through bonding, how the adhesive can be applied quickly enough to keep up with the battery assembly process, and how to finalise its high-loading filler and matrix systems.
Sustainability
Another difficult set of trade-offs is presented by the conflict between solutions that increase pack-level energy density and power density, and the need for repair, reuse, repurposing and recycling.
“Contemporary cell-to-pack designs with structurally integrated battery cells may be interpreted by re-X players as unthoughtful packaging, as difficulty in disassembly entails more resources for re-X, and it also makes recycling less economical,” Dr Lee says. “Shredding or roasting the whole battery pack might be a solution, but their economic feasibility needs to be validated.” Henkel’s search for a solution involves participating in consortia and initiating multi-stakeholder projects. De-bonding on demand has been identified as the leading candidate to enable design for re-X, and by extension the sustainable use of batteries. “Different technological concepts have already been proposed, eliciting a strong response from industry,” Dr Lee says.
For more details about Henkel’s e-mobility solutions go to: http://henkel-adhesives.com/emobility
ONLINE PARTNERS
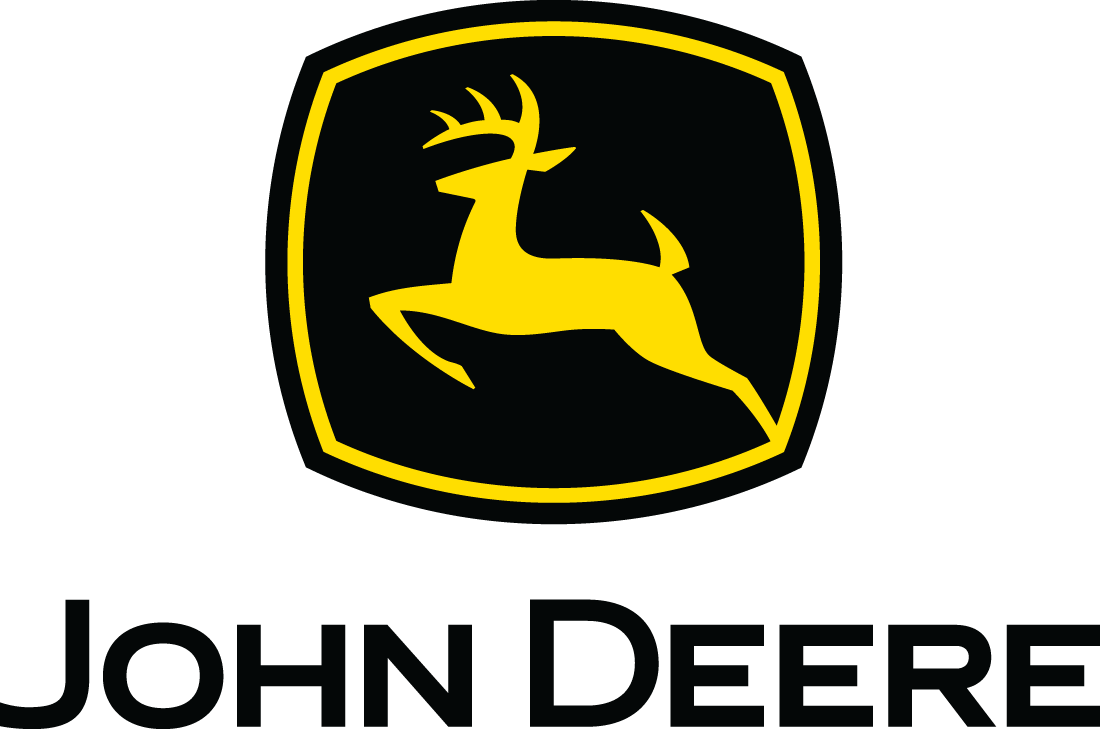
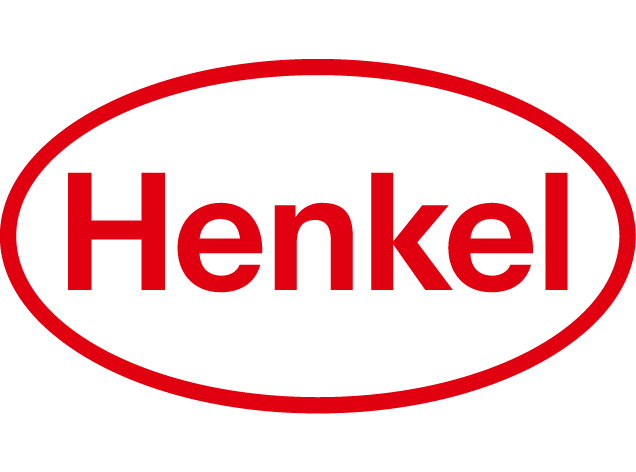
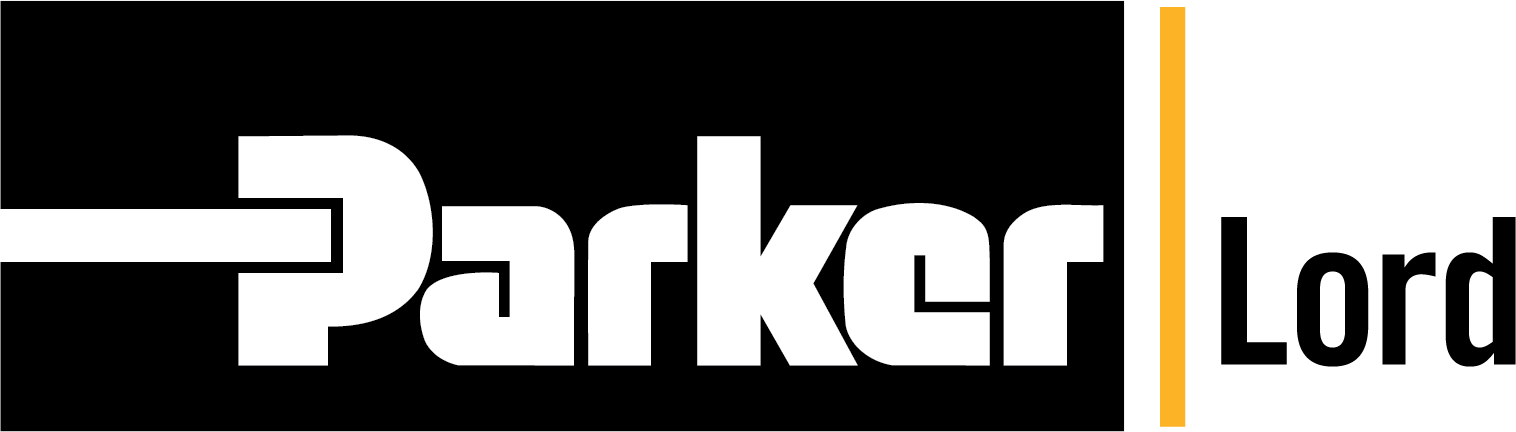
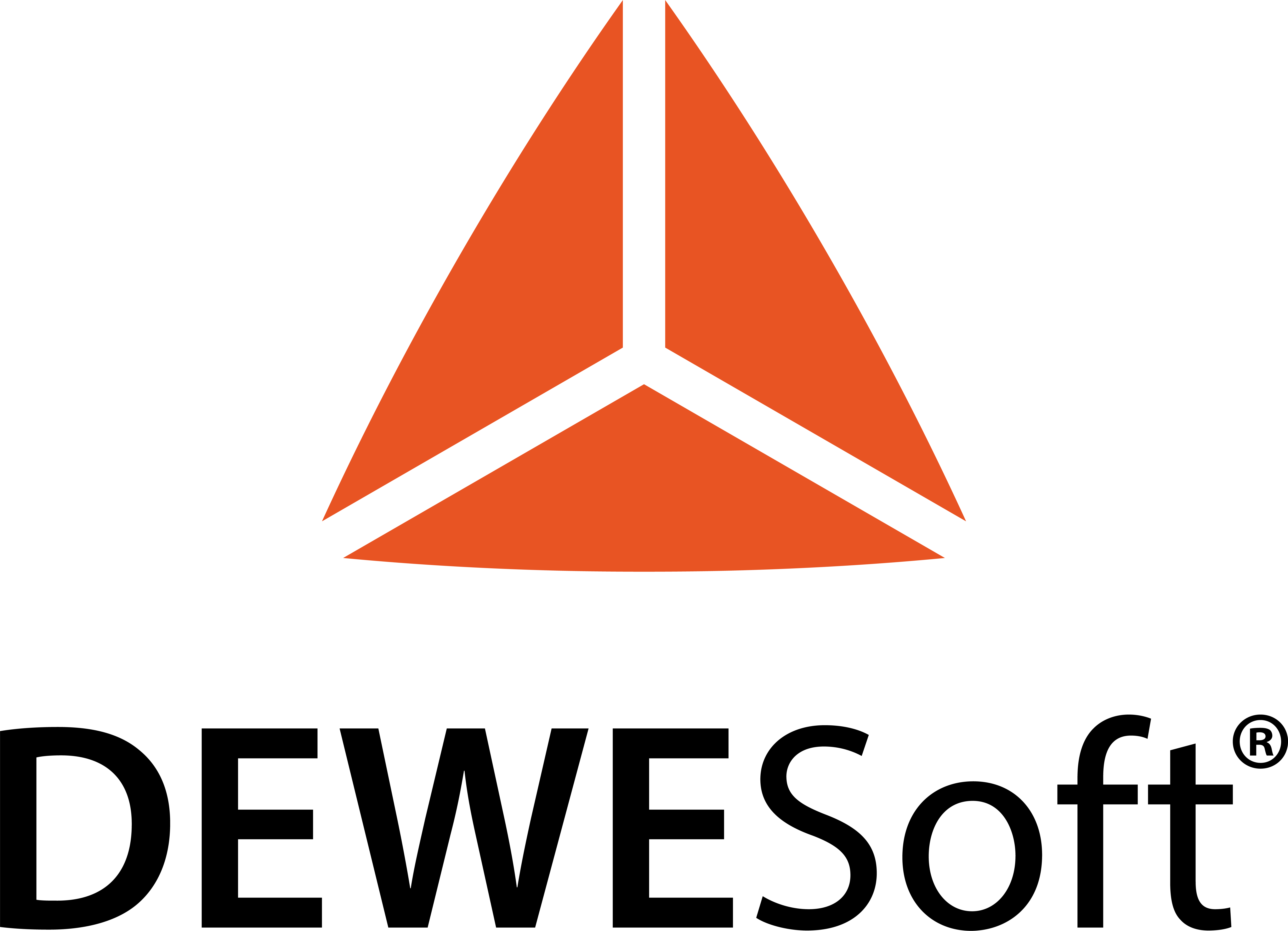
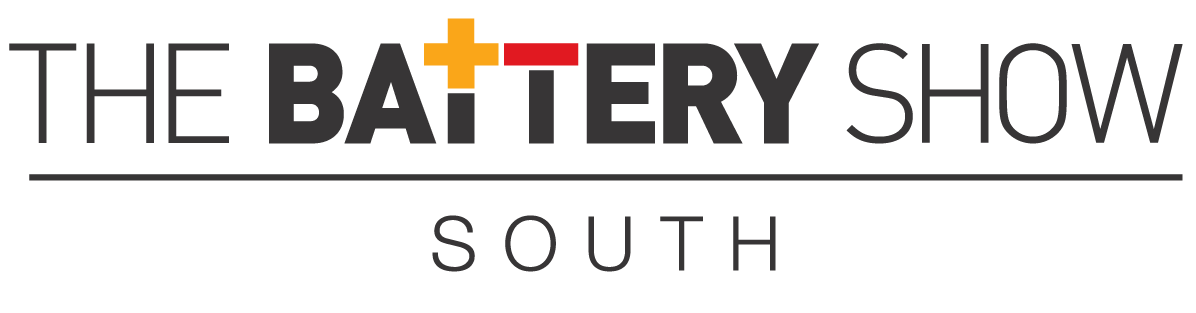
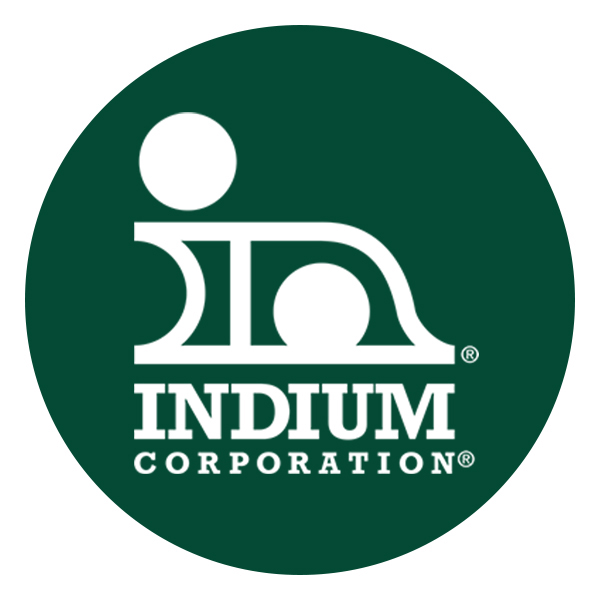
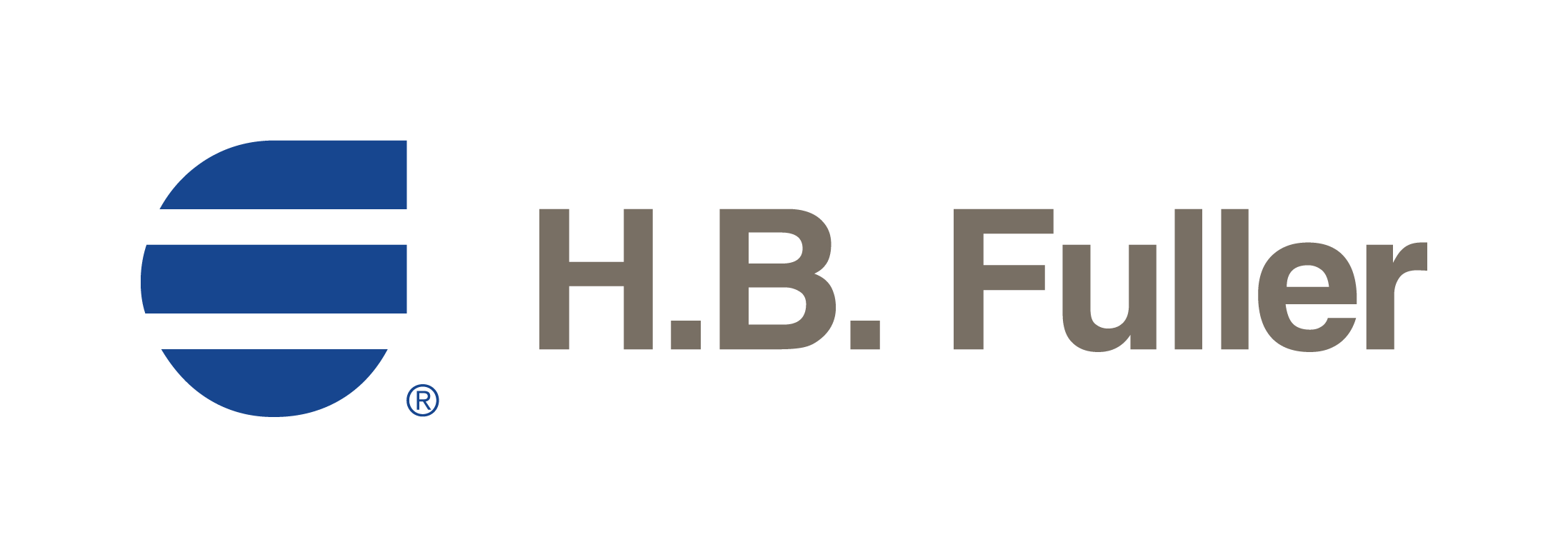