Graphene-free liquid cooling
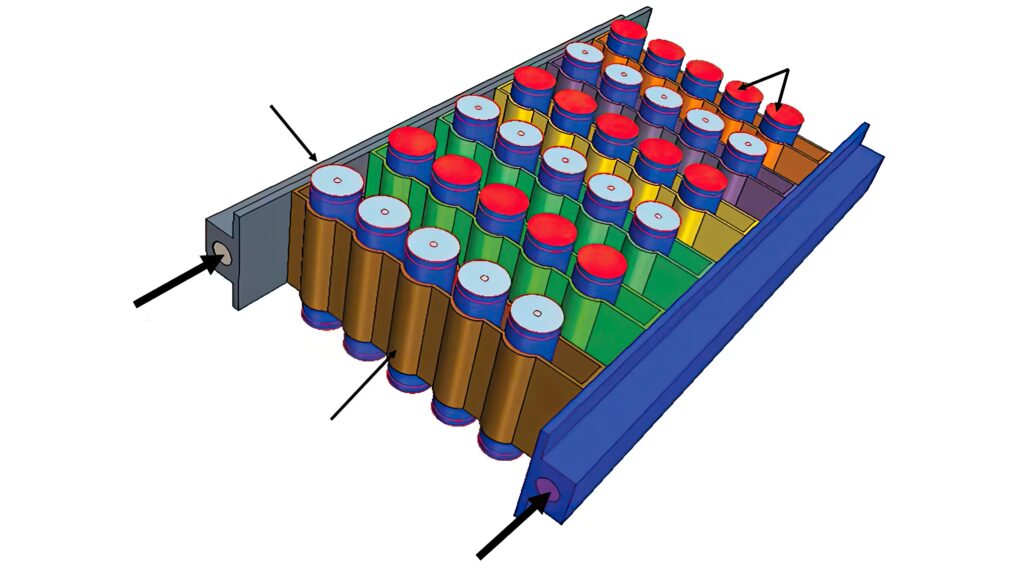
Researchers at Samsung have developed a design for a liquid-cooled thermal management system (TMS) for large lithium-ion battery packs (writes Nick Flaherty).
They first built a coupled 3D electrochemical/thermal model of a battery pack that avoids the use of materials such as graphene. Simulation showed that it is the contact resistance that has the greatest impact on the pack’s thermal performance, and the temperature performance across the pack could be determined from a single cell.
The team used a computational fluid dynamics (CFD) tool from Siemens to simulate the 3D flow of liquid around the cells in the pack and the spatial variance involved in heat generation to address thermal management issues.
For the large battery packs that operate at the high discharge rates typically used in EVs, CFD studies have shown that liquid cooling is more effective than air cooling, enabling the design of more compact and efficient batteries.
The researchers then built a 30-cell test pack from commercially available 18,650- cell Li-NCA/C cells with six cells in series and five in parallel. Elements made of highly conductive metal transferred heat from the cylindrical cells to the coolant channel and then to the coolant liquid, which in this case was water rather than glycol.
The characterisation of heat generation was obtained by constructing a 3D CFD-based electrochemical model of the battery that could be validated against experimental results, then used to simulate and evaluate the performance of the TMS under various operating conditions.
The project used two tools from Siemens. Simcenter STAR-CCM+ was used to simulate the flow and conjugate heat transfer, while Simcenter Battery Design Studio was used to obtain electrochemical input data. The combination was used to simulate the performance of the battery.
The 3D TMS model was used to compute the performance of the representative battery pack. It was found the average temperature difference between the hottest and coldest cells was only 0.5 Kelvin (K). Observing a clear pattern in the temperature rise, the researchers found that a properly defined temperature coefficient could predict the temperature of other cells from the temperature of just one cell.
In EVs, power for operating the TMS comes from energy extracted from the battery. Reducing the energy requirement for the TMS reduces its drain on the battery, optimising coolant flow rate.
The Simcenter STAR-CCM+ model revealed that more heat is stored in the battery pack in lower coolant flow velocity conditions, indicating that at lower flow velocities less heat is transferred into the coolant.
In most battery packs, maximum temperature variation is limited to 3 K along the direction of the flow stream. The experimental model easily met the 3 K limit and could effectively cool the pack, even at low-flow velocities.
The results of simulations agreed with experimental measurements, validating the model against the experiment with greater than 90% accuracy.
The temperature rises in the battery pack using the experimental TMS are of the same order as those reported in research literature that used graphene as a phase change material (PCM) based TMS. Although such PCM-based TMS are compact, this new one does not require the use of such novel materials and can therefore be produced at lower cost.
Other battery packs built using the symmetry of the total pack were successfully simulated, together with the TMS as suitable candidates for e-mobility powertrains.
Click here to read the latest issue of E-Mobility Engineering.
ONLINE PARTNERS
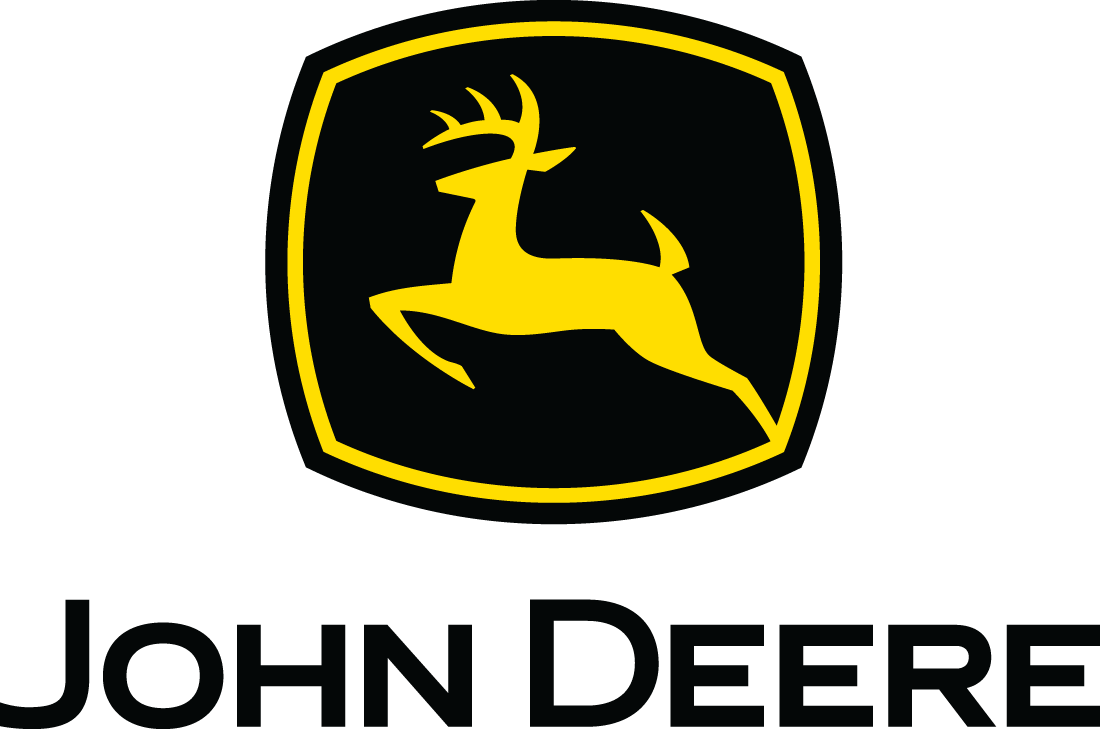
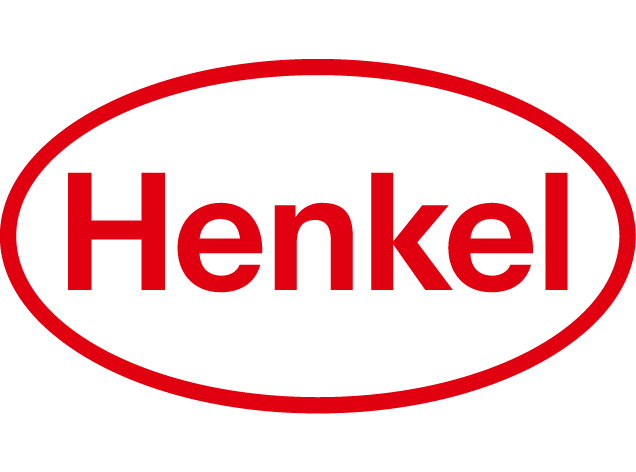
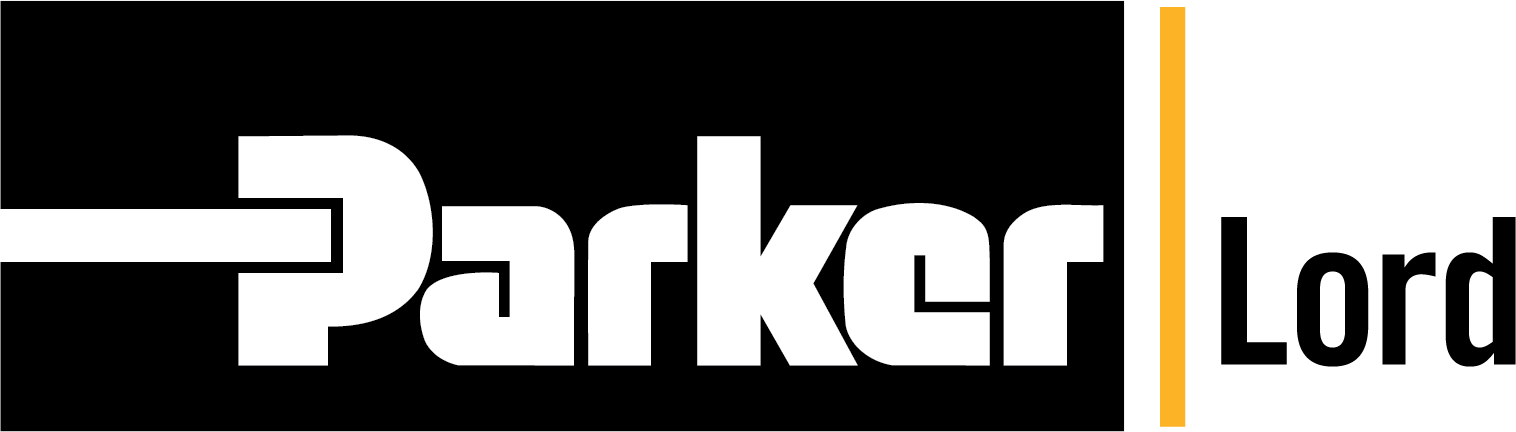
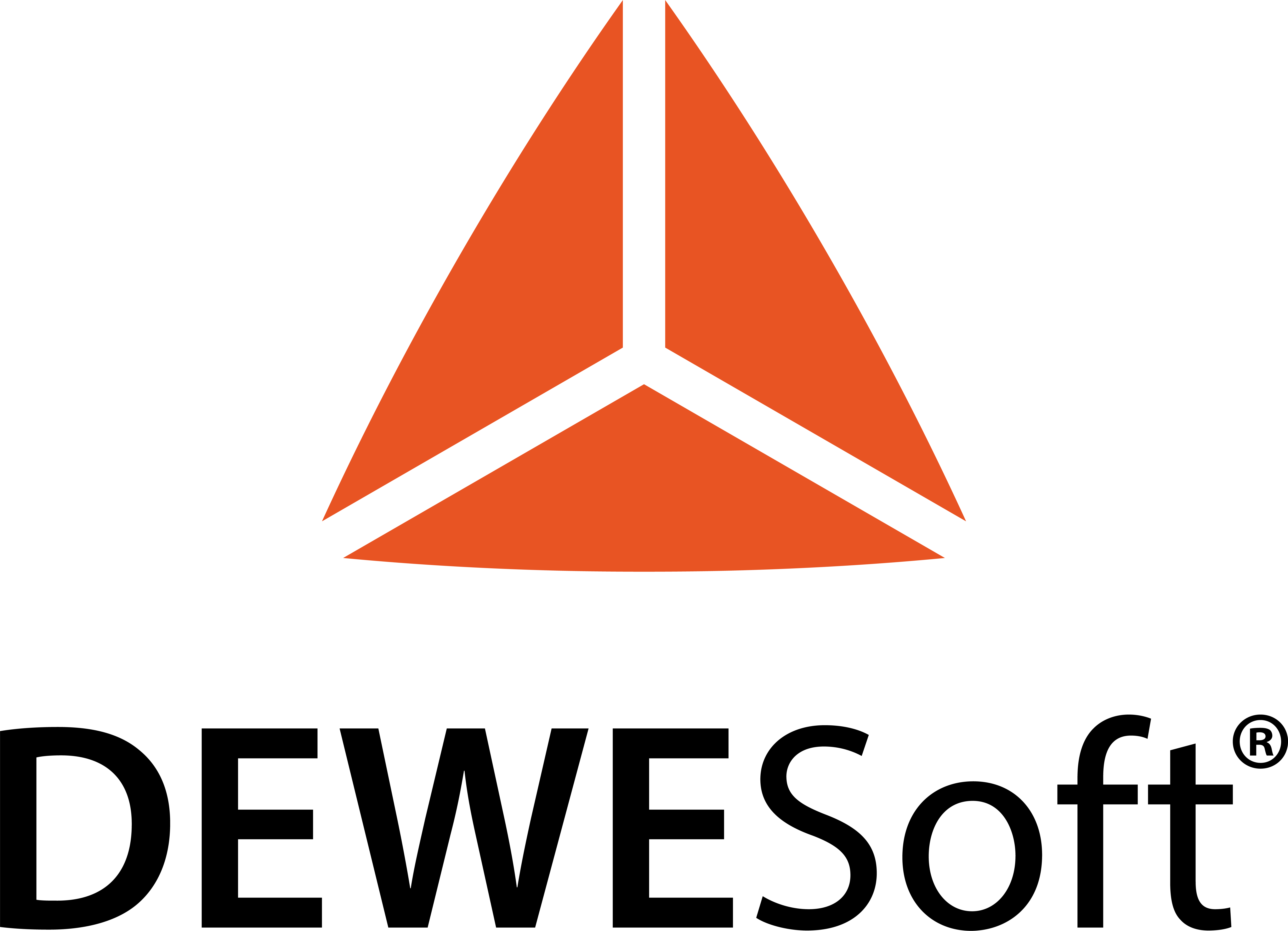
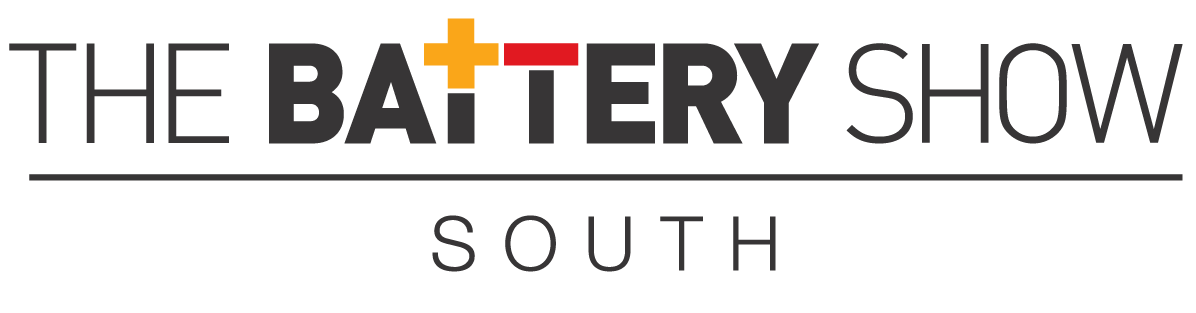
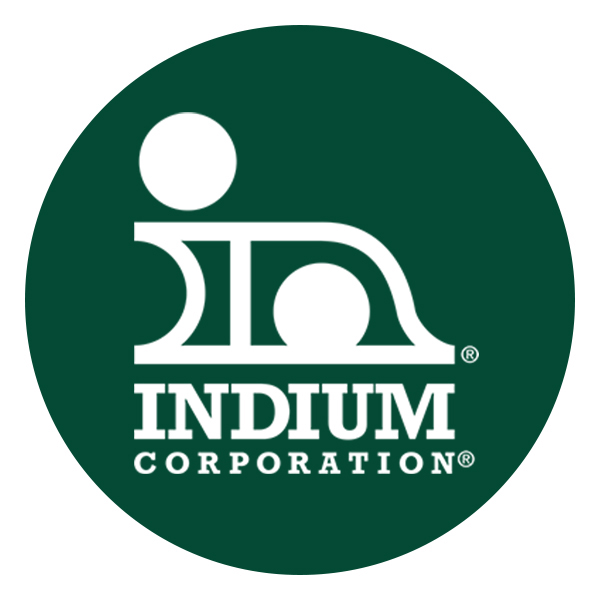
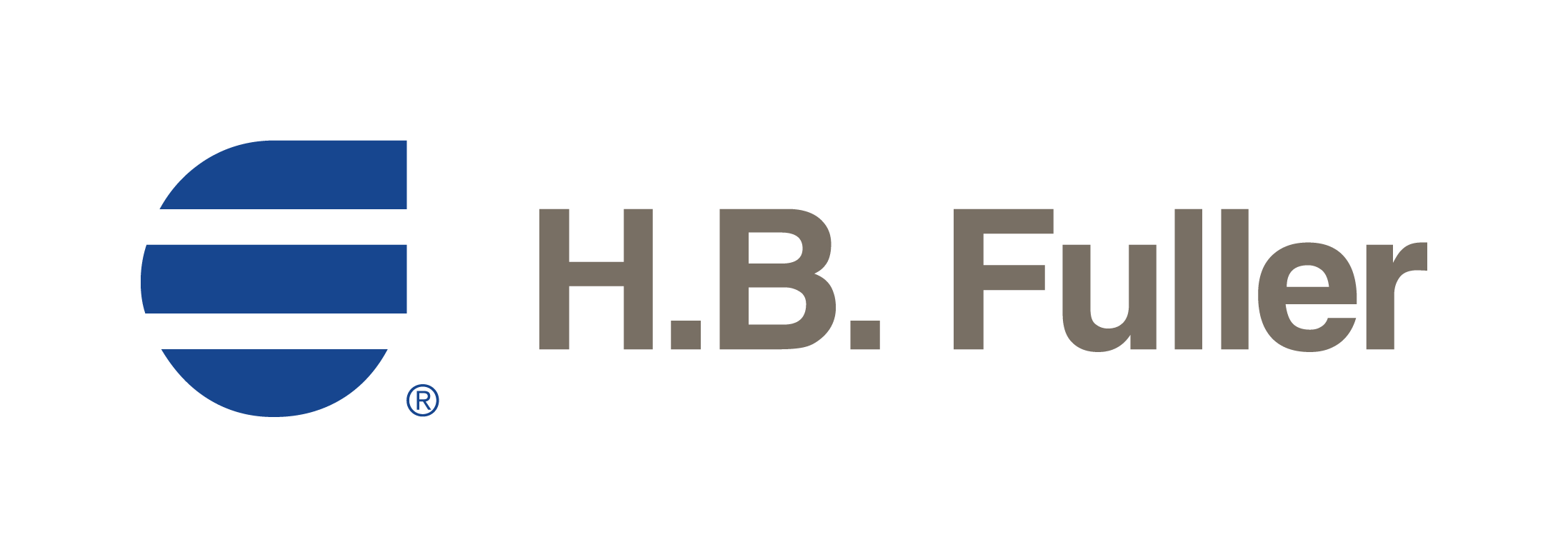