Fellten Charge Qube
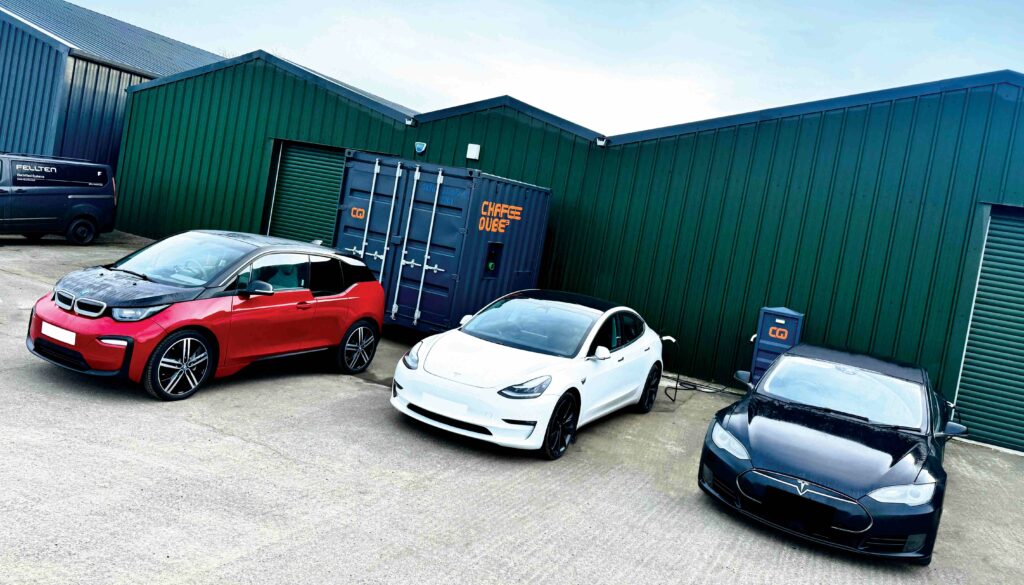
(Image courtesy of Fellten)
Boxing clever
Peter Donaldson investigates a containerised system that can charge multiple vehicles and doesn’t need a grid connection
Until the electric power grid is able to support fast charging for EVs everywhere, there is likely to always be a market for something like Fellten’s Charge Qube – a containerised system that stores energy in repurposed battery packs and can charge multiple vehicles simultaneously, with or without a connection to the grid.
The system is initially intended for sites that need charging capacity and either don’t yet have planning permission for permanent installations or they don’t need it. Fleet depots transitioning to EVs may fall into the first category.
Building contractors wanting to replace diesel generators on site to charge electrified off-highway vehicles and other equipment, and open-air festival and show venues are likely to fall into the second category.
Weighing at least 3.5 t, depending on the number of battery packs installed, the system is designed to be delivered to the site on a flat-bed truck with an integral crane, and it can be positioned on any piece of level, dry ground firm enough to take its weight.
Once delivered, it can be put into service in under two hours. Today, the maximum capacity is 450 kWh with six 75 kWh battery packs in a 10 ft container format; 20 ft container options are being finalised with capacity up to 900 kWh.
For fleet operators and businesses that need overnight charging for multiple vehicles, the system can be equipped with a pair of Type 2 AC chargers on Qube itself, and two each on five satellite ‘pavilions’.
It can charge up to 12 vehicles at the same time at up to 7 kW per port. There is also an integral, 22 kW charger for rapid top-ups during the day. The smart charging software prioritises overnight charging and recharges the onboard battery pack in 6.5 hours.
Qubes equipped with a pair of 150 kW Combined Charging System (CCS) fast chargers are aimed at businesses and public charging networks that need rapid charging capabilities. Outputs range from 400-800 V, depending on customer requirements and the battery packs used.
If needed for only a short period of time, during which it will not need recharging, Qube can operate as a standalone system. However, it can also be connected to the grid or any kind of trickle-charging device, including diesel or multi-fuel generators, solar panels and wind turbines. Multiple Qubes can be daisy-chained together.
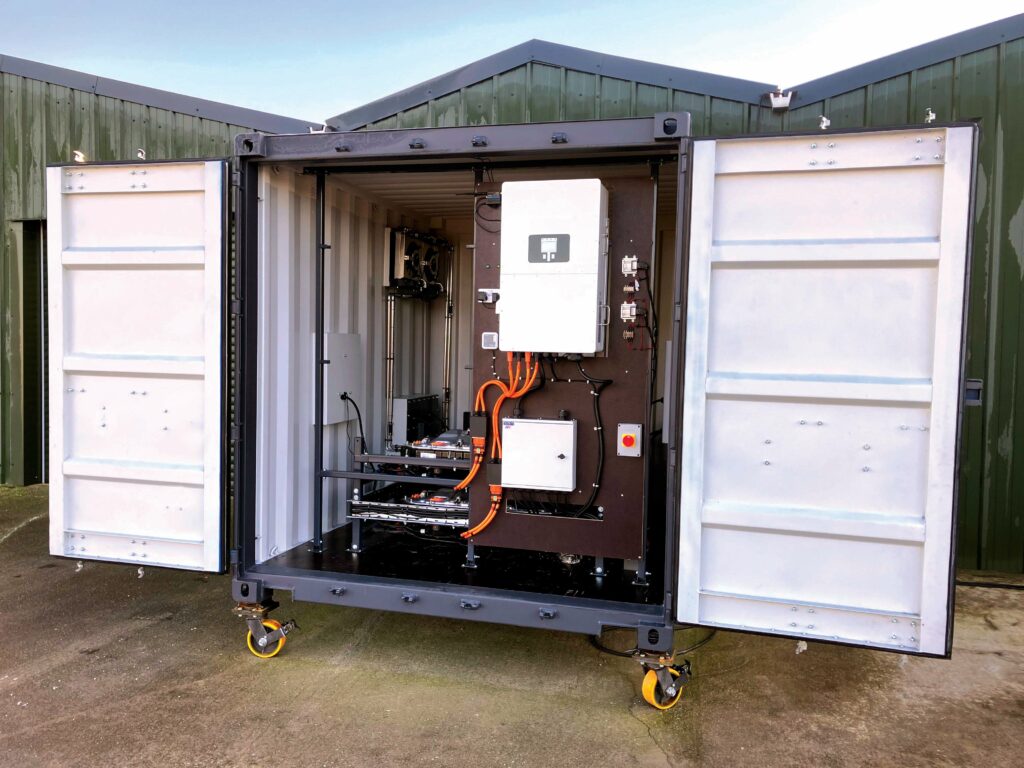
(Image courtesy of Peter Donaldson)
Second-life packs and containers
An important part of Fellten’s business model for Qube is the use of second-life components, which cut manufacturing costs and reduce the carbon footprint, says CEO and co-founder Chris Hazell.
“The fact that we are using second-life components but others are not makes it more cost-effective for us to build, and allows us to sell it for less. There’s also a major benefit for bigger companies because the environmental impact is lower and the carbon offset is a lot better,” he says.
The battery packs in Qube are not (as may be expected) ones that have degraded to 80% of their original capacity. Fellten also converts classic cars to electric power, and it has years of experience dismantling and reworking battery packs from many manufacturers, including Tesla, Volkswagen, Jaguar Land Rover (JLR) and Kia.
“The whole industry has realised that batteries last way longer than anticipated,” says Jerome Andre, EV advocate and consultant for Fellten. “We’ve seen early Tesla Model S cars run with their original battery packs to 400,000 miles with no issues whatsoever.”
“It’s very rare to find a lithium-ion EV battery that has degraded as far as to have only 80% of its original capacity left,” Hazell notes. He recalls that when working on a contract for JLR about three years ago, for which Fellten was dismantling iPace batteries for second-life applications, they never found one with less than 88% of its original capacity.
“These were packs from prototypes and vehicles used in the iPace race series. Those packs were still surprisingly good, even though they’d just been absolutely abused.
“What you tend to find is there’s a degradation curve, and once you get down near the 80% it flattens out. What we’re expecting with these is that, keeping them between 20-80% charge, they’ll slowly get down to 80% capacity and stay there for a long period of time. Looking at current reports we’re seeing 25 years life expectancy for a lithium-ion battery.”
Instead, the packs used by Fellten are undamaged, healthy units, taken from vehicles written off after minor accidents.
The Qube I was shown in mid-January was fitted with a pair of Tesla Model 3 packs for a capacity of 150 kWh. The packs were supported by a steel framework and stacked one on top of the other. They had space above them for more pairs, doubling or tripling capacity to 300 kWh or 450 kWh. Andre says it is possible to install eight packs for a capacity of 600 kWh.
Qube is not limited to packs from any one manufacturer, so Fellten can make the most of whatever is available. Today, Tesla packs are plentiful, and the company anticipates also using units from Kia and BYD.
The structure of Qube is made from half a 20 ft-long ISO container by conversion specialist Titan Containers. It arrives at Fellten’s premises near Bristol, UK, fully painted with the cut-outs for the charge ports and heat exchanger, plus all the internal bracketry and support structure, so it is ready for Fellten to install the battery packs, power electronics, thermal management and control equipment.
Empty, the container weighs 1.2 t, Andre says. With each battery pack at 400 kg, total container weights will range from2.5 t to 4 t, well under the maximum allowable gross weight of a 10 ft container.
Other than the change in length, no structural modifications are made to the container, as the openings for the charge ports are made in the wall panels. It therefore retains its original strength, so it can be stacked several high, which provides additional benefits.
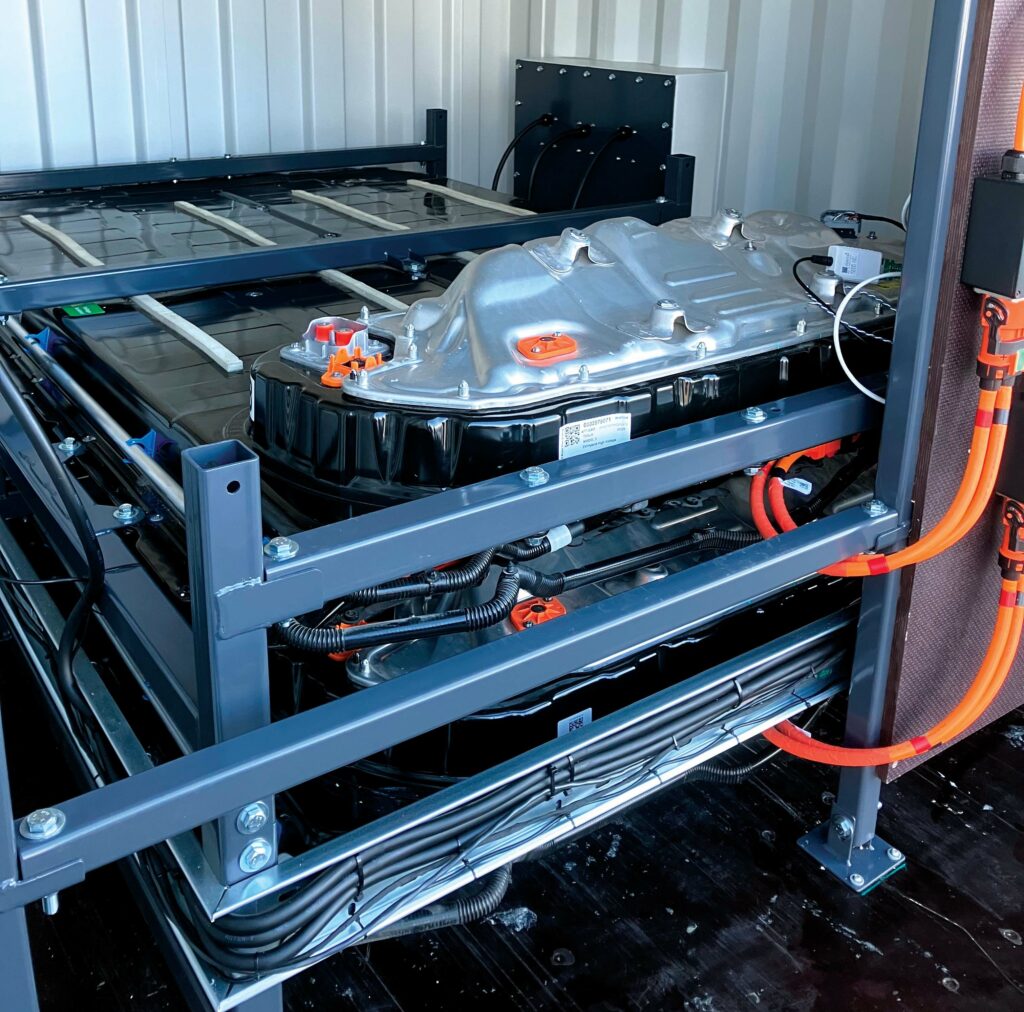
(Image courtesy of Peter Donaldson)
Power electronics
At the heart of the AC charging system is an off-the-shelf inverter that was the subject of a long and thorough search, which enabled Fellten to go ahead with Qube’s development, as Hazell explains: “We designed the Charge Qube five years ago, but then found we had to buy so much power electronics to get it to do what we wanted it to that it was never going to be financially viable.
“Everything back then was 48 V, so it just wasn’t efficient, and it wasn’t until new inverters came out that can do phase-balancing and tie into the grid, as well as running off-grid in one unit, that it became viable,” he says.
“It is rated up to 1000 V, so that means we can use complete OEM battery packs, whereas before we had to take the battery packs apart and change the voltage on them.
“Now we can take a complete Tesla, VW or JLR battery pack, for example, and put them in at 400 V or 800 V. They stay completely sealed just as they came from the OEM vehicle.”
All the AC components are connected by a distribution board from Proteus Switchgear. “It all comes into and out of that one board.”
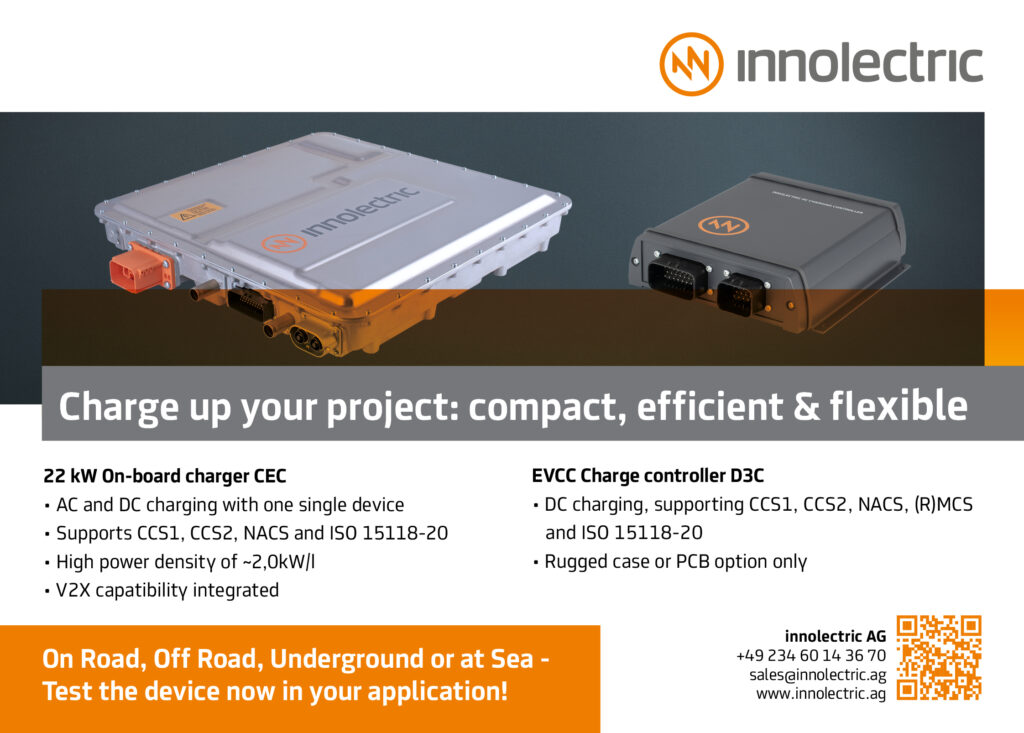
Battery management
Qube’s main control computer, which is based on a Raspberry Pi, oversees the battery packs, along with the rest of the subsystems.
“We’ve had to write all custom software to work with those battery packs. We run all the OEM software on it, including all the safety systems you get in an OEM vehicle,” Hazell says.
Also, all the original BMSs are retained unmodified. “If there are six packs in the Qube, there are six BMSs. Each pack runs completely stand-alone. It’s got its own set of contactors and its own safety systems, so if there is an issue a pack can take itself fully offline,” he says.
As a further precaution, every pack is managed by the same version of the BMS software, which runs on the main computer.
Another benefit of using unmodified packs is that they retain all the resistance to stressors such as fire, vibration and impact that the OEM built in for the original application in a car. This means they are robust enough to shrug off any stresses to which they are subjected when Qube is moved between locations, he points out.
“We mount each pack in the same way,” he adds. “We keep in the same orientation using the same mounting point, so we know it’s going to be rugged.”
All the battery packs are liquid-cooled, and Qube has its own cooling system that serves all the packs with multiple pumps sourced from Davies Craig. The coolant is piped to a heat exchanger that consists of a pair of OEM-supplied Tier 1 radiators and fans, which also cools the interior of the Qube and all its electronics, including the air-cooled inverter, which does not need much cooling.
“As long as we maintain the same cooling systems, we know the batteries are cooled correctly internally because they’ve all been designed by the OEM to be super-efficient without us having to design a whole new system from scratch,” Hazell says. “It has covered a lot of the hard work for us once we get the software right.”
The coolant pumps come on for a minute every 10 minutes just to circulate the water ethylene glycol (WEG) mixture through the battery packs to make sure they are all at the same temperature, he explains.
“They are not running all the time because the batteries are making minimal effort, far less than they would in the original car, but we still run the pumps for set periods just to make sure there are no hotspots,” he says. “But, if the batteries go over a set temperature, the pumps kick on continually and then the fans can kick on in addition.”
Separate temperature sensors inside the container are also monitored by the computer, which switches the fans on to cool it, even if the batteries don’t need cooling. There is also a tube heater system that comes on automatically to prevent the temperature inside Qube falling below 10 C. For hotter climates, Fellten plans to fit an air-conditioning system.
“The batteries have an easier life in the Charge Qube than they do in the car because they’ve got so much extra capacity,” Hazell explains.
“On the smallest one we do, which has a 150 kWh battery capacity with a 50 kW inverter, we’re doing a 0.3 C or 0.4 C discharge, whereas a Tesla or an iPace might charge at 3 C – crazy fast. And, in a 0-60 sprint, peak discharge on them is going to be, say, 4 C. So, in our situation, they’re just tickled, they’re not under any stress, so they last a lot longer.”
Battery packs are linked together in pairs using a series connection to achieve the desired voltage, and also as a protective measure against the effects of different levels and rates of degradation.
“At no point do we link two batteries in parallel,” he emphasises. “If you have one that’s badly degrading one that’s not, normally you’ll find that the stronger battery will buffer the weaker one, and it will degrade the stronger battery really quickly by exceeding its maximum discharge rate.”
Hazell explains that the inverter has multiple high-voltage (HV) inputs that are isolated from each other to cope with multiple packs. Within the inverter are multiple HV buses that handle the DC-to-AC conversion. One inverter can handle two pairs of batteries. A Qube with six batteries (three pairs) would have two inverters.
“That is the way we have managed it, just to remove that risk of potential issues with paralleling packs,” he says. “Most of the risk in energy storage comes from this, because if you have multiple packs parallel and you get one bad cell, all the good ones can rapidly charge the bad one, degrade really quickly and cause a thermal runaway event.”
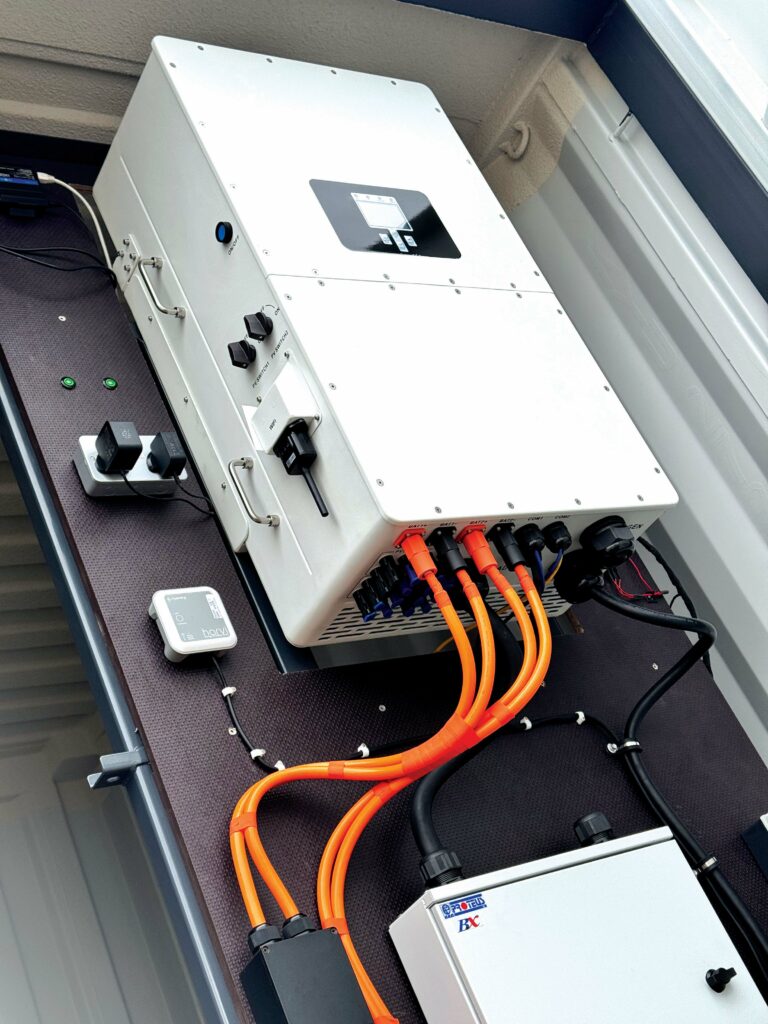
(Image courtesy of Fellten)
Fire safety
To deal with electrical fires, Qube has a CO2 or powder extinguisher in the roof, which is triggered when the internal temperature rises high enough to expand a heat-sensitive fluid so that it breaks a glass bulb and releases the extinguishing agent. Obviously, other arrangements are needed for battery thermal events and fires.
The thermal management system monitors each pack individually, and automatically shuts the systems down if a pack overheats, while the container has vents near the top to clear gases released from a battery in thermal runaway.
Fellten works with local fire services and it has obtained a standard fitting for a fire hose. The plan is to install such a fitting at the front of every Charge Qube, which will allow firefighters to clip on a hose and leave it running. The container will eventually overflow through the top vents. Lower down there are more vents with silicone seals designed to let air in and out normally, but these will be forced shut by water pressure as the container fills, Hazell explains.
Ironically, it is possible for water to both trigger and suppress thermal runaway in a pack by first shorting out and then taking the heat away. A test by a customer (who will remain nameless) proved this. Battery packs are not sealed unless all the HV connectors are in, and the customer filled the case containing the pack with salt water.
“A couple of cells went bad, but because the battery was submerged in cold water at the same time it never went into full thermal runaway,” he says. “The water that came out was warm.”
Fellten has taken precautions against this problem by blanking off all the unused connectors on each pack to ensure they are sealed.
Connectivity
Fellten plans to monitor its Qube fleet through the cloud and it fits every unit with its own communication system, which can include any combination of wi-fi, cellular and satcom, with the choice depending on the amount of data that has to be moved.
“We put a small StarLink satcom system on there because we know we can push big amounts of data. Long term, I think it will be mainly 5 g,” Andre notes.
Naturally, remote management raises cybersecurity issues, and the company is currently working its way towards certification for compliance with international information security standard ISO/IEC 27001.
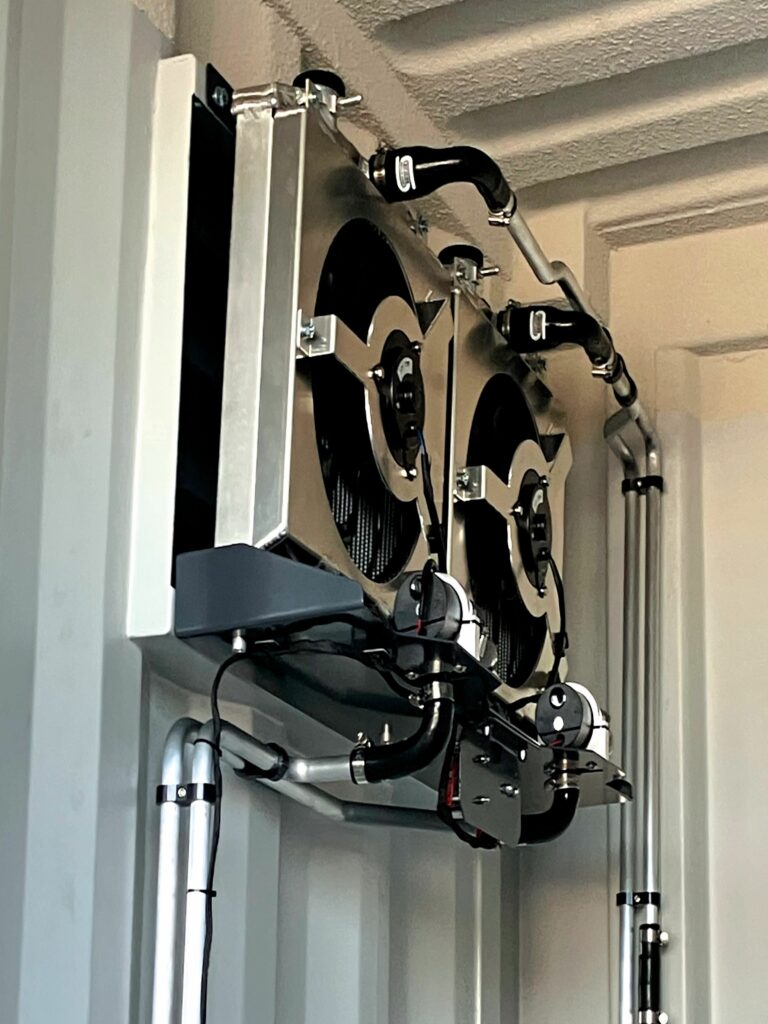
(Image courtesy of Peter Donaldson)
High-rate charging
While CCS is nominally a standard for high-rate DC charging, there are enough differences between implementations for vehicle OEMs to face a lot of work to ensure compatibility with all the chargers they are likely to encounter.
Fellten went through this with its own vehicle conversions and the expertise it gained from that experience led it to focus on developing the DC-DC conversion side. It decided to focus on the power electronics and buy in the front end from IoTecha, a company with which they work on the car conversion side of the business. IoTecha produces a CCS plug, cable and screen running customer interface software.
“That component will tell us what voltage and amperage it needs, and then we ramp up our DC-DC units in order to deliver that to the car,” Hazell says.
“The reason we want to do the main DC-DC conversion is that we can go direct from high-voltage DC in the battery straight to DC out, rather than having to go DC to AC and back to DC again, which is what a lot of people are doing, and there is an efficiency loss every time.”
Hazell expects that some Qubes, particularly those used on construction sites, will retain the inverter to provide AC power to tools and cabins, and a couple of CCS chargers for heavy plant equipment and off-highway vehicles.
“It means you don’t have to have a massive AC inverter. You could have a 50 kW inverter, but then put your money into DC-DC units that can put out 200-300 kW peak,” he says.
“The AC inverter would also charge Qube using a genset on site that can be a lot smaller than normal because it doesn’t need to handle peak loads.”
The company is also working on vehicle-to-grid (V2G) for Qube and it is testing a prototype CCS charger designed for V2G on site. However, there is much work to be done on the software, particularly the communication protocols, before it will work properly.
“There is a set communication protocol for CCS, but for some reason the charging companies vary how they use that protocol. The problem is that it is not managed. There is no one body responsible for CCS,” Hazell says.
Fellten is still finalising its pricing structure, says Andre, but the system is available for purchase, lease or rental to suit different customer needs. Entry-level configurations are positioned in the higher five-figure range, while larger-capacity systems are in the six-figures. Leasing options will also be available, with monthly rates reflecting system size and terms.
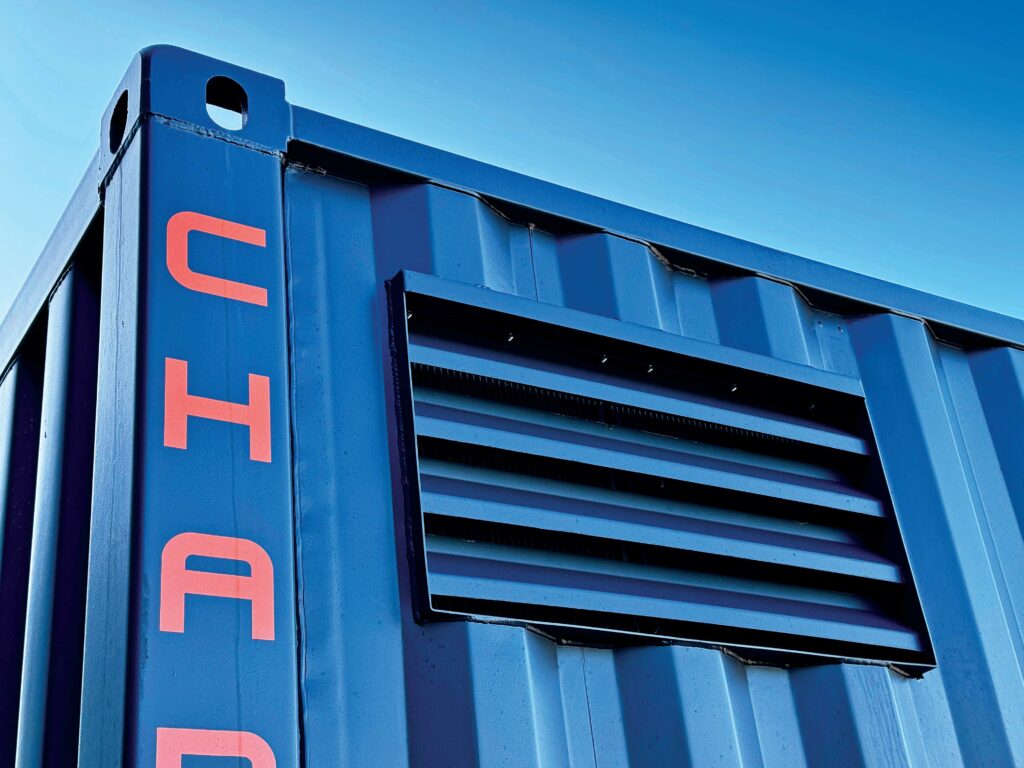
(Image courtesy of Fellten)
Specifications
Weight: From 3.5 t, depending
on container size and number of battery packs
Energy capacity: 150-450 kWh in 10 ft containers, 600 kWh and 900 kWh in 20 ft. All versions are daisy-chainable
Input power: 32 A, 3-phase or optional 63 A, 3-phase
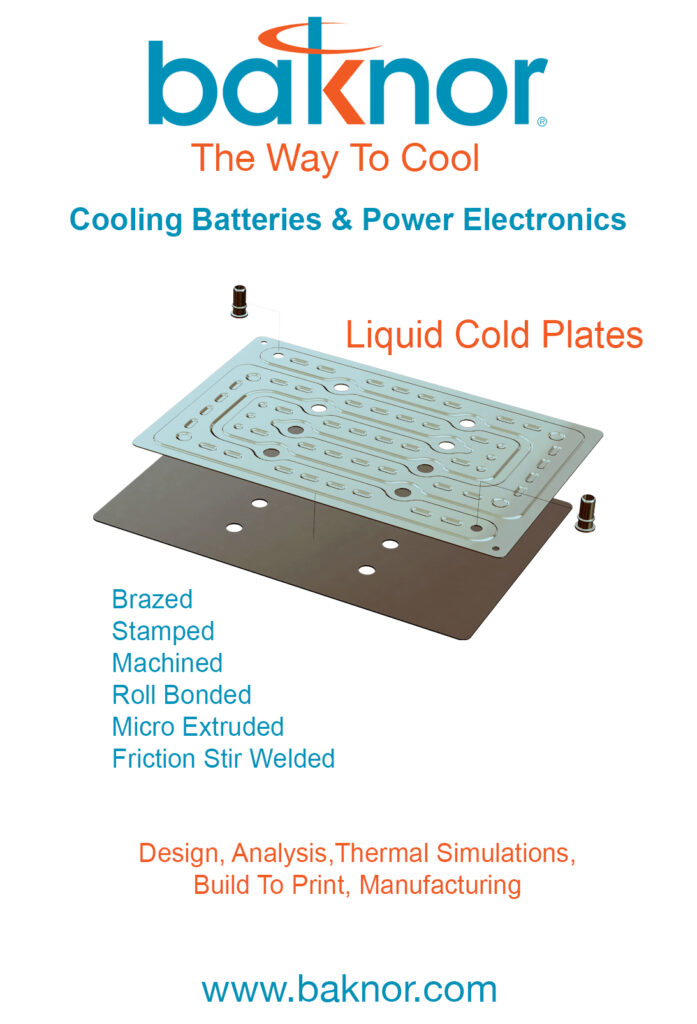
Output power: 63 A, 3-phase or optional 125 A, 3-phase
Dimensions: 10 ft long x 8 ft 6 in high x 8 ft wide (2.99 m long x 2.59 m high x 2.44 m wide)
Optional features: Solar and wind input integration, Starlink connectivity
Type 2 AC charger variants:
CQ3-323-12T2-150, -300, -450 and -600
CCS DC fast-charger variants:
CQ3-323-CCS150-300 and -CCS150-450
Some key suppliers:
Heat exchangers: AlliSport
Chargers: Autel
Coolant pumps: Davies Craig
Chargers: Myenergi
CCS charging controllers: IoTecha
Container supply and preparation: Titan Containers
ONLINE PARTNERS
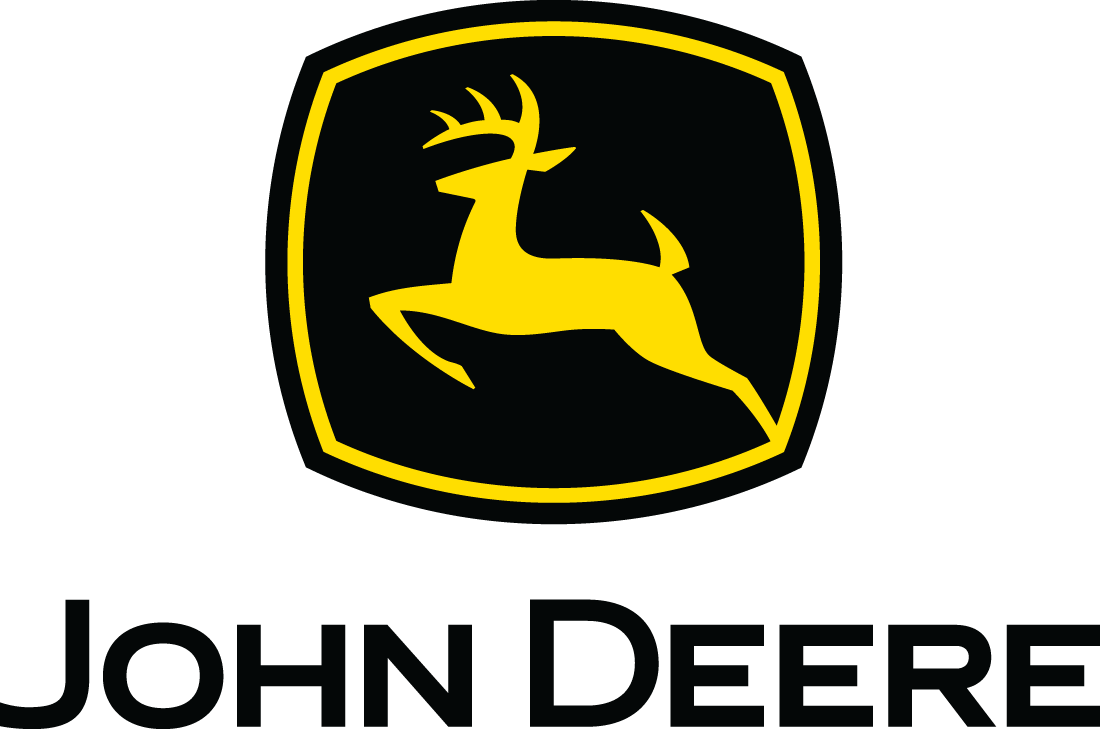
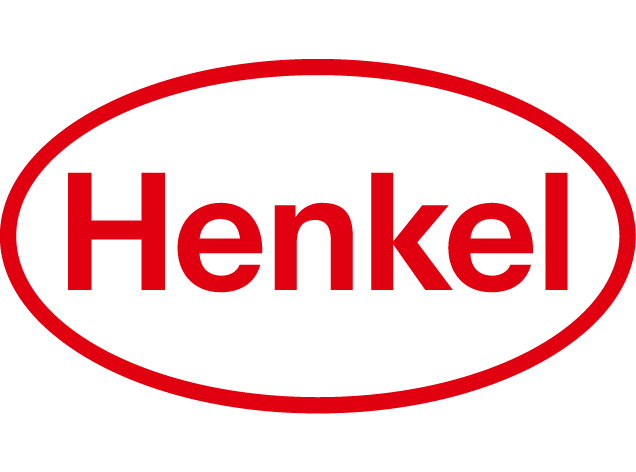
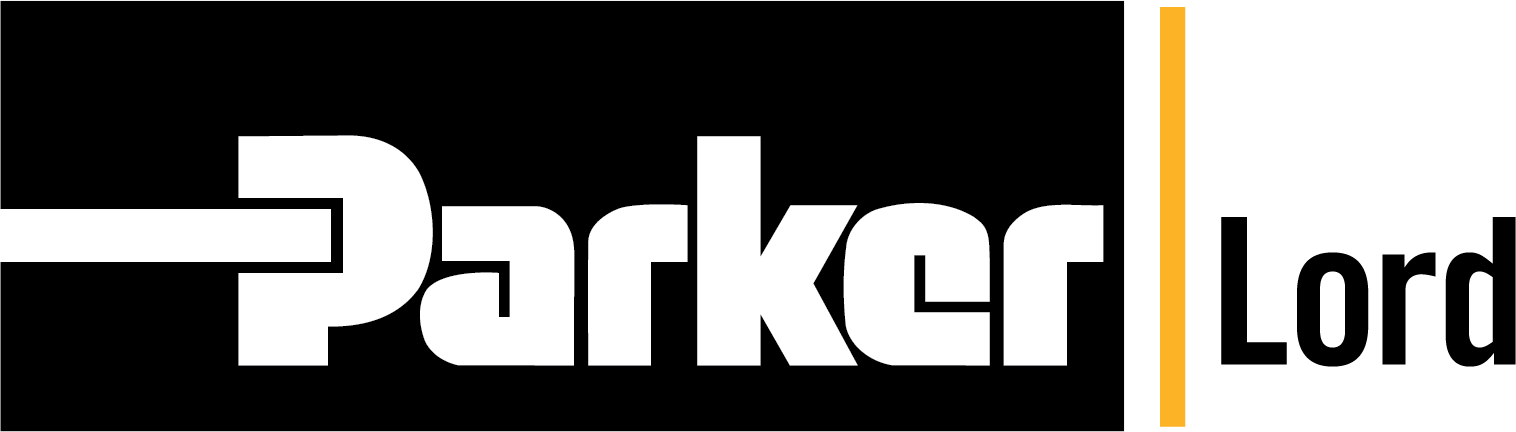
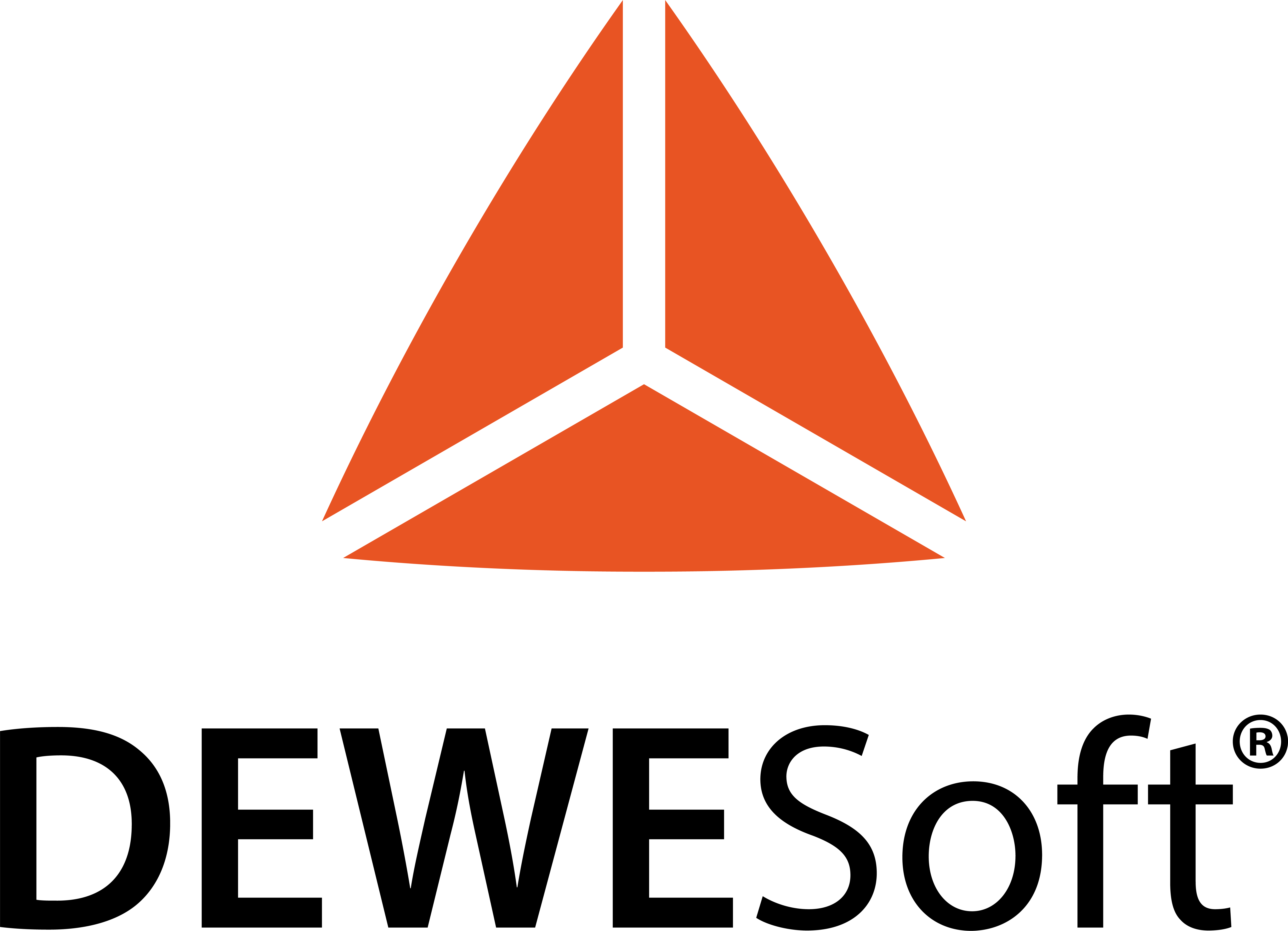
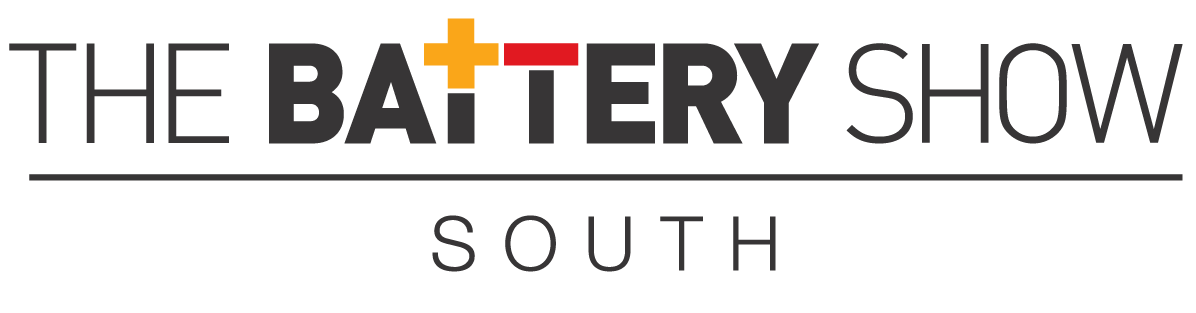
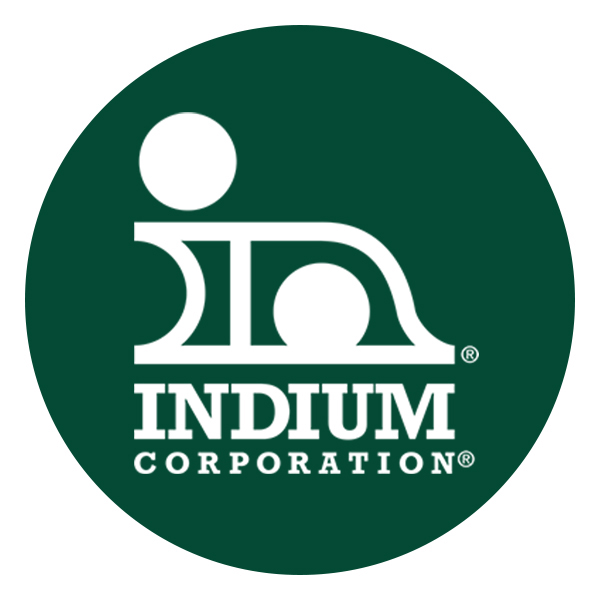

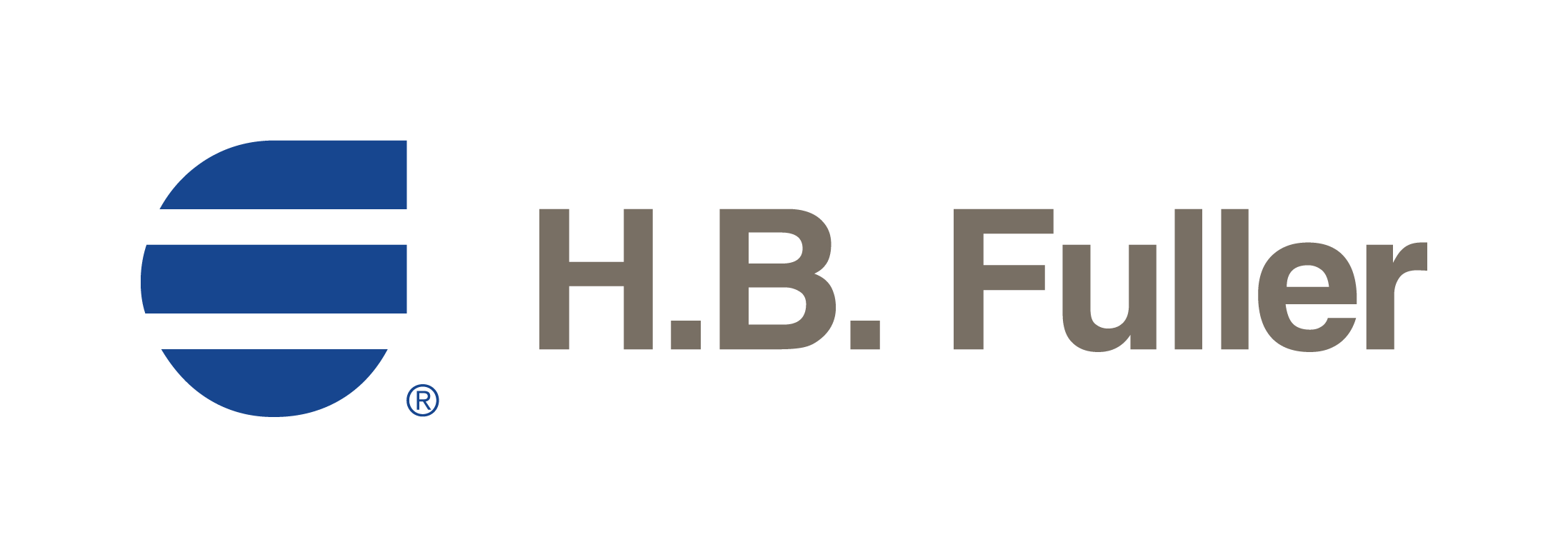
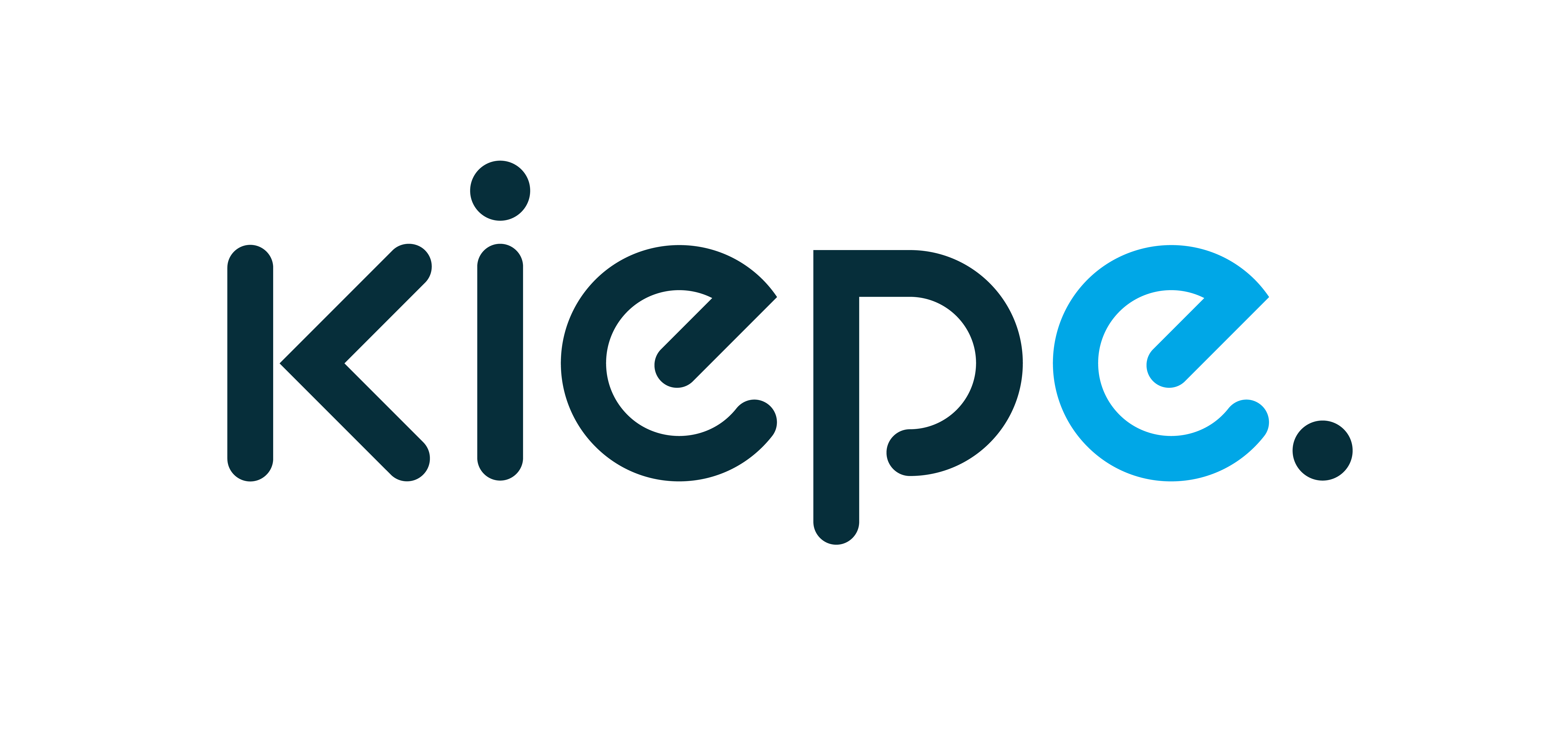
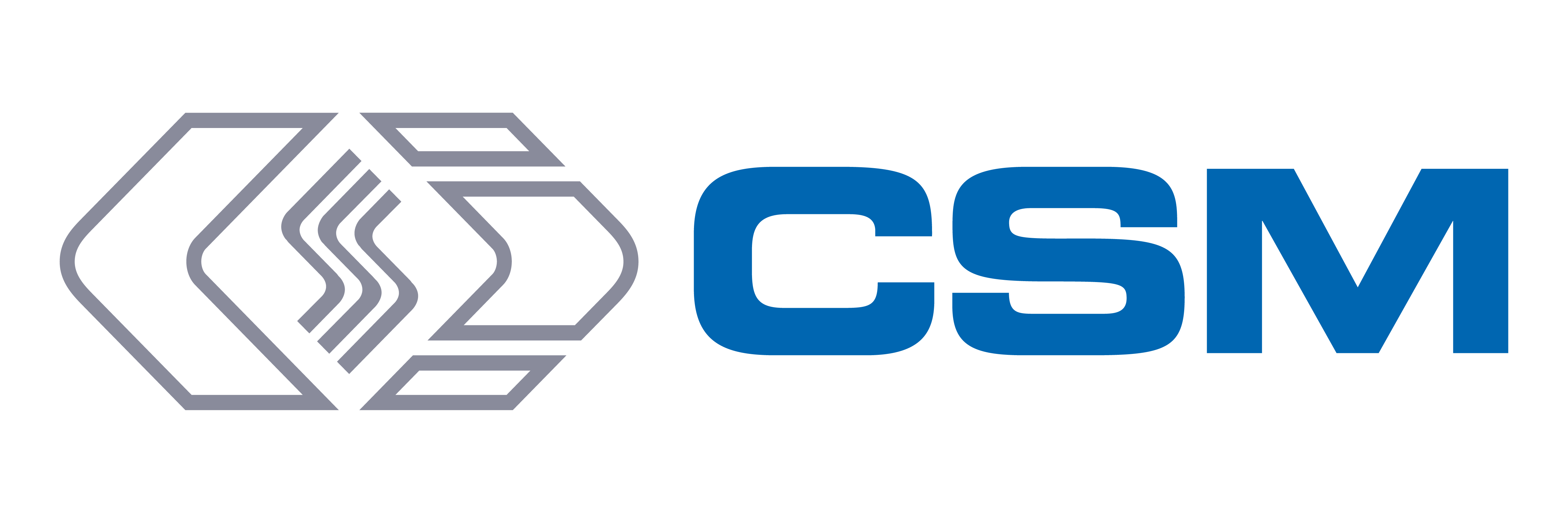