Far-UK shows carbon fibre skateboard EV chassis
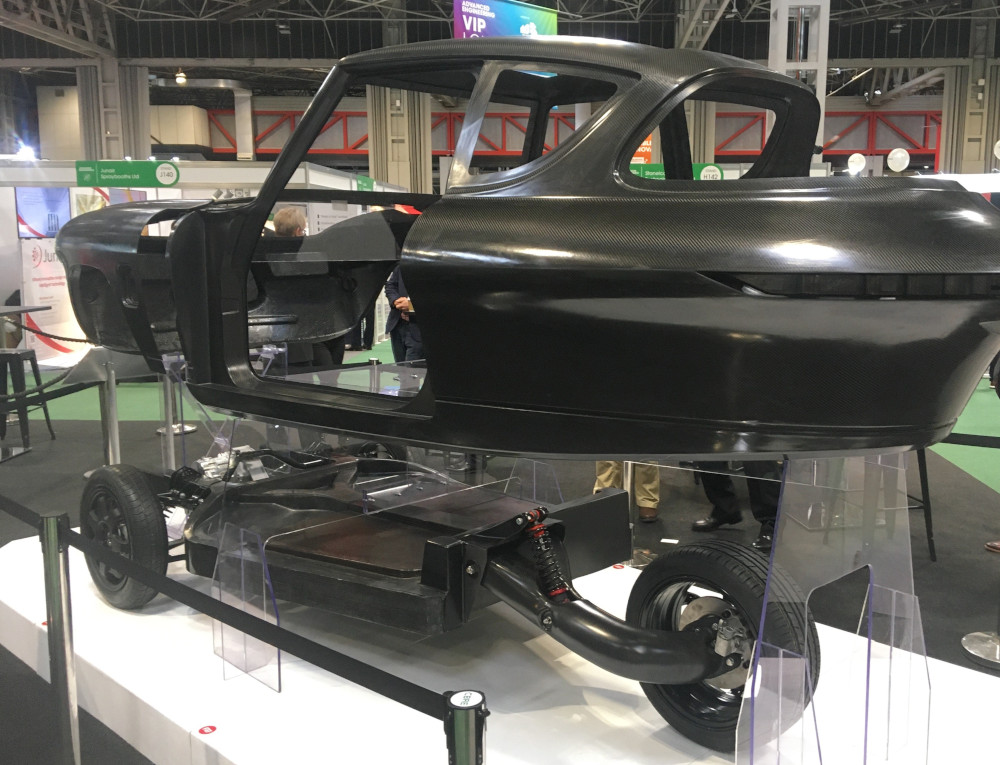
(Photos by the author)
UK composite construction specialist Far-UK is developing a primarily carbon fibre skateboard chassis concept that can be applied to light vehicles with different configurations of wheelbase, track and either three or four wheels (writes Peter Donaldson).
The platform is designed to help reduce barriers to entry for new vehicles by optimising the cost and time associated with developing automotive transport intended for low to medium production volumes. Aimed at passenger vehicles in the L5 to L7 and M1 classes up to 1200 kg gross vehicle weight, the chassis will provide the primary structure for small cars, with the emphasis on economy and efficiency, according to David Goodwin, Far UK’s engineering manager.
One of these is the Nobe Cars 100 GT battery-electric coupe, a three-wheeled, two-seat vehicle styled to recall some of the most attractive designs of the 1960s. Far-UK displayed the chassis with a Nobe body suspended above it at the Advanced Engineering show at the NEC in Birmingham last November.
Far-UK worked with Nobe on prototype vehicles, designing and making the chassis as well as managing the structure builds at its facility in Nottingham, England. Several UK suppliers contributed to the project, and one of which, KS Composites, produced the carbon fibre bodywork that was on display.
Far-UK anticipates body-on-frame construction being the way forward for these vehicles as production ramps up. Goodwin explains, “The first vehicles had a monocoque construction, which for the first few gives you a very good structure, quite cost-effectively. However you can’t scale up the production and retain cost-effectiveness.
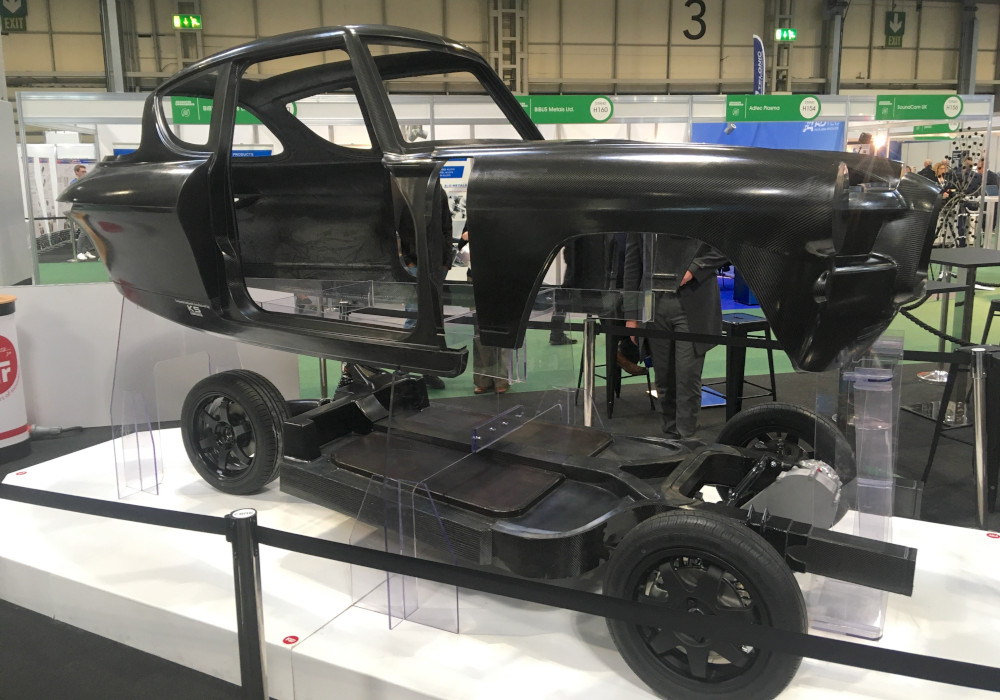
“With this new approach, the chassis is made up of several beams that are then joined together with adhesive bonds to form the structure. That means you can make up each beam in a separate flow or cell and then bring them together, so it allows us to decrease the overall takt time and manage the total cost.”
Starting at the front, the chassis has Far-UK’s polymer composite crush cans; in the example at the show, the reinforcing fibre was made entirely of carbon. The company also makes them in aluminium and with a carbon fibre composite-aluminium hybrid to meet the performance, mass and cost requirements, Goodwin notes.
The crush can material used is a prepreg carbon fibre/epoxy system. “We spent a lot of time developing how those cans behave on impact, so we can tune them now for different vehicle weights and get very predictable behaviour,” Goodwin says.
To the rear of the crush cans is the steel subframe that houses the steering, suspension, braking, motor and transmission. Far-UK refers to this as its front-end module, which it also plans to offer as a developed and tested standalone subsystem that vehicle manufacturers can integrate into their own products.
The unit on display was a mock-up, and Far-UK is working with LSCP and 3J Driveline to productionise the module through the EV Mode project, which is part-funded by the Niche Vehicle Network. “It lets new market entrants get out there quicker and for less initial outlay,” Goodwin says.
After the subframe come the two “fairly traditional sills” that run down the sides, carrying structural loads and protecting the battery pack from impacts. There is also a central box beam that bifurcates to meet the crush cans at the front and serves as a load path that goes down the middle of the chassis.
“The advantage with this construction, with several individual beams bonded together, means we can slightly alter the load path for different vehicles and vehicle weights to get it to perform how we need it to, whether it is in a crash or for torsional or bending stiffness,” Goodwin says.
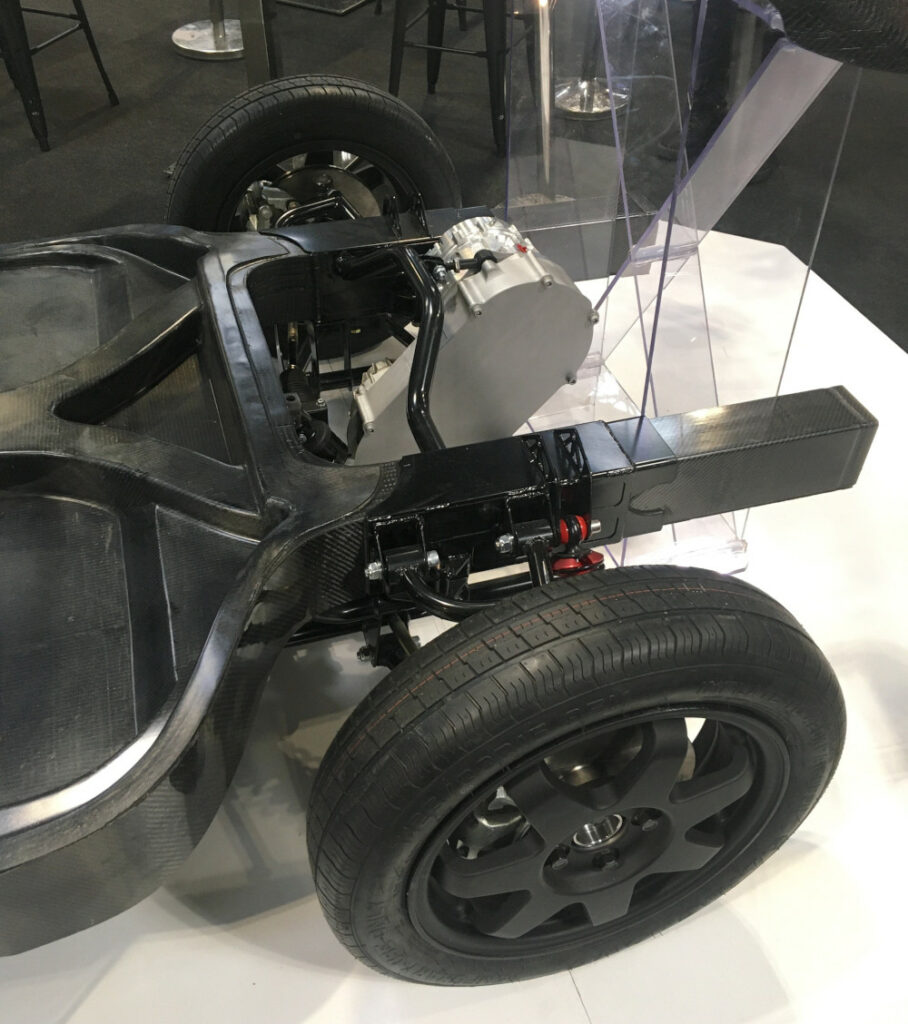
Two panels positioned between the central beam and the sills on either side form both the floor of the vehicle and the lid of the battery box. The material here is a polyfurfuryl alcohol (PFA)-based resin reinforced with glass fibre. PFA is a bio-resin derived from sugar cane and has inherent fire-resistant properties.
The structure terminates at the rear in a carbon-fibre composite plate that meets the central box beam, the sills and the mounts for the single-sided swing arm that suspends the rear wheel, and its mono-shock spring and damper unit. This arm is a large-diameter carbon fibre composite tube that curves round to meet the wheel hub.
The body is attached to the chassis with an intermediate supporting structure, also made from carbon fibre composite. This bolts up to the chassis, sharing some of the fixture points with the battery box. “Basically we bring the space frame structure from above and the battery from below, and bolt through common holes,” Goodwin says.
In the front subframe module is the powertrain, which consists of a new e-motor coupled to a simple continuously variable transmission. “It is a very small package, which helps in this sort of vehicle, but it also means the motor runs at its optimal speed more often,” Goodwin says.
“That has allowed us to downsize the motor, and we have some calculations that show it will improve range, although we have yet to evaluate that in the real world. The literature cites between 5 and 7%, and by pushing it a bit more in a lighter vehicle we hope to get 10%.
“The motor itself weighs only 13 kg. We don’t know the exact weight of the gearbox yet, but it should be similar. That’s all coming in over the next 6 to 9 months, when we will have developed the package and can start testing it on the road.”
ONLINE PARTNERS
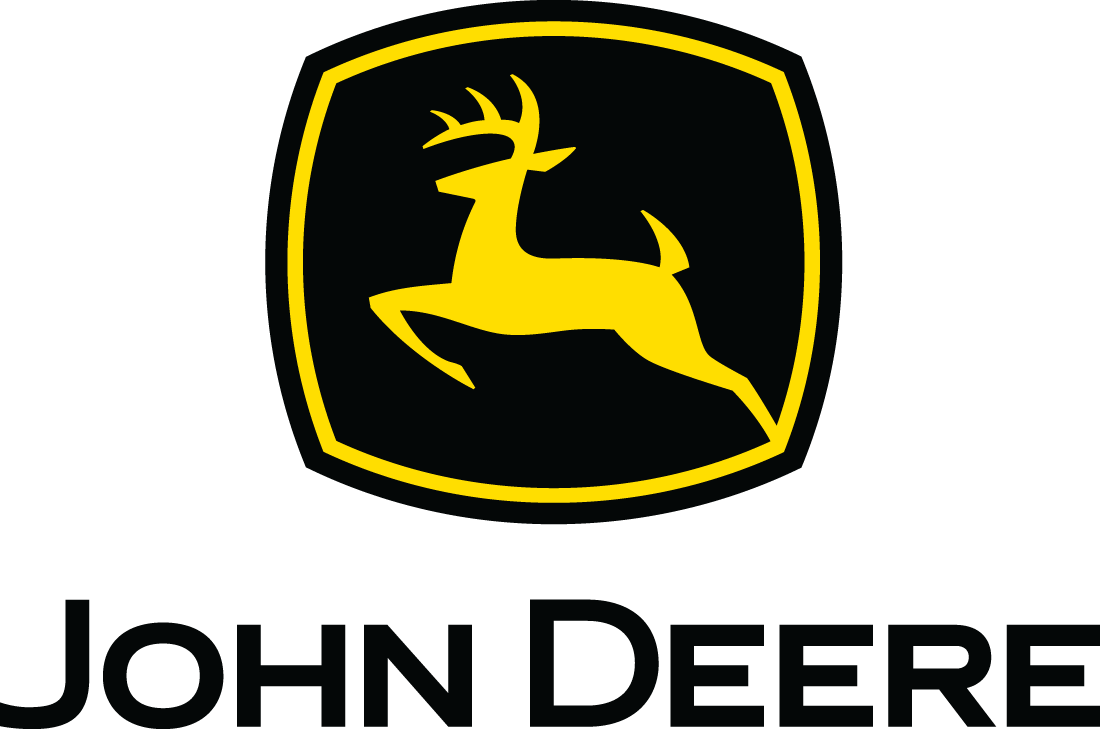
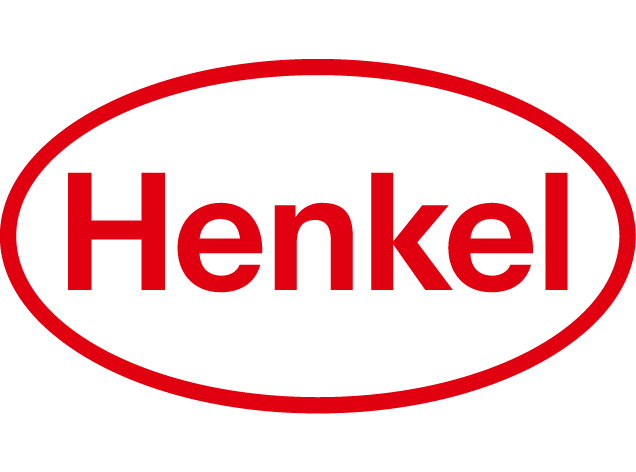
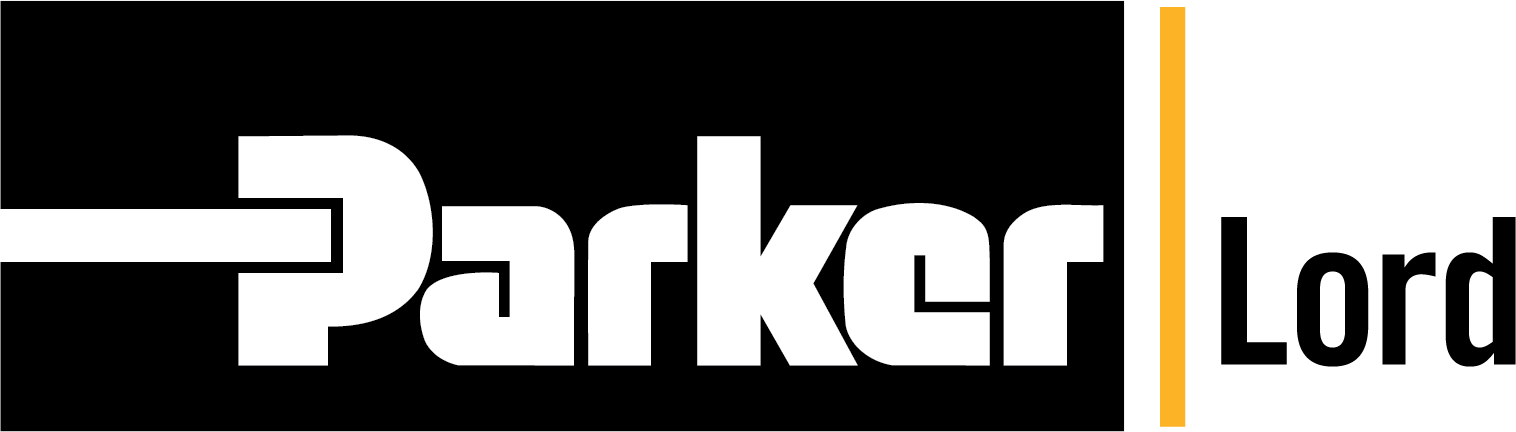
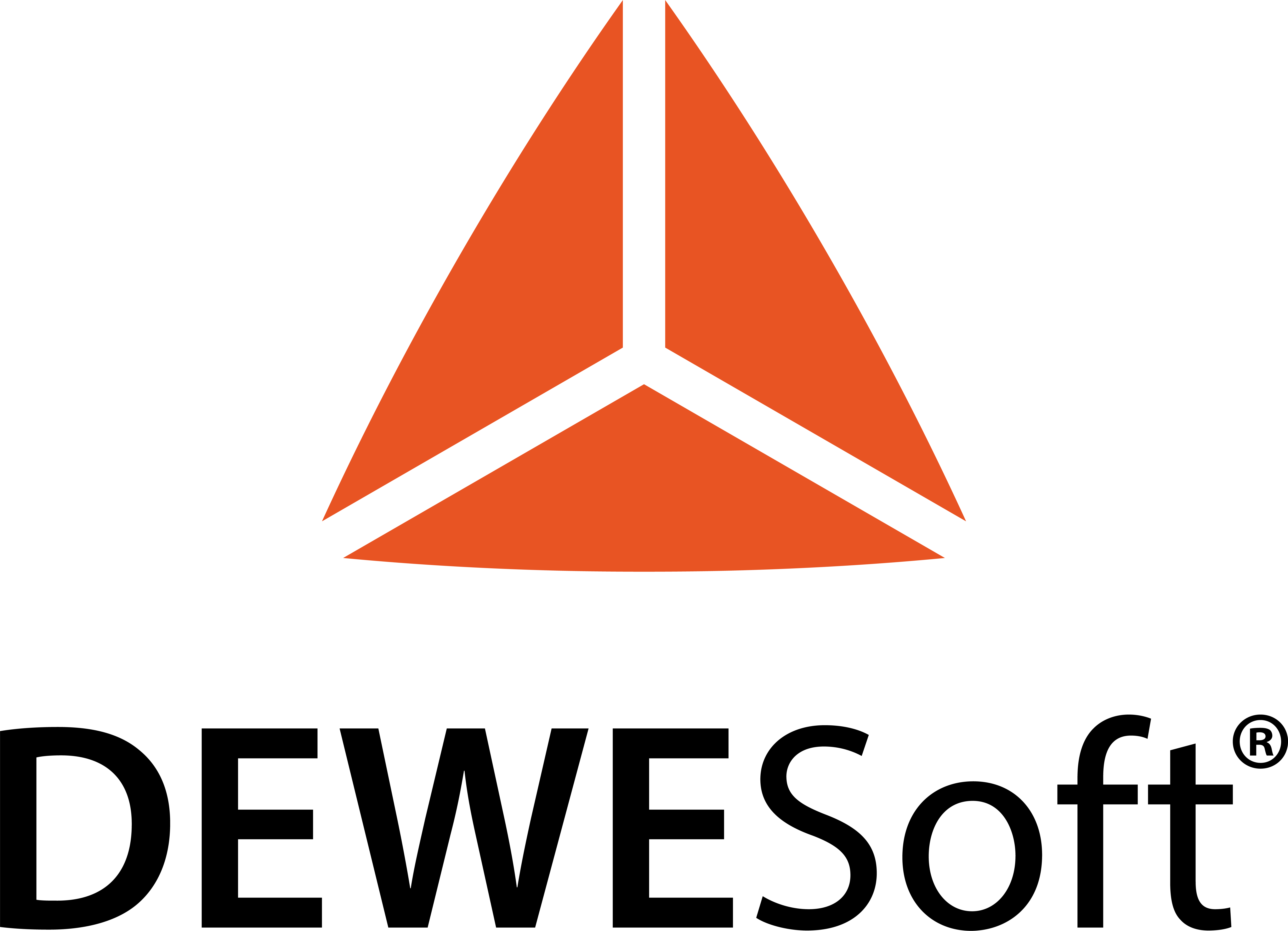
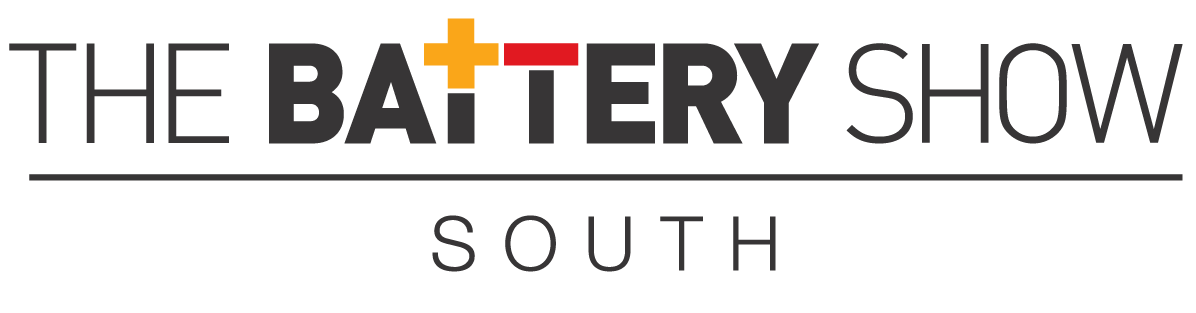
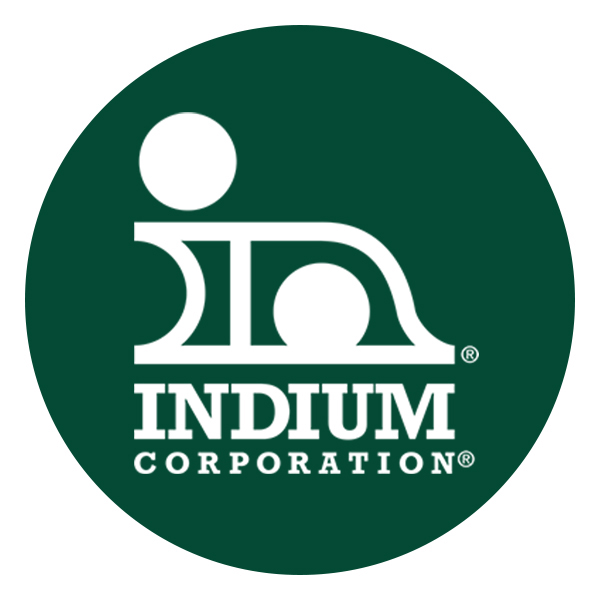
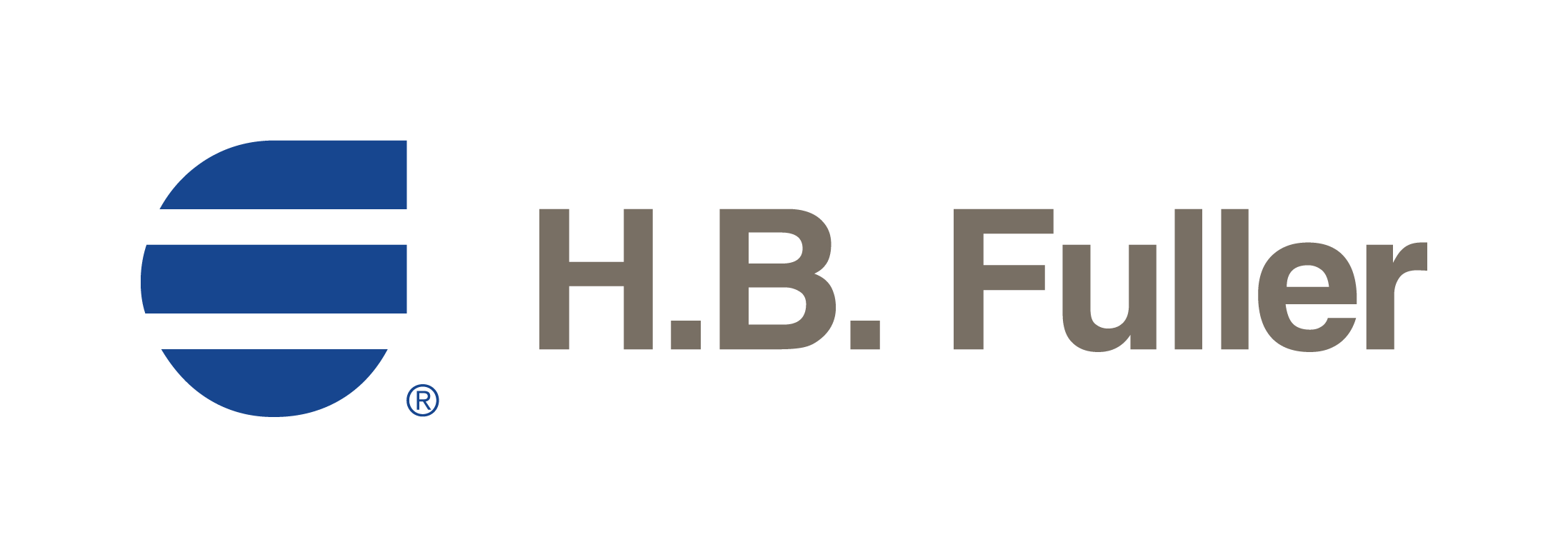