EVIE Street Sweeper
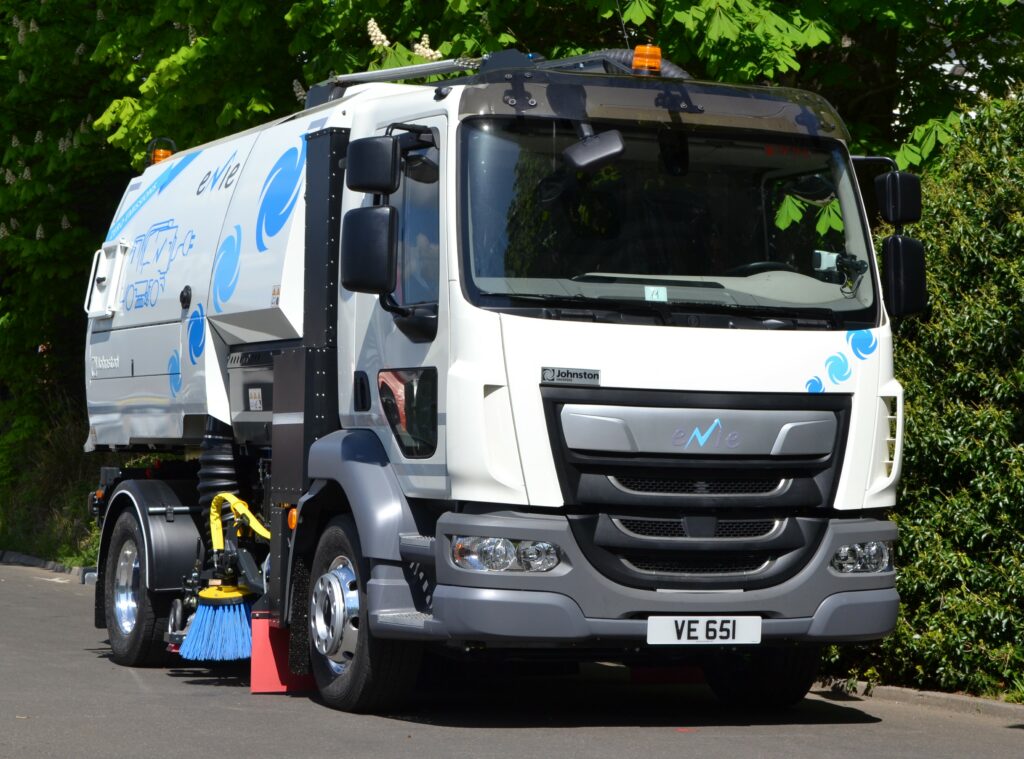
Clean bill of health
Rory Jackson explains what went into developing this battery powered road sweeper.
Integrating a zero-emissions powertrain into a street-sweeper. vehicle makes sense for a number of reasons. The principal purpose of such vehicles – to maintain a clean environment in cities and towns, without leaving pollutants behind – should be reason enough. From that perspective alone, the cleaner the streets, the better the investment.
There is also a growing regulatory impetus, as reflected in the increasing number of ultra-low and zero-emissions zones in large municipalities. Electric street-sweepers therefore look to be a perfect fit for sanitation departments aiming for compliance with stricter emissions laws and zones.
To that end, UK company Johnston Sweepers has developed the Electric Vehicle Intelligent Electronics, or EVIE, system.
A typical sweeper vehicle – in the UK at least – has two diesel engines. One serves as the main drive system, while the other is an auxiliary engine for onboard systems.
Although these provide considerable power for the traction, sweeping brushes, vacuum and other onboard systems, they also produce emissions as the sweeper travels, often slowly and close to pedestrians.
“In that instance, we think an electric powertrain coupled with an air sweeper is a very good way to improve local emissions, as well as air quality,” says Gareth Knopp, innovation and simulation manager of sweeper trucks. He led the EVIE’s development at Johnston Sweepers’ parent company Bucher Municipal, which shares an engineering department with Johnston.
“An air sweeper entrains particulate matters such as PM2.5 and PM10 from the road so you can pick them up,” he says. These are classes of particulates measuring between 2.5 and 10 μm in diameter, which can cause heart disease, cancer and other serious medical conditions.
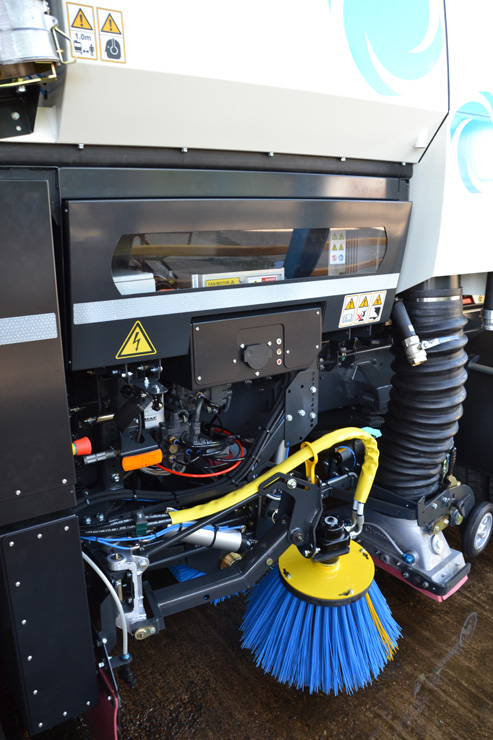
Power and other systems
Rather than two diesel engines, the EVIE is powered by a lithium iron phosphate (LiFePO4) rechargeable energy storage system rated to 600 V with 200 kWh of usable energy.
This battery chemistry was selected partly to assuage fears stakeholders might have over the safety of electric power, as lithium iron phosphate is far less likely to go into thermal runaway than other battery types such as lithium nickel manganese cobalt oxide.
“It’s also proven technology. We have people who’ve been working with these batteries for some time, and amassed data through cycling and testing the lifespan of the batteries,” Knopp adds.
This battery chemistry was also selected for its long-term stability – it is rated for a lifespan of 3000 charges – and for its low toxicity. Although the battery voltage is rated at 600 V, the actual nominal figure is 576 V, as the overall energy storage uses 48, 12 V cells.
The batteries are also arranged into what is effectively two packs of 24 modules, connected through the battery management system (BMS).
Rather than being connected distinctly in series or parallel, the packs are operated in series (via a masterslave arrangement in the BMS) but charged in parallel, using two 22 kW chargers. The cells then balance themselves when reconnected together after charging.
“We’ve designed the battery pack and its architecture in this way, and also to fit it in the middle of the EVIE. Every other truck manufacturer or e-truck conversion company installs the big ‘coffin’ batteries down the side of the chassis, but that’s where we need to have all our sweeping gear,” Knopp explains.
“So those designs wouldn’t work for us, and even though several companies are developing solutions at the moment for electric trucks, they’re still not going to be suitable for our application.”
The battery configuration also allows more flexibility in terms of the power supply for charging, as they can be treated as two 288 V packs. They can therefore be charged with a 400 V charger, whereas, as Knopp explains, “If they were connected in series all the time, you’d have to use an 800 V charger, because of course you have to put in a voltage that’s higher than the battery’s nominal voltage.”
If a module is damaged and needs to be replaced, the remaining cells will continue to power the various electric motors and other systems throughout the vehicle in the meantime.
The EVIE has two brushes – one on either side, typically made from polymer or steel tines. These sweep debris out of the kerbs, corners and crevices of the road, and place it in front of two vacuum nozzles (with one sitting behind each brush) which then convey it into the hopper (the onboard container for dust and debris). The suction for vacuuming this debris is generated by a backwards-curved centrifugal fan, powered by a Phi Power motor.
The sweeper’s traction drive uses a Sumo HD HV3500-9P electric motor from propulsion system developer TM4. This liquid-cooled permanent magnet motor has a peak power rating of 350 kW and a peak torque of 3500 Nm (2581 lb-ft). It comes with a nine-phase inverter and runs on a propshaft to a 6.33:1 rear axle.
In addition, another motor runs an air-conditioning compressor, another runs an air compressor for the brakes and lifting and lowering the brushes on the truck, while there is another for the steering (with a 24 V back-up steering motor). Two other motors drive the hydraulic pumps that spin the sweeper brushes, making a total of eight.
“The chassis is a standard DAF LF,” says Knopp. “We removed the engine, the drivetrain, the transmission and most of the rest of the powertrain, but kept the propshaft and the rear axle.”
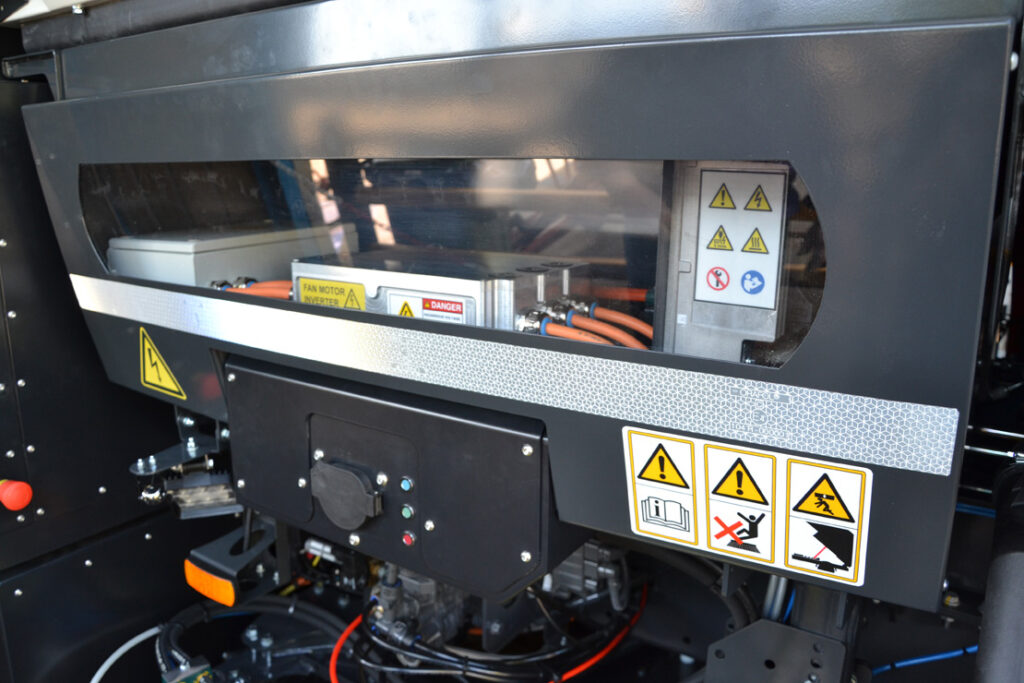
Initial vehicle checks
An electric powertrain naturally needs less maintenance than one with an ICE. The EVIE has two 22 kW chargers integrated that require a three-phase power supply.
Aside from ensuring there is a suitable charging source, most of the safety and operational checks for the EVIE are common to all sweeper trucks, such as checking the tyres and that the warning lights are working. As the traction motor is liquid-cooled, the operator also has to check the level of fluid (a 40/60 water-glycol mixture) and top it up if necessary.
Once a month, the battery packs need to be discharged to between 10% and 15% capacity, and then fully recharged to 100%. This helps to preserve the battery’s lifespan and recalibrate the system to correctly calculate the state of charge.
“There are no filters to change, no air filters to check; the only other thing you really need to do is make sure it is charged overnight so that you have enough power for the day,” Knopp comments.
Johnston Sweepers EVIE specifications
Vehicle weight: 16 tonnes
Battery energy: 230 kWh
Battery voltage: 576 V
Charging cycles: 3000
Charge time: up to five hours on a 415 V AC three-phase connector; up to 63 A, 44 kW, or up to 10 hours on a Category 2 AC connector up to 22 kW
Maximum road speed: 80 kph
Operating speed: 8 kph
Payload capacity: 6 tonnes
Water capacity: 1.5 tonnes
With a 200 kWh capacity for the batteries, and a 44 kW charger, it usually takes between four and five hours to recharge fully, with roughly half-an-hour after that for the cells to balance, meaning about five to fiveand-a-half hours’ maximum charge time.
“That assumes you have a 63 A supply, for which we offer a cable option,” Knopp says. “Basically it’s the highest current you can carry before you have to use some kind of cooling for the cable. If you already have a 415 V three-phase supply in your factory or workshop, you’re literally just plugging in another piece of equipment to charge the EVIE.”
The two-pack arrangement also means a 32 A cable can be used, although that will double the maximum charge time to between eight and nine hours.
In operation
The powertrain gives the vehicle a maximum speed of about 95 kph/ 60 mph (where the law allows). In urban zones and similar, the EVIE typically consumes an average of less than 1 kWh/km, although the exact figure naturally varies as the vehicle accelerates and decelerates.
“With an average load, and doing an urban and extra-urban cycle, the vehicle will use that sort of power,” Knopp says. “It really depends on how you’ve adjusted the settings of the vehicle and how you use it.”
As mentioned, one of the onboard electric motors powers a hydraulic pump. It drives the hydraulics for EVIE’s sweeper brushes, which spin at up to 120 rpm depending on the amount of debris to be collected.
“The key to effective sweeper brush operation is high torque but low speed,” Knopp explains. “We need something up to 60-70 Nm of torque per brush. For that, we need to find a suitable high-torque, low-weight and affordable motor, with something like an IP69k protection rating.
There is another motor driving the low-pressure water pump, which helps to suppress dust at the brushes and lubricates the nozzle and inlet tubes.
Pneumatics are used to lift and lower the brushes to street level. As the brushes spin, they drive the swept particles into the inlet nozzles that sit just behind them, the particles being sucked in by the air drawn from the motor driving the centrifugal vacuum fan.
Additional sprays of water from a clean-water tank pump spray about the vacuum nozzles to help suppress any dust. That helps stray dust and debris to congeal into larger particles, to stop them floating through the air and to make them easier for vacuuming into the nozzles.
“We have about 1500 litres, or 1.5 tonnes, of water on the truck to begin with,” Knopp adds.
During this sweeping operation, the 16-tonne EVIE travels at a rough average of 8 kph (2.22 m/s). At that speed, the traction motor consumes about 6-8 kW, depending on the load on the vehicle such as the amount of debris collected and the water remaining.
These figures will vary further depending on the amount of visible dirt and debris to be cleared. If the EVIE is being used to pick up non-visible particulate matter then more than 8 kph could be suitable, but if there is a lot of consumer waste or fallen leaves for example, 8 kph might be the maximum to ensure effective cleaning.
Motor control
Typically the vacuum fan motor runs at between 70% and 75% of its maximum revs – between 2450 and 2625 rpm, out of a maximum of 3500 – which is suitable for sucking up most particulates. Alternatively, an EVIE’s driver can use a ‘boost mode’ if there is a lot of heavier debris.
“While we’ve typically operated the vacuum motor on a speed-control basis, we’re trying to move towards a more torque-oriented system of control, to make the sweeping more intelligent in terms of how efficiently and optimally it can pick up larger debris,” Knopp says.
“We’ve done a lot of CFD modelling of the vehicles in order to infer what the airflow is like at varying rpm levels and torques from the different motors.
“It’s similar to the 3D fuel maps you can construct for running an ICE powertrain, but showing airflow pressure and torque instead. From there, we hope to optimise the system for the kind of torques and revs we might be asked to provide.”
That means the driver should eventually be able to select a fixed torque at which to run the fans, with the rpm changing by virtue of that torque, rather than the closed-loop speed control method used at the moment.
The vacuum fan at maximum draws around 55 kW, compared to 75 kW on a typical sweeper, with no loss of vacuum power.
The company hopes to reduce that further, to potentially 35 kW or less in the near future, with further CFD modelling to optimise the airflow and mechanical processes to save power and thus extend operation time between charges.
“Most of the power draw comes from the vacuum fan, and we’re looking to get the average use down to between 25 and 50 kW,” comments Knopp.
“That could mean between four and six hours’ sweeping time, with the endgoal being an eight-hour uninterrupted shift.
“We’re using data from 30 municipalities across the UK, to create a picture of how the street sweepers are actually used. That will enable us to optimise the vehicle’s settings to make them as energy-efficient as possible.”
Once drawn into the vacuum head, dust and debris are sucked up a vertical shaft and deposited in the EVIE’s hopper bin, which can collect up to 6 tonnes of waste before needing to unload it in a designated area such as a local tip.
A typical day’s work for the EVIE would consist of roughly 65-80 km of travel, particularly in municipal areas. After emptying its last load into a refuse tip, the EVIE might then return to its original depot, or it might finish at a different one to make deployment easier for the next day’s operation.
The EVIE is of course cleaned at the end of its day’s work.
“Because of the batteries and all the electrical systems we’ve integrated, we’ve made sure to design the most effective ingress protection systems we can – IP69k where possible – because we recommend the use of a highpressure hand lance to wash the EVIE down,” Knopp notes.
The future
The EVIE’s driver has a wide array of electrical, hydraulic, and pneumatic systems to consider, as well as several variables and screens to draw their attention. To ease the cognitive burden on the driver, Bucher is looking into autonomy capabilities as well as the aforementioned efficiency improvements in the airflow and mechanics.
“These autonomous functions might use some kind of image recognition at the front of the EVIE, which will enable an onboard computer to make intelligent determinations,” suggests Knopp.
“For example, if the EVIE identifies a certain kind of rubbish at a certain distance ahead, and it’s travelling at 0.5 m/s, it could feed that back into the power management and control systems to allocate the power for the brushes, the vacuum and the traction motor, to optimise the power drawn by each part.”
For the past 18 months, each EVIE system (of which there are about 1200) has been fitted with a telematics system and logging device. These have enabled usage information to be collected, and optimise the vehicle design and begin planning future autonomous capabilities.
“We can also combine the variables on the speed and power draw of the various motors and pumps with open data resources to determine the optimum routes according to the weather, traffic levels and road inclines, to enable longer endurance,” Knopp says.
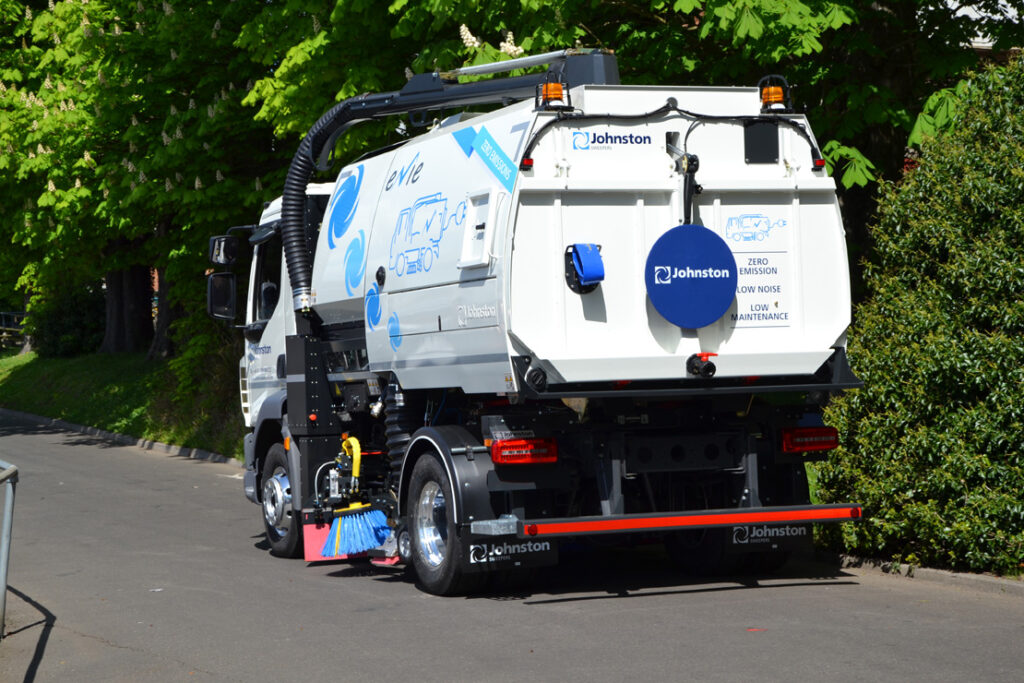
With a close eye on advancements in intelligence and efficiency, the EVIE is clearly heading towards providing cleaner and smarter city streets for us all.
Key suppliers
Traction motor and inverter: TM4
Vacuum fan motor: Phi Power
Vehicle chassis: DAF
Onboard charger: BRUSA
Three-phase charging cable: Mennekes
ONLINE PARTNERS
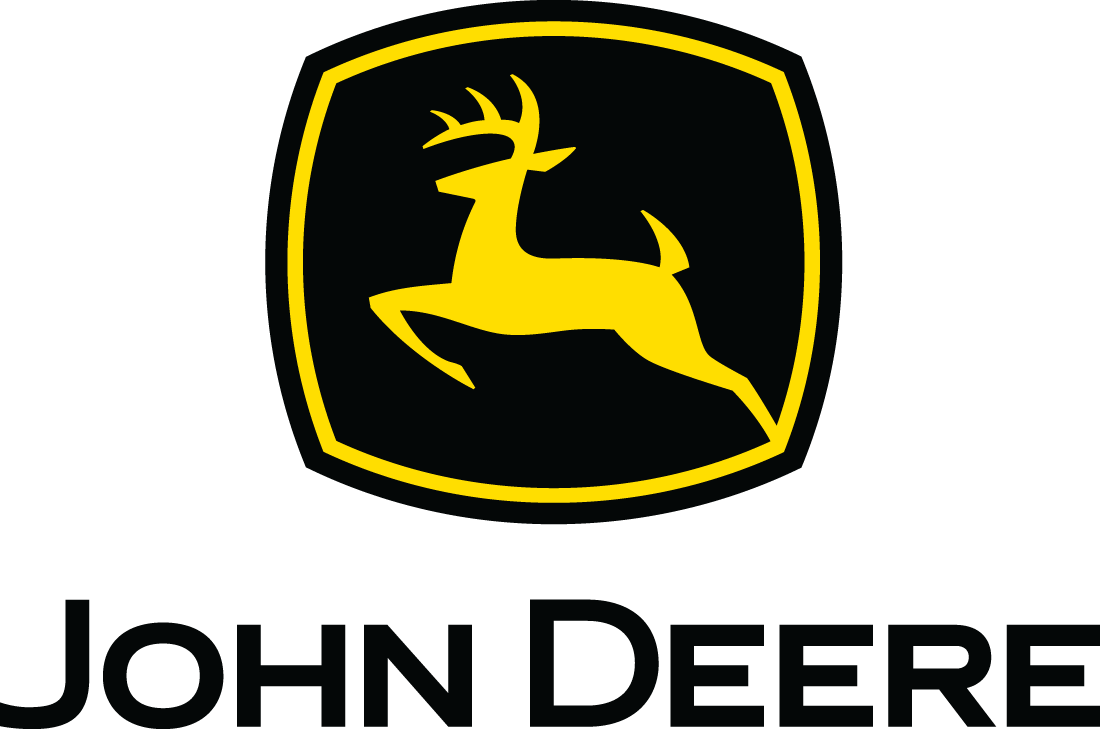
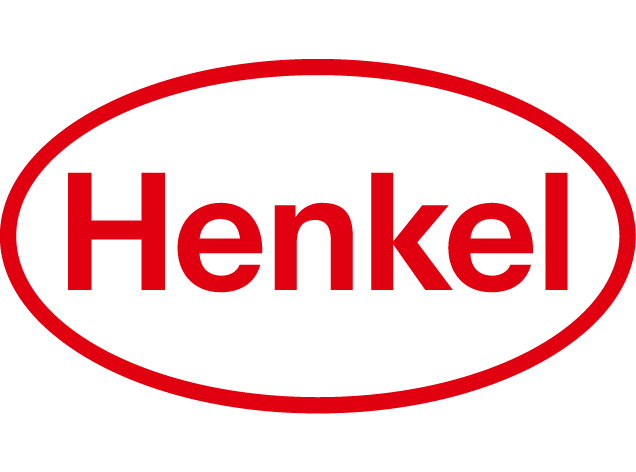
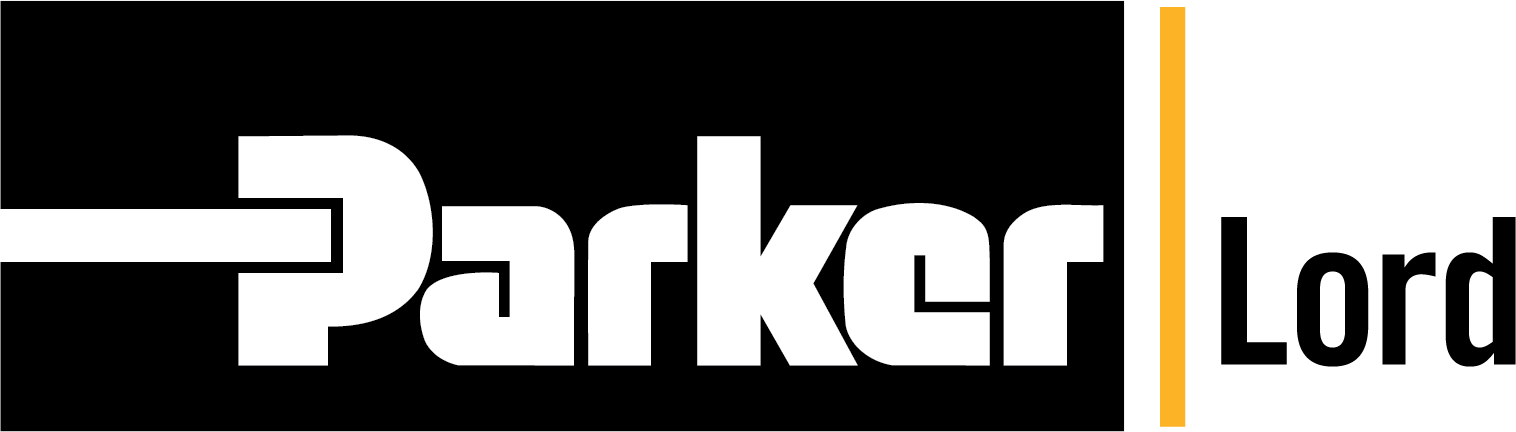
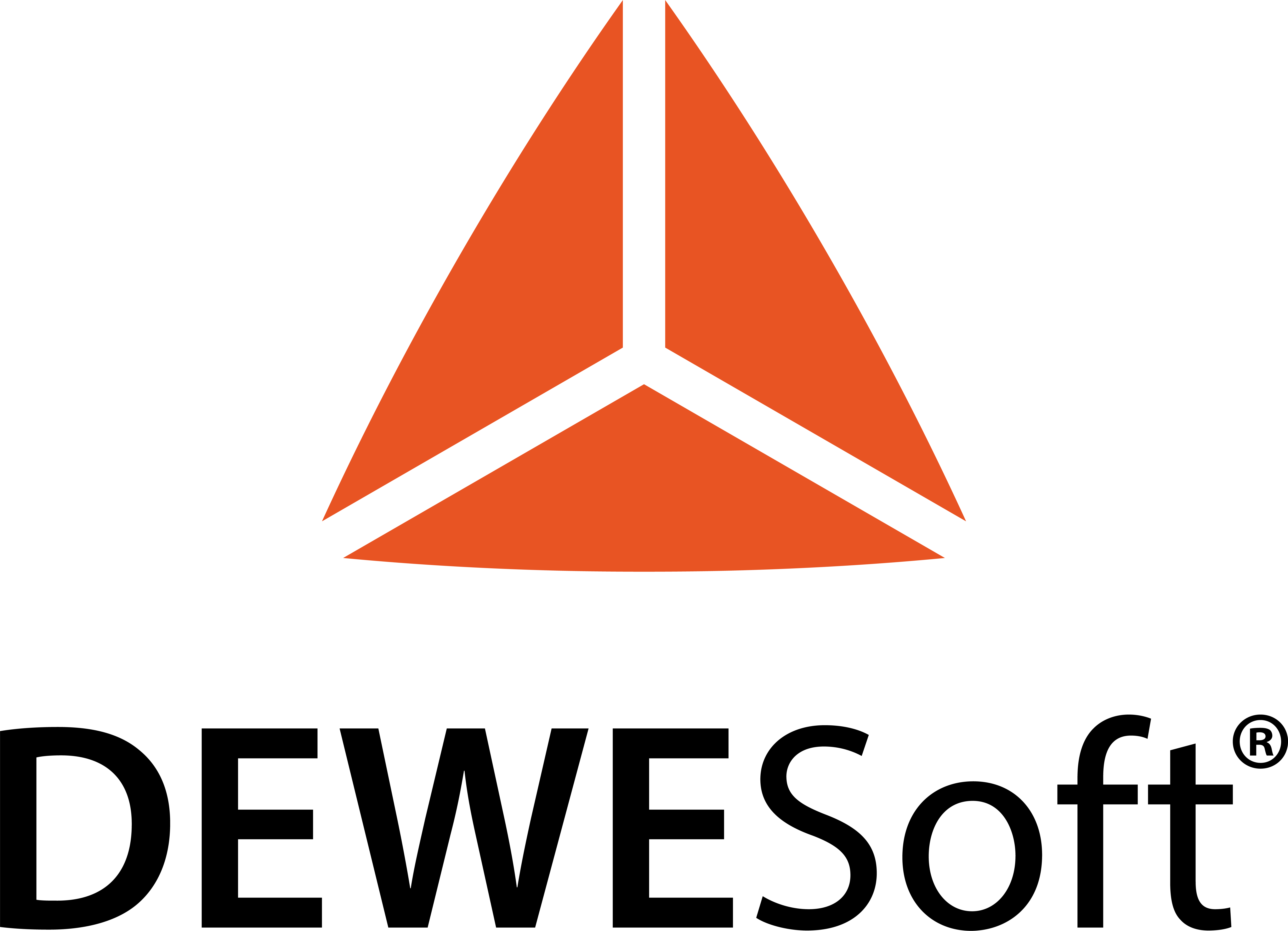
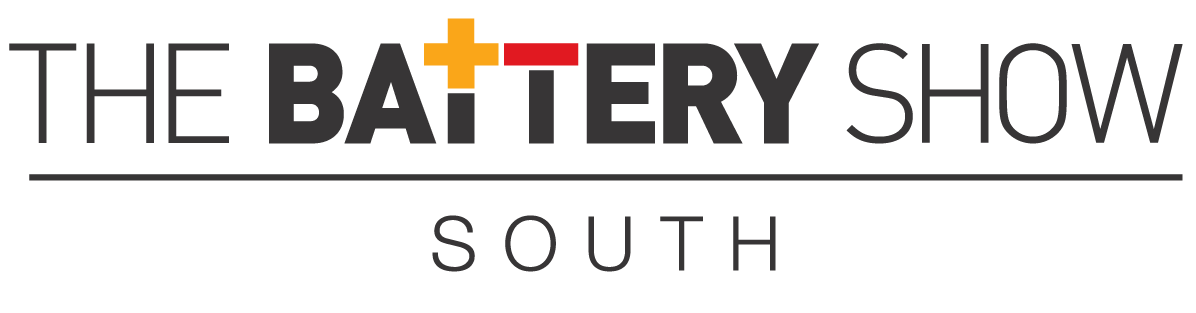
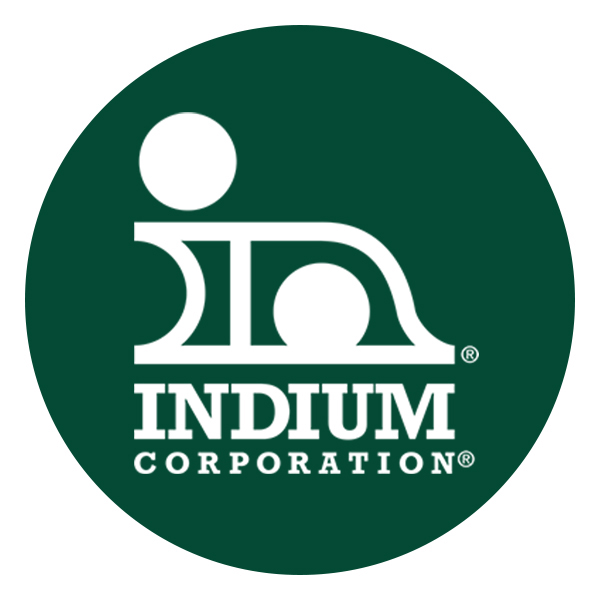

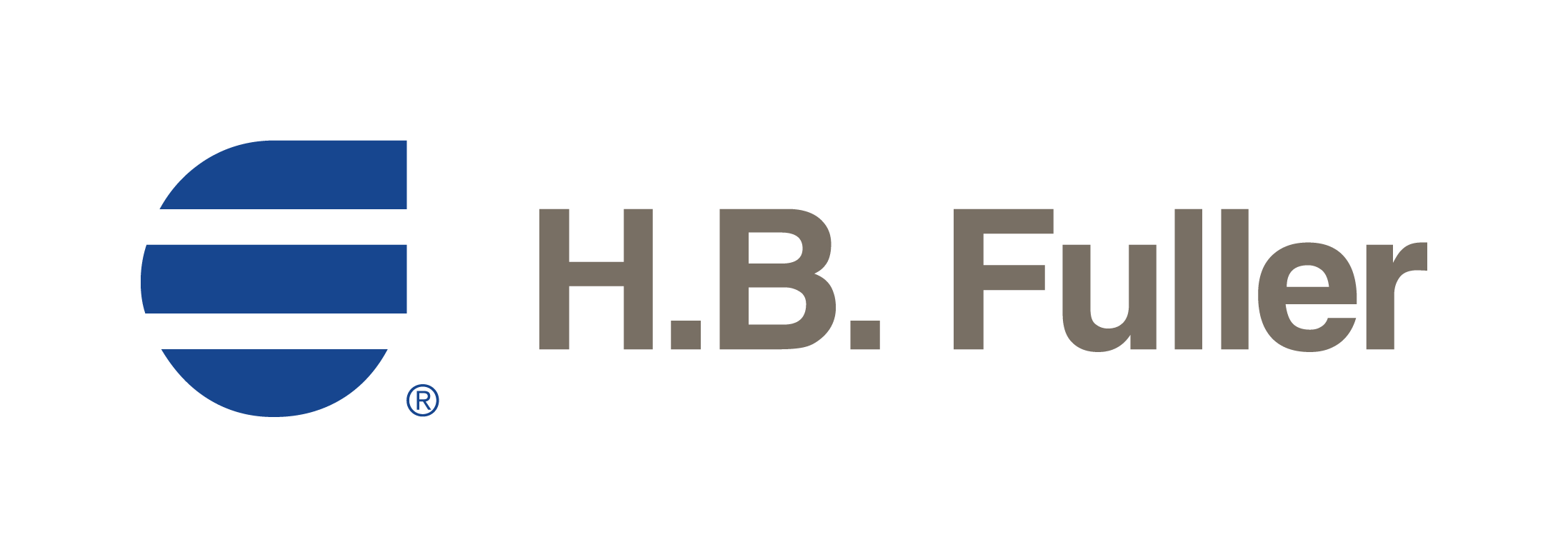
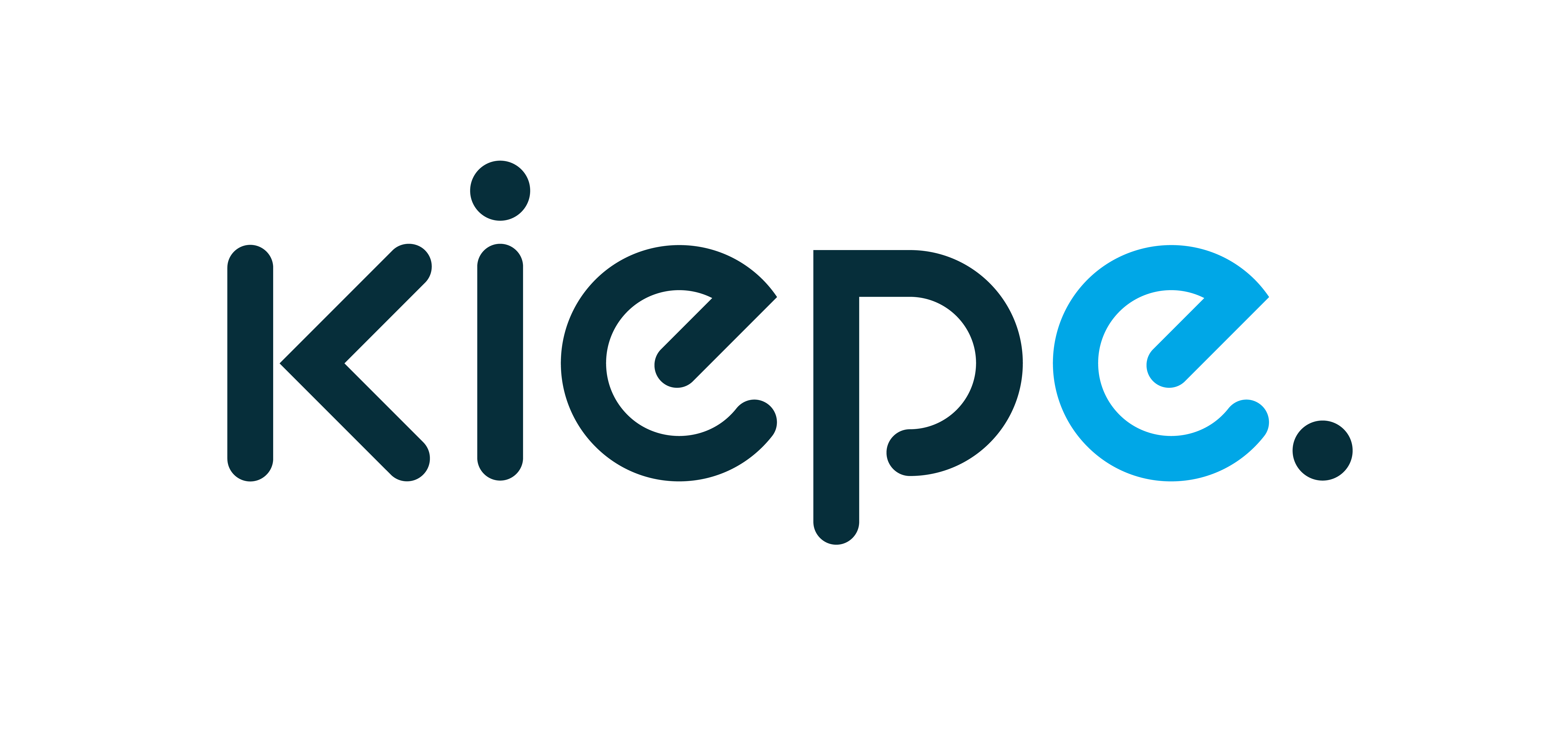
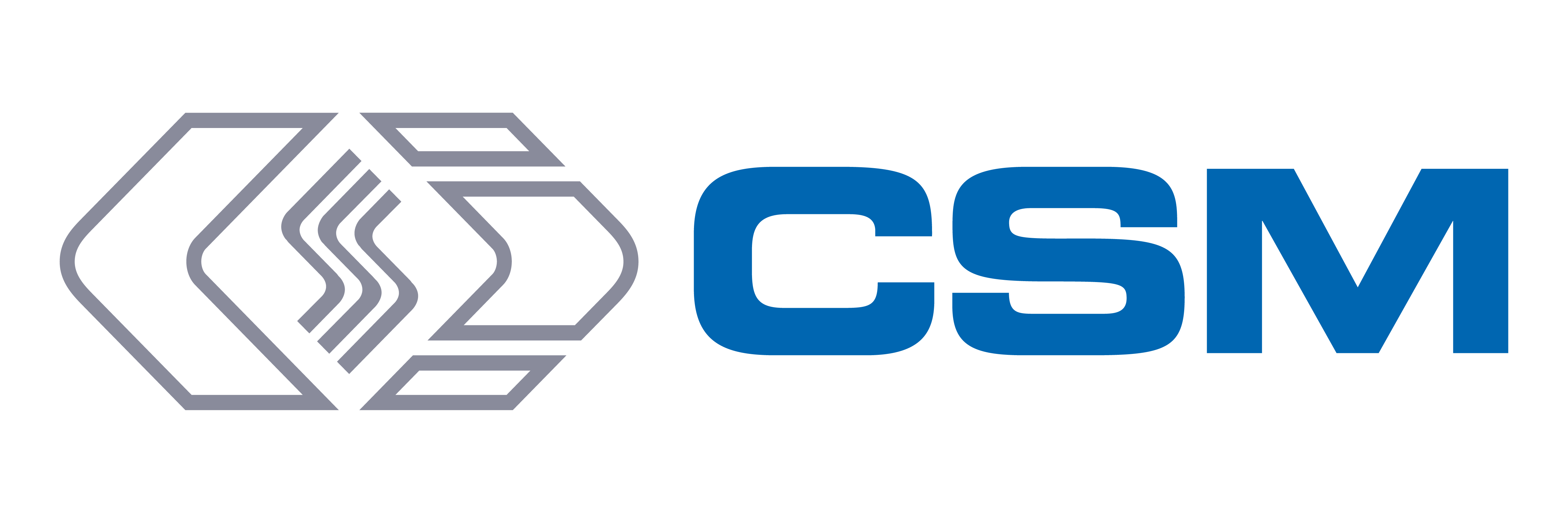