The EV support structure
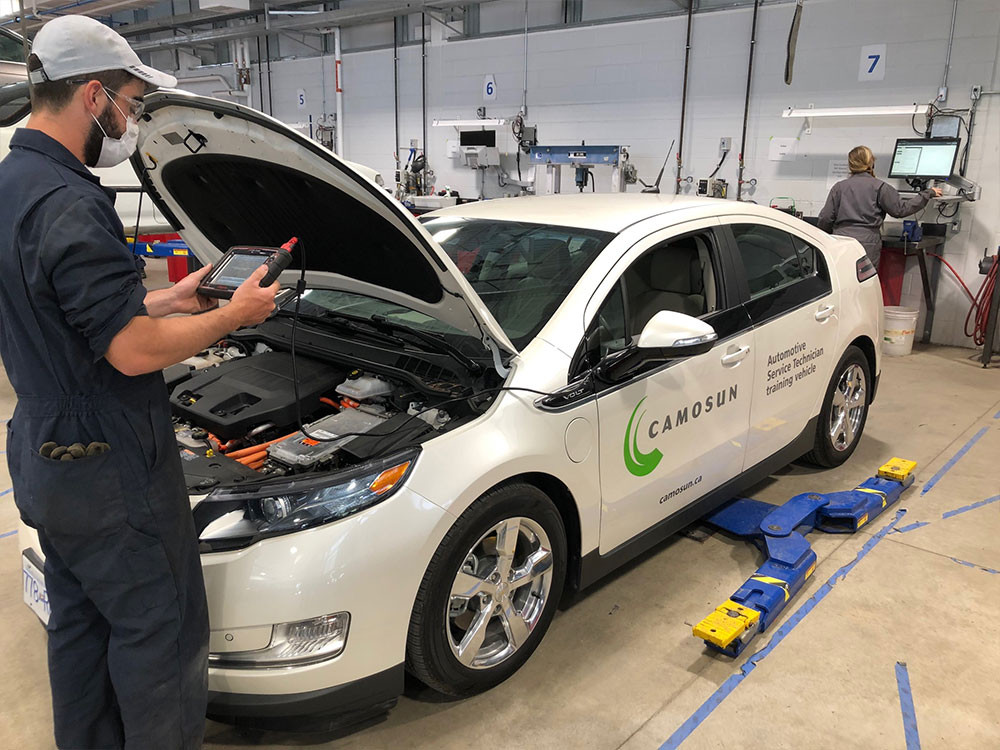
One of the signs of maturity we should look for in BEV technology is the existence of a robust market in used cars, writes Peter Donaldson. Evidence of this would include a good choice of makes and models with prices that, while strong, are significantly lower than new prices, and they reflect age, mileage, service history and overall condition. Underpinning this would be a large network of independent service and repair shops, either marque specialists or generalists able to work on a wide variety of makes and models.
Crucially, they should be able to perform lasting and warrantied repairs to batteries, e-machines, power electronics and computer modules, as well as components such as suspension and brakes common to EVs and ICE vehicles. We are not there yet, however, and there are more than a few obstacles in the way, many caused by policies pursued by vehicle OEMs.
One of these hurdles is access to proprietary software and diagnostic tools. Most EVs rely heavily on software to manage everything from battery performance, health and safety to driving dynamics. And diagnosis often requires specialised and proprietary equipment, access to which is typically restricted. This makes it difficult for independent repair shops to diagnose problems or update software without the OEM’s direct involvement.
Another barrier is access to technical data and information such as service bulletins, wiring diagrams, software updates and other critical information essential for properly servicing a vehicle.
Often, EV manufacturers control the distribution of spares more tightly than traditional vehicle manufacturers do, making it difficult for independents to get the parts they need, and both delaying repairs and increasing their cost, or even forcing customers to go to the official dealership and sidelining independent businesses.
Many EV manufacturers tie warranties and service agreements to the use of their own service centres or those authorised by them, discouraging customers from using independent repair shops. Furthermore, obtaining authorisation from OEMs to become a service centre can be a daunting process for an independent, one that involves significant investment in training, equipment and facilities that many small shops cannot afford.
An EV’s battery is a particularly tightly controlled item, partly because of the risks involved in working with high-energy, high-voltage electrical systems, but also as a means of exerting control. They are often regarded as sealed units, meaning they are not intended to be serviced by anyone other than the manufacturer or its agents, and the costs involved with repair and certainly with replacement are often so high that they put otherwise sound vehicles beyond economical repair. Together, these factors often make it not worthwhile or too financially risky for independents.
The risks involved can also create insurance and liability issues to the point that independents face higher premiums or difficulty obtaining cover.
There is also the issue of expertise. Technicians must be trained in high-voltage batteries, power electronics, BMS and other EV-specific technologies such as e-machines and thermal management, and this can be prohibitively expensive and time-consuming for smaller organisations.
Furthermore, as EV technology, service tools and repair methods continue to evolve, ongoing training to stay up to date is vital, but adds to the burden.
Engineers are coming up with solutions that make batteries easier to repair, such as automated/guided dismantling to de-bondable adhesives, TIMs and sealants, and reworkable potting materials. However, corporate policies decided in boardrooms at C-level must be changed or EVs will come to be seen as disposable items after their first decade or so of life, and that could kill the market for new ones.
ONLINE PARTNERS
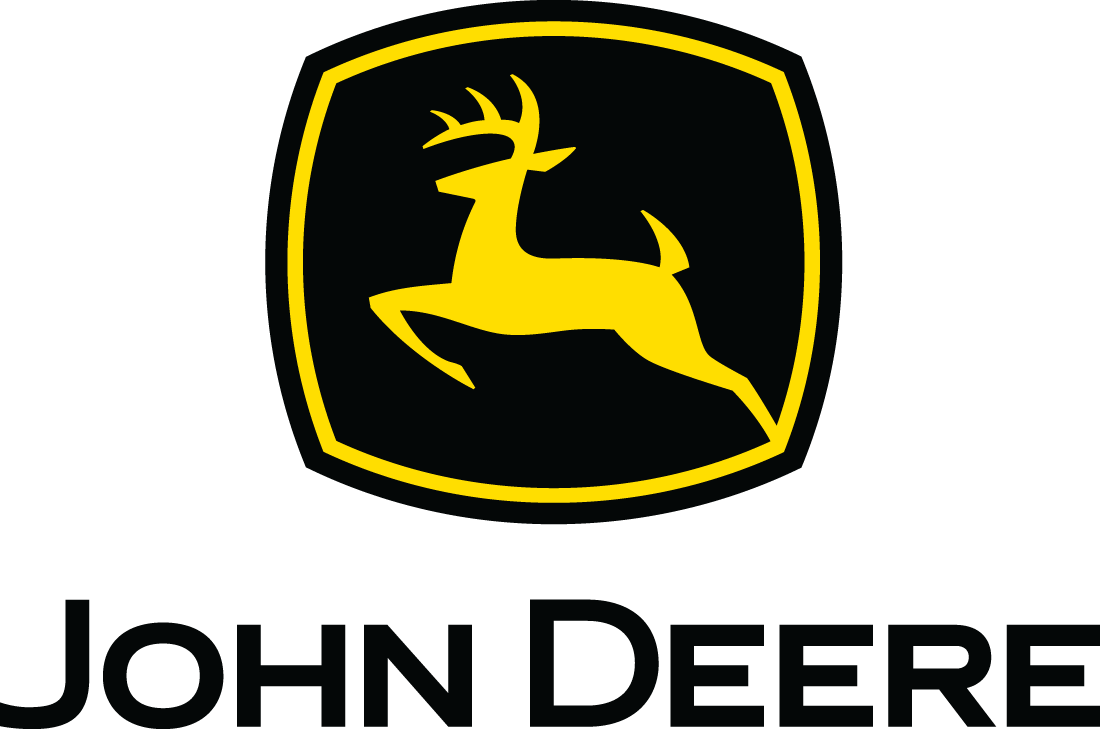
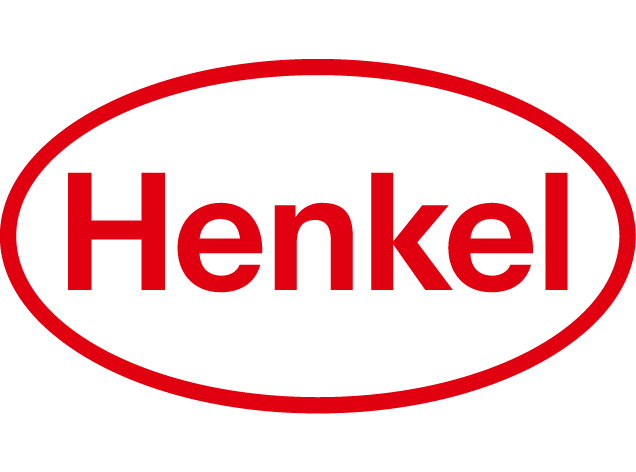
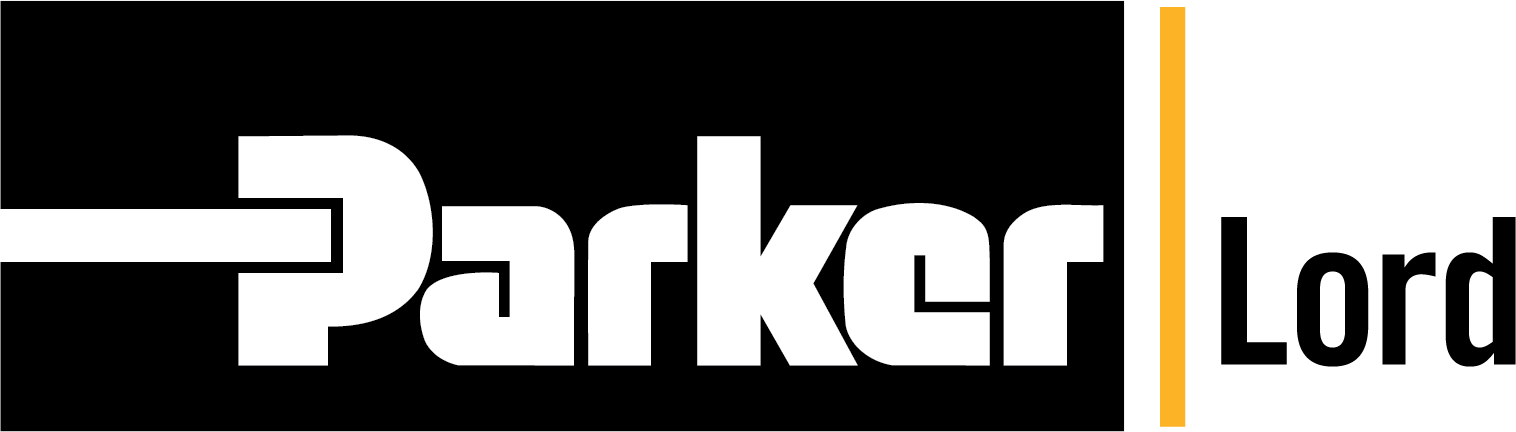
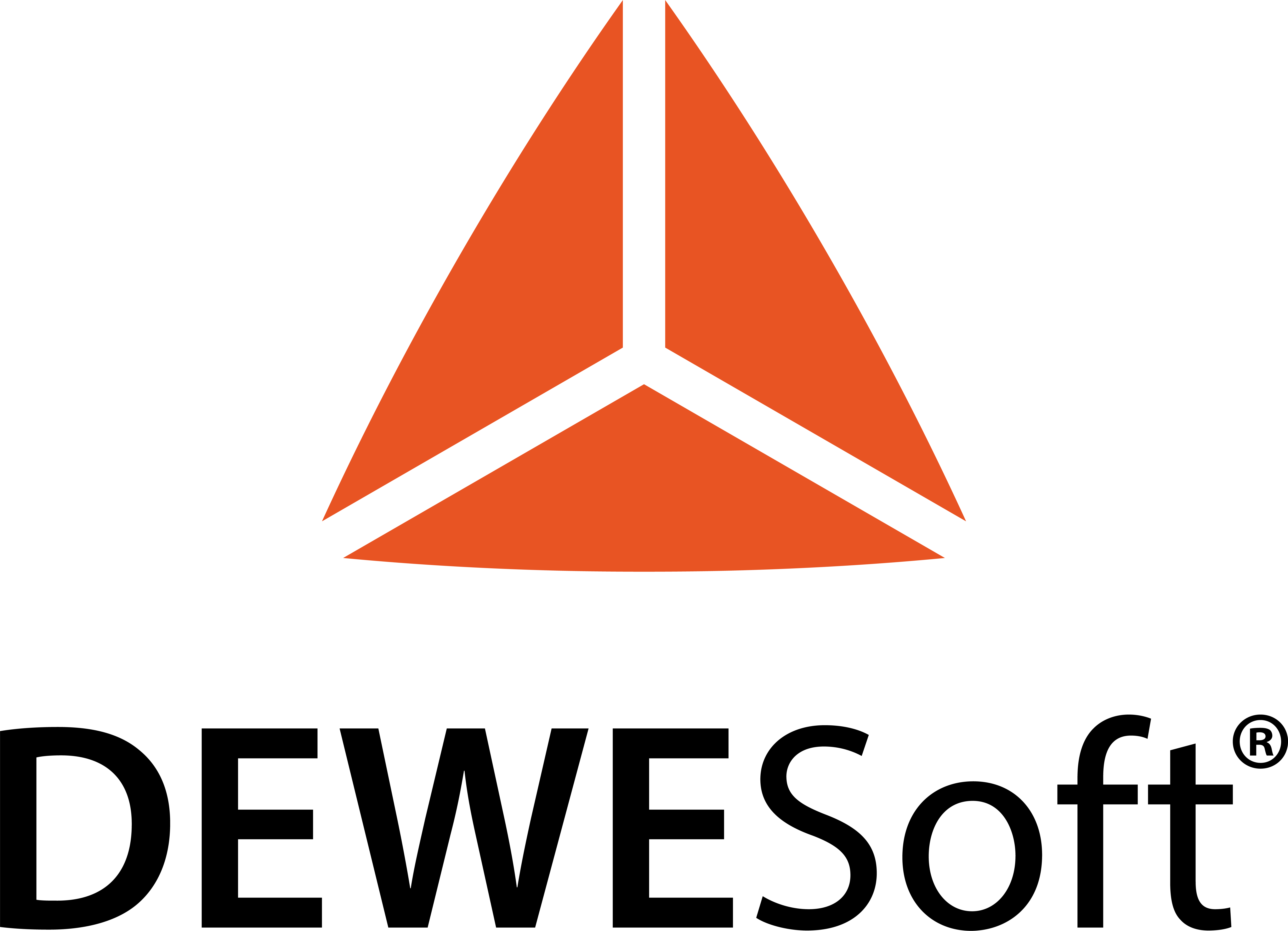
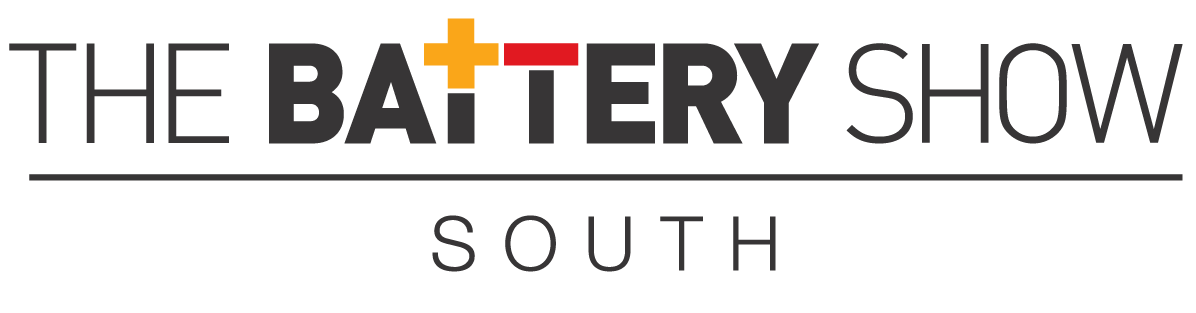
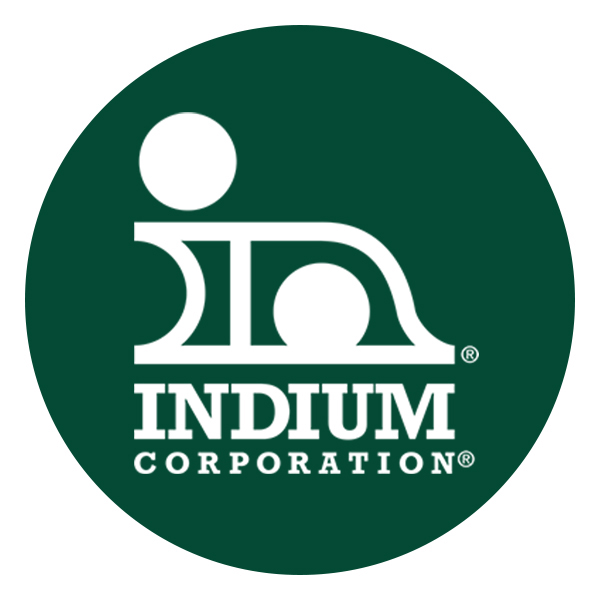

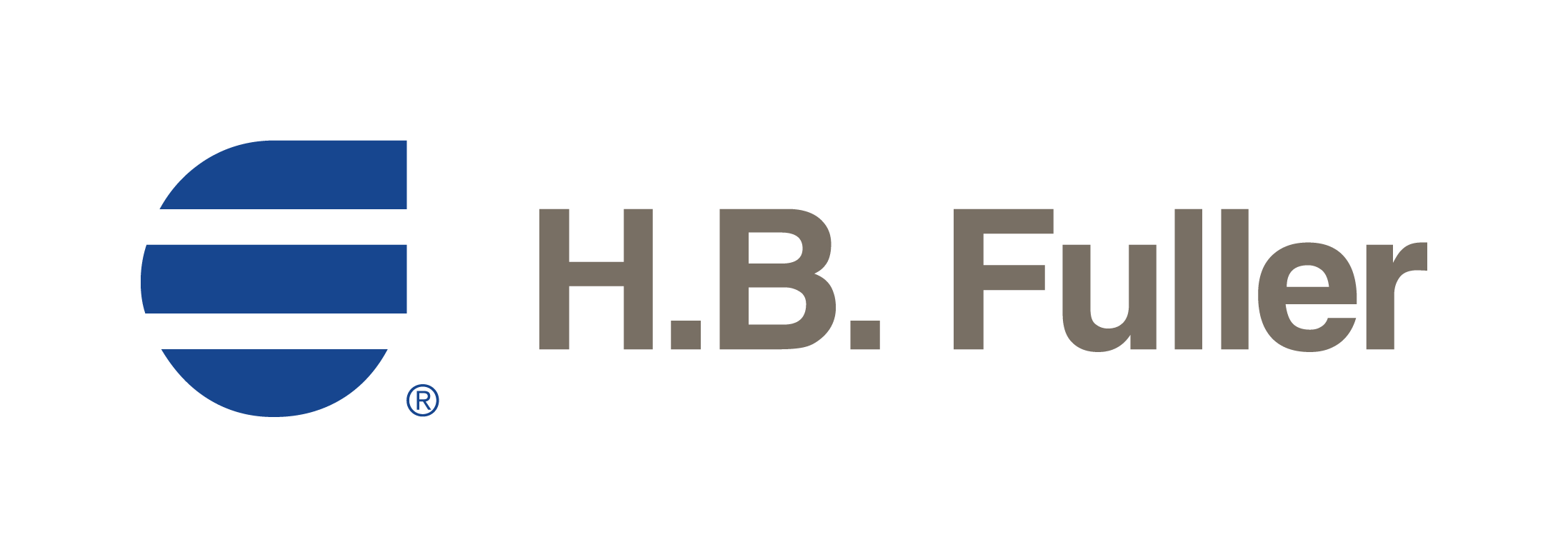
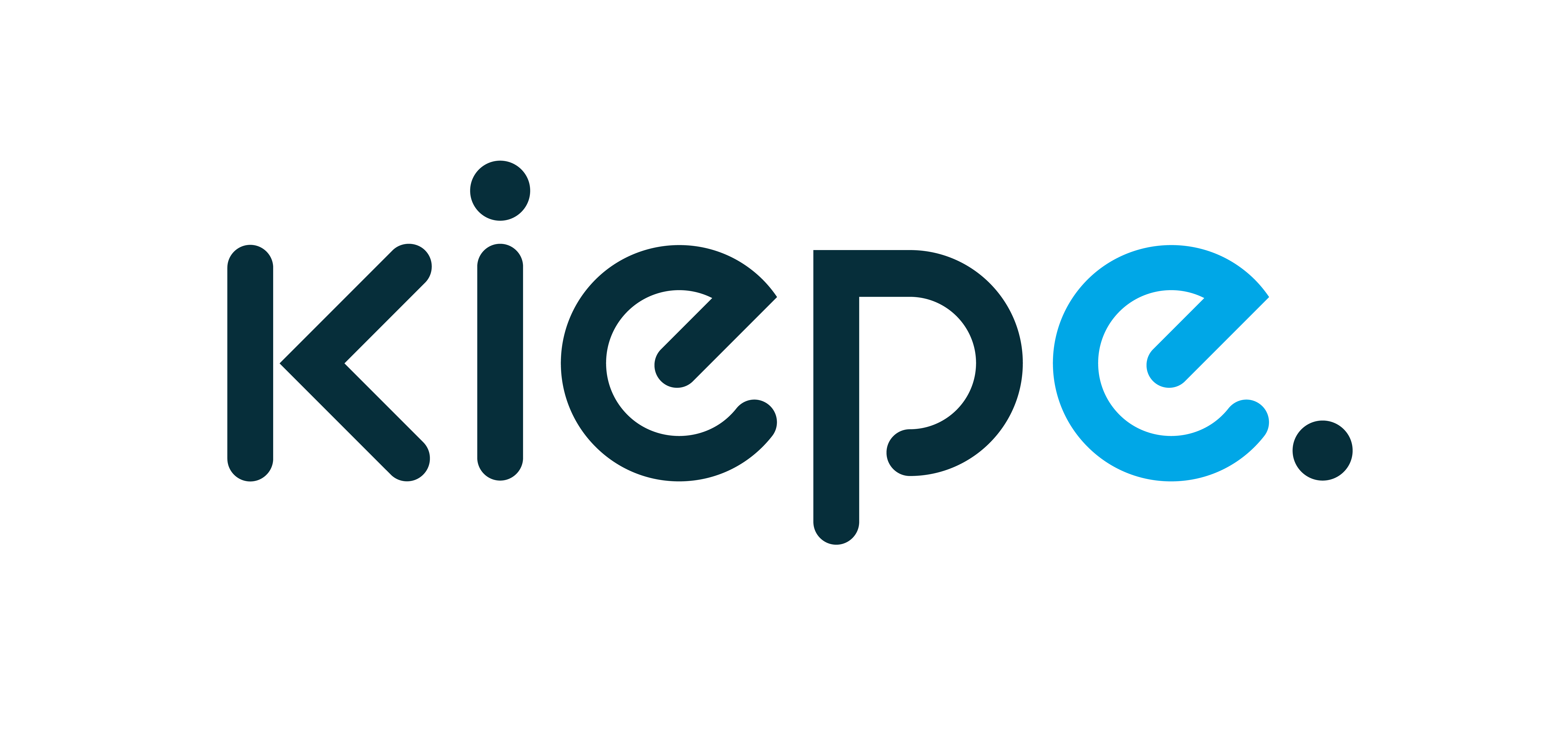
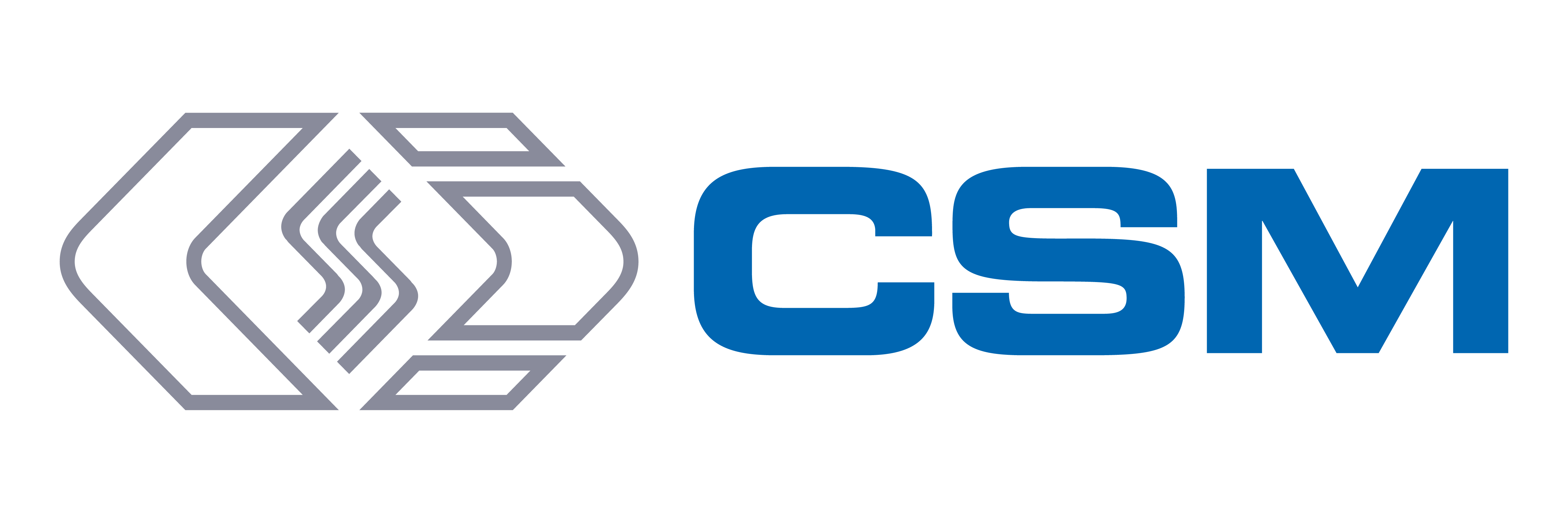