Erwin Quarder metal-plastic bonding delivers heat exchanger advances
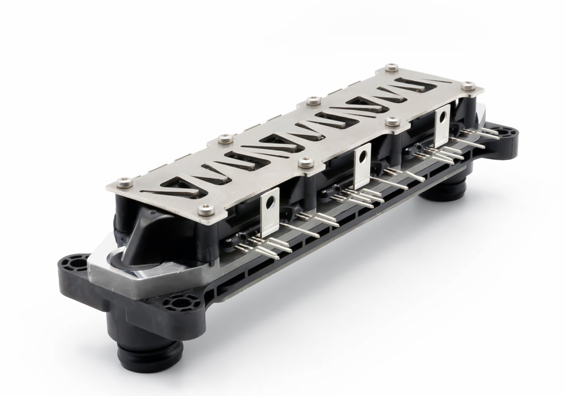
(Image courtesy of Erwin Quarder)
Thermal management is a major issue in the development of new electronic architectures. Current state-of-the-art heat-exchanger designs are restricted by the use of classic aluminium manufacturing options such as extrusion, forming or roll-bonding, but a new approach from Quarder Group could be about to revolutionise things.
The company has applied its experience of more than 50 years in the field of plastic injection moulding to create its MPDB® technology, which allows the direct connection of metal and plastic.
The unique ability to bond these two materials opens the door to some significant potential advantages, including:
Design freedom
The greater design freedom of plastic parts allows thermal engineers to create completely new fluid-flow concepts, improving their ability to limit and maintain maximum temperatures, and temperature spread in each range. Plastic also makes it easier to reduce the number of overall parts, as coolant connectors or features for electrical safety can be directly integrated and reduce manufacturing complexity.
Elimination of weak points
Direct bonding can put an end to the need for brazing, sealing and screw connections, eliminating potential weak points within the manufacturing process.
Lightweight
The lower density of plastic compared with aluminium offers a weight reduction up to 40%, opening the door to design and build more lightweight coolers while increasing power and energy density in different applications.
Adaptability
The mechanical strength and flexibility of plastic can be adjusted by adding glass fibres to various base polymers, while various suitable additives can be used to influence material properties with regard to flammability rating, air and creepage distances or dielectric strength.
Thermal benefits
The thermal insulation properties of plastic can help to keep heat or cooling power at the right place and maintain proper condensate management.
Cost-effective materials
A variety of polymer bases can be used, including PPS, PPA or PK. Blends such as PA/ABS are under investigation. This can help manage manufacturing costs, and the reduced processing results in a need for fewer raw materials.
The combination of these benefits gives this new technology significant potential, but as metal still plays an important role in efficient heat exchangers, the challenge is how to combine the two materials in a reliable way to fulfil all industry-related requirements.
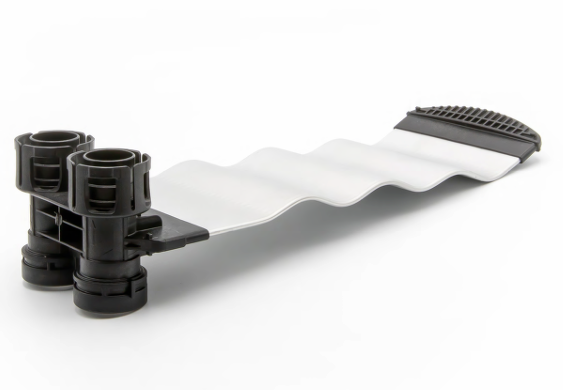
How it works
Erwin Quarder Group owns a bonding process that allows hybrid heat exchangers to be built for various applications using chemical or mechanical methods.
To achieve the plastic-metal bond, the aluminium surface is first structured to create a micro-nanostructure, resulting in an extreme increase in surface area. The plate is then brought to the melting temperature of the plastic, so that it melts and flows into the cavities and undercuts in the structured aluminium surface, filling all the cavities. The structures in the sub-micrometric range are completely wetted with plastic, ensuring there are no air pockets or voids. Once the component has cooled, a media and gas-tight connection is created between the aluminium and the plastic.
Click here to read the latest issue of E-Mobility Engineering.
ONLINE PARTNERS
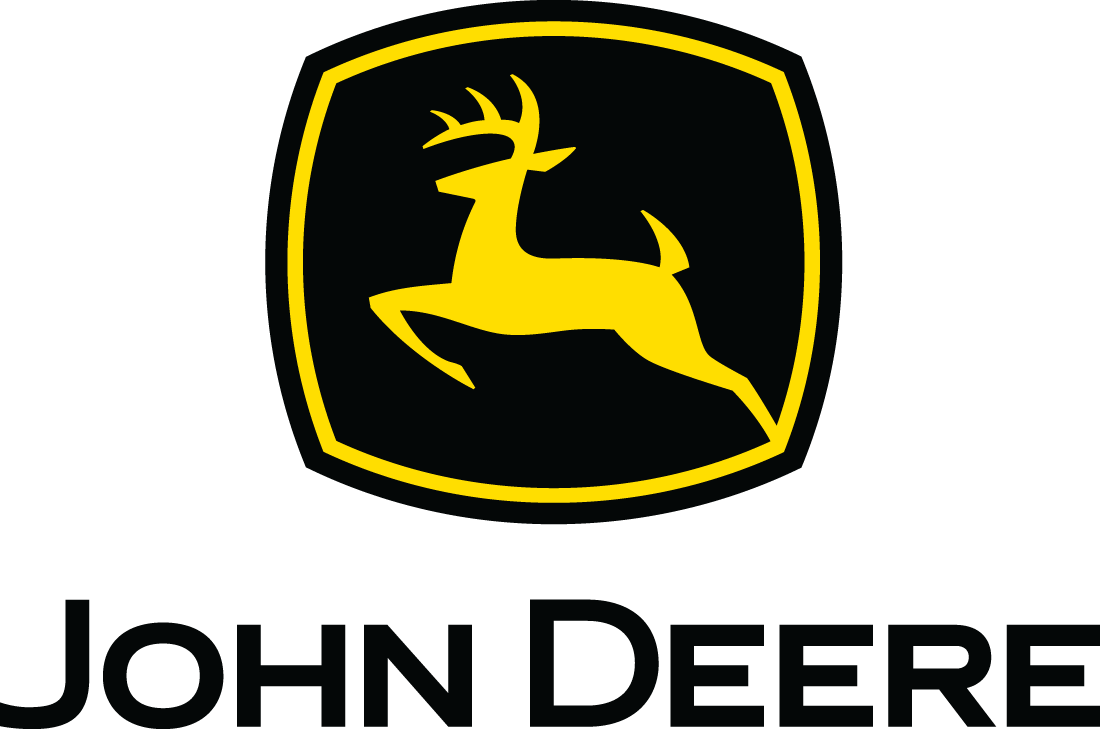
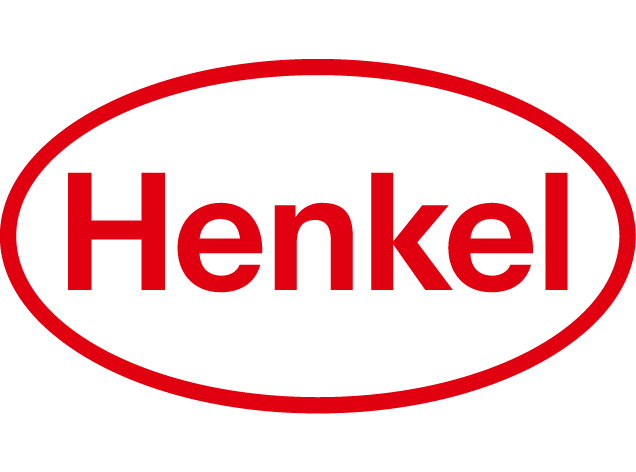
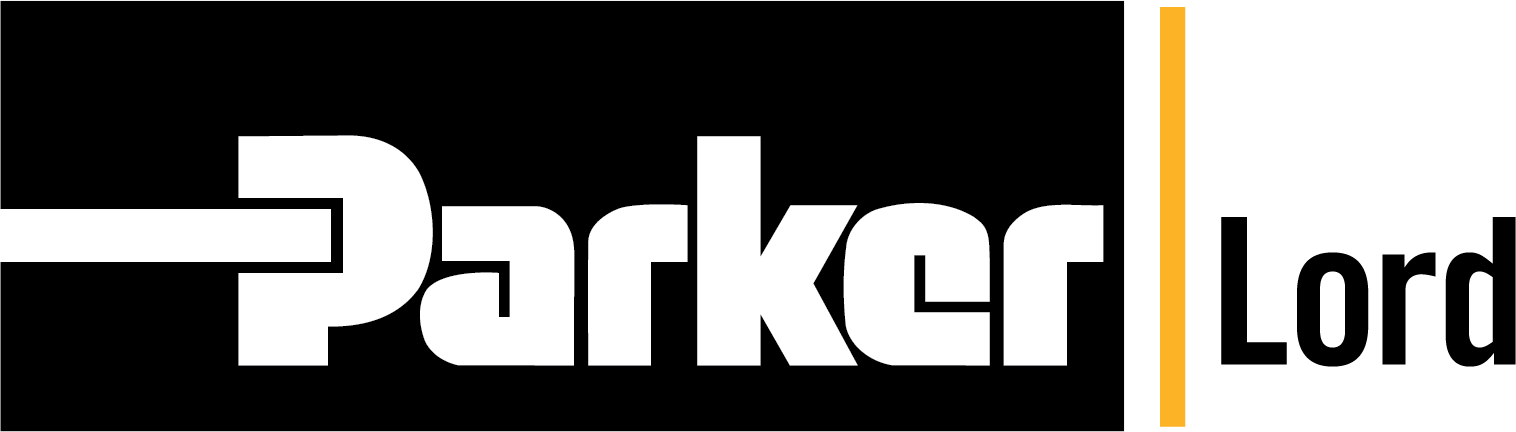
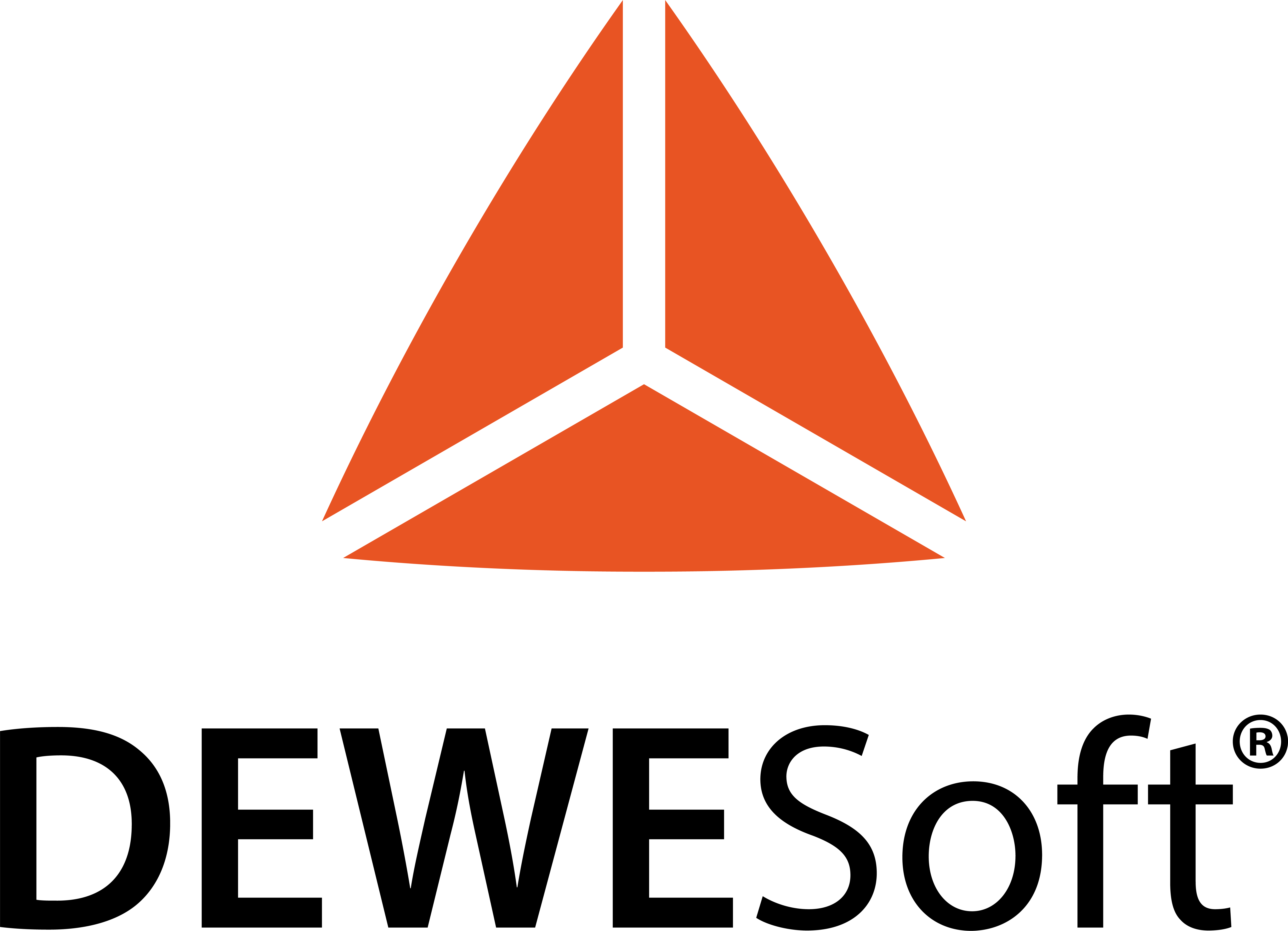
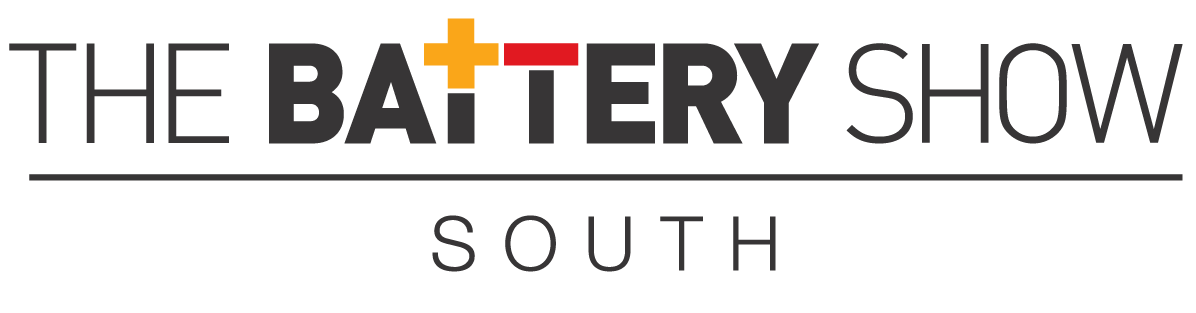
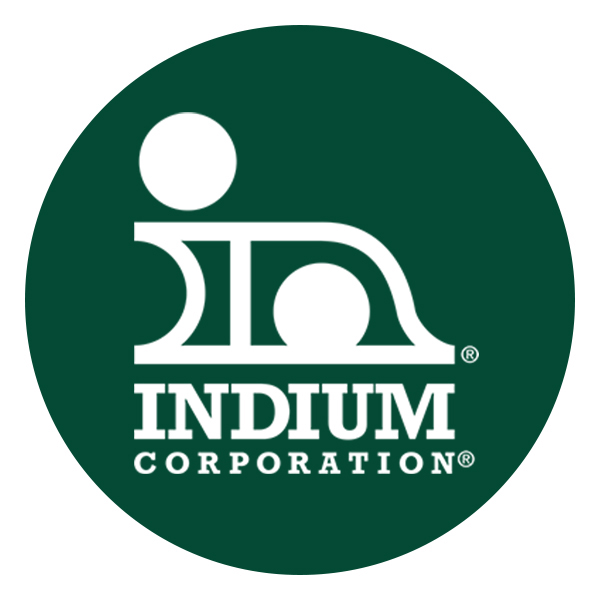
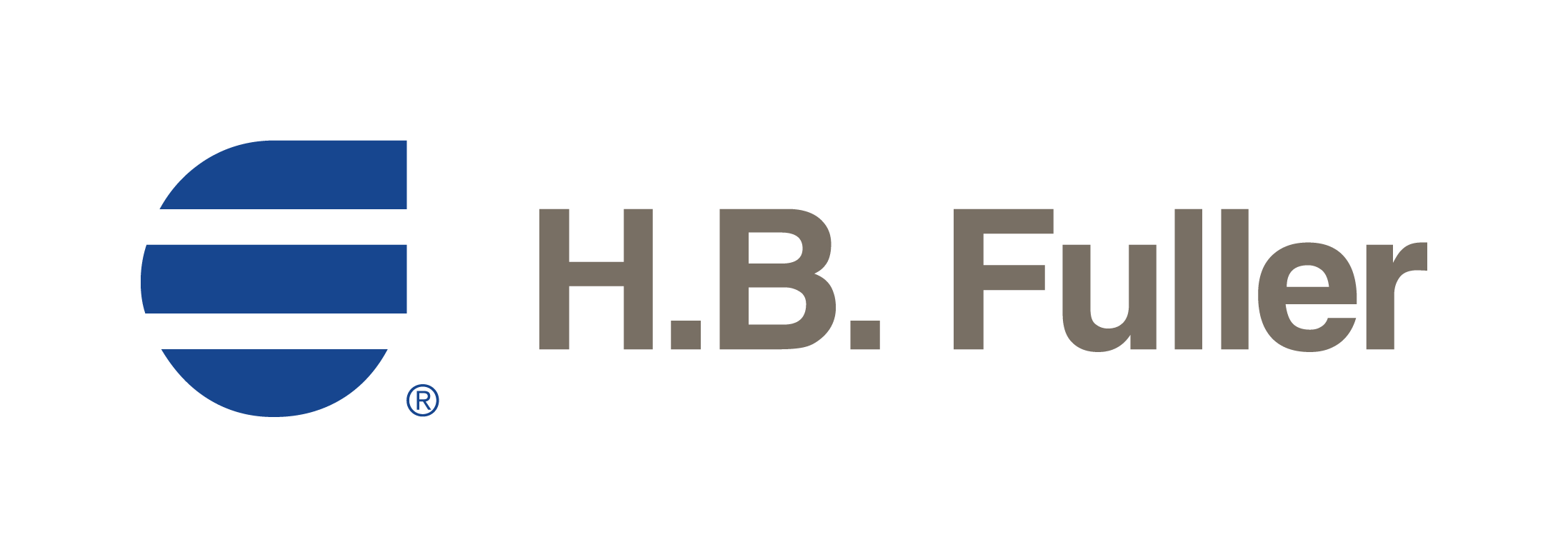