Equipmake’s ZED system for buses set to enter service
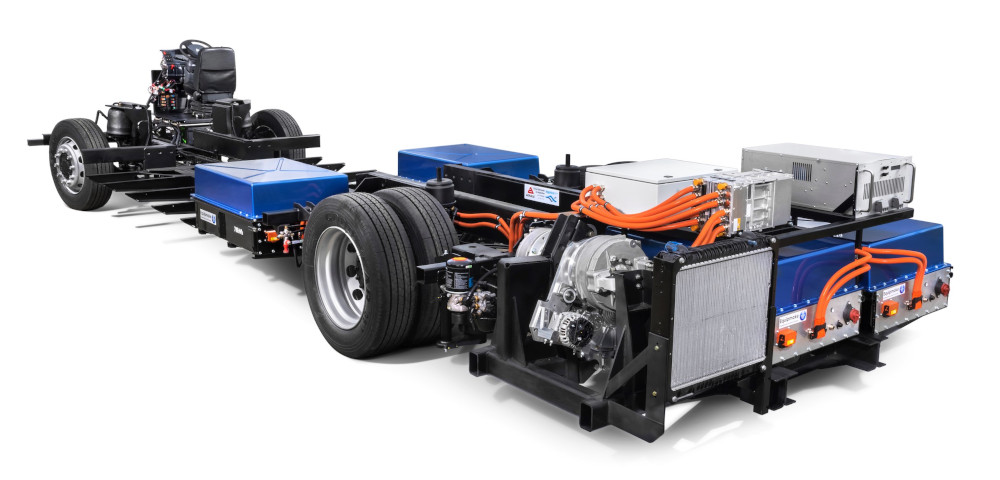
(Courtesy of Equipmake)
Developing heavy-duty powertrains for integrating into electric passenger buses is fundamentally different from other EV applications, owing to their unique drive cycles and weight-carrying considerations, and their dramatically different HVAC requirements (writes Rory Jackson).
Unlike other EVs, an electric bus can expend as much energy on heating and cooling its cabin interior as it does when in motion. Optimising an electric powertrain around enabling such environmental management and hence ensuring the comfort and well-being of passengers involves a lot of work in tuning the battery, power converter and motor systems.
That has been a major focus for UK-based Equipmake over the past several years. The result is its Zero Emission Drivetrain (ZED), which consists of an in-house electric motor, inverter and all the power electronics. It also comes with a battery that can power an existing diesel bus or be used in an entirely new model, such as the company’s Jewel E double-decker.
The ZED also features Equipmake’s own, bus-specific HVAC system, and for each application the company says it optimises this set-up to make the best use of every watt-hour of energy.
“While cars can be driven in all sorts of different ways, the drive cycles of city buses are largely the same around the world, which helped us design an electric traction motor with the best efficiency across that sort of drive cycle,” says Ian Foley, CEO at Equipmake. “Many motor producers tend to cherry-pick a ‘peak efficiency’ figure for their datasheets, but what really matters is how a motor behaves throughout a vehicle’s entire driving cycle.”
The ZED’s 200 kg radial flux motor has a 3500 rpm maximum speed, a 3500 Nm peak torque output, and 400 kW peak power (although it never hits that last figure during bus operations). It is an IPM type, using V-shaped magnets slotted into a laminated rotor to maximise the reluctance torque generated, torque density being critical to the drive cycle of a bus – more so than straightforward power, Foley says.
Future designs might alternatively follow a patented ‘spoked’ configuration, in which the magnets are arranged like spokes on a wheel. That, Equipmake has discovered, works well for producing high combined power and torque density.
“The stator uses concentrated windings, which has proven great for manufacturing reliability,” Foley notes. “We were tempted to use hairpin windings, but in the solutions we investigated, the tooling and other set-up costs were too high – particularly so for low-volume production – and the greater internal copper packing density was offset by a comparable increase in copper overhangs and hence losses around the edges.”
On the other hand, in terms of benchmarking HVAC efficiency, Foley comments that a typical bus HVAC system has a coefficient of performance of between 2.5 and 3. That means that for every kilowatt put into its heating system, it will successfully transfer 2.5-3 kW of heat into its target environment. That contrasts with some HVAC systems in buildings, which easily achieve coefficients of 5 or higher.
“There are some obvious things you can do to hit that higher figure, such as recover heat from the motors and inverters,” Foley adds. “However, it isn’t easy for a small company like ours to take on the engineering complexity entailed in that, so optimising the components in the HVAC has also been key.”
The components have been designed using the optimisation software suite from Altair Engineering, which Equipmake regards as among the best tools for simulation and hence design optimisation. It attributes a 7% reduction in its powertrain’s weight-to-power ratio to its work with Altair.
“Through that software, we can take between 20 and 30 electric motor parameters, such as magnet widths and lengths, and the stator-rotor air gap size, and set a range of performance and simulation rules. Our computer then processes that for about a week before producing a set of optimisations we can implement when engineering our next motor iteration,” Foley explains.
ONLINE PARTNERS
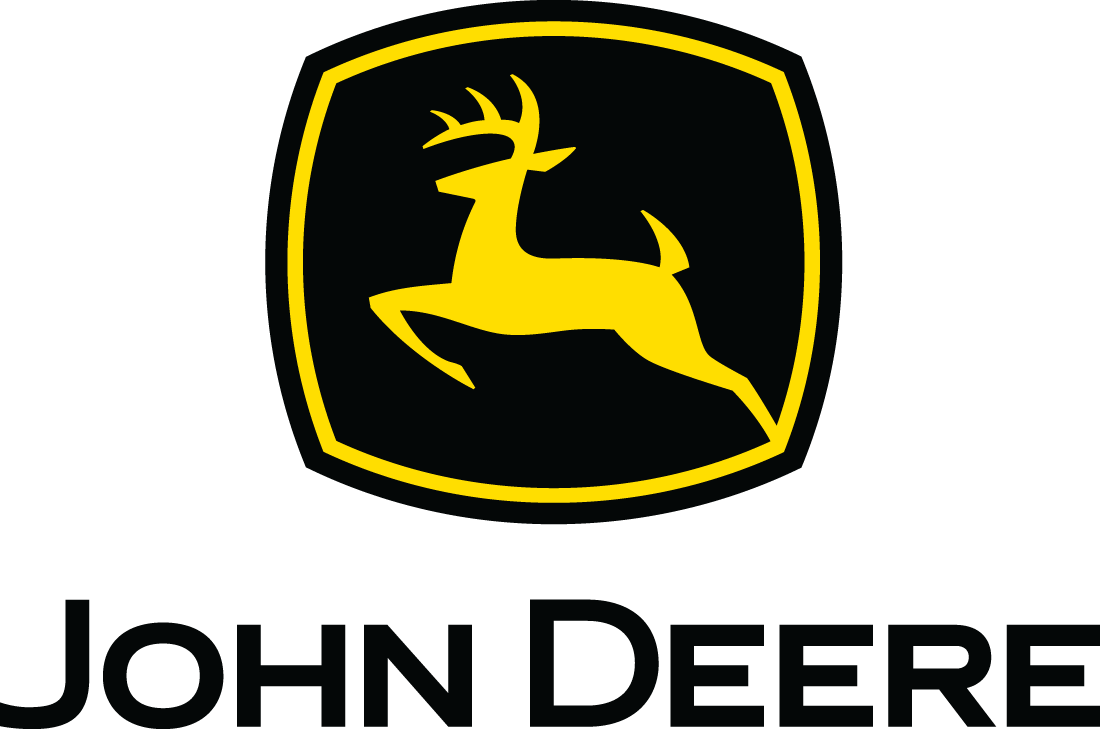
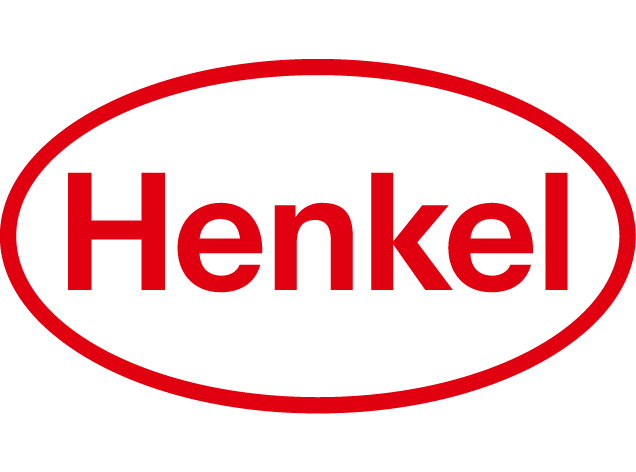
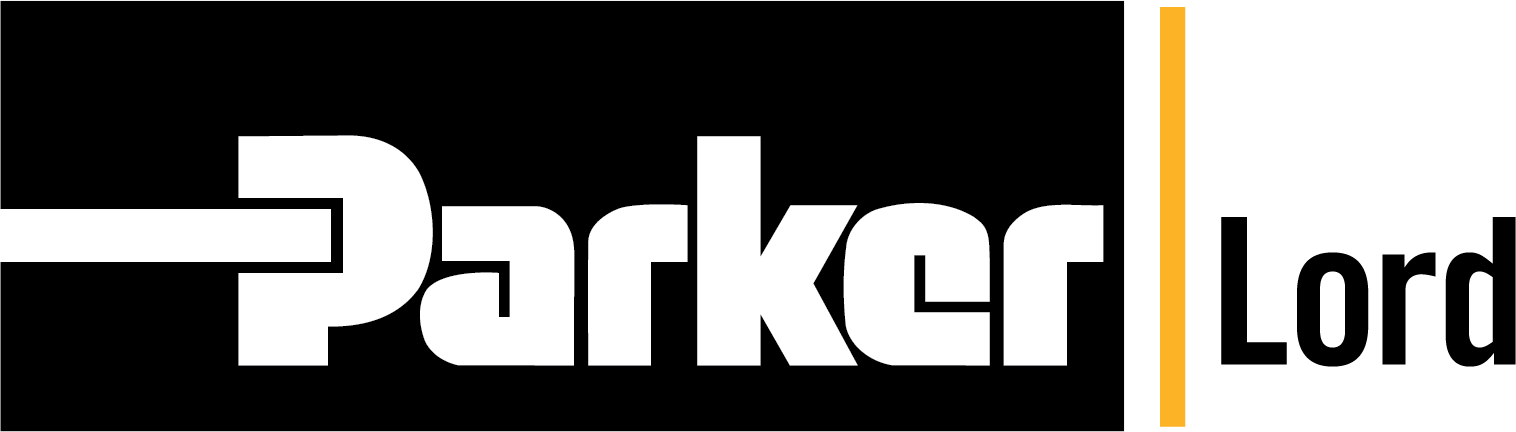
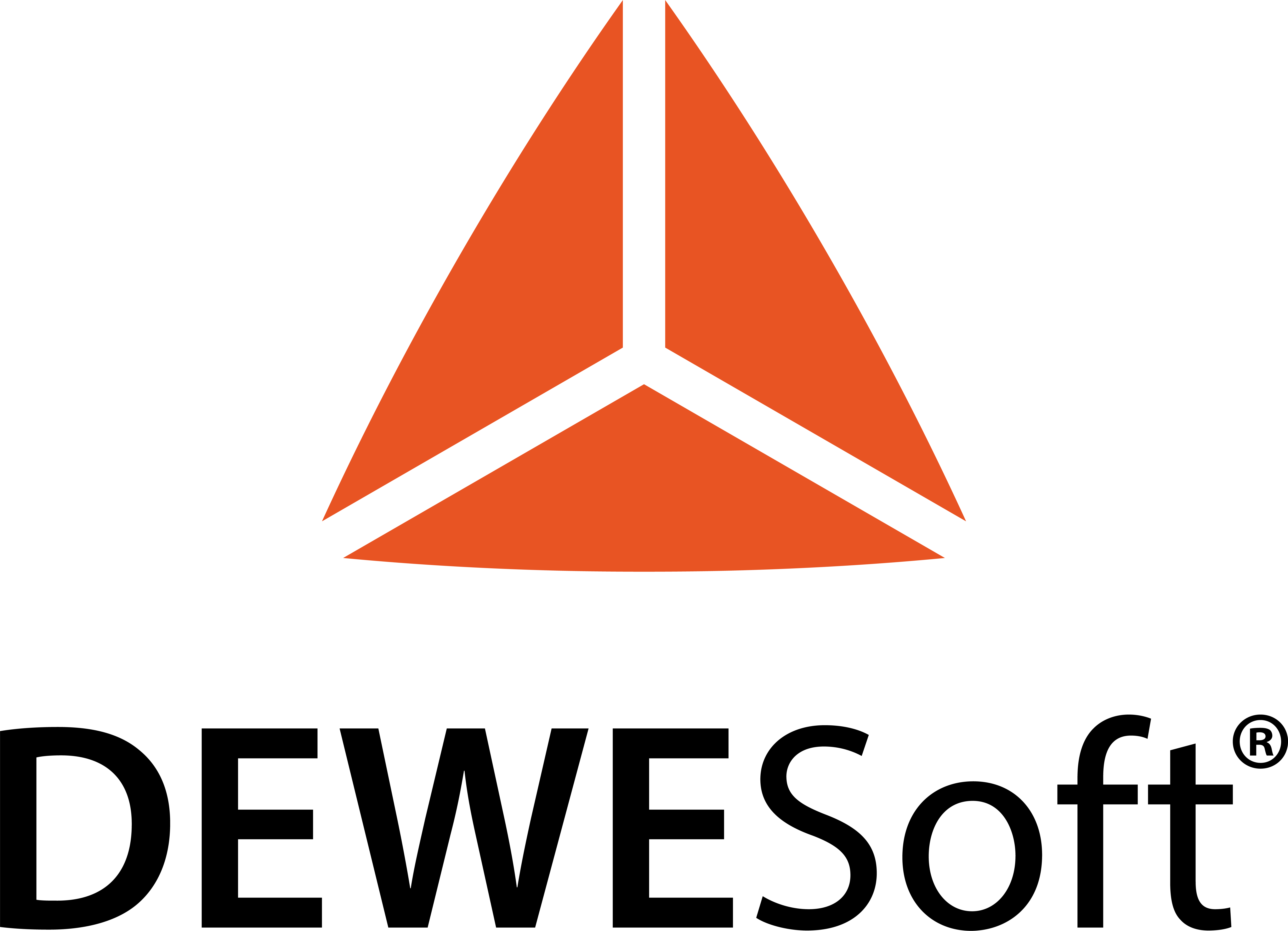
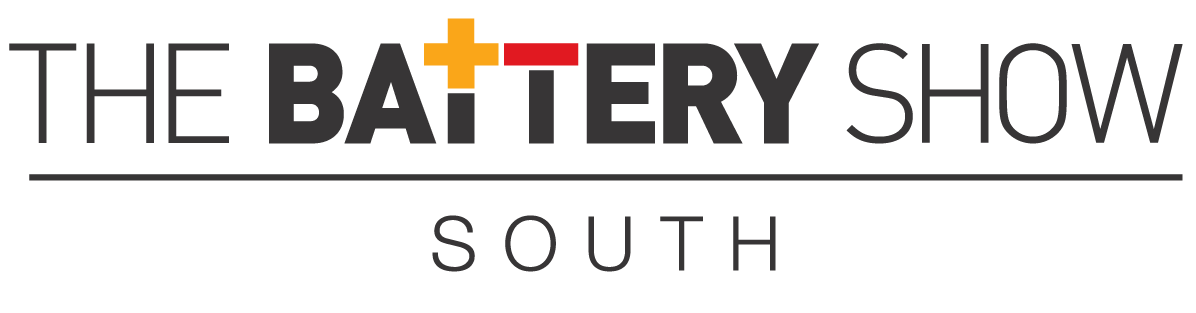
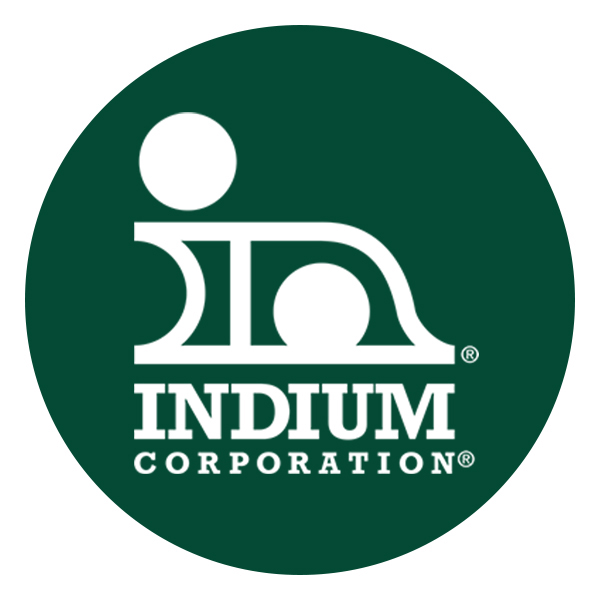

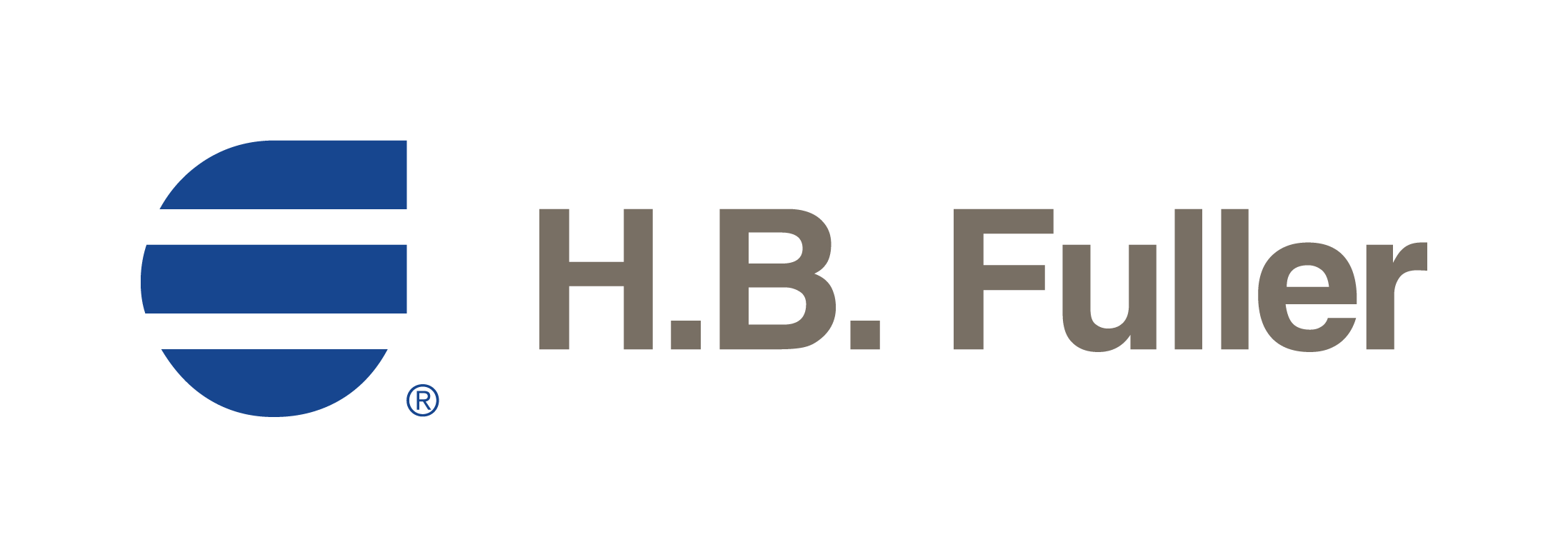
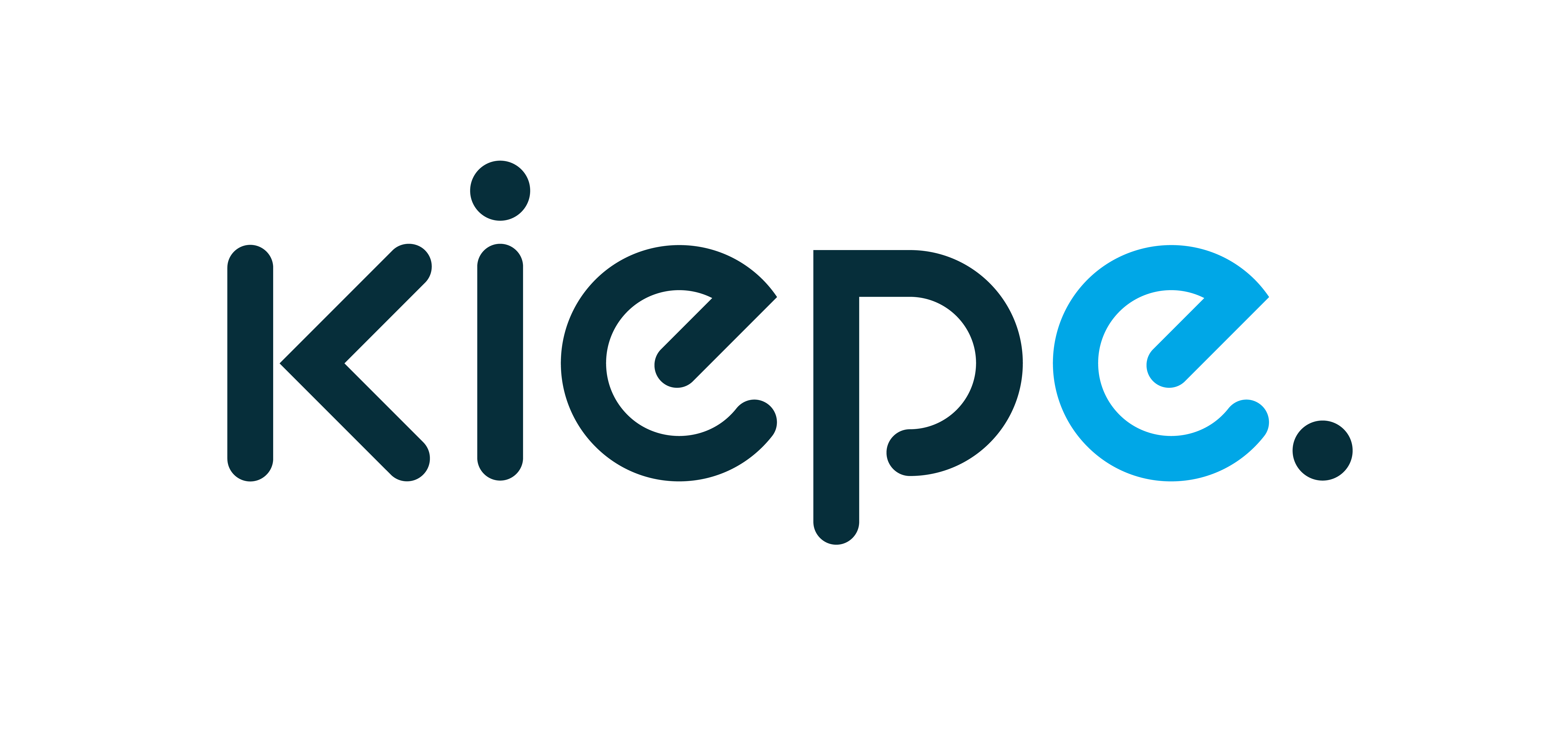
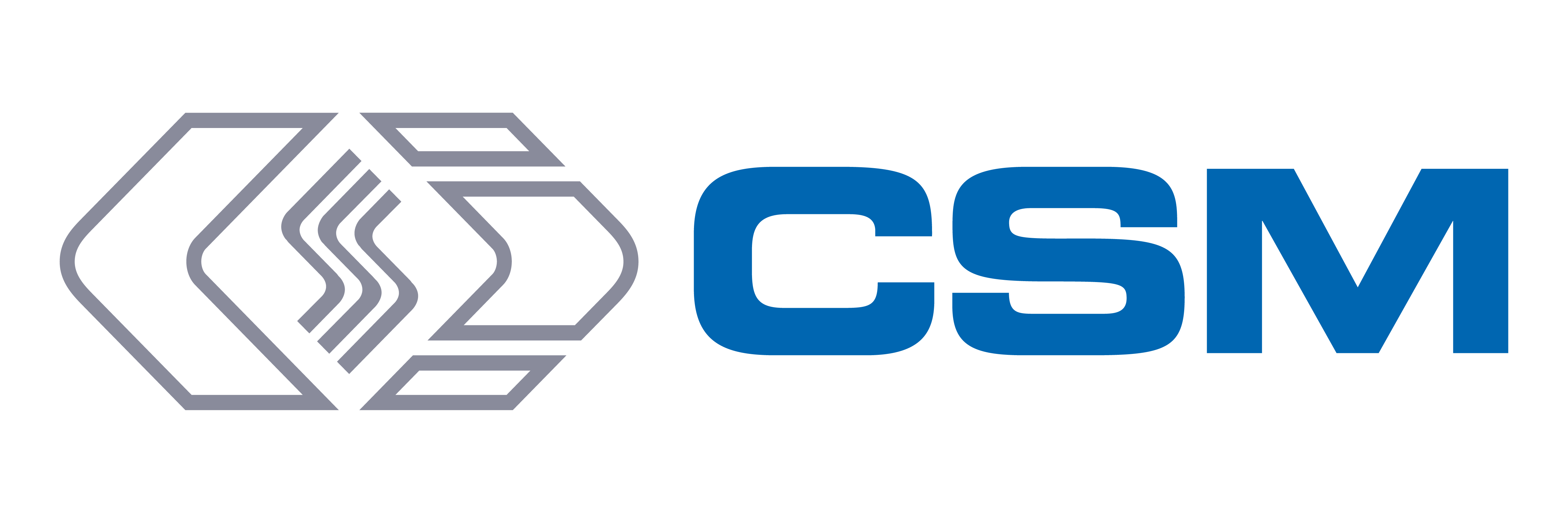