New motor architecture could be a game-changer
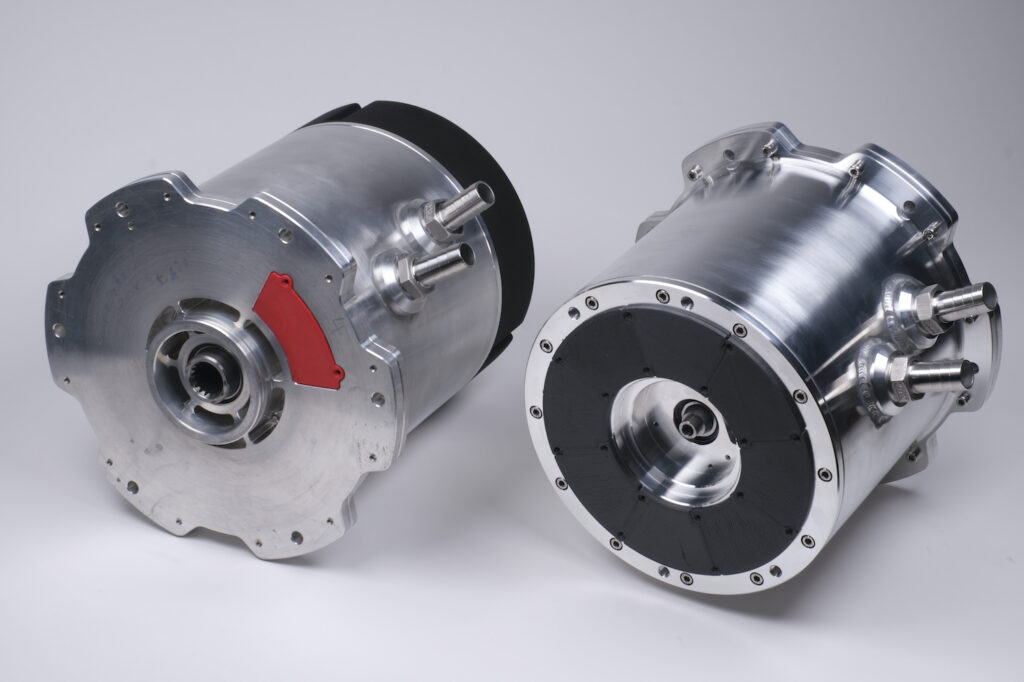
(Images courtesy of ePropelled)
At a time when EV manufacturers are eager for efficiency gains of 2-3% in their powertrains, any new technology capable of providing 10% or more would transform the state of competition among vehicle OEMs (writes Rory Jackson).
With an eye towards enabling that, US company ePropelled has developed and patented a new type of electric motor architecture, which it has manufactured and installed in a Tata Tiago hatchback and which it displayed at the Cenex-LCV show in the UK in September.
The company calls its new motor technology eDTS, which stands for electric dynamic torque switching. Testing thus far confirms that the power efficiency of e-motors adopting this architecture is at least 15% higher than with conventional designs.
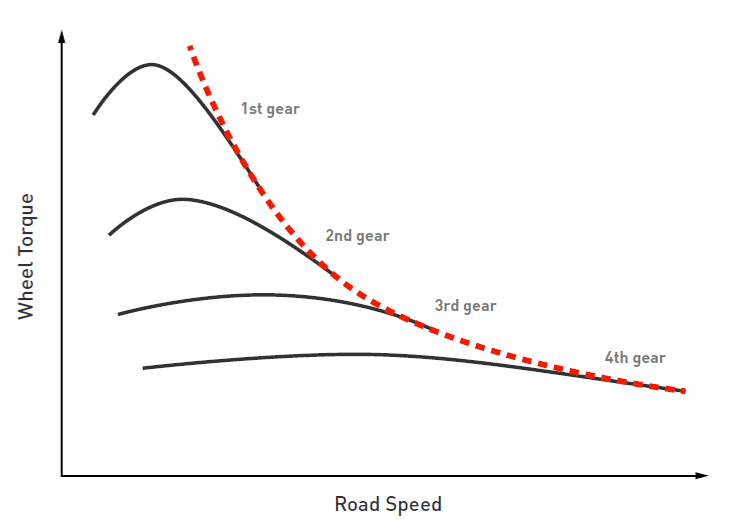
Explaining the eDTS’ technological principles exclusively to EME, ePropelled’s head of EV strategy David Hudson says, “A conventional fixed-winding configuration gives a typical electric motor a torque curve that’s high and flat at the top, then tails off and becomes asymptotic as you run towards high speed. That’s because you are relying on field-weakening to reduce back-EMF.
“What we’ve done is configure the windings in multiple paths and geometries, with each one corresponding to a different speed-torque output, and we can dynamically switch between those windings.
“At low speeds, an eDTS motor operates at very high torque. As you accelerate, you switch to a higher-range set of windings that give you much higher speeds and lower torques, as well as much higher efficiency at those high speeds because you don’t need field-weakening current.
“So we’re optimising the peak power efficiency of our e-motors at different speeds, similar to the action of a mechanical gearbox in a traditional IC engine powertrain, except we use no mechanical parts, only windings in the armature.”
The result is that the speed-to-torque ratios of eDTS motors produce a torque curve identical to that of an IC engine using multiple gearbox ratios, with cascading output curves corresponding to each gear.
With eDTS, EVs could switch between a first, second or third ‘gear’ winding as they drive at different speeds. That means a higher starting torque, extended constant power, and
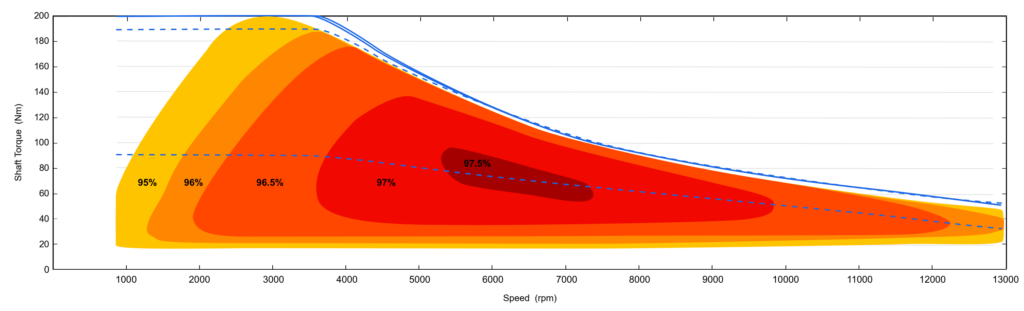
reduced current requirements compared with typical electric motors that have a single point of peak efficiency, and effectively waste energy when driving at any speed outside that point.
The architecture is scalable for any feasible size of electric motor, and Hudson anticipates that configuring each eDTS motor for two to four speed settings should be sufficient for most road EV requirements. Technically though, many more could be installed in any given electric propulsion motor without issue.
As well as enhancing EV ranges and reducing EV drivers’ charging costs, the company also notes that the 15%-plus reduction in EV energy requirements could be critical for reducing the degree of energy infrastructure investment needed to enable en masse switching from IC engines to EVs.
The eDTS concept was initially developed using digital twin software simulations, before assembling and testing prototypes on a dynamometer and then integrating them into an existing test EV. That final step allowed the results to be compared with the EV’s original drivetrain, which used a Bosch e-motor.
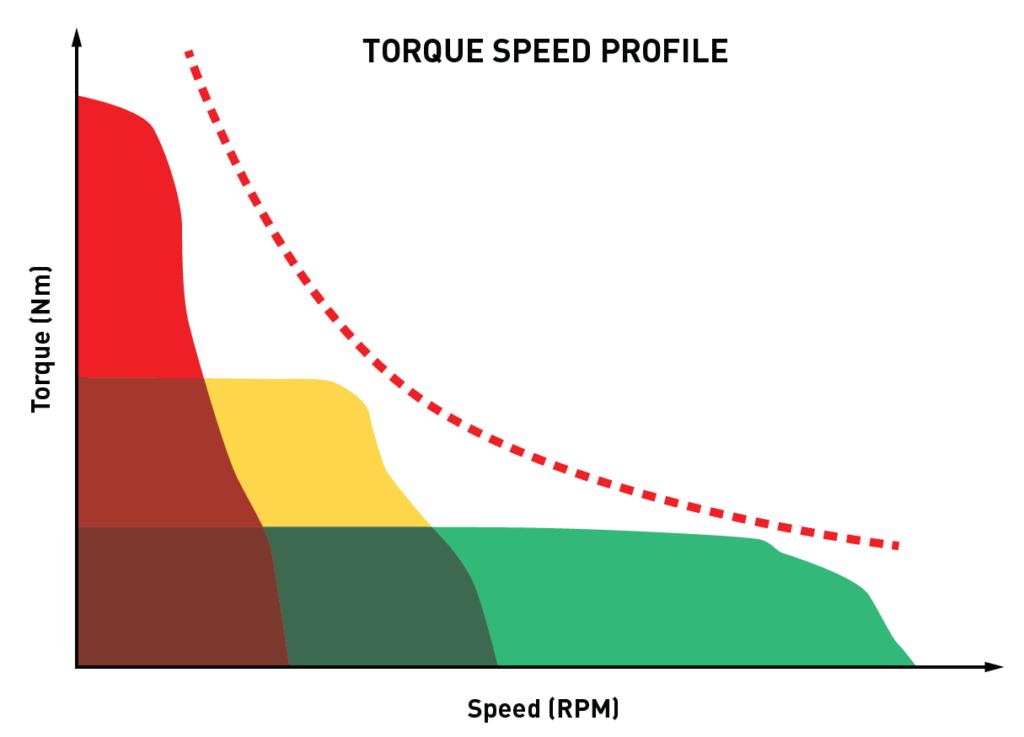
ONLINE PARTNERS
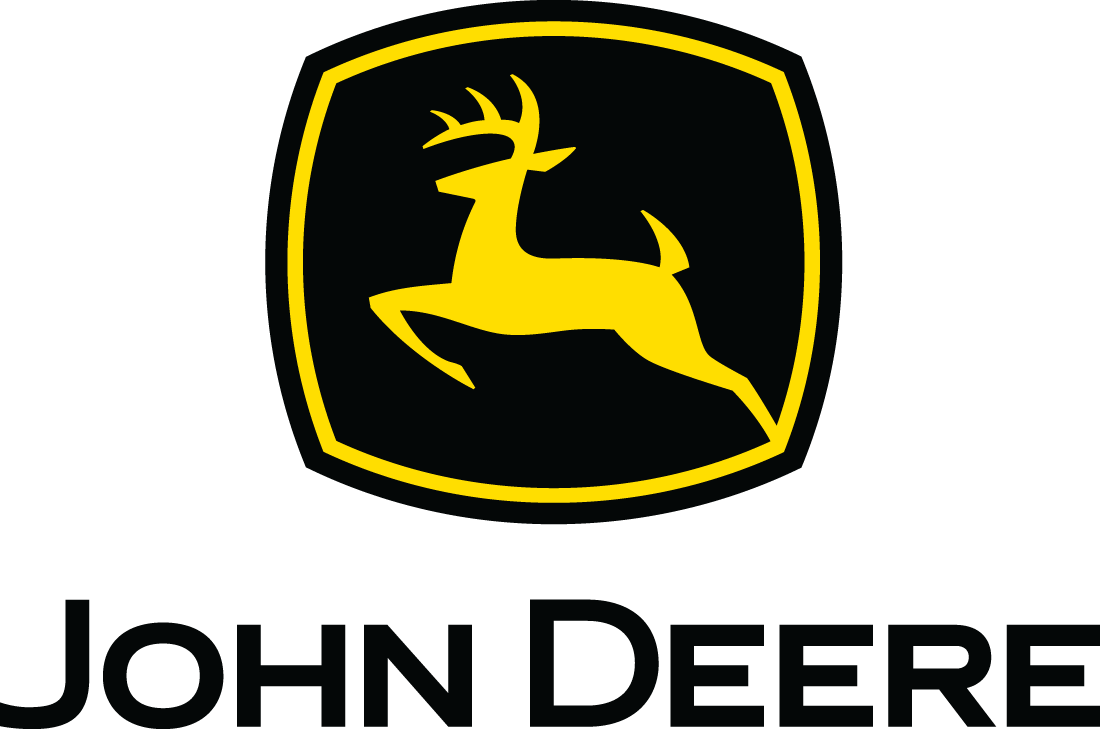
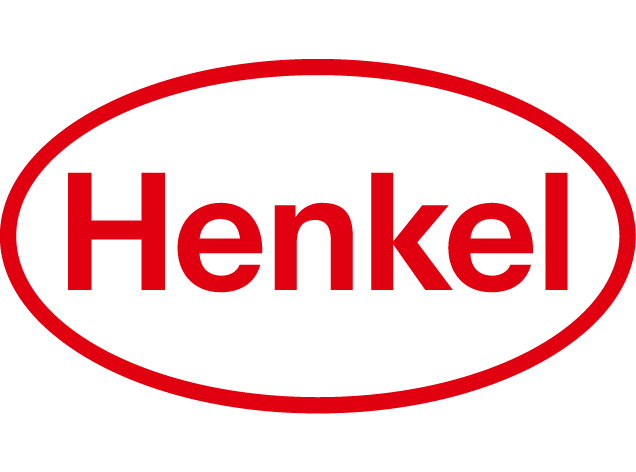
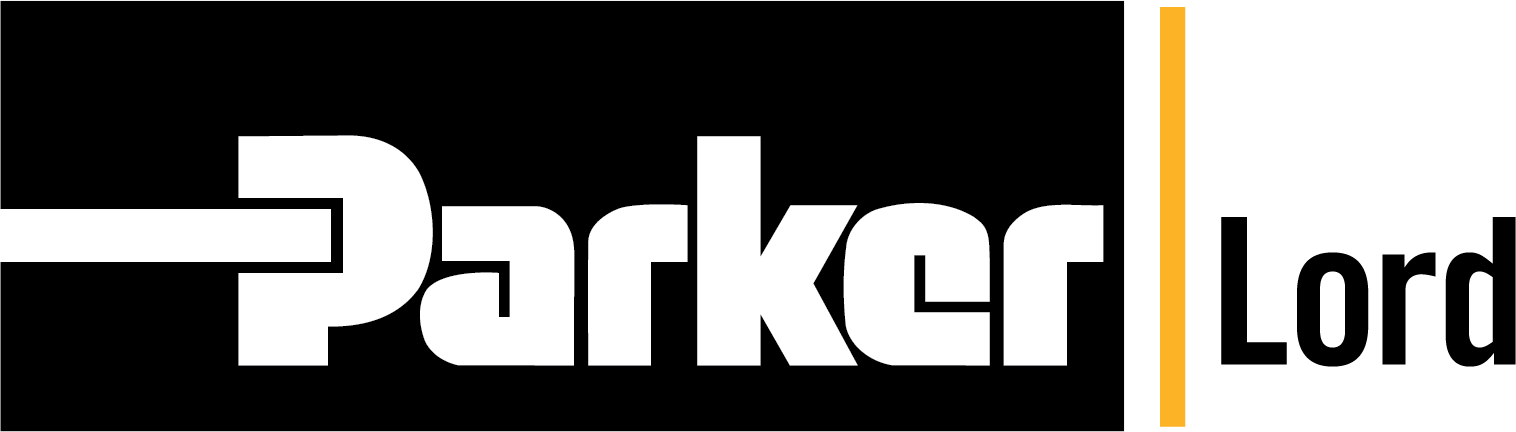
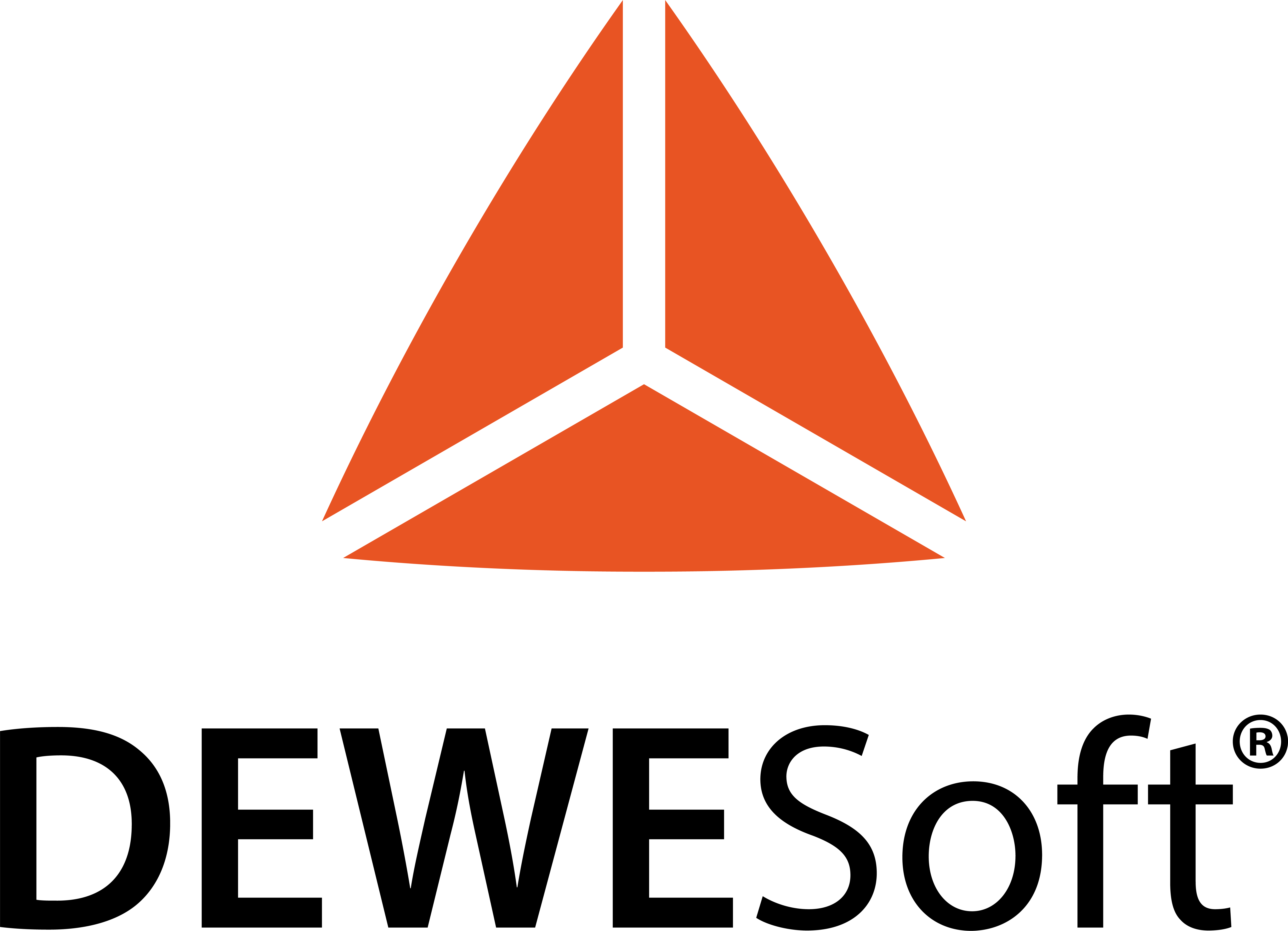
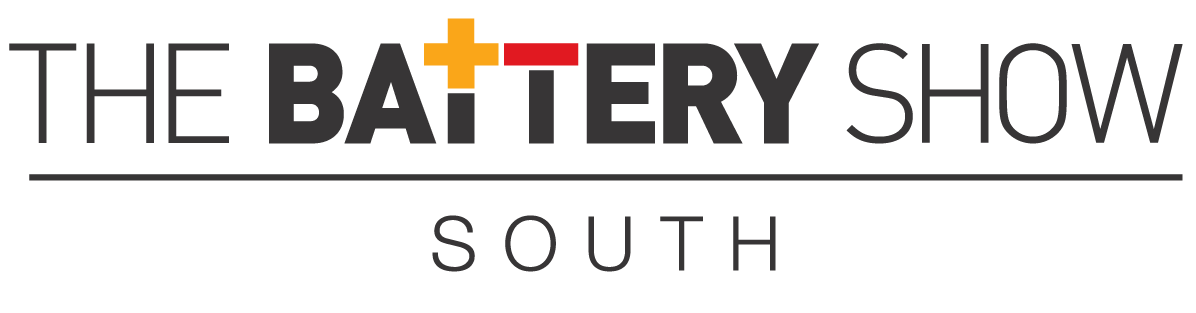
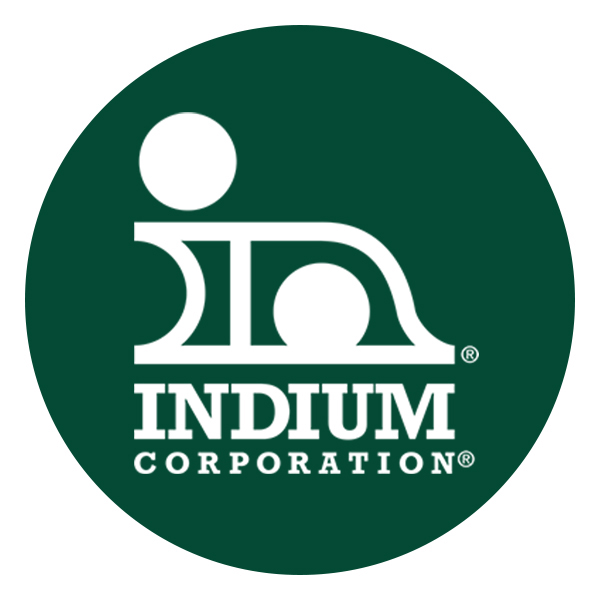

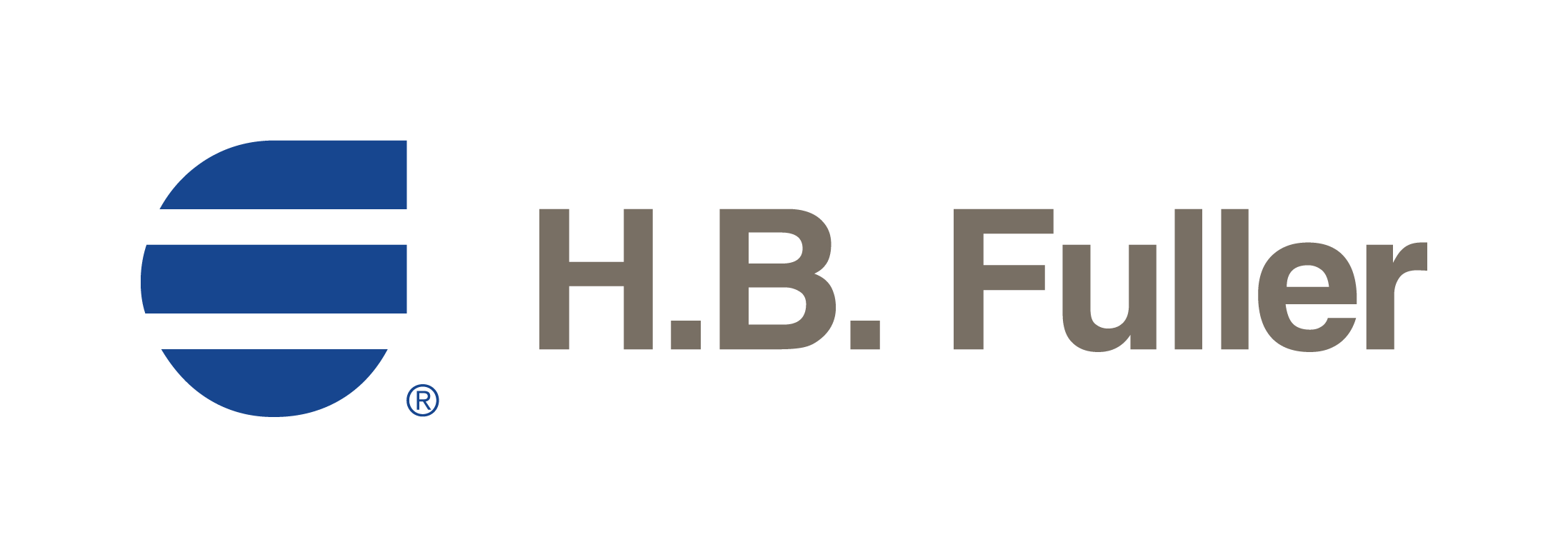
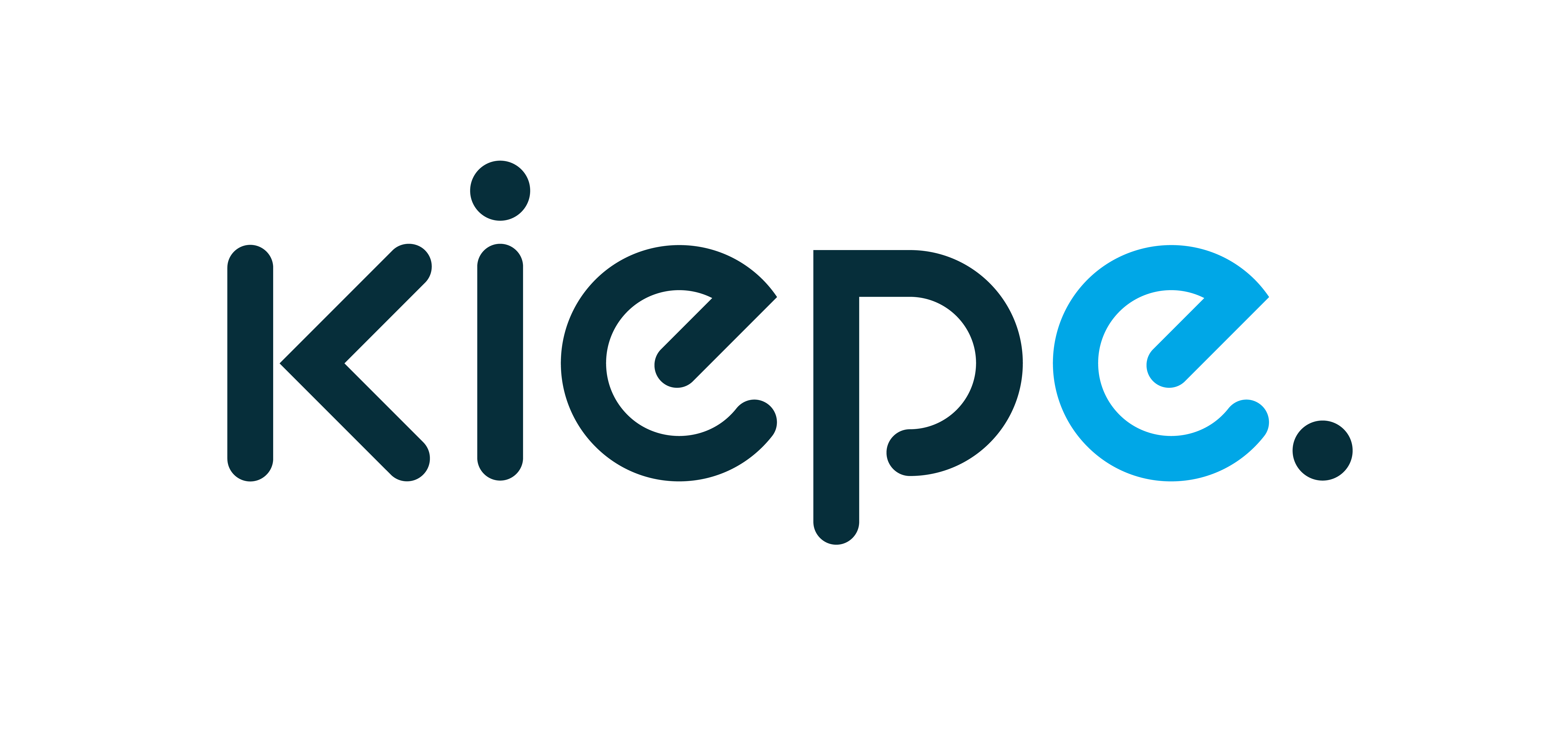
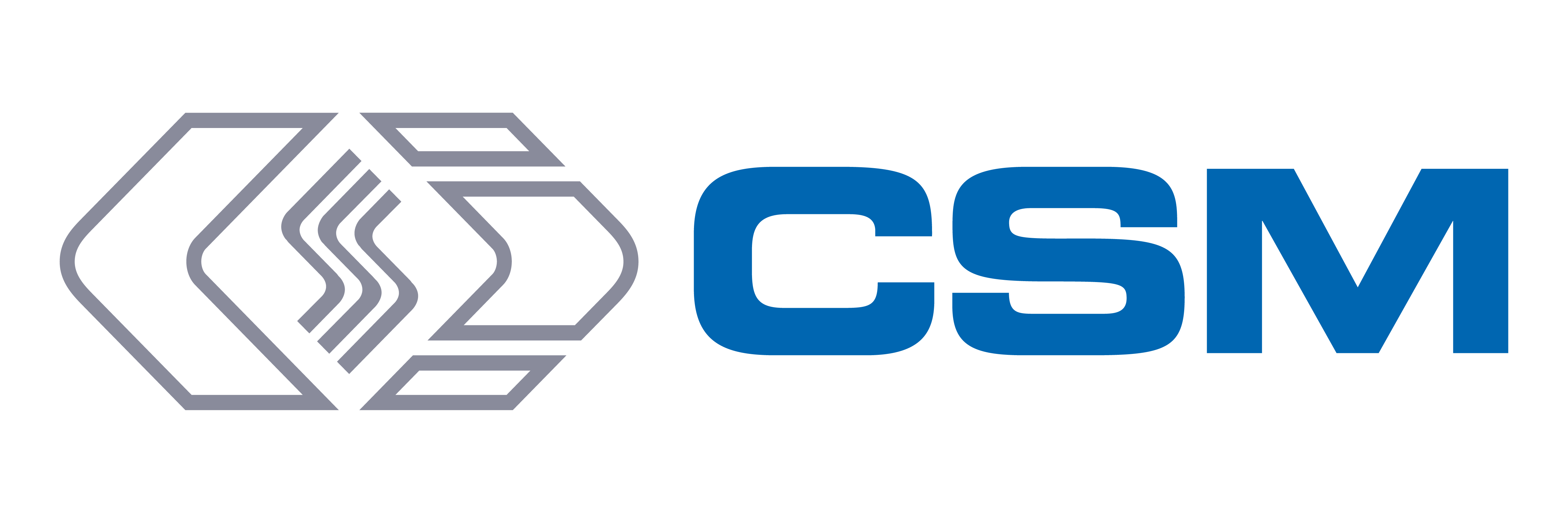