Energica Eva Ribelle
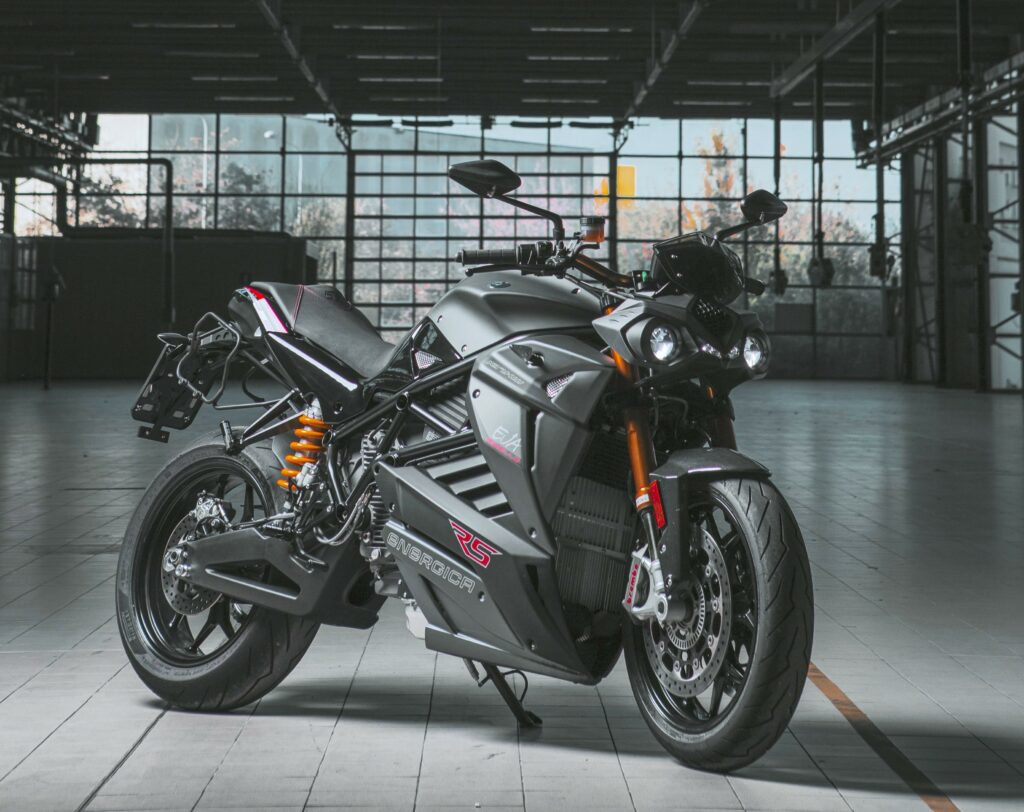
(Images courtesy of Energica. Photo: Marcello Mannoni)
Rory Jackson explores how this e-bike combines the efficiency for urban commuting with the performance for recreational use.
Rebel with two causes
Since its founding in 2014, the Energica Motor Company has sought to combine cuttingedge electrical engineering with designs that capture the ergonomics and aesthetics needed to thrive in the world of luxury motorbikes.
Based in Modena, in Italy’s Motor Valley, the company is a subsidiary of manufacturing services multinational CRP Group, which specialises in additive manufacturing and precision machining for motorsport and other sectors. That has given Energica access to expertise in materials science and racing technology, both of which have been leveraged across Energica’s many motorbike models.
But although high-power, aerodynamically designed motorbikes are typically associated with racing, Energica knows only too well that commuters and urban riders (in the consumer as well as commercial markets) stand to gain the most financially from switching away from IC engines to all-electric powertrains.
The knowledge and engineering expertise at its disposal have culminated in the Energica Eva Ribelle (meaning ‘Rebel’).
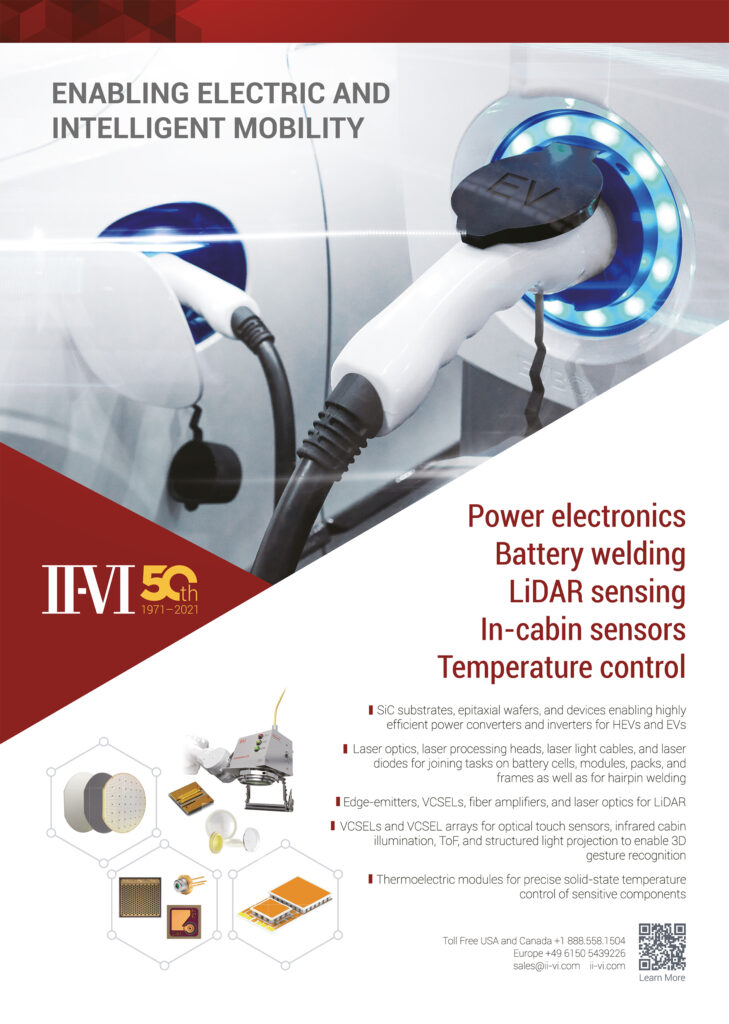
First unveiled in 2019, and achieving production readiness last year, the company calls it “the world’s only electric streetfighter” in reference to sport bikes that dispense with several of the typical fairings on more standard motorbike designs. It also has comparatively larger headlights and handlebars, to create a more aggressive and stylish feel for prospective owners.
Although the Eva Ribelle is slightly heavier than other all-electric motorbikes, at 270 kg (compared with the 219 kg of the Lightning Strike, covered in EME 4, Autumn 2019, for example), what the rider gets in exchange are some of the highest parameters for operating capabilities currently available for EVs of this type.
The Eva Ribelle represents a marriage of performance and efficiency. It has a maximum power output of 107 kW (145 bhp) and a 21.5 kWh battery that gives a range between charges of up to 400 km. It can also be fully recharged within an hour using a DC fast charge Mode 4 power supply.
At the time of writing, Energica was poised to release the next generation of the Eva Ribelle, the 2021 Eva Ribelle RS. This will feature enhanced acceleration: where the 2020 Eva Ribelle can go from 0 to 100 kph in 2.8 seconds, the RS will be able to do that in 2.6 seconds, thanks to a new mapping of key power parameters installed in the VCU and a very slight alteration to the transmission.
Although the 2020 and 2021 Eva Ribelles are otherwise similar, the company adds that the upgrade from the former to the latter will only be available with new bikes, rather than as part of an upgrade kit, owing to homologation requirements.
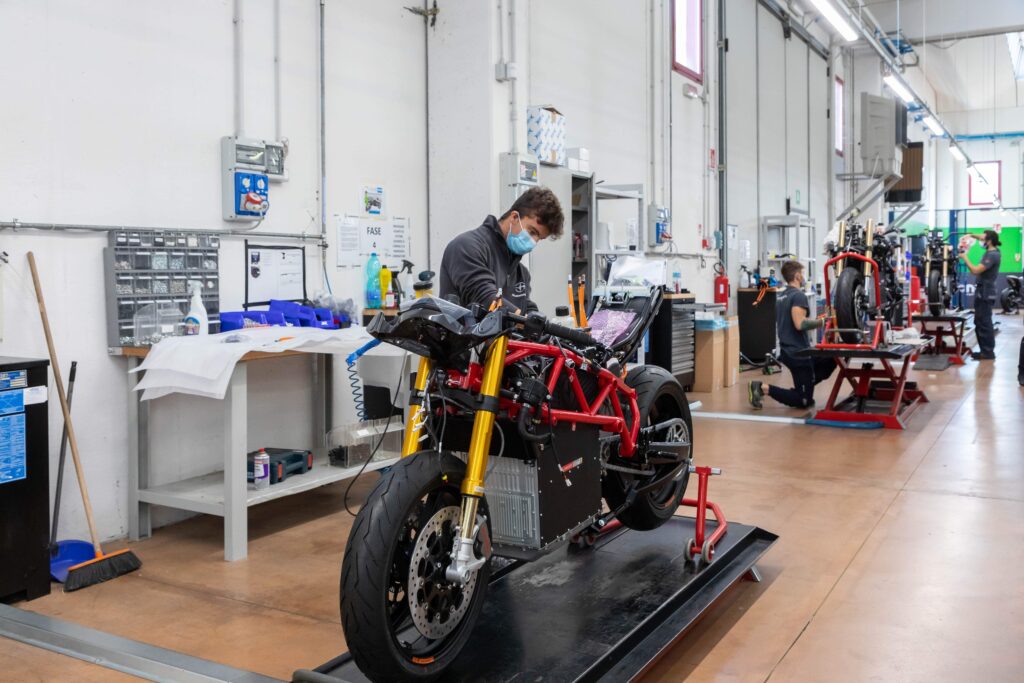
History of Energica
Around 2006, a team of engineers under Giampiero Testoni – then CEO of CRP Racing, now the CTO of Energica – had been working on 250 cc and 125 cc two-stroke motorbike engines for a number of European championships, and gradually expanded their focus to include total redesigns of the frames, swingarms and eventually entire motorbikes, not to mention other engine types.
“We started looking into electric powertrains in 2009, around the time of the first TTXGP zero-carbon race on the Isle of Man,” Testoni recalls.
“In December that year, some organisers at the TTXGP asked people at CRP if they were interested in building electric motorbikes for their race. At the time, CRP wasn’t so well-versed in electric machines, but they knew that taking on this kind of project could be a good investment for the future, so in the following January we started working on our first EV motorbike, and we were racing with it by June.”
Subsequent successes motivated CRP to pursue the commercialisation of electric motorbikes. By the end of 2011, it had produced a mock-up for the EICMA (Esposizione Internazionale Ciclo Motociclo e Accessori) show in Milan, to promote what was then the new idea of e-motorbikes.
Positive feedback garnered at the EICMA spurred further investment into that work, so in 2012 CRP began securing long-term suppliers for its e-mobility components and investing in a working prototype to show at EICMA 2012.
This prototype used all-new designs for the battery pack, frame, swingarms, motor housing and fairings, with extensive 3D printing and CNC machining by CRP. It also incorporated third-party inverters, rotors and stators.
It was test driven by a number of industry journalists in late 2012, after which CRP’s engineers ramped up their work on optimising the electronics. That included the design of its own vehicle control unit (VCU) for managing the motorbike’s powertrain, operations, comms and onboard systems.
“In 2014, CRP split off the electric motorbike team to officially found the Energica Motor Company,” Testoni says. “We started selling our first model, the Energica Ego, by the end of that year, with the first Energica Eva being completed and sold in 2015. Other models followed each year thereafter.”
While the CRP Group still has majority ownership, Energica went public in 2016, to raise funding for expanding its production and r&d capabilities, as well as boosting other departments in key ways. It now employs about 60 people, up from the original team of three engineers in CRP’s racing division.
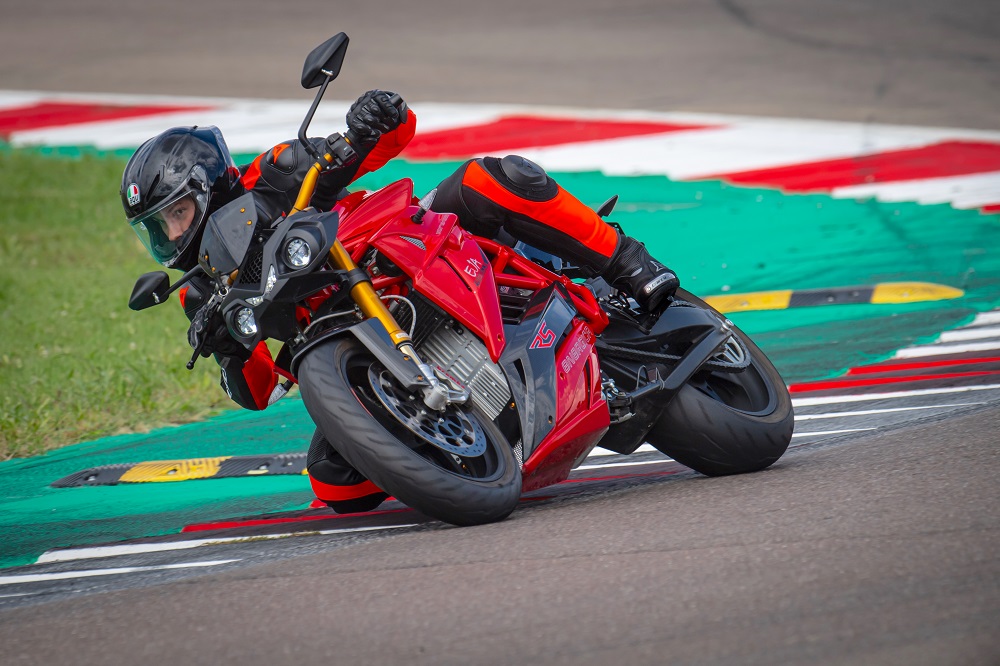
Creating the 2020 Eva Ribelle

Development of the 2020 Eva Ribelle took just under a year. Energica had been inspired to develop a new version of its commercial Eva model that could fully use the energy and power of the company’s newest battery pack, which had been put through its paces in the Energica Ego Corsa motorbikes used for the 2019 MotoE World Cup.
“We tend to update our models annually, in time for the EICMA show each November,” Testoni explains. “We’ll present mock-ups of new models at the EICMA, then develop prototypes and iterate them to production readiness in the subsequent first or second quarter.
“At EICMA 2019, we introduced our new battery pack for all three of our bike series, for users who wanted more range while still selling the original versions with the standard packs. The Ego became the Ego+ and the SS9 became the SS9+, but for the Eva we decided to do a complete redesign.”
Compared with the original 2015 Eva, the 2020 Eva Ribelle was planned to feature a number of changes. For example, while the original Eva’s bodywork was made largely from carbon fibre, the new bodywork has been made predominantly from plastic, to improve the repeatability of its manufacturing as well as reduce its production costs and lead times.
To lower the overall weight of the model by 15 kg compared with its predecessor, redesigns were made to the rear subframe, and the onboard charger was swapped for a lighter system. Further, smallerscale modifications were also made throughout.
“For new models, we typically start with the design team focusing on the fairings, and the mechanics team optimising the frame, seat and positioning of parts,” Testoni says. “That is so the teams can coordinate their work to ensure the outer and inner sections fit each other’s constraints.
“The electronics team will then see to the integration, testing and optimisation of new chargers, battery packs and any other parts that we are looking to upgrade.
“Lastly, our technicians put together the prototypes and start testing them to see how they behave at different mileages, speeds, inclines and so on. The electronics and mechanics teams then make adjustments based on the testing feedback, and new prototypes are iterated until we reach production readiness. All of that takes place within nine months, essentially every year.”
About 80% of the testing on the Eva Ribelle was performed on roads in real-world conditions, while the other 20% or so was divided between static tests – for firmware and components, charging performance and other electrical parameters, for example – and trials on dynamometers.
Shock, vibration and environmental trials of individual components were performed in accordance with homologation processes by external companies, to achieve European certifications for safety and performance prior to sales.
To that end, the Eva Ribelle was also shipped to a company in Spain for testing its range, braking and lights on a European-certified dynamometer.
“We also do extensive structural testing in-house, since we’ve already done all the calculations for FEA in CATIA,” Testoni adds.
“But we need to be sure they’re correct, so we give our external testing partner our data on test set-ups and loads, which they feed into their machines and then proceed with their structural trials.
“Those consist of ‘pull’ tests on the rear subframe, simulated crashes at the front, applications of lateral forces, and many others.”
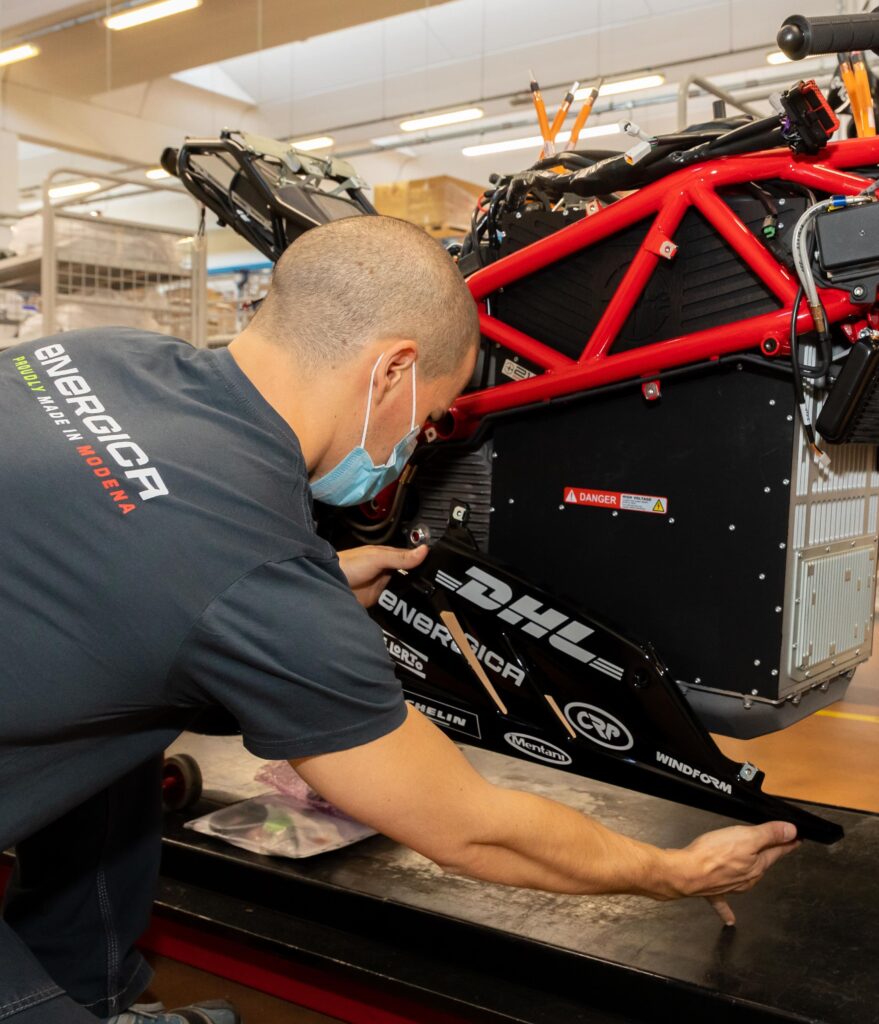
Vehicle architecture
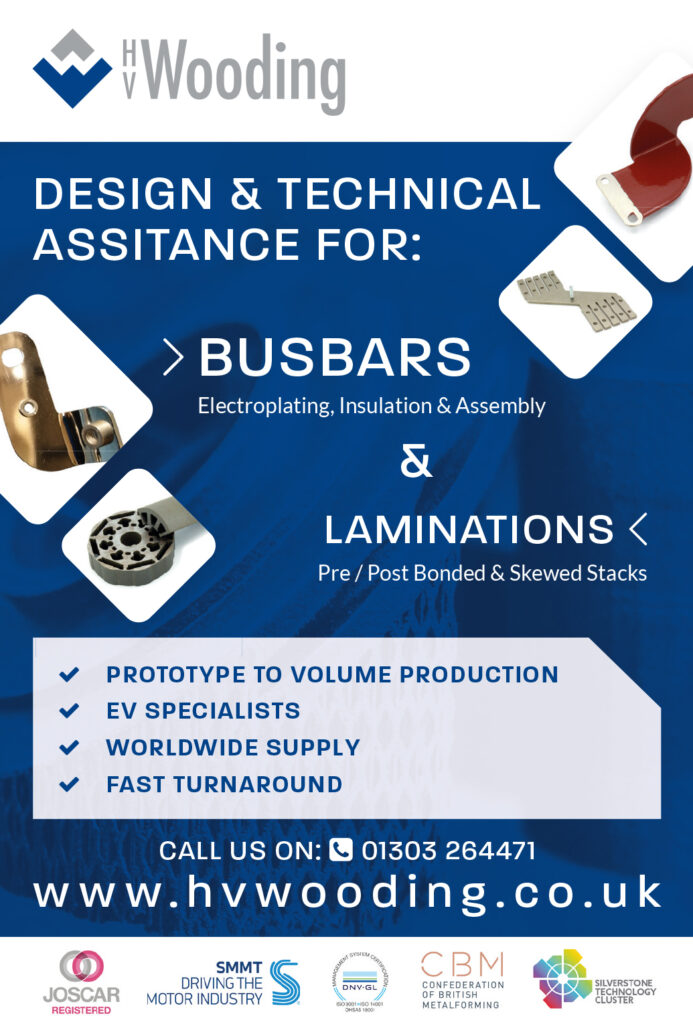
Designing an electric motorbike entails tackling several challenges that conventional IC-engined motorbike manufacturers don’t have to contend with.
For one, given the ‘youth’ of the world of electric motorbikes, there are fewer points of historical engineering reference upon which to draw inspiration or take caution when making design choices. For example, designers and engineers cannot simply swap out fuel motors and tanks for their electric equivalents and hope for the best.
Testoni explains, “As well as carefully considering where to fit each component and how the connections between them will be routed, you still need to balance the weight distribution across the bike. You need to end up with something you can manufacture at scale while still improving the range each year. That’s the real sticking point – customers always want more range.
“Fortunately though, the technology for small batteries has improved to the point where the range achievable by EV bikes is almost comparable to petrol powered sport bikes.”
Starting at the front, the battery pack is installed just behind the forward wheel, taking up space from the bottom of the motorbike to about half the height of a standard fuel tank.
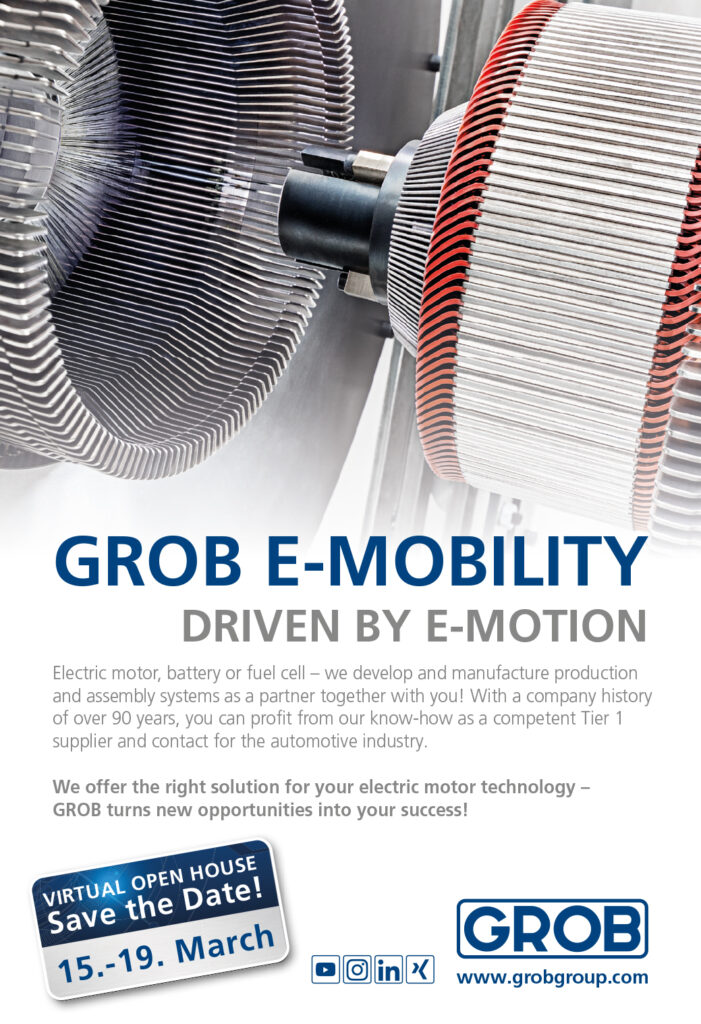
Testoni explains, “By putting the battery there, we get to keep the pack nice and simple, and we found that the rideability and centre of gravity worked just as well as in a petrol bike with this arrangement.”
The VCU is mounted above the battery housing, with the motor inverter installed on top of the VCU. Behind the battery pack, the motor is mounted in a central position within the vehicle frame – roughly between where the rider’s legs would be – to ensure the right placement for the transmission to the rear wheel.
“The two biggest parts to install are the battery pack and motor,” Testoni says. “Once you’ve figured out the optimal locations for those, other parts such as the inverter can be moved around to meet the different needs for cabling, heat and so on.”
The CCS input port for DC and AC recharging are installed in the rear subframe, beneath the driver’s seat. The onboard charger is mounted below the midpoint, between the driver’s and passenger’s seats.
From early on, the Eva Ribelle’s frame has been designed for easy access to, and removal of, the battery pack. It was found that otherwise, routine maintenance would require disassembly of the entire motorbike.
In the present arrangement, the battery pack and motor are bolted together, the forward frame is enclosed on either side of those, and the pack and motor housing are both fastened to the frame. Overall, it is estimated that it takes 30 minutes to remove and then disassemble the battery pack.
The Eva Ribelle’s main structure is built on a tubular trellis frame cast from high-resistance steel, both for structural strength and for mounting some parts. The inverter, for example, is fixed to one of the pairs of tubes, in addition to being bolted to the VCU.
The original race bike was built from aluminium – a popular metal for its strength-to-weight properties but too expensive to use in casting the kind of frame Energica wanted.
“Also, when something went wrong with an aluminium casting, we often found we had to throw away the whole part – you can’t make a cost-effective EV if you have to throw away and replace its main structure every time there’s some damage or you want to make a change,” Testoni explains.
“With this steel frame though, if you want to modify something it’s relatively simple to weld a new part in a new position. It’s not much heavier than a normal motorbike’s aluminium structure, because the tubes provide all the support we need at just 1.5 mm thickness or thereabouts.
“That said, the swingarm is cast as a single piece from aluminium. It’s quite a complex part, but once cast it’s very robust and lightweight. It does not need any welding, and it handles the torsion and bending needed for that part very effectively. The wheels are also made from cast aluminium.”
The plastics used in the cowls, fairings and fenders are mainly polypropylene (PPE) and acrylonitrile butadiene styrene (ABS), with injection moulding or thermoforming used to shape the different parts as needed. The former technique is more costeffective for large quantities of parts, while the latter is better for small batches or one-off parts requested by individual customers.
Testoni adds that fibreglass-reinforced polyimide has been used for the front mask for increased stiffness, and PPE for fenders, while the lower tank covers are made from ABS.
Battery technology
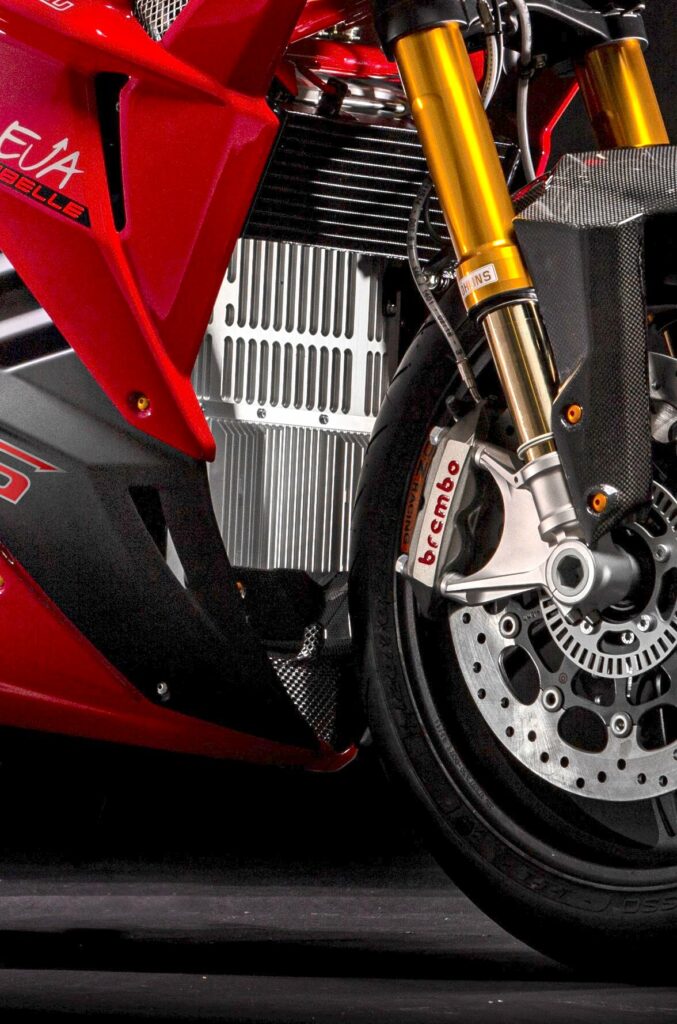
As mentioned, the 2020 Eva Ribelle uses the company’s latest battery pack, which incorporates two strings of batteries connected in parallel, each of which consists of 81 cells connected in series.
The full weight of the 21.5 kWh pack – including all the cells, enclosure, battery management system (BMS), contactors, DC-DC converters and so on – comes to just under 100 kg. The pack is rated to 300 V, although in practice its operating supply voltage is 296 V.
Energica buys bare cells that are chosen according to its research into the available chemistries, form factors and energy parameters, before constructing the modules and packs to designs that have been simulated and optimised by their engineers.
“We use pouch-type cells in this pack,” Testoni remarks. “I’ve always had a strong preference for this type, even though much of the industry has long insisted that cylindrical cells are the best compromise between manufacturability, safety, energy density and so on.
“You can see nowadays though that much of the automotive industry is switching to the latest generation of pouch cells, which have a very similar energy density to the newest cylindrical cells.
“What’s more, the cooling of pouch cells is easier than with other types, and the overall power density can be better too because it’s easier to pack the cells among each other and the BMS.
“They may need longer packaging and assembly times than a fully automated factory line for cylindrical cells, but the end result for the user is a more energy-dense battery that makes the best possible use of space out of any available cell type. Cylindrical cells are very good, but there’s always a lot of leftover space between them.”
In Energica’s previous generation of battery pack, the choice of cell gave a specific energy rating of roughly 170 Wh/kg, whereas the newer one provides 225-230 Wh/kg – an increase of more than 32% in the energy-toweight ratio. There has been no change of chemistry, however; both the older and newer packs use nickel manganese cobalt (NMC) cells.
Although the company has experimented with other chemistry types, it says NMC has always had the best qualities. For example, tests of lithium cobalt oxide cells returned higher specific power measurements, but the cells were less stable and therefore unsafe. Lithium iron phosphate was also tested but could not provide the necessary energy or power densities, and NCA (nickel cobalt aluminium) performed well but was only available in cylindrical form factors.
“We also looked at lithium titanate [LTO] cells, but LTO is best mainly when you need to charge and discharge repeatedly and rapidly – hardly ideal for a commuter or city motorbike,” Testoni adds.
“For many EVs, the subject of chemistry choice is now down to which variant of NMC to pick – such as NMC 622 or 811 – and whichever can reduce the cathode’s proportion of cobalt and increase that of the nickel to get better energy density.
“Solid-state NMC batteries might be the real game-changer, for both energy and safety. We’re already testing prototypes of some. They are at a very early stage but the technology looks very promising so far. Once we can balance safety and stability with manufacturability it’ll mean a big step forward for EVs, but that might still be a few years away.” Energica’s in-house battery testing facilities include climate chambers, resistive load banks, battery cycling test benches and more.
“It is the same groups of tests we perform on different cells at different temperatures, repeatedly measuring critical parameters like energy capacity for losses over cycles,” Testoni notes. “That’s an especially important process to have, because the world of pouch cells doesn’t really have industry standards.
“When you choose a pouch cell, you essentially have to make a battery pack for that cell from a blank sheet, and if you’re building an EV, you need to design a second pack architecture in case something turns out to be wrong with your first choice. It’s very different from 21700 or 18650 cells, which have largely identical standards and designs; pouch cells are designed differently from one supplier to the next, so if you’re forced to change supplier, you’re forced to change your pack.”
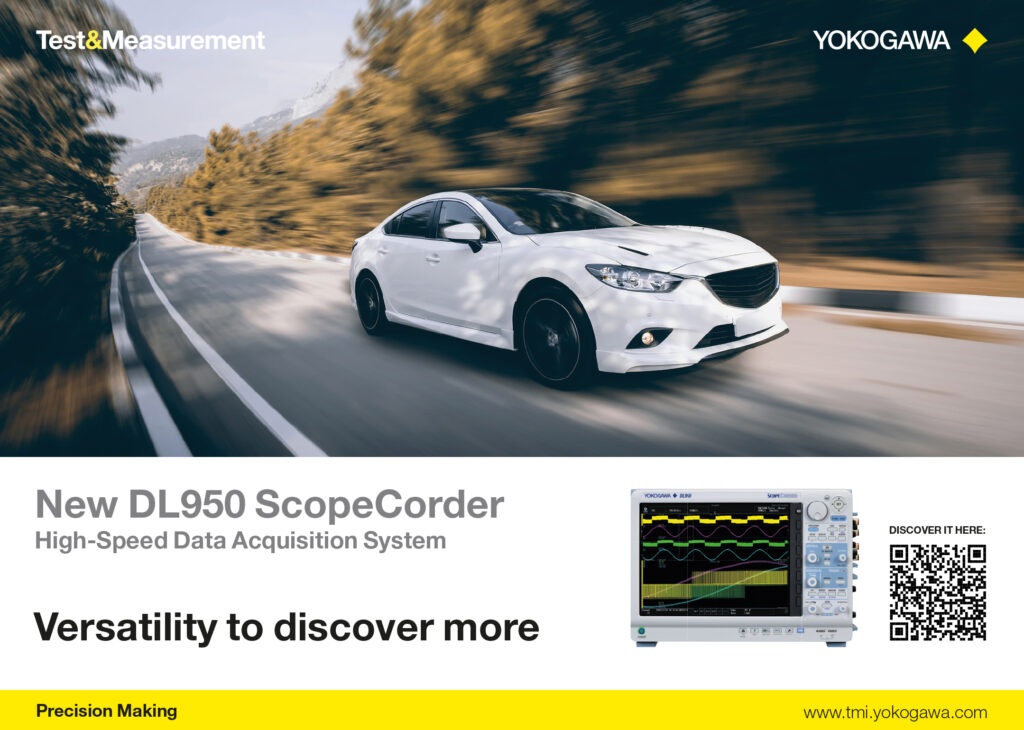
Energica has also created its own BMS – in terms of the electronics and the algorithms – to optimise voltage output and current draw based on temperature, state of charge (SoC) and other key factors, while also prioritising longer-term performance goals such as energy efficiency and lifetime.
“We started with a COTS though slightly modified BMS, but we’re in the process of switching to our own design, which will be finished soon,” Testoni says.
“By focusing on cell balancing and accurate measurements of parameters like SoC, voltage and current, we hope to migrate most of the intelligent battery management decisions – those relating to opening and closing the contactors, or safety-critical functions, for example – over to our VCU. That will simplify the BMS and concentrate its accuracy and reliability on what we really need specifically for running the battery.”
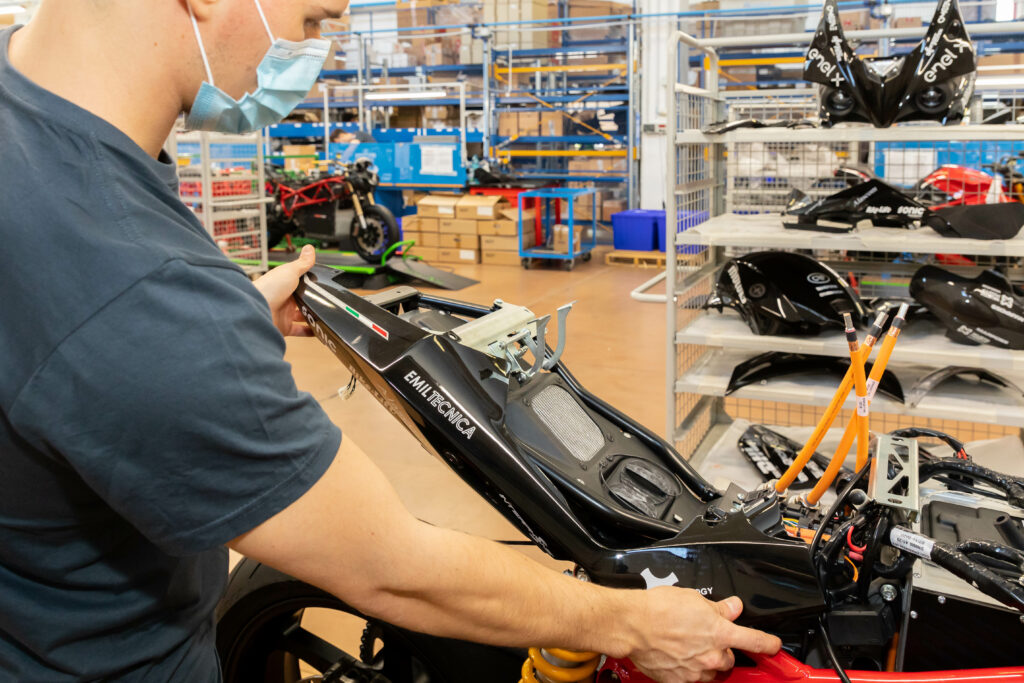
Drive control
The VCU controls almost all the key functions of the motorbike, including the ride-by-wire system, traction control and cruise control, all of which are calculated according to Energica’s algorithms.
The algorithms also provide commands for other critical components, such as supplying torque values for the inverter to target. Meanwhile, the VCU balances other key parameters such as the battery’s SoC and cell temperatures as it performs its high-power switching to control the motor.
In addition to controlling the speed limit of the motorbike – which, as standard, is set at 200 kph on the Eva Ribelle and 240 kph on its Ego bike, for example – the VCU’s algorithms are responsible for defining and enacting the drivetrain’s four riding and regeneration modes.
The four riding modes are titled Urban, Eco, Rain and Sport, and they differ mainly in terms of power and torque distribution. For example, Rain allows only gentle acceleration curves, to ensure safety on wet roads. By contrast, Sport offers the sharpest rates of acceleration.
Urban mode is a compromise between those two, given that urban traffic will oscillate between jammed and empty roads depending on the street and time of day. Eco mode is designed to preserve battery power and maximise range by having the slowest acceleration rates, as well as limiting the speed to 90 kph.
“Of course, someone could be in Sport mode and just choose to drive very slowly, and wind up with the same range as in Eco mode,” Testoni says. “Specific energy consumption depends most on how much torque you use, and acceleration requires torque.
“The modes are there to help riders limit and balance their use of the battery’s energy, not to miraculously supercharge their speed or unlock extra range that the battery might have otherwise kept from them.”
The four regeneration modes are High, Medium, Low and Off, and refer to the energy recouped by each mode and how the braking behaves relative to on an IC-engined motorbike.
Testoni explains, “When regen is off, the Eva’s braking feels similar to when braking a bike powered by a two-stroke engine. Low regeneration is like braking with a four-cylinder four-stroke engine, medium regenerative braking is like a three-cylinder, and high regeneration is as a two-cylinder and can allow you to coast down to a complete stop without needing the brakes.”
The VCU also controls the six different traction modes, which are safety-related and determine the level of freedom the traction system gives the rider. For example, Level 6 is described by Testoni as “the most invasive – as soon as the VCU detects some slip at the wheels at Level 6, it will start to slow and put corrective limits on speed and handling to keep the rider from injuring themself.
“Level 1 is the least intrusive: it will leave full control to the rider unless a lot of slip is occurring. Some riders will want to tackle corners quite hard, and some will find the VCU’s AI uncomfortably intrusive, so we want to give them the freedom to choose how much the bike helps them.”
Included in the traction control system is a patented electronic assisted braking system designed to provide an antilocking capability at the rear wheel. It is activated when the throttle is closed.
This system was developed out of a concern that, on rainy days, riders on wet slick-tarmac roads might be in danger of falling or losing control, especially when closing the throttle to brake while using the highest regenerative braking mode.
“On a petrol bike you’d pull the clutch, but this bike has no clutch, so one of our engineers developed this system,” Testoni says. “The VCU calculates the speed differential between the two wheels while regeneration is happening, and if necessary it lowers the percentage of regenerative torque to the rear wheel to stop it from locking.”
Also, CAN is used as the interface bus between the VCU and its connected systems. It includes a patented system for encrypting and decrypting information, and extensive shielding on all HV and LV cables; the impedance control on the CAN bus wiring is set to 120 .
“The amount of shielded wiring we’ve used in this set-up maybe isn’t as efficient as it possibly could be in terms of weight and costs gone into cable harnesses, but it hugely improves safety in terms of minimising EMI,” Testoni says.
“We’ve tested the wiring arrangement and each individual hardware component in anechoic chambers and across every mode of operation – as required for Italian homologation – to make sure we never accidentally have a stray wire acting as an antenna and interrupting the smooth running of the bike.”
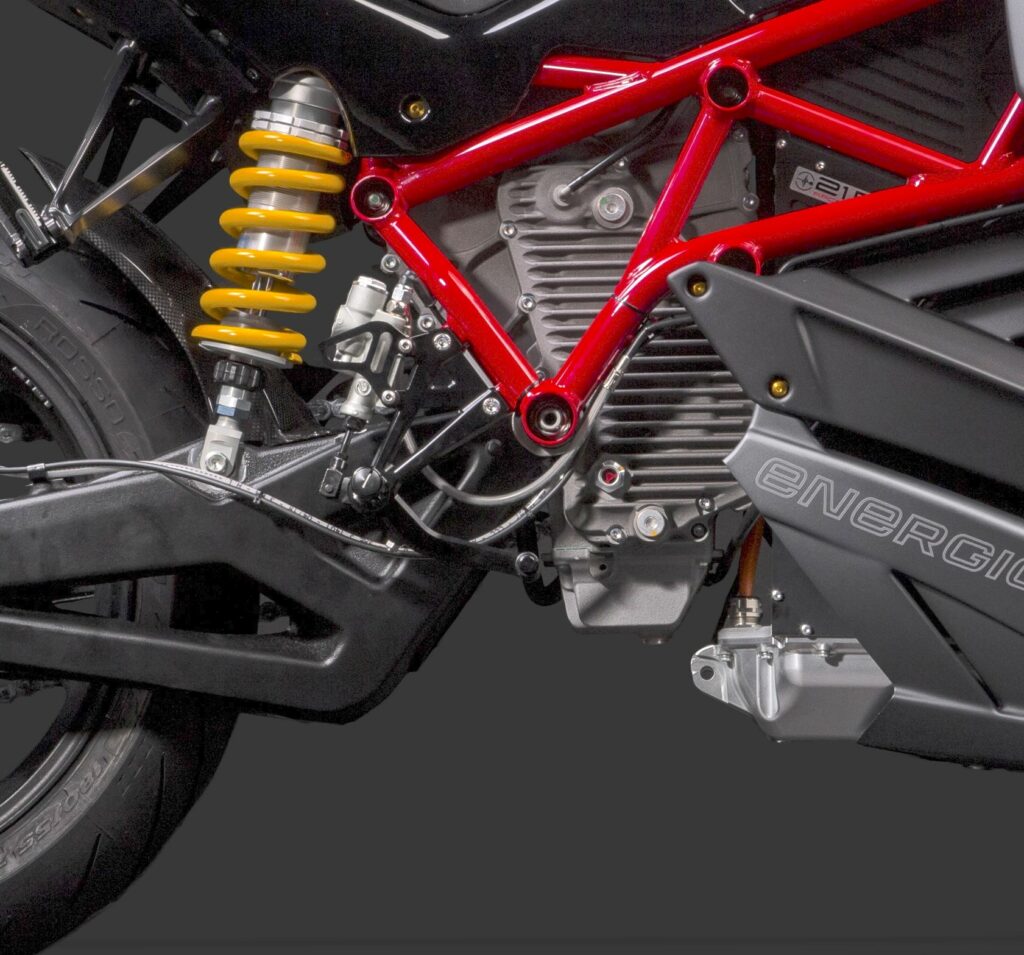
Drivetrain
As discussed in our Dossier on the Lightning Strike, Lightning Systems selected a radial-flux AC induction motor for the bike’s traction, citing greater manufacturing costeffectiveness than permanent magnet AC (PMAC) motors as well as lower failure rates, since induction motors cannot be demagnetised in the way permanent magnet motors can.
Energica however has designed the Eva Ribelle to use a radial-flux PMAC motor with an internal rotor and external stator, for several reasons – chief among those being power and torque. The company sees PMACs, particularly those with internally mounted permanent magnets, as the most power-dense traction solutions on the EV market.
“Of course, they are a little less efficient at high speeds than induction motors, as PMACs need more current to balance for the counter-electromotive force that builds up linearly with speed,” Testoni says. “But for the kind of motorbike we want to create, the 30% increase in power density – and hence the power and torque – you can get from a PMAC is worth it.
“In practice, we’ve experienced no difference in failure rates between asynchronous and synchronous machines. If you use proper cooling, and carry out regular maintenance checks and monitor the motor’s health, each will last just as long as the other without any problems.
“We’re also seeing some interesting technological advances in permanent magnets that stand to significanly lower the high costs typically associated with rare earth elements, such as hybridised systems that combine elements of both kinds of e-motor to reduce the costs compared with PMACs and gain efficiencies associated with either type.”
A radial-flux design was also chosen over an axial-flux machine owing to the former’s general advantages in weight, torque and packaging, this last factor being especially important given the limited space for fitting a wide axial-flux motor inside a motorbike frame.
In addition, the higher voltages required to reach top speeds with axial-flux designs were seen as a disadvantage for the power architecture Energica wanted.
The motor’s top power output of 107 kW is achieved at a speed of about 5000 rpm. Between the motor and the rear wheel is a single-speed transmission system that uses straight cut steel gears, specially designed not just for mechanical strength and long life but also to help reproduce the sound a conventional motorbike makes when revving, given the importance of such acoustics to customers.
The transmission starts with a primary gear reduction, which is set at a ratio of about 2:1; as the e-motor driveshaft spins at 5000 rpm, the driven sprocket thus spins at 2500 rpm. The sprocket then connects to a secondary reduction that consists of a front sprocket, a rear sprocket and a chain.
“The front sprocket has 16 teeth – 15 if it’s the RS version of the bike – and the rear has 44, so the secondary reduction is 2.75:1,” Testoni says.
“The transmission’s total reduction is just over 5:1. If the motor is producing 107 kW and spinning at 5000 rpm, the rear wheel will be turning at about 1000 rpm, and that gets you your 200 kph top speed.”
Power electronics
As mentioned, the Eva Ribelle’s DCDC converters are mounted inside the battery pack. They are 600 W systems and are based on an in-house design, for stepping the 300 V battery output down to a 12 V supply. That latter voltage is suitable for powering the VCU, horn, charger control system, user interface and all the lights on the bike.
The onboard charger is a COTS MOSFET-based system, rated to charge at up to 3.3 kW at 340 V and with an operating current of 11-12 A.
The inverter on the other hand is based on silicon IGBTs. It is a 400 V system rated at a typical efficiency of 97%, with a peak power of 120 kW and up to a maximum of 400 A.
“For the future, we’re looking into all the different power transistors, especially to see how we might improve the performance and management of our inverters through something like silicon carbide or gallium nitride,” Testoni adds. “We’d first need to see though how we could tackle issues such as the cost, availability, homologation and EMC that come with those new technologies.”
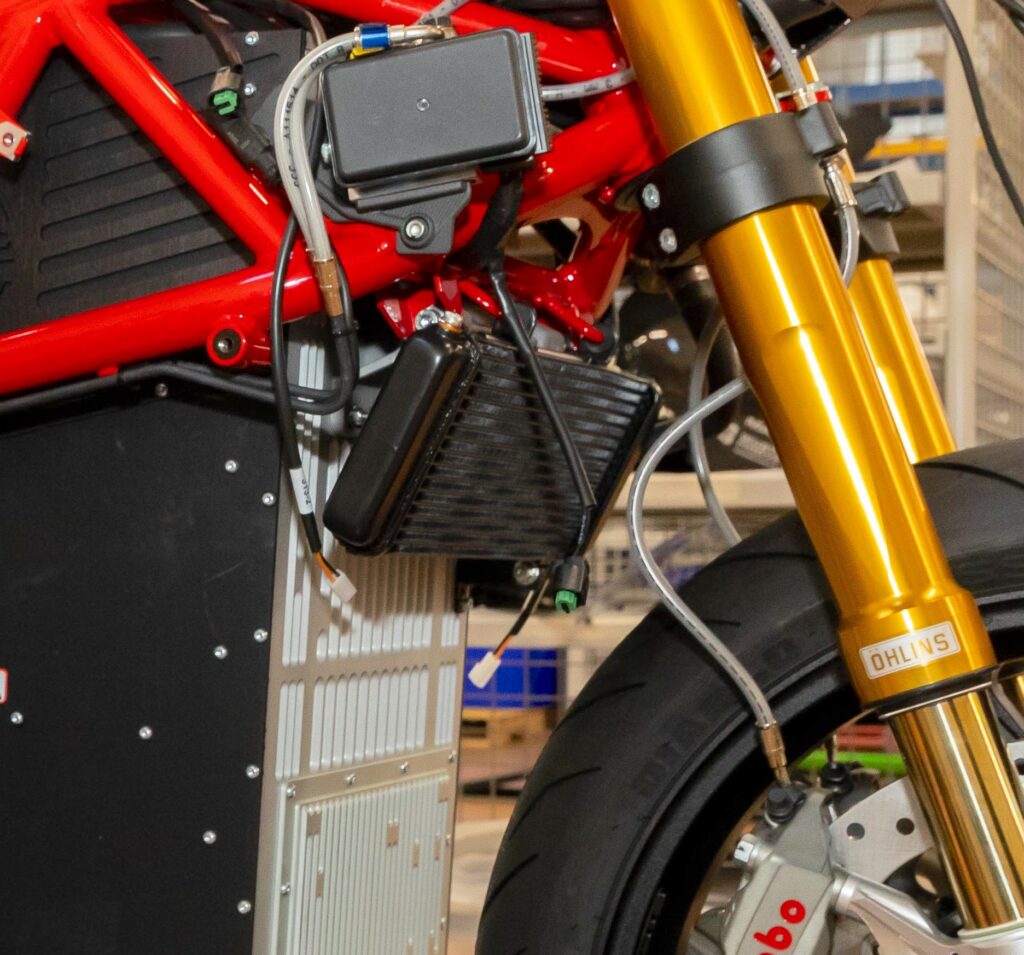
Thermal and lubrication management
An oil pump and delivery circuit is used to deliver oil to the motor for cooling, as well as to the motor’s bearings for lubrication. “The oil’s dielectric quality means there is no issue with short-circuiting when using oil for both lubrication and cooling,” Testoni says.
“We cool the copper directly, not externally on the stator housing. We spray directly onto the winding, and we also have a hollow shaft in the rotor into which we pump oil directly. That cools the inside of the motor, and oil is also centrifuged to spread throughout and across the outside of the rotor, to spread the cooling effect and also to lubricate the bearings.
“This architecture cools very efficiently. For instance, we paired this system with an external radiator for liquid-cooling the motor on one of our racing bikes, but ended up not even needing the radiator.
“The hollow shaft in particular was something custom that we asked for from our motor supplier, while we designed the housing, the oil pump, how much oil the pump needed to output to provide sufficient cooling and lubrication, and so on.”
An oil sump underneath the motor collects the oil, and the oil pump sits nearby, driven by a secondary shaft that runs off of the motor’s driveshaft. From the pump, a delivery hose runs upwards before splitting into two lines. One goes to the hollow driveshaft, the other connects to the motor housing, the latter being designed with an internal network of holes for distributing oil droplets to the stator windings.
For added safety, the windings are also impregnated with a thermally insulating resin during the motor’s manufacture.
Lubrication of the reduction gears and chain is achieved by housing them inside a separate oil sump, which has cooling fins around it to provide the modest heat sink needed for this area (relative to the greater cooling needed for the motor).
On top of the inverter is a water cooling plate, with a small radiator in the front of the bike for heat exchange and a pump in the return channel from the inverter to the radiator.
Although the inverter does not consistently get hot, the temperature gradients from the IGBTs can be quite steep, so a water-based system is key to quickly balancing the temperature of the inverter between these momentary extremes.
A thermal transfer sheet is also used to bond the cooling plate to the inverter and provide rapid conduction of heat from the unit to the plate.
The sheet is first cut to Energica’s dimensions, and its engineers then simply peel off its outer layers to expose the adhesive that provides the bonding.
“Thermal and adhesive pastes and resins are great, but they’re messy in how they distribute themselves,” Testoni notes. “However, a solid sheet is uniform, flat, easy to handle and easy to remove for servicing or replacing parts.”
The batteries use passive air cooling. The front of the housing is CNC machined with cooling fins, with a clear opening in front of the pack; it sits behind the front wheel, enabling a constant flow of cooling air while riding. An upcoming version of the enclosure will have additional fins cut into the sides of the housing to see if it provides any major advantages.
Testoni notes that this newer enclosure is mainly for internal r&d, as the current housing design has proven sufficient for thermal management in all tests and simulations.
In any case, active thermal management is provided by the BMS, which monitors the internal temperature and administers very slight decreases in power draw to individual cells to cool them down without noticeably affecting the speed or acceleration.
Further passive thermal management is provided by thermal interface pads from Hala, which are made from silicone and fibreglass and are placed between the two battery modules and inside the housing walls.
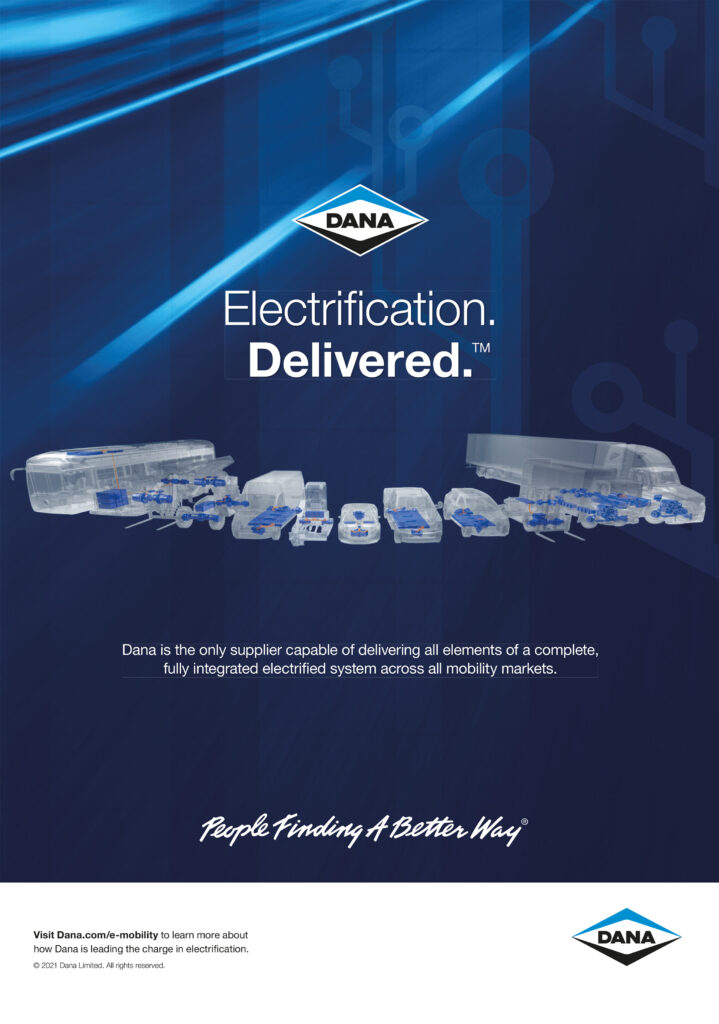
These serve to transfer heat out from the internal parts to the surface of the battery, as well as insulating them by preventing heat from being transferred from one side of the battery to the other.
The onboard charger is fitted with an electric fan, which delivers air directly onto cooling fins on the charger’s housing. The fast charger typically needs no cooling, as its current goes straight to the battery.
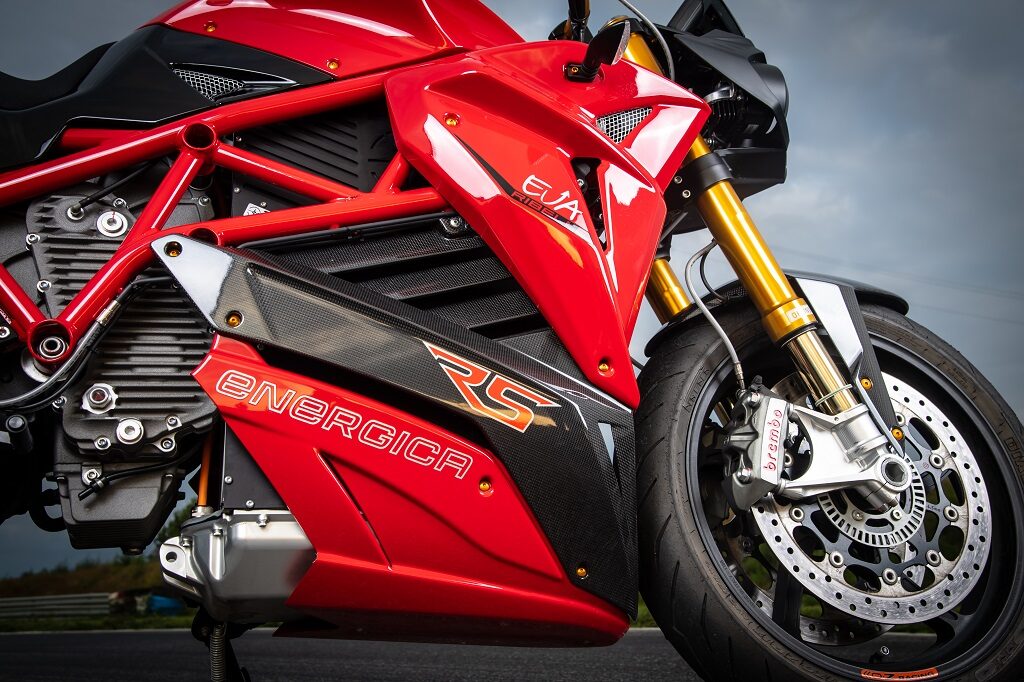
Future plans
At the time of writing, Energica was preparing for the new season of MotoE, its preparations including new targets for performance and overall efficiency, with weight reductions, handling improvements and other fine-tuning to the engineering of the Ego Corsa motorbikes.
The company intends to continue its practice of transferring its technological improvements from the racetrack to the road, so these racebike innovations can be expected to enhance the 2022 Evas as well as the rest of Energica’s range in the years ahead.
Specifications
Energica Eva Ribelle Battery-electric motorbike
Dimensions: 2140 x 1152 x 870 mm
Wheelbase: 1465 mm
Seat height: 790 mm
Maximum power output: 107 kW
Maximum speed: 200 kph
Maximum torque: 215 Nm
Acceleration: 0-100 kph in 2.8 seconds
Maximum battery energy: 21.5 kWh
Maximum range: 400 km
Maximum AC charge: 3 kW, 220 V
Battery lifespan: 80% capacity after 1200 cycles
Some key suppliers
Battery management system: in-house
Battery cells: undisclosed
Busbars: HV Wooding
DC-DC converters: in-house
DC-DC converters: TDK Lambda
Cable glands: Lapp
LV cabling: TE Connectivity
LV cabling: various
HV cabling: undisclosed
Electric motors: undisclosed
Thermal transfer materials: Hala
User display: COBO
Inverters: undisclosed
Manufacturing machinery: CRP Group
Brakes: Brembo
Chains: Regina
Tyres: Pirelli
ONLINE PARTNERS
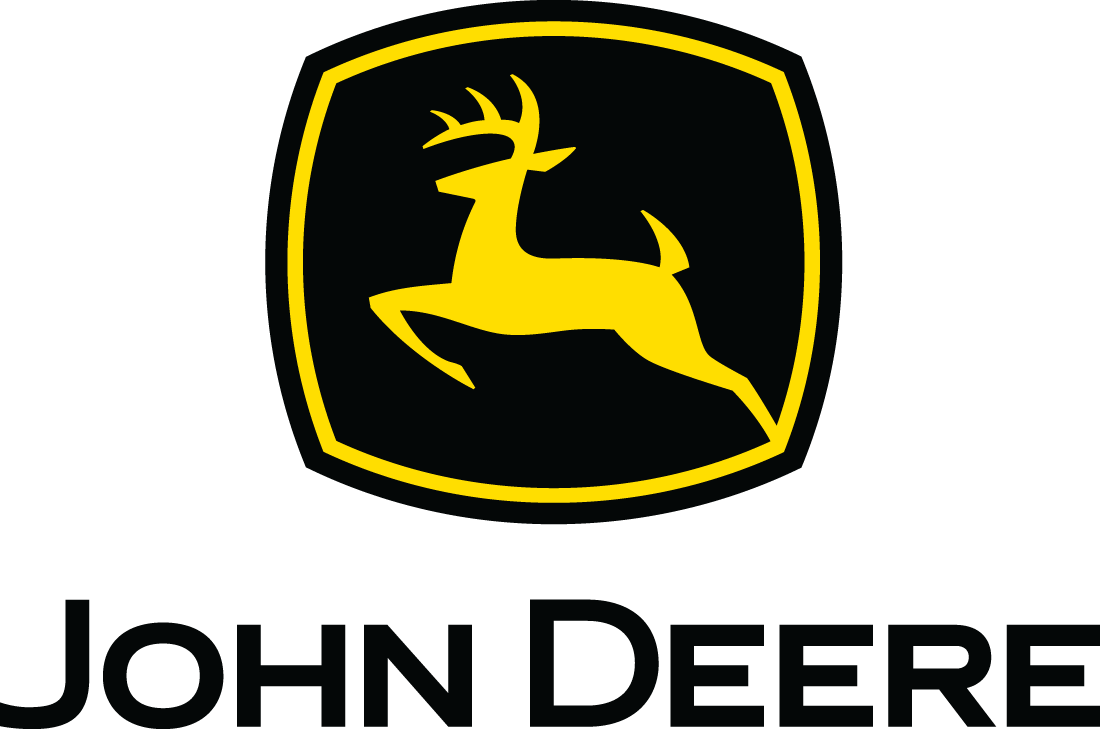
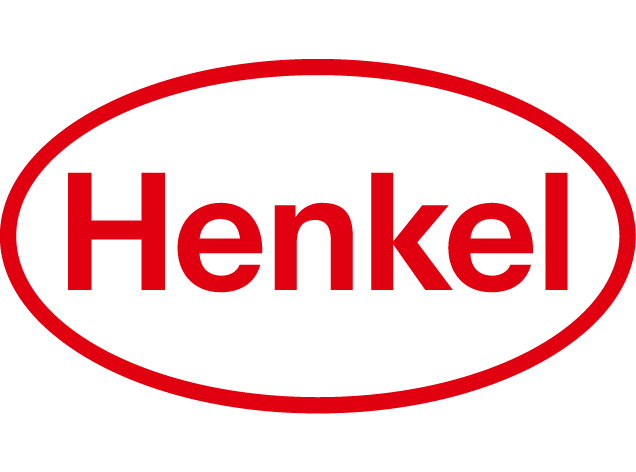
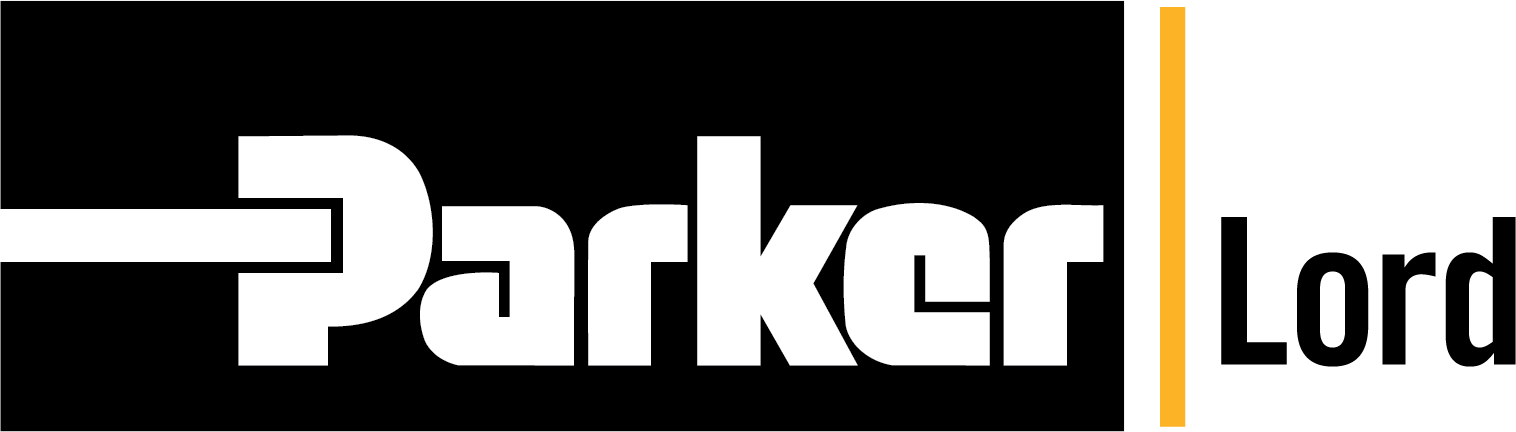
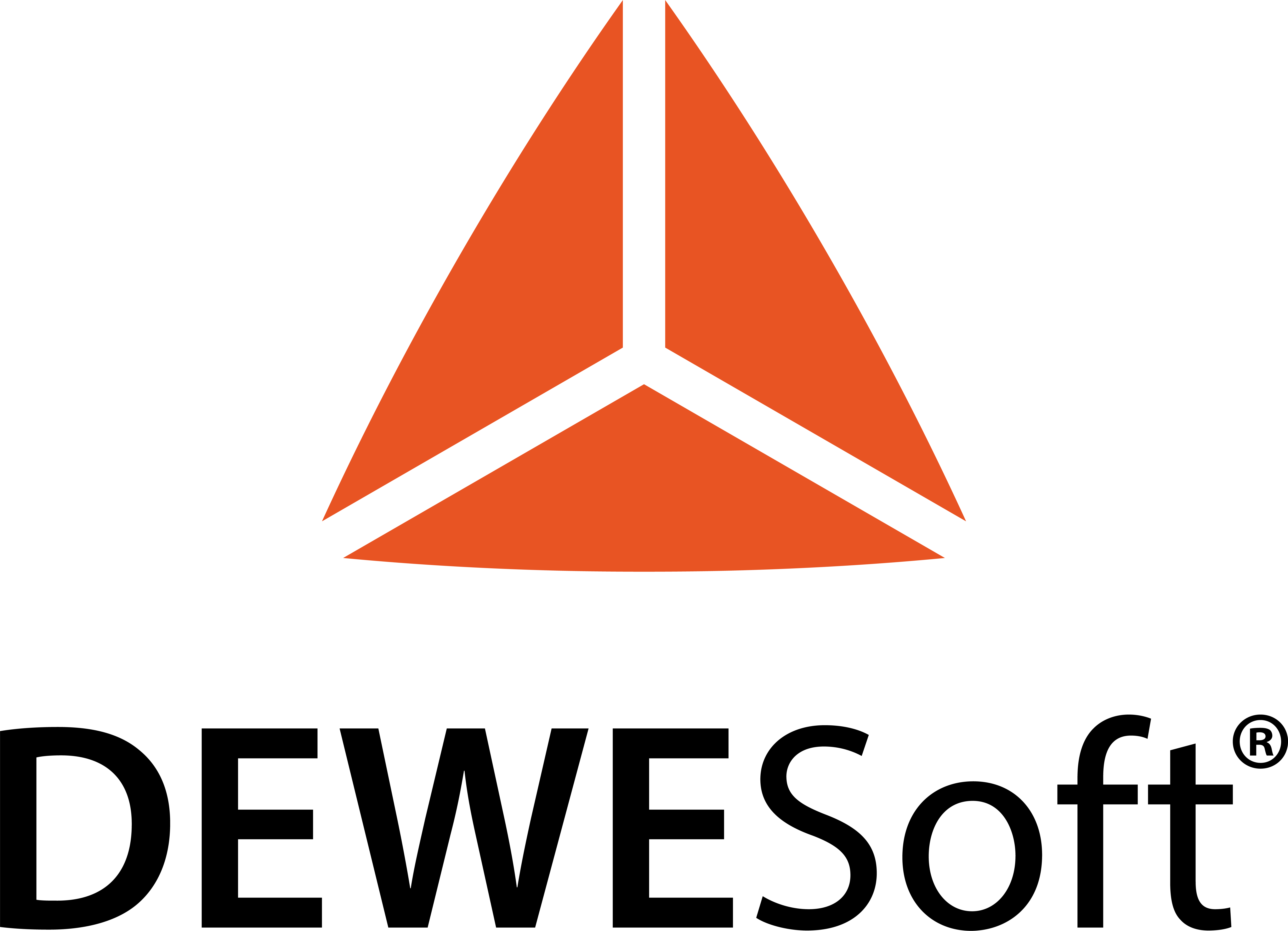
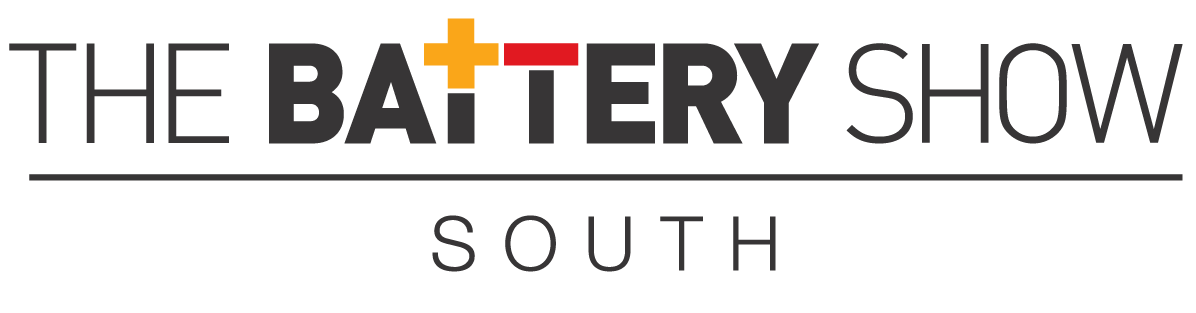
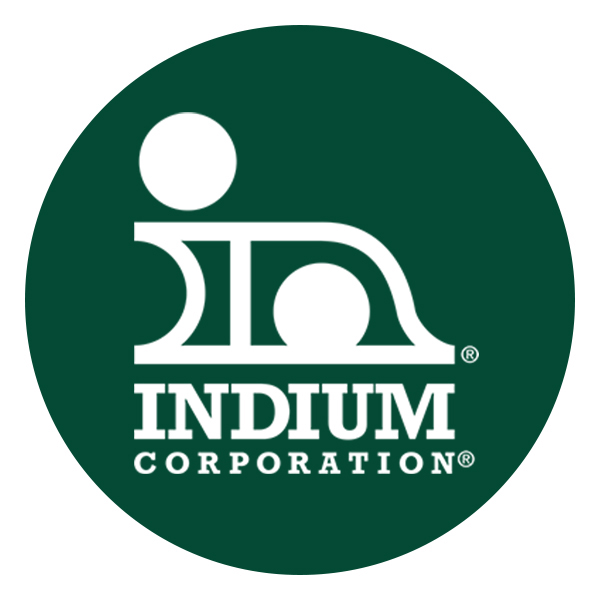

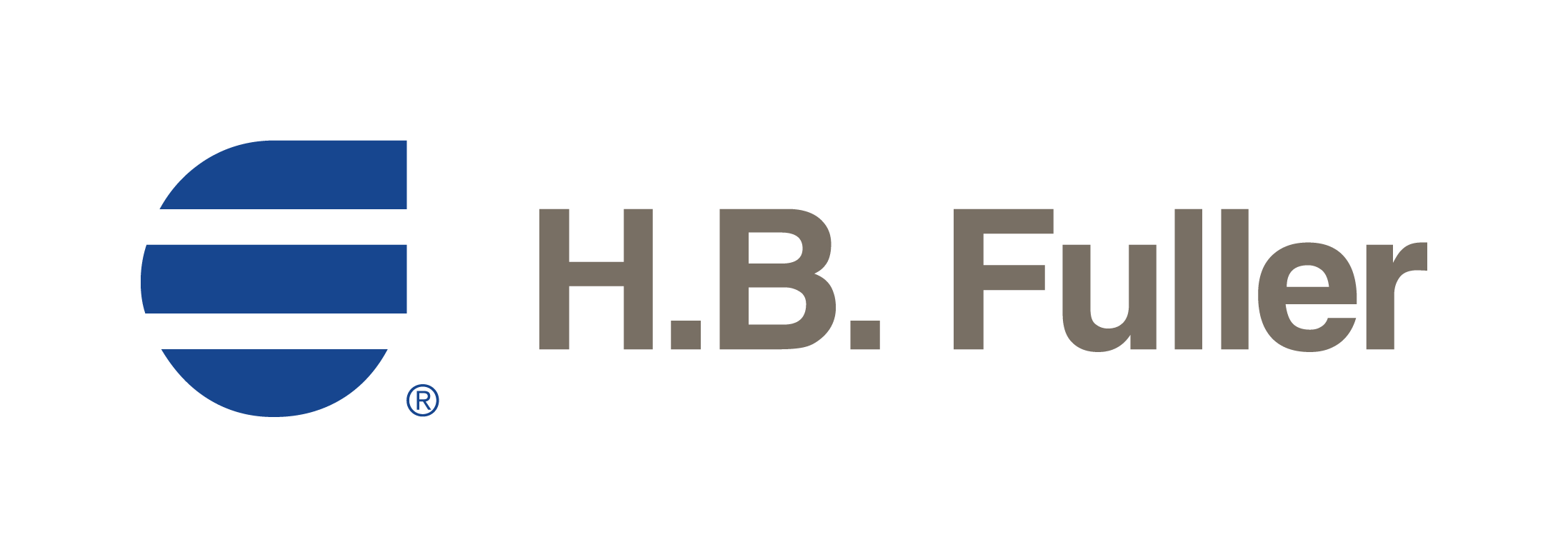
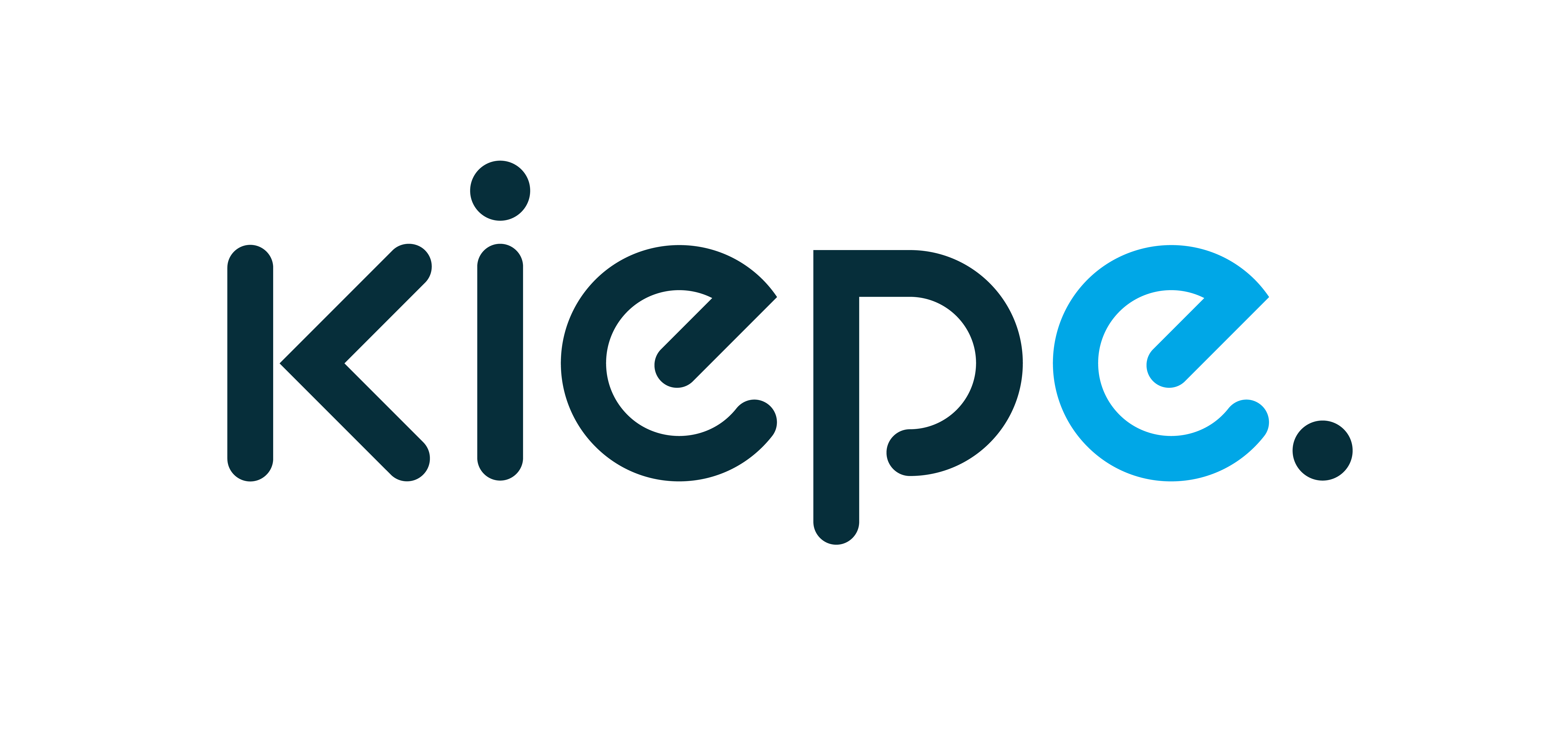
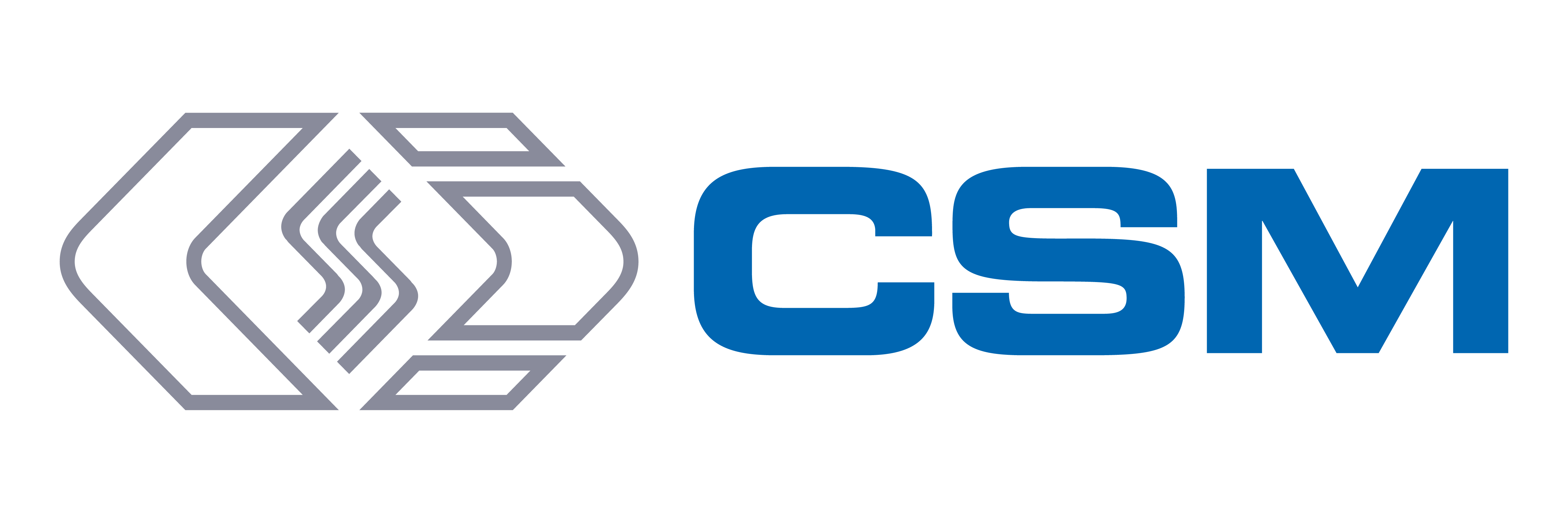