Electrogenic E-type conversion
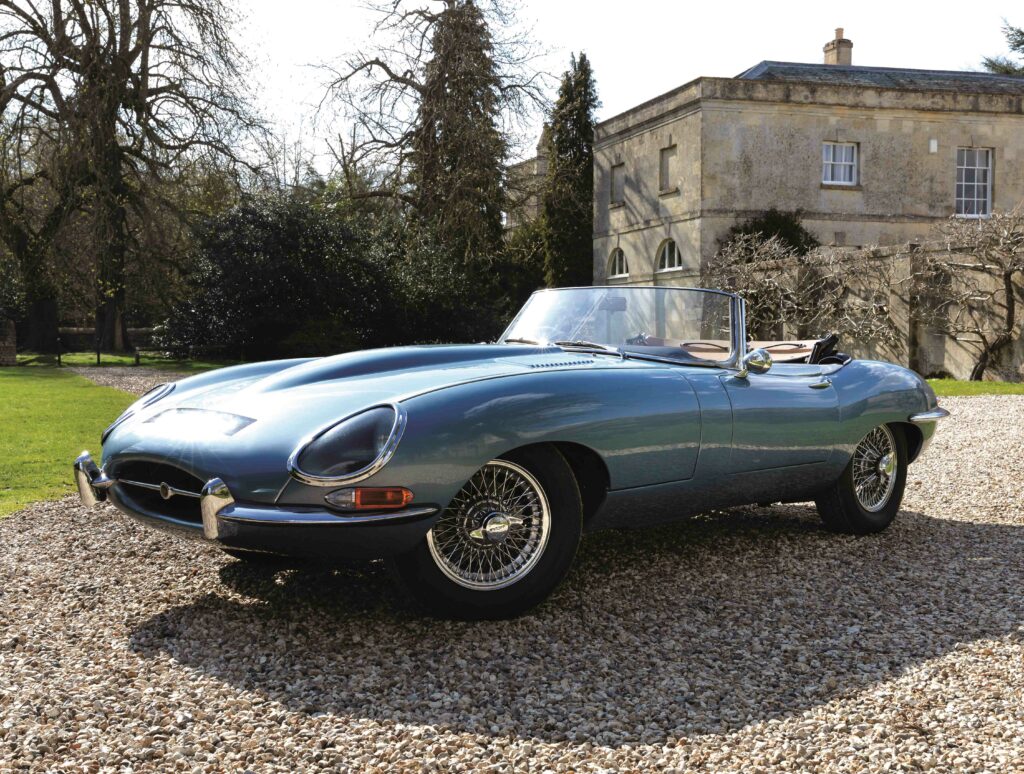
(Images courtesy of Electrogenic)
New kits on the block
Peter Donaldson reports on an electric powertrain developer that undertakes bespoke conversions for classic cars
Electrogenic is a leading developer of electric powertrains for niche vehicle manufacturers. It also carries out bespoke conversions of classics, such as the E-type Jaguar, to electric power and produces conversion kits.
With a background in clean energy and electrical engineering, founder and CEO Steve Drummond started the firm with a small team in 2018, moving into premises in Kidlington near Oxford in 2019. Then the pandemic stymied the original plan to focus on the business-to-business (B2B) approach, supplying powertrains to the EV industry.
“The business customers went away, so we pivoted the company at that time to business-to-customer (B2C) to see if anybody wanted their cars converted and, happily, it turned out that quite a few people did,” Drummond says.
Bespoke conversions undertaken by Electrogenic form an eclectic set of iconic machinery, including: the 1929 Rolls-Royce Phantom II; the Porsche 356C; the Citroen DS; the Volkswagen Karmann Ghia, Beetle and Camper models; and Morgan’s 4/4. Electrogenic now offers conversion kits for classic Land Rovers such as the Series I, II and III, and Defender models, the original Mini, G-body and 964 variants of the Porsche 911, and the focus of this article, the E-type Jag.
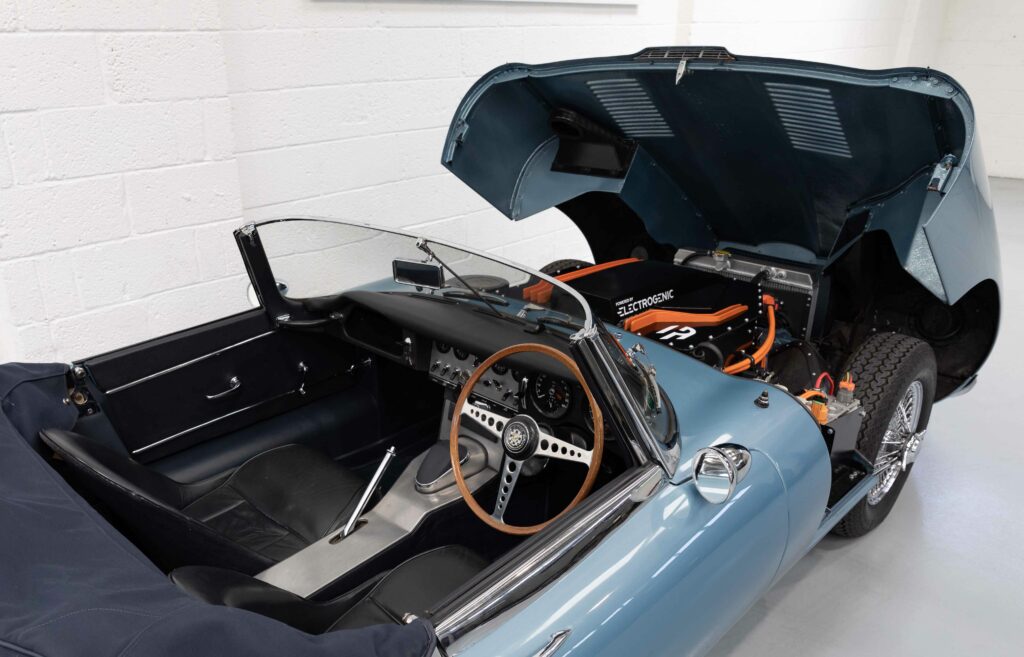
Drivetrain development
Electrogenic continues to expand, particularly in the B2B area, as demand for EV drivetrains from small manufacturers and the defence industry grows. In addition to Drummond, the executive team includes chief engineer Francis Prime, chief financial officer Andy Camoenié and head of brand Vic Crofts. There are 17 employees and the company is recruiting more.
Drummond regards drivetrain development as the core activity, centred on the creation of vehicle-specific battery packs, built up from commercially available standard modules and run by bought-in battery management systems (BMS). However, Electrogenic develops its own Vehicle Control Unit (VCU) technology for high-level control of the entire powertrain, as well as designing printed circuit boards and software for dashboards, body control modules and other electronic components for modern EVs.
In addition, the company designs and builds mechanical transmissions that help adapt electric motors to classic vehicles’ existing driveline components.
The Kidderminster facility covers about 20,000 ft2 across two buildings: one dedicated to mechanical work, and the other for electrical/electronic r&d and manufacturing plus a showroom, offices and vehicle storage. The firm also has a small unit at the nearby Bicester Heritage historic vehicle centre on a former RAF airfield, which is also used for track testing and marketing.
Installation of Electrogenic’s kits in customers’ vehicles is carried out by independent specialists with deep knowledge of the original cars and an established customer base.
“They have a demand from within that customer base for an electric option,” Drummond says. “We train them to fit our kits and we give them all the tools. The kits are manufactured in our factory and are complete, so you have everything you need to install them.”
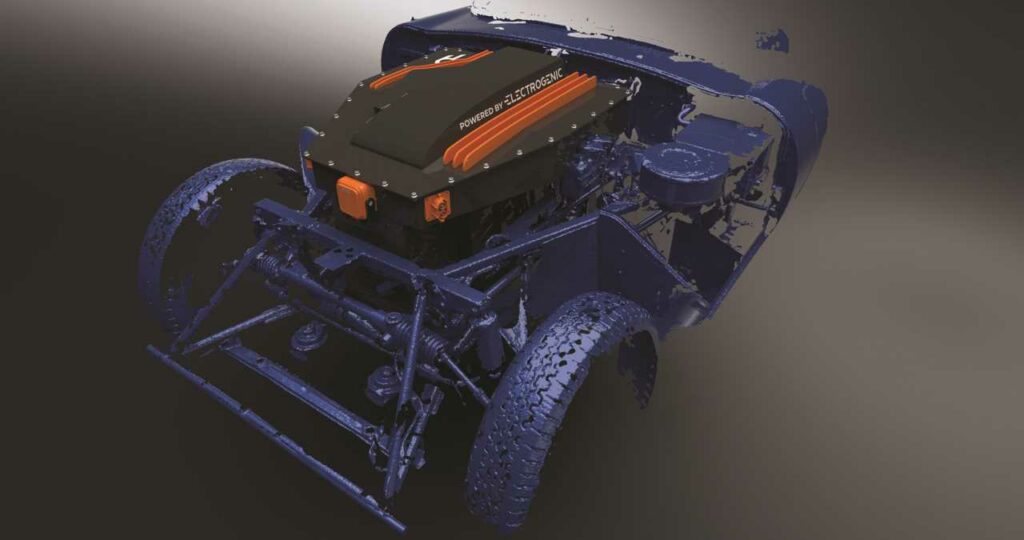
Installation support
Each kit comes with key ancillaries mounted to the major components. “For example, the vacuum pump and vacuum chamber for the brake servo are already mounted to the side of the battery box; the cooling pumps are already mounted and piped up. If you have power steering (the E-type does not), the pumps are already mounted. All of the cables are pre-terminated, the wiring loom comes ready-made and everything just bolts in,” Drummond explains.
During installation of these kits, the original vehicle structure does not need to be drilled or cut, with the main physical tasks being to bolt in the kit and wire up the dashboard. Before they can hand the car to the customer, however, they need to commission it, which involves putting it through a computer-driven checking process.
“We provide them with all the support they need, both over the phone and electronically. We have a plug-in electronic diagnostic unit they use for commissioning the car in a step-by-step process,” Drummond says.
This unit can help with troubleshooting. It picks up any faults in the 12 V wiring, which triggers the safety systems that protect the high-voltage circuits and prevent the car from starting.
“Often, it is something as simple as a brake switch being wired the wrong way round, or something like that. It tells you all that stuff and, when you’ve fixed it, you get green lights, commissioning is complete, and the car can be driven away,” he says.
Electrogenic also provides installers with brand support to give their customers more confidence in the car. “Their customers know they are great at making beautiful E-types, but they might doubt the installer’s knowledge of electric drive, so what they get from us is that ‘Power by Electrogenic’ brand support,” he adds.
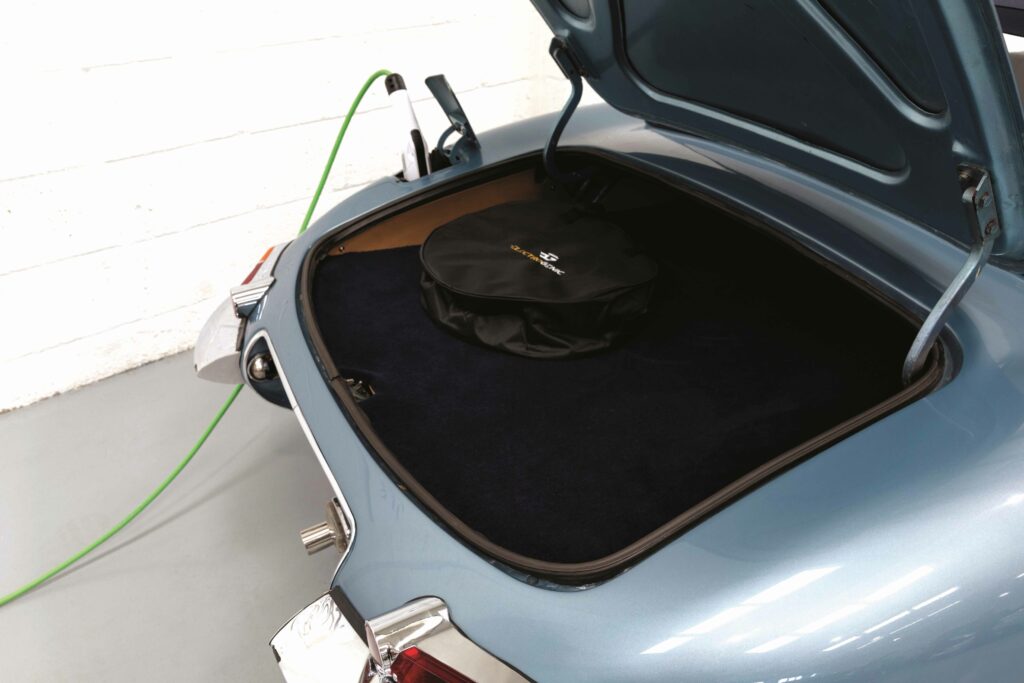
Choosing a candidate
In deciding which vehicles to offer conversion kits for, Electrogenic relies on gauging demand, and early in the company’s life that was expressed by people asking them to convert Land Rovers. Drummond says: “I couldn’t imagine anything further from an ideal EV as they are large, heavy and square, but we said yes, and now we do more Land Rovers than everything else put together.”
In contrast, some classic cars seem better candidates for conversion than others, in part because the original ICE powertrain was not as good as it could have been from the start; the Citroen DS being a good example. “That had a compromised engine and seems ideal for an electric conversion. It is a beautiful car, but it is a very difficult one to convert. We are working our way towards a kit for it, but it isn’t going to be available any time soon,” he says.
One of the many ways in which an E-type differs from a Land Rover or a Citroen DS is that the 3.8 and 4.2 litre straight-six, and the 5.3 litre V12 engines are central to the character of the originals in sound and feel, and such a fundamental change might present an emotional barrier to someone who wants an E-type.
“The motivation for owners differs with different vehicles, but our typical E-type customer is somebody who has at least one example already, but wants one they can drive every day,” Drummond says.
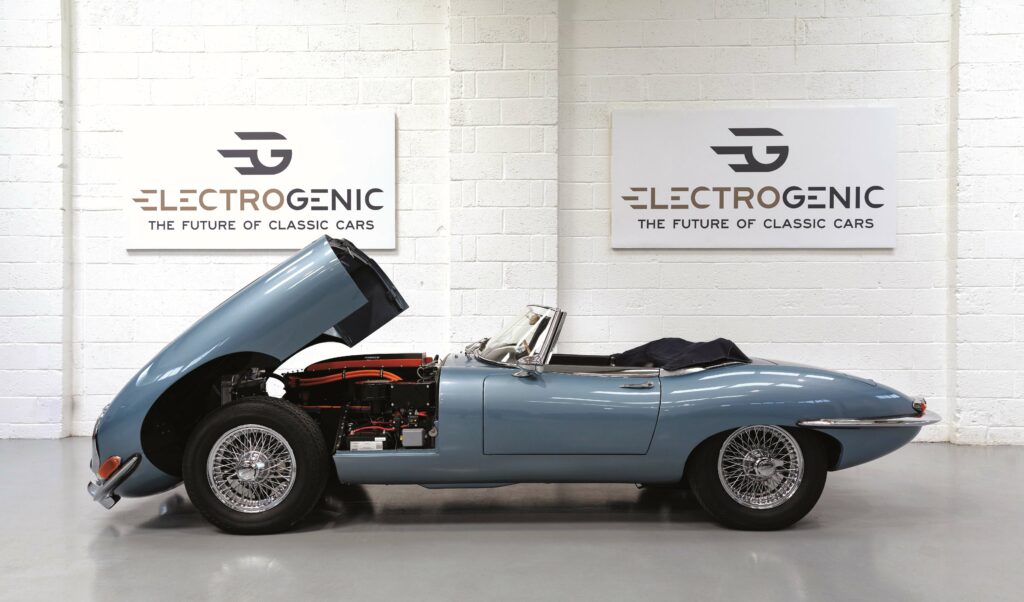
Conversion challenges
As with many classic cars, the E-type presents a challenge in engineering an EV conversion because the space available for the components is limited, despite the car’s long nose hinting at a cavernous engine bay.
“It looks big, but when you open the bonnet there’s very little room in there, and most of it is taken up by the space frame chassis. The original engine was long, but also quite narrow, so fitting the batteries in that space is a challenge.”
In a way, Electrogenic makes life more difficult for itself with its insistence on not cutting or drilling into the original structure. Therefore, all of the new components need to fit onto the mounting points for the parts that have been removed, particularly the engine, gearbox and fuel tank. The different sizes, shapes and positions of some of the new components often oblige Electrogenic to build supporting structures, such as subframes, crossmembers, brackets and mounting plates to bridge the gap between where the new component has to fit and the most convenient original mounting point.
“When you’re just locating something like a pump, it’s no big deal, but when it’s the motor, which has to be supported in the right way in isolation mounts, etc, it can get complicated,” Drummond says.
Electrogenic sources most of the electric drivetrain components from leading manufacturers. Drummond says running the company is very much like running a miniature version of a major automotive OEM.
“We have to have the same processes and it all works in the same way. We have to have all the same parts systems and design protocols, and we work to set standards. In terms of designing the drivetrains, we basically do the same as they do. They buy the motor, the battery modules and the inverter from specialist manufacturers, and then they do the design integration and write the software. And that’s what we do.”
Drummond emphasises that much of the know-how and practical skill lies in areas such as integrating the boxy battery modules into an enclosure that complies with all the applicable safety regulations and enables the resulting pack to fit into an unusual space.
“In some ways, our challenges are greater than, say, Ford’s because they can build the car around the battery, whereas we have to build the battery into the car, which is not so easy.”
Filling the box
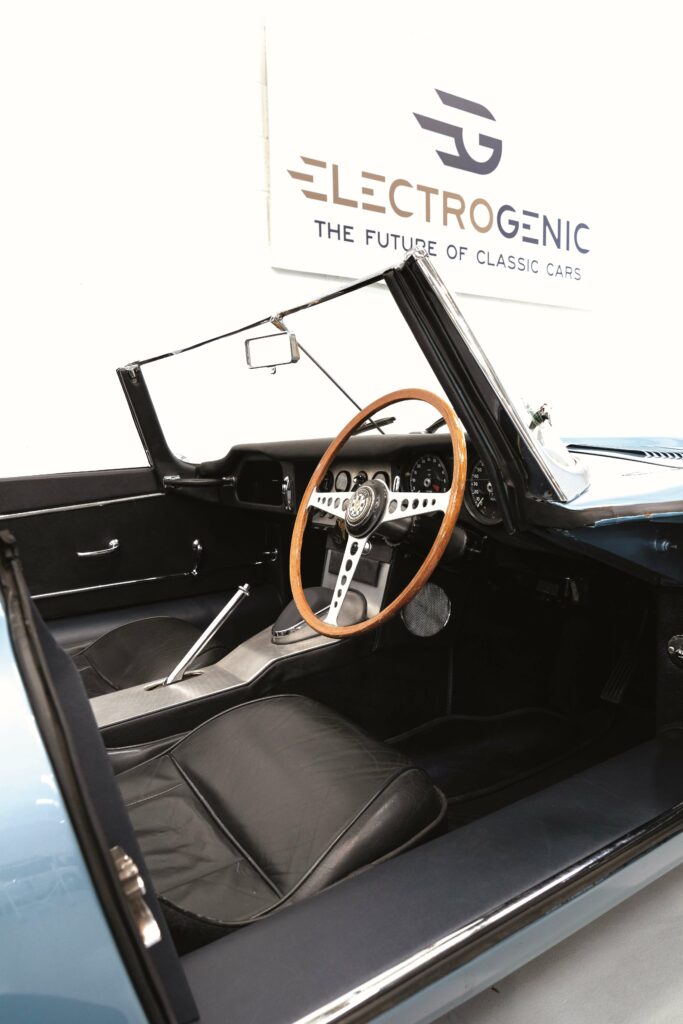
Because of the limited space available and the effort to make installation of the kit as simple as possible, Electrogenics puts a lot of equipment besides the cells inside its battery enclosures. In addition to the interconnects and busbars, there are thermal management system components and power distribution units, for example, which the company also manufactures.
In the E-type there are two battery enclosures, one at the front and one at the back, welded together from 2 mm-thick, laser-cut, mild steel sections. The front enclosure contains all the power-distribution components and the main contactors, along with the above-mentioned thermal management components and the BMS. The front enclosure is bolted to the original engine and transmission mounts, while the rear enclosure is attached to the E-type’s fuel-tank mounts.
Electrogenic has developed “cassette mechanisms”, designed to hold the battery modules in various orientations in different-shaped battery enclosures in different vehicles, and the BMS mounts directly onto these mechanisms. “What you end up with is a beautifully engineered box that has a whole bunch of connections on the side, some for the high voltage and some for the low voltage,” says Drummond.
The firm designed a single-speed reduction gearbox to connect the electric motor to the original prop shaft, which is made by an outside contractor. Offered with a ratio of either 2:1 or 2.45:1, this transmission lets the owner specify a ratio that prioritises either the top speed or starting torque, respectively. This has an extension that bolts onto the original gearbox mounts, and the original prop shaft simply bolts onto that.
The Series 1 and 2 E-types have a stiffener plate positioned at the bottom of the bulkhead, between the engine bay and the passenger compartment. As this plate bolts in between the chassis rails, it is technically not part of the chassis, which has allowed Electrogenics to modify it to support fixtures for the two isolation mounts supporting the drive motor, which sits in the transmission tunnel.
Motor, voltage and battery decisions
There are two options for the motor itself, one sourced from the UK and the other from China – both radial flux units to fit the narrow space of the transmission tunnel.
“One of the nice things about having made all the effort to develop our own VCU software is that it means we can use any motor we like. Manufacturers typically don’t supply their motors with software and often don’t supply the inverter either, so if you don’t write your own software, your options are very limited.”
Drummond says the powertrain design process begins with how you want the vehicle to perform, which drives motor choice. “Motors come in certain operating voltages, and so that the motor you choose determines the operating voltage, you build a battery to deliver that operating voltage.”
While Electrogenic builds EV powertrains that run on voltages from 48 V upwards, most of its off-the-shelf kits run at nominal voltages of 350-390 V, and the sports version of the E-type kit has a maximum of 450 V.
“The envelope for batteries is determined by the physical space in the car, and the extent to which you want to load up the suspension,” Drummond says. “That determines the upper bound on the battery volume. Then, you have discrete steps as you trade-off between motor voltage and how you combine battery modules to come up with approximately the volume and kilowatt hours you’re looking for.
“That gets you to your high-level spec of motor power, torque and rpm, as interpreted by your transmission to give you the final rpm and torque ranges at the wheels. Then, that influences your choice of battery specification, and you go around the loop until you get a combination you’re happy with.”
For the E-type conversion, a nickel manganese cobalt oxide (NMC) chemistry was chosen by Electrogenic for both battery pack options; one with a rated capacity of 40 kWh and the other at 60 kWh, which provide ranges of 140-150 miles and 200 miles, respectively. These are made up of VDA modules of about 6.8 kWh each, which are of a standard size and shape, and secured by the cassette system.
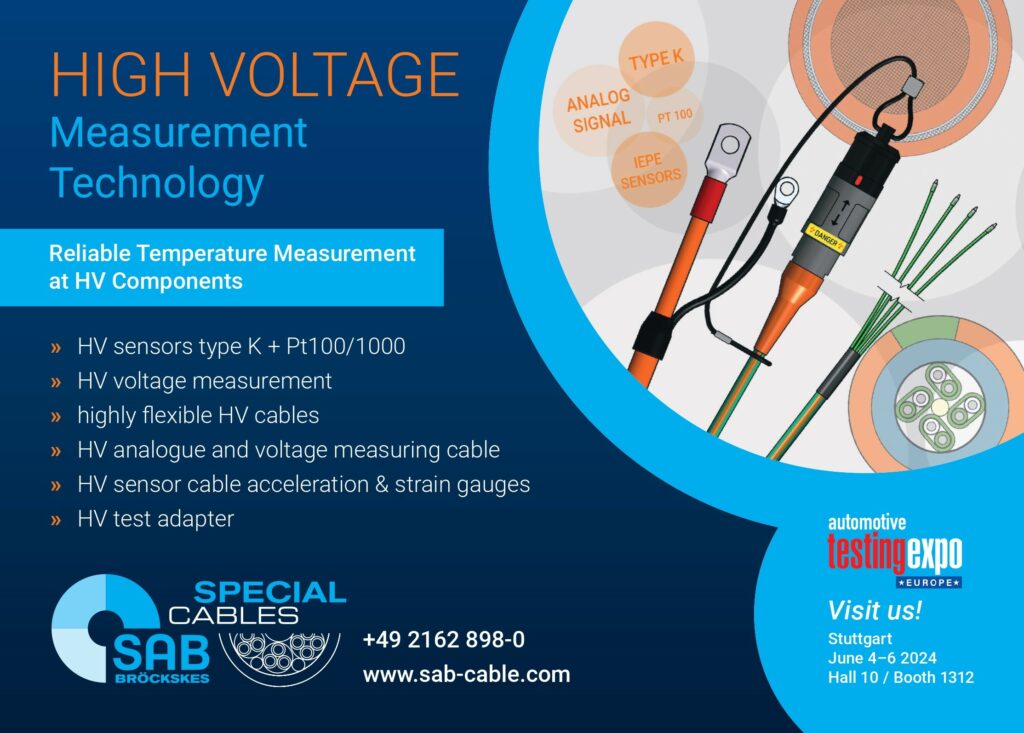
Thermal management & safety
The thermal management system includes cooling plates that slot between the modules with an interface consisting of thermally conductive paste. “To get good thermal conductivity, you need to make sure you don’t have any air in there insulating things,” says Drummond.
A pumped supply of water ethylene glycol coolant runs through the cooling plates, moving in and out of the enclosure through connections to a bespoke radiator.
Electrogenic does not use the original radiators, partly because they tend to be old, and partly because the vehicle needs two separate cooling loops and associated heat exchangers – one for the battery and the other for the motor and power electronics, such as the inverter and onboard charger – while also leaving room for an air-conditioning condenser.
“Obviously, the radiators don’t need to be as big as they do for an internal combustion engine of equivalent power, so that’s the saving grace in terms of weight and volume,” says Drummond.
The company takes a system-level approach to battery and electrical safety, including an industry-standard, high-voltage interlock loop (HVIL), insulation monitoring, and crash switches that open the battery contactors in the event of a severe impact.
The BMS has a ‘master-slave’ distributed architecture. Instead of wires running from every battery cell to a central point, the system has a series of distributed microprocessors balancing the charges among the cells in each module, and reporting states of charge and temperature to the BMS computer over a CAN bus. This enables sophisticated management of the battery while requiring far less wiring.
“We manage the power demands on the battery in accordance with temperature limits and we manage the cooling system, both through VCU processes based on information supplied by the BMS,” says Drummond.
As with the other conversion kits, the E-type has a 12 V electrical system with its own battery, whose main job is to operate the contactors that activate the HV system, of which the DC-DC converter is a part. In normal operation, the DC-DC converter supplies all the 12 V electrics and trickle-charges the 12 V battery, which retains enough energy to keep the car lights on, even if the driver ignores the warnings and allows the traction battery to run down, and it also preserves the radio presets when the car is switched off.
The other major design element is the electronics and control software. “Because that’s our software, we control the whole environment, so we can make it do what we want. You can have different drive modes, although in an E-type the standard EV options are normally fine. We have a sports mode, a traffic mode that gives more re-gen on lift-off so you can drive on one pedal, and an economy mode,” Drummond says. “The system allows you to select modes, but also manages the way the vehicle drives.”
The firm also builds the electronics that control the original dials on the dashboard, repurposing some of them. While the speedometer still shows speed, the rev counter shows the driver how much power is being used and how much is flowing back to the battery via re-gen at any given moment, along with the battery’s state of charge. “The same device can drive display screens, but most of our customers don’t want screens,” Drummond says.
Running on a CAN bus, the instrument control system converts the digital signal’s output by the electric powertrain’s electronics to the analogue electrical/mechanical inputs that the old dials need. For example, the box of tricks simulates the square waves that the rev counter looks for when counting sparks from the ICE’s spark plugs, so it can drive it, even though the square waves now represent different parameters. Drummond says the system takes vehicle speed from the motor rpm and the fixed transmission ratio, and interpolates them into an rpm for the speedometer.
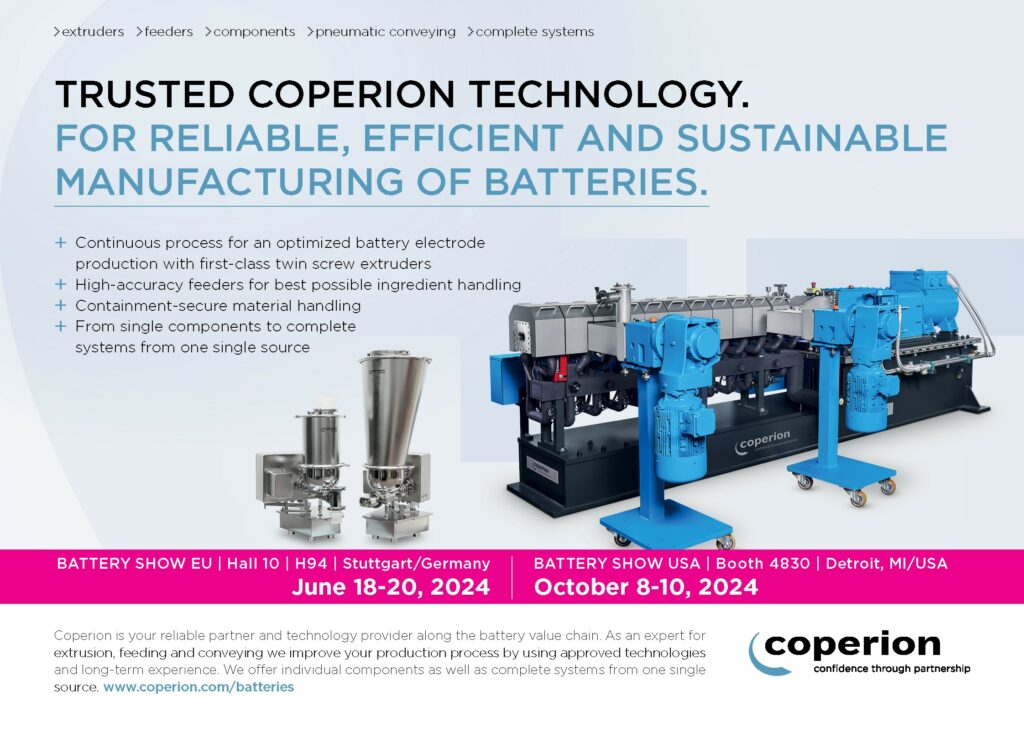
Vehicle control philosophy
In overall control of the entire powertrain is the VCU. “There are different philosophies, but the approach we take to the VCU is to implement it as a central command module,” Drummond says.
“When you put your foot on the accelerator pedal, that moves a potentiometer, which provides a signal that tells the VCU how hard the driver wants to accelerate. Then, the VCU asks the BMS if it can take the required amount of power, and if the BMS says yes, the VCU tells the inverter to supply that much power to the motor. But, if the BMS says no, there is a whole decision tree of what happens. There’s a whole bunch of interlock safety systems that make sure the way the car responds to the controls is commensurate with the health of the batteries,” he explains.
That control philosophy also extends to usability features that can be provided as custom options, such as offroad hill-descent modes for the Land Rovers that Electrogenic is working on for the British Army, or traction control and cruise control for the E-type.
What’s next?
Although there are many physical differences among the classic cars for which Electrogenic builds conversion kits, the basic electrical and electronic architecture is common to all of them. This approach enables them to create kits for other cars more easily, and there are several currently in the works, including one for the DeLorean and the Jaguar XJS.
ONLINE PARTNERS
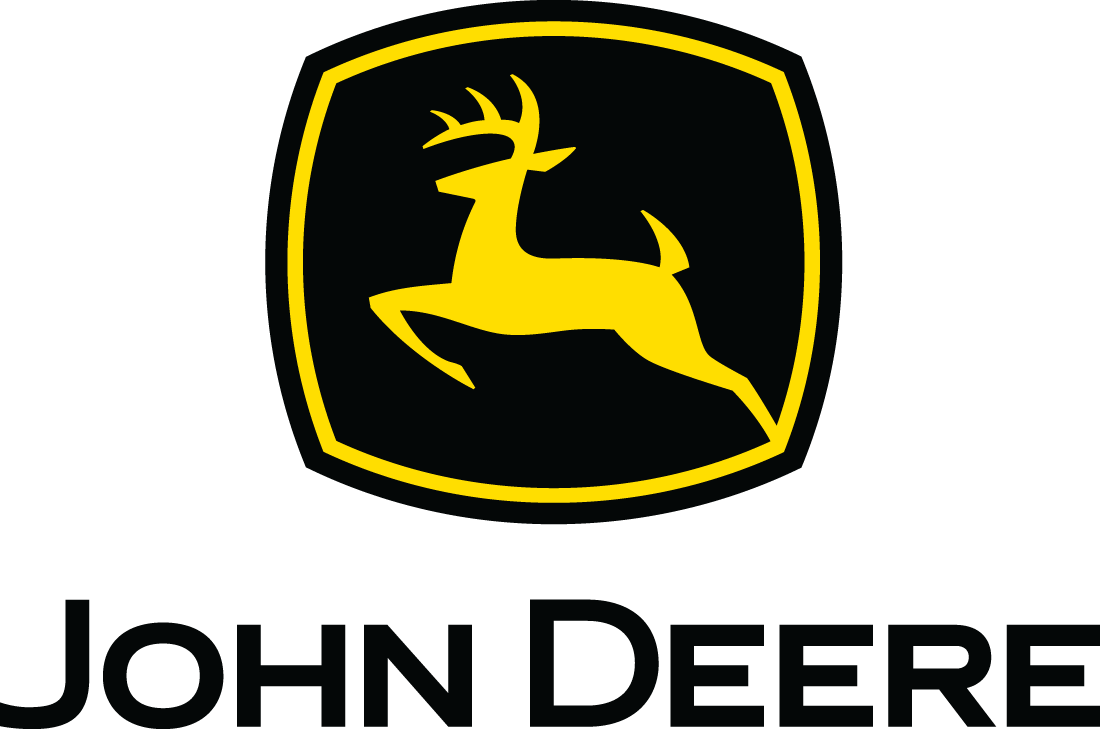
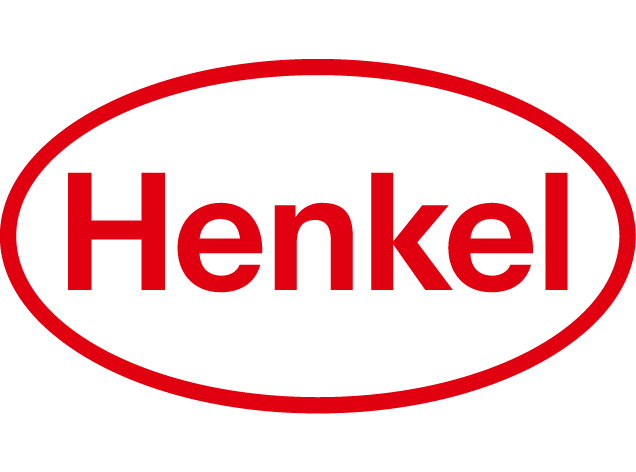
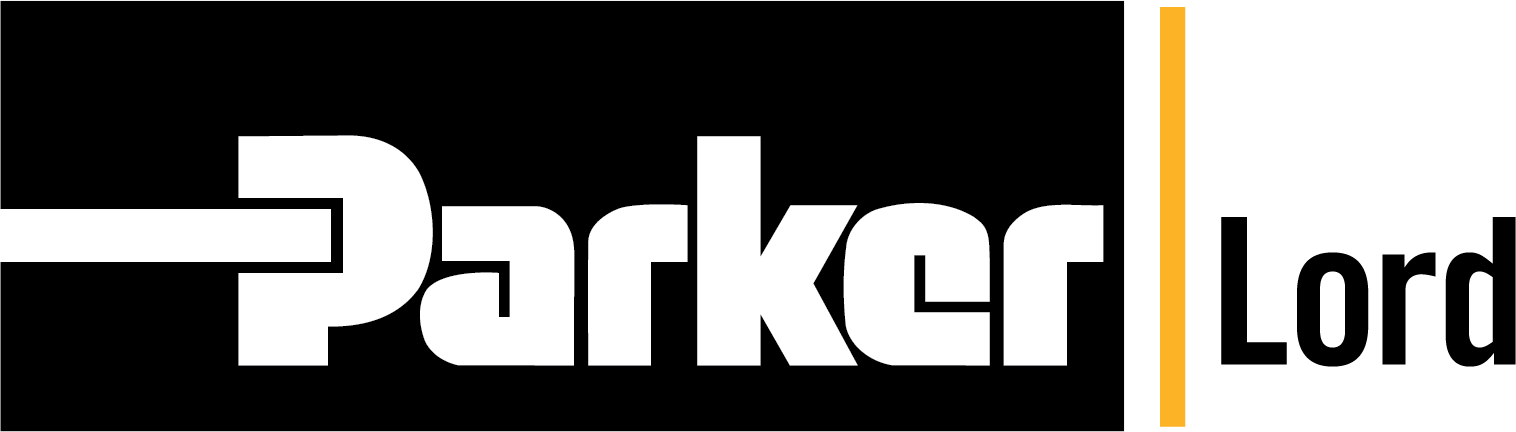
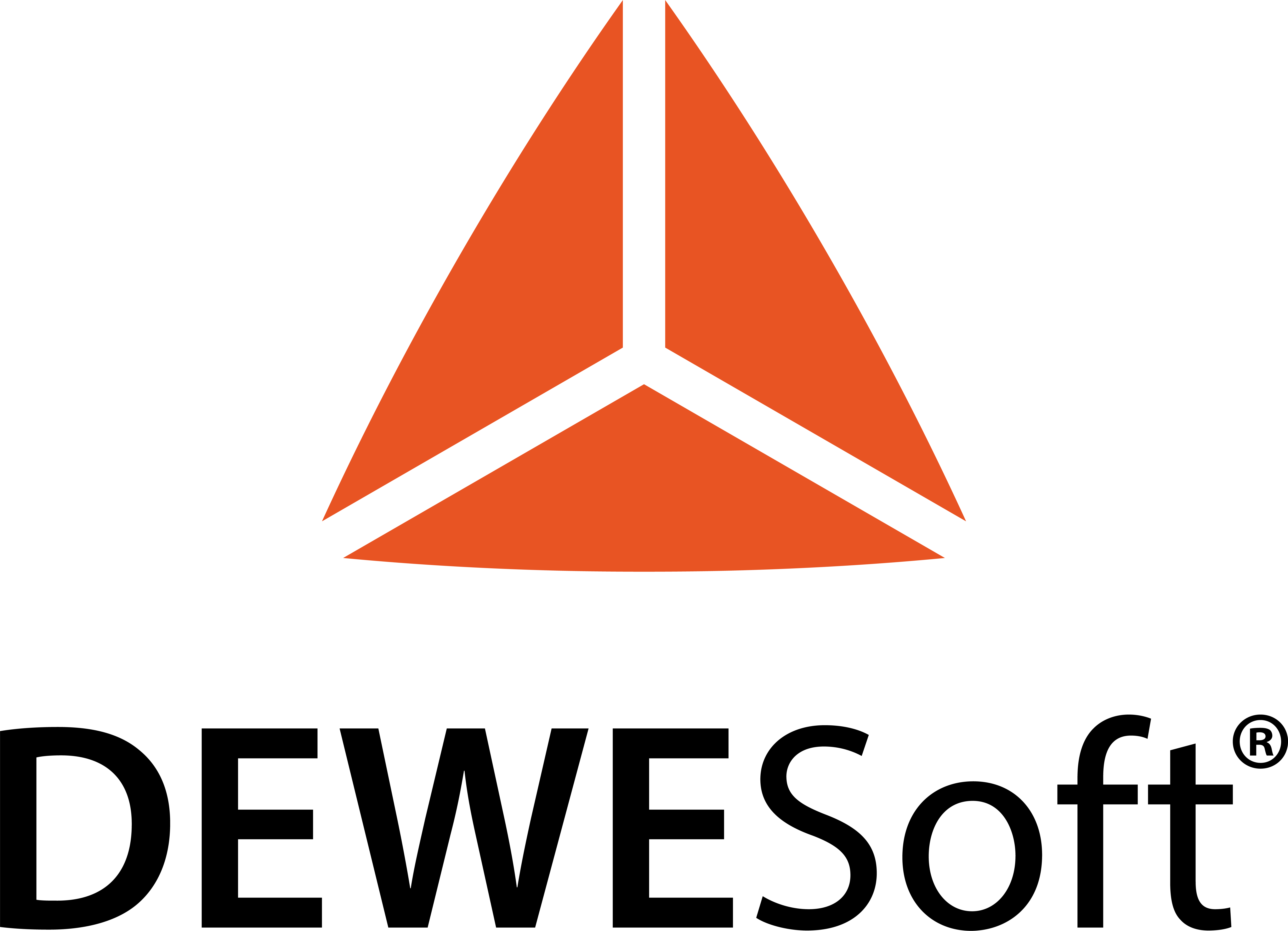
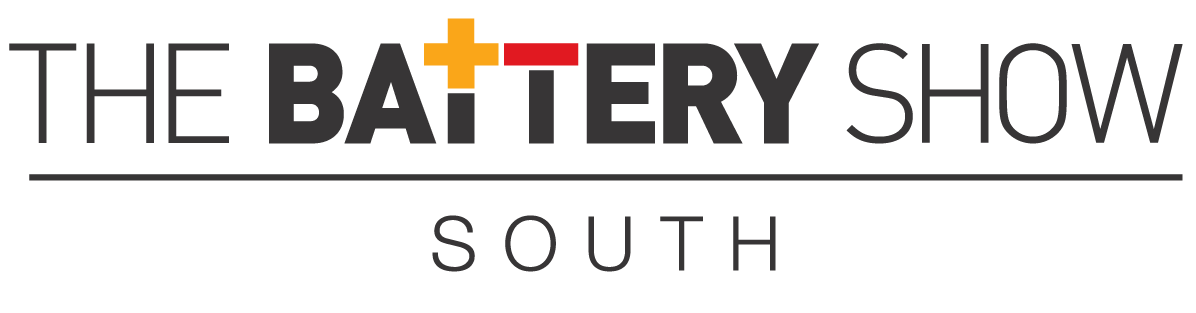
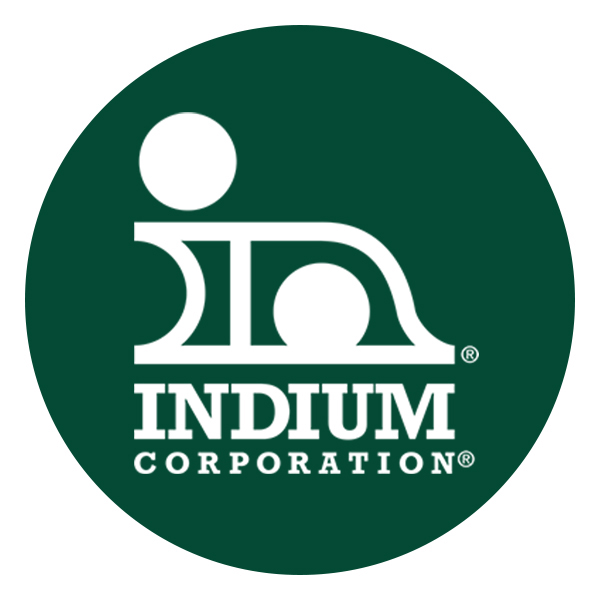

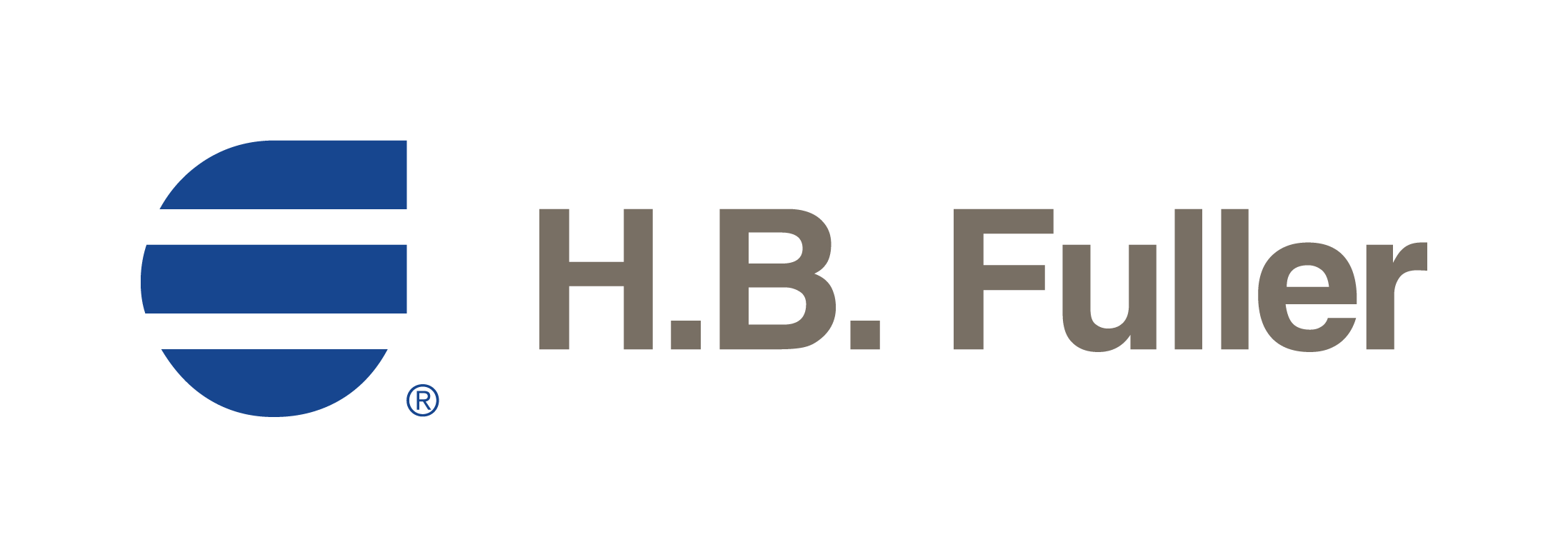
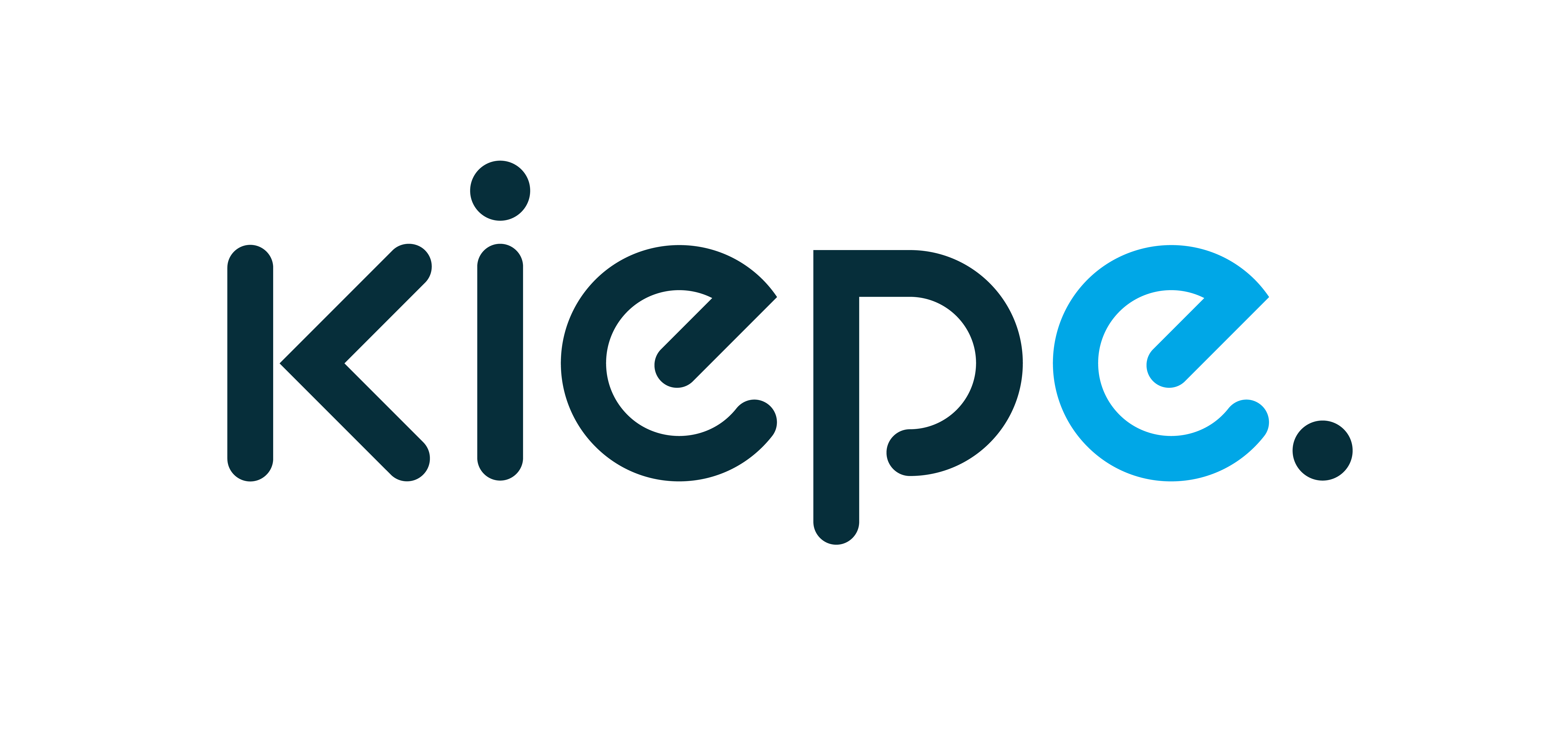
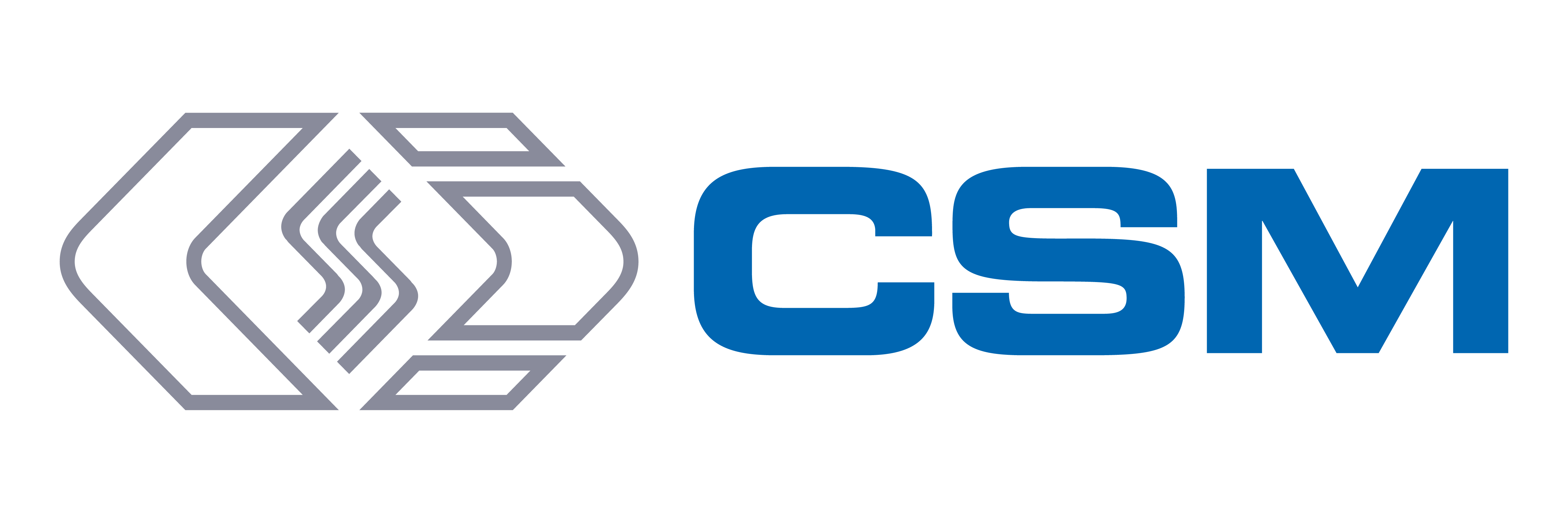