Dynisma DMG simulators
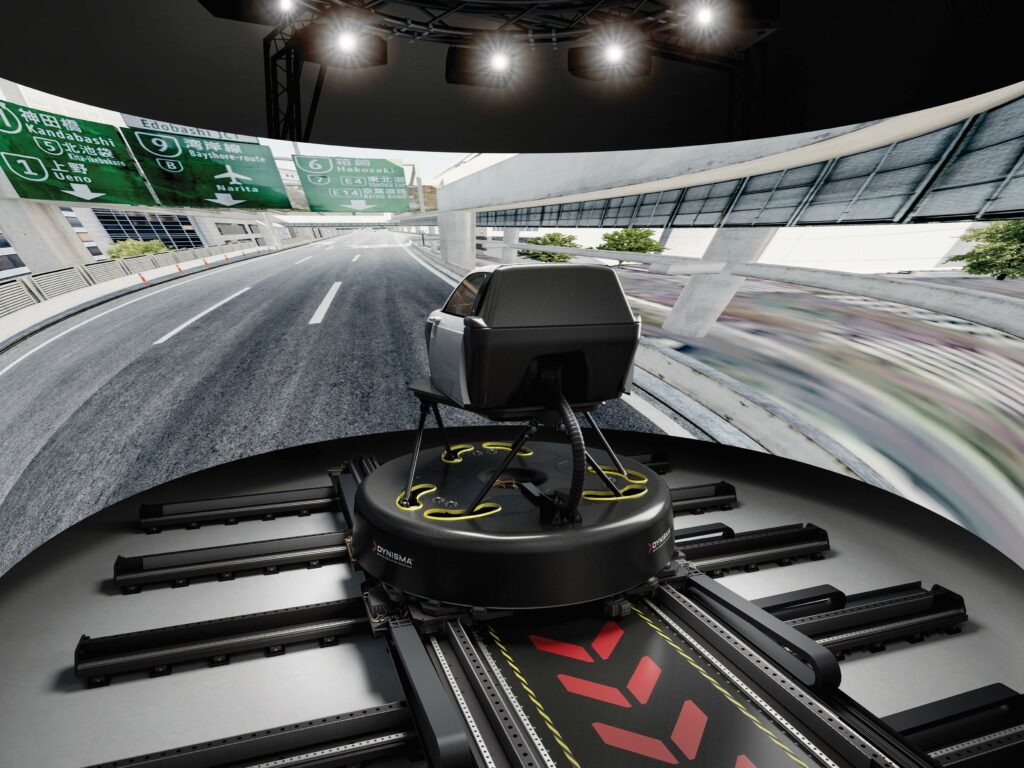
(All images courtesy of Dynisma)
Seamless simulation
Peter Donaldson checks out simulators designed to give drivers the most realistic response and feel
Dynisma’s DMG family of simulators is designed to reduce the time and expense involved in building and testing vehicles by moving as much prototype development as possible into the virtual world. We caught up with the company’s commercial director, Simon Holloway, to bring us up to speed.
These simulators are characterised by low latency and high bandwidth to provide the most realistic response and feel, along with adaptability to a wide range of vehicle types and testing scenarios in all kinds of driving conditions, from race tracks and cities to highways, country lanes and offroad courses.
The DMG-1, DMG-X and DMG-360XY models feature an innovative motion system that eliminates the inherent friction of conventional actuators and carries a cabin whose light, stiff, composite structure avoids unwanted resonance.
The DMG family can also run computer models of complete powertrains, chassis, suspension and brakes, and even advanced driver aids and human-machine interfaces (HMI) for battery electric, fuel cell, hybrid and internal combustion engine (ICE) vehicles, from Formula One cars to SUVs.
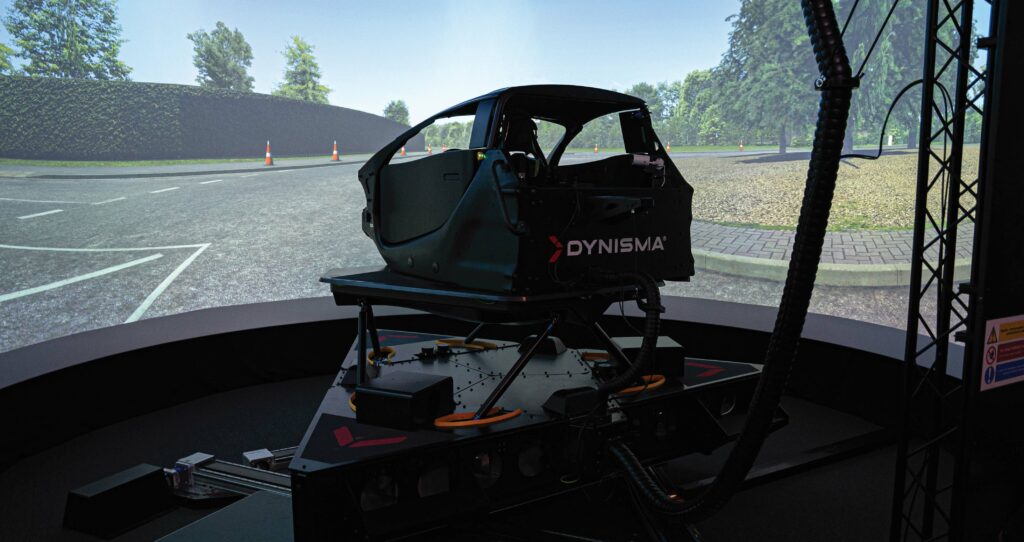
Speeding development
As manufacturers transition from ICE platforms to EV-specific designs, the ability to test virtual prototypes early in the development cycle becomes invaluable, Holloway says. Traditional methods involve creating mule vehicles and other physical prototypes. Dynisma’s simulators allow engineers to explore scenarios virtually and make rapid adjustments, and test them under consistent conditions.
For early development, the virtual environment is particularly valuable in the exploration of different battery configurations and placements, such as centralised or distributed layouts, before any physical prototypes are created. This saves time and resources.
“You can replicate all those different things in the simulator before you physically cut any metal or build a battery,” Holloway says.
Later in the development cycle, it also makes A-B-A testing much easier. This involves running the car with an initial setup, changing the spring rates or suspension geometry, for example, and then running the same test again as a comparison, subsequently returning it to its original spec to run the same test a third time to confirm that any differences in behaviour are caused by the new setup.
“You can do the testing a lot quicker. Unlike a real car, where weather conditions might change or the tyres are 20% more worn, the simulator ensures consistency.”
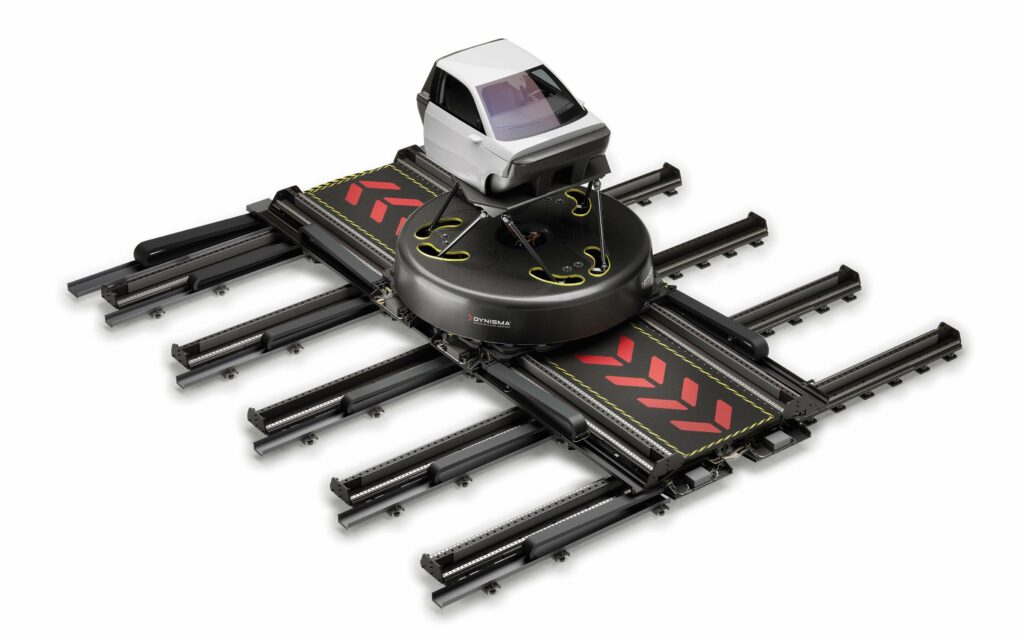
Family values
The DMG-1 is Dynisma’s entry-level simulator, designed for vehicle dynamics, ride and performance testing. It has been adopted by several OEMs, including McLaren Automotive. The DMG-X represents a step up, offering higher frequency, heave and payload capabilities, making it suitable for applications such as noise, vibration and harshness (NVH) testing, and simulating larger vehicles such as SUVs.
The flagship model, the DMG-360XY, features a 5 m travel range and unlimited yaw, which enables realistic simulations of complex manoeuvres, such as lane changes and city driving without the constraints of recentring.
“In traditional simulators with limited yaw, obviously, if you’re driving around a city block or around a roundabout, at some point the simulator has to move itself back to centre. With unlimited yaw, the simulator never recentres,” he says. “Velocity in yaw is one of those things that you really feel, so if you can remove that miscue, it obviously helps the immersion in the scenario.”
Holloway says one of the most revolutionary aspects of Dynisma’s simulators is its focus on minimising latency and maximising bandwidth, addressing two major issues in traditional systems. “In simulators that have much higher latencies and lower bandwidths you sometimes feel like you’re driving on glass or a magic carpet. You have that floating feeling, because they don’t have the definition and the fidelity for what you’re driving on,” he says.
“Latency is one of the biggest issues,” he adds, noting that typical simulators exhibit 20-30 milliseconds of delay, which disrupts realistic driving responses.
In contrast, Dynisma’s simulators can achieve latency of 3-5 milliseconds, which ensures a seamless connection between driver inputs, vehicle model responses and motion cues. This precision significantly enhances the realism of the driving experience, and prevents motion sickness caused by the mismatch between what drivers see and what they feel.
Bandwidth refers to the range of frequencies over which the simulator can respond accurately to driver inputs and replicate the dynamics of the vehicle being modelled. Dynamic events range from low-frequency motions, such as gradual acceleration and cornering, to high-frequency phenomena such as vibrations and bumps.
Sufficient bandwidth ensures both low- and high-frequency dynamics are represented accurately, and it is crucial to represent the behaviour of anti-lock braking, traction control, lane-keeping assistance and other advanced driver assistance system (ADAS) technologies.
High fidelity and low latency enable precise testing of features such as torque vectoring, regenerative braking and the handling characteristics of EV platforms.
Holloway explains: “If you’re using four-wheel torque vectoring, you could replay and feel what’s happening within each wheel, just like it does on the real vehicle.”
Precision is important given the shift in EV design paradigms, such as the use of skateboard-style chassis/battery pack combinations and lower centres of gravity, needing reoptimisation of suspension geometries and vehicle dynamics.
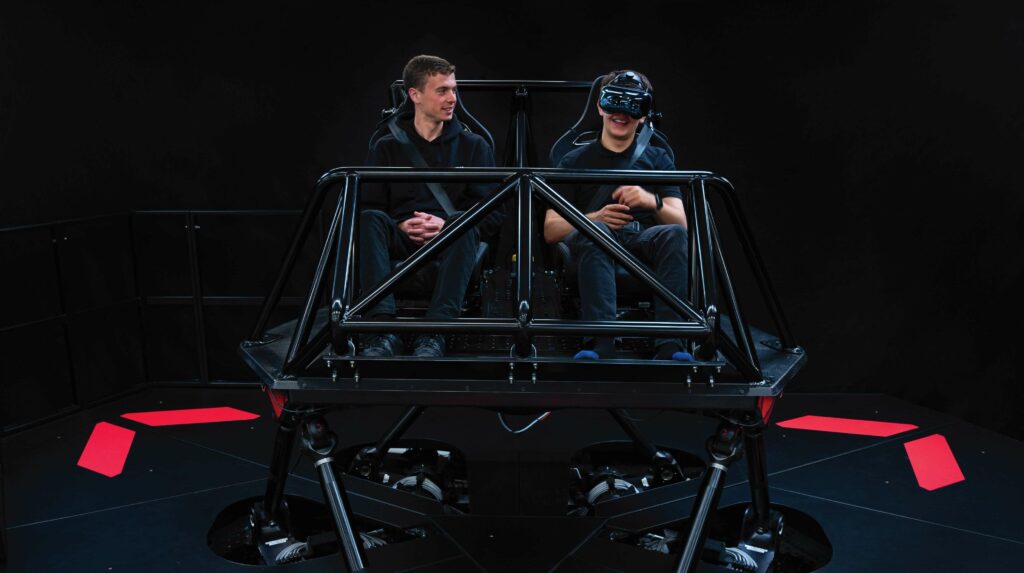
Frequency response and fidelity
Holloway emphasises the importance of the simulators’ ability to replicate real-world vibrations and oscillations. With frequency capabilities exceeding 100 Hz, the DMG simulators provide high-resolution feedback that mirrors the tactile sensations of driving.
“If you drive over a 5 mm painted cleat or curb, the high fidelity means you feel every little movement underneath the car,” he says.
This level of detail is critical for both motorsport and roadcar applications as it captures the nuances of tyre behaviour and surface interactions.
Holloway argues that the ability to test and refine tyre designs early in the development cycle is a major benefit. He points out that simulators can align tyre performance with vehicle characteristics much earlier than traditional methods, reducing reliance on mule vehicles, which often compromise tyre designs.
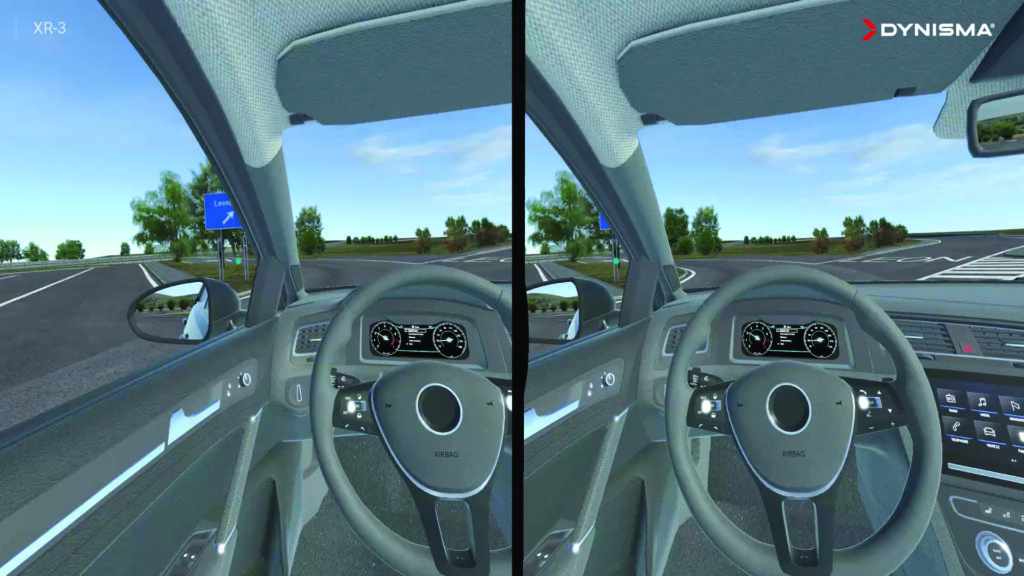
Unique motion system
Dynisma’s motion system is designed to be highly adaptable and capable of simulating a wide range of vehicles with minimal setup changes. Engineers can also scale motion inputs to match the vehicle’s characteristics, ensuring realistic feedback, even on smaller platforms. For example, the DMG-1’s high-frequency platform provides the initial motion cues, while the lower-frequency platform adds extended travel for manoeuvres requiring sustained forces.
At the heart of the DMG simulators is a patented motion-generation technology that eliminates friction and mechanical resistance associated with the gearboxes and actuators used in more conventional simulators. This allows the motion system to respond more quickly.
Holloway says the motion system’s mechanism is similar to that of a Formula One car’s suspension, using motors that drive a rocker and pushrod system. This setup ensures smooth, immediate and highly responsive motion.
Eliminating traditional gearboxes and actuators makes the simulators smoother and quieter. This facilitates the simulation of powertrain vibrations – an important cue for motorsport drivers and engineers.
Holloway explains: “In an EV, as a motor regenerates, those higher-frequency vibrations can be replayed, helping to refine the driving experience.”
Dynisma’s simulators often use carbon-fibre cabin structures, which reduce weight and increase stiffness. This design guarantees that the structure’s natural resonant frequencies are a long way from the forcing frequencies to which they will be subjected, ensuring vibration and noise originate from the simulated environment rather than the simulator itself, Holloway says. This enhances the fidelity of NVH testing.
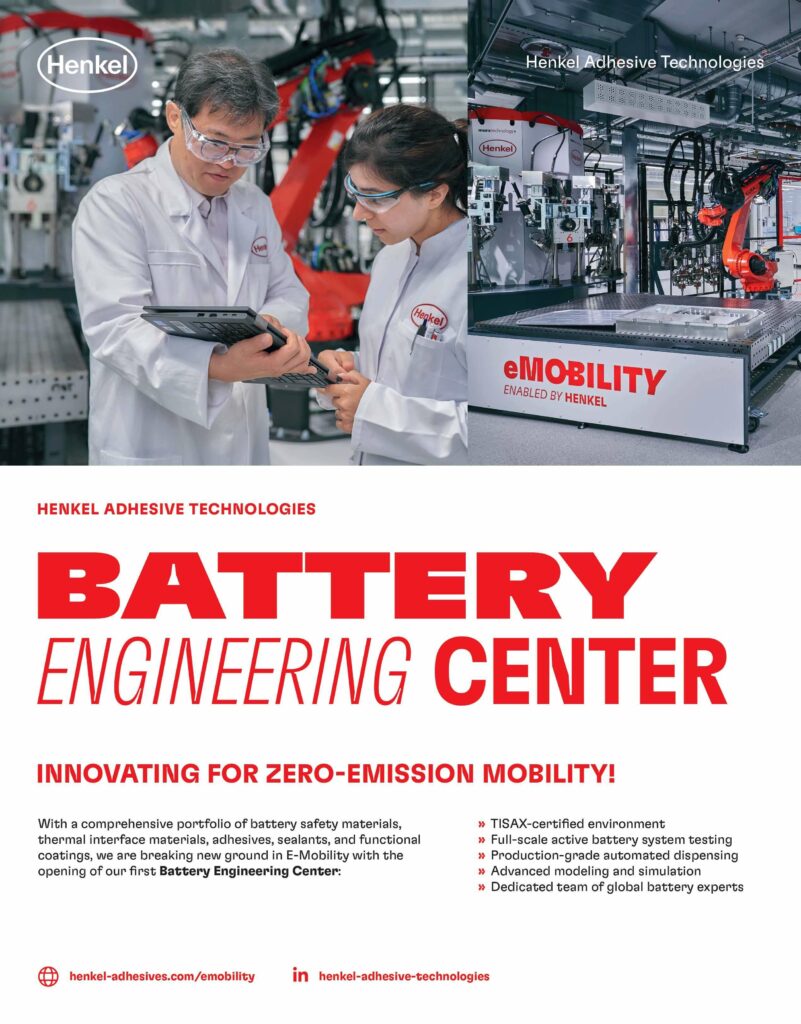
Powertrain modelling
Dynisma’s simulators also support iterative powertrain modelling. Holloway says manufacturers can refine their models over the development cycle, starting with low-fidelity models for early decisions and transitioning to high-fidelity simulations as the design progresses. This iterative process enables seamless integration of existing powertrain designs into new vehicle models.
“Taking that model that you already have and then being able to supplement it with the other vehicle model, you can test out those behaviours and styles, and see what it looks like,” he says.
Such adaptability is invaluable in optimising powertrain configurations and predicting performance outcomes before physical prototypes are built. It is essential to reproduce the effects of the torque and power characteristics of a wide variety of electric motor types.
Holloway says the simulators can run sophisticated powertrain models capable of replicating throttle response, torque delivery, and both regenerative and mechanical braking behaviour in real time. This enables engineers to experiment with different torque and power curves, and observe their effects immediately without requiring physical modifications.
This flexibility extends to incorporating hardware and software-in-the-loop into the simulations. By integrating real electronic control units (ECUs) into the simulation, engineers can test how the hardware interacts with the software under various conditions, which helps to ensure optimal performance and shorten development cycles.
Understanding energy
One of the primary challenges in EV development is understanding real-world energy consumption. Holloway highlights how simulators address this issue by including human drivers in the loop: “Being able to put different demographics of drivers into the vehicle that will drive in different styles… can give you some real, quantitative data.”
This approach allows manufacturers to evaluate how driving behaviour has an impact on range and energy efficiency, beyond theoretical models based on standardised test cycles.
Holloway says simulators can analyse how different driving styles impact battery health and service life, so long as the vehicle model includes a high-fidelity model of the battery. Comparing how driving styles affect battery degradation helps the development of better battery management strategies. This process enables engineers to strike a balance between maintaining performance and extending battery life, ensuring a better overall experience for end-users.
Moreover, simulators can model scenarios such as a battery’s behaviour at a low state of charge (SoC) or its capacity over time. These tests provide valuable data on how to manage power availability without frustrating the driver.
Dynisma’s simulators enable evaluation of energy management systems and predictive software algorithms in real time. Holloway says engineers can model different driving styles and modes to check their impact on energy use and range. “It gives you the ability to, rather than use a theoretical ideal driver, evaluate different people’s use of that, and how it affects range and energy efficiency.”
Heat and air
The simulators also support thermal-management testing. By incorporating fidelity modelling of battery heating and cooling behaviour, they can simulate such challenging scenarios as high acceleration, hill climbs and fast charging. Engineers can evaluate how the battery management system (BMS) responds to thermal stress and optimise its performance to ensure the vehicle remains driveable under extreme conditions.
Simulators also allow for iterative design of thermal-management systems, including the evaluation of technologies such as dielectric or air cooling, while considering their impact on aerodynamics through changing the number, size, shape and position of heat exchangers.
Holloway underscores the importance of integrating real-world variability into thermal testing, noting: “When you’re developing a vehicle and doing a thermal-management system, you will do that around probably a theoretical drive cycle. But, by putting a person in the loop and driving it, you can replicate how a real driver is going to drive it.”
This ensures designs are robust enough to handle diverse real-world scenarios. By including aerodynamics in a model of the vehicle loaded in the simulator, engineers can adjust aero balance, simulate active aerodynamic components and even test fault scenarios, such as the failure of an active aero surface during high-speed driving and its impact on driver control.
“You could simulate what would happen in a high-speed driving scenario if one of the spoiler motors failed,” Holloway says.
Dynisma’s simulators also enable engineers to experiment with driver feedback systems, such as haptic pedals, which provide tactile cues to drivers, helping them optimise energy usage.
Holloway says: “By using active pedals, we can change the force feedback… You can test different scenarios about how that feels.” This is particularly useful for calibrating systems such as regenerative braking and throttle sensitivity.
Refining regen
Regenerative braking systems in EVs present unique design challenges, including seamless transitions with mechanical braking. The DMG simulators excel in testing these scenarios. Engineers can fine-tune parameters such as the degree of regenerative braking and evaluate how drivers perceive the transitions.
Holloway notes that simulators make it possible to test how confident the driver is during the switch between braking modes, and adjust settings for optimal comfort and safety. They also allow for testing with diverse driver demographics to gather comprehensive feedback.
He highlights the benefits of using a simulator over real-world testing, stating: “You can test it with a bigger demographic of users to get better feedback for what the attribute wants to be like.”
This versatility allows the development of braking systems that feel intuitive across a range of driving styles and scenarios, from high-speed highways to urban environments.
ADAS development
The DMG simulators also play a role in developing and refining ADAS features, being designed to excel at simulating road conditions and environmental scenarios. Holloway says simulators can replicate varying grip levels, surface types and even complex scenarios such as aquaplaning, enabling their responses to be evaluated in extreme or edge-case conditions. “You could simulate scenarios in which half the car goes through a large puddle,” he adds.
Such scenarios are crucial for evaluating how ADAS responds to transient conditions that might confuse traditional cruise control or other automated systems. These insights help to optimise ADAS algorithms and vehicle safety features in a safe environment.
Holloway describes how Dynisma’s technology can create scenarios that trigger features such as lane-keeping assistance and emergency braking to test their impact on driver comfort and safety.
“You can replicate how lane keeping affects the driving and what it does to the vehicle,” he says. This allows manufacturers to gather feedback from a diverse group of drivers and fine-tune them to meet user expectations.
Additionally, the simulators can simulate Level 4 autonomous driving scenarios, focusing on passenger comfort. Testing these scenarios ensures vehicles offer a pleasant ride, even when passengers are texting or watching a film.
“The industry is not going to succeed if everybody feels ill in the cars that are driving themselves,” Holloway adds.
Real and virtual sensors
The simulators’ hardware-in-the loop capabilities allow real ADAS sensors to be integrated into simulations. “We can mount a physical camera onto the simulator and take feedback from that,” Holloway elaborates.
The simulator display’s fidelity is good enough to provide reliable information to the camera, so long as the customer-provided visuals are capable.
“We integrate whatever the customer wants to use. Some customers have scanned a city, some have scanned the local roads around their facility, so they have very good visualisations. What the visualisation software guys are now doing is building in things that respond to active sensors,” he says. “There isn’t a real person walking across the road, but the system can give a signal to the Lidar or the radar that says there is.”
Evaluating HMI
Testing of HMI designs is another area that the DMG simulators support, incorporating physical mock-ups and virtual environments. The physical mock-up replicates the interior of a vehicle, complete with realistic A-pillars, dashboards and control systems, while the virtual environment leverages virtual-reality or mixed-reality headsets. These setups allow manufacturers to evaluate the way drivers interact with various HMI configurations under realistic driving conditions.
Holloway stresses the importance of assessing interactions with flat-panel touchscreens versus physical switches, considering how different designs affect usability. “Trying to press a flat-panel instrument button while you’re driving over a cobbled road is going to be pretty difficult.”
The simulators enable engineers to evaluate challenges early in the development cycle, avoiding costly design changes later.
Additionally, the simulators support eye-tracking technologies, which provide valuable data on how drivers visually engage with the HMI. Engineers can analyse factors such as the placement of displays, reflections and the effects of thicker A-pillars on visibility. The ability to alter variables such as time of day and lighting conditions further enhances the realism and depth of HMI testing.
Simulators also improve the sustainability of vehicle development as traditional testing involves transporting them worldwide to assess performance under diverse conditions in a process that incurs substantial carbon emissions.
Engineers can replicate environmental conditions such as temperature variations, road grip and weather effectively instantly. “We can change the conditions in the simulator with a click of a button,” he says.
Navigating uncertainty
As the industry debates the future of propulsion systems, Dynisma’s simulators are well-suited to exploring the whole electrification space for powertrain options, as it is far from inevitable that everything will be a full BEV and the pendulum may swing back to hybrids.
“Obviously, there’s a lot of talk in the whole powertrain and vehicle market at the moment, and I think there’s a lot of work to be done in modelling, simulation and development there,” Holloway says.
Simulators enable engineers to model and test various hybrid configurations – plug-in, serial and parallel – while examining their effects on energy use and performance.
Holloway emphasises the importance of simulation in exploring ‘what if’ scenarios, enabling manufacturers to pivot more quickly in response to market or regulatory changes.
Since its founding in 2017, Dynisma has grown rapidly, serving both the automotive and motorsport sectors, and deliveries are scheduled as far ahead as 2026.
The DMG-360XY is at the top of Dynisma’s range, shown here with wraparound display, cabin on a rocker-and-pushrod motion system, 5 m travel range and unlimited yaw (All images courtesy of Dynisma)
Entry-level DMG-1 is aimed at the development of vehicle dynamics, ride and performance, featuring direct-drive motion and high bandwidth for realistic driver feel
The DMG-360XY’s 5 m horizontal travel happens on longitudinal and lateral tracks, while the revolving platform supporting the cabin on pushrods enables its unlimited yaw
DMG-X offers higher frequency, heave and payload capabilities than DMG-1, and also supports the use of virtual reality for human-machine interface development and testing work
Dynisma’s simulators support eye-tracking, which is a valuable tool for measuring where drivers spend their attention when they have to interact with the HMI while driving.
Click here to read the latest issue of E-Mobility Engineering.
ONLINE PARTNERS
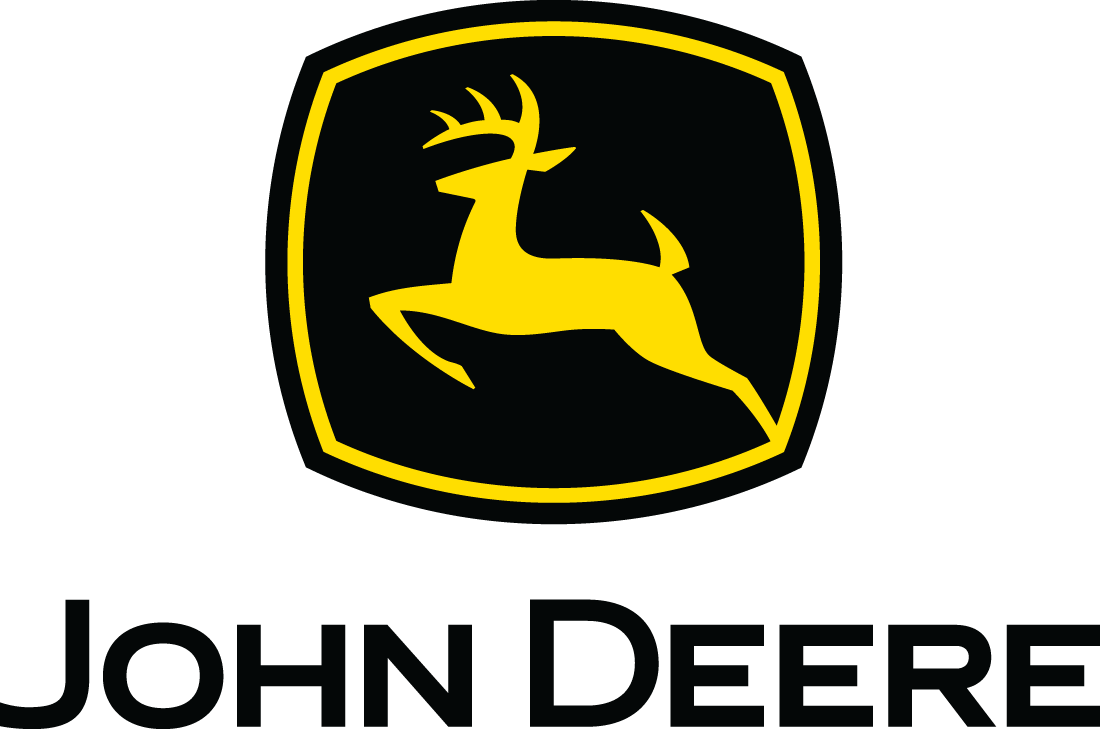
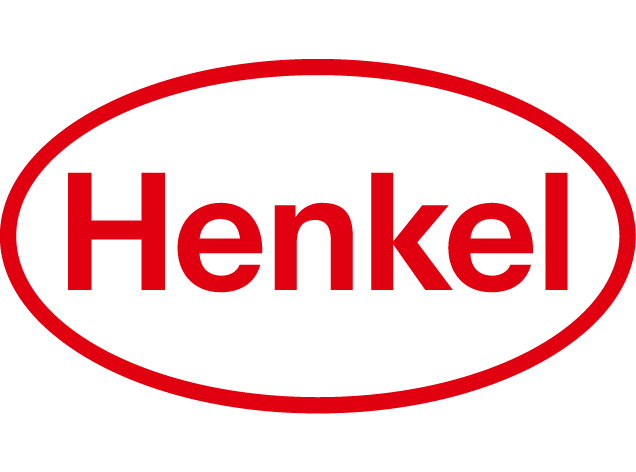
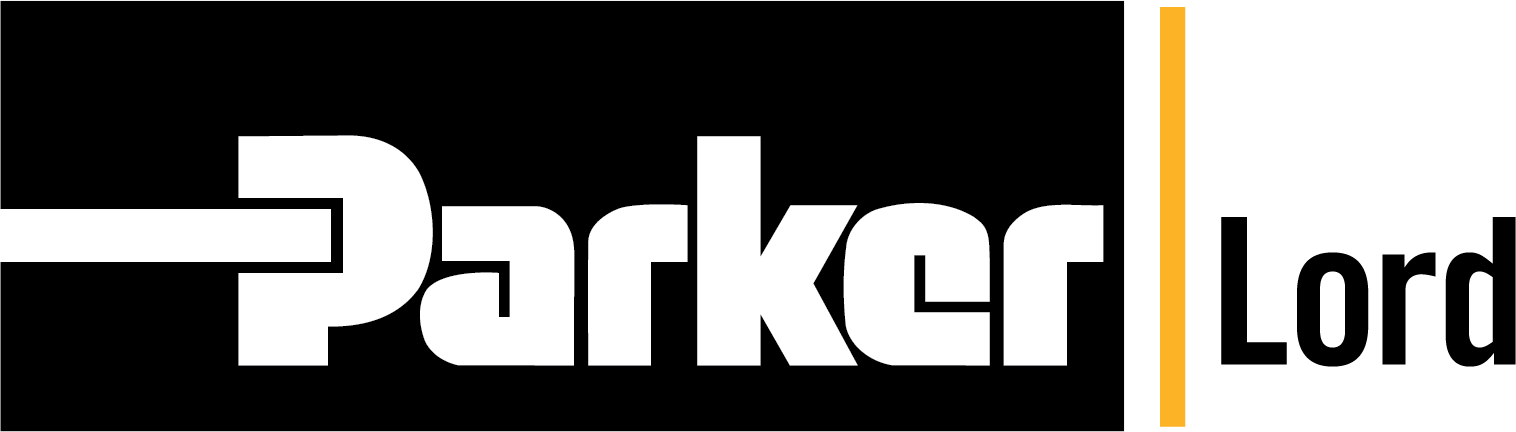
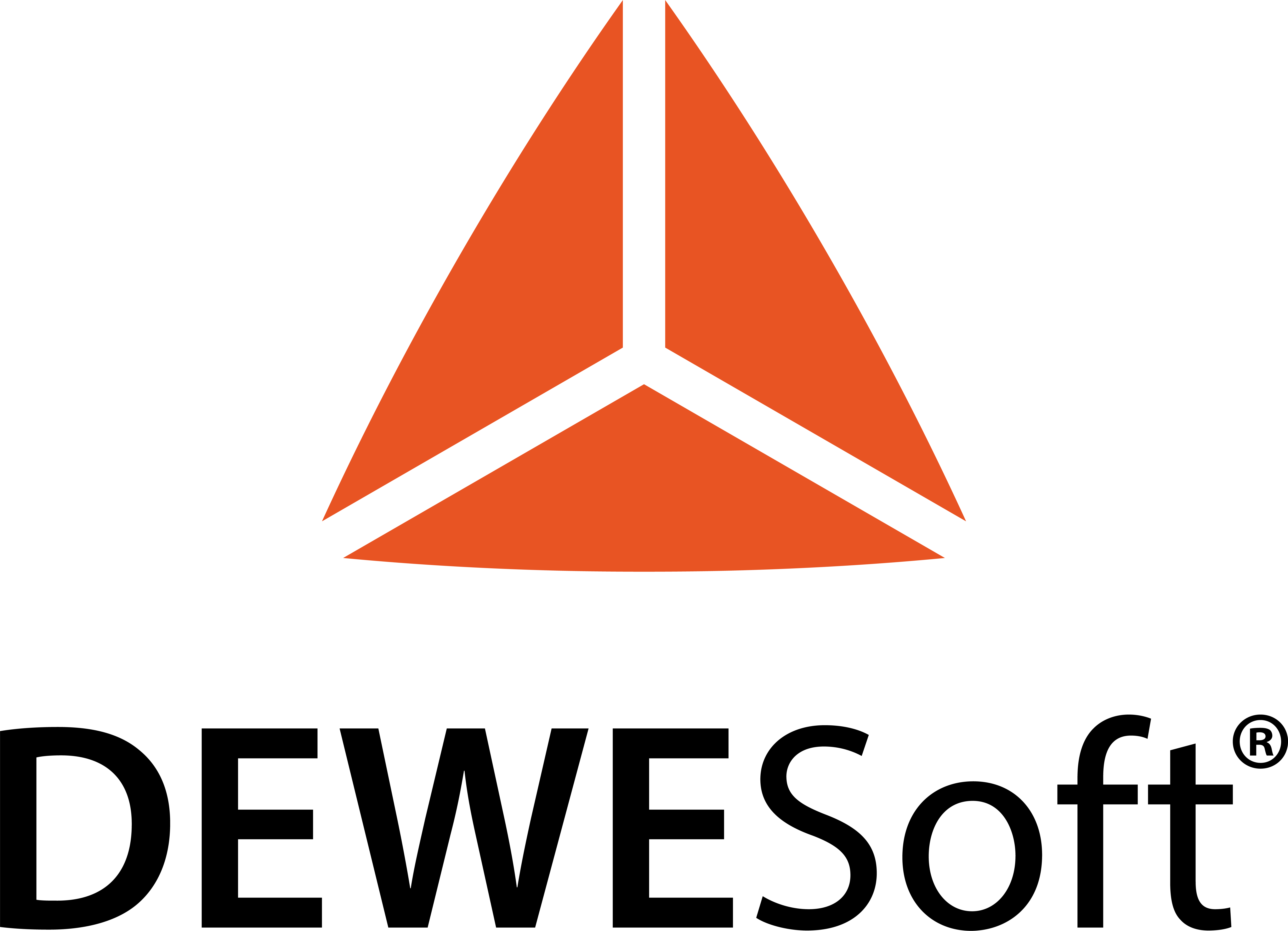
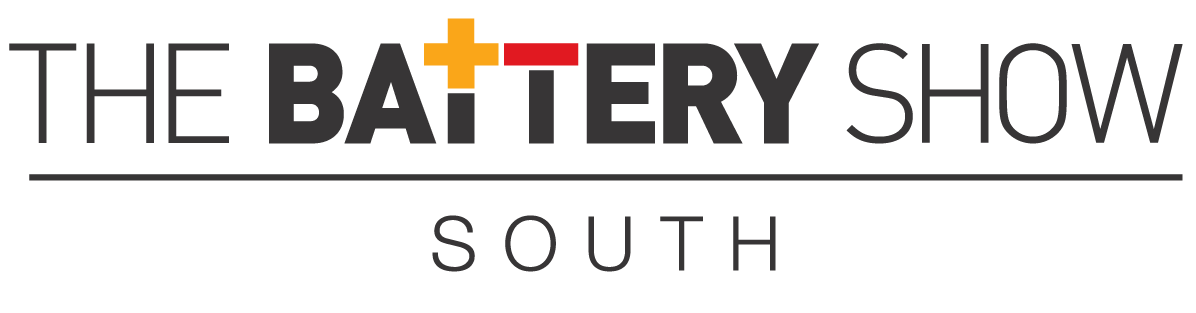
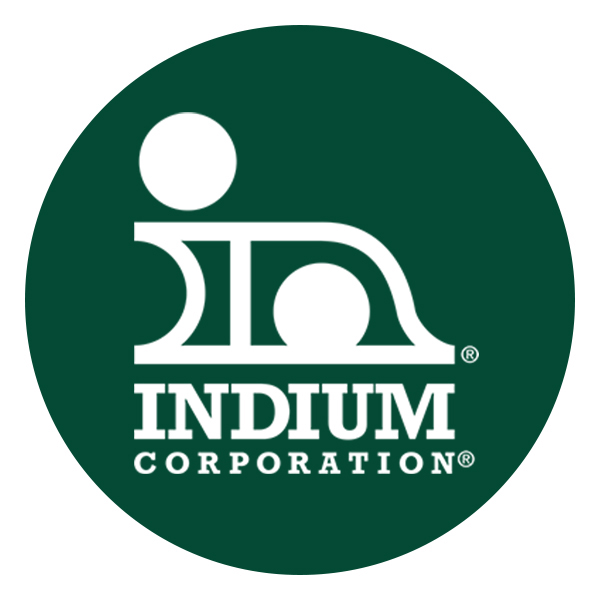
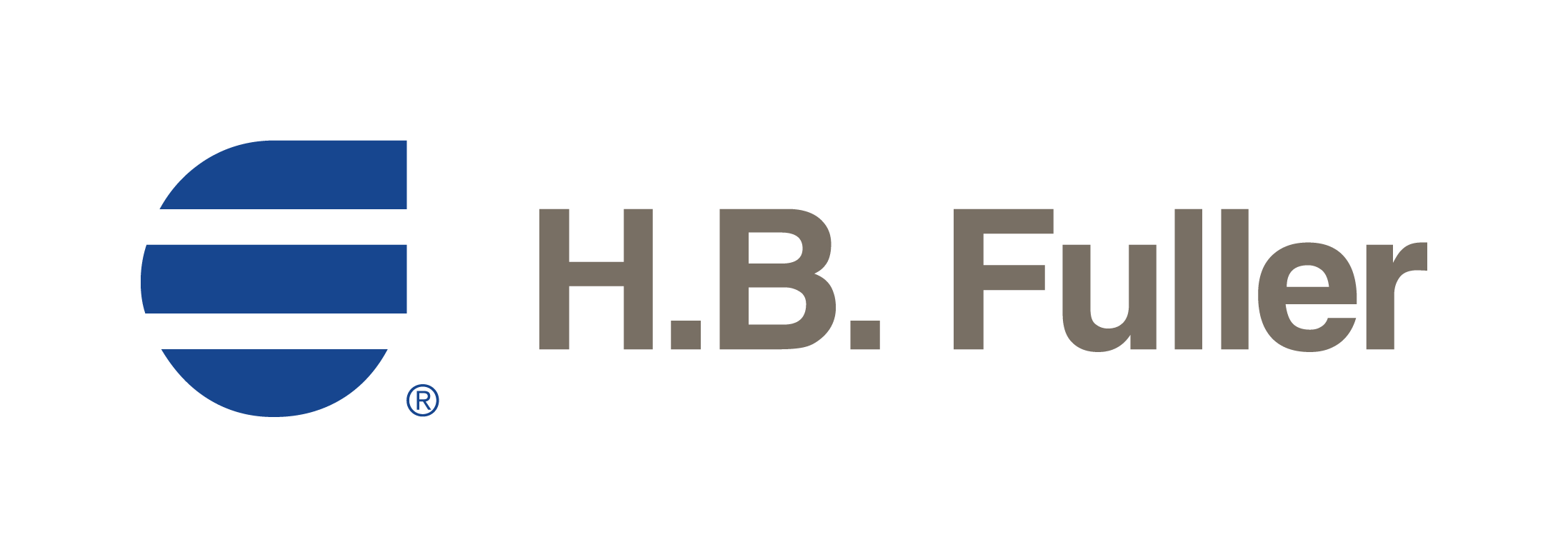