Successful test of aircraft rim motor
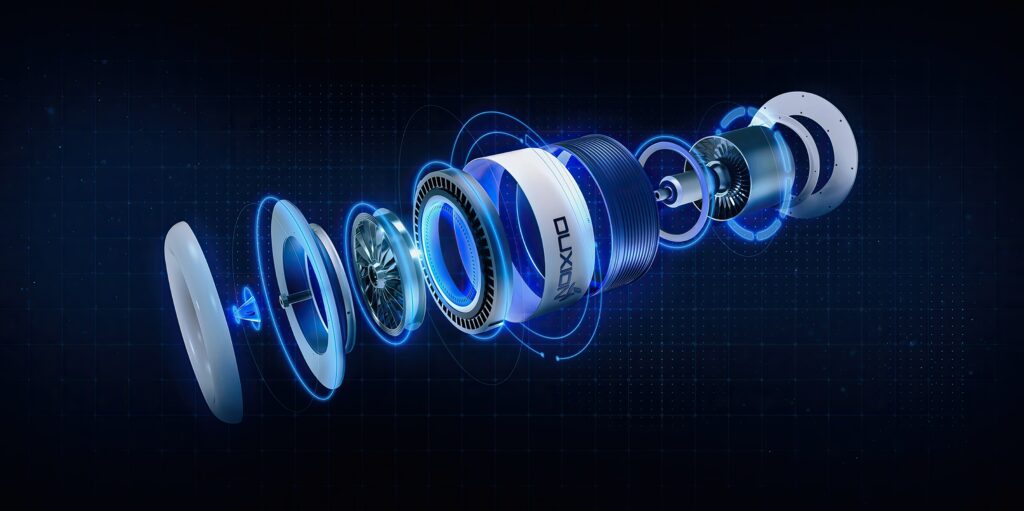
(Image courtesy of Duxion)
Duxion Motors has successful ground tested its patented eJet Motor for electric aviation, writes Nick Flaherty. The successful ground testing of the scaled prototype at Summerside, Prince Edward Island, Canada, included both low-speed and high-speed testing.
The patented rim driven design of the eJet motor uses permanent magnet technology and a new hybrid cooling system to deliver a higher power to weight ratio for the electrification of jet aircraft. The integrated ducted fan system adds forced convective cooling to the liquid cooling system, increasing power density and reliability.
With today’s ducted fan propulsion systems, the motor is typically located inside the duct and coaxial with the fan and the fan blades are attached to a central hub connected to a motor shaft. To achieve a higher thrust, a motor with a higher power rating may be used. However, motors with higher power ratings tend to have larger outer diameters, which reduce propulsion efficiency when the motor is located inside the duct.
To compensate for efficiency losses due to the motor being located downstream of the fan blades, the fan blades are longer to generate the necessary level of thrust. However, a larger motor and larger fan blades significantly increase the weight of the propulsion system and as the size and weight of the propulsion system increases, the thrust-to-weight ratio for the system typically goes down. This type of system may also suffer from significantly increased vibrations which leads to more frequent maintenance, increased vulnerability to mechanical failure and/or generate higher levels of audible noise.
Instead of this approach and its drawbacks, in the eJet the ducted fan blades are integrated into the motor for higher efficiency. This removes the need for a driven motor shaft and increases propulsion efficiency. Putting the motor in the rim allows a relatively high aspect ratio between the diameter and axial length to accommodate a set of polyphase multi-polar stator windings. This enables scaling to higher output power without reaching magnetic saturation in the yoke or in the teeth of the stator.
One of the issues with such a design is the centrifugal forces and/or hoop stresses during high speed operation, so some components of the rotor and fan assembly are pre-loaded in a radial direction during their manufacture and/or assembly. This means these components are under compression when the rotor and fan assembly is at rest.
For example, rotor magnets positioned on an outer surface of the shroud and/or the fan blades may be pre-loaded in compression. By pre-loading components of the rotor and fan assembly, a portion of the centrifugal forces generated during rotation of the rotor and fan assembly may be effectively offset by relieving the pre-compressed stress. This results in less net tensile stress on the rotor and fan assembly during high-speed operation.
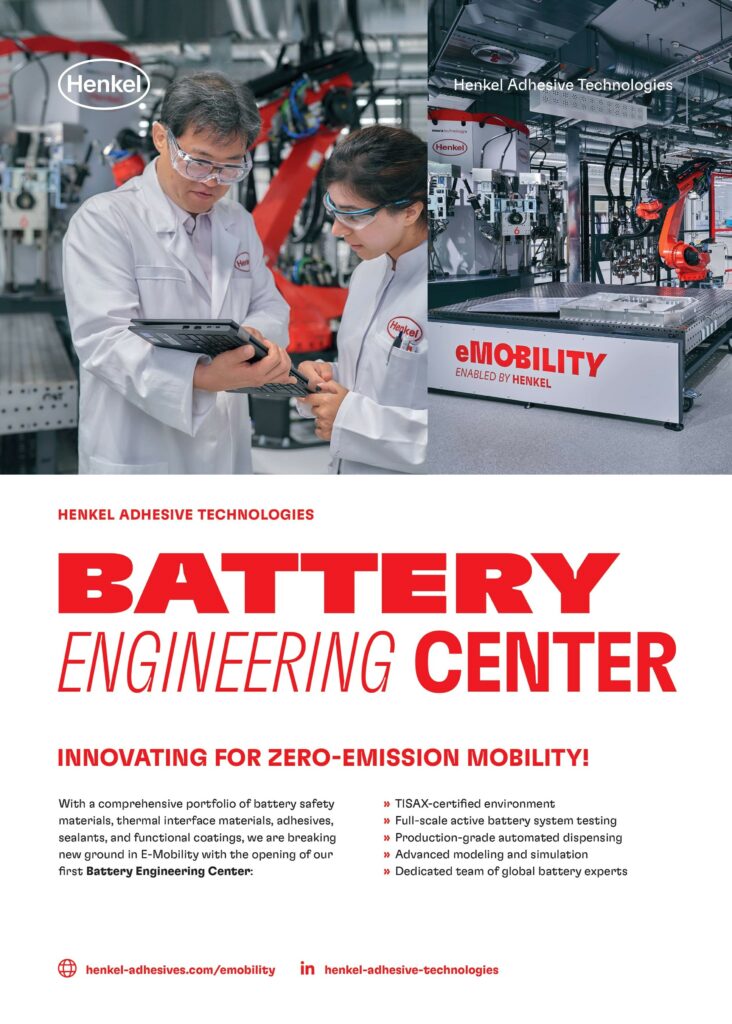
With the rim motor, the stator of the motor is positioned in the nacelle and comprises one or more stator windings while the rotor and fan assembly is positioned in the primary flow path. The rotor and fan assembly has multiple rotor magnets positioned on the outer surface of the fan shroud and concentric with the one or more stator windings. The fan hub is mounted on a central support shaft via one or more bearings and multiple fan blades extend between the inner surface of the fan shroud and the outer surface of the fan hub.
“The eJet Motor is the world’s first rim-driven jet propulsion motor, with the means of matching existing jet engine thrust but without the emissions,” said Rick Pilgrim, Chairman and CEO of Duxion Motors. “The eJet Motor is novel, scalable, and can be configured to serve a broad base of airframes.”
He also notes that this rim motor design also has less vibration and is quieter than combustion jet engines.
ONLINE PARTNERS
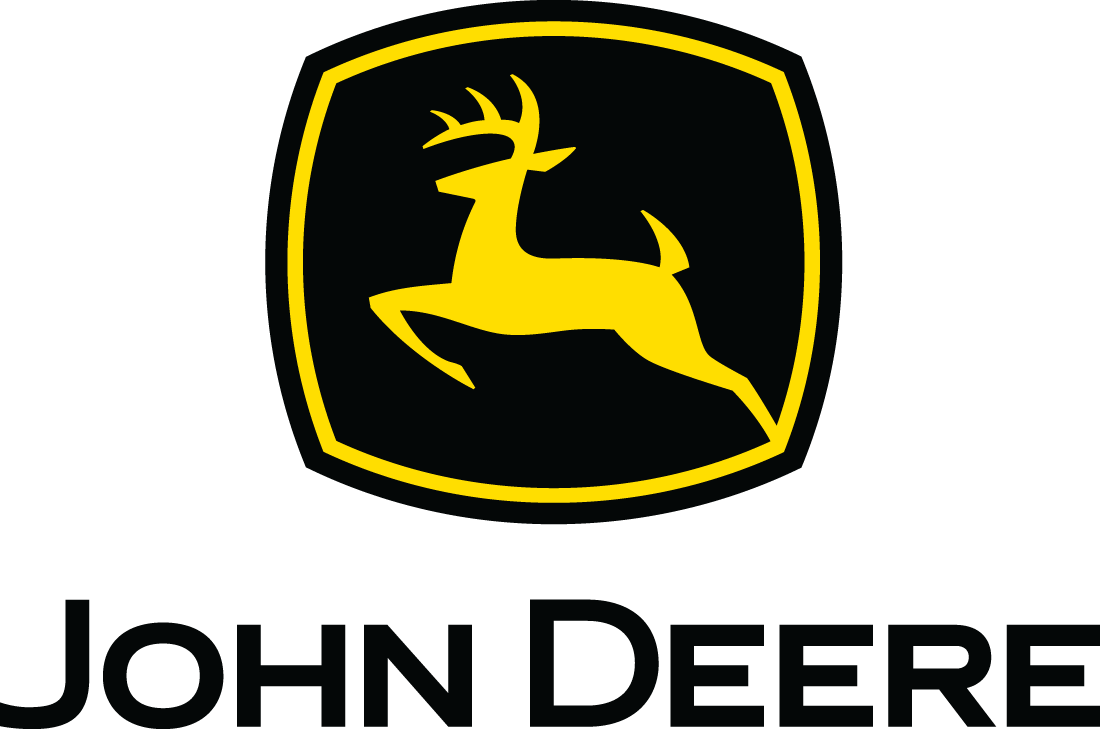
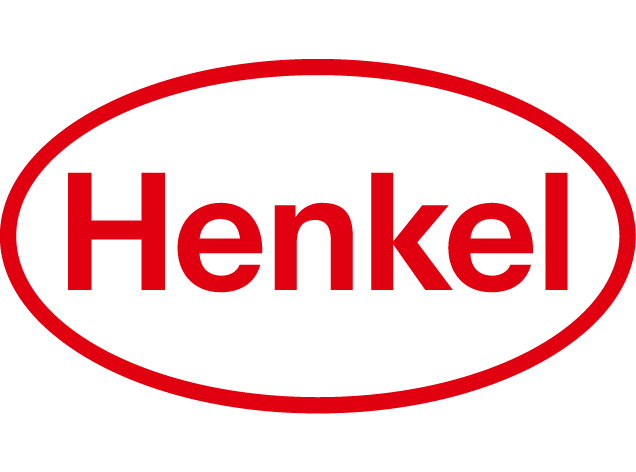
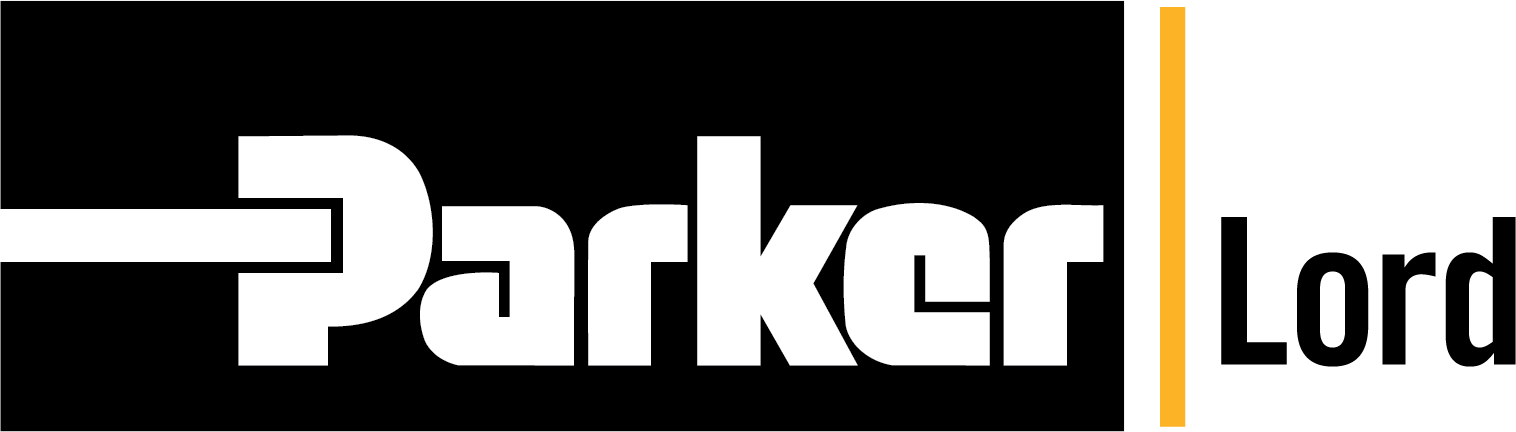
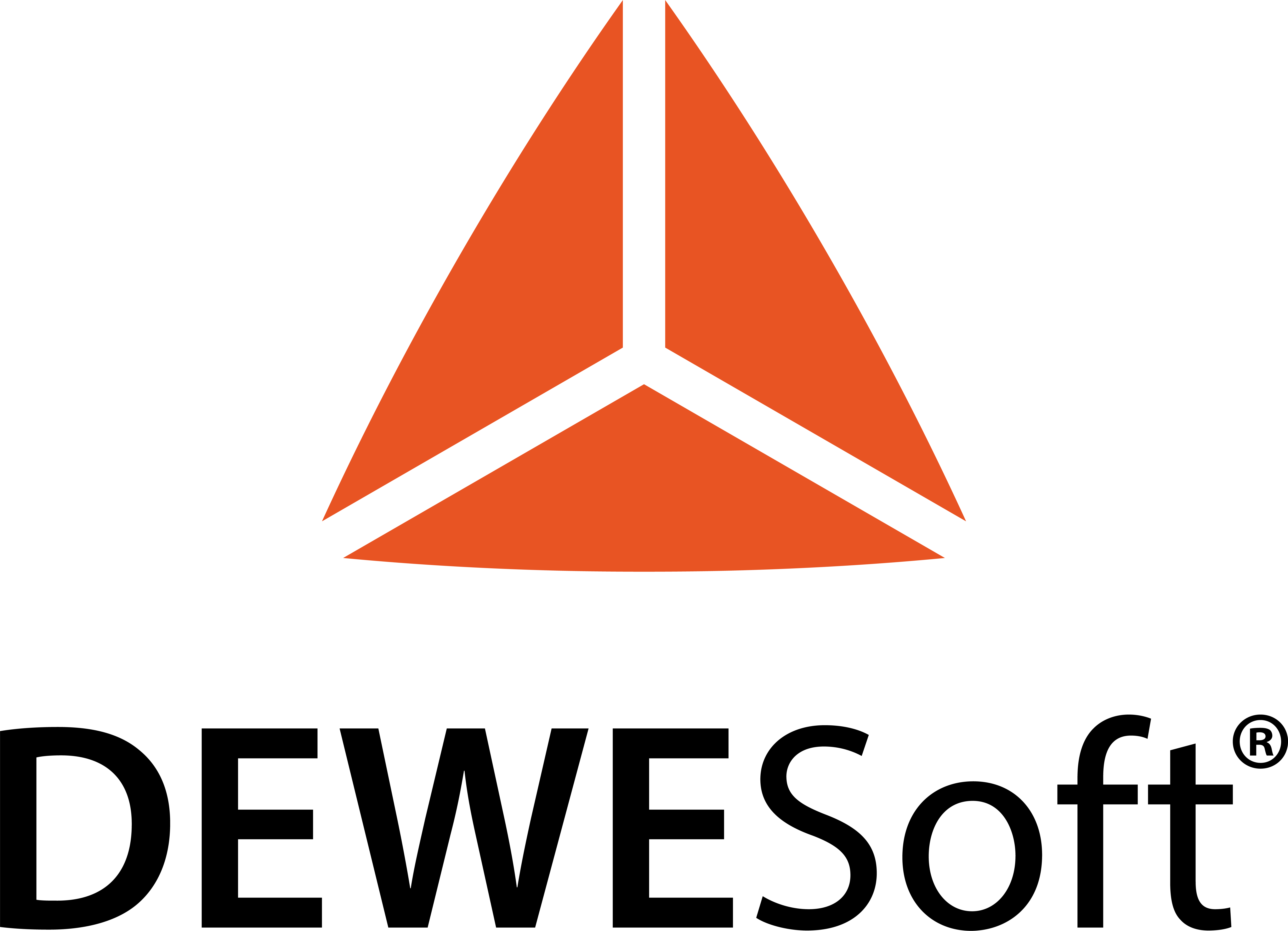
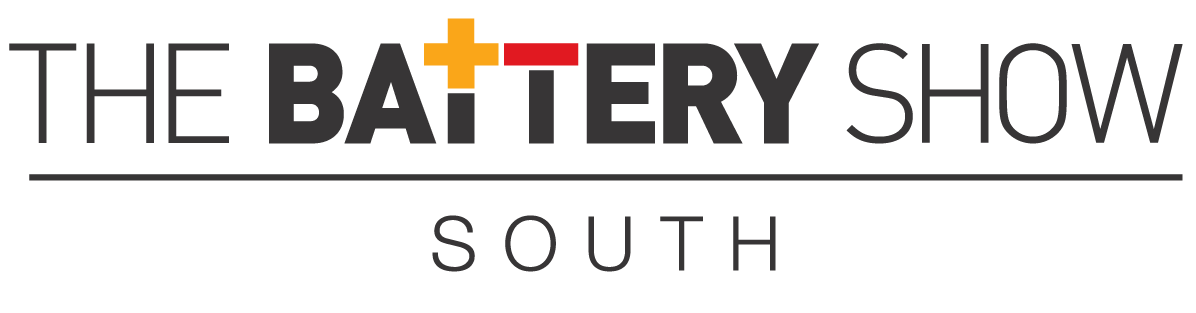
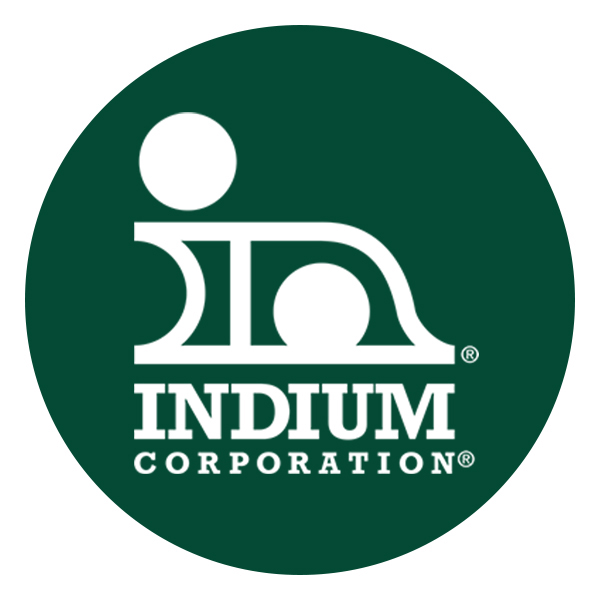

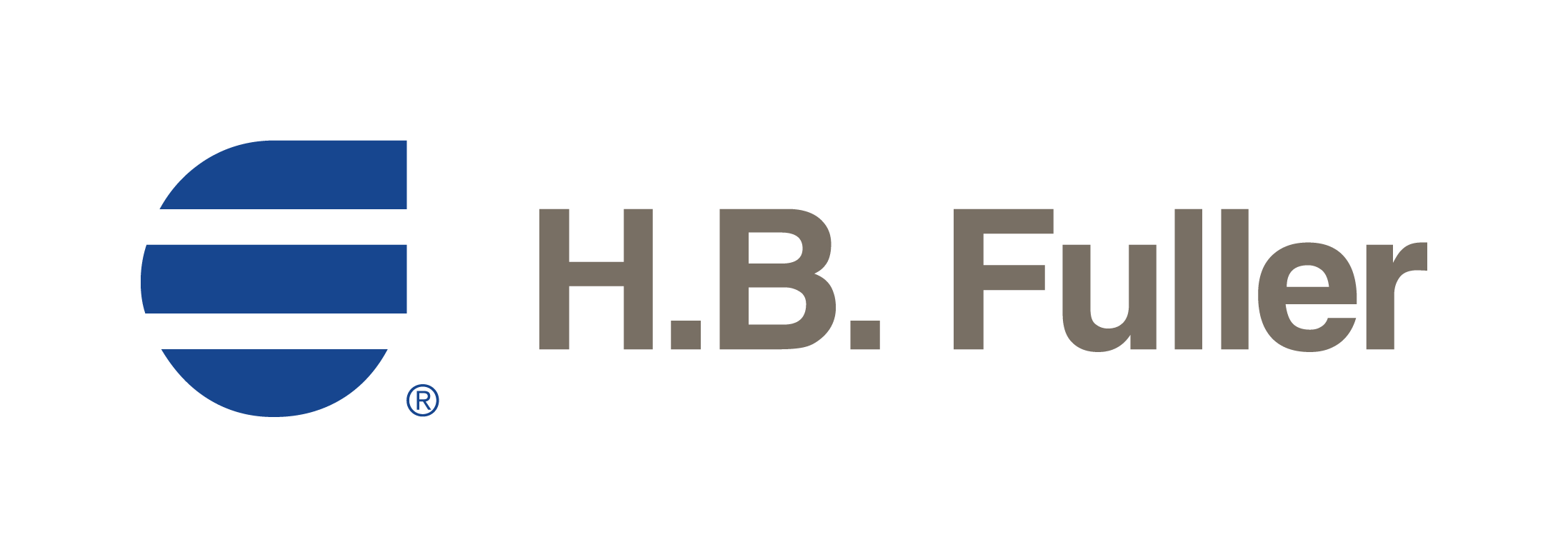
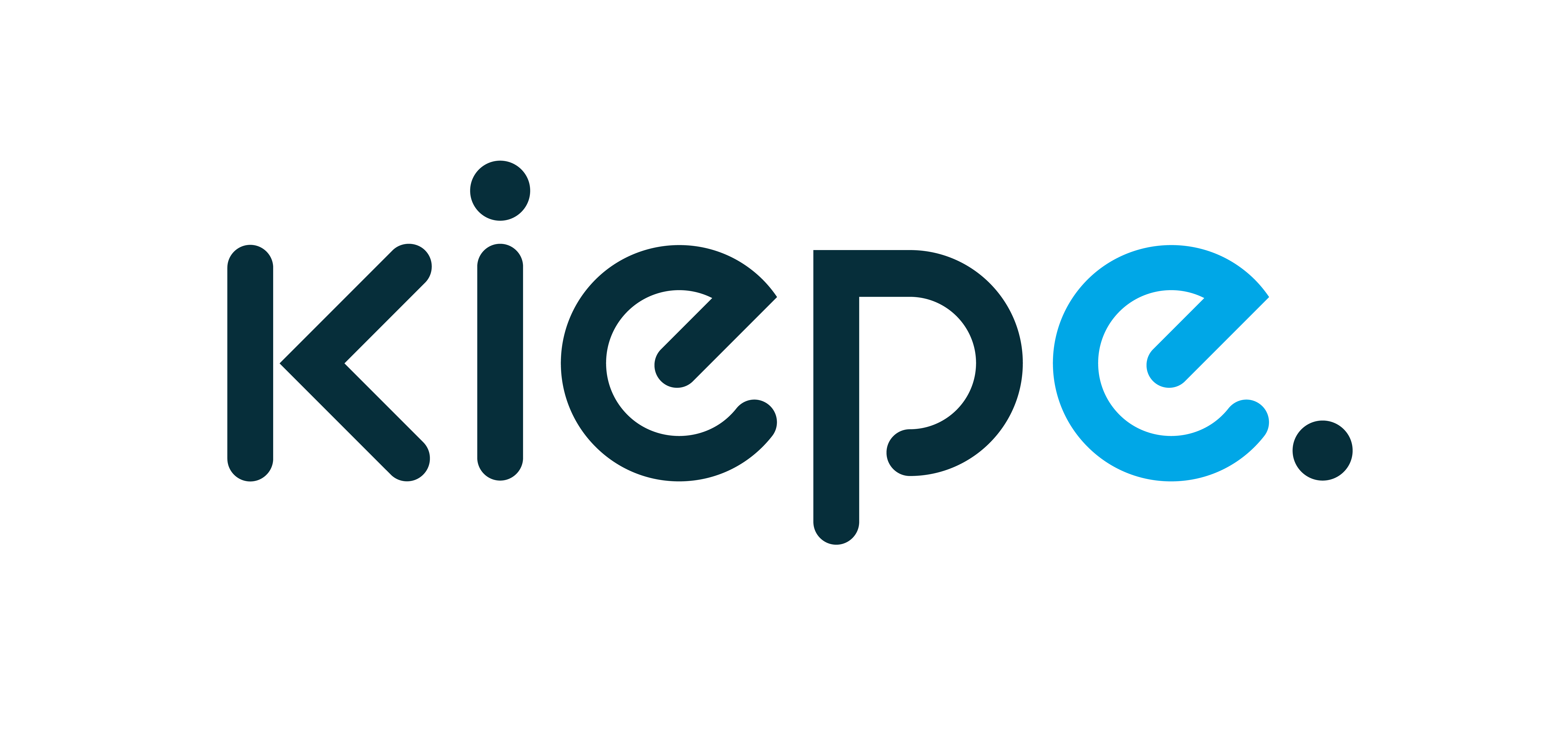
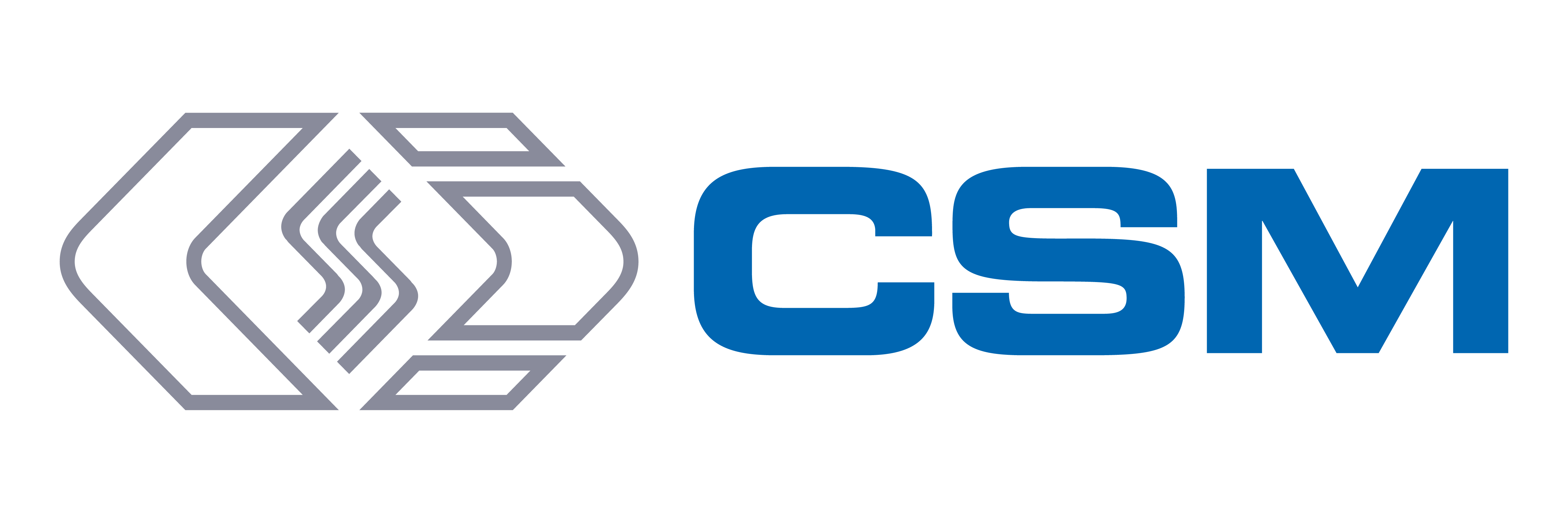