Coveme electric motor slot and battery spacer insulation for high-voltage applications
With motor voltages in many e-mobility applications effectively doubling from the 400 V region to 800 V or more, one of the issues that arises is preventing breakdown of the insulation within the motor slots, with the key stressor being partial discharges. Italian insulation specialist Coveme has developed processing improvements for DuPont Nomex dielectric material, making it capable of withstanding such discharges and enabling the material to be applied at scale by existing production machinery. Coveme has also launched a new humidity resistant Nomex material for battery cell and module spacers, writes Peter Donaldson.
One of the primary purposes of slot insulation materials is to form a barrier to prevent arcing among those components that could lead to motor failure. The essential properties of such materials include characteristics to withstand high-voltage electric fields, such as dielectric strength and the capability of avoiding or resisting partial discharges. Another is a low, dielectric constant to minimise energy stored in electric fields, and the consequent electrical losses and heating.
Materials also need high thermal conductivity to dissipate heat, high thermal stability, good chemical stability to resist degradation by exposure to moisture, oils and other substances, and high resistance to tracking, which is the formation of unwanted conductive paths though surface erosion or contamination. Materials commonly used today in lower-voltage motors are laminates consisting of a layer of Kapton between two layers of Nomex.
Partial discharges are essentially sparks that start to eat their way through insulation material, with a cumulative effect that eventually results in a short circuit, explains Alberto Rumi, technical manager, insulation materials at Coveme.
By virtue of its expertise in converting technologies, Coveme has developed, in partnership with Dupont, a mica-containing slot-and-phase insulation paper that is capable of withstanding partial discharges over the long term at 800 V or more. This range of materials has been specifically designed, bearing in mind processability with current stator assembly lines.
Rumi says: “DyTerm Blue shows an exceptional, partial discharge endurance, which is 1,000 times better than traditional slot liners and improves other important characteristics, like thermal conductivity.”
The flexible, multi-layer laminate is now at the industrialisation stage, and Coveme is in talks with major providers of automated motor-manufacturing machinery.
“We are collaborating on material tests that try it out on their equipment,” he says. “There is a formation process and then you insert it into the stator. After that, the whole motor is typically varnished or impregnated, and our material has perfect compatibility with the impregnation varnishes and resins.”
Rumi also says the material has further room for improvement and growth into other sectors where motor voltages may go even higher, such as heavier vehicles like trucks, buses and off-highway machinery.
Enlarging its range of insulation materials for e-mobility, Coveme has just launched a battery spacer material, DyBond HR, developed in partnership with Schweizer, which provides both dielectric and thermal insulation between cells within modules, and between modules within packs. Essentially, DyBond HR is a form of Nomex that has been treated with a humidity resistant resin that ensures it retains its dimensions and does not swell or warp when exposed to moisture, either in storage or in operation, Rumi explains.
While adding resistance to humidity, the resin preserves all of the insulating, heat-resistant and flame-resistant properties of the Nomex, while adding its own flame-retardant properties that provide a further barrier against fire.
Already in service in customers’ EV batteries, DyBond HR can be supplied by Coveme as rolls or sheets, or through a partner as shaped components ready for fitting.
Click here to read the latest issue of E-Mobility Engineering.
ONLINE PARTNERS
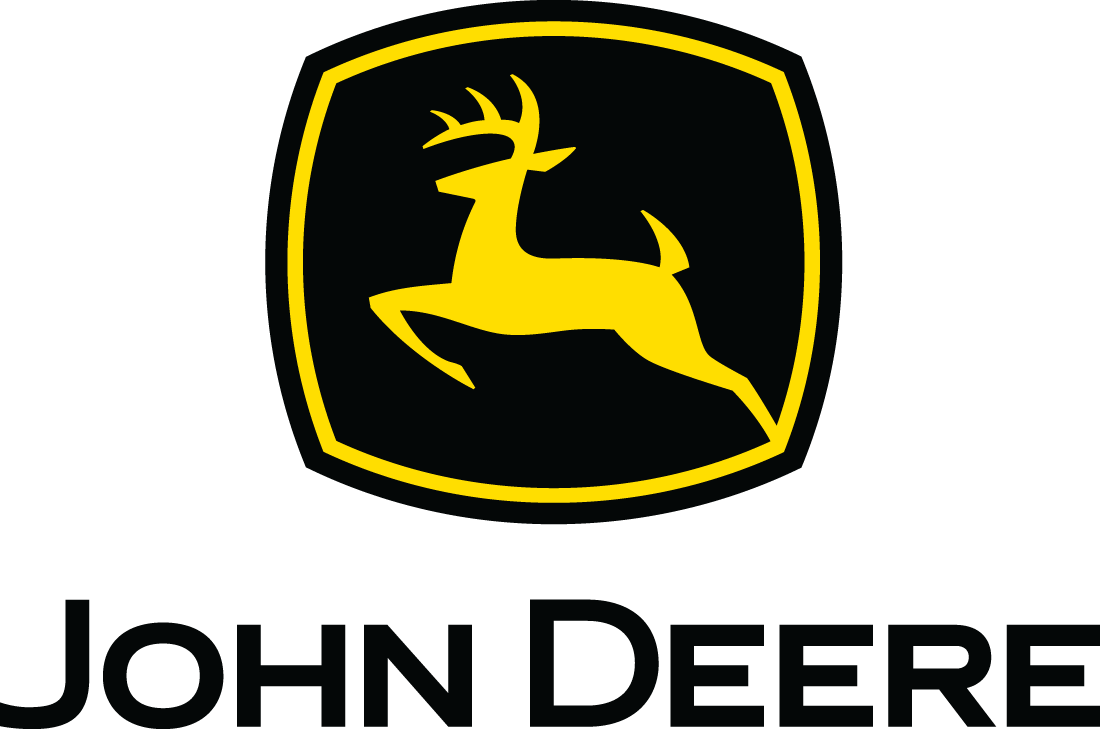
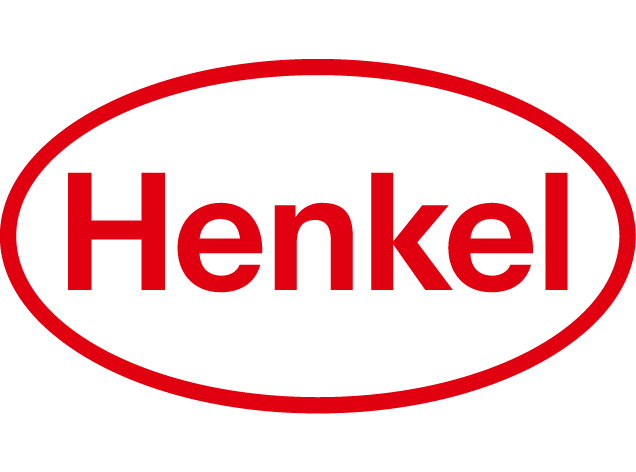
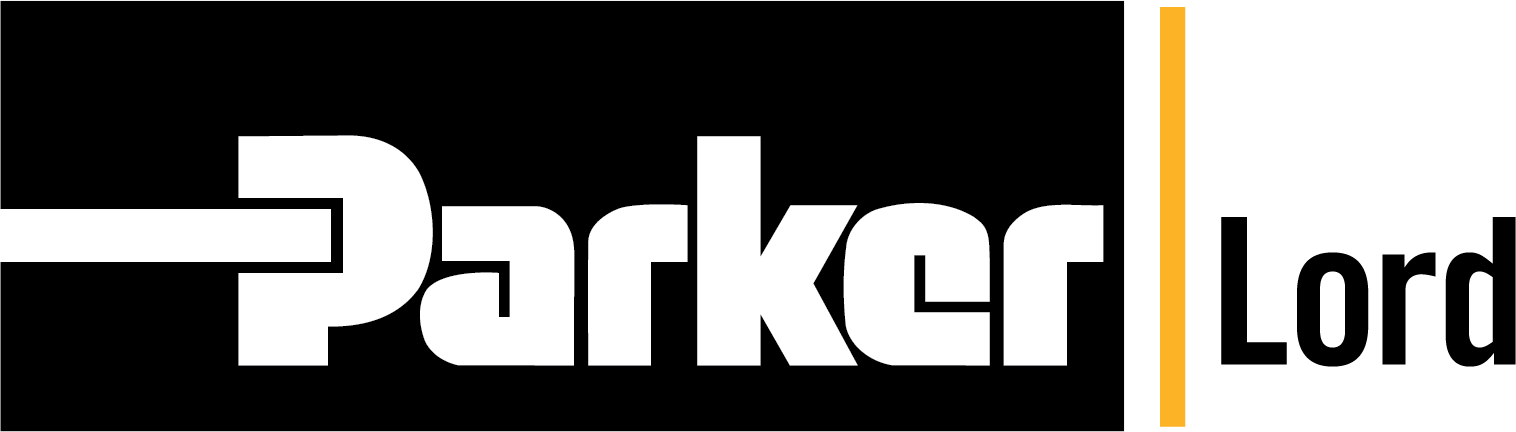
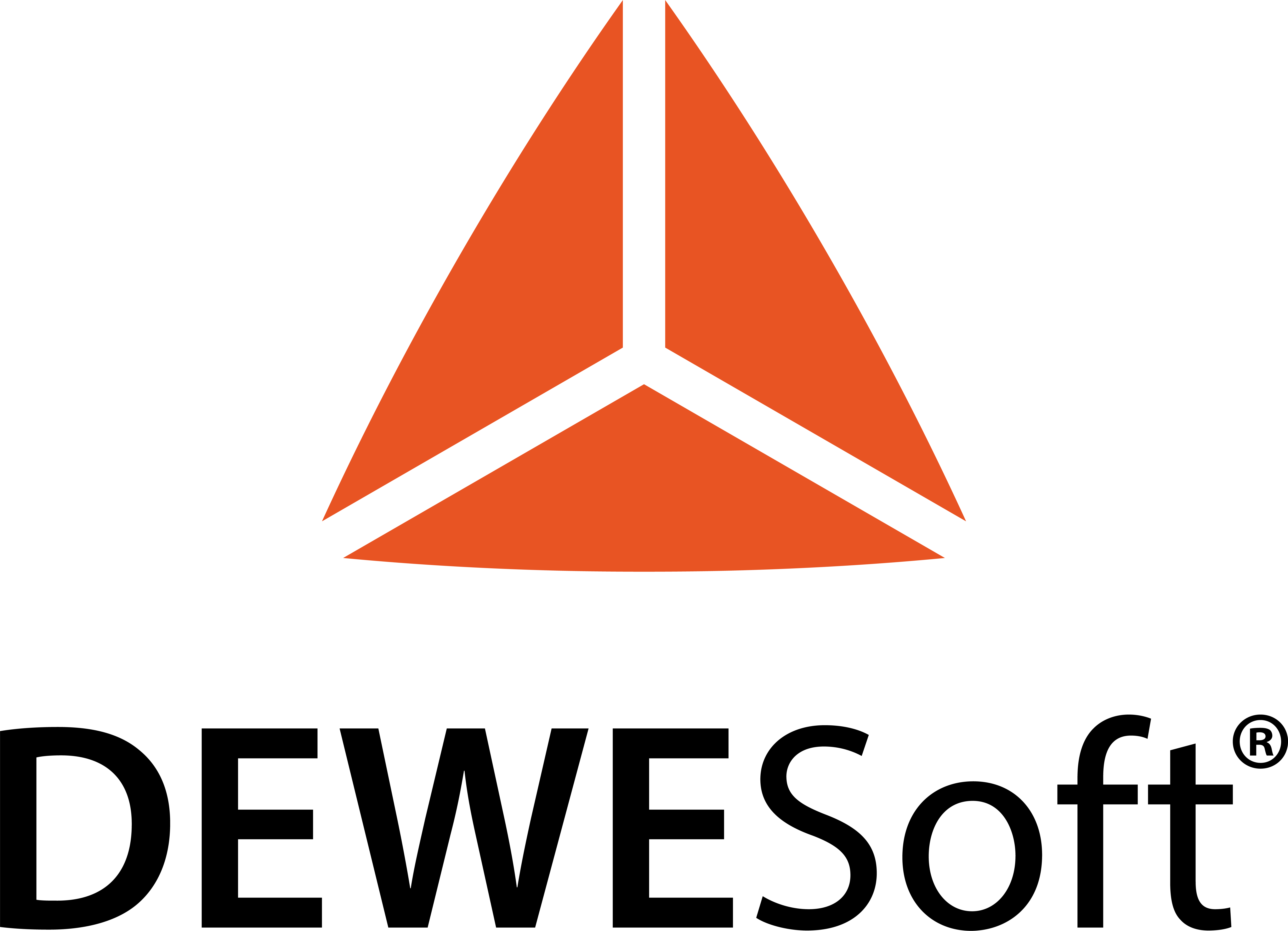
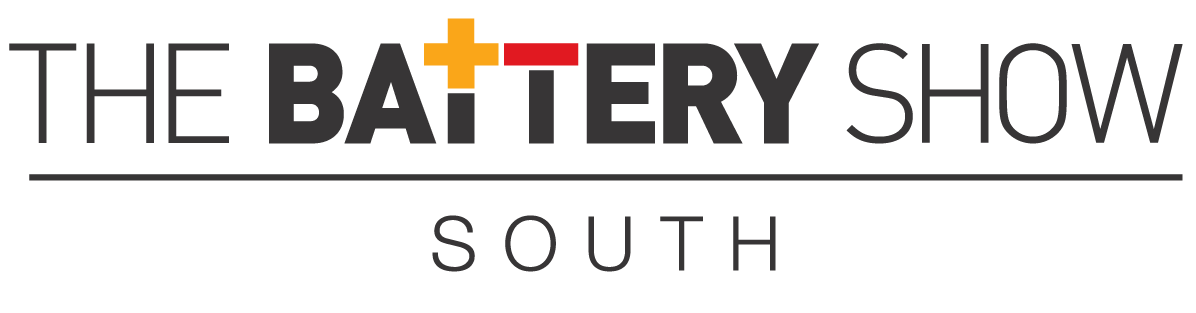
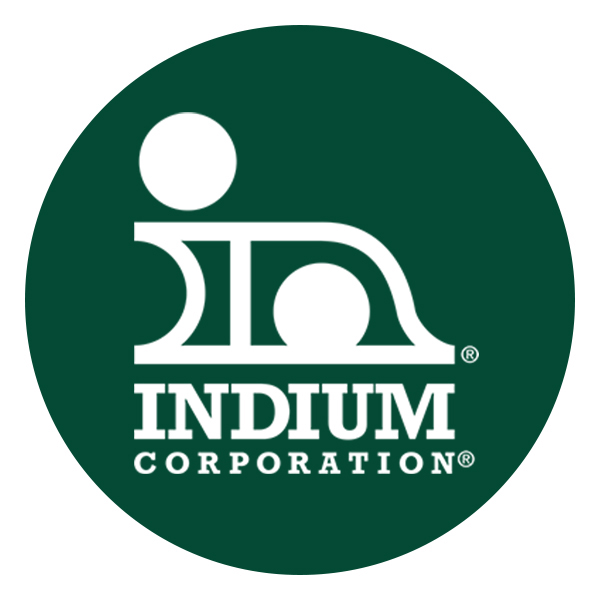

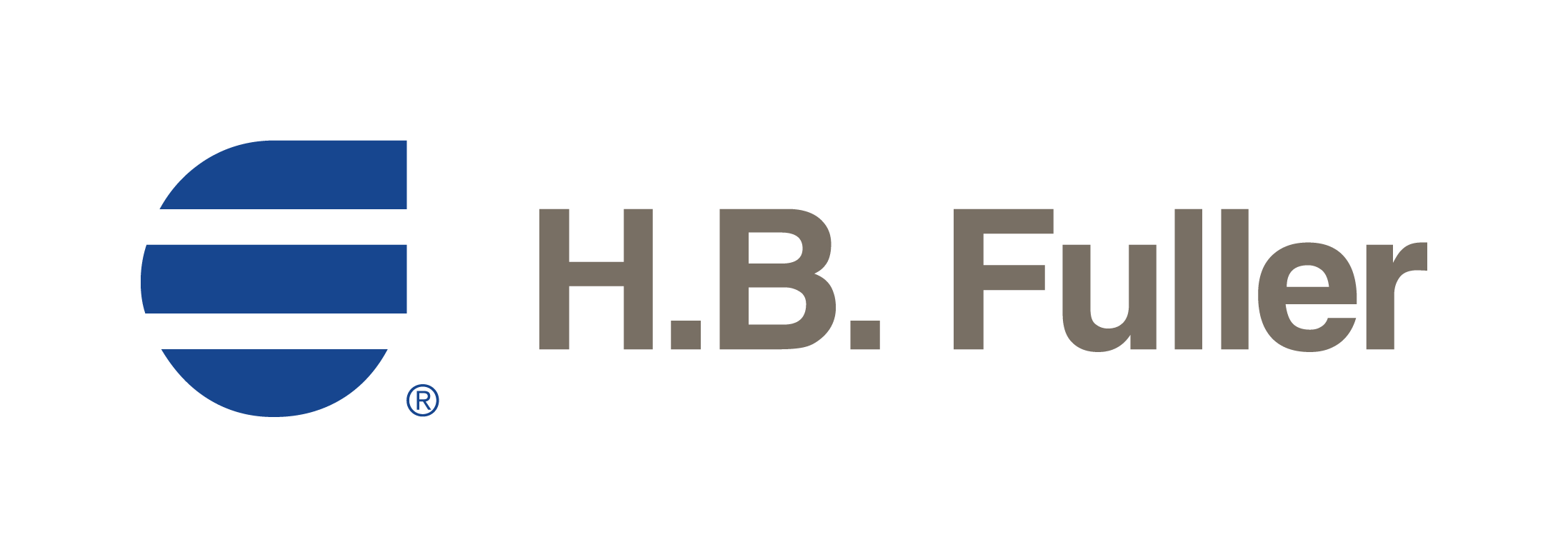
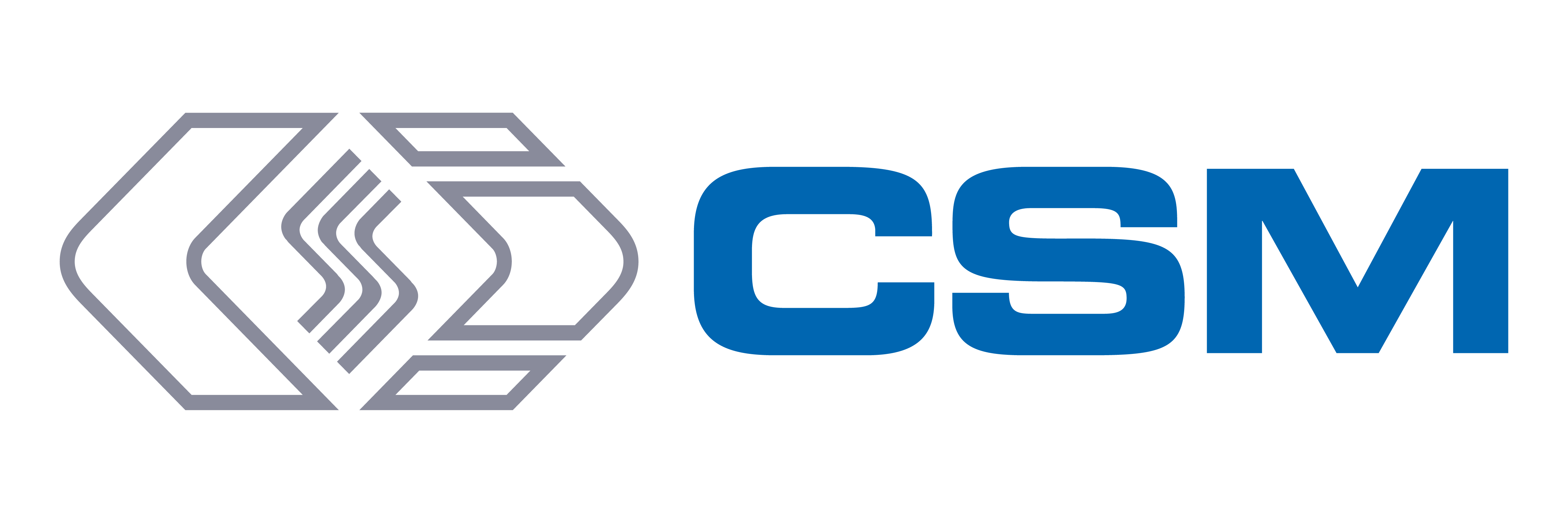
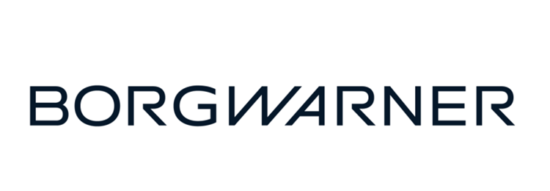