Cool SiC inverters move
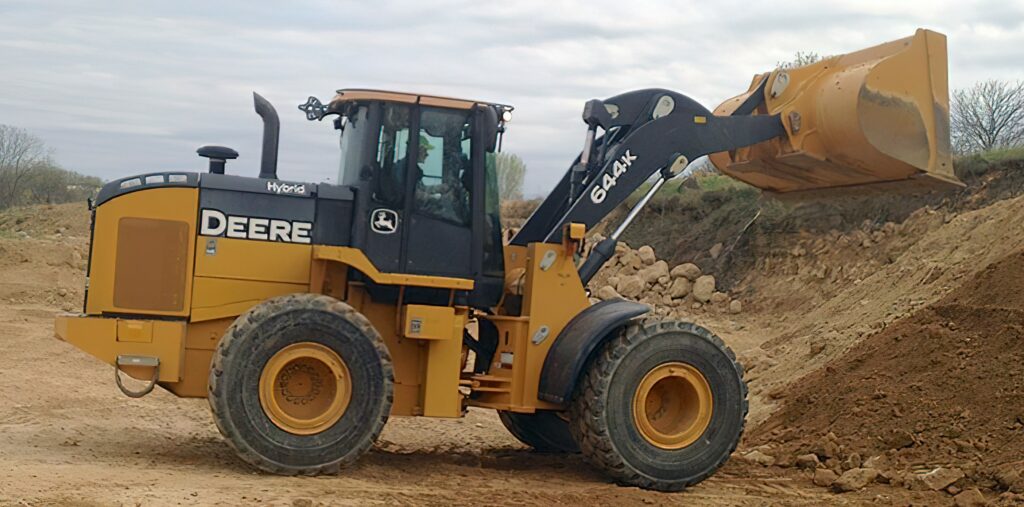
Researchers at the US National Renewable Energy Laboratory (NREL) have been working with heavy-duty equipment maker John Deere on a new thermal management system for SiC inverters (writes Nick Flaherty).
Equipment such as trucks and construction machines account for 39% of greenhouse gas emissions in the transportation sector, so there has been a focus on electrifying these systems.
The inverter is responsible for controlling the power flow between DC and AC electrical systems in order to run vehicle systems, accessories, and electric machines such as motors and generators. Using SiC transistors can provide a four times increase in power density over previous silicon-only inverters, but this is driving the need for more efficient thermal management.
“The key to NREL’s design innovations for SiC thermal management is to improve the heat transfer coefficient, which allows this system to cool itself efficiently and continuously during operation with the engine coolant,” said Kevin Bennion, NREL senior researcher and a thermal management expert.
The thermal management system helps to optimise system efficiency while regulating the operating temperatures of the SiC modules, which are directly cooled using 115 C water-ethylene glycol.
A common strategy for the thermal management of EV inverters is to run a fluid coolant parallel to the component’s surface to transfer heat and cool the system quickly. However, the NREL system incorporates a perpendicular jet flow with mini-channel- and mini-manifold-based cooling systems to extract heat from the inverter and power module. This design enables a heat transfer coefficient as high as 93,000 W/(m2K), more than four times higher than current commercial systems.
The design uses an existing diesel engine’s cooling system for a simplified engine-coolant-capable architecture. Conventional heavy-duty inverters require a separate coolant system to operate successfully while ensuring the inverters’ durability. By eliminating the need for a separate cooling circuit, the NREL design achieves a power density of 43 kW/litre, which the researchers say is a 378% improvement over baseline silicon systems.
The smaller size of the cooling system and the inverter allows for a smaller and lighter system, with benefits to efficiency and operating costs. The technology has been evaluated by the John Deere engineering team led by Dr Brij Singh.
ONLINE PARTNERS
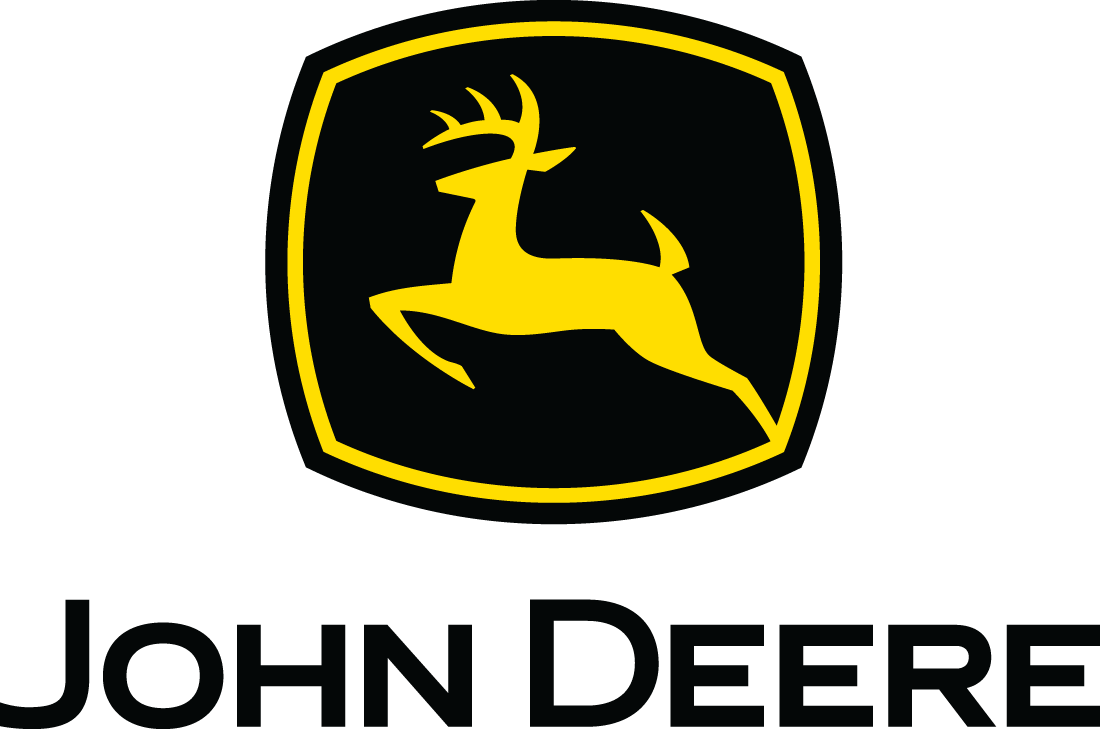
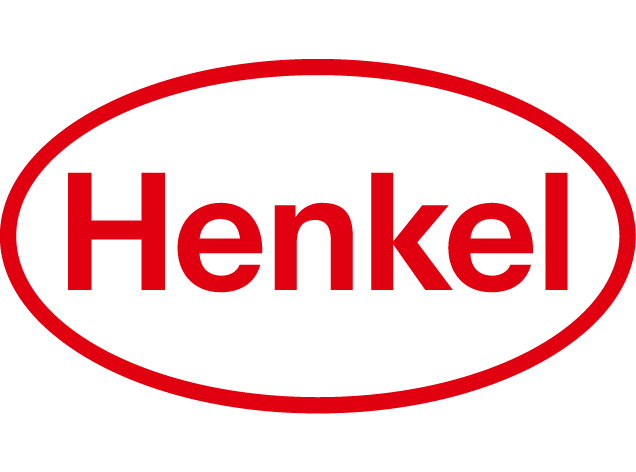
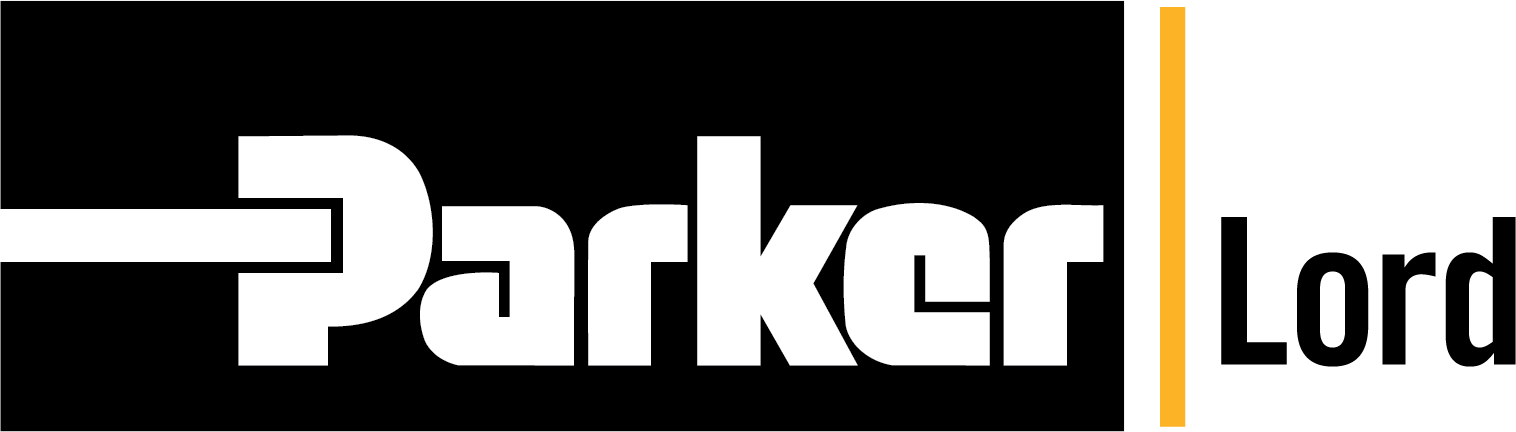
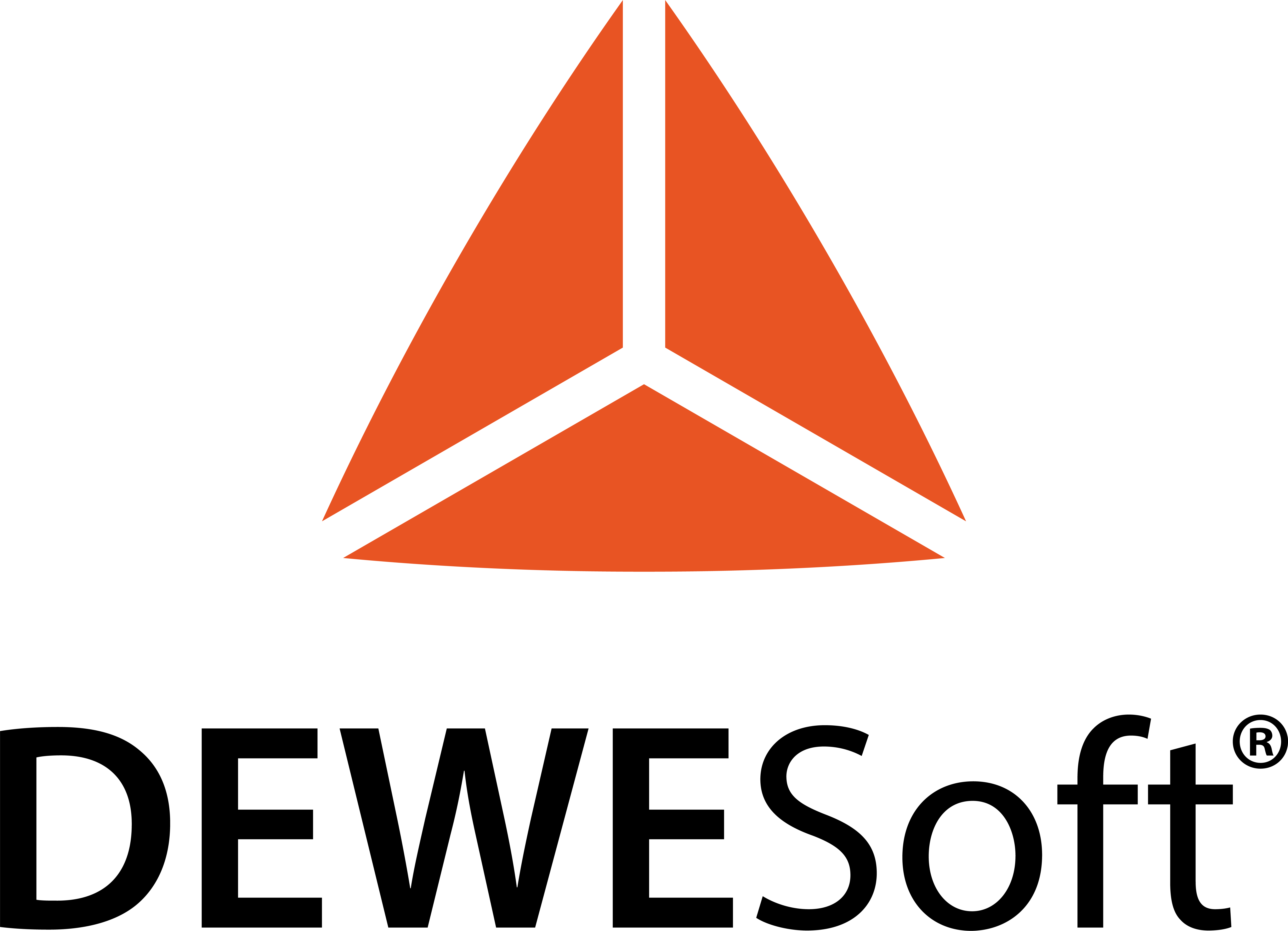
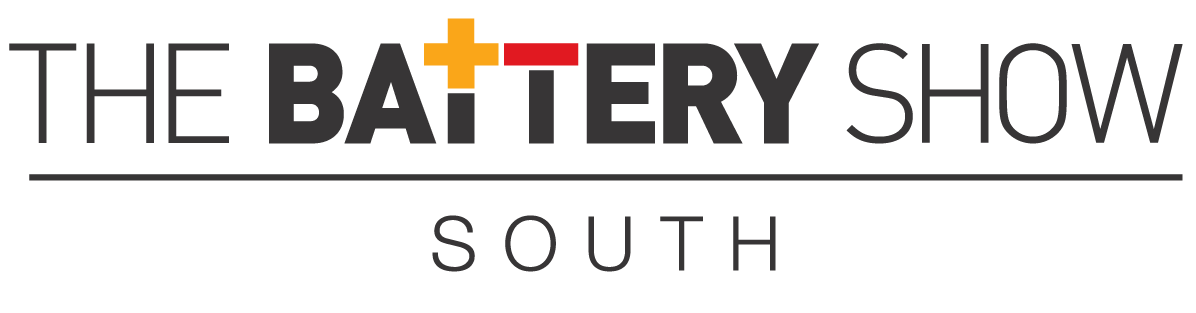
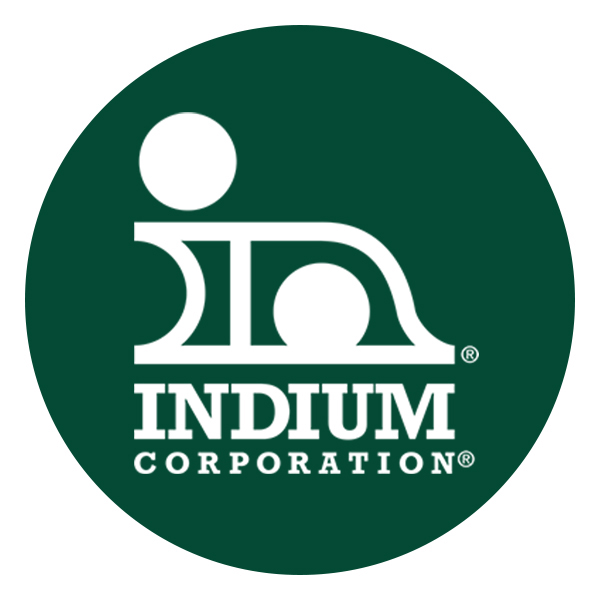

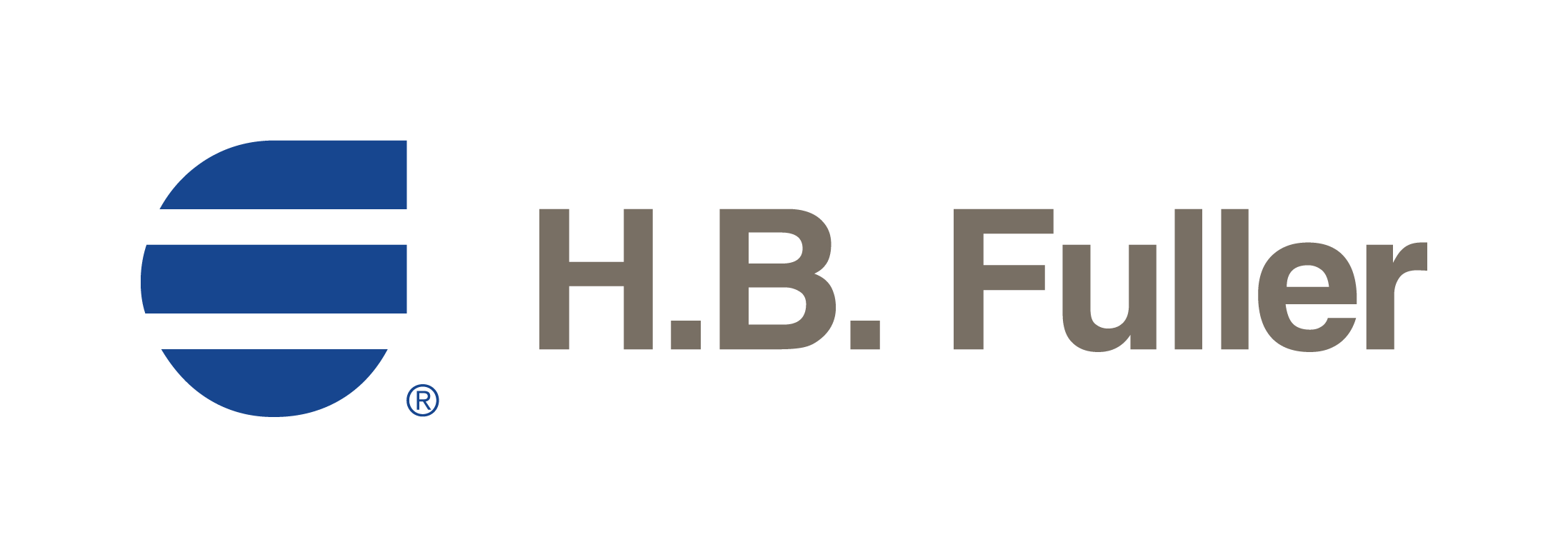
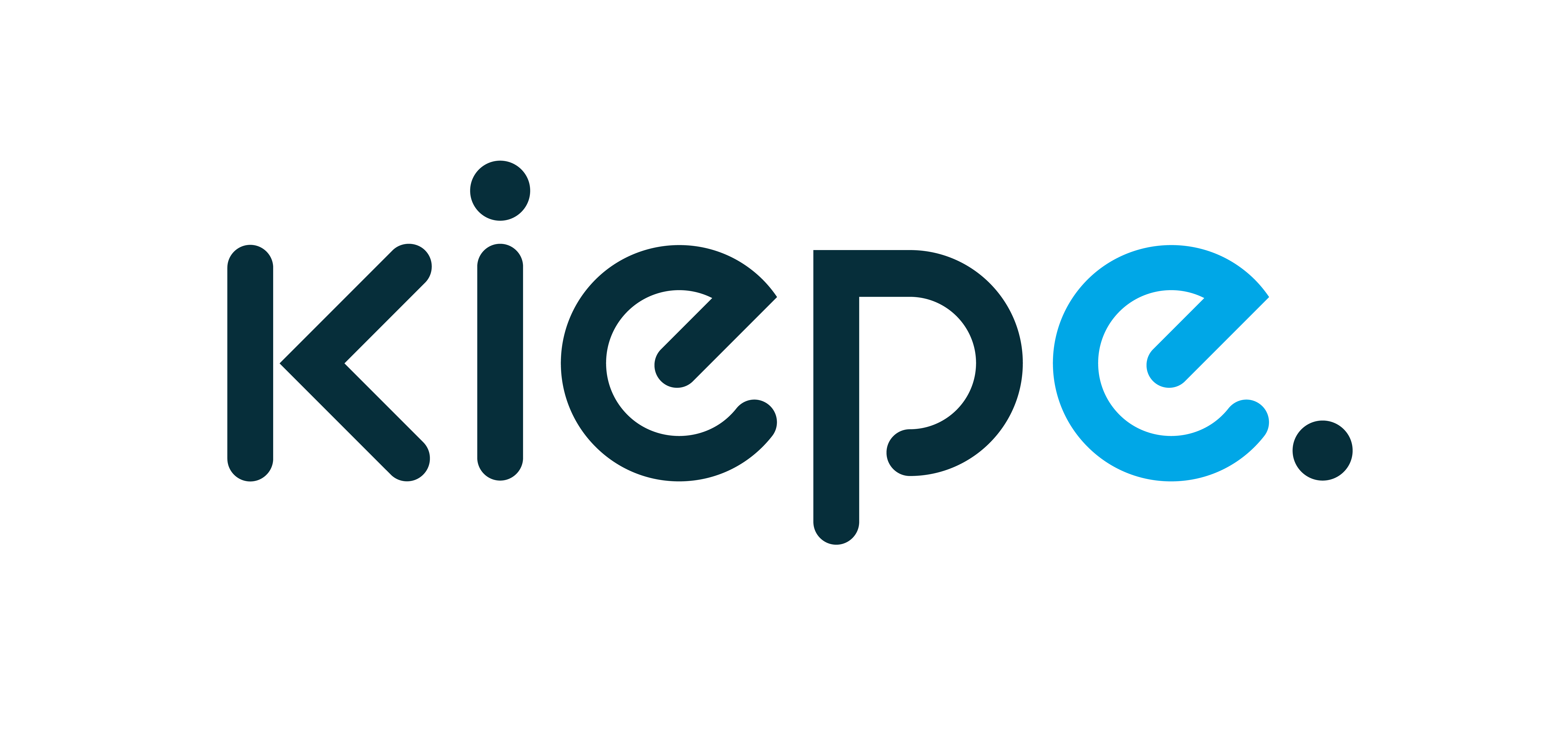
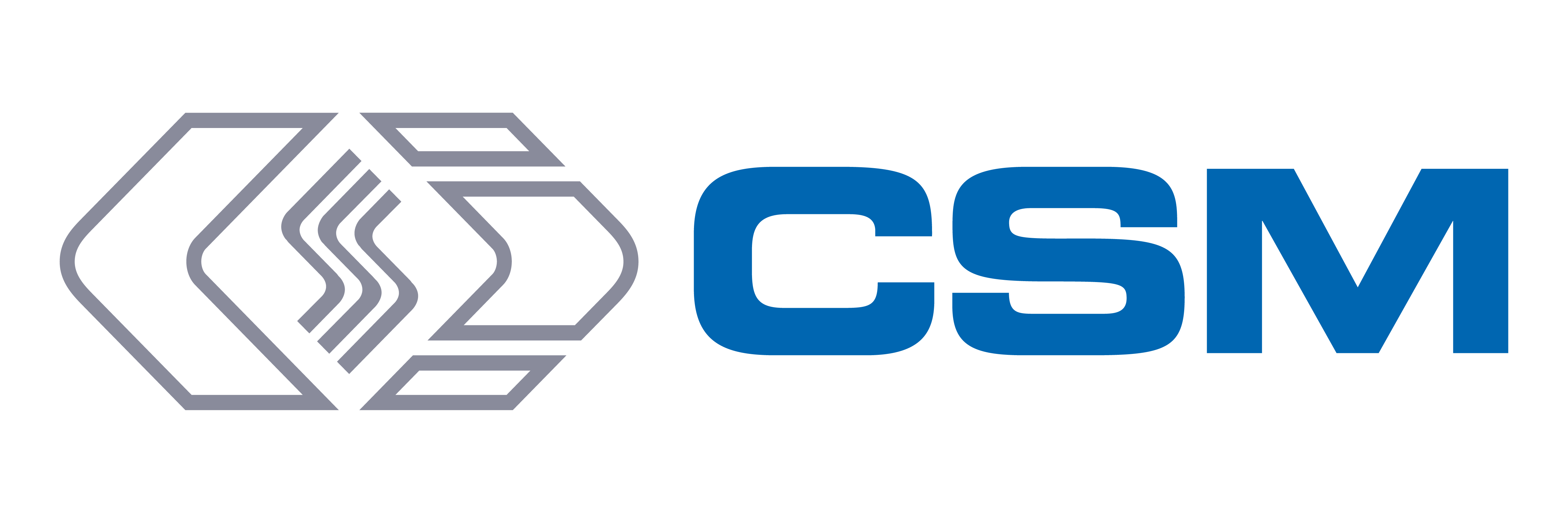