Cathode materials
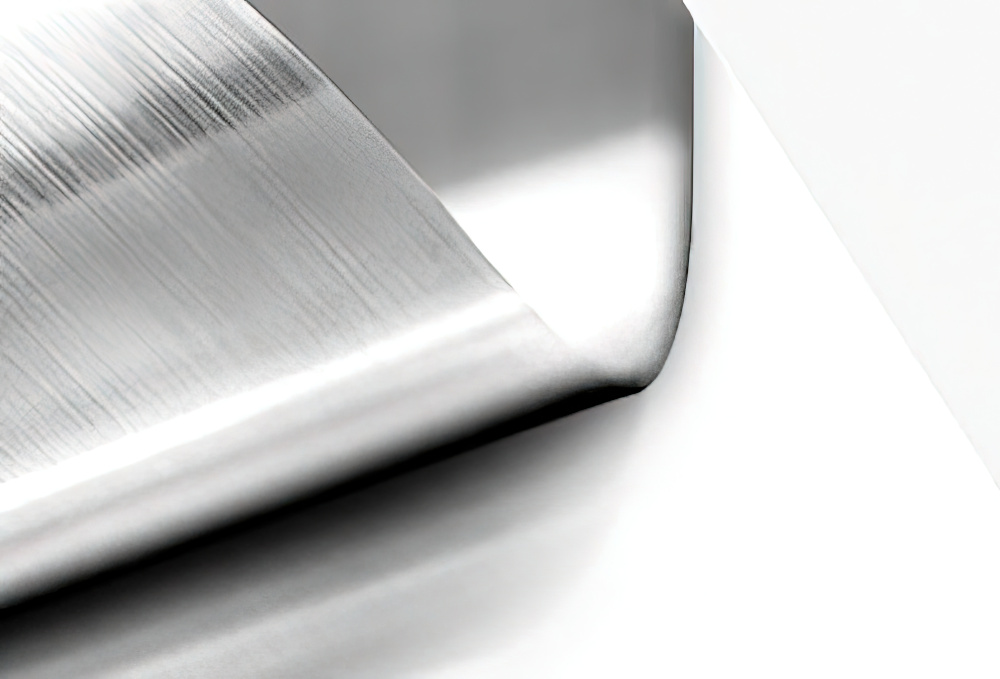
(Courtesy of Targray)
Positive steps
Researchers have been announcing advances in lithium-ion cathode materials and their manufacture, as Nick Flaherty reports
There are three main types lithium-ion batteries for e-mobility, all with different balances of energy capacity, charging rate and long-term stability. There are however also many different approaches to constructing cathodes, using different chemical compositions, crystal structures and methods of high-volume manufacturing. Principally, the cathode types are layered oxides with nickel, manganese and cobalt (NMC), and spinel and polyanion oxides such as lithium iron phosphate (LFP).
The first layered oxide cathode used lithium cobalt dioxide (LiCoO2), where Li+ and trivalent Co3+ ions are ordered on the alternate planes with a cubic close-packed array of oxide ion. This is referred to as the O3 structure.
This enabled a substantial increase in the operating voltage from less than 2.5 V from earlier sulphide cathodes to around 4 V, allowing a cell to be assembled without having to use a metallic lithium anode, with fast charge/discharge characteristics and good reversibility.
The large charge and size differences between Li+ and Co3+ ions lead to good ordering of the ions, which is critical to support fast 2D lithium-ion diffusion and conductivity. That means LiCoO2 remains one of the best cathodes to date, thanks to its 4 V operating voltage.
The LiCoO2 cathode solved two major challenges associated with the sulphide cathodes. As well as the higher voltage, it allows a lithium-free anode using materials such as graphite or silicon to be paired with LiCoO2 to give the modern-day lithium-ion cell that was pioneered by Sony in 1991.
However, despite good electrochemical performance, the practical capacity of LiCoO2 is limited to around 140 mAh/g, says Professor Arumugam Manthiram, Chair in Engineering at the Walker Department of Mechanical Engineering at the University of Texas and developer of the polyanion oxide technology.
This capacity limit has led to a number of other layered LiCoO2 oxides being investigated over the years, driving the substitution of cobalt with manganese and nickel for NMC cathodes.
Some of these oxides can be directly synthesised using direct high-temperature reactions, while others such as LiMnO2 and LiFeO2 do not crystallise in the O3 structure when synthesised by high-temperature reactions, but can be obtained by ion-exchanging the sodium analogues (NaMO2) with lithium salts.
In NMC, the Mn3+ tends to become oxidised during synthesis to Mn4+ by reducing Ni3+ to Ni2+. The Mn4+ helps the incorporation of the nickel as a stable Ni2+ into NMC and serves as a structural stabiliser without participating in the charge/discharge process.
In NMC, each transition-metal ion has its own advantages and disadvantages (see table) with chemical stability and structural stability, in which cobalt and manganese are diametrically opposed.
Manganese does not suffer from any chemical instability involving oxygen release from the lattice, in contrast to cobalt. On the other hand, manganese suffers from structural instability as it can readily migrate from the transition-metal plane to the lithium plane, leading to a voltage decay during cycling. However, it is more abundant and environmentally benign than cobalt, which can only be sourced from a small number of mines around the world with many in unstable economies.
In contrast, cobalt enjoys good structural stability without such cation migration.
Nickel lies between manganese and cobalt in all the five criteria in the table, and there is a trend is to progressively increase the nickel content and decrease the cobalt content in NMC so that the capacity can be increased while lowering the cost.
For example, NMC powders from materials supplier Targray include NMC333, 532, 622 and 811. NMC333 has an energy density of 154.8 mAh/g, while 532 reaches 187.0 mAh/g at 4.5 V, 622 reaches 175 mAh/g and 811, the most popular, reaches 203.4 mAh/g at 4.3 V.
Spinel oxides
Chemical stability | Mn > Ni > Co |
Structural stability | Co > Ni > Mn |
Electrical conductivity | Co > Ni > Mn |
Abundance | Mn > Ni > Co |
Environmental benignity | Mn > Ni > Co |
LiMn2O4, or spinel, has a cubic close-packed array of octahedral oxide ions. The 3D lithium-ion diffusion pathway allows fast lithium-ion conductivity to provide even faster charge/discharge characteristics for Li1-xMn2O4 with good reversibility compared to LiCoO2, says Prof Manthiram.
This gives an operating voltage of 4 V with a practical capacity of less than 130 mAh/g.
Interestingly, an additional lithium can be inserted into an empty octahedral site (at a position called 16c) at 3 V to form a lithiated spinel called Li2[16c]Mn2[16d]O4.
Spinel is of particular interest for solid-state batteries as materials such as LiNi0.5Mn1.5O4 (LNMO) have a high energy density, low in cost and are environmentally friendly as they use no cobalt, However, sulphide solid electrolytes are not compatible with an LNMO cathode, so work is being done on sulphurising LNMO for an essentially new LNMOS cathode. This can improve the compatibility of the layers in a solid-state battery and provide three times higher initial discharge capacity along with improved cycle stability.
Other versions of spinel use titanium or vanadium, but one titanium material, LiTi2O4, operates at around 1.5 V so it is not suitable as a cathode. Nor is the vanadium material LiV2O4 a practical choice, since it suffers from structural changes and a lower voltage, of around 3 V, Prof Manthiram says
One important advantage on moving from LiCoO2 to LiMn2O4 is the significant reduction in cost, as manganese is as much as 100 times cheaper than cobalt. However, one critical issue with LiMn2O4 is the dissolution of manganese from the lattice into the electrolyte in presence of trace amounts (ppm levels) of hydrogen ions if the electrolyte is too acid. That can degrade the cathode but also promotes the migration of manganese to the anode and can severely poison a graphite anode, and as a result reduce the cycle life of lithium-ion cells.
There have been efforts to prepare both LiCo2O4 and LiNi2O4 spinel oxides by chemically extracting 50% lithium from LiCoO2 and LiNiO2 to obtain Li0.5CoO2 and Li0.5NiO2, followed by heating at moderate temperatures of 200-400 ºC to transform the layered phase to spinel phase.
However, such attempts result in either incomplete transformation at low temperatures or loss of oxygen. That creates a mixture of spinel-like phases and reduced Co3O4 or NiO phases owing to the instability of Co3+/4+ and Ni3+/4+. These spinel-like phases also exhibit poor electrochemical performance owing to a lack of well-formed crystalline structures.
Another approach has been to partially substitute manganese with other ions such as chromium, cobalt and nickel. One example is LiMn1.5Ni0.5O4 spinel, where the manganese exists as Mn4+ and the nickel exists as Ni2+, as in NMC cathodes. LiMn1.5Ni0.5O4 operates at about 4.7 V with a reversible capacity of about 135 mAh/g. However, LiMn1.5Ni0.5O4 spinel suffers from capacity fade owing to the lack of suitable stable electrolyte at 4.7 V.
Polyanion oxides
The third class of cathode is the polyanion oxides using molybdenum. Both Fe2(MoO4)3 and Fe2(WO4)3 cathodes exhibit a flat discharge voltage of 3 V, which is higher than that seen with simple oxides such as Fe2O3 or Fe3O4 (less than 2.5 V).
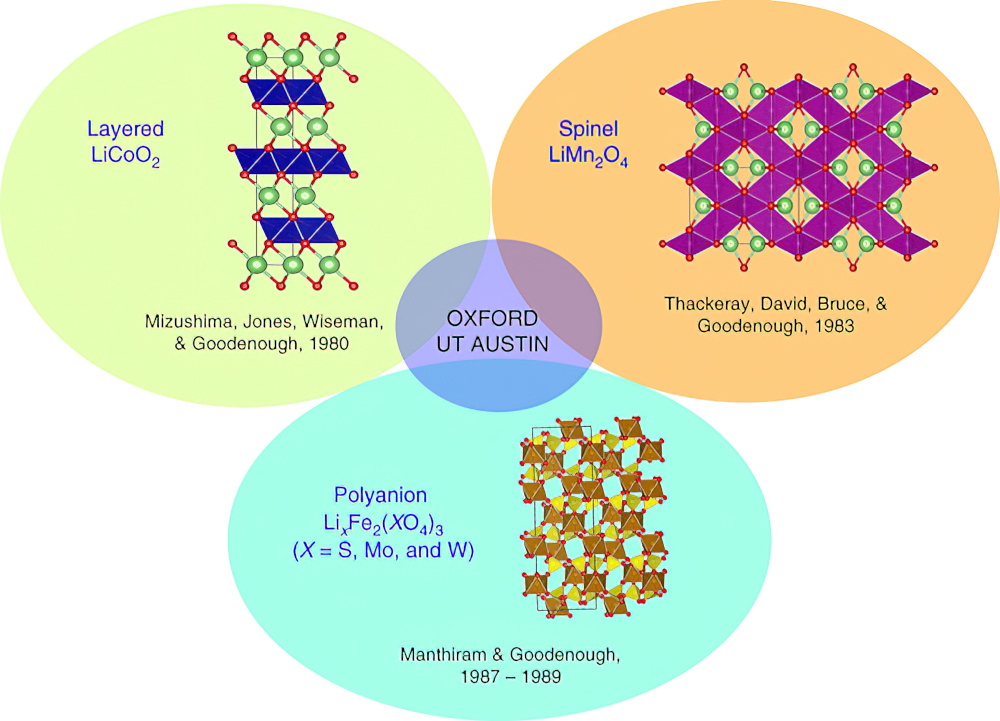
(Courtesy of Arumugam Manthiram)
This ability to increase the operating voltage by going from simple oxides to polyanion oxides led to polyanion oxides with phosphate groups being investigated in the late 1980s.
LiTi2(PO4)3, LiZrTi(PO4)3, NbTi(PO4)3 and SbTi(PO4)3 all had an operating voltage of 2-3 V, with the LixSbTi(PO4)3 system displaying the highest voltage of 3 V compared with about 1.5 V for the Ti3+/4+ couple in a simple oxide such as TiO2.
The ability to increase the voltage drastically to as high as about 5 V in polyanion oxide cathodes, for example in LiMPO4, has led to a range of sulphates, phosphates and silicates being used in lithium-ion cells as well as sodium-ion cells with Li3V2(PO4)3, Na3V2(PO4)3, and Na3V2(PO4)2F3 and LiFePO4.
After Sony commercialised lithium-ion batteries with LiCoO2 cathodes and graphite anodes in 1991, researchers focused on polyanion oxides, says Prof Manthiram, driving the identification of olivine LiFePO4 as a cathode material in 1997.
LFP materials such as PLFP02113 from Targray have a high specific capacity of 0.2C discharge (more than 150 mAh/g) with a 10C discharge rate and low-temperature performance for applications such as electric buses.
Pros and cons
Layered and spinel class of oxides offer good electronic conductivity, while the polyanion oxide class suffers from poor electronic conductivity. That means polyanion oxide cathodes require the particles to be synthesised small and coated with conductive carbon, which often increases the processing cost and introduces inconsistencies in performances.
Layered and spinel oxides have close-packed structure with high densities, while the polyanion class of oxides generally have lower densities, which is further reduced by that need to make them as small particles coated with carbon, leading to a lower volumetric energy density and more suited to e-mobility applications with lower peak power requirements, such as trucks.
However, the polyanion cathodes have high thermal stability and better safety than the layered and spinel oxide cathodes. The small carbon-coated particles can also sustain higher charge/discharge rates thanks to their good structural integrity, despite their lower volumetric energy density.
Using abundant transition metals such as iron rather than cobalt also offers sustainability advantages.
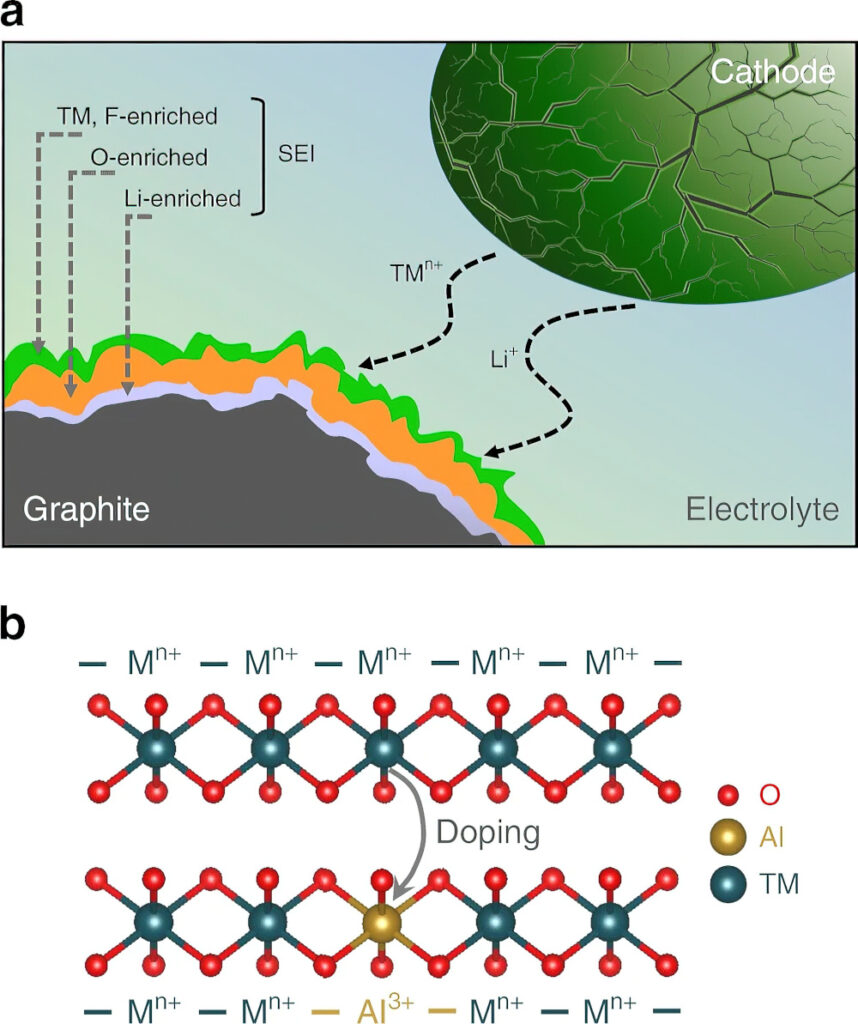
(Courtesy of Arumugam Manthiram)
Between the layered and spinel oxides, layered oxides are more appealing. They have a wider range of compositions than spinel oxides owing to the inability to stabilise highly oxidised M3+/4+ states by conventional synthetic processes for the spinel oxides.
The spinel cathodes are largely limited to LiMn2O4, and the high operating voltage of about 4.7 V and the higher power capability is appealing, but production is hampered by the lack of adequate electrolytes that can survive at this higher operating voltage.
More recently, increasing the nickel content and lowering or eliminating the cobalt content in NMC cathodes is becoming much more prominent. However, layered oxides with a high nickel content have three critical challenges – cycle instability, thermal instability and air instability.
The deposition of metals on the graphite anodes compromises the electrolyte and leads to the formation of a thick solid electrolyte interphase (SEI) layer, which grows with the cycles as more transition-metal ions dissolve and migrate to the anode. After a certain number of cycles, typically more than 500, the SEI layer’s thickness also increases with increasing nickel content owing to the increasing transition-metal dissolution and deposition on the graphite anode.
High-nickel cathodes also suffer from cracks during the charging cycles, which further exaggerates the surface reactivity with the electrolyte and increases the metal dissolution and SEI formation, resulting in rapid capacity fade as cycling progresses.
However, doping the cathode with aluminium and using surface stabilisation strategies to minimise the volume changes, crack formation and surface reactivity can help to overcome the challenges with high-nickel cathodes.
These layered oxide cathodes with high-nickel content have become appealing, but intuitive bulk and surface stabilisation strategies are needed to overcome the associated cycle, thermal and air instabilities.
Altered microstructure
To improve the energy per unit volume of cathode materials, researchers in Russia have developed two versions of NMC cathodes with a single crystal microstructure.
“Cathode materials are an important bottleneck as far as EV batteries are concerned,” says Professor Artem Abakumov, principal investigator at Skoltech Energy.
“The cathodes in batteries powering electric cars tend to use layered transition metal oxides, including nickel-rich ones. We have improved two commonly used materials of this kind, achieving a 10-25% increase in energy density. That translates into smaller cathodes, more compact batteries and therefore greater energy storage capacity for the same volume. As an added bonus, the material is slower to deteriorate.”
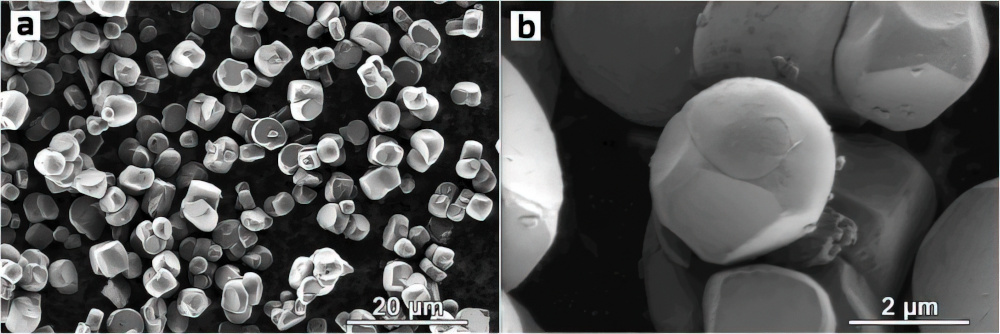
(Courtesy of Skoltech)
Without changing the chemical composition, Skoltech researchers improved NMC811 (eight parts nickel, one part manganese, one cobalt) and NMC622 (six parts nickel, two manganese, two cobalt) cathodes by tweaking the microstructure.
Conventional NMCs are powdered polycrystalline materials, where each secondary particle consists of randomly oriented grains. The crystal structure within any given grain is nearly flawless, but no two grains fit perfectly together and there are some empty spaces at grain boundaries. Creating a single crystal eliminates these gaps.
“Our material is a single-crystal NMC with spherical particles, which combines the best of both worlds as far as maximising density goes,” says Aleksandra Savina, a researcher on the project at Skotech. “Unlike polycrystals, the powder particles don’t have an internal structure, so there are no wasted spaces at grain boundaries. On top of that, you can pack more spherically shaped single crystals into the same limited volume than octahedron-shaped ones, so you get more density too.”
Besides denser packing, the spherical shape of the crystals reduces the area of contact with the electrolyte, minimising unwanted interactions that over time cause cathode degradation owing to crack formation in the particles of conventional NMCs. That should prolong the operating life of the cathode and battery.
To create the single crystal, the researchers tweaked the synthesis procedure. This starts with a precursor with homogeneously distributed nickel, manganese and cobalt, mixing in lithium hydroxide or some other source of lithium. This is annealed at high temperatures.
“What we do is after adding the lithium-containing compound, we also mix in an inert salt that has a low melting point, and we melt that mixture and anneal at high temperature,” says Alina Pavlova from the project. “We then wash away the salt and anneal again to get rid of the products of any unwanted reactions with water.
“The key though is that, depending on which inert salt is used and in what amount, the particle geometry will change. With conventional synthesis, on the other hand, there’s really not much you can do to affect morphology.”
The team identified the salt parameters that promoted spherical particle formation. Tests confirmed that the resulting material had the same energy storage capacity per unit mass as the commercial analogues but had greater energy density, enabling more power to be packed into the same limited space.
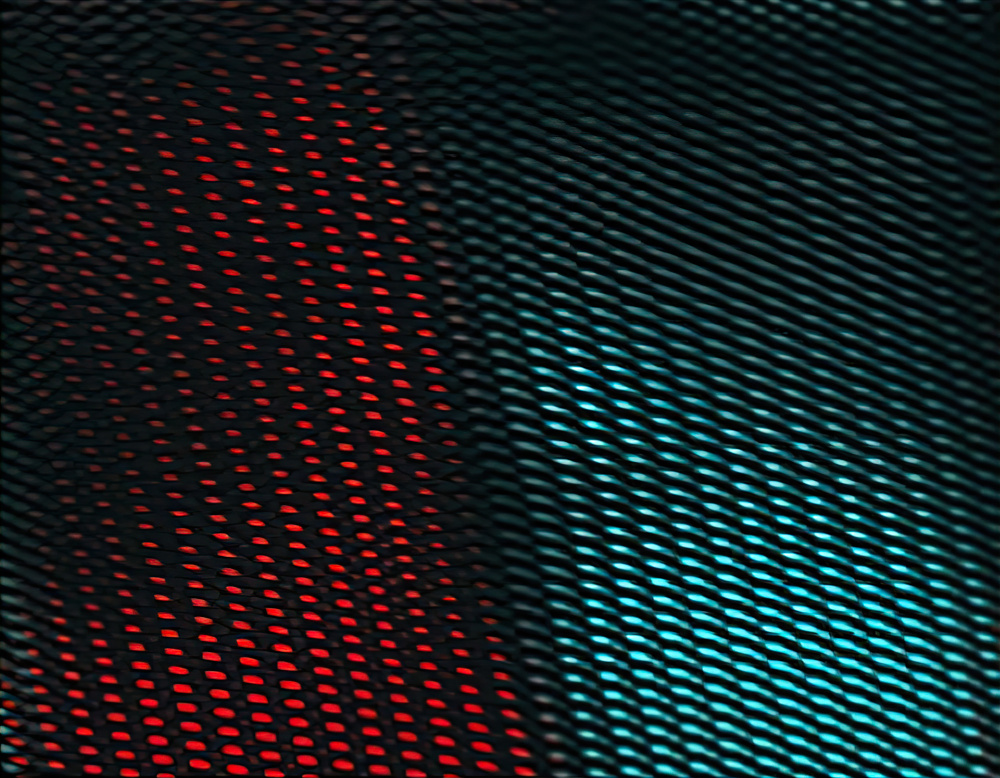
(Courtesy of Argonne National Laboratory)
The researchers are now experimenting with particle size, combining smaller and larger spheres for denser packing. The team will also pursue layered transition metal oxides that would replace even more cobalt and manganese atoms with nickel, further enhancing energy storage capacity.
However, there is a drive to retain cobalt. Researchers at Stanford University have shown that cobalt’s thermodynamic stability in layered structures is essential in enabling access to higher energy densities without sacrificing performance or safety, effectively lowering battery costs per kWh despite increasing raw material costs.
The supply growth required to support intermediate cobalt-content cathodes for 1.3 billion EVs by 2050 is within historical trends for major industrial metals, says Professor William Gent at Stanford, although providing sufficient supply from unstable economies – or what he calls “challenging jurisdictions” – is likely to remain a problem.
Cathode cracks
Researchers at the US Department of Energy’s Argonne National Laboratory have also been working on single-crystal cathodes.
“The present-day NMC cathode has posed a major barrier to operation at high voltage,” says Guiliang Xu, assistant chemist at Argonne. “During the charge/discharge cycles, performance rapidly declines owing to cracks forming in the cathode particles. For several decades, battery researchers have been seeking ways to eliminate those cracks.
Xu and his team had previously developed a protective polymer coating around each polycrystalline particles to minimise cracking at the grain boundaries. They also looked at a different approach to avoid this cracking that involves using single-crystal particles; however this material still formed cracks with cycling, so they looked at the reason for this cracking.
“When we look at the surface morphology of these particles, they look like single crystals,” says Argonne physicist Wenjun Liu. “But when we use a synchrotron X-ray diffraction microscopy and other techniques, we find boundaries hiding inside.”
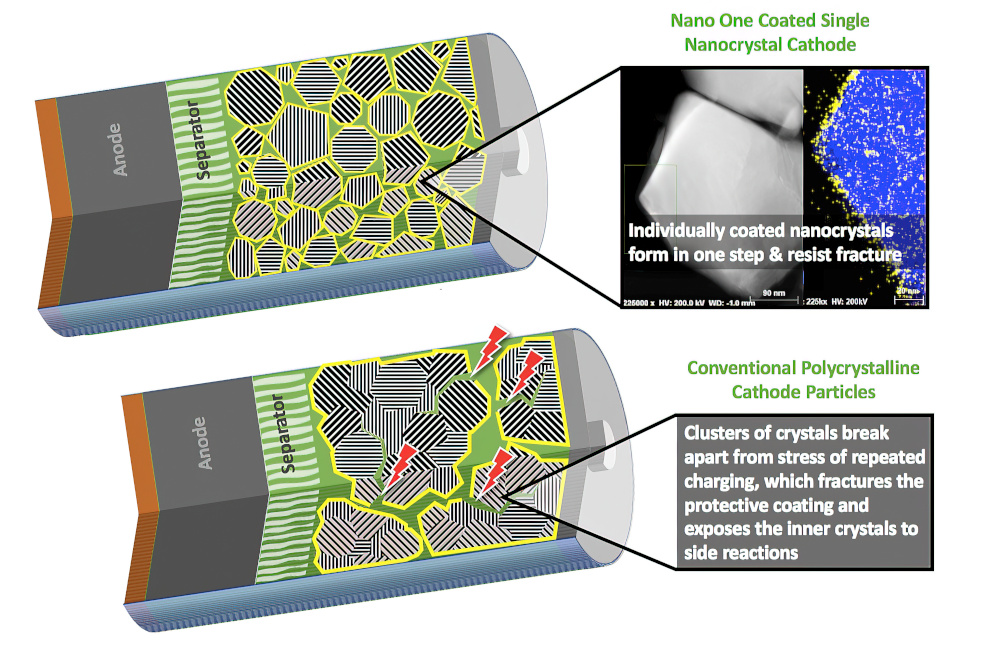
(Courtesy of Nano One Materials)
The team developed a method for producing boundary-free single crystals by focusing on the oxygen redox instability from the domain boundaries in single-crystalline cathode particles. By investigating single-crystalline cathodes with different domain boundaries structures, they could eliminate the boundaries and improve the mechanical integrity during battery cycling.
Testing small cells with such single-crystal cathodes showed a 25% increase in energy storage per unit volume, with almost no loss of performance over 100 cycles of testing. By contrast, over the same cycle life, the capacity declined by 60-88% in NMC cathodes composed of single crystals with many internal boundaries or with coated polycrystals.
“We now have guidelines that battery manufacturers can use to prepare cathode material that is boundary-free and works at high voltages,” says Khalil Amine, an Argonne Distinguished Fellow who worked on the project. “And the guidelines should apply to other cathode materials besides NMC.”
These show how the structure of the cathode depends on a combination of materials and the manufacturing process.
The processes for manufacturing cathodes are also coming under scrutiny for the cost of the energy to create the high temperatures needed, the greenhouse gases produced as a result, and the cost of materials such as cobalt.
One-pot process
Addressing this issue, Nano One has developed a ‘one-pot’ process to reduce the complexity of the manufacturing process.
“When you look at cathodes for lithium batteries, there are the lithiated NMC with transition metal oxides, and the other class is the phosphate LFPs, sometimes with manganese which gives you LMFP,” says Dr Stephen Campbell, CTO at Nano One.
“They are very different materials with different markets, and there is no single winner as they are application-specific. Instead, we have a technology that changes the way the materials are made.”
“NMC is made using metal sulphates as a precursor, but the conventional way of manufacturing makes it difficult to meet the sustainability requirements of Europe and the US, as there is a lot of sodium sulphate as waste,” he says. “That means you can’t take the manufacturing from China and put it into the US or Europe.”
Rather than using sulphates as a feedstock, the Nano One uses metals with a bio-material that burns away as ash.
“The big difference in the ‘one-pot’ approach,” Dr Campbell says. “The traditional process has up to 12 manufacturing steps – with a precursor, grinding with lithium hydroxide as a strong alkali, drying it and keeping it dry, then putting it in a furnace to get the lithium soak into the oxide – which can take 30 to 40 hours. That was fine with cell phone batteries but producing 1 Mt of lithium produces 2-4 Mt of waste.”
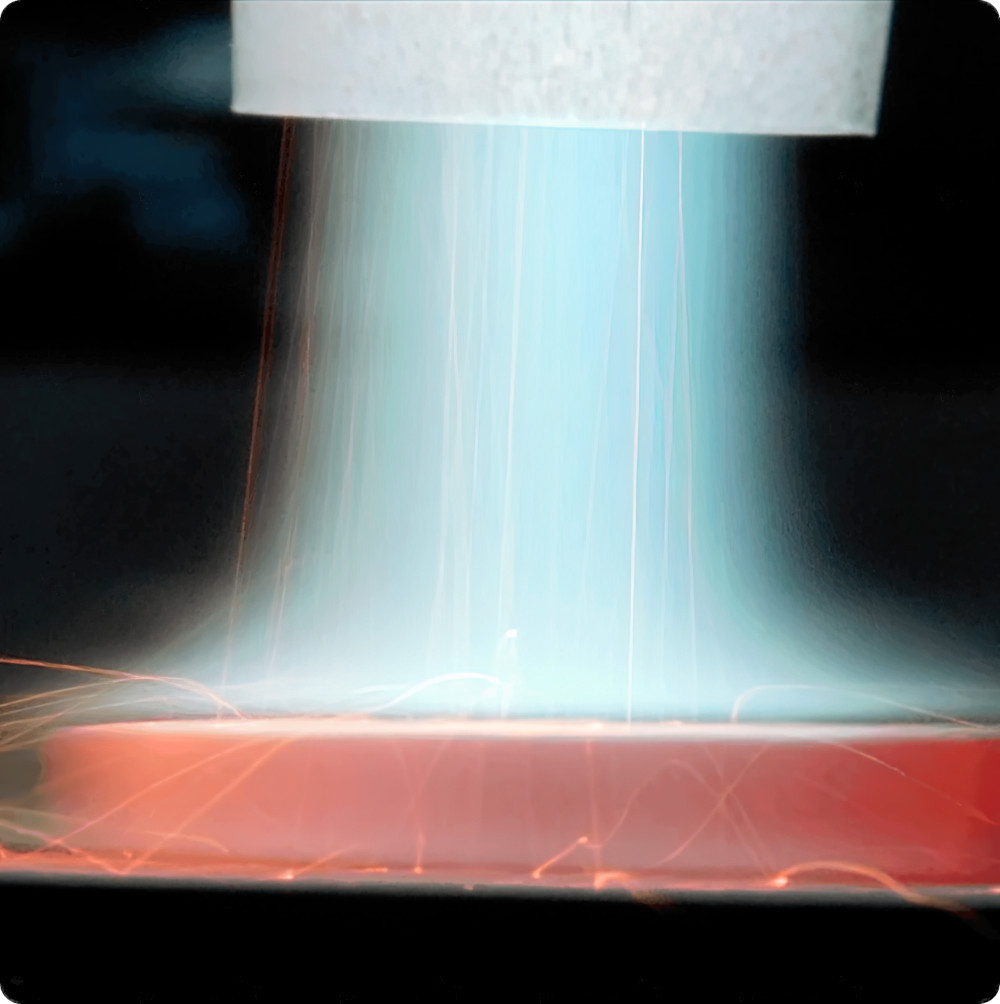
(Courtesy of 6K)
“Instead we put lithium, nickel, manganese, cobalt and all the doping materials into a reactor. The chemical process is very different from the conventional process, and the reagents are bio-derived to reduce greenhouse gas emissions,” he says.
The process doesn’t have a coating step; the cathode materials come out coated. The reagents also burn up, reducing the waste.
“We have a shorter firing time in oxygen, less than 10 hours, which leads to a more durable material,” Dr Campbell says. “We make our own pouch cells and have seen some very promising results.”
The company is applying its process philosophy to a range of cathode active materials. The plan is to build up manufacturing capacity for LFP in North America alongside what it calls a Multi-Cam Piloting Hub, which will develop piloted processes for high-nickel NMC and manganese-rich materials.
It is buying the only existing LFP plant in North America, in Canada, and plans to pilot the process for other materials.
“We are also working with collaborators on next-generation materials. It’s a different chemistry with the phosphates, so there are different reagents and feedstocks, but the materials are all available outside China as we are looking to establish a sustainable supply chain,” Dr Campbell says.
Microwave processing
Process developer 6K is using microwaves to create high temperatures that create cathode materials with smaller grains as well as single crystals. Its UniMelt process can be used to create NMC811 crystals of 1-3 microns as well as single-crystal NMC cathodes.
The ability to produce smaller sizes by adjusting the manufacturing process enables cathode developers to improve charge time, extend runtime and improve power.
“We are responding to demand from customers in the EV and consumer battery markets who are seeking higher nickel content and smaller NMCs,” says Dr Richard Holman, VP of battery products at 6K. “Our team was able to adapt the NMC-622 process to produce NMC-811 at over 200 mAh/g, and dial in sizes from 1-3 microns.
The microwave process can be used with essentially any chemistry, says the company. The combination of chemistry and morphology control means materials can be independently designed to optimise them for power, energy density and cost.
6K has already used the process for LTO, NMC-333, NMC-532, NMC-622, NMC-811 and higher nickel NMC cathodes as well as silicon anodes including nano-structured foam and intermetallic composite powders.
Conclusion
There are many options for cathode materials in lithium-ion batteries for e-mobility applications, from NMC to LFP and spinel for solid-state cells. Research into the different materials and crystal structures continues to boost the energy density of cells, while new manufacturing processes are aiming to deliver these materials more cost-effectively for the sustainable high-volume production needed to supply the industry around the world.
ONLINE PARTNERS
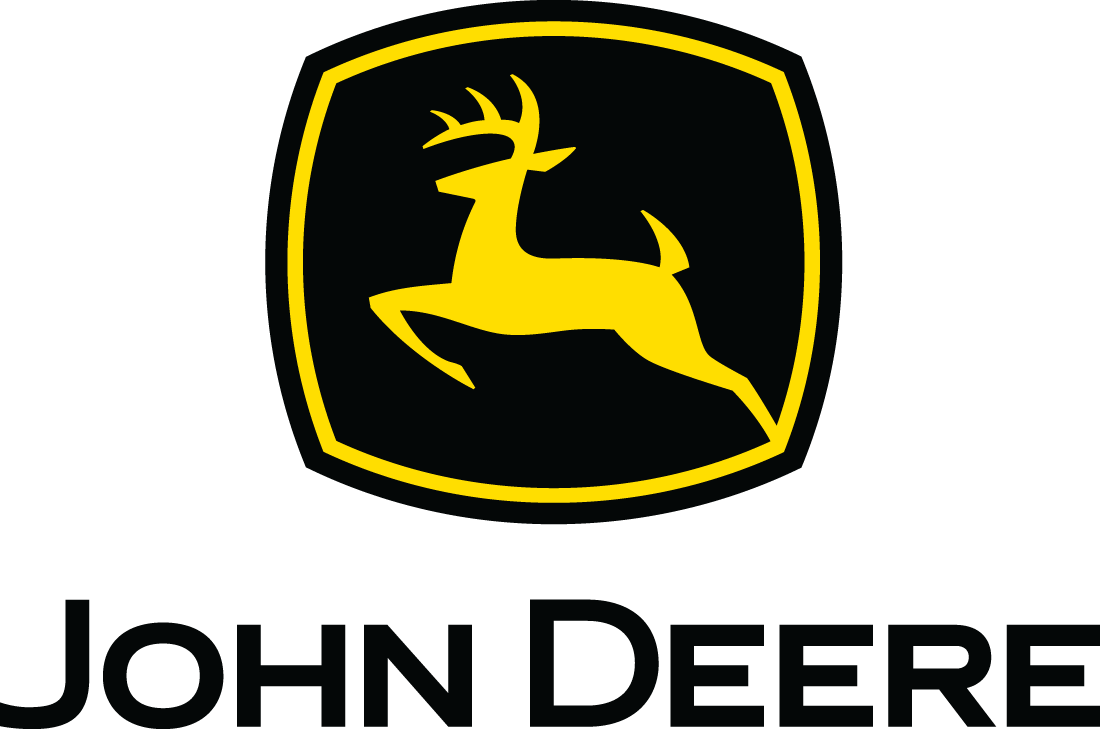
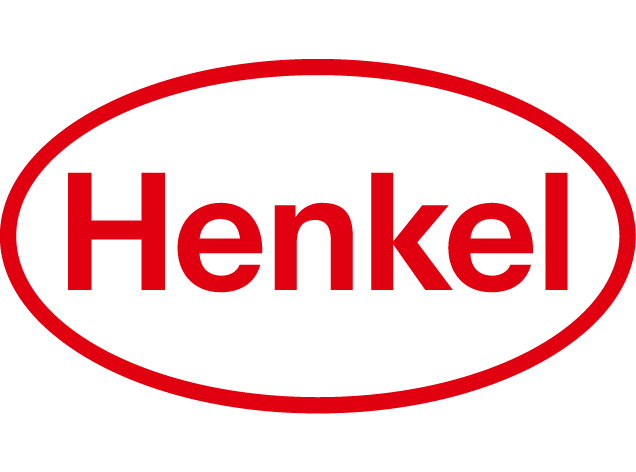
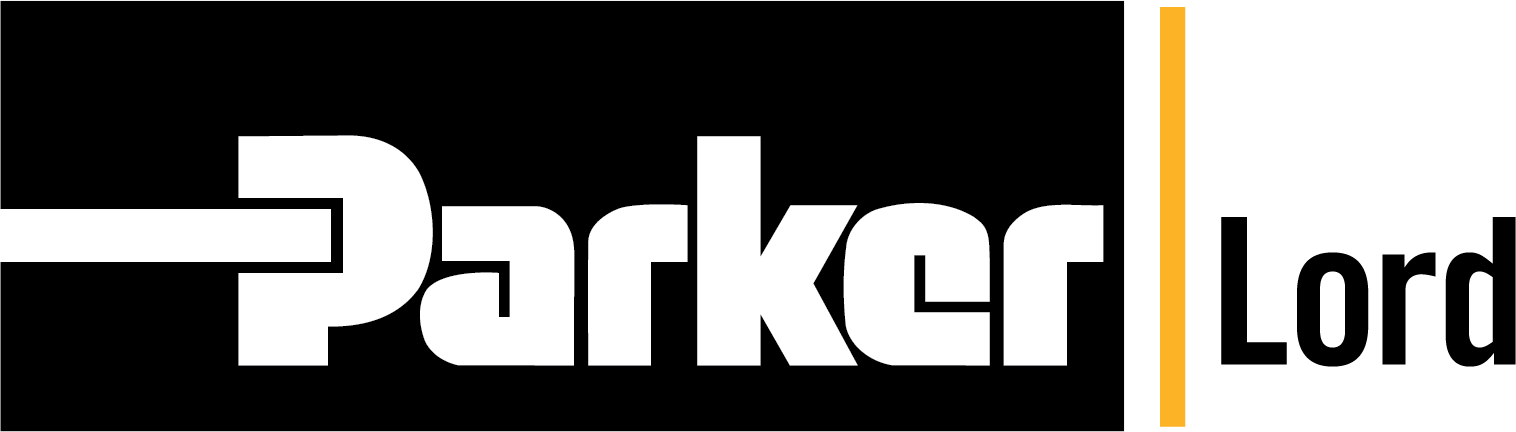
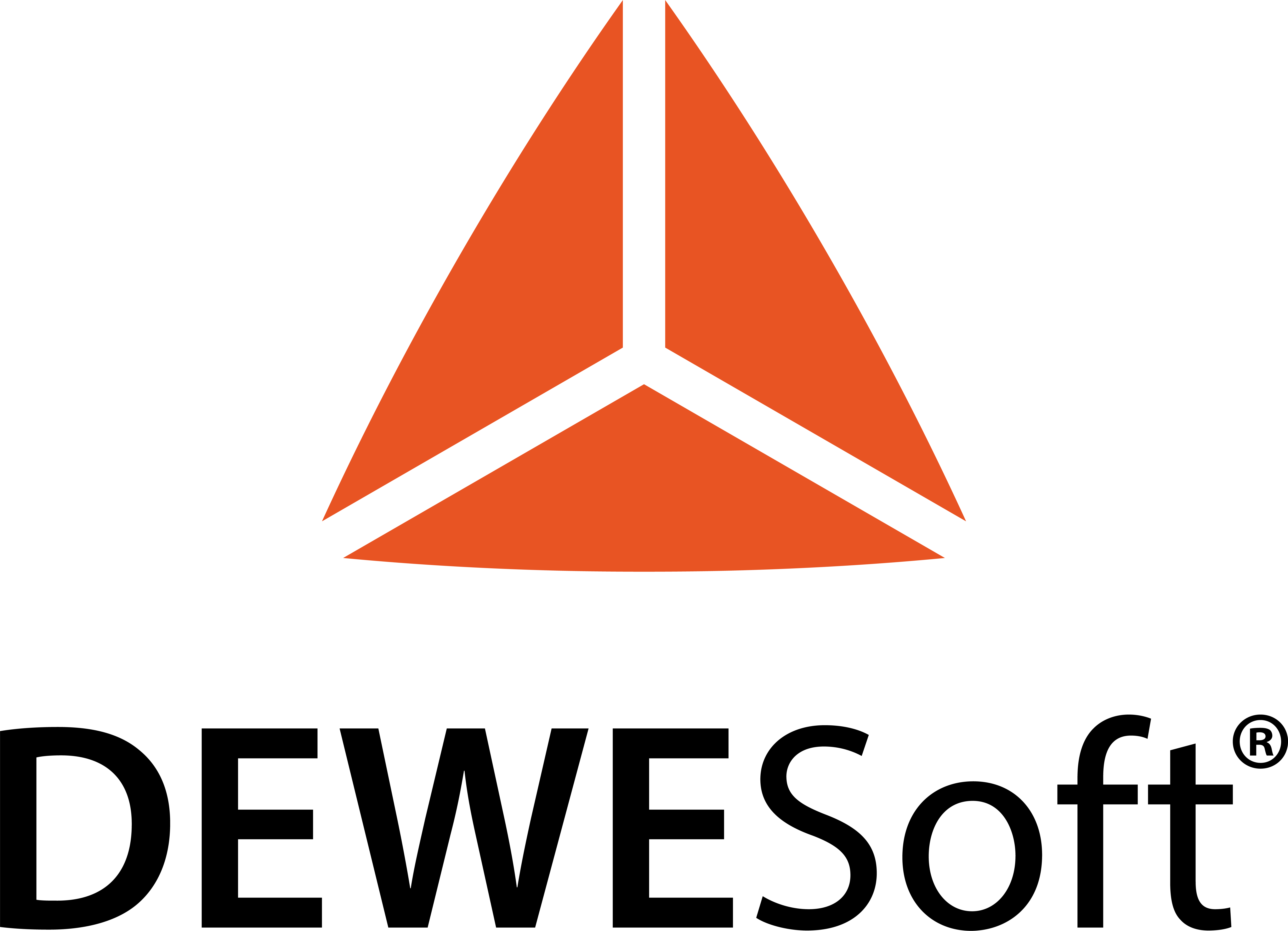
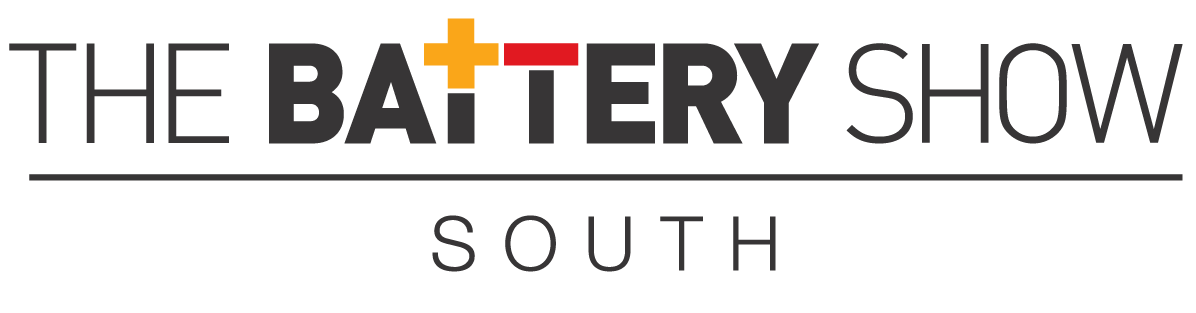
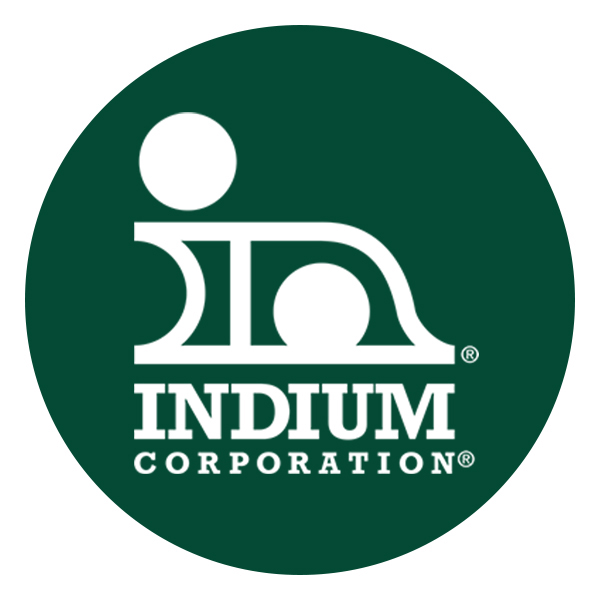

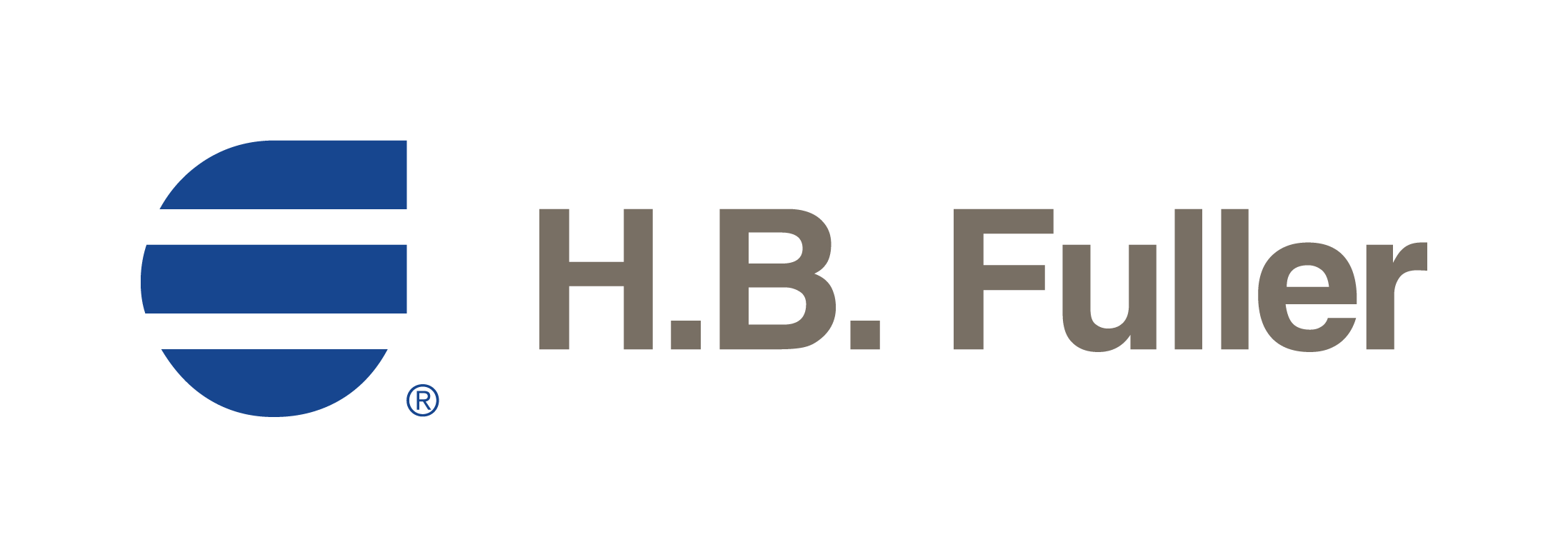
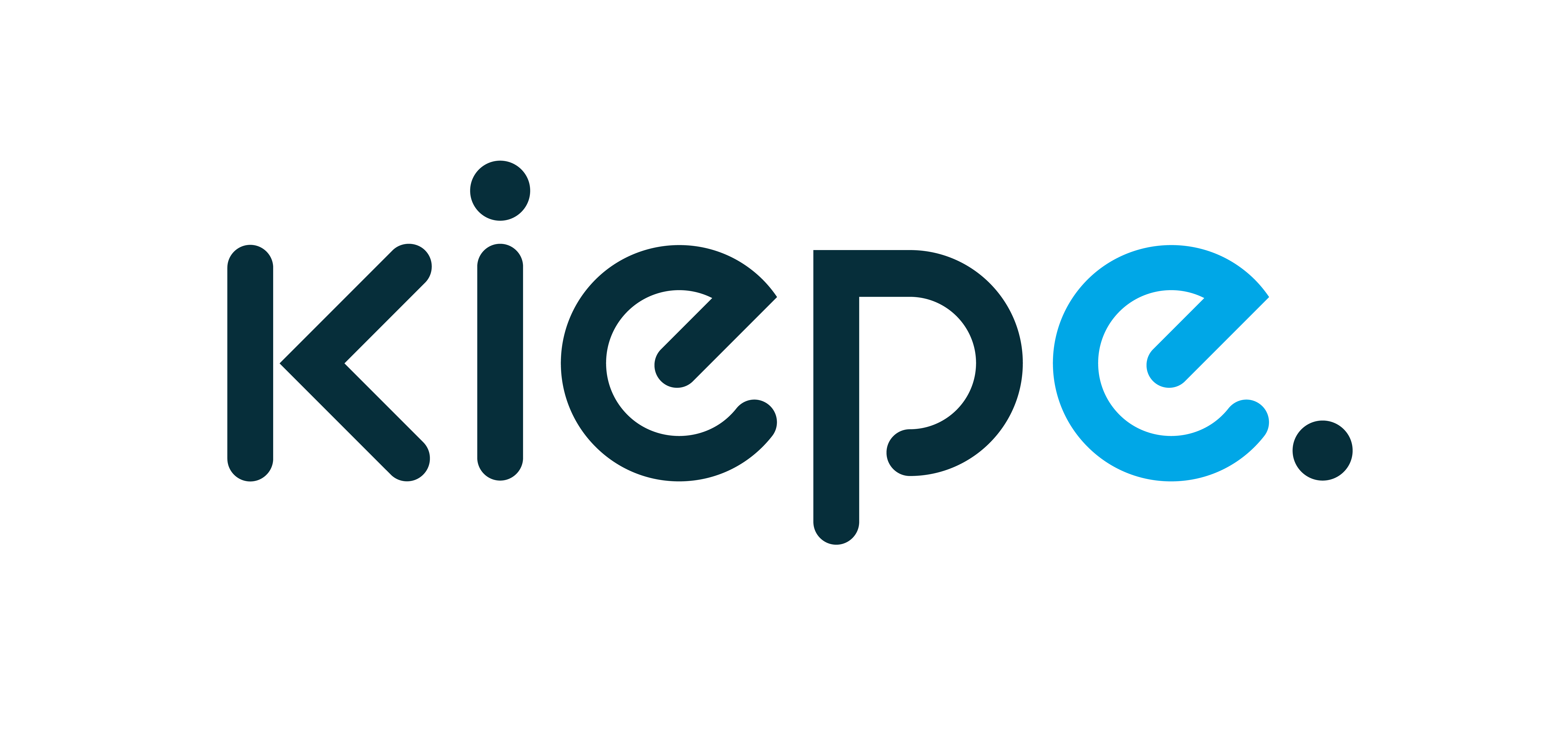
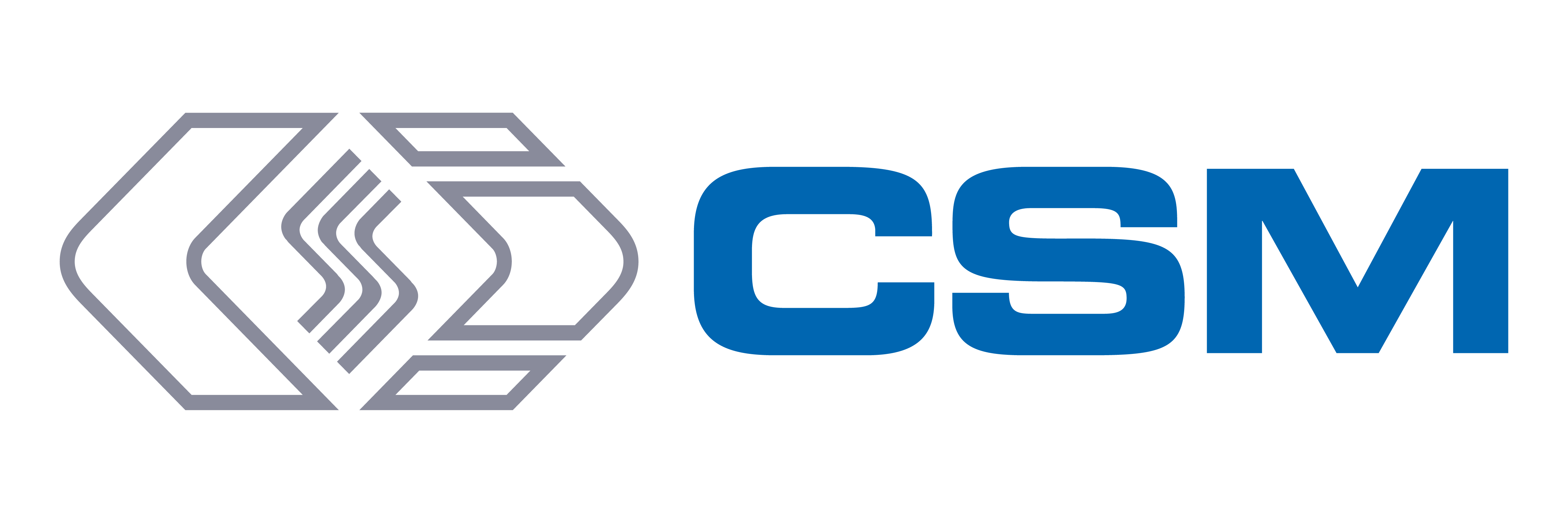