Burger Group launches actuators for thermal management
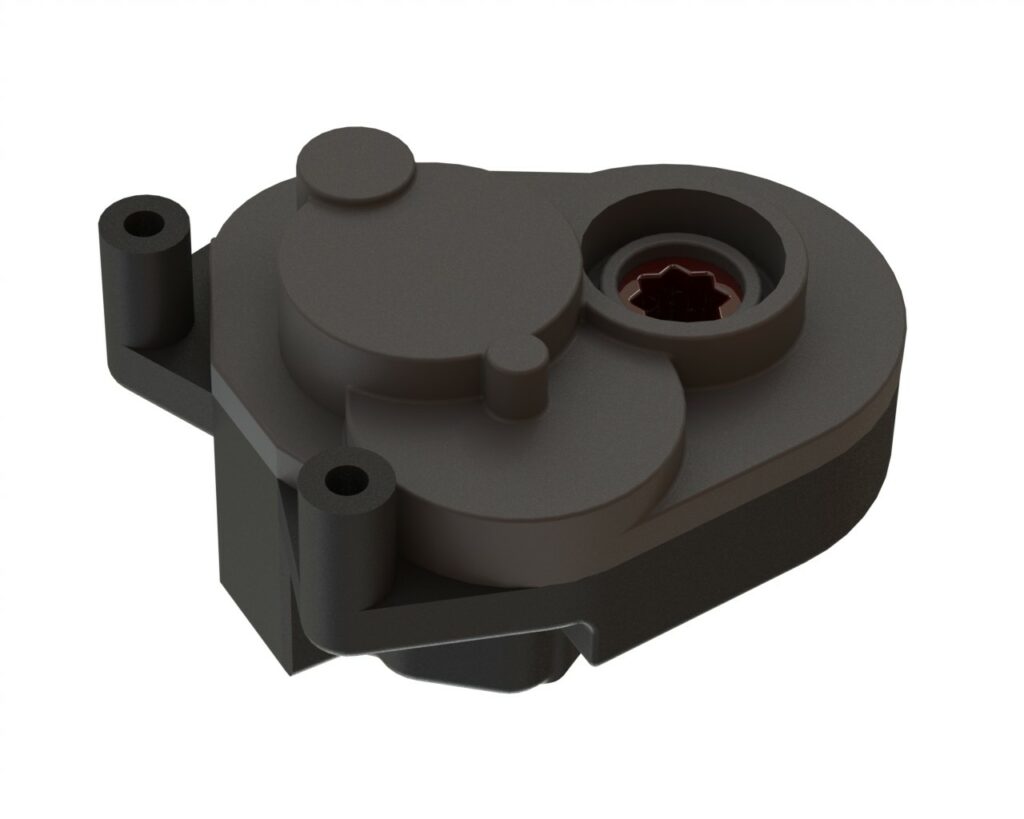
(Images courtesy of the Burger Group)
Automotive products developer Burger Group has developed a range of electromechanical valve actuators for tackling the specific requirements of controlling active thermal management systems in vehicles (writes Rory Jackson).
Stefan Schafer, the company’s business development manager, says, “I’ve been working in thermal management for about 10 years now. Based on trends I’ve seen in the industry, EV OEMs are moving towards these kinds of modules for coolant, refrigerant or both. They are being engineered with a rising count of valves for delivering fluid to critical points of thermal concern, be it in battery packs, power electronics, HVACs and so on.
“COTS actuators are too limited and lack adjustability in terms of torque to work in these new kinds of thermal management module, especially as their designs are going from having three or four ports per valve to upwards of five and six, with more ports meaning bigger, heavier rotation bodies mounted to the valves. Tesla for instance has an eight port-per-valve module now, and Nio is using a nine-port valve.”
New automotive standards also aim to forbid the use of PTFE, which many COTS actuators might still integrate in their case seals. The Burger Group has therefore optimised four actuator products to work without PTFE seals and provide the torque densities necessary for managing high numbers of fluid ports.
These come in standardised form factors and performance ratings, although the various parts inside each one can be chosen to customise the unit for specific customer requirements, for example by selecting the DC motor inside each actuator for the necessary torque, choosing the gearbox materials to meet a specified lifespan, or reshaping the housing to create a drop-in replacement for a different actuator.
“Most thermal management actuators use gears made from polyoxymethylene, but we can also use polyetheretherketone – which is more expensive but has a longer lifespan – as well as stainless steels, aluminiums and others,” Schafer says.
“We can also use different methods of position sensing depending on lifespan and integrity requirements, such as Hall effect sensors with a magnet in the gear output shaft for readings accurate to ±1º.”
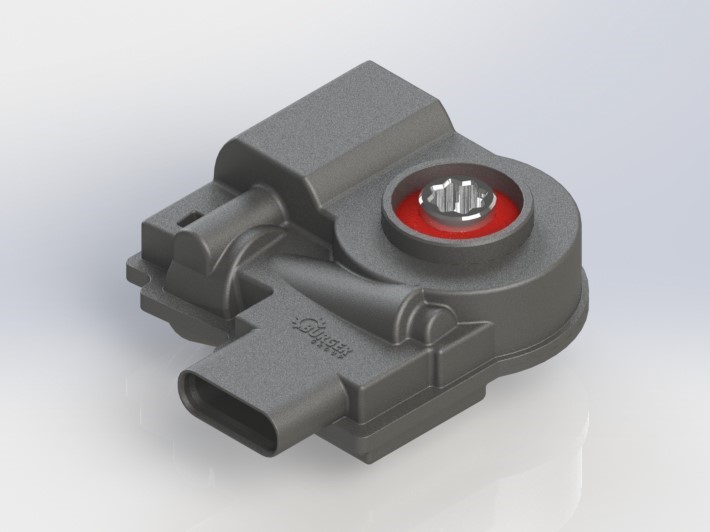
Its HTDC and HTBL actuators are new products developed from blank sheets for new thermal management requirements. Also included in the range are its EVO and FS (Failsafe) actuators, which the company is now customising for torque and other parameters.
The HTDC and HTBL both weigh just under 150 g, measure 80 x 70 x 36 mm, produce 1 Nm of torque in nominal operation (up to a peak of just over 1.5 Nm), and can function in temperatures from -40 to +105 ºC, with a system lifespan of 300,000 cycles. The HTBL is designed with a BLDC motor, while the HTDC has a brushed DC motor.
“The BLDC motor in the HTBL was created especially by a specialist designer at the University of Munich for the torque and pricing suited for the thermal management market, so it’s a unique design, frameless to save weight and part costs,” Schafer says.
The EVO meanwhile weighs just under 135 g, measures 98 x 82 x 40 mm and produces 0.2 Nm of torque up to 0.8 Nm peak, while lasting for 1 million cycles and working in -40 to +160 ºC environments; it can also be designed with a brushed or brushless motor. The FS lasts for 600,000 cycles, and is a 310 g brushed-motor system measuring 130 x 90 x 57 mm and producing the same torque as the EVO.
“There are built-in passive safety features too,” Schafer add. “For instance, the FS actuator integrates a spring, such that if electricity in a car is shut off, it is mechanically turned back to a certain point. We also have springs with different levels of mechanical force depending on how fast customers want their valves passively fixed or closed.
“Our ability to customise is helped by the fact that we’re not optimised solely for high-volume production. Trucks, buses and off-road vehicles will need smaller, bespoke volumes, and we can go down to batches of 15,000 per unit design.”
All four units operate on 12 or 24 V buses, and interface over PWM or LIN bus, with 24 V CAN to be available on the HTDC, HTBL and FS from early 2024, which the Burger Group is offering with truck and bus integrations particularly in mind. The FS can also work via non-smart buses.
Click here to read the latest issue of E-Mobility Engineering.
ONLINE PARTNERS
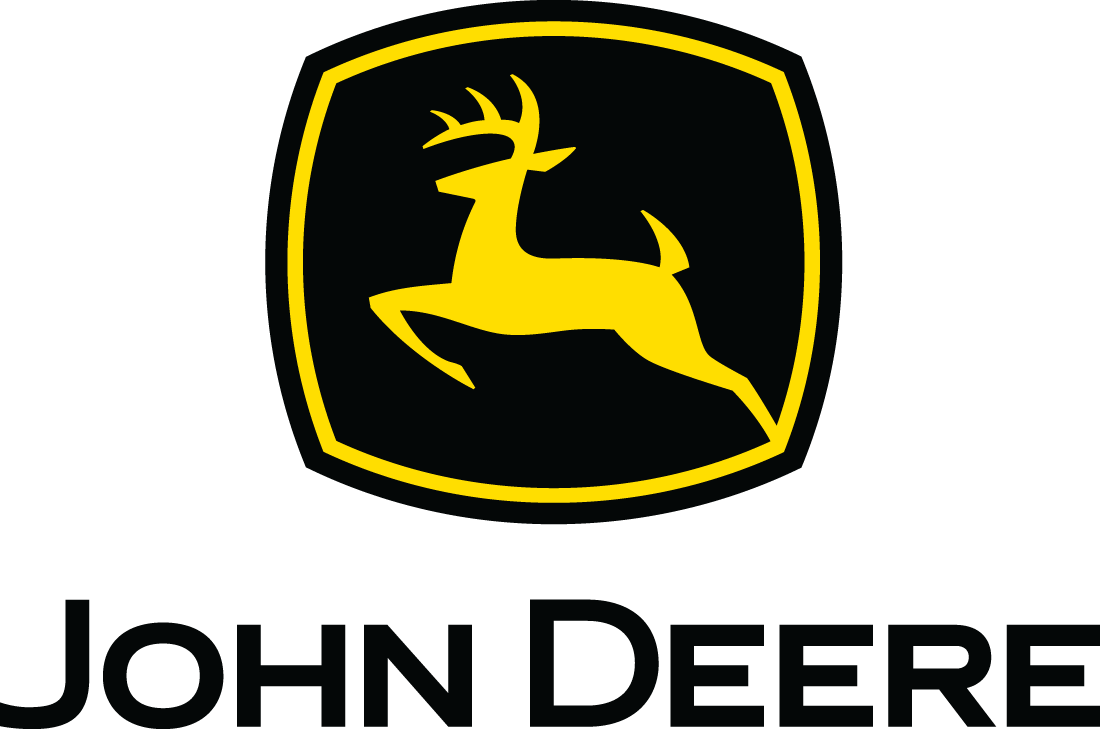
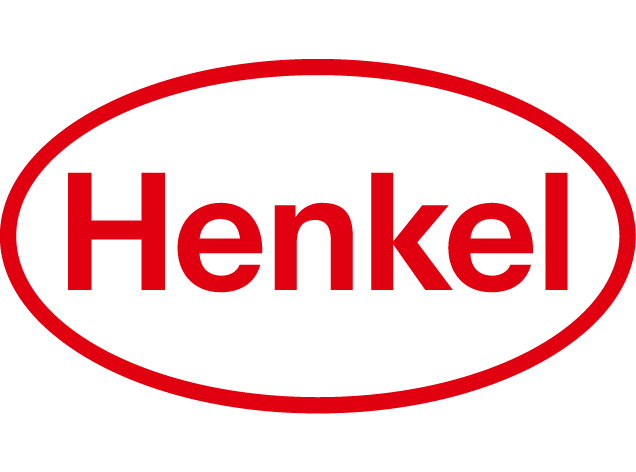
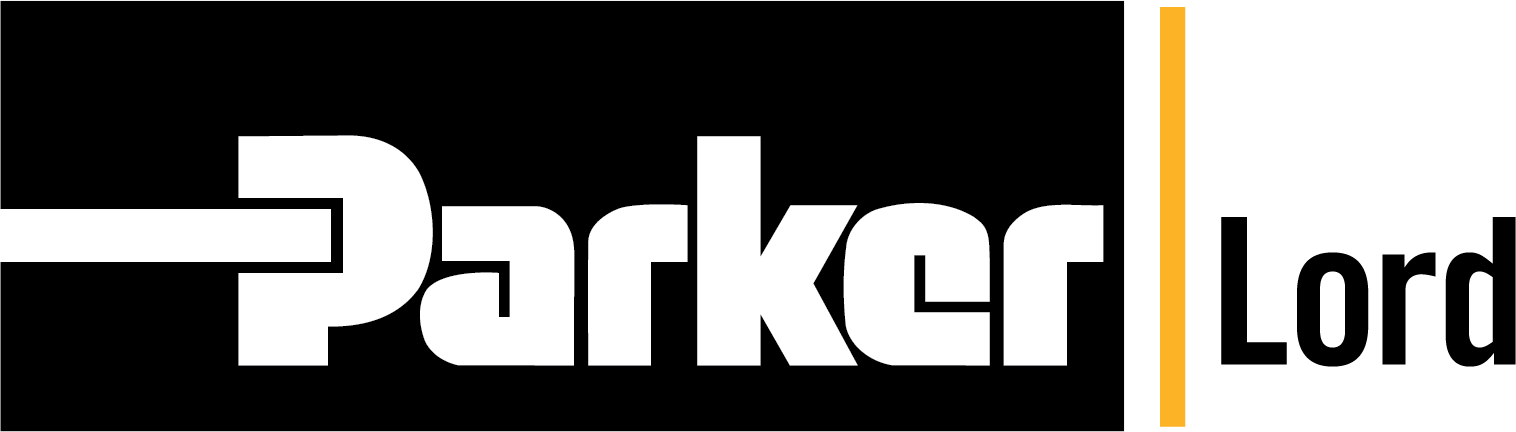
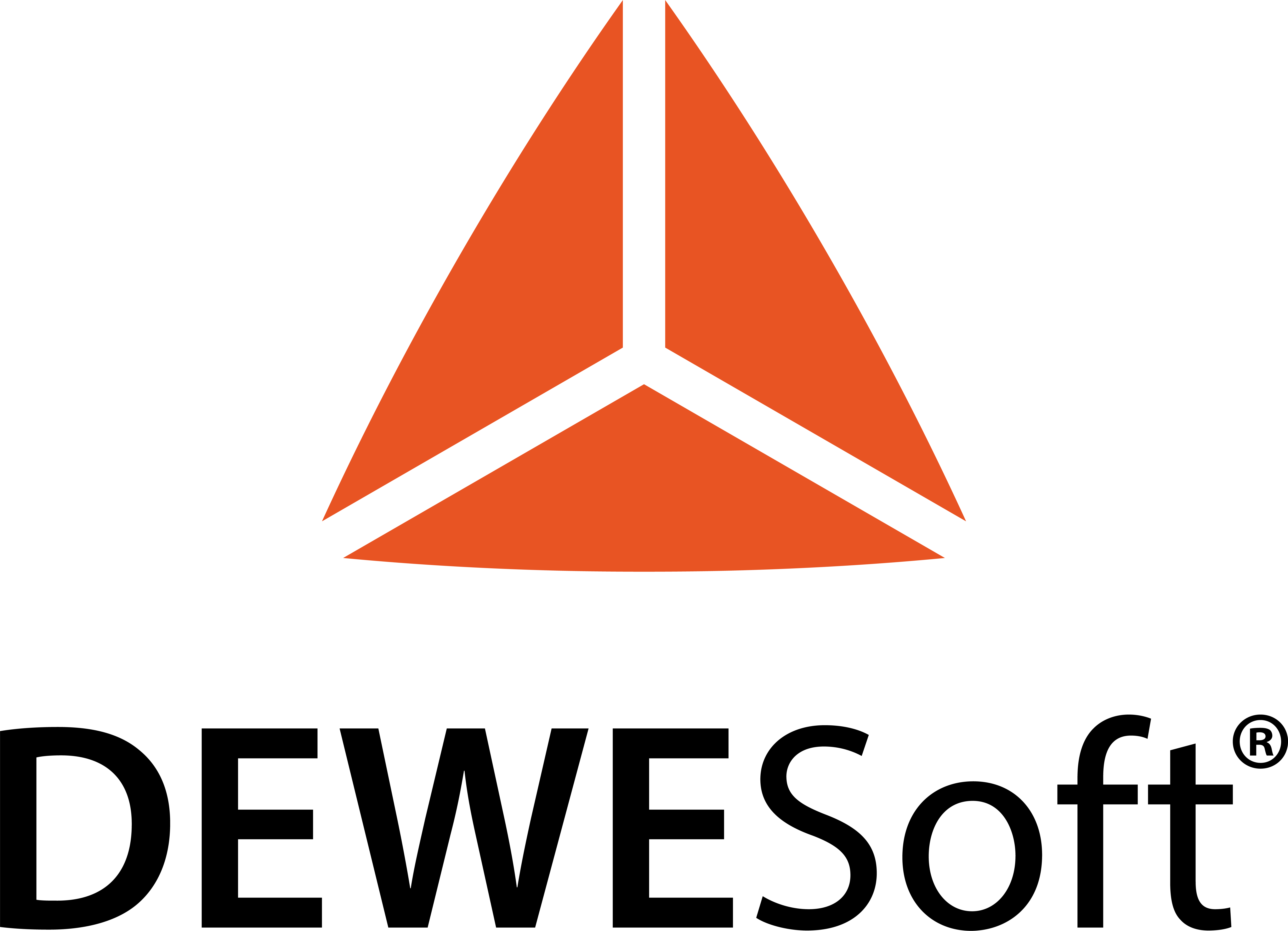
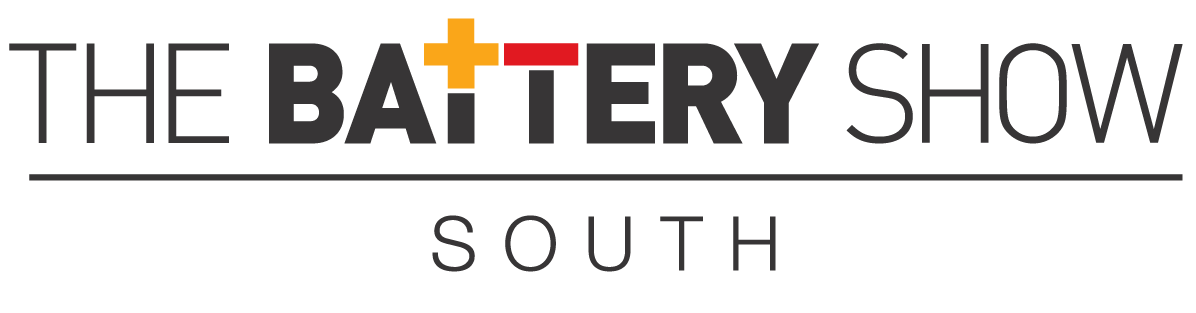
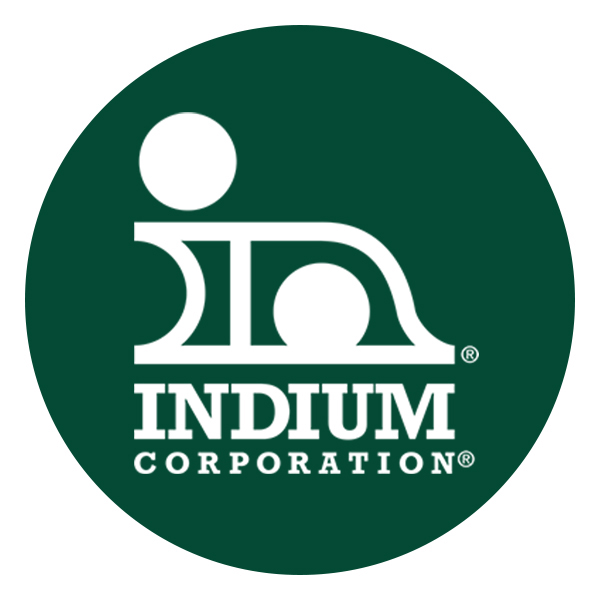
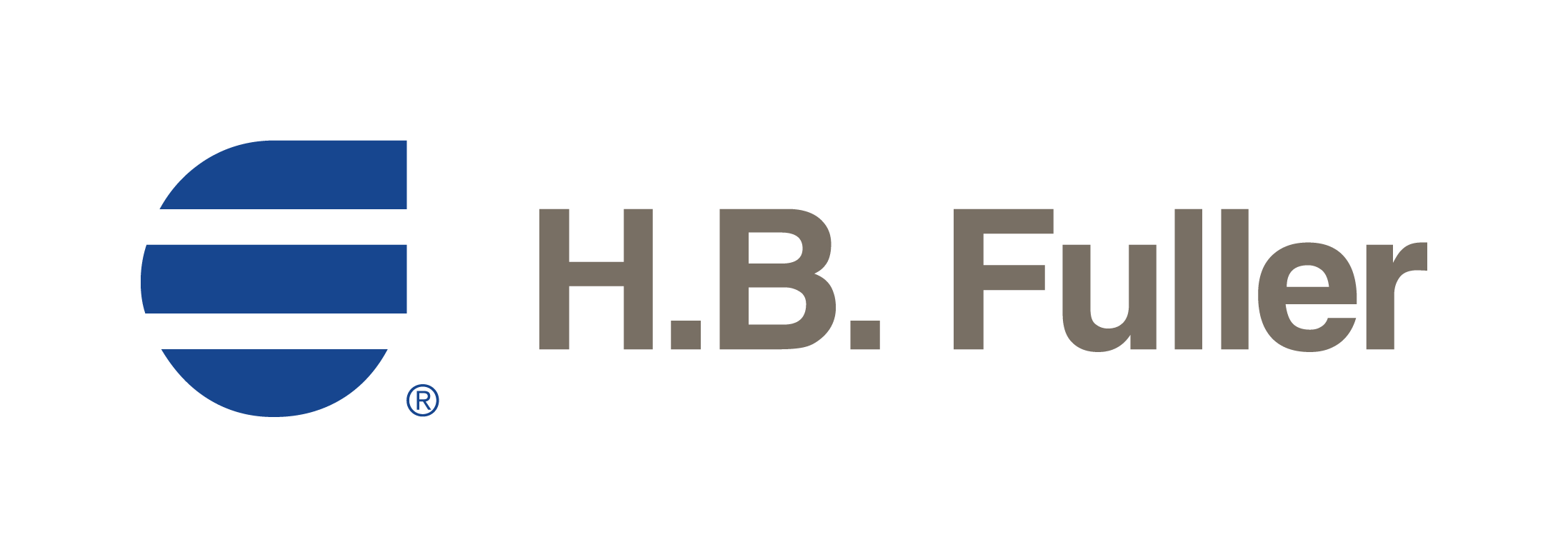